钢铝结合商用车车架轻量化技术综述
全铝及钢-铝混合车身轻量化连接技术

全铝及钢-铝混合车身轻量化连接技术作者:何聪吴丁磊来源:《汽车世界·车辆工程技术(上)》2020年第01期摘要:由于时代的发展,在汽车工业制造的过程中,铝合金开始逐渐受到重视,并且广泛的使用于汽车制造行业中。
在传统的汽车制造行业里,汽车制造的原材料多为钢材,随着铝及铝合金材料的逐渐流行,汽车制造也开始使用铝合金、纯铝等材料充当原材料。
这就涉及到了多种材料的拼接与连接。
轻量化的连接技术就能够使得铝混合材料有较好的连接效果,因此本文将对铝混合车身的轻量化连接技术进行分析与研究。
关键词:全铝及钢;铝混合车身;轻量化连接1 铝混合车身的优势概述铝混合车身相比较传统的全钢车身而言,有十分明显的优势。
传统的全钢制车身太过笨重,不利于日常的使用。
而铝混合车身则完全继承了铝混合原料的特点,质量较轻。
同样大小的铝混合材料,重量只有全钢制材料的三分之一,故而哪怕使用铝混合材料制成车身,也能够比全钢制的车身轻便不少,这样轻便的车身很符合车身轻量化的绿色设计理念,故而有推广的可能性。
再者,使用铝混合材料来进行车身制造,是可以不用进行防锈处理的,因为铝混合材料不怎么容易生锈。
倘若汽车已经过了使用年限,需要报废,那么使用铝混合材料制成的车身,还有利于回收这一大优点。
故而对于汽车制造而言,使用铝混合材料进行轻量化车身制造是很有必要的,有它来替代传统的纯钢制材料是必然的,符合社会的发展潮流。
2 现阶段连接技术分析现阶段的铝混合材料连接技术,主要分为三大类型,第一种是采用焊接技术来进行铝混合材料的连接。
这种连接是热连接,在工业制造中经常使用到的激光焊以及电阻电焊的方法,就属于这类焊接技术。
第二种是机械连接,机械连接在工业制造中也使用得较为广泛,但是机械连接与焊接技术不尽相同,机械连接是冷连接工艺,各种类型的铆接便都属于机械连接工艺。
除了这两种工艺之外,还有一种连接工艺叫粘接,粘接是一种复合型的连接技术,但是比起前两种而言,粘接运用的范围便没有那么普遍了,因此在下文的表格中,粘接技术不做深入的阐述与分析。
车身轻量化与钢铝一体化结构新技术研究

车身轻量化与钢铝一体化结构新技术研究进展前言着眼于可持续发展,节约资源、减少环境污染成为世界汽车工业界亟待解决的两大问题。
汽车每减重10%,油耗可降低6%~8%。
因此减轻汽车重量是节约能源和提高燃料经济性的最基本途径之一。
车身质量占汽车总质量的40%左右,车身的轻量化对于整车的轻量化起着举足轻重的作用,汽车轻量化正成为21世纪汽车技术的前沿和热点.实现车身结构轻量化主要有两个途径:一是选用强度更高、重量更轻的新材料,例如铝合金、高强度钢材等;二是设计更合理的车身结构,使零部件薄壁化、中空化、小型化、复合化以及对车身零部件进行结构和工艺改进等。
第一种途径在目前看来应该是车身轻量化的主流,针对规模化生产的需要,已有很多轻质材料应用于车身制造工业,如高强度钢、铝合金和碳纤维等.第二种途径是利用有限元法和优化设计等方法对车身进行结构分析及优化设计,以减小车身骨架和车身钢板的质量.以上两种途径是相辅相成的,必须采取材料替换与结构改进相结合的方法,才可能在保证汽车整体质量和性能不受影响的前提下,最大限度地减轻各零部件的质量。
钢铝一体化车身框架结构是在传统的车身骨架钢质结构中,有些构件或组件用铝合金材料代替,且通过优化设计和性能模拟方法确定钢铝的不同比例及以铝代钢的部位,实现车身框架结构的轻量化和高强度。
这种结构是车身轻量化的两种根本途径结合的典型应用,完全符合车身轻量化的发展技术路线。
1 国内外车身轻量化技术的发展现状1.1 运用新材料实现车身轻量化自1973年石油危机以来,世界各汽车厂在轿车上进行轻量化研究的进展较为明显。
现代汽车中占自重90%的6类材料大体为:钢55%~60%,铸铁12%~15%,塑料8%~12%,铝6%~10%,复合材料4%,陶瓷及玻璃3%。
用新型板材及轻型材料(如镁、铝、塑料和复合材料等)替换车身骨架及内、外壁板原有的钢材来实现轻量化是车身轻量化技术重要途径之一,主要体现在以下几个方面。
9.6米厢式货车铝合金车厢轻量化设计及优化

9.6米厢式货车铝合金车厢轻量化设计及优化9.6米厢式货车铝合金车厢轻量化设计及优化随着物流运输业的不断发展,货车作为一种重要的运输工具,其设计和制造也面临着挑战。
在货车设计中,车厢的负重能力和车身的轻量化是关键的考虑因素之一。
本文将着眼于9.6米厢式货车铝合金车厢的轻量化设计和优化。
首先,我们需要了解铝合金在车身设计中的优势。
相对于传统的钢材,铝合金具有更高的强度和较低的密度。
这使得铝合金适合于重量敏感的应用,如货车车厢。
同时,铝合金具有良好的耐腐蚀性能,可以延长车身的寿命。
在设计过程中,我们需要考虑车厢的稳定性和刚性。
通过材料替换,使用铝合金能够减少车身的自重,从而提高整体的有效载重能力。
此外,车厢的结构设计也需要满足载货稳定性的要求,确保货物在运输过程中不会发生移动或损坏。
在保持结构稳定性的前提下,轻量化设计需要考虑到材料的合理分布和形状优化。
通过使用优化设计软件和有限元分析方法,我们可以确定最佳的材料厚度和材料位置,以提高整体的刚度,并减少不必要的材料浪费。
此外,使用铝合金还可以采用回收再利用的方式,减少资源浪费和环境污染。
除了材料的优化,我们还可以通过其他设计手段来进一步降低车身的重量。
例如,可以采用空心结构、蜂窝结构或者梁柱结构来代替传统的实心结构,以实现更高的强度和更低的重量。
此外,采用高强度螺栓和焊接技术可以提高连接处的强度和刚度,进一步降低车身的重量。
此外,我们还需要考虑到车辆的安全性。
在轻量化设计中,我们不能仅仅追求减少重量而忽视安全性。
因此,在设计过程中,我们需要对车辆进行全面的结构强度分析和碰撞模拟,以确保车身在意外情况下能够提供足够的保护。
这可以通过使用高强度材料、加厚关键结构部件和合理布置吸能区域来实现。
综上所述,9.6米厢式货车铝合金车厢的轻量化设计和优化是一项挑战,但也是十分重要的。
通过合理的材料选择、优化的结构设计和全面的安全考虑,我们可以实现车身重量的降低,提高车辆的负载能力,并减少资源的消耗。
汽车轻量化解决方案全铝车身结构技术
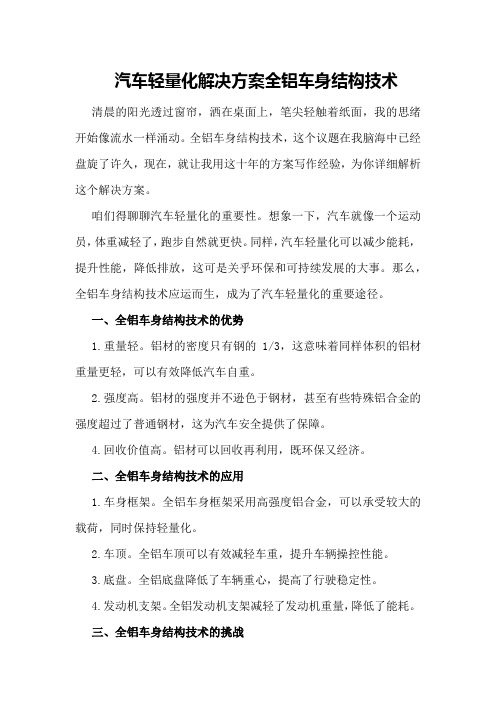
汽车轻量化解决方案全铝车身结构技术清晨的阳光透过窗帘,洒在桌面上,笔尖轻触着纸面,我的思绪开始像流水一样涌动。
全铝车身结构技术,这个议题在我脑海中已经盘旋了许久,现在,就让我用这十年的方案写作经验,为你详细解析这个解决方案。
咱们得聊聊汽车轻量化的重要性。
想象一下,汽车就像一个运动员,体重减轻了,跑步自然就更快。
同样,汽车轻量化可以减少能耗,提升性能,降低排放,这可是关乎环保和可持续发展的大事。
那么,全铝车身结构技术应运而生,成为了汽车轻量化的重要途径。
一、全铝车身结构技术的优势1.重量轻。
铝材的密度只有钢的1/3,这意味着同样体积的铝材重量更轻,可以有效降低汽车自重。
2.强度高。
铝材的强度并不逊色于钢材,甚至有些特殊铝合金的强度超过了普通钢材,这为汽车安全提供了保障。
4.回收价值高。
铝材可以回收再利用,既环保又经济。
二、全铝车身结构技术的应用1.车身框架。
全铝车身框架采用高强度铝合金,可以承受较大的载荷,同时保持轻量化。
2.车顶。
全铝车顶可以有效减轻车重,提升车辆操控性能。
3.底盘。
全铝底盘降低了车辆重心,提高了行驶稳定性。
4.发动机支架。
全铝发动机支架减轻了发动机重量,降低了能耗。
三、全铝车身结构技术的挑战1.成本较高。
相较于传统钢材,铝合金的成本较高,这无疑增加了汽车制造成本。
2.加工难度大。
铝合金的加工工艺较为复杂,对生产线的要求较高。
3.结构设计难度。
全铝车身结构的设计需要充分考虑材料的特性,这对设计师提出了更高的要求。
四、解决方案1.降低成本。
通过优化供应链,提高材料利用率,降低铝合金成本。
2.提高加工技术。
引入先进的加工设备和技术,提高铝合金的加工效率和质量。
3.加强结构设计。
结合材料特性,优化车身结构设计,提高车辆性能。
4.推广应用。
加大全铝车身结构技术的宣传力度,提高市场认可度。
写着写着,阳光已经悄然移动,时间在指尖流转。
汽车轻量化解决方案全铝车身结构技术,这个议题就像一幅画卷,在我面前缓缓展开。
基于铝合金材料应用的重卡车架设计及轻量化

基于铝合金材料应用的重卡车架设计及轻量化周友明】,程一明2,李骏】,姚明波1(1.东风柳州汽车有限公司,广西柳州545000;2.广西艾盛创制科技有限公司,广西柳州545000)摘要:重卡车架的轻量化对于节能减排、提高产品市场竞争力等方面有着直接的影响。
铝合金材料在重卡车架的应用对于重卡减重有着显著的效果。
以目前量产车型车架为基础,结合CAE有限元仿真分析手段,重点关注车架强度、刚度性能,以铝合金车架代替原钢制车架,从而以材料替换及结构优化的手段,实现车架轻量化的目标。
根据仿真分析结果,车架主体纵梁及横梁替换为铝合金材料后,在考虑成型工艺及连接工艺的前提下,车架整体强度、刚度性能达到钢制车架水平,方案可行,轻量化效果显著。
关键词:重卡;轻量化;车架;铝合金;刚度;强度;有限元中图分类号:U463.1文献标志码:A文章编号:1002-2333(2021)05-0091-04 Design and Lightweight of Heavy Truck Frame Based on Aluminum Alloy Material ApplicationZHOU Youming1,CHENG Yiming2,LI Jun1,YAO Mingbo1(1.Dongfeng Liuzhou Automobile Co.,Ltd.,Liuzhou545000,China;2.Guangxi Aisheng Chuangzhi Technology Co.,Ltd.,Liuzhou545000,China) Abstract:The lightening of heavy truck frame has a direct impact on energy conservation,emission reduction and improve product market competitiveness.This paper takes the current mass-produced vehicle frame as the research goal. Combined with CAE finite element simulation analysis,the strength and stiffness performance of the frame are concerned, and the aluminum alloy frame is used to replace the original steel frame,so as to achieve the goal of lightweight frame by means of material replacement and structural optimization.According to the simulation analysis results,after the main body of the frame longitudinal are replaced with aluminum alloy material,the overall strength and stiffness performance of the frame can reach the level of steel frame under the premise of considering the forming process and connection process. The scheme is feasible and the lightweight effect is significant.Keywords:heavy truck;lightweight;frame;aluminum alloy;stiffness;strength;finite element0引言根据欧洲铝协的数据表明,汽车质量每减重100kg,每百公里可节约0.6L燃油。
全铝及钢-铝混合车身轻量化连接技术
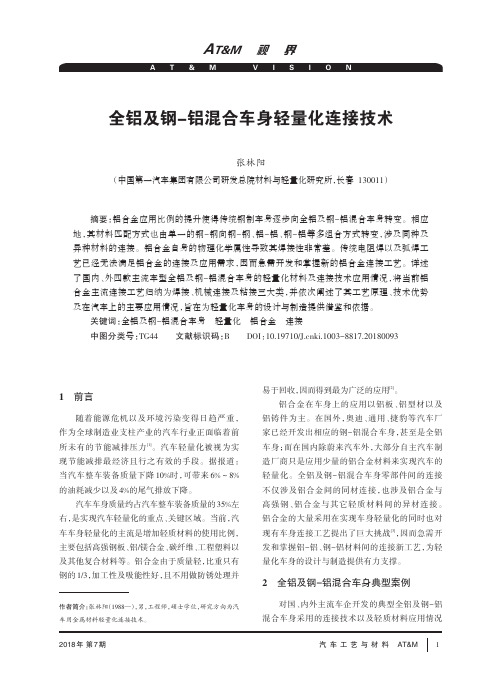
摘要:铝合金应用比例的提升使得传统钢制车身逐步向全铝及钢-铝混合车身转变。
相应地,其材料匹配方式也由单一的钢-钢向钢-钢、铝-铝、钢-铝等多组合方式转变,涉及同种及异种材料的连接。
铝合金自身的物理化学属性导致其焊接性非常差。
传统电阻焊以及弧焊工艺已经无法满足铝合金的连接及应用需求,因而急需开发和掌握新的铝合金连接工艺。
详述了国内、外四款主流车型全铝及钢-铝混合车身的轻量化材料及连接技术应用情况,将当前铝合金主流连接工艺归纳为焊接、机械连接及粘接三大类,并依次阐述了其工艺原理、技术优势及在汽车上的主要应用情况,旨在为轻量化车身的设计与制造提供借鉴和依据。
关键词:全铝及钢-铝混合车身轻量化铝合金连接中图分类号:TG44文献标识码:BDOI :10.19710/ki.1003-8817.20180093全铝及钢-铝混合车身轻量化连接技术张林阳(中国第一汽车集团有限公司研发总院材料与轻量化研究所,长春130011)作者简介:张林阳(1988—),男,工程师,硕士学位,研究方向为汽车用金属材料轻量化连接技术。
1前言随着能源危机以及环境污染变得日趋严重,作为全球制造业支柱产业的汽车行业正面临着前所未有的节能减排压力[1]。
汽车轻量化被视为实现节能减排最经济且行之有效的手段。
据报道:当汽车整车装备质量下降10%时,可带来6%~8%的油耗减少以及4%的尾气排放下降。
汽车车身质量约占汽车整车装备质量的35%左右,是实现汽车轻量化的重点、关键区域。
当前,汽车车身轻量化的主流是增加轻质材料的使用比例,主要包括高强钢板、铝/镁合金、碳纤维、工程塑料以及其他复合材料等。
铝合金由于质量轻,比重只有钢的1/3,加工性及吸能性好,且不用做防锈处理并易于回收,因而得到最为广泛的应用[2]。
铝合金在车身上的应用以铝板、铝型材以及铝铸件为主。
在国外,奥迪、通用、捷豹等汽车厂家已经开发出相应的钢-铝混合车身,甚至是全铝车身;而在国内除蔚来汽车外,大部分自主汽车制造厂商只是应用少量的铝合金材料来实现汽车的轻量化。
钢铝混合车身连接工艺概述

钢铝混合车身连接工艺概述一、车身轻量化途径汽车轻量化技术可以分为:结构优化设计、轻量化材料的应用和先进制造工艺等3个主要方面。
其中,结构优化设计方面包括:汽车结构的尺寸优化、形状优化、拓扑优化和多学科设计优化;轻量化材料的应用方面包括:高强度钢、铝合金、镁合金、塑料和复合材料等;先进制造工艺方面包括:液压成型和激光焊接等。
二、混合材料车身未来的汽车车身应由钢和一些铝合金、镁合金、碳纤维、塑料等轻质材料共同制造,即混合材料车身。
混合材料车身结构的理念能较好地兼顾各方面的要求,寻求轻量化效果、工艺性、安全性和成本等总体上的最优化,代表了今后汽车车身结构发展的最新趋势。
钢铝混合车身结构即是在传统钢结构车身骨架中,将某些结构构件用高强度钢板和铝合金等轻质材料替代,以充分发挥高强度钢板在强度和价格方面的优势,同时兼顾铝合金板材在减重及吸能方面的优势,通过材料和结构的优化设计和性能模拟的方法确定不同材料分布的部位。
三、铝合金车身在国内的应用国内铝合金车身应用得比较广泛及成熟的车企有奇瑞捷豹路虎和上汽通用凯迪拉克,国内也有少量车企有应用,例如蔚来汽车(车型未量产)、北汽新能源、奇瑞新能源等。
四、铝合金车身主要连接工艺从目前的研究大部分车企应用情况来看,比较适用于铝合金车身及钢铝混合车身的连接工艺有:铝点焊、SPR x压力连接(C1inching)、热熔自攻丝(FDS)、弧焊、激光焊、粘接、包边、螺柱焊、摩擦搅拌焊等。
1、铝合金点焊因铝合金熔点低、线膨胀率高、导电率高、表面易氧化等特性,铝点焊须采用大电流、短时间、多脉冲、大电极压力,所以铝点焊时输出大电流对焊机、变压器(最大达230KVA)及焊枪的供电要求高,大电极压力需焊枪结构牢固可靠。
大电流易产生强磁场,焊接工装需防磁以防焊接时通讯信号丢失。
常见的铝合金点焊形式有:①常规铝合金点焊;②螺旋状电极铝合金点焊;③电极带式铝点焊。
常规铝合金点焊的主要焊钳供应商有加拿大Center1ine等公司。
钢铝一体化车身框架结构关键技术及最新进展

钢铝一体化车身框架结构关键技术及最新进展钟长艺;余本善【摘要】综述应用钢铝一体化车身框架结构实现车身轻量化的最新进展及关键技术难点.在传统的车身骨架钢制结构中,有些构件或组件用铝合金代替,且通过优化设计和性能模拟方法确定钢铝的比例和以铝代钢的部位,可实现车身轻量化和高强度.但铝和钢可焊接性差、存在电化学腐蚀等问题,成为结构设计的难点.同时必须保证车辆发生碰撞时,车身结构的指定部位能够吸能碰撞能量.因此关键技术涉及钢铝连接技术、电化学腐蚀、碰撞安全、新的成型工艺技术、拓扑结构优化.%The latest development and difficulties of key technology in applying steel aluminum combined structure as automobile body to realize the lightweight of the body are summarized in it.In traditional steel skeleton structure of automobile body,some components or assembly could be replaced with aluminum alloy,which ratio of steel and aluminum and the location of aluminum instead of steel could be confirmed through optimization design and performance simulation method to realize the lightweight and high strength of the body.However ,with poor weldability and electrochemical corrosion of aluminum and steel,it has been a difficulty in structural design,Meanwhile the specific part of the bodytructure should be guaranteed to be able to absorb the collision energy when collision occurs,,Ther fore the key technology involves joining technology of steel and aluminum,electrochemical corrision,collision safety as well as new forming process and optimization of topological structure.【期刊名称】《机械设计与制造》【年(卷),期】2012(000)001【总页数】3页(P251-253)【关键词】钢铝一体化;轻量化;连接技术;碰撞安全【作者】钟长艺;余本善【作者单位】华南理工大学机械与汽车工程学院,广州510640;华南理工大学机械与汽车工程学院,广州510640【正文语种】中文【中图分类】TH16;U270.21 前言着眼于长远的可持续发展,节约资源、减少环境污染成为世界汽车工业界亟待解决的两大问题[1]。
重型载重汽车车架轻量化设计研究
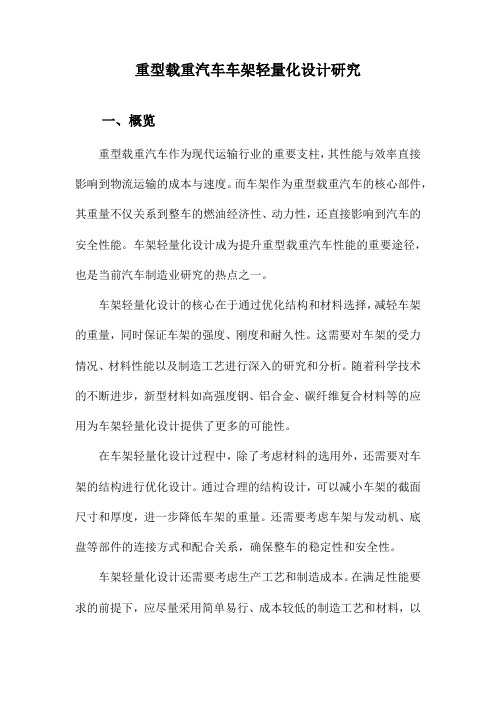
重型载重汽车车架轻量化设计研究一、概览重型载重汽车作为现代运输行业的重要支柱,其性能与效率直接影响到物流运输的成本与速度。
而车架作为重型载重汽车的核心部件,其重量不仅关系到整车的燃油经济性、动力性,还直接影响到汽车的安全性能。
车架轻量化设计成为提升重型载重汽车性能的重要途径,也是当前汽车制造业研究的热点之一。
车架轻量化设计的核心在于通过优化结构和材料选择,减轻车架的重量,同时保证车架的强度、刚度和耐久性。
这需要对车架的受力情况、材料性能以及制造工艺进行深入的研究和分析。
随着科学技术的不断进步,新型材料如高强度钢、铝合金、碳纤维复合材料等的应用为车架轻量化设计提供了更多的可能性。
在车架轻量化设计过程中,除了考虑材料的选用外,还需要对车架的结构进行优化设计。
通过合理的结构设计,可以减小车架的截面尺寸和厚度,进一步降低车架的重量。
还需要考虑车架与发动机、底盘等部件的连接方式和配合关系,确保整车的稳定性和安全性。
车架轻量化设计还需要考虑生产工艺和制造成本。
在满足性能要求的前提下,应尽量采用简单易行、成本较低的制造工艺和材料,以降低整车的生产成本,提高市场竞争力。
重型载重汽车车架轻量化设计是一个涉及材料、结构、工艺等多方面的复杂问题。
通过深入研究和分析,采用合理的设计方法和手段,可以实现车架的轻量化,提高重型载重汽车的性能和效率,为物流运输行业的发展做出贡献。
1. 重型载重汽车在社会经济中的地位与作用重型载重汽车作为道路交通的重要载体,在社会经济发展中占据着举足轻重的地位。
它们不仅是货物运输的主要工具,还是基础设施建设、物流运输、农业生产等领域不可或缺的力量。
随着全球经济一体化的加速推进,重型载重汽车的需求日益增长,对社会经济的发展起着重要的支撑作用。
重型载重汽车在货物运输中发挥着关键作用。
无论是长途运输还是短途配送,重型载重汽车都能以其强大的承载能力和稳定的性能,确保货物安全、高效地到达目的地。
在国际贸易中,重型载重汽车更是扮演着重要角色,它们穿梭于世界各地的港口、仓库和物流中心,将货物运送到各个角落,为国际贸易的繁荣做出了巨大贡献。
浅析重型商用车车架轻量化技术的发展及应用

浅析重型商用车车架轻量化技术的发展及应用东风柳州汽车有限公司 姓名:周友明 学号:P12020121 0 引言随着经济的快速发展,环境污染和能源短缺问题越来越明显,而汽车数量的增加更使这些问题日益严重。
因而,轻型、节能、环保、安全、舒适、低成本成为各汽车制造厂家追求的目标。
2009年备受世界瞩目的哥本哈根会议在全球掀起一股热烈的“哥本哈根”环保风,“低碳经济”已成为社会各界最为关注的热门词汇[1]。
近年来,得益于国家政策的扶持和国内市场的旺盛需求,我国汽车工业发展极为迅速,同时汽车也消耗了大量的不可再生能源,使一些地区出现了大面积的汽油、柴油和天然气等能源相对不足的现象,对人们的日常生活和农工业生产带来了很大的影响,对经济的发展产生了直接限制作用,所以节能减排已成为汽车工业界目前有待解决的重大问题,尤其是节能和环保更是关系到人类的可持续发展。
因此,推进汽车的节能环保显得尤为重要。
1 商用车车架轻量化的意义目前,我国商用车保有量占全部汽车保有量的23%左右,而燃油消耗占到整个汽车用油量的70%[2],其中重型商用车的耗油量又占全部商用车耗油量的70%以上。
因此,汽车节能降耗重点就是要抓重型商用车的节能降耗。
轻量化技术是提高汽车燃油经济性、减少尾气排放、节约材料消耗的有效手段。
根据国外的研究数据表明,汽车整车质量每降低100公斤,百公里油耗可降低0.3~0.6升;汽车整车质量每减重10%,油耗可降低5%~8%[3]。
国内通过试验对比分析,某典型重型商用车减轻自重的10%,可以降低油耗4.75%[4]。
另外,轻量化对环保也很有好处,车辆每减轻100公斤,CO排放量可减少约5g/km[5]。
同时,轻量化可2减少原材料消耗,降低零件成本,增加企业的收益。
因此,轻量化对于消费者、企业以及社会环境都是有益的。
对载货汽车来说,轻量化不但减轻了自身质量还提高了载质量利用系数(汽车最大承载质量与汽车整备质量之比),这是一个综合衡量轻量化的系数,也是国内外商用车设计的基本准则。
重型商用车的轻量化技术论述
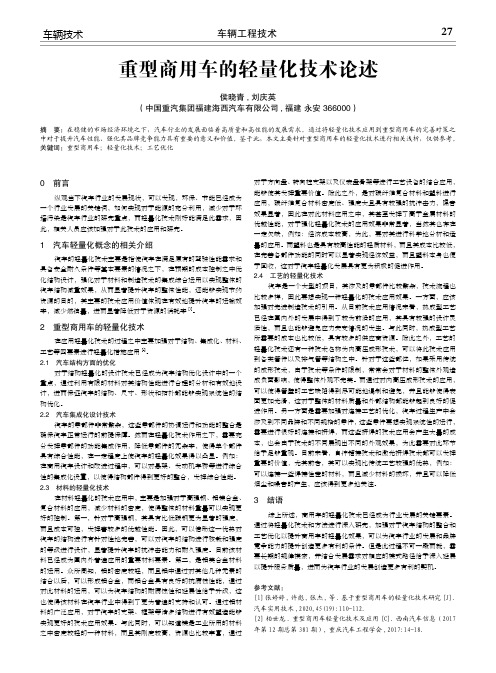
车辆工程技术27车辆技术0 前言纵观当下汽车行业的发展现状,可以发现,环保、节能已经成为一个行业发展的关键词,如何实现对于能源的充分利用,减少对于环境污染是汽车行业的研究重点,而轻量化技术刚好能满足此需求,因此,相关人员应该加强对于此技术的应用和研究。
1 汽车轻量化概念的相关介绍汽车的轻量化技术主要是指使汽车在满足原有的驾驶性能需求和具备安全耐久条件等基本要素的情况之下,在预期的成本控制之中优化结构设计,强化对于材料和制造技术的集成综合运用以实现整体的汽车结构减重效果,从而显著提升汽车的整体性能,还能够实现节约资源的目的,其主要的技术应用价值体现在有效地提升汽车的运输效率,减少燃油量,进而显著降低对于资源的消耗率[1]。
2 重型商用车的轻量化技术在应用轻量化技术的过程之中主要加强对于结构、集成化、材料、工艺等四要素进行轻量化措施应用[2]。
2.1 汽车结构方面的优化对于结构轻量化的设计技术已经成为汽车结构优化设计中的一个重点,通过利用有限的材料对其结构性能进行合理的分析和有效地设计,进而保证汽车的结构、尺寸、形状和拓扑都能够实现系统性的结构优化。
2.2 汽车集成化设计技术汽车的零部件非常繁杂,这些零部件的协调运行和功能的整合是确保汽车正常运行的前提保障。
然而在轻量化技术作用之下,需要充分发挥零部件的功能集成作用,降低零部件的冗杂率,使得单个部件具有综合性能,在一定程度上使汽车的轻量化效果得以凸显。
例如:在商用汽车设计和改进过程中,可以对悬架、发动机车桥等进行综合性的集成化设置,以使得结构部件得到更好的整合,发挥综合性能。
2.3 材料的轻量化技术在材料轻量化的技术应用中,主要是加强对于高强钢、铝镁合金、复合材料的应用,减少材料的密度,使得整体的材料重量可以实现更好的控制。
第一,针对于高强钢,其具有比低碳钢更为显著的强度,而且成本可控,发挥着较多的优越性能。
因此,可以借助这一优势对汽车的结构进行有针对性地完善,可以对汽车的结构进行核载和强度的等级进行设计,显著提升汽车的抗冲击能力和耐久强度。
铝合金在轻量化车身中的应用及连接技术
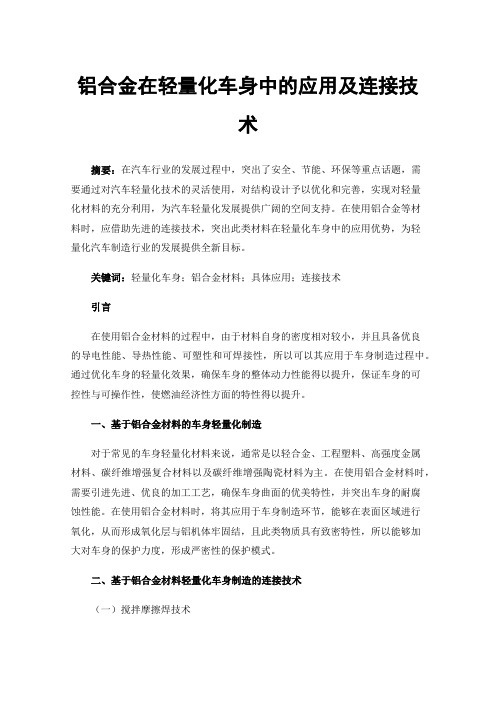
铝合金在轻量化车身中的应用及连接技术摘要:在汽车行业的发展过程中,突出了安全、节能、环保等重点话题,需要通过对汽车轻量化技术的灵活使用,对结构设计予以优化和完善,实现对轻量化材料的充分利用,为汽车轻量化发展提供广阔的空间支持。
在使用铝合金等材料时,应借助先进的连接技术,突出此类材料在轻量化车身中的应用优势,为轻量化汽车制造行业的发展提供全新目标。
关键词:轻量化车身;铝合金材料;具体应用;连接技术引言在使用铝合金材料的过程中,由于材料自身的密度相对较小,并且具备优良的导电性能、导热性能、可塑性和可焊接性,所以可以其应用于车身制造过程中。
通过优化车身的轻量化效果,确保车身的整体动力性能得以提升,保证车身的可控性与可操作性,使燃油经济性方面的特性得以提升。
一、基于铝合金材料的车身轻量化制造对于常见的车身轻量化材料来说,通常是以轻合金、工程塑料、高强度金属材料、碳纤维增强复合材料以及碳纤维增强陶瓷材料为主。
在使用铝合金材料时,需要引进先进、优良的加工工艺,确保车身曲面的优美特性,并突出车身的耐腐蚀性能。
在使用铝合金材料时,将其应用于车身制造环节,能够在表面区域进行氧化,从而形成氧化层与铝机体牢固结,且此类物质具有致密特性,所以能够加大对车身的保护力度,形成严密性的保护模式。
二、基于铝合金材料轻量化车身制造的连接技术(一)搅拌摩擦焊技术在使用搅拌摩擦焊技术的过程中,需要使用铝重金属和钢重金属,将其应用于焊接过程中,突出此类焊接方法的重要作用。
通过设置高效化的搅拌头旋转模式,使其能够与待焊工件之间进行摩擦,从而产生大量的热能,将其作为基本热源,直接应用于焊缝区域的金属处理环节,使金属能够经历热塑性变形、流动、扩散以及在结晶等基本过程,保证冶金结合的牢固性,形成完善的共享连接方法。
通过对搅拌摩擦焊方法予以细致划分,通常还能够将其分为搅拌摩擦点焊与搅拌摩擦焊等两种形式,需要结合铝合金车身轻量化工艺的实施要求,筛选出合适的搅拌摩擦焊操作方法。
基于多目标优化的钢-铝混合轻量化车架设计
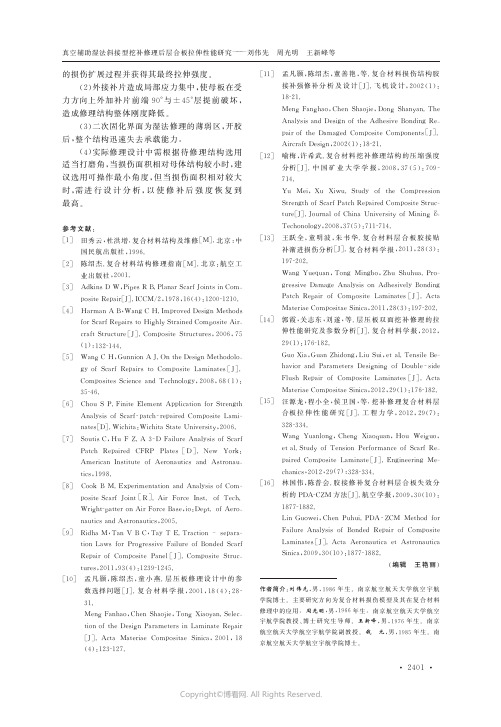
的损伤扩展过程并获得其最终拉伸强度㊂(2)外接补片造成局部应力集中,使母板在受力方向上外加补片前端90°与±45°层提前破坏,造成修理结构整体刚度降低㊂(3)二次固化界面为湿法修理的薄弱区,开胶后,整个结构迅速失去承载能力㊂(4)实际修理设计中需根据待修理结构选用适当打磨角,当损伤面积相对母体结构较小时,建议选用可操作最小角度,但当损伤面积相对较大时,需进行设计分析,以使修补后强度恢复到最高㊂参考文献:[1] 田秀云,杜洪增.复合材料结构及维修[M].北京:中国民航出版社,1996.[2] 陈绍杰.复合材料结构修理指南[M].北京:航空工业出版社,2001.[3] A d k i n sD W,P i p e sRB.P l a n a r S c a r f J o i n t s i nC o m-p o s i t eR e p a i r[J].I C C M/2,1978,16(4):1200‐1210.[4] H a r m a nAB,W a n g C H.I m p r o v e dD e s i g nM e t h o d sf o r S c a r fR e p a i r s t oH igh l y S t r ai n e dC o m p o s i t eA i r-c r a f tS t r u c t u r e[J].C o m p o s i t eS t r u c t u r e s,2006,75(1):132‐144.[5] W a n g C H,G u n n i o nAJ.O n t h eD e s i g nM e t h o d o l o-g y o fS c a r f R e p a i r st o C o m p o s i t e L a m i n a t e s[J].C o m p o s i t e sS c i e n c ea n d T e c h n o l o g y,2008,68(1):35‐46.[6] C h o uSP.F i n i t eE l e m e n tA p p l i c a t i o nf o rS t r e n g t hA n a l y s i so fS c a r f‐p a t c h‐r e p a i r e dC o m p o s i t eL a m i-n a t e s[D].W i c h i t a:W i c h i t aS t a t eU n i v e r s i t y,2006.[7] S o u t i sC,H uFZ.A3‐D F a i l u r eA n a l y s i so fS c a r fP a t c h R e p a i r e d C F R P P l a t e s[D].N e w Y o r k:A m e r i c a nI n s t i t u t e o f A e r o n a u t i c sa n d A s t r o n a u-t i c s,1998.[8] C o o kB M.E x p e r i m e n t a t i o na n d A n a l y s i so fC o m-p o s i t eS c a r fJ o i n t[R].A i r F o r c eI n s t.o f T e c h.W r i g h t‐p a t t e r o nA i rF o r c eB a s e,i o:D e p t.o fA e r o-n a u t i c s a n dA s t r o n a u t i c s,2005.[9] R i d h aM,T a nV BC,T a y T E.T r a c t i o n–s e p a r a-t i o nL a w sf o rP r o g r e s s i v eF a i l u r eo fB o n d e dS c a r fR e p a i ro f C o m p o s i t e P a n e l[J].C o m p o s i t e S t r u c-t u r e s,2011,93(4):1239‐1245.[10] 孟凡颢,陈绍杰,童小燕.层压板修理设计中的参数选择问题[J].复合材料学报,2001,18(4):28‐31.M e n g F a n h a o,C h e nS h a o j i e,T o n g X i a o y a n.S e l e c-t i o no f t h eD e s i g nP a r a m e t e r s i nL a m i n a t eR e p a i r[J].A c t a M a t e r i a e C o m p o s i t a e S i n i c a,2001,18(4):123‐127.[11] 孟凡颢,陈绍杰,董善艳,等.复合材料损伤结构胶接补强修补分析及设计[J].飞机设计,2002(1):18‐21.M e n g F a n g h a o,C h e nS h a o j i e,D o n g S h a n y a n.T h eA n a l y s i s a n dD e s i g no f t h eA d h e s i v eB o n d i n g R e-p a i r o f t h eD a m a g e d C o m p o s i t eC o m p o n e n t s[J].A i r c r a f tD e s i g n,2002(1):18‐21.[12] 喻梅,许希武.复合材料挖补修理结构的压缩强度分析[J].中国矿业大学学报,2008,37(5):709‐714.Y u M e i,X u X i w u.S t u d y o f t h e C o m p r e s s i o nS t r e n g t ho f S c a r f P a t c hR e p a i r e dC o m p o s i t e S t r u c-t u r e[J].J o u r n a l o fC h i n aU n i v e r s i t y o f M i n i n g&T e c h o n o l o g y,2008,37(5):711‐714. [13] 王跃全,童明波,朱书华.复合材料层合板胶接贴补渐进损伤分析[J].复合材料学报,2011,28(3):197‐202.W a n g Y u e q u a n,T o n g M i n g b o,Z h u S h u h u a.P r o-g r e s s i v eD a m a g e A n a l y s i so n A d h e s i v e l y B o n d i n gP a t c h R e p a i ro f C o m p o s i t e L a m i n a t e s[J].A c t aM a t e r i a eC o m p o s i t a eS i n i c a,2011,28(3):197‐202.[14] 郭霞,关志东,刘遂,等.层压板双面挖补修理的拉伸性能研究及参数分析[J].复合材料学报,2012,29(1):176‐182.G u oX i a,G u a nZ h i d o n g,L i uS u i,e t a l.T e n s i l eB e-h a v i o ra n d P a r a m e t e r s D e s i g n i n g o f D o u b l e‐s i d eF l u s h R e p a i ro f C o m p o s i t e L a m i n a t e s[J].A c t aM a t e r i a eC o m p o s i t a eS i n i c a,2012,29(1):176‐182.[15] 汪源龙,程小全,侯卫国,等.挖补修理复合材料层合板拉伸性能研究[J].工程力学,2012,29(7):328‐334.W a n g Y u a n l o n g,C h e n g X i a o q u a n,H o u W e i g u o,e t a l.S t u d y o fT e n s i o nP e rf o r m a n c eo fS c a r fR e-p a i r e dC o m p o s i t e L a m i n a t e[J].E n g i n e e r i n g M e-c h a n i c s,2012,29(7):328‐334.[16] 林国伟,陈普会.胶接修补复合材料层合板失效分析的P D A‐C Z M方法[J].航空学报,2009,30(10):1877‐1882.L i nG u o w e i,C h e n P u h u i.P D A‐Z C M M e t h o df o rF a i l u r e A n a l y s i so fB o n d e d R e p a i ro fC o m p o s i t eL a m i n a t e s[J].A c t a A e r o n a u t i c ae t A s t r o n a u t i c aS i n i c a,2009,30(10):1877‐1882.(编辑 王艳丽)作者简介:刘伟先,男,1986年生㊂南京航空航天大学航空宇航学院博士㊂主要研究方向为复合材料损伤模型及其在复合材料修理中的应用㊂周光明,男,1966年生㊂南京航空航天大学航空宇航学院教授㊁博士研究生导师㊂王新峰,男,1976年生㊂南京航空航天大学航空宇航学院副教授㊂钱 元,男,1985年生㊂南京航空航天大学航空宇航学院博士㊂㊃1042㊃真空辅助湿法斜接型挖补修理后层合板拉伸性能研究 刘伟先 周光明 王新峰等Copyright©博看网. All Rights Reserved.基于多目标优化的钢铝混合轻量化车架设计辛 勇 叶 盛南昌大学,南昌,330031摘要:以国产某S U V 车架为研究对象,建立了车架有限元模型,对车架进行弯曲刚度㊁扭转刚度分析,并进行模态分析和模态试验,验证模型的有效性㊂利用正交试验法确定了材料轻量化部件,并将这些部件的钢材料替换成铝合金,得到钢铝混合轻量化车架㊂针对钢铝混合轻量化车架刚度和模态性能的减弱问题,采用基于折中规划法的多目标形貌优化方法对部件进行优化改进,提高了车架的刚度和模态性能㊂设计结果表明,使用钢㊁铝材料结合多目标优化方法设计的钢铝混合轻量化车架相比原钢质车架在保证一定的刚度和模态性能条件下,质量减轻了6.7k g㊂关键词:车架;正交试验;钢铝混合;多目标形貌优化;轻量化中图分类号:U 463 D O I :10.3969/j.i s s n .1004-132X.2014.17.024D e s i g no f S t e e l ‐a l u m i n u m H y b r i dL i g h t w e i g h t F r a m e b y M u l t i ‐o b j e c t i v eO pt i m i z a t i o n X i nY o n g Y eS h e n gN a n c h a n g U n i v e r s i t y ,N a n c h a n g,330031A b s t r a c t :T a k i n g a nS U Vf r a m ea s r e s e a r c hs u b j e c t ,a f i n i t ee l e m e n tm o d e lw a se s t a b l i s h e d ,i t s b e n d i n g ,t o r s i o n a l s t i f f n e s s a n dm o d a lw e r e a n a l y z e d ,a n d t h em o d a l v a l u ew a s c o m pa r e dw i t h t e s t o n e t o e n s u r et h e m o d e le f f e c t i v e n e s s .O r t h o g o n a l t e s t m e t h o d w a su s e dt od e t e r m i n et h el i g h t w e i gh t c o m p o n e n t s ,a n dt h e i r s t e e lm a t e r i a l sw e r e r e p l a c e db y a l u m i n u ma l l o y ,s oas t e e l ‐a l u m i n i u m h yb r i d l i g h t w e i g h t f r a m ew a s o b t a i n e d .T h e nc o m p r o m i s e p r o g r a mm i n g m u l t i ‐o b j e c t i v em o r p h o l o g y o p t i m i -z a t i o nde s i g nm e t h o dw a s a d o p t e d t o i m p r o v e i t s s t if f n e s s a n dm o d a l p r o p e r t y .R e s u l t so f t h ed e s i gn s h o wt h a t ,u s i n g s t e e l ,a l u m i n u ma n dm u l t i ‐o b j e c t i v e o p t i m i z a t i o n ,t h e n e ws t e e l ‐a l u m i n u ml i g h t w e i gh t f r a m em a s sw i l l b e 6.7k g l i g h t e r t h a n t h e o r i g i n a l s t e e l o n ew i t h aw e l l g u a r a n t e e f o r t h e s t i f f n e s s a n d m o d a l pe rf o r m a n c e .K e y w o r d s :f r a m e ;o r t h og o n a l t e s t ;s t e e l ‐a l u m i n i u mh y b ri d ;m u l t i ‐o bj e c t i v em o r p h o l o g y o p t i m i z a -t i o n ;l i g h t w e i gh t 收稿日期:2013 04 01基金项目:国家自然科学基金资助项目(50645032);江西省科技攻关计划资助项目(C 0202400)0 引言车架不仅要承载来自各方向的力和力矩,保证有足够的刚度和强度,而且还应具有合适的固有模态频率,避免产生共振,保证良好的乘坐舒适性和足够的使用寿命[1]㊂文献[2]阐述了当整车的质量减轻10%时,可以节省燃油6%~8%㊂S U V 车架是连接车身与悬架的主要承载部件,其质量一般在150k g 左右,在整车质量中占有较大比重,因此对车架进行轻量化设计具有较大的研究空间㊂与汽车用钢铁材料相比,铝合金具有密度小㊁比强度和比刚度较高㊁弹性好㊁抗冲击性能好和再回收率㊁再生率高等一系列优良特征[3]㊂美国资深汽车工程师D a v i dS c h o l e s 曾预言,未来轿车上的每一个零件都有可能用铝合金生产[4]㊂超高强度铝合金主要是以A l ‐Z n ‐M g‐C u 系为主的合金,目前已开始广泛应用于飞机和火箭等军事领域[5]㊂由于车架结构及载荷的复杂性,研究者将轻量化优化设计与有限元分析和材料属性研究相结合,能够获得很好的效果[6]㊂目前对汽车车架的轻量化设计主要都是倾向于结构优化改进,很少注重新型轻量化材料的使用,因此,从新型轻量化材料入手并结合拓扑形貌结构优化设计对车架进行轻量化研究具有一定的探索意义㊂本研究以某国产S U V 车架为研究对象,对其进行刚度和模态仿真分析,使用铝合金材料,结合正交试验法确定材料轻量化目标;同时针对车架性能降低的问题,建立折中规划的多目标形貌优化数学模型进行优化设计,得到满足刚度和模态性能的钢铝混合轻量化车架模型㊂1 车架刚度及模态有限元分析1.1 车架有限元模型建立为确保计算精度高㊁计算时间短,选取10mm×10mm 的单元来离散车架所有部件㊂最终得到的车架网格模型中含有四边形单元64027个,三角形单元2004个㊂车架各零件之间的连接方式为点焊㊁缝焊和螺栓连接㊂本研究不考虑焊接或者螺栓失效的问题,故为了缩短分析㊃2042㊃中国机械工程第25卷第17期2014年9月上半月Copyright ©博看网. All Rights Reserved.时间,将所有的连接均采用刚性单元来模拟㊂车架的材料为高强度钢Q345,其弹性模量为210G P a,泊松比为0.3,密度为7.85×103k g/m3,车架总质量为143.0k g㊂建立的整个车架有限元模型如图1所示,图中数字标号1㊁2㊁3㊁4㊁5㊁6分别代表第1到第6横梁㊂图1 车架有限元模型1.2 车架弯曲刚度和扭转刚度分析弯曲工况边界条件为:约束车架后部螺旋簧支架支撑点X㊁Y㊁Z三个方向的平动自由度,约束前轮轴线对应的车架纵梁位置Y Z方向的平动自由度,在车架中间位置的左右纵梁上各施加1000N的垂直于Z轴的力,如图2所示㊂提取车架左右纵梁中间受力位置的Z向位移来评价车架弯曲刚度大小,Z向位移大小均为-1.50mm㊂计算得出车架的弯曲刚度K=1333N/mm,满足同类汽车车架弯曲刚度最低目标值为1200N/mm的要求[7]㊂图2 车架弯曲刚度扭转工况边界条件为:约束车架后部螺旋簧支架支撑点X㊁Y㊁Z三个方向的平动自由度,在前轴位置中点(通过建立R i g i d刚性单元与车架上前悬对应的位置连接)处约束Z方向的平动自由度,在前轮轴线对应的车架纵梁位置分别施加沿Z方向的一对反力,力的大小为1000N,如图3所示㊂采用左右纵梁前部受力位置的Z方向位移评价扭转刚度,左右纵梁Z向最大位移分别为4.62mm和-4.62mm,两受力点间距离为图3 车架扭转刚度710mm,计算得出车架的扭转角:φ=(π/180)a r c t a n((4.62+4.62)/710)=0.013(r a d)车架的扭转刚度:G J=M T/φ=(1000×0.71)/0.013=54615(N㊃m/r a d)满足同类汽车车架扭转刚度最低目标值为5×104N㊃m/r a d的要求[7]㊂1.3 车架模态分析及有限元模型验证车架的模态性能直接关系到车辆的安全性㊁舒适性和可靠性[8]㊂本文先对车架模型进行了自由模态分析,为了验证模型的可靠性,对车架整体结构进行了模态试验[9]㊂模态试验主要采用的仪器或设备有:S U V车架㊁L M S T e s t.L a b测试系统软件㊁L M SS C A D A SⅢ多通道数据采集前端㊁加速度传感器㊁力传感器㊁激振器和功率放大器等㊂用橡皮绳将车架自由地悬挂在空中来模拟车架 自由自由”的边界条件㊂根据车架几何模型自由模态振型分析结果选择车架测试点位置,为体现车架整体结构,最终在车架上确定了56个测试点,车架某段测试点分布如图4所示㊂对采集的数据进行集中处理并计算模态振型,其试验原理如图5所示㊂由于低阶模态频率和相应振型对结构的动态特性影响最大,因此这里只列出了车架前5阶模态频率㊂模态频率仿真结果与试验结果及振型对比见表1㊂由表1可以看出,计算得到的模态频率和试验值误差不大,说明本研究所建立的车架有限元模型及分析方法是可靠的㊂图4车架某段测试点分布图图5 车架模态试验原理㊃3042㊃基于多目标优化的钢铝混合轻量化车架设计 辛 勇 叶 盛Copyright©博看网. All Rights Reserved.表1 车架模态频率及振型阶数12345计算模态频率(H z)23.7127.1445.1248.6659.66试验模态频率(H z )24.8728.8646.5350.0461.84振型一阶扭转一阶弯曲弯扭组合一阶横摆弯扭横摆组合误差(%)4.665.963.032.763.532 钢铝混合车架设计本研究选用A l ‐Z n ‐M g‐C u 系(7系列)超高强度铝合金置换车架某些横梁和纵梁部件的钢材料,并采用正交试验法来确定置换部件,置换部件的弹性模量为71G P a ,泊松比为0.33,密度为2.81×103k g/m 3㊂建立正交试验表,选择车架的1~11号部件为参考因素,具体做法是:改变这些部件材料的弹性模量㊁泊松比和密度等参数,形成12组试验方案,进行软件模拟仿真试验,考核各参考部件对车架的弯曲㊁扭转刚度和一阶模态3个指标的影响㊂考虑到车架的对称性,内外各板相对称的部位统一标号,内外板标号分别见图6㊁图7所示㊂图6 车架内板标号图7 车架外板标号在此优化事件中,优化对象为图1㊁图6和图7中标号的11个部件,变量为部件的材料,11个部件构成样本空间,每个部件为影响事件的一个因素,每个因素设定钢和铝合金两个材料水平,这就构成了一个11因素2水平的优化问题㊂采用正交试验法进行仿真,构建正交试验表L 12(211)如表2所示㊂1~11代表影响刚度和模态性能的11个因素,L ㊁H 代表两种材料水平,L 代表铝合金,H 代表钢,s d 表示弯曲工况最大位移,s r 表示扭转工况最大位移,f1表示一阶模态频率,进行12次试验仿真计算㊂表2 L 12(211)正交试验表试验因素性能指标1234567891011s d (mm )s r (mm )f 1(H z )综合性能1L L L L L L L L LLL4.2411.3619.0534.652L L LLLHH H HH H 1.525.1923.29303L LH HHLLLHH H1.706.8621.1829.744L H L HHLHHLL H2.888.0620.5031.445L H H LHH L HLH L2.317.7321.0031.046LHH H L H H L HL L 3.839.1019.9432.877H L H H LL HHLHL2.276.5322.6731.478H L HL HHHLLL H 3.608.5819.5131.699HLL HHHLHHL L 3.379.7319.8232.9210H H HL LL LHHLH3.158.4020.1631.7111H H L HLHLL LHH1.737.5319.9929.2512HHLLHLHLHHL 2.066.6522.1630.87对各因素的显著性水平进行检验,方差分析见表3㊂由显著性水平可知,因素1㊁2㊁4㊁5㊁6对试验的结果影响不显著,故可得车架的1㊁2㊁4㊁5㊁6号部件材料的更换对车架总体性能的影响不大,因此,这里选择1㊁2㊁4㊁5㊁6号部件为材料替换对象㊂对钢铝混合车架弯曲㊁扭转工况和模态进行分析得出,s d 为1.52mm ,s r 为5.19mm ,f1为23.48H z㊂对比原车架与钢铝混合车架的刚度和模态性能可知,钢铝混合车架的弯曲㊁扭转刚度和一阶模态相比原车架均有所下降㊂为使得到的结构和尺寸更加合理,刚度与模态性能均不低于原车架的刚度与模态性能,笔者建立多目标优化数学模型对钢铝混合车架的以上11个主要部件进行形貌优化设计㊂3 钢铝混合车架的多目标形貌优化一般来说,不同的载荷工况将得到不同的结构拓扑㊂传统的多目标优化问题采用线性加权法将多目标问题转化为单目标问题进行求解,但对于非凸优化问题来说,该方法不能确保得到所有的P a r e t o 最优解[10]㊂现今研究多目标拓扑优化㊃4042㊃中国机械工程第25卷第17期2014年9月上半月Copyright ©博看网. All Rights Reserved.表3 方差分析表变异来源偏差平方和自由度均方F值Fα显著水平10.2810.281.27 20.80210.8023.6532.3212.3210.55 40.4310.431.95 50.42210.4221.92 60.3710.371.68 71.2811.285.82 81.2211.225.55 91.3711.376.23 1010.89110.8949.5 115.31715.31724.17F0.05(1,25)= 4.24F0.01(1,25)= 7.77*********误差e10.211重复误差e20.0124总误差e0.2225总变异24.92136问题一般采用折中规划法㊂形貌优化是一种形状最佳化方法,即在板形结构中寻找最优的加强筋分布的概念方法㊂利用折中规划法可以将车架多工况下的弯曲刚度和扭转刚度及低阶固有频率的多目标优化问题转化为单目标优化问题[11‐12]㊂本研究利用折中规划法结合平均频率法得到多目标优化的综合目标函数,该方法可以有效地求解出多目标函数的最优解,从而为多目标优化提供解决方案㊂在本研究中,对钢铝混合车架进行了柔度最小化㊁固有频率最大化以及多目标的形貌优化,其结果显示多目标形貌优化方法能够较大地提高车架的刚度和模态性能㊂3.1 弯曲和扭转工况刚度优化目标函数对于刚度提高问题,通常把刚度最大问题等效为柔度最小问题来研究,柔度则用应变能来定义[13]㊂于是由折中规划法结合平均频率法可得到多刚度优化的目标函数:m i nρC(ρ)=[∑m k=1w q k(C k(ρ)-C m i n kC m a x k-C m i n k)q]1q(1)式中,m为载荷工况数量;w k为第k个工况的权值;q为惩罚因子,q≥2,本研究中取值为2;C k(ρ)为第k个工况的柔度目标函数;C m a x k㊁C m i n k分别为第k个工况柔度目标函数的最大值与最小值㊂3.2 固有模态频率优化目标函数通过最大化结构的动态响应,使结构的基频高于结构可能的共振频率,减小由结构不合理导致的噪声,对提高乘员舒适性有重要意义,所以对振动频率的优化设计十分必要㊂在优化过程中经常会遇到如此情况:当其中一个阶次的频率达到最大时,其他阶次的频率可能降到一个较低的值,而且几阶频率之间可能会相互调换次序,这样就会出现目标函数振荡问题㊂为避免出现几阶频率目标函数振荡的现象,本研究用平均频率公式来定义固有频率优化的目标函数,如下式所示:m i nx={x1,x2, ,x n}Λ(ρ)=λ0+s(∑f i=1w iλi-λ0)-1(2)式中,Λ(ρ)为平均频率;λi为第i阶特征频率;λ0㊁s为给定的参数,用来调节目标函数;w i为第i阶频率的权重系数; f为优化的低阶频率的阶次㊂3.3 考虑刚度与频率要求的多目标优化函数结构多目标优化是同时考虑多刚度目标和振动频率目标的优化㊂由折中规划法结合平均频率法可得到多目标优化的综合优化函数,如下式所示:m i n F(ρ)=[w2(∑m k=1w k C k(ρ)-C m i n kC m a x k-C m i n k)2+(1-w)2(Λm a x-Λ(ρ)Λm a x-Λm i n)2]12(3)式中,F(ρ)为综合目标函数;w为柔度目标函数的权重;Λm a x㊁Λm i n分别为频率目标函数的最大值和最小值㊂当车架位于其中一个工况时:k=1,w k=1; C1(ρ)为柔度,是设置的变量;C m a x1为形貌优化前钢铝复合车架的柔度,其值最大,弯曲工况时其值为1450N㊃mm,扭转工况时其值为3196N㊃mm;C m i n1为形貌优化后钢铝混合车架的柔度,其值最小,弯曲工况时其值为1185N㊃mm,扭转工况时其值为2568N㊃mm;Λ(ρ)为一阶固有频率,是设置的变量;Λm a x为优化后模型的一阶固有频率,是经过优化得到的最大频率值,为26.04H z;Λm i n为优化前模型的一阶固有频率,该频率值最小,为23.48H z;w为加权值,在0~1之间㊂3.4 钢铝混合车架的多目标折中规划形貌优化设计多目标形貌优化与多目标拓扑优化方法类似,不同的是拓扑优化用单元密度变量,而形貌优化用形状变量㊂利用O p t i S t r u c t中提供的自定义函数来定义上文所提到的折中规划公式和平均频率公式,把定义好的函数设为响应,把响应作为目标函数进行优化㊂本研究中视弯曲和扭转工况同等重要,即取两工况的权值相等;同样在模态频率形貌优化中也将各阶频率的权值取为相等,取车架前5阶频率;在多目标形貌优化的综合目标函数中,取柔度权值w=0.4,频率权值为0.6[14‐15],其中弯曲和扭转工况柔度权值各为0.2,前5阶频率每阶权值各为0.12㊂经过分析计算,函数经过7次迭代达到收敛,优化过程结束㊂车架的弯曲柔度㊁扭转柔度㊁一阶模态频率以及总质量的收敛过程如图8~图11所示㊂优化前后得到的钢铝混合车架与原型钢质车㊃5042㊃基于多目标优化的钢铝混合轻量化车架设计 辛 勇 叶 盛Copyright©博看网. All Rights Reserved.架的质量及性能对比见表4㊂为了对比形貌优化后的钢铝混合车架与原型钢质车架结构上的区别,在此给出了1号㊁4号㊁10号及11号部件优化前后的部分结构变化图,见图12~图15㊂图8 弯曲柔度迭代曲线图9 扭转柔度迭代曲线图10 一阶模态频率迭代曲线图11 车架总质量迭代曲线表4 优化前后车架性能对比指标车架质量(k g )弯曲柔度(N ㊃mm )扭转柔度(N ㊃mm )一阶频率(H z)原型钢质车架143.01434296823.71优化前钢铝混合车架131.81450319623.48优化后钢铝混合车架136.31204258825.94图12 1号部件优化前后结构对比图13 4号部件优化前后结构对比图14 10号部件优化前后结构对比图15 11号部件优化前后结构对比由图8~图11可知,使用折中规划的多目标形貌优化法对钢铝混合车架进行优化设计,达到了提高车架性能的目的㊂表4表明,优化后的钢铝混合车架与优化前对比,虽然质量稍有增大,但是弯曲㊁扭转柔度下降明显,分别下降了246N ㊃mm 和608N ㊃mm ,且一阶频率提高了2.46H z,车架的刚度和模态性能得到明显提高;与原型钢质车架对比,总质量减轻了6.7k g,一阶频率提高了2.23H z ,弯曲和扭转刚度也均有明显提高㊂由图12~图15可知,形貌优化使得车架结构某些区域增加了加强筋,达到改变其结构提高其性能的目的㊂经过对比分析可知,优化后的钢铝混合轻量化车架结构满足同类汽车车架的设计目标值㊂激光对接焊热量集中㊁热源能准确控制㊁应力应变小㊁焊接接头强度高㊁耐腐蚀性好,与其他焊接方法相比,更适合钢㊁铝异种材料的焊接[16],因此,此车架中钢㊁铝不同材料间的连接在满足一定的强度下可考虑采用激光对接焊㊂文献[17]指出,喷射成形具有传统铸造㊁粉末冶金所不具备的优越特性,是目前工业化制备屈服强度800M P a 以上超高强度铝合金很好的途径,国内外对A l ‐Z n ‐M g‐C u 系铝合金坯料制备及变形加工的研究方法主要为O s p r e y 喷射成形工艺和挤压加工,故本研究选用的A l ‐Z n ‐M g ‐C u 系超高强度铝合金部件可采用喷射成形结合挤压加工工艺加工得到㊂4 结语采用正交试验法以及显著性水平分析可以简单快速地确定材料轻量化对象,经过材料轻量化(铝合金材料替换钢材料)后,车架质量减重显著㊂使用折中规划的多目标形貌优化法,对钢铝混合轻量化车架进行加强筋结构与布局设计,最终得到的优化车架模型与原型钢质车架相比,质量减小了6.7k g ,一阶频率提高了2.23H z ,且弯曲㊁扭转刚度均得到较大的提高㊂此研究达到了保证车架刚度和模态性能的同时,减轻车架质量的目的㊂㊃6042㊃中国机械工程第25卷第17期2014年9月上半月Copyright ©博看网. All Rights Reserved.。
钢铝混合材料车身结构轻量化设计关键问题与应用研究龙宪阁

钢铝混合材料车身结构轻量化设计关键问题与应用研究龙宪阁发布时间:2021-09-10T06:24:38.911Z 来源:《中国科技人才》2021年第17期作者:龙宪阁[导读] 对车身结构进行轻量化整改对于车辆行业的发展来说是非常重要的,能够使汽车燃油更加经济实惠,而且还有助于减少有害物质的排放。
宁波吉利汽车研究开发有限公司辽宁大连 116000摘要:对车身结构进行轻量化整改对于车辆行业的发展来说是非常重要的,能够使汽车燃油更加经济实惠,而且还有助于减少有害物质的排放。
和以往单一钢制材料相比,钢铝混合材料可以更好的满足多方面的需求,使车身轻量化在工艺、安全性以及成本等多方面都得到优化。
文章通过简述汽车车身轻量化的含义,进而分析轻量化材料类别,最后讨论材料的发展历程。
关键词:钢铝混合材料;汽车车身;轻量化在当前这个经济社会迅速发展的新时期,汽车逐渐成为人们生活中不可或缺的代步工具,大家对于汽车各方面性能的要求也越来越高,关注的重点慢慢集中到车辆辅助设备中。
利用钢铝混合材料进行车身结构设计就是以以往的钢结构车身骨架为基础,把其中的一部分构件利用强度更大的钢铝材料进行替换,这样能够使钢板在实用性与经济性方面的优势充分体现出来。
1 车身结构轻量化的含义轻量化,顾名思义就是指在符合碰撞条件并确保车辆的各项性能不会发生变化的基础之下尽可能使汽车各个部件的重量减小,使质量、特性以及成本三个方面达到最佳平衡。
目前,对车身结构进行轻量化整改的方法有三类:第一是对车辆的结构进行轻量化改造,对内部的零件进行薄壁化、中空化等优化;第二是利用现代化轻质材料,类似于镁、铝等金属、塑料或是截面厚度比较小但强度大的钢材;第三是利用现代化生产工艺,类似于液压成型、激光拼焊等等。
根据当前一些调查信息可以了解到,一直到2012年的年底,我国具有的机动车数目达到了2.38亿。
这是我国具有的汽车数目第一次高于1亿,在世界上占据第二的位置。
车身材料的轻量化与强度提升

车身材料的轻量化与强度提升随着汽车工业的不断发展,在保证车辆安全性的前提下,车身材料的轻量化和强度提升成为了一个重要的课题。
车身材料的选择和设计对车辆的性能、燃油经济性和环保性都有着直接的影响。
本文将探讨车身材料的轻量化与强度提升的方法和技术。
一、先进材料在车身结构中的应用1. 高强度钢材的应用高强度钢材具有较高的屈服强度和抗拉强度,可以提升车身结构的强度和刚性,减轻车身自重。
通过选用高强度钢材,可以在保持车辆安全性的同时,实现车身重量的降低。
2. 铝合金的应用铝合金具有较低的密度和较高的强度,是一种理想的轻量化材料。
在现代汽车制造中,铝合金广泛应用于车身部件、车顶、车门等重要部位,显著降低了车身重量,提高了燃油经济性。
3. 碳纤维复合材料的应用碳纤维复合材料具有极高的强度和刚性,同时具备较低的密度和良好的抗腐蚀性能。
在超跑和高性能车辆中,碳纤维复合材料广泛应用于车身结构和车身板材,能够显著降低车辆自重,提升车辆性能。
二、材料优化设计与工艺改进1. 材料优化设计通过材料的优化设计,可以实现材料的轻量化与强度提升。
比如通过调整合金配比来提高钢材的强度,或者通过控制碳纤维复合材料的纤维方向来提高其刚性。
材料的优化设计需要结合材料性能和实际使用要求进行综合考虑。
2. 工艺改进合理的工艺改进可以进一步加强车身结构的强度和刚性。
例如,采用先进的焊接工艺可以提高焊接接头的强度和密封性,碳纤维复合材料的层压工艺可以提高材料的强度和疲劳寿命。
三、智能化车身结构设计智能化车身结构设计是近年来的一个研究热点。
通过引入传感技术和控制系统,可以实现车身结构的智能调节和优化。
比如在车辆发生碰撞时,通过传感器感知碰撞力度并相应地调整车身结构,实现对碰撞能量的吸收和分散,从而提高车辆的安全性。
总结:车身材料的轻量化与强度提升是汽车工业发展的趋势,也是减少排放、提高燃油经济性的重要手段。
通过应用先进材料、优化材料设计与工艺改进,以及智能化车身结构设计,可以实现车身轻量化和强度提升的目标,为汽车工业的发展做出贡献。
铝合金汽车轻量化技术

铝合金汽车轻量化技术概述随着环保意识的增强和汽车行业的发展,轻量化成为汽车制造业的重要趋势。
铝合金作为一种轻质、高强度的材料,被广泛应用于汽车制造中,以实现汽车的轻量化。
本文将介绍铝合金汽车轻量化技术的应用、优势和最新发展。
铝合金在汽车制造中的应用铝合金在汽车制造中的应用主要集中在车身和发动机部件上。
车身部件铝合金在车身部件中的应用可以有效地降低车身重量,提高燃油效率和减少尾气排放。
常见的铝合金车身部件包括车门、车顶、引擎盖、车身框架等。
发动机部件铝合金在发动机部件中的应用可以减轻整个发动机系统的重量,提高燃烧效率和散热性能。
铝合金在发动机缸体、缸盖、曲轴箱等部件中的应用已成为现代发动机的主流。
铝合金汽车轻量化的优势铝合金汽车轻量化具有以下优势:轻质高强与传统的钢铁材料相比,铝合金的密度较低,同时具有较高的强度和刚度。
因此,使用铝合金可以在保证结构强度的同时,降低整车的重量,提高燃油经济性。
耐腐蚀铝合金具有良好的抗腐蚀性能,可避免车身和发动机部件由于腐蚀而导致的功能损失和安全隐患。
可塑性铝合金具有良好的可塑性,可以通过模压和挤压等加工工艺实现复杂车身组件的生产。
这有助于降低制造成本,并提高生产效率。
可回收性铝合金可以100%回收再利用,有助于减少资源消耗和环境污染。
铝合金汽车轻量化技术的最新发展为了进一步推动铝合金汽车轻量化,科学家和工程师们在铝合金材料和生产工艺方面不断进行研究和创新。
新型铝合金材料研究人员正在开发新型铝合金材料,以提高其强度和成本效益。
新型材料的研发包括优化合金成分、微观结构设计以及表面处理等方面。
先进的生产工艺为了更好地利用铝合金材料的优势,研究人员正在开发和改进铝合金零件的生产工艺。
这包括改良的铝合金模压工艺、挤压工艺和焊接工艺等。
多材料混合为了在不同部位采用最合适的材料,一些汽车制造商正在开发多材料混合的解决方案。
通过在关键部位使用铝合金,而在其他部位使用其他材料,可以在保证结构强度的同时,进一步降低整车的重量。
基于多目标优化的钢铝混合轻量化车架设计
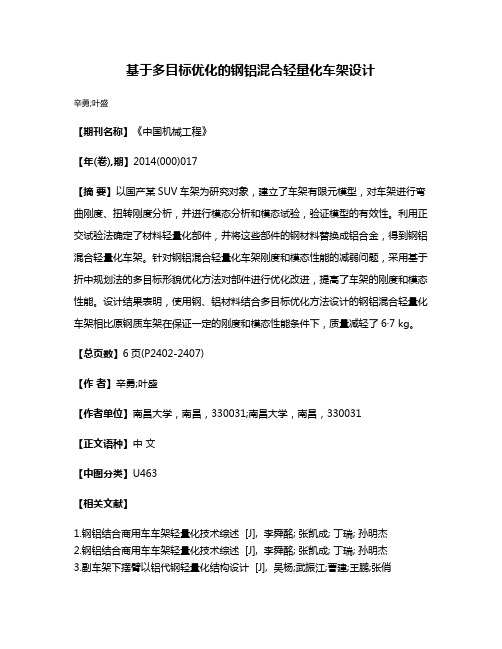
基于多目标优化的钢铝混合轻量化车架设计
辛勇;叶盛
【期刊名称】《中国机械工程》
【年(卷),期】2014(000)017
【摘要】以国产某SUV车架为研究对象,建立了车架有限元模型,对车架进行弯曲刚度、扭转刚度分析,并进行模态分析和模态试验,验证模型的有效性。
利用正交试验法确定了材料轻量化部件,并将这些部件的钢材料替换成铝合金,得到钢铝混合轻量化车架。
针对钢铝混合轻量化车架刚度和模态性能的减弱问题,采用基于折中规划法的多目标形貌优化方法对部件进行优化改进,提高了车架的刚度和模态性能。
设计结果表明,使用钢、铝材料结合多目标优化方法设计的钢铝混合轻量化车架相比原钢质车架在保证一定的刚度和模态性能条件下,质量减轻了6·7 kg。
【总页数】6页(P2402-2407)
【作者】辛勇;叶盛
【作者单位】南昌大学,南昌,330031;南昌大学,南昌,330031
【正文语种】中文
【中图分类】U463
【相关文献】
1.钢铝结合商用车车架轻量化技术综述 [J], 李舜酩; 张凯成; 丁瑞; 孙明杰
2.钢铝结合商用车车架轻量化技术综述 [J], 李舜酩; 张凯成; 丁瑞; 孙明杰
3.副车架下摆臂以铝代钢轻量化结构设计 [J], 吴杨;武振江;曹建;王鹏;张俏
4.钢铝结合商用车车架轻量化技术综述 [J], 谢成才
5.钢铝混合白车身在汽车轻量化中的应用及乘用车轻量化实例 [J], 王浩;陈鹏;钟万泽
因版权原因,仅展示原文概要,查看原文内容请购买。
钢-铝混合驾驶室材料-结构轻量化设计

钢-铝混合驾驶室材料-结构轻量化设计
王超;李明;成艾国;何智成;于万元
【期刊名称】《汽车工程》
【年(卷),期】2024(46)4
【摘要】为了得到更为完善的商用车驾驶室轻量化设计,提出了钢-铝混合驾驶室材料-结构一体化轻量化方法。
首先基于灵敏度分析、等刚度近似理论与等强度理论
建立了性能驱动的材料选择方法,并针对钢制驾驶室初步设计了钢-铝混合材料方案。
然后通过折衷规划法的拓扑优化识别了驾驶室关键传力路径,并加强了相关结构。
其次考虑驾驶室零件厚度、截面尺寸设计参数,建立了驾驶室质量、刚度及模态性
能的径向基函数的代理模型,并采用多目标粒子群优化方法对驾驶室进行多目标优
化设计。
优化结果表明,在满足驾驶室刚度、模态和碰撞性能的要求下,驾驶室质量
减轻了12.8%。
该方法对钢-铝混合驾驶室轻量化有实际的工程指导价值。
【总页数】11页(P735-744)
【作者】王超;李明;成艾国;何智成;于万元
【作者单位】湖南大学;广西科技大学机械与汽车工程学院;柳州职业技术学院
【正文语种】中文
【中图分类】U46
【相关文献】
1.全铝及钢-铝混合车身轻量化连接技术
2.基于多目标优化的钢铝混合轻量化车架设计
3.论全铝及钢-铝混合车身轻量化连接技术
4.全铝与钢-铝混合车身轻量化的连接技术探讨
5.全铝及钢-铝混合车身轻量化连接技术
因版权原因,仅展示原文概要,查看原文内容请购买。
- 1、下载文档前请自行甄别文档内容的完整性,平台不提供额外的编辑、内容补充、找答案等附加服务。
- 2、"仅部分预览"的文档,不可在线预览部分如存在完整性等问题,可反馈申请退款(可完整预览的文档不适用该条件!)。
- 3、如文档侵犯您的权益,请联系客服反馈,我们会尽快为您处理(人工客服工作时间:9:00-18:30)。
钢铝结合商用车车架轻量化技术综述李舜酩; 张凯成; 丁瑞; 孙明杰【期刊名称】《《重庆理工大学学报(自然科学版)》》【年(卷),期】2019(033)010【总页数】8页(P1-8)【关键词】轻量化; 钢铝结合车架; 结构优化设计; 连接工艺【作者】李舜酩; 张凯成; 丁瑞; 孙明杰【作者单位】南京航空航天大学能源与动力学院南京210016【正文语种】中文【中图分类】U463.32目前,商用车保有量占汽车总量的10%左右,但总体燃料消耗量占汽车燃料总消耗量的55%~60%,百公里排放量约为乘用车排放量的3~4倍[1]。
而轻量化技术作为提高汽车燃油经济性和减少尾气排放的有效手段,对商用车来说,在减轻了自身质量的同时,还提高了载质量利用系数[2]。
一般重型商用车整备质量为8~18 t,车架质量为500~1 200 kg,车架占商用车整备质量的5%~10%[3],因此车架轻量化对整车轻量化的贡献非常可观。
车架承受着整车的簧载质量,同时还要受到来自不平度路面、行驶速度和方向改变而产生的外部激励,以及动力传动系统等产生的内部激励,所以车架要求足够的刚度、强度和可靠性。
目前车架轻量化主要依靠3个方面进行[4]:① 结构优化设计,包括尺寸优化、形貌优化和拓扑优化等,并结合多学科手段使得优化结果满足所有学科的要求,目前车架优化考虑的性能主要有刚度、强度和模态,而大多数研究在优化过程中未将疲劳考虑在内;② 轻量化材料的应用,包括高强度钢和铝合金等,目前钢铝结合和全铝在车身上的应用较为常见,而在车架上的使用相对较少;③ 先进制造工艺,包括热冲压成形和激光焊等。
生产超高强度钢和超强度铝需要更高要求的制造工艺,而且保证钢铝材料能够在车上正常使用,需要设计相应的钢铝异种材料的连接工艺。
因此,基于传统的车架钢制结构,采用铝合金材料制作部分零件,根据性能模拟、优化设计等方式,综合考虑刚度、强度、模态和疲劳性能,对铝替代钢的零件加以确定,并配合相应的连接工艺是今后实现商用车架轻量化的一个重要方向。
1 钢铝材料在车架上的国内外应用现状因商用车车架需要安装各大总成及承受所产生的载荷,所以目前商用车车架纵梁及横梁等多采用钢板冲压加工成槽型结构。
随着车架的发展,车架的强度级别提高到510、590、610、700 MPa和750 MPa等,以适应不同用途的需求。
2000年以前,国内各商用车整车厂在车架上采用的主要是以如Q345和16MnL等普通强度等级的钢材。
在2000年以后,国内整车厂开始研发使用高强度钢板。
东风商用车在2004年开始研发使用抗拉强度为590 MPa级的热轧高强度钢板,其在2007年批量用于车架纵梁的生产[5]。
同年,开始了抗拉强度为700 MPa级热轧高强度钢板纵梁的试制工作。
2012年设计推出的第一款量产的轻量化牵引车车架上采用了750 L高强度钢板,由原来的双层车架优化为单层,局部通过增加加强板以满足强度要求,减重幅度显著[6]。
近年来,北京福田戴姆勒汽车有限公司成功试制了屈服强度为620~700 MPa级别的汽车用大梁钢的车架纵梁,试制产品满足工艺及质量要求,并完成道路可靠性试验,使整车轻量化和安全性合理的匹配与平衡,达到了轻量化的目的[7]。
目前,国内重型卡车车架纵梁截面多为U字型直梁与变截面弯梁,材料多选用低合金高强度热轧中厚度钢板,厚度4~10 mm,材料牌号多为510~690 L,通过冲孔、压型、切割、合梁及钻孔等工序加工为成品纵梁。
少部分车型采用了700~800 MPa级别的大梁钢板,甚至热处理车架。
欧美发达国家的重卡车系中,如奔驰、沃尔沃、斯堪尼亚、曼恩等系列车系,其车架用钢强度普遍已达到700~800 MPa级别水平[8],部分公司还采用了1 200 MPa级别以上的热处理车架,甚至铝合金车架,车架重量明显低于国内同类产品。
全钢制车架不符合轻量化,而全铝合金车架成本又太高且强度不足,钢铝结合车架利用铝合金替代部分钢制零件,在保证强度的同时,既节省成本,又达到了轻量化的目的。
在发达国家,商用车的铝化率已经超过80%,而中国商用车的铝化率除个别车种如冷藏车外,其他的均很低,发展空间较大[9]。
北美地区车型轻量化设计进行得较早,铸造铝合金研究处于领先水平,铸造工艺先进,也是最早将铸铝合金应用在重型货车底盘的连接及承载零部件上的地区。
目前使用铸造铝合金的零件包括横梁及大部分底盘支架,主要采用普通铸造及加压铸造工艺[10]。
但近几年随着新型的超高强度的铝合金的出现,汽车制造商有了一个真正的替代方案,超高强度铝合金关键优点是突出的密度-强度比,这允许其与超高强度钢相同的机械性能并显著地节省重量[11]。
在未来的十几年中,肯联铝业等铝制造商将继续投资于研究和开发,以推动超高强度的铝合金发展,为汽车制造商提供额外的选择,使车辆在不牺牲安全性的前提下,质量更轻。
国内新修订的GB1589于2016年7月正式发布,其对商用车的轴荷及质量限值均进行了压缩。
如果总质量下降而整备质量不变,会导致载质量降低,因此,商用车轻量化的需求因政策而加大。
考虑到国内路况和超载问题,目前车架的纵梁和横梁仍采用钢制,但其他附件,如油箱和轮毂正逐渐由钢向铝合金过渡。
扬州中集通华专用车有限公司于2016年2月推出了一款钢铝混合的45英尺的鹅颈骨架车,主体车架采用高强度钢板,附件一律采用5系和6系铝合金材质。
就目前发展趋势,材料是商用车轻量化的重要途径之一,先进高强钢、铝合金、镁合金、非金属复合材料等用在国产商用车上已经屡见不鲜,促进了商用车的轻量化,但是我国目前商用车先进材料的应用比例和应用的成熟度相较国外先进水平还是比较低的。
国内特别是车架仍是以510~590 MPa级大梁钢板为主,铝合金在车架上的总体应用率较低。
2 钢铝结合车架所面临的关键问题钢铝结合车架结构的理念虽然已经引起国内外汽车企业的高度重视,并在实际的车架制造中有了一定的体现,但是这种车架结构的开发方法与传统的单一材料车架结构相比有很大的不同,仍然面临着一些关键问题亟待解决。
首先,钢和铝的物理特性有较大的区别,2种材料的熔点与热膨胀系数相差较大,焊接过程中难以形成熔核,且易形成脆性的金属间化合物,难以保证接头强度,受热后引起内应力难以消除[12]。
另外,铝和钢的电位相差较大,易于发生电化学反应,故钢铝材料结合车架很难通过传统的电阻点焊进行连接,如何克服铝和钢物理化学性质的巨大差异是连接技术的一大难点。
其次,车架轻量化的前提是基于强度和刚度条件进行的,对于铝合金来说,7075铝合金在T6温度下达到约500 MPa的屈服点,在T7温度下的屈服点约为450 MPa。
450~500 MPa的屈服点已经非常高,然而如果考虑相同的产品厚度,超高强度钢仍然具有1 100 MPa的屈服强度,强度明显更高。
铝合金在强度和刚度方面明显低于钢板。
再次,钢铝结合车架结构的核心是将合适的材料应用于合适的部位,以充分发挥钢和铝在强度、刚度、轻量化方面各自的优势,最大程度上实现车架的轻量化和重要性能的最优。
然而,如何为每一个零部件确定其适合的材料,即如何科学地进行材料选择,从众多的可选材料组合中找出最符合设计要求的材料,显然是重点考虑的问题。
最后,采用轻量化材料的前提是保证材料替换的结构的各项基本性能仍达到设计要求。
在采用轻质材料的同时,还需结合结构优化设计以及相匹配的制造工艺,才能达到理想的轻量化效果。
因此,结构优化后结构形式的变化问题、轻质材料的制造工艺以及异种材料间的连接问题,都是多材料结构面临的关键问题。
综上所述,钢铝结合车架面临着异种金属间的连接技术、材料匹配、高强度钢和铝合金的先进成形工艺技术、电化学腐蚀及热变形不协调等突出问题。
对于试图在成本约束下进一步减小车架重量的汽车工业而言,这些问题的解决都是迫切需要的。
3 钢铝结合车架CAE优化方法3.1 钢铝结合结构研究乘用车排放标准更高,为了节能减排,铝合金材料在20世纪80年代就已经应用在车身上,且铝合金在乘用车材料中的使用比例逐年提高。
随着近年来商用车排放标准的日益严苛,商用车同样需要进行轻量化。
虽然目前的成形技术还达不到商用车车架全铝,但设计钢铝结合结构是目前解决轻量化难题的可行途径之一。
一般来说,钢铝结合车架的结构优化分成两个部分:第一部分,首先根据强度和刚度等安全指标作为约束,把材料作为变量组进行优化,以得到材料分配后的车架;第二部分,对选定好材料的车架进行优化,以强度、刚度和模态特性等作为约束,把板厚等作为变量进行结构优化,最后获得满足多种指标的车架轻量化方案。
有关研究[13]以某国产SUV车架为例,对其进行刚度和模态仿真分析,使用铝合金材料,结合正交试验法确定材料轻量化目标。
建立优化设计数学模型,进行多目标形貌优化设计,得到满足刚度和模态性能的钢铝复合车架模型。
相关研究[14]对基于耐撞性的车身前端结构钢铝混合材料轻量化设计,以简化模型中的前保险杠、吸能盒、副车架前横梁等构件为对象,采用均匀实验设计与RBF近似模型,建立了综合考虑总质量、总吸能、白车身扭转刚度、前纵梁后端峰值碰撞力等性能在内的钢铝混合材料与板厚组合多目标优化问题的数学模型,最终取得了研究对象减重29.1%的轻量化效果。
3.2 计算机仿真优化研究20世纪70年代,随着计算力学和计算机硬件的发展,解决一些复杂结构的问题也变得越来越方便,从而推动了结构轻量化的发展。
20世纪90年代以后,国外众多研究者加入到商用车及乘用车车架的计算仿真工作中来,Bhope等[15]借助有限元软件对挂车底盘进行改进,最终减轻了其重量;Nor等[16]通过CATIA对拖车车架进行有限元分析,设计工字梁尺寸提高其安全系数。
近年来,轻量化理论方法和CAE软件不断出现,应用越来越成熟。
目前我国的轻量化研究主要采用这种方式,如南京航空航天大学的研究团队[17]利用ANSYS根据满载时均布载荷作用在车架上的计算工况对车架进行了结构参数优化设计,使车架质量降低了17.9%。
湖南大学的研究团队[18]运用区间分隔拓扑优化并综合尺寸优化确定了车架的最终尺寸,最终减重10%。
安徽理工大学的有关研究[19]利用Optistruct以扭转工况下最大应力值为约束对纵梁、横梁、连接板、尾梁和后加强板进行尺寸优化,使车架总质量较少约11.8%。
然而有限元仿真存在着计算量过大、收敛速度缓慢甚至不收敛等难题,为解决这些难题,通常采用试验设计提取采样点建立近似模型的方法来代替复杂有限元仿真,达到简化优化过程和减少计算成本的目的。
试验设计是建立近似模型的前提和基础,为了构造具有较高精度的近似模型,必须选择合适的试验设计方法,使样本点能够按照一定的规律分布在设计空间内,较为准确地反映系统输入与输出之间的关系。