电解铜废液的处理方法与设计方案
含铜蚀刻废液处理方法及系统与流程

含铜蚀刻废液处理方法及系统与流程下载提示:该文档是本店铺精心编制而成的,希望大家下载后,能够帮助大家解决实际问题。
文档下载后可定制修改,请根据实际需要进行调整和使用,谢谢!本店铺为大家提供各种类型的实用资料,如教育随笔、日记赏析、句子摘抄、古诗大全、经典美文、话题作文、工作总结、词语解析、文案摘录、其他资料等等,想了解不同资料格式和写法,敬请关注!Download tips: This document is carefully compiled by this editor. I hope that after you download it, it can help you solve practical problems. The document can be customized and modified after downloading, please adjust and use it according to actual needs, thank you! In addition, this shop provides you with various types of practical materials, such as educational essays, diary appreciation, sentence excerpts, ancient poems, classic articles, topic composition, work summary, word parsing, copy excerpts, other materials and so on, want to know different data formats and writing methods, please pay attention!摘要:含铜蚀刻废液是半导体制造过程中产生的一种有害废液,含有高浓度的铜离子和其他有害物质,对环境造成严重污染。
实验室废液的处理
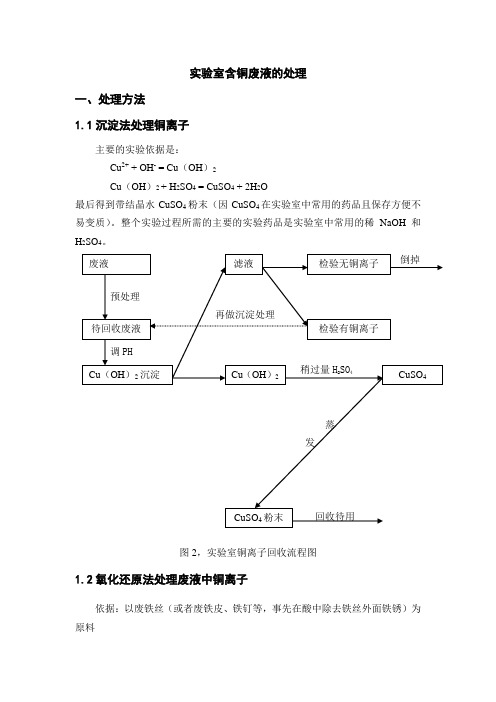
实验室含铜废液的处理一、处理方法1.1沉淀法处理铜离子主要的实验依据是:Cu 2+ + OH - = Cu (OH )2Cu (OH )2 + H 2SO 4 = CuSO 4 + 2H 2O最后得到带结晶水CuSO 4粉末(因CuSO 4在实验室中常用的药品且保存方便不易变质)。
整个实验过程所需的主要的实验药品是实验室中常用的稀NaOH 和H 2SO 4。
倒掉预处理再做沉淀处理调PH稍过量H 2SO 4蒸发回收待用图2,实验室铜离子回收流程图1.2氧化还原法处理废液中铜离子依据:以废铁丝(或者废铁皮、铁钉等,事先在酸中除去铁丝外面铁锈)为原料CuSO 4粉末 废液待回收废液Cu (OH )2沉淀 滤液 Cu (OH )2 检验无铜离子 检验有铜离子 CuSO 4Fe2O3+3H2SO4=Fe2(SO4)3+3H2OCu2++Fe=Cu+Fe2+铜是不活泼金属,不能与稀硫酸直接反应,所以先把同转化为氧化铜后再与稀硫酸反应2Cu+O2=2CuOCuO+H2SO4=CuSO4+H2O直接加H2SO4,过滤,滤渣为铜可直接回收,滤液加碱成氢氧化铁,加酸回收为Fe2(SO4)3二、实验2.1 氢气还原氧化铜实验的废液的处理实验药品与仪器:Zn片、稀H2SO4、碱石灰、CuO粉末、布氏漏斗、滤纸、玻璃棒、试剂瓶、中型坩埚、启普发生器、硬质管、酒精灯、U型管。
实验原理:Zn + H2SO4 = ZnSO4 + H2↑H2 + CuO = Cu + H2OCuO + H2SO4 = CuSO4 + H2O实验步骤:⑴检验启普发生器的气密性,按下图连接实验装置;⑵用托盘天平取CuO粉末10.0g,平铺在硬质管的中部,托盘天平称量硬质管的质量;⑶检验纯度后通入H2一段时间后点燃酒精灯,待黑色粉末消失时熄灭酒精灯,通H2到试管干燥冷却;⑷称量硬质管和以还原的CuO质量,记录数据;⑸还原产物倾入烧杯中并用稀H2SO4,冲洗硬质管壁,减压抽滤,用稀H2SO4洗涤固体Cu;⑹干燥固体Cu并称量,滤液在坩埚中蒸发至干并用分析天平称量,回收CuSO·5H2O4⑺把回收产品放入试剂瓶,整理实验设备。
一种铜电解废液的处理方法

一种铜电解废液的处理方法
铜电解废液是铜电解过程中产生的废液,含有高浓度的铜离子和其他金属离子。
下面是一种处理铜电解废液的方法:
1. 混合废液预处理:将不同批次的废液混合在一起,以平衡各种金属离子的浓度。
检测废液中的铜离子浓度,确保处理过程中稳定。
2. 中和处理:使用碱性物质(如氢氧化钠或碱金属碳酸盐)逐渐加入废液中,中和废液的酸性。
中和后,废液呈中性或略碱性。
3. 沉淀分离:通过添加沉淀剂(如石灰水或硫酸钙)来沉淀金属离子,使它们形成金属沉淀。
沉淀物可以通过离心或过滤分离出来。
4. 过滤:将沉淀物分离出废液,可以使用纸滤器或其他过滤设备。
5. 精密沉淀:使用其他沉淀剂(如次硫酸钠或二硫化钠)进一步沉淀废液中残余的金属离子。
6. 液固分离:将精密沉淀物与废液分离,可以通过过滤或离心分离。
7. 废液处理:废液中可能还含有一些有害物质,如氰化物。
对于含氰废液,可以使用氯气氧化或经过特殊处理以使其变得无害。
废液经处理后可以进行中和、
过滤等步骤,以净化处理废液。
8. 再利用:处理后的废液中,铜离子浓度相对较高,可以回收利用。
通过电解再生可以将废液中的铜离子还原为纯铜,然后可以重新用于电解生产中。
需要注意的是,铜电解废液处理过程中需要严格遵守环境保护法规,避免污染环境。
同时,废液处理过程中产生的固体废物也需要循环利用或正确处理,以降低环境污染风险。
此外,具体处理方法还需根据废液的具体组成和特性进行调整和优化。
废液铜方案

废液铜方案1. 简介废液铜是指混合有铜离子的废水或废液,在铜加工、电路板制造和电镀等工业过程中产生。
废液铜含有可回收的铜资源,如果不加以处理和回收利用,不仅浪费了资源,还会对环境造成污染。
因此,开发和使用废液铜处理方案对于资源节约和环境保护具有重要意义。
本文将介绍一种废液铜处理方案,包括废液铜的处理过程、处理方法以及处理后的资源利用途径。
2. 废液铜的处理过程废液铜的处理过程可以分为预处理、沉淀、电积和资源回收等步骤。
2.1 预处理在进行废液铜的处理之前,需要对废液进行预处理。
预处理主要包括调整废液的pH值和去除杂质等步骤。
调整废液的pH值可以通过添加酸或碱来实现,使废液处于适宜的酸碱度范围。
去除杂质可以通过净化剂、过滤器等方法来实现,以保证后续处理步骤的顺利进行。
2.2 沉淀废液经过预处理后,进入到沉淀槽中进行沉淀处理。
沉淀是指将废液中的铜离子转化成固体沉淀物的过程。
沉淀过程中,可以添加沉淀剂来加速铜离子的沉淀速度和效率。
常用的沉淀剂包括氢氧化钠、氢氧化钙等。
2.3 电积沉淀后的废液通过过滤等处理后,可以进行电积处理。
电积是指使用电流通过废液中的铜离子,在电极上进行还原,生成纯铜的过程。
电积过程中,需要使用特定的电解质溶液和电极。
经过一段时间的电积,废液中的铜离子会逐渐被还原成纯铜。
2.4 资源回收经过沉淀和电积处理后,生成的纯铜可以进行资源回收利用。
纯铜可以被用于再次生产铜制品,从而实现废液铜的循环利用。
同时,废液中的其他有价值的元素和材料也可以通过进一步的处理和析出来实现资源回收。
3. 废液铜处理方法废液铜的处理方法可以根据不同的生产过程和要求进行选择。
以下是常见的废液铜处理方法:•氨水沉淀法:利用氨水与废液铜中的铜离子反应生成沉淀,通过沉淀的形式进行铜离子的去除。
•离子交换法:通过离子交换树脂将废液中的铜离子进行吸附和去除。
•电析法:利用电流在电解槽中进行沉积,将废液中的铜离子还原为纯铜。
电路板的刻蚀和废液的处理
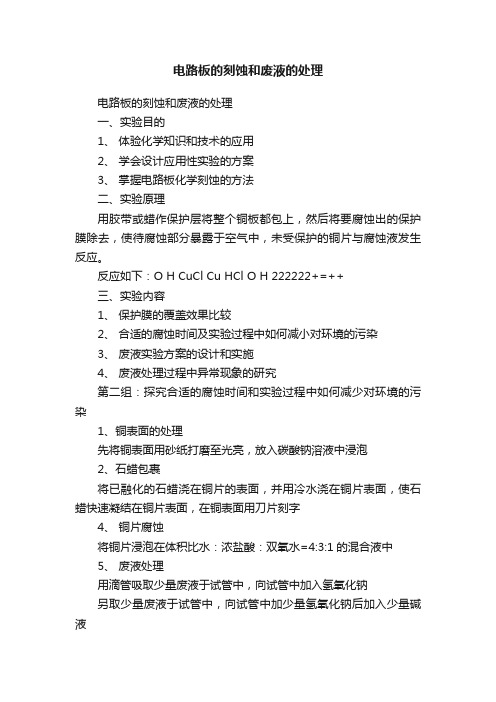
电路板的刻蚀和废液的处理
电路板的刻蚀和废液的处理
一、实验目的
1、体验化学知识和技术的应用
2、学会设计应用性实验的方案
3、掌握电路板化学刻蚀的方法
二、实验原理
用胶带或蜡作保护层将整个铜板都包上,然后将要腐蚀出的保护膜除去,使待腐蚀部分暴露于空气中,未受保护的铜片与腐蚀液发生反应。
反应如下:O H CuCl Cu HCl O H 222222+=++
三、实验内容
1、保护膜的覆盖效果比较
2、合适的腐蚀时间及实验过程中如何减小对环境的污染
3、废液实验方案的设计和实施
4、废液处理过程中异常现象的研究
第二组:探究合适的腐蚀时间和实验过程中如何减少对环境的污染
1、铜表面的处理
先将铜表面用砂纸打磨至光亮,放入碳酸钠溶液中浸泡
2、石蜡包裹
将已融化的石蜡浇在铜片的表面,并用冷水浇在铜片表面,使石蜡快速凝结在铜片表面,在铜表面用刀片刻字
4、铜片腐蚀
将铜片浸泡在体积比水:浓盐酸:双氧水=4:3:1的混合液中
5、废液处理
用滴管吸取少量废液于试管中,向试管中加入氢氧化钠
另取少量废液于试管中,向试管中加少量氢氧化钠后加入少量碱液
四、注意事项
1、铜表面一定要处理干净
2、刻蚀时应在通风橱中进行
3、过氧化氢具有强腐蚀性,不要滴手上
4、取用铜片使要用镊子
五、实验现象。
废电解液的处理
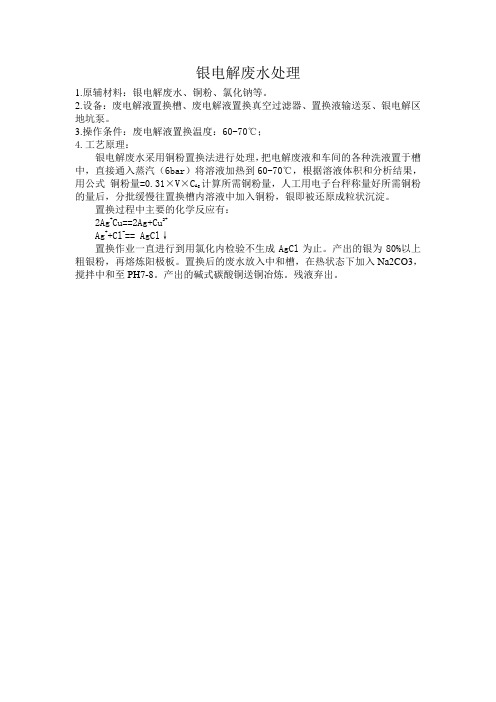
银电解废水处理
1.原辅材料:银电解废水、铜粉、氯化钠等。
2.设备:废电解液置换槽、废电解液置换真空过滤器、置换液输送泵、银电解区地坑泵。
3.操作条件:废电解液置换温度:60-70℃;
4.工艺原理:
银电解废水采用铜粉置换法进行处理,把电解废液和车间的各种洗液置于槽中,直接通入蒸汽(6bar)将溶液加热到60-70℃,根据溶液体积和分析结果,用公式铜粉量=0.31×V×C Ag计算所需铜粉量,人工用电子台秤称量好所需铜粉的量后,分批缓慢往置换槽内溶液中加入铜粉,银即被还原成粒状沉淀。
置换过程中主要的化学反应有:
2Ag+Cu==2Ag+Cu2+
Ag++Cl-== AgCl↓
置换作业一直进行到用氯化内检验不生成AgCl为止。
产出的银为80%以上粗银粉,再熔炼阳极板。
置换后的废水放入中和槽,在热状态下加入Na2CO3,搅拌中和至PH7-8。
产出的碱式碳酸铜送铜冶炼。
残液弃出。
电解铜箔废水处理工艺介绍

电解铜箔生产涉及的废水包括重金属废水、综合废水和生活污水。
重金属废水分别为含镍废水、含铬废水、含铜废水、含锌废水,每类重金属废水单独设置1套“表处车间后处理回用水系统+水处理中心中水回用系统”,根据废水类别,具体处理工艺会有所区别。
①含镍废水:经表处车间后处理回用水系统采用“过滤+一级RO 系统+EDI精除盐”工艺处理后,产出纯水率80%,纯水回用于水洗工序,产生的20%浓水进入水处理中心的含镍废水中水回用系统,经“过滤+二级RO系统+EDI精除盐”工艺处理后,产生纯水率75%,纯水回用于水洗工序,产生的25%浓水经“过滤+三级RO系统+EDI 精除盐”工艺处理后,产生纯水率70%,纯水返回原水池经处理后回用,产生的30%浓水经树脂吸附系统处理达到废水中未检出镍后,排入综合废水处理系统。
含镍废水处理系统回用水率为98.5%。
②含铬废水:经表处车间后处理回用水系统采用“还原系统+过滤+一级RO系统+EDI精除盐”工艺处理后,产出纯水率80%,纯水回用于水洗工序,产生的20%浓水进入水处理中心的含铬废水中水回用系统,经“过滤+二级RO系统+EDI精除盐”工艺处理后,产生纯水率75%,纯水回用于水洗工序,产生的25%浓水经“过滤+三级RO 系统+EDI精除盐”工艺处理后,产生纯水率70%,纯水返回原水池经处理后回用,产生的30%浓水经树脂吸附系统处理达到废水中未检出铬后,排入综合废水处理系统。
含铬废水处理系统回用水率为98.5%。
③含铜废水:经表处车间后处理回用水系统采用“过滤+一级RO 系统+EDI精除盐”工艺处理后,产出纯水率80%,纯水回用于水洗工序,产生的20%浓水进入水处理中心的含铜废水中水回用系统,经“过滤+二级RO系统+EDI 精除盐”工艺处理后,产生纯水率75%,纯水回用于水洗工序,产生的25%浓水经“NF膜”处理后,产生纯水率70%,纯水返回原水池经处理后回用,产生的30%浓水进入综合废水处理系统处理。
矿产
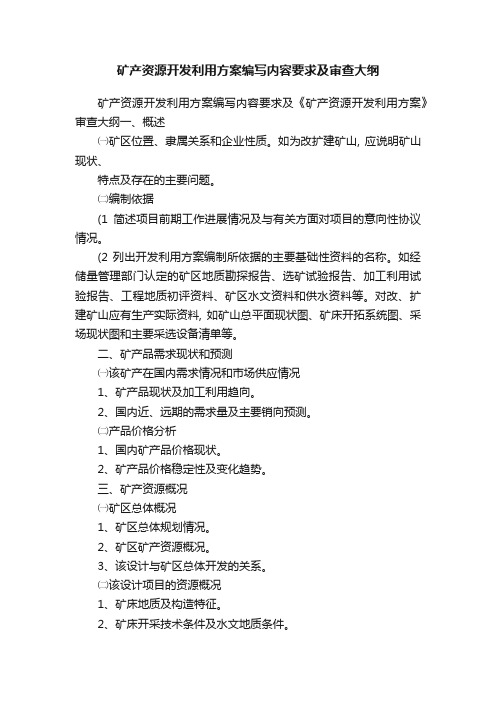
矿产资源开发利用方案编写内容要求及审查大纲
矿产资源开发利用方案编写内容要求及《矿产资源开发利用方案》审查大纲一、概述
㈠矿区位置、隶属关系和企业性质。
如为改扩建矿山, 应说明矿山现状、
特点及存在的主要问题。
㈡编制依据
(1简述项目前期工作进展情况及与有关方面对项目的意向性协议情况。
(2 列出开发利用方案编制所依据的主要基础性资料的名称。
如经储量管理部门认定的矿区地质勘探报告、选矿试验报告、加工利用试验报告、工程地质初评资料、矿区水文资料和供水资料等。
对改、扩建矿山应有生产实际资料, 如矿山总平面现状图、矿床开拓系统图、采场现状图和主要采选设备清单等。
二、矿产品需求现状和预测
㈠该矿产在国内需求情况和市场供应情况
1、矿产品现状及加工利用趋向。
2、国内近、远期的需求量及主要销向预测。
㈡产品价格分析
1、国内矿产品价格现状。
2、矿产品价格稳定性及变化趋势。
三、矿产资源概况
㈠矿区总体概况
1、矿区总体规划情况。
2、矿区矿产资源概况。
3、该设计与矿区总体开发的关系。
㈡该设计项目的资源概况
1、矿床地质及构造特征。
2、矿床开采技术条件及水文地质条件。
矿产
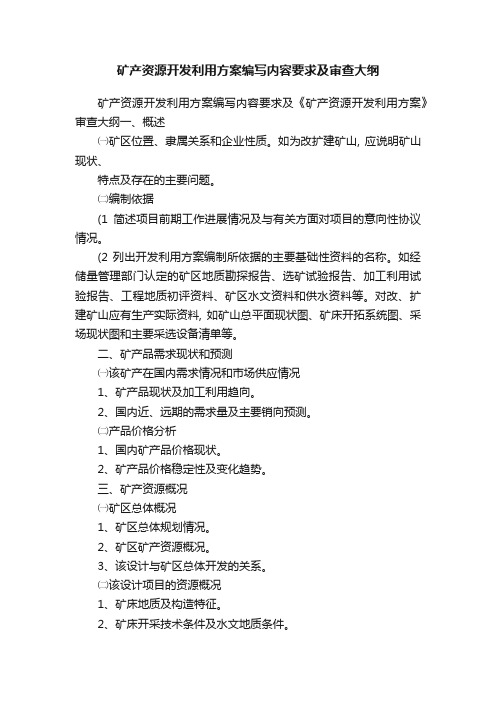
矿产资源开发利用方案编写内容要求及审查大纲
矿产资源开发利用方案编写内容要求及《矿产资源开发利用方案》审查大纲一、概述
㈠矿区位置、隶属关系和企业性质。
如为改扩建矿山, 应说明矿山现状、
特点及存在的主要问题。
㈡编制依据
(1简述项目前期工作进展情况及与有关方面对项目的意向性协议情况。
(2 列出开发利用方案编制所依据的主要基础性资料的名称。
如经储量管理部门认定的矿区地质勘探报告、选矿试验报告、加工利用试验报告、工程地质初评资料、矿区水文资料和供水资料等。
对改、扩建矿山应有生产实际资料, 如矿山总平面现状图、矿床开拓系统图、采场现状图和主要采选设备清单等。
二、矿产品需求现状和预测
㈠该矿产在国内需求情况和市场供应情况
1、矿产品现状及加工利用趋向。
2、国内近、远期的需求量及主要销向预测。
㈡产品价格分析
1、国内矿产品价格现状。
2、矿产品价格稳定性及变化趋势。
三、矿产资源概况
㈠矿区总体概况
1、矿区总体规划情况。
2、矿区矿产资源概况。
3、该设计与矿区总体开发的关系。
㈡该设计项目的资源概况
1、矿床地质及构造特征。
2、矿床开采技术条件及水文地质条件。
矿产
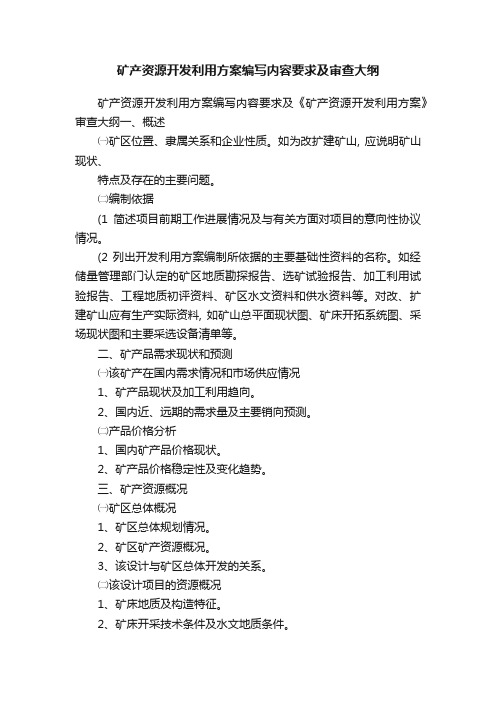
矿产资源开发利用方案编写内容要求及审查大纲
矿产资源开发利用方案编写内容要求及《矿产资源开发利用方案》审查大纲一、概述
㈠矿区位置、隶属关系和企业性质。
如为改扩建矿山, 应说明矿山现状、
特点及存在的主要问题。
㈡编制依据
(1简述项目前期工作进展情况及与有关方面对项目的意向性协议情况。
(2 列出开发利用方案编制所依据的主要基础性资料的名称。
如经储量管理部门认定的矿区地质勘探报告、选矿试验报告、加工利用试验报告、工程地质初评资料、矿区水文资料和供水资料等。
对改、扩建矿山应有生产实际资料, 如矿山总平面现状图、矿床开拓系统图、采场现状图和主要采选设备清单等。
二、矿产品需求现状和预测
㈠该矿产在国内需求情况和市场供应情况
1、矿产品现状及加工利用趋向。
2、国内近、远期的需求量及主要销向预测。
㈡产品价格分析
1、国内矿产品价格现状。
2、矿产品价格稳定性及变化趋势。
三、矿产资源概况
㈠矿区总体概况
1、矿区总体规划情况。
2、矿区矿产资源概况。
3、该设计与矿区总体开发的关系。
㈡该设计项目的资源概况
1、矿床地质及构造特征。
2、矿床开采技术条件及水文地质条件。
矿产
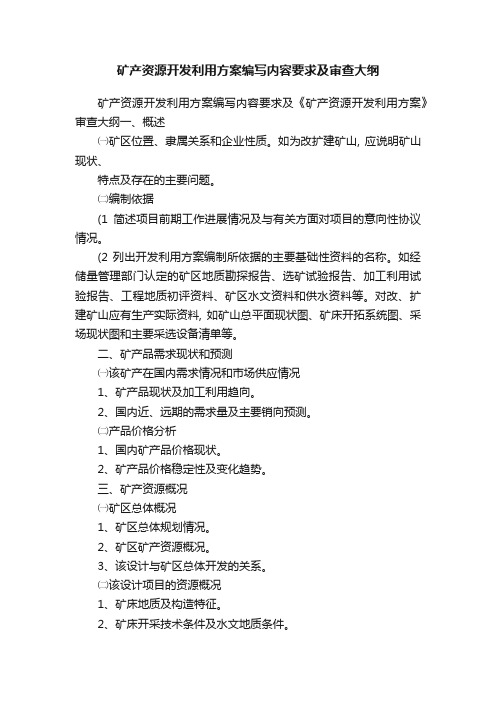
矿产资源开发利用方案编写内容要求及审查大纲
矿产资源开发利用方案编写内容要求及《矿产资源开发利用方案》审查大纲一、概述
㈠矿区位置、隶属关系和企业性质。
如为改扩建矿山, 应说明矿山现状、
特点及存在的主要问题。
㈡编制依据
(1简述项目前期工作进展情况及与有关方面对项目的意向性协议情况。
(2 列出开发利用方案编制所依据的主要基础性资料的名称。
如经储量管理部门认定的矿区地质勘探报告、选矿试验报告、加工利用试验报告、工程地质初评资料、矿区水文资料和供水资料等。
对改、扩建矿山应有生产实际资料, 如矿山总平面现状图、矿床开拓系统图、采场现状图和主要采选设备清单等。
二、矿产品需求现状和预测
㈠该矿产在国内需求情况和市场供应情况
1、矿产品现状及加工利用趋向。
2、国内近、远期的需求量及主要销向预测。
㈡产品价格分析
1、国内矿产品价格现状。
2、矿产品价格稳定性及变化趋势。
三、矿产资源概况
㈠矿区总体概况
1、矿区总体规划情况。
2、矿区矿产资源概况。
3、该设计与矿区总体开发的关系。
㈡该设计项目的资源概况
1、矿床地质及构造特征。
2、矿床开采技术条件及水文地质条件。
矿产
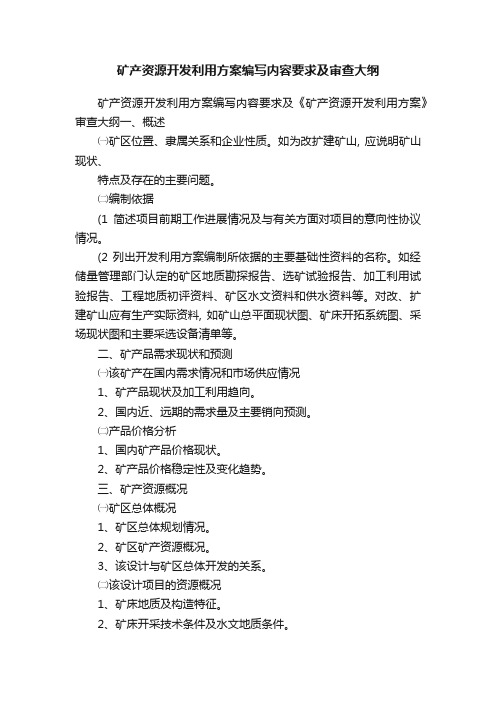
矿产资源开发利用方案编写内容要求及审查大纲
矿产资源开发利用方案编写内容要求及《矿产资源开发利用方案》审查大纲一、概述
㈠矿区位置、隶属关系和企业性质。
如为改扩建矿山, 应说明矿山现状、
特点及存在的主要问题。
㈡编制依据
(1简述项目前期工作进展情况及与有关方面对项目的意向性协议情况。
(2 列出开发利用方案编制所依据的主要基础性资料的名称。
如经储量管理部门认定的矿区地质勘探报告、选矿试验报告、加工利用试验报告、工程地质初评资料、矿区水文资料和供水资料等。
对改、扩建矿山应有生产实际资料, 如矿山总平面现状图、矿床开拓系统图、采场现状图和主要采选设备清单等。
二、矿产品需求现状和预测
㈠该矿产在国内需求情况和市场供应情况
1、矿产品现状及加工利用趋向。
2、国内近、远期的需求量及主要销向预测。
㈡产品价格分析
1、国内矿产品价格现状。
2、矿产品价格稳定性及变化趋势。
三、矿产资源概况
㈠矿区总体概况
1、矿区总体规划情况。
2、矿区矿产资源概况。
3、该设计与矿区总体开发的关系。
㈡该设计项目的资源概况
1、矿床地质及构造特征。
2、矿床开采技术条件及水文地质条件。
- 1、下载文档前请自行甄别文档内容的完整性,平台不提供额外的编辑、内容补充、找答案等附加服务。
- 2、"仅部分预览"的文档,不可在线预览部分如存在完整性等问题,可反馈申请退款(可完整预览的文档不适用该条件!)。
- 3、如文档侵犯您的权益,请联系客服反馈,我们会尽快为您处理(人工客服工作时间:9:00-18:30)。
本技术公开了一种电解铜废液的处理方法,包括以下步骤:浸出、回收铜、除铁铝、回收镍。
本技术的电解铜废液的处理方法萃取分离铜后,采取化学除杂和萃取除杂相结合,不但得到了高纯镍产品,还将氧化铜矿和电解铜废液中的钴、锌、锰等有价金属富集起来,作为副产品。
权利要求书1.一种电解铜废液的处理方法,其特征在于包括以下步骤:(1)浸出:将细磨后氧化铜矿投入反应槽加水调浆,并加入电解铜废液进行常压加热搅拌浸出,控制温度为40-80℃,搅拌速度为200-500r/min,终点pH控制为1.0-3.0,反应时间为2-4h,反应完成后,过滤,得到浸出液和浸出渣;(2)回收铜:使用铜萃取剂将步骤(1)所得浸出液中的铜萃入有机相,分相后得到负载铜有机相和第一萃余液;负载铜有机经2mol/L硫酸溶液反萃后可得纯净的硫酸铜溶液;(3)除铁、铝:先通过加入氧化剂将步骤(2)所得第一萃余液中二价铁氧化成三价铁,再通过加入碱性中和剂调节其PH到3.5-5.0,除去铁和铝,过滤得到滤液和滤渣;(4)回收镍:采用皂化P507有机将步骤(3)所得滤液中Ca、Co、Mn、Zn、Mg以及微量的Fe和Al萃入有机相;分相后得到负载杂质有机相和第二萃余液;第二萃余液即纯净的硫酸镍液。
2.根据权利要求1所述的电解铜废液的处理方法,其特征在于:第(4)步得到的所述第二萃余液经加入碳酸钠沉淀生产碱式碳酸镍产品。
3.根据权利要求1或2所述的电解铜废液的处理方法,其特征在于:第(4)步得到的负载杂质有机相经4级酸洗后用3mol/L硫酸5级反萃,所得反萃液可返回钴湿法冶炼车间用于矿浆浆化或作为副产品外售。
4.根据权利要求3所述的电解铜废液的处理方法,其特征在于:反萃后有机相经3酸洗、2级水洗后可循环使用。
技术说明书一种电解铜废液的处理方法技术领域本技术涉及化工冶金技术领域,特别是一种电解铜废液的处理方法。
背景技术国内现有铜冶炼企业通常采用电解法精炼纯铜,在电解铜过程中,电解液中镍、钴、铁等杂质会逐步富集,当杂质离子富集到一定程度时将会阴极铜的质量,因此需要定期排放电解铜废液。
电解铜废液中硫酸浓度高达170-280g/L,含镍40-60g/L,铜5-10g/L,铁3-8g/L,还含有微量的钴、钙、锌、锰等,给综合回收带来了困难。
目前,一些企业将电解铜废液先进行脱铜处理,然后再从脱铜液中进行蒸发、冷却结晶收集硫酸镍粗产品,这种方法存在能耗高、对设备要求较高、产品杂质含量高等缺点,难以实现利润。
《湖北理工学院学报》2003年第6期名为“利用电解铜废液除杂制硫酸铜的研究”的论文报道了通过添加碱性物质将电解铜废液中和到pH范围内,水解除铁后,依次沉淀铜、镍,最终得到粗氢氧化铜和氢氧化镍产品,此种方式不仅消耗了大量的中和剂,而且产品杂质含量高、附加值少,且其中的钴资源没有得到合理的利用。
中国技术专利CN1472365“电解铜废液处理工艺”公布了一种电解铜废液处理工艺,通过一次或分次加入工业硫酸,进行酸析依次分离出硫酸母液、硫酸铜、硫酸镍,但酸析过程对设备要求较高,且增加了操作人员在生产过程中的风险性,而且缺少除杂工序使得所得产品杂质含量较高,不利于大规模生产。
技术内容本技术的最主要目的在于提供了一种电解铜废液的处理方法,具有方法简单、产品纯度高和成本低廉的特点。
本技术公开了一种电解铜废液的处理方法,包括以下步骤:(1)浸出:将细磨后氧化铜矿投入反应槽加水调浆,并加入电解铜废液进行常压加热搅拌浸出,控制温度为40-80℃,搅拌速度为 200-500r/min,终点pH控制为1.0-3.0,反应时间为2-4h,反应完成后,过滤,得到浸出液和浸出渣;(2)回收铜:使用铜萃取剂将步骤(1)所得浸出液中的铜萃入有机相,分相后得到负载铜有机相和第一萃余液;负载铜有机经 2mol/L硫酸溶液反萃后可得纯净的硫酸铜溶液;(3)除铁、铝:先通过加入氧化剂将步骤(2)所得第一萃余液中二价铁氧化成三价铁,再通过加入碱性中和剂调节其PH到3.5-5.0,除去铁和铝,过滤得到滤液和滤渣;(4)回收镍:采用皂化P507有机将步骤(3)所得滤液中Ca、 Co、Mn、Zn、Mg以及微量的Fe和Al萃入有机相;分相后得到负载杂质有机相和第二萃余液;第二萃余液即纯净的硫酸镍液。
进一步地,所述步骤(1)中,氧化铜矿中硫含量小于0.1wt%,经细磨后-100目的颗粒比例大于90%。
进一步地,所述步骤(2)中,反萃得到的硫酸铜液返回铜电解车间得到金属铜,也可以直接进行蒸发结晶制备硫酸铜产品。
进一步地,所述步骤(4)中,得到的负载杂质有机相经4级酸洗后用3mol/L硫酸5级反萃,所得反萃液可返回钴湿法冶炼车间用于矿浆浆化或作为副产品外售。
进一步地,第(4)步得到的所述第二萃余液经加入碳酸钠沉淀生产碱式碳酸镍产品。
本技术的技术原理在于:利用氧化铜矿消耗电解铜废液中的高浓度硫酸,同时使其中的铜、钴以硫酸盐的形式进入溶液,其中电解铜废液中的二价铁离子可作为还原剂将氧化铜矿中微量的钴还原出来;所得浸出液经铜萃取-反萃后即可得到硫酸铜溶液;所得第一萃余液经水解除铁、铝后,再通过萃取深度除杂,所得第二萃余液即为纯净的硫酸镍溶液;负载杂质有机相经反萃后,所得反萃液因含钴等有价金属溶液可送往钴生产工序。
其中主要化学反应方程式为:CuO+H2SO4=CuSO4+H2OCoOOH+Fe2++4H+=Co2++2H2OCu2(OH)2CO3+2H2SO4=2CuSO4+3H2O+CO2与其他电解铜废液中铜镍回收方法相比,本方法萃取分离铜后,采取化学除杂和萃取除杂相结合,不但得到了高纯镍产品,还将氧化铜矿和电解铜废液中的钴、锌、锰等有价金属富集起来,作为副产品。
附图说明图1是本技术的工艺流程图。
具体实施方式为了使本技术领域的人员更好地理解本技术的技术方案,下面结合实施例及附图对本技术产品作进一步详细的说明。
实施例1本技术公开了一种电解铜废液的处理方法,如图1包括以下步骤:(1)浸出:将细磨后氧化铜矿投入反应槽加水调浆,并加入电解铜废液进行常压加热搅拌浸出,控制温度为80℃,搅拌速度为 500r/min,终点pH控制为2.0,反应时间为2h,反应完成后,过滤,得到浸出液和浸出渣;(2)回收铜:使用铜萃取剂将步骤(1)所得浸出液中的铜萃入有机相,分相后得到负载铜有机相和第一萃余液;负载铜有机经 2mol/L硫酸溶液反萃后可得纯净的硫酸铜溶液;(3)除铁、铝:先通过加入氧化剂将步骤(2)所得萃余液中二价铁氧化成三价铁,再通过加入碱性中和剂调节其PH到5.0,除去铁和铝,过滤得到滤液和滤渣;(4)回收镍:采用皂化P507有机将步骤(3)所得滤液中Ca、 Co、Mn、Zn、Mg以及微量的Fe和Al萃入有机相;分相后得到负载杂质有机相和第二萃余液;第二萃余液即纯净的硫酸镍液。
所述第二萃余液经加入碳酸钠沉淀生产碱式碳酸镍产品。
负载杂质有机相经4 级酸洗后用3mol/L硫酸5级反萃,所得反萃液可返回钴湿法冶炼车间用于矿浆浆化或作为副产品外售。
反萃后有机相经3酸洗、2级水洗后可循环使用。
实施例2本技术公开了一种电解铜废液的处理方法,包括以下步骤:(1)浸出:将细磨后氧化铜矿投入反应槽加水调浆,并加入电解铜废液进行常压加热搅拌浸出,控制温度为60℃,搅拌速度为 350r/min,终点pH控制为1.0,反应时间为4h,反应完成后,过滤,得到浸出液和浸出渣;(2)回收铜:使用铜萃取剂将步骤(1)所得浸出液中的铜萃入有机相,分相后得到负载铜有机相和第一萃余液;负载铜有机经 2mol/L硫酸溶液反萃后可得纯净的硫酸铜溶液;(3)除铁、铝:先通过加入氧化剂将步骤(2)所得萃余液中二价铁氧化成三价铁,再通过加入碱性中和剂调节其PH到4.5,除去铁和铝,过滤得到滤液和滤渣;(4)回收镍:采用皂化P507有机将步骤(3)所得滤液中Ca、 Co、Mn、Zn、Mg以及微量的Fe和Al萃入有机相;分相后得到负载杂质有机相和第二萃余液;第二萃余液即纯净的硫酸镍液。
所述第二萃余液经加入碳酸钠沉淀生产碱式碳酸镍产品。
负载杂质有机相经4 级酸洗后用3mol/L硫酸5级反萃,所得反萃液可返回钴湿法冶炼车间用于矿浆浆化或作为副产品外售。
反萃后有机相经3酸洗、2级水洗后可循环使用。
实施例3本技术公开了一种电解铜废液的处理方法,包括以下步骤:(1)浸出:将细磨后氧化铜矿投入反应槽加水调浆,并加入电解铜废液进行常压加热搅拌浸出,控制温度为40℃,搅拌速度为200r/min,终点pH控制为3.0,反应时间为3h,反应完成后,过滤,得到浸出液和浸出渣;(2)回收铜:使用铜萃取剂将步骤(1)所得浸出液中的铜萃入有机相,分相后得到负载铜有机相和第一萃余液;负载铜有机经 2mol/L硫酸溶液反萃后可得纯净的硫酸铜溶液;(3)除铁、铝:先通过加入氧化剂将步骤(2)所得萃余液中二价铁氧化成三价铁,再通过加入碱性中和剂调节其PH到3.5,除去铁和铝,过滤得到滤液和滤渣;(4)回收镍:采用皂化P507有机将步骤(3)所得滤液中Ca、 Co、Mn、Zn、Mg以及微量的Fe和Al萃入有机相;分相后得到负载杂质有机相和第二萃余液;第二萃余液即纯净的硫酸镍液。
所述第二萃余液经加入碳酸钠沉淀生产碱式碳酸镍产品。
负载杂质有机相经4 级酸洗后用3mol/L硫酸5级反萃,所得反萃液可返回钴湿法冶炼车间用于矿浆浆化或作为副产品外售。
反萃后有机相经3酸洗、2级水洗后可循环使用。
实施例4本技术公开了一种电解铜废液的处理方法,包括以下步骤:(1)浸出:将细磨后氧化铜矿(含Co 0.72%、Ni 0.011%、Cu 23.41%)投入反应槽加水调浆,并按液固比2.4:1mL/g加入电解铜废液,进行常压加热搅拌浸出,控制温度为80℃,搅拌速度为 200r/min,终点pH控制为3.0,反应时间为4h,反应完成后,过滤,得到浸出液和浸出渣;(2)回收铜:配置含20%LIX984的磺化煤油溶液作为萃取体系,通过3级萃取将步骤(1)所得浸出液中的铜萃入有机相,分相后得到负载铜有机相和第一萃余液;所得第一萃余液中Cu<0.01g/L;负载铜有机采用2mol/L硫酸溶液3级反萃;反萃得到的硫酸铜液返回铜电解车间得到金属铜,也可以直接进行蒸发结晶制备硫酸铜产品;反萃后有机相经酸洗再生后循环使用。
(3)除铁、铝:先通过加入总铁量0.4倍氯酸钠将步骤(2)所得第一萃余液中二价铁氧化成三价铁,温度控制在85℃,再通过加入碳酸氢铵调节其pH到5.0,反应2h,过滤得到滤液和滤渣;(4)回收镍:配置含25%P507煤油溶液作为萃取体系,采用 9mol/L氢氧化钠溶液2级皂化后经7级萃取将步骤(3)所得滤液中 Ca、Co、Mn、Zn、Mg、Fe和Al等杂质萃入有机相;分相后得到负载杂质有机相和第二萃余液;所得第二萃余液中Ca、Co、Mn、Zn、Mg、 Fe和Al等金属离子均<4mg/L,经加入碳酸钠沉淀生产碱式碳酸镍产品。