聚氨酯配方
聚氨酯软泡配方

聚氨酯软泡的配方因所需硬度、密度和弹性等特性而异,以下提供了三种不同配方的聚氨酯软泡:
1、密度为8kg/立方米的软泡配方:
聚醚:100份
水:7份
硅油:2.8份
辛酸亚锡:0.7份
胺催化剂:0.17份
二氯甲烷:30份
TDI指数:117(即79.7+8.7=76.61.17=89.6)
2、密度为12kg/立方米的软泡配方:
聚醚:100份
水:6份
硅油:1.5份
辛酸亚锡:0.3份
胺催化剂:0.14份
二氯甲烷:15份
TDI指数:120
3、密度为16kg/立方米的软泡配方:
聚醚:100份
水:4.9份
硅油(l-580):1.3份
辛酸亚锡:0.3份
a33催化剂:0.12份
二氯甲烷:9.3份
填料:8份
TDI指数:62
这些配方仅供参考,实际生产中可能因材料品牌、环境温度和湿度等因素有所调整。
建议在专业人士指导下进行操作。
聚氨酯合成工艺
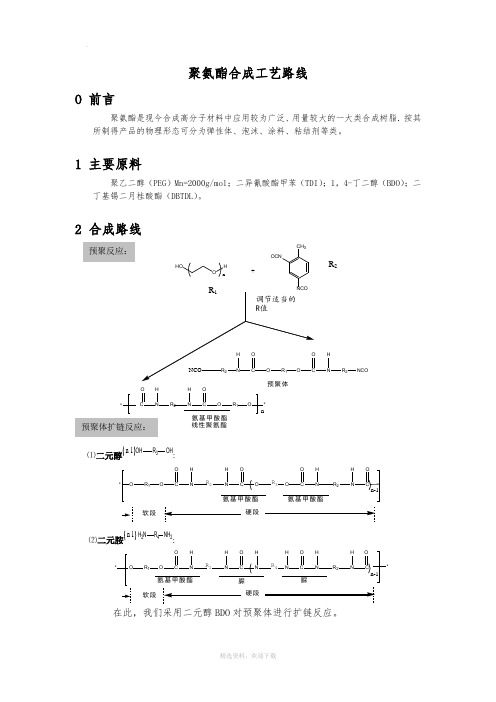
聚氨酯合成工艺路线O 前言聚氨酯是现今合成高分子材料中应用较为广泛、用量较大的一大类合成树脂.按其所制得产品的物理形态可分为弹性体、泡沫、涂料、粘结剂等类。
1 主要原料聚乙二醇(PEG)Mn=2000g/mol;二异氰酸酯甲苯(TDI);1,4-丁二醇(BDO);二丁基锡二月桂酸酯(DBTDL)。
2 合成路线2NCOC N R2HON COOHR1O**n氨基甲酸酯R2N COOHR3O C NHOO R1O C NHOR2N COH*n-1氨基甲酸酯氨基甲酸酯R2N CONHR4N C NHOO R1O C NHOR2N COHn-1氨基甲酸酯**H H脲脲软段硬段线性聚氨酯硬段在此,我们采用二元醇BDO对预聚体进行扩链反应。
预聚反应:扩链反应后所得的聚氨酯中的硬段部分再发生交联反应后就可得到交联聚氨。
R2N COHO R1O C NHOR2N COO R3O C NHOO R1O C NHOR2N COHn-1R2N COO R3O C NHOO R1O C NHOR2N COHn-1硬CNOHN HC OR22.1 聚醚脱水准确称量一定质量的PEG于500mL的三口烧瓶中,升温并抽真空,在内温为110~115℃①,真空度133.3Pa的条件下,脱水1.5小时②,然后冷却至50℃以下,放入干燥的仪器内密闭保存备用。
说明:①PEG在125℃会分解,故脱水时温度不能高于此分解温度,应控制在110~115℃。
②异氰酸酯与水反应后会使预聚物的粘度增大,进而使预聚物的贮存稳定性显著降低。
所以在实验过程中对多元醇等原材料的含水量和环境湿度都有严格要求。
合成前要将PEG加热真空脱水,并对实验仪器进行干燥脱水,反应还要在干燥氮气保护下进行,以避免空气湿度的影响。
2.2 预聚反应在干燥三口烧瓶的按配方量①将TDI溶液滴入已经脱水的PEG聚醚溶液中②,再加入微量的催化剂DBTDL③,搅拌均匀后,此时不加热④,自动升温约半小时后到(80±5)℃⑤,恒温计时反应2h得到预聚物,密封保存。
常用水性聚氨酯涂料配方

常用水性聚氨酯涂料配方
水性聚氨酯涂料是一种环保型涂料,具有良好的附着力、耐磨性、耐化学物质腐蚀、耐水性和气相透性等特点,被广泛应用于家具、建筑、汽车和木制品等领域。
以下是几种常用的水性聚氨酯涂料配方。
1.签发箱木器涂料:
-异丙醇:250克
-水:150克
-异六亚甲基二异氰酸酯:250克
-超稀的尿素醛树脂:20克
-环氧丙烷:5克
-搅拌20分钟
2.家具聚酯颜料涂料:
-赛白粉:50克
-环氧乙烷:100克
-偶乙烯二胺:100克
-福尔马林:100克
-含有聚酯树脂的溶剂:200克
-混合均匀
3.乳胶聚酯家具涂料:
-乳胶乳:150克
-聚酯树脂:70克
-聚醚:30克
-偶乙烯二胺:10克
-油漆稠化剂:10克
-搅拌均匀
4.汽车防腐聚酯漆配方:
-聚丙烯酸:400克
-聚醋酸乙烯酯单体:300克
-溶剂:50克
-铝粉:300克
-适量的颜料
-混合均匀后添加固化剂
5.木器底漆:
-乳胶乳:400克
-聚酯树脂:200克
-环氧底漆:100克
-偶乙烯二胺:10克
-钛白粉:150克
-油漆稠化剂:10克
-混合均匀
以上是几种常用的水性聚氨酯涂料配方,每种涂料的成分比例和配方可以根据具体需求进行微调。
值得注意的是,使用涂料时需严格按照产品说明书操作,确保操作安全和涂层质量。
聚氨酯实用配方(详细含硅油小料配比)

聚氨酯实用配方(详细含硅油小料配比)聚氨酯硬泡配方计算方法(实用)一:硬泡组合料里最需要计算的东西是黑白料比例(重量比)是不是合理,另一个正规的说法好像叫“异氰酸指数”是否合理,翻译成土话就是“按重量比例混合的白料和黑料要完全反应完”。
因此,白料里所有参与跟-NCO反应的东西都应该考虑在内。
理论各组分消耗的-NCO摩尔量计算如下㈠主料:聚醚、聚酯、硅油(普通硬泡硅油都有羟值,因为加了二甘醇之类的稀释,部分泡沫稳定剂型硅油还含有氨基)配方数乘以各自的羟值,然后相加得数Q,S1 = Q÷56100㈡水:水的配方量W S2 = W÷9㈢参与消耗-NCO的小分子物:配方量为K,其分子量为M,官能度为N S3 =K× N/M(用了两种以上小分子的需要各自计算再相加)S = S1+S2+S3 基础配方所需粗MDI份量[(S×42)÷0.30 ] ×1.05 (所谓异氰酸指数1.05)其实以上计算只是一个最基本的消耗量,由于黑白料反应过程复杂,实际-NCO消耗量肯定不止这个数,比如有三聚催化剂的情况,到底额外消耗了多少-NCO,这个没人说得清楚。
另外,聚醚里有水分,偏高0.1%就很严重;聚醚羟值也是看人家宣传单的,我见过有聚醚羟值范围跨度90mgKOH/g,那个计算数出来后只能参考,不能认真![试验设计]之“冰箱、冷柜”类本组合料体系重要要求及说明1、流动性要好,密度分布“尽量”均匀。
首先要考虑粘度,只有体系粘度小了,初期流动性才会好(主份平均粘度6000mPa.S以下,组合料350mPa.S以下),其次体系中的钾、钠杂离子要控制在一个低限(20ppm以内),从而可控制避免三聚反应提前,即:体系粘度过早变大。
如果流动性欠佳,发泡料行进至注料口远端就会出现拉丝痕致使泡孔结构橄榄球化,这个位置一定抗不住低温收缩。
2、泡孔细密,导热系数要低。
不难理解泡孔细密是导热系数低的第一前提,此时首先考虑加有403或某些芳香胺醚进入体系(它们所起的作用是首先与-NCO反应,其生成物与其它组份互溶、乳化稳定性提升,并保证发泡体系初期成核稳定,也就是避免迸泡,从而使泡孔细密)其次聚醚本身单独发泡其泡孔结构要好(例如以山梨醇为起始的635SA比蔗糖为起始的1050泡孔要细密均匀得多,还有含有甘油为起始剂的835比1050细密,即便是所谓的4110牌号的聚醚,含丙二醇起始的比二甘醇的好。
聚氨酯胶水配方
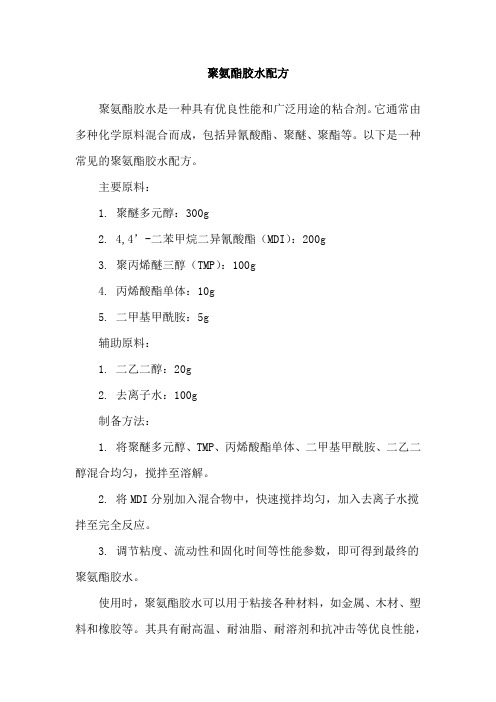
聚氨酯胶水配方
聚氨酯胶水是一种具有优良性能和广泛用途的粘合剂。
它通常由多种化学原料混合而成,包括异氰酸酯、聚醚、聚酯等。
以下是一种常见的聚氨酯胶水配方。
主要原料:
1. 聚醚多元醇:300g
2. 4,4’-二苯甲烷二异氰酸酯(MDI):200g
3. 聚丙烯醚三醇(TMP):100g
4. 丙烯酸酯单体:10g
5. 二甲基甲酰胺:5g
辅助原料:
1. 二乙二醇:20g
2. 去离子水:100g
制备方法:
1. 将聚醚多元醇、TMP、丙烯酸酯单体、二甲基甲酰胺、二乙二醇混合均匀,搅拌至溶解。
2. 将MDI分别加入混合物中,快速搅拌均匀,加入去离子水搅拌至完全反应。
3. 调节粘度、流动性和固化时间等性能参数,即可得到最终的聚氨酯胶水。
使用时,聚氨酯胶水可以用于粘接各种材料,如金属、木材、塑料和橡胶等。
其具有耐高温、耐油脂、耐溶剂和抗冲击等优良性能,
广泛应用于汽车、航空、建筑、包装等领域。
聚氨酯密封胶六个配方成分举例
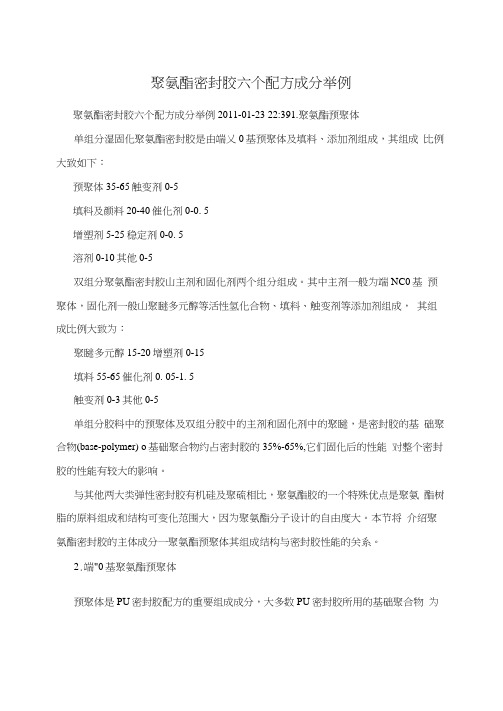
聚氨酯密封胶六个配方成分举例聚氨酯密封胶六个配方成分举例2011-01-23 22:391.聚氨酯预聚体单组分湿固化聚氨酯密封胶是由端乂0基预聚体及填料、添加剂组成,其组成比例大致如下:预聚体35-65触变剂0-5填料及颜料20-40催化剂0-0. 5增塑剂5-25稳定剂0-0. 5溶剂0-10其他0-5双组分聚氨酯密封胶山主剂和固化剂两个组分组成。
其中主剂一般为端NC0基预聚体,固化剂一般山聚瞇多元醇等活性氢化合物、填料、触变剂等添加剂组成,其组成比例大致为:聚瞇多元醇15-20增塑剂0-15填料55-65催化剂0. 05-1. 5触变剂0-3其他0-5单组分胶料中的预聚体及双组分胶中的主剂和固化剂中的聚瞇,是密封胶的基础聚合物(base-polymer) o基础聚合物约占密封胶的35%-65%,它们固化后的性能对整个密封胶的性能有较大的影响。
与其他两大类弹性密封胶有机硅及聚硫相比,聚氨酯胶的一个特殊优点是聚氨酯树脂的原料组成和结构可变化范围大,因为聚氨酯分子设计的自由度大。
本节将介绍聚氨酯密封胶的主体成分一聚氨酯预聚体其组成结构与密封胶性能的关系。
2.端"0基聚氨酯预聚体预聚体是PU密封胶配方的重要组成成分,大多数PU密封胶所用的基础聚合物为纯粹的端NC0聚瞇型PU预聚体。
在其制备时通常通过选择其原料聚瞇多元醇(一般为二元醇或三元醇)的分子量、二元醇及三元醇混合使用的比例、二异亂酸酯(TDI及MDI)的种类,以制备合适的预聚体。
在设计预聚体的制备配方时,一般要考虑使原料的NCO/OH摩尔比控制在1. 5-2. 5范围内,且所制备的预聚体的游离NCO质量白分含量在1%-4%之间。
据日本太阳星(Sunsta)技研株式会社伊藤等人报道,采用分子量在4000-8000 之间的聚氧化丙烯-氧化乙烯三醇(含E0链节的量为20%以下)及过量的MDI制成预聚体A,用分子量2000-6000的PPG与过量TDI反应制成预聚体B。
水性聚氨酯的配方

水性聚氨酯的配方1、改性三聚体交联剂产品可由TDI 、IPDI 、MD I 和XDI 等异氰酸酯制造。
其芳香族NCO 反应温度在(120—150) ℃,脂肪族NCO 反应温度在(150—200) ℃。
它的最大优点是无黄变, 水白透明, 较适用于羧酸型等水性聚氨酯的常温交联剂。
为增强综合性能, 需采用两个NCO 基团活性不同的二异氰酸酯,并要将反应中产生的端NCO 用多元醇- 羧酸反应掉, 以利于胺中和及产物的水溶性。
由于其熔点高,反应需分阶段在有机溶剂中进行, 有机膦催化剂及120 ℃以上温度, 异氰酸酯可发生自缩聚反应,生成三聚体化合物。
其催化剂中戊杂环膦化氢是最有效的, 反应温度低, 收率可达90 % , 再用三聚催化法促进反应完全,并对残基进行封闭。
产品配方:NCO :多元醇羧酸( 物质的量比) 为6:1:1.43。
工艺步骤: 多元醇- 羧酸溶液制备, 按配方将新戊二醇、苯偏三甲酸酐、DMPA 、二甲苯、甲苯加入反应釜搅拌,升温至80 ℃, 完成溶解后, 升温至148 ℃回流脱水至透明后, 过滤出料备用。
亚胺预聚体的制备: 按配方将二甲苯、甲苯加入反应釜, 升温至148 ℃回流脱水后, 加入10 % 磷酸( 甲苯) 液降温至120 ℃, 通入氮气, 将TD I 、IPDI 加入单体滴加釜, 在2 . 5h 内完成滴加后,升温至130 ℃反应1h , 将10 % 戊杂环膦化氢液加入滴加釜, 开始缓慢滴加,不断观察物料反应情况, 防止爆聚, 滴完在130℃反应2h 、140 ℃1h 、145 ℃30min , 降温至70 ℃, 将多元醇- 羧酸液加入滴加釜开始滴加,滴完在70 ℃反应(2—3) h , 检测NCO 转化率达96 % , 加入10 % 醋酸锂液, 此时有两种工艺: 一是降温至25 ℃, 静置7d ; 二是升温至(80—90) ℃反应(2—3) h , 测游离TD I 在0.3% 以下, 加入10 % 对甲苯磺酸甲酯液、10 % 二甲基吡唑液升温至85 ℃反应20min , 抽真空脱出2/3量的有机溶剂, 再加入亲水溶剂调节固含量为50 % , 降温至50 ℃加入50 % 三乙胺水溶液、N-甲苯二乙醇胺调节p H值至8.5 , 升温到60 ℃反应至透明, 降温到40 ℃出料。
聚氨酯的配方及工艺

线形热塑性聚氨酯原料用量(质量份)聚己内酯二醇(Mn:2000):20001,6-己二醇:112.0三羟甲基丙烷: 6.700TDI(80/20): 348.0有机锡催化剂: 1.2‰丁酮:1058聚氨酯油合成①配方:原料规格用量(质量份)醇酸树脂上步合成产品1000二甲苯聚氨酯级620.0甲苯二异氰酸酯工业级165.5二月桂酸二丁基锡分析醇 1.2‰丁醇5%②合成工艺:a. 将上步合成的醇酸树脂、50%二甲苯加入反应釜,升温至600C,在N2的继续保护下,将甲苯二异氰酸酯滴入聚合体系,约2h滴完;用剩余二甲苯洗涤甲苯二异氰酸酯滴加罐,并加入反应釜。
b. 保温1h,加入催化剂;将温度升至800C,保温反应;5h后取样测NCO含量,当NCO含量小于0.5%时,加入正丁醇封端0.5h。
降温,调固含、过滤、包装。
实例2聚酯基潮气固化聚氨酯的合成(1)配方:原料规格用量(质量份)聚己内酯二醇工业级,Mn:1500 3200聚己内酯三醇工业级,Mn:500 550.0二月桂酸二丁基锡化学纯0.5‰(以固体分计)二甲苯聚氨酯级2682甲苯二异氰酸酯工业级1230NCO理论含量:5.5%;NCO平均官能度:2.40。
(2)合成工艺:①依配方将聚己内酯多元醇加入聚合釜,加入50%的二甲苯共沸带水,至无水带出,通入N2保护,将温度降至600C。
②在N2的继续保护下,将甲苯二异氰酸酯滴入聚合体系,约2.5h滴完;用剩余二甲苯洗涤甲苯二异氰酸酯滴加罐,并加入反应釜。
③保温2h,加入催化剂;将温度升至800C,保温反应;2h后取样测NCO含量,当NCO含量稳定后(一般比理论值小0.5%),降温、过滤、包装。
1.羟基树脂合成实例实例1 羟基丙烯酸树脂的合成(1)配方:原料规格用量(质量份)丙二醇甲醚醋酸酯聚氨酯级111.0二甲苯(1)聚氨酯级140.0丙烯酸-β-羟丙酯工业级150.0苯乙烯工业级300.0甲基丙烯酸甲酯工业级100.0丙烯酸正丁酯工业级72.00丙烯酸工业级8.000叔丁基过氧化苯甲酰(1)工业级18.00叔丁基过氧化苯甲酰(2)工业级 2.000二甲苯(2)聚氨酯级100.0(2)合成工艺:①先将丙二醇甲醚醋酸酯、二甲苯(1)加入聚合釜中,通氮气置换反应釜中的空气,加热升温到1300C。
聚氨酯的配方及工艺

线形热塑性聚氨酯原料用量(质量份)聚己内酯二醇(Mn:2000):20001,6-己二醇:112.0三羟甲基丙烷: 6.700TDI(80/20): 348.0有机锡催化剂: 1.2‰丁酮:1058聚氨酯油合成①配方:原料规格用量(质量份)醇酸树脂上步合成产品1000二甲苯聚氨酯级620.0甲苯二异氰酸酯工业级165.5二月桂酸二丁基锡分析醇 1.2‰丁醇5%②合成工艺:a. 将上步合成的醇酸树脂、50%二甲苯加入反应釜,升温至600C,在N2的继续保护下,将甲苯二异氰酸酯滴入聚合体系,约2h滴完;用剩余二甲苯洗涤甲苯二异氰酸酯滴加罐,并加入反应釜。
b. 保温1h,加入催化剂;将温度升至800C,保温反应;5h后取样测NCO含量,当NCO含量小于0.5%时,加入正丁醇封端0.5h。
降温,调固含、过滤、包装。
实例2聚酯基潮气固化聚氨酯的合成(1)配方:原料规格用量(质量份)聚己内酯二醇工业级,Mn:1500 3200聚己内酯三醇工业级,Mn:500 550.0二月桂酸二丁基锡化学纯0.5‰(以固体分计)二甲苯聚氨酯级2682甲苯二异氰酸酯工业级1230NCO理论含量:5.5%;NCO平均官能度:2.40。
(2)合成工艺:①依配方将聚己内酯多元醇加入聚合釜,加入50%的二甲苯共沸带水,至无水带出,通入N2保护,将温度降至600C。
②在N2的继续保护下,将甲苯二异氰酸酯滴入聚合体系,约2.5h滴完;用剩余二甲苯洗涤甲苯二异氰酸酯滴加罐,并加入反应釜。
③保温2h,加入催化剂;将温度升至800C,保温反应;2h后取样测NCO含量,当NCO含量稳定后(一般比理论值小0.5%),降温、过滤、包装。
1.羟基树脂合成实例实例1 羟基丙烯酸树脂的合成(1)配方:原料规格用量(质量份)丙二醇甲醚醋酸酯聚氨酯级111.0二甲苯(1)聚氨酯级140.0丙烯酸-β-羟丙酯工业级150.0苯乙烯工业级300.0甲基丙烯酸甲酯工业级100.0丙烯酸正丁酯工业级72.00丙烯酸工业级8.000叔丁基过氧化苯甲酰(1)工业级18.00叔丁基过氧化苯甲酰(2)工业级 2.000二甲苯(2)聚氨酯级100.0(2)合成工艺:①先将丙二醇甲醚醋酸酯、二甲苯(1)加入聚合釜中,通氮气置换反应釜中的空气,加热升温到1300C。
聚氨酯白料配方

聚氨酯白料配方
聚氨酯是一种广泛应用的高分子材料,可用于制备各种产品,包括弹性体、涂料、胶粘剂等。
聚氨酯的白料配方取决于具体的应用和要求。
以下是一种常见的聚氨酯白料配方示例:
主要原料:
1. 聚醚多元醇或聚酯多元醇(聚氧化环丙烷、聚酯多元醇等)- 45%
2. 异佛尔酮二异氰酸酯或甲基苯异氰酸酯 - 40%
3. 反应助剂(催化剂、成链剂等) - 15%
配方过程:
1. 将聚醚多元醇或聚酯多元醇加入反应釜中,并在适当的温度下加热搅拌。
2. 逐渐加入异佛尔酮二异氰酸酯或甲基苯异氰酸酯,并在适当的温度下反应搅拌。
3. 加入反应助剂,如催化剂和成链剂,并继续搅拌反应。
4. 控制反应的时间和温度,使反应达到适当的程度。
5. 结束反应后,将白料熔融倾倒入模具或其他制品形成器具中。
6. 对制品进行固化或固化后的后处理,如修整、打磨等。
这只是一种常见的聚氨酯白料配方示例,实际配方可能会因具体应用、产品要求和原料的不同而有所不同。
在实际应用中,应根据具体需求进行合理的调整和优化。
聚氨酯实用配方(详细含硅油小料配比)

聚氨酯硬泡配方计算方法(实用)一:硬泡组合料里最需要计算的东西是黑白料比例(重量比)是不是合理,另一个正规的说法好像叫“异氰酸指数”是否合理,翻译成土话就是“按重量比例混合的白料和黑料要完全反应完”。
因此,白料里所有参和跟-NCO反应的东西都应该考虑在内。
理论各组分消耗的-NCO摩尔量计算如下㈠主料:聚醚、聚酯、硅油(普通硬泡硅油都有羟值,因为加了二甘醇之类的稀释,部分泡沫稳定剂型硅油还含有氨基)配方数乘以各自的羟值,然后相加得数Q,S1 = Q÷56100㈡水:水的配方量W S2 = W÷9㈢参和消耗-NCO的小分子物:配方量为K,其分子量为M,官能度为N S3 =K× N/M(用了两种以上小分子的需要各自计算再相加) S = S1+S2+S3 基础配方所需粗MDI份量[(S×42)÷0.30 ] ×1.05 (所谓异氰酸指数1.05)其实以上计算只是一个最基本的消耗量,由于黑白料反应过程复杂,实际-NCO消耗量肯定不止这个数,比如有三聚催化剂的情况,到底额外消耗了多少-NCO,这个没人说得清楚。
另外,聚醚里有水分,偏高0.1%就很严重;聚醚羟值也是看人家宣传单的,我见过有聚醚羟值范围跨度90mgKOH/g,那个计算数出来后只能参考,不能认真![试验设计]之“冰箱、冷柜”类本组合料体系重要要求及说明1、流动性要好,密度分布“尽量”均匀。
首先要考虑粘度,只有体系粘度小了,初期流动性才会好(主份平均粘度6000mPa.S以下,组合料350mPa.S以下),其次体系中的钾、钠杂离子要控制在一个低限(20ppm以内),从而可控制避免三聚反应提前,即:体系粘度过早变大。
如果流动性欠佳,发泡料行进至注料口远端就会出现拉丝痕致使泡孔结构橄榄球化,这个位置一定抗不住低温收缩。
2、泡孔细密,导热系数要低。
不难理解泡孔细密是导热系数低的第一前提,此时首先考虑加有403或某些芳香胺醚进入体系(它们所起的作用是首先和-NCO反应,其生成物和其它组份互溶、乳化稳定性提升,并保证发泡体系初期成核稳定,也就是避免迸泡,从而使泡孔细密)其次聚醚本身单独发泡其泡孔结构要好(例如以山梨醇为起始的635SA比蔗糖为起始的1050泡孔要细密均匀得多,还有含有甘油为起始剂的835比1050细密,即便是所谓的4110牌号的聚醚,含丙二醇起始的比二甘醇的好。
聚氨酯合成工艺

聚氨酯合成工艺路线O 前言聚氨酯是现今合成高分子材料中使用较为广泛、用量较大的一大类合成树脂.按其所制得产品的物理形态可分为弹性体、泡沫、涂料、粘结剂等类。
1 主要原料聚乙二醇(PEG )Mn=2000g/mol ;二异氰酸酯甲苯(TDI );1,4-丁二醇(BDO );二丁基锡二月桂酸酯(DBTDL )。
2 合成路线HOOH nCH 3OCNNCO+调节适当的R 值NCOR 2NCO OH R 1OCNR 2H O NCO预聚体CNR 2H ONCO OH R 1O**n氨基甲酸酯R 2NCO OHR 3O CNH OO R 1OCNH OR 2NCO H *n-1氨基甲酸酯氨基甲酸酯R 2NCO NHR 4NCNH O OR 1OCNH OR 2NCO H n-1氨基甲酸酯**H H脲脲软段硬段线性聚氨酯软段硬段在此,我们采用二元醇BDO 对预聚体进行扩链反应。
扩链反应后所得的聚氨酯中的硬段部分再发生交联反应后就可得到交联聚氨。
⑴二元醇OHR 3OHn-1:⑵二元胺H 2N R 4NH 2n-1:预聚体扩链反应: 预聚反应:交联反应:R 1R 2R 2NCO OHR 3O CNH OOR 1OCNH OR 2NCO H n-1R 2N COOR 3O CNH OOR 1OCNH OR 2NCO H n-1R 2NCO OR 3O CNH O OR 1OCNH OR 2NCO H n-1硬段C N O HN H CO R 22.1 聚醚脱水准确称量一定质量的PEG 于500mL 的三口烧瓶中,升温并抽真空,在内温为110~115℃①,真空度133.3Pa 的条件下,脱水1.5小时②,然后冷却至50℃以下,放入干燥的仪器内密闭保存备用。
说明:①PEG 在125℃会分解,故脱水时温度不能高于此分解温度,应控制在110~115℃。
②异氰酸酯和水反应后会使预聚物的粘度增大,进而使预聚物的贮存稳定性显著降低。
聚氨酯弹性体参考配方

聚氨酯弹性体参考配方配方如下:1.聚酯多元醇:60-70份2.异佛尔酮二异氰酸酯(TDI):30-40份3.链延长剂:2-3份4.稳定剂:0.2-0.5份5.催化剂:0.5-1份6.塑料化剂:根据需要添加聚酯多元醇是聚氨酯制备的主要原料,可以选择聚酯多元醇根据需要的性能来确定。
常用的聚酯多元醇有聚酯多元醇A、聚酯多元醇B等。
聚酯多元醇具有良好的柔软性、耐磨性和低温性能。
异佛尔酮二异氰酸酯(TDI)是聚氨酯制备的硬段原料,可以通过调整其用量来控制聚氨酯材料的硬度和弹性。
在配方中,可以根据需要将TDI分为两个部分添加,一部分作为预聚体与聚酯多元醇反应,另一部分作为链延长剂与预聚体反应,从而得到所需的硬度和弹性。
链延长剂用于调节聚氨酯材料的分子量和柔软性,一般选择具有双官能团的分子作为链延长剂。
常用的链延长剂有乙二醇、丁二醇等。
稳定剂用于提高聚氨酯材料的稳定性,防止氧化和黄变等现象的发生。
可以选择有机锡化合物等作为稳定剂。
催化剂用于促进聚氨酯材料的硬化反应,常用的催化剂有二甲苯胺(DMA)、四乙基二氮唑(DABCO)等。
塑料化剂可以根据需要添加,用于调节聚氨酯材料的流动性和柔软性。
常用的塑化剂有聚醚、聚乙烯醇等。
配方制备过程如下:1.将聚酯多元醇、TDI和链延长剂按照配方比例混合搅拌,使其均匀混合。
2.添加稳定剂和催化剂,继续搅拌混合。
3.如有需要,可以添加塑化剂进行调节,继续搅拌混合。
4.将混合物倒入模具中,进行加热硬化过程,通常需要在150-200°C下进行。
5.根据需要,可以通过改变硬化温度和时间来调节聚氨酯弹性体的硬度和弹性。
以上是一种聚氨酯弹性体的参考配方和制备过程,需要根据具体需求进行调整。
在实际制备过程中,还需要进行反应的控制和工艺的优化,以获得所需的产品性能。
聚氨酯砂浆配方

聚氨酯砂浆配方
聚氨酯砂浆的配方因具体用途和要求的性能而有所不同。
以下是一个常用的聚氨酯砂浆配方:
主要材料:
聚氨酯树脂:100份
多元醇:30-40份
辅助材料:
砂子:200份
环氧树脂:20-30份
金属粉末(如铝、铜等):5-10份
配方步骤:
1.将聚氨酯树脂和多元醇按100:30-40的比例混合。
2.将砂子、环氧树脂和金属粉末混合在一起。
3.将混合物分别倒入两个桶中。
4.按照一定比例,将两个桶中的混合物混合在一起。
5.搅拌混合物至均匀,注意时间不宜过长。
6. 将混合好的聚氨酯砂浆倒入需要修补或涂覆的部位。
这只是一个常用的配方,具体配方应根据具体用途和要求的性能而定。
在使用聚氨酯砂浆的过程中,应遵循相关的安全操作和使用规范,确保人身和环境
安全。
聚氨酯配方
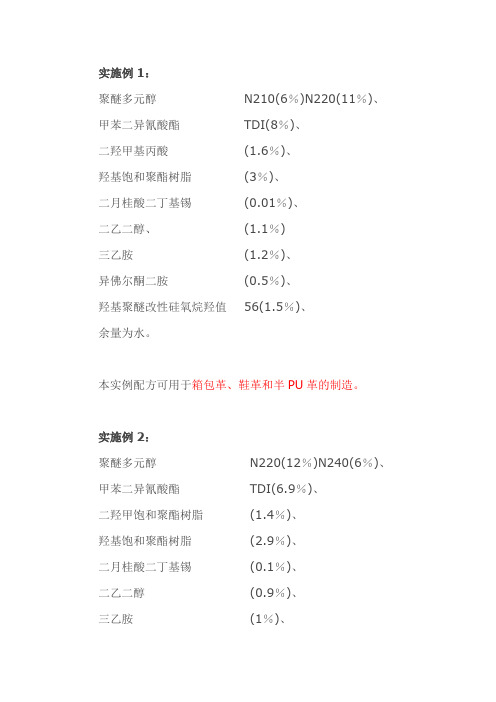
实施例1:聚醚多元醇N210(6%)N220(11%)、甲苯二异氰酸酯TDI(8%)、二羟甲基丙酸(1.6%)、羟基饱和聚酯树脂(3%)、二月桂酸二丁基锡(0.01%)、二乙二醇、(1.1%)三乙胺(1.2%)、异佛尔酮二胺(0.5%)、羟基聚醚改性硅氧烷羟值56(1.5%)、余量为水。
本实例配方可用于箱包革、鞋革和半PU革的制造。
实施例2:聚醚多元醇N220(12%)N240(6%)、甲苯二异氰酸酯TDI(6.9%)、二羟甲饱和聚酯树脂(1.4%)、羟基饱和聚酯树脂(2.9%)、二月桂酸二丁基锡(0.1%)、二乙二醇(0.9%)、三乙胺(1%)、异佛尔酮二胺(0.4%)、羟基聚醚改性硅氧烷羟值56 (1.8%)、余量为水。
本实例配方可用于服装革、软箱包革和半PU革的制造。
实施例3:聚醚多元醇N210(6%)N220(12%)、甲苯二异氰酸酯TDI(6.5%)、二羟甲基丙酸(1.5%)、羟基饱和聚酯树脂(2%)、二月桂酸二丁基锡(0.01%)、二乙二醇(1.3%)、三乙胺(0.9%)、异佛尔酮二胺(0.4%)、羟基聚醚改性硅氧烷羟值56(1%)、余量为水。
本实施例尤其适宜PU和PVC革的粘接层。
实施列4:聚醚多元醇N210(6%)N220(14%)、甲苯二异氰酸酯TDI(9%)、二羟甲基丙酸(1.7%)、羟基饱和聚酯树脂(4%)、二月桂酸二丁基锡(0.0l%)、二乙二醇(1.2%)、三乙胺(1.3%)、异佛尔酮二胺(0.5%)、羟基聚醚改性硅氧烷羟值56(0.5%)、余量为水。
本实施例尤其适宜PU革的改色和直涂压花处理.具体实施方法是:先将聚醚多元醇120℃脱水,冷却到60℃加多异氰酸酯85~95℃预聚3小时;在加入二羟甲基丙酸和羟基丙烯酸树脂、二月桂酸二丁基锡75~80℃反应2小时;再加入二乙二醇羟基聚醚改性硅氧烷75~80℃反应3小时;冷却到40℃以下加三乙胺中和10分钟后加去离子水2200转/分钟分散15分钟;再加异佛尔酮二胺扩链分散25分钟既的固含量30~40%的革用改性水性聚氨酯树脂。
水性聚氨酯的配方

1、改性三聚体交联剂产品可由TDI 、IPDI 、MD I 和XDI 等异氰酸酯制造。
其芳香族NCO 反应温度在(120—150) ℃,脂肪族NCO 反应温度在(150—200) ℃。
它的最大优点是无黄变, 水白透明, 较适用于羧酸型等水性聚氨酯的常温交联剂。
为增强综合性能, 需采用两个NCO 基团活性不同的二异氰酸酯,并要将反应中产生的端NCO 用多元醇- 羧酸反应掉, 以利于胺中和及产物的水溶性。
由于其熔点高,反应需分阶段在有机溶剂中进行, 有机膦催化剂及120 ℃以上温度, 异氰酸酯可发生自缩聚反应,生成三聚体化合物。
其催化剂中戊杂环膦化氢是最有效的, 反应温度低, 收率可达90 % , 再用三聚催化法促进反应完全, 并对残基进行封闭。
产品配方:NCO :多元醇羧酸( 物质的量比) 为6:1:1.43。
工艺步骤: 多元醇- 羧酸溶液制备, 按配方将新戊二醇、苯偏三甲酸酐、DMPA 、二甲苯、甲苯加入反应釜搅拌,升温至80 ℃, 完成溶解后, 升温至148 ℃回流脱水至透明后, 过滤出料备用。
亚胺预聚体的制备: 按配方将二甲苯、甲苯加入反应釜, 升温至148 ℃回流脱水后, 加入10 % 磷酸( 甲苯) 液降温至120 ℃, 通入氮气, 将TD I 、IPDI 加入单体滴加釜, 在2 . 5h 内完成滴加后, 升温至130 ℃反应1h , 将10 % 戊杂环膦化氢液加入滴加釜, 开始缓慢滴加, 不断观察物料反应情况, 防止爆聚, 滴完在130℃反应2h 、140 ℃1h 、145 ℃30min , 降温至70 ℃, 将多元醇- 羧酸液加入滴加釜开始滴加,滴完在70 ℃反应(2—3) h , 检测NCO 转化率达96 % , 加入10 % 醋酸锂液, 此时有两种工艺: 一是降温至25 ℃, 静置7d ; 二是升温至(80—90) ℃反应(2—3) h , 测游离TD I 在0.3% 以下, 加入10 % 对甲苯磺酸甲酯液、10 % 二甲基吡唑液升温至85 ℃反应20min , 抽真空脱出2/3量的有机溶剂, 再加入亲水溶剂调节固含量为50 % , 降温至50 ℃加入50 % 三乙胺水溶液、N-甲苯二乙醇胺调节p H 值至8.5 , 升温到60 ℃反应至透明, 降温到40 ℃出料。
聚氨酯实用配方(详细含硅油小料配比)
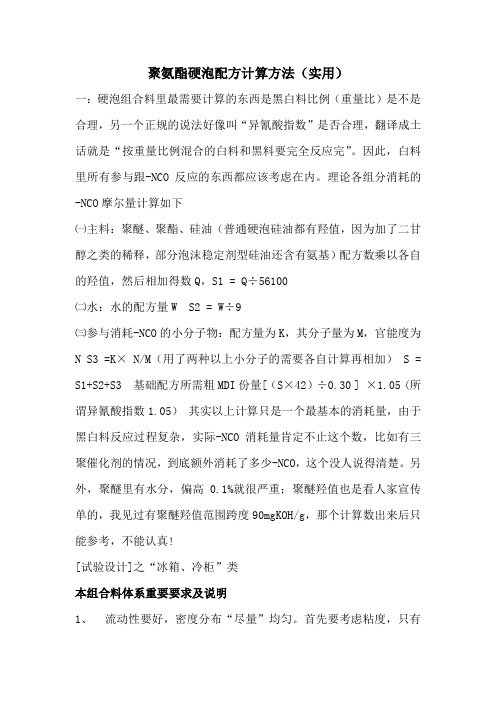
聚氨酯硬泡配方计算方法(实用)一:硬泡组合料里最需要计算的东西是黑白料比例(重量比)是不是合理,另一个正规的说法好像叫“异氰酸指数”是否合理,翻译成土话就是“按重量比例混合的白料和黑料要完全反应完”。
因此,白料里所有参与跟-NCO反应的东西都应该考虑在内。
理论各组分消耗的-NCO摩尔量计算如下㈠主料:聚醚、聚酯、硅油(普通硬泡硅油都有羟值,因为加了二甘醇之类的稀释,部分泡沫稳定剂型硅油还含有氨基)配方数乘以各自的羟值,然后相加得数Q,S1 = Q÷56100㈡水:水的配方量W S2 = W÷9㈢参与消耗-NCO的小分子物:配方量为K,其分子量为M,官能度为N S3 =K× N/M(用了两种以上小分子的需要各自计算再相加) S = S1+S2+S3 基础配方所需粗MDI份量[(S×42)÷0.30 ] ×1.05 (所谓异氰酸指数1.05)其实以上计算只是一个最基本的消耗量,由于黑白料反应过程复杂,实际-NCO消耗量肯定不止这个数,比如有三聚催化剂的情况,到底额外消耗了多少-NCO,这个没人说得清楚。
另外,聚醚里有水分,偏高0.1%就很严重;聚醚羟值也是看人家宣传单的,我见过有聚醚羟值范围跨度90mgKOH/g,那个计算数出来后只能参考,不能认真![试验设计]之“冰箱、冷柜”类本组合料体系重要要求及说明1、流动性要好,密度分布“尽量”均匀。
首先要考虑粘度,只有体系粘度小了,初期流动性才会好(主份平均粘度6000mPa.S以下,组合料350mPa.S以下),其次体系中的钾、钠杂离子要控制在一个低限(20ppm以内),从而可控制避免三聚反应提前,即:体系粘度过早变大。
如果流动性欠佳,发泡料行进至注料口远端就会出现拉丝痕致使泡孔结构橄榄球化,这个位置一定抗不住低温收缩。
2、泡孔细密,导热系数要低。
不难理解泡孔细密是导热系数低的第一前提,此时首先考虑加有403或某些芳香胺醚进入体系(它们所起的作用是首先与-NCO反应,其生成物与其它组份互溶、乳化稳定性提升,并保证发泡体系初期成核稳定,也就是避免迸泡,从而使泡孔细密)其次聚醚本身单独发泡其泡孔结构要好(例如以山梨醇为起始的635SA比蔗糖为起始的1050泡孔要细密均匀得多,还有含有甘油为起始剂的835比1050细密,即便是所谓的4110牌号的聚醚,含丙二醇起始的比二甘醇的好。
聚氨酯的配方
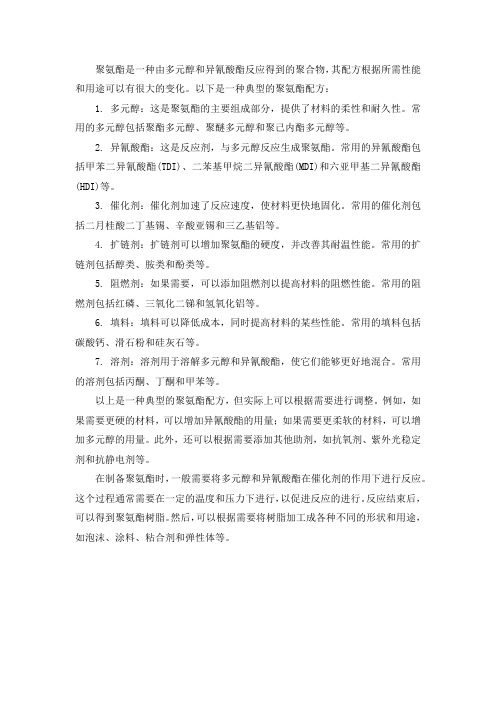
聚氨酯是一种由多元醇和异氰酸酯反应得到的聚合物,其配方根据所需性能和用途可以有很大的变化。
以下是一种典型的聚氨酯配方:1. 多元醇:这是聚氨酯的主要组成部分,提供了材料的柔性和耐久性。
常用的多元醇包括聚酯多元醇、聚醚多元醇和聚己内酯多元醇等。
2. 异氰酸酯:这是反应剂,与多元醇反应生成聚氨酯。
常用的异氰酸酯包括甲苯二异氰酸酯(TDI)、二苯基甲烷二异氰酸酯(MDI)和六亚甲基二异氰酸酯(HDI)等。
3. 催化剂:催化剂加速了反应速度,使材料更快地固化。
常用的催化剂包括二月桂酸二丁基锡、辛酸亚锡和三乙基铝等。
4. 扩链剂:扩链剂可以增加聚氨酯的硬度,并改善其耐温性能。
常用的扩链剂包括醇类、胺类和酚类等。
5. 阻燃剂:如果需要,可以添加阻燃剂以提高材料的阻燃性能。
常用的阻燃剂包括红磷、三氧化二锑和氢氧化铝等。
6. 填料:填料可以降低成本,同时提高材料的某些性能。
常用的填料包括碳酸钙、滑石粉和硅灰石等。
7. 溶剂:溶剂用于溶解多元醇和异氰酸酯,使它们能够更好地混合。
常用的溶剂包括丙酮、丁酮和甲苯等。
以上是一种典型的聚氨酯配方,但实际上可以根据需要进行调整。
例如,如果需要更硬的材料,可以增加异氰酸酯的用量;如果需要更柔软的材料,可以增加多元醇的用量。
此外,还可以根据需要添加其他助剂,如抗氧剂、紫外光稳定剂和抗静电剂等。
在制备聚氨酯时,一般需要将多元醇和异氰酸酯在催化剂的作用下进行反应。
这个过程通常需要在一定的温度和压力下进行,以促进反应的进行。
反应结束后,可以得到聚氨酯树脂。
然后,可以根据需要将树脂加工成各种不同的形状和用途,如泡沫、涂料、粘合剂和弹性体等。
- 1、下载文档前请自行甄别文档内容的完整性,平台不提供额外的编辑、内容补充、找答案等附加服务。
- 2、"仅部分预览"的文档,不可在线预览部分如存在完整性等问题,可反馈申请退款(可完整预览的文档不适用该条件!)。
- 3、如文档侵犯您的权益,请联系客服反馈,我们会尽快为您处理(人工客服工作时间:9:00-18:30)。
聚氨酯床垫配方及性能①为非芳香族的胺类催化剂。
②为改性的甲苯二异氰酸酯。
③60%的MDI与40% 的TDI (65/35)的混合物。
半硬泡自结皮PU泡沫配方配方组成(质量份)1# 2# 3# 4#聚醚多元醇100 100 100 100乙二醇7 -- 7 --1,4丁二醇-- 8 -- 8三亚乙基二胺 1.5 1.5 1.5 1.5F11 17 17 17 17液化MDI(1040指数)30-40(105) 30-40(105)液化MDI(1050指数)30-40(105) 30-40(105) 低密度低硬度高回弹PU泡沫塑料配方组成(质量份)1# 2# 聚醚100 100 水 2.4 2.4 二乙醇胺 1 2二(2-二甲胺基乙基)醚0.06 0.06 硅泡沫稳定剂0.06 0.06 T9 0.10 0.15 F11 5 5 TDI8020 30-50(103) 30-50(103)高回弹海绵配方供参考高活性聚醚多元醇....................100份TDl........................................43.4份DEOA....................................1.5份水.........................................3.5份L5333...................................1.0份A230.....................................0.23份D22.......................................0.04份慢回弹枕头配方1030=40330=503628=10水=3A33=0.8DMEA=0.52乙=1.5A1=0.153002=0.8141B=25TDI/MDI=2:1聚氨酯高回弹MDI组合料配方A33--0.3DMEA--0.62乙--0.53乙--0.3141B--1.5H20--0.155596-5005=3比1中硬度高回弹PU配方配方组成(质量份)1# 2#聚醚100 100水 2.4 2.8二乙醇胺 1.2 1二(2-二甲胺基乙基)醚0.08 0.08硅泡沫稳定剂0.4 0.4T9 0.15 0.15TDI8020 30-40(110)30-40(110)密度为8kg/m3 的软泡配方配方原料重量份数聚醚三元醇,羟值56 100水 6.6三乙烯二胺(33 %溶液) 0.18TEGOSTAB B8110硅油 3.8(非水介性的聚硅烷一聚氧烷共聚物高活性泡沫稳定剂,高施米特公司产品)幸酸亚锡0.4二氯甲烷34TDI 80/20 103密度,kg/m3 8低密度自结皮配方(座椅用)330N:55POP:45EG: 6A33:0.3DMEA: 0.45TEOA: 0.85A-1: 0.2B8681:0.5H20: 0.3141B: 12NE-113:48~50聚氨酯床垫的配方聚氨酯床垫配方及性能生产方式聚醚型“冷熟化”模塑软泡聚醚型“冷熟化”模塑软泡用途作各种坐垫作全泡沫家具配方/份聚醚(分子量为3000)100 聚醚(分子量为4800) 100 水3 水2.5三亚乙基二胺0.3 稳定剂1三乙胺0.4 三乙醉胺1交联剂①0.6 三乙胺0.4稳定剂1 三亚乙基二胺0.2异氰酸酯②46.4 异氰酸酯③39性能密度/(kg/cm3) 43 密度/(kg/cm3) 40拉伸强度/MPa 0.06 拉伸强度/MPa 0.06伸长率/% 135 伸长率/% 90压缩负荷(40%)/Pa 2352 压缩负荷(40%)/Pa 2156压缩变形(90%)/% 4.1 压缩变形(90%)/% 3回弹率/% 62 回弹率/% 70①为非芳香族的胺类催化剂。
②为改性的甲苯二异氰酸酯。
③60%的MDI与40% 的TDI(65/35)的混合物。
汽车坐垫高硬度高回弹配方高活性聚醚40聚合物多元醇60水 3.5DMOA 1.7A1 0.12A33 0.35D22 0.00310366 1.2TDI/PMDI=1:1B/A=43%密度为23k/m3软泡配方(一)原料重量份数5613聚醚100水 3.6二氯甲烷 3.5硅油L-560 1,14三乙烯二胺(33%溶液) O.06双-(二甲胺基乙基)醚(A-I). 0.02DABCO T-10 O.35TDI 47.7TDI指数109性能密度,kg/m3 23.0压缩硬度,65%N 28025%,N 142拉伸强度.KPa 126撕裂强度.N/M 491伸长率,% 200回弹率,% 49压缩永久变形,50% 2.5密度为16kg/m3软泡配方聚醚V oranol 3010 100水 3.6CFC—F11 22硅油.BF 2370 1.2三乙烯二胺(33%溶液) 0.45 .辛酸亚锡0.267DI 80/20 48.3.TDI指数105性能密度(KG/M3) : 16.3 .压陷硬度(ILD),N.25% 3265 % 86拉伸强度Kpa 86.9撕裂强度,N/cm: 3.97伸长率-% 339回弹率% : 38乱孔海绵配方配方:聚醚多元醇 (100)异氰酸酯 (51)水.............................4.0L--501.......................0.005硅油..........................1.1A--33 .......................0.13T--9 .........................0.28密度 (28)======================================================== 热模塑发泡30-35密度的参考配方生产热模塑泡沫制品的典型配方见以下2个表。
表2 DOW CHem.Co热模塑泡沫典型配方聚氨酯催化剂产品一览表美国气体产品编号公司产品编号产品介绍胺类催化剂DABCO 33LVR A-33 33%三乙烯二胺的二丙二醇溶液,工业标准产品。
DABCOR 1027 1027 改性三乙烯二胺,用于单乙醇聚酯及聚醚鞋底原液系统,能调整纤维及脱模时间。
DABCO 1028 1028 改性三乙烯二胺,用于1,4丁二醇聚酯及聚醚鞋底原液系统,能调整纤维及脱模时间。
DABCO 8154 8154 延迟性三乙烯二胺型催化剂,可改善泡沫流动性。
DABCO B16 B16 改善表面固化,适用于模塑及其他自结皮系统。
DABCO BDMA BDMA 减低于高水份配方中产生之脆性及表面固化。
DABCO BL-11 A-1 70%双(二甲胺基乙基)醚的二丙二醇溶液,「发泡」型催化剂。
DABCO BL-17 BL-17 具有延迟反应效果的双(二甲胺基乙基)醚衍生物。
DABCO BL-22 BL-22 复合胺,具有强烈「发泡」效果,可取代BL-11。
DABCO Crystalline 固体胺固体三乙烯二胺,工业标准产品。
DABCO CS-90 CS-90 复合胺,具有强烈「发泡」作用,改善泡沫密度梯度及开孔效果,可减少箱泡角落破裂。
DABCO DC-2R DC-2 特殊复合胺,适用于硬质喷涂加速固化,优良储存稳定性。
DABCO DMAEE DMAEE 低气味表面固化催化剂,与33LV等主要基础催化剂共用。
DABCO DMDEE DMDEE 「发泡」催化剂,尤其适用于单组份密封泡沫,与MDI相溶而不反应。
DABCO DMEA DMEA 温和平衡性催化剂,乳白时间较短。
DABCO EG EG 凝胶催化剂,33%三乙烯二胺的乙二醇溶液,用于鞋材乙二醇系统。
DABCO NE200(新) NE200 特殊低雾化反应型「发泡」催化剂。
DABCO NE400(新) NE400 低气味,特殊低雾化反应型催化剂,用于聚酯泡沫。
DABCO NE500(新) NE500 特殊低雾化反应型「胶化」催化剂,能大大减低气味及雾化。
DABCO NE600(新) NE600 特殊低雾化反应型「发泡」催化剂,能大大减低气味及雾化。
DABCO NE1060(新) NE1060 特殊低雾化反应型「胶化」催化剂。
DABCO S-25 S-25 凝胶催化剂,25%三乙烯二胺,75% 1,4丁二醇混合物。
DABCO T T 发泡型催化剂,有低雾化效果,用于包装材料。
DABCO TMR TMR 用于聚异氰脲酸酯(PIR),加速末段固化而不影响乳白时间。
DABCO TMR-2 TMR-2 用于聚异氰脲酸酯(PIR),但反应较温和,能缩短硬质泡沫脱模时间。
DABCO TMR-3 TMR-3 用于聚异氰脲酸酯(PIR),但反应最慢,有延迟作用。
DABCO TMR-4 TMR-4 三聚反应催化剂,提供优良流动性效果。
DABCO TMR-30 DMP-30 三(二甲氨基甲基)-2,4,6-苯酚基本三聚反应催化剂。
DABCO XDMTM XDM 辅助性催化剂,能改善表皮外观及固化。
POLYCATR5 PC5 强烈「发泡」型催化剂,硬泡工业标准催化剂,能改善泡沫流动性。
POLYCAT8 PC8 二甲基环己胺,标准催化剂。
POLYCAT9 PC9 叔胺类,低气味硬质催化剂,可取代二甲基环己胺,特别适用于硬质喷涂系统。
POLYCAT12 PC12 叔胺类催化剂,反应性较弱,可增加泡沫硬度。
POLYCAT17 PC17 平衡性,低雾化催化剂,可改善表面固化,特别适用于头枕等产品。
POLYCAT18(新) PC-18 特殊共催化剂,延迟起发时间而不影响末段固化;改善板材上边固化。
POLYCAT33 PC-33 改性二甲基环己胺,低气味硬质催化剂,工业标准产品。
POLYCAT41 PC-41 三聚催化剂,优良发泡效果;适用于水份量较高的各类硬泡系统,能缩短脱模时间。
POLYCAT48 PC48 特殊平衡型催化剂,可帮助改善流动性,提高尺寸稳定性,特别适用于低密度配方可单独或配合其他催化剂使用。
POLYCAT58 PC58 低气味,表面固化催化剂。
POLYCAT77 PC77 平衡反应催化剂,优良开孔及表面固化效果,能增强模塑泡沫回弹力。
POLYCAT92 PC92 特殊复合胺,有延长乳白,减少海绵破裂损耗,适用于低至高密度配方,特别适用于慢回弹。
其他国家产品编号公司产品编号产品介绍C-225 C-225 延迟型吹发及交联平衡,改善流动性。
PC CAT DBU DBU 1,8二氮杂双环[5,4,0]十一碳烯-7,强凝胶催化剂。
SMP SMP 复合叔胺,增加泡沫硬度AS-33 AS-33 改性三乙烯二胺,延迟催化剂,模塑、箱式、软泡PCCAT NP15 N15 双-(3-二甲基氨丙基)氨基-2-丙醇胺,低气味、高回弹DMBA 二甲基苄胺ZF-1 低雾化,发泡型催化剂,可替代A-1TMEDA 四甲基乙二胺辅助催化剂TMPTA 四甲基丙二胺辅助催化剂L-33 低雾化,凝胶型催化剂,性能可替代A-33NMM N-甲基吗啉,聚氨酯快泡,开孔DMP 1,4-二甲基哌嗪,自结皮金属类催化剂DABCO K-15 K-15 70%辛酸钾于二乙二醇溶液,标准PIR催化剂。