商用车车架横梁的应力分析
重型自卸汽车车架横梁异常断裂原因分析

[2] WANG Yaj un (王亚军),HUANG Ping(黄平),LI Shengcai(李生才).Stati stics of industrial acci dents in China during the period from M arch to J une i n 2004[J].Journal o f Safety and Environment(安全与环境学报),2004,4(4):93-96[3] Sys tem of Fi re Disas ter and Fire Rescue(火灾及火灾救援信息管理系统).Fire records in Kunming during the period from 2004to 2006(2004 2006年昆明市火灾记录)[DB].[4] HE Shuiqing(何水清),WANG Shan(王善).Structural reliabilityanalysis and design (结构可靠性分析与设计)[M ].Beijing:Na tional Defense Industry Press,1993:33-34[5] F AN Weicheng(范维澄),SUN Junhua(孙军华),L U Shouxiang(陆守香).M ethodologies o f fire risk evaluation (火灾风险评估方法学)[M ].Beijing:Science Press,2004:112-150[6] GEN TLE J E.Elements of computational statistics [M ].New York:Spri nger Science Press,2005[7] LIU Baoding (刘宝碇),PENG Ji n (彭锦).A course in uncertaintytheory(不确定理论教程)[M ].Beijing:Tsinghua Universi ty Press,2005:21-69Statistic analysis of fire accidents in urban villages of KunmingSONG Zhi gang 1,C HE N Shuo 2,BAI Yu1(1Faculty of Civil Eng i neering and Architecture,Kunming Uni versity of Science and Technology,Kun ming 650224,China;2Fi re Protec ti on Section of Panlong District,Kun ming 650224,China)Abstract:This paper is ai med to provide our analysis on the si tuation of the fire accidents in urban villages (UVs)of Kunming.To under stand the fire characteristic features in UVs,we have studied the fire records from 2004to 2006in the said areas and analyzed the causes that led to such fires.In such areas,one of which is the speeding up of the process of urbanization in the country.It has become a critical problem for the UVs to lack strict city planning and specialized resi dential admi nistration and management,which has turned to be a key to social disorder and reasons to lead fire accidents.Accordi ng to fire sites,the fire records can be first of all classified into two categories,those taking place in UVs and those taking place non UVs.Bayesian algori thm calculation indicates that the fire probabilities of buildings in UVs prove qui te different with higher risk buildings clustered to gether with the corresponding risk ratio.We have also done the corre lation analysis (CAFSC)on the building fire cause.The analysis shows that there is significan t dissi milari ty between the C AFSC results for UVs and those for non UVs.The dissi milarity reflects the differen t features of the fire sites or/and fire causes in UVs that are distin guished from those in non UVs.Many of the features in UVs prove to be in conformity wi th the field inves tigation.Key words:safety engineering;fi re;risk;statistic;urban village CLC number:X928 01 D ocument code:A Article ID:1009 6094(2008)06 0112 05*收稿日期:2008-07-16作者简介:刘大维,教授,博士,从事地面-车辆系统与控制技术研究,qdldw@163 com 。
商用车车架横梁的应力分析
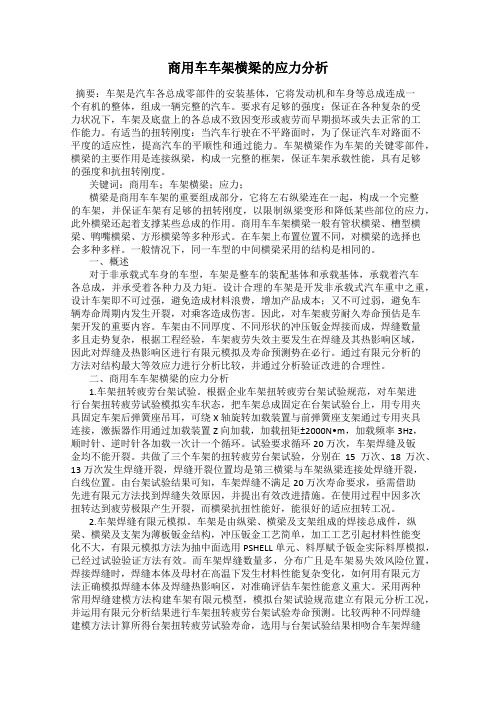
商用车车架横梁的应力分析摘要:车架是汽车各总成零部件的安装基体,它将发动机和车身等总成连成一个有机的整体,组成一辆完整的汽车。
要求有足够的强度:保证在各种复杂的受力状况下,车架及底盘上的各总成不致因变形或疲劳而早期损坏或失去正常的工作能力。
有适当的扭转刚度:当汽车行驶在不平路面时,为了保证汽车对路面不平度的适应性,提高汽车的平顺性和通过能力。
车架横梁作为车架的关键零部件,横梁的主要作用是连接纵梁,构成一完整的框架,保证车架承载性能,具有足够的强度和抗扭转刚度。
关键词:商用车;车架横梁;应力;横梁是商用车车架的重要组成部分,它将左右纵梁连在一起,构成一个完整的车架,并保证车架有足够的扭转刚度,以限制纵梁变形和降低某些部位的应力,此外横梁还起着支撑某些总成的作用。
商用车车架横梁一般有管状横梁、槽型横梁、鸭嘴横梁、方形横梁等多种形式。
在车架上布置位置不同,对横梁的选择也会多种多样。
一般情况下,同一车型的中间横梁采用的结构是相同的。
一、概述对于非承载式车身的车型,车架是整车的装配基体和承载基体,承载着汽车各总成,并承受着各种力及力矩。
设计合理的车架是开发非承载式汽车重中之重,设计车架即不可过强,避免造成材料浪费,增加产品成本;又不可过弱,避免车辆寿命周期内发生开裂,对乘客造成伤害。
因此,对车架疲劳耐久寿命预估是车架开发的重要内容。
车架由不同厚度、不同形状的冲压钣金焊接而成,焊缝数量多且走势复杂,根据工程经验,车架疲劳失效主要发生在焊缝及其热影响区域,因此对焊缝及热影响区进行有限元模拟及寿命预测势在必行。
通过有限元分析的方法对结构最大等效应力进行分析比较,并通过分析验证改进的合理性。
二、商用车车架横梁的应力分析1.车架扭转疲劳台架试验。
根据企业车架扭转疲劳台架试验规范,对车架进行台架扭转疲劳试验模拟实车状态,把车架总成固定在台架试验台上,用专用夹具固定车架后弹簧座吊耳,可绕X 轴旋转加载装置与前弹簧座支架通过专用夹具连接,激振器作用通过加载装置Z 向加载,加载扭矩±2000N•m,加载频率3Hz,顺时针、逆时针各加载一次计一个循环。
车架受力分析
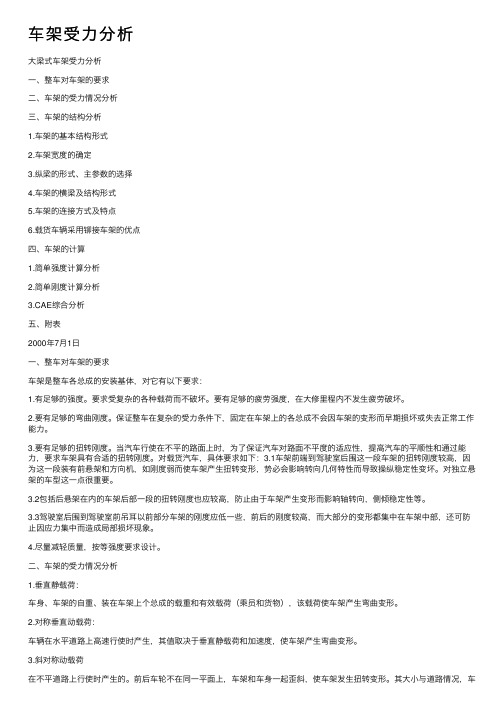
车架受⼒分析⼤梁式车架受⼒分析⼀、整车对车架的要求⼆、车架的受⼒情况分析三、车架的结构分析1.车架的基本结构形式2.车架宽度的确定3.纵梁的形式、主参数的选择4.车架的横梁及结构形式5.车架的连接⽅式及特点6.载货车辆采⽤铆接车架的优点四、车架的计算1.简单强度计算分析2.简单刚度计算分析3.CAE综合分析五、附表2000年7⽉1⽇⼀、整车对车架的要求车架是整车各总成的安装基体,对它有以下要求:1.有⾜够的强度。
要求受复杂的各种载荷⽽不破坏。
要有⾜够的疲劳强度,在⼤修⾥程内不发⽣疲劳破坏。
2.要有⾜够的弯曲刚度。
保证整车在复杂的受⼒条件下,固定在车架上的各总成不会因车架的变形⽽早期损坏或失去正常⼯作能⼒。
3.要有⾜够的扭转刚度。
当汽车⾏使在不平的路⾯上时,为了保证汽车对路⾯不平度的适应性,提⾼汽车的平顺性和通过能⼒,要求车架具有合适的扭转刚度。
对载货汽车,具体要求如下:3.1车架前端到驾驶室后围这⼀段车架的扭转刚度较⾼,因为这⼀段装有前悬架和⽅向机,如刚度弱⽽使车架产⽣扭转变形,势必会影响转向⼏何特性⽽导致操纵稳定性变坏。
对独⽴悬架的车型这⼀点很重要。
3.2包括后悬架在内的车架后部⼀段的扭转刚度也应较⾼,防⽌由于车架产⽣变形⽽影响轴转向,侧倾稳定性等。
3.3驾驶室后围到驾驶室前吊⽿以前部分车架的刚度应低⼀些,前后的刚度较⾼,⽽⼤部分的变形都集中在车架中部,还可防⽌因应⼒集中⽽造成局部损坏现象。
4.尽量减轻质量,按等强度要求设计。
⼆、车架的受⼒情况分析1.垂直静载荷:车⾝、车架的⾃重、装在车架上个总成的载重和有效载荷(乘员和货物),该载荷使车架产⽣弯曲变形。
2.对称垂直动载荷:车辆在⽔平道路上⾼速⾏使时产⽣,其值取决于垂直静载荷和加速度,使车架产⽣弯曲变形。
3.斜对称动载荷在不平道路上⾏使时产⽣的。
前后车轮不在同⼀平⾯上,车架和车⾝⼀起歪斜,使车架发⽣扭转变形。
其⼤⼩与道路情况,车⾝、车架及车架的刚度有关。
商用车车架横梁的应力分析

摘要: 针 对 商 用车车 架 常用 的管状 横 梁 、 槽 型横 梁及 鸭嘴横 梁 , 利 用有 限元 分析 软件 分 别建 立 以 3
种 不 同横 梁为主 的 车 架模 型 并进行 应 力对 比分析 , 从模态、 刚度 和 强度 等 3个 方 面分析 不 同横 梁
的 车 架之 间的差 别 , 为 不 同用途及 类型 的 车架设 计提 供 了参 考 。
关键 词 : 商 用车 ; 车架; 中间横 梁 ; 应 力分析
中图分类 号 : U 4 6 3 . 3 2
文献标 识码 : A
文 章编 号 : 2 0 9 5— 5 0 9 X( 2 0 1 7 ) 0 4— 0 l l 7— 0 3
横 梁 是商 用车 车架 的重 要组 成部 分 , 它将 左 右 纵 梁连 在 一起 , 构 成 一 个 完 整 的 车架 , 并 保 证 车架 有 足够 的扭 转 刚度 , 以限制 纵梁 变形 和 降低某 些部 位 的应 力 , 此 外 横 梁 还 起 着 支 撑 某 些 总 成 的 作 用 。商用 车 车 架 横 梁 一 般 有 管 状 横 梁 、 槽 型 横 梁、 鸭嘴横梁 、 方 形横 梁 等 多种 形 式 。在 车 架 上 布 置位置 不 同 , 对 横梁 的选 择 也会 多种 多样 。一 般情
明显较 低 , 管状横 梁 车架 1阶扭 矩模 态频 率 相对 较
后轴 扭 转 工 况 的 定 义 : 在 后 轴 左 侧 添 加 1 0 0 0 0 N向上 的 力 , 在 后 轴 右侧 添 加 1 0 0 0 0 N 向下
高, 但 其能 量 相 对 集 中 在 圆 管 上 , 3种 横 梁 结 构 车
收稿 日期 : 2 0 l 7— 0 l—l 9
桁架单梁门式起重机主梁结构应力分析报告
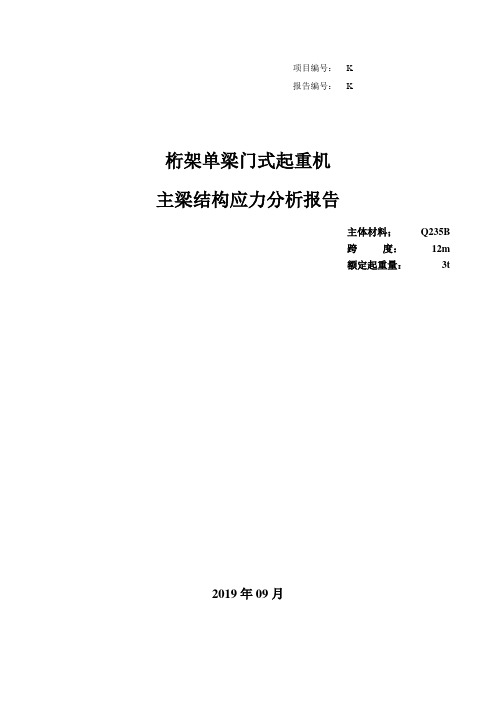
项目编号:K报告编号:K桁架单梁门式起重机主梁结构应力分析报告主体材料;Q235B跨度:12m额定起重量:3t 2019年09月目录1 概述 (1)2 工作依据 (1)3 工作内容 (1)4 主梁的有限元分析 (1)5 应力分析结果 (4)5.1 工况1计算结果 (4)5.2 工况2计算结果 (7)5.3 工况3计算结果 (9)5.4 工况4计算结果 (10)6 结论 (12)6.1 结果汇总 (12)6.2 应变片布点位置建议 (13)1 概述河南省九峰起重机有限公司(简称“乙方”)设计并生产的ZJF桁架单梁门式起重机,于2016年9月在河南赵九峰研究院(以下简称“甲方”)九峰基地进行压力试验。
对乙方开发的桁架单梁门式起重机主梁,按照《电动葫芦桥式起重机型式试验细则》,对主梁强度、刚度进行有限元计算,并与应力测试结果进行对比。
采用ANSYS17.0软件完成本次分析计算。
2 工作依据(1)甲乙双方签订的合同;(2)甲方提供的“ZJF桁架单梁门式起重机”设计图纸;(3)GB/T 3811—2008《起重机设计规范》;(4)《桥门式起重机型式试验细则》;(5)《机械设计手册》化学工业出版社。
3 工作内容3.1 主梁强度和刚度分析(1)建立ZJF桁架单梁门式起重机的有限元数值分析模型;(2)计算ZJF桁架单梁门式起重机在不同工况作用下主梁的应力、变形。
3.2 工况类型(1)额定载荷跨中,计算主梁在额载下的应力和变形;(2)额定载荷悬臂端,计算主梁在额载下的应力和变形;(3)1.25倍额定载荷跨中,计算主梁的应力;(4)1.25倍额定载荷悬臂端,计算主梁的应力。
4主梁的有限元应力分析4.1几何模型ZJF桁架单梁门式起重机主要由筋板和轨道等组成,图1为主梁结构图。
第1页共13页赵九峰作品桁架单梁门式起重机主梁结构应力分析报告第2页 共13页图1 ZJF 桁架单梁门式起重机主梁结构图4.2有限元实体模型根据桁架单梁门式起重机主梁的几何模型,建立了有限元模型,结构主要由型钢焊接而成。
载重150吨平车底架结构应力分析

第16卷第2期 佛山科学技术学院学报(自然科学版) Vol.16No.21998年6月 Journal of Foshan University (Natural Science Edition )Jun .1998载重150吨平车底架结构应力分析单 明*摘 要 论述了采用SUP ERSAP 93程序对某载重150t 平车底架结构进行应力分析,为进一步设计提供了理论的依据。
关键词 底架 结构 应力分析中图分类号 U27 U46目前国际上广泛采用的拖车和铁路平车底架的结构是凹型折角式,它具有结构工艺简单、增加凹底架承载面长度、自重轻等特点。
本文中,采用广泛用于钢结构强度计算的SU-PERSAP93软件对平车大底架结构的计算结果进行应力分析。
1 平车底架结构载重150t 平车底架结构采用16Mnq 低合金钢全焊接封闭结构。
整个结构由四块纵向腹板、上下盖板、隔板、前后立板以及多块筋板组焊而成,结构示意图如图1所示。
图1 大底架结构及控制截面示意图 该车大底架沿纵、横向截面对称,全长为17350mm,两心盘中心距为16650mm,大底架承载面长9000mm 、宽2750mm,大底架承载梁截面高度为700mm,两端面高度为600mm ,折角部前后立板互相平行并与水平面之夹角为75°。
收稿日期3*佛山科学技术学院教务处,佛山 5:1997-0-0428000大底架腹板厚为10mm(折角部分厚为20mm),凹底部承载梁上盖板厚为20mm,下盖板厚为25mm ,端梁上下盖板厚均为14mm ,前立板厚为20mm ,后立板厚为20mm ,折角部隔板厚为16mm,其余处隔板厚均为10mm 。
2 结构分析模型2.1 结构离散模型由于大底架结构和计算载荷(垂直静、动载荷,纵向力及扭转载荷)均对称或反对称于大底架的横向和纵向中心平面,故取1/4大底架[1]进行计算,考虑到大底架为空间结构,主要由板状构件焊接组成,因而采用四边形或三角形线性板壳单元进行有限元计算,整个计算模型的网格,除了由纵横交错的腹板、隔板、盖板等形成的自然节点外,适当增加了部分节点,特别是在凹底折角部位及连接部位等结构突变处采用了加密的网格以提高分析精度,结构节点数为3170个,单元数为3314个。
一种重卡管状横梁断裂的失效分析及改善方法

收 稿 日期 :02— 4—1 21 0 3
作者简 介 : 剑波 (9 0 ) 男 , 谢 18 一 , 工程硕士 , 工程 师 , 主要从 事重卡动力系统 的产品开发和改进研究 。
6 8
四 川 兵 工 学 报
ht :/ c gjusr. o t / sb .o r v cm/ p e
—
96.
( 责任 编 辑
鲁
进)
( 接第 6 上 5页 )
对 于 主 轴 的 动 态 性 能 研 究 , 时 间 与 过 程 的 角 度 , 在 从 旨
为提高主轴运作 的高效性与准确性 提供依据 , 此可 以提高 如 加工精度 。动态 性能 包括 力学性 能 , 动频 率等 各种 性 能。 振 对机床主轴工作 状态下的动态性能 的评估 , 更好地把 握机 能 床 的工作性 能与机床 的发展 。
扩张应力 。② 应 力 腐 蚀 断裂 是 一 种 与 时间 有关 的滞 后 破 坏, 这和氢滞后开 裂 完全 类似 。③ 应 力 腐蚀 开裂 是 一种 低
应力脆性 断裂 。 该 管 状 梁 一 般 出现 断 裂 的部 位 在 发 动 机 着 力 点 上 , 接 焊
参 考文献 :
胡 玉梅 , 士 星 , 以轩 , , 动 机 悬 置 系统 优 化 方 法 张 向 等 发
直板 时热 影响区域较 大 , 使局 部材 质 的应力 发生 变化 , 因此
才 出 现 了 轴 向 方 向 的垂 直 断 裂 。
发生脆性断裂 的原 因是存 在和焊缝相 交 的构 造缝 隙 , 或 相 当于构造缝 隙的未透 焊缝 。构造焊缝 相当 于狭 长 的裂纹 , 造成 高度 的应力集 中 , 焊缝则造成高额 残余 拉应力并使 近旁
商用车车架常用横梁的力学性能研究

( Do n g f e n g C o mme r c i a l V e h i c l e T e c h n i c a l Ce n t e r o f DEC V , Wu h a n 4 3 0 0 5 6 , C h i n a )
设计 ・ 研究 I 商用车车架常用横梁的力学性能研究
d o i : 1 0 . 3 9 6 9 6 . i s s n . 1 0 0 5 - 2 5 5 0 . 2 0 1 3 . 0 4 . 0 0 3
收稿 日 期 :2 0 1 3 — 0 2 — 2 3
商用车车架 常用横梁 的
力学性能研究
题 , 同时不 利 于 降低 车 架 自重 及成 本 。为 了优 化 车架 横 梁
墨 孙 毕 任 动 国 业 东 系 兵 于 风 统 湖 商 科 南 用 仿 大 车 真 学 技 系 工 术 统 程 主 中 力 心 管 底 工 学 专 程 盘 业 部 师 传 ,
主要 研 究 方 向为 汽 车 仿 真分 析 、 结 构优 化及 安 全 性分 析 。 商 用 车 常用 的横 梁种 类 很 多 ,但 是 由于没 有 确 切 的横 梁 弯 曲 和扭 转 性 能参 数 ,因此 总 布置 进 行 车架 设 计 时往 往
架优 化设计 提供 了理 论依 据 。
关键 词 :商用 车横 梁 ;力学性 能 ;优化 设计
中图分类号 :U 4 6 3 . 3 2
文献标志码 :A
文章编号 :1 0 0 5 — 2 5 5 0( 2 0 1 3 )0 4 — 0 0 1 0 — 0 5
横梁的受力分析
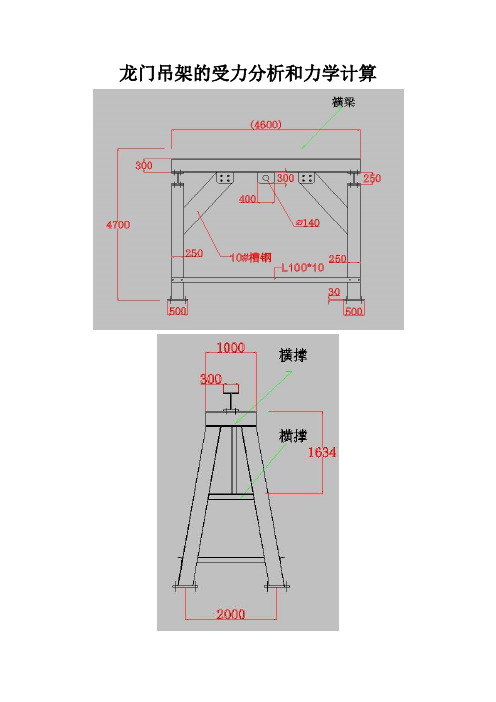
龙门吊架的受力分析和力学计算一、横梁的受力分析和验算已知:梁材料为Q235 30# H 型钢,取许用应力值:110KN/mm 2。
额定载荷:150000N ,葫芦重:1550N ,吊绳重:500N ,梁自重:4278N ,M 为最大弯距,P 为最大载荷(150000+1550+500+427)=158.3KN ,L 为梁长,通过查阅工具书查得:M=PL, 所以P=M/L 由如下剪刀、弯距图可知:4600383.3()1212pl p M p N mm === 经查工具书表查得:I=1/12(b 2h 23-b 1h 13) Z=I/H 2/2 h1=270 b1=290 h2=300 b2=300相对中性面惯性矩I 与截面系数Z 为:336464321(300300290270)199.310()12199.3102132.910()/300I mm I Z mm H I =⨯-⨯=⨯⨯⨯===⨯P=4110132.910381355381.4383.3N KN ⨯⨯=≈ 因为P F =150000N+1550N+500N+4278N=156328N ≈158.3KN <381.4KN 。
此横梁符合受力设计要求。
简支受力分析图P 6P7.38剪刀图Pl29.52Pl12弯距图FW1F R2二、横撑1的受力分析和验算选用Q235 25#H 型钢,其中额定载荷为:158710.8N ,梁自重:724N ,取许用应力值为:110KN/mm 2,M 为最大弯距,P 为最大载荷,L2为梁长, 通过查阅工具书查得:M=PL ,所以P=M/L由如下剪刀、弯距图可知:M=cos7.5P 1/2=1000×0.248·P 1=248 P 1 (N ·mm) 由前面计算得:I=1057.9×105(mm 4) Z=846.3×103(mm 3)37110846.310375.410375.4248P N KN ⨯⨯==⨯≈ 因为P F =158710.8N+724N=159434.8N ≈159.4KN <375.4KN 此横梁符合受力设计要求。
车架横梁上加强筋对局部应力和整车质量影响分析

车架横梁上加强筋对局部应力和整车质量影响分析罗运张怡陈吉清(华南理工大学机械与汽车工程学院,广东广州,510640)摘要:通过建立某半承载式客车整车骨架有限元模型,利用有限元分析手段,采用对比的方法提出加强筋布局的有效加强区域和非有效加强区域,从最大应力角度分析加强筋在有效加强区域内不同布局对V型推力杆支座连接件在制动瞬间的加强效果,体现加强筋的加强作用。
在连接关系和焊接工艺允许的前提下提出三种加强筋布局方案,并对比三种方案的应力分布规律和应力极值,确定加强筋在有效加强区域内的最优布局,并以最优布局的结构为基础,在整车模型下进行尺寸优化和优化结果的分析验证。
由分析结果得出,在有效加强区域内合理设计加强筋,能有效提高局部承载能力,在保持原承载能力的基础上进行尺寸优化,减轻结构的质量。
关键词:车架横梁;加强筋;有效加强区域;尺寸优化1 引言客车前围骨架风挡下横梁和侧围第一立柱接头、后围骨架风挡下横梁和后围立柱接头都设计有加强筋,加强筋的布局位置单一;车门上框架以及车桥前后仓门立柱和侧围腰梁接头处设计有加强型钢,加强型钢的布局位置确定,这两种情况的加强结构有效的提高接头的强度。
目前市场上很多豪华型大型客车均采用空气悬架系统,车架一些结构同传统的板簧式客车车架有些差别,车架的某根横梁承受客车制动瞬间的冲击载荷,为了保证横梁具有足够的强度,在横梁上设计两块加强筋,加强筋的位置由设计者对结构的感知程度确定。
市场上一些客车的横梁加强筋都设计在横梁中部,沿ZX面对称分布。
但这种设计方式能否改善横梁的应力分布及横梁制动瞬间承受冲击载荷的能力,需要分析验证。
本文通过横梁带有加强筋和没有加强筋的分析确定目前加强筋设计方案可行性,并通过对比其它的加强筋设计方案,确定加强筋设计的优选方案,最后对选择的结构进行了尺寸优化。
2 整车骨架有限元模型建立客车车身是一个极其复杂的空间薄壁杆系结构,同时包括部分应力蒙皮。
由于一些非主要承载件对骨架结构的变形和制动工况纵向和横向推力杆支座连接件应力分布影响很小,而且考虑这些结构对问题的求解规模和准确性有很大的影响,因此本文分析模型不考虑蒙皮和装饰件,整车模型如图1所示。
大跨度钢结构桥梁设计中的应力分析与加固措施

大跨度钢结构桥梁设计中的应力分析与加固措施钢结构桥梁是现代桥梁建设中常用的一种形式,大跨度钢结构桥梁更是其重要分支。
而在大跨度钢结构桥梁的设计中,应力分析与加固措施是其重中之重。
本篇文章将会从这两个方面进行探讨。
一、应力分析应力分析是大跨度钢结构桥梁设计中至关重要的一环。
在进行应力分析的过程中,首先需要进行荷载计算,涉及到的荷载主要包括自重、活荷载、温度荷载等。
而对于荷载计算,需要对其进行细致、合理的计算,以免在设计中出现偏差。
当荷载计算确定后,接下来需要进行应力分析。
应力分析是针对不同荷载情况下结构的受力情况进行分析,并确定结构在受力过程中的应力分布情况。
在进行应力分析的过程中,需要综合考虑材质、结构形式、荷载情况等因素,并对应力分布情况进行仿真模拟,确定其安全性。
应力分析完成后,需要进行力学性能验证。
通过试验或者其他方法进行验证,以确定荷载情况下结构的安全性。
如果结构的安全性证明不足,需要进一步进行加固措施。
二、加固措施当大跨度钢结构桥梁的应力分析证明不足以满足安全要求时,需要进行加固措施。
加固措施是结构设计中不可或缺的一环。
加固措施应该适应实际情况,不同情况下的加固措施也应有所不同。
在加固措施中,最常见的就是增加构件的横截面积。
增加构件的横截面积可以有效地加强结构的抗扭强度和抗剪强度,提高结构的稳定性。
同时,在薄弱节点处设置钢板、钢管进行加固也是一种有效的措施。
此外,在现代技术的帮助下,注浆加固技术、纤维增强技术等新技术也被广泛应用在大跨度钢结构桥梁的加固中。
这些新兴技术通常具有成本低、施工便捷、加固效果显著等优点,被广泛认可和应用。
总体而言,大跨度钢结构桥梁的设计中,应力分析与加固措施是密切相关的。
通过对应力分析的细致分析和加固措施的合理设计,可以提高结构的安全性,确保大跨度钢结构桥梁在使用过程中的安全性。
载重货车车架的静力学分析

10.16638/ki.1671-7988.2019.16.043载重货车车架的静力学分析*洪雨,彭闪闪*,王玲芝,许星月,刘通,尹宗军(安徽信息工程学院机械工程学院,安徽芜湖2411001)摘要:车架承受传递给它的各种力和力矩,其必须具有足够的抗弯刚度和强度。
文章以某商用货车车架为原型,利用ANSYS workbench有限元分析软件对车架的四种典型静态工况,包括承载、扭转与弯曲,得到了各工况下该车架的变形和应力分布。
关键词:货车车架;有限元分析;工况中图分类号:U463.32 文献标识码:A 文章编号:1671-7988(2019)16-118-03Static analysis of truck frame*Hong Yu, Peng Shanshan*, Wang Lingzhi, Xu Xingyue, Liu Tong, Yin Zongjun ( Anhui Institute of Information Technology School of Mechanical Engineering, Anhui Wuhu 241100 ) Abstract:The frame experiences the various forces and moments transmitted to it, which must have sufficient bending stiffness and strength. In this paper, the frame of a commercial truck is taken as the prototype, and the four typical static working conditions of the frame, including load-bearing, torsion and bending, are analyzed using ANSYS workbench (a finite element analysis software). The corresponding deformation and stress distribution of this frame under each working condition are obtained.Keywords: truck frame; finite element analysis; working conditionCLC NO.: U463.32 Document Code: A Article ID: 1671-7988(2019)16-118-03前言货车整车大部分的重量都由车架承受,在行驶时车架还需承受来自车内各部件的力和力矩的作用。
横梁受力及变形分析

横梁受力及变形分析
横梁系统为复杂空间结构,需搭建三维受力模型,根据结构特征和装配接触做力系叠加。
对横梁系统而言,受到横梁自重和刀架自重的体积力作用,及组件接触面间表面力作用,前者引起整理结构变形,后者引起局部结构变形,在切削状态还受切削力外力作用引起复杂动态变形。
考虑组件装配接触间隙,接触形式,液压油膜厚度等因素,变形问题复杂。
首先简化结构模型,做整体受力计算简图。
一、横梁本身受自重和刀架重力三维力系搭建
横梁两端靠立柱支撑,梁反面垂直导向面与立柱导轨面结合,结合面定量润滑,液压机构控制后端压板与立柱导轨面夹紧,自此产生Y向面压与垂向静摩擦力。
本机床为重型机床,横梁自重40t,刀架组件重20t,大重量体积力导致横梁产生较大弯曲和扭转变形,必须进行补偿,避免变形导致机床精度超差。
在不考虑横梁和刀架组装结构、组合形式的前提下,做横梁受力模型。
根据横梁受力分析,刀架在横梁中间位置,滑枕向下伸出最长时,横梁变形最大。
即图1中a=0时。
注:O ,K ——横梁、刀架重心。
分别以两点为原点建立横梁全局坐标系和刀架局部坐标系,(a,b,c)为局部坐标系在全局坐标系中坐标;利用UG得到的重量报告
知刀架重心在横梁中间位置时(a,b,c)=(0,619.765,164.5676)。
F1,F2——左右支撑力;
M1,M2——左右支撑扭矩;
G1 ,G2——横梁自重,刀架自重;
G2` ——刀架自重等效力;
M3 ——刀架自重力偶扭矩.
图1 横梁三维受力分析图。
重型载货汽车车架开裂分析与减重优化

重型载货汽车车架开裂分析与减重优化重型载货汽车的车架是整个车身的基础,负责承载车身、发动机、传动系统等各种重要部件的负荷。
然而,在长期的实际使用中,由于道路的震动、负荷的波动等因素,车架会遭受各种压力和挑战,可能会出现裂纹,严重时甚至会导致车身失稳,危及行车安全。
因此,对于重型载货汽车车架的开裂问题,需要进行深入的分析,并实施有效的减重优化措施。
首先,车架开裂的可能原因有很多,其中最常见的原因是由于车架本身的材质问题和设计问题。
例如,使用质量较差的钢材或焊接不良容易导致车架出现弯曲、变形、脆化等问题;车架的结构设计不合理或过于复杂,容易形成应力集中,从而导致裂纹的产生。
因此,在车架的设计、制造环节中,需要严格控制原材料的质量、加强工艺过程的监控,减少结构复杂度,同时根据承载能力和路况等因素进行科学合理的设计和结构优化。
其次,针对车架开裂问题,需要采取有效的减重措施。
重型载货汽车的质量和尺寸较大,车架是造成不必要的质量和能耗消耗的最主要原因之一,而减重不仅可以提高车架的强度和稳定性,降低物体的能量消耗,同时还能提高汽车的燃油效率,节约燃料成本。
减重的具体方案可以根据不同的实际需求进行调整,例如,采用轻量化材料,如铝镁合金、碳纤维等;减少车架结构的重量,如简化结构、减少节点数量、优化连接方式等;加强车身的信号控制和自适应控制等,从而提高汽车的驾驶效率和安全性能。
总的来说,重型载货汽车车架的开裂问题,需要从多方面进行分析和解决。
而减重优化应该是车架维护和改进的一个重要方向,通过适当的材料和结构优化,可以提高车架的稳定性和相应的经济效益。
除了材料选择和结构优化,在车架维护和改进方面,也应该考虑到合理的使用和保养。
特别是对于已经出现了开裂问题的车架,需要进行及时的维修和更换。
在日常使用中,谨慎驾驶和合理的负载分配也是避免车架开裂的重要措施。
过高的行驶速度和不合理的负载分布都会给车架带来额外的压力和挑战,而且在道路行驶时,需要注意避免颠簸和跌落等问题,保持平稳的行驶。
某车型副车架横梁的应力分析及优化
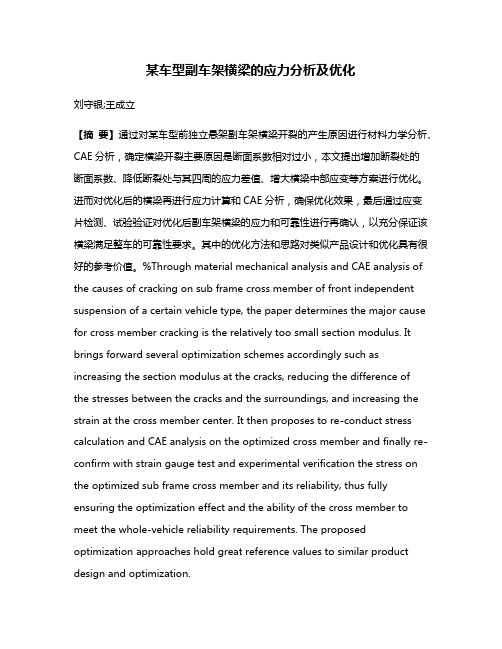
某车型副车架横梁的应力分析及优化刘守银;王成立【摘要】通过对某车型前独立悬架副车架横梁开裂的产生原因进行材料力学分析、CAE分析,确定横梁开裂主要原因是断面系数相对过小,本文提出增加断裂处的断面系数、降低断裂处与其四周的应力差值、增大横梁中部应变等方案进行优化。
进而对优化后的横梁再进行应力计算和CAE分析,确保优化效果,最后通过应变片检测、试验验证对优化后副车架横梁的应力和可靠性进行再确认,以充分保证该横梁满足整车的可靠性要求。
其中的优化方法和思路对类似产品设计和优化具有很好的参考价值。
%Through material mechanical analysis and CAE analysis of the causes of cracking on sub frame cross member of front independent suspension of a certain vehicle type, the paper determines the major cause for cross member cracking is the relatively too small section modulus. It brings forward several optimization schemes accordingly such as increasing the section modulus at the cracks, reducing the difference ofthe stresses between the cracks and the surroundings, and increasing the strain at the cross member center. It then proposes to re-conduct stress calculation and CAE analysis on the optimized cross member and finally re-confirm with strain gauge test and experimental verification the stress on the optimized sub frame cross member and its reliability, thus fully ensuring the optimization effect and the ability of the cross member to meet the whole-vehicle reliability requirements. The proposed optimization approaches hold great reference values to similar product design and optimization.【期刊名称】《汽车实用技术》【年(卷),期】2014(000)008【总页数】4页(P41-44)【关键词】副车架;横梁;应力;断面系数;应力分析;优化【作者】刘守银;王成立【作者单位】安徽江淮汽车股份有限公司技术中心,安徽合肥 230022;安徽江淮汽车股份有限公司技术中心,安徽合肥 230022【正文语种】中文【中图分类】U463.33CLC NO.:U463.33Document Code:AArticle ID:1671-7988(2014)08-41-04某车型的前轴为麦弗逊前独立悬架,在试验场强化路试验过程中前轮受到撞击后,副车架横梁发生开裂现象,如图1所示。
重型汽车管状横梁、盆梁失效分析与改进

10.16638/ki.1671-7988.2021.011.011重型汽车管状横梁、盆梁失效分析与改进袁鹏涛,邢继琼,鲍文芳,袁丽,梁永,陆昱州(陕西重型汽车有限公司,陕西西安710200)摘要:为解决某重型汽车管状横梁、盆梁总成失效率高及各个供应商故障率差异较大的问题,采用质量工具及系统分析方法,找出了影响重型汽车管状横梁、盆梁失效的关键影响因子,通过CAE分析方法对现有结构进行分析,并对改进方案进行了应力应变分析及验证,确定最优方案,提出从设计方面对该型重型汽车管状横梁、盆梁总成进行改进,并对售后表现进行跟踪,改进效果佳,售后故障率大幅下降。
关键词:管状横梁;盆梁总成;质量工具[1];系统分析方法[1];CAE分析中图分类号:U463 文献标识码:A 文章编号:1671-7988(2021)11-30-04Failure Analysis and Improvement of Tubular Beam and Basin Beam of Heavy Truck Yuan Pengtao, Xing Jiqiong, Bao Wenfang, Yuan Li, Liang Yong, Lu Yuzhou(Shaanxi Heavy-duty Motor Company Limited, Shaanxi Xi’an 710200)Abstract: In order to solve the problems of high failure rate of tubular beam and basin beam assembly of a heavy-duty truck and great difference of failure rate among different suppliers, the key influencing factors of tubular beam and basin beam of heavy-duty truck are found out by using quality tools and system analysis method. The existing structure is analyzed by CAE analysis method, and the stress-strain analysis and verification of the improvement scheme are carried out, and the best result is determined it is proposed to improve the tubular beam and basin beam assembly of the heavy truck from the design aspect, and track the after-sales performance. The improvement effect is good and the after-sales failure rate is greatly reduced.Keywords: Tublar; Basin beam assembly; Quality tools[1]; Systemic analysis method[1]; CAE analysisCLC NO.: U463 Document Code: A Article ID: 1671-7988(2021)11-30-041 前言众所周知,管梁主要作用为缓解车辆重载状态下在恶劣路面运行时车架扭转变形[2],消除应力,防止车架开裂造成重大安全事故,盆梁与管梁的作用为相辅相成关系,盆梁的存在更进一步改善车架的扭转变形。
中型载货汽车车架有限元静力学分析
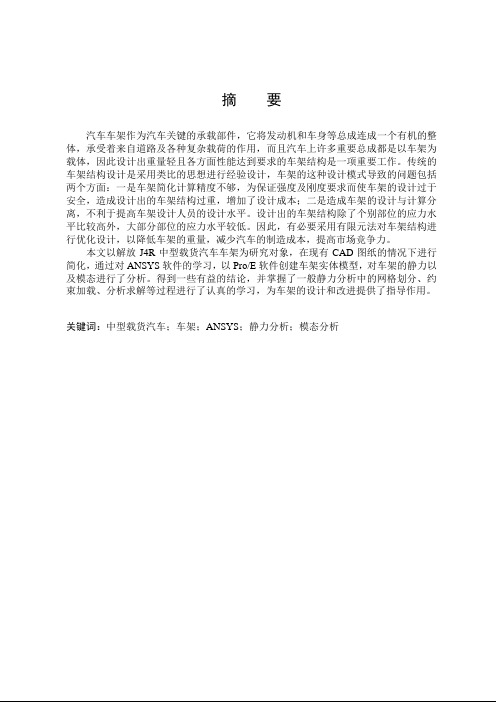
摘要汽车车架作为汽车关键的承载部件,它将发动机和车身等总成连成一个有机的整体,承受着来自道路及各种复杂载荷的作用,而且汽车上许多重要总成都是以车架为载体,因此设计出重量轻且各方面性能达到要求的车架结构是一项重要工作。
传统的车架结构设计是采用类比的思想进行经验设计,车架的这种设计模式导致的问题包括两个方面:一是车架简化计算精度不够,为保证强度及刚度要求而使车架的设计过于安全,造成设计出的车架结构过重,增加了设计成本;二是造成车架的设计与计算分离,不利于提高车架设计人员的设计水平。
设计出的车架结构除了个别部位的应力水平比较高外,大部分部位的应力水平较低。
因此,有必要采用有限元法对车架结构进行优化设计,以降低车架的重量,减少汽车的制造成本,提高市场竞争力。
本文以解放J4R中型载货汽车车架为研究对象,在现有CAD图纸的情况下进行简化,通过对ANSYS软件的学习,以Pro/E软件创建车架实体模型,对车架的静力以及模态进行了分析。
得到一些有益的结论,并掌握了一般静力分析中的网格划分、约束加载、分析求解等过程进行了认真的学习,为车架的设计和改进提供了指导作用。
关键词:中型载货汽车;车架;ANSYS;静力分析;模态分析ABSTRACTAs an important component, frame carrying the whole vehicle, such as assembly, take the engine and body together into an organic whole,endure the loads from the road and many kind of complex loads, and many important assemblys are based on frame,use the frame as a vector. So design a lightweight and all aspects of performance to meet the requirements of the frame structure is an important work. The frame structure of traditional design is the idea of experience with analog design, this methed caused two problems: First, simplify the calculation accuracy of the frame is not enough to ensure the strength and stiffness requirements of leaving the frame design is too safe, resulting the frame structure designed overweight. Second is caused by separation of design and calculation of the frame, the frame is not conducive to raising the level of the designer's design. In addition to the frame structure designed for individual parts of the stress level is relatively high, most parts of the stress level low. Therefore, it is necessary to use finite element method to optimize the design of the frame structure to reduce the chassis weight, reduce vehicle manufacturing costs, improve market competitiveness.In this paper, use FAW J4R medium truck frame for the study, in study of ANSYS software ,and use Pro / E software to create solid models of the static frame and the mode were analyzed. Get some useful conclusions, and mastery of the general process of static analysis for improved frame design and provide guidance.Key words: MediumTruck ;Frame;ANSYS;Static Analysis;Modal Analysis目录摘要 (I)A bstract (II)第1章绪论 (1)1.1 选题的背景 (1)1.2 选题的目的 (1)1.3 选题的意义 (1)1.4 研究现状 (2)1.5 课题主要内容 (4)第2章有限元基础及ANSYS软件介绍 (5)2.1 有限元分析简介 (5)2.2 有限元方法的基本求解过程 (6)2.3 有限元分析的误差及建模准则 (7)2.4有限元分析软件ANSYS简介 (9)2.4.1 ANSYS的发展概述 (9)2.4.2 典型的ANSYS分析过程 (10)2.4.3 ANSYS的主要功能 (11)2.4.4 ANSYS的主要特点 (12)2.4.4 ANSYS软件提供的分析类型 (13)2.5 本章小结 (14)第3章车架有限元模型的建立 (15)3.1 车架的实体建模 (15)3.1.1 Pro/E软件简介 (15)3.1.2 Pro/E软件基本功能 (16)3.1.3 几何建模的简化 (16)3.2 应用Pro/E软件三维几何模型的建立 (18)3.3 应用ANSYS软件对车架模型进行网格划分 (19)3.4 实体单元Solid 45的简介 (21)3.5 本章小结 (24)第4章车架有限元的静力级模态分析 (25)4.1 车架静力分析 (25)4.1.1 车架受力情况 (25)4.1.2车架结构静力分析及约束处理 (26)4.2 车架模态分析 (33)4.2.1 结构动力性能分析方程 (34)4.2.2 车架结构模态分析 (34)4.2.3 分析结果 (41)4.3 本章小结 (41)结论 (42)参考文献 (43)致谢 (44)附录 (45)第1章绪论1.1 选题的背景车架是汽车各总成的安装基体,它将发动机和车身等总成连成一个有机的整体,承受着来自道路及各种复杂载荷的作用,而且汽车上许多重要总成都是以车架为载体,因此设计出重量轻且各方面性能达到要求的车架结构是一项重要工作。
浅析重卡车横梁布置对车架强度的影响

浅析重卡车横梁布置对车架强度的影响作者:王永来源:《汽车世界·车辆工程技术(中)》2019年第02期摘要:重卡车横梁的布置对于车架强度会产生不同程度的影响,分析重卡车对横梁布置产生的影响,可以为重卡车横梁布置与优化设计提供有效参考与支持。
基于此,文章主要对重卡车横梁布置对车架强度的影响进行了简单的分析论述,通过有限元模式对其进行了分析,探究了重卡车横梁布置对车架强度的影响的主要因素与完善对策与手段。
关键词:横梁布置;车架强度;影响车架是汽车的骨架,是汽车承载的基础,承载着多数的零部件以及总成系统,车架要承受来自车内外的各种荷载形式。
对此,车架要具有充足的强度与合适的刚度,这样才可以保障其整体性能指标。
分析重卡车横梁布置,了解其对车架强度产生的影响,探究轻量化方式,缩减车架的结构,具有一定价值与意义。
1 重卡车横梁布置对车架强度的影响横梁是连接纵梁的重要零部件,可以保障车架扭转刚度以及承受的纵向荷载,也是支撑汽车上主要零部件的结构,横梁的布置会直接的影响车架的强度。
在凹凸不平的路面上行驶过程中,汽车就会因为超过车辆的应力车架而导致其出现垂直性的冲击荷载问题。
同时,车架设计或者在附属装置中会产生一些局部的扭矩力,这样就会导致车架断裂等问题的出现。
例如,车架纵梁前部横截面相对较小,在发动机与变速器的位置则就会影响横梁的分布,此种布置会降低车架的整体刚度,进而造成纵梁前部位置断裂等问题的出现。
而在汽车的上下坡、转弯或者装载不均匀等状况之下也会导致车架因为局部过载而造成车架断裂等问题的出现。
车架也会因为与纵梁的悬臂和在垂直而造成局部的扭曲问题,这些问题都会造成车架断裂等问题的出现。
车架横梁布置会对车架强度产生较为严重的影响,在实践中要分析重卡横梁布置状况,了解其具体状况,探究其对车架强度产生的影响。
2 车架结构与横梁布置(1)车架结构。
车架主要是通过纵梁、发动机支架、离合器支架等相关理论观念部件组合形成。
车架总成后横梁应力测试

车架总成后横梁应力测试技术邻作者:月落文章所包含领域及技术点:应力测试、车架、ansys1.试验目的针对改装后的车架总成,测试后横梁在设计最大负荷作用下的应力分布及最大应力值,并与有限元计算结果比较,验证其强度是否达到设计值。
2.引用标准GBT6792-2009客车骨架应力和形变测量方法GB T12534-90汽车道路试验方法通则3.试验条件及试验车辆的准备3.1试验场地与环境a.试验用车架总成按设计图纸按1:1比例制造;b.试验场地为室内,常温。
3.2试验仪表、器具a.电阻应变仪,测量范围0~30000me,分辨率1me;b.数据采集器,A/D转换率200kHz;A/D分辨率16位;c.电阻应变花,阻值120Ù;屏蔽电缆d.钢尺,卡尺,秒表。
3.3其他车辆试验条件的准备应符合GB/T12534的有关规定。
4.应力测量方法4.1确定测点布置方案选择车架后横梁总成车钩孔位置附近、后横梁总成的内、外沿平整处。
按结构受力情况,根据有限元分析结果,确定最大应变出现的区域,各测点均采用电阻应变花。
4.2确定应变片栅长与种类根据应力分布梯度,选择合适的应变片栅长与种类。
4.3应变片粘贴与引线焊接对测量区域进行清洗后,用手砂轮或砂纸打磨表面,去掉铁锈、油漆和污垢,达到左右,按布置方案用记号笔画出标记线,用四位惠斯顿电桥测量各应变片的电阻值,要求其偏差在±0.5欧姆以内,然后用胶水进行粘贴。
粘贴完毕后,焊接应变片引线。
焊接之前应在靠近应变片位置处粘贴接线端子,焊接引线时要注意与基体的绝缘,引出电缆要注意屏蔽。
焊接完成后要对应变片、接线端子一起采用密封胶做防潮和绝缘处理。
4.4应变仪的连接与调平应变花的每个应变片采用单臂方式接入电阻应变仪,每一支路都单独调平,注意接入与所用应变花相同阻值的温度补偿电阻。
5.车架装卡与载荷施加车架装卡利用试验场地提供的设备,安装方法依照使用说明书进行。
载荷施加在牵引钩上,最大载荷30吨。
- 1、下载文档前请自行甄别文档内容的完整性,平台不提供额外的编辑、内容补充、找答案等附加服务。
- 2、"仅部分预览"的文档,不可在线预览部分如存在完整性等问题,可反馈申请退款(可完整预览的文档不适用该条件!)。
- 3、如文档侵犯您的权益,请联系客服反馈,我们会尽快为您处理(人工客服工作时间:9:00-18:30)。
商用车车架横梁的应力分析
摘要:车架是汽车各总成零部件的安装基体,它将发动机和车身等总成连成一
个有机的整体,组成一辆完整的汽车。
要求有足够的强度:保证在各种复杂的受
力状况下,车架及底盘上的各总成不致因变形或疲劳而早期损坏或失去正常的工
作能力。
有适当的扭转刚度:当汽车行驶在不平路面时,为了保证汽车对路面不
平度的适应性,提高汽车的平顺性和通过能力。
车架横梁作为车架的关键零部件,横梁的主要作用是连接纵梁,构成一完整的框架,保证车架承载性能,具有足够
的强度和抗扭转刚度。
关键词:商用车;车架横梁;应力;
横梁是商用车车架的重要组成部分,它将左右纵梁连在一起,构成一个完整
的车架,并保证车架有足够的扭转刚度,以限制纵梁变形和降低某些部位的应力,此外横梁还起着支撑某些总成的作用。
商用车车架横梁一般有管状横梁、槽型横梁、鸭嘴横梁、方形横梁等多种形式。
在车架上布置位置不同,对横梁的选择也
会多种多样。
一般情况下,同一车型的中间横梁采用的结构是相同的。
一、概述
对于非承载式车身的车型,车架是整车的装配基体和承载基体,承载着汽车
各总成,并承受着各种力及力矩。
设计合理的车架是开发非承载式汽车重中之重,设计车架即不可过强,避免造成材料浪费,增加产品成本;又不可过弱,避免车
辆寿命周期内发生开裂,对乘客造成伤害。
因此,对车架疲劳耐久寿命预估是车
架开发的重要内容。
车架由不同厚度、不同形状的冲压钣金焊接而成,焊缝数量
多且走势复杂,根据工程经验,车架疲劳失效主要发生在焊缝及其热影响区域,
因此对焊缝及热影响区进行有限元模拟及寿命预测势在必行。
通过有限元分析的
方法对结构最大等效应力进行分析比较,并通过分析验证改进的合理性。
二、商用车车架横梁的应力分析
1.车架扭转疲劳台架试验。
根据企业车架扭转疲劳台架试验规范,对车架进
行台架扭转疲劳试验模拟实车状态,把车架总成固定在台架试验台上,用专用夹
具固定车架后弹簧座吊耳,可绕X 轴旋转加载装置与前弹簧座支架通过专用夹具
连接,激振器作用通过加载装置Z 向加载,加载扭矩±2000N•m,加载频率3Hz,
顺时针、逆时针各加载一次计一个循环。
试验要求循环20 万次,车架焊缝及钣
金均不能开裂。
共做了三个车架的扭转疲劳台架试验,分别在15 万次、18万次、13 万次发生焊缝开裂,焊缝开裂位置均是第三横梁与车架纵梁连接处焊缝开裂,
白线位置。
由台架试验结果可知,车架焊缝不满足20 万次寿命要求,亟需借助
先进有限元方法找到焊缝失效原因,并提出有效改进措施。
在使用过程中因多次
扭转达到疲劳极限产生开裂,而横梁抗扭性能好,能很好的适应扭转工况。
2.车架焊缝有限元模拟。
车架是由纵梁、横梁及支架组成的焊接总成件,纵梁、横梁及支架为薄板钣金结构,冲压钣金工艺简单,加工工艺引起材料性能变
化不大,有限元模拟方法为抽中面选用PSHELL 单元、料厚赋予钣金实际料厚模拟,已经过试验验证方法有效。
而车架焊缝数量多,分布广且是车架易失效风险位置,焊接焊缝时,焊缝本体及母材在高温下发生材料性能复杂变化,如何用有限元方
法正确模拟焊缝本体及焊缝热影响区,对准确评估车架性能意义重大。
采用两种
常用焊缝建模方法构建车架有限元模型,模拟台架试验规范建立有限元分析工况,并运用有限元分析结果进行车架扭转疲劳台架试验寿命预测。
比较两种不同焊缝
建模方法计算所得台架扭转疲劳试验寿命,选用与台架试验结果相吻合车架焊缝
建模方法,并应用该有限元建模方法查找焊缝开裂原因,提出改进方案。
一般来说,焊缝可以通过rigid 单元、Weld 单元或Pshell 单元模拟,根据多年企业经验,采用rigid 单元、Weld 单元会导致有限元结果偏刚,并且rigid 单元不能赋予焊缝
疲劳材料属性,因此不能采用rigid 单元、Weld 单元来预测焊缝疲劳耐久寿命。
因此,采用单元模拟焊缝,单元可以灵活赋予不同厚度、不同材料来模拟焊缝属性,网格平均尺寸7mm,单元类型为CQUADR&CTRIAR,焊缝单元垂直焊接平面,焊缝单元沿着实际焊缝位置分布,焊缝单元不能穿过焊接钣金单元的对角线。
焊
缝单元及相邻单元尽量采用四边形网格并保证良好的网格质量。
企业研究表明,
焊缝本体及焊缝热影响区材料疲劳耐久属性相近且均与钣金母材不同,因此焊缝
本体及热影响区属性要区别于钣金母材单独赋予材料、料厚属性。
通过比较两种
不同材料、料厚属性单元焊缝建模方法下疲劳耐久寿命结果,确定适用于预测车
架疲劳耐久台架试验寿命的焊缝建模方法。
3.车架强度分析。
车架强度分析分为静强度分析和疲劳分析。
静强度分析又
分为垂向加速度静载工况、横向转弯工况和对角扭转工况,因对角扭转工况对车
架考察最为严格,本次分析只进行对角扭转工况下的静强度分析。
对角扭转工况
定义: 通过对角轮中心同时抬高一定高度值来实现车架扭转。
前轮一侧约束平动
自由度,另一侧约束自由度,其中自由度参照车架分析载荷定义值给定。
其他轮
约束自由度,其中一侧自由度参照车架分析载荷定义值给定,保证车架扭转的实现。
,管状横梁车架管横梁两端连接板应力较小,钢管部分应力偏大; 槽型横梁
车架槽横梁连接板局部应力较大; 鸭嘴横梁车架与车架连接部分局部应力偏大,
但整体应力最小。
综上所述,管状横梁车架最大应力点值相对较小,槽型横梁车
架最大应力点值最大,鸭嘴横梁车架最大应力点值居于两者之间。
4.焊缝寿命预估。
一是焊缝应变载荷历程。
以采用焊缝建模方法所得焊缝开
裂处起始单元应力为例,介绍焊缝应力载荷历程构建过程,由有限元静强度分析
结果可知,加载顺时针扭矩时,开裂焊缝起始单元应力为240MPa,加载逆时针
扭矩时,该单元应力为-203MPa,由疲劳理论可知,金属疲劳寿命与载荷幅值有关,与载荷波形无关,因此采用单位三角载荷构造台架应力载荷历程。
由法则转
换线性应力为局部应力应变历程,法则是基于对称循环应力应变进行计算的,因
此再由法则修正平均应力应变对寿命影响,转换成对称应力应变循环,以便于应
用焊缝应变-寿命曲线进行寿命预估。
零部件表面光滑度、表面处理工艺等表面状态对零件寿命有显著影响,表面越光滑越不容易产生疲劳裂纹,而焊缝表面比较
粗糙,降低了疲劳寿命,因此,进行焊缝寿命预测时,根据企业经验,以系数
0.6 修正焊缝粗糙表面对寿命影响。
二是焊缝寿命分析结果。
将焊缝台架动态应
变历程与焊缝应变-寿命曲线导入中,求得车架焊缝寿命。
方法得出第三横梁与纵梁连接处焊缝寿命14 万次,焊缝建模方法预估疲劳耐久寿命已满足20 万次寿命
要求,不能再现台架焊缝开裂问题。
方法所得焊缝寿命不满足20 万次寿命要求,具有开裂风险,与车架扭转台架疲劳试验结果吻合,且开裂位置一致,故可以采
用方法模拟车架扭转台架疲劳试验以找到焊缝开裂原因、优化方案并快速验证优
化方案。
三、结束语
横梁是商用车车架的重要组成部分,它将左右纵梁连在一起,构成一个完整
的车架,并保证车架有足够的扭转刚度,以限制纵梁变形和降低某些部位的应力,此外横梁还起着支撑某些总成的作用。
选用的有限元分析方法预测焊缝开裂风险
位置与台架试验开裂位置一致。
参考文献:
[1]钱立军,吴道俊,祝安定.基于模态应力恢复的车架疲劳寿命计算研究[J].中国机械工程,2017,22(7):780-784
[2]韩旭,朱平,余海东.基于刚度和模态性能的轿车身轻量化研究[J].汽车工程,2017,29(7):545 -546.
[3]王文涛,上官文斌,段小成.基于线性疲劳累计损伤橡胶悬置疲劳寿命预测研究[J].机械工程学报,2016,148(10):56-65.。