液化气芳构化工艺研究
芳构化装置工艺介绍

芳构化装置一、装置简介芳构化装置,主要原料混合碳四液化气,产品有轻芳烃、重芳烃,民用液化气等。
原料混合碳四液化气,通过原料加热炉加热后,在反应器内与催化剂接触,经过低聚、环化,脱氢芳构化反应生成粗芳烃混合物,经过吸收稳定系统分离成合格的民用液化气和混合芳烃,再通过分馏分离成轻芳和碳9以上重芳烃。
装置区共有油、气罐16台,水储罐2台,其中地下密闭排放罐1台,机泵20台套。
为了防止污染环境和对操作人员造成损害,装置区所有排放的有机液体均排往密闭排放罐,然后根据情况再进行处理和排放。
二、工艺原理反应部分:轻烃芳构化的机理十分复杂。
一般认为,轻烃在分子筛的酸中心上芳构化反应时经历下列步骤:a)通过在酸中心上发生化学吸附生成正碳离子得到活化;b)正碳离子进一步脱氢和裂解生成乙烯、丙烯、丁烯和戊烯。
这些小烯烃是芳烃分子的建筑单元。
这步反应属于吸热反应;c)小烯烃分子在B酸中心上低聚(二聚、三聚)生成C6-C8烯烃,后者再通过异构化和环化生成芳烃前体(带6元环的前体)。
这步反应属于强放热反应;d)芳烃前体在L酸中心上通过脱氢生成苯、甲苯和C8芳烃等。
这步反应属于吸热反应。
在上述反应中,原料在酸中心上生成正碳离子的步骤最为关键。
它决定了芳构化反应的活性和选择性。
C3-C8之间的轻烃分子都可以在催化剂的酸中心上通过脱氢和裂解生成乙烯、丙烯、丁烯和戊烯。
当反应温度和催化剂的酸度相同时,从不同碳数的轻烃原料出发,可以得到具有同样热力学平衡分布的乙烯、丙烯、丁烯和戊烯。
由于基本建筑单元的种类和浓度分布相近,所以从不同碳数的轻烃原料出发都可以得到苯、甲苯和C8芳烃等产物,并且原料对芳烃产物的分布影响不大。
但是,若两种芳构化原料的碳数不同(如C3、C4、C5、C6、C7、C8)、结构不同(如直链烃、支链烃和环烷烃)和碳-碳键饱和程度不同(如烷烃、单烯烃、二烯烃),则其芳构化的活性、热效应和芳烃产率会有一定差别。
一般来说,碳数越小的原料在酸中心上生成正碳离子越困难,其芳构化活性越低;在同碳数下,烯烃比烷烃更容易生成正碳离子,因而其活性较高;另外,异构烷烃因可以生成相对稳定的叔碳正碳离子,因此其芳构化活性高于正构烷烃。
ZSM—5分子筛上液化石油气芳构化反应的研究

ZSM—5分子筛上液化石油气芳构化反应的研究
贺岩峰;彭承麟;王树江
【期刊名称】《长春工业大学学报(自然科学版)》
【年(卷),期】1992(000)001
【摘要】采用常压连续流动微反装置,考察了液化石油气在HZSM-5分子筛及各种改性分子筛上的芳构化反应,并对抑制积炭延长分子筛活性稳定性方面做了研究。
根据测得的催化剂样品上的吡啶吸附红外光谱及氨的TPD结果,提出了芳构化的活性中心是由B酸与L酸共同构成,B酸与L酸应有适宜配比的观点。
【总页数】1页(P62)
【作者】贺岩峰;彭承麟;王树江
【作者单位】化学工程系;化学工程系
【正文语种】中文
【中图分类】TE626.7
【相关文献】
1.FCC汽油在ZSM-5分子筛上的芳构化反应 [J], 刘多强;都长飞;高崇峰
2.醚后碳四在ZSM-5分子筛催化剂上的芳构化反应性能 [J], 樊金龙;许磊;徐亚荣
3.水对ZSM-11分子筛上干气芳构化反应性能的影响 [J], 李文亮;朱向学;刘盛林;张爽;谢素娟;刘善和;谷顺明;徐龙伢;曾蓬
4.ZSM-5分子筛催化剂上液化石油气低温芳构化制取高辛烷值汽油 [J], 宋月芹;徐龙伢;谢素娟;吴治华;王清遐
5.ZSM—5型分子筛催化剂上的丙烷芳构化反应 [J], 路宵霞;辛峰
因版权原因,仅展示原文概要,查看原文内容请购买。
C_4液化气芳构化制芳烃催化剂的研究
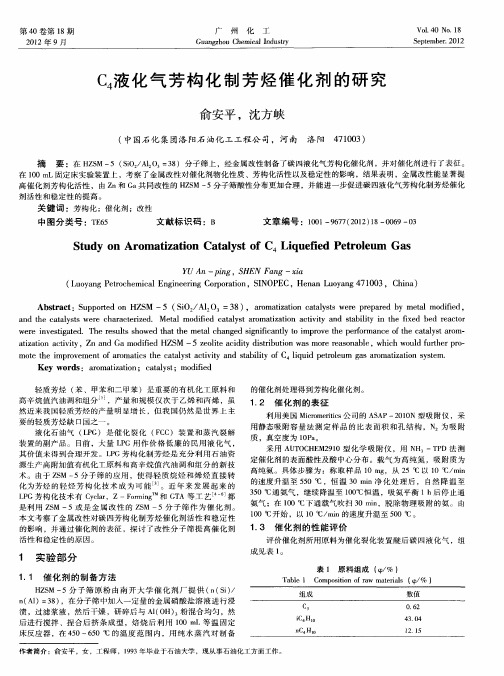
关键 词 :芳构化;催化剂;改性
中 图分类 号 :T 6 E5
文献标 识 1)8 06 — 3 0 1 97 (02 1 — 09 0
S u n Ar m a ia i n Ca ay to t dy o o tz to t l s fC Li ue e t oe q f d Pe r lum a i G s
俞安平 ,沈方峡
( 国石 化 集 团洛 阳石 油化 工 工程公 司 ,河 南 洛 阳 4 10 ) 中 7 0 3 摘 要 :在 H S 5(i A: 3 )分子筛上,经金属改性制备了碳四液化气芳构化催化剂, Z M一 S / I = 8 O O 并对催化剂进行了表征。
在 10m 0 L固定床实验装置上 ,考察 了金属改性对催 化剂物化性质 、芳构化活性 以及稳定性的影响 ,结果表明 ,金属改性能显 著提 高催 化剂芳构化活性 ,由 z n和 G 共 同改性 的 H S 一 a Z M 5分子筛酸性分布更加合理 ,并能进一步促进碳 四液化气芳构化制芳烃催化
轻质芳烃 ( 、甲苯和二 甲苯 )是重要 的有机化 工原料和 苯 高 辛 烷 值 汽 油 调 和 组 分 … ,产 量 和 规 模 仅 次 于 乙烯 和 丙 烯 ,虽 然 近 来 我 国轻 质 芳 烃 的产 量 明 显 增 长 ,但 我 国仍 然 是 世 界 上 主
要 的 轻 质 芳 烃 缺 口国之 一 。 液化石油气 ( P L G)是 催化 裂化 ( C F C)装置 和蒸汽 裂解 装 置 的副 产 品 。 目前 ,大 量 L G 用 作 价 格 低 廉 的 民用 液 化 气 , P 其 价 值 未 得 到 合 理 开发 。L G芳 构 化 制 芳 烃 是 充 分 利 用 石 油 资 P 源 生 产 高 附 加 值 有 机 化 工原 料 和 高 辛 烷 值 汽 油 调 和 组 分 的 新 技 术 。 由于 Z M 一 S 5分 子 筛 的 应 用 ,使 得 轻 质 烷 烃 和 烯 烃 直 接 转 化 为 芳 烃 的 轻 烃 芳 构 化 技 术 成 为 可 能 J 近 年 来 发 展 起 来 的 。 L G芳 构 化 技 术 有 C c r P yl ,Z —F r n 。 和 G A 等 工 艺 _ 都 a o g mi 。 T 4
液化石油气芳构化技术综述

主要通 过催化 重整 工艺 和蒸汽 裂解制 乙烯工 艺生产 B X, 者 T 二
的 主要 原 料 均 为 石 脑 油 。 随 着 我 国 乙烯 工 业 的发 展 , 于 蒸 汽 用 裂 解 制 乙烯 的 石 脑 油 需 求 增 加 , 脑 油 供 应 不 足 , 约 了 B X 石 制 T
料, 芳烃馏分中 B X含量均约为 9 %, 中苯 2 .% ~ 20 、 T 2 其 79 3 .% 甲 苯 4 .% ~ 2 9 二 甲苯 1 .% 一2 .%。B 11 4 . %、 88 18 P公 司于 2 0世纪 8 0年代在苏格兰 G agm uh的炼油厂中建成 了规模为 10 rne ot 00桶/
中图 分类 号 :Q4 ,Q0 T21T 25
文献 标识 码 : A
文章 编 号 :01 97 (02 1 —03 0 10 —6721)1 05 —2
Re iw ft ve o he LPG r m a ia i n Te h lg e A o tz to c no o is
合 成 树 脂 、 成 橡 胶 以 及 各 种 精 细 化 学 品 。B X 中 的 甲 苯 和 二 合 T 甲苯 还 是 生 产 高 辛 烷 值 汽 油 的 重 要 调 和 组 分 , 车 工 业 快 速 发 汽 展使高辛烷值 汽油需求增加 , 加剧 了 B X的供需 矛盾 J 目前 , T 。
HZSM-5分子筛在液化气芳构化反应中的催化性能研究中期报告
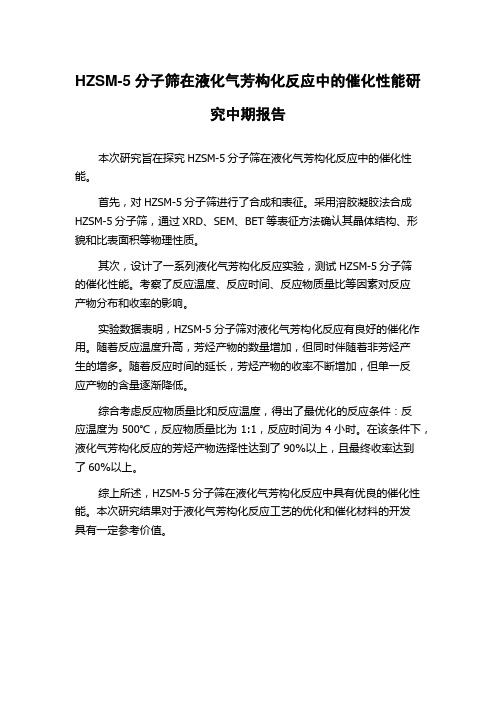
HZSM-5分子筛在液化气芳构化反应中的催化性能研
究中期报告
本次研究旨在探究HZSM-5分子筛在液化气芳构化反应中的催化性能。
首先,对HZSM-5分子筛进行了合成和表征。
采用溶胶凝胶法合成HZSM-5分子筛,通过XRD、SEM、BET等表征方法确认其晶体结构、形貌和比表面积等物理性质。
其次,设计了一系列液化气芳构化反应实验,测试HZSM-5分子筛
的催化性能。
考察了反应温度、反应时间、反应物质量比等因素对反应
产物分布和收率的影响。
实验数据表明,HZSM-5分子筛对液化气芳构化反应有良好的催化作用。
随着反应温度升高,芳烃产物的数量增加,但同时伴随着非芳烃产
生的增多。
随着反应时间的延长,芳烃产物的收率不断增加,但单一反
应产物的含量逐渐降低。
综合考虑反应物质量比和反应温度,得出了最优化的反应条件:反
应温度为500℃,反应物质量比为1:1,反应时间为4小时。
在该条件下,液化气芳构化反应的芳烃产物选择性达到了90%以上,且最终收率达到
了60%以上。
综上所述,HZSM-5分子筛在液化气芳构化反应中具有优良的催化性能。
本次研究结果对于液化气芳构化反应工艺的优化和催化材料的开发
具有一定参考价值。
液化石油气制芳烃研究及应用
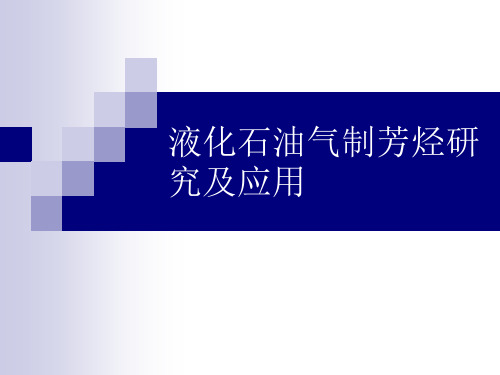
Zn/HZSM-5催化剂上的芳构化反应,虽然已有许 多的报道
但对Zn物种在芳构化中所起的作用、Zn的存在状 态等仍有争议,对金属改性催化剂上芳烃的分布 规律、C6-C9烯烃中间体的形成途径尚未有深入 的研究报道
对此类催化剂上积碳的形成及消除的研究较少, 如何在高温反应条件下抑制Zn的流失,还需要做 进一步的研究
其它工艺轻烃的芳构化工艺还有Mobil公司开发, 以C3~C4烃为原料的Mobil工艺;KTI公司开 发,以C2~C3烃为原料的Pyroform工艺等
有关C1和C2烃类为原料由热力学数据表 明难度较大 ,烷烃向芳烃转化,随着链的变短 而变得不利
甲烷在非氧化条件下直接合成苯,需要很高 的温度才能进行
Cyclar工艺可选用高压和低压两种加工方案
高压方案较低压方案可节省投资 25% ;低压 方案芳烃收率高 ,但催化剂用量要增
Aroforming工艺是IFP和Salutec共同开发 的 ,原料为液化天然气 ,经脱除杂质后 ,分馏 为C3、C4、C5(带凝析油 )
催化剂为含有浸渍金属氧化物助剂的沸石 分子筛
反应器为串联的固定床或移动床 ,带有平衡 两组中间加热器 ,互相切换进行反应和再生
1.3 Z-Forming工艺(1)
Z-Forming工艺是由日本三菱油公司和千代 田公司联合开发的
该工艺与Cyclar工艺不同之处是催化剂采用 具有专利权的金属硅酸盐沸(metallosilicate)
液体产品除C5组分外均为芳烃,因此液体产 品经脱戊烷后,不需芳烃抽提即可得到苯、 甲苯和二甲苯(含乙苯)等产品
C5组分和重芳烃可作为高辛烷值汽油的调 和组分或另作他用
反应器含有叠置式径向流串联的四部分,回 收部分采用深冷分离,可得到95%的氢气
液化气芳构化
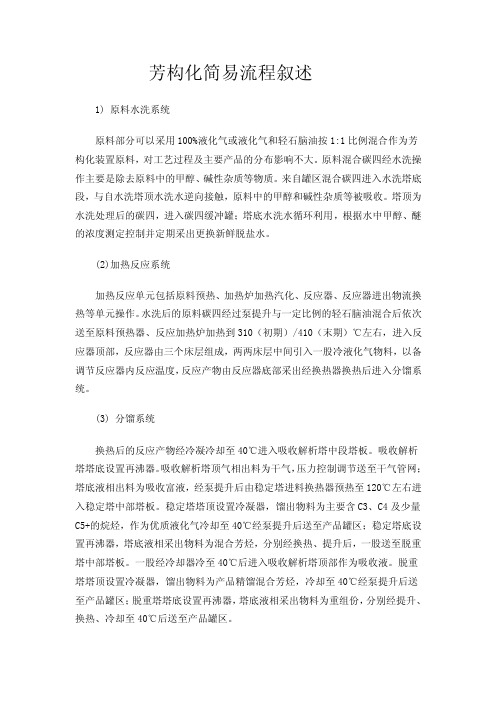
芳构化简易流程叙述1) 原料水洗系统原料部分可以采用100%液化气或液化气和轻石脑油按1:1比例混合作为芳构化装置原料,对工艺过程及主要产品的分布影响不大。
原料混合碳四经水洗操作主要是除去原料中的甲醇、碱性杂质等物质。
来自罐区混合碳四进入水洗塔底段,与自水洗塔顶水洗水逆向接触,原料中的甲醇和碱性杂质等被吸收。
塔顶为水洗处理后的碳四,进入碳四缓冲罐;塔底水洗水循环利用,根据水中甲醇、醚的浓度测定控制并定期采出更换新鲜脱盐水。
(2)加热反应系统加热反应单元包括原料预热、加热炉加热汽化、反应器、反应器进出物流换热等单元操作。
水洗后的原料碳四经过泵提升与一定比例的轻石脑油混合后依次送至原料预热器、反应加热炉加热到310(初期)/410(末期)℃左右,进入反应器顶部,反应器由三个床层组成,两两床层中间引入一股冷液化气物料,以备调节反应器内反应温度,反应产物由反应器底部采出经换热器换热后进入分馏系统。
(3) 分馏系统换热后的反应产物经冷凝冷却至40℃进入吸收解析塔中段塔板。
吸收解析塔塔底设置再沸器。
吸收解析塔顶气相出料为干气,压力控制调节送至干气管网;塔底液相出料为吸收富液,经泵提升后由稳定塔进料换热器预热至120℃左右进入稳定塔中部塔板。
稳定塔塔顶设置冷凝器,馏出物料为主要含C3、C4及少量C5+的烷烃,作为优质液化气冷却至40℃经泵提升后送至产品罐区;稳定塔底设置再沸器,塔底液相采出物料为混合芳烃,分别经换热、提升后,一股送至脱重塔中部塔板。
一股经冷却器冷至40℃后进入吸收解析塔顶部作为吸收液。
脱重塔塔顶设置冷凝器,馏出物料为产品精馏混合芳烃,冷却至40℃经泵提升后送至产品罐区;脱重塔塔底设置再沸器,塔底液相采出物料为重组份,分别经提升、换热、冷却至40℃后送至产品罐区。
(4) 再生系统反应进行一段时间后,随着反应器中催化剂表面结焦量的增加,催化剂表面活性降低,当检测到产品质量不能满足要求时,需将反应器切换出反应系统进行催化剂烧焦再生处理。
C_4液化气中丁烯在纳米ZSM-5沸石上芳构化
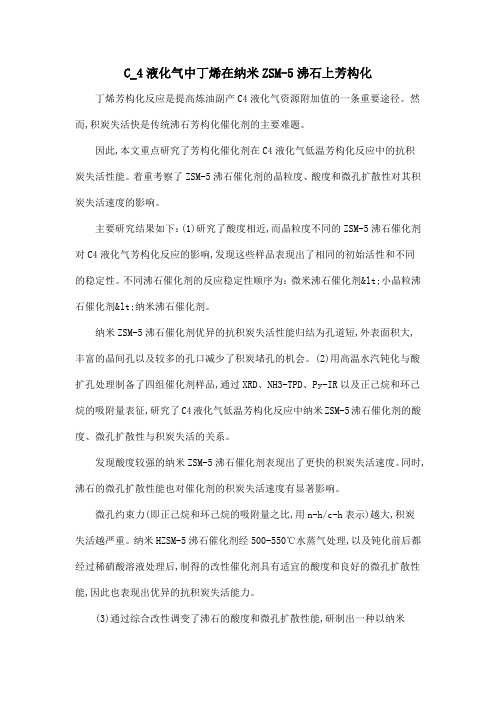
C_4液化气中丁烯在纳米ZSM-5沸石上芳构化丁烯芳构化反应是提高炼油副产C4液化气资源附加值的一条重要途径。
然而,积炭失活快是传统沸石芳构化催化剂的主要难题。
因此,本文重点研究了芳构化催化剂在C4液化气低温芳构化反应中的抗积炭失活性能。
着重考察了ZSM-5沸石催化剂的晶粒度、酸度和微孔扩散性对其积炭失活速度的影响。
主要研究结果如下:(1)研究了酸度相近,而晶粒度不同的ZSM-5沸石催化剂对C4液化气芳构化反应的影响,发现这些样品表现出了相同的初始活性和不同的稳定性。
不同沸石催化剂的反应稳定性顺序为:微米沸石催化剂<小晶粒沸石催化剂<纳米沸石催化剂。
纳米ZSM-5沸石催化剂优异的抗积炭失活性能归结为孔道短,外表面积大,丰富的晶间孔以及较多的孔口减少了积炭堵孔的机会。
(2)用高温水汽钝化与酸扩孔处理制备了四组催化剂样品,通过XRD、NH3-TPD、Py-IR以及正己烷和环己烷的吸附量表征,研究了C4液化气低温芳构化反应中纳米ZSM-5沸石催化剂的酸度、微孔扩散性与积炭失活的关系。
发现酸度较强的纳米ZSM-5沸石催化剂表现出了更快的积炭失活速度。
同时,沸石的微孔扩散性能也对催化剂的积炭失活速度有显著影响。
微孔约束力(即正己烷和环己烷的吸附量之比,用n-h/c-h表示)越大,积炭失活越严重。
纳米HZSM-5沸石催化剂经500-550℃水蒸气处理,以及钝化前后都经过稀硝酸溶液处理后,制得的改性催化剂具有适宜的酸度和良好的微孔扩散性能,因此也表现出优异的抗积炭失活能力。
(3)通过综合改性调变了沸石的酸度和微孔扩散性能,研制出一种以纳米ZSM-5沸石为催化剂母体的DLG-1催化剂,表现出了良好的抗积炭失活性能以及C4液化气中丁烯的低温芳构化性能。
研究了反应条件、C4液化气原料组成、杂质含量以及反应气氛对DLG-1催化剂上C4液化气低温芳构化反应的影响。
发现除了催化剂外,适宜的反应条件、清洁的原料(例如,较低的二烯烃和硫化物含量以及无碱性氮化物)以及临氢反应都对进一步提高催化剂的抗积炭失活性能起到了重要作用。
中国科学院大连化学物理研究所液化气芳构化技术实现工业化
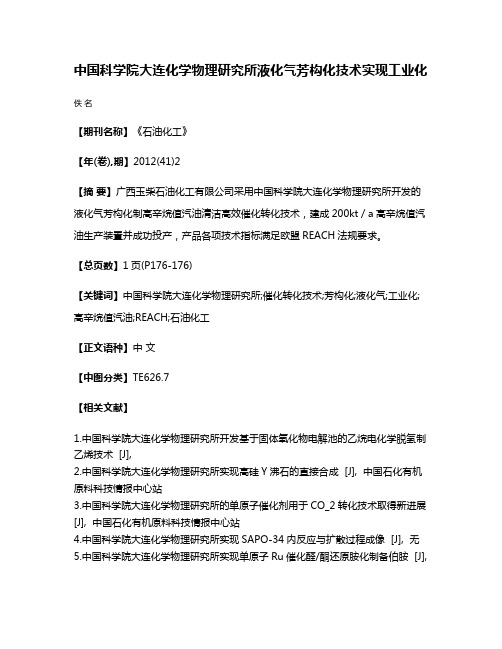
中国科学院大连化学物理研究所液化气芳构化技术实现工业化佚名
【期刊名称】《石油化工》
【年(卷),期】2012(41)2
【摘要】广西玉柴石油化工有限公司采用中国科学院大连化学物理研究所开发的液化气芳构化制高辛烷值汽油清洁高效催化转化技术,建成200kt/a高辛烷值汽油生产装置并成功投产,产品各项技术指标满足欧盟REACH法规要求。
【总页数】1页(P176-176)
【关键词】中国科学院大连化学物理研究所;催化转化技术;芳构化;液化气;工业化;高辛烷值汽油;REACH;石油化工
【正文语种】中文
【中图分类】TE626.7
【相关文献】
1.中国科学院大连化学物理研究所开发基于固体氧化物电解池的乙烷电化学脱氢制乙烯技术 [J],
2.中国科学院大连化学物理研究所实现高硅Y沸石的直接合成 [J], 中国石化有机原料科技情报中心站
3.中国科学院大连化学物理研究所的单原子催化剂用于CO_2转化技术取得新进展[J], 中国石化有机原料科技情报中心站
4.中国科学院大连化学物理研究所实现SAPO-34内反应与扩散过程成像 [J], 无
5.中国科学院大连化学物理研究所实现单原子Ru催化醛/酮还原胺化制备伯胺 [J],
因版权原因,仅展示原文概要,查看原文内容请购买。
中科院科技成果——液化气芳构化生产高辛烷值汽油、调和油和车用汽油燃料
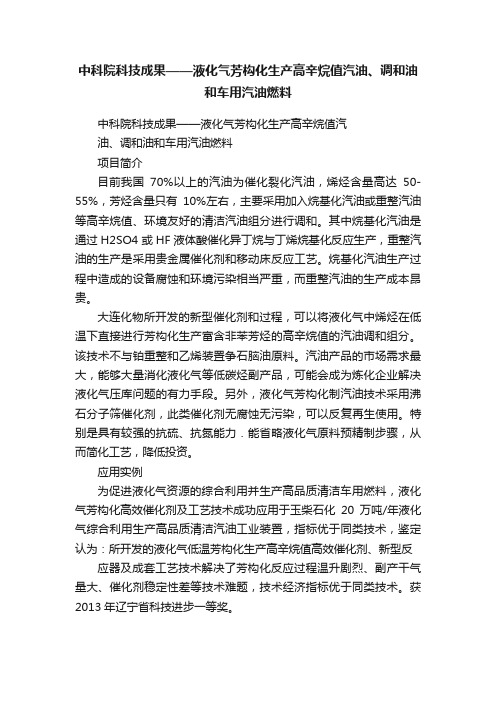
中科院科技成果——液化气芳构化生产高辛烷值汽油、调和油
和车用汽油燃料
中科院科技成果——液化气芳构化生产高辛烷值汽
油、调和油和车用汽油燃料
项目简介
目前我国70%以上的汽油为催化裂化汽油,烯烃含量高达50-55%,芳烃含量只有10%左右,主要采用加入烷基化汽油或重整汽油等高辛烷值、环境友好的清洁汽油组分进行调和。
其中烷基化汽油是通过H2SO4或HF液体酸催化异丁烷与丁烯烷基化反应生产,重整汽油的生产是采用贵金属催化剂和移动床反应工艺。
烷基化汽油生产过程中造成的设备腐蚀和环境污染相当严重,而重整汽油的生产成本昂贵。
大连化物所开发的新型催化剂和过程,可以将液化气中烯烃在低温下直接进行芳构化生产富含非苯芳烃的高辛烷值的汽油调和组分。
该技术不与铂重整和乙烯装置争石脑油原料。
汽油产品的市场需求最大,能够大量消化液化气等低碳烃副产品,可能会成为炼化企业解决液化气压库问题的有力手段。
另外,液化气芳构化制汽油技术采用沸石分子筛催化剂,此类催化剂无腐蚀无污染,可以反复再生使用。
特别是具有较强的抗硫、抗氮能力.能省略液化气原料预精制步骤,从而简化工艺,降低投资。
应用实例
为促进液化气资源的综合利用并生产高品质清洁车用燃料,液化气芳构化高效催化剂及工艺技术成功应用于玉柴石化20万吨/年液化气综合利用生产高品质清洁汽油工业装置,指标优于同类技术,鉴定认为:所开发的液化气低温芳构化生产高辛烷值高效催化剂、新型反应器及成套工艺技术解决了芳构化反应过程温升剧烈、副产干气量大、催化剂稳定性差等技术难题,技术经济指标优于同类技术。
获2013年辽宁省科技进步一等奖。
20万吨/年液化气芳构化工业装置。
液化气芳构化简单原理
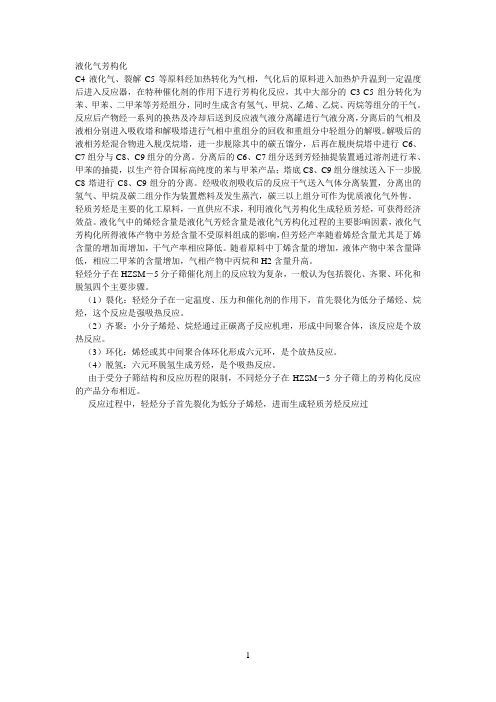
液化气芳构化C4液化气、裂解C5等原料经加热转化为气相,气化后的原料进入加热炉升温到一定温度后进入反应器,在特种催化剂的作用下进行芳构化反应,其中大部分的C3-C5组分转化为苯、甲苯、二甲苯等芳烃组分,同时生成含有氢气、甲烷、乙烯、乙烷、丙烷等组分的干气。
反应后产物经一系列的换热及冷却后送到反应液气液分离罐进行气液分离,分离后的气相及液相分别进入吸收塔和解吸塔进行气相中重组分的回收和重组分中轻组分的解吸。
解吸后的液相芳烃混合物进入脱戊烷塔,进一步脱除其中的碳五馏分,后再在脱庚烷塔中进行C6、C7组分与C8、C9组分的分离。
分离后的C6、C7组分送到芳烃抽提装置通过溶剂进行苯、甲苯的抽提,以生产符合国标高纯度的苯与甲苯产品;塔底C8、C9组分继续送入下一步脱C8塔进行C8、C9组分的分离。
经吸收剂吸收后的反应干气送入气体分离装置,分离出的氢气、甲烷及碳二组分作为装置燃料及发生蒸汽,碳三以上组分可作为优质液化气外售。
轻质芳烃是主要的化工原料,一直供应不求,利用液化气芳构化生成轻质芳烃,可获得经济效益。
液化气中的烯烃含量是液化气芳烃含量是液化气芳构化过程的主要影响因素,液化气芳构化所得液体产物中芳烃含量不受原料组成的影响,但芳烃产率随着烯烃含量尤其是丁烯含量的增加而增加,干气产率相应降低。
随着原料中丁烯含量的增加,液体产物中苯含量降低,相应二甲苯的含量增加,气相产物中丙烷和H2含量升高。
轻烃分子在HZSM-5分子筛催化剂上的反应较为复杂,一般认为包括裂化、齐聚、环化和脱氢四个主要步骤。
(1)裂化:轻烃分子在一定温度、压力和催化剂的作用下,首先裂化为低分子烯烃、烷烃,这个反应是强吸热反应。
(2)齐聚:小分子烯烃、烷烃通过正碳离子反应机理,形成中间聚合体,该反应是个放热反应。
(3)环化:烯烃或其中间聚合体环化形成六元环,是个放热反应。
(4)脱氢:六元环脱氢生成芳烃,是个吸热反应。
由于受分子筛结构和反应历程的限制,不同烃分子在HZSM-5分子筛上的芳构化反应的产品分布相近。
C4液化气非临氢低温芳构化反应的研究

大连理工大学硕士学位论文C4液化气非临氢低温芳构化反应的研究姓名:王中乾申请学位级别:硕士专业:能源化工指导教师:郭洪臣20090601大连理工大学硕士学位摘要石油炼制过程和石油化工过程中副产大量的C4液化气。
长期以来这些C4液化气作为廉价的燃气使用,综合利用率低,浪费了石油资源。
将液化气转化成高附加值产品不仅能带来经济效益而且还提高了石油资源的综合利用率。
C4液化气低温芳构化制高辛烷值汽油组分,工艺过程相对简单,成本低,是一条值得重视的C4LPG 利用途径。
本论文主要在前期纳米ZSM.5分子筛工作基础之上制得DLG.2催化剂,研究了反应条件和原料中杂质对低温芳构化反应的影响。
发现:在非临氢条件下,C4液化气在 DLG.2系列催化剂上进行芳构化反应时,可得到较高的液体收率(45%以上,并且液体产物中芳烃含量较高(液体中芳烃含量64%。
反应温度和进料空速对液收有较大影响,但反应压力影响较小。
催化剂DLG.2.30在非临氢下反应最优条件为:380℃,0.5MPa 和WHSVc4LI,G=0.83h"1。
C4液化气原料中的二甲醚(DME对芳构化反应性能有明显的不利影响。
原料中的二甲醚(DME能JJI:I速催化剂的失活。
二甲醚含量越高,催化剂失活速度越快。
最后,本文在最佳反应条件下,对DLG.2.30进行了1000h的长运转稳定性考察。
结果表明:DLG.2.30具有相对稳定的液体收率,反应1000h后有芳构化活性。
对液体产物进行馏分分析、体积组成测定和实际测定辛烷值,结果发现:液体产物各项指标均分别达到了GBl7930.2006(III类,93撑的规定。
实测得的研究法辛烷值(RON达到95.8, 马达法辛烷值(MON达到83.4。
关键词:纳米ZSM-5沸石;液化气;芳构化;汽油;反应条件;二甲醚C4液化气非临氢低温芳构化反应的研究C4LPG Low—temperature Aromatization without Using HE as Carrier Gas AbstractC4Liquefied Petroleum Gas(C4LPGis a main by—product in the petroleum refineries and petrochemical industries.It has long been used as low-value fuel,which wastes a hugeamount of our imported crude oil.The transformation of C4LPG into value.added gasolineproduct can not only bring economic benefit,but alSO raise the utilization rate of precious petroleum resource.To obtain gasoline via the aromatization of C4LPG is a simple and cost-effective.It displays good application prospect.The study mainly focuses on the influences of reaction conditions and the impurity of C4 LPG on the lOW temperature aromatization of C4LPG over modified nano.sized ZSM.5 zeolite catalyst DLG.2which is prepared recently.It is found that:the aromaization of C4 LPG over DLG-2is featured by high liquid products yield(45,叭一%and high arenes contents in liquid products(64,吼-%.Both temperature and Feed Velocity have notably influences on the aromatization of C4LPG..The reaction pressure has little influence on the aromatizationof C4LPG.The optimum reaction conditions for DLG.2.30catalyst are 380℃,0.5MP 巩 WHSVC4LPG=0.83h~,in the absence of H2carrier gas.11le influence of dimethyl ether(DMEin C4LPG feedstock on the catalyst performance Was studied.It is found that,DME in C4LPG feed stock Can strongly worse the performance of aromatization catalyst.DME in C4LPG feedstock accelerates catalyst deactivation.,nlc more DME in the C4LPG feedstock,the faster the catalyst deactive.For the reason,it iS better to nse DME free C4LPG feedstock.The durability of catalyst DLG.2.30Was studied under the optimum conditions.It iS found that DLG-2-30has a relatively stable liquid yield.Fuel property evaluation indicated that.the gasoline product generated by the aromatization of C4LPG over DLG-2-30has research octane number of 95.8(RON,and motor octane number of 83.4(MON.It carl meet the GB 17930—2006(I/I,93撑standard.Key Words:nano.-sized ZSM.-5zeolite;C4LPG;aromatizationgasoline;reactiong conditions;dimethyl ether(DME大连理工大学硕士学位论文大连理工大学学位论文版权使用授权书本人完全了解学校有关学位论文知识产权的规定,在校攻读学位期间论文工作的知识产权属于大连理工大学,允许论文被查阅和借阅。
液化气芳构化生产芳烃技术及工业应用进展

剂芳构化的主要反应条件。 综述 了国内外典 型的液化气芳构化工艺技术 , 介绍 了每种工艺技术的工业应用情况 , 并展望 了液化气芳构化技术的发展趋势 。
关 键 词 :液 化 气 ;芳 构 化 ;反 应 机 理 文献标识码 : A 文章 编 号 : 17 — 4 0( 0 2) 6 0 2- 3 6 10 6 2 1 0 - 6 9 0 中 图分 类号 :T 1 Q4 3
Ab t a t T es u c n p l ai n o G r i l t d c d Re ci n me h n s o P ao t ai n wa sr c : h o r e a d a p i t f c o LP we esmp y i r u e . a t c a im fL G r mai t s n o o z o d s u s d.T ee f c f i e c in c n i o so r m ai ai n p ro m a c f h a ay t si t d c d T p c l ic se h fe t man r a t o d t n n a o t t e f r n eo t ec t l s wa r u e . y ia o o i z o n o
f . i o i gS i u i e s y Lio i g F s u 0 , Ch n  ̄ 1 L a n n h h aUn v r i , a n n u h n 1 3 01 t 1 i a
2 Ch n a q u Co t c i g& En i e r g Co p r t n Lio i g Br n h,Lio i gF s u 0 6 Ch n ) . i aHu n i n r t a n gn e i r o ai a n n a c n o a nn u h n 13 0 , 1 ia
中科院科技成果——液化气芳构化生产BTX芳烃和车用汽油燃料
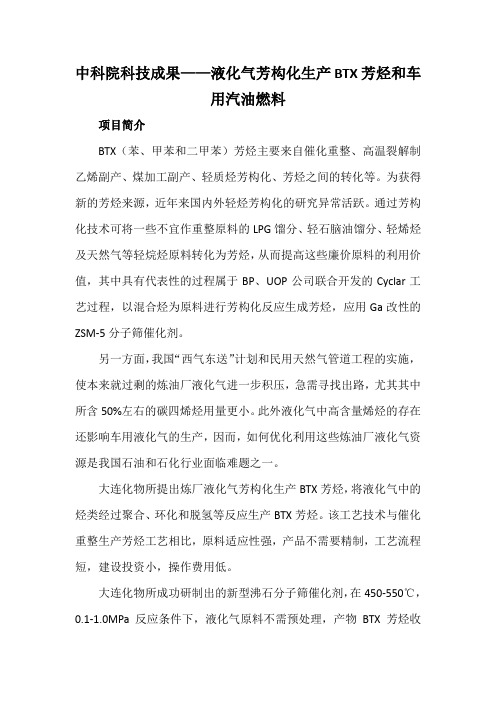
中科院科技成果——液化气芳构化生产BTX芳烃和车
用汽油燃料
项目简介
BTX(苯、甲苯和二甲苯)芳烃主要来自催化重整、高温裂解制乙烯副产、煤加工副产、轻质烃芳构化、芳烃之间的转化等。
为获得新的芳烃来源,近年来国内外轻烃芳构化的研究异常活跃。
通过芳构化技术可将一些不宜作重整原料的LPG馏分、轻石脑油馏分、轻烯烃及天然气等轻烷烃原料转化为芳烃,从而提高这些廉价原料的利用价值,其中具有代表性的过程属于BP、UOP公司联合开发的Cyclar工艺过程,以混合烃为原料进行芳构化反应生成芳烃,应用Ga改性的ZSM-5分子筛催化剂。
另一方面,我国“西气东送”计划和民用天然气管道工程的实施,使本来就过剩的炼油厂液化气进一步积压,急需寻找出路,尤其其中所含50%左右的碳四烯烃用量更小。
此外液化气中高含量烯烃的存在还影响车用液化气的生产,因而,如何优化利用这些炼油厂液化气资源是我国石油和石化行业面临难题之一。
大连化物所提出炼厂液化气芳构化生产BTX芳烃,将液化气中的烃类经过聚合、环化和脱氢等反应生产BTX芳烃。
该工艺技术与催化重整生产芳烃工艺相比,原料适应性强,产品不需要精制,工艺流程短,建设投资小,操作费用低。
大连化物所成功研制出的新型沸石分子筛催化剂,在450-550℃,0.1-1.0MPa反应条件下,液化气原料不需预处理,产物BTX芳烃收
率>50%,液化气中烯烃<5%,催化剂单程寿命20-30天,总寿命2年以上。
目前完成了分子筛和催化剂的工业放大(100公斤级),拟进行工业化试生产。
液化石油气芳构化技术一览
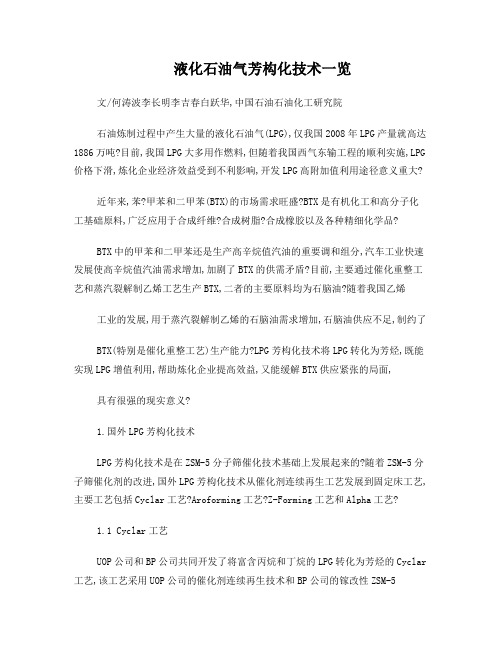
液化石油气芳构化技术一览文/何涛波李长明李吉春白跃华,中国石油石油化工研究院石油炼制过程中产生大量的液化石油气(LPG),仅我国2008年LPG产量就高达1886万吨?目前,我国LPG大多用作燃料,但随着我国西气东输工程的顺利实施,LPG 价格下滑,炼化企业经济效益受到不利影响,开发LPG高附加值利用途径意义重大?近年来,苯?甲苯和二甲苯(BTX)的市场需求旺盛?BTX是有机化工和高分子化工基础原料,广泛应用于合成纤维?合成树脂?合成橡胶以及各种精细化学品?BTX中的甲苯和二甲苯还是生产高辛烷值汽油的重要调和组分,汽车工业快速发展使高辛烷值汽油需求增加,加剧了BTX的供需矛盾?目前,主要通过催化重整工艺和蒸汽裂解制乙烯工艺生产BTX,二者的主要原料均为石脑油?随着我国乙烯工业的发展,用于蒸汽裂解制乙烯的石脑油需求增加,石脑油供应不足,制约了BTX(特别是催化重整工艺)生产能力?LPG芳构化技术将LPG转化为芳烃,既能实现LPG增值利用,帮助炼化企业提高效益,又能缓解BTX供应紧张的局面,具有很强的现实意义?1.国外LPG芳构化技术LPG芳构化技术是在ZSM-5分子筛催化技术基础上发展起来的?随着ZSM-5分子筛催化剂的改进,国外LPG芳构化技术从催化剂连续再生工艺发展到固定床工艺,主要工艺包括Cyclar工艺?Aroforming工艺?Z-Forming工艺和Alpha工艺?1.1 Cyclar工艺UOP公司和BP公司共同开发了将富含丙烷和丁烷的LPG转化为芳烃的Cyclar 工艺,该工艺采用UOP公司的催化剂连续再生技术和BP公司的镓改性ZSM-5沸石催化剂配方?Cyclar工艺由反应器?催化剂再生单元和产物分离装置三部分组成?与连续催化剂再生铂重整装置类似,四个径向绝热反应器自上而下叠置排列,催化剂依靠重力从上至下依次经过各个反应器,从最下面的反应器出来的催化剂送到再生器再生,再生催化剂再进入第一个反应器?由于反应吸热,从上一反应器出来的物料经预热后进入下一反应器进行反应?Cyclar工艺的反应温度为482~537℃?产物组成受原料种类的影响,以丙烷为原料,芳烃收率?氢气收率和干气收率分别为63.1%?5.9%和31%;以丁烷为原料,则分别为65.9%?5.2%和28.9%?无论以丙烷还是丁烷为原料,芳烃馏分中BTX含量均约为92%,其中苯27.9%~32.0%?甲苯41.1%~42.9%?二甲苯18.8%~21.8%?BP公司于20世纪80年代在苏格兰Grangemouth的炼油厂中建成了规模为1000桶/开工日的Cyclar工艺试验装置?1999年末在沙特阿拉伯建成了第一个120万吨/年原料规模的Cyclar工业装置,三苯产量达到78.7万吨/年(苯25.2万吨/年,甲苯35.8万吨/年,混合二甲苯17.7万吨/年)?Cyclar工艺由于采用移动床反应器和催化剂连续再生技术,投资费用高,操作复杂?1.2 Aroforming工艺IFP公司和Salutec公司共同开发的Aroforming工艺适用于轻石脑油和LPG 等原料的芳构化?催化剂为金属氧化物改性的择形分子筛,芳构化反应在等温固定床管式反应器上进行,当催化剂失活时,将反应切换到另一反应器进行,再对原反应器中的催化剂进行再生处理?LPG芳构化产物组成与Cyclar工艺相近?由于采用固定床管式反应器,Aroforming工艺较Cyclar工艺简单,但催化剂单程运转周期仅12h,需频繁再生处理?1.3 Z-Forming工艺日本Mitsubishi石油公司和Chiyoda公司联合开发了以LPG和轻石脑油生产BTX的Z-Forming技术?该工艺采用的催化剂为Ⅷ族?ⅡB和ⅢB族元素的金属硝酸盐改性的沸石,有较好的活性和选择性?该工艺采用4台固定床反应器,反应器串联排列?因反应吸热,反应器之间设加热炉?反应器入口温度为500~600℃,反应压力为0.3~0.7MPa,液时空速为0.5~2.0h-1?反应产物为芳烃?高纯度氢气和燃料气,具体组成随原料种类略有不同,大体为氢气2.8%~3.4%?燃料气34.1%~42.7%?芳烃53.9%~63.1%(其中苯?甲苯和二甲苯分别约为15%?20%和10%)?芳烃中由于所使用的杂原子沸石催化剂抗中毒能力不够,需对原料进行加氢精制,造成投资增加,而且,催化剂的单程运转周期短,不足十天?1.4 Alpha工艺日本Sanyo石油公司开发了将富含烯烃(30%~80%)的轻烃转化为芳烃的Alpha 工艺?该工艺使用的Zn改性ZSM-5分子筛催化剂预先在650℃下进行水热处理,能抑制反应中Zn流失和催化剂结焦,提高芳烃选择性和催化剂稳定性?反应在两组并列的固定床切换反应器上进行,经预热的原料进入其中的一个反应器进行绝热反应,所得产物经与原料换热后进入分离系统?Alpha工艺的反应温度500~550℃,反应压力为0.2~0.5MPa,质量空速2~4h-1,芳烃收率为50%~65%,芳烃分布为苯14%?甲苯44%?二甲苯30%?C9+芳烃13%?1993年在日本冈山水岛建成一套3500桶/开工日的Alpha工艺工业装置?Alpha工艺所用催化剂的单程运转周期较上述工艺明显提高,可达数天至数十天?2 国内液化石油气芳构化技术近年来,国内LPG等轻烃芳构化技术取得了显著进步,数项LPG芳构化技术实现了工业化?目前,国内液化石油气芳构化技术主要有洛阳石化工程公司开发的GTA工艺和大连理工大学开发的Nano-form-ing工艺?2.1 GTA工艺GTA工艺所用的富含烯烃的催化裂化混合C4馏分原料,在通常的芳构化过程中生焦能力强,催化剂单程寿命短?由于烯烃芳构化反应为放热反应,反应过程中取热困难?GTA工艺首先用金属硝酸盐溶液浸渍HZSM-5分子筛,对催化剂的酸性进行调变,平衡稳定性与活性的关系;另外,GTA工艺采用科学的催化剂装填方式和合理的取热方式,使芳构化反应能够平稳进行?GTA工艺采用固定床反应器?反应-再生生产方式?反应产物由富气和液体产物组成,在吸收稳定系统内富气和液体逆向接触后在稳定塔内使气液充分分离?在反应温度530℃,进料空速0.25h-1,反应压力0.10MPa的条件下,催化裂化C4馏分GTA芳构化得到的产物组成为:干气19.96%,LPG24.17%,液体产物46.4%?液体产物中苯?甲苯?二甲苯的含量分别为16.69%?甲苯43.71%和24.76%?2.2 Nano-forming工艺传统芳构化工艺采用的微米级大晶粒ZSM-5沸石催化剂抗积炭能力弱,产物中干气生成量大,催化剂单程运转周期短等问题严重阻碍了芳构化技术的工业应用?近年来,郭洪臣等利用纳米级ZSM-5分子筛催化剂优异的抗积炭失活能力,开发出Nano-forming轻烃芳构化工艺?该工艺采用固定床反应器,反应温度为500~600℃,原料预精制后进行反应,主产品为苯?甲苯和二甲苯,同时副产氢气和C9+重芳烃?同己有的芳构化工艺相比,Nano-forming工艺由于采用纳米ZSM-5沸石分子筛催化剂,催化剂的抗积炭能力显著增强,单程运转周期不低于1个月,避免了催化剂的频繁再生,同时,催化剂的使用寿命得到延长,可达2年,降低了操作成本?前述LPG芳构化技术的反应温度普遍较高(500~600℃),产物中干气含量高,原料利用率低?为了提高芳构化工艺的经济性,石油化工研究院与大连理工大学合作,在较低的温度下(360~410℃)和装有纳米HZSM-5沸石分子筛催化剂的固定床反应器中通过芳构化和烷基化反应将液化石油气中的丁烯完全转化,生产高辛烷值汽油组分,同时将联产的丙烷和丁烷作为优质乙烯裂解原料?在200mL 固定床模试装置上试验表明,催化剂单程运转周期超过1000h,产物中汽油组分的收率为30.65%,其中苯的含量不大于1.3%,研究法辛烷值和马达法辛烷值分别为98.8和87.9,是优质的高辛烷值汽油调合组分?焦炭和干气的产率之和不大于2%,显示出良好的应用前景?3 结语总体来说,经过半个多世纪的发展,LPG芳构化技术得到了长足的发展,形成了多套工业化技术?催化剂寿命提高,实现了从移动床到固定床的转变,经济性得到了提高?具体来说,上述工业化技术在原料适应性?芳烃收率和芳构化产物组成等方面存在差异?为进一步提高LPG芳构化技术的经济性,应在继续重视开发长寿命催化剂,减少催化剂再生频率的同时,注重副产物综合利用和芳构化产物选择性研究,以便充分利用LPG资源,以及能在生产化工原料芳烃时,提高苯和二甲苯的选择性,在生产高辛烷值汽油调和组分时,提高甲苯和二甲苯的选择性?继续阅读。
- 1、下载文档前请自行甄别文档内容的完整性,平台不提供额外的编辑、内容补充、找答案等附加服务。
- 2、"仅部分预览"的文档,不可在线预览部分如存在完整性等问题,可反馈申请退款(可完整预览的文档不适用该条件!)。
- 3、如文档侵犯您的权益,请联系客服反馈,我们会尽快为您处理(人工客服工作时间:9:00-18:30)。
绝热移动床 Ga /MFI 500 ~600 ~0畅4
等温固定床
绝热固定床
改性 HZSM -5 改性纳米 ZSM -5
450 ~540
500 ~600
0畅1 ~0畅4
0畅3 ~0畅5
空速 ( WHSV) /h -1
原料 产品方案 BTX 收率 /% 再生方式 再生周期
~4
丙烷、丁烷 BTX ~60
连续再生 连续再生
48%、 5%、 0畅5%。 催化剂再生部分与 GAT -I 工艺基本相似。 也是采用氮气
中配空气的方式对失活催化剂进行烧焦再生, 并设置再生气干 燥及脱硫器。 再生系统是一个闭路循环系统, 再生气循环使 用。 开始进行烧焦作业时, 需对系统进行热氮气吹扫, 当循环 氮气中氧含量小于 0畅5%( φ) 时, 然后配比一定量的空气进行 烧焦。 当反应器没有温升时, 烧焦再生过程结束。
摘 要: 液化气芳构化生产 BTX 具有较大的经济效益。 工业应用的液化气芳构化技术主要有 Cyclar 工艺、 GTA -I 工艺、
Nano -forming 工艺三种。 通过比较研究这三种工艺的有关工艺操作参数及技术经济指标, 液化气深加工企业在选择液化气芳构化 技术时, 需结合企业自身情况, 建议采用 Cyclar 工艺或者 Nano -forming 工艺。
~0畅3
~0畅5
富含烯烃液化气 富含烯烃液化气
BTX
BTX
~49 反应器切换
~48 注
副产液化气回炼
副产液化气 不回炼
副产液化气 不回炼
设备投资
高
低
低
规模效应 /
( 万吨 /年)
>40
<20
<20
5 结 论
通过研究, Cyclar 工艺与 Nano -forming 工艺具有一定的优 势。 对于液化气来源比较困难的企业 , 建议采用 Cyclar 工艺, 使 液化气原料中的丁烷组分也可以得到利用, 而且原料也不需要 进行提纯处理, 但是由于 Cyclar 工艺反应再生系统复杂, 投资加 大, 一般适用于大型装置; 对于液化气来源比较容易, 或者丁烷 有其他利用途径的企业, 建议采用 Nano -forming 工艺, 该工艺 具有操作周期相对长、 投资低等优点。 GTA -I 工艺来源于劣质 汽油改质技术, 在液化气芳构化生产 BTX 方面应用不多。
第 42 卷第 16 期 2014 年 8 月
生产技术
广 州 化 工 Guangzhou Chemical Industry
液化气芳构化工艺研究
Vol畅42 No畅16 Aug畅2014
吕绍毛1 , 蒋 静2 , 李 季1 , 李菲洋1
(1 中国石油集团东北炼化工程有限公司锦州设计院, 辽宁 锦州 121001; 2 锦州市财经学校, 辽宁 锦州 121001)
关键词: 液化气; 芳构化; 苯; 甲苯; 二甲苯
中图分类号: TE65 文献标志码: B 文章编号: 1001 -9677(2014)016 -0128 -02
Technology Research for LPG Aromatization
LV Shao -mao1 , JIANG Jing2 , LI Ji1 , LI Fei -yang1 (1 Northeast Refining & Chemical Engineering Co 畅, Ltd畅, CNPC, Jinzhou Design Institute , Liaoning Jinzhou 121001; 2 Jinzhou School of Finance and Economics , Liaoning Jinzhou 121001, China)
催化剂再生部分采用氮气中配空气的方式对失活催化剂进 行烧焦再生。 由于再生气需要干燥及脱硫, 因而再生部分设置 再生气干燥及脱硫器各一台。 再生系统是一个闭路循环系统, 再生气循环使用。 再生时再生系统中应充满氮气, 并补进一定 量的空气, 以保证再生气的氧含量。 再生气干燥剂在使用一段 时期后需要再生以脱除干燥剂吸附的水分。 再生气脱硫剂的更 换时间为两年, 装置运行两年后将其卸出更换新脱硫剂。
表 1 常见液化气芳构化技术比较 Table 1 The compare of LPG aromatization technology
工艺方法
Cyclar
GTA -I
Nano -forming
技术来源
BP /UOP
洛阳石化 工程研究院
大连理工大学
反应器类型 催化剂
反应温度 /℃ 反应压力 /MPa
最早工业化的液化气芳构化技术是 Cyclar 工艺。 1983 年英 国石油公司 (BP) 及 UOP 共同开发成功, 采用该工艺的 4 万 吨 /年工业示范装置于 1989 年 9 月在苏格兰开工, 第一套 40 万 吨 /年工业化装置于 1990 年在同地投产。 Cyclar 工艺是将烷烃 ( 主要是丙烷及丁烷混合物) 选择性地转化为高附加值 BTX, 原料烷烃首先要经过脱氢反应生产烯烃, 然后烯烃进一步转化 成芳烃。 Cyclar 工艺反应再生系统与 UOP 公司的石脑油铂重整 工艺反 应 再 生 系 统 基 本 相 同。 Cyclar 工 艺 操 作 温 度 500 ~ 600 ℃, 操作压力 0畅4 MPa, 质量空速 4 h -1 左右[4] 。 反应生成 物中氢气、 干气、 BTX、 重芳烃、 烧焦损失质量分率分别大约 7%、 27%、 60%、 5%、 1畅0%。 由于脱氢反应需要较高的反应 温度以提高反应速度, 导致较多烃类发生裂解生成干气, 因此 Cyclar 工艺原料一次利用率低, 一般需将副产的低烯烃含量液 化气回炼, 以提高原料液化气的利用率[5] 。 由于应用了移动床 反应器、 催化剂连续再生和副产液化气回炼等技术, 芳烃收率 较高, 造成建设投资高, 因此该工艺比较适合于大规模装置。
Key words: LPG; aromatization; benzene; toluene; xylene
苯、 甲苯、 二甲苯 ( BTX) 是重要的 基 础 化 工 原 料。 目 前 BTX 主要来源于石脑油铂重整工艺和裂解制乙烯工艺。 由于我
1 Cyclar 工艺
国石脑油芳烃潜含量低, 石脑油铂重整装置提供 BTX 数量有 限; 裂解制乙烯装置副产 BTX 少, 同时由于原料轻质化现象日 趋加剧, BTX 产率越来越低。 近年来, 我国合成纤维、 合成树 脂、 合成橡胶等行业快速发展, 对 BTX 的需求快速增长, 每年 需进口大量 BTX 以满足国内市场需求。
4 液化气芳构化技术比较
近年来, 我国西气东输工程顺利实施, 页岩气及煤层气行 业快速发展, 天然气成为燃气重要来源, 大量碳四不再作为燃 气使用, 碳四高附加值利用成为当务之急。 液化气芳构化技 术, 既是一种碳四高附加值利用方案, 也能为市场提供紧缺的 BTX, 具有一定的市场前景与经济效益[10] 。 由于液化气芳构化 技术种类繁多, 各技术区别较大, 碳四加工企业需结合自身条 件, 选择适合自身条件的液化气芳构化技术。 表 1 分别列举了 Cyclar 工艺、 GTA -I 工艺、 Nano -forming 工艺三种工艺参数, 包括操作温度、 操作压力、 BTX 收率、 建设投资、 生产周期等 方面。
近些年, 轻烃芳构化 (液化气、 轻石脑油、 凝析油等芳构 化) 生产 BTX 或高辛烷值汽油调合组分的研究与应用十分广 泛, 我国相继建成投产的轻烃芳构化装置超过 10 套。 与轻石 脑油芳构化生产高辛烷值汽油调合组分相比, 液化气芳构化生 产 BTX 具有更高的经济效益, 因此相应的研究与应用也更加深 入。
Abstract: Aromatization of LPG producing BTX had great economic benefits 畅There were three main aromatization technologies of LPG applied in industry , including the Cyclar process , the GTA -I process, and the Nano -forming process畅Through the comparative study of the three processes about the operation parameters and economic -technical index, the enterprises should consider the LPG process condition when select aromatization technology , and the cyclar process or nano -forming process maybe more suitable畅
3 Nano -forming 工艺
Nano -forming 液化气芳构化工艺由大连理工大学开发, 首 套 10 万吨 /年工业化装置已经于 2006 年在山东淄博建成投产。 研究表明分子筛晶粒大小对积碳有较大的影响, 大连理工大学 开发出的纳米分子筛催化剂, 比传统微米分子筛具有优越的抗 积炭失活能力, 催化剂单程连续运转周期可达 30 天以上[8] 。
作者简介: 吕绍毛 (1982 -) , 男, 工程师, 主要从事石油化工工程设计。
第 42 卷第 16 期
吕绍毛, 等: 液化气芳构化工艺研究
129
组份。 2005 年, 在 GAP 工艺的基础上, 开发出 GTA -I 工艺, 用于将富含烯烃液化气转化成 BTX, 并有多套工业化装置采用 该技术建成投产。 GTA -I 工艺采用两组反应器, 每组为 2 台 绝热式固定床反应器, 一共 4 台反应器。 每组反应器段间由加 热炉补充热量, 当催化剂活性降低时把原料切入另外一组反应 器, 并对失活催化剂进行烧焦再生。 两组反应器切换操作, 使 整个操作呈连续状态。 反应再生部分设置 3 台加热炉, 分别是 反应进料加热炉、 反应器段间加热炉、 烧焦再生加热炉。 反应 器操作温度为 450 ~540 ℃左右。 操作压力 0畅1 ~0畅4 MPa 左右, 质量空速 0畅3 h -1 左右[6] , 反应生成物中氢气、 干气、 低烯烃 含量液 化 气、 BTX、 重 芳 烃、 烧 焦 损 失 质 量 分 率 分 别 大 约 1畅8%、 16畅1%、 31畅5%、 49%、 1畅1%、 0畅5%。 GTA -I 工 艺 采用金属改性 HZSM -5 分子筛催化剂, 催化剂使用寿命 2 年 以上, 反应再生切换周期大约 10 天[7] 。