汽车悬架振动试验系统
汽车悬架振动试验台垂向主振动的有效性分析
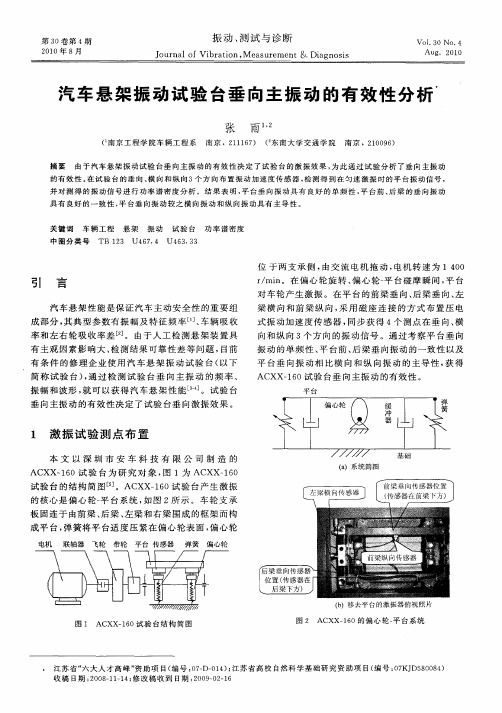
振 幅和波 形 , 可 以获 得汽 车 悬 架性 能 [ ] 就 3 。试 验 台
垂 向主振 动 的有 效 性决 定 了试 验 台垂 向激 振效 果 。
1 激 振 试 验 测 点 布 置
本 文 以 深 圳 市 安 车 科 技 有 限 公 司 制 造 的
AC X一 6 X 1 0试 验 台 为 研 究 对 象 , 1为 AC X一 6 图 X 10 试 验 台 的结 构 简 图[ 。AC X一 6 5 ] X 1 O试 验 台产 生 激 振 的核 心是 偏 心 轮一 台系统 , 图 2所 示 。车 轮 支 承 平 如 板 固连于 由前 梁 、 后梁 、 梁 和右 梁 围成 的框架 而 构 左 成平台, 弹簧 将平 台适 度 压 紧在 偏 心轮 表 面 , 心 轮 偏
关 键 词 车 辆 工 程
中图分类号
悬 架 振 动 试 验 台 功 率 谱 密 度
T 2 U4 7 4 U4 3 3 B13 6 . 6.3
位 于 两 支 承 侧 , 交 流 电 机 拖 动 , 机 转 速 为 14 0 由 电 0
引 言
汽 车悬 架 性能 是保 证 汽车 主 动安 全 性 的重要 组
成部 分 , 典型 参数 有 振 幅及 特 征频 率 n 、 其 ]车辆 吸收
率 和左 右轮 吸 收率 差 L 。 由于人 工检 测 悬 架装 置 具 2 ] 有主 观 因素 影 响大 、 测结果 可靠性 差 等 问题 , 检 目前
向和 纵 向 3个方 向的振 动 信号 。通 过考 察平 台垂 向
r mi 。在偏 心 轮旋 转 、 心轮一 台碰摩 瞬间 , 台 / n 偏 平 平 对车 轮 产生 激 振 。在平 台 的前 梁垂 向、 后梁 垂 向、 左 梁横 向和 前 梁纵 向 , 用 磁 座 连 接 的方 式 布 置压 电 采 式振 动加 速 度传 感 器 , 步获 得 4个 测点 在 垂 向 、 同 横
GB4783-84汽车悬挂系统的固有频率和阻尼比测定方法
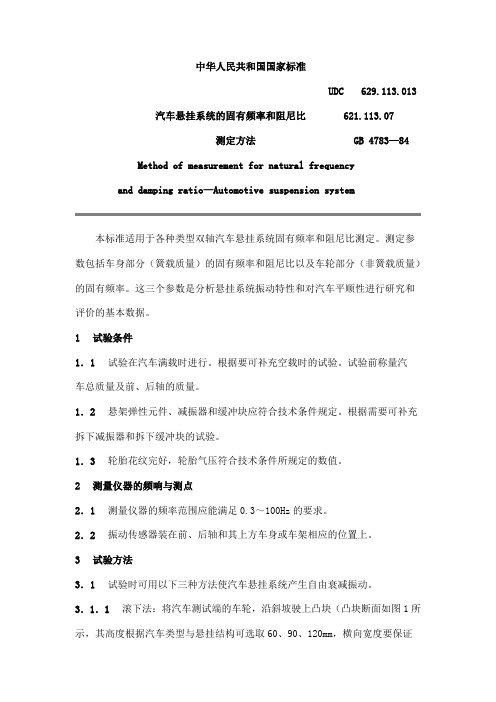
中华人民共和国国家标准UDC 629.113.013汽车悬挂系统的固有频率和阻尼比621.113.07测定方法GB 4783—84 Method of measurement for natural frequencyand damping ratio—Automotive suspension system本标准适用于各种类型双轴汽车悬挂系统固有频率和阻尼比测定。
测定参数包括车身部分(簧载质量)的固有频率和阻尼比以及车轮部分(非簧载质量)的固有频率。
这三个参数是分析悬挂系统振动特性和对汽车平顺性进行研究和评价的基本数据。
1试验条件1.1试验在汽车满载时进行。
根据要可补充空载时的试验。
试验前称量汽车总质量及前、后轴的质量。
1.2悬架弹性元件、减振器和缓冲块应符合技术条件规定。
根据需要可补充拆下减振器和拆下缓冲块的试验。
1.3轮胎花纹完好,轮胎气压符合技术条件所规定的数值。
2测量仪器的频响与测点2.1测量仪器的频率范围应能满足0.3~100Hz的要求。
2.2振动传感器装在前、后轴和其上方车身或车架相应的位置上。
3试验方法3.1试验时可用以下三种方法使汽车悬挂系统产生自由衰减振动。
3.1.1滚下法:将汽车测试端的车轮,沿斜坡驶上凸块(凸块断面如图1所示,其高度根据汽车类型与悬挂结构可选取60、90、120mm,横向宽度要保证车轮全部置于凸块上),在停车挂空档发动机熄火后,再将汽车车轮从凸块上推下、滚下时应尽量保证左、右轮同时落地。
3.1.2抛下法:用跌落机构将汽车测试端车轴中部由平衡位置支起60或90mm,然后跌落机构释放,汽车测试端突然抛下。
3.1.3拉下法:用绳索和滑轮装置将汽车测试端车轴附近的车身或车架中部由平衡位置拉下60或90mm,然后用松脱器使绳索突然松脱。
注:用上述三种方法试验时,拉下位移量、支起高度或凸块高度的选择要保证悬架在压缩行程时不碰撞限位块,又要保证振动幅值足够大与实际使用情况比较接近。
汽车动力总成悬置系统振动分析及优化设计

上海交通大学硕士学位论文
摘 要
汽车动力总成悬置系统振动分析及优化设计
摘 要
汽车动力总成振动是汽车振动的主要激振源之一,对汽车的舒适性 和 NVH 特性有很大的影响。 设计合理的动力总成悬置系统可以减少振动 传递,提高乘坐舒适性。本文以国产某轿车为研究对象,对动力总成悬 置系统隔振性能进行了分析研究。本文的研究工作包括以下几个方面: 首先,运用拉格朗日方程,建立了动力总成悬置系统动力学方程。 根据试验所获得的模型参数,在 Matlab 和 ADAMS 软件环境中建立了六 自由度仿真模型。 其次,结合实车试验,验证了所建模型准确性,并从系统固有频率 配置及振动解耦角度分析了悬置系统的振动特性;根据实际条件,以提 高系统振动解耦率为目标,应用优化算法对动力总成悬置刚度参数进行 优化设计,通过仿真分析比较了优化前后的固有特性,结果表明优化有 效提高了系统固有频率配置合理性和系统振动解耦率。 最后,建立了动力总成-整车十三自由度动力学模型,其仿真结果表 明优化后悬置刚度参数能改善怠速隔振特性,所建立的模型可以作为悬 置系统优化设计的虚拟样机。 本文的研究结果表明优化设计后的悬置系统其隔振特性有了较大的 改进,所运用的研究方法对悬置系统的优化设计具有一定的指导意义。
k sf k sr csf csr
ϕ
xi yi zi i′ j ′ k ′ PjI q
C
广义坐标方向单位矢量 往复惯性力 ( N ) 二阶往复惯性力 ( N ) 六自由度系统质量矩阵 六自由度系统刚度矩阵 位置转移矩阵 十三自由度系统质量矩阵
T F
第
JIS D 汽车零部件振动试验方法 中文版
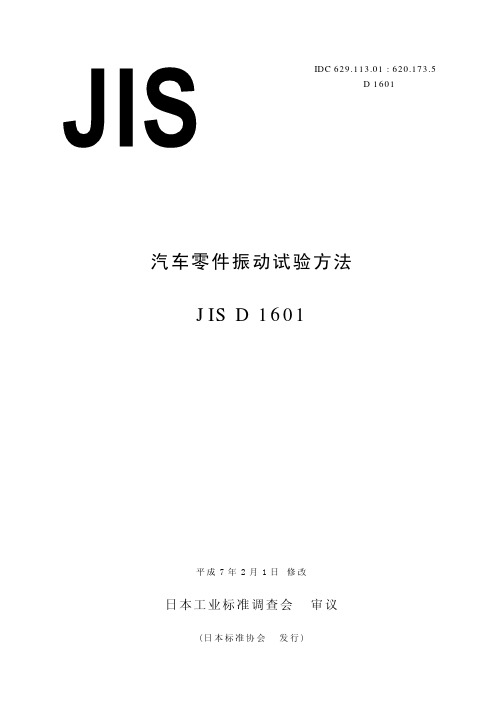
IDC 629.113.01 : 620.173.5D 1601汽车零件振动试验方法JIS D 1601平成7年2月1日修改日本工业标准调查会审议(日本标准协会发行)日本工业标准JIS汽车零件振动试验方法D1601-19951.适用范围 本标准规定了汽车零件(以下称零件)的振动试验方法。
2.试验种类 试验种类分以下几类。
⑴ 共振点检测试验 求零件共振振动频率的试验⑵ 振动性能试验 研究施振时零件性能的试验⑶ 振动耐久试验 研究以一定的振动频率激振,相对于振动的零件耐久性的试验⑷ 扫描振动耐久试验 研究按同样的比例连续增减振动频率激振,相对于振动的零件耐久性的试验3.振动条件分类 振动性能试验及振动耐久试验的振动条件分以下几种。
⑴ 零件的振动条件,按被安装的汽车的种类分:1种 主要指轿车系列2种 主要指公共汽车系列3种 主要指货车系列4种 主要指二轮汽车系列⑵ 零件振动条件按,被安装的状态分:A种 安装在车体或悬架装置的弹簧上,振动较小时B种 安装在车体或悬架装置的弹簧上,振动较大时C种 安装在发动机上,振动较小时D种 安装在悬架装置的弹簧下和安装在发动机上,振动较大时,振动条件分类及相应产品示例如参考表1。
4.试验条件4.1试验顺序 试验按共振点检测试验,振动性能试验,振动耐久试验或扫描振动耐久试验的顺序 进行。
不过,共振点检测试验和振动性能试验,或共振点检测试验和振动性能试验及扫描振动耐久试验同时进行也可以。
4.2 零件的安装 零件安装在振动试验台上的状态原则上应接近于零件的使用状态。
4.3 零件的动作 试验原则上要按零件的动作状态进行。
4.4 施振方法 相对于零件的安装状态,按顺序施加上下、左右、前后垂直的简谐振动。
但是,简谐振动的高次谐波含有率⑴,原则上在振动加速度的25%以内。
注⑴:简谐振动的高次谐波含有率的计算如下:⑴以正弦波振动的振动加速度±a(m/s2),按下式计算:a=Kf2A×10-3其中,K=2π2≈19.74f:振动频率(Hz)A:全振幅(mm)24附图2 振动频率67Hz时的振幅7D 1601 1995附图3 振动频率133Hz时的振幅8附图4 振动频率167Hz时的振幅9附图5 振动频率200Hz时的振幅10附图6 振动频率400Hz时的振幅1112。
悬架震动实验报告

一、实验目的1. 了解汽车悬架系统的基本组成和工作原理。
2. 掌握汽车悬架系统震动实验的基本方法和步骤。
3. 分析不同路面条件下汽车悬架系统的震动特性。
4. 评估悬架系统减震性能对汽车舒适性和稳定性的影响。
二、实验原理汽车悬架系统是连接车身和车轮的部件,其主要功能是传递和缓冲来自路面的冲击,保持车轮与地面的良好接触,提高汽车的行驶稳定性、舒适性和安全性。
悬架系统由弹性元件、导向机构和减震器组成。
本实验通过在不同路面条件下对汽车悬架系统进行震动实验,分析其震动特性。
三、实验设备1. 汽车一辆2. 震动传感器3. 数据采集器4. 激励器5. 路面模拟器6. 悬架系统参数测试仪7. 计算机8. 相关软件(如ADAMS、MATLAB等)四、实验步骤1. 实验准备(1)将汽车停放在水平路面上,确保车身平稳。
(2)连接振动传感器,将传感器安装在汽车悬架系统上。
(3)将数据采集器与计算机连接,并打开相关软件。
(4)设置实验参数,如采样频率、路面模拟条件等。
2. 实验实施(1)启动激励器,模拟不同路面条件(如平坦路面、坑洼路面、波浪路面等)。
(2)启动数据采集器,记录汽车悬架系统的震动数据。
(3)重复上述步骤,进行多次实验,以确保数据的准确性。
3. 数据处理与分析(1)将采集到的数据导入计算机,进行滤波、降噪等处理。
(2)根据实验数据,分析不同路面条件下汽车悬架系统的震动特性。
(3)评估悬架系统减震性能对汽车舒适性和稳定性的影响。
五、实验结果与分析1. 不同路面条件下汽车悬架系统的震动特性(1)平坦路面:汽车悬架系统震动较小,减震性能较好。
(2)坑洼路面:汽车悬架系统震动较大,减震性能较差。
(3)波浪路面:汽车悬架系统震动较大,减震性能较差。
2. 悬架系统减震性能对汽车舒适性和稳定性的影响(1)舒适性:悬架系统减震性能越好,汽车行驶过程中乘客的舒适性越高。
(2)稳定性:悬架系统减震性能越好,汽车在行驶过程中越稳定,操控性越好。
基于损伤等效的汽车减振器耐久试验方法研究

基于损伤等效的汽车减振器耐久试验方法研究作者:刘伟庞方超张冠勇王春辉来源:《时代汽车》2020年第08期摘要:新旧版本的减振器行业标准共规定了三种耐久试验方法,文章介绍了每种方法的具体实施细节,并基于损伤等效理论,提出了利用Miner法则和伪损伤建立三者的当量关系及相关性的方法,最后进行台架试验验证,考核减振器阻尼力的衰减率和漏油情况,结果证明该方法是可行的。
关键词:减振器耐久;损伤等效;伪损伤减振器是汽车悬架系统的重要组成部分,它通过其自身的阻尼作用可以迅速衰减车辆因路面冲击产生的振动,对汽车的舒适性和操作稳定性发挥着关键的作用。
在使用过程中,减振器要提供稳定和持续的阻尼,这就要求减振器有良好的耐久性[1]。
目前国内减振器的耐久试验方法主要参考行业标准QC/T 491-1999及QC/T 545-1999,2018年发布了最新版本QC/T 491-2018,并于2019年正式实施。
标准中规定了减振器耐久的具体方法参数,本文将基于损伤等效理论,分析标准中各种耐久试验方法的区别及相关性。
1 常用减振器耐久试验方法(1)单动试验:这是QC/T 545-1999里规定的一个过渡性方法,新标准中删除了这种方法。
试验时减振器一端固定,另一端做简谐运动,循环次数1×106次。
通常情况减振器上端固定,下端运动,试验速度0.52m/s,即振幅±50mm,频率1.67Hz,波形如图1所示。
(2)双动试验:顾名思义,试验时减振器上下两端同时沿垂直方法运动,这是目前最常用的耐久试验方法。
QC/T 491-2018中规定了两种方式,第一种是低频端(上端)频率1.67Hz,振幅±50mm,高频端(下端)频率10Hz,振幅±8mm;第二种是低频端(上端)频率1Hz,振幅±40mm,高频端(下端)频率12Hz,振幅±10mm,试验时任选其中一种方法。
不过,使用目前主流的减振器台架试验时往往采用单动模拟双动的方式进行,即减振器上端固定,下端运行高频和低频的叠加波,波形如图2所示。
车辆悬架振动试验台介绍

车辆悬架振动试验台简介和操作规程
一、设备简介
车辆悬架振动试验台由激振源、悬架机构、载荷、传感器和计算机控制系统构成。
由激振源生成模拟路面激励的振动,传递给悬架机构和载荷,由悬架机构和载荷上安装的加速度及位置传感器等测量出振动信号,反馈给计算机控制系统。
控制系统根据振动控制策略生成控制信号,传递给悬架机构中的作动器生成实时可调的阻尼力,实现对振动的衰减。
该实验台可进行减振器的示功特性试验,主动、半主动、被动悬架的振动控制。
二、操作规程
1. 检查确认运动机构、传感器、电气元件及线路处于正常状态。
2. 启动控制计算机,运行控制程序使系统处于闭环控制状态。
3. 启动液压泵、调节压力达到工作压力状态。
4. 运行激振控制程序、输出模拟路面的振动激励。
5. 运行悬架作动器的控制程序,启动振动控制。
6. 观察、记录实验结果。
7. 实验结束后,卸载压力、关闭油源,关闭激励以及作动器控制程序。
三、注意事项
1. 实验开始前注意检查确保电气元件状态正常、连线正确。
2. 设备运转之前,注意清理场地,保持运动件运动空间无障碍。
3. 在实验开始时,注意对液压阀先闭环后再启动油源。
4. 在实验停止时,先关闭油源,再解除液压阀闭环控制。
交通学院实验中心。
乘用车四分之一悬架试验台设计

乘用车1/4悬架试验台设计摘要:汽车悬架是乘用车必不可少的机构,不论是乘用车还是商用车,都离不开悬架机构,它关系到乘用车的乘坐平顺性,减缓乘用车车身和车桥的振动,当乘用车受到来自地面的冲击时,或者其他外界的激励,缓和这些外界激励造成的冲击作用,此外还关系到驾驶人员和乘坐人员的安全性与否。
鉴于悬架装置的重要性,此次设计的共振式汽车减振试验台来检测其性能。
首先分析了减振试验台的工作原理,说明了减振试验台的设计要求,再对减振试验台的零部件进行设计分析,然后进行相应的强度校核,并作了技术经济性分析,表明设计的减振试验台符合设计要求。
这种方法的优点在于试验台性能稳定,数据可靠性好,但缺点是检测参数单一,对悬架装置不能形成全面的分析与故障诊断,无法全面反映悬架装置的技术状况。
关键词:减振器;谐振式试验台;谐振频率;谐振振幅The design of passenger car’s suspension test-bedAbstract:Car suspension is essential for passenger cars, whether passenger cars or commercial vehicles, are inseparable from the suspension mechanism, it is related to the passenger ride ride comfort, slow down the car body and axle Vibration, when the passenger car from the impact of the ground, or other external incentives to ease the impact of these external incentives, but also related to the safety of drivers and passengers or not.In view of the importance of suspension devices, the design resonant vehicle vibration reduction test bed to detect its performance. First analyzes the working principle of vibration test rig, vibration test rig is described in the design requirements, and design analysis was carried out on the vibration test rig parts, then the corresponding intensity, and the technical economy analysis, shows that the design of vibration test rig conform to the design requirements. This method is to test the advantages of stable performance, good reliability data, but the disadvantage is that single detection parameters, the suspension could not form a comprehensive analysis and fault diagnosis, can not fully reflect the technical condition of the suspension.Keywords: Suspension resonant;Test stand;Resonant frequency;Resonant amplitude目录摘要 (I)Abstract .................................................................................................................................... I I 1 绪论 .. (1)1.1 国外汽车检测技术发展状况 (1)1.2 中国汽车维修行业的基本情况 (1)1.2.1 汽车维修行业存在的基本问题 (1)1.2.2 汽车维修行业面临的新形势 (2)1.2.3 汽车维修行业的发展趋势 (3)1.3 汽车悬架性能试验技术的发展状况 (3)2 汽车减振试验台的设计 (7)2.1 汽车减振器工作原理 (7)2.2 试验台的设计 (7)2.3 检测台设计注意事项 (8)3 零部件设计 (9)3.1 电机的设计 (9)3.1.1 计算电机的平均转矩 (9)3.1.2 电机的过载能力校验 (10)3.2 偏心轴的设计 (10)3.2.1 轴的受力分析 (10)3.2.2 确定轴颈参数 (11)3.2.3 轴的疲劳强度校核 (12)3.2.4 轴的挠度校核 (12)3.3 轴上键的强度校核 (13)3.4 联轴器的设计 (13)3.5 偏心轴轴承的设计 (14)3.6 轴承座的设计 (14)3.7 飞轮的设计 (14)3.8 滚动导向柱的设计 (15)3.9 弹簧的设计 (16)3.9.1 选择初始数据 (16)3.9.2 弹簧的校核 ............... (16)3.10 传感器的设计 (17)3.11 振动板的设计 (18)3.12 盖板设计 (19)3.12.1 校核盖板的刚度 (19)3.12.2 计算盖板的质量 (19)3.13 驱动盖板的电动机设计 (19)3.14 减速器的设计 (20)3.15 齿轮齿条的设计 (20)3.15.1 齿轮初步设计 (20)3.15.2 齿条的设计 (21)4 技术经济性分析 (22)5 总结与体会 (23)参考文献 (24)致谢 (25)1 绪论1.1 国外汽车检测技术发展状况A.制度化德国的汽车工业走在世界前列,汽车检测技术同样实力强劲,这得益于汽车检测各项技术的制度化,对汽车安全性以及环保性检测有一套行之有效的标准规范,各个汽车检测场都必须遵守这些标准规范以及规章制度,否则会受到严厉的处罚。
- 1、下载文档前请自行甄别文档内容的完整性,平台不提供额外的编辑、内容补充、找答案等附加服务。
- 2、"仅部分预览"的文档,不可在线预览部分如存在完整性等问题,可反馈申请退款(可完整预览的文档不适用该条件!)。
- 3、如文档侵犯您的权益,请联系客服反馈,我们会尽快为您处理(人工客服工作时间:9:00-18:30)。
附件:
详细技术参数
汽车悬架振动试验系统由振动台、功率放大器、冷却装置及控制采集配套设备组成。
1.振动台技术参数
●额定正弦激振力: ≥ 6kN
●额定随机激振力: ≥ 6kN
●额定冲击推力≥ 12kN
●频率范围(Hz):≥ 100 Hz
●最大负载: ≥300kg
●环境条件:温度:0-40℃、湿度:<85%(25℃)
●保护装置: 过载保护;过热保护;过电流保护;过电压保护;过位移保护;
驱动电源保护;限流保护;模块直通保护;模块温度保护。
2.功率放大器
●采用智能型,液晶触摸屏控制;
●信噪比≥65dB
●显示方式液晶显示工作时的输出电流、输出电压、台体温度、电网电压等重要
参数
●控制方式功率放大器系统由微处理器对系统进行控制
●谐波失真:≤ 1.0%
●DC-AC转换效率:> 95%
●平均无故障工作时间(MTBF):>3000小时
●系统保护:电网过压、电网欠压、电网缺相、逻辑故障、功率模块直通、功率模块
温度、输出过流、输出过压、驱动电源、台体位移、台体温度、外部连锁等保护电路。
3.冷却装置
●功率:≥ 4kW
●风机流量:≥ 0.33m3/s
●环境温度: 0~40 ℃
●电缆配置长度≥6m
4.控制采集配套要求
●软件上实现了随机、正弦、典型冲击和谐振四个功能
●通道数:至少2个以上同步输入通道
●主流品牌液晶19寸以上计算机
●彩色喷墨A4打印机
●信噪比: >100dB
●分辨率:24位模数转换(ADC)
●电压范围:±10V的峰值电压
●幅值精度:2mV
●操作系统:Windows XP及以上版本
●自动产生Word试验报告
●随机性能指标:动态范围为90dB,控制精度为±1dB,频率范围:从 0-1000Hz
●正弦性能指标:波形失真度<0.3%,频率分辨率为0.01%,频率范围:1Hz-5000Hz
●典型冲击控制:脉冲类型:半正弦、前峰锯齿波、后峰锯齿波、三角波、矩形
脉冲持续时间:0-3000mS ,频率范围:0-20000Hz。
●加速度传感器:进口单向传感器(电荷输出型),2个。