注塑成型简介
注塑成型工艺特点及应用

注塑成型工艺特点及应用注塑成型工艺特点及应用注塑成型是一种常见的塑料加工工艺,广泛应用于制造各种塑料制品。
它的主要特点如下:1. 高效率:注塑成型工艺能够快速地将熔融状态的塑料注入模具中进行制品成型。
注塑成型机的工作周期短,能够实现连续生产,提高生产效率。
2. 复杂形状:注塑成型工艺可以制造各种形状复杂的产品,包括中空构件、薄壁构件等。
通过合理设计模具结构,可以精确地复制模具的细节,使得成型的制品具有高精度和高质量。
3. 材料广泛:注塑成型工艺适用于广泛的塑料材料,包括热塑性塑料和热固性塑料。
根据产品需要,可以选择不同的塑料材料进行注塑成型,满足不同产品的性能需求。
4. 自动化程度高:注塑成型工艺可以实现全自动化生产,降低劳动成本。
注塑成型机自动化程度高,通过模具开关、温度控制、压力和速度调节等功能实现稳定的生产过程。
注塑成型工艺广泛应用于各个领域,下面以几个典型的应用为例进行介绍:1. 日用品:注塑成型工艺可以制造各种塑料日用品,如牙刷、塑料杯、塑料梳子等。
注塑成型的高效率和成本优势,使得塑料日用品在市场上具有竞争力。
2. 电子产品:注塑成型工艺广泛应用于电子产品的制造过程中,如手机壳、电视外壳等。
注塑成型可以制造出具有良好外观和高精度的塑料制品,满足电子产品对外观和尺寸要求。
3. 汽车零部件:注塑成型工艺在汽车工业中得到广泛应用。
注塑成型可以制造汽车零部件,如车灯壳、内饰件等。
通过注塑成型,可以实现汽车零部件的大规模生产和质量保证。
4. 医疗器械:注塑成型工艺应用于医疗器械的制造过程中。
医疗器械对产品的精度和卫生要求较高,注塑成型工艺可以制造出符合要求的塑料器械。
5. 塑料包装:注塑成型工艺广泛应用于塑料包装行业,如食品包装、制药包装等。
通过注塑成型,可以制造出不同形状和尺寸的塑料包装容器,满足不同产品的包装需求。
总结起来,注塑成型工艺具有高效率、复杂形状、材料广泛、自动化程度高等优点,适用于各个领域的制造过程中。
注塑成型模具简介
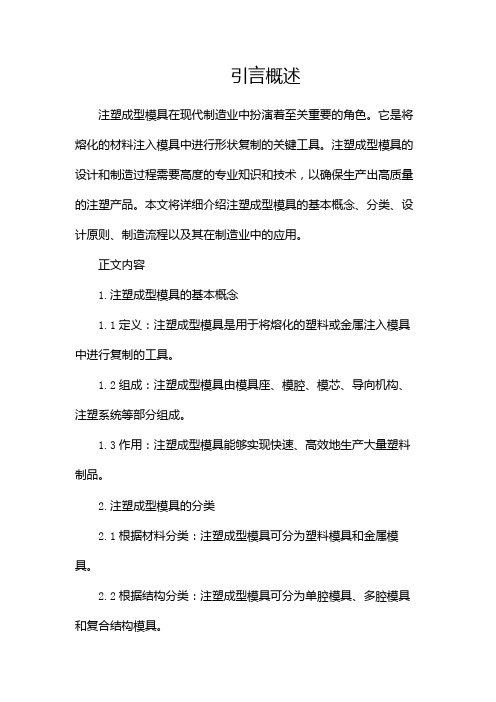
引言概述注塑成型模具在现代制造业中扮演着至关重要的角色。
它是将熔化的材料注入模具中进行形状复制的关键工具。
注塑成型模具的设计和制造过程需要高度的专业知识和技术,以确保生产出高质量的注塑产品。
本文将详细介绍注塑成型模具的基本概念、分类、设计原则、制造流程以及其在制造业中的应用。
正文内容1.注塑成型模具的基本概念1.1定义:注塑成型模具是用于将熔化的塑料或金属注入模具中进行复制的工具。
1.2组成:注塑成型模具由模具座、模腔、模芯、导向机构、注塑系统等部分组成。
1.3作用:注塑成型模具能够实现快速、高效地生产大量塑料制品。
2.注塑成型模具的分类2.1根据材料分类:注塑成型模具可分为塑料模具和金属模具。
2.2根据结构分类:注塑成型模具可分为单腔模具、多腔模具和复合结构模具。
2.3根据用途分类:注塑成型模具可分为家电类模具、汽车类模具、日用品类模具等。
3.注塑成型模具的设计原则3.1材料选择:根据被制品的材料特性选择合适的模具材料。
3.2结构设计:考虑产品结构特点,优化模具的设计以提高生产效率和产品质量。
3.3流道设计:合理设计模具的流道,以确保塑料材料能够均匀地流入模腔。
3.4冷却系统设计:设计合理的冷却系统,以加快模具的冷却速度,提高生产效率。
3.5注塑系统设计:选用适当的注塑机和配套设备,确保注塑过程的稳定性和精度。
4.注塑成型模具的制造流程4.1设计:根据产品要求进行模具设计,包括三维建模和工程图纸设计。
4.2制造模腔:根据设计图纸制造模腔部分,包括线切割、精密加工等工艺。
4.3制造模芯:根据设计图纸制造模芯部分,包括CNC加工、磨削等工艺。
4.4装配:将模腔和模芯装配在一起,并进行调试和测试。
4.5表面处理:根据需求进行模具表面处理,如电镀、喷涂等。
5.注塑成型模具在制造业中的应用5.1汽车制造:注塑成型模具广泛应用于汽车内饰件、外观件等的生产。
5.2家电制造:注塑成型模具用于电视机壳体、空调面板等家电制品的生产。
注塑成型的概念

注塑成型的概念
注塑成型(Injection Molding)是一种常用的塑料加工方法,通过将熔化的塑料注入模具中,并在模具中冷却和固化,最终得到所需的塑料制品。
注塑成型的概念包括以下几个方面:1. 注塑机:注塑成型过程中使用的设备,用于将塑料加热熔化并注入模具中。
注塑机通常由注射装置、锁模装置、液压系统和控制系统等部分组成。
2. 模具:注塑成型过程中塑料制品的形状和尺寸由模具决定。
模具由上模板和下模板组成,通过锁模装置固定在注塑机中。
3. 塑料材料:注塑成型使用的塑料材料通常是以颗粒状或粉末状存在的塑料原料。
常见的塑料材料包括聚丙烯(PP)、聚乙烯(PE)、聚氯乙烯(PVC)、聚苯乙烯(PS)等。
4. 注塑成型工艺:注塑成型工艺包括以下几个步骤:首先将塑料颗粒放入注塑机的料斗中,通过加热和融化使其成为熔融态,然后使用注射装置将熔融塑料注入模具的腔道中,待冷却固化后,通过开模装置将成型的塑料制品从模具中取出。
注塑成型具有生产周期短、生产效率高、成本相对较低等优点。
它被广泛应用于制造各种塑料制品,如塑料零件、容器、包装材料、电子产品外壳等。
注塑成型工艺介绍
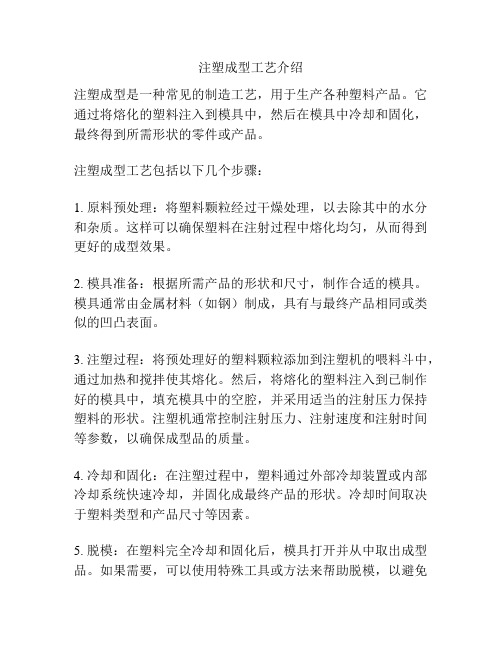
注塑成型工艺介绍注塑成型是一种常见的制造工艺,用于生产各种塑料产品。
它通过将熔化的塑料注入到模具中,然后在模具中冷却和固化,最终得到所需形状的零件或产品。
注塑成型工艺包括以下几个步骤:1. 原料预处理:将塑料颗粒经过干燥处理,以去除其中的水分和杂质。
这样可以确保塑料在注射过程中熔化均匀,从而得到更好的成型效果。
2. 模具准备:根据所需产品的形状和尺寸,制作合适的模具。
模具通常由金属材料(如钢)制成,具有与最终产品相同或类似的凹凸表面。
3. 注塑过程:将预处理好的塑料颗粒添加到注塑机的喂料斗中,通过加热和搅拌使其熔化。
然后,将熔化的塑料注入到已制作好的模具中,填充模具中的空腔,并采用适当的注射压力保持塑料的形状。
注塑机通常控制注射压力、注射速度和注射时间等参数,以确保成型品的质量。
4. 冷却和固化:在注塑过程中,塑料通过外部冷却装置或内部冷却系统快速冷却,并固化成最终产品的形状。
冷却时间取决于塑料类型和产品尺寸等因素。
5. 脱模:在塑料完全冷却和固化后,模具打开并从中取出成型品。
如果需要,可以使用特殊工具或方法来帮助脱模,以避免损坏或变形。
6. 后处理:根据产品的要求,可能需要进行后处理工艺,如修边、打磨、修整等,以获得最终的产品质量和外观效果。
注塑成型工艺的优点在于可以生产复杂形状的产品,并具有良好的尺寸稳定性和表面质量。
此外,注塑成型可以批量生产,提高生产效率和降低成本。
然而,注塑成型也存在一些限制,如模具制作成本较高、制作周期长、塑料材料的选择受限等。
因此,在进行注塑成型之前,需要仔细评估产品设计和成本效益,以确保工艺的可行性。
总而言之,注塑成型是一种常用、高效且灵活的制造工艺,广泛应用于各个行业,从电子产品到家具、汽车零部件等。
它为生产高质量和复杂形状的塑料产品提供了可靠的解决方案。
注塑成型是一种常见的制造工艺,广泛应用于各个行业。
它能够生产出各种形状复杂、尺寸稳定的塑料制品,包括塑料壳体、容器、零部件、玩具等。
注塑成型概念
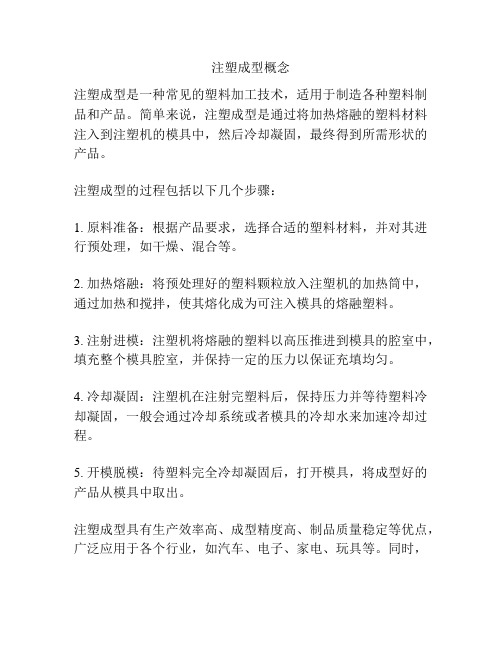
注塑成型概念
注塑成型是一种常见的塑料加工技术,适用于制造各种塑料制品和产品。
简单来说,注塑成型是通过将加热熔融的塑料材料注入到注塑机的模具中,然后冷却凝固,最终得到所需形状的产品。
注塑成型的过程包括以下几个步骤:
1. 原料准备:根据产品要求,选择合适的塑料材料,并对其进行预处理,如干燥、混合等。
2. 加热熔融:将预处理好的塑料颗粒放入注塑机的加热筒中,通过加热和搅拌,使其熔化成为可注入模具的熔融塑料。
3. 注射进模:注塑机将熔融的塑料以高压推进到模具的腔室中,填充整个模具腔室,并保持一定的压力以保证充填均匀。
4. 冷却凝固:注塑机在注射完塑料后,保持压力并等待塑料冷却凝固,一般会通过冷却系统或者模具的冷却水来加速冷却过程。
5. 开模脱模:待塑料完全冷却凝固后,打开模具,将成型好的产品从模具中取出。
注塑成型具有生产效率高、成型精度高、制品质量稳定等优点,广泛应用于各个行业,如汽车、电子、家电、玩具等。
同时,
注塑成型也可以通过调整注塑机的参数和模具设计来实现不同形状和尺寸的产品生产。
几种常用塑料的成型工艺介绍
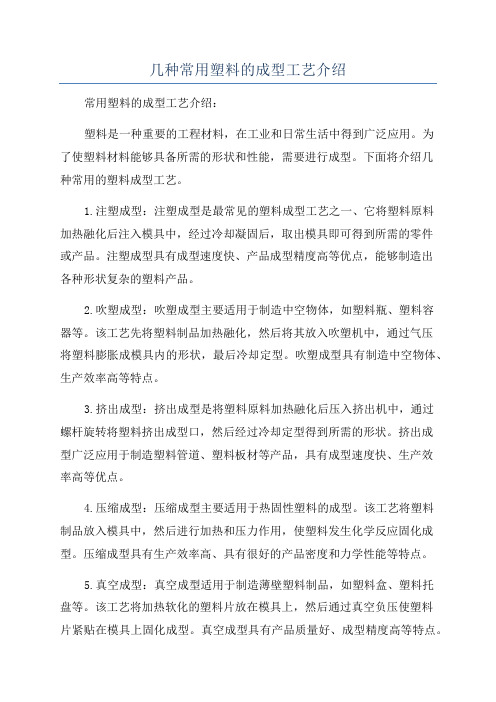
几种常用塑料的成型工艺介绍常用塑料的成型工艺介绍:塑料是一种重要的工程材料,在工业和日常生活中得到广泛应用。
为了使塑料材料能够具备所需的形状和性能,需要进行成型。
下面将介绍几种常用的塑料成型工艺。
1.注塑成型:注塑成型是最常见的塑料成型工艺之一、它将塑料原料加热融化后注入模具中,经过冷却凝固后,取出模具即可得到所需的零件或产品。
注塑成型具有成型速度快、产品成型精度高等优点,能够制造出各种形状复杂的塑料产品。
2.吹塑成型:吹塑成型主要适用于制造中空物体,如塑料瓶、塑料容器等。
该工艺先将塑料制品加热融化,然后将其放入吹塑机中,通过气压将塑料膨胀成模具内的形状,最后冷却定型。
吹塑成型具有制造中空物体、生产效率高等特点。
3.挤出成型:挤出成型是将塑料原料加热融化后压入挤出机中,通过螺杆旋转将塑料挤出成型口,然后经过冷却定型得到所需的形状。
挤出成型广泛应用于制造塑料管道、塑料板材等产品,具有成型速度快、生产效率高等优点。
4.压缩成型:压缩成型主要适用于热固性塑料的成型。
该工艺将塑料制品放入模具中,然后进行加热和压力作用,使塑料发生化学反应固化成型。
压缩成型具有生产效率高、具有很好的产品密度和力学性能等特点。
5.真空成型:真空成型适用于制造薄壁塑料制品,如塑料盒、塑料托盘等。
该工艺将加热软化的塑料片放在模具上,然后通过真空负压使塑料片紧贴在模具上固化成型。
真空成型具有产品质量好、成型精度高等特点。
6.3D打印成型:3D打印成型是近年来快速发展的塑料成型工艺之一、它通过从计算机模型中将物体分解为薄层,然后逐层累积加工,最终形成所需的塑料产品。
3D打印成型具有高度灵活性和个性化定制能力,适用于制造小批量、复杂结构的塑料产品。
以上是几种常用的塑料成型工艺的介绍。
不同的工艺适用于不同的塑料材料和产品形状需求,可以根据具体需求选择合适的成型工艺。
注塑成型技术

80%
未来发展
未来注塑成型技术将朝着智能化 、绿色化、自动化等方向发展, 进一步提高生产效率和产品质量 。
02
注塑成型原理及工艺流程
注塑成型原理
注塑成型是一种热塑性塑料加工方法,通过高温熔融塑料颗粒, 然后在高压下注入模具,冷却固化后得到产品。
注塑成型原理基于塑料的物理性质,如热塑性、流动性、热传导 性等,以及模具设计和注塑机的工作原理。
注塑成型技术
目
CONTENCT
录
• 注塑成型技术概述 • 注塑成型原理及工艺流程 • 注塑成型材料 • 注塑模具设计与制造 • 注塑成型设备 • 注塑成型技术的应用与发展趋势
01
注塑成型技术概述
定义与特点
定义
注塑成型技术是一种塑料加工方法,通过高温将塑料原料熔化, 然后注入模具中,冷却后形成所需的塑料制品。
注塑成型技术正与工业自动 化和人工智能技术相结合, 实现智能化生产,提高生产 效率和产品质量。
环保可持续发展
随着环保意识的提高,注塑 成型技术正朝着更加环保和 可持续发展的方向发展,减 少生产过程中的环境污染。
定制化生产
随着消费者需求的多样化, 注塑成型技术正朝着能够快 速生产定制化产品的方向发 展。
经济效益
注塑成型技术能够实现大规模生产,提高生产效率 ,降低生产成本,为企业带来经济效益。
注塑成型技术的发展历程
80%
早期注塑机
早期的注塑机采用液压系统,体 积较大,操作复杂,但能够完成 简单的塑料制品生产。
100%
现代注塑机
随着技术的不断发展,现代注塑 机采用电气控制系统和新型的液 压系统,具有更高的精度和效率 。
定期保养
对液压系统进行清洗、更换油 滤、检查加热器等。
tpr注塑成型工艺参数
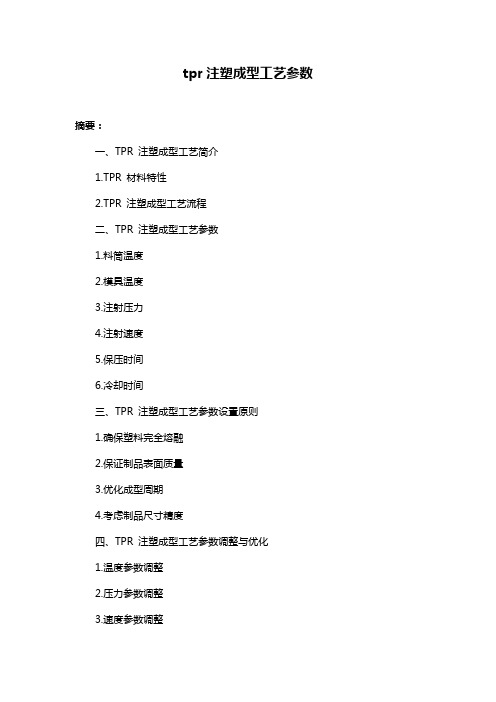
tpr注塑成型工艺参数摘要:一、TPR 注塑成型工艺简介1.TPR 材料特性2.TPR 注塑成型工艺流程二、TPR 注塑成型工艺参数1.料筒温度2.模具温度3.注射压力4.注射速度5.保压时间6.冷却时间三、TPR 注塑成型工艺参数设置原则1.确保塑料完全熔融2.保证制品表面质量3.优化成型周期4.考虑制品尺寸精度四、TPR 注塑成型工艺参数调整与优化1.温度参数调整2.压力参数调整3.速度参数调整4.时间参数调整正文:TPR 注塑成型工艺是一种将热塑性弹性体(TPR)通过注塑机进行加工制造的工艺。
TPR 材料具有优异的弹性和耐磨性,广泛应用于汽车、电子、家电等领域。
本文将详细介绍TPR 注塑成型工艺的参数设置及优化方法。
一、TPR 注塑成型工艺简介TPR 材料是一种具有橡胶与塑料特性的材料,具有较高的弹性、强度和耐磨性。
TPR 注塑成型工艺流程包括:原料准备、注塑机调试、模具安装、注射成型、制品取出、冷却定型等步骤。
二、TPR 注塑成型工艺参数1.料筒温度:料筒温度是影响TPR 材料熔融的重要参数。
适当的料筒温度可以确保塑料完全熔融,避免因温度过低导致塑料不能完全熔融,或因温度过高导致塑料降解。
2.模具温度:模具温度会影响制品的表面质量和尺寸精度。
适当的模具温度可以降低制品的内应力,提高制品的表面质量。
3.注射压力:注射压力是影响TPR 注塑成型工艺的关键参数。
合适的注射压力可以保证制品的密度和强度,避免制品出现缺陷。
4.注射速度:注射速度过快或过慢都会影响制品的质量。
合适的注射速度可以保证制品的尺寸精度,避免出现熔接痕、气泡等缺陷。
5.保压时间:保压时间过长或过短都会影响制品的质量。
合适的保压时间可以保证制品的密度和强度,避免出现缺陷。
6.冷却时间:冷却时间过长或过短都会影响制品的尺寸和性能。
合适的冷却时间可以保证制品的尺寸精度,避免制品变形或破裂。
三、TPR 注塑成型工艺参数设置原则1.确保塑料完全熔融:料筒温度、注射压力和注射速度等参数需相互配合,确保塑料能够完全熔融,避免出现缺料、熔接痕等缺陷。
注塑成型的原理

注塑成型是一种广泛应用于制造业中的塑料加工技术。
它是通过将熔融状态的塑料材料注入到模具中,并在冷却固化后取出制成成型品的一种方法。
注塑成型具有高效、精确、经济等优点,被广泛应用于汽车零部件、电器外壳、日用品等领域。
注塑成型的原理可以简单描述为以下几个步骤:1.塑料加料:将原料塑料颗粒或粉末放入注塑机的料斗中,并通过螺杆将塑料颗粒推进到机筒中。
在机筒中,塑料被加热并逐渐熔化。
2.注射:当塑料完全熔化后,注塑机会将熔化的塑料注入到模具中。
注塑机通过推动螺杆,使熔融塑料通过喷嘴进入模具的注射腔。
注塑机通常具有锁模系统,可确保模具保持紧闭状态以防止熔融塑料泄漏。
3.压力保持:一旦注射腔被填满,注塑机会施加一定的压力使熔融塑料在腔内保持一定的时间。
这是为了确保塑料完全填充模具的每个细节,尽可能减少缩短或变形。
4.冷却:在塑料填充完毕并保持一定时间后,注塑机会停止注塑并开始冷却过程。
冷却时间取决于塑料材料的性质和成型品的厚度。
较厚的零件需要更长的冷却时间。
冷却可以通过循环水系统或其他冷却介质完成。
5.开模和脱模:当塑料冷却固化后,注塑机会打开模具并将成型品从注射腔中取出。
模具通常可以分为两块,称为固定模和活动模。
注塑机通过分离这两个模块来获得成型品。
6.循环重复:完成一个注塑循环后,整个过程将会循环重复。
注塑机将再次加热塑料颗粒,注入到模具中,并再次进行压力保持和冷却。
这样就可以连续生产多个相同的成型品。
注塑成型的原理基于热塑性塑料的熔化和冷却固化过程。
热塑性塑料具有可再加热和再塑性的特点,因此可以通过注塑成型的方法进行加工。
在整个注塑成型的过程中,各个步骤的参数和条件需要根据具体的塑料材料和成型品的要求进行调整。
总结起来,注塑成型的原理就是将熔化的塑料注入模具中,通过压力保持使塑料充分填充到模具的每个细节,然后进行冷却固化,并最终取出成型品。
这种成型方式高效、精确且经济,广泛应用于各个制造行业中。
以上就是关于注塑成型的原理的介绍,希望对您有所帮助。
注塑成型工艺
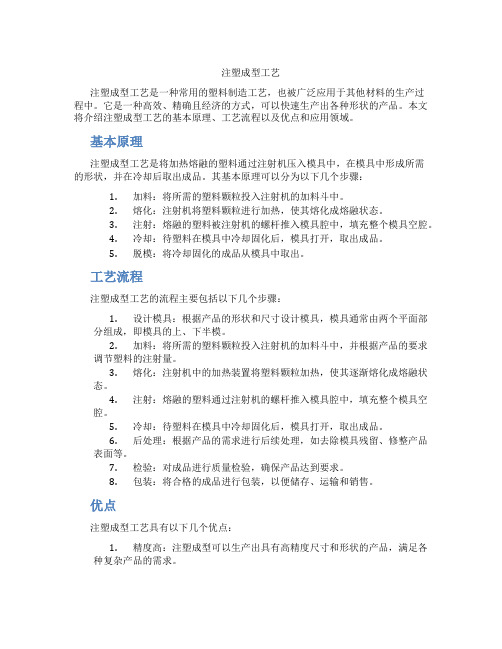
注塑成型工艺注塑成型工艺是一种常用的塑料制造工艺,也被广泛应用于其他材料的生产过程中。
它是一种高效、精确且经济的方式,可以快速生产出各种形状的产品。
本文将介绍注塑成型工艺的基本原理、工艺流程以及优点和应用领域。
基本原理注塑成型工艺是将加热熔融的塑料通过注射机压入模具中,在模具中形成所需的形状,并在冷却后取出成品。
其基本原理可以分为以下几个步骤:1.加料:将所需的塑料颗粒投入注射机的加料斗中。
2.熔化:注射机将塑料颗粒进行加热,使其熔化成熔融状态。
3.注射:熔融的塑料被注射机的螺杆推入模具腔中,填充整个模具空腔。
4.冷却:待塑料在模具中冷却固化后,模具打开,取出成品。
5.脱模:将冷却固化的成品从模具中取出。
工艺流程注塑成型工艺的流程主要包括以下几个步骤:1.设计模具:根据产品的形状和尺寸设计模具,模具通常由两个平面部分组成,即模具的上、下半模。
2.加料:将所需的塑料颗粒投入注射机的加料斗中,并根据产品的要求调节塑料的注射量。
3.熔化:注射机中的加热装置将塑料颗粒加热,使其逐渐熔化成熔融状态。
4.注射:熔融的塑料通过注射机的螺杆推入模具腔中,填充整个模具空腔。
5.冷却:待塑料在模具中冷却固化后,模具打开,取出成品。
6.后处理:根据产品的需求进行后续处理,如去除模具残留、修整产品表面等。
7.检验:对成品进行质量检验,确保产品达到要求。
8.包装:将合格的成品进行包装,以便储存、运输和销售。
优点注塑成型工艺具有以下几个优点:1.精度高:注塑成型可以生产出具有高精度尺寸和形状的产品,满足各种复杂产品的需求。
2.生产效率高:注塑成型工艺可以实现自动化生产,生产效率高、周期短。
3.可塑性强:注塑成型适用于大部分塑料材料,可以生产出各种硬度、透明度、色彩和质地的产品。
4.产品质量稳定:注塑成型工艺可以控制各个生产环节,减少产品缺陷,保证产品质量稳定。
应用领域注塑成型工艺广泛应用于各个领域,其中一些主要的应用领域包括:1.汽车工业:注塑成型工艺在汽车制造中应用广泛,可以生产汽车内饰件、外观件、电子设备等。
几种常用塑料的成型工艺介绍

几种常用塑料的成型工艺介绍常用塑料的成型工艺主要有注塑成型、挤出成型、吹塑成型、压延成型和热成型等。
以下将对这几种常用的成型工艺进行详细介绍。
1.注塑成型:注塑成型是最常用的塑料成型工艺之一、它通过将熔融的塑料注入到闭合的模具中,使其在模具中冷却固化,并获得所需的形状和尺寸。
这种成型工艺适用于大多数热塑性塑料,如聚乙烯、聚丙烯、聚氯乙烯等。
注塑成型具有生产效率高、成型周期短、尺寸精确等优点,因此广泛应用于制造塑料制品。
2.挤出成型:挤出成型是将熔融塑料通过挤出机加热和加压后,通过模具挤压成型。
挤出成型适用于长条状或不规则截面的塑料制品,如塑料管、塑料板、塑料薄膜等。
挤出成型的工艺过程简单,设备投资相对较低,但成型周期较长。
常见的挤出机包括单螺杆挤出机和双螺杆挤出机。
3.吹塑成型:吹塑成型是将加热的塑料取出塑料颗粒放入吹塑机的模冲中,通过内外压力使其塑化,并在成型模具壁上冷却固化。
吹塑成型适用于容器、瓶子等中空塑料制品的生产。
该工艺分为挤出吹塑和注射吹塑两种,挤出吹塑适用于生产大型中空容器,而注射吹塑适用于生产小型容器。
4.压延成型:压延成型是将熔融的塑料通过过辊进行挤压和冷却固化,形成所需的塑料薄板或薄膜。
压延成型适用于生产大型、平整的塑料制品,如塑料板材、塑料薄膜等。
压延成型工艺简单、成型速度快,但需要生产设备管道相对较长。
5.热成型:热成型是将硬化或部分硬化的塑料通过受热加热软化,然后通过模具压制形成所需形状的成型工艺。
热成型适用于板材或薄膜的生产,如吸塑制品、塑料包装等。
常见的热成型方法包括真空成型、热压成型和热吹成型等。
通过以上介绍,我们可以了解到几种常用的塑料成型工艺,包括注塑成型、挤出成型、吹塑成型、压延成型和热成型。
每种成型工艺都有其适用的塑料类型和成型产品,选择适合的成型工艺可以提高生产效率和产品质量。
tpr注塑成型工艺参数

TPR注塑成型工艺参数1. 简介TPR(热塑性橡胶)是一种特殊的材料,具有橡胶的弹性和塑料的可加工性。
TPR 注塑成型是一种常用的加工方法,通过在高温和压力下将熔融的TPR材料注入模具中,经冷却后得到所需形状的制品。
本文将详细介绍TPR注塑成型工艺参数,包括温度、压力、速度等方面。
2. 工艺参数2.1 温度温度是影响TPR注塑成型质量的重要参数之一。
合适的温度可以保证熔融状态下的TPR材料流动性和可加工性。
通常,温度分为以下几个部分:2.1.1 喂料区温度喂料区温度指进料斗和螺杆进给区域的温度。
一般来说,喂料区温度应控制在180-220摄氏度之间。
2.1.2 加热区温度加热区温度指螺杆上加热器设置的温度。
根据不同的TPR材料,加热区温度一般控制在180-240摄氏度之间。
2.1.3 螺杆头温度螺杆头温度是指注塑机喷嘴处的温度,一般来说,螺杆头温度应控制在200-260摄氏度之间。
2.2 压力压力是控制TPR注塑成型过程中的重要参数之一。
合适的压力可以保证熔融TPR材料充分填充模具空腔,并得到良好的尺寸和表面质量。
2.2.1 注射压力注射压力是指将熔融TPR材料注入模具时所施加的压力。
注射压力通常根据模具设计和工件要求进行调整,一般控制在50-150MPa之间。
2.2.2 保压压力保压压力是指在注射完成后继续施加的压力,以确保TPR材料充分填充模具空腔并防止产生缩孔或气泡。
保压时间一般为5-30秒,保压时间结束后释放保压压力。
2.3 速度速度是控制TPR注塑成型过程中的重要参数之一。
合适的速度可以保证TPR材料充分填充模具空腔,并得到良好的尺寸和表面质量。
2.3.1 螺杆转速螺杆转速是控制TPR材料进给和熔融的关键参数。
通常情况下,螺杆转速应根据具体情况进行调整,一般控制在20-100r/min之间。
2.3.2 注射速度注射速度是指将熔融的TPR材料注入模具时的速度。
注射速度应根据具体工件要求进行调整,一般控制在5-50cm/s之间。
注塑成型的原理
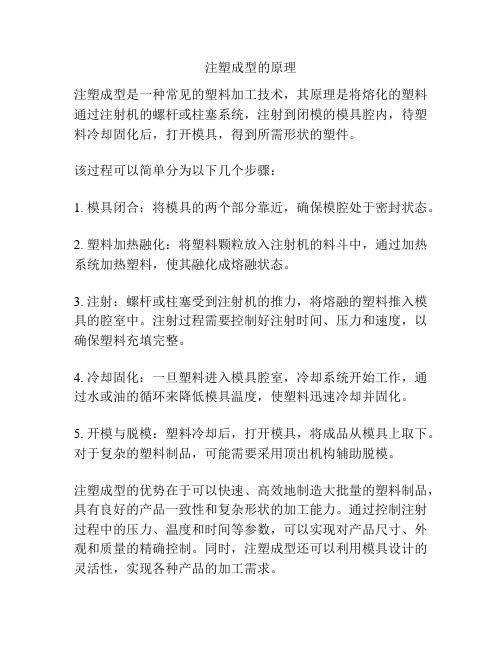
注塑成型的原理
注塑成型是一种常见的塑料加工技术,其原理是将熔化的塑料通过注射机的螺杆或柱塞系统,注射到闭模的模具腔内,待塑料冷却固化后,打开模具,得到所需形状的塑件。
该过程可以简单分为以下几个步骤:
1. 模具闭合:将模具的两个部分靠近,确保模腔处于密封状态。
2. 塑料加热融化:将塑料颗粒放入注射机的料斗中,通过加热系统加热塑料,使其融化成熔融状态。
3. 注射:螺杆或柱塞受到注射机的推力,将熔融的塑料推入模具的腔室中。
注射过程需要控制好注射时间、压力和速度,以确保塑料充填完整。
4. 冷却固化:一旦塑料进入模具腔室,冷却系统开始工作,通过水或油的循环来降低模具温度,使塑料迅速冷却并固化。
5. 开模与脱模:塑料冷却后,打开模具,将成品从模具上取下。
对于复杂的塑料制品,可能需要采用顶出机构辅助脱模。
注塑成型的优势在于可以快速、高效地制造大批量的塑料制品,具有良好的产品一致性和复杂形状的加工能力。
通过控制注射过程中的压力、温度和时间等参数,可以实现对产品尺寸、外观和质量的精确控制。
同时,注塑成型还可以利用模具设计的灵活性,实现各种产品的加工需求。
注塑成型定义
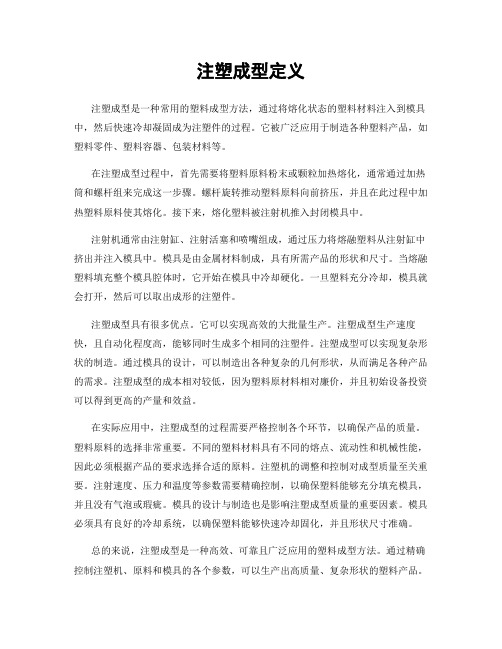
注塑成型定义注塑成型是一种常用的塑料成型方法,通过将熔化状态的塑料材料注入到模具中,然后快速冷却凝固成为注塑件的过程。
它被广泛应用于制造各种塑料产品,如塑料零件、塑料容器、包装材料等。
在注塑成型过程中,首先需要将塑料原料粉末或颗粒加热熔化,通常通过加热筒和螺杆组来完成这一步骤。
螺杆旋转推动塑料原料向前挤压,并且在此过程中加热塑料原料使其熔化。
接下来,熔化塑料被注射机推入封闭模具中。
注射机通常由注射缸、注射活塞和喷嘴组成,通过压力将熔融塑料从注射缸中挤出并注入模具中。
模具是由金属材料制成,具有所需产品的形状和尺寸。
当熔融塑料填充整个模具腔体时,它开始在模具中冷却硬化。
一旦塑料充分冷却,模具就会打开,然后可以取出成形的注塑件。
注塑成型具有很多优点。
它可以实现高效的大批量生产。
注塑成型生产速度快,且自动化程度高,能够同时生成多个相同的注塑件。
注塑成型可以实现复杂形状的制造。
通过模具的设计,可以制造出各种复杂的几何形状,从而满足各种产品的需求。
注塑成型的成本相对较低,因为塑料原材料相对廉价,并且初始设备投资可以得到更高的产量和效益。
在实际应用中,注塑成型的过程需要严格控制各个环节,以确保产品的质量。
塑料原料的选择非常重要。
不同的塑料材料具有不同的熔点、流动性和机械性能,因此必须根据产品的要求选择合适的原料。
注塑机的调整和控制对成型质量至关重要。
注射速度、压力和温度等参数需要精确控制,以确保塑料能够充分填充模具,并且没有气泡或瑕疵。
模具的设计与制造也是影响注塑成型质量的重要因素。
模具必须具有良好的冷却系统,以确保塑料能够快速冷却固化,并且形状尺寸准确。
总的来说,注塑成型是一种高效、可靠且广泛应用的塑料成型方法。
通过精确控制注塑机、原料和模具的各个参数,可以生产出高质量、复杂形状的塑料产品。
这种成型方法应用广泛,从汽车零件到电子产品外壳,从日常用品到医疗器械,注塑成型在各个领域都扮演着重要的角色。
随着科技的不断发展,注塑成型技术也将不断改进和创新,为人们创造更多高性能、高品质的塑料产品。
注塑成型工艺
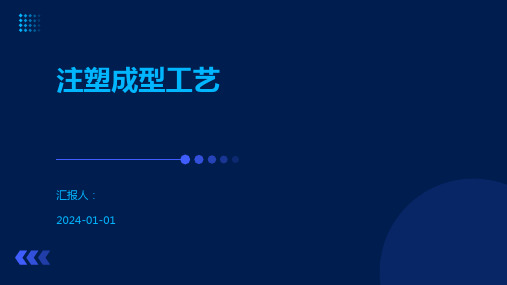
06
注塑成型新技术与发展趋势
高压注塑技术
总结词
高压注塑技术是一种提高注塑效率和减少材料浪费的工艺。
详细描述
高压注塑技术通过提高注射压力,使塑料在更短的时间内注入模具,减少了注 射时间和压力损失。这不仅提高了生产效率,而且减少了材料浪费和成本。
微注塑技术
总结词
微注塑技术是一种制造微小尺寸塑料零件的工艺。
收缩变形
合理控制模具温度和塑料温度,确保塑料冷 却均匀,减少收缩变形。
注塑制品的质量检测与控制
尺寸检测
使用测量工具对注塑制品进行尺寸检测,确保符合设计要求。
外观检测
检查注塑制品的外观,确保无气泡、裂纹、色差等缺陷。
结构检测
通过X光、超声波等手段对注塑制品内部结构进行检测,确保无缺陷。
性能检测
根据产品需求进行各种性能测试,如耐温、耐压、耐腐蚀等。
注塑成型工艺
汇报人: 2024-01-01
目录
• 注塑成型工艺简介 • 注塑成型原理 • 注塑成型设备 • 注塑成型材料 • 注塑成型质量控制 • 注塑成型新技术与发展趋势
01
注塑成型工艺简介
定义与特点
定义
注塑成型是一种塑料加工方法,通过 高温将塑料熔化,然后注入模具中冷 却固化,最后得到所需的塑料制品。
增韧改性
添加增韧剂,改善材料韧性。
阻燃改性
添加阻燃剂,提高材料的阻燃性能。
05
注塑成型质量控制
注塑成型常见问题及解决方案
填充不足
调整注射压力、注射速度和注射时间,确保 塑料充分填充模具。
溢料
检查模具设计,确保模具的流道和浇口设计 合理,避免塑料过度流动。
表面缺陷
优化模具温度和塑料温度,提高塑料流动性 ,减少表面缺陷。
注塑成型原理

注塑机根据塑化方式分为柱塞式注塑机和螺杆式注塑机;按机器的传动方式又可分为液压式、机械式和液压—机械(连杆)式;按操作方式分为自动、半自动、手动注塑机。 按开闭模方向与射胶方向分卧式注塑机、立式注塑机、角式注塑机、多模转盘式注塑机等。
1) 卧式注塑机:其合模部分和注射部分处于同一水平中心线上,且模具是沿水平方向打开的。其特点是:机身矮,易于操作和维修;机器重心低,安装较平稳;制品顶出后可利用重力作用自动落下,易于实现全自动操作。目前,市场上的注塑机多采用此种型式。
⑴ 注射装置:
主要作用是使塑料均匀地塑化熔融,以足够压力和速度将一定量的熔料注入模具的型腔中。并对模腔中的熔料进行保压、补缩。当树脂在模具内流动时,则控制螺杆的移动速度(射出速度),并在填充树脂後用压力(保压压力)进行控制。
当达到一定的螺杆位置或射出压力时,则从速度控制切换成压力控制。 它主要由塑化部件(螺杆、机筒、螺杆头、喷嘴等)、料斗、计量装置、传动装置、注射和注射座移动油缸等组成。 注射螺杆的特点:注射螺杆与挤出螺杆有许多相似之处,但由于注射成型机与挤出成型机操作条件不同,所以有很多区别如下:
1、螺杆具有塑化和注射两种功能 2、注射螺杆在塑化时,对制品不 发生直接的联系,仅作预塑用; 3、塑料在塑化过程中,所经历的热历程要比挤出时长; 4、注射螺杆在塑化和注射时,均要发生轴向位移,同时螺杆又处于时转时停的间歇式工作状态,形成了注射螺杆塑化过程的非稳定性。
因此从结构上对比,注射螺杆挤出螺杆有以下几点不同: 1、注射螺杆的长径比和压缩比比较小; 2、注射螺杆均化段的螺槽较深; 3、注射螺杆的加料段较长,而均化段较短 4、注射螺杆的头部结构具有特殊形式。
注塑成型工艺原理
第一节 注塑成型概述
注塑成型定义
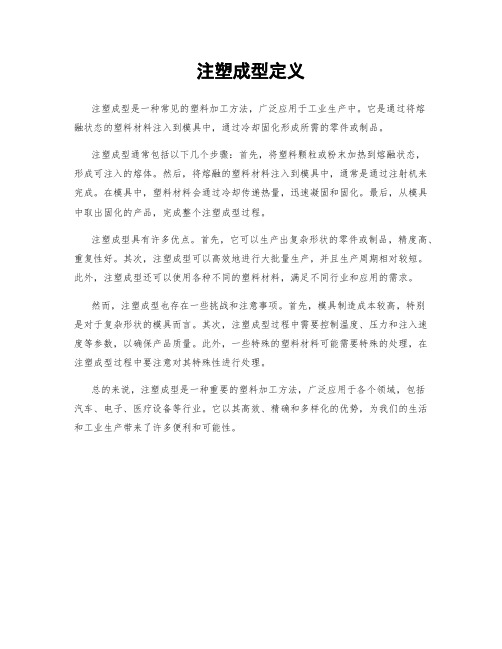
注塑成型定义
注塑成型是一种常见的塑料加工方法,广泛应用于工业生产中。
它是通过将熔
融状态的塑料材料注入到模具中,通过冷却固化形成所需的零件或制品。
注塑成型通常包括以下几个步骤:首先,将塑料颗粒或粉末加热到熔融状态,
形成可注入的熔体。
然后,将熔融的塑料材料注入到模具中,通常是通过注射机来完成。
在模具中,塑料材料会通过冷却传递热量,迅速凝固和固化。
最后,从模具中取出固化的产品,完成整个注塑成型过程。
注塑成型具有许多优点。
首先,它可以生产出复杂形状的零件或制品,精度高、重复性好。
其次,注塑成型可以高效地进行大批量生产,并且生产周期相对较短。
此外,注塑成型还可以使用各种不同的塑料材料,满足不同行业和应用的需求。
然而,注塑成型也存在一些挑战和注意事项。
首先,模具制造成本较高,特别
是对于复杂形状的模具而言。
其次,注塑成型过程中需要控制温度、压力和注入速度等参数,以确保产品质量。
此外,一些特殊的塑料材料可能需要特殊的处理,在注塑成型过程中要注意对其特殊性进行处理。
总的来说,注塑成型是一种重要的塑料加工方法,广泛应用于各个领域,包括
汽车、电子、医疗设备等行业。
它以其高效、精确和多样化的优势,为我们的生活和工业生产带来了许多便利和可能性。
注塑成型技术简介

注塑成型技术简介注塑成型技术是一种常见的塑料成型工艺,通过将熔化后的塑料注入模具中,再经过冷却凝固而得到所需形状的制品。
该技术具有高效、经济、精确和多样化的特点,广泛应用于日常生活和工业生产中。
注塑成型技术包括模具设计、原料选择、熔融加工、注塑成型和后处理等步骤。
首先,根据所需产品的形状和尺寸,设计制造相应的模具。
模具通常由金属材料制成,具有空腔和流道。
原料选择对成品的质量和性能至关重要,目前常用的塑料原料有聚丙烯(PP)、聚乙烯(PE)和聚氯乙烯(PVC)等。
在熔融加工阶段,将塑料原料通过熔化和混合的过程,使其变成可注入模具的熔融物料。
这通常通过将塑料颗粒放入注塑机中进行加热和融化完成。
注塑机由注射装置和锁模装置组成,注射装置负责将熔融物料注射到模具中,并在一定的压力下将模具封闭。
注塑成型是指将熔融物料注入到模具的过程。
在注塑期间,塑料将填充模具的空腔和流道,随后通过冷却水或其他冷却介质进行冷却,促使塑料凝固。
凝固后,模具开启,制品可取出。
最后,根据产品要求进行后处理。
这可能包括去除模具留下的毛刺,修整边缘,上色或上漆等。
注塑成型技术的优点包括:生产效率高,可进行连续生产;制品精确,形状符合设计要求;成品质量稳定,表面光滑;适用范围广泛,可生产各种材质的制品;自动化程度高,劳动力成本低。
注塑成型技术广泛应用于日常生活中,如塑料容器、玩具、电器外壳等产品的制造,也应用于工业生产中,如汽车零部件、电子元器件等。
随着科技进步,注塑成型技术不断创新改进,为各种行业带来了更多的应用前景。
注塑成型技术作为一种高效、经济、精确和多样化的塑料成型工艺,已经成为现代工业发展不可或缺的重要技术之一。
在过去几十年间,注塑成型技术经历了飞速的发展,从最初的手工操作到现在的全自动化注塑机,不断提高生产效率和产品质量。
注塑成型技术的优点之一是可以实现高效率的大规模生产。
由于注塑成型可以通过自动化生产线实现连续生产,能够迅速地制造大量相同尺寸、相同形状的产品。
- 1、下载文档前请自行甄别文档内容的完整性,平台不提供额外的编辑、内容补充、找答案等附加服务。
- 2、"仅部分预览"的文档,不可在线预览部分如存在完整性等问题,可反馈申请退款(可完整预览的文档不适用该条件!)。
- 3、如文档侵犯您的权益,请联系客服反馈,我们会尽快为您处理(人工客服工作时间:9:00-18:30)。
成降解
Injection Molding Material
Thermoplastics and Degradation 热塑性塑料和降解
T e m p e r a t u r e
Degradation 降解
Time 时间
Injection Molding
Barrel Unit The Reciprocating Screw
Barrel Unit The Reciprocating Screw
Shot
回转力矩 和背压
Rotation and Back Pressure
出量
Screw Rotation Feeds and Shears Material Into a Melt. Melt Collects Into Front of Barrel, Forcing Screw Back
Injection Molding Process
Model of Amorphous Polymers
Locked 固态 Entanglements
TG
Stiff Flow 难于流动
Easier Flow 较易流动
Raise Temperature of Polymer
Adding Heat Increases Space 外热提供空间 Between Molecular Chains 在分子链之间
固態
Rigid Solid
難於流動
較易流動
TG
Soft Solid
TM
Flows Easily
Raise Temperature of Polymer
Adding heat increases space between molecular chains but crystalline structure prevents flow.
Injection Molding Non Good Parts
充填不足(shot short)
是熔融塑料未完全流遍成型空 間(模穴的各個角落之現象.
診斷: 診斷
•不正确的进料 •注射压力和速度过低 •注射时间太短 •止回阀有問題. •模具排气不良 •模温过低 •料温过低或料熔体粘度太高
Injection Molding Non Good Parts
Injection Molding Non Good Parts
銀條(sliver streaks)
診斷: 銀條是在成型品表面或表面附近,沿 診斷 材料流動方向,呈現的銀白色條紋. •材料降解(料筒有热点, 材料在喷嘴处
有死角) •注射压力或速度过低或过高 •背压过低 •在浇口,机器喷嘴或热流道摩擦烧焦 •料温过高 •在塑胶粒中有污染 •过多水分
Injection Molding Variables
Melt Temperature
熔融温度
35
M e l t F l o w
30 25 20 15
101 @ 600 deg. F
LEXAN?101 550 deg F.
(in.) 10
5 0 .030 .060 .090 .120 .150 .180 .210 .240
• 浇口太小 • 浇口位置不當 • 浇口太长 • 模具过冷 • 料温过低 • 喷嘴有滴垂
Injection Molding Non Good Parts
頂白
成型品脫模之際,因頂出銷的頂力 或成型品倒鉤位之阻力,該部呈現 白色痕跡.
診斷: 診斷
•產品脱模角度不 夠 •模具排氣不良 •保压过大 •顶针过少或太小 •顶针粘住制品 •頂針頂出力不平 衡
Injection Molding Plastic
塑料類型
材料 塑料(高分子) 熱固性
工程 無定型 PC ABS MPPO PEI 結晶性 PPS PET POM PA 無定型 PMMA PS PVC
熱塑性
通用 結晶性 PE PP
Injection Molding Plastic 塑膠分子結構
Injection Molding Process Model of Crystalline Polymers
表观粘度
100
100
1000
10000
Shear Rate (1/s)
剪切速率
Injection Speed affects the viscosity of the molten material.
注射速度影响熔体粘度
Injection Molding Variables
Injection Pressure Profile 注射压力曲线
通过螺杆回转,熔体聚集于料筒前 部,反作用力使螺杆后退。
熔化混合
Injection Molding Equipment
Barrel Unit The Recjection Pressure
流動射出
在一定壓力,速度下熔體從噴嘴 的充填成型過程 流道 澆口 型腔
燒焦(burn marks)
成形品表面因材料過熱所致的 變色及成型品的銳角部份或肋 • 的前端等材料焦黑的現象. • • • • • • •
診斷: 診斷
机器止回阀问题 注射速度过快 背压过大 模具排气不良 模溫過高 摩擦烧焦 检查澆口及主流道大小 塑膠原料降解
Injection Molding Non Good Parts
制件冷却和固化
Hot Melt
Solid Part Cooled Mold
热熔体
固化的制件
温度较低的模具
Injection Molding Non Good Parts 黑點(black points) 来源:
机器
• 停机时间过长 • 机器长时间不用 • 未清干净料筒 • 喷嘴/止逆阀不良 • 不合适螺杆类型 模具 • 在浇口和流道上有 死角
Injection Molding Variables
Cushion 缓冲垫
Material remaining in barrel when the ejection phase is completed.
注过程结束后,残于料筒前 注过程结束后, 端的熔体
The injection molding process should allow a cushion to provide sufficient packing pressure in the Cushion (3~5mm) mold
Fill Time Time
Screw Run Time
填充时间
Injection Molding Equipment
Barrel Unit The Reciprocating Screw
Cushion (3~5mm)
缓冲垫
Packing Pressure
保压
壓縮保壓
模腔填滿塑膠后,繼續施加於 模腔塑膠上的注射壓力.
Wall Thickness in Inches壁厚(In)
Increased Melt Temperature yields increased Flow.提高熔融温度导致增加流动 However, Too High a Melt Temperature May Cause Degradation.但,过高熔融温度造
材料
•塑胶粒中杂质 •其它树脂降解 •来自料筒壁面降 解物 •次料/受污染原料 其它 •生产/操作环境 •注塑加工参数
Injection Molding Non Good Parts 噴射痕(flow marks) 診斷: 診斷 是熔融材料流動的痕跡,以澆 口為中心而呈現的條紋模樣. • 注射速度太快
注射成型基本原理簡介
注塑成型是一种注射兼模塑的成型的方法, 又稱注射成型.是塑料成型加工最普通也是最早 的成型方法. 注塑過程包括預塑,計量,注射,充模,泠卻定 型等過程,得到一定幾何形狀和精度的塑件制品. 注塑工藝參數的選擇和調整及原料,模具, 設備對制品質量將產生直接影響.
目錄
塑膠特性簡介 成型基本原理 成型常見不良及分析
謝謝!!!
缓冲垫
注过程必须要有缓冲垫以保证 有效的保压
Injection Molding variables
Barrel Unit 加料 The Reciprocating Screw
冷卻固化
產品冷卻固化而脫模后 又不致於發生變形.
Injection Molding Process
Part Cooling and Solidification
收縮(sink marks)
成型品表面產生凹陷的現象. 是體積 收縮所致,通常見於肉厚部分,肋或凸 出的背面,直接澆口肉厚不均的部份.
診斷: 診斷
无足够的材料或较厚肋 •注射压力过低 •射胶时间太短 •机器融胶能力不足 • •模温太高 •浇口过小 •流道过长 •產品肋/壁厚比不當 •浇口位置不當 •模具排气不良
Injection Molding Process Injection Flow 熔融流動
Injection Molding Variables
Injection Speed 注射速度
A p p a 1000 r e n t V i s c o s i t y (Pa/s) 10 LEXAN?141 @ 644 deg F LEXAN?141 @608 deg F LEXAN?141 @572 deg F
Peak Injection Pressure
注射压力峰值
液 压 压 力P
r e s s u r e
H y d r a u l i c
Back Pressure
Pressure Applied by Injection Ram to Force the Plastic From the Barrel to the Mold.