辊压机预粉磨技术
辊压机技术
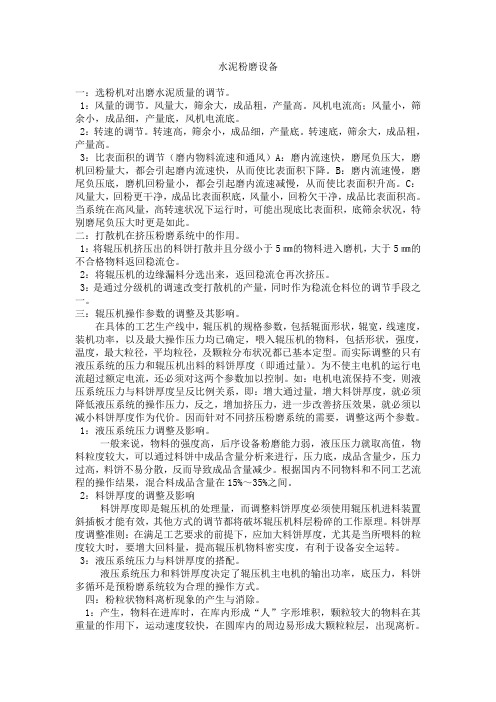
水泥粉磨设备一:选粉机对出磨水泥质量的调节。
1:风量的调节。
风量大,筛余大,成品粗,产量高。
风机电流高;风量小,筛余小,成品细,产量底,风机电流底。
2:转速的调节。
转速高,筛余小,成品细,产量底。
转速底,筛余大,成品粗,产量高。
3:比表面积的调节(磨内物料流速和通风)A:磨内流速快,磨尾负压大,磨机回粉量大,都会引起磨内流速快,从而使比表面积下降。
B:磨内流速慢,磨尾负压底,磨机回粉量小,都会引起磨内流速减慢,从而使比表面积升高。
C:风量大,回粉更干净,成品比表面积底,风量小,回粉欠干净,成品比表面积高。
当系统在高风量,高转速状况下运行时,可能出现底比表面积,底筛余状况,特别磨尾负压大时更是如此。
二:打散机在挤压粉磨系统中的作用。
1:将辊压机挤压出的料饼打散并且分级小于5㎜的物料进入磨机,大于5㎜的不合格物料返回稳流仓。
2:将辊压机的边缘漏料分选出来,返回稳流仓再次挤压。
3:是通过分级机的调速改变打散机的产量,同时作为稳流仓料位的调节手段之一。
三:辊压机操作参数的调整及其影响。
在具体的工艺生产线中,辊压机的规格参数,包括辊面形状,辊宽,线速度,装机功率,以及最大操作压力均已确定,喂入辊压机的物料,包括形状,强度,温度,最大粒径,平均粒径,及颗粒分布状况都已基本定型。
而实际调整的只有液压系统的压力和辊压机出料的料饼厚度(即通过量)。
为不使主电机的运行电流超过额定电流,还必须对这两个参数加以控制。
如:电机电流保持不变,则液压系统压力与料饼厚度呈反比例关系,即:增大通过量,增大料饼厚度,就必须降低液压系统的操作压力,反之,增加挤压力,进一步改善挤压效果,就必须以减小料饼厚度作为代价。
因而针对不同挤压粉磨系统的需要,调整这两个参数。
1:液压系统压力调整及影响。
一般来说,物料的强度高,后序设备粉磨能力弱,液压压力就取高值,物料粒度较大,可以通过料饼中成品含量分析来进行,压力底,成品含量少,压力过高,料饼不易分散,反而导致成品含量减少。
水泥辊压机预粉磨系统的工艺计算
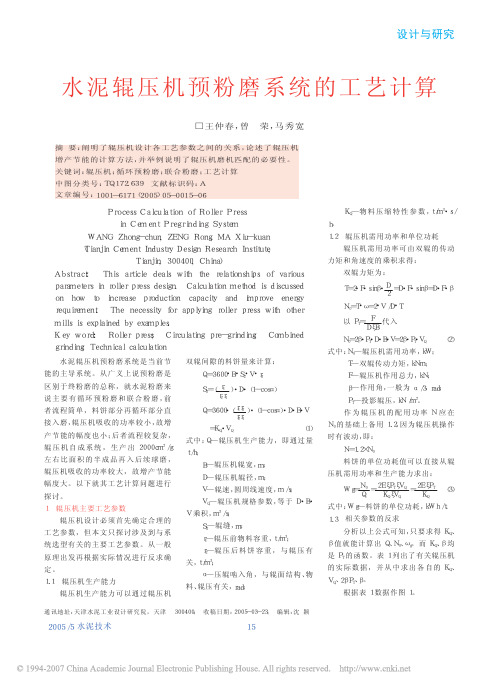
水泥辊压机预粉磨系统是当前节能的主导系统。
从广义上说预粉磨是区别于终粉磨的总称,就水泥粉磨来说主要有循环预粉磨和联合粉磨,前者流程简单,料饼部分再循环部分直接入磨,辊压机吸收的功率较小,故增产节能的幅度也小;后者流程较复杂,辊压机自成系统,生产出2000cm2/g左右比面积的半成品再入后续球磨,辊压机吸收的功率较大,故增产节能幅度大。
以下就其工艺计算问题进行探讨。
1辊压机主要工艺参数辊压机设计必须首先确定合理的工艺参数,但本文只探讨涉及到与系统选型有关的主要工艺参数。
从一般原理出发再根据实际情况进行反求确定。
1.1辊压机生产能力辊压机生产能力可以通过辊压机双辊间隙的料饼量来计算:Q=3600・B・S2・V・r2S2=(r1r2r1)・D・(1-cosα)Q=3600・(r1r2r2r1)・(1-cosα)・D・B・V=KQ・VQ(1)式中:Q—辊压机生产能力,即通过量t/h;B—辊压机辊宽,m;D—辊压机辊径,m;V—辊速,圆周线速度,m/s;VQ—辊压机规格参数,等于D・B・V乘积,m3/s;S2—辊缝,m;r1—辊压前物料容重,t/m3;r2—辊压后料饼容重,与辊压有关,t/m3;α—压辊啮入角,与辊面结构、物料、辊压有关,rad;KQ—物料压缩特性参数,t/m3・s/h。
1.2辊压机需用功率和单位功耗辊压机需用功率可由双辊的传动力矩和角速度的乘积求得:双辊力矩为:T=2・F・sinβ・D2=D・F・sinβ=D・F・βN0=T・ω=2・V/D・T以PT=FDξB代入N0=2β・PT・D・B・V=2β・PT・VQ(2)式中:N0—辊压机需用功率,kW;T—双辊传动力矩,kNm;F—辊压机作用总力,kN;β—作用角,一般为α/3,rad;PT—投影辊压,kN/m2。
作为辊压机的配用功率N应在N0的基础上备用1.2,因为辊压机操作时有波动,即:N=1.2×N0料饼的单位功耗值可以直接从辊压机需用功率和生产能力求出:Wg=N0Q=2EξPTξVQKQξVQ=2EξPTKQ(3)式中:Wg—料饼的单位功耗,kWh/t。
关于预粉磨系统的联想
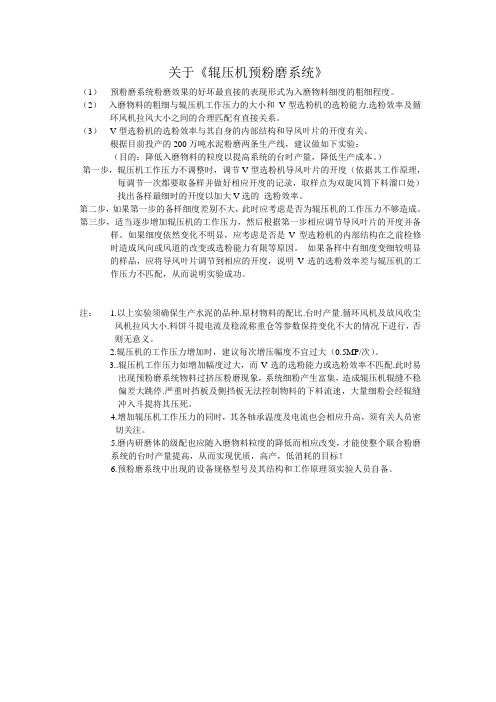
关于《辊压机预粉磨系统》(1)预粉磨系统粉磨效果的好坏最直接的表现形式为入磨物料细度的粗细程度。
(2)入磨物料的粗细与辊压机工作压力的大小和V型选粉机的选粉能力.选粉效率及循环风机拉风大小之间的合理匹配有直接关系。
(3)V型选粉机的选粉效率与其自身的内部结构和导风叶片的开度有关。
根据目前投产的200万吨水泥粉磨两条生产线,建议做如下实验:(目的:降低入磨物料的粒度以提高系统的台时产量,降低生产成本。
)第一步,辊压机工作压力不调整时,调节V型选粉机导风叶片的开度(依据其工作原理,每调节一次都要取备样并做好相应开度的记录,取样点为双旋风筒下料溜口处)找出备样最细时的开度以加大V选的选粉效率。
第二步,如果第一步的备样细度差别不大,此时应考虑是否为辊压机的工作压力不够造成。
第三步,适当逐步增加辊压机的工作压力,然后根据第一步相应调节导风叶片的开度并备样。
如果细度依然变化不明显,应考虑是否是V型选粉机的内部结构在之前检修时造成风向或风道的改变或选粉能力有限等原因。
如果备样中有细度变细较明显的样品,应将导风叶片调节到相应的开度,说明V选的选粉效率差与辊压机的工作压力不匹配,从而说明实验成功。
注: 1.以上实验须确保生产水泥的品种.原材物料的配比.台时产量.循环风机及放风收尘风机拉风大小.料饼斗提电流及稳流称重仓等参数保持变化不大的情况下进行,否则无意义。
2.辊压机的工作压力增加时,建议每次增压幅度不宜过大(0.5MP/次)。
3..辊压机工作压力如增加幅度过大,而V选的选粉能力或选粉效率不匹配.此时易出现预粉磨系统物料过挤压粉磨现象,系统细粉产生富集,造成辊压机辊缝不稳偏差大跳停.严重时挡板及侧挡板无法控制物料的下料流速,大量细粉会经辊缝冲入斗提将其压死。
4.增加辊压机工作压力的同时,其各轴承温度及电流也会相应升高,须有关人员密切关注。
5.磨内研磨体的级配也应随入磨物料粒度的降低而相应改变,才能使整个联合粉磨系统的台时产量提高,从而实现优质,高产,低消耗的目标!6.预粉磨系统中出现的设备规格型号及其结构和工作原理须实验人员自备。
不同辊压机水泥粉磨流程节电
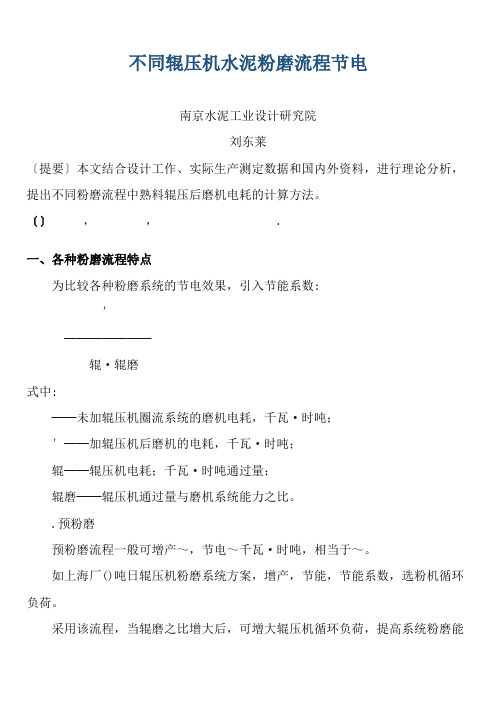
不同辊压机水泥粉磨流程节电南京水泥工业设计研究院刘东莱〔提要〕本文结合设计工作、实际生产测定数据和国内外资料,进行理论分析,提出不同粉磨流程中熟料辊压后磨机电耗的计算方法。
〔〕,, .一、各种粉磨流程特点为比较各种粉磨系统的节电效果,引入节能系数:′───────辊·辊磨式中:──未加辊压机圈流系统的磨机电耗,千瓦·时吨;′──加辊压机后磨机的电耗,千瓦·时吨;辊──辊压机电耗;千瓦·时吨通过量;辊磨──辊压机通过量与磨机系统能力之比。
.预粉磨预粉磨流程一般可增产~,节电~千瓦·时吨,相当于~。
如上海厂()吨日辊压机粉磨系统方案,增产,节能,节能系数,选粉机循环负荷。
采用该流程,当辊磨之比增大后,可增大辊压机循环负荷,提高系统粉磨能力,系统单位电耗降低,如表所示。
值得注意的是,西班牙厂与厂磨机功率相近,但前者宽径比大();后者宽径比小(),辊压机配用功率×千瓦,比前者大,节能系数不如前者大(后者,前)。
说明加大辊压机宜增加宽径比。
表.混合式粉磨系统混合式粉磨系统可节能~,提高产量~。
该系统是将系统的粗料返回辊压机重新辊压,返回的粗料为来自选粉机的粗料和辊压机面的边缘料。
混合式粉磨系统选粉机的回料含细粉多,小于微米约,半终粉磨则不超过。
如图所示。
当无辊压机边料循环时,不宜返回太多,因为过多的细粉很难在喂料系统中与粗料混合均匀。
可控制在~的选粉粗料。
辊压机有边缘回料可适当提高这个比例,但不宜大于。
辊压机边缘料循环的优点:料仓料混合均匀,机器运转平稳,电流波动小;入磨料粒度变小,增产节电。
产生边缘粗料的原因:由于进入辊压机物料受压不均,压力由中间向两端降低。
中间压力大,物料流速慢,边缘流速大。
产生所谓“边界效应”。
根据我院在木渎厂辊压机实测,辊压后成品(中间料饼)与未压好的边料(散料)之比,竟达~比~。
图是辊压机无循环时,出辊压机料及入辊压机料的粒度组成曲线。
水泥辊压机终粉磨工艺的实践

水泥辊压机终粉磨工艺的实践
水泥辊压机终粉磨工艺是水泥生产过程中的重要环节,主要用于将水泥生产过程中的粗磨料进行细磨,以获得所需的最终产品质量。
在水泥辊压机终粉磨工艺的实践中,一般包括以下几个步骤:
1. 进料系统:将粗磨料通过搬运设备输送到辊压机的进料口,确保料流的稳定和连续。
2. 辊压系统:在辊压机中,通过辊子的压力和摩擦力,将粗磨料进行细磨。
辊压机内部通常包含两个或三个磨辊,它们之间的间隙可以调节,以控制磨碎程度。
3. 分选系统:在辊压机的出料口附近设置分选器,通过分离出不符合要求的粉末颗粒,确保终粉产品的粒度分布符合要求。
4. 输送系统:将终粉产品通过输送设备输送到储存仓或装车点,以备后续使用或销售。
在实践中,水泥辊压机终粉磨工艺需要根据具体水泥生产线的情况和产品要求进行相应的调整和优化。
主要考虑以下几个因素:
1. 辊压机参数的调整:包括磨辊间隙、磨辊转速、辊压力等参数的设定,以使得磨磨料达到期望的细度和稳定性。
2. 分选系统的优化:通过调整分选器的风速和篦板的布局,控制终粉产品的粒度分布。
3. 辅助设备的配合:如加热设备、冷却设备等,用于控制辊压机的温度和磨磨料的湿度,以保证终粉产品的质量稳定。
总之,在水泥辊压机终粉磨工艺的实践中,需要根据具体情况进行调整和优化,以获得最佳的终粉产品质量和产能。
辊压机在水泥粉磨系统中的应用

!$!$!
操作控制 在正常操作控制过程中 ! 只须监控设备状态和调节一
些过程参数 " &% $ 辊压机喂料量 通过调节斜插板开度 " 开度大 ! 则喂料多 " 反之 ! 则喂 料少 " 主要依据辊压机功率决定 ! 一般为 *"")3*"67 时 ! 效 果最好 " &! $ 磨喂料量 通过调节入磨皮带转速 " 转速快 ! 则喂料多 " 反之 ! 则 喂料少 " 主要依据水泥磨能力来定 ! 取 **()5*( 为佳 "
!$!$%
开机投料 &% $ 水泥磨系统已经正常运转 " &! $ 辊压 机 系 统 所 属 机 ’ 电 ’ 仪 ’ 自 动 化 设 备 均 处 在 正
常状态 " &+ $ 现场巡检确认现场设备完好 " &# $ 中控 操 作 员 选 择 辊 压 机 系 统 程 序 组 ! 启 动 该 组 系 统设备 " &* $ 设备启动完毕 ! 检查确认各设备状态及参数 " 如均 处在正常状态 ! 则可进行喂料 " &5 $ 选择辊压机喂料阀门 ! 物料此时进入辊压机系统 " &3 $ 当称重仓料位达 3"( 时 !横插阀打开 " 操作员只须 缓慢打开斜插板进行喂料即可 "
)"!
辊间隙检测报警 当动辊一侧的轴承座或动辊整体后退量过大 ! 达到设
定保护值时 ! 该辊间隙检测报警 " 曾有一段时期 ! 该辊间隙 经常报警 ! 严重影响了生产 " 最终查明为检测辊间隙的探 针动作不灵活所致 " 通过更换新探针 !报警消除 "
孙天力-辊压机生料终粉磨操作手册
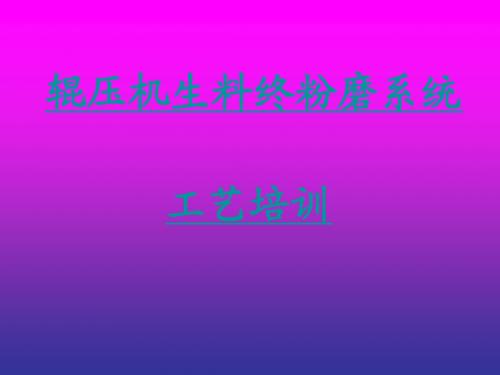
启动操作顺序
序号 操作步骤
1、定辊稀油站
检查与调整
1、检查油泵管路阀门 是否打开
2、动辊稀油站
8
3、如油温低,稀油站 2、检查油箱的温度, 油箱要加热 适时打开冷却水 4、干油润滑站 阀门
启动操作顺序
序号 操Байду номын сангаас步骤
液压系统启动
检查与调整
1、注意监测辊缝是否在要 求范围内
9
2、检查液压站油位和油温
2、金属探测器
11 3、电磁除铁器
4、定量给料机
启动操作顺序
序号 操作步骤 检查与调整
根据化验室的要求设定原料 配比 调整定量给料 机的供料比例 12
启动操作顺序
序号 操作步骤
设定喂料量
检查与调整
根据辊压机主电机的功率, 系统压力等随时调整喂料量
13
启动操作顺序
序号 操作步骤 打开稳流仓下气 动阀,调整辊压 机进料阀门 检查与调整 1、待稳流仓内物料在 60~70%时打开 2、保证辊压机饱和喂料 3、防止稳流仓满冒仓
启动操作顺序
序号 操作步骤
1、定辊主电机
检查与调整
1、注意启动电流 2、如果主机第一次未能 启动,检查后进行第二次 启动,两次启动要有一定 时间间隔
10
2、动辊主电机
启动操作顺序
序号 操作步骤
1、皮带输送机
检查与调整
1、长时间不喂料,辊 压机长时间空负荷 运行,电耗增加 2、为了减少磨机断料 时间,必须做好原 料调配站进料工作
序号 操作步骤 1、阀门 检查与调整 1、注意风机的启动电流, 待电流稳定后慢慢调速 2、通知废气处理系统注意 调整阀门和温度
5
2、风机
辊压机及其挤压粉磨工艺系统的操作

辊压机及其挤压粉磨工艺系统的操作1 前言挤压粉磨工艺是国际八十年代中期新开发的新型节能粉磨技术。
自1990年江苏省江阴市水泥厂国内第一台辊压机投产以来,在我国生产实际中应用已有多年的历史。
截止1995年11月的不完全统计,国内销售近二百台辊压机,已投产也有一百多台。
正如所有的新技术那样,辊压机在推广应用初期无论从设备还是工艺,都存在逐步认识与完善的过程,而经过几年的使用,经验得到积累,技术日臻完善。
随着辊面结构的改进和新技术新材料的应用,辊面磨损修复问题已逐步得到解决。
伴随着不同工艺系统的研究开发,挤压粉磨工艺的各项技术经济指标大幅度提高。
辊压机的操作方式也由于不同工艺流程,不同的物料情况,不同的设备配置方式而发生较大的变化,其突出特点之一就是在相同主电机功率条件下,辊压机液压系统的操作压力,料饼的厚度以及各种回料循环量等参数间的调节。
由压力和物料循环量的不同形成低压大循环和高压小循环为特征的操作方式。
辊压机设计参数之一就是单位辊宽线压力值,对Φ1000辊径的辊压机,单位辊宽线压力设计值为100kN/cm,正常操作在(40-80)kN/cm之间。
所谓低压一般为(40~60)kN/cm,高压为(60-80)kN/cm。
本文就不同情况下辊压机及其在不同工艺系统中的操作方式谈一些体会,以供使用辊压机的厂家参考。
2 辊压机操作参数的调整及其影响当一台辊压机应用于具体的工艺生产线中时,其规格参数,包括辊面形状、辊宽、线速度、装机功率以及液压系统最大操作压力均已确定。
喂入辊压机新鲜物料的物性,包括物料的形状、强度、温度、最大粒度、平均粒径及颗粒分布状况都已基本定型。
因而此时辊压机可以调整的参数,实际只有液压系统压力和辊压机出料的料饼厚度(即通过量)。
为不使主电动机的运行电流超过其额定电流,还必须对这两个参数的调整加以控制。
如果假设辊压机主电机电流保持不变,则液压系统的压力与料饼厚度呈反比例关系。
即增大通过量,增大料饼厚度,就必须降低液压系统的操作压力。
浅谈对带辊压机预粉磨水泥磨系统的操作

( 2)稳 流仓 高低 。
①称 重仓仓位大幅快速下降 ,确定粗粉 回料溜 子堵料 时 ,一定要保证稳 流仓有足够空间贮料 ( 以
"C n r l p rt n , o to ea i J O o
下 降 ,打散分级机 电流异常 ,出磨水泥细度变粗可 判断打散分级 机筛 网出现破洞 ,应立 即止料停机 , 待机修焊好筛网方可开机。
挤压联合粉磨系统中物料 的破碎及预粉磨 主要
是 由辊压 机 承担 ,磨 机 主 要发 挥 研 磨 作 用 ,所 以操
电流非常关键 ,操作 中应密切关注电流变化 ;确保 提升机 的正常运转是系统设备高运转率 的重要前 提
之一。
作 中应 多观察辊缝并及 时调准 ;导料板插入深度越 深 ,辊缝越小 ,辊压机功率越低 ,最终导致系统产
中控正常操作的控制参数见表2 。
表2 正常操作控 制参数 项目 控制参数 料饼斗提 辊 压机 电 电 流/ A 流/ A 3 5 30 2 0 2+5 辊压机液 压 力/ a MP 75 85 . . ~ 辊缝 /m m 2—5 2 3 磨机主电机 电流 / A 10 8 磨机压差 / a MP 1 . 0 分级机转速 /(/ i r n) a r 70 0 入库斗提 电流 / A 4 5
机转 速 ,一 般来说 ,转 速低 、产 量低 ;转速 高 、 产量 高 ;但 打散 机转速 过 高 ,则会 使打散 机风 轮 磨损 过快 ,减短 其寿命 ,我司打 散机转 速一般 在
5 0~7 0/ i之 间调节 为宜 。 0 5r n m
量 能促进水泥 的水化速度 ,调节合适 的凝结时 间, 达到不 同标号水泥所需 的强度 ;石膏如果 断料或掺
辊压机预粉磨技术的应用
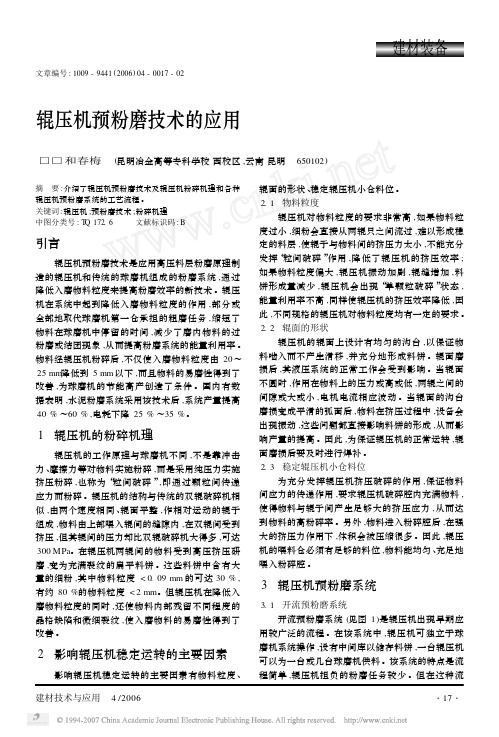
15 %左右 ,这些漏料与料饼的物理性能 (粒度 、易磨 性等 )差异很大 ,对球磨机的产量有明显影响 。打 散分级机可将漏料和粒度不合格的粗料选出 ,返回 辊压机喂料仓 ,既解决了辊压机“边缘效应 ”的负面 影响 ,又缓解了辊压机“过饱和喂料 ”的需求 。同时 打散分级机将粒度合格的物料喂入球磨机 ,既保证了 球磨机的节能高产 ,还可以根据球磨机生产能力的需 要 ,调节粗 、细物料的分选比例 ,合理地控制粉磨系统 的运行负荷 。由于联合粉磨系统依靠打散分级机对 预粉碎产品进行把关 ,因而辊压机可采用低压、大循 环的运行机制 ,以减轻辊面磨损 ,提高设备安全运转 率 。联合粉磨是在前面辊压机预粉磨系统系统的基 础上发展起来的 ,由于其增产 、节能的幅度最大 ,而且 更易解决机组的大型化问题 ,所以发展也最快。 3. 4 半终粉磨系统
1 辊压机的粉碎机理
辊压机的工作原理与球磨机不同 ,不是靠冲击 力 、摩擦力等对物料实施粉碎 ,而是采用纯压力实施 挤压粉碎 ,也称为“粒间破碎 ”,即通过颗粒间传递 应力而粉碎 。辊压机的结构与传统的双辊破碎机相 似 ,由两个速度相同 、辊面平整 ,作相对运动的辊子 组成 ,物料由上部喂入辊间的缝隙内 ,在双辊间受到 挤压 ,但其辊间的压力却比双辊破碎机大得多 ,可达 300 M Pa。在辊压机两辊间的物料受到高压挤压研 磨 ,变为充满裂纹的扁平料饼 。这些料饼中含有大 量的细粉 ,其中物料粒度 < 0. 09 mm 的可达 30 % , 有约 80 %的物料粒度 < 2 mm。但辊压机在降低入 磨物料粒度的同时 ,还使物料内部残留不同程度的 晶格缺陷和微细裂纹 ,使入磨物料的易磨性得到了层粉磨原理制 造的辊压机和传统的球磨机组成的粉磨系统 ,通过 降低入磨物料粒度来提高粉磨效率的新技术 。辊压 机在系统中起到降低入磨物料粒度的作用 ,部分或 全部地取代球磨机第一仓承担的粗磨任务 ,缩短了 物料在球磨机中停留的时间 ,减少了磨内物料的过 粉磨或结团现象 ,从而提高粉磨系统的能量利用率 。 物料经辊压机粉碎后 ,不仅使入磨物料粒度由 20~ 25 mm降低到 5 mm 以下 ,而且物料的易磨性得到了 改善 ,为球磨机的节能高产创造了条件 。国内有数 据表明 ,水泥粉磨系统采用该技术后 ,系统产量提高 40 % ~60 % ,电耗下降 25 % ~35 %。
辊压机生料终粉磨系统的生产工艺流程
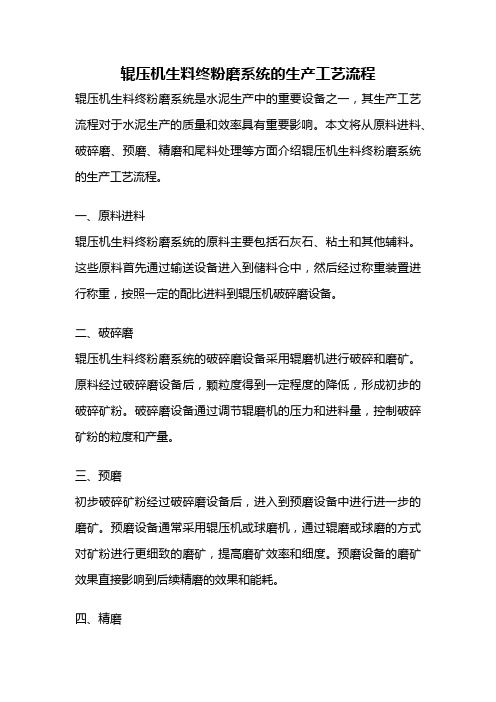
辊压机生料终粉磨系统的生产工艺流程辊压机生料终粉磨系统是水泥生产中的重要设备之一,其生产工艺流程对于水泥生产的质量和效率具有重要影响。
本文将从原料进料、破碎磨、预磨、精磨和尾料处理等方面介绍辊压机生料终粉磨系统的生产工艺流程。
一、原料进料辊压机生料终粉磨系统的原料主要包括石灰石、粘土和其他辅料。
这些原料首先通过输送设备进入到储料仓中,然后经过称重装置进行称重,按照一定的配比进料到辊压机破碎磨设备。
二、破碎磨辊压机生料终粉磨系统的破碎磨设备采用辊磨机进行破碎和磨矿。
原料经过破碎磨设备后,颗粒度得到一定程度的降低,形成初步的破碎矿粉。
破碎磨设备通过调节辊磨机的压力和进料量,控制破碎矿粉的粒度和产量。
三、预磨初步破碎矿粉经过破碎磨设备后,进入到预磨设备中进行进一步的磨矿。
预磨设备通常采用辊压机或球磨机,通过辊磨或球磨的方式对矿粉进行更细致的磨矿,提高磨矿效率和细度。
预磨设备的磨矿效果直接影响到后续精磨的效果和能耗。
四、精磨预磨后的矿粉进入到精磨设备中进行最后的精细磨矿。
精磨设备通常采用球磨机,通过添加适量的石膏和控制磨机的转速,使矿粉达到所需的细度要求。
精磨设备的磨矿效果和运行稳定性对水泥品质和能耗具有重要影响。
五、尾料处理精磨后的矿粉经过筛分设备进行筛分,将达不到细度要求的尾料重新送回到预磨设备进行再次磨矿,以提高磨矿效率和细度。
同时,通过风力输送装置将符合要求的终粉送入水泥仓进行储存和包装。
辊压机生料终粉磨系统的生产工艺流程包括原料进料、破碎磨、预磨、精磨和尾料处理等步骤。
通过合理控制每个环节的工艺参数,如进料量、磨矿压力、转速等,可以达到所需的水泥细度和产量要求。
同时,辊压机生料终粉磨系统的生产工艺流程还需要考虑能耗和设备维护等因素,以提高生产效率和降低生产成本。
辊压机球磨机联合粉磨工艺流程
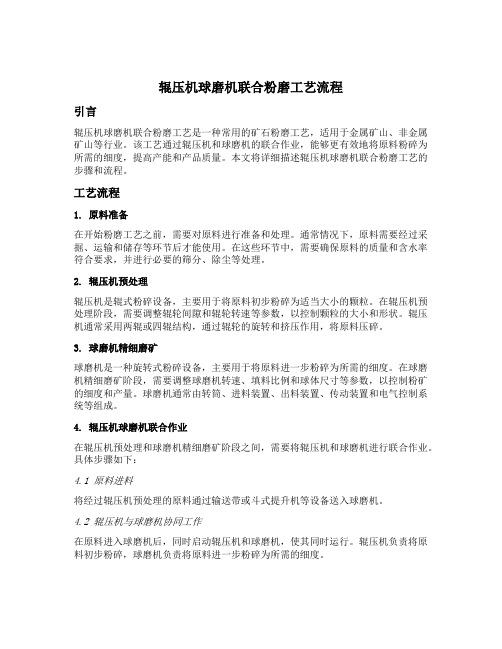
辊压机球磨机联合粉磨工艺流程引言辊压机球磨机联合粉磨工艺是一种常用的矿石粉磨工艺,适用于金属矿山、非金属矿山等行业。
该工艺通过辊压机和球磨机的联合作业,能够更有效地将原料粉碎为所需的细度,提高产能和产品质量。
本文将详细描述辊压机球磨机联合粉磨工艺的步骤和流程。
工艺流程1. 原料准备在开始粉磨工艺之前,需要对原料进行准备和处理。
通常情况下,原料需要经过采掘、运输和储存等环节后才能使用。
在这些环节中,需要确保原料的质量和含水率符合要求,并进行必要的筛分、除尘等处理。
2. 辊压机预处理辊压机是辊式粉碎设备,主要用于将原料初步粉碎为适当大小的颗粒。
在辊压机预处理阶段,需要调整辊轮间隙和辊轮转速等参数,以控制颗粒的大小和形状。
辊压机通常采用两辊或四辊结构,通过辊轮的旋转和挤压作用,将原料压碎。
3. 球磨机精细磨矿球磨机是一种旋转式粉碎设备,主要用于将原料进一步粉碎为所需的细度。
在球磨机精细磨矿阶段,需要调整球磨机转速、填料比例和球体尺寸等参数,以控制粉矿的细度和产量。
球磨机通常由转筒、进料装置、出料装置、传动装置和电气控制系统等组成。
4. 辊压机球磨机联合作业在辊压机预处理和球磨机精细磨矿阶段之间,需要将辊压机和球磨机进行联合作业。
具体步骤如下:4.1 原料进料将经过辊压机预处理的原料通过输送带或斗式提升机等设备送入球磨机。
4.2 辊压机与球磨机协同工作在原料进入球磨机后,同时启动辊压机和球磨机,使其同时运行。
辊压机负责将原料初步粉碎,球磨机负责将原料进一步粉碎为所需的细度。
4.3 控制参数调整根据实际情况和生产要求,及时调整辊压机和球磨机的转速、进料量、出料量等参数,以控制粉矿的细度和产量。
4.4 粉矿出料经过联合作业后的粉矿通过球磨机的出料装置排出,并经过筛分装置进行筛分,得到所需的产品。
5. 粉矿处理经过辊压机球磨机联合作业后得到的粉矿需要进行处理和加工。
通常情况下,需要对粉矿进行干法或湿法分级、除尘、干燥等处理,以满足产品质量要求。
辊压机联合粉磨系统具有优质、高产、低能耗的综合优势

辊压机联合粉磨系统具有优质、高产、低能耗的综合优势摘要:最近几年来,随着水泥工业化的进程及生产工艺、进程操纵技术的不断升级,水泥粉磨工艺和装备由以球磨机为主,进展为高效率的立式磨、辊压机等多种新型粉磨设备并用,几种设备的工艺组合,并朝着粉磨设备大型化、提升机工艺操纵技术智能化方面进展,以知足水泥生产大型化、现代化的要求。
辊压机料床粉磨技术是一项先进而成熟的粉磨技术,在辊压机的各类粉磨流程中,由V型静态选粉机和辊压机组成的联合粉磨系统尤其具有优质、高产、低消耗等综合优势。
关键词:辊压机新型粉磨联合粉磨粉磨系统水泥质量粉磨效率综合优势一、联合粉磨生产优势1.节能、环保、确保水泥质量粉磨在制造水泥工程中占有超级重要的地位,不管是生料(半成品)仍是水泥(成品)需要通过粉磨来取得,每生产1吨水泥,需要粉磨各类物料3、5吨左右,电耗约为100~,其中60%~70%的电耗消耗在粉磨中。
尤其是水泥粉磨系统比生料粉磨系统耗电量更大,这是因为水泥熟料质量差时,熟料中的硅酸二钙含量高时难磨,粉磨效率就会明显降低,电耗明显增加。
从水泥的水化和硬化反映、胶凝性有效利用率、强度尤其是初期强度来考虑,水泥磨的越细越好,如此还能改善其泌水性和易性等,水泥还要考虑产品的颗粒散布,力争做到节能、环保、确保水泥质量。
2.实现宏伟目标节能是增进经济社会可持续进展、实现全面建设小康社会宏伟目标的关键之一。
工业是能源和原材料的要紧消耗大户,水泥工业又是大量耗能的工业,因此节能降耗成为我国水泥工业长期而重要的任务,实现这一目标的关键在于提高粉磨效率,降低粉磨作业电耗。
实际生产中,以辊压机为代表的料床预粉磨系统是料床粉磨的主导。
预粉磨分为循环预粉磨、混合粉磨、联合粉磨和半终粉磨。
相对球磨机一级闭路粉磨工艺,联合粉磨和半终粉磨流程具有明显的系统优势。
尽管半终粉磨在系统增产方面具有更好的成效,但其节能幅度却略低于联合粉磨,且设备选型时受到必然限制,因此在实际工程设计中,联合粉磨流程取得了加倍普遍的应用。
辊压机预粉磨工艺计算

4.345132072
水泥熟料:2.1~2.6kWh/t;水泥生料:2.1~2.6kWh/t;
矿渣:4.3~5.2kWh/t
计算公式:Kg=2β
*PT/KQ
GB/T 288-1994 调心滚子轴承241MB/W33
11500
1 6280
轻微冲击:1.0~1.2,中等冲击:1.2~1.8 P=F/2*fd
7500 181 3.05 0.037 552 448.880
8000 173 3.2 0.034 554 429.040
8500 160 3.35 0.032 556 396.800
9000 160 3.5 0.03 560 1388.800
1642.8
于200~215t/m3·s/h; ·s/h
工况参数
入磨粒度Φ
辊子直径D 辊子宽度B 辊子圆周线速度V 辊子转速n
mm
m m m/s r/min
70
1.6 1 1.55 18.5
辊压机预粉磨工艺计算
辊子间隙Smin
m
n=ω/2Π
辊压前物料容重ρ1
t/m3
水泥熟料一般为1.5~1.6t/m3,石灰石取1.4
1.6
轴承寿命
h
物料的压缩特性参数KQ t/m3·s/h
辊压机生产能力Q
t/h
辊压机双棍需用功率N
kW
辊压机的配用功率N0
kW
168.1677721 428.544 417.056
1812.163727 2000
投影辊压PT 物料压缩特性参数KQ 料饼的单位功耗Wg 作用角sinβ[=α/3] 计算参数(2β·PT) 辊压机生产能力Q
~1.5t/m3
辊压机预粉磨系统提产技术措施
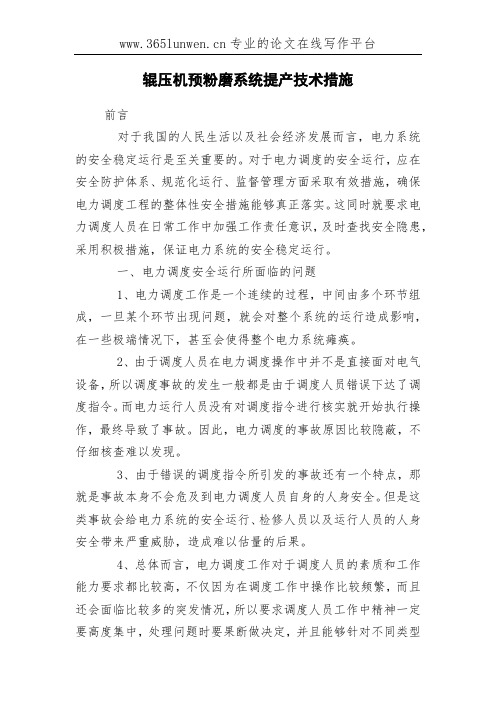
专业的论文在线写作平台
辊压机预粉磨系统提产技术措施
前言
对于我国的人民生活以及社会经济发展而言,电力系统的安全稳定运行是至关重要的。
对于电力调度的安全运行,应在安全防护体系、规范化运行、监督管理方面采取有效措施,确保电力调度工程的整体性安全措施能够真正落实。
这同时就要求电力调度人员在日常工作中加强工作责任意识,及时查找安全隐患,采用积极措施,保证电力系统的安全稳定运行。
一、电力调度安全运行所面临的问题
1、电力调度工作是一个连续的过程,中间由多个环节组成,一旦某个环节出现问题,就会对整个系统的运行造成影响,在一些极端情况下,甚至会使得整个电力系统瘫痪。
2、由于调度人员在电力调度操作中并不是直接面对电气设备,所以调度事故的发生一般都是由于调度人员错误下达了调度指令。
而电力运行人员没有对调度指令进行核实就开始执行操作,最终导致了事故。
因此,电力调度的事故原因比较隐蔽,不仔细核查难以发现。
3、由于错误的调度指令所引发的事故还有一个特点,那就是事故本身不会危及到电力调度人员自身的人身安全。
但是这类事故会给电力系统的安全运行、检修人员以及运行人员的人身安全带来严重威胁,造成难以估量的后果。
4、总体而言,电力调度工作对于调度人员的素质和工作能力要求都比较高,不仅因为在调度工作中操作比较频繁,而且还会面临比较多的突发情况,所以要求调度人员工作中精神一定要高度集中,处理问题时要果断做决定,并且能够针对不同类型。
立磨及水泥辊压机联合粉磨系统操作技术

立磨及水泥辊压机联合粉磨系统操作技术第一篇:立磨及水泥辊压机联合粉磨系统操作技术立磨机及辊压机的操作无论窑操还是磨操,首先要明确系统内在的逻辑关系,这就要求操作员对系统工艺和设备的特性清楚了解。
把握好定性与定量的辩证关系。
接班时首先要向前一个班人员了解系统的运行情况。
哪些设备存在隐患,产、质量情况如何。
看全分析报告单,了解物料的易磨性,这样可以进行针对性的控制。
既要熟悉中控操作界面,又要对现场设备十分了解,所以要经常到现场了解设备的情况。
特别是当现场设备发生故障时,要知道发生故障的原因和解决故障的方法。
立磨立磨是利用磨辊在磨盘上的相对碾压来粉磨物料的设备。
对立磨正常运行的影响主要有几个方面:(1)磨机的料层。
合适的料层厚度和稳定的料层,是立磨稳定运行的基础。
料层太厚,粉磨效率降低,当磨机的压差达到极限时会塌料,对主电机和外排系统都将产生影响;料层太薄,磨机的推动力增加,对磨辊磨盘和液压系统都有损伤。
(2)磨机的振动。
磨机的振动过大,不仅会直接造成机械破坏,并且影响产、质量。
产生振动的因素有:磨机的基础、研磨压力、料层的厚度、风量及风温、蓄能器压力、辊面或磨盘的磨损状况等。
物料对磨机振动的影响及处理方法:物料对磨机振动的影响,主要表现在物料粒度、易磨性及水分。
在立磨运行过程中,要形成稳定的料层,就要求入磨物料具有适宜的级配,要有95%以上的粒度小于辊径的3%。
喂料粒度过大将导致易磨性变差。
由于大块物料之间空隙没有足够多的细颗粒物料填充,料床的缓冲性能差,物料碾碎时的冲击力难以吸收,导致磨机的振动增加。
喂料粒度过小,特别是粉状料多时,由于小颗粒物料摩擦力小,流动性好。
缺乏大块物料构成支撑骨架,不易形成稳定的料床。
磨辊不能有效地压料碾压,大量的粉状物料会使磨内气流粉尘浓度和通风阻力增大,当达到极限时会产生塌料,导致磨机振动增加。
当操作员发现物料过细,尤其是立磨内压差已明显上升时,应及时调整喂料,降低研磨压力和出口温度并加大喷水量,适当降低选粉机转速。
辊压机及挤压联合粉磨技术讲义

辊压机及挤压联合粉磨技术讲义辊压机部分一、工作原理和工作方式:该设备根据高压料层粉碎能耗低的原理,采用单颗粒粉碎群体化的工作方式,脆性物料经过高压区挤压后使物料粒度迅速减小,<0.08mm的细粉含量达20%~30%,<2mm的物料含量达70%以上,在所有经挤压后的物料表面存有大量的裂纹,易磨性显著改善,使物料在进入下一工序的粉磨时所需的粉磨能耗大幅度降低,获得大幅度增产节能的效果。
辊压机的核心部分是两个辊径辊宽相同,相向转动的磨辊,辊压机采用的工作方式是在两个相向转动的磨辊之间形成高压力区,采用过饱和喂料的方式在磨辊上方设置用于保证仓内料位的称重仓,料位由称重传感器以负反馈方式控制,形成具有一定料压的料柱,通过进料装置喂入两磨辊之间,磨辊将物料拉入辊隙后在压力区以高压将物料压成密实的料饼后从辊隙间落下进入下一工序。
由于辊压机工作时采用完全正压力对物料实施挤压,同时在辊面菱形花纹对物料的限制作用下,物料与磨辊之间无产生剪切效果的相对滑移(注:在获得相同粉碎效果的前提下,剪应变所需能量是压应变的5倍),所以上述工作方式不仅节省能耗,辊面磨损也很小。
二、设备结构:设备由主机架、轴系、液压系统、润滑系统、进料装置、传动系统、检测系统等组成。
1、主机架:主机架用于承受设备的挤压粉碎力,分别由上、下横梁,左、右立柱,承载销,定位销,导轨及高强度联接螺栓组等组成。
上、下横梁采用工字型结构,左、右立柱则采用工字型与箱型相结合的结构形式,均具有较高的刚度,通过高强度螺栓组的联接使整个机架形成一个刚性的整体。
承载销将立柱上所受到的挤压粉碎力传递到上、下横梁;定位销则用于确定两侧上、下横梁的中心距。
安装于两侧下横梁的导轨是活动辊轴承座的导向装置,两侧的导轨宽度稍有不同,靠近传动一侧的导轨稍宽。
高强度螺栓组是确保主机架联接的关键,不可用普通螺栓代替,同时必须保证联接紧密可靠。
2、液压系统原理和操作:液压系统为设备的挤压粉碎力提供所必需的压力源,起液压弹簧作用,并兼有液压保护功能,其性能直接影响挤压粉碎物料的质量和设备的安全运行。
- 1、下载文档前请自行甄别文档内容的完整性,平台不提供额外的编辑、内容补充、找答案等附加服务。
- 2、"仅部分预览"的文档,不可在线预览部分如存在完整性等问题,可反馈申请退款(可完整预览的文档不适用该条件!)。
- 3、如文档侵犯您的权益,请联系客服反馈,我们会尽快为您处理(人工客服工作时间:9:00-18:30)。
调节插板的维护
辊压机调节插板的主要作用是调节进入辊压 机两辊之间的料床的厚度, 通过手轮可以实现插板的上下移动,插板向 上提起过多,进入两辊之间的料床较厚,辊 缝较大,使物料大量冲过,造成下道工序的 负荷增大。插板向下插入过多,料床较薄, 易使辊压机产生震动,损坏扭矩支撑地脚螺 栓。 生产中应根据实际情况调节插板,使形成的 料饼厚度在30mm左右,并做好定期的检 查更换。
ห้องสมุดไป่ตู้
最高喂料温度:100℃ 最大喂料湿度:1.5% 辊子轴冷却用水: 2×1.5m3/h 定辊电动机功率: 功率710kW 电压(频率)6000V(50) 动辊电动机: 功率710kW 电压(频率)6000V(50)
行星减速器PBZF300-45 干油润滑系统电机功率 0.18KW 定辊减速机油用水量 9 m3/h 电机 电压:380V 功率:4KW 动辊减速机油站用水量 9 m3/h 电机 电压:380V 功率:4KW液压油站冷却 水量 1.5 m3/h 电机功率:5.5KW电加热器功率:1.1KW
自动堆焊
自动堆焊与手工堆焊的主要区别是引燃电弧、焊丝 送进、焊炬和工件的相对移动等全部由机械自动进 行,克服了手工堆焊生产率低、劳动强度大等主要 缺点。
液压系统
为压辊提供压力 液压油站(泵) 组 成 部 分 液压油缸 蓄能器 控制阀
液压系统
液压系统为压辊提供压力, 它是由两大、两小蓄能器,四 个平油缸、站等组成的液气联 动系统。主要有油泵、蓄能器、 液压缸、控制阀件组成。蓄能 器预先充压至小于正常操作压 力,当系统压力达到一定值时 喂料,辊子后退,继续供压至 操作设定值时,油泵停止。
整体锻造表层堆焊式挤压辊
热装式挤压辊 镶套式挤压辊
挤压辊的辊面形式
光滑辊面
光滑辊面制造、维修成本较低,辊面腐蚀易修复。 当喂料量不稳定时,会产生振动和冲击。 咬合角小,挤压后的料饼较薄,产量较低。
沟面辊面
克服光滑辊面的缺点, 其结构形式通过堆焊 来实现。
沟面辊面的三种结构形式
环状波纹堆焊层
人字形波纹
我国辊压机发展史
自上世纪八十年代中期,合肥水泥研究设 计院、天津水泥工业设计研究院、洛阳矿山机 器厂、唐山水泥机械厂四家单位联合引进德国 KHD公司辊压机设计制造技术,经过二十年 的不断完善,国产辊压机的辊径由800mm发 展到今天的1600mm ;辊宽由200mm发 展到今天的1400mm;装机功率由 90kW×2发展到今天的1120kW×2;整机 重量由30多吨发展到今天的200多吨,通过 量由40t/h发展到今天的800t/h;配套磨机 的产量由20t/h发展到今天的180t/h,辊压 机产品质量逐步提高,节能幅度达30%以上。 国产辊压机二十年的发展历程,可以分成三个 阶段:
我国辊压机发展史
研究开发阶段(1986年—1992年)
1986年“挤压粉磨技术新工艺及设 备研究”列为国家“七五”重点科技攻 关项目 1989年4月合肥水泥研究设计院和海安 建材机械厂联合研制的 Ø1000×300mm在江苏省江阴水泥 厂Ø2.2×6.5m的生料磨成功应用。推 出第一台国产辊压机,取得了使磨机增 产67.8%,节电32.1%的效果。 达
斜井字波纹
堆焊方法
手工堆焊
是利用电弧或氧—乙炔火焰产生的热量熔 化基体金属和焊条,采用手工操作进行堆 焊的方法。它适用于工件数量少,没有其 他堆焊设备的条件下,或工件外形不规则、 不利于机械化、自动化堆焊的场合。这种 方法不需要特殊设备,工艺简单,应用普 遍,但合金元素烧损很多,劳动强度大, 生产率低。
结构
辊压机构造
辊压机构造
挤压辊 液压系统 传动装置 喂料装置 主机架
挤压辊
组成
固定辊:用螺栓固定在机架上 滑动辊:两端用四个平行油缸施加压力, 可在机架上水平移动
挤压辊的结构形式
镶套式: 不常用,料软时用 整体式: 常用,表面堆焊耐 磨材料
侧挡板的维护
辊压机在运转时存在边缘漏料的现 象,这一部分物料没有经过辊压机 的挤压而直接进入打散机,使打散 机负荷、磨损加大。 在生产中应每天做好侧挡板的检查 工作,确保侧挡板与辊端面间隙不 大于2mm,间隙过大时,通过拧 动压紧螺栓顶紧侧挡板
称重稳流仓
称重稳流仓的作用并不在于称重,而在于稳流。 当稳流仓中有一定料位时,会对辊压机产生均 匀连续的料床压力,挤压效果良好。如果稳流 仓料位不足或是空仓,使得料床压力波动较大, 挤压效果较差,同时由于打散机返回的部分细 粉会造成辊压机震动和下料管部位的大量扬尘 生产中在稳流仓中保持70%以上的料位较为 合理。
辊轴
喂料装置
保证物料均匀、定量进入压力区 组成 挡板 侧挡板 调节插板
辊端挡板
辊压机工作原理(1)
待粉碎的物料由上方的进料漏斗、喂料 装置加入,受两辊的慢速相对运动被强 制带入两辊间隙, 经历满料密实、 层压粉碎、结团 排料三个阶段被 粉碎
辊压机工作原理(2)
我国辊压机发展史
快速发展阶段(2000年至今)
水泥产业结构调整,淘汰立窑,发展 新型干法, 这就要求国产化辊压机也朝 着大型化发展,我国及时开发出装机功率 在1120kW×2的大型 HFCG160-140辊压机, 与Ф 4.2×13m开路水泥磨配套,产量可达 170t/h以上,而Ф 4.2×13m闭路水泥磨配 套的产量则可达180t/h以上,取得增产 100%,节电30%的实际应用效果。
辊压机主要参数确定
辊子直径与宽度 直径: D= K d d max D---------辊子直径(规格直径), (mm) Kd--------系数,Kd=10~24 Dmax------- 喂料最大粒度,(mm) 宽度: D/L=1~2.5
辊压机主要参数确定
辊隙:
S
min
=KsD
辊压机粉碎系统
预粉磨系统 半终粉磨系统 终粉磨系统 混合粉磨系统
预粉磨系统
仅用于 老厂改 造
目前 常用
半终粉磨系统
终粉磨系统
发展趋 向
终粉磨系统
发展趋 向
正常工作情况下油泵不工作,系统中如压力过大,液压油排至蓄 能器,使压力降低,保护没备,若压力继续超过上限值时,自动卸 压。操作中系统压力低于下限值时,自动启泵增压。
传动装置
由两台电机分别带动动、定辊运行 组成部分 电机 万向联轴节 减速机 辊轴
传动过程
电机
万向联轴节
减速机
S min -----两辊中心连线上的最小辊隙, mm Ks--------最小辊隙系数,水泥原料取 0.020~0.030,水泥熟料取 0.016~0.024 D-------辊子外直径,m
辊压机主要参数确定
辊压
一般控制在140~180MPa之间,设 计最大压力200MPa。 辊速: K
满料密实阶段(与破碎机相同) 物料在重力和拉入力作用下,颗粒受压力 而靠紧、破碎、密实,颗粒之间由点接触 变为面接触,形成密实的颗粒料层。
辊压机工作原理(3)
层压粉碎阶段 密实的颗粒料层继续向两辊最小间隙处 前进,密实度增高,压力急剧增高,颗 粒之间进行压力传递,使众多颗粒产生 微细裂纹而被粉碎。
辊压机工作原理(4)
结团排料阶段 已碎的众多细颗粒,因间隙继续减小,重新 排列各自的位置,个别“难碎”的大颗粒被 众多细颗粒包围,产生“结团”,形成“料 饼”。
本厂辊压机参数
辊压机 HFCG150 轧辊直径:1500mm 轧辊宽度:1000mm 通过量(熟料):415~500t/h 喂料粒度:≤80mm 产品平均粒度: <2mm 65% <0.09mm 20% 轧辊线速度: 1.54m/s
我国辊压机发展史
整改提高阶段(1993年—1999年)
经国家“八五”、“九五”重点科技 攻关课题的持续研究,集十余年的应用经 验,推出了具有自主知识产权,设计更合 理、性能更优越,可靠性更高的第三代 HFCG系列辊压机。有效解决了包括辊压机 偏辊、偏载、水平振动和传动系统扭振等 一系列关键性技术难题。
第三章
辊压机
辊压机构造与原理 辊压机主要参数确定 辊压机性能与应用 辊压机操作与维护 辊压机粉碎系统
辊压机发展史
辊压机又称挤压磨或辊压磨是继立式磨之后, 20世纪80年代发展起的一种新型节能增产 的粉磨设备。被称为继窑外分解技术之后有 一重大技术进步 第一台辊压机于1985年在德国洪堡(KHD) 公司研制成功并用到生产中以来,目前辊压 机以普遍用于生料、水泥、矿渣、煤等矿石 的粉磨。 目前最大的辊压机是为 Ø2000×1000mm传动功率2500Kw
应用
建材、冶金、化工脆硬物料的粉碎, 不适用软质料 水泥生产中用于生料、水泥的预粉 碎及生料的终粉磨
效果
产品中小于2 mm的占80~90%, 且小于80um的达20~30%
辊压机的操作与维护
挤压力 调节插板的维护 侧挡板的维护 称重稳流仓
挤压力
辊压机的挤压力是辊压机安全稳定运行的重 要参数, 挤压力的大小直接影响挤压效果的好坏,但 挤压力并不是越大越好。挤压力过大,物料 被挤压得过于密实,物料颗粒之间产生聚合 现象,造成打散机分级困难,同时加大了辊 面的磨损;挤压力过小,物料形不成致密的 料饼,影响料床粉碎力功效。 辊压机挤压力一般控制在9~11MP左右较 为理想。