棒材连轧生产设备特点概述
棒材轧机区设备功能说明介绍模板之欧阳历创编

轧机区设备控制功能说明书2007年4月30日项目代号水平轧机 C.S.001立式轧机 C.S.002平立转换轧机 C.S.0036V轧机后的飞剪(1号飞剪) C.S.00412V轧机后的飞剪(2号飞剪) C.S.005中轧后辊道 C.S.006精轧后辊道 C.S.007立式活套器 C.S.008夹送辊 C.S.00918H/V轧机后的飞剪(3号飞剪) C.S.010轧机区设备控制功能说明书C.S. 001水平轧机1.概述水平轧机共9架●1H、3H为Φ610mm轧机●5H为Φ530mm轧机●7H、9H、11H为Φ470mm轧机●13H、15H、17H为Φ380mm轧机每架轧机由以下几部分组成:●底座●拉扞和轧辊组(机架)●锁紧装置●横移液压缸,布置在轧机传动侧●液压马达(手动)压下机构●上下辊弹性阻尼减振器平衡●万向接轴托架装置2.电气元件详见电机表及各分项描述3.功能描述换孔型的工作过程●机架锁紧液压缸松开;●横移液压缸动作,驱动轧机在底座上水平移动以对中孔型;●机架锁紧缸闭合,锁紧轧机。
换机架的工作过程轧机主电机停转;轧机锁紧缸松开;轧机横移液压缸动作推动轧机横移到操作侧换辊位置;万向接轴托架插销缸插销缩回;轧机横移液压缸动作拉动万向接轴托架横移到传动侧极限位置;(此时,轧辊轴头与万向接轴辊端轴套脱开)吊车将轧机机架整体吊走,新轧机机架吊入;轧机横移液压缸动作推动万向接轴托架横移到操作侧换辊位置;(此时,轧辊轴头与万向接轴辊端轴套重合)万向接轴托架插销缸插销伸出;轧机横移液压缸动作拉动轧机横移对中孔型使轧机处于正常轧钢位置;轧机锁紧缸闭合。
此即水平轧机的完整换辊过程。
换孔型或换机架过程的连锁:只有当轧机锁紧缸松开,轧机才能横移;只有当轧机锁紧缸锁紧轧机,主电机才能工作;只有当主电机停止时,才能进行换辊操作。
机架锁紧1.电气元件9个锁紧缸电磁阀,每个机架1个,为双线圈电磁阀2.功能描述每架轧机设4个锁紧缸,2个在入口侧,2个在出口侧锁紧缸有杆腔进油时,机架被松开并可移动锁紧缸无杆腔进油时,机架被锁紧每架轧机的锁紧缸由一个双电控阀控制3.操作工的控制装置在主操作室上:仅设定“就地操作”方式选择主操作室不进行操作“机架未锁紧”指示(CRT)无线遥控操作箱1个选择开关,用于“机架”及“机旁闭锁”选择1个“锁紧”按钮1个“松开”按钮“锁紧”、“松开”指示机架横移电气元件9个双线圈电磁阀,每个机架1个功能描述双线圈中的一个得电,机架“推进”;另一个得电,机架“拉出”3. 操作工的控制装置在主操作室上:仅设定“就地操作”方式选择不进行操作无线遥控操作箱:1个选择开关,用于“机架”和“机旁闭锁”选择1个按钮,机架“推进”1个按钮,机架“拉出”接轴托架与轧机机架的联接电气元件9个双线圈电磁阀,控制插销缸,每架轧机1个功能描述每个接轴托架上设1个液压插销缸轧机工作和机架横移时,插销杆必须处于伸出状态,将机架与接轴托架联接在一起只有在机架“推出”轧线进行换辊时,活塞杆方可收回;此时,机架与接轴托架“松开”操作工的控制装置A.主操作室上不进行操作仅设定“就地操作方式”设9个指示灯,“插销缸未伸出”(CRT)B.无线遥控操作箱1个机架选择开关1个按钮“缸伸出”1个按钮“缸收回”“收回”显示轧辊压下装置电气元件9个双线圈电磁阀,每个机架1个功能描述通过压下机构实现上辊的径向调整液压马达压下液压马达设在轧机传动侧3. 操作工的控制装置在主操作室上不进行操作仅设定“就地操作”方式选择无线遥控操作箱1个选择开关,用于“机架”和“机旁闭锁”选择1个按钮“抬起”1个按钮“压下”轧机齿轮箱稀油润滑电气元件•9个电接点压力表,每架轧机1个•9个油流信号器,每架轧机1个功能描述•用于稀油润滑低压报警轧机区设备控制功能说明书C.S.002立式轧机1.概述立式轧机共7架●2V、4V为Φ610mm轧机●6V为Φ530mm轧机●8V、10V、12V为Φ470mm轧机●14V为Φ380mm轧机每架立式轧机由以下几部分组成:●底座●换辊小车●拉扞和轧辊组(机架)●锁紧装置●横移液压缸,布置在轧机传动侧(上方)●液压马达(手动)压下机构●上下辊弹性阻尼减振器平衡●万向接轴托架装置2.电气元件详见电机表及各分项描述3.功能描述换孔型的工作过程●机架锁紧液压缸松开;●横移液压缸动作,驱动轧机在底座上下移动以对中孔型;●机架锁紧缸闭合,锁紧轧机。
某厂优质棒材轧线的技术特点

某厂优质棒材轧线的技术特点【摘要】本文介绍了某厂优质棒材轧线的生产工艺、设备装备及技术特点。
【关键词】优质棒材;设备;技术;特点0 前言某厂优质棒材工程于2013年6月投产。
本项目是其产品结构优化调整,淘汰落后、新建等量产能替换项目。
本项目从热送辊道至精轧机组的采用国产设备,其减定径机组、轧线控冷区域和精整区,采用引进工艺技术和关键设备。
1 产品及原料设计年产量为80万吨,产品规格品种为Ф14~70mm的直条光面圆钢。
主要钢种:优质碳素结构钢、冷镦钢、弹簧钢、轴承钢、易切削钢和合金结构钢等。
使用的全部为合格连铸方钢坯,断面尺寸:220×260×10000mm,单根坯料重量:4400kg。
2 轧线主要设备车间工艺平面布置简图见图1。
2.1 钢坯加热炉轧线设1座燃高炉煤气侧进、侧出的双蓄热步进梁式加热炉,采用汽化冷却。
炉型:步进梁式加热炉加热炉尺寸:有效长:41m、内宽:10.8m采用变频调速的单独传动悬臂辊道装出炉,侧进侧出。
加热炉设计主要特点:(1)采用高产、低耗、自动化程度高、生产灵活的侧进侧出步进梁式加热炉;(2)加热炉的水梁和立柱采用汽化冷却;(3)采用错位梁技术和高温段水梁采用骑卡安装的高合金耐热垫块;(4)设置第一加热段、第二加热段、均热段三个控制段进行炉温和空燃比自动控制;(5)采用蓄热式热回收和换向燃烧技术,空煤气双蓄热,预热温度约1000℃,排烟温度降低到180℃以下;(6)采用蜂窝体蓄热式烧嘴结构,单个烧嘴的蜂窝体检修方便,可单独更换;(7)采用分段分侧换向技术,管路较为简单;(8)采用先进、实用、可靠的加热炉自控装置,换向系统自动控制,具有定时换向,顺序换向、超温强迫换向等功能,操作方便可靠;(9)配备先进的加热炉自动化系统,由PLC集中控制管理加热炉各系统和过程。
加热炉实现三段炉温自动控制,以适应钢坯装炉温度的变化和产量变化,对钢坯实行有效灵活的加热。
2.2 轧机选型及主要技术参数生产线设26架轧机,其中1H~21V为无牌坊短应力线轧机,5机架三辊减定径机组。
现代化小型棒材车间工艺与设备特点

现代化小型棒材车间工艺与设备特点(中冶东方工程技术有限公司,内蒙古,包头 014010)摘要:文章结合山西宏阳钢铁有限公司年产95万t的棒材车间的工艺与装备,介绍了现代化小型棒材车间的工艺与设备特点。
关键词:小型棒材车间;工艺;设备中图分类号:TG333 文献标识码:A 文章编号:1007—6921(XX)11—0083—02我国是一个发展中的大国,消费市场巨大,随着这些年经济建设的发展,对钢铁的需求,特别是对线棒材需求量不断加大,国此各个钢厂也争先恐后地新上了许多棒材生产线,提高棒材的产量,以满足不断扩大的市场需求,市场的需求也向我们提出了新的课题,怎样提高轧机的产量及产品精度,提高轧机的效能及成材率等等这些问题就摆在我们的面前,综观近年来国内外新建小型轧钢车间的技术及装备,当前小型轧机的发展方向是以连铸化无扭连轧为基础,采用热送热装。
轧钢工艺的发展也主要围绕着三高技术开展,即:高性能,高精度,高效率。
本文结合山西宏阳钢铁公司棒材车间的技术及装备来介绍。
1 现代化小型棒材车间的工艺特点1.1 连铸坯热送连铸坯热送连铸连轧是当今冶金工业的发展方向。
实现热送热装可作为连铸连轧的第一步,热送连铸坯的温度>400℃,即能达到一定的节能效果。
采用直接热装的优点是:①减少加热炉燃料消耗,提高了加热炉的产量,可降低燃料消耗30%~45%。
中国钢铁工业10年来产量翻了一番,而钢铁工业总能耗仅增加了34%,这是10年来中国钢铁工业持续增长的一个重要原因。
其中采用连铸连轧带来的能源大量节约是功不可没的。
②减少加热时间及金属消耗,一般可比冷装减少0.1%~0.3%的金属消耗。
③减少了钢坯库存量、厂房面积和起重设备,减少人员、降低建设投资和生产成本。
④缩短了生产周期。
⑤生产实践经验表明,直接热装还可以减少钢坯表面裂纹,提高金属收得率。
山西宏阳钢铁公司棒材车间加热炉上料方式为热坯上料。
连铸机拉出的热连铸坯每四根一组经过渡台架送到上料辊上,由上料辊道关往钢坯称进行称重,称重后送往加热炉炉尾,被固定热源板停止,然后由推钢机推入加热炉内进行加热。
pqf连轧管机芯棒运行的方式和特点

pqf连轧管机芯棒运行的方式和特点连轧管机芯棒是指用于连续轧制管材的机械设备,它的运行方式和特点对于提高管材生产效率和质量具有重要意义。
一、连轧管机芯棒的运行方式:连轧管机芯棒是通过一系列轧制工序,将毛坯经过多次轧制、拉伸和收卷等操作,逐步变成成品管材的过程。
具体的运行方式如下:1. 上料:将原料毛坯装载到机械设备的进料轧辊上,通过传送带或者其他装置将毛坯送入轧机的工作区域。
2. 热轧:毛坯经过预热处理后,进入热轧轧机。
在高温状态下,通过一对或多对轧辊的旋转,将毛坯连续轧制成管材。
热轧过程中,轧机会产生巨大的压力,将毛坯逐渐拉长并形成管状。
3. 冷轧:热轧后的管材需要经过冷轧工序,以提高管材的质量和精度。
冷轧一般采用两辊式或三辊式轧机,通过辊轧的方式将管材进一步拉伸和整形,使其尺寸更加准确,表面更加光滑。
4. 拉伸:冷轧后的管材经过拉伸工序,通过拉伸机将管材拉长,使其达到所需的长度。
拉伸过程中,管材会受到较大的拉力,从而改变其晶粒结构,提高其力学性能和物理性能。
5. 直条切割:拉伸后的管材经过切割工序,将长条状的管材切割成所需长度的管材。
切割一般采用机械切割或者火焰切割等方式。
6. 收卷:切割后的管材经过收卷工序,将其卷绕成卷筒状,便于储存和运输。
收卷一般采用卷取机或卷曲机等设备。
二、连轧管机芯棒的特点:连轧管机芯棒具有以下几个特点,使其在管材生产中得到广泛应用:1. 高效率:连轧管机芯棒采用连续生产方式,可以实现高速轧制管材。
相比于传统的离散生产方式,连轧机具有更高的生产效率和更低的能耗。
2. 精度高:连轧管机芯棒通过精密的控制系统,可以实现对管材尺寸和形状的高度控制,保证管材的精度和一致性。
3. 管材质量好:连轧管机芯棒通过热轧、冷轧和拉伸等多道工序的处理,可以改善管材的组织结构和性能,提高管材的强度、韧性和耐腐蚀性。
4. 适用范围广:连轧管机芯棒可以轧制各种材质的管材,包括碳钢、合金钢、不锈钢等。
pqf连轧管机芯棒运行的方式和特点

pqf连轧管机芯棒运行的方式和特点连轧管机芯棒是一种用于连续轧制管材的设备。
它由一系列的轧辊和辊道组成,通过对材料进行连续轧制,以使其形成所需的管材。
连轧管机芯棒的运行方式和特点对于了解该设备的工作原理和优势非常重要。
连轧管机芯棒的运行方式主要包括进料、轧制和出料三个过程。
首先,原材料进入机芯棒,经过切割和加热后,进入轧辊。
轧辊通过对材料进行辊压,使其逐渐变形为所需的管材形状。
然后,经过一系列的轧制过程,管材在机芯棒中逐渐成形。
最后,成形的管材从机芯棒的出料端排出。
连轧管机芯棒的特点有以下几个方面。
连轧管机芯棒具有高效性。
由于连续的轧制过程,机芯棒能够实现高速生产,大大提高了生产效率。
相比传统的离散轧制方式,连轧管机芯棒可以连续轧制多个管材,减少了生产中的停机时间,提高了生产效率。
连轧管机芯棒具有高精度性。
轧辊和辊道的设计和加工精度决定了轧制出的管材的精度。
连轧管机芯棒采用精密的轧辊和辊道,能够实现高精度的轧制,保证了管材的质量和尺寸的一致性。
连轧管机芯棒具有高稳定性。
机芯棒采用连续的轧制方式,材料在整个轧制过程中保持连续的运动,减少了材料的变形和变形的不均匀性。
同时,机芯棒采用稳定的辊道和辊压力控制装置,能够确保轧制过程的稳定性和一致性。
连轧管机芯棒具有灵活性。
机芯棒可以根据不同的轧制需求调整辊道和轧辊的布局和设置,以适应不同材料和管材的轧制需求。
这种灵活性使得机芯棒能够适应不同的生产要求,提高了生产的灵活性和适应性。
连轧管机芯棒具有节能性。
机芯棒采用先进的辊道设计和轧辊材料,降低了能量损失,减少了能源消耗。
同时,机芯棒还采用了先进的控制系统,能够对轧制过程进行精确的控制和调节,减少了能源的浪费。
连轧管机芯棒是一种高效、高精度、高稳定性、灵活性和节能的轧制设备。
它通过连续的轧制过程,实现了高速、高精度的管材生产,适应了不同的生产需求。
连轧管机芯棒在管材生产领域具有重要的应用价值,对于提高管材生产的效率和质量有着重要的意义。
棒材热轧机的特点是什么

棒材热轧机的特点是什么
目前,我国在钢筋轧制生产线中,已基本实现了主要工序主体装
备国产化,棒、线材生产线主体装备已达到国际先进水平。
新型国产
高刚度轧机、悬臂式辊环轧机、精密轧制设备、各类控制冷却装置、
各类飞剪机、锯切装置、多种结构类型的冷床等装备广泛应用于国内
外轧钢生产线,基本取代了同类进口产品,为国家冶金工业发展做出
了突出贡献。
1、以连铸坯为原料,一火轧成,生产成本低。
2、连铸与加热炉紧凑布置,连铸坯热送热装,节能达到30%—45%。
3、步进式加热炉加热,加热均匀,自动化程度高。
4、炉后设高压水除鳞装置,提高了表面质量。
5、轧线18个机架平/立交替布置,全线采用无扭转轧制,生产事故少,效率高。
6、轧机采用短应力线轧机,轧机刚度高,辊缝对称调整操作方便,机架整体更换,轧辊孔型和导卫在轧辊间调整,在线调整少。
7、轧线主传动采用直流传动或交流调速传动,实现轧线速度无级调速。
8、采用切分轧制工艺生产钢筋。
9、采用步进式冷床,冷却效率高,冷却质量好。
棒材厂全连轧线工艺设备特点及改造措施
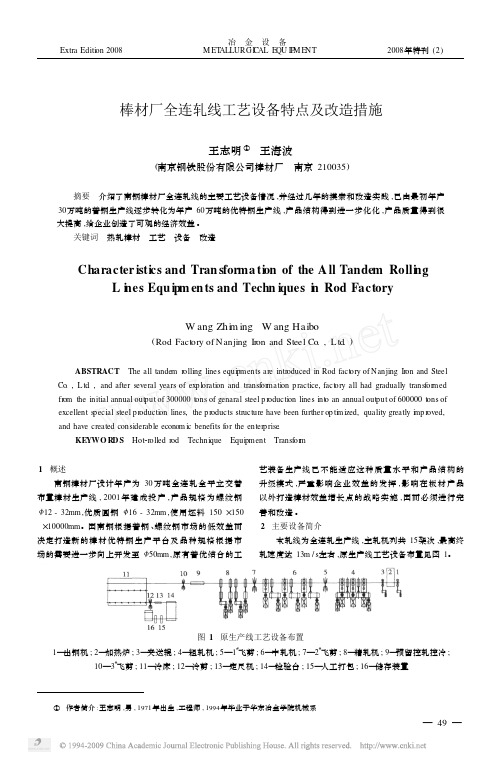
棒材厂全连轧线工艺设备特点及改造措施王志明① 王海波(南京钢铁股份有限公司棒材厂 南京210035)摘要 介绍了南钢棒材厂全连轧线的主要工艺设备情况,并经过几年的摸索和改造实践,已由最初年产30万吨的普钢生产线逐步转化为年产60万吨的优特钢生产线,产品结构得到进一步化化,产品质量得到很大提高,给企业创造了可观的经济效益。
关键词 热轧棒材 工艺 设备 改造Character isti cs and Tran sforma ti on of the A ll Tandem Rolli n gL i n es Equ i p m en ts and Techn i ques i n Rod FactoryW ang Zhi m ing W ang Haibo(Rod Fact ory of Nanjing Ir on and Steel Co .,L td .)ABSTRACT The all tande m r olling lines equi pments are intr oduced in Rod fact ory of Nanjing Ir on and Steel Co .,L td .,and after several years of exp l orati on and transfor mati on p ractice,fact ory all had gradually transf or med fr om the initial annual out put of 300000t ons of genaral steel p r oducti on lines int o an annual out put of 600000t ons of excellent s pecial steel p r oducti on lines,the p r oducts structure have been further op ti m ized,quality greatly i m p r oved,and have created considerable econom ic benefits f or the enter p rise .KE YWO R D S Hot 2r olled r od Technique Equi pment Transfor m1 概述南钢棒材厂设计年产为30万吨全连轧全平立交替布置棒材生产线,2001年建成投产,产品规格为螺纹钢<12-32mm ,优质圆钢<16-32mm ,使用坯料150×150×10000mm 。
概述优质钢棒材轧线的技术特点

概述优质钢棒材轧线的技术特点02优质钢棒材生产线,其中轧线主要机械设备和生产工艺技术从意大利DANIELI公司引进,电气传动和自动控制设备由ABB公司供货。
其余部分设备为国内公司供货。
本生产线具备典型的生产优质合金钢棒材的技术特点。
1轧线主要设备1.1钢坯加热炉采用两段梁步进梁加热炉1座,炉内悬臂辊道侧进侧出。
加热炉以高焦混合煤气为燃料。
加热炉能力:额定160t/h(冷装碳素结构钢)。
最大180t/h(冷装碳素结构钢)。
加热炉分均热段、加热段、预热段3个燃烧控制段和不供热段,以满足合金钢加热要求。
炉底步进机构由液压驱动。
加热炉设备顺控和燃烧控制采用PLC控制。
1.2轧机采用16架平/立交替布置的高刚度短应力线轧机加减径定径机组,按8+8+减定径机布置,可以用200mm×200mm钢坯生产产品大纲规定的所有产品。
200mm×200mm、160mm×160mm钢坯采用同一生产孔型系统,实现全线无扭轧制。
所有产品都从减定径机轧出。
轧机规格:Ф700/Ф610×760mm 4架Ф530/Ф460×760mm 4架Ф430/Ф370×650mm 8架二辊预应力定径机:Ф380/Ф340×400mm3架四辊高精度定径机:Ф380/Ф350×70mm1架设计最大精轧速度为15m/s。
1.3控轧控冷设备中轧机至减定径机间设置控轧水箱,减径定径机出口设置控制冷却水箱,轧线设置较完善的控轧控冷设备。
中轧机至减定径机间设置2个水冷段,第一段为3个水箱,第二段为2个水箱,均温距离约83m,可以实现减定径机的热机轧制。
减径定径机出口至倍尺飞剪间设置2个水冷段,每段1个水箱,对有些品种实现控制冷却。
1.4剪机轧线共设剪机5台。
(1)3H轧机入口侧设液压摆式卡断剪1台,用于粗轧机故障时卡断轧件。
(2)粗轧出口设曲柄式切头飞剪,用于轧件切头及事故碎断。
- 1、下载文档前请自行甄别文档内容的完整性,平台不提供额外的编辑、内容补充、找答案等附加服务。
- 2、"仅部分预览"的文档,不可在线预览部分如存在完整性等问题,可反馈申请退款(可完整预览的文档不适用该条件!)。
- 3、如文档侵犯您的权益,请联系客服反馈,我们会尽快为您处理(人工客服工作时间:9:00-18:30)。
棒材连轧生产设备特点概述
字数:3206 字号:大中小
摘要:本文介绍了当代国际先进水平的小型棒材连轧设备特点及主要技术参数,其中包括:步进梁式加热炉采用汽化冷却、红圈轧机、控制冷却、连续定尺剪切全部轧机和飞剪采用变频调速交流电机驱动等情况。
关键词:棒材;连轧机;工艺参数;设备特点
1概况
棒材连轧车间的加热炉改为步进梁式,采用汽化冷却。
轧机、飞剪、堆垛机、打捆机、液压及润滑设备由国外引进,全部交流主电机、电气设备及计算机系统从德国SIMENS 公司引进。
这条连轧生产线的工艺及机、电设备都达到了90年代后期国际水平。
此条棒材生产线还为将来实现热送热装、高线大盘卷生产、型材生产、无头轧制、在线测径等工艺和技术预留了足够的位置。
同时设备设计充分考虑了将来生产其它产品时设备的兼容问题。
一、生产设备布置特点
车间原料跨距连铸成品跨只有6m,连铸坯由运送小车送来,再由天车吊至+5.0m平台上的冷装料台架;热送时则由保温辊道直接送来,再由提升机提升至+5.0m平台上。
当轧机产量不超过连铸机产量时可实现连续热装。
从上料开始即对坯料进行全线自动跟踪,实现炉批号的自动化管理。
采用汽化冷却的步进梁式加热炉、不仅可节能而且加热质量高,入出炉均采用炉内悬。
全线18架轧机采用平-立交替布置,第14、16、18架为平/立转换机架,以实现带肋钢筋切分、扁钢及型钢生产工艺的最佳化。
红圈轧机刚度高,可采用低温轧制工艺,不仅可节能而且金属烧损少,视钢种不同,开轧温度在900~950℃,相应的金属烧损为0.6%~0.7%。
1~10架轧机为微张力控制,10~18架为立活套控制(切分时末2架也采用活套控制),实现无张力轧制,以保证产品精度,产品尺寸偏差可达到1/3DIN标准公差范围的水平。
对带肋钢筋进行轧后余热淬火加芯热回火处理,可使带肋钢筋的综合力学性能提高1~2级。
倍尺剪采用优化剪切技术,可使上
冷床的倍尺都为定尺的整数倍,、且每支坯只出1支短定尺,从而提高了成材率及产品定尺率。
冷床为步进齿条式,产品冷却质量高,性能均匀。
冷床具有根据要求自动编组的功能,方便定尺剪切操作。
生产线上设置3台计数器、对棒材可实现自动计数、成捆包装,扁钢产品可自动堆垛,将来生产型钢时稍添加配件即可实现型钢的自动堆垛。
打捆也由打捆机自动完成。
孔型系统采用椭圆-圆系统,轧件变形均匀,易于调整,可减少换辊次数,提高作业率。
粗轧前4架为平辊无槽轧制,备辊简单,辊耗低,且有利于氧化铁皮脱落。
对小规格带肋钢筋(Φ10~Φ16mm)进行3线或2线切分生产,可大大提高轧机生产率,平衡轧机的小时产量,减少轧制道次,提高坯料的热装热送率。
Φ14、Φ16mm钢筋为2线切分,最末机架为立式布置。
二、主要设备特点
1加热炉
(1)有效面积为24m×12.8m,单排装料侧进侧出,燃料为高、焦炉混合煤气,热值1800×4.18kJ/m3,设有一、二级自动控制(二级为燃烧优化及生产管理系统)。
产量150t/h,最大为170t/h。
(2)入炉辊道中设有坯料称重测长装置,可记录每支坯料的重量及在炉内的准确定位。
(3)装配有目前先进的汽化冷却技术,既节水节能,又提高了加热质量。
2轧机
(1)全线18架轧机分为粗、中、精轧3组,每组6架,全部为红圈轧机(二辊短应力线)。
其特点是普碳钢轧机按合金钢轧机选型,刚度高,将来可扩大品种生产合金钢产品。
轧辊为双支撑多轧槽,四列短圆柱轴承,上下辊由液压马达对称调整辊缝。
轧槽的更换由液压横移来实现,机架还设有轧辊轴向调整装置,轧辊和导卫的安装均在轧辊间内完成,1~10架由天车整机架吊换,11~18架为快速换机架小车完成机架更换。
18架轧机均采用单独的变频调速交流电机驱动,轧辊轴承全部为油-气润滑。
(2)主轧机基本性能参数见表2。
3飞剪
(1)全线共有4台飞剪、1#、2#剪具有切头尾及碎断功能,3#剪为组合式倍尺飞
剪,除切倍尺外,还具有切头尾和碎断功能。
(2)飞剪技术性能见表3。
4穿水冷却装置
(1)位于精轧机组之后,用于Φ10~Φ40mm带肋钢筋的轧后余热淬火和芯热回火处理。
该装置由4条水冷线、3条通道和1条辊道安装在同一小车上组成,其中3条水冷线用于2~3线切分带肋钢筋的水冷,1条用于非切分带肋钢筋的水冷,3条通道和辊道用于将不穿水产品送至冷床。
小车可横移实现水冷线和辊道的相互更换,方便生产组织。
(2)水冷线采用THERMEX专利技术,闭环控制,总长35m,沿轧制方向分为5段,以冷却不同规格的产品。
水量为750m3/h,水压为2.4MPa,可将轧件表层由950℃剧冷至250℃,使冷却速度大于形成马氏体的临界速度,从而在轧件表层一定深度内形成马氏体组织。
5冷床
(1)冷床为步进齿条式,宽度方向分3段由变频调速交流电机驱动。
出口侧设有齐头辊道,倍尺对齐后被托起,减少轧件与对齐辊面之间的磨损。
入冷床辊道中有3块电磁裙板,用于穿水轧件的制动。
冷床输出辊道中有2个电磁辊,保证轧件在连续切定尺过程中头部齐整。
(2)冷床面积为12.5m×120m,齿数73个,齿槽宽110mm,输入侧齿条间距为200mm,动齿条最小动作周期为3s,输入轧件速度为3~18m/s,输出辊道速度为1~2.5m/s,对齐辊速度为0.3~1m/s,开设8个槽。
6自动磁性堆垛机
自动磁性堆垛机属简单堆垛机,位于定尺收集框处,共2台,用于扁钢和大圆钢(≥Φ32mm)的自动堆垛,每台可分成2段单独使用,收集双排6m定尺,也可作为一台使用,收集大于7m的定尺材。
将来生产型钢时,添加部分配件即可实现型钢堆垛。
堆垛捆重1~5t,每捆尺寸(150~400)mm×(150~400)mm,捆长12m。
7自动打捆机
(1)定尺成捆后,由打捆机自动完成捆扎,每个收集台架配2台打捆机,间距可调,以实现腰之间的间距均匀。
(2)为OMV型棒材打捆机,可打单腰或双腰(即一次绕2圈绑丝),打捆周期:单腰为7.5s,双腰为9.5s,捆直径Φ150~Φ350mm,捆重1~5t。
三、自动化控制系统
此轧线采用具有当今世界先进水平的自动化控制系统,分一、二两级,由德国SIMENS 公司设计制造。
两级控制的主要功能如下。
1二级自动控制
主要用于车间的生产管理,有物料跟踪,生产程序表及生产报表的自动生成、贮存和打印,故障报警的显示记录。
2一级自动控制
主要功能有:(1)炉内钢坯自动定位;(2)图形化人机界面,以图来显示轧线的运行状态并对轧线进行组态及设定;(3)级联控制;(4)轧件信号跟踪及自动废品检测;(5)微张力和活套控制,以及动态速降补偿;(6)紧急停车后的轧辊自动打开;(7)轧线自适应控制,可自动消除人的设定及轧辊的磨损所带来的误差,控制系统使工艺参数(辊缝、断面面积及形状、速度等)自动调整到最佳状态;(8)飞剪控制及优化剪切;(9)虚拟轧制,模拟钢坯通过轧线来检验轧线的辅助设施工作是否正常;(10)事件记录及趋势记录;(11)通讯接口。
四、结论
这条生产线为外资贷款、主要关键设备为引进的项目,其工艺技术代表着棒材连轧的国际先进水平。
它的建成投产将为改变品种结构,提高产品质量,增强企业的市场竞争力打下坚实的基础。
也可为其他冶金企业棒材连轧生产线的建设提供参考。