熔模铸造
熔模铸造流程

熔模铸造流程
熔模铸造是一种常见的金属铸造工艺,其流程包括模具制作、熔炼金属、注入、冷却凝固和脱模等步骤。
下面将详细介绍熔模铸造的具体流程。
首先,模具制作是熔模铸造的第一步。
模具通常由耐火材料制成,可以承受高温和高压。
模具的制作需要根据所需铸件的形状和尺寸进行设计,然后用石膏或陶瓷材料制成模具。
接着,熔炼金属是熔模铸造的第二步。
选择适当的金属材料,将其放入熔炼炉中加热,直到金属完全熔化。
在熔炼过程中,需要控制好炉温和金属成分,以确保铸件的质量。
然后,注入是熔模铸造的第三步。
将熔化的金属倒入预先制作好的模具中,填满整个模腔。
注入时需要注意金属的流动速度和压力,以避免气孔和缺陷的产生。
随后,冷却凝固是熔模铸造的第四步。
待金属注入模具后,开始冷却凝固。
在这个过程中,金属逐渐从液态转变为固态,同时释放出大量热量。
冷却时间的长短和冷却速度的控制对铸件的质量有
着重要影响。
最后,脱模是熔模铸造的最后一步。
待铸件完全冷却后,将模具打开,取出成品铸件。
在脱模过程中需要小心操作,以免损坏铸件或模具。
总的来说,熔模铸造流程包括模具制作、熔炼金属、注入、冷却凝固和脱模等多个步骤。
每个步骤都需要精细操作,以确保最终铸件的质量和形状符合要求。
通过不断改进工艺和技术,熔模铸造在制造业中扮演着重要的角色,被广泛应用于航空航天、汽车、机械等领域。
熔模铸造流程
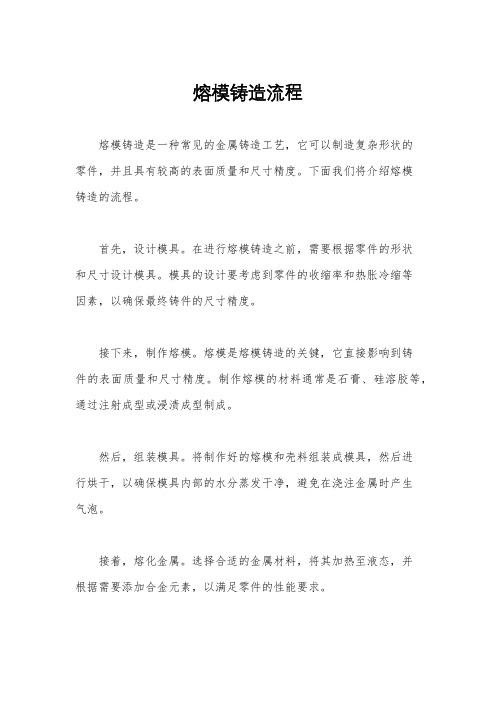
熔模铸造流程
熔模铸造是一种常见的金属铸造工艺,它可以制造复杂形状的
零件,并且具有较高的表面质量和尺寸精度。
下面我们将介绍熔模
铸造的流程。
首先,设计模具。
在进行熔模铸造之前,需要根据零件的形状
和尺寸设计模具。
模具的设计要考虑到零件的收缩率和热胀冷缩等
因素,以确保最终铸件的尺寸精度。
接下来,制作熔模。
熔模是熔模铸造的关键,它直接影响到铸
件的表面质量和尺寸精度。
制作熔模的材料通常是石膏、硅溶胶等,通过注射成型或浸渍成型制成。
然后,组装模具。
将制作好的熔模和壳料组装成模具,然后进
行烘干,以确保模具内部的水分蒸发干净,避免在浇注金属时产生
气泡。
接着,熔化金属。
选择合适的金属材料,将其加热至液态,并
根据需要添加合金元素,以满足零件的性能要求。
然后,浇注金属。
将熔化的金属倒入模具中,填充整个模腔,
然后等待金属冷却凝固。
接下来是模具拆除。
待金属冷却凝固后,拆除模具,取出铸件。
最后,进行后处理。
包括去除浇口、毛刺、氧化皮等,然后进
行热处理、表面处理等工艺,最终得到成品铸件。
总的来说,熔模铸造流程包括设计模具、制作熔模、组装模具、熔化金属、浇注金属、模具拆除和后处理。
这一流程需要严格控制
各个环节,以确保最终铸件的质量和性能。
熔模铸造具有生产效率高、成本低、表面质量好等优点,因此在航空航天、汽车、军工等
领域得到广泛应用。
熔模铸造工艺知识培训

02 熔模铸造工艺流程
制作模料
选择合适的模料
涂刷脱模剂
根据铸件的材料和尺寸要求,选择合 适的模料,如石英砂、刚玉砂等。
为了方便脱模,需要在模料表面涂刷 一层脱模剂。
混合与搅拌
将模料按照一定比例混合,并使用搅 拌机充分搅拌,使其达到均匀的稠度。
制作蜡模
01
02
03
模具组装
将搅拌好的模料填入模具 中,并确保填满整个模具 腔体。
低成本材料
通过降低材料成本,提高熔模铸造的性价比和市场竞争力。
多功能性材料
开发具有特殊性能如抗菌、抗静电等新型熔模铸造材料,满足特定 需求。
熔模铸造工艺的优化与创新
简化工艺流程
减少生产环节,提高生产效率,降低生产成本。
环保型工艺
研发无污染或低污染的熔模铸造工艺,降低生产过程中的环境污 染。
高效冷却技术
熔模铸造在航空发动机、航天器结构件等 方面得到广泛应用,为航空航天事业的发 展提供重要支持。
THANKS FOR WATCHING
感谢您的观看
02
该工艺涉及多个步骤,包括制作 蜡模、脱蜡、焙烧、浇注金属等 。
熔模铸造的特点
高精度
熔模铸造能够获得高精 度的金属零件,表面光
洁度较高。
适用范围广
可用于各种金属材料, 如钢、铝、铜、不锈钢
等。
灵活性高
可以生产各种形状和大 小的零件,尤其适用于 复杂结构零件的生产。
成本较高
由于工艺复杂,需要较 高的设备和人力投入,
浇注过程的质量控制
浇注温度
浇注温度过高可能导致金属液过 热,过低则可能导致金属液流动
性差,影响充型能力。
浇注速度
熔模铸造工艺(3篇)

第1篇一、熔模铸造工艺的定义熔模铸造工艺,又称精密铸造,是一种将金属熔化后注入预先制成的型腔中,冷却凝固后取出金属制品的铸造方法。
该工艺主要用于制造形状复杂、尺寸精度要求高的零件。
二、熔模铸造工艺的原理熔模铸造工艺的基本原理是将可熔化的材料(如蜡、塑料等)制成所需形状的熔模,再将熔模组装成型腔,将熔融金属注入型腔,冷却凝固后取出金属制品。
具体过程如下:1. 制作熔模:将可熔化的材料制成所需形状的熔模,通常采用手工或机械加工方法。
2. 组装型腔:将熔模组装成型腔,并固定在型腔架上。
3. 熔化金属:将金属加热至熔化状态。
4. 注入金属:将熔融金属注入型腔,使其填充熔模形成的型腔。
5. 冷却凝固:将型腔冷却至室温,使金属凝固。
6. 脱模:将型腔从金属制品中取出,得到所需的金属制品。
三、熔模铸造工艺的过程1. 熔模制作:根据零件图纸,采用手工或机械加工方法制作熔模。
熔模应保证形状、尺寸和精度符合要求。
2. 组装型腔:将熔模组装成型腔,并固定在型腔架上。
3. 熔化金属:选择合适的金属材料,将其加热至熔化状态。
4. 注入金属:将熔融金属注入型腔,确保填充完全。
5. 冷却凝固:将型腔冷却至室温,使金属凝固。
6. 脱模:将型腔从金属制品中取出,得到所需的金属制品。
7. 后处理:对金属制品进行清理、去毛刺、抛光等后处理。
四、熔模铸造工艺的应用熔模铸造工艺广泛应用于以下领域:1. 航空航天:制造发动机叶片、涡轮盘、机匣等高精度零件。
2. 汽车:制造发动机缸体、缸盖、曲轴等关键部件。
3. 电子:制造集成电路封装、精密模具等。
4. 医疗器械:制造心脏支架、人工关节等精密医疗器械。
5. 机械制造:制造齿轮、轴承、凸轮等精密零件。
五、熔模铸造工艺的优缺点1. 优点:(1)高精度:熔模铸造工艺可以制造形状复杂、尺寸精度高的零件。
(2)高复杂度:可以制造形状复杂、尺寸精度高的零件,满足各种复杂结构的制造需求。
(3)高质量:金属熔化后注入型腔,减少了氧化、污染等不良因素的影响,保证了金属制品的质量。
熔模铸造的特点和应用范围

熔模铸造的特点和应用范围1. 熔模铸造简介好嘞,今天咱们来聊聊熔模铸造。
这玩意儿可不是普通的铸造工艺,而是一种高超的技术。
想象一下,就像做蛋糕,先得有模具,熔模铸造就是这个模具的艺术家。
它的基本原理简单粗暴,先把蜡模做出来,然后浇上熔融金属,等金属冷却固化,最后把蜡融掉,嘿,神奇的金属部件就出炉了!听起来是不是挺酷的?2. 熔模铸造的特点2.1 高精度首先,熔模铸造最大的特点就是高精度。
你可以把它想象成在拼拼图,拼得越仔细,最后的图案就越完美。
这种铸造方式能达到非常细致的形状和表面光滑度,简直是“工艺中的工艺”!比如说,汽车零件、航空器组件,都是对精度有着近乎苛刻要求的地方,熔模铸造轻松驾驭。
2.2 复杂形状再来说说它的另一个牛逼之处,那就是能做复杂形状的部件。
比方说,一些形状奇特的艺术品或者高科技的仪器,传统铸造可能会发愁,但熔模铸造可不怕。
就像会魔法一样,蜡模能随心所欲地造型,成品完全符合设计师的想法,简直是一种“想象力与技术结合”的完美体现!3. 熔模铸造的应用范围3.1 航空航天接下来,我们聊聊熔模铸造的应用范围。
这东西用得可广了,首先在航空航天领域那是无人能敌。
飞机、火箭的发动机部件,很多都得靠熔模铸造来实现,没办法,安全第一呀!而且,随着科技的发展,这些部件还得轻、强、耐高温,熔模铸造就能满足这些要求,简直是个超级英雄!3.2 医疗器械再说医疗器械。
想想看,手术刀、植入物,这些东西对精度和材料的要求都非常高,稍微差点可就“麻烦大了”。
熔模铸造在这方面也是大展拳脚,很多高精度的医疗器械部件,都是通过这项技术来制作的。
可以说,熔模铸造不仅仅是个技术活,更是关乎人命的大事,想想都觉得责任重大呢。
4. 小结总的来说,熔模铸造是个神奇的存在,凭借它的高精度和能制造复杂形状的特点,在各个行业里大放异彩。
无论是航天还是医疗,它都能发挥不可替代的作用。
就像一位默默无闻的英雄,在背后默默奉献,却又总能让人心生敬意。
熔模铸造名词解释

熔模铸造名词解释熔模铸造(fusion mold casting)【熔模铸造的定义】:熔模铸造工艺是将与砂型或型芯材料相适应的粘结剂和耐火材料加入已干燥的砂型(芯)中,在其中浇注熔融金属而成型,经焙烧后,获得所需铸件的方法。
它是以适当成分的型砂和熔融金属,在高温下,于型中凝固而得到铸件。
这种铸造方法主要用来生产形状复杂的砂型铸件,如汽车的发动机缸体、缸盖、变速箱壳体、差速器壳体等零件。
它不仅用于生产有色合金铸件,也可用于生产钢铁铸件。
熔模铸造设备,主要包括熔模铸造用涂料(专业浇注料)自硬砂造型设备、合箱设备、退火炉、型壳焙烧炉、起重设备、熔模铸造用中小型冲天炉、大型回火窑及普通、焙烧炉等。
铸造方法包括重力铸造、低压铸造、压力铸造、消失模铸造、离心铸造、熔模铸造、实型铸造、陶瓷型铸造、金属型铸造、消失模铸造等多种铸造方法。
【熔模铸造的特点】: 1、在机械制造中,它可以用来精密铸造复杂的单件或小批量多品种的小零件。
例如用来生产汽车发动机的曲轴和凸轮轴、柴油机的活塞和缸套、飞机的发动机、坦克的履带板等。
此外,电机壳体、仪表板、手表壳体、自行车的零件,也都采用这种铸造方法。
2、这种铸造方法,由于所用的型砂和金属不经过高温加热,因而原料来源丰富、价格便宜、生产成本低廉;而且可以一机多用,使生产不受铸件大小和批量的限制,特别适用于机床、仪表、内燃机、汽车等行业的批量生产。
3、但这种铸造方法只能生产一些形状简单的零件,如一些有色合金铸件,灰铸铁件等。
同时由于生产率低,劳动条件差,质量也比较差,一般只用于大型和特大型铸件的生产。
不锈钢热轧板进行全流程快速热镀锌,连续生产能力达150万吨/年以上,钢板质量可以达到国际热镀锌标准,热镀锌防腐性能远远高于喷涂工艺。
此外,还能应用到压铸领域,解决了电磁阀防腐蚀问题,在压铸件厚度≥1mm以下,无锌花、微孔、凹坑、裂纹、焊瘤、氧化皮、积碳、石墨、增碳等缺陷,降低了表面缺陷,提升了压铸件的质量。
精密铸造工艺-熔模铸造
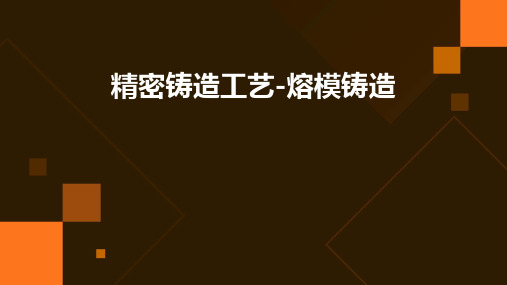
一定的强度
在搬运和组装过程中不易损坏。
易于脱壳
在铸件冷却后能够顺利脱去壳型,不 损伤铸件表面。
合金选择与性能要求
符合产品使用要求
良好的铸造性能
根据产品的使用环境和性能要求选择合适 的合金种类和牌号。
合金应具有较低的熔点和良好的流动性, 以便于充型和补缩。
安全操作规程及培训要求
制定安全操作规程
明确各工序的安全操作要求和注 意事项,确保操作人员严格遵守
。
应急预案与演练
对新员工和转岗员工进行安全培 训,提高员工的安全意识和操作
技能。
安全培训与教育
对涉及特种作业的员工,如电工 、焊工等,必须持证上岗,确保 操作安全。
特种作业人员持证上岗
制定针对熔模铸造过程中可能出现 的紧急情况的应急预案,并定期进 行演练,提高员工的应急处置能力。
加强人才培养
加强人才培养和引进,培养一支高素质、专业化的熔模铸造技术人才队伍,推动行业的技 术进步和可持续发展。例如,建立完善的人才培养和激励机制,吸引和留住优秀人才。
感谢您的观看
THANKS
蜡料选择与性能要求
低熔点和高流动性
确保蜡料在注射时能够充分填充模具,形成 精确的蜡模。
易于脱模
与模具材料之间有良好的分离性,降低脱模 难度。
稳定性好
在存放和使用过程中不易变质或产生缺陷。
对环境友好
无毒无害,符合环保要求。
壳型材料及其性能要求
高耐火度
能够承受高温金属液的冲刷而不破裂 或变形。
良好的透气性
较高的力学性能
良好的耐蚀性和耐磨性
合金应具有足够的强度、硬度和韧性等力 学性能,以满足产品的使用要求。
熔模铸造简介

熔模铸造简介1.熔模铸造发展概况1.1. 概述熔模铸造又称熔模精密铸造,是一种近净形的液态金属成型工艺,应用该工艺获得的每个铸件都是经多种工序、多种材料、多种技术共同协作综合的结果。
熔模铸造通常是指在易熔材料制成的模样表面包覆若干层耐火材料制成型壳,再将模样熔化排出型壳,从而获得无分型面的铸型,经高温焙烧后即可填砂浇注的铸造方案。
由于模样广泛采用蜡质材料来制造,故常将熔模铸造称为“失蜡铸造”。
1.2. 工艺流程熔模铸造工艺全过程:1.蜡模成型:将蜡料压入金属型腔模具,冷却取出形成蜡模;2.组树:将若干蜡模焊在一根蜡制的浇注系统上,组成蜡模组;3.沾浆:将蜡模组浸入水玻璃和石英粉配置的浆料中;4.硬化壳:将蜡模组放入硬化剂中进行硬化,如此重复数次,直到蜡模表面形成一定厚度的硬化壳;5.熔蜡制壳:将带有硬壳的蜡模组加热,使蜡熔化后从浇口中流出,形成铸型空腔;6.熔炼浇注:将液态金属浇入模壳,形成铸件毛坯;7.清理型壳:待浇注后的产品充分冷却后,使用人工锤击或振动脱壳机使模壳从铸件上分离。
最后,利用切割的方法分离出模组上的铸件产品,得到所需铸件。
2.模料2.1. 模料要求制模材料的性能不单应保证方便地制得尺寸精确和表面光洁度高,强度好,重量轻的熔模,它还应为型壳的制造和获得良好铸件创造条件。
模料一般用蜡料、天然树脂和塑料(合成树脂)配制。
凡主要用蜡料配制的模料称为蜡基模料,它们的熔点较低,为60~70℃;凡主要用天然树脂配制的模料称为树脂基模料,熔点稍高,约70~120℃。
熔模铸造对模料的要求:1.热物理性能①熔点:模料的熔点及凝固温度区间应适中,熔点一般在50~80 ℃范围为宜,模料的凝固温度一般选择在5~10 ℃,以便配制模料、制模及脱蜡工艺的进行。
②热稳定性:热稳定性是指当温度升高时,模料抗软化变形的能力。
蜡基模料的热稳定性常以软点来表示,它是以标准悬臂试样加热保温2 h的变形量(挠度)达2 mm时的温度作为软化点,模料软化点一般应比制模车间的温度高10 ℃以上为宜。
熔模铸造的名词解释

熔模铸造的名词解释熔模铸造是一种先进的铸造工艺,广泛应用于制造工业。
熔模铸造是一种以模具作为铸造形象的铸造方法,其特点是可以制造出高精度、复杂形状的零件。
随着科技的不断进步,熔模铸造在现代制造领域的应用也越来越广泛。
熔模铸造的核心技术是利用耐高温的材料制作出模具,再通过熔化模具材料得到复杂形状的零件。
这种制造方法首先需要制作一个用于铸造的模具。
一般来说,模具是由石膏、陶瓷或金属材料制成的。
对于复杂形状的零件,需要使用高精度的数控机床或3D打印技术制作模具。
制作好模具后,下一步是进行熔融,也就是将铸造材料加热融化。
常用的铸造材料包括金属合金、陶瓷材料和高聚物材料等。
在熔融过程中,需要控制好温度,确保铸造材料能够充分融化,并且达到适当的流动性。
熔融后的铸造材料会填充到模具中,然后经过冷却固化。
在熔模铸造过程中,最关键的一步是模具的破壞。
模具形成了最终零件的形状,因此需要将模具取出以获得铸造件。
这个过程称为解模。
解模需要非常小心,以避免对零件造成损害。
有些零件形状复杂,内部空洞较多,模具解体后可能需要采用化学方法或机械方法去除。
与传统的铸造方法相比,熔模铸造具有一些显著的优势。
首先,熔模铸造能够制造出极为复杂的形状,包括内部空洞、细节部分和薄壁结构等。
这种能力在航空航天、汽车制造和医疗设备制造等领域非常重要。
其次,熔模铸造可以实现精密和高度一致的零件制造。
这得益于模具的高精度和熔融过程的精确控制。
熔模铸造在实际应用中有一些限制。
首先,制作模具的成本相对较高,特别是针对小批量生产和个性化生产。
其次,熔模铸造需要耗费较多时间。
模具的制作和冷却时间都需要一定的时间。
因此,对于需要快速生产的产品,熔模铸造可能不是最佳选择。
然而,熔模铸造的技术不断发展和创新。
近年来的3D打印技术的应用使得熔模铸造的成本和时间得到了改善。
这使得熔模铸造在更多领域中得到了广泛应用,特别是在汽车和航空航天行业。
总之,熔模铸造是一种高精度、复杂形状零件制造的先进工艺。
熔模铸造和消失模铸造

熔模铸造和消失模铸造- 原理。
- 熔模铸造又称失蜡铸造。
首先用易熔材料(如蜡料)制成精确的可熔性模型(熔模),在模型上包覆若干层耐火涂料,制成型壳。
然后将模型熔化排出型壳,从而获得无分型面的铸型,再经高温焙烧后进行浇注,得到铸件。
- 工艺过程。
- 制造熔模:通常采用注射成型等方法制作蜡模,蜡模的精度直接影响铸件的精度。
- 制造型壳:将蜡模浸入耐火涂料中,随后撒上砂粒等耐火材料,经干燥硬化后形成型壳。
这个过程要重复多次以增加型壳的强度。
- 脱蜡:通过加热使蜡模熔化流出型壳,脱蜡后的型壳要进行高温焙烧,以进一步提高其强度和去除残留的蜡质等杂质。
- 优点。
- 铸件精度高,可以铸造形状复杂的零件,如航空发动机叶片等具有精细内部结构和复杂外形的部件。
- 表面光洁度好,能够减少后续的加工工序。
- 适用于各种合金材料的铸造,包括一些难加工的高温合金等。
- 缺点。
- 工艺过程复杂,生产周期较长,从制造熔模到最终得到铸件需要多道工序。
- 成本相对较高,由于需要使用高质量的蜡料、耐火材料,并且工序较多导致人力成本也较高。
- 原理。
- 消失模铸造是将与铸件尺寸形状相似的泡沫模型粘结组合成模型簇,刷涂耐火涂料并烘干后,埋在干石英砂中振动造型,在负压下浇注,使模型气化,液体金属占据模型位置,凝固冷却后形成铸件。
- 工艺过程。
- 制作泡沫模型:利用聚苯乙烯(EPS)或聚甲基丙烯酸甲酯(PMMA)等泡沫材料,通过数控加工、模具发泡等方法制作出与铸件形状一致的泡沫模型。
- 模型组合与粘结:将多个泡沫模型按照设计要求组合在一起,使用专用的粘结剂进行粘结。
- 涂挂涂料:在模型表面涂挂耐火涂料,以防止浇注时金属液对泡沫模型的冲刷,并使型砂能够更好地成型。
- 优点。
- 铸件尺寸精度较高,由于泡沫模型的可塑性,可以制造一些具有复杂内腔结构的铸件。
- 工艺简单,不需要分型面,减少了因分型面带来的铸造缺陷。
- 成本较低,设备相对简单,并且泡沫材料成本较低。
熔模铸造

2、型壳铸造
(1)浸涂料 ) 将蜡模组置于涂料中浸渍, 将蜡模组置于涂料中浸渍,使涂料均 匀地覆盖在蜡模组的表层 (2)撒沙 是机子涂料后的蜡模组均匀地粘附一 层石英砂 (3)硬化 制壳时,每涂挂和撒沙一层后, 制壳时,每涂挂和撒沙一层后,必须 进行化学硬化和干燥
(4)脱蜡 从型壳中取出蜡模形成铸模空腔, 从型壳中取出蜡模形成铸模空腔,必 须进行脱蜡
冷却之后,将型壳破坏,取出铸件, 冷却之后,将型壳破坏,取出铸件,然源自去掉浇 冒口, 道、冒口,清理毛刺等
三、熔模铸造的特点和使用范围 熔模铸造的特点和使用范围
特点: 特点: 铸件的精度高,表面光洁。 1、铸件的精度高,表面光洁。 2、可制造难以砂型铸造或机械加工的形状 很复杂的薄壁铸件。(最小壁厚0.3 。(最小壁厚0.3㎜ 很复杂的薄壁铸件。(最小壁厚0.3㎜,最 小孔径2.5 2.5㎜ 小孔径2.5㎜) 3、适用于各种合金铸件 4、生产批量不受限制
熔模铸造的工艺过程可分为蜡模铸造、 熔模铸造的工艺过程可分为蜡模铸造、 型壳铸造、 型壳铸造、焙烧浇注三个主要阶段
1、蜡模铸造
(1)制造压型 压型是用来制造单个蜡模的专用模 (2)蜡模的压制 将蜡料加热到糊状后, 将蜡料加热到糊状后,在2-3个大气压 力下,将蜡料压入到压型内, 力下,将蜡料压入到压型内,待蜡料冷却 凝固便可从压型内取出,然后修去毛刺, 凝固便可从压型内取出,然后修去毛刺, 即得单个蜡模 (3)组装蜡模 可提高生产率、降低成本, 可提高生产率、降低成本,一型多铸
生产工艺复杂且周期长, 5、生产工艺复杂且周期长,机械加工压型成 本高每所用的耐火材料、 本高每所用的耐火材料、模料和粘结剂价 格较高, 格较高,铸件成本高
由于受熔模及型壳强度限制,铸件不宜过大 由于受熔模及型壳强度限制, 或过长, 或过长,仅适于从几十克到几千克的小铸 一般不超过45 45㎏ 件,一般不超过45㎏
熔模铸造工艺

所有铸件材料
铸件内部较大的缩孔、裂纹等缺 铸钢件、铸铁件等通磁
陷
材料
渗透探伤
铸件表面裂纺
B、防锈
不锈钢等非磁性材料
目的:保证铸件库存状态不锈蚀; 方法:防锈液浸入法。
3.3.12、品质检查
A、外观质量
标准:Q/DFLCM0108-2006 熔模精密铸件技术条件
检验内容 铸件尺寸、形状和
重量 表面粗糙度
密封性检验 盐雾试验 抗氧化试验 磁性能测定
成品(不需加工):按标准包装要求,定箱入库; 半成品(需后序加工):装箱发下序加工
四、熔模铸造应用范围
从产品类别来看,熔模精密铸件主要分为两大 类:军工、航空类产品与商品类产品。前者质量 要求高,后者质量不如前者。随着冷战时代的结 束,各国军工产品大幅度减少,但民航、大型电 站及工业涡轮发动机的发展,使得军工、航空类 产品所占比例变化不大。现在熔模铸造除用于航 空、军工部门外,几乎应用于所有工业部门,如 电子、石油、化工、能源、交通运输、轻功、纺 织、制药、医疗器械等领域。
B、制壳操作流程
硅溶胶制壳工艺没有化学硬化, 干燥脱水
3.3.5、脱蜡
A、脱蜡是模型蜡从模壳中脱出形成型腔的过程,脱蜡前 模壳存在时间不低于24h; B、脱蜡方法:热水法和高压蒸气法
脱蜡时注意事项: ➢ 清理浇口杯顶残砂:防止浮砂落入型腔; ➢ 加入补充硬化剂:热水脱蜡时加入1%盐酸,型壳得到 补充硬化,并可防止蜡料皂化; ➢ 脱蜡水严禁沸腾:防止将槽底的砂粒翻起进入型腔; ➢ 脱蜡后的型壳禁止杯口向上放置:防止脏物落入型腔。 ➢ 槽液定期清理与更换。
五、熔模铸造工艺发展趋势
1、更大更薄:目前,熔模铸造生产的精密铸件,最大轮廓尺寸可 达1.8m,而最小壁厚却不到2mm,最大铸件重量接近1000kg。
熔模铸造的优势与应用

06
熔模铸造的未来展望
技术创新
数字化技术
01
利用先进的数字化技术,如3D打印和CAD软件,提高熔模铸造
的精度和生产效率。
智能化生产
02
引入自动化和智能化设备,实现熔模铸造过程的自动化控制和
智能化管理。
新型材料
03
研发新型耐热、高强度、轻质的铸造材料,提高熔模铸造产品
的性能和品质。
应用拓展
航空航天领域
适用范围广
熔模铸造适用于各种不同材质的铸件生产,如钢、铁、铜、 铝等。
由于熔模铸造的模具制作灵活,可以根据不同需求快速调整 模具,从而适应不同形状和大小的铸件生产。
生产效率高
熔模铸造的模具使用寿命长,可以重复使用多次,降低了 生产成本。
由于熔模铸造的模具制作周期短,因此可以快速实现从设 计到生产的转化,缩短了产品上市时间。
利用熔模铸造技术制造高性能的航空航天零 部件,满足高精度、高强度、轻质化的要求 。
汽车工业
扩大熔模铸造在汽车工业的应用范围,如发 动机、变速器等关键零部件的制造。
新能源领域
将熔模铸造技术应用于新能源领域,如太阳 能光热发电的集热器部件制造。
绿色发展
01
02
03
环保材料
采用环保、低能耗的铸造 材料,降低熔模铸造过程 中的能耗和污染。
制模阶段
总结词
详细描述熔模铸造制模阶段的过程
详细描述
详细描述熔模铸造制模阶段的过程
制壳阶段
总结词
详细描述熔模铸造制壳阶段的过程
详细描述
制壳阶段是在模具表面涂覆耐火材料,形成一层壳体,用于保护模具和产品。这一阶段 需要选用高质量的耐火材料,并采用适当的涂覆工艺,以确保壳体的厚度、均匀性和可
熔模精密铸造实践报告总结(2篇)

第1篇一、引言熔模精密铸造是一种先进的铸造技术,具有精度高、表面光洁、机械性能好等优点,广泛应用于航空航天、汽车、医疗器械等领域。
本报告主要对熔模精密铸造的实践过程进行总结,分析存在的问题及改进措施,以期为今后类似项目的实施提供参考。
二、熔模精密铸造实践过程1. 原材料准备熔模精密铸造的原材料主要包括蜡、石英砂、粘土、水、耐火材料等。
在实践过程中,首先要对原材料进行筛选和加工,确保其质量符合要求。
2. 熔模制作熔模制作是熔模精密铸造的关键环节。
具体步骤如下:(1)蜡模制作:根据产品图纸,采用手工或机器加工方法制作蜡模,要求蜡模表面光滑、尺寸准确。
(2)蜡模组合:将多个蜡模组合成一个整体,以便后续进行熔模铸造。
(3)熔模组装:将蜡模组合体放入砂箱中,进行熔模组装,确保砂箱内的蜡模组合体与砂箱内壁之间形成良好的密封。
3. 熔模铸造熔模铸造主要包括以下步骤:(1)预热:将砂箱内的熔模预热至一定温度,以降低蜡模熔化时的收缩应力。
(2)熔化蜡模:将预热后的熔模放入熔化炉中,熔化蜡模。
(3)浇注:将熔化的金属液浇注到砂箱内的蜡模中,使金属液填充蜡模空腔。
(4)冷却凝固:待金属液凝固后,取出砂箱,去除砂模,得到铸件。
4. 铸件后处理铸件后处理主要包括以下步骤:(1)打磨:对铸件表面进行打磨,去除浇注系统和浇注冒口等。
(2)热处理:根据铸件材料性能要求,进行相应的热处理。
(3)检验:对铸件进行尺寸、形状、表面质量、机械性能等方面的检验。
三、存在问题及改进措施1. 问题一:蜡模精度不足原因分析:蜡模制作过程中,手工加工误差较大,导致蜡模精度不足。
改进措施:采用高精度加工设备,如数控机床等,提高蜡模加工精度。
2. 问题二:熔模铸造过程中出现缩孔、裂纹等缺陷原因分析:熔模铸造过程中,金属液冷却速度过快,导致缩孔、裂纹等缺陷。
改进措施:优化熔模设计,采用合理的浇注系统,降低冷却速度,提高铸件质量。
3. 问题三:铸件表面质量差原因分析:铸件表面质量受多种因素影响,如熔模表面质量、浇注温度、冷却速度等。
熔模铸造的工艺设计要点及注意事项
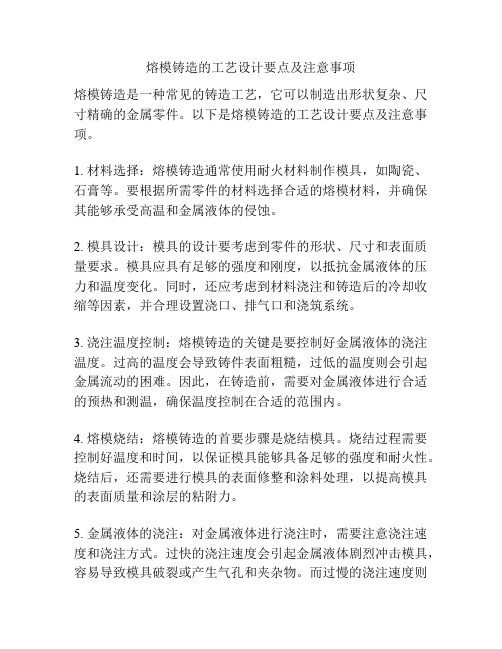
熔模铸造的工艺设计要点及注意事项熔模铸造是一种常见的铸造工艺,它可以制造出形状复杂、尺寸精确的金属零件。
以下是熔模铸造的工艺设计要点及注意事项。
1. 材料选择:熔模铸造通常使用耐火材料制作模具,如陶瓷、石膏等。
要根据所需零件的材料选择合适的熔模材料,并确保其能够承受高温和金属液体的侵蚀。
2. 模具设计:模具的设计要考虑到零件的形状、尺寸和表面质量要求。
模具应具有足够的强度和刚度,以抵抗金属液体的压力和温度变化。
同时,还应考虑到材料浇注和铸造后的冷却收缩等因素,并合理设置浇口、排气口和浇筑系统。
3. 浇注温度控制:熔模铸造的关键是要控制好金属液体的浇注温度。
过高的温度会导致铸件表面粗糙,过低的温度则会引起金属流动的困难。
因此,在铸造前,需要对金属液体进行合适的预热和测温,确保温度控制在合适的范围内。
4. 熔模烧结:熔模铸造的首要步骤是烧结模具。
烧结过程需要控制好温度和时间,以保证模具能够具备足够的强度和耐火性。
烧结后,还需要进行模具的表面修整和涂料处理,以提高模具的表面质量和涂层的粘附力。
5. 金属液体的浇注:对金属液体进行浇注时,需要注意浇注速度和浇注方式。
过快的浇注速度会引起金属液体剧烈冲击模具,容易导致模具破裂或产生气孔和夹杂物。
而过慢的浇注速度则会导致金属液体凝固不完全。
此外,还需注意金属液体的均匀浇注,避免产生冷隔。
6. 冷却和晾热处理:在铸造完成后,需要对铸件进行冷却和晾热处理。
冷却过程应缓慢进行,以防止因温度变化引起的热应力和变形。
晾热处理有助于提高铸件的机械性能和组织均匀性。
总之,熔模铸造的工艺设计要点及注意事项包括材料选择、模具设计、浇注温度控制、熔模烧结、金属液体的浇注和冷却晾热处理等。
合理的工艺设计能够确保铸件的质量和精度,提高生产效率和产品品质。
继续写:7. 模具温度控制:熔模铸造中,模具温度的控制是非常重要的。
模具的温度过高会导致模具磨损加剧,模具寿命减少,并且可能引起铸件的气孔和缺陷。
第一章.熔模铸造
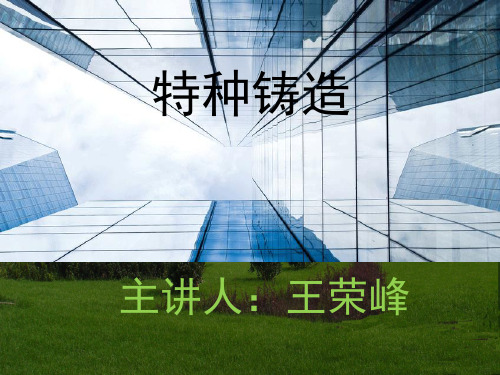
目前常用的铝硅系耐火材料有以下几种: 1)粘土质耐火材料 是指Al2O3的质量分数约30%一46%,矿物组成以 高岭石为主的耐火粘土,其分子式为 Al2O3·2SiO2·2H2O。分为生料(软质粘土) 和熟 料(硬质粘土),主要用于加固层涂料。
2)铝矾土( Al2O3含量在45~80% )
高岭石及含水氧化铝(水铝石αAl2O3·H2O、波 美石γAl2O3·H2O,三水铝石Al2O3·3H2O等)。 3)莫来石质耐火材料( Al2O3含量在67~72% ) Al2O3含量在67~72% 。
1、对粘结剂性能的要求 应能将粉状和粒状耐火材料牢固地粘结在一起。使 型壳具有足够高的强度; 应具有良好的耐热性,以保证型壳在高温焙烧、浇 注以及铸件凝固过程中具有足够的高温强度, 粘结剂最终生成的耐高温氧化物,在高温下应具有 良好的化学稳定性。 应能很好润湿熔模,与模料不起化学反应,保证准 确复制出熔模轮廓,使型壳内表面光滑; 具有适当的粘度,保证制壳过程中有良好的涂挂性 和渗透性。
α鳞石英应在1470℃时转变为α方石英,但若快 速加热,α鳞石英将过热而在1670℃熔化为熔体 (DD‘)。
正常条件下,α鳞石英不变为α石英。 在高低温转变中,方石英之间的体积变化最为剧烈, 其次是石英,鳞石英变化最微弱。 熔体(熔融石英)经急冷后得到石英玻璃。
(2)熔模铸造用硅砂牌号:
硅砂适用于碳钢、低合金钢、铸铁及铜合余铸件 不适用于高锰钢及高合金钢铸件。
2)浓度
水玻璃的浓度实际指的是其中硅酸钠的含量,一般用 密度来间接表示。
一般用密度表示:
低密度:粘度低,可配制粉液比高的涂料,型壳工作 表面的致密,但制的的型壳强度低,一般只用在制 面层涂料,常取ρ=1.25~1.27g/cm3。
熔模铸造

序论熔模铸造:英文名称:investment casting定义:在由易熔材料制成的模样上涂敷耐火材料形成型壳,熔出模样,注入液态金属冷却后,获得铸件的方法。
1.1 发展概况熔模铸造是用可溶性一次模和一次型使铸件成型的铸造方法。
现代熔模铸造工艺是用压型压制熔模、打开压型取出熔模、组合模组、将模组浸入涂料桶中上涂料、撒砂、让型壳干燥,形成一定厚度的型壳、脱除型壳中的蜡、型壳焙烧、浇注金属液、脱壳和清理。
熔模铸造又称失腊法,它的产品精密、复杂、接近铸件最后形状,可不加工或很少加工就可以使用,故熔模铸造是一种近净形成性的现金工艺。
失腊法是用腊制作所要铸成器物的模子,然后在腊模上涂以泥浆,这就是泥模。
泥模晾干后,在焙烧成陶模。
一经焙烧,腊模全部熔化流失,只剩陶模。
一般制泥模时就留下了浇注口,再从浇注口灌入铜液,冷却后,所需的器物就制成了。
用这种方法铸出的铜器既无范痕,又无垫片的痕迹,用它铸造镂空的器物更佳。
中国传统的熔模铸造技熔模铸造术对世界的冶金发展有很大的影响。
现代工业的熔模精密铸造,就是从传统的失蜡法发展而来的。
虽然无论在所用蜡料、制模、造型材料、工艺方法等方面,它们都有很大的不同,但是它们的工艺原理是一致的。
四十年代中期,美国工程师奥斯汀创立以他命名的现代熔模精密铸造技术时,曾从中国传统的失腊法得到启示。
1955年奥斯汀实验室提出首创失蜡法的呈请,日本学者鹿取一男根据中国和日本历史上使用失蜡法的事实表示异议,最后取得了胜诉。
在易熔材料制成模样,在模样表面包覆若干层耐火材料制成型壳,再将模样熔化排出型壳,从而获得无分型面的铸型,经高温焙烧后即可填砂浇注的铸造方案。
由于模样广泛采用蜡质材料来制造,故常将熔模铸造称为“失蜡铸造”。
熔模铸件的形状一般都比较复杂,铸件上可铸出孔的最小直径可达0.5mm,铸件的最小壁厚为0.3mm。
在生产中可将一些原来由几个零件组合而成的部件,通过改变零件的结构,设计成为整体零件而直接由熔模铸造铸出,以节省加工工时和金属材料的消耗,使零件结构更为合理。
熔模铸造工艺设计(3篇)

第1篇摘要:熔模铸造是一种精密铸造方法,具有精度高、表面光洁、尺寸稳定性好等优点。
本文介绍了熔模铸造的基本原理、工艺流程、材料选择、熔模制作、浇注系统设计、冷却系统设计、质量检测等方面的内容,以期为熔模铸造工艺设计提供参考。
一、熔模铸造基本原理熔模铸造是利用蜡或塑料等可熔化材料制作成具有复杂形状的熔模,然后将熔模放入型壳中,通过加热使熔模熔化,金属液体充填熔模所形成的空腔,冷却凝固后取出型壳,得到与熔模形状相同的金属铸件。
熔模铸造工艺具有以下特点:1. 精度高:熔模铸造的精度可达0.1mm,表面光洁度可达Ra0.1~0.2μm。
2. 材料广泛:可用于各种金属材料的铸造,如不锈钢、铝合金、铜合金、钛合金等。
3. 可铸性优良:熔模铸造适用于形状复杂、尺寸精度要求高的铸件。
4. 生产周期短:熔模铸造工艺流程短,生产周期短,可满足大批量生产的需求。
二、熔模铸造工艺流程1. 设计与工艺分析:根据铸件要求,进行铸件设计、材料选择、工艺参数确定等。
2. 熔模制作:采用蜡或塑料等可熔化材料制作熔模,熔模形状与铸件相同。
3. 型壳制作:将熔模放入型壳中,通过加热使熔模熔化,金属液体充填熔模所形成的空腔。
4. 浇注系统设计:根据铸件要求,设计合理的浇注系统,确保金属液体充填铸件空腔。
5. 冷却系统设计:设计合理的冷却系统,保证铸件冷却均匀,避免产生缩孔、裂纹等缺陷。
6. 铸造:将金属液体浇注到型壳中,经过冷却凝固后取出型壳,得到铸件。
7. 后处理:对铸件进行打磨、抛光、热处理等工序,提高铸件质量。
三、材料选择1. 熔模材料:蜡、塑料等可熔化材料,具有良好的可塑性、熔点适中、表面光洁度高。
2. 型壳材料:耐火度高、导热性好、强度高的材料,如耐火土、硅砂等。
3. 金属液体:根据铸件材料要求,选择合适的金属液体,如不锈钢、铝合金、铜合金等。
四、熔模制作1. 熔模设计:根据铸件形状、尺寸、精度要求,设计合理的熔模结构。
2. 熔模制造:采用蜡或塑料等材料,采用手工或机械加工方法制作熔模。
- 1、下载文档前请自行甄别文档内容的完整性,平台不提供额外的编辑、内容补充、找答案等附加服务。
- 2、"仅部分预览"的文档,不可在线预览部分如存在完整性等问题,可反馈申请退款(可完整预览的文档不适用该条件!)。
- 3、如文档侵犯您的权益,请联系客服反馈,我们会尽快为您处理(人工客服工作时间:9:00-18:30)。
组装模组
型壳制造、 脱蜡、焙烧
填砂、浇注
观看 影片
熔模铸造的特点
1)、铸件尺寸精度高(CT4-CT7);表面 粗糙度低(Ra1.6-6.3μm)。减少了铸件的 切削加工余量,甚至可实现近净型铸造。
2)、能生产形状复杂的薄壁铸件。如前机 匣(由内、外环和14件叶片组成)。如发动 机叶片,叶型的最小壁厚可达0.7mm。
不合理
5).减少不通孔
合理
不合理
6).简化压型加工
合理
不合理
7).设计必要的工艺筋
A).防止环形件、框型件变形设计的工艺筋
B).防止铸件开口部位变形而设计的工艺筋
C).减少大平面,防止壳形变形
8).设计必要的工艺孔
A).防止大平面型壳变形设计工艺孔
B).减少热节、防止缩孔设计工艺孔
二.铸件结构要素及工艺参数选定
4.在熔化易熔模时,起液体模料流出的通 道作用,浇注系统应能保证排除模料通畅。
二、浇注系统结构
按浇注系统组成分为: 1)直浇道一内浇道结构形式: 直浇道兼起冒口作用,操作方便,但排渣不利。
2)横浇道一内浇道结构形式: 常用于顶注,有利于顺序凝固。
3)直浇道一横浇道一内浇道结构形式
按合金液注入铸件部位分为: 1)顶注式: 合金液从型腔的顶部注入,铸件自下而上凝固, 合金液易飞溅,排气不畅,适用于高度较低的 铸件。
2.0
2.0 2.5 2.5
3.0~4.0
3.0~4.5 3.0~5.0 3.5~5.0
2.5
2.5 3.0 3.0
3.5~5.0
4.0~5.0 4.0~6.0 4.0~6.0
3.0
3.5 3.5 3.5
铝合金
碳钢 高温合金
2.0~2.5
2.0~2.5 0.9~2.0
1.5
1.5 0.6
2.5~4.0
1 熔模铸造
1.1
概述
定义:用熔模材料(通常为低熔点的 材料如蜡料)制成熔模样件并组成模 组,然后在模组表面上涂料(耐火材 料),待干燥固化后,将模组加热熔 出模料形成中空型壳,经高温烧结后 浇注金属液体,清理后得到铸件。由 于熔模材料通常为蜡基材料,因此又 称“失蜡铸造”。
工艺流程:
压型制造
熔模样件 制造
当量热节圆直径Dc的求法
重量系数K的求法
当量热节法计算举例 制动凸轮铸件如图所示,铸件重230g
1)铸件热节部位截面axb:16mm×30mm 2)由图查当量热节直径Dc,用直尺连接a=30mm, b=16mm,两点交Dc线于一点,即得Dc=21mm。
3)根据铸件重量W=230g,Dc=21mm。查图求重 量系数K,用直尺连接W,Dc两点交K线于一点, 该点为K=0.89。 4)根据d=K×Dc,可求得d=0.89×21=18.8mm 5) 当采用矩形内浇道时,先定矩形某一边尺 寸a=16mm,然后返过来应用图,由a=16, d=18.8查得b=23mm,于是内浇道截面尺寸定为 16×23mm
常用压型类型
类型
机械加工压型
特 点
1.材料通常为钢,也有使用铜合金、铝合金 2.尺寸精度可以充分满足设计要求,型腔表面粗糙度 Ra=1.6~0.4цm 3.使用寿命可达10万次以上 4.制造成本高 1.材料:低熔点合金(通常熔点不超过300℃) 2.尺寸精度比机械加工压型低,型腔表面粗糙度 Ra=3.2~0.8цm 3.使用寿命可达几千次以上 4.制造成本较低 1.材料:石膏 2.尺寸精度低,型腔表面粗糙度Ra=6.3~1.6цm 3.母模可用木模,生产周期短,成本低
1.2.2 熔模铸造浇注系统设计
一、浇注系统作用 1.把液体金属引入型腔 注意充型平稳,避免金属液氧化和卷入气体, 保证不产生冷隔和浇不足缺陷。 2.补充液体金属凝固时体积收缩 浇注系统应能保证补缩时通道畅通,并保证 能提供给铸件必要的补缩金属液,避免铸件 产生缩孔、疏松。
3.在组焊与制壳时起支撑易熔模和型壳作 用。要求有足够强度,防止制壳过程中易熔 模脱落。
一、铸件结构的合理性 铸件结构是否合理,对于铸件质量、生产工 艺的可行性和简易性以及生产成本等影响很大, 根据生产实际,总结出铸件结构合理性的几条 基本原则。
1).易于从压型中取模
合理
不合理
合理
不合理
2).易于抽芯
合理
不合理
合理
不合理
3).壁厚均匀,减少热节
合理
不合理
4).避免大平面
合理
2.5~4.0 1.5~3.0
2.0
2.0 0.8
3.0~5.0
3. 0~5.0 2.0~4.0
2.5
2.5 1.0
3.5~6.0
3.5~6.0 —
3.0
3.0 —
4.0~7.0
4.0~7.0 —
3.5
4.0 —
2.圆角
一般情况下铸件上各转角处都设计成圆角, 否则容易产生裂纹、缩松。铸件上内圆角和 外圆角按下式计算 r=(d+δ)/k R=r+ (d+δ)/2 r——转角内圆角mm;R——转角外圆角mm d, δ——连接壁的壁厚;k——转角的圆角 系数,根据角度大小接图选取。
应用范围
1.生产批量大的铸件 2.要求尺寸精度高、表面粗糙度 值低的铸件
低熔点合金铸造 压型
1.生产批量较大(几千件)的铸 件 2.机械加工困难的、型腔复杂的 压型 3.试生产铸件 1.单件小批生产 2.精度要求较低铸件 3.试生产铸件
石膏压型
硅橡胶压型
1.材料:硅橡胶 2.填充性好,复制性强、周期短 3.精度低,抗拉强度低、寿命短 4.质地较软,使用时外形需要硬质材料衬托
5.加工余量
熔模铸件单面加工余量(单位 mm)
≤50 铸件最大尺寸 单面加工余量 浇口面加工余量 0.5 0.5~0.1 1.0~1.5 2.0~4.0 1.5~2.0 2.0~3.0 >50 ~120 >120 ~250 >250 ~400 >400 ~630
6.线收缩率
影响熔模铸件尺寸的收缩因素包括合金 的收缩;模料的收缩;型壳的膨胀等, 这几方面综合的影响称为熔模铸件的综 合线收缩率。
2.耐热性 模料耐热性是指温度升高时其抗软化变形的能 力,它影响着熔模和铸件的精度。通常用热变 形量来表示,要求35℃温度时模量热变形量 △H35-2≤2mm。
3.收缩率 模料热胀冷缩小,才能提高熔模尺寸精度,也 才能减少脱腊时因模料膨胀引起的型壳胀裂现 象。因此模料的线收缩率是模料重要的性能指 标之一,一般应小于1%。优质模料线收缩率仅 为0.3%~0.5%。
1.最小壁厚 由于熔模铸造的型壳内表面光洁,并且一般 为热型壳浇注,因此熔模铸件壁厚允许设计 得较薄,最小壁厚与合金种类及铸件轮廓尺 寸有关。
熔模铸件的最小壁厚(单位:mm)
铸 件 轮 廓 尺 寸 铸件 材料 >10~50 >50~100 >100~200 铸 件 最 小 壁 厚 推荐值 最 小 值 0.7 推荐值 最 小 值 1.0 推荐值 最 小 值 1.5 推荐值 最 小 值 2.0 推荐值 最 小 值 2.5 >200~500 >350
热节圆直径的求法
b.当量热节法
该方法是根据补缩需要,把铸件热节换算成 一个圆柱体单元,并令该单元与铸件热节具 有相同凝固模数和重量,此单元圆柱体的直 径称为当量热节直径,那么,内浇道尺寸的 大小就以此当量直径为基础,推导出一个计 算公式:
d=k×Dc 式中 d—内浇道尺寸,mm K—重量系数 Dc—当量热节直径,mm 当内浇道为圆截面时,则d即为内浇道直径, 当铸件热节部位的截面形状为长方形断面axb 时,可由图求得当量热节圆直径Dc,K为重量 系数,根据铸件重量W和Dc,由图查出。
铅锡合金
1.0~1.5
1.5~2.0
2.0~3.0
2.5~3.5Βιβλιοθήκη 3.0~4.0锌合金
铸铁 铜合金 镁合金
1.5~2.0
1.5~2.0 2.0~2.5 2.0~2.5
1.0
1.0 1.5 1.5
2.0~3.0
2.0~3.5 2.5~4.0 2.5~4.0
1.5
1.5 2.0 2.0
2.5~3.5
2.5~4.0 3.0~4.0 3.0~4.0
3.铸造斜度
为了便于取模,抽芯,在拔模面应设有铸造 斜度,铸造斜度的取值如下。 熔模铸件的铸造斜度
铸造斜度面高 h/mm 非加工面斜度 外表面 内表面
≤20 取值 >20-50 >50-100
>100
0º 20´ 0º 15´ 0º 10´
0º 10´
1º 0º 30´ 0º 30´
0º 15´
4.最小铸出孔
S内≤S横≤S直
优点: 1)金属液完全充满浇注系统,可防止金属 液卷入气体。 2)有较好挡渣能力 缺点:进入型腔流速高、产生喷溅和冲砂、 氧化。
开放式浇注系统 S直 ≤S横≤ S内 优点:因为金属液不能充满浇注系统, 金属液流动平稳,充型快;
缺点:挡渣效果差。
2)、内浇道尺寸的确定 a.比例系数法
3)、合金材料不受限制. 钢铁、铜、铝、钛、 镁等。熔点高的镍基高温合金;锌、锡等低熔 点金属。
4)、熔模铸造存在一定局限性。工艺流程 烦琐,生产周期长、铸件尺寸不宜太大。
熔模铸造典型产品应用实例
1.2 熔模铸件工艺设计
1.2.1 铸件结构设计
目的就是对于一些零件图做必要修改,得到适 合熔模铸造特点的最合理的铸件结构。
2)侧注式: 合金液从型腔侧面注入,铸件补缩好,应用 较广泛。
3)底注式: 合金液型腔底部平稳注入,不易产生夹渣。气 孔。不利于顺序凝固,需增设冒口。
三、浇注系统计算
步骤: 1)确定浇注系统形式:
封闭式或开放式。