硅橡胶补强填料的研究进展
纳米粒子增强室温硫化硅橡胶力学性能的研究进展
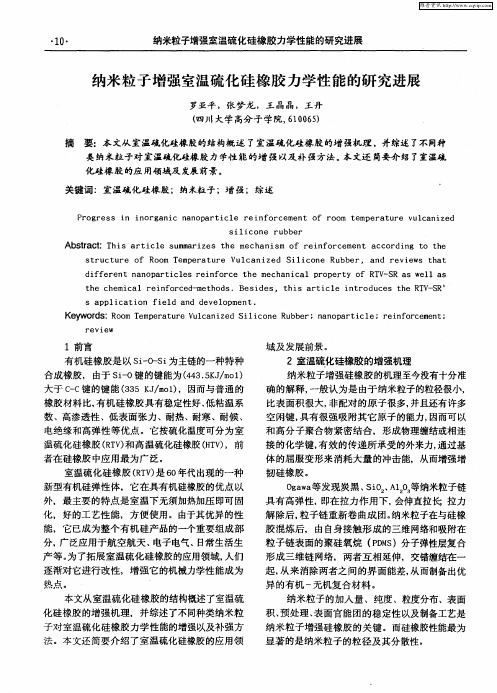
・
1. 0
纳米粒子增强室温硫化硅橡胶 力学性能的研究进展
纳米 粒 子 增强室温硫化 硅 橡 胶 力 学性 能 的研 究进展
罗亚平 ,张梦 龙 ,王 晶 晶 ,王 丹
( 四川大学 高分子学院, 10 5 6 06)
摘 要 :本 文从 室 温硫 化硅橡 胶的结 构概 述 了室温 硫 化硅 橡 胶 的增 强机 理 ,并综述 了不 同种
产 等 。 了拓展 室 温硫 化 硅 橡胶 的应用领 域 , 为 人们 逐 渐对 它进 行 改性 ,增 强它 的机 械力学性 能成为
热点。
本文从室温硫化硅橡胶的结构概述 了室温硫 化硅橡胶的增强机理,并综述了不同种类纳米粒 子 对 室 温硫化 硅 橡胶 力 学 性 能的增 强以及补 强方 法 。本文还 简 要介 绍 了 室 温硫化 硅橡胶 的应 用领
具有高弹性, 即在拉力作 用下, 会伸直拉长 拉力 ; 解 除后 , 粒子 链 重新 卷 曲 成 团 。 米粒 子在 与硅橡 纳 胶混炼后, 由自身接触形 成的三维网络和吸附在 粒子链表面的聚硅氧烷 ( DS P M )分子弹性层复合 形成三维链网络,两者互相延伸,交错缠结在一 起, 从来消除两者之间的界 面能差, 从而制备出优 异 的 有机 一无机复 合 材 料 。
室温硫化硅橡胶 的性 能影响,发现得到的复合材
料具 有 了 以前 没有 的 良好 的 静 电屏 蔽性 能,且 二 氧化 钛 粒 子有 较 明显 的补 强 作 用 。
3. 其 他 纳 米粒 子增 强 R V S 3 T-R
效果好 , 所得硅橡胶的各 种性 能都非常好, 是硅橡 胶 补强 填 料 中研 究 最 多 、 最成 熟 的一种 。 沉淀法 白 炭 黑含 水 量较 大 、 子 较 粗 、比表面积 低 , 粒 制得 的
有机硅胶粘剂的研究进展

有机硅胶粘剂的研究进展肖凯斐(西安工业大学北方信息工程学院,机电信息系,陕西省西安市710032)摘要 :综述了有机硅胶粘剂的组成、种类、性能及其应用,并对硅橡胶胶粘剂在粘接性、导热性、固化性能的研究进展进行了叙述。
关键词 :硅橡胶硅树脂有机硅压敏胶胶粘剂Study on high temperature-resistant anaerobicadhesiveXiaokaifei( Xi'an Technological University North Institute Of InformationEngineering,Mechanical and electrical information system ,Shan'xiProvince,Xi'an 710032)Abstract: The compositions, categories, properties and applications of organosilicon adhesives were reviewed. Moreover , the bonding ability, heat conductivity and curing of silicone rubber type adhesive w ere introduced.Keywords:Silicone rubber Silicone resin Organosilicon pressure sensitive adhesive Adhesive有机硅材料是一类性能优异、功能独特、用途极广的新材料,是高分子新型材料中产业规模最大的材料之一,是一种关系着技术革新、国防现代化、国民经济发展及人民生活水平提高的新材料。
有机硅聚合物是含有硅元素的众多高分子化合物的总称,因主链以硅氧键(-Si-O-)组成,侧链可链接各种有机基团,具有无机和有机聚合物的双重性能。
水化硅酸钙粉体对硅橡胶的补强作用
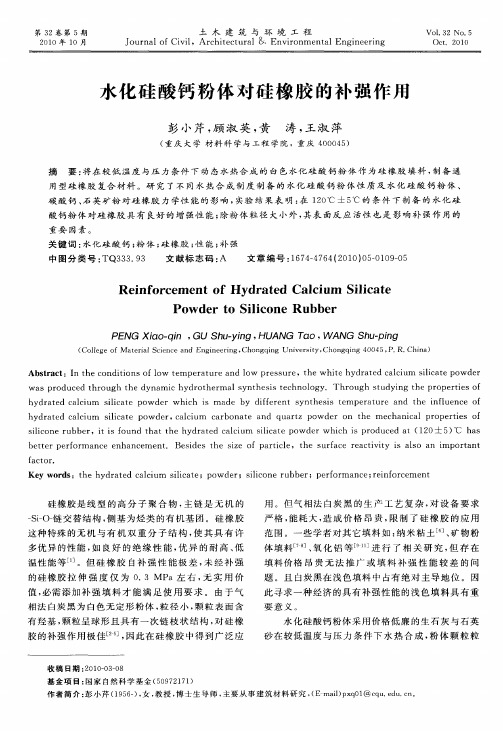
T 8 平 均 粒 径 1 5 m。 3, . 5“
1 2 实 验 仪 器 .
混炼 和硫 化设 备 及操 作 程 序 》 。混炼 时 原 料 的添 加 顺序 为 : 胶一试 验 粉 体一 白炭 黑 一结 构控 制 剂 一 生
1 1 1 水 热 合 成 原 材 料 生 石 灰 , 地 : 庆 山 洞 . . 产 重
村 , 至平 均 粒 径 1 4 m; 英 砂 , 地 : 庆 云 磨 .9 石 产 重
阳 , 至 平 均 粒 径 1 9 m。 磨 .6 1 1 2 制 备 硅 橡 胶 复 合 材 料 的 原 材 料 甲 基 乙 烯 . . 基 硅 橡 胶 1 02型 , 构 控 制 剂 , 昊 晨 光 化 工 研 究 1— 结 中 院 ; 气 相 法 白炭 黑 AS 2 0 沈 阳 化 工 股 份 有 限 公 2 一0 , 司; 化剂 , 苏省海 安县东 洋化 工 ; 性碳 酸钙 , 硫 江 改 重
多 优异 的性 能 , 良好 的绝 缘 性 能 , 异 的耐 高 、 如 优 低 温性 能 等_ 。但硅 橡 胶 自补 强 性 能 极 差 , 经 补 强 1 ] 未 的硅橡胶 拉 伸 强 度 仅 为 0 3MP . a左 右 , 实 用 价 无 值, 必需 添加 补 强 填料 才 能 满 足使 用 要 求 。 由于 气
的补强作用 。
1 4 硅 橡 胶 复 合 材 料 的 制 备 .
l 实 验 部 分
1 1 原 材 料 .
5种试验 粉体 制备 硅橡 胶 复合 材 料 的配方 见 表
2 。另增加 了 1 不添 加试验 粉体 , 组 其他 条件 相 同 的
纳米二氧化硅在硅橡胶中的补强作用
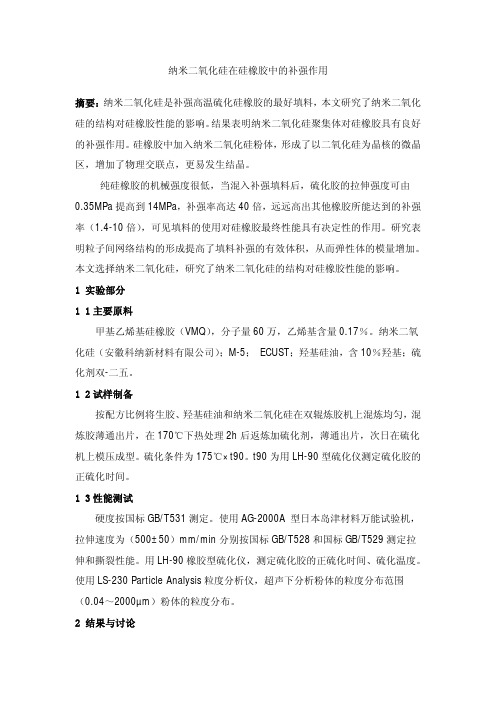
纳米二氧化硅在硅橡胶中的补强作用摘要:纳米二氧化硅是补强高温硫化硅橡胶的最好填料,本文研究了纳米二氧化硅的结构对硅橡胶性能的影响。
结果表明纳米二氧化硅聚集体对硅橡胶具有良好的补强作用。
硅橡胶中加入纳米二氧化硅粉体,形成了以二氧化硅为晶核的微晶区,增加了物理交联点,更易发生结晶。
纯硅橡胶的机械强度很低,当混入补强填料后,硫化胶的拉伸强度可由0.35MPa提高到14MPa,补强率高达40倍,远远高出其他橡胶所能达到的补强率(1.4-10倍),可见填料的使用对硅橡胶最终性能具有决定性的作用。
研究表明粒子间网络结构的形成提高了填料补强的有效体积,从而弹性体的模量增加。
本文选择纳米二氧化硅,研究了纳米二氧化硅的结构对硅橡胶性能的影响。
1.实验部分1.1主要原料甲基乙烯基硅橡胶(VMQ),分子量60万,乙烯基含量0.17%。
纳米二氧化硅(安徽科纳新材料有限公司);M-5;ECUST;羟基硅油,含10%羟基;硫化剂双-二五。
1.2试样制备按配方比例将生胶、羟基硅油和纳米二氧化硅在双辊炼胶机上混炼均匀,混炼胶薄通出片,在170℃下热处理2h后返炼加硫化剂,薄通出片,次日在硫化机上模压成型。
硫化条件为175℃×t90。
t90为用LH-90型硫化仪测定硫化胶的正硫化时间。
1.3性能测试硬度按国标GB/T531测定。
使用AG-2000A 型日本岛津材料万能试验机,拉伸速度为(500±50)mm/min分别按国标GB/T528和国标GB/T529测定拉伸和撕裂性能。
用LH-90橡胶型硫化仪,测定硫化胶的正硫化时间、硫化温度。
使用LS-230 Particle Analysis粒度分析仪,超声下分析粉体的粒度分布范围(0.04~2000µm)粉体的粒度分布。
2.结果与讨论2.1纳米二氧化硅存在的结构形式如图1所示,纳米二氧化硅的原生粒子为2-20nm的球形粒子,球形粒子间通过化学键联结成50-500nm的珍珠串结构的支链聚集体,此结构的聚集体不能通过剪切等机械力分散,是补强硅橡胶的最基本单元,聚集体间又通过氢键形成了结构松散的网状的附聚体。
硅橡胶性能及其研究进展
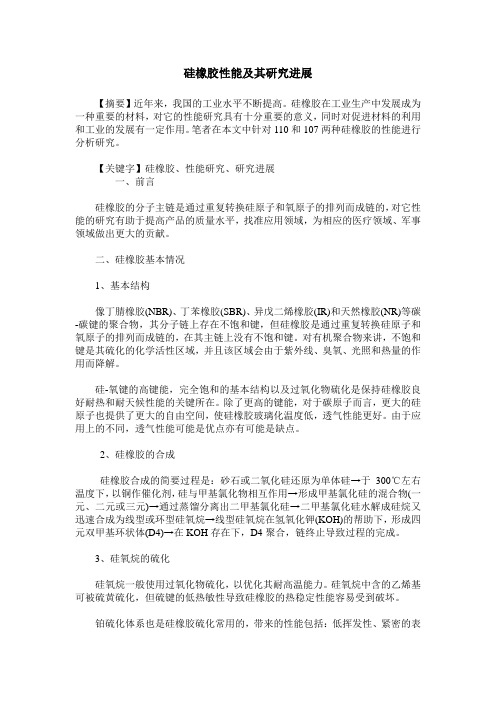
硅橡胶性能及其研究进展【摘要】近年来,我国的工业水平不断提高。
硅橡胶在工业生产中发展成为一种重要的材料,对它的性能研究具有十分重要的意义,同时对促进材料的利用和工业的发展有一定作用。
笔者在本文中针对110和107两种硅橡胶的性能进行分析研究。
【关键字】硅橡胶、性能研究、研究进展一、前言硅橡胶的分子主链是通过重复转换硅原子和氧原子的排列而成链的,对它性能的研究有助于提高产品的质量水平,找准应用领域,为相应的医疗领域、军事领域做出更大的贡献。
二、硅橡胶基本情况1、基本结构像丁腈橡胶(NBR)、丁苯橡胶(SBR)、异戊二烯橡胶(IR)和天然橡胶(NR)等碳-碳键的聚合物,其分子链上存在不饱和键,但硅橡胶是通过重复转换硅原子和氧原子的排列而成链的,在其主链上没有不饱和键。
对有机聚合物来讲,不饱和键是其硫化的化学活性区域,并且该区域会由于紫外线、臭氧、光照和热量的作用而降解。
硅-氧键的高键能,完全饱和的基本结构以及过氧化物硫化是保持硅橡胶良好耐热和耐天候性能的关键所在。
除了更高的键能,对于碳原子而言,更大的硅原子也提供了更大的自由空间,使硅橡胶玻璃化温度低,透气性能更好。
由于应用上的不同,透气性能可能是优点亦有可能是缺点。
2、硅橡胶的合成硅橡胶合成的简要过程是:砂石或二氧化硅还原为单体硅→于300℃左右温度下,以铜作催化剂,硅与甲基氯化物相互作用→形成甲基氯化硅的混合物(一元、二元或三元)→通过蒸馏分离出二甲基氯化硅→二甲基氯化硅水解成硅烷又迅速合成为线型或环型硅氧烷→线型硅氧烷在氢氧化钾(KOH)的帮助下,形成四元双甲基环状体(D4)→在KOH存在下,D4聚合,链终止导致过程的完成。
3、硅氧烷的硫化硅氧烷一般使用过氧化物硫化,以优化其耐高温能力。
硅氧烷中含的乙烯基可被硫黄硫化,但硫键的低热敏性导致硅橡胶的热稳定性能容易受到破坏。
铂硫化体系也是硅橡胶硫化常用的,带来的性能包括:低挥发性、紧密的表面硫化、在任何介质中的超快硫化,铂硫化体系具有比传统过氧化硫化对应物略低的热稳定性能。
室温硫化硅橡胶增强改性的研究进展

a d o fi at o wa e n m di c i n ys ar al O r o ed. t as p n ou t m n S p op s A l t. oi t t he ai di e ti n r c o
o t e e e c ou r m t pe at r V ca z Si i o ru b . f h r s ar h ab t oo em r u e ui ni ed 1 c ne b er
维普资讯
广东橡胶)2 0 年 第 1 期 ) 07 0
室温 硫化硅 橡胶 增强 改性 的研 究进展
f r g e s n e n o c m e n o f c t o f r o t m e a u e u c n e P o r s i r i f r e n t a d m i a i n O o m e p r t r v l a i d z
Si n u b ac or ng 1j Co er b er c di to ts i me h c ani m s of ei fo c e r n r em nt. a d lS s m a n a O u m ~ ri e t e r r s n hi p r z d h p og es i t S a t,Th RT —SR t pe e V— S y s,p Of m nc a an a e r Or e e dv t g s
量 的增 加 ,R V T 硅橡 胶 的硬 度 、 伸 强度 、 长率 拉 伸 和撕裂 强 度 均呈 上 升趋 势 ,当添加 2 份处理 气相 5
RV T 硅橡胶的增强
RV T 硅橡胶为非晶结构,其分子间的引力较
小, 没有 经补 强 的硫化 硅橡 胶的 强度较 低 , 拉伸 强
填料在硅橡胶改性中的应用

Apr. ,2020Vol.37,No.22020 年 4 月第37卷第2期长治学院学报Journal of Changzhi University 填料在硅橡胶改性中的应用张龙(长治学院电子信息与物理系,山西长治 046011)摘要:传统硅橡胶在耐热性能、力学性能等方面存在缺陷,严重制约了其进一步发展和应用。
鉴于此,对硅橡胶性能进行改善和提高成为一项重要的工作。
相关研究提出的许多方法取得了良好效果,其中, 使用白炭黑、碳纳米管、石墨烯、POSS 等填料对硅橡胶改性的研究进展迅速,硅橡胶的一些特性得到了大幅改善和提高。
关键词:填料;硅橡胶;改性;应用中图分类号:0472 文献标识码:A 文章编号:1673-2014( 2020 )02-0020-07引言硅橡胶是一种被广泛使用的高性能聚合物弹性体,其分子链兼具无机与有机性质,拥有优良的 物理和化学特性[1-3],比如抗高低温、绝缘性、耐紫外 辐射、阻燃性、耐候性、耐化学性及化学稳定性冋,这主要归因于比C-C 键的键能(345.7 kJ/mol)强的Si-O 键的键能(443.7 kJ/mol)和较高的Si-O 键离 子化特性[9-11]。
多年来,随着相关基础研究、技术开发以及应用研究所的进展,已经在日常生活、电子 电器、汽车工业、航空航天产业、半导体工业以及医疗器械等领域得到了广泛应用(如图1所示)[12-15]o在电子电器应用方面,需要将某些电子元器件进行包封、密封、灌封等以实现防潮、防水、防尘、 防震等目的,这就需要用到电子封装胶,常见的电子封装胶主要有有机硅、聚氨酯、环氧树脂等[16]o 硅 橡胶因其优异的性能,在电子电器行业得到了广泛 应用。
传统硅橡胶在力学性能、耐热性能、突出的粘 接性能和耐老化性能等方面尚显不足[6, 17,18]o 常用的改性方法有使用填料、对硅橡胶主链进行接枝或 进行交联反应等[319],其中通过在硅橡胶中增加填料 来实现改性,已经取得了极大的研究进展。
白炭黑补强硅橡胶机理

白炭黑补强硅橡胶机理白炭黑是一种常用的填料,可以用来补强硅橡胶材料。
它具有高比表面积、优异的增强效果和抗老化性能,因此被广泛应用于橡胶制品的生产中。
补强硅橡胶的机理主要包括物理机械作用和化学作用两个方面。
首先,白炭黑的高比表面积能够提供更多的接触面积,增加与硅橡胶的物理结合力。
其次,白炭黑的颗粒形状和尺寸能够增加硅橡胶的机械强度,提高其抗拉强度和耐磨性。
在物理机械作用方面,白炭黑填料与硅橡胶基体之间形成了一种物理上的键合关系。
白炭黑颗粒的高比表面积使其能够与硅橡胶分子链相互作用,形成一种物理上的吸附作用。
这种吸附作用能够增加硅橡胶的黏附能力和内聚力,使其具有更好的拉伸性能和耐磨性。
在化学作用方面,白炭黑填料还能与硅橡胶基体发生化学反应,增强其化学键合力。
白炭黑的表面含有许多活性基团,可以与硅橡胶中的官能团发生反应,形成化学键。
这种化学键能够提高硅橡胶的耐热性、耐油性和耐腐蚀性,使其在复杂的工作环境中具有更好的稳定性和耐用性。
除了物理机械作用和化学作用,白炭黑还能够通过改变硅橡胶的微观结构来提高其性能。
白炭黑填料的加入可以改变硅橡胶的晶粒尺寸和分布,使硅橡胶具有更细密的结构和更均匀的分布。
这种微观结构的改变能够提高硅橡胶的物理力学性能,使其具有更好的弹性和韧性。
总的来说,白炭黑补强硅橡胶的机理是通过物理机械作用、化学作用和微观结构调控三个方面来实现的。
白炭黑的高比表面积和颗粒形状能够增加硅橡胶的物理强度和黏附能力,而其表面的活性基团则能够与硅橡胶发生化学反应,增强其化学性能。
此外,白炭黑的加入还能够改变硅橡胶的微观结构,进一步提高其性能。
因此,白炭黑作为一种常用的填料,能够有效地补强硅橡胶材料,提高其综合性能,广泛应用于橡胶制品的生产中。
功能型液体硅橡胶的研究进展_张飞豹
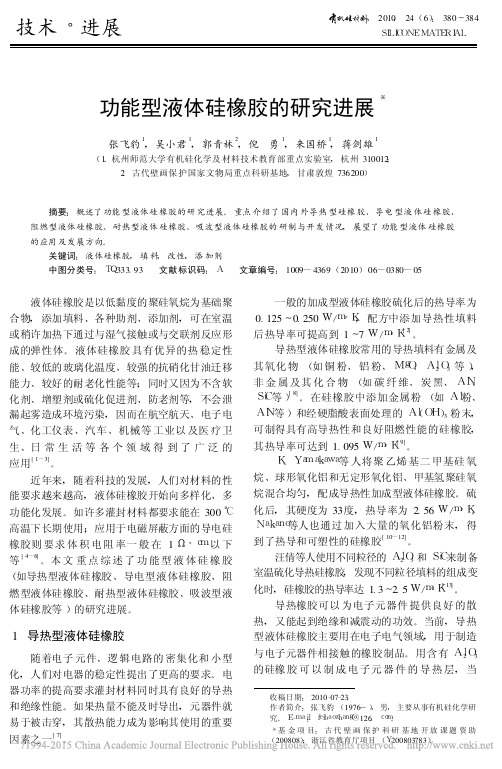
5 吸波型液体硅橡胶
随着电子 、 计算机与电信技术的迅猛发展及 广泛应用 , 电磁环境也日趋丰富和复杂 , 由于电 磁波辐射而导致的信息泄露事件时有发生 , 直接 威胁到国家的政治 、 经济 、 军事的安全 。 因此 , 世界各国科学家采用各种技术手段来抑制或消除 电磁辐射 。 最通用的方法 就是对电磁波 进行屏 蔽 , 因而促进了电磁屏蔽材料的发展 。
· 382 ·
灌封材料 、 密封 材料都要求能在 300 ℃以上长期使用 。
杨始燕等经过长期的研究合成了一种聚硅氮 烷交联剂 (KH-CL), 它可在非催化条件下发生 交联反应 , 并且可消除体系中残余的或由氧化反 应产生的硅羟基和水等 , 从而消除或延缓硅橡胶 的主链降解, 大幅度提高耐温性能。这种名为 KH-CL-RTV的硅橡胶在 350 ℃氮气中加热 24 h 的质量损失率相当于用原硅酸乙酯交联体系的硫化 胶在 200 ℃老化后的质量损失率 , 并且在 350 ℃氮 气中老化 24 h后的力学性能几乎不变 [ 32] 。
液体硅橡胶是以低黏度的聚硅氧烷为基础聚 合物 , 添加填料 、 各种助剂 、 添加剂 , 可在室温 或稍许加热下通过与湿气接触或与交联剂反应形 成的弹性体 。 液体硅橡胶 具有优异的热 稳定性 能 、 较低的玻璃化温度 、 较强的抗硝化甘油迁移 能力 、 较好的耐老化性能等 ;同时又因为不含软 化剂 、 增塑剂或硫化促进剂 、 防老剂等 , 不会泄 漏起雾造成环境污染 , 因而在航空航天 、 电子电 气 、 化工仪表 、 汽车 、 机械等 工业以 及医 疗卫 生、日 常生 活等 各个领 域得 到了 广泛 的 应用[ 1 -3] 。
气相二氧化硅对硅橡胶的补强机理
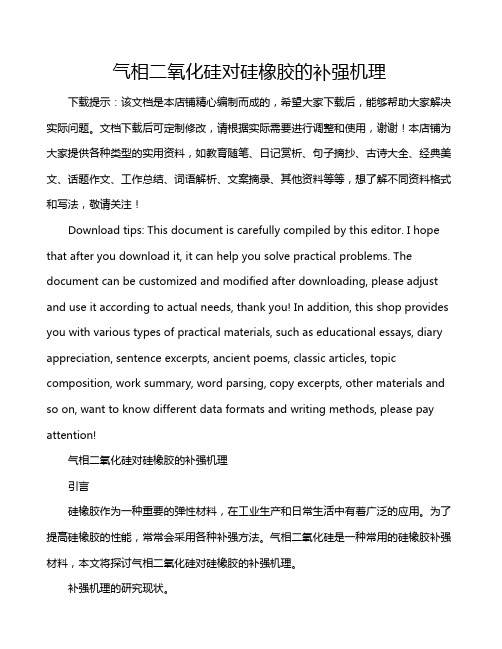
气相二氧化硅对硅橡胶的补强机理下载提示:该文档是本店铺精心编制而成的,希望大家下载后,能够帮助大家解决实际问题。
文档下载后可定制修改,请根据实际需要进行调整和使用,谢谢!本店铺为大家提供各种类型的实用资料,如教育随笔、日记赏析、句子摘抄、古诗大全、经典美文、话题作文、工作总结、词语解析、文案摘录、其他资料等等,想了解不同资料格式和写法,敬请关注!Download tips: This document is carefully compiled by this editor. I hope that after you download it, it can help you solve practical problems. The document can be customized and modified after downloading, please adjust and use it according to actual needs, thank you! In addition, this shop provides you with various types of practical materials, such as educational essays, diary appreciation, sentence excerpts, ancient poems, classic articles, topic composition, work summary, word parsing, copy excerpts, other materials and so on, want to know different data formats and writing methods, please pay attention!气相二氧化硅对硅橡胶的补强机理引言硅橡胶作为一种重要的弹性材料,在工业生产和日常生活中有着广泛的应用。
加成型硅橡胶用补强填料的研究进展

加 成 型 硅 橡 胶 是 指 含 乙烯 基 的 聚 硅 氧 烷 ( 称基胶 )与交 联剂 含 氢硅 油在 铂 催 化剂 作 用 简
淀 法 白 炭 黑 代 替 部 分 气 相 法 白 炭 黑 以 降 低
成本 。
下 ,于一定 温度 下通过 硅氢 加成反应 形成 的具 有
三维 网状结 构 的 弹性 体 。与 缩 合 型硅 橡胶 相 比 , 加成 型硅橡 胶具 有硫 化 过 程 中没 有 副 产 物产 生 、 收缩率极 小 、能深 层硫化 、催 化剂用 量少 、交联 密度 和硫 化 速 度 易 于控 制 、综 合 性 能 优 异 等 优
白炭黑 对 加 成 型 液 体 硅 橡 胶 具 有 较 好 的增 强 效
果 ,拉 伸强度 可达 4 9MP ,撕裂 强度 8K / . a N m, 扯 断伸 长率 1 5 1 。 5 % 2 j
1 白炭 黑
加 成型硅 橡胶 最主要 的补 强手段 是添加 白炭
黑 。常用 的白炭 黑分 为气相 法和沉 淀法 两类 。气
・
20 ・ l
哺 - | 材 斟 g l .
第2 卷 5
时 ,习惯上称 为 甲基 MQ硅 树脂 ;当部 分 R为乙 烯基或 H 时 ,则 分 别 称 为 甲基 乙烯 基 MQ硅 树
脂或 甲基氢基 M Q硅 树 脂 。M Q硅 树 脂 的物 理 性
氧烷链 节 的 甲基 乙烯基 MQ硅树脂 ,通 过调节 其
述 了其 补 强 机 理 和 加 成 型硅 橡 胶 补 强 的发 展 方 向。
关键词 :加成 ,硅橡胶 ,白炭黑 ,M Q硅树脂 ,有机 蒙脱土
中图 分 类 号 :T 3 39 Q 3.3 文 献 标 识 码 :A 文 章 编 号 :10 4 6 (0 1 3— 2 9— 4 0 9— 3 9 2 1 )0 0 0 0
纳米活性碳酸钙对室温硫化硅橡胶补强作用研究

对硅 橡胶 材料 的补强机 理 等方 面 的相关研 究 尚不
充分 ,文 献数 量也 相对 较少 。因此 ,有必 要进 一
步研 究纳 米碳 酸 钙对硅 橡胶 的补 强 。本 实验 选取 4种纳 米 活性碳 酸 钙作 补强 填 料 ,分 别 制 备 了脱 醇 型单 组分 室温 硫 化 ( R T V一1 ) 硅 橡 胶 。从 对
仪 :N i c o l e t i S 1 0 , 美 国 赛 默 飞 公 司 ;热 失 重 ( T G) 分析仪 :Q 5 o o,美 国 T A公 司 ;x 射线 衍
射仪 ( X R D) :R i g a k u D / M a x一1 1, 日本 理 学公
司 ;扫 描 电 镜 :Hi t a c h i S一4 8 0 0 , 日本 日立 公 司 ;电子 万能试 验 机 :A G S—J , 日本 岛 津 公 司 ;
测 试
1 实验
1 . 1 主要原 料及 仪器
,
收 稿 日期 :2 0 1 6— 0 9—2 8 。 作者简介 :王天强 ( 1 9 8 5 一) ,男 ,博士 ,主要从事硅橡胶 的开 发 及 应 用 研 究 。E 。 m a i l :w t q 1 9 8 5 1 1 1 0 @1 6 3 . c o m。
胶) :黏 度 2 0 0 0 0 m P a ・ s ,瓦 克 化 学 有 限公 司 ; 纳米 活性碳 酸 钙 :市售 ,1 粉料 产 自山西 兰花 华 明纳 米材 料股 份有 限公 司 ,2 、3 、4 粉 料分 别 产 自其 它 不 同厂 家 ;二 月 桂 酸 二 丁 基 锡 :工 业
的胶料稠度越 高,对硅橡胶 的补 强效果越显著 ;同时 ,填料 自身形貌越规整 、在硅橡胶 中的分散性越 好也会
改性凹凸棒土补强硅橡胶的性能研究
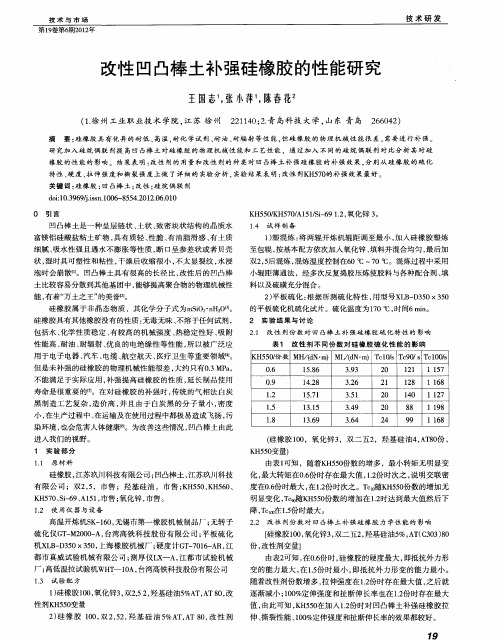
寿命是很重要 的 。在对硅橡胶 的补强时 , 传统 的气相法 白炭
黑制造 工艺复杂 , 造价高 , 并且 由于 白炭 黑 的分 子量小 , 密度 小, 在生产过程 中、 在运输及在使用过程 中都极易造成飞扬 , 污
15 . 18 _
1 .5 31 1 .9 36
34 .9 36 .4
技 术 与 市场
第 1卷第6 0 2 9 期2 1 年
技 术 研 发
改性 凹凸棒 土补强硅橡胶 的性能研 究
王国志’张小萍 , , 陈舂花
(. 州工业 职业技 术 学院 , 1 徐 江苏 徐 州 2 1 4 ;. 岛科 技 大 学, 东 青 岛 2 64 ) 2 10 2青 山 60 2
12 使 用 仪 器 与 设 备 .
用于 电子 电器 、 车、 汽 电缆 、 航空航天 、 医疗 卫生等重要领域H 。
但是未补强的硅橡胶的物理机械性能很差 , 大约只有03 a . MP , 不能满足于实际应用 , 补强提高硅橡胶 的性质 , 延长制 品使用
K 5 o份数 H 5/ MW (N m ML ( m a ・1 / N・ 1 d
06 . 09 .
12 .
1/ T 9 / c O/ 0 c 0 ST 1os s
2 0 2 1
2 0
1 .6 58 1 .8 42
1. 571
39 .3 32 .6
351 .
11 2 18 2
1 40
Байду номын сангаас
117 5 118 6
1 2 1 7
2 实 验 结 果与 讨 论 21 改 性 剂份 数 对 凹 凸棒 土补 强硅 橡 胶 硫 化特 性 的影 响 . 表 1 改 性 剂 不 同份 数 对 硅 橡胶 硫 化 性 能 的 影 响
加成型液体硅橡胶合成及其补强因素的研究 (1)
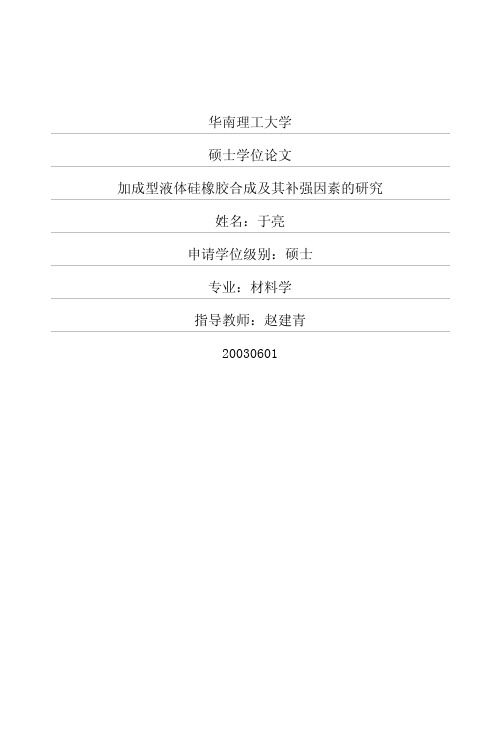
华南理工大学硕士学位论文加成型液体硅橡胶合成及其补强因素的研究姓名:于亮申请学位级别:硕士专业:材料学指导教师:赵建青20030601摘要摘要本文对端乙烯基聚二甲基硅氧烷的合成过程和硫化过程,以及加成型液体硅橡胶补强因素进行了研究。
全文共分三部分,第一部分为端乙烯基聚二甲基硅氧烷合成催化剂和合成动力学的分析;第二部分为影响端乙烯基聚二甲基硅氧烷硫化时间各因素的研究;第三部分为影响加成型液体硅橡胶力学性能各因素的研究。
I发现合成端乙烯基聚二甲基硅氧烷的两种常用催化剂KOH和Me4NOH有非常不同的封端剂利用率,分别为52.1%和71.9%。
对两种催化剂下聚合反应的动力学进行了研究,从分子结构的角度解释了动力学曲线中出现分子量峰值的原因。
结合催化剂的不同后处理方式确定了KOH和Me。
NOH的较合适的反应温度分别为145℃和110℃。
并建立了本试验条件下产物分子量与粘度之间的拟合公式lgn=4.3519Mn--16.24。
JI研究了端乙烯基聚二甲基硅氧烷在硫化过程中交联剂、催化剂和抑制剂对胶料硫化时间的影响。
发现交联剂的最佳比例是使Si.H:Si—Vi处于1.6-1.8:1。
催化剂的添加量以10ppm为宜,过多或过少都会增长硫化时问。
抑制剂能够有效的增加硫化时间。
当催化剂为10ppm,抑制剂添加0.2%时胶料有较合适的硫化时间。
III研究了影响加成型液体硅橡胶力学性能的各种因素。
发现基础胶料的数均分子量、分子量分布和乙烯基含量分别为42000、1.6左右和0.12~0.16%时胶料有最好的力学性能。
石英粉是硅橡胶降低成本的廉价填料,但由于相容性不好,使填充胶料的力学性能下降很多,必须经过偶联剂处理使用。
通过电镜发现偶联剂可以有效提高填料和胶料的相容性。
而且由于乙烯基三甲氧基硅烷偶联剂中含有的乙烯基可以在硫化过程中参加交联反应,增加填料和胶料的结合,所以用它处理的填料有更高的撕裂强度等力学性能。
石英粉可以与白炭黑并用作为硅橡胶的补强填料。
二氧化硅在硅橡胶中的补强机理

二氧化硅(SiO2)在硅橡胶中起到了补强作用,主要有以下几个机理:
1.填充效应:二氧化硅作为一种填充剂,能够填充橡胶基体中的空隙和孔隙,增加材料的
密实程度。
填充效应提高了硅橡胶的硬度和抗拉强度。
2.界面相互作用:二氧化硅与硅橡胶基体之间形成物理或化学吸附的界面,这种相互作用
可以增加硅橡胶的力学强度和耐磨性。
界面相互作用还可以防止填料的分散和沉淀,提高橡胶制品的稳定性。
3.增加粘合强度:二氧化硅表面常常经过特殊处理,例如使用有机硅偶联剂对其进行改性。
这样处理后的二氧化硅能够与硅橡胶基体更好地结合,并增加粘合强度。
4.刚性增强:二氧化硅具有较高的硬度和刚性,加入适量的二氧化硅可以增加硅橡胶的刚
性和弹性模量。
这对于需要较高刚性和抗变形能力的硅橡胶制品非常重要。
5.抗老化和耐热性提升:二氧化硅具有优异的抗氧化性质,能够有效阻止硅橡胶材料的老
化过程。
此外,二氧化硅还能增强硅橡胶的耐热性,使其在高温条件下保持稳定性能。
总的来说,二氧化硅在硅橡胶中通过填充效应、界面相互作用、粘合强度增加、刚性增强以及抗老化和耐热性提升,起到了补强作用,提高了硅橡胶的力学性能和耐久性。
国外硅橡胶补强技术进展

胶 , 其 物 理 机械 性 能 达到 应 用 的要 求 , 为硅 橡 使 成
胶 产 品 开 发 中的关 键 步 骤 。
1 发 展 现 状
自从 1 4 9 5年 高 温 硫 化 二 甲 基 硅 橡 胶 首 先 问
世 以来 , 橡 胶 的性 能 与应 用 均 已有 了 长 足的 发 硅
率和 较 低 的 密 度 。
裹 1 膏 强 度 、 透 明 液 体 硅 橡 胶 的 性 能 参 数 高
收 稿 日期 : 0 2 0 . 9 2 0 .5 1
棋考 料学院在读硕士生 ) 河南开封市人, 介: 亮( 7 一 , 于 1 8 男, 9 华南理工大学
,
主攻方 向为硅橡胶材料的研尧开
补强 白炭 黑 ) 撕 裂 强度 可达 4 , 0~5 N m。② 在 0k /
乙烯基 硅橡胶 中加 入 高 乙烯 基 含 量 的低 相 对 分 子
质量 聚硅氧烷 ( 俗称 C胶 ) 以 4 , 白炭黑 为 补强 剂 、
化 了吸 附层 内分 子 问 的 吸引 力 ; 填料 表 面基 团 ( 如 s0 表面 硅 羟基 ) 可 与橡 胶 链 形 成 强 的 化学 键 。 i’ 还 拉 伸强 度 、 裂强 度等 破坏力 学参数 主 要 与强 的化 撕 学 键数 量有 关 。因此对 硅橡 胶 的补强 来说 , 但要 不
活 性 , 够与 硅橡 胶链 形成 一定 的化学 键 。例 如 未 能
经处 理 的 SO i 2的表 面 含 有 大量 的硅 羟基 , 为 补 作
的价格 相 当昂贵 , 大大 增加 了成本 。和有 机橡 胶 相 比 , 强后 的硅橡 胶虽 然在 常温 下的 机械 强度 仍不 补 如天 然橡胶 、 丁苯 橡胶等 , 由于 其耐 热 性好 , 以 但 所
加成型液体硅橡胶补强体系优化
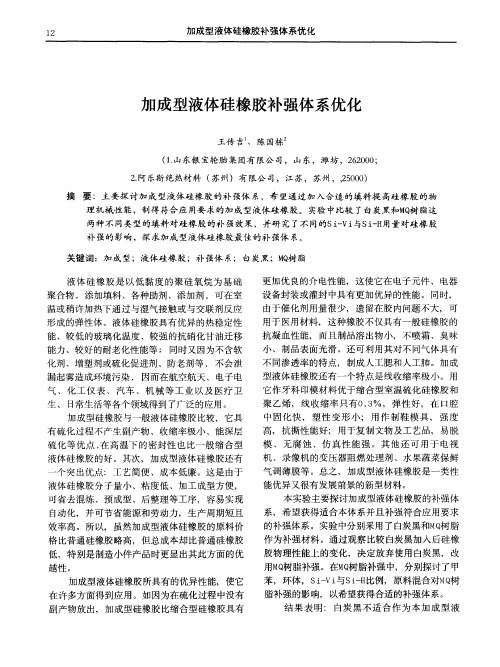
有助于胶料 的补强;在本加成型液体硅橡胶体系 中,只 采用M Q 树 脂 补 强不 能达 到 应用 要求 ,需 加
入其 它 补强 材料 。
讯实业有限公司;恒速搅拌器:S - 2 1 2 型 上海 申顺生物科技有 限公司
1 . 3反 应方 程式
1 、实验部分
1 . 1实验 原 料 以及生 产 厂家
1 2
加成 型液 体硅橡 胶 补强 体 系优 化
加成 型液体 硅橡 胶补强体系优化
王传 吉 、 陈 国栋
( 1 . 山东银 宝轮胎 集 团有 限公 司, 山 东,潍坊 ,2 6 2 0 0 0 ;
2 . 阿 乐斯 绝 热材料 ( 苏州 )有 限公 司 ,江 苏 ,苏 州 ,, 2 5 o o o )
型液体硅橡胶还有一个特点是线收缩率极小 。用 它作牙科 印模材料优于缩合型室温硫化硅橡胶和 聚 乙烯 ,线 收 缩 率 只有 0. 3 % ,弹 性 好 , 在 口腔 中固 化 快 , 塑 性 变 形 小 ; 用 作 制鞋 模 具 , 强 度
高 ,抗 撕性 能 好 ;用于 复 制 文物 及 工艺 品 ,易 脱
更加 优 良的介 电性 能 ,这 使它 在 电子元 件 、电器 设备 封 装 或灌 封 中具 有 更加 优异 的性 能 。同 时,
由于催化剂用量很少,遗 留在胶 内问题不大,可
用 于 医用材 料 ,这 种 橡 胶不 仅具 有 一般 硅 橡胶 的 抗 凝血 性 能 ,而 且 制品 溶 出物小 ,不 喷霜 、臭 味 小 、制 品表 面光 滑 。还 可 利用 其对 不 同气 体 具有 不 同渗 透 率 的特 点 ,制 成 人工腮 和人 工肺 。加 成
补 强的影响 ,探 求加 成 型液体 硅橡 胶 最佳 的 补 强体 系。
纳米SiO_2填充硅橡胶的补强机理研究进展_陈玉刚

纳米SiO2填充硅橡胶的补强机理研究进展陈玉刚1,2,石耀刚1,李 晓2(1 中国工程物理研究院化工材料研究所,绵阳621900;2 福州大学化学化工学院,福州350108)摘要 简单介绍了纳米SiO2的表面化学性质及其粒子的聚集状态;归纳了物理吸附作用、氢键作用方式及共价键结合方式等基本的纳米SiO2与硅橡胶的作用方式;以纳米SiO2-纳米SiO2、纳米SiO2-硅橡胶的不同作用为基础列举了键合胶、复合团聚体及互穿网络模型等几种补强模型,并总结了其在补强过程中发挥的作用,从而对其补强机理研究进展进行更为详细的概括和介绍。
关键词 纳米SiO2 补强模型 补强机理中图分类号:TQ333 文献标识码:AResearch Progress on Reinforcement Mechanism of Nano-SiO2Filled Silicone RubberCHEN Yugang1,2,SHI Yaogang1,LI Xiao2(1 The Institute of Chemical Materials,China Academy of Engineering Physics,Mianyang 621900;2 College of Chemistry andChemical Engineering,Fuzhou University,Fuzhou 350108)Abstract The state of aggregation and chemical properties on the surface of nano-SiO2are introduced and thedifferent modes of physical adsorption and action of hydrogen bond and covalent bond between nano-SiO2and siliconrubber are summarized.Based on different modes of action in nano SiO2-nano SiO2and nano SiO2-silicone rubber,se-veral reinforcement models such as bond adhesive model,composite aggregate model and interpenetrating network mo-del are listed and these reinforcement models important impact on the reinforcement process are reviewed,so as to of-fer more detailed summarization and introduction of advance in reinforcement mechanism.Key words SiO2nanoparticle,reinforcement model,reinforcement mechanism 陈玉刚:男,1987年生,硕士生,主要从事硅橡胶泡沫材料补强方面的研究 E-mail:yugang_0322@126.com 石耀刚:通讯作者,男,1969年生,研究员,主要从事硅橡胶泡沫材料补强方面的研究 Tel:0816-2494992 E-mail:shiygang@sina.com 在硅橡胶中加入纳米SiO2能够显著增强硫化橡胶的定伸应力、拉伸强度、撕裂强度和耐磨性,延长橡胶制品的使用寿命,这种现象通常被称为补强。
钙硅橡胶根管充填材料的研究进展与应用前景展望
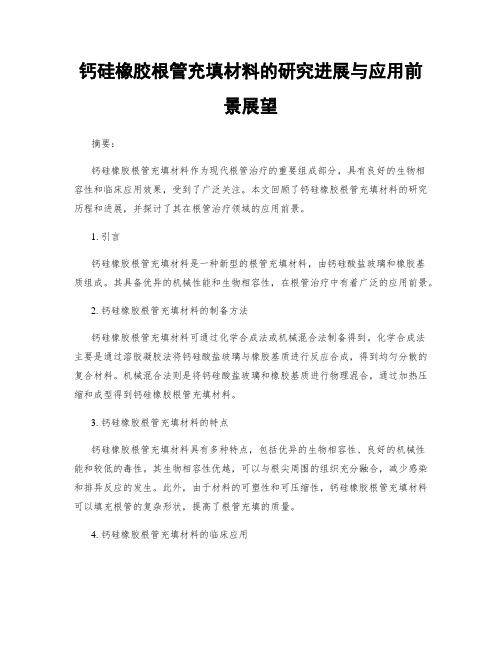
钙硅橡胶根管充填材料的研究进展与应用前景展望摘要:钙硅橡胶根管充填材料作为现代根管治疗的重要组成部分,具有良好的生物相容性和临床应用效果,受到了广泛关注。
本文回顾了钙硅橡胶根管充填材料的研究历程和进展,并探讨了其在根管治疗领域的应用前景。
1. 引言钙硅橡胶根管充填材料是一种新型的根管充填材料,由钙硅酸盐玻璃和橡胶基质组成。
其具备优异的机械性能和生物相容性,在根管治疗中有着广泛的应用前景。
2. 钙硅橡胶根管充填材料的制备方法钙硅橡胶根管充填材料可通过化学合成法或机械混合法制备得到。
化学合成法主要是通过溶胶凝胶法将钙硅酸盐玻璃与橡胶基质进行反应合成,得到均匀分散的复合材料。
机械混合法则是将钙硅酸盐玻璃和橡胶基质进行物理混合,通过加热压缩和成型得到钙硅橡胶根管充填材料。
3. 钙硅橡胶根管充填材料的特点钙硅橡胶根管充填材料具有多种特点,包括优异的生物相容性、良好的机械性能和较低的毒性。
其生物相容性优越,可以与根尖周围的组织充分融合,减少感染和排异反应的发生。
此外,由于材料的可塑性和可压缩性,钙硅橡胶根管充填材料可以填充根管的复杂形状,提高了根管充填的质量。
4. 钙硅橡胶根管充填材料的临床应用钙硅橡胶根管充填材料在临床根管治疗中得到了广泛应用。
其可在根管内形成连续的根管充填体,提高了根管治疗的成功率。
此外,钙硅橡胶根管充填材料还具有止血、抗菌和抗炎的功能,有助于根尖周围组织的修复和愈合。
5. 钙硅橡胶根管充填材料的研究进展目前,钙硅橡胶根管充填材料的研究主要集中在其制备方法和性能改良上。
许多研究者探讨了不同物理和化学改性方法对钙硅橡胶根管充填材料机械性能和生物相容性的影响。
其中包括添加纳米颗粒、表面改性和引入新型增强剂等。
这些研究为钙硅橡胶根管充填材料的性能改良提供了新的思路和方法。
6. 钙硅橡胶根管充填材料的应用前景展望随着根管治疗技术的不断发展,钙硅橡胶根管充填材料的应用前景也变得更加广阔。
未来的研究可以从以下几个方面展开:(1)进一步改进钙硅橡胶根管充填材料的制备方法,提高其力学性能和生物相容性;(2)探索新型的增强剂和纳米颗粒改性方法,提高钙硅橡胶根管充填材料的综合性能;(3)研究钙硅橡胶根管充填材料在修复根尖囊肿和牙周炎等疾病中的应用,拓展其临床应用领域。
- 1、下载文档前请自行甄别文档内容的完整性,平台不提供额外的编辑、内容补充、找答案等附加服务。
- 2、"仅部分预览"的文档,不可在线预览部分如存在完整性等问题,可反馈申请退款(可完整预览的文档不适用该条件!)。
- 3、如文档侵犯您的权益,请联系客服反馈,我们会尽快为您处理(人工客服工作时间:9:00-18:30)。
Ke r s sl o er b e ;rifr igflr y wo d :ic n u b r enocn l ;me h nc lpo e y rve i ie c a ia rp  ̄ ;e iw
Ab t a t Th c a c lsr ngh o n en o c d slc n u be s v r o Th i y t mp o e sr c : e me h nia te t fu r i f r e iio e r b r i e y lw. e man wa o i r v t e p y ia n c a ia r pete fu r i fr e iio e r bb ri d n enfr i g fl r i t h h sc la d me h n c lp o ris o n en o c d slc n u e s a di g r i o cn il n i. e
沉淀法 白炭黑、 纤维与碳纳米 管、 短 纳米碳酸钙在硅橡胶 补强中的应用研究概况 。 关键词 : 硅橡胶 ; 补强填料 ; 物理机 械性 能 ; 述 综
中 图分 类 号 .Q 3 .8 T 30 3 3 文献标识码 : A 文 章 编 号 :0 8—0 1 2 1 1 0 3 10 2 X(0 0)2— 0 3—0 4
第1 2期
王
林, : 等 硅填料的研究进展
王 林 , 张 利 , 小兰, 刘 李金 辉
20 1 ) 5 04 ( 山东 省科 学 院 新 材料 研究 所 , 山东 济南
摘要: 纯硅橡胶的机械强度很低 , 添加补强填料是提高硅橡胶物 理机械性能 的主要 手段。简 要介绍 了近年来 有关气 相法 白炭黑 、
的拉伸 强度达 到 1MP 4 a以上 , 强 率 高 达 4 补 O倍 , 远 远 高 出其 他橡 胶 所 能达 到 的补 强 率 ( . 14~1 0倍 ) 。 本 文简要 介绍 了近 年 来 有关 气相 法 白炭 黑 、 淀 法 沉 白炭黑 、 纤维 与碳 纳米 管 、 短 纳米 碳 酸钙 在硅橡 胶 补
到 了广泛 的应用 。硅橡 胶分 子 呈 螺旋 形 结 构 , 子 分
链非 常柔顺 , 间相 互 作用 力较 弱 ,分 子 问 内 聚能 链 密度低 , 很难 结 晶 , 致 纯 硅 橡 胶 的机 械 强 度 极 差 , 导
硫化后 拉伸 强度 只有 0 3~0 5 a 除 了某 些 医学 . . MP , 领域外 , 一般 没有 实 际 用 途 。 添加 补 强填 料 是 调 整 硅橡胶 物理 机 械性 能 的 主要 手 段 【 ]可 使 硅 橡 胶 1 ,
Ree r hPr g eso i c n b e if rigFie sa c o rs fSl o eRu b rRen o cn l r i l
W NG Ln, HA iL U X a A i Z NG L , I io—ln , IJn—h i a L i u ( e ae a Istt o h n ogA a e f ce csJ a 2 0 1 C ia N w M t l ntue f a dn cdmyo i e ,i n 5 0 4, hn ) i r i S S n n
—
硅、 甲基 三 氯 化 硅 等 ) 氢 氧 焰 中高 温 水 解 生 成 的 在 带 有表 面羟 基 和吸 附水 的无 定 形絮状 半透 明的纳 米 二氧化 硅 产 品 。其 二 氧 化 硅 质 量 分 数 在 9 .% 以 98 上 , 均 粒 径 8~1 m, 平 9 n 比表 面 积 10— 8 m 3 4 0 ・ g D P吸收值 1 5 2 0 m g 具 有极好 的 ~, B . 0— .0a ・ ~, 介 电性 能 , 它是 一 种 在 世 界 范 围 内真 正 工 业 化 的纳 米材 料 。气 相法 白炭 黑 的折 射 率 为 1 4 0 , 近许 .60 接 多有机 溶剂 和 有机 聚合 物 的折 射 率 , 因而 加 入气 相
T e r if r e n f i c n u b r yr if r i gf lrs c sf me i c h e n oc me t l o e r b e en o cn l u h a u d s ia,p e i i td s i a h r — osi b i e l r cp t e i c ,s ot a l
硅橡胶 是 高分 子 的 硅有 机 化 合 物 , 由二硅 醇 缩 聚 制得 , 以 S 一 是 i 0一S 为 主链 的兼 具 无 机性 、 和 i 饱 性、 高极性 ( 1 5%离 子性 ) 的线 性 聚 硅 氧烷 高 分子 弹 性 体 。由于 S —O键 的 键 能 (4 .k/ 1 大 于 C i 4 3 5Jmo) C键 的键 能 ( 5 k/ 1 , 3 5 Jmo) 因而与 普 通 的橡 胶材 料
法 白炭 黑一 般 不会 影 响产 品 的透 明性 。气 相法 白炭
相 比, 硅橡 胶具有 非 常好 的耐 高低 温 、 耐候 、 耐臭 氧 、 抗 电弧 、 电气绝缘 性 、 化 学 品 、 透 气 性 及 生理 惰 耐 高 性 等性 能 , 在航 空 、 航 、 宇 电气 电子 、 工仪 表 、 化 汽车 、 机 械等工业 以及 医疗 卫 生 、 日常 生 活 的 各个 领 域 得