丰田管理手册
丰田6S管理手册

目录第一章 6S管理活动的内容31S 整理:----------------------------------------------------------------- 3 2S 整顿:----------------------------------------------------------------- 3 3S 清扫:----------------------------------------------------------------- 3 4S 清洁:----------------------------------------------------------------- 3 5S 安全:----------------------------------------------------------------- 4 6S 素养:----------------------------------------------------------------- 4第二章 6S管理的目的41、改善和提高企业形象------------------------------------------------------ 42、促成效率的提高---------------------------------------------------------- 43、改善零件及物料在库周转率------------------------------------------------ 44、减少甚至消除故障,保障品质---------------------------------------------- 55、保障企业安全生产-------------------------------------------------------- 56、降低生产成本------------------------------------------------------------ 57、改善员工精神面貌,使组织活力化------------------------------------------ 58、缩短作业周期,确保交货期------------------------------------------------ 5第三章 6S管理的作用5一亏损为零——是最佳的推销员--------------------------------------------- 5 二浪费为零——是节约专家------------------------------------------------- 6 三不良为零——是品质零缺陷的护航者-------------------------------------- 6 四投诉为零——标准化的推动者--------------------------------------------- 6 五缺勤率为零——可形成愉快的工作现场------------------------------------- 6 六故障为零——是交货期的保证--------------------------------------------- 7 七切换产品时间为零——高效率的前提--------------------------------------- 7 八事故为零——是安全的软设备--------------------------------------------- 7第四章 6S管理对干部的责任7第五章 6S管理对员工的要求8一整理------------------------------------------------------------------- 8 二整顿------------------------------------------------------------------- 8 三清扫------------------------------------------------------------------- 8 四清洁------------------------------------------------------------------- 9 五素养------------------------------------------------------------------- 9 六安全------------------------------------------------------------------- 9第六章 6S管理要领9一整理------------------------------------------------------------------- 9 二整顿------------------------------------------------------------------ 11 三清扫------------------------------------------------------------------ 11 四清洁------------------------------------------------------------------ 12 五安全------------------------------------------------------------------------------- 12六素养------------------------------------------------------------------ 12第七章 6S要求参照标准13第一节生产现场标准------------------------------------------------------- 13 一划区------------------------------------------------------------------ 13 二标识(另外设计)------------------------------------------------------ 13 三通道------------------------------------------------------------------ 13 四地面------------------------------------------------------------------ 14 五设备------------------------------------------------------------------ 14 六物料放置-------------------------------------------------------------- 14 七记录桌,椅,工柜------------------------------------------------------ 14 八防护用品-------------------------------------------------------------- 15 九卫生工具-------------------------------------------------------------- 15 十墙壁,天花板,门窗---------------------------------------------------- 15 十一配线、配管---------------------------------------------------------- 15 十二危险物品------------------------------------------------------------ 15 十三工艺,质量记录------------------------------------------------------ 15 十四制度执行------------------------------------------------------------ 16 十五工作素养------------------------------------------------------------ 16 第二节办公室标准--------------------------------------------------------- 16一、文件夹---------------------------------------------------------------- 16二、资料柜、文件柜-------------------------------------------------------- 16三、办公桌---------------------------------------------------------------- 17四、电脑管理-------------------------------------------------------------- 17五、电话管理-------------------------------------------------------------- 17 第三节员工礼仪标准------------------------------------------------------- 17一、生活礼仪-------------------------------------------------------------- 17二、日常工作礼仪---------------------------------------------------------- 18三、会客礼仪-------------------------------------------------------------- 19四、电话接听礼仪 --------------------------------------------------------------------- 20附则:226S管理流程--------------------------------------------------------------- 22第一章 6S管理活动的内容1955年,日本企业针对地、物、提出了整理、整顿2个S。
TOYOTAS安全卫生管理手册精选

TOYOTA-5S安全卫生管理手册目录1.XXXX的基本方针:提供顾客100%满意的服务,创建员工100%满意的公司。
2.XXXX企业基础:危机管理体制,人才培养,环境安全以及5S的推行3.5S方针的策略重点:3.1建立使顾客100%满意的质量保证体制3.2改进业务流程、削减在库、遵守交期3.3强化成本竞争力3.4积累与提高生产技术力3.5提高新技术的推广速度3.6构筑企业基础4.5S与环境安全的目标4.1提高生产性4.2提高服务水平和维修产品质量4.3提高速度4.4提高人员素质4.5提高安全性5.5S的定义5.1整理:工作现场,区别要与不要的东西,只保留有用的东西,撤除不需要的东西;5.2整顿:把要用的东西,按规定位置摆放整齐,并做好标识进行管理;5.3清扫:将不需要的东西清除掉,保持工作现场无垃圾,无污秽状态;5.4清洁:维持以上整理、整顿、清扫后的局面,使工作人员觉得整洁卫生;5.5修养:通过进行上述4S的活动,让每个员工都自觉遵守各项规章制度,养成良好的工作习惯,做到“以厂为家、以厂为荣”的地步。
6.5S活动的职责6.1办公室负责组织整个公司的5S及安全卫生的检查6.2各部门负责按5S管理要求对本部门的5S及安全卫生进行检查6.3责任部门负责对5S及安全卫生检查中发现的问题进行改进7.5S活动的要求7.1良好的仪表及礼仪:统一规范的着装要求,良好的坐姿、站姿,电话礼仪,整洁、明亮、大方、舒适的接待环境7.2单一整洁的办公室:台面整洁,文具单一化管理,公用设施责任人标识7.3生产工具管理:单一化管理7.4现场管理:分区划线,员工工作井然有序,工作环境清洁明亮7.5工作速度和效率:最佳的速度和零不良率7.6空间效率:对现场分区划线,对各场地的利用率予于分析,增加有限空间的利用价值7.7严明的小组督导:上班前经理、班组长对员工进行检查督导,工作过程中,对发现的问题及时开展小组督导,下班前对全天的工作进行总结7.8工作评估:自我评估与综合考核评价相结合8.5S对应的措施8.1整理的措施8.1.1清除不用物品的措施a)进行整理,首先要根据情况,分清什么需要,什么不需要。
丰田基层管理者手册
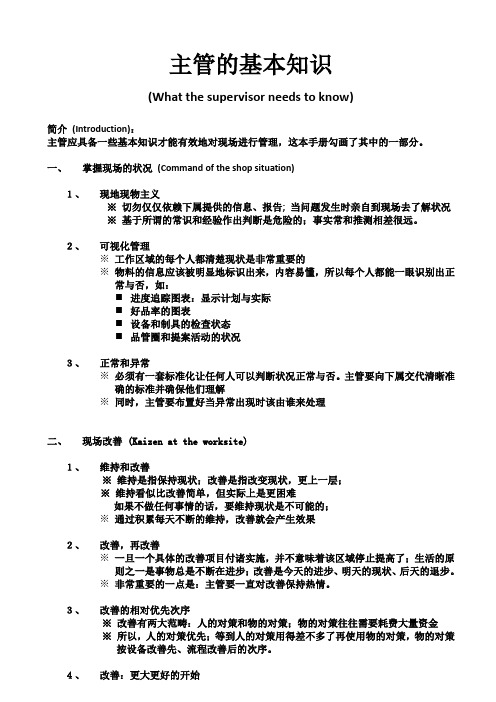
主管的基本知识(What the supervisor needs to know)简介(Introduction):主管应具备一些基本知识才能有效地对现场进行管理,这本手册勾画了其中的一部分。
一、掌握现场的状况(Command of the shop situation)1、现地现物主义※切勿仅仅依赖下属提供的信息、报告; 当问题发生时亲自到现场去了解状况※基于所谓的常识和经验作出判断是危险的;事实常和推测相差很远。
2、可视化管理※工作区域的每个人都清楚现状是非常重要的※物料的信息应该被明显地标识出来,内容易懂,所以每个人都能一眼识别出正常与否,如:⏹进度追踪图表:显示计划与实际⏹好品率的图表⏹设备和制具的检查状态⏹品管圈和提案活动的状况3、正常和异常※必须有一套标准化让任何人可以判断状况正常与否。
主管要向下属交代清晰准确的标准并确保他们理解※同时,主管要布置好当异常出现时该由谁来处理二、现场改善 (Kaizen at the worksite)1、维持和改善※维持是指保持现状;改善是指改变现状,更上一层;※维持看似比改善简单,但实际上是更困难如果不做任何事情的话,要维持现状是不可能的;※通过积累每天不断的维持,改善就会产生效果2、改善,再改善※一旦一个具体的改善项目付诸实施,并不意味着该区域停止提高了;生活的原则之一是事物总是不断在进步;改善是今天的进步、明天的现状、后天的退步。
※非常重要的一点是:主管要一直对改善保持热情。
3、改善的相对优先次序※改善有两大范畴:人的对策和物的对策;物的对策往往需要耗费大量资金※所以,人的对策优先;等到人的对策用得差不多了再使用物的对策,物的对策按设备改善先、流程改善后的次序。
4、改善:更大更好的开始※不要认为改善是很困难的事,采取积极地态度;如果你想到改善是更大更强的开始,改善会成为你的第二本能。
※改善之初困难在于实践,所以总要认真对待下属的改善建议,无论那些建议看起来多么细小,切勿打击下属做出的改善。
【精益学堂】5S管理手册(丰田版)二

【精益学堂】5S管理手册(丰田版)二HLEAN_SYSTEM精益生产宣传和推广,传播精益文化、工具、方法,介绍先进的精益生产体系,帮助企业进一步改善,最大化地减少浪费,降低成本,增加附加价值和利润,从而提升企业竞争力。
整理的措施清除不用物品的措施:•进行整理,首先要根据情况,分清什么需要,什么不需要。
•分清使用频度后,按层次规定放置的位置。
清除不用物品,按下列程序进行:•确定对策范围和目标值;•实施的准备;•区别不用物品的方法教育;•计量化和判断;•管理人员的巡回检查、判断和指导。
大扫除方法大扫除的注意要点:•注意高空作业的安全;•爬上或钻进机器时要注意;•使用洗涤剂或药品时要注意;•使用錾凿工具或未用惯的机器时要注意;•扫除时要注意,不要由于使用洗涤剂而使设备生锈或弄坏设备。
消除问题和损坏地方的方法•总的检查一下有问题的地方,对象是:建筑物、屋脊、窗户、通道天棚、柱子、管路线路、灯泡、开关、三项一套、台、棚架、更衣室、外壳的盖的脱落或破损以及安全支架和扶手的损坏等,要采取措施彻底解决这些问题以及长锈、脱落、杂乱等。
消灭污垢发生的措施消灭污垢产生根源的不力原因:•不了解现状、不认为是问题、问题意识淡薄;•对产生的根源未着手解决,对问题放任不管;•清扫困难或对保持清洁感觉困难而灰心;•解决的技术办法不足或因未动脑筋而缺乏技术。
消灭污垢发生根源的措施程序:•明确什么是污垢;•大扫除;•规定脏的重点部位;•详细调查一下为什么脏了;•研究措施方案;•确定措施方案并付诸实施。
整顿的措施整顿的办法(三原则)规定放置场所•规定办法要遵循一定的规律性,如何保持这种规律性,就是整理、整顿的方法研究,也是个技术问题。
规定放置的方法•所谓好的放置方法,是指查找容易和取拿方便。
遵守保管规则•为了遵守放置场所的规定,必须彻底贯彻从哪儿拿走,还放回哪儿。
此外,为防止缺货,对库存管理和出库方法进行训练也很重要。
这是搞好整理整顿决定性的办法。
【精益学堂】5S管理手册(丰田版)二

【精益学堂】5S管理手册(丰田版)二HLEAN_SYSTEM精益生产宣传和推广,传播精益文化、工具、方法,介绍先进的精益生产体系,帮助企业进一步改善,最大化地减少浪费,降低成本,增加附加价值和利润,从而提升企业竞争力。
8. 5S对应的措施整理的措施清除不用物品的措施:进行整理,首先要根据情况,分清什么需要,什么不需要。
分清使用频度后,按层次规定放置的位置。
清除不用物品,按下列程序进行:确定对策范围和目标值;实施的准备;区别不用物品的方法教育;计量化和判断;管理人员的巡回检查、判断和指导。
大扫除方法大扫除的注意要点:注意高空作业的安全;爬上或钻进机器时要注意;使用洗涤剂或药品时要注意;使用錾凿工具或未用惯的机器时要注意;扫除时要注意,不要由于使用洗涤剂而使设备生锈或弄坏设备。
消除问题和损坏地方的方法总的检查一下有问题的地方,对象是:建筑物、屋脊、窗户、通道天棚、柱子、管路线路、灯泡、开关、三项一套、台、棚架、更衣室、外壳的盖的脱落或破损以及安全支架和扶手的损坏等,要采取措施彻底解决这些问题以及长锈、脱落、杂乱等。
消灭污垢发生的措施消灭污垢产生根源的不力原因:不了解现状、不认为是问题、问题意识淡薄;对产生的根源未着手解决,对问题放任不管;清扫困难或对保持清洁感觉困难而灰心;解决的技术办法不足或因未动脑筋而缺乏技术。
消灭污垢发生根源的措施程序:明确什么是污垢;大扫除;规定脏的重点部位;详细调查一下为什么脏了;研究措施方案;确定措施方案并付诸实施。
整顿的措施整顿的办法(三原则)规定放置场所规定办法要遵循一定的规律性,如何保持这种规律性,就是整理、整顿的方法研究,也是个技术问题。
规定放置的方法所谓好的放置方法,是指查找容易和取拿方便。
遵守保管规则为了遵守放置场所的规定,必须彻底贯彻从哪儿拿走,还放回哪儿。
此外,为防止缺货,对库存管理和出库方法进行训练也很重要。
这是搞好整理整顿决定性的办法。
东西放置场所的规定办法撤掉不用物品减少50%库存量,车间里(岗位上)原则上一种东西只留1个,其他一律清理除去。
丰田公司叉车安全管理手册

丰田公司叉车安全管理手册目录• 1. 简介• 2. 叉车安全操作– 2.1 叉车操作员安全准则– 2.2 叉车日常检查– 2.3 叉车安全装备– 2.4 叉车驾驶技巧• 3. 叉车日常维护– 3.1 保养计划– 3.2 叉车维护指南– 3.3 预防维护• 4. 应急处理– 4.1 紧急情况处理流程– 4.2 叉车事故处理– 4.3 应急演练• 5. 叉车培训与考核– 5.1 叉车培训计划– 5.2 考核评估• 6. 可持续改进– 6.1 叉车安全管理评估– 6.2 安全隐患和问题识别– 6.3 风险管理与改善1. 简介丰田公司一直致力于提供高品质、高安全性的叉车产品。
本安全管理手册旨在为叉车操作员提供必要的安全指导,确保叉车在使用过程中的安全运行。
本手册涵盖了叉车操作的各个方面,包括操作准则、日常维护、应急处理、培训与考核、可持续改进等内容。
2. 叉车安全操作2.1 叉车操作员安全准则叉车操作员是保障叉车安全运行的关键环节,以下是叉车操作员应遵守的安全准则:•遵守相关法规和公司规章制度。
•具备充分的叉车操作知识和技能。
•仅在有足够可视性的情况下行驶。
•注重巡视,注意周围环境和人员。
•使用叉车时应佩戴安全帽和其他个人防护装备。
•禁止携带其他乘员或物品超过叉车额定负载能力。
2.2 叉车日常检查叉车操作前需要进行一系列的检查,以确保叉车的安全运行:•检查液压、燃料、润滑油等液体是否足够。
•检查刹车系统、转向系统和传动系统是否正常运行。
•检查电池是否充满电。
•检查轮胎是否完好、气压是否正常。
•检查灯光和信号装置是否正常。
2.3 叉车安全装备叉车的安全装备是确保操作员安全的重要保障:•安全帽:保护操作员头部安全。
•叉车安全带:固定操作员身体,防止受伤。
•叉车灭火器:应急情况下灭火,防止火灾扩大。
•护目镜和耳塞:保护操作员眼睛和听力。
2.4 叉车驾驶技巧叉车的安全驾驶技巧对操作员来说至关重要:•缓慢行驶,避免突然加速和刹车。
丰田汽车公司5S管理手册
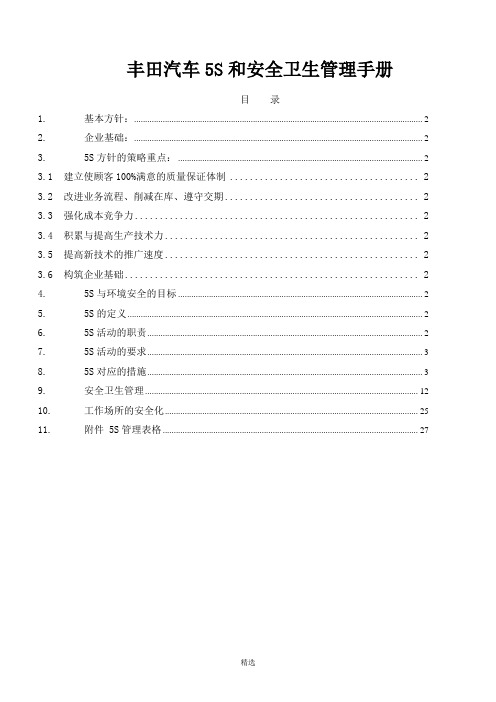
丰田汽车5S和安全卫生管理手册目录1.基本方针: (2)2.企业基础: (2)3.5S方针的策略重点: (2)3.1 建立使顾客100%满意的质量保证体制 (2)3.2 改进业务流程、削减在库、遵守交期 (2)3.3 强化成本竞争力 (2)3.4 积累与提高生产技术力 (2)3.5 提高新技术的推广速度 (2)3.6 构筑企业基础 (2)4.5S与环境安全的目标 (2)5.5S的定义 (2)6.5S活动的职责 (2)7.5S活动的要求 (3)8.5S对应的措施 (3)9.安全卫生管理 (12)10.工作场所的安全化 (25)11.附件 5S管理表格 (27)1.基本方针:提供顾客100%满意的服务,创建员工100%满意的公司。
2.企业基础:危机管理体制,人才培养,环境安全以及5S的推行3.5S方针的策略重点:3.1建立使顾客100%满意的质量保证体制3.2改进业务流程、削减在库、遵守交期3.3强化成本竞争力3.4积累与提高生产技术力3.5提高新技术的推广速度3.6构筑企业基础4.5S与环境安全的目标4.1提高生产性4.2提高服务水平和维修产品质量4.3提高速度4.4提高人员素质4.5提高安全性5.5S的定义5.1整理:工作现场,区别要与不要的东西,只保留有用的东西,撤除不需要的东西;5.2整顿:把要用的东西,按规定位置摆放整齐,并做好标识进行管理;5.3清扫:将不需要的东西清除掉,保持工作现场无垃圾,无污秽状态;5.4清洁:维持以上整理、整顿、清扫后的局面,使工作人员觉得整洁卫生;5.5修养:通过进行上述4S的活动,让每个员工都自觉遵守各项规章制度,养成良好的工作习惯,做到“以厂为家、以厂为荣”的地步。
6.5S活动的职责6.1办公室负责组织整个公司的5S及安全卫生的检查6.2各部门负责按5S管理要求对本部门的5S及安全卫生进行检查6.3责任部门负责对5S及安全卫生检查中发现的问题进行改进7.5S活动的要求7.1良好的仪表及礼仪:统一规范的着装要求,良好的坐姿、站姿,电话礼仪,整洁、明亮、大方、舒适的接待环境7.2单一整洁的办公室:台面整洁,文具单一化管理,公用设施责任人标识7.3生产工具管理:单一化管理7.4现场管理:分区划线,员工工作井然有序,工作环境清洁明亮7.5工作速度和效率:最佳的速度和零不良率7.6空间效率:对现场分区划线,对各场地的利用率予于分析,增加有限空间的利用价值7.7严明的小组督导:上班前经理、班组长对员工进行检查督导,工作过程中,对发现的问题及时开展小组督导,下班前对全天的工作进行总结7.8工作评估:自我评估与综合考核评价相结合8.5S对应的措施8.1整理的措施8.1.1清除不用物品的措施a)进行整理,首先要根据情况,分清什么需要,什么不需要。
丰田6S管理手册
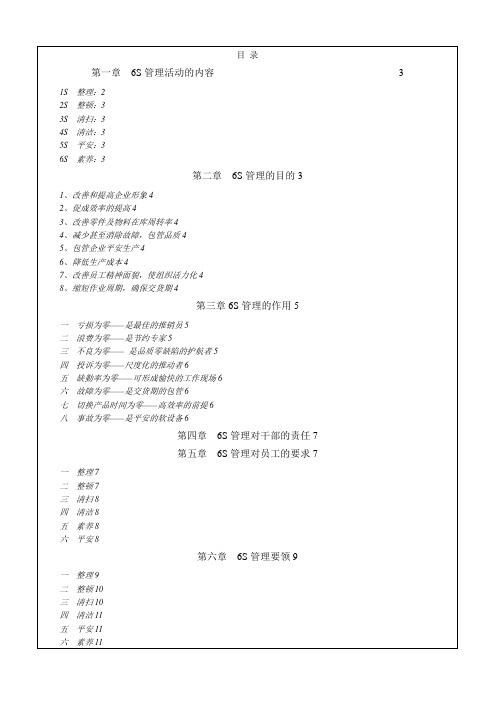
优良的品质来自于优良的工作环境。通过经常性的清扫,点检,不竭净化工作环境,防止污物损坏机器, 维持设备的高效率运转,提高产品品质。
5、包管中心平安生产:
储存明确,物归原位,工作场合宽敞明亮,通道疏通,地上不会随意摆放不该放置的物品。如果工作场 合有条不紊,意外的发生也会减少,当然平安就会有包管。
6S 素养:
训练员工追求良好的工厂整洁,有自律精神,要求员工严守作业规则,坚持良好的工作习惯,职工自觉 动手,创造一个整齐,清洁,方便的工作现场。 目的:遵章守纪,严格要求自己,加强个人修养从而提升公司的形象和知名度。 开始 6S 活动的意义在于创造一个文明良好的工作环境,是工作环境人性化,工厂合理化,实现平安生 产,高生产率和零浪费。
二、整顿:
1.设备、机器仪器等摆放整齐,干净,调养好,均处于最佳运行状态; 2.工具均为可用工具,有调养,有定位放置,且各工具均一目了然; 3.零件保管有定位; 4.文件档案明确定位,均有目录,易检索,有次序且整齐,任何人均可随时使用; 5.陈述,日报表即日上交,且数据准确; 6.分拣作业场合按分歧的工作流程和类别进行明确区分且标识清楚。
六、故障为零——是交货期的包管:
1.车间无尘化; 2.无碎屑,碎块和漏油,漏水,经常擦拭的调养,机器稼动力高; 3.设备产能,人员效率稳定,综合效益可掌控性高; 4.每周进行点检,防范于未然。
七、切换产品时间为零——高效率的前提:
1.整洁规范的工厂机器正常运转,作业效率大幅上升; 2.完全的 6S 让初学者或新人一看就能立即上岗作业。
第四章 6S 管理对干部的责任
一、结合公司的行动目标; 二、负责本部分的 6S 宣传,教育; 三、对部分内的工作区域进行划分; 四、监督本部分物料摆放; 五、帮忙手下解决活动中的困难点; 六、分析和改善活动中的问题; 七、督促手下的清扫点检工作; 八、检查员工服装仪容,行为规范; 九、上班之后点名与服装仪容清查,下班之前平安检查与巡视。 十、作好各种平安监督记录。
丰田汽车公司5S管制手册1.doc

丰田汽车公司5S管理手册1 广汽丰田汽车有限公司和安全卫生管理手册5S丰田汽车录目基本方针:1....................................................................................................... ........... ................. 2 .企业基础:2....................................................................................................... ........... ................. 2 .方针的策略重点:5S3....................................................................................................... .........22 ...................................... 满意的质量保证体制100%建立使顾客3.12 ....................................... 改进业务流程、削减在库、遵守交期3.22 ......................................................... 强化成本竞争力3.32 ................................................... 积累与提高生产技术力3.42 ................................................... 提高新技术的推广速度3.53.6 2 ........................................................... 构筑企业基础与环境安全的目标5S4....................................................................................................... .........2的定义5S5....................................................................................................... .. (2)活动的职责5S6....................................................................................................... ........... ........... 3 .活动的要求5S7............................................................................................................................. 3 .对应的措施5S8....................................................................................................... ........... ........... 3 .安全卫生管理9....................................................................................................... ........... .. (13)工作场所的安全化10....................................................................................................... ........... .. 25管理表格5S附件11....................................................................................................... ......... .. (27)广汽丰田汽车有限公司1.基本方针:满意的公司。
丰田6S管理手册之欧阳语创编

2.无缺陷,无不良,好的声誉在客户之间口碑相传,忠实的客户越来越多;
3.顾客满意的部门,增强下单信心;
4.很多人来参观学习,提升公司的知名度;
5.大家愿意来公司工作,以公司为荣;
6.清洁明朗的工作环境,能留住优秀员工;
7.整理,整顿,清扫,清洁,安全和修养维持良好,并且成为习惯,以整洁为基础的工厂有更大的发展空间。
九、上班之后点名与服装仪容清查,下班之前安全检查与巡视。
十、作好各种安全监督记录。
1.每月确定二至三天作为整理日;
2.通道状况整洁畅通;
3.工作场所的设备材料均为日内需用物品,且整理好,其余物品置于储藏室,不再使用的物品或已废弃物品按废弃处理;
4.工具箱内工具为近日需用,且整齐;
5.办公桌上下及抽屉内物品均为工作必须的物品,且干净整齐;
1.遵守操作规程,不会发生工伤事故;
2.产品按标准要求生产,降低产品的不合格率;
3.环境整洁有序,异赏一眼就可以看得见;
4.干净整洁的生产现场,可以提高员工品质意识;
5.员工知道预防问题而非仅是处理问题;
6.强调危险预知训练,增强安全意识。
1.人们能正确地执行各项规章制度;
2.去任何岗位都能立即上岗作业;
5.在有活力的一流工作场所,员工都由衷感到自豪和骄傲;
6.工作环境清爽舒适,员工有被尊重的感觉;
7.员工凝聚力增强,工作更愉快。
1.车间无尘化;
2.无碎屑,碎块和漏油,漏水,经常擦拭的保养,机器稼动力高;
3.设备产能,人员效率稳定,综合效益可把握性高;
4.每周进行点检,防范于未然。
1.整洁规范的工厂机器正常运转,作业效率大幅上升;
【精益学堂】5S管理手册(丰田版)二
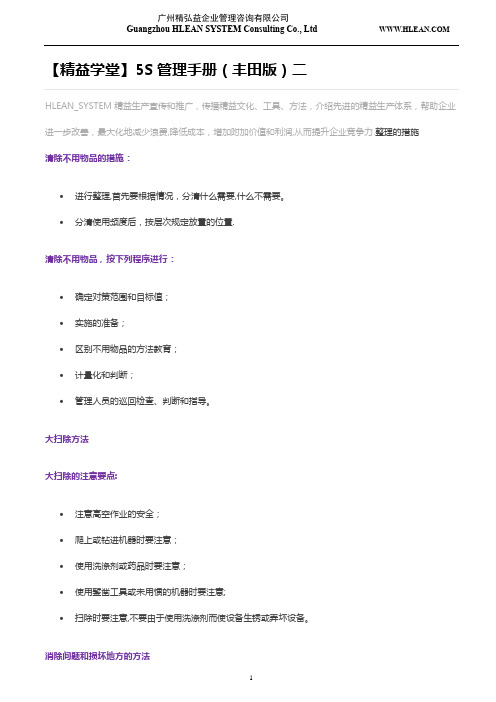
整顿的办法(三原则)
规定放置场所
规定办法要遵循一定的规律性,如何保持这种规律性,就是整理、整顿的方法研究,也是个技术问题。
规定放置的方法
所谓好的放置方法,是指查找容易和取拿方便。
遵守保管规则
为了遵守放置场所的规定,必须彻底贯彻从哪儿拿走,还放回哪儿。此外,为防止缺货,对库存管理和出库方法进行训练也很重要。这是搞好整理整顿决定性的办法。
限制东西摆放的高度也很重要,它有助于防止掉下来、倒下来或库存过多。
台座座阁板、台车等
减少台座和阁板的使用数量。东西放在台座和阁板上。不用的撤掉或收拾起来.
台座和阁板高矮不一样时,下面需要适当垫一下、摆成几层高度.
台座或阁板不直接放在地上,用东西垫起来.
尽量少用吊车和叉车而使用台车效率高。
管线的整理、整顿
功能部位任何时候都保持光洁,而使人自豪。
做的过程重要
标准或核对确认表的确定和填写过程很重要。不是上级分配了才去做,而是作业人员实际参加设备的检查过程去确定和填写.
在现场通过实物进行指导
对现场目视管理的重点的如何,监督者要到现场,通过实物和现象进行指导.
为什么对那个地方总得经常清扫检查呢?对该部位的功能、结构、原理学懂了吗?
清扫、检查是容易做到?
目视、大小、好坏的判断难易程度如何?
此外,再不能想办法找到更容易做到的目视方法吗?
从内部向外部集中可能吗?
对功能部位要明确标志,使谁一看都能知道.
状态的定量化:表示管理界限和明确异常现象。
教育(教养)的措施
教育是指改变人们的习惯要养成良好的习惯:
为取得良好的结果,需要明确规定行动的准则。
正确的传达和良好的培训,准确地传授.
3S店服务部管理手册丰田as

3S店服务部管理手册丰田as目录一、岗位责任及权限1-6服务部经理1服务部副经理1技术主管1-2车间主管2客户服务员2保修鉴定员2-3信息治理员3质量检验员3培训讲师3工具资料治理员3-4油漆技师4机修技师4电工技师4钣金修理技师4备件经理5仓库治理员5备件销售员5备件打算员5-6保险主管6保险业务员6保险文秘6二、接车、交车、售后服务流程7-(一)、接车工作流程71、车辆进店接车员(服务顾咨询)操作流程描述8(二)、紧急对应工作流程9(三)、交车修理质量操纵工作流程10(四)、提醒服务工作流程11(五)、修后跟踪流程12三、零部件出入库操作流程13(一)设备保养和修理制度13-14(二)车间工具、设备治理规定14-15(三)车间材料请购、采买流程16服务部管理手册岗位责任及权限:服务部经理服务部副经理技术主管车间主管客户服务员保修鉴定员信息治理员质量检验员培训讲师工具资料治理员油漆技师机修技师电工技师钣金修理技师备件经理仓库治理员备件销售员备件打算员保险主管保险业务员保险文秘二、接车、交车、售后服务流程1、车辆进店接车员(服务顾咨询)操作流程描述 ★ 日常行为规则:按时上班,清洁工作区域,保持设备整洁。
清点仪器、设备、工具数量,并保证仪器、设备、工具工作状态良好。
协助技师完成工作区域的检查工作。
★ 车辆进店初检流程:车辆进店,第一向客户咨询好,如:“您好!请咨询需要什么关心?”等有关礼貌用语;向客户索取车钥匙,倾听、确认客户的陈述和要求,并向客户讲明有关收费情形;在“接车服务单”上记录好客户及车辆的信息资料,以左前方车头走到车辆左前方,检查左前漆面;打开左前门,检查车门合页是否有异响,门饰板、门提、拉手损害情给方向盘、正副驾驶座套上防护套;坐入车内,检查车内是否有客户的遗留物品,作好记录;降下左前车窗,检查玻璃完好及升降情形(如果是电动车窗,能够检查四个车窗的升降器工作情形,否则需按顺序依次检查升降情形);打开钥匙门(不着车),检查外表显示、音响、雨刷器摆动及回复位置、(天线)工作情形以及车内装置完好情形;下车,检查左前轮胎胎面质量及胎压;检查左雨刷片;转到车前,检查机器盖漆面、前风挡、前灯罩总成完好情形;掀开机器盖,检查机油、刹车油、玻璃水、冷却液、转向助力液、电转到右前方,检查右前漆面;B/左前C/车内E/车前 D/左前F/右前A/咨询打开右前门,检查车门合页是否有异响,门饰板、门提、拉手损害情形;如是手摇车窗,检查右前玻璃完好及升降情形;检查右前胎轮胎胎面质量及胎压;检查右雨刷片;走到右后方,检查右后漆面;打开右后门,检查车门合页是否有异响,门饰板、门提、拉手损害情形;如是手摇车窗,检查右后玻璃完好及升降情形;检查右后胎轮胎胎面质量及胎压;转到车后部,检查后备箱、后部漆面、后风挡、后灯罩总成完好情形;打开后备箱,检查备胎胎面质量及胎压;检查备用工具如:千斤顶、扳手等完整情形;转到左后侧,检查左后漆面;打开左后门,检查车门合页是否有异响,门饰板、门提、拉手损害情形;如是手摇车窗,检查左后玻璃完好及升降情形;检查左后胎轮胎胎面质量及胎压;在机油无亏损的情形下,着车检查空调、各种灯光工作情形(在机油未达到机油尺最低限度的情形下禁止着车,并应向客户做出讲明);由接车员将车辆开至复检工位,并将“接车服务单”交至车间主任处,由车间主任派工复检。
丰田应商管理手册
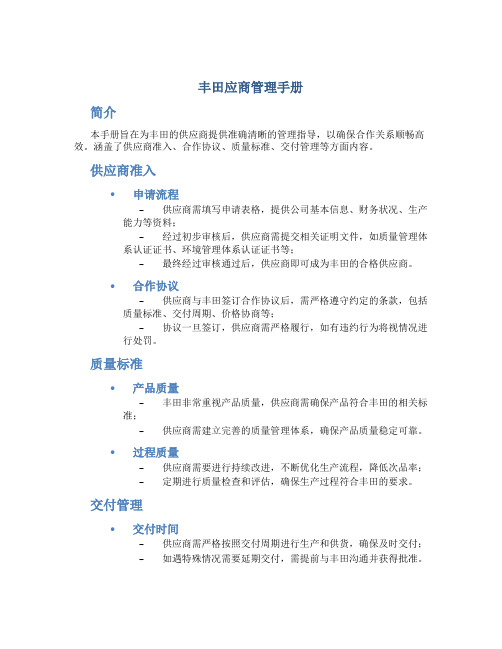
丰田应商管理手册
简介
本手册旨在为丰田的供应商提供准确清晰的管理指导,以确保合作关系顺畅高效。
涵盖了供应商准入、合作协议、质量标准、交付管理等方面内容。
供应商准入
•申请流程
–供应商需填写申请表格,提供公司基本信息、财务状况、生产能力等资料;
–经过初步审核后,供应商需提交相关证明文件,如质量管理体系认证证书、环境管理体系认证证书等;
–最终经过审核通过后,供应商即可成为丰田的合格供应商。
•合作协议
–供应商与丰田签订合作协议后,需严格遵守约定的条款,包括质量标准、交付周期、价格协商等;
–协议一旦签订,供应商需严格履行,如有违约行为将视情况进行处罚。
质量标准
•产品质量
–丰田非常重视产品质量,供应商需确保产品符合丰田的相关标准;
–供应商需建立完善的质量管理体系,确保产品质量稳定可靠。
•过程质量
–供应商需要进行持续改进,不断优化生产流程,降低次品率;
–定期进行质量检查和评估,确保生产过程符合丰田的要求。
交付管理
•交付时间
–供应商需严格按照交付周期进行生产和供货,确保及时交付;
–如遇特殊情况需要延期交付,需提前与丰田沟通并获得批准。
•运输方式
–供应商需选择合适的运输方式,确保产品安全送达目的地;
–需对货物进行适当的包装,以防运输过程中发生损坏。
结语
本手册对丰田的供应商管理提供了详细指导,希望供应商能够认真遵守相关规定,与丰田建立互信合作的关系,共同发展壮大。
丰田5S管理制度
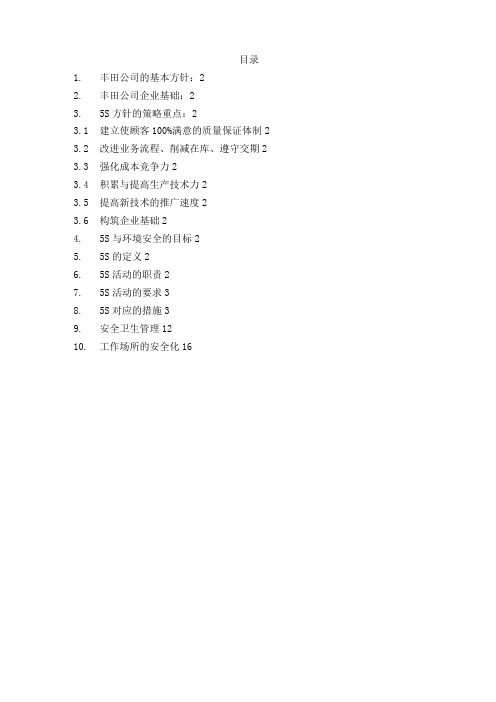
目录1.丰田公司的基本方针:22.丰田公司企业基础:23.5S方针的策略重点:23.1建立使顾客100%满意的质量保证体制2 3.2改进业务流程、削减在库、遵守交期2 3.3强化成本竞争力23.4积累与提高生产技术力23.5提高新技术的推广速度23.6构筑企业基础24.5S与环境安全的目标25.5S的定义26.5S活动的职责27.5S活动的要求38.5S对应的措施39.安全卫生管理1210.工作场所的安全化161.丰田公司的基本方针:提供顾客100%满意的服务,创建员工100%满意的公司。
2.丰田公司企业基础:危机管理体制,人才培养,环境安全以及5S的推行3.5S方针的策略重点:3.1建立使顾客100%满意的质量保证体制3.2改进业务流程、削减在库、遵守交期3.3强化成本竞争力3.4积累与提高生产技术力3.5提高新技术的推广速度3.6构筑企业基础4.5S与环境安全的目标4.1提高生产性4.2提高服务水平和维修产品质量4.3提高速度4.4提高人员素质4.5提高安全性5.5S的定义5.1整理:工作现场,区别要与不要的东西,只保留有用的东西,撤除不需要的东西;5.2整顿:把要用的东西,按规定位置摆放整齐,并做好标识进行管理;5.3清扫:将不需要的东西清除掉,保持工作现场无垃圾,无污秽状态;5.4清洁:维持以上整理、整顿、清扫后的局面,使工作人员觉得整洁卫生;5.5修养:通过进行上述4S的活动,让每个员工都自觉遵守各项规章制度,养成良好的工作习惯,做到“以厂为家、以厂为荣”的地步。
6.5S活动的职责6.1办公室负责组织整个公司的5S及安全卫生的检查6.2各部门负责按5S管理要求对本部门的5S及安全卫生进行检查6.3责任部门负责对5S及安全卫生检查中发现的问题进行改进5S 活动的要求良好的仪表及礼仪:统一规范的着装要求,良好的坐姿、站姿,电话礼仪,整洁、明亮、大方、舒适的接待环境单一整洁的办公室:台面整洁,文具单一化管理,公用设施责任人标识生产工具管理:单一化管理现场管理:分区划线,员工工作井然有序,工作环境清洁明亮工作速度和效率:最佳的速度和零不良率空间效率:对现场分区划线,对各场地的利用率予于分析,增加有限空间的利用价值严明的小组督导:上班前经理、班组长对员工进行检查督导,工作过程中,对发现的问题及时开展小组督导,下班前对全天的工作进行总结工作评估:自我评估与综合考核评价相结合5S 对应的措施整理的措施1清除不用物品的措施 a)进行整理,首先要根据情况,分清什么需要,什么不需要。
- 1、下载文档前请自行甄别文档内容的完整性,平台不提供额外的编辑、内容补充、找答案等附加服务。
- 2、"仅部分预览"的文档,不可在线预览部分如存在完整性等问题,可反馈申请退款(可完整预览的文档不适用该条件!)。
- 3、如文档侵犯您的权益,请联系客服反馈,我们会尽快为您处理(人工客服工作时间:9:00-18:30)。
储存明确,物归原位,工作场所宽敞明亮,通道畅通,地上不会随意摆放不该放置的物品。如果工作场所有条不紊,意外的发生也会减少,当然安全就会有保障。
通过实施6S可以减少人员,设备,场所,时间等等的浪费,从而降低生产成本。
整齐,清洁的工作环境,创造良好的物流工作现场,提高现场的工作效率和质量,提升员工的工作热情,塑造良好的企业形象;同时,由于口碑相传,会成为其他公司的学习对象。
良好的工作环境和工作气氛,有修养的工作伙伴,物品摆放有序,不用寻找,员工可以集中精神工作,工作兴趣高,效率自然会提高。
整洁的工作环境,有效的保管和布局,能够做到必要时能立即取出所需的物品。工序间物流通畅,能够减少甚至消除寻找,滞留时间,改善在库周转率。
1.建立清扫责任区(室内外):
(1)利用中心平面图,标识各责任区及负责人;
(2)各责任区应细化成各自的定置图。
2.执行例行扫除,清理脏污:
(1)规定例行扫除的内容,每周的清扫时间和内容;
(2)清扫过程中发现不良之处,应加以改善;
(3)清扫应细心,具备不容许污秽存在的观念;
(4)清扫用品本身保持清洁有归位。
3.调查污染源,予以杜绝:
(1)脏污是一切异常与不良的根源。如:电路板上的脏污,是短、断路的主要原因。设备上的金属粉末及铁锈,将会影响到产品的整洁度,影响到产品的质量;
(2)调查脏污的源头,对污染的形态,对象予以明确化,并调查其发生部位,发生量,影响程度,最后进行研究,采取对策;
(3)检讨脏污的对策:一是针对源流部分进行管理,杜绝脏污产生。二是在无法杜绝污染发生时应在污染产生后进行有效的收集,清理。
5.报告,日报表即日上交,且数据准确;
6.分拣作业场所按不同的工作流程和类别进行明确区分且标识清楚。
1.通道及作业场所必须随时清扫,干净整齐;
2.工柜或记录桌面,桌柜,椅子及四周均干净亮丽;
3.窗,墙,做到干净整洁,很是舒爽;
4.设备,工具,仪器需保持干净,使用中防止不干净措施,并随时清理。
1.通道和作业区划线清楚,地面有清扫,感觉舒畅;
1.遵守操作规程,不会发生工伤事故;
2.产品按标准要求生产,降低产品的不合格率;
3.环境整洁有序,异赏一眼就可以看得见;
4.干净整洁的生产现场,可以提高员工品质意识;
5.员工知道预防问题而非仅是处理问题;
6.强调危险预知训练,增强安全意识。
1.人们能正确地执行各项规章制度;
2.去任何岗位都能立即上岗作业;
1.至少在行业内被称赞为最干净,整洁的工厂;
2.无缺陷,无不良,好的声誉在客户之间口碑相传,忠实的客户越来越多;
3.顾客满意的部门,增强下单信心;
4.很多人来参观学习,提升公司的知名度;
5.大家愿意来公司工作,以公司为荣;
6.清洁明朗的工作环境,能留住优秀员工;
7.整理,整顿,清扫,清洁,安全和修养维持良好,并且成为习惯,以整洁为基础的工厂有更大的发展空间。
对于放置处与被放置物,都要想办法使其能立即取出使用。另外,使用后要能容易恢复到原位,误放时能马上知道。
1.要落实前一步骤整理工作:
(1)整理工作没落实则不仅空间浪费,而且零件或产品会因变旧不能使用而造成浪费;
(2)不要的东西也要管布置流程,确定放置场所:
4.建立清扫基准,作为规范:
建立清扫基准:清扫对象,清扫方法,重点,要求标准,周期,时机,使用的清扫工具,使用时间,负责人。
1.落实前3S工作,并充分利用文宣活动,维持新鲜的活动气象。
2.制定目视管理,颜色管理的基准:
(1)借整顿标示彻底塑造一个地、物明朗化的现场,从而达到目视管理的要求;
(2)目视管理的方法:利用管理标签标出设备的管理级数、精度、保养周期等。
6.仓库有定位且在管理状态,任何人均易了解,退还也简单方便;
7.在库货物用明显标志区分,不得互相混合;
8.生活用品摆放整齐,且不影响正常分拣作业。
1.设备、机器仪器等摆放整齐,干净,保养好,均处于最佳运行状态;
2.工具均为可用工具,有保养,有定位放置,且各工具均一目了然;
3.零件保管有定位;
4.文件档案明确定位,均有目录,易检索,有次序且整齐,任何人均可随时使用;
3.仪表整洁,精神饱满,感觉有活力;
4.讲究卫生,不随地吐痰,不乱仍垃圾;
5.时间观念强,约定的时间尽量提前做好;
6.待人礼貌热情,常用礼貌用语;
7.尊重年长同事,服从上司领导。
1.所在的工作场所全面检查,包括看得到的和看不到的:
(1)地面上的搬运工具、产品、原料、设备、杂物等;
(2)工作台(操作台)上的工具、生产用护具、个人物品等;
3.清除不需要物品:需要使用“红牌作战”的技巧,处理那些不要的物品。
(1)红牌作战的对象为机器,设备,库存物品,材料,作业工具,用品;
(2)红牌张贴基准:物品不明者,物品变质者,物品过期者;
(3)不要物的集中处理及清除。
4.调查需要物品的使用频度,决定日常用量:
使 用 次 数
判 断 基 准
一年未用过一次的物品
(3)办公区域内抽屉和橱柜里的文档、桌上的办公用品、公告板等;
(4)墙上的指示牌、挂架、风扇、配线、管道等;
(5)室外的废弃物品、不用的材料等。
2.制定“需要”和“不需要”的判别基准:
(1)工作场所全面检查后,所有的物品一一判别,哪些是“要”的,哪些是“不要”的;
(2)制定“要”和“不要”的基准表,并经开会决定基准,同时要反省不要物产生的根源。
(1)参照管理中“依使用频率判断之基准”,决定放置场所;
(2)流程布置基本上遵循的原则是:综合原则,最短距离原则,流程化原则,安全与满足感原则以及弹性化原则;
(3)物品的保管要定位、定时,要恰当确定放置场所的最适空间地域范围;
(4)分拣线附近只能放真正需要使用的物品;
(5)无法规定位置放置的物品,应挂“暂放”标识牌,注明原因,放置时间,负责人,预计放至何时等。
提高生产效率,降低生产成本。节省消耗品,工具,材料成本,降低产品不良率,节省工程变换时间及作业时间,产品交期有保证。
1.避免库房,货架过剩;
2.避免托盘,地牛车,叉车等搬运工具过剩;
3.避免机器,设备闲置;
4.避免“寻找,等待,避让”等动作引起的浪费;
5.消除“拿起,放下,清点,搬运”等无附加值动作。
2.地面随时清扫,无污物,干净亮丽;
3.桌柜及四周环境必须随时清理,令人感觉舒服;
4.洗手间应经常清理,无异味,干净清爽;
5.储存室物品应摆放整齐。
1.认真学习领会安全知识;
2.遵守各种作业规程;
3.随时检查工作过程中存在的各种安全隐患并及时排出。
1.日常6S活动均积极参加,活动热烈;
2.工作服,干净整洁;
任何时候都要维持高水准的工厂整洁,其要点是不搞突击,贵在坚持和保持,清洁就是美观,让人舒服。
目的:防止产品的污染和浪费,能留住优秀的员工。
即遵守作业指导书和操作规程,其要点是不违章操作。
目的:稳定产品品质,提高生产量,排出各种危险事故,降低公司的风险。
训练员工追求良好的工厂整洁,有自律精神,要求员工严守作业规则,保持良好的工作习惯,职工自觉动手,创造一个整齐,清洁,方便的工作现场。
1955年,日本企业针对地、物、提出了整理、整顿2个S。后来因管理的需求及水准的提升,才陆续增加了其余的4个S。从而形成了广泛推行的6S架构,也使其重点由环境品质扩及到人的行为品质,在安全、卫生、效率、品质及成本方面得到较大的改善。
6S活动的内容:包括对现场的整理、整顿、清扫、清洁、安全和素养。由于他们日文罗马拼音的字头均为S,故称6S。
目的:遵章守纪,严格要求自己,加强个人修养从而提升公司的形象和知名度。
开始6S活动的意义在于创造一个文明良好的工作环境,是工作环境人性化,工厂合理化,实现安全生产,高生产率和零浪费。
实施6S活动可以改善产品品质,提高生产能力,降低生产成本,确保准时交货,确保安全生产及保持员工高昂的士气。概括来讲,推行6S最终要达到的目的有八点:
2.彻底的6S让初学者或新人一看就能立即上岗作业。
1.整理,整顿之后通道等休息场所不会被占用;
2.物品放置,搬运方法和积载高度等考虑了安全因素;
3.工作场所明亮,宽敞使物流一目了然;
4.通路畅通;
5.货物摆放位置标示明确;
6.员工正确地执行各项规章制度,不会违规操作;
7.所有的设备都进行清洁,检修,能预先发现存在的问题,从而及时消除隐患;
8.消防设施齐备,灭火器放置位置,逃生路线明确,万一发生火灾或地震时员工生命安全有保障。
一、结合公司的行动目标;
二、负责本部门的6S宣传,教育;
三、对部门内的工作区域进行划分;
四、监督本部门物料摆放;
五、帮助部属解决活动中的困难点;
六、分析和改善活动中的问题;
七、督促部属的清扫点检工作;
八、检查员工服装仪容,行为规范;
人人都变成有修养的员工,有尊严和成就感,对自己的工作尽心尽力,并带动改善意识(可以实施合理化提案改善活动),增加组织的活力。
由于实施了“一目了然”的管理,使异常现象明显化,减少人员,设备,时间的浪费,生产顺畅,提高了作业效率,缩短了作业周期,从而确保交货期。
归结起来6S有八个作用:亏损为零,不良为零,浪费为零,故障为零,切换产品时间为零,事故为零,投诉为零,缺勤为零。
3.谁都明白工作该怎样做,怎样做才算做好了;
4.工作方便又舒适;
5.品质稳定,如期达成生产目标。
1.一目了然的工作场所,没有浪费,免强,不均衡等蔽端;
2.岗位明亮,干净,无灰尘无垃圾的工作场所让人工作愉快,不会让人厌倦和疲劳;