疲劳断裂特征
焊接结构的疲劳断裂

2023最新整理收集 do something
本章内容:1.焊接结构疲劳失效的分类及危害 2.焊接疲劳断裂的特征 3.焊接结构疲劳的原因及影响因素 4.焊接结构疲劳的防治措施
疲劳断裂是金属结构失效的一种主要形式。 大量统计资料表明,由于疲劳而失效的金属结构, 约占失效结构的90%。
劳极限”,
钢材的疲劳强度与抗拉强度之间的关系: σ-1 = (0.45~0.55)σb 条件疲劳极限:
钢材的循环次数一般取 N = 107 有色金属的循环次数一般取 N = 108
陶瓷、高分子材料-疲劳抗力很低; 金属材料-疲劳强度较高; 纤维增强复合材料-较好的抗疲劳性能。
四、疲劳断裂的类型
2、晶界处开裂 晶界就是面缺陷; 位错运动易发生塞积,出现应力集中,晶界
开裂。
3、相界面开裂 两相(包括第二相、夹杂)间的结合力差,
各相的形变速率不同,易在相结合处或弱相内出 现开裂。 只有首先达到临界尺寸的裂纹核,才能继续
长大。
二、疲劳裂纹扩展过程及机理
1、裂纹扩展的两个阶段 第一阶段 沿主滑移系,以纯剪切方式向内扩展;扩展速
例如,某电厂水冷壁下的集箱(15钢)在 长期运行中受热不均匀经受较大的交变热 应力,致使集箱产生热疲劳破坏。
1、基本概念 在循环热应力和热应变作用下,产生的
疲劳称为热疲劳。
热疲劳属低周疲劳(周期短;明显塑性 变形)。
由温度和机械应力叠加引起的疲劳,称 为热机械疲劳。
2、热应力的产生 外部约束 不让材料自由膨胀; 内部约束 温度梯度,相互约束,产生热应力。 热应变 导致裂纹的萌生,扩展。
这种应力称为交变应力。
二、平均应力:
三、应力幅:
疲劳破坏特征
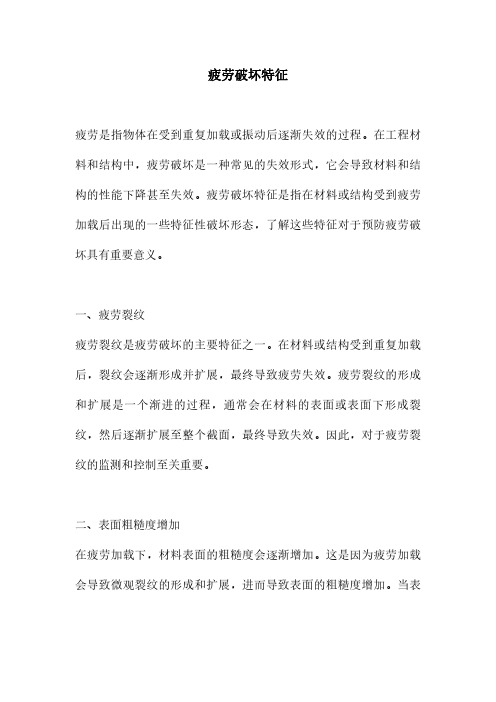
疲劳破坏特征
疲劳是指物体在受到重复加载或振动后逐渐失效的过程。
在工程材料和结构中,疲劳破坏是一种常见的失效形式,它会导致材料和结构的性能下降甚至失效。
疲劳破坏特征是指在材料或结构受到疲劳加载后出现的一些特征性破坏形态,了解这些特征对于预防疲劳破坏具有重要意义。
一、疲劳裂纹
疲劳裂纹是疲劳破坏的主要特征之一。
在材料或结构受到重复加载后,裂纹会逐渐形成并扩展,最终导致疲劳失效。
疲劳裂纹的形成和扩展是一个渐进的过程,通常会在材料的表面或表面下形成裂纹,然后逐渐扩展至整个截面,最终导致失效。
因此,对于疲劳裂纹的监测和控制至关重要。
二、表面粗糙度增加
在疲劳加载下,材料表面的粗糙度会逐渐增加。
这是因为疲劳加载会导致微观裂纹的形成和扩展,进而导致表面的粗糙度增加。
当表
面粗糙度增加到一定程度时,会导致应力集中和疲劳裂纹的形成,加剧了疲劳破坏的发展。
三、变形增加
在疲劳加载下,材料或结构的变形会逐渐增加。
这是因为疲劳加载会导致材料的塑性变形,进而导致变形增加。
随着变形的增加,材料或结构的强度和刚度会逐渐下降,最终导致疲劳失效。
综上所述,疲劳破坏特征包括疲劳裂纹的形成和扩展、表面粗糙度的增加以及变形的增加。
了解这些特征对于预防疲劳破坏具有重要意义,可以通过监测和控制这些特征来延缓疲劳失效的发生,提高材料和结构的使用寿命。
简述疲劳破坏的特征。
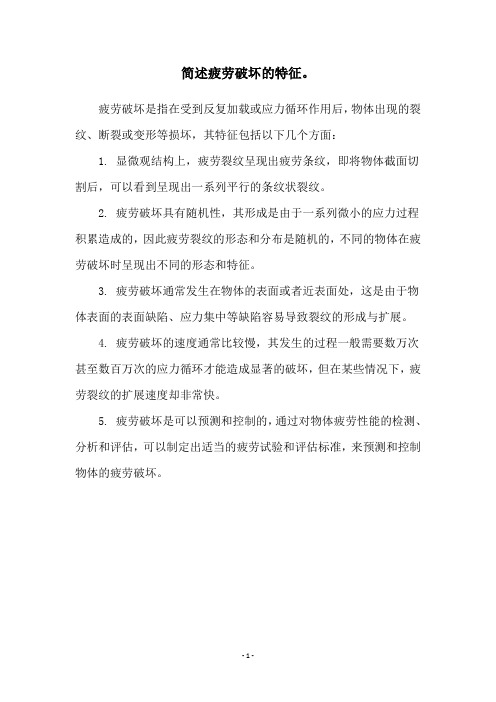
简述疲劳破坏的特征。
疲劳破坏是指在受到反复加载或应力循环作用后,物体出现的裂纹、断裂或变形等损坏,其特征包括以下几个方面:
1. 显微观结构上,疲劳裂纹呈现出疲劳条纹,即将物体截面切割后,可以看到呈现出一系列平行的条纹状裂纹。
2. 疲劳破坏具有随机性,其形成是由于一系列微小的应力过程积累造成的,因此疲劳裂纹的形态和分布是随机的,不同的物体在疲劳破坏时呈现出不同的形态和特征。
3. 疲劳破坏通常发生在物体的表面或者近表面处,这是由于物体表面的表面缺陷、应力集中等缺陷容易导致裂纹的形成与扩展。
4. 疲劳破坏的速度通常比较慢,其发生的过程一般需要数万次甚至数百万次的应力循环才能造成显著的破坏,但在某些情况下,疲劳裂纹的扩展速度却非常快。
5. 疲劳破坏是可以预测和控制的,通过对物体疲劳性能的检测、分析和评估,可以制定出适当的疲劳试验和评估标准,来预测和控制物体的疲劳破坏。
- 1 -。
疲劳断裂的基本特征

疲劳断裂的基本特征疲劳断裂是一种金属和材料在长时间的应力作用下逐渐产生裂纹并最终失效的现象。
它是一种破坏行为,常见于机械结构和工程材料中。
疲劳断裂的基本特征包括裂纹形成、裂纹扩展和失效破坏。
疲劳断裂的形成通常经历三个阶段。
首先是应力集中,也就是在材料表面或内部出现应力集中的区域。
这种应力集中可以由缺陷、凹槽、划痕等引起。
其次是裂纹的形成,应力集中区域的材料开始发生微小的裂纹,这些裂纹通常是微观的,难以察觉。
最后是裂纹的扩展,随着应力的作用,裂纹逐渐扩展,最终导致材料的失效。
疲劳断裂的特点是裂纹的扩展是一个渐进性的过程。
在应力作用下,裂纹从微小到逐渐扩展,直到达到材料的强度极限。
这个过程被称为裂纹的扩展阶段。
裂纹扩展的速度受到多个因素的影响,包括应力水平、应力周期、材料的力学性能等。
一般来说,应力水平越高、应力周期越大、材料的力学性能越差,裂纹扩展的速度越快。
疲劳断裂的失效破坏通常是突然发生的。
在裂纹扩展到一定程度后,材料的强度将急剧下降,裂纹会迅速扩展并导致材料的失效。
这种失效破坏是突然发生的,没有明显的预警信号。
因此,对于承受疲劳载荷的结构和材料,必须进行定期的检测和维护,以防止疲劳断裂的发生,确保结构的安全性。
为了预防和控制疲劳断裂,人们采取了许多措施。
首先是改善材料的力学性能,提高材料的韧性和强度,减少裂纹扩展的速度。
其次是设计合理的结构,避免应力集中的出现,减少裂纹的形成。
此外,还可以采用表面处理、应力涂层、热处理等方法来提高材料的抗疲劳性能。
在使用过程中,要注意控制应力水平和应力周期,避免过大的应力作用。
疲劳断裂是一种常见的材料失效形式,它具有裂纹形成、裂纹扩展和失效破坏等基本特征。
了解疲劳断裂的特点,对于改善材料的抗疲劳性能、设计合理的结构以及确保结构的安全性具有重要意义。
通过采取合适的预防和控制措施,可以有效地避免疲劳断裂的发生,延长材料和结构的使用寿命。
低周疲劳断裂的断口特征
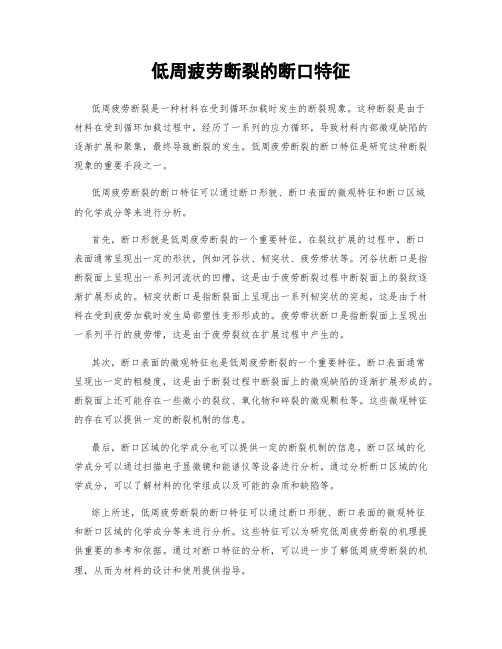
低周疲劳断裂的断口特征低周疲劳断裂是一种材料在受到循环加载时发生的断裂现象。
这种断裂是由于材料在受到循环加载过程中,经历了一系列的应力循环,导致材料内部微观缺陷的逐渐扩展和聚集,最终导致断裂的发生。
低周疲劳断裂的断口特征是研究这种断裂现象的重要手段之一。
低周疲劳断裂的断口特征可以通过断口形貌、断口表面的微观特征和断口区域的化学成分等来进行分析。
首先,断口形貌是低周疲劳断裂的一个重要特征。
在裂纹扩展的过程中,断口表面通常呈现出一定的形状,例如河谷状、韧突状、疲劳带状等。
河谷状断口是指断裂面上呈现出一系列河流状的凹槽,这是由于疲劳断裂过程中断裂面上的裂纹逐渐扩展形成的。
韧突状断口是指断裂面上呈现出一系列韧突状的突起,这是由于材料在受到疲劳加载时发生局部塑性变形形成的。
疲劳带状断口是指断裂面上呈现出一系列平行的疲劳带,这是由于疲劳裂纹在扩展过程中产生的。
其次,断口表面的微观特征也是低周疲劳断裂的一个重要特征。
断口表面通常呈现出一定的粗糙度,这是由于断裂过程中断裂面上的微观缺陷的逐渐扩展形成的。
断裂面上还可能存在一些微小的裂纹、氧化物和碎裂的微观颗粒等。
这些微观特征的存在可以提供一定的断裂机制的信息。
最后,断口区域的化学成分也可以提供一定的断裂机制的信息。
断口区域的化学成分可以通过扫描电子显微镜和能谱仪等设备进行分析。
通过分析断口区域的化学成分,可以了解材料的化学组成以及可能的杂质和缺陷等。
综上所述,低周疲劳断裂的断口特征可以通过断口形貌、断口表面的微观特征和断口区域的化学成分等来进行分析。
这些特征可以为研究低周疲劳断裂的机理提供重要的参考和依据。
通过对断口特征的分析,可以进一步了解低周疲劳断裂的机理,从而为材料的设计和使用提供指导。
变应力下,零件疲劳断裂的特征
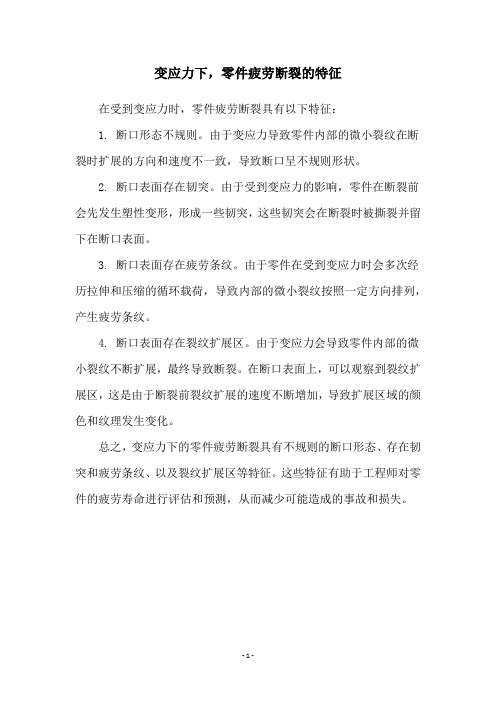
变应力下,零件疲劳断裂的特征
在受到变应力时,零件疲劳断裂具有以下特征:
1. 断口形态不规则。
由于变应力导致零件内部的微小裂纹在断裂时扩展的方向和速度不一致,导致断口呈不规则形状。
2. 断口表面存在韧突。
由于受到变应力的影响,零件在断裂前会先发生塑性变形,形成一些韧突,这些韧突会在断裂时被撕裂并留下在断口表面。
3. 断口表面存在疲劳条纹。
由于零件在受到变应力时会多次经历拉伸和压缩的循环载荷,导致内部的微小裂纹按照一定方向排列,产生疲劳条纹。
4. 断口表面存在裂纹扩展区。
由于变应力会导致零件内部的微小裂纹不断扩展,最终导致断裂。
在断口表面上,可以观察到裂纹扩展区,这是由于断裂前裂纹扩展的速度不断增加,导致扩展区域的颜色和纹理发生变化。
总之,变应力下的零件疲劳断裂具有不规则的断口形态、存在韧突和疲劳条纹、以及裂纹扩展区等特征。
这些特征有助于工程师对零件的疲劳寿命进行评估和预测,从而减少可能造成的事故和损失。
- 1 -。
疲劳断口的典型宏观特征
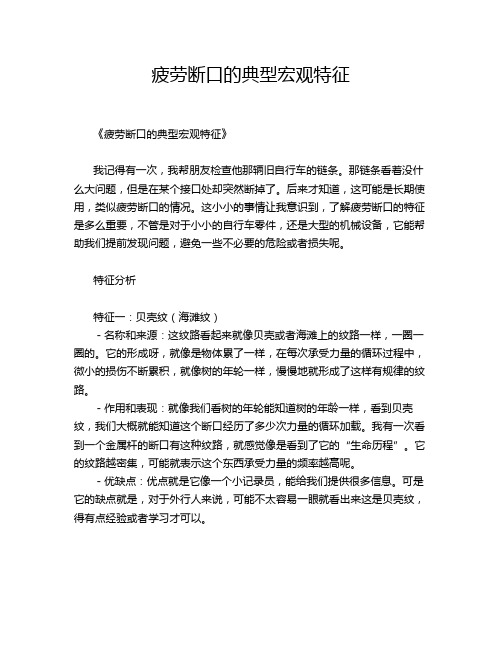
疲劳断口的典型宏观特征《疲劳断口的典型宏观特征》我记得有一次,我帮朋友检查他那辆旧自行车的链条。
那链条看着没什么大问题,但是在某个接口处却突然断掉了。
后来才知道,这可能是长期使用,类似疲劳断口的情况。
这小小的事情让我意识到,了解疲劳断口的特征是多么重要,不管是对于小小的自行车零件,还是大型的机械设备,它能帮助我们提前发现问题,避免一些不必要的危险或者损失呢。
特征分析特征一:贝壳纹(海滩纹)- 名称和来源:这纹路看起来就像贝壳或者海滩上的纹路一样,一圈一圈的。
它的形成呀,就像是物体累了一样,在每次承受力量的循环过程中,微小的损伤不断累积,就像树的年轮一样,慢慢地就形成了这样有规律的纹路。
- 作用和表现:就像我们看树的年轮能知道树的年龄一样,看到贝壳纹,我们大概就能知道这个断口经历了多少次力量的循环加载。
我有一次看到一个金属杆的断口有这种纹路,就感觉像是看到了它的“生命历程”。
它的纹路越密集,可能就表示这个东西承受力量的频率越高呢。
- 优缺点:优点就是它像一个小记录员,能给我们提供很多信息。
可是它的缺点就是,对于外行人来说,可能不太容易一眼就看出来这是贝壳纹,得有点经验或者学习才可以。
- 对事物性质或使用体验的影响:如果在一个机器的零件上发现了贝壳纹,那这个零件可能就已经承受了很多次的压力了,它的强度可能已经大打折扣了。
就像我们穿的鞋子,鞋底要是出现了类似的磨损纹路,那这双鞋可能就离坏掉不远了。
- 安全性和潜在问题:如果忽视了贝壳纹,可能会导致一些严重的后果。
比如在飞机的零部件上,如果有这种特征而没被发现,在飞行过程中可能会发生断裂,那可就是大灾难了。
特征二:疲劳源区- 名称和来源:这个区域就像是疲劳断口的“源头”。
它通常是因为零件在制造的时候可能存在一些小缺陷,或者是在使用过程中受到了一些局部的应力集中。
比如说一个金属块上有个小坑洼,每次受力的时候,这个小坑洼的地方受到的力就会比其他地方大很多,时间长了,这里就成了疲劳源区。
铝合金疲劳断裂的断口特征
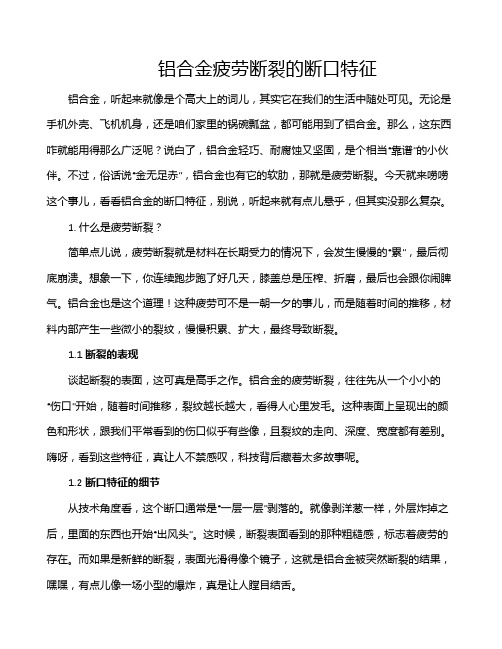
铝合金疲劳断裂的断口特征铝合金,听起来就像是个高大上的词儿,其实它在我们的生活中随处可见。
无论是手机外壳、飞机机身,还是咱们家里的锅碗瓢盆,都可能用到了铝合金。
那么,这东西咋就能用得那么广泛呢?说白了,铝合金轻巧、耐腐蚀又坚固,是个相当“靠谱”的小伙伴。
不过,俗话说“金无足赤”,铝合金也有它的软肋,那就是疲劳断裂。
今天就来唠唠这个事儿,看看铝合金的断口特征,别说,听起来就有点儿悬乎,但其实没那么复杂。
1. 什么是疲劳断裂?简单点儿说,疲劳断裂就是材料在长期受力的情况下,会发生慢慢的“累”,最后彻底崩溃。
想象一下,你连续跑步跑了好几天,膝盖总是压榨、折磨,最后也会跟你闹脾气。
铝合金也是这个道理!这种疲劳可不是一朝一夕的事儿,而是随着时间的推移,材料内部产生一些微小的裂纹,慢慢积累、扩大,最终导致断裂。
1.1 断裂的表现谈起断裂的表面,这可真是高手之作。
铝合金的疲劳断裂,往往先从一个小小的“伤口”开始,随着时间推移,裂纹越长越大,看得人心里发毛。
这种表面上呈现出的颜色和形状,跟我们平常看到的伤口似乎有些像,且裂纹的走向、深度、宽度都有差别。
嗨呀,看到这些特征,真让人不禁感叹,科技背后藏着太多故事呢。
1.2 断口特征的细节从技术角度看,这个断口通常是“一层一层”剥落的。
就像剥洋葱一样,外层炸掉之后,里面的东西也开始“出风头”。
这时候,断裂表面看到的那种粗糙感,标志着疲劳的存在。
而如果是新鲜的断裂,表面光滑得像个镜子,这就是铝合金被突然断裂的结果,嘿嘿,有点儿像一场小型的爆炸,真是让人瞠目结舌。
2. 为什么铝合金会疲劳断裂?哎,生活不易,材料也一样难。
铝合金疲劳断裂,最主要的原因就是各种应力。
不管是咱们日常使用中产生的静态应力,还是偶尔的冲击,时间久了,铝合金就像人一样,受不了的。
尤其在一些高强度环境下,铝合金真的容易变成“脆弱的小白兔”,到最后一触即发,炸成碎片。
2.1 环境因素的干扰别小看了环境因素,温度、湿度甚至是化学物质都能给铝合金带来“小麻烦”。
构件发生疲劳断裂时微观形貌特征

构件发生疲劳断裂时微观形貌特征一、引言疲劳断裂是材料科学和工程领域中一个重要的问题,它导致许多实际工程中的失效事故。
研究材料在疲劳载荷下的断裂行为及其微观形貌特征对于预防疲劳断裂具有重要的意义。
本文将探讨构件在疲劳断裂发生时的微观形貌特征。
二、疲劳断裂的基本特征1. 疲劳断裂是指在交变应力作用下,材料在较短时间内经历多次应力循环后出现断裂的现象。
2. 疲劳断裂的形貌特征包括疲劳裂纹的形态和扩展方向等。
三、微观形貌特征的分析1. 晶粒形貌特征在疲劳断裂过程中,晶粒会逐渐失去规则的排列状态,形成疲劳裂纹。
晶粒在断裂前后的形态变化对于断裂的过程和机制具有重要的意义。
2. 疲劳裂纹的扩展疲劳裂纹的扩展路径是材料疲劳断裂行为中的重要特征之一。
疲劳裂纹往往呈现出交错、分叉等形态,揭示了材料在疲劳断裂过程中的特殊应力状态及其对裂纹形成的影响。
3. 微观结构的变化材料在疲劳断裂过程中,其微观结构会发生变化,如晶粒尺寸的变化、位错堆积等。
这些变化对材料的强度和断裂性能都有重要影响,因此对微观结构的研究可以揭示材料疲劳断裂的机制。
四、疲劳断裂的机制1. 晶界滑移与扩展在疲劳断裂过程中,晶界的滑移与扩展是一个重要的机制。
晶界滑移的不规则扩展对材料的疲劳性能有重要影响。
2. 前驱裂纹的形成疲劳断裂过程中,前驱裂纹的形成是一个重要的环节。
微观形貌特征的分析可以帮助揭示前驱裂纹形成的机制。
3. 微观缺陷的影响材料在制备和应力加载过程中存在着各种微观缺陷,这些缺陷对疲劳断裂的形貌特征有重要的影响。
研究微观缺陷对疲劳断裂的影响,可以为材料设计和工程应用提供重要参考。
五、研究方法1. 金相显微镜观察金相显微镜是研究材料微观形貌特征的重要工具之一,通过观察材料的金相组织和晶粒形貌特征,可以揭示材料疲劳断裂的微观机理。
2. 电镜观察电镜是研究材料微观结构和形貌特征的重要手段,其高分辨率的观察能力可以揭示材料微观形貌特征的细节。
3. 数值模拟数值模拟是研究材料断裂行为和微观形貌特征的重要方法,通过模拟材料在疲劳载荷下的行为,可以揭示材料的疲劳断裂机制和微观形貌特征。
疲劳断裂的断口特征

疲劳断裂的断口特征疲劳断裂是指材料在反复加载下发生的断裂现象,通常发生在金属材料中。
与静态加载下的断裂不同,疲劳断裂的断口特征具有一些独特的特点。
本文将详细介绍疲劳断裂的断口特征。
1.断口形态:疲劳断裂的断口通常呈现出平面状的特点。
与静态断裂相比,疲劳断裂的断口形态更为平整,几乎没有韧突。
这是因为在疲劳断裂发生时,材料受到反复加载,导致断裂表面的塑性变形局部消失,使断口面显得平滑。
2.断口特征:疲劳断裂的断口通常呈现出沿着材料加载方向的特征。
即在金属材料的拉伸方向上会出现沿着材料加载方向延展的沟槽状断裂面。
这是因为在疲劳断裂过程中,裂纹的扩展方向通常与应力主轴方向(加载方向)垂直。
断口上也常见到横向的细小裂纹。
3.层状纹理:疲劳断裂的断口表面常常呈现出层状纹理。
这是由于疲劳断裂过程中,材料内部的裂纹扩展速度会与外部加载频率一致,导致断口形成沿裂纹扩展方向的“疲劳纹”或称为“疲劳条纹”。
这些纹理一般与材料的晶粒方向垂直,并且逐渐扩展进入材料内部。
4.波纹状断口:疲劳断裂的断口表面通常呈现出波纹状的特征。
这是由于裂纹在扩展过程中会遇到不同的晶粒,在晶粒界面处会发生细小的局部塑性形变,导致断口表面呈现出波浪状。
5. 轭型断口:在一些情况下,疲劳断裂的断口会呈现出轭型(chevron)的特征。
轭型断口是指裂纹扩展迅速并呈现出V字形的形状,类似于牛轭。
这种断口形态通常出现在晶粒细小且均匀的材料中,例如高强度钢。
6.焊缝位置:在焊接结构中,疲劳断裂通常在焊缝附近发生。
这是由于焊接过程中引入了应力集中、晶界腐蚀等因素,导致焊缝附近的材料更容易发生疲劳断裂。
总之,疲劳断裂的断口特征包括平面状的断口形态、沿加载方向的断口特征、层状纹理、波纹状断口、轭型断口等。
这些断口特征能够帮助工程师分析疲劳断裂的原因,并采取相应的措施预防疲劳断裂的发生。
疲劳断裂的特征分类及基础知识

No.1疲劳与断裂的概念1.疲劳:金属材料在应力或应变的反复作用下发生的性能变化称为疲劳。
2.疲劳断裂:材料承受交变循环应力或应变时,引起的局部结构变化和内部缺陷的不断地发展,使材料的力学性能下降,最终导致产品或材料的完全断裂,这个过程称为疲劳断裂,也可简称为金属的疲劳。
引起疲劳断裂的应力一般很低,疲劳断裂的发生,往往具有突发性、高度局部性及对各种缺陷的敏感性等特点。
No.2疲劳断裂的分类1.高周疲劳与低周疲劳如果作用在零件或构件的应力水平较低,破坏的循环次数高于10万次的疲劳,称为高周疲劳。
例如弹簧、传动轴、紧固件等类产品一般以高周疲劳见多。
作用在零件构件的应力水平较高,破坏的循环次数较低,一般低于1万次的疲劳,称为低周疲劳。
例如压力容器,汽轮机零件的疲劳损坏属于低周疲劳。
2.应力和应变分析应变疲劳——高应力,循环次数较低,称为低周疲劳;应力疲劳——低应力,循环次数较高,称为高周疲劳。
复合疲劳,但在实际中,往往很难区分应力与应变类型,一般情况下二种类型兼而有之,这样称为复合疲劳。
3.按照载荷类型分类弯曲疲劳、扭转疲劳、拉压疲劳、接触疲劳、振动疲劳、微动疲劳。
No.3疲劳断裂的特征宏观:裂纹源→扩展区→瞬断区。
裂纹源:表面有凹槽、缺陷,或者应力集中的区域是产生裂纹源的前提条件。
疲劳扩展区:断面较平坦,疲劳扩展与应力方向相垂直,产生明显疲劳弧线,又称为海滩纹或贝纹线。
瞬断区:是疲劳裂纹迅速扩展到瞬间断裂的区域,断口有金属滑移痕迹,有些产品瞬断区有放射性条纹并具有剪切唇区。
微观:疲劳断裂典型的特征是出现疲劳辉纹。
一些微观试样中还会出现解理与准解理现象(晶体学上的名称,在微观显象上出现的小平面),以及韧窝等微观区域特征。
No.4疲劳断裂的特点(1)断裂时没有明显的宏观塑性变形,断裂前没有明显的预兆,往往是突然性的产生,使机械零件产生的破坏或断裂的现象,危害十分严重。
(2)引起疲劳断裂的应力很低,往往低于静载时屈服强度的应力负荷。
疲劳断裂的基本形式
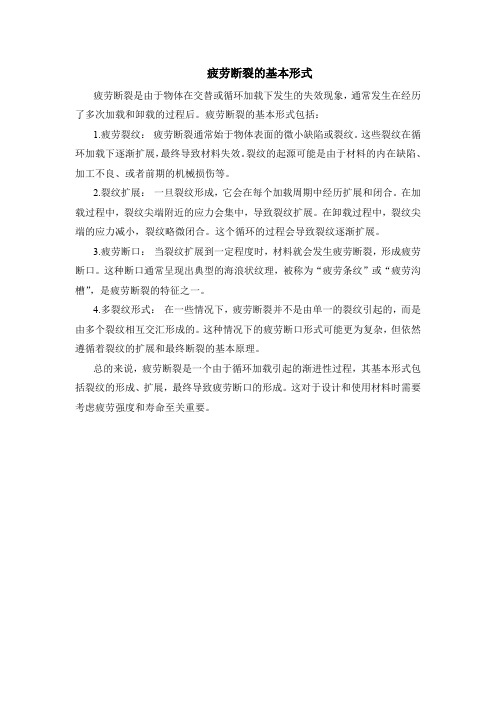
疲劳断裂的基本形式
疲劳断裂是由于物体在交替或循环加载下发生的失效现象,通常发生在经历了多次加载和卸载的过程后。
疲劳断裂的基本形式包括:
1.疲劳裂纹:疲劳断裂通常始于物体表面的微小缺陷或裂纹。
这些裂纹在循环加载下逐渐扩展,最终导致材料失效。
裂纹的起源可能是由于材料的内在缺陷、加工不良、或者前期的机械损伤等。
2.裂纹扩展:一旦裂纹形成,它会在每个加载周期中经历扩展和闭合。
在加载过程中,裂纹尖端附近的应力会集中,导致裂纹扩展。
在卸载过程中,裂纹尖端的应力减小,裂纹略微闭合。
这个循环的过程会导致裂纹逐渐扩展。
3.疲劳断口:当裂纹扩展到一定程度时,材料就会发生疲劳断裂,形成疲劳断口。
这种断口通常呈现出典型的海浪状纹理,被称为“疲劳条纹”或“疲劳沟槽”,是疲劳断裂的特征之一。
4.多裂纹形式:在一些情况下,疲劳断裂并不是由单一的裂纹引起的,而是由多个裂纹相互交汇形成的。
这种情况下的疲劳断口形式可能更为复杂,但依然遵循着裂纹的扩展和最终断裂的基本原理。
总的来说,疲劳断裂是一个由于循环加载引起的渐进性过程,其基本形式包括裂纹的形成、扩展,最终导致疲劳断口的形成。
这对于设计和使用材料时需要考虑疲劳强度和寿命至关重要。
疲劳断裂的特征分类及基础知识
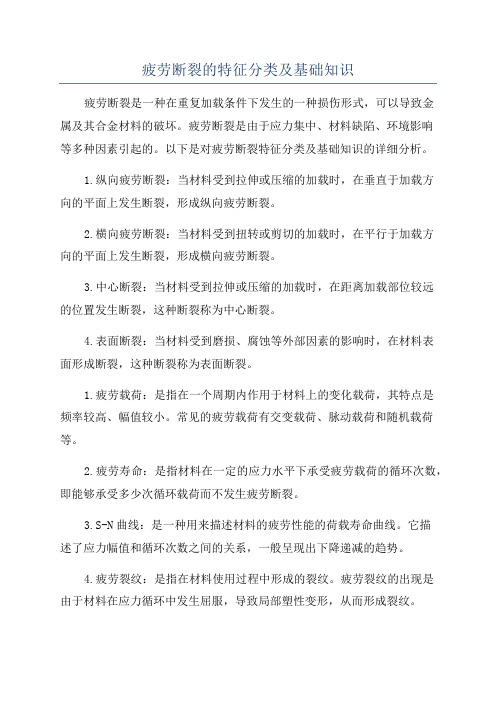
疲劳断裂的特征分类及基础知识疲劳断裂是一种在重复加载条件下发生的一种损伤形式,可以导致金属及其合金材料的破坏。
疲劳断裂是由于应力集中、材料缺陷、环境影响等多种因素引起的。
以下是对疲劳断裂特征分类及基础知识的详细分析。
1.纵向疲劳断裂:当材料受到拉伸或压缩的加载时,在垂直于加载方向的平面上发生断裂,形成纵向疲劳断裂。
2.横向疲劳断裂:当材料受到扭转或剪切的加载时,在平行于加载方向的平面上发生断裂,形成横向疲劳断裂。
3.中心断裂:当材料受到拉伸或压缩的加载时,在距离加载部位较远的位置发生断裂,这种断裂称为中心断裂。
4.表面断裂:当材料受到磨损、腐蚀等外部因素的影响时,在材料表面形成断裂,这种断裂称为表面断裂。
1.疲劳载荷:是指在一个周期内作用于材料上的变化载荷,其特点是频率较高、幅值较小。
常见的疲劳载荷有交变载荷、脉动载荷和随机载荷等。
2.疲劳寿命:是指材料在一定的应力水平下承受疲劳载荷的循环次数,即能够承受多少次循环载荷而不发生疲劳断裂。
3.S-N曲线:是一种用来描述材料的疲劳性能的荷载寿命曲线。
它描述了应力幅值和循环次数之间的关系,一般呈现出下降递减的趋势。
4.疲劳裂纹:是指在材料使用过程中形成的裂纹。
疲劳裂纹的出现是由于材料在应力循环中发生屈服,导致局部塑性变形,从而形成裂纹。
5.疲劳断裂预测:为了避免材料在使用过程中发生疲劳断裂,科学家和工程师会进行疲劳断裂预测。
这个过程包括材料的疲劳性能测试、疲劳寿命预测和结构设计等。
总结起来,疲劳断裂是一种由应力集中、材料缺陷和环境影响等引起的金属材料破坏形式。
根据断裂的位置和形状可以将其分类为纵向疲劳断裂、横向疲劳断裂、中心断裂和表面断裂。
了解疲劳载荷、疲劳寿命、S-N曲线、疲劳裂纹以及疲劳断裂预测等基础知识有助于理解和预防疲劳断裂的发生。
研究和应用这些知识对于材料的设计和使用至关重要。
疲劳断裂过程和断口的特征

疲劳断裂过程和断口的特征
疲劳断裂是材料在反复应用或循环载荷作用下,逐渐累积损伤最终导致破坏的一种现象。
这种断裂过程通常非突发性,而是随着时间推移而缓慢发展。
疲劳断裂的过程大致可以分为三个阶段:裂纹的形成(初始疲劳阶段)、裂纹的扩展以及最终的快速断裂。
1.(裂纹形成阶段:这个阶段发生在材料表面或近表面微小缺陷处,由于循环载荷的作用,这些区域会产生应力集中,并开始形成微裂纹。
这个阶段中,裂纹通常沿着与最大剪切应力方向成45度角的方向扩展,并且裂纹增长速率相对较慢。
2.(裂纹扩展阶段:随着时间的推移和循环次数的增加,裂纹将逐渐扩大。
在宏观上,可以观察到裂纹沿着垂直于施加载荷方向扩展,形成所谓的“疲劳海滩花纹”或“条纹线”,这是由于载荷变化引起的裂纹前进速度不一所致。
此阶段的断口通常比较平坦,有时呈现颗粒状或纤维状特征。
3.(最终断裂阶段:当裂纹达到临界尺寸,剩余截面无法承受应用载荷时,材料将发生快速的断裂。
这个阶段的断口往往呈现出较粗糙的、有剪切唇的特征,这是由于在最后断裂过程中,材料在局部区域经历了较大的塑性变形。
疲劳断口的显著特征包括有起始点或疲劳源区、裂纹扩展区和快速断裂区。
起始点往往是材料表面的缺陷、刻痕或内部夹杂物。
裂纹扩展区可能表现出典型的疲劳辉纹,它们是因裂纹前缘不断前进而在断口面上形成的条带状痕迹。
快速断裂区则显示出过载后的粗糙断口,有时伴有剪切唇。
了解疲劳断裂过程和断口特征对于材料的疲劳寿命预测、结构设计和失效分析具有重要意义。
通过仔细检查断口特征,可以识别出疲劳裂纹的起源,分析裂纹扩展的历史,从而为改进材料性能和预防未来疲劳失败提供依据。
疲劳断裂特征

rN r (N 持久疲劳极限 ND )
由于ND很大,所以在作疲劳试验时,常规定一个循环次数N0(称为循环基数),用N0 及其相对应的疲劳极限σr来近似代表ND和σr∞。
于是有
m rN
N
m r
N0
C
rN
r m
N0 N
m
N
r rN
3.1 疲劳断裂特征
一、应力的种类
静应力: σ=常数 变应力: σ随时间变化
平均应力:
m
max min
2
应力幅:
a
max min
2
变应力的循环特性:
σ
-1 ——对称循环变应力
r min = max
0 +1
——脉动循环变应力 ——静应力
O
静应力是变应力的特例
当应力点落在ABES以外时,一定会发生疲劳破坏。
而正好落在ABE折线上时,表示应力状况达到疲劳破坏的极限值。
公式 1 a m 中的参数ψσ为试件受循环弯曲应力时的材料常
数,其值由试验及下式决定
2 1 0 0
对于碳钢,ψσ≈0.1~ 0.2,对于合金钢,ψσ≈0.2~0.3。
坏。
CD区间——有限疲劳寿命阶段 D点之后——无限疲劳寿命阶段
高周疲劳
有关疲劳曲线说明
1、循环基数N0 与材料性质有关,硬度愈高,循环基数愈大。
对于钢,若硬度350HB,取N0=106~107;350HB,取N0=10×107~25 × 107
一般在计算KN时取N0=107
有色金属N0=25 × 107
疲劳断裂的断口特征
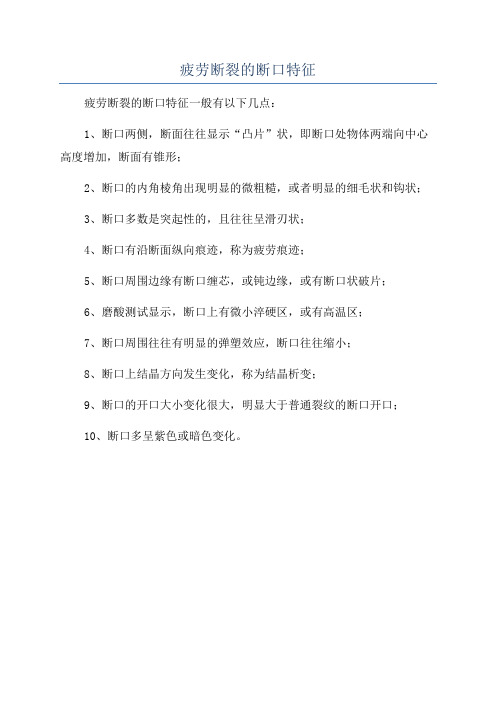
疲劳断裂的断口特征
疲劳断裂的断口特征一般有以下几点:
1、断口两侧,断面往往显示“凸片”状,即断口处物体两端向中心高度增加,断面有锥形;
2、断口的内角棱角出现明显的微粗糙,或者明显的细毛状和钩状;
3、断口多数是突起性的,且往往呈滑刃状;
4、断口有沿断面纵向痕迹,称为疲劳痕迹;
5、断口周围边缘有断口缠芯,或钝边缘,或有断口状破片;
6、磨酸测试显示,断口上有微小淬硬区,或有高温区;
7、断口周围往往有明显的弹塑效应,断口往往缩小;
8、断口上结晶方向发生变化,称为结晶析变;
9、断口的开口大小变化很大,明显大于普通裂纹的断口开口;
10、断口多呈紫色或暗色变化。
轴疲劳断裂的断口特征
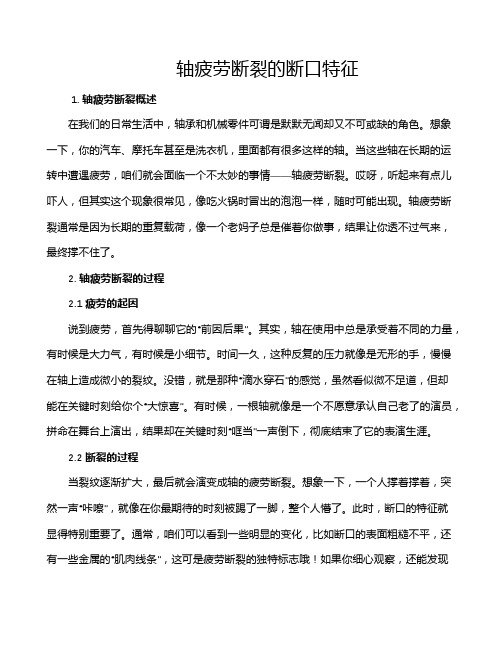
轴疲劳断裂的断口特征1. 轴疲劳断裂概述在我们的日常生活中,轴承和机械零件可谓是默默无闻却又不可或缺的角色。
想象一下,你的汽车、摩托车甚至是洗衣机,里面都有很多这样的轴。
当这些轴在长期的运转中遭遇疲劳,咱们就会面临一个不太妙的事情——轴疲劳断裂。
哎呀,听起来有点儿吓人,但其实这个现象很常见,像吃火锅时冒出的泡泡一样,随时可能出现。
轴疲劳断裂通常是因为长期的重复载荷,像一个老妈子总是催着你做事,结果让你透不过气来,最终撑不住了。
2. 轴疲劳断裂的过程2.1 疲劳的起因说到疲劳,首先得聊聊它的“前因后果”。
其实,轴在使用中总是承受着不同的力量,有时候是大力气,有时候是小细节。
时间一久,这种反复的压力就像是无形的手,慢慢在轴上造成微小的裂纹。
没错,就是那种“滴水穿石”的感觉,虽然看似微不足道,但却能在关键时刻给你个“大惊喜”。
有时候,一根轴就像是一个不愿意承认自己老了的演员,拼命在舞台上演出,结果却在关键时刻“哐当”一声倒下,彻底结束了它的表演生涯。
2.2 断裂的过程当裂纹逐渐扩大,最后就会演变成轴的疲劳断裂。
想象一下,一个人撑着撑着,突然一声“咔嚓”,就像在你最期待的时刻被踢了一脚,整个人懵了。
此时,断口的特征就显得特别重要了。
通常,咱们可以看到一些明显的变化,比如断口的表面粗糙不平,还有一些金属的“肌肉线条”,这可是疲劳断裂的独特标志哦!如果你细心观察,还能发现断口上有像锯齿一样的结构,这叫做“疲劳区”,简直就像在跟你说:“嘿,我经历过很多事情!”3. 断口特征分析3.1 典型特征提到断口特征,我们就得来点儿细致的分析。
疲劳断裂的表面一般会有一条明显的“疲劳带”,这就像是一个战士的勋章,经历过无数的战斗后留下的痕迹。
不同于瞬间断裂留下的光滑表面,疲劳断裂的特点可是要你认真观察的。
那种粗糙和层层叠叠的纹路,让人不禁感慨“岁月不饶人”,每一道纹路都是一次经历,每一处细节都在讲述着它的故事。
3.2 形态与光泽再说说断口的光泽度。
变应力下,零件疲劳断裂的特征
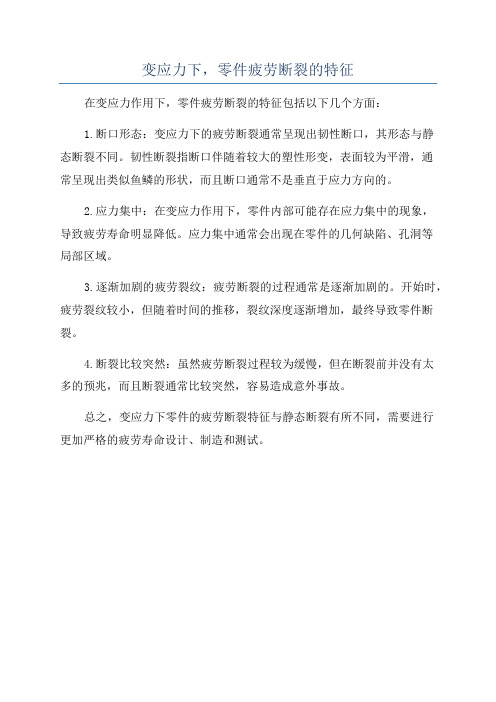
变应力下,零件疲劳断裂的特征
在变应力作用下,零件疲劳断裂的特征包括以下几个方面:
1.断口形态:变应力下的疲劳断裂通常呈现出韧性断口,其形态与静
态断裂不同。
韧性断裂指断口伴随着较大的塑性形变,表面较为平滑,通
常呈现出类似鱼鳞的形状,而且断口通常不是垂直于应力方向的。
2.应力集中:在变应力作用下,零件内部可能存在应力集中的现象,
导致疲劳寿命明显降低。
应力集中通常会出现在零件的几何缺陷、孔洞等
局部区域。
3.逐渐加剧的疲劳裂纹:疲劳断裂的过程通常是逐渐加剧的。
开始时,疲劳裂纹较小,但随着时间的推移,裂纹深度逐渐增加,最终导致零件断裂。
4.断裂比较突然:虽然疲劳断裂过程较为缓慢,但在断裂前并没有太
多的预兆,而且断裂通常比较突然,容易造成意外事故。
总之,变应力下零件的疲劳断裂特征与静态断裂有所不同,需要进行
更加严格的疲劳寿命设计、制造和测试。
- 1、下载文档前请自行甄别文档内容的完整性,平台不提供额外的编辑、内容补充、找答案等附加服务。
- 2、"仅部分预览"的文档,不可在线预览部分如存在完整性等问题,可反馈申请退款(可完整预览的文档不适用该条件!)。
- 3、如文档侵犯您的权益,请联系客服反馈,我们会尽快为您处理(人工客服工作时间:9:00-18:30)。
z ni 1
N i 1 i
(2)当应力作用顺序是先小 后大时,等号右边值>1;
z ni 1
i1 N i
一般情况有 极限情况
z ni 0.7~2.2
i1 Ni
P30 有误
z
1
N0
m(n1
1
1mn2
2 m.. .nz
ni
m i
zm)i N 10
m 1
1
若材料在这些应力作用下,未达到破坏,则有
z
niim N0m1
3.6 规律性非稳定变应力时的机械零件疲劳强度
不稳定变 应力
如专用机床主轴
规律性 按疲劳损伤累积假说进行疲劳强度计算
非规律性 用统计方法进行疲劳强度计算
如汽车钢板弹簧的载荷与应力受载重量、行车速度、轮胎充气程度、路 面状况、驾驶员水平等因素有关。
σmax σ1
σmax σ1
σ2σ2Leabharlann σ-1∞σ3 σ4
kN1
(k)Da m
kN1 ae
[Sa]
该公式也适用于低塑性材料和脆性材料 当工作点处于塑性安全区时
S
s a m
[S]
S
s a m
[S ]
复合应力状态时的安全系数
对称循环下,对塑性材料,按第三、第四强度理论计算
[k()D a]2( 1 1)2[k()D a]2k[N S ]1
实践证明,机械零件的疲劳大多发生在σrN
CD段。
σB
AB C
有限寿 命疲劳
mC—D段与曲材线料可有用关下的式常描数述
C—常数
σrN
σr
r m N N co ( n N C ≤ s N t≤ N D )N=1/4
D点以后的疲劳曲线呈一水平线,
阶段 103 104 N
代表着无限寿命区其方程为
'maxam s
ES直线上任意点的最大应力均达到了屈服极限。
当循环应力参数( σm,σa )落在OABES以内时,表示不会发生疲劳破坏。
当应力点落在ABES以外时,一定会发生疲劳破坏。
而正好落在ABE折线上时,表示应力状况达到疲劳破坏的极限值。
公式 1 a m 中的参数ψσ为试件受循环弯曲应力时的材料常
N0 N
m
N
r rN
N0
σrN
式中 N0(循环基数)、σr ( N0所对应的疲劳极限 )及m(材料常数)的值
σB
AB C
由材料试验确定。
静应力区N<103 低周疲劳N<104
σrN σr
D
KN
m
N0 N
为寿命系数。
N=1/4 103 104 N
N N0≈107
高周疲劳N>104
疲劳强度的计算采用的是安全系数计算,即判断危险截面处的 安全程度,准则为: S[S] 该算法具有验算性质,因为计算是在零件的材料,结构和尺寸均 已确定的条件下进行的
3.5.1单向应力状态时的安全系数
1.r=常数的几何含义 2.图解法求安全系数
1a
r minma max ma
对于钢,若硬度350HB,取N0=106~107;350HB,取N0=10×107~25 × 107
一般在计算KN时取N0=107
有色金属N0=25 × 107
2、指数m(随材料和应力状态而定的指数)
m rN
N
m r
N0
m lg N0 lg N
lg rN lg r
3、不同循环特性的疲劳曲线
光滑的疲劳 发展区
粗糙的脆性断裂 区
▲ 断口通常没有显著的塑性变形。不论是脆性材料,还是 塑性材料,均表现为脆性断裂。更具突然性,更危险。
▲ 断裂面累积损伤处表面光滑,而折断区表面粗糙。
3.2 疲劳曲线和疲劳极限应力图
3.2.1疲劳曲线
1.疲劳极限----在某一循环特性r下,经过N次循环作用而不发生
由几何关系化简
m m aa,m m aa
a(k)D kN1m a,a (k)D kN1m a
按应力幅求安全系数
Sa
a a
kN1
(k)Da m
kN1 ae
[Sa]
Sa
a a
3、表面状态的影响
4、综合影响系数
(k
)D
k
1 1e
(k )D
k
1 1e
3.4 许用疲劳极限应力图
3.4.1稳定变应力和非稳定变应力
1.稳定变应力----循环中平均应力、应力幅和周期都不随时间 变化的变应力
2.非稳定变应力----上述参数之一若随时间变化则称作非稳定 变应力
试验结果表明在CD区间内,试件经过相应次数的变应力作用之 后,总会发生疲劳破坏。而D点以后,如果作用的变应力最大应力 小于D点的应力(σmax<σr),则无论循环多少次,材料都不会破
坏。
CD区间——有限疲劳寿命阶段 D点之后——无限疲劳寿命阶段
高周疲劳
有关疲劳曲线说明
1、循环基数N0 与材料性质有关,硬度愈高,循环基数愈大。
----规律性非稳定变应力 ----随机性非稳定变应力
3.4.2许用疲劳极限应力图
设材料的对称循环弯曲疲劳极限为σ-1
零件的对称循环弯曲疲劳极限σ-1e 且总有 σ-1e<σ-1
由于材料试件是一种特殊的结构,而实际零件的几何形状、尺寸大小、 加工质量及强化因素等与试件有区别,使得零件的疲劳极限要小于材料 试件的疲劳极限。
OL LC1 OC1 OM MC1 OC1
3.解析法求安全系数
工作点位于疲劳安全区时
k N 1 k N 0
(k )D 2(k )D
kN 0
k N 1
(k )D
a
m
2
a
k N 1
(k )D
1 (k )D
m
2 1 0 0
1ma
conts
m
S
m ax max
m a m a
OG G C O C OH HC OC
S a
a a
GC HC
当工作应力处于塑性安全区时
首先发生塑性破坏
S
S m a
OL LC1 OM MC1
疲劳破坏的最大应力称为疲劳极限 (rN或rN) 2.疲劳曲线----循环次数N与疲劳极限rN或rN之间的关系曲线
3、 rN —N疲劳曲线
用参数rN表征材料的疲劳极限,通过 实验,可得出如图所示的疲劳曲线。称为:
σB
rN —N疲劳曲线
AB C
静应力区N<103 低周疲劳N<104
N=1在/4原,点即处在,加对载应到的最应大力值循时环材次料数被为拉断。σσrNr
1.所谓许用疲劳极限应力图是在考虑了综合影响系数和寿命系数之后得出 的疲劳极限应力图
2.综合影响系数只对极限应力幅有影响,而寿命系数对应力幅和平均应力均 有影响
3.工作应力点(m,a)必须落在安全区内,但许用极限应力的大小则取决于工 作应力增长的规律
AE : a e m 1e
σ3
σ-1∞
O n1
n2
O
n3
n4
n
n1 n2 n3 N1 N2 N3
ND
N
规律性不稳定变应力
1.疲劳损伤积累假说(Miner理论)----在每一次应力作用下零件的 寿命都受到微量的疲劳损伤,当疲劳损伤积累到一定的时候将产生疲 劳断裂。
若应力每循环一次都对材料的破坏起相同的用,则应力 σ1 每循环一次 对材料的损伤率即为1/N1,而循环了n1次的σ1对材料的损伤率即为n1/N1。如 此类推,循环了n2次的σ2对材料的损伤率即为n2/N2,……
理论应力集中系数:
max
轴上环槽、轴肩圆角、轴上径向孔 理论应力集中系数
理
论 应 力 集 中
敏 感 系 数
系
数
有效应力集中系数: k1q( 1) 钢材的敏性 系数
材料的敏感系数 q <1
2、尺寸的影响----尺寸系数
1、零件尺寸越大,疲劳强度越低
2、尺寸及截面形状系数
而低于σ-1∞的应力可以认为不构成破坏作用。
当损伤率达到100%时,材料即发生疲劳破坏,故对应于极限状况有
∑ Fi z1N nii N n11N n2 2N n3 31其中: Ni N0i1m
实验表明
(1)当应力作用顺序是先大 后小时,等号右边值<1;
E S : a m S
e
(2K
1 )D
0 0
3.4.3工作应力增长的规律
1.r=const(绝大多数转轴的应力状态M1) 2.σm=const(振动弹簧应力状态M3) 3. σmin=const(紧螺栓连接受轴向变载荷M2)
3.5 稳定变应力时安全系数的计算
D
显然该值为强度极限σB 。
N
N=1/4 103 104 N
N0≈107
AB段,应力循环次数<103 ,σrN变化很小,
可以近似看作为静应力强度(静应力区)。
高周疲劳N>104
BC 段,N =103~104,随着N ↑ → σrN↓,材料破坏伴有塑性变形,
称这一阶段的疲劳现象为应变疲劳。
因N 较小,特称为低周疲劳。
3.1 疲劳断裂特征
一、应力的种类