工艺知识芳构化
芳构化装置工艺介绍

芳构化装置一、装置简介芳构化装置,主要原料混合碳四液化气,产品有轻芳烃、重芳烃,民用液化气等。
原料混合碳四液化气,通过原料加热炉加热后,在反应器内与催化剂接触,经过低聚、环化,脱氢芳构化反应生成粗芳烃混合物,经过吸收稳定系统分离成合格的民用液化气和混合芳烃,再通过分馏分离成轻芳和碳9以上重芳烃。
装置区共有油、气罐16台,水储罐2台,其中地下密闭排放罐1台,机泵20台套。
为了防止污染环境和对操作人员造成损害,装置区所有排放的有机液体均排往密闭排放罐,然后根据情况再进行处理和排放。
二、工艺原理反应部分:轻烃芳构化的机理十分复杂。
一般认为,轻烃在分子筛的酸中心上芳构化反应时经历下列步骤:a)通过在酸中心上发生化学吸附生成正碳离子得到活化;b)正碳离子进一步脱氢和裂解生成乙烯、丙烯、丁烯和戊烯。
这些小烯烃是芳烃分子的建筑单元。
这步反应属于吸热反应;c)小烯烃分子在B酸中心上低聚(二聚、三聚)生成C6-C8烯烃,后者再通过异构化和环化生成芳烃前体(带6元环的前体)。
这步反应属于强放热反应;d)芳烃前体在L酸中心上通过脱氢生成苯、甲苯和C8芳烃等。
这步反应属于吸热反应。
在上述反应中,原料在酸中心上生成正碳离子的步骤最为关键。
它决定了芳构化反应的活性和选择性。
C3-C8之间的轻烃分子都可以在催化剂的酸中心上通过脱氢和裂解生成乙烯、丙烯、丁烯和戊烯。
当反应温度和催化剂的酸度相同时,从不同碳数的轻烃原料出发,可以得到具有同样热力学平衡分布的乙烯、丙烯、丁烯和戊烯。
由于基本建筑单元的种类和浓度分布相近,所以从不同碳数的轻烃原料出发都可以得到苯、甲苯和C8芳烃等产物,并且原料对芳烃产物的分布影响不大。
但是,若两种芳构化原料的碳数不同(如C3、C4、C5、C6、C7、C8)、结构不同(如直链烃、支链烃和环烷烃)和碳-碳键饱和程度不同(如烷烃、单烯烃、二烯烃),则其芳构化的活性、热效应和芳烃产率会有一定差别。
一般来说,碳数越小的原料在酸中心上生成正碳离子越困难,其芳构化活性越低;在同碳数下,烯烃比烷烃更容易生成正碳离子,因而其活性较高;另外,异构烷烃因可以生成相对稳定的叔碳正碳离子,因此其芳构化活性高于正构烷烃。
轻烃芳构化技术及应用

轻烃芳构化技术及应用近几年来,随着石油资源的日益减少,将丰富廉价的轻烃,转变为高附加值的苯、甲苯、二甲苯(BTX)的研究已成为当今重要的研究课题和热点问题。
轻烃芳构化是近年来发展起来的一种生产芳烃的新工艺,用于生产芳烃或高辛烷值汽油的调和组分。
轻烃芳构化基本机理是低碳烯烃在固体酸表面活化成正碳离子,然后转化为低碳烯烃中间物种,再低度共聚生成六碳至九碳烯烃等低聚物。
低聚物再通过环化、异构化和脱氢等反应步骤生成芳烃。
轻烃芳构化技术主要为非临氢,有两种工艺路线。
一种是芳烃型芳构化工艺路线,原料可以为轻烯烃和碳3以上烷烃,包括炼厂气、液化气、混合C4、裂解C5、油田轻烃等。
主要产物是以三苯为主的芳烃(液相产品芳烃含量98%以上),反应温度较高(高于500℃),不仅可以转化碳四中的烯烃,同时碳四烷烃也可以得到转化,缺点是会产生较多的干气(15%左右)。
另一种是汽油型芳构化工艺路线,以高辛烷值汽油调合组分作为目的产物,原料可以为直馏汽油、加氢焦化汽油、轻石脑油、混合碳四、液化石油气等,反应温度较低(一般300-450℃),干气产量较低(低于2%),所得汽油辛烷值较高(RON 85-93或更高)。
国外在上世纪八十年代开始低碳烃的芳构化技术研究,陆续开发出以LPG为原料的移动床芳构化Cyclar工艺(UOP/BP)、采用固定床的M2-Forming工艺(Mobil)和Aroforming工艺(IFP)等轻烃芳构化技术。
20世纪80年代初,国内开始对轻烃芳构化催化剂进行探索。
华东理工大学和山西煤化所分别对金属改性的ZSM - 5 沸石用于轻烃芳构化进行研究;抚研院以富含丁烯的C4 馏分、丙烷及混合C3 为原料,在改性的HZSM- 5沸石催化剂上进行了芳构化反应考察。
上世纪90年代,中国石化有关研究机构、大连理工大学等单位也分别开发了各自的轻烃芳构化技术。
轻烃芳构化技术目前主要有以下三个方面的应用:1)直馏石脑油芳构化改质生产高辛烷值汽油调合组分;由于直馏石脑油芳构化改质的汽油收率远低于直馏石脑油进催化重整的汽油收率,因此直馏石脑油芳构化改质技术仅仅适用于没有催化重整装置的炼油企业,技术的推广应用受到较大的限制。
石脑油芳构化生产工艺

石脑油芳构化生产工艺石脑油是一种石油产品,主要由碳氢化合物组成,是一种重要的石油化工原料。
是通过对石脑油进行加氢裂化和催化重整等过程,将其转化为芳香烃类产品的工艺,是一种重要的石化工艺之一。
1.石脑油芳构化生产工艺的原理石脑油芳构化是将石脑油中的不饱和烃和环烷烃经加氢裂化和重整反应,转化为芳香烃类产品的过程。
在加氢裂化过程,石脑油中的不饱和烃被加氢饱和,形成环烷烃,然后经过重整反应,环烷烃再发生脱氢、脱碳等反应,生成苯、甲苯、二甲苯等芳香烃类产品。
2.石脑油芳构化生产工艺的步骤(1)催化裂化:将石脑油在催化剂的作用下进行裂化反应,生成乙烯、丁烯、丙烯等烯烃和环烷烃,这些烃类是后续芳构化反应的原料。
(2)加氢处理:将裂化生成的烯烃和环烷烃经过加氢处理,使其发生氢化反应,生成相应的饱和烃。
(3)芳构化反应:经过加氢处理后的烷烃在催化剂的作用下进行芳构化反应,脱氢、脱碳、重排等反应,最终生成苯、甲苯、二甲苯等芳香烃类产品。
(4)产品分离、纯化:将芳构化反应生成的混合芳烃产品进行分离、纯化,得到高纯度的苯、甲苯、二甲苯等芳香烃产品。
3.石脑油芳构化生产工艺的优点(1)利用率高:石脑油芳构化生产工艺可以有效利用石脑油中的烃类原料,将其转化为有较高附加值的芳香烃产品。
(2)产品多样性:通过芳构化反应可以得到苯、甲苯、二甲苯等多种芳香烃产品,可以满足不同行业的需求。
(3)环保节能:石脑油芳构化生产工艺中涉及到的加氢、催化等反应都是在相对温和的条件下进行的,不会产生大量废气、废水等环境污染问题。
总的来说,石脑油芳构化生产工艺是一种重要的石化工艺,可以有效转化石脑油中的烃类原料为芳香烃产品,具有利用率高、产品多样性、环保节能等优点。
在今后的工业发展中,这种工艺将会得到更广泛的应用和推广。
芳构化的系统升温和调整操作

芳构化的系统升温和调整操作1)反应系统a 在醚后液化气和石脑油进入反应器之后,逐渐调整F201炉出口温度从150℃至200℃之间,观察有无温升发生,如果没有温升,则继续升温直至有温升,反应被引发。
注意观察反应器R201床层各点温度变化情况,当温升逐渐变小时,说明反应减弱,则继续提高炉出口温度,让R201温度达到300℃以上。
继续观察R201床层温度分布。
当R201上部温度达到350℃时,小量给反应中间进料,观察R201床层温度分布。
须知在反应中间进料开始进入反应器时,各换热器还没有热源,反应中间进料的温度很低而且呈液态,故在开始给反应中间进料时,要控制小流量,以防反应被“扑灭”。
当反应逐渐正常,反应器温度控制在300-350℃。
在此过程中须时刻注意反应进料量和反应中间进料量的调节,使反应器床层温度达到平衡。
b 观察反应产物凝液分离罐V204液位,当其达到预先设定的控制范围时,即开启去吸收解吸塔T201的反应液泵P204,并建立反应产物凝液分离罐V204液位自动控制。
2) 吸收稳定系统a 观察吸收解吸塔T201底液位和温度,当其达到预先设定的控制范围时,即开启去稳定塔T202的吸收解吸塔底泵P205和稳定塔进料泵P203,并建立T201底液位和产物气液分离罐V203液位自动控制。
b 观察稳定塔T202底液位和温度,当其达到预先设定的控制范围时,即开启去吸收解吸塔T201顶的吸收剂泵P207,并按要求实施吸收剂流量的自动控制。
随后开启P206吸收解吸塔中段循环泵,同时开启塔T202底去脱重塔T203的调节阀,并实施T202底液位自动控制。
c 按工艺要求建立稳定塔T202顶压力控制。
观察稳定塔回流罐V205液位,当其达到预先设定的控制范围时,即开启稳定塔顶回流泵P208,并建立稳定塔顶温度自动控制。
同时建立稳定塔回流罐V205液位自动控制,将稳定塔顶产物由稳定塔回流罐V205经稳定塔顶回流泵P208一部分送去V-212,一部分作为稳定塔回流,另一部分去反应。
芳构化反应机理

芳构化反应机理芳构化活性越低;在同碳数下,烯烃比烷烃更容易生成正碳离子,因而其活性较高;另外,异构烷烃因可以生成相对稳定的叔碳正碳离子,因此其芳构化活性高于正构烷烃。
当用烯烃含量较低的FCC装置产的C4液化气制芳烃时,由于原料中烷烃含量高,活化时需要发生更多的裂解或脱氢反应,因此,虽然此后的烯烃低聚、环化反应为强放热,但整个芳构化反应会表现为净吸热。
另一方面,当用烯烃含量较高的原料,如裂解抽余碳四或裂解碳五为原料生产芳烃时,由于这些烯烃可以直接通过吸附变成正碳离子,进而发生低聚、环化反应生成芳烃前体,减少了裂解或脱氢反应生成正碳离子环节,所以整个芳构化反应会表现为净放热反应。
同催化重整反应相比,芳构化反应相对节能,而重整反应耗能较大。
这主要是因为:重整反应采用C6-C8烷烃为原料,主要发生脱氢反应,因此只有吸热过程;虽然芳构化技术中的芳烃前体也必须通过脱氢反应才能生成芳烃(吸热),但是芳构化技术中采用的轻烃原料一般含有相当一部分烯烃,因此总体上脱氢反应比重整工艺减少。
其次,由于轻烃分子在生成芳烃时必须经过低聚和环化反应,而这些反应是强放热反应。
因此,同重整反应相比,芳构化反应吸热程度低,而且其中一些放热反应所放出的热量可抵消另外一些吸热反应所吸收的热量(吸热和放热的平衡点根据原料性质不同而不同)。
值得注意的是,虽然烯烃和二烯烃容易芳构化,但对于进入反应器的芳构化原料中的烯烃和二烯烃含量还是要做适当限制。
这是因为,烯烃浓度过高时容易在设备及催化剂表面发生聚合,缩短催化剂单程操作周期。
二烯烃的危害甚于单烯烃。
在实际生产中,一方面要通过原料控制二烯烃的含量,同时要注意保持足够的芳构化干气循环。
另外,轻烃中的水分、含氧化合物和氮也是催化剂的毒物,应该加以严格控制。
水分和含氧化合物反应生成的水分能够钝化催化剂上的酸性活性中心,缩短催化剂的寿命;而碱性氮则能中和破坏酸性中心,缩短催化剂单程操作周期及催化剂寿命。
芳构、异构化工艺参数
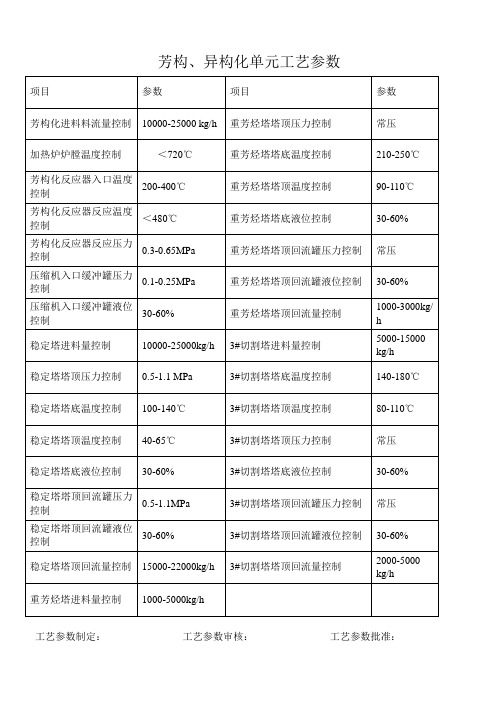
项目
参数
项目
参数
芳构化进料料流量控制
10000-25000 kg/h
重芳烃塔塔顶压力控制
常压
加热炉炉膛温度控制
<720℃
重芳烃塔塔底温度控制
210-250℃
芳构化反应器入口温度控制
200-400℃
重芳烃塔塔顶温度控制
90-110℃
芳构化反应器反应温度控制
<480℃
重芳烃塔塔底液位控制
3#切割塔进料量控制
5000-15000 kg/h
稳定塔塔顶压力控制
0.5-1.1 MPa
3#切割塔塔底温度控制
140-180℃
稳定塔塔底温度控制
100-140℃
3#切割塔塔顶温度控制
80-110℃
稳定塔塔顶温度控制
40-65℃
3#切割塔塔顶压力控制
常压
稳定塔塔底液位控制
30-60%
3#切割塔塔底液位控制
30-60%
稳定塔塔顶回流罐压力控制
0.5-1.1MPa
3#切割塔塔顶回流罐压力控制
常压
稳定塔塔顶回流罐液位液位控制
30-60%
稳定塔塔顶回流量控制
15000-22000kg/h
3#切割塔塔顶回流量控制
2000-5000 kg/h
重芳烃塔进料量控制
1000-5000kg/h
30-60%
芳构化反应器反应压力控制
0.3-0.65MPa
重芳烃塔塔顶回流罐压力控制
常压
压缩机入口缓冲罐压力控制
0.1-0.25MPa
重芳烃塔塔顶回流罐液位控制
30-60%
压缩机入口缓冲罐液位控制
30-60%
芳构化技术 文档

芳构化技术一、芳构化技术的诞生轻质芳烃(苯、甲苯、二甲苯)是最基本的石油化工原料之一,随着合成橡胶、合成纤维、合成树脂三大合成材料的迅猛发展及国民经济对其它精细化学品需求的不断增长,轻质芳烃的需求急速增长。
另外,燃料油市场对高辛烷值汽油的需求量也在不断增长,轻质芳烃正是高辛烷值清洁汽油的重要调合组份,我国绝大多数的清洁汽油中芳烃含量远低于国家标准对芳烃含量的要求,因此,开发新的芳烃来源和生产技术显得越来越重要。
目前,催化重整技术是炼油企业获得优质石油芳烃或高辛烷值汽油调合组分的最主要手段。
催化重整反应的重要特征是将直馏石脑油中的环烷烃经脱氢等过程转化为芳烃。
所以,无论早期的半再生重整工艺还是经催化剂及工艺改进后的连续重整工艺,均要求原料具有一定的芳烃潜含量(主要指环烷烃含量)。
对原料组成的要求事实上限制了由催化重整生产芳烃的原料资源。
轻烃芳构化技术是近二十年来发展的一种新的石油加工技术,其特征是利用改性的沸石分子筛催化剂将低分子的烃类直接转化为苯、甲苯和二甲苯等轻质芳烃。
轻烃芳构化技术与目前炼厂采用的重整工艺相比,具有以下优点:(1)使用的分子筛催化剂具有很好的抗硫、抗氮能力,原料无需深度加工;(2)芳烃产率不受原料油芳烃潜含量的限制,原料不需预分馏;(3)低压、非临氢操作,其基本建设投资少,操作费用低;(4)通过改变催化剂配方及芳构化反应工艺条件,可在一定范围内调整产品分布,以适应市场需要;(5)芳构化反应产生的干气富含氢气,可以作为加氢装置的氢源。
随着现代工业的发展,作为基础化学工业原料和高辛烷值汽油组分的轻质芳烃的需求量不断增加,而石油资源却日益短缺,因此,立足现有石油资源,利用芳构化工艺过程来拓宽生产芳烃的原料资源、增加芳烃产量具有很强的现实意义。
二、轻烃芳构化技术概况二十世纪70年代初,美国Mobil公司合成出了ZSM-5型硅铝沸石,并将其应用于催化剂研究中,进而开发出生产芳烃的催化剂和工艺,使得从其它途径生产芳烃成为可能。
芳构化反应机理

2.2 工艺原理及特点液化气芳构化装置的目的是将来自界区的碳四组分其它适宜的原料在DLP催化剂的作用下,通过芳构化反应转化为含有苯、甲苯及二甲苯的混合芳烃,同时生成含有氢气、甲烷及碳二至碳五馏分的气相。
然后通过一系列的分离,最终产出符合标准的混合芳烃、轻芳烃及重芳烃,同时副产低烯烃的液化气及少量的干气。
C4液化气等低碳烃在芳构化催化剂中进行芳构化反应的过程较为复杂,以烷烃为例一般要经过脱氢、齐聚、环化及芳构化等过程最终才能生成芳烃,而烯烃的转化则没有脱氢的过程。
上述过程中,烷烃脱氢的过程为吸热过程,而齐聚、环化及芳构化过程为放热的过程,所以烷烃的芳构化生成芳烃的能耗要比烯烃的芳构化过程要高。
在低温条件下生产轻芳烃汽油组分时,齐聚、环化及芳构化的反应为主导反应,所以是一个强的放热反应。
2.2.1 工艺原理反应机理液化石油气等轻烃的芳构化机理十分复杂。
一般认为,轻烃在分子筛的酸中心上芳构化反应时经历下列步骤:a)通过在酸中心上发生化学吸附生成正碳离子得到活化;b)正碳离子进一步脱氢和裂解生成乙烯、丙烯、丁烯和戊烯。
这些小烯烃是芳烃分子的建筑单元。
该步反应属于吸热反应;c)小烯烃分子在B酸中心上低聚(二聚、三聚)生成C6-C8烯烃,后者再通过异构化和环化生成芳烃前体(带6元环的前体)。
该步反应属于强放热反应;d)芳烃前体在L酸中心上通过脱氢生成苯、甲苯和C8等芳烃。
这步反应属于吸热反应。
在上述反应中,原料在酸中心上生成正碳离子的步骤最为关键,它决定了芳构化反应的活性和选择性。
C3-C8之间的轻烃分子都可以在催化剂的酸中心上通过脱氢和裂解生成乙烯、丙烯、丁烯和戊烯。
当反应温度和催化剂的酸度相同时,从不同碳数的轻烃原料出发,可以得到具有同样热力学平衡分布的乙烯、丙烯、丁烯和戊烯。
由于基本建筑单元的种类和浓度分布相近,所以从不同碳数的轻烃原料出发都可以得到苯、甲苯和C8等芳烃产物,并且原料对芳烃产物的分布影响不大。
芳构化
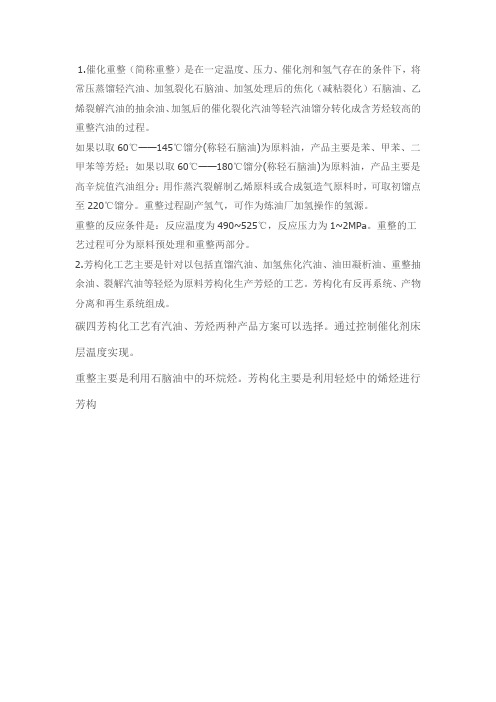
1.催化重整(简称重整)是在一定温度、压力、催化剂和氢气存在的条件下,将常压蒸馏轻汽油、加氢裂化石脑油、加氢处理后的焦化(减粘裂化)石脑油、乙烯裂解汽油的抽余油、加氢后的催化裂化汽油等轻汽油馏分转化成含芳烃较高的重整汽油的过程。
如果以取60℃——145℃馏分(称轻石脑油)为原料油,产品主要是苯、甲苯、二甲苯等芳烃;如果以取60℃——180℃馏分(称轻石脑油)为原料油,产品主要是高辛烷值汽油组分;用作蒸汽裂解制乙烯原料或合成氨造气原料时,可取初馏点至220℃馏分。
重整过程副产氢气,可作为炼油厂加氢操作的氢源。
重整的反应条件是:反应温度为490~525℃,反应压力为1~2MPa。
重整的工艺过程可分为原料预处理和重整两部分。
2.芳构化工艺主要是针对以包括直馏汽油、加氢焦化汽油、油田凝析油、重整抽余油、裂解汽油等轻烃为原料芳构化生产芳烃的工艺。
芳构化有反再系统、产物分离和再生系统组成。
碳四芳构化工艺有汽油、芳烃两种产品方案可以选择。
通过控制催化剂床层温度实现。
重整主要是利用石脑油中的环烷烃。
芳构化主要是利用轻烃中的烯烃进行芳构。
芳构化操作规程(终结版)
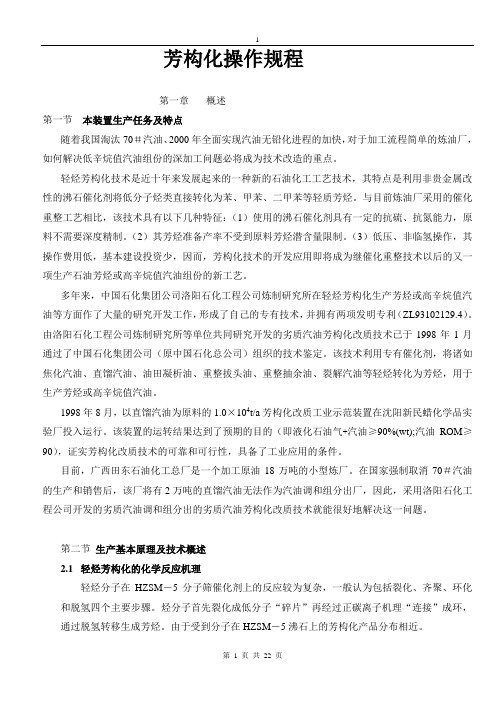
芳构化操作规程第一章概述第一节本装置生产任务及特点随着我国淘汰70#汽油、2000年全面实现汽油无铅化进程的加快,对于加工流程简单的炼油厂,如何解决低辛烷值汽油组份的深加工问题必将成为技术改造的重点。
轻烃芳构化技术是近十年来发展起来的一种新的石油化工工艺技术,其特点是利用非贵金属改性的沸石催化剂将低分子烃类直接转化为苯、甲苯、二甲苯等轻质芳烃。
与目前炼油厂采用的催化重整工艺相比,该技术具有以下几种特征:(1)使用的沸石催化剂具有一定的抗硫、抗氮能力,原料不需要深度精制。
(2)其芳烃准备产率不受到原料芳烃潜含量限制。
(3)低压、非临氢操作,其操作费用低,基本建设投资少,因而,芳构化技术的开发应用即将成为继催化重整技术以后的又一项生产石油芳烃或高辛烷值汽油组份的新工艺。
多年来,中国石化集团公司洛阳石化工程公司炼制研究所在轻烃芳构化生产芳烃或高辛烷值汽油等方面作了大量的研究开发工作,形成了自己的专有技术,并拥有两项发明专利(ZL93102129.4)。
由洛阳石化工程公司炼制研究所等单位共同研究开发的劣质汽油芳构化改质技术已于1998年1月通过了中国石化集团公司(原中国石化总公司)组织的技术鉴定。
该技术利用专有催化剂,将诸如焦化汽油、直馏汽油、油田凝析油、重整拔头油、重整抽余油、裂解汽油等轻烃转化为芳烃,用于生产芳烃或高辛烷值汽油。
1998年8月,以直馏汽油为原料的1.0×104t/a芳构化改质工业示范装置在沈阳新民蜡化学品实验厂投入运行。
该装置的运转结果达到了预期的目的(即液化石油气+汽油≥90%(wt);汽油ROM≥90),证实芳构化改质技术的可靠和可行性,具备了工业应用的条件。
目前,广西田东石油化工总厂是一个加工原油18万吨的小型炼厂。
在国家强制取消70#汽油的生产和销售后,该厂将有2万吨的直馏汽油无法作为汽油调和组分出厂,因此,采用洛阳石化工程公司开发的劣质汽油调和组分出的劣质汽油芳构化改质技术就能很好地解决这一问题。
芳构化——精选推荐

芳构化芳构化是指氢化芳香族化合物经脱氢转变成为芳香族化合物的反应芳构化反应是烷烃、烯烃环化后进一步氢转移反应,反应过程不断放出氢原子,最后生成芳烃。
采用Mo担载的质量分数为6%、经过先碱后酸预处理的Mo/HZSM-5作为催化剂,在不同反应温度和反应空速下,比较了甲烷的转化率、苯的生成速率和积炭的收率。
结果表明,当反应温度为700℃,反应空速为1400mL/(g·h)时,甲烷无氧芳构化性能最佳。
芳构化反应在有机合成和天然产物的构造分析中有重要意义。
例如:1、过去曾将胆固醇经芳构化得到菲的衍生物,从而确定了胆固醇的碳骨架;2、在石油工业中,环烷烃和烷烃等经脱氢和环化等反应变成芳烃的过程,也称芳构化或石油芳构化。
这是从石油中获得芳烃的重要途径。
催化重整中芳构化的反应有哪些特点1、催化重整化学反应的类型在催化重整反应中发生的化学反应主要是有以下五类:(1)六员环烷烃的脱氢反应(2)五员环烷的异构脱氢反应(3)烷烃的环化脱氢反应(4)直链烷烃异构化反应(5)加氢裂化反应2、前三类反应都是生成芳烃的反应,无论是生产芳烃还是高辛烷值汽油,这些反应都是有利的。
六元环烷的脱氢反应进行的很快,在工业条件下能达到化学平衡,五元环烷的异构脱氢反应比六元环烷的脱氢反应慢的多,但大部分也能转化为芳烃;烷烃环化脱氢反应的速率较慢,在铂重整过程中,转化为芳烃的转化率很小。
在铂铼等双金属和多金属催化剂重整的芳烃转化率有很大的提高。
加氢裂化反应生成较小烃分子,而且在催化重整条件下的加氢裂化还包含有异构化反应,因此加氢裂化反应有利于提高辛烷值。
但是过多的加氢裂化反应会使液体产物收率降低,因此,对加氢裂化反应要适当控制。
3、在催化重整条件下,各种烃类都能发生异构化反应,其中最有意义是五员环烷烃异构化生成六员环烷烃和正构烷烃的异构化反应。
正构烷烃异构化可提高汽油的辛烷值。
同时,异构烷烃比正构烷烃更易于进行环化脱氢反应,也间接地有利于生成芳烃。
化学工艺学重点知识点
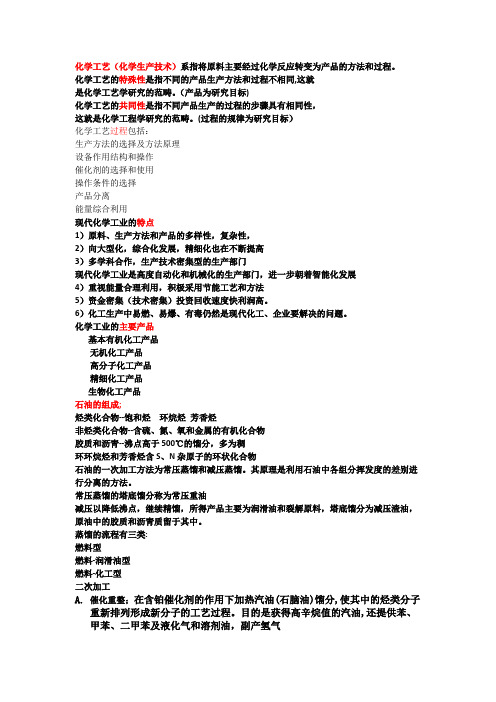
化学工艺(化学生产技术)系指将原料主要经过化学反应转变为产品的方法和过程。
化学工艺的特殊性是指不同的产品生产方法和过程不相同,这就是化学工艺学研究的范畴。
(产品为研究目标)化学工艺的共同性是指不同产品生产的过程的步骤具有相同性,这就是化学工程学研究的范畴。
(过程的规律为研究目标)化学工艺过程包括:生产方法的选择及方法原理设备作用结构和操作催化剂的选择和使用操作条件的选择产品分离能量综合利用现代化学工业的特点1)原料、生产方法和产品的多样性,复杂性,2)向大型化,综合化发展,精细化也在不断提高3)多学科合作,生产技术密集型的生产部门现代化学工业是高度自动化和机械化的生产部门,进一步朝着智能化发展4)重视能量合理利用,积极采用节能工艺和方法5)资金密集(技术密集)投资回收速度快利润高。
6)化工生产中易燃、易爆、有毒仍然是现代化工、企业要解决的问题。
化学工业的主要产品基本有机化工产品无机化工产品高分子化工产品精细化工产品生物化工产品石油的组成;烃类化合物--饱和烃环烷烃芳香烃非烃类化合物--含硫、氮、氧和金属的有机化合物胶质和沥青--沸点高于500℃的馏分,多为稠环环烷烃和芳香烃含S、N杂原子的环状化合物石油的一次加工方法为常压蒸馏和减压蒸馏。
其原理是利用石油中各组分挥发度的差别进行分离的方法。
常压蒸馏的塔底馏分称为常压重油减压以降低沸点,继续精馏,所得产品主要为润滑油和裂解原料,塔底馏分为减压渣油,原油中的胶质和沥青质留于其中。
蒸馏的流程有三类:燃料型燃料-润滑油型燃料-化工型二次加工A.催化重整;在含铂催化剂的作用下加热汽油(石脑油)馏分,使其中的烃类分子重新排列形成新分子的工艺过程。
目的是获得高辛烷值的汽油,还提供苯、甲苯、二甲苯及液化气和溶剂油,副产氢气辛烷值是表示汽油抗爆性的指标。
将汽油样与异辛烷(规定辛烷值为100)和正庚烷(规定辛烷值为0)的混合溶液在标准试验汽油机中比较。
当油样的抗爆性与某一浓度溶液抗爆性相同时,溶液中异辛烷的体积百分浓度就是该汽油的辛烷值。
芳构化反应系统工艺流程

芳构化反应系统工艺流程(总4页)本页仅作为文档封面,使用时可以删除This document is for reference only-rar21year.March芳构化反应系统工艺流程混合碳四液化汽和石脑油是在KCIA-Ⅱ分子筛催化剂的作用下,经过碳四烯烃的叠合、脱氢环化、脱氢芳构化及烷烃的裂解等系列催化反应,生成混合芳烃,及副产品液化汽和干气。
反应是强放热反应。
1)工艺流程及说明:A.加热反应部分加热反应单元包括原料-产物换热器、加热炉、反应器、等单元设备操作。
由MTBE或罐区来的原料C4和石脑油分别进入原料缓冲罐(V202、V201)。
原料C4经泵P202提升后,经计量控制,一线送至原料-产物换热器E201,另一线送至产物-注冷料换热器E202;石脑油经泵P201提升后经计量控制,与一线原料C4混合送至原料-产物换热器E201。
混合原料分别经原料-产物换热器E201、E203、加热炉F201加热至280-390℃后由反应器R201顶部进入反应器。
部分原料液化气(或贫稀液化气)经产物-注冷料换热器E202加热汽化后,经计量控制分两线由反应器R201中部两催化剂床层之间注入反应器,以便于调节反应床层温度。
反应产物由反应器R201底部采出分别经原料-产物换热器E203、(E-202)、E201换热后进入产物气液分离罐V203,罐底部凝液经泵P203提升后计量控制后进入稳定塔;罐顶分离出的气相经产物空冷器AC201、产物水冷器E204冷却至40℃后进入产物凝液分离罐V204,罐顶部采出为不凝气,进入吸收解吸塔T201中部塔板,底部采出液相,经泵P204提升后进入吸收解吸塔中部塔板。
B.催化剂再生部分反应进行一段时间后,随着反应器R201中催化剂表面结焦的增加,催化剂表面活性降低,当检测到产品质量不能满足要求时,需将反应器R201切换出反应系统进行催化剂烧焦再生处理。
催化剂再生采用氮气和空气作为再生气体,并控制再生气体中的氧含量,以防止反应催化剂床层再生烧焦超温破坏催化剂。
醋酸芳构化

醋酸芳构化醋酸芳构化是一种有机化学反应,通过该反应可以将醋酸酯转化为芳香醇或芳香酮。
在此过程中,醋酸酯分子中的酯基被取代,形成具有芳香性质的化合物。
这种反应在有机合成中具有广泛的应用。
在醋酸芳构化反应中,通常使用碱性条件下的催化剂。
常见的催化剂包括碱金属如钠、钾或碱土金属如钙、镁等。
此外,还可以使用碱性溶剂如氢氧化钠或碳酸钠来促进反应的进行。
反应过程中,醋酸酯首先与碱性溶剂中的氢氧根离子发生酰氧根亲核取代反应,生成相应的酰氧根盐。
然后,酰氧根盐再与醋酸酯分子内的羟基发生亲核取代反应,形成中间产物。
最后,中间产物经过脱水作用,生成芳香醇或芳香酮。
醋酸芳构化反应的机理可以分为两步。
首先是酰氧根亲核取代反应,该反应是一个速率决定步骤。
酰氧根离子与醋酸酯发生亲核取代反应,形成酰氧根盐。
然后,酰氧根盐与醋酸酯分子内的羟基发生亲核取代反应,生成中间产物。
中间产物经过脱水反应,生成芳香醇或芳香酮。
醋酸芳构化反应具有以下几个特点。
首先,该反应可以在温和的条件下进行,不需要高温或高压。
其次,反应底物种类丰富,可以适用于不同结构的醋酸酯。
此外,该反应产率较高,且容易控制反应条件,具有较好的可重复性。
醋酸芳构化反应在有机合成中有广泛的应用。
一方面,该反应可以用于合成具有芳香性质的化合物,如香精、香料等。
另一方面,该反应还可以用于合成药物、染料等有机化合物。
总结起来,醋酸芳构化是一种重要的有机化学反应,通过该反应可以将醋酸酯转化为芳香醇或芳香酮。
该反应在有机合成中具有广泛的应用,可以合成具有芳香性质的化合物。
醋酸芳构化反应的机理包括酰氧根亲核取代反应和脱水反应。
该反应具有温和的条件、丰富的底物种类和较高的产率等特点。
通过合理控制反应条件,可以实现对目标化合物的选择性合成。
- 1、下载文档前请自行甄别文档内容的完整性,平台不提供额外的编辑、内容补充、找答案等附加服务。
- 2、"仅部分预览"的文档,不可在线预览部分如存在完整性等问题,可反馈申请退款(可完整预览的文档不适用该条件!)。
- 3、如文档侵犯您的权益,请联系客服反馈,我们会尽快为您处理(人工客服工作时间:9:00-18:30)。
工艺知识芳构化工艺知识装置概况:1、轻油芳构化装置,产品较重终馏点较高2、装置改造,利用稳定塔再上溶剂油装置生产溶剂油3、由于分离溶剂油的可操作性,改为利用溶剂油装置对轻油芳构化原料进行预处理脱除重组分---拔精粗200#4、正值经济危机之际,原料油涨价而汽油降价,进行液化气芳构化流程改造,再利用溶剂油装置脱轻柴5、为了更加容易控制反应器床层温度进行反应器改造,并更换R101B/D催化剂为液化气芳构化的专用催化剂为了更加容易,期间进行的小流程改造不断;大家也看到了,改造的地方也比较多,都是为了操作稳定容易减少劳动强度与损耗,希望大家在以后的操作生产中能提出更好的流程改造方案。
1、富压机中间冷却器退油2、溶剂油装置的脱丁烷塔顶放空至罐区3、V110放空改至液化气外送线4、吸收塔干气调节阀前改至液化气外送至液化气产品罐给罐区补压,调节阀后补压;由于液化气芳构化的催化剂不同,分阀前阀后补压5、烧焦再生的补风线加调节阀控制补风量,补风管线加粗防冻6、再生系统加放空调节阀改造,空压机入口加调节阀7、P301、P302外送合在一起;P303外送与P305合在一起,P304外送与P306合在一起8、仪表风分净化风与非净化风两条线,烧焦用非净化风9、V101加放空调节阀10、V106向V101压油流程11、脱色塔进料的分布器堵,改用脱己烷塔当脱色塔使用液化气芳构化的理论知识:用富含烯烃(丁烯)的液化气作为原料,在反应器进行液化气芳构化轻油芳构化的主要反应是:裂化、齐聚、环化、脱氢液化气芳构化的主要反应为:叠合反应(属齐聚反应)此反应为强放热反应,所以反应器床层温度是温升而不是温降,有效地控制床层温度是重点;还进行环化、脱氢反应。
叠合反应是指两个或者两个以上的烯烃分子生成一个高分子量的烯烃的过程。
原料中烯烃含量越高,反应放出的温度越多,床层温度越高,反应周期缩短。
液化气芳构化的影响因素:1、原料组成对芳构化反应的影响随着原料中烯烃含量的增加,液体收率和芳烃增加,干气产率下降。
丁烯比丙烯更易发生芳构化反应。
同等烯烃总含量的原料中,丁烯含量越高,其中液体产物收率越高,干气产率越低。
同时,丁烷较丙烷更易发生芳构化反应。
液化气芳构化生成的芳烃中以轻质芳烃为主,但芳烃的具体分布有一定的差别,其中苯含量变化较大。
主要表现为,苯含量随着原料中丁烯含量的升高而降低,相应的二甲苯的含量随着丁烯行量的升高而增加。
丙烷是丁烯芳构化反应的主要产物,随着原料丁烯含量的增加而增加;丙烷发生芳构化反应的量很少,丁烷比丙烷易发生芳构化反应。
随着烯烃含量的增加,芳构化干气中的氢含量高,这是因为在高温下,烯烃芳构化的芳烃产率高,且反应中主要是通过环烷直接脱氢生成芳烃。
原料中的丁烯含量是液化气芳构化过程的主要影响因素,液化气芳构化所得液体产物中芳烃含量不受原料性质的影响,随着烯烃含量尤其是丁烯含量的增加芳烃产率增加,干气产率相应降低;原料中丁烯含量影响液体产物中苯和气相产物中丙烷和氢气含量。
2、进料量空速=单位时间的进料量/催化剂的装填量如果进料量和藏量都以重量(体积)单位计算,称为重量(体积)空速。
藏量=反应器催化剂的量重量空速=总进料量(t/h)/ 藏量(t/h)体积空速=总进料量(m3/h)/ 藏量(m3/h)R101B/D装填量约为9t,R101A/C装填量不足6.25t3、反应温度随着床层温度的升高,催化剂的活性略有提高,所以在后期不断的提高床层温度。
最好的液收率温度为370-420℃;随温度的升高,结焦速度增快,易失活。
4、反应压力压力越高,脱氢反应速率下降。
反应器:固定床轴向反应器在进行多相过程的设备中,若有固相参与,且处于静止状态时,则设备内的固体颗粒物料层,称为固定床。
按照反应气体在催化床中的流动方向,固定床反应器可分为轴向流动与径向流动。
轴向流动反应器中气体流向与反应器的轴平行,而径向流动催化床中气体在垂直于反应器轴的各个横截面上沿半径方向流动。
反应器的三段冷进料:A1 B1 C1 D1搭在反应器入口的氮气线上(无论是反应还是再生,倒流程时注意检查相应的冷进料;特别是再生时,因为冷进料都是双阀没打盲板;近期发现有班组再生时氮气流程开着,用时再开,用完关上)A/B/C/D2 A/B/C/D3从反应器催化剂卸料口改造进入反应器。
B2 B3 D2 D3已打盲板。
饱和蒸汽压:在一定温度下,纯液体在与它表面上的蒸汽呈平衡状态时,由此蒸汽产生的压力称为饱和蒸汽压。
液化气芳构化生成的芳烃中含苯、二甲苯较多,辛烷值比较高,97以上。
辛烷值:汽油抗爆性的表示单位。
在数值上等于规定条件下与试样抗爆性相同的标准燃料中所含异辛烷的体积百分数。
MON和RON都是表示汽油辛烷值的符号。
其中MON表示马达法辛烷值,RON表示研究法辛烷值。
(M+R)/2则表示汽油的抗爆指数。
汽油的辛烷值与其抗爆性有着密切的关系。
汽油的抗爆性是衡量汽油质量最重要的性能指标之一。
一定压缩比的内燃机,必须燃用具有一定辛烷值的汽油,才能保证发动机气缸内的正常燃烧而不致产生爆震。
对气化器式发动机使用的车用汽油,通常采用研究法辛烷值(RON)和马达法辛烷值(MON)进行评价,分别反映汽车在低速和高速行驶条件下的抗爆性。
液化气芳构化生产的芳烃要求:饱和蒸汽压冬季≤88Kpa、夏季≤74Kpa;终馏点≤205℃液化气芳构化生成的芳烃辛烷值不可控,不作要求;轻油芳构化通过反应温度控制辛烷值。
调和汽油时的添加剂:MTBE (甲基叔丁基醚) MMT(甲基环戊二烯三羰基锰) 添加调和剂时还要求锰含量≤0.0018g/L产品液化气的C5≤3% 烯烃含量以2%为界限进不同产品罐(交接罐时一定记清交接的液位,与装车对一下液位,不自顾自的记,注意交接。
)催化剂概念:是一种物质,它能够加速反应的速率而不改变该反应的标准自由焓变化,这种作用称为催化作用,涉及催化剂的反应称为催化反应。
催化剂会诱导化学反应发生改变,而使化学反应变快或在较低的温度环境下进行化学反应。
催化剂的活性是指:物质的催化作用的能力,是催化剂的重要性质之一。
工业生产上常以每单位容积(或质量)催化剂在单位时间内转化原料反应物的数量来表示。
催化剂的失活就是催化能力的降低或失去。
失活原因:中毒、烧结、热失活、结焦堵塞。
(1)中毒:a) 暂时中毒:毒物在活性中心上吸附或化合时生成的键强度相对较弱,可采取适当的方法除去毒物,使催化剂活性恢复。
b) 永久中毒:毒物与催化剂活性组分相互作用形成很强的化学键,很难用一般的方法除去让催化剂活性恢复,这种中毒叫不可逆中毒或永久中毒。
c) 选择性中毒:催化剂中毒后可能失去对某一反应的催化能力,但对别的反应仍有催化活性,这种现象为选择性中毒。
(2)结焦和堵塞引起的失活:催化剂表面的含碳沉积物称为结焦。
以有机物为原料、以固体为催化剂的多相催化反应过程中几乎都可能发生结焦,由于含碳物质和其它物质在催化剂孔中沉积造成孔径减小(或孔口缩小)使反应物分子不能扩散进孔中,这种现象称为堵塞,所以常把堵塞归并为结焦中,总的活性衰退称为结焦失活,它是催化剂失活中最普遍最常见的失活形式。
(3) 烧结和热失活:催化剂的烧结和热失活是指由高温引起的催化剂结构和性能的变化。
高温除了引起催化剂的烧结外,还会引起其它变化,主要包括化学组成和相组成的变化,半熔晶粒长大,活性组分被载体包埋,活性组分由于生成挥发性物质或可升华的物质流失。
为什么开工时冷换系统要先冷后热的开?停工时又要先热后冷的停?答:冷换系统的开工顺序,冷却器要先进冷水,换热器要先进冷油。
这是由于先进热油会造成各部件热胀,后进冷介质会使各部件急剧收缩。
这种温差可促使静密封点产生泄露,故开工时不允许先进热油。
反之,停工时要先停热油后停冷油,道理相同。
水冷器是控制入口水量好还是控制出口水量好?答:对油品冷却器而言,用冷却水入口阀控制弊多利少。
控制入口可节省冷水,但入口水量限死可引起冷却器内水流短路或流速减慢,造成上热下凉。
采用出口控制能保证流速和换热效果。
一般不易使用入口控制。
淹塔:在生产的过程中,由于气相或液相的流量过大,上下两层的塔板压降增大到使液体无法正常下流。
当管内液体满到一定程度后使下层塔板的液体满到上层去,这种现象称为液泛(即淹塔)。
当液泛开始时塔的压降急剧上升,效率则急剧下降,正常的操作就被打破,其产生的原因有以下几个方面:1)气相量过大:使得大量液滴从泡沫层中喷出到达上层塔板,冷凝回流后增大了降液管负荷及塔板的压降,产生淹塔现象。
2)液体流量过大:降液管面积不足,使液体不能及时通过,也会产生淹塔,有时降液管堵塞也会产生这种现象。
主要的防治方法有:1)尽量加大降液管截面积,但会减少塔板开孔面积。
2)改进塔盘结构,降低塔盘压力降。
3)控制液体回流量不能太大。
漏液:液体在塔盘上横向流动并经降液管流入下一层塔盘。
如果气相负荷过小,塔内气速很低,大量的液体由于重力的作用,会从阀孔或舌形塔盘的舌孔直接漏到下一层塔盘,这种现象称为“漏液”。
由于漏液使气液两相没有充分接触,降低了塔盘的效率,所以处理量应控制在允许范围内,不可随意减小。
安全阀:当工作压力超过规定数值时能自动打开泄压,而当压力复原后又能自动关闭的阀门叫安全阀。
重沸器的原理就是热虹吸效应;热虹吸效应:是一种热循环运动。
热虹吸式再沸器依靠塔釜内的液体静压头和再沸器内两相流的密度差产生的推动力而形成的热虹吸式循环运动进行工作潜热:物质在物态变化时所吸收或放出的热量叫做潜热。
工艺流程图:用图形符号表明工艺流程所使用的机械设备及其相互联系的系统图。
塔、罐、重沸器、泵、调节阀、阀门、冷凝器、换热器、安全阀、流量压力温度液位控制仪表等。
简易的流程图没那么多要求。
阀:是在流体系统中,用来控制流体的方向、压力、流量的装置。
按作用和用途分类:(1) 截断阀:截断阀又称闭路阀,其作用是接通或截断管路中的介质。
包括闸阀、截止阀、蝶阀、球阀、旋塞阀和隔膜等。
(2) 止回阀:止回阀又称单向阀或逆止阀,其作用是防止管路中的介质倒流。
(3) 安全阀:当工作压力超过规定数值时能自动打开泄压,而当压力复原后又能自动关闭的阀门叫安全阀。
安全阀类的作用是防止管路或装置中的介质压力超过规定数值,从而达到安全保护的目的。
(4) 调节阀:其作用是调节介质的压力、流量等参数。
(5) 分流阀:其作用是分配、分离或混合管路中的介质。
截止阀就是可以截流及调节流量的阀,一般小于公称口径DN50场合用它。
截止阀有单向密封效果好的特点。
闸阀的启闭件是闸板,闸板的运动方向与流体方向相垂直,闸阀只能作全开和全关,不适合作调节和节流。
球阀特点是本身结构紧凑,密封可靠,结构简单,维修方便,密封面与球面常在闭合状态,不易被介质冲蚀,易于操作和维修,适用于水、溶剂、酸和天然气等一般工作介质,而且还适用于工作条件恶劣的介质,如氧气、过氧化氢、甲烷和乙烯等。