表面处理检验标准2016-01
表面处理检验标准
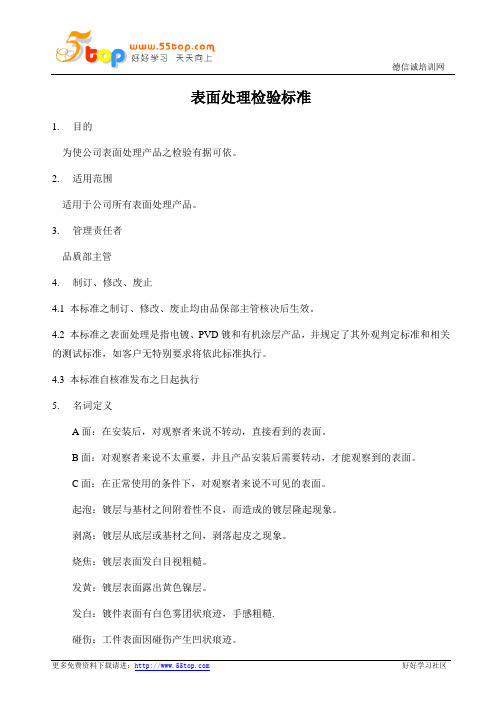
表面处理检验标准1.目的为使公司表面处理产品之检验有据可依。
2.适用范围适用于公司所有表面处理产品。
3.管理责任者品貭部主管4.制订、修改、废止4.1 本标准之制订、修改、废止均由品保部主管核决后生效。
4.2 本标准之表面处理是指电镀、PVD镀和有机涂层产品,并规定了其外观判定标准和相关的测试标准,如客户无特别要求将依此标准执行。
4.3 本标准自核准发布之日起执行5.名词定义A面:在安装后,对观察者来说不转动,直接看到的表面。
B面:对观察者来说不太重要,并且产品安装后需要转动,才能观察到的表面。
C面:在正常使用的条件下,对观察者来说不可见的表面。
起泡:镀层与基材之间附着性不良,而造成的镀层隆起现象。
剥离:镀层从底层或基材之间,剥落起皮之现象。
烧焦:镀层表面发白目视粗糙。
发黄:镀层表面露出黄色镍层。
发白:镀件表面有白色雾团状痕迹,手感粗糙.碰伤:工件表面因碰伤产生凹状痕迹。
5.10划伤:产品表面被尖锐物体划出线状痕迹。
5.11擦伤:产品表面因包装运输,安装操作等工作过程中擦出细微线状痕迹。
5.12砂眼:机加、铸造、焊接、压铸件抛光后,表面留有较大凹洞。
电镀品表现为较明现的孔眼.5.13针孔:机加、抛光或电镀后看到的部件表面上的小孔,它是由材质不良或焊接不良而引起的缺陷。
5.14麻点:产品表面细微小点常有群体现象。
5.15杂质:产品表面较明显凸状附着物,手感粗糙,有刮手的感觉.5.16露底材:镀件表面,未镀上铬、镍及PVD处理层之现象。
5.17弧伤:镀后产品表面呈雪花状痕迹。
5.18色差:同一产品不同表面,同一批产品不同表面,不同批产品表面,与标准色样板有较明显差异。
5.19脱落:产品镀后表面镀层脱落,露出原电镀表面。
5.20变形:产品连接边、直角边、圆弧面明显变形及螺纹变形。
5.21砂印:产品表面留下抛光前打砂工序痕迹。
5.22毛边:产品加工时表面留下的薄金属片或金属毛刺。
5.23过度抛光:工作表面、平面、圆弧面抛光后波浪状痕迹。
表面处理工艺及检验标准.

目录表面处理工艺规程 (1)表面磷化工艺规程 (1)表面电镀工艺规程 (3)表面发黑处理工艺规程 (12)表面淬火处理工艺规程 (17)金属表面处理检验规程 (19)表面磷化处理检验规程 (19)表面电镀检验规程 (20)表面发黑处理检验规程 (23)高频淬火检验规程 (24)一、表面处理工艺规程1、表面磷化工艺规程122.表面镀铬工艺规程2.1镀铬浴的分类2. 1.1 铬酸—硫酸浴(Sargent浴)2. 1.2 氟化物含有浴氟化物含有浴硅氟化物含有浴硼氟化物含有浴2.1.3 铬酸钠浴2.1.4 硫酸铬浴2.1.5 黑色铬浴2.2 Sargent浴(1)浴成分与组成Sargent浴的成分为铬酸及触媒的硫酸,单独的铬酸溶液无法镀铬,但加1种或2种以上的酸根为触媒在阴极帮助的还原析出时,即可电镀.触媒根可用硫酸盐和氟化物,硫酸盐有硫酸、硫酸铬等,指化物有氟酸、氟化铵、氟化钠、氟化钾、硅氟化钠、硅氟酸、硼氟酸之类的错氟化物.铬酸与硫酸的配合比在镀铬的析出条件中很重要,CrO3:SO4在50:1~200:1之间,大致要保持100:1的比例,触媒根用1种以上时,要计算全量,此时,相当于以触媒效果与硫酸根相等的当量计算的值之总计.因而,Sargent浴的标准浴组成为铬酸250g/ι、硫酸2.5g/ι,现在使用铬酸100g/ι的低浓度到400~500g/ι的高浓度浴.镀铬浴在建浴时,溶解铬酸(CrO3,无水铬酸)250g/ι,加100:1的2.5g/ι硫酸即可,但铬酸常混有少量硫酸,故须相对减少硫酸的添加量.无水铬酸为红褐色的片状结晶,很易溶解水中,入水后搅拌速溶.铬酸与硫酸量是以分析决定,铬酸量可由比重得知概略,标准液大致是玻美21度.如此建浴的铬酸一硫酸溶液为深红色透明液,由此溶液电镀也得不到满足的镀铬,但电解后变成稍不透明的暗红色液,比重也成玻美22~23度.理由是CrO3因电解而还原,液中局部生成3价铬,此3价铬的存在对镀铬有极重要的影响,含有3价铬的溶液才能得满足的镀铬.镀铬液须含有3价铬,除了电解而还原生成以外,也可直接添加草酸(10g/ι成2.75g/ιCr³)柠檬酸、碳酸铬、氢氧化铬等还原剂还原,但以电解生成法最好,下为药品还原法的式子一例.2CrO3+3(HCOO)2→Cr2O3+6CO2+3H2O 电解生成法的两极用铅板,在开始析出铬的电流密度电解.浴温越高或硫酸根越多越快,例如浴温60℃、以10A/dm²的阳极电流密度电解100小时生在约3g/ι的3价铬宜为2~3g/ι,设为5g/ι以下,此量不宜过多或过少,液中须保持约3g/ι,这关连硫酸量与阳极.(2)浴成分的作用Sargent浴的浴成分为铬酸、硫酸(触媒根)、3价铬,无水铬酸溶于水,CrO3+H2O«H2CrO4,成为铬酸液,再如H2CrO4«2H+SO4电离,此SO4²¯使铬酸的一部份成为硫酸铬(Cr(SO4)3),Cr(SO4)3«2Cr³⁺+3SO4²¯.也可为硫酸以外的酸或硫酸盐,但不宜用有氧化作用的酸、溶解阳极铅的酸—硝酸、盐酸、醋酸、磷酸或其盐.最好用有还原性的酸,诸如硼酸、氟酸或其盐、错盐等.有机酸虽有还原性,但会与铬酸作用而分解,所以只用于3价铬的生成.金属盐除了铬盐之外,会增加其它金属成分,所以不大使用.在以上的浴成分,液中有H⁺、4²¯、Cr⁺、SO4²¯存在,3价铬量多时,因此组成而暗色较强,成不透明,比重增高,适当的组成为250 CrO3‧3Cr2O3.镀铬的析出机构有各种假说,假说经下示过程.1. Cr⁶⁺→Cr³⁺→Cr⁺2. Cr⁶⁺→Cr³⁺→Cr²⁺→Cr⁺3. Cr⁶⁺→Cr⁺有Sargent等研究,尚无定说,下面概述一例.将铬酸水溶液电解的话,在阴极还原铬酸,如下产生3价铬和游离碱.HCrO4¯+3H2O+3⊖→Cr³⁺+7OH2H2CrO4-3⊕→Cr(OH)CrO4+3OH¯3价铬成为盐基性铬酸铬的不导性薄膜,包覆阴极,其后不还原铬酸,此皮膜为微孔性,通过此微孔,只离子半径小的H放电.在阳极是氧放,电只引起水的分解.但是,液中若有硫酸或氟酸之类的阴离子,此离子很小,藉静电引力被拉入铬酸铬此膜的微孔中,接触盐基成分,溶解皮膜分子,同时生成Cr³,皮膜有孔的话, HCrO4¯径此孔到达极,引起上式的反应,皮膜再生,但在此皮膜反复溶解再生的同时,往Cr³还原,并发生氢,此3价铬直接或径2价铬的阶段析出金属铬.3价铬的存在不直接关连铬的电着机构,但影响光泽电流密度范围、液电阻、包覆力等.(3)电镀条件(a)铬酸浓度的影响铬酸浓度的标准为250g/ι实际有100g/ι的低浓度浴到400~500g/ι的高浓度浴,高浓度浴与低浓度浴的差异不大明显,分别有下示特色:高浓度浴低浓度浴光泽稍劣良包覆力稍劣良硬度低高电流效率劣良液电阻小稍高镀层的外观关连浴温与电流密度变方,可得良好镀金的浴温和电流密度的范围大致一定,铁、镍素地上镀铬的浴温与电流密度的关系,浴温一定时,电流密度低处为乳白色,增大电流密度时,即成光泽电镀范围.增大电流密度时,成为灰色.光泽范围因素地种类而稍有不同,在镀镍上较小,在铜、黄铜上较大,由此图可知,光泽电镀范围在低温移到低电流密度,在高温移到高电流密度范围,但低温时,光泽范围减小,周边部容易发生灰色部,高温时,需要大电流的光泽差,故用45~55℃的范围.欲得无裂纹的镀铬时要在55~60℃之间.铁、镍素地上的电流密度为浴温(℃) 标准电流密度(A/dm²)50 20~3555 30~50浴温的1/2~2/3值为电流密度范围.镀铬发生的列纹在电镀初期为针孔状,不发生裂纹,随着镀层厚度的增大,裂纹会生长,大致在0.25~0. 5μ以内尚无裂纹.裂纹数受浴温与电流密度影响,在CrO3 250g/ι、H2SO4 2.5g/ι的浴中,随浴温的上升及电流密度的增加而减少裂纹数.内部应力因浴温的影响而大变,在20 A/dm²的电流密度,在40℃最小,密着性良好.电镀速度取决于浴温、电流密度,电流效率值在一般用条件下约为5~20%,此范围为光泽电镀范围.电镀速度在普通浴的浴温50℃、电流密度30时,析出1μ所需时间约2分半,1小时约成25μ的厚度,在同一浴温,电镀速度并非正比于电流密度,电流效率随电流密度的增加而激增.铬酸浓度增大时,比较两图,可知电镀速度、电流效率都下降.这些电镀速度、电流效率值是在电流均匀分布于被镀阴极全体的条件下决定,在实际的电镀作业条件中,铬的均匀电着性不良,电流很少均匀分布于复杂物品全体.损失于吊架等的电流也占某种比率,所以电镀速度或电流效率在实际作业中未必完全一致,但使电镀条件接近试验条件的话,但使电镀条件接近试验条件的话,平均值适用此值.(4)镀浴的管理铬酸因掏出、铬的析出、飞散、铬酸铅的生面而消耗,但因阴极用不溶性极,可由阴极溶解而补充,而且摇出量极多,在装饰镀铬作业中约达7成,飞散所致的消耗约占2成,因而,铬酸的洗净回收及飞沬防止剂可防止消耗.铬酸的被给量是将浴中的铬量定量而决定,现场是每日测定比重,推定消费量,因液中含有3价铬或铁分等而增高比重,所以实际为玻美23~24,配合比重测定,每月化学分析1~2次,可维持铬量.硫酸因掏出、飞散而消耗,但不因铬酸的析出或铬酸铅的生成而消费,所以消费率小于铬酸.硫酸分是藉分析决定,将钡所致的沉淀离心沈淀的迅速3、表面发黑处理工艺规程常温发黑处理工艺,主要由以下工艺步骤完成:1)清洗;2)脱脂:工件必须完全浸入脱脂液中;脱脂液浓度ph值12-14,处理时间10-30min,每过3-5分钟上下抖动几次,药液浓度低于ph12时补充脱脂粉;3)水洗;4)酸洗:酸洗液浓度ph值2-4,处理时间5-10min;5)水洗;6)发黑:池液浓度ph值2.5-3.5,处理时间10-12min;7)水洗;8)吹干;9)上油。
零件表面处理检验规范

零件表面处理检验规范一、适用范围本规范适用于、氧化、化学处理、喷塑、、喷砂、拉丝等金属表面处理的检验。
二、术语和定义A级表面:在使用过程中总能被客户看见的部分(如:面壳的正面和顶面,后壳的顶面,手柄,透镜,按键及键盘正面,探头整个表面等)。
B级表面:在使用过程中常常被客户看见的部分(如:面壳的左右侧面,底壳或后壳的左右侧面及背面等)。
这些表面允许有轻微不良,但是不致引起挑剔客户不购买产品。
C级表面:在使用过程中很少被客户注意到的表面部分(如:面壳的底面,底壳或后壳的底面,内部零件表面)。
此表面的外观缺陷应合理而且不至于给客户觉得该产品质量不佳。
金属表面:包括、氧化、钝化等表现为金属质感的表面,非喷涂表面。
基材花斑:电抛光、电镀或氧化前因基体材料腐蚀、或者材料中的杂质、材料微孔等原因所造成的、与周围材质表面不同光泽或粗糙度的斑块状花纹外观。
抛光区:对基材上的腐蚀、划伤、焊接区、铆接区等部位进行机械打磨抛光后表现出的局部高光泽、光亮区域。
浅划痕:镀(膜/塑/漆)层表面划伤,但未伤及底层(即底层未暴露);对其它无镀(膜/塑/漆)层表面则为:目测不明显、手指甲触摸无凹凸感、未伤及材料本体的伤痕。
数控冲床加工中机床台面对板材的摩擦产生的轻微痕迹属于此类划痕。
深划痕:镀(膜/塑/漆)层表面划伤,且已伤至底层(即底层已暴露出来);对其它无镀(膜/塑/漆) 层表面则为:目测明显、手指甲触摸有凹凸感、伤及材料本体的伤痕。
凹坑:由于基体材料缺陷,或在加工过程中操作不当等原因而在材料表面留下的小坑状痕迹。
凹凸痕:因基材受撞击或校形不良等而呈现出的明显变形、凹凸不平的现象,手摸时有不平感觉。
烧伤:拉丝、电抛光、电镀处理时因操作不当、造成零件表面过热而留下的烧蚀痕迹。
水印:电镀、氧化或电抛光后因清洗水未及时干燥或干燥不彻底所形成的斑纹、印迹。
露白:镀锌钝化膜因磨擦而被去除、露出新层,或因缝隙截留溶液导致的无钝化膜现象,呈现为区别于周围颜色的白色。
表面处理检验标准
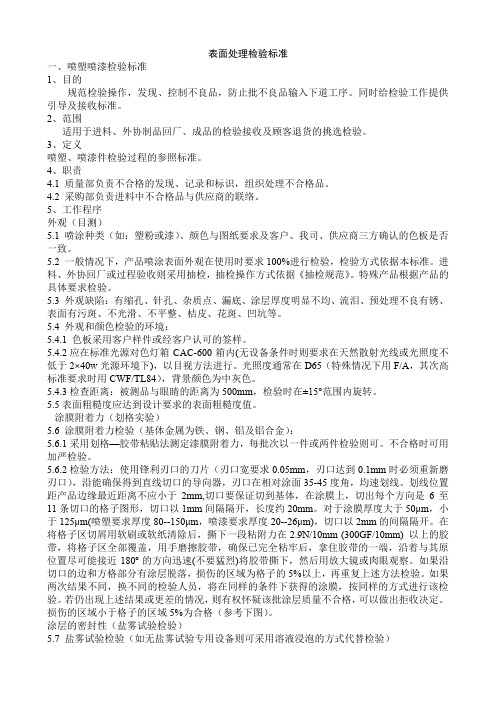
表面处理检验标准一、喷塑喷漆检验标准1、目的规范检验操作,发现、控制不良品,防止批不良品输入下道工序。
同时给检验工作提供引导及接收标准。
2、范围适用于进料、外协制品回厂、成品的检验接收及顾客退货的挑选检验。
3、定义喷塑、喷漆件检验过程的参照标准。
4、职责4.1 质量部负责不合格的发现、记录和标识,组织处理不合格品。
4.2 采购部负责进料中不合格品与供应商的联络。
5、工作程序外观(目测)5.1 喷涂种类(如:塑粉或漆)、颜色与图纸要求及客户、我司、供应商三方确认的色板是否一致。
5.2 一般情况下,产品喷涂表面外观在使用时要求100%进行检验,检验方式依据本标准。
进料、外协回厂或过程验收则采用抽检,抽检操作方式依据《抽检规范》。
特殊产品根据产品的具体要求检验。
5.3 外观缺陷:有缩孔、针孔、杂质点、漏底、涂层厚度明显不均、流泪、预处理不良有锈、表面有污斑、不光滑、不平整、桔皮、花斑、凹坑等。
5.4 外观和颜色检验的环境:5.4.1 色板采用客户样件或经客户认可的签样。
5.4.2应在标准光源对色灯箱CAC-600箱内(无设备条件时则要求在天然散射光线或光照度不低于2×40w光源环境下),以目视方法进行。
光照度通常在D65(特殊情况下用F/A,其次高标准要求时用CWF/TL84),背景颜色为中灰色。
5.4.3检查距离:被测品与眼睛的距离为500mm,检验时在±15°范围内旋转。
5.5表面粗糙度应达到设计要求的表面粗糙度值。
涂膜附着力(划格实验)5.6 涂膜附着力检验(基体金属为铁、钢、铝及铝合金):5.6.1采用划格—胶带粘贴法测定漆膜附着力,每批次以一件或两件检验则可。
不合格时可用加严检验。
5.6.2检验方法:使用锋利刃口的刀片(刃口宽要求0.05mm,刃口达到0.1mm时必须重新磨刃口),沿能确保得到直线切口的导向器,刃口在相对涂面35-45度角,均速划线。
划线位置距产品边缘最近距离不应小于2mm,切口要保证切到基体,在涂膜上,切出每个方向是6至11条切口的格子图形,切口以1mm间隔隔开,长度约20mm。
表面处理检测规范
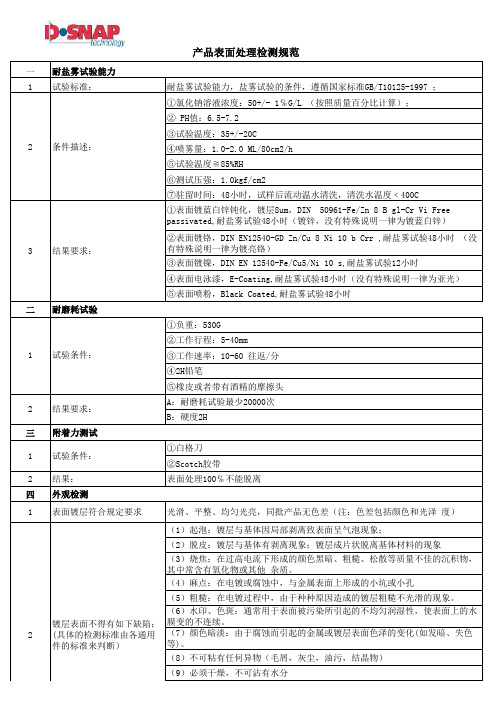
2检查周期:每批;3.数量:依MIL-STD-105E抽样计划水准。
第一節 電鍍層外觀檢驗金屬零件電鍍層的外觀檢驗是最基本﹐最常用的檢驗方。
外觀不合格的鍍件就無需進行其它項目的測試。
檢驗時用目力觀察﹐按照外觀可將鍍件分為合格的﹑有缺陷的和廢品三類。
外觀不良包括有針孔﹐麻點﹐起瘤﹑起皮﹑起泡﹑脫落﹑陰陽面﹑斑點﹑燒焦﹑暗影﹑樹枝狀和海綿狀江沉積層以及第 二節 結合力試驗鍍層結合力是指鍍層與基體金屬的結合強度﹐即單位面積的鍍層從基體金屬上剝離所需要的力。
鍍層結合力不好﹐多數原因是鍍前外理不良所致。
另外﹐鍍液成分與工藝規范不當或基體金屬與鍍層金屬的熱膨脹系 評定鍍層與基體金屬結合力通常采用定性方法。
車間定性測量法﹐是以鍍層金屬和基體金屬的物理-機械性能的不同為第 三節 電鍍層厚度的測量電鍍層厚度的測量方法有破壞檢測法與非破壞檢測法兩大類。
其中破壞檢測法有點滴法﹑液流法﹑溶解法﹑電量法和 測量時除溶解法等是鍍層的平均厚度外﹐其余多數是鍍層的局部厚度。
因此﹐測量時至少應在有代表性部位測量三個第 四節 孔隙率的測定鍍層的孔隙是指鍍層表面直至基體金屬的細小孔道 。
孔隙大小影響鍍層的防護能力。
測定孔隙的方法有貼濾法﹑涂膏1. 貼濾紙法﹕將浸有測試溶液的潤濕紙貼于經預處理的被測試閏上﹐濾紙上的試液滲入孔隙中與中間鍍層或基體金屬作2. 涂膏法﹕將含有相應試液的膏狀物涂覆于被測試樣上﹐通過泥膏中的試液滲入鍍層孔隙與基體金屬或中間鍍層作用﹐3. 浸漬法﹕將試樣浸于相應試液中﹐通過試液滲入鍍層孔隙與基體金屬或中間鍍層作用﹐在鍍層表面產生有色斑點﹐然第五節 鍍層顯微硬度的測定一、 硬度是鍍層的重要機械性能之一。
鍍層的硬度決定于鍍層金屬的結晶組織。
為了消除基體材對鍍層的影響和鍍層厚第六節 鍍層內應力的測試二、 鍍層內應力是指在沒有外在載荷的情況下﹐鍍層內部所具有的一種平衡應力。
用來測量鍍層宏觀應力的方法有﹕幻第七節 電鍍層脆性測試三、 鍍層脆性是鍍層物理性能中的一項重要指標。
金属表面处理检验规范.(DOC)
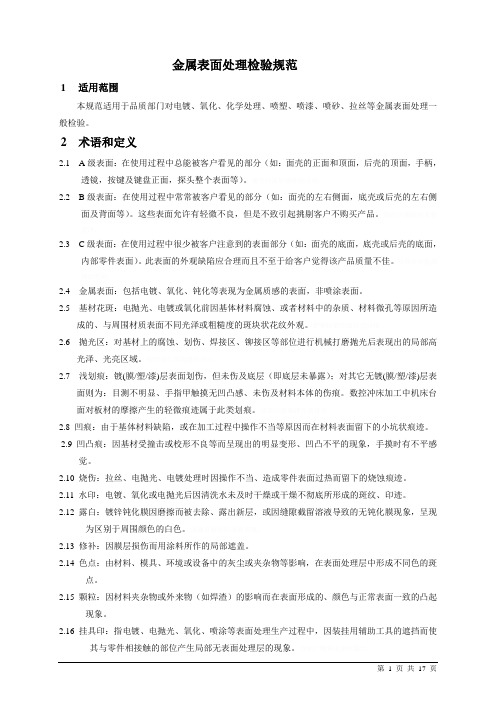
金属表面处理检验规范1适用范围本规范适用于品质部门对电镀、氧化、化学处理、喷塑、喷漆、喷砂、拉丝等金属表面处理一般检验。
2术语和定义2.1 A级表面:在使用过程中总能被客户看见的部分(如:面壳的正面和顶面,后壳的顶面,手柄,透镜,按键及键盘正面,探头整个表面等)。
2.2 B级表面:在使用过程中常常被客户看见的部分(如:面壳的左右侧面,底壳或后壳的左右侧面及背面等)。
这些表面允许有轻微不良,但是不致引起挑剔客户不购买产品。
2.3 C级表面:在使用过程中很少被客户注意到的表面部分(如:面壳的底面,底壳或后壳的底面,内部零件表面)。
此表面的外观缺陷应合理而且不至于给客户觉得该产品质量不佳。
2.4 金属表面:包括电镀、氧化、钝化等表现为金属质感的表面,非喷涂表面。
2.5 基材花斑:电抛光、电镀或氧化前因基体材料腐蚀、或者材料中的杂质、材料微孔等原因所造成的、与周围材质表面不同光泽或粗糙度的斑块状花纹外观。
2.6 抛光区:对基材上的腐蚀、划伤、焊接区、铆接区等部位进行机械打磨抛光后表现出的局部高光泽、光亮区域。
2.7 浅划痕:镀(膜/塑/漆)层表面划伤,但未伤及底层(即底层未暴露);对其它无镀(膜/塑/漆)层表面则为:目测不明显、手指甲触摸无凹凸感、未伤及材料本体的伤痕。
数控冲床加工中机床台面对板材的摩擦产生的轻微痕迹属于此类划痕。
2.8 凹痕:由于基体材料缺陷,或在加工过程中操作不当等原因而在材料表面留下的小坑状痕迹。
2.9凹凸痕:因基材受撞击或校形不良等而呈现出的明显变形、凹凸不平的现象,手摸时有不平感觉。
2.10 烧伤:拉丝、电抛光、电镀处理时因操作不当、造成零件表面过热而留下的烧蚀痕迹。
2.11 水印:电镀、氧化或电抛光后因清洗水未及时干燥或干燥不彻底所形成的斑纹、印迹。
2.12 露白:镀锌钝化膜因磨擦而被去除、露出新层,或因缝隙截留溶液导致的无钝化膜现象,呈现为区别于周围颜色的白色。
2.13 修补:因膜层损伤而用涂料所作的局部遮盖。
表面处理检验标准2016_01
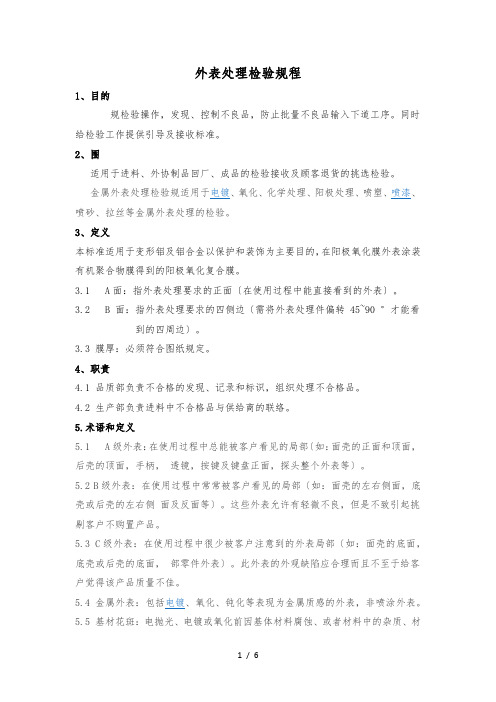
外表处理检验规程1、目的规检验操作,发现、控制不良品,防止批量不良品输入下道工序。
同时给检验工作提供引导及接收标准。
2、围适用于进料、外协制品回厂、成品的检验接收及顾客退货的挑选检验。
喷砂、拉丝等金属外表处理的检验。
3、定义本标准适用于变形铝及铝合金以保护和装饰为主要目的,在阳极氧化膜外表涂装有机聚合物膜得到的阳极氧化复合膜。
3.1 A面:指外表处理要求的正面〔在使用过程中能直接看到的外表〕。
3.2 B 面:指外表处理要求的四侧边〔需将外表处理件偏转45~90 °才能看到的四周边〕。
3.3 膜厚:必须符合图纸规定。
4、职责4.1 品质部负责不合格的发现、记录和标识,组织处理不合格品。
4.2 生产部负责进料中不合格品与供给商的联络。
5.术语和定义5.1 A级外表:在使用过程中总能被客户看见的局部〔如:面壳的正面和顶面,后壳的顶面,手柄,透镜,按键及键盘正面,探头整个外表等〕。
5.2 B级外表:在使用过程中常常被客户看见的局部〔如:面壳的左右侧面,底壳或后壳的左右侧面及反面等〕。
这些外表允许有轻微不良,但是不致引起挑剔客户不购置产品。
5.3 C级外表:在使用过程中很少被客户注意到的外表局部〔如:面壳的底面,底壳或后壳的底面,部零件外表〕。
此外表的外观缺陷应合理而且不至于给客户觉得该产品质量不佳。
5.4 金属外表:包括电镀、氧化、钝化等表现为金属质感的外表,非喷涂外表。
5.5 基材花斑:电抛光、电镀或氧化前因基体材料腐蚀、或者材料中的杂质、材料微孔等原因所造成的、与周围材质外表不同光泽或粗糙度的斑块状花纹外观。
5.6 抛光区:对基材上的腐蚀、划伤、焊接区、铆接区等部位进展机械打磨抛光后表现出的局部高光泽、光亮区域。
5.7 浅划痕:镀(膜/塑/漆)层外表划伤,但未伤及底层〔即底层未暴露〕;对其它无镀(膜/塑/漆)层表面那么为:目测不明显、手指甲触摸无凹凸感、未伤及材料本体的伤痕。
数控冲床加工中机床台面对板材的摩擦产生的轻微痕迹属于此类划痕。
金属表面处理检验规范.(DOC)

金属表面处理检验规范1 适用范围本规范适用于品质部门对电镀、氧化、化学处理、喷塑、喷漆、喷砂、拉丝等金属表面处理一般检验。
2术语和定义2.1 A级表面:在使用过程中总能被客户看见的部分(如:面壳的正面和顶面,后壳的顶面,手柄,透镜,按键及键盘正面,探头整个表面等)。
2.2 B级表面:在使用过程中常常被客户看见的部分(如:面壳的左右侧面,底壳或后壳的左右侧面及背面等)。
这些表面允许有轻微不良,但是不致引起挑剔客户不购买产品。
2.3 C级表面:在使用过程中很少被客户注意到的表面部分(如:面壳的底面,底壳或后壳的底面,内部零件表面)。
此表面的外观缺陷应合理而且不至于给客户觉得该产品质量不佳。
2.4金属表面:包括电镀、氧化、钝化等表现为金属质感的表面,非喷涂表面。
2.5基材花斑:电抛光、电镀或氧化前因基体材料腐蚀、或者材料中的杂质、材料微孔等原因所造成的、与周围材质表面不同光泽或粗糙度的斑块状花纹外观。
2.6抛光区:对基材上的腐蚀、划伤、焊接区、铆接区等部位进行机械打磨抛光后表现出的局部高光泽、光亮区域。
2.7浅划痕:镀(膜/塑/漆)层表面划伤,但未伤及底层(即底层未暴露);对其它无镀(膜/塑/漆)层表面则为:目测不明显、手指甲触摸无凹凸感、未伤及材料本体的伤痕。
数控冲床加工中机床台面对板材的摩擦产生的轻微痕迹属于此类划痕。
2.8凹痕:由于基体材料缺陷,或在加工过程中操作不当等原因而在材料表面留下的小坑状痕迹。
2.9凹凸痕:因基材受撞击或校形不良等而呈现出的明显变形、凹凸不平的现象,手摸时有不平感觉。
2.10烧伤:拉丝、电抛光、电镀处理时因操作不当、造成零件表面过热而留下的烧蚀痕迹。
2.11水印:电镀、氧化或电抛光后因清洗水未及时干燥或干燥不彻底所形成的斑纹、印迹。
2.12露白:镀锌钝化膜因磨擦而被去除、露出新层,或因缝隙截留溶液导致的无钝化膜现象,呈现为区别于周围颜色的白色。
2.13修补:因膜层损伤而用涂料所作的局部遮盖。
表面处理检测项目与方法

表面处理检测项目与方法一、表面处理的定义1. 表面处理:改变材料表面之物理,机械及化学性质之加工技术统称为表面处理或称为表面加工。
表面处理的对象非常广泛,从传统工业到现在的高科技工业,从以前的金属表面到现在的塑料,非金属的表面.它使材料更耐腐蚀,更耐磨耗,更耐热,它使材料之寿命延长,此外改善材料表面之特性,光泽美观等提高产品之附加价值。
2.表面处理的种类:镀(电镀、浸渍镀)、涂装、热浸镀以及乾氏镀法(PVD物理气相沉积法)3. 表面处理电镀层性能的测定项目:镀层厚度、孔隙率、机械物理性能和耐腐蚀性能等二、当前表面处理检测室的测试项目1膜厚测试11热淬火测试2CASS12胶带剥离测试3AASS13锯痕测试4NSS14锉刀测试5SO2测试15抗磨损测试6电位差测试16水浸测试7微孔数测试17铅笔硬度测试8冷热循环测试18抗化学性测试9气候交变测试19落砂测试10光泽度测试20光泽度测试……1.膜厚测试方法执行标准库仑法ASTM B504 X-射线荧光法ASTM B568金相显微镜法(仲裁方法)ASTM B4871.1 库仑法:属于电化学方法,又叫电量法或阳极溶解法。
它是用电解液对镀层进行阳极溶解,然后计算所消耗的电量,以此来计算镀层的厚度。
这种方法是测厚基础方法,准确度高、方便,并不受基体的限制,适合于单层和多层金属镀层厚度的测量,属于有损测厚方法。
1.2X-射线荧光法:X射线测厚法是用射线激发物质产生状态变化而发出可测信息的测试方法。
其工作原理是当被测物质经X射线或粒子射线照射后,由于吸收多余的能量而变成不稳定的状态。
从不稳定状态要回到稳定状态,吸收了能量的物质必须将多余的能量释放出来,是以荧光或光的形态释放出来,从而提供了可供测量的信息。
根据这一原理制作出了荧光X射线镀层厚度测量仪或成分分析仪。
这类仪器就是测量这种被释放出来的荧光的能量及强度,来对试样进行定性分析和定量分析。
由于这种测试是非破坏性的,并且可以在很微小的面积上测量镀层厚度,因此是现在流行的高性能测厚仪器。
(完整版)表面处理标准汇总.doc
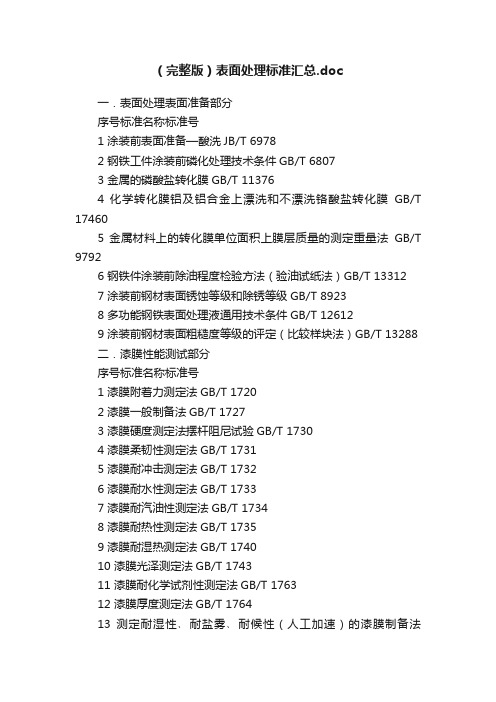
(完整版)表面处理标准汇总.doc一.表面处理表面准备部分序号标准名称标准号1 涂装前表面准备—酸洗JB/T 69782 钢铁工件涂装前磷化处理技术条件GB/T 68073 金属的磷酸盐转化膜GB/T 113764 化学转化膜铝及铝合金上漂洗和不漂洗铬酸盐转化膜GB/T 174605 金属材料上的转化膜单位面积上膜层质量的测定重量法GB/T 97926 钢铁件涂装前除油程度检验方法(验油试纸法)GB/T 133127 涂装前钢材表面锈蚀等级和除锈等级GB/T 89238 多功能钢铁表面处理液通用技术条件GB/T 126129 涂装前钢材表面粗糙度等级的评定(比较样块法)GB/T 13288二.漆膜性能测试部分序号标准名称标准号1 漆膜附着力测定法GB/T 17202 漆膜一般制备法GB/T 17273 漆膜硬度测定法摆杆阻尼试验GB/T 17304 漆膜柔韧性测定法GB/T 17315 漆膜耐冲击测定法GB/T 17326 漆膜耐水性测定法GB/T 17337 漆膜耐汽油性测定法GB/T 17348 漆膜耐热性测定法GB/T 17359 漆膜耐湿热测定法GB/T 174010 漆膜光泽测定法GB/T 174311 漆膜耐化学试剂性测定法GB/T 176312 漆膜厚度测定法GB/T 176413 测定耐湿性﹑耐盐雾﹑耐候性(人工加速)的漆膜制备法GB/T 176514 色漆和清漆涂层老化的评级方法GB/T 176615 色漆和清漆耐中性盐雾性能的测定GB/T 177116 色漆和清漆人工气候老化和人工辐射暴露(滤过的氙弧辐射)GB/T 186517 漆膜颜色标准GB/T 318118 色漆和清漆耐水性的测定浸水法GB/T 520919 涂层附着力的测定法拉开法GB/T 521020 涂膜硬度铅笔测定法GB/T 673921 涂膜弯曲试验(圆柱轴)GB/T 674222 色漆和清漆划痕试验GB/T 927923 色漆和清漆漆膜的划格试验GB/T 928624 色漆和清漆杯突试验GB/T 975325 色漆和清漆不含金属颜料的色漆漆膜之20°﹑60°和85°镜面GB/T 9754光泽的测定26 人造气氛腐蚀试验盐雾试验GB/T 1012527 金属和其他非有机覆盖层通常凝露条件下的二氧化硫腐蚀试验GB/T 978928 色漆和清漆漆膜厚度的测定GB/T 13452.229 色漆和清漆钢铁表面上的丝状腐蚀试验GB/T 13452.430 色漆和清漆耐湿性的测定连续冷凝法GB/T 1389331 色漆涂层粉化程度的测定方法及评定GB/T 1482632 绝缘漆漆膜击穿强度测定法HG/T 2-57三.部分涂料标准序号标准名称标准号1 电泳漆漆膜制备法HG/T2 —10462 电泳漆电导率测定法HG/T 2-10473 电泳漆泳透力测定法HG/T 2-10484 电泳漆库仑效率测定法HG/T 2-10495 电泳漆沉积量测定法HG/T 2-10506 电泳漆泳透力测定法(钢管法)HG/T 2-10517 涂料粘度测定法GB/T 17238 涂料细度测定法GB/T 17249 涂料固体含量测定法GB/T 172510 涂料遮盖力测定法GB/T 172611 涂料流平性测定法GB/T 175012 涂料产品分类,命名和型号GB/T 270513 涂料产品的取样GB/T 318614 色漆和清漆词汇第一部分通用术语GB/T 5206.115 色漆和清漆词汇第二部分树脂术语GB/T 5206.216 色漆和清漆词汇第三部分颜料术语GB/T 5206.317 色漆和清漆词汇第四部分涂料及涂膜物化性能术语GB/T 5206.418 色漆和清漆词汇第五部分涂料及涂膜病态术语GB/T 5206.519 色漆和清漆用漆基皂化值的测定法GB/T 674420 色漆和清漆密度的测定GB/T 675021 色漆和清漆挥发物和不挥发物的测定GB/T 675122 涂料及有关产品闪光测定法闭口杯平衡法GB/T 6753.523 色漆流挂性的测定GB/T 926424 色漆和清漆用原材料取样GB 928525 饰面型防火涂料防火性能分级及试验方法防火性能分级GB 15442.126 饰面型防火涂料防火性能分级及试验方法大板燃烧法GB/T 15442.227 饰面型防火涂料防火性能分级及试验方法隧道燃烧法GB/T 15442.328 饰面型防火涂料防火性能分级及试验方法小室燃烧法GB/T 15442.429 粉末涂料烘烤时质量损失的测定GB/T 1659230 涂料产品检验 , 运输和储存通则HG/T 2458四.安全与环保标准序号标准名称标准号1 涂装作业安全规程涂漆前处理工艺安全及其通风净化GB 76922 涂装作业安全规程静电喷枪及其辅助装置安全技术条件GB 147733 涂装作业安全规程涂漆工艺安全及其通风净化GB 65144 涂装作业安全规程喷漆室安全技术规定GB 144445 涂装作业安全规程涂层烘干室安全技术规定GB 144436 污水综合排放标准GB 8978国际标准部分序号标准名称标准号1 色漆和清漆 - 试验用标准样板ISO 15142 色漆和清漆 - 划痕试验ISO 15183 色漆和清漆 - 弯曲试验(圆柱轴)ISO 15194 色漆和清漆 - 压痕试验ISO 15205 色漆和清漆 - 摆杆阻尼试验ISO 15226 色漆和清漆、石油和有关产品闪点的测定- 闭杯平衡法ISO 15237 色漆和清漆 - 研磨细度的测定ISO 15248 色漆和清漆 - 划格试验ISO 24099 色漆和清漆 - 漆膜厚度的测定ISO 280810 色漆和清漆 - 密度的测定ISO 281111 色漆和清漆 - 在20°、60°和85°非金属色漆漆膜镜面光泽的测定ISO 281312 色漆和清漆 - 巴克霍尔压痕试验ISO 281513 色漆和清漆 - 在高剪切速率下粘度的测定ISO 288414 色漆和清漆 - 色漆和清漆以及色漆和清漆用漆基的不挥发物的测定ISO 325115 色漆和清漆–色漆的目视比色ISO 366816 色漆、清漆、石油和有关产品- 闪点的测定- 快速平衡法ISO 367917 色漆、清漆、石油和有关产品- 闪点 / 非闪点试验 - 快速平衡法ISO 368018 色漆和清漆用漆基 - 皂化值的测定 - 滴定法ISO 368119 色漆和清漆用漆基 - 酸值的测定 - 滴定法ISO 368220 色漆和清漆–术语对照表 - 第 1 部份:通用术语双语种版本ISO 4617-121 色漆和清漆–术语对照表- 第 2 部份:三语种版本ISO 4617-222 色漆和清漆–术语对照表- 第 3 部份:三语种版本ISO 4617-323 色漆和清漆–术语对照表- 第 4 部份:三语种版本ISO 4617-424 色漆和清漆–词汇 - 第 1 部份:通用术语三语种版本ISO 4618-125 色漆和清漆–词汇 - 第 2 部份:薄膜在老化过程中不良变化及其原始缺ISO 4618-2陷术语三语种版本26 色漆和清漆–词汇 - 第 3 部份:树脂术语三语种版本ISO 4618-327 色漆和清漆–钢面的丝状腐蚀试验ISO 462328 色漆和清漆–粘合力拉开试验ISO 462429 色漆和清漆用漆基 - 羟基值的测定 - 滴定法ISO 462930 色漆和清漆用漆基- 耐湿性能的测定(连续冷凝作用)ISO 627031 色漆和清漆 - 落锤试验ISO 627232 色漆和清漆 - 压痕试验(球体或棱锥体)ISO 644133 色漆和清漆用漆基 - 遮盖力的测定 - 第 1 部份:用于白色和浅色色漆的ISO 6504-1Kubelka-Munk 法34 色漆和清漆 - 弯曲试验(圆锥形心轴)ISO 686035 色漆和清漆 - 耐中性盐雾的测定ISO 725336 粉末涂料 - 第 7 部份:烘烤质量损失的测定ISO 8130-737 粉末涂料 - 第 9 部份:取样ISO 8130-938 金属的磷酸盐转化膜 - 确定要求的方法ISO 971739 化学转化膜 - 铝及铝合金上的漂洗和不漂洗铬酸盐转化膜ISO 1054640 人造气氛腐蚀试验 - 盐雾试验ISO 922741 金属材料上的转化膜- 单位面积上膜层质量的测量- 重量法ISO 389242 试验方法标准盐雾试验ASTM B11743 试验方法标准醋酸 - 盐雾试验ASTM B28744 试验方法标准铜加速的醋酸 - 盐雾试验( CASS试验)ASTM B36845 试验方法标准用锥形挠曲机试验附着的有机涂层的伸长ASTM D52246 试验方法标准镜面光泽ASTM D52347 方法标准试验色漆、清漆、喷漆和有关产品用钢板的制备ASTM D60948 方法标准评定涂漆钢材表面生锈等级ASTM D61049 方法标准外用色漆粉化程度的评定ASTM D65950 方法标准色漆起泡程度的测定ASTM D71451 方法标准有机涂层干膜厚度的测定ASTM D100552 方法标准在钢板上油漆的户外暴露试验ASTM D101453 方法标准在非磁性金属底材上的色漆、清漆、喷漆及有关产品的非ASTM D1400金属涂层干膜厚度的测定54 试验方法标准清漆的弹性或柔韧性ASTM D164255 试验方法标准清漆干膜的耐水性和耐碱性ASTM D164756 方法标准涂漆用铝与铝合金表面的处理ASTM D173057 方法标准涂漆用热浸铝表面处理ASTM D173158 方法标准涂漆用镁合金表面的处理ASTM D173259 方法标准色漆、清漆、喷漆及其有关产品试验用铝合金样板的处理ASTM D173360 试验方法标准用圆柱轴装置试验附着的有机涂层的伸长ASTM D173761 试验方法标准有机涂层的附着力ASTM D219762 方法标准试验色漆、清漆、喷漆及其有关产品用的热浸、非钝化镀ASTM D2201锌钢板的处理63 试验方法标准有机涂层抗快速变型(冲击)的作用ASTM D279464 试验方法标准涂层抗碎裂性ASTM D317065 试验方法标准漆膜孔隙率ASTM D325866 试验方法标准用胶带试验测定附着力ASTM D335967 试验方法标准用铅笔试验测定漆膜厚度ASTM D336368 推荐作法标准用磁场法或涡流法(电场法)测定涂层厚度ASTM E37669 试验方法标准管道涂层的耐冲击性(石灰石落降试验)ASTM G1370 试验方法标准管道涂层的耐冲击性(落锤试验)ASTM G1471 试验方法标准管道涂层的耐穿透性(圆头棒法)ASTM G17。
表面处理标准
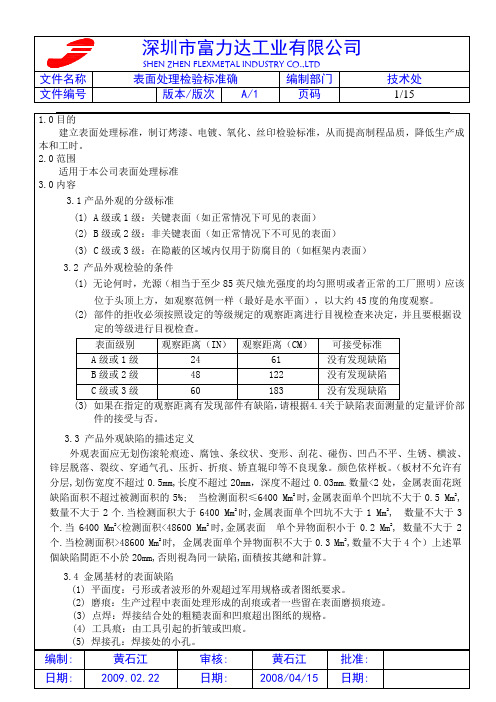
FULIDA文件名称表面处理检验标准确编制部门技术处文件编号版本/版次A/1 页码13/15(1) 依图面对照检查网板字体、字号、字高、丝印内容、丝印颜色及丝印位置尺寸是否符合要求。
(2) 检查网板是否有破损现象。
(3) 丝印网板进行编号,以方便查询使用。
(4) 丝印网板在使用完毕后,必须进行清洁处理后方可将丝印网板进行归位放置。
3.9.3 调配油墨:(1)热固化性油墨,油墨型号:1300系列,稀释剂 T-1000(或开油水)。
比例:油墨比稀释剂为:100:10(2) 焗烤固化:炉温145℃±5℃,恒温时间15分钟。
(3) QSTP系列型自干固化油墨.(4) 油墨与硬化剂比例4:1混合均匀备加稀释剂783.比例为10~20%调合均匀。
(5) 常温(25℃)下干燥时,表干时间30分~1小时,安全硬化时间为24小时,热固化条件:炉温120℃,时间10分钟。
注:混合后油墨粘度随时间,温度增加而增大。
25℃时可使用4H,因此注意随用随配,在允许使用时间内完成。
3.9.4 油墨类的保存期限及环境要求:(1) 油墨的保存期,根据油墨盒上标示的有效期执行,超过有效期的油墨进行标示隔离,不能再使用。
(2) 温度(25±5)℃;湿度30%-75%RH。
3.9.5 丝印要求:(1) 将网板定位后,再用卡尺、卷尺检查定位尺寸是否符合图纸要求。
(2) 丝印时,保证网板与料品之间有一定的间隙(依网板松紧)。
(3) 丝印后根据图纸/样本检查丝印字体、字高、丝印内容、丝印颜色及丝印位置尺寸是否符合图纸/样本要求,并检查有无漏印、错印、重印、少墨、毛边、缺损、断线、飞溅及油墨污染其它部位等不良现象。
(4) 制程检验,对丝印定位尺寸每20件检查一次,若图纸未注尺寸公差,当最大的外观尺寸≥450mm, 按照GB/T 1804-2000一般公差未注公差的线性和角度尺寸的公差:线性尺寸的极限偏差数值(c级)进行;当最大的外观尺寸<450mm,按照GB/T 1804-2000一般公差未注公差的线性和角度尺寸的公差:线性尺寸的极限偏差数值(m级)进行(客户有要求时按其要求执行)。
金属表面处理检验规范
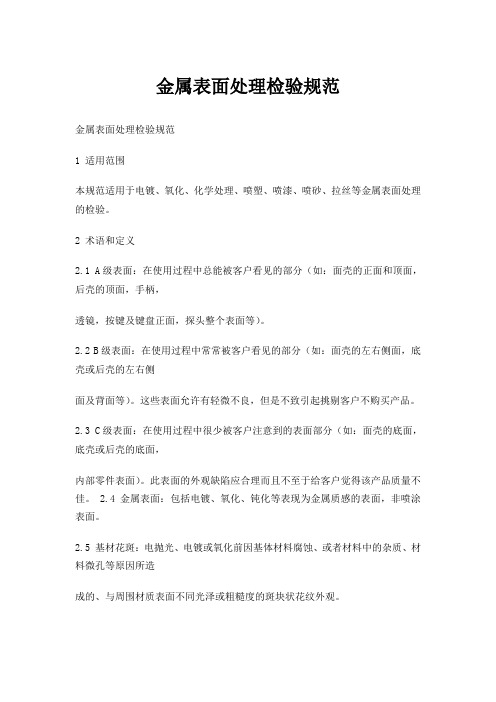
金属表面处理检验规范金属表面处理检验规范1 适用范围本规范适用于电镀、氧化、化学处理、喷塑、喷漆、喷砂、拉丝等金属表面处理的检验。
2 术语和定义2.1 A级表面:在使用过程中总能被客户看见的部分(如:面壳的正面和顶面,后壳的顶面,手柄,透镜,按键及键盘正面,探头整个表面等)。
2.2 B级表面:在使用过程中常常被客户看见的部分(如:面壳的左右侧面,底壳或后壳的左右侧面及背面等)。
这些表面允许有轻微不良,但是不致引起挑剔客户不购买产品。
2.3 C级表面:在使用过程中很少被客户注意到的表面部分(如:面壳的底面,底壳或后壳的底面,内部零件表面)。
此表面的外观缺陷应合理而且不至于给客户觉得该产品质量不佳。
2.4 金属表面:包括电镀、氧化、钝化等表现为金属质感的表面,非喷涂表面。
2.5 基材花斑:电抛光、电镀或氧化前因基体材料腐蚀、或者材料中的杂质、材料微孔等原因所造成的、与周围材质表面不同光泽或粗糙度的斑块状花纹外观。
2.6 抛光区:对基材上的腐蚀、划伤、焊接区、铆接区等部位进行机械打磨抛光后表现出的局部高光泽、光亮区域。
2.7 浅划痕:镀(膜/塑/漆)层表面划伤,但未伤及底层(即底层未暴露);对其它无镀(膜/塑/漆)层表面则为:目测不明显、手指甲触摸无凹凸感、未伤及材料本体的伤痕。
数控冲床加工中机床台面对板材的摩擦产生的轻微痕迹属于此类划痕。
2.8 深划痕:镀(膜/塑/漆)层表面划伤,且已伤至底层(即底层已暴露出来);对其它无镀(膜/塑/漆)层表面则为:目测明显、手指甲触摸有凹凸感、伤及材料本体的伤痕。
2.9 凹坑:由于基体材料缺陷,或在加工过程中操作不当等原因而在材料表面留下的小坑状痕迹。
2.10 凹凸痕:因基材受撞击或校形不良等而呈现出的明显变形、凹凸不平的现象,手摸时有不平感觉。
2.11 烧伤:拉丝、电抛光、电镀处理时因操作不当、造成零件表面过热而留下的烧蚀痕迹。
2.12 水印:电镀、氧化或电抛光后因清洗水未及时干燥或干燥不彻底所形成的斑纹、印迹。
(整理)零部件表面处理标准
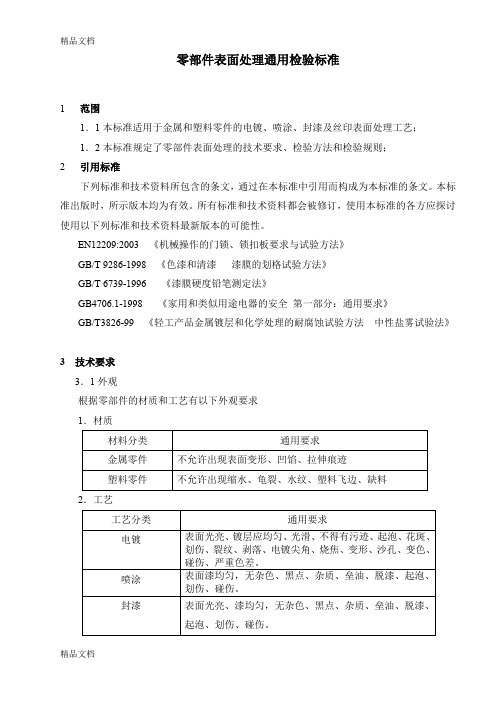
零部件表面处理通用检验标准1范围1.1本标准适用于金属和塑料零件的电镀、喷涂、封漆及丝印表面处理工艺;1.2本标准规定了零部件表面处理的技术要求、检验方法和检验规则;2 引用标准下列标准和技术资料所包含的条文,通过在本标准中引用而构成为本标准的条文。
本标准出版时,所示版本均为有效。
所有标准和技术资料都会被修订,使用本标准的各方应探讨使用以下列标准和技术资料最新版本的可能性。
EN12209:2003 《机械操作的门锁、锁扣板要求与试验方法》GB/T 9286-1998 《色漆和清漆漆膜的划格试验方法》GB/T 6739-1996 《漆膜硬度铅笔测定法》GB4706.1-1998 《家用和类似用途电器的安全第一部分:通用要求》GB/T3826-99 《轻工产品金属镀层和化学处理的耐腐蚀试验方法中性盐雾试验法》3技术要求3.1外观根据零部件的材质和工艺有以下外观要求1.材质2.工艺3.2颜色颜色必需符合以下要求,并且不能出现色差及色斑。
1.图纸有要求基础色调(色标)的,按图纸标注的PANTONE基础色调执行;2.图纸没要求基础色调(色标)的,按样品封样要求执行。
3.3镀层和漆层附着力按照4.3中的方法进行试验,镀层或涂层应满足切口交叉处有少许涂层脱落,但交叉切割总面积受影响不能明显大于5%的百格刀划格试验要求。
3.4镀层和漆层硬度按照4.4中的方法进行试验,镀层或涂层应满足牌号为HB的铅笔硬度试验,试验的结果为划痕后,不能出现涂层擦伤或见到材料底部的颜色。
3.5 镀层和漆层盐雾试验按照4.6中的方法进行试验,镀层或漆层应满足以下等级的盐雾试验,并且镀层和漆层不应有起泡、腐蚀、褪色、涂层脱落及生锈等现象。
3.6 镀层和漆层耐溶性按照4.5中的方法进行试验,镀层或涂层(包括丝印层)应满足酒精及汽油各15S 的擦试试验,并且镀层和漆层不应有起泡、腐蚀、褪色、变色、涂层脱落及发涨等现象。
注:本要求只适用于涉及外观的零部件上。
钣金表面处理通用检验标准

检验标准名称:表面处理通用检验标准图号:DMBM0.402. 003拟制:***审核:***标准化:***IQC会签:***批准:***目次○、总则................................................................................................................................. 1一、电镀镍检验标准............................................................................................................. 11.1 试样要求.................................................................................................................. 11.2 外观.......................................................................................................................... 11.3 镀层厚度.................................................................................................................. 21.4 结合强度.................................................................................................................. 21.5 耐蚀性...................................................................................................................... 2二、电镀锌检验标准............................................................................................................. 32.1 试样要求.................................................................................................................. 32.2 外观.......................................................................................................................... 32.3 镀层厚度.................................................................................................................. 42.4 结合强度.................................................................................................................. 42.5 耐蚀性...................................................................................................................... 42.6 白色钝化膜的存在性试验...................................................................................... 4三、装饰镀铬检验标准......................................................................................................... 53.1试样要求................................................................................................................... 53.2 外观.......................................................................................................................... 53.3 镀层厚度.................................................................................................................. 53.4 结合强度.................................................................................................................. 63.5 耐蚀性...................................................................................................................... 6四、喷漆检验标准................................................................................................................. 74.1 试片要求.................................................................................................................. 74.2 颜色.......................................................................................................................... 74.3 光泽.......................................................................................................................... 74.4 外观.......................................................................................................................... 74.5 漆层厚度.................................................................................................................. 84.6 附着力...................................................................................................................... 84.7 抗冲击性.................................................................................................................. 84.8 耐溶剂(无水乙醇)性.......................................................................................... 8五、粉末喷涂检验标准......................................................................................................... 95.1 试片要求.................................................................................................................. 95.2 颜色.......................................................................................................................... 95.3 光泽.......................................................................................................................... 95.4 外观.......................................................................................................................... 95.5 涂层厚度.................................................................................................................. 95.6 附着力.................................................................................................................. 105.7 抗冲击性.............................................................................................................. 105.8 耐溶剂(无水乙醇)性...................................................................................... 10六、铝合金化学氧化检验标准......................................................................................... 116.1 试片要求.............................................................................................................. 116.2 外观...................................................................................................................... 116.3 耐蚀性.................................................................................................................. 11七、铝合金喷砂光亮阳极化检验标准............................................................................. 127.1 试片要求.............................................................................................................. 127.2 外观...................................................................................................................... 127.3 氧化膜厚度.......................................................................................................... 127.4 耐蚀性.................................................................................................................. 127.5 封闭质量.............................................................................................................. 12八、喷砂及拉丝检验标准................................................................................................. 138.1 拉丝件.................................................................................................................. 138.2 喷砂件.................................................................................................................. 13表面处理通用检验标准○、总则0.1 零部件表面处理前应去除毛刺、飞边、划痕、氧化层等缺陷,锐边棱角倒钝。
零件表面处理检验

1.目的:确定有表面处理的零件进料验收标准。
2.范围:本标准规定了有表面处理的零件检验要求及试验方法、试验要求。
3.定义3.1.功能性外观缺陷:功能性表面缺陷是指产品构件的基材在产品使用过程中被腐蚀。
不允许在任何已经处理完毕的零件存在任何功能性外观缺陷。
3.2.装饰性外观缺陷:装饰性外观缺陷导致构件不能像期望的那样外观完好,但它不会造成功能失效。
本规范规定装饰性外观缺陷的种类、部位和可接受的限度。
3.3.活动手感与配合状态缺陷:活动手感与配合状态缺陷覆盖了做工问题,如本体与控制圈等配合的松紧程度和过大的配合间隙。
产品做工问题对于产品性能和由此决定的顾客满意度的影响,轻则削弱客户对产品美感的认同,重则导致客户不能正确安装或者操作产品。
备注:PVD :如果该列为“X ”,则该缺陷存在于PVD 表面处理。
电镀:如果该列为“X ”,则该缺陷存在于电镀表面处理。
喷涂:如果该列为“X ”,则该缺陷存在于喷涂表面处理。
3.5 面的划分:本标准中产品外观收货检验A 、B 、C 、D 面域划分(可参考下图示): A 面:这是决定产品外观效果最关键的区域,是主要可视面;B 面:是容易看到的可视面;C 面:在安装后的可见区域中,这是不重要的区域。
在安装后C 面不能直接看得到。
通常,你必须大幅度移动头部或产品可动部件才能看得到。
D 面:是不重要的面,在安装之后被覆盖从而看不到。
花洒本体D 面C 面A面A面C 面B 面A 面4.检验方法4.1按物距30cm,目距40cm,入射角45°(在自然光下或40瓦的日光灯下),旋转工件,检查表面是否有装饰性外观缺陷与功能性外观缺陷,各区域检验时间不超过3秒,并根据5.2外观缺陷判定标准来判定允收或拒收。
4.2检查成品的活动手感、配合和做工是否满足要求(如本体与控制圈等配合的松紧程度、零部件之间装配间隙、水流效果等)。
此外请注意:●用肉眼检查,放大镜通常只用来作为对确认缺陷或检查特殊的视觉要求。
表面处理检验规范(含表格)
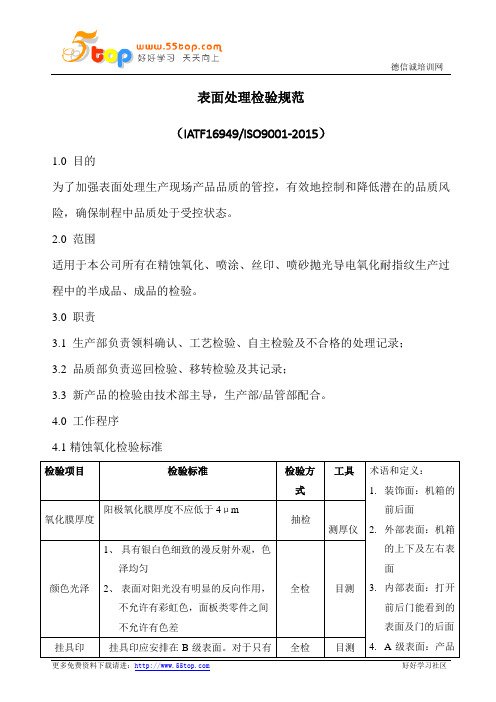
表面处理检验规范(IATF16949/ISO9001-2015)1.0 目的为了加强表面处理生产现场产品品质的管控,有效地控制和降低潜在的品质风险,确保制程中品质处于受控状态。
2.0 范围适用于本公司所有在精蚀氧化、喷涂、丝印、喷砂抛光导电氧化耐指纹生产过程中的半成品、成品的检验。
3.0 职责3.1 生产部负责领料确认、工艺检验、自主检验及不合格的处理记录;3.2 品质部负责巡回检验、移转检验及其记录;3.3 新产品的检验由技术部主导,生产部/品管部配合。
4.0 工作程序4.1精蚀氧化检验标准检验项目检验标准检验方式工具术语和定义:1.装饰面:机箱的前后面2.外部表面:机箱的上下及左右表面3.内部表面:打开前后门能看到的表面及门的后面4.A级表面:产品氧化膜厚度阳极氧化膜厚度不应低于4μm抽检测厚仪颜色光泽1、具有银白色细致的漫反射外观,色泽均匀2、表面对阳光没有明显的反向作用,不允许有彩虹色,面板类零件之间不允许有色差全检目测挂具印挂具印应安排在B级表面。
对于只有全检目测A级表面的零件,其挂具印应位于边角位置,并要求其大小控制在S≤1.0 且P≤2在公司的客户处进行安装、操作及日常维护时能被看到的表面。
装饰面、外部表面,内部表面均属A级表面5.B级表面:除A级表面以外的表面6.外观检验条件:在自然光或光照度在300-600LX的近似自然光下(如40W日光灯,距离500mm处),相距为600-650mm,观测时间为10秒,且检查者位于被检查表面的正面,视线、光线分别与被检查面呈45-90°,要求检查者的校正视力不低于1.2。
7.标准中W表示宽度、S表示面积、L表示长度、水印1、安装板、面板类零件装饰面不允许2、其它结构件外部表面S≤1.0 且P≤23、其它结构件内部表面S≤3.0 且P≤2全检目测划痕1、安装板、面板类零件装饰面不允许2、其它结构件外表面W≤0.3、L≤20、H≤0.1且P≤3 或W≤0.3、L≤40 、H≤0.1且P≤13、其它结构件内部表面W≤0.3、L≤20 且P≤3 或W≤0.3、L≤40且P≤2或L≤80 且P≤1全检目测小凹坑1.外部表面每100*100范围内1处缺陷面积S﹤1.0;内部表面每处缺陷面积S﹤2.5全检目测凸起颗粒1.安装板,面板类零件装饰面每100*100范围内S≤0.3且 P≤12.其它结构件外表面每100*100范围内S≤0.3且 P≤3 或S≤0.5且P≤2 或S≤0.7且P≤1全检目测异物脏污不允许全检目测拉丝1、原则上,不提倡拉丝。
零件表面处理检验规范
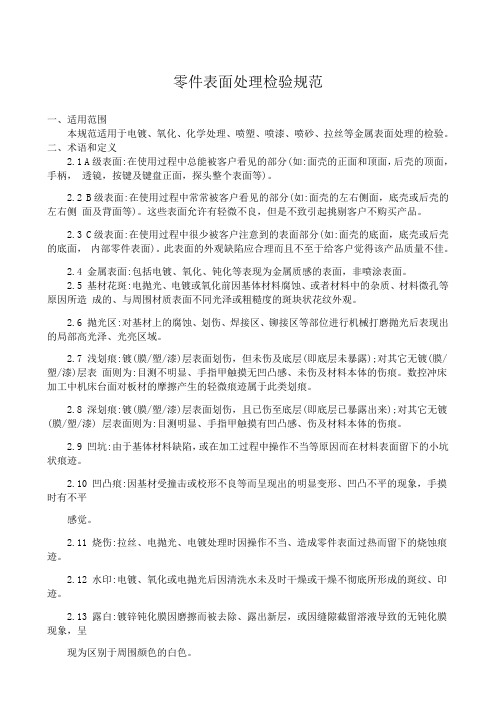
零件表面处理检验规范一、适用范围本规范适用于电镀、氧化、化学处理、喷塑、喷漆、喷砂、拉丝等金属表面处理的检验。
二、术语和定义2.1 A级表面:在使用过程中总能被客户看见的部分(如:面壳的正面和顶面,后壳的顶面,手柄,透镜,按键及键盘正面,探头整个表面等)。
2.2 B级表面:在使用过程中常常被客户看见的部分(如:面壳的左右侧面,底壳或后壳的左右侧面及背面等)。
这些表面允许有轻微不良,但是不致引起挑剔客户不购买产品。
2.3 C级表面:在使用过程中很少被客户注意到的表面部分(如:面壳的底面,底壳或后壳的底面,内部零件表面)。
此表面的外观缺陷应合理而且不至于给客户觉得该产品质量不佳。
2.4 金属表面:包括电镀、氧化、钝化等表现为金属质感的表面,非喷涂表面。
2.5 基材花斑:电抛光、电镀或氧化前因基体材料腐蚀、或者材料中的杂质、材料微孔等原因所造成的、与周围材质表面不同光泽或粗糙度的斑块状花纹外观。
2.6 抛光区:对基材上的腐蚀、划伤、焊接区、铆接区等部位进行机械打磨抛光后表现出的局部高光泽、光亮区域。
2.7 浅划痕:镀(膜/塑/漆)层表面划伤,但未伤及底层(即底层未暴露);对其它无镀(膜/塑/漆)层表面则为:目测不明显、手指甲触摸无凹凸感、未伤及材料本体的伤痕。
数控冲床加工中机床台面对板材的摩擦产生的轻微痕迹属于此类划痕。
2.8 深划痕:镀(膜/塑/漆)层表面划伤,且已伤至底层(即底层已暴露出来);对其它无镀(膜/塑/漆) 层表面则为:目测明显、手指甲触摸有凹凸感、伤及材料本体的伤痕。
2.9 凹坑:由于基体材料缺陷,或在加工过程中操作不当等原因而在材料表面留下的小坑状痕迹。
2.10 凹凸痕:因基材受撞击或校形不良等而呈现出的明显变形、凹凸不平的现象,手摸时有不平感觉。
2.11 烧伤:拉丝、电抛光、电镀处理时因操作不当、造成零件表面过热而留下的烧蚀痕迹。
2.12 水印:电镀、氧化或电抛光后因清洗水未及时干燥或干燥不彻底所形成的斑纹、印迹。
表面处理标准
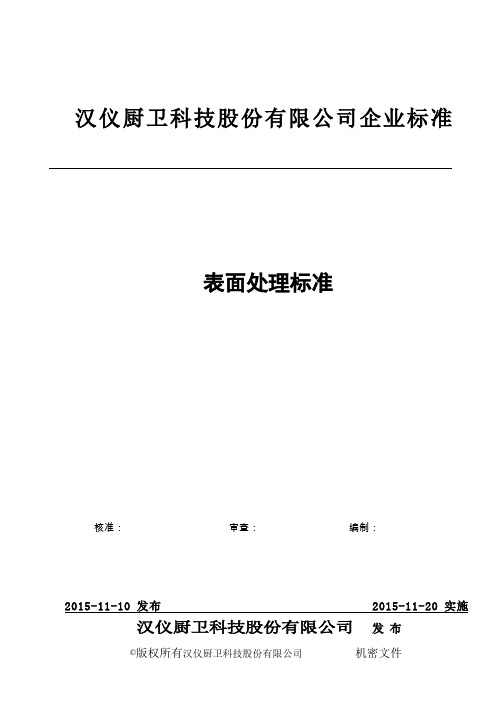
汉仪厨卫科技股份有限公司企业标准表面处理标准核准:审查:编制:2015-11-10发布 2015-11-20实施汉仪厨卫科技股份有限公司发布目次1 范围 (1)2 定义 (1)3 规范性引用文件 (1)4 材料 (1)5表面处理盐雾试验的要求 (1)6 铜合金电镀表面处理标准 (2)7 锌合金∕铝合金电镀表面处理标准 (3)8 塑料电镀表面处理标准 (4)9 不锈钢电镀表面处理标准 (5)10.CASS试验(铜加速盐雾试验)与ASS试验(乙酸盐雾试验)等效对照表 (6)附录A百格试验方法 (7)附录B 漆膜铅笔硬度试验方法 (8)表面处理标准1、范围本标准适用于五金洁具类产品的所有铜合金、锌合金/铝合金、塑料、不锈钢等基材的(Cu+)Ni+Cr 电镀表面处理。
2、定义:无。
3、规范性引用文件下列文件中的条款通过本标准的引用而成为本标准的条款。
凡是不注日期的引用文件,其最新版本适用于本标准。
GB/T 10125 人造气氛腐蚀试验盐雾试验GB/T 6461-2002 金属基体上金属和其他无机覆盖层经腐蚀试验后的试样和试件的评级GB/T 1732 漆膜耐冲击测定法4、材料4.1 用于表面处理的材料必须不应对人体健康和环境产生危害。
5、表面处理盐雾试验的要求5.1 试验方法应符合GB/T 10125和汉仪厨卫科技股份有限公司的要求;判定方法应符合GB/T 6461-2002的要求。
6、铜合金电镀表面处理标准6.6 表面处理验收的标准是以盐雾试验和淬火试验为强制执行要求;镀层厚度试验、剥离试验、耐变色试验及耐磨擦试验为非强制执行要求。
在满足以上强制执行要求检测项目的前提下,铜合金产品可根据实际情况选择镀酸铜。
7、锌合金/铝合金电镀表面处理标准7.6表面处理验收的标准是以盐雾试验和淬火试验为强制执行要求;镀层厚度试验、剥离试验、耐变色试验及耐磨擦试验为非强制执行要求。
在满足其它检测项目的前提下,铝合金的铜镀层为可选择电镀或不电镀。
- 1、下载文档前请自行甄别文档内容的完整性,平台不提供额外的编辑、内容补充、找答案等附加服务。
- 2、"仅部分预览"的文档,不可在线预览部分如存在完整性等问题,可反馈申请退款(可完整预览的文档不适用该条件!)。
- 3、如文档侵犯您的权益,请联系客服反馈,我们会尽快为您处理(人工客服工作时间:9:00-18:30)。
表面处理检验规程1、目的规范检验操作,发现、控制不良品,防止批量不良品输入下道工序。
同时给检验工作提供引导及接收标准。
2、范围适用于进料、外协制品回厂、成品的检验接收及顾客退货的挑选检验。
3、定义本标准适用于变形铝及铝合金以保护和装饰为主要目的,在阳极氧化膜表面涂装有机聚合物膜得到的阳极氧化复合膜。
3.1 A面:指表面处理要求的正面(在使用过程中能直接看到的表面)。
3.2 B 面:指表面处理要求的四侧边(需将表面处理件偏转45~90 °才能看到的四周边)。
3.3 膜厚:必须符合图纸规定。
4、职责4.1 品质部负责不合格的发现、记录和标识,组织处理不合格品。
4.2 生产部负责进料中不合格品与供应商的联络。
5.术语和定义5.1 A级表面:在使用过程中总能被客户看见的部分(如:面壳的正面和顶面,后壳的顶面,手柄,透镜,按键及键盘正面,探头整个表面等)。
5.2 B级表面:在使用过程中常常被客户看见的部分(如:面壳的左右侧面,底壳或后壳的左右侧面及背面等)。
这些表面允许有轻微不良,但是不致引起挑剔客户不购买产品。
5.3 C级表面:在使用过程中很少被客户注意到的表面部分(如:面壳的底面,底壳或后壳的底面,内部零件表面)。
此表面的外观缺陷应合理而且不至于给客户觉得该产品质量不佳。
5.4 金属表面:包括电镀、氧化、钝化等表现为金属质感的表面,非喷涂表面。
5.5 基材花斑:电抛光、电镀或氧化前因基体材料腐蚀、或者材料中的杂质、材料微孔等原因所造成的、与周围材质表面不同光泽或粗糙度的斑块状花纹外观。
5.6 抛光区:对基材上的腐蚀、划伤、焊接区、铆接区等部位进行机械打磨抛光后表现出的局部高光泽、光亮区域。
5.7 浅划痕:镀(膜/塑/漆)层表面划伤,但未伤及底层(即底层未暴露);对其它无镀(膜/塑/漆)层表面则为:目测不明显、手指甲触摸无凹凸感、未伤及材料本体的伤痕。
数控冲床加工中机床台面对板材的摩擦产生的轻微痕迹属于此类划痕。
5.8 深划痕:镀(膜/塑/漆)层表面划伤,且已伤至底层(即底层已暴露出来);对其它无镀(膜/塑/漆) 层表面则为:目测明显、手指甲触摸有凹凸感、伤及材料本体的伤痕。
5.9 凹坑:由于基体材料缺陷,或在加工过程中操作不当等原因而在材料表面留下的小坑状痕迹。
5.10 凹凸痕:因基材受撞击或校形不良等而呈现出的明显变形、凹凸不平的现象,手摸时有不平感觉。
5.11 烧伤:拉丝、电抛光、电镀处理时因操作不当、造成零件表面过热而留下的烧蚀痕迹。
5.12 水印:电镀、氧化或电抛光后因清洗水未及时干燥或干燥不彻底所形成的斑纹、印迹。
5.13 露白:镀锌钝化膜因磨擦而被去除、露出新层,或因缝隙截留溶液导致的无钝化膜现象,呈现为区别于周围颜色的白色。
5.14 修补:因膜层损伤而用涂料所作的局部遮盖。
5.15 色点:由材料、模具、环境或设备中的灰尘或夹杂物等影响,在表面处理层中形成不同色的斑点。
5.16 颗粒:因材料夹杂物或外来物(如焊渣)的影响而在表面形成的、颜色与正常表面一致的凸起现象。
5.17 挂具印:指电镀、电抛光、氧化、喷涂等表面处理生产过程中,因装挂用辅助工具的遮挡而使其与零件相接触的部位产生局部无表面处理层的现象。
5.18 氢脆:由于浸蚀、除油或电镀等过程中金属吸收氢原子和有应力存在下而引起的脆性。
5.19 针孔:表面处理上可看见类似针剌成的微小孔。
5.20 孔隙率:单位面积上针孔的个数。
5.21 起泡:在电镀中由于镀层与底金属之间失去结合力而引起一种凸起状缺陷。
5.22 流痕:喷涂涂料过多且不均匀干燥导致的流痕,或镀层厚度不均造成零件表面的异常区域。
5.23 桔皮:喷涂表面因涂料附着力差而导致起皱,象桔子皮样的外观。
5.24 粉化:氧化膜表面疏松引起的粉沫状物。
5.25 露底:局部无表面处理层的现象。
6.1 SQA/TQC工程师根据此规范监督供应商的金属表面处理制程控制、外观检验和性能检验。
6.2 IQC和机加中心质检员根据此规范进行成品检验。
7.检验方案7.1 一致性和外观:全检项,或由IQC工程师根据实际来料品质状况依据《检验方案调整工作规范》对具体物料检验方案实施调整;7.2 性能:抽检项。
IQC或机加中心质检员每批零件核查供应商检验报告,每季度对每种表面处理至少检验一次。
当外观检验发现存在有可能影响性能的缺陷时,需及时检验该批零件或制作试样进行性能检验。
8.检验项目及方法8.1试片制作要求8.1.1 若测试面积足够,可以实际零件做试样。
8.1.2 当表面处理后的工件大小、形状或材料不适用于试验时,或者当表面处理零件数量太少或价格昂贵而不适合于进行破坏性试验时,可通过制作标准试片进行性能检验。
8.1.3 表面粗糙度:Ra ≤ 1.6µm;8.1.4 表面处理:与被测零件同批次进行相同的表面处理工艺。
8.1.5 试样必须在表面处理24小时以后三天以内进行试验。
8.2 外观检验视力:校正视力1.0以上。
目视距离:检查物距眼睛40cm~60cm。
目视角度:45度~90度(检查时产品应转动)。
目视时间:A级面约15秒/面,B、C面约10秒/面。
灯光:大于500 LX的照明度或正常迈瑞公司车间照明度。
9喷砂拉丝9.1 喷砂和拉丝的目数符合图纸要求,图纸未指明时喷砂按120目的标准,拉丝按220目的标准;9.2拉丝方向按图纸要求,图纸未指明时与零件长边方向一致;9.3 拉丝后整个表面纹路均匀;9.4喷砂后零件表面不得有明显变形,形位公差符合图纸要求。
10 塑层漆层10.1喷塑喷漆的颜色符合图纸要求,以目视检验为主,不得有明显色差;比对标准色板或签样,以一致或极接近为合格;对目视有异议时用色差仪检测,判定标准按MRSZS05N01-311 《产品颜色及色板管理工作规范》。
10.2电泳漆层颜色符合图纸要求,图纸未指明时为黑色。
11电镀锌11.1 镀层结晶均匀、细致;颜色符合图纸要求,图纸未指明时为彩虹色;11.2 允许表面缺陷:由于零件表面状态不同而导致同一零件上有不均匀的颜色或光泽,盲孔、通孔深处可以无镀层。
12 电镀镍12.1 镀层结晶均匀、细致;普通镍镀层呈稍带淡黄色的银白色,光亮镍镀层是光亮的银白色;12.2 允许表面缺陷:由于零件表面状态不同而导致同一零件上有不均匀的颜色或光泽,盲孔、通孔深处无镀层,但需防锈处理。
13化学镀镍13.1镀层结晶均匀、细致;呈稍带浅黄色的银白色或钢灰色;13.2允许表面缺陷:由于零件表面状态不同而导致同一零件上有不均匀的颜色或光泽。
14电镀硬铬14.1镀层结晶均匀、细致;呈略带浅蓝的银白色到亮灰色;14.2允许表面缺陷:由于零件表面状态不同而导致的同一零件上有不均匀的颜色或光泽,盲孔、通孔深处可以无镀层。
15电镀装饰铬15.1镀层结晶均匀、细致;呈镜面般光亮的银白色;15.2允许表面缺陷:盲孔、通孔深处可以无镀层。
16 电镀金16.1镀层结晶均匀、细致;硬金(合金)镀层为略带微红或微棕色的浅黄色;纯金镀层应是有光泽的金黄色;16.2允许表面缺陷:由于零件表面状态不同而导致的同一零件上有不均匀的颜色或光泽;盲孔、通孔深处可以无镀层。
17 电镀银17.1镀层结晶均匀、细致;呈银白色;17.2允许表面缺陷:由于零件表面状态不同而导致的同一零件上有不均匀的颜色或光泽,盲孔、通孔深处可以无镀层。
18铝合金(硬质)阳极氧化18.1 膜层均匀、完整;膜层颜色符合图纸要求,图纸未指明时为本色。
18.2 允许表面缺陷:由于零件表面状态不同而导致的同一零件上有不均匀的颜色或光泽。
19铝合金化学氧化19.1 膜层均匀、完整;膜层颜色符合图纸要求,图纸未指明时化学氧化为无色透明。
19.2 允许表面缺陷:由于零件表面状态不同而导致的同一零件上有不均匀的颜色或光泽。
20 钢铁发蓝(发黑)20.1膜层均匀、完整,碳钢、低合金钢为黑色;合金钢按其化学成分和含量的不同可呈蓝色、紫色至褐色;铸铁、硅钢为带黄色至棕红色的黑色;铸钢呈暗褐色;20.2允许表面缺陷:由于热处理、焊接或表面加工状态不同而有不同的颜色和光泽。
氮化或渗碳处理的表面灰白、浅红或采虹色。
21 不锈钢钝化21.1不锈钢钝化后表面应为接近金属本色、银白、灰白或钢灰色;21.2允许表面缺陷:因材质问题,在同一零件上色泽可稍有不同,可有轻微的水流痕迹;在焊接温度影响区内可有氧化色彩。
22 不锈钢电抛光22.1电抛光表面应光亮、平滑、均匀;22.2允许表面缺陷:零件凹下部位由于抛光不到的发暗。
23 记录见《外协件入厂检验记录》24.再确认过程有如下情况之一时,应随时进行再确认。
1) 操作人员发生变更时2) 机械加工工艺有重大变更时3) 车间生产环境有重大变更时4)机械加工设备报废、更换时5)质量事故批量发生时25. 将检验合格的外协件转入下道工序。
编订:批准:日期:。