内压缩流程与外压缩流程空分装置能耗的比较
空分技术
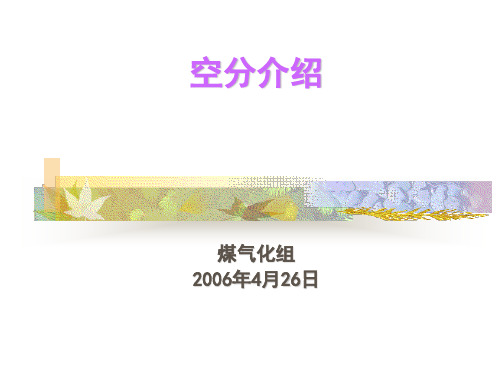
此流程尤其适用于为向以含碳物质为原料的制氢装置提供高压氧、 氮
低温分离技术的发展——内压缩流程
此流程尤其适用于为向以含碳物质为原料的制氢装置提供高压氧、 氮
与常规低压外压缩流程相比,不仅液氧泵的维护要比氧压机简单, 而且液氧泵的价格比离心式氧压机要便宜得多,故可减少液氧内 压缩流程设备的投资费用
至工艺所需压力~0.63MPa 过滤后的空气质量要求:固体物含量<0.5 ml/Nm3,粒径<0.1微米 对原料空气的质量要求:
杂质名称 机械杂质 CO2
C2H2
CnHm
允许含量
<30mg/m3(标) ≤350ml/m3 ≤0.5ml/m3 ≤30ml/m3
流程简述——预冷和前端净化
压缩后的空气在空冷塔(E2416)中以对流形式被两层喷淋冷却 水冷却和清洗。在底部,空气被来自(P2466A/B)水泵的循环冷 却水预冷,在顶部,空气被经水冷塔(E2417)、冷冻水泵 (P2467A/B)和氨冷器 (E2422)后冷冻水冷却。最终空气出空冷 塔温度~13°C。
流程简述
流程特点
此装置采用氮气循环单泵内压缩流程,即采用增压氮气循环压缩 机+液氧泵并通过换热器系统的合理组织来取代氧压机,同时增 压氮气循环压机即做产品氮压机又做循环增压氮压机
合理配套自动化程度高的后备贮存系统 原料空气自洁式过滤器的滤筒能在不停车条件下更换
采用径向流分子筛吸附器结构,具有气流分配均匀,占地小,配 管简单等优点;特殊的吸附剂对氧化亚氮吸附率>90%
装置所需冷量由压缩空气或压缩氮气膨胀做功制取 早期发展:产品提取率的提高、原料空气的净化、换热器效率的
空分设备知识介绍
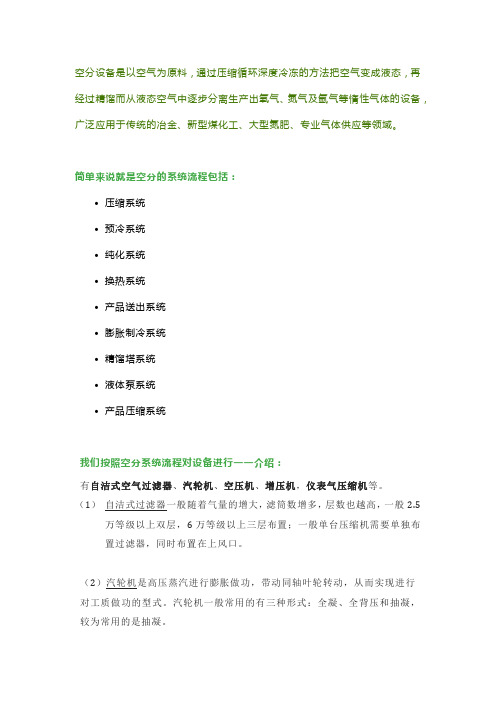
空分设备是以空气为原料,通过压缩循环深度冷冻的方法把空气变成液态,再经过精馏而从液态空气中逐步分离生产出氧气、氮气及氩气等惰性气体的设备,广泛应用于传统的冶金、新型煤化工、大型氮肥、专业气体供应等领域。
简单来说就是空分的系统流程包括:•压缩系统•预冷系统•纯化系统•换热系统•产品送出系统•膨胀制冷系统•精馏塔系统•液体泵系统•产品压缩系统我们按照空分系统流程对设备进行一一介绍:有自洁式空气过滤器、汽轮机、空压机、增压机,仪表气压缩机等。
万等级以上双层,6万等级以上三层布置;一般单台压缩机需要单独布置过滤器,同时布置在上风口。
对工质做功的型式。
汽轮机一般常用的有三种形式:全凝、全背压和抽凝,较为常用的是抽凝。
产能耗低2%左右,投资高80%;空压机采用出口放空,不设置回流管路,一般有最小吸入流量防喘振要求,采用入口导叶进行流量调节,进口国产机组均是四级压缩三级冷却(末级不冷却)。
主空压机配备一套水洗系统,用以冲洗各级叶轮和蜗壳表面沉积物。
该系统随主机成套。
(5)增压机一般大型空分装置投资采用单轴等温型离心压缩机和齿轮式离心压缩机两种,其中齿轮式在能耗上占较大优势,尤其压比较大的工况。
(6)仪表气压缩机一般有三种形式:无油螺杆机,活塞式和离心式。
由于活塞式和离心式天然无油,所以不需要除油装置,只需要配套干燥装置(除水)和精密过滤器(除固体颗粒)即可;而螺杆机一般有有油和无油然后除油两种,喷油螺杆机需要设置除油装置,同时需要设置精度非常高的除油过滤器,以满足工艺要求,这种机型的优势是价格较便宜;无油螺杆采用干转子或者水润滑,这种机型优点是绝对不含油,缺点是价格较贵。
气量500Nm³/h以下适合选活塞式;气量在2000Nm³/h以下适合选螺杆机或活塞机;气量在2000Nm³/h以上即三种机型都可以选,气量大时离心式压缩机较有优势,其易损件较少,同时好维护,性价比较高。
仪表压缩机在开车时使用,正常运行后由分子筛纯化器后抽取。
低温法大型空分氧气的内压缩流程和外压缩流程的选择

低温法大型空分氧气的 内压缩流程和外压缩流程的选择
杨漠源 (中冶南方工程公司上海分公司2019007)
摘要:上世纪90年代以前,内压缩流程又名“化工型流程”,用于用氧压力较高的化工企业;外压缩流程又名“冶 金型流程”,用于中等用氧压力的钢铁企业。随着科学技术的发展,大型空分的氧气升压已有多种方式可供选 择。本文就其投资、成本和能耗进行了比较,并按照节省投资、能源和因地制宜的原则,提出了自己独到建议。 关键词:内压缩流程;外压缩流程;氧压机;液氧泵
上世纪90年代以前,内压缩流程又名“化工型流程”,用于用氧压力较高的化工企业;外压 缩流程又名“冶金型流程”,用于中等用氧压力的钢铁企业。随着科学技术的发展,大型空分的 氧气升压已有多种方式可供选择。这几种方式的投资、成本和能耗也在不断的变化中,特别是 近10年来,氧气内压缩流程的工艺和设备得到了较快的发展,除了在用氧压力较高(6—9MPa)
52
技术论谈篇
一30bar范围内中压空气压力是氧气压力的2.2~2.1倍。这就是内压缩流程能耗高的原因。 虽然增压机的效率高于氧压机,但只能缩小能耗的差距,改变不了总的结果。
内压缩流程的能耗高于氧压机流程,这一点已被公认。至于高几个百分点,各家说法不一, 从2%一11%不等,因为它不仅与增压空气的流量和压力有关,还决定于流程组织和氧压机、增 压机的效率。只有当同一厂商为同一产品规格在同样的自然条件下选用同一厂家的压缩机时, 二种流程的能耗比较才接近真实。如参数文献[1]提到的林德为33250N矗/h空分设备所做的 二种能耗比较图(图2),在30bar时内压缩流程总功率为22400kw,外压缩流程为21150kw,内压 缩的能耗高5.9%。笔者还就林德提供的宝钢60000Nm3/h内压缩流程和武钢60000Nm3/h外压 缩流程的能耗进行了详细的比较。60000Nm3/h内压缩流程能耗按宝钢数据,60000Nm3/h外压 缩流程能耗在武钢数据的基础上,换算成与宝钢六万的产品规格.水温、气温条件一致,并将中 压和高压氮压机的流量和压力按宝钢数据进行了修正,空压机能耗按32℃水温和苏尔寿的效 率进行了修正,修正后的总能耗为37991kw,宝钢60()00Nm3/h内压缩流程总能耗为40456kw,比 同样条件的外压缩流程高6.5%。这一数据与宝钢60000Nm3/h林德的内压缩与APCI的外压缩 比较结果相近。参考图6的5.9%数据,笔者以为就目前的工艺水平和压缩机的效率情况,在考 虑了增压机和氧压机效率差诸因素之后,内压缩流程的能耗仍然高于外压缩约6~6.5%。
1000207987

收稿日期:2006206227作者简介:孙日光(1966— ),男,助理工程师,毕业于武汉冶金安全技术职工大学,现任酒钢动力厂制氧部副部长。
酒钢21000m 3/h 空分设备工艺特点及调试体会孙 日 光(酒泉钢铁公司动力厂制氧部,甘肃省嘉峪关市 735100) 摘要:简介了酒钢21000m 3/h 空分设备的工艺流程,分析了流程和设备配置的特点,阐述了空分设备安装调试中得到的经验。
关键词:大型空分设备;外压缩流程;制氩系统;调试中图分类号:T Q116111 文献标识码:BOperating character istics and commissioning of 21000m 3Πh a irseparation unit at JiugangSun Ri 2guang(Oxygen Produc i ng Works of Power Division ,J iuquan Iron &Ste el Group C o 1,Ltd 1,J iayuguan 735100,Gansu ,P 1R 1China)Abstract :A brie f intr oduction of operating characteristics of 21000m 3Πh air separation unit in Jiugang (Jiuquan Ir on &Steel G roup C o 1,Lt d 1)is follow ed by an analysis of its flow and configuration.The exper ience from installation and comm i ssioning of the air separation unit i s also presented.K eyw ords :Large scale air se paration unit ;External com pression flow ;Argon recovery system ;C ommissioning 酒泉钢铁公司(简称酒钢)3套21000m 3/h 空分设备是为酒钢“200万t 铁钢”项目以及酒钢不锈钢工程配套的最重要的公辅工程,也是酒钢“十五”以及“十一五”期间重要的建设项目。
再谈内压缩流程与外压缩流程能耗的比较

内压缩流程与外压缩流程空分装置能耗的比较江楚标陈明敏中国空分设备公司摘要:由于不可逆性较大和产品提取率略低,当氧气压力为30bar时,内压缩空分流程空分装置的产品单位能耗要高于外压缩流程。
氧气压力不同,两者产品单位能耗的差距是不同的。
随着液体膨胀机等先进单元设备的使用,这种差距将缩小。
只要采取可靠的措施,国内空分设备的设计、制造、成套公司也能设计、制造和成套出可靠先进的内压缩流程大型空分装置。
关键词:能耗比较怎样比较液体膨胀机一、序在“内压缩空分流程及与常规流程的比较”[1]一文中,我们指出内压缩流程空分装置的能耗(制氧+压氧)要比常规流程高3~7%。
文献[2]认为,要高5%~7%。
最近有一些用户对我们说:他们听有些制造厂商介绍,内压缩流程的能耗要比常规流程低(也指氧压为30bar)。
在有些报道和文章中,一些企业和作者也有意无意地作类似的报道和介绍。
因此,我们认为对这个问题有进一步加以讨论的必要。
二、在30bar的氧压下,内压缩流程空分装置的产品单位能耗要高于外压缩流程内压缩流程首先用于氧气终压高于其临界压力(51.3bar)的化工用户。
当时的主要考虑既不是能耗的高低,也不是投资的多少,而是因为大流量氧气的高压压缩不够安全,即主要是基于安全可靠性的考虑。
随着技术的不断进步,到90年代初,常规外压缩流程空分装置的氧气提取率已达99%以上,在控制液体产量使进上塔的膨胀空气量小于加工空气量的10%时,氩的提取率可大于80%,单位制氧+压氧(到30bar)能耗可达≤0.568Kwh/m3[2]。
膨胀空气进下塔的外压缩流程,氩的提取率可达92%以上。
与此同时,内压缩流程的氧、氩提取率也有了极大的提高,单位产品能耗也随之大大降低。
但到目前为止,在一定的氧压范围内,内压缩流程空分装置的单位产品能耗仍然要高于外压缩流程。
当氧纯度为98%及以下时,这个氧压范围为15~45bar[3]。
当氧纯度99.6%时,这个氧压范围还会有所扩大。
内压缩流程空分设备氧气纯度调节方法分析

内压缩流程空分设备氧气纯度调节方法分析浙江绍兴三锦石化有限公司,浙江省绍兴市312000摘要:液氧内压缩流程空分设备与氧气外压缩流程空分设备工艺流程不同,上塔提馏段氧气纯度调节方法差异较大。
内压缩流程空分设备采用空气循环增压、膨胀空气进下塔、液氧内压缩及氮气外压缩、全精馏制氩工艺流程关键词:内压缩流程;空分设备;氧气纯度;调节方法引言液氧内压缩流程空分设备自投入运行,在空分设备开车、运行时对上塔提馏段氧气纯度采用不同调节方法,经过对内压缩流程空分设备上塔提馏段氧气纯度不同调节方法进行分析及实际运用效果比较,认为内压缩流程空分设备氧气纯度调节方法与传统的外压缩流程空分设备氧气纯度调节方法有较大不同。
1空分流程简介制氧生产使用的是空分设备,其中4台空压机在生产中为用3备1,2台膨胀机用1备1,纯化器1组再生切换使用。
生产流程为:1台空压机提供原料气体,通过预冷机机组使原料气体降温,经油水分离器后进入纯化器进行干燥净化,去除水分、二氧化碳和碳氢化合物后的洁净空气进入主换热器,经过热交换温度降至-173℃后进入空分塔进行精馏;冷却原料气体的冷量由制冷循环系统提供,制冷循环系统使用的气体为经过纯化器净化后的洁净空气,由2台空压机循环气体,加压后的洁净空气进入增压机增压后进入膨胀端,压力下降,气体对外做功,温度下降,膨胀后的空气温度在-183℃左右进入主换热器用于冷却原料空气,换热后的气体再由空压机压缩提高压力。
在循环过程中,损耗的气体用原料气体进行补充。
2制冷系统密封分析制冷循环系统气路是闭合运行的,经过启动调整后的循环空气量相对稳定。
在不考虑原料气体影响的前提下,循环系统密封不严密会使未净化的空气进入循环系统或冷却器微漏,导致主换热器堵塞,系统无法正常运行。
近年来多次出现主换热器堵塞问题,经排查发现是由于循环系统密封不严,大气进入循环系统,水分、二氧化碳等杂质在主换热器中析出导致堵塞。
2.1分子筛吸附效果影响空分设备主要采用纯化器净化原料空气,纯化器中装填13X-APG型分子筛。
内压缩空分原理

内压缩空分(Internal Compression Air Separation, ICAS)原理是基于空气分离的低温精馏技术,通过多级压缩、冷却、液化和精馏等步骤,实现对空气中氧气、氮气和其他稀有气体的高效分离。
在传统的空分设备中,通常需要独立的压缩机将空气压缩至所需压力后进行后续处理。
而内压缩空分工艺则将一部分压缩与膨胀过程结合在同一台或多台机组内部完成,以优化能效并简化流程。
具体来说,内压缩空分的主要特点包括:
1. 空气压缩:首先,空气经过滤器去除杂质后被送入离心式或轴流式压缩机进行多级压缩,提高压力以便于后续的液化。
2. 预冷与纯化:压缩后的高温高压空气经由一系列换热器逐步预冷,并通过分子筛吸附器或其他净化装置除去水分、二氧化碳等杂质,确保进入主换热器和精馏塔的空气纯净且温度足够低。
3. 内压缩环节:不同于常规外压缩流程,在内压缩空分中,从上塔顶部抽出的部分富氧气体或者下塔底部
抽出的部分富含氮气的液体,在精馏过程中被再次增压,这一增压过程在设备内部集成,而不是通过外部独立的压缩机完成。
4. 制冷与液化:利用膨胀机制冷(如节流阀或透平膨胀机)使空气深度冷却到液化温度,随后进入精馏塔进行分离。
5. 精馏分离:在精馏塔内,根据各组分沸点的不同,通过多次蒸馏和冷凝过程,实现氧气、氮气以及其他惰性气体的逐一分离。
6. 产品提取:分离得到的产品气体(液氧、液氮、液氩等)被取出存储或汽化供应给用户。
内压缩空分工艺的优势在于可以减少压缩机的数量和运行能耗,同时提高了系统的紧凑性和整体效率。
不过,该工艺设计复杂度较高,需要精确控制不同工况下的能量交换和物料平衡。
5000Nm_3_h空分的两种内压缩流程比较
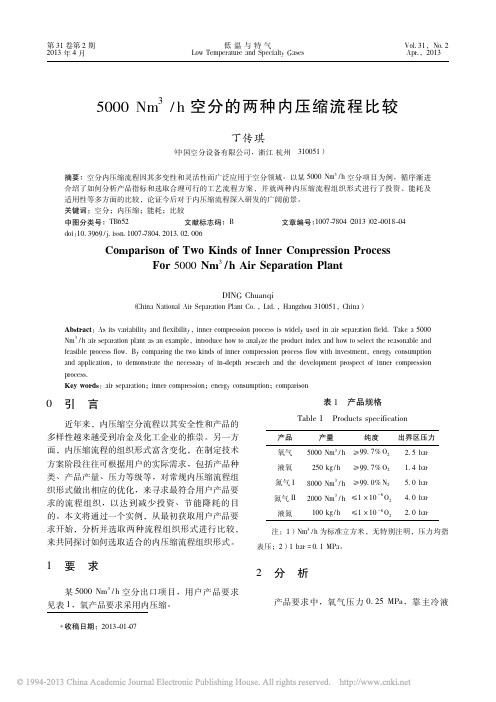
介绍了如何分析产品指标和选取合理可行的工艺流程方案,并就两种内压缩流程组织形式进行了投资、能耗及
适用性等多方面的比较,论证今后对于内压缩流程深入研发的广阔前景。
关键词: 空分; 内压缩; 能耗; 比较
中图分类号: TB652
文献标志码: B
文章编号: 1007-7804( 2013) 02-0018-04
空压机一压到底,膨胀空气进下塔流程: 通过 流程的优化,取消了独立的增压机,采用多一级叶 轮的空压机来替代。从流程组织上来看,工艺流程 得到进一步简化,机组间的配管将十分简便。从设 备投资上看,目前国产空压机制造工艺成熟,运行 性能稳定,价格上与同时购置空压机、增压机两台 机组相比有明显优势。另外,采用膨胀空气进下塔 流程,空压机排气量较膨胀空气进上塔流程减少约 2100 Nm3 / h,装置氧提取率已达 95% 以上,且上 塔回流比能够得到充分保证,工况变负荷能力强, 液体产品尤其是液氮产品产量有较大的调节空间。 经流程计算,在其他产品产量不变的情况下,液氮 产量最大能达到约 350 kg / h。但是,通过比较也发
3比较
3. 1 流程比较 膨胀空气进上塔流程: 出分子筛纯化系统的空
气除去用作仪表空气部分外,其余分三路: 第一路 空气直接进入主换热器,被返流出来的气体冷却接 近露点抽出,直接进下塔参与精馏; 第二路空气进 入空气增压机组增压后进入主换热器,被液化后节 流进下塔参与精馏; 第三路空气进入增压透平膨胀 机增压,经主换热器冷却至一定温度后去膨胀机膨 胀,膨胀后进上塔参与精馏。
Table 4 Expansion turbine
Table 2 Main air compressor ( incl. the instrument air and the loss)
开封空分大中型内压缩流程空分设备的研发

刘 景 武 ,马 源 (开封 空分 集 团有 限公 司设 计 研 究 院 ,河 南 省 开 封 市 公 园 路 28号 475002)
摘 要 : 总 结 开 封 空 分 内压 缩 流 程 空 分 设 备 技 术 的 发 展 历 程 、 流 程 的 分 类 及 工 艺 流 程 组 织 和 大
20世 纪 90年代 中期 以前 ,国 内设 计 生 产 的空 分设备 几乎 全是外 压缩 流 程 。20世 纪 90年 代 中后 期 ,随着气 体市 场需求 的变 化 ,用户对 空分 产品 的 品种要 求越 来越 高 ,越 来越 多 的用户要 求采 用 内压 缩流 程 。 目前 ,要 求 lO000m。/h等 级 以 上 空 分 设 备采 用 内压 缩流 程 的用 户越 来越 多 。以往在 冶金行 业采 用较普 遍 的是外压 缩 流程 ,现 已有 很多 冶金行 业 的用户 要求采 用 内压缩 流程 ,而 国外 用户 或 国内 独 资企业 用户更 偏重选 择 内压缩 流程 。 内压 缩流程 以其 安全 可靠 ,占地 面积小 ,液 体产 品产量 大等优 势逐 步被用 户所 接受 。
中型 内压 缩流程 空 分设备 的 系统配置 ,阐述 开封 空分 新技 术的研 究与 开发情 况。
关 键 词 : 大 型 空 分 设 备 ; 内压 缩 流 程 ;流 程 组 织 ; 系 统 配 置
中图分类 号 :TB657.7
文献 标识 码 :A
Research and development of large and medium scale air separation units with internal compression process at Kaifeng
大型液氧“内压缩”中压空分流程主要参数分析计算

如上节所述 ,大型 中压液氧 “ 内压缩”空分装置加工空气压力确定,与小型中压空分装 置 加工空气 压力确定有所 不同 小型 中压空分 加工空气 压力 由全装置热平衡确 定 而该 中压 空分流程加 上空气 压力要 由主换热器热段 中部最小传热温差来确定 。 如果 人为取定该处最小传热温差 , 根据 主换热器热段最小传 热温差以上部分热平衡就能确定 P 3 主换 热器热 平衡图如右面 图 2 示( 所 图中将纯 N , 与污 N 合并为氮气 , Z 简化计算过程) 。图 2中在主换热 器热段与冷段均 存在一条最小传热温差线。 热段中部最 小传热温差线 1一般比高压氧最大 比热温度处稍低。 。 高 压氧压力大于临界压力 , 该最小传热温差线处温度高 于 氧气 临界温度 , 并随高压氧 压力升高而升高 ; 高压氧 压 图 2 主换热 器热平衡 图 力等于或低于氧气临界压力 , 该处温度 为对应氧气 临界 温度或沸点温度。冷段 中部最小传热温差线 2 于加工空气沸点温度处或稍低 。 处 3 1 主换 热器热平街关 系式 . 按图 2 主换热器热平衡式如 F: 所示
量 多 为好 。
再从空分塔精馏的角度分析 ,也以取出液氧产品为好 。因为,取出液氧产品,对空分塔 精馏影响不大 ;而取出液 氮产 品,致使空分上塔精馏段 回流 比下降 ,氮气质量难以保证 。需 要用更高效率的上塔结构.增 加设备一次投资。否则 ,要降低空分塔氧气提取率 ,增加单位 纯 产品能耗 。
2 影响增压 后加工空气压力因素分析
2 1 筑 气与空 气( . 或氮气’ 力学性质 不同,正好与 热交换要 求相 反。致使增 压后空气压力 . 热 ( 如图 1 P , 中 3下同) 升高。 从热力学性质看 , 氧气沸点温度与临界温度 比空气( 氮气 ) , 或 高 在换热器 中相 同压力下 , 氧气 比热大的温度段比空气比热大的温度段 高。而换热器热交换要求冷侧氧气 比热大的温度 温度段比热侧空气比热大 的温度段低 ,才能保证热交换 比较 完全。否则 ,需要提高空气 压力 P 或者增加与氧气换热的空气流量比例 。大型液氧 “ , 内压缩”中压空分 流程 ,输出产品氧气 一般都高于氧临界压力,氧气最大 比热温度段在氧气临界温度 以上。同时 ,随着氧气压力的 升高 ,最大比热温度随之升高 。如 用与氧气等量的空气 与液氧 完全换热 ,空气压力需高达氧
浅析制氧装置的工艺和设备节能要点

浅析制氧装置的工艺和设备节能要点发表时间:2020-10-23T02:45:47.545Z 来源:《防护工程》2020年17期作者:吴冰[导读] 氧气和氮的生产是化工和能源行业消耗的一大部分,特别是电力消耗,其工艺和设备的节能设计更为重要。
身份证:13020319850804****摘要:当前,能源消费不断增加,温室效应日益严重,工业节能减排要求不断增大。
化工行业的特点是高能耗,环境污染大,节能减排压力大。
氧气制造机广泛分布在化工行业,能耗较高。
因此,基于工艺、设备的节能设计更显重要。
当前,最为常用的是深冷法制氧,其主要设备有空压机、分馏塔系统、电加热器、氧压缩器、氮压缩器、水冷却器等主要设备,应合理选用这些设备,采取节能措施,达到最高节能效果。
关键词:制氧装置;节能减排;深冷法;制氧工艺在工业气体中,氧气、氮气、氩气、二氧化碳等都具有一定的物理和化学性质,在工业生产的各个领域发挥着重要的作用。
氧气和氮的生产是化工和能源行业消耗的一大部分,特别是电力消耗,其工艺和设备的节能设计更为重要。
1.基于制氧装置工艺的节能分析1.1常用制氧工艺截至目前,工业生产中常用的制氧工艺主要有电解法、膜法富氧、深冷法、变压吸附法等。
这几种制氧工艺的区别如表1-1所示。
表1-1 常见制氧工艺的区别从表1-1中可以看出,深冷法的效果最佳,已经广泛应用于制氧工艺,适合大型化的工业制氧生产。
1.2氧气压缩方式的两种流程从生产流程上看,氧气的压缩有两种,分别是外压缩和内压缩。
外压缩流程,主要使用氧压机将空分设备中的低压氧气压缩出来,再送往用气点,;内压缩流程,使用液氧泵压缩液态氧气,再经换热器将其汽化,随后送往用气点。
两种流程不同的是:外压缩流程所使用的设备占比面积大于内压缩流程,而两种流程相同的是,均具有初始投资低、能源消耗低、氧气供应可靠、安全程度高、经济效益良好等特点。
1.3深冷法制氧工艺的系统和设备1.3.1深冷法制氧工艺深冷法,使用分子筛净化空气,同步使用增压膨胀流程,经精馏塔填料制取氩气,主要消耗能源工质是水、电等。
关于空分装置试车问题及解决方案

关于空分装置试车问题及解决方案【摘要】本文介绍了榆神能化公司80000Nm3/h空分装置的流程特点、试车过程中的问题及处理方法。
【关键词】空分流程特点试车一、前言陕西延长石油榆神能化公司80000Nm3/h空分装置由杭州杭氧集团公司成套设计供货,采用一拖二压缩机组、预冷系统、分子筛吸附净化、增压透平膨胀机制冷、规整填料、液氧液氮内压缩流程,于2022年9月产出合格氧氮,相关产品指标详见下表。
截至目前装置运行平稳,本文对该装置试车以来的问题及解决方法进行总结。
二、流程特点1、冷却水采用闭式冷却水。
若厂区循环冷却水与各化工装置共同使用,难免存在介质泄露,导致循环水TDS、电导率、浊度、COD等偏高,为保证装置的长周期安全稳定运行,在装置选型期决定采用闭式冷却水进行冷却。
2、氮气等级多,且氮气使用量大。
3、纯化系统中分子筛采用三层设计,惰性氧化铝+活性氧化铝+分子筛,在能够有效吸附空气中的水分、二氧化碳、碳氢化合物、氮氧化合物的同时,且能够保证分子筛的使用寿命及使用效果。
4、精馏塔采用规整填料塔,压降小,滞留量少,调节灵敏,提高了对氧氮的分离能力,并有利于装置的变负荷生产,且极大的降低了单位产品的能耗。
5、在设计高压液空节流阀的同时设计液体膨胀发电机(200kw),在装置平稳运行时由高压节流阀切换为液体膨胀机运行每年可发电量约为160万千瓦时。
6、主冷凝蒸发器采用双腔四层设计,在保证装置安全运行的同时极大的降低了装置能耗。
7、氧氮产品采用经典的内压缩工艺流程,保证了氧气系统的安全运行,与外压缩流程相比装置能耗大大降低。
8、冷箱设计安全可靠,因冷箱内装有珠光砂进行保冷,若存在泄漏需要停装置并将珠光砂拔掉后方可进行检修,每次需要十几天到二十几天的检修时间,为防止冷箱内设备与管道泄漏,采用以下技术措施:①主冷箱内所有连接处采用焊接形式,不得采用法兰连接,并且所有焊口100%进行射线探伤,在投用前并进行耐压性、气密性试验、裸冷试验,各项合格后方可填装保冷珠光砂。
液氧内压缩流程特点

液氧内压缩流程特点
液氧内压缩流程是一种在低温环境下,通过内压缩机对液氧进行加压、增压和输送的工艺流程。
这种流程广泛应用于航天、医疗、化工等领域,具有其独特的特点。
首先,液氧内压缩流程的安全性极高。
由于液氧具有极低的温度和极高的反应活性,因此在处理过程中需要特别注意安全问题。
液氧内压缩流程采用封闭式设计,可以有效防止液氧泄漏,大大降低了安全事故的风险。
其次,液氧内压缩流程的效率高。
与传统的外压缩流程相比,内压缩流程可以直接将液氧压缩至所需的压力,避免了液氧在气化和再液化过程中的能量损失,提高了工作效率。
再次,液氧内压缩流程的操作简便。
内压缩流程采用了自动化控制系统,可以自动调节液氧的流量和压力,减少了人工操作的复杂性和错误率,提高了工作效率。
最后,液氧内压缩流程的设备投资和运行成本较低。
内压缩流程的设备结构简单,维护方便,且能源消耗低,长期运行下来,能为企业节省大量的成本。
简析空分装置工艺技术路线的分析及比选

简析空分装置工艺技术路线的分析及比选文章首先对分离技术进行分析,分别介绍了低温法、吸附法以及膜分离法等,对空分装置工艺技术路线的选择进行探讨,无论是液态产品的工艺选择,还是气态产品的工艺选择,都要根据产品的实际需求进行选择。
标签:空分装置;工艺技术;技术路线;分析;选择1 引言空分装置是利用深度冷冻的方式,对空气中O2、N2以及其他稀有气体等,按照气体的沸点的区别而进行逐个分离的装置。
随着现代科学技术的进步和发展,空分技术在一定程度上实现从高能耗向节能环保的过渡,而且分子筛系统、预冷系统、分馏塔上塔以及膨胀机系统都有比较好的发展趋势。
本文对有关空分装置工艺技术路线的分析及比选进行研究和探讨,不足之处,敬请指正。
2 分离技术分析2.1 低温法低温法首先是把空气进行压缩,使其膨胀降温,最后空气被液化,然后利用氧气、氮气的气化温度的区别,氧气的沸点是90K,氮的沸点是77K,沸点较低的氮气和氧气相比较而言更加容易被气化,在精馏塔内和温度较高的蒸气相互接触,液体中氮气被蒸发,气体中液氧被冷凝,使得上升蒸汽中含氮量提升,下流液体中含氧量增大,以此实现空气分离的目的。
让空气液化,其要求是要把空气冷却到100K之下,我们把这种方法称之为深度冷冻;通过沸点差把液空进行分离,我们称之为精馏过程,而低温分离法就是结合了深度冷冻和精馏过程,是现阶段应用较为广泛的空气分离方法。
除此之外,现阶段我国生产的空分装置型式和种类比较多,包括生产气态氧、氮的设备,生产液态氧、氮气的设备,然而就低温分离法来说,我们可以把其基本流程分为四个方面,也就是高压、中压、高低压以及全低压流程。
2.2 吸附法吸附分离法就是利用某种特殊物质,让空气吸附,通过分子筛的吸附塔,对具有不同吸附特点的空气进行分离,比如有些分析筛5A、13X等,对于氮气具有很强的吸附能力,仅仅让氧气分子通过吸附塔,从而得到了较高纯度的氧气;有的分子筛,比如说碳分子筛,对于氧气有较高的吸附能力,那么可以得到较高纯度的氮分子。
典型空分流程的简述及运行能耗分析

典型空分流程的简述及运行能耗分析发表时间:2018-07-05T14:46:23.793Z 来源:《建筑模拟》2018年第6期作者:邬从军马靖棠[导读] 以伊犁新天煤化工KDON-51000/26000空分装置为背景,简单介绍了空分装置的工艺流程以及装置运行中的能耗分析。
伊犁新天煤化工有限责任公司新疆伊犁哈萨克自治州 835000摘要:以伊犁新天煤化工KDON-51000/26000空分装置为背景,简单介绍了空分装置的工艺流程以及装置运行中的能耗分析。
关键字:工艺流程;原理;能耗;分析伊犁新天煤化工有限责任公司是浙江能源集团和山东能源新矿集团共同投资成立的国有合资企业。
地处新疆自治区伊犁哈萨克自治州伊宁市,公司占地面积5700亩,于2010年开工建设,2017年建成投产,以年产20亿Nm3煤制天然气为主,该项目是目前国内外已建成的最大单体煤制天然气项目。
其中空分装置采用杭氧公司内压缩流程,氧产量51000Nm3/h,氮气产量26000Nm3/h。
其中空分装置是整个项目最重要的部分之一,它的稳定运行是后续工段连续稳定的重要保障。
1、空气分离的方法及原理空气中的主要成分是氧和氮,它们分别以分子状态存在。
分子是保持它原有性质的最小颗粒,直径的数量级在10-8cm,而分子的数目非常多,并巨不停地在作无规则运动,因此,空气中的氧、氮等分子是均匀地相互搀混在,起的,要将它们分离开是较困难的。
目前主要有3种分离方法。
(1)低温法先将空气通过压缩、膨胀降温.直至空气液化,再利用氧、氮的气化温度(沸点)不同(在气压力下,氧的沸点为90K,氮的沸点为77K).沸点低的氮相对于氧要容易气化这个特性,在精馏塔内让温度较高的蒸气与温度较低的液体不断相互接触,液体中的氮较多地蒸发,气体中的氧较多地冷凝.使上升蒸气中的含氮量不断提高,下流液体中的含氧量不断增大,以此实现将空气分离。
要将空气液化,需将空气冷却到100K以下的温度,这种制冷叫深度冷冻;而利用沸点差将液空分离的过程叫精馏过程.低温法实现空气分离是深冷与精馏的组合,是目前应用最为一泛的空气分离方法。
空分设备换热器设计及温差选取

空分设备换热器设计及温差选取蒋旭【摘要】The design software environment of common air separator heat exchange sys-tem is introduced, while the design of heat exchanging resistance of air separator, heat ex-change for gases, liquids and gas-liquid mixtures and the choice of temperature difference of heat exchanger are described in detail. With the rapid development of air separation sector, studying, rationally analyzing and utilizing the heat exchange system of air separator bear great significance for improving the designing ability of the industry.%介绍了一般空分设备换热系统的设计软件环境,同时对空分设备的换热阻力设计,对气体、液体以及气液混合物的换热及换热器温差选取进行了详尽的阐述。
随着空分行业的蓬勃发展,研究并合理地分析应用空分换热系统对提升行业设计能力有重大意义。
【期刊名称】《冶金动力》【年(卷),期】2014(000)008【总页数】6页(P26-30,35)【关键词】空分设备;换热器;设计【作者】蒋旭【作者单位】中空能源设备有限公司,浙江杭州 310052【正文语种】中文【中图分类】TB657.71 前言板翅式换热器结构紧凑、轻巧,我国从20世纪50年代开始在空分设备中应用板翅式换热器,板翅式换热器在设计制造都经历了艰难的过程。
200MW富氧燃烧电站三塔空分流程模拟与优化

200MW富氧燃烧电站三塔空分流程模拟与优化韩涛;余学海;廖海燕;王艳君;黄科;廖彬【摘要】为降低空气分离(简称空分)制氧单耗,提高富氧燃烧发电系统效率,根据富氧燃烧的需氧特点,提出了三塔空分制氧流程.采用Hysys软件对三塔空分流程进行了模拟,对塔板数、进料位置、空气压缩机中间抽气压力等关键参数进行了优化,并分析了不同制氧浓度下空分系统的制氧单耗.研究结果表明,制氧单耗随氧产品纯度的升高而增加.氧浓度为97%时,三塔空分流程的制氧单耗为0.3544 kW·h/m3,较双塔流程降低近10%,三塔空分流程的制氧单耗优于传统双塔流程,为进一步降低富氧燃烧空分制氧单耗提供了参考.【期刊名称】《中国电力》【年(卷),期】2016(049)004【总页数】7页(P134-140)【关键词】CO2捕集;富氧燃烧;空分;三塔【作者】韩涛;余学海;廖海燕;王艳君;黄科;廖彬【作者单位】神华国华(北京)电力研究院有限公司,北京 100025;神华国华(北京)电力研究院有限公司,北京 100025;神华国华(北京)电力研究院有限公司,北京100025;四川空分设备(集团)有限责任公司,四川简阳641400;四川空分设备(集团)有限责任公司,四川简阳641400;四川空分设备(集团)有限责任公司,四川简阳641400【正文语种】中文【中图分类】TKI6;X511富氧燃烧技术具有燃烧效率高、排烟损失小、NOx排放浓度大幅度降低等优点,与现有电站燃烧方式在技术上具有良好的承接性,是实现CO2大规模富集和减排的重要研究方向之一[1-3]。
与常规空气燃烧技术相比,富氧燃烧技术增加了空分装置,使系统循环热效率降低约10%。
制氧单耗低、动态响应快的空分制氧工艺的开发对降低富氧燃烧电站的能耗和成本至关重要[4-5]。
为降低空分制氧单耗和富氧燃烧系统能耗,许多学者从空分系统优化、制氧设备供电方式和富氧燃烧全系统集成优化等方面开展了相关研究。