品质管理的三现五原则
三现五原则培训讲义

五原则
1.
◎现状把握的目的 1.真对问题全面调查事实. 2.掌握变异. 3.归纳可疑方向
查明要因 真因追查
5W分析 特性要因图 再现试验 NG再现试验 OK再现实验
2.
问题 要因 真因 查明真因
不良原因 流出原因
≈
何谓三现五原则
≈
适当对策
*已留入市场处理
临时对策
*库存成品处理 *半成品处理 *在库物料处理
标准化
S.O.P修正
*试验规范 *限度样品
三现五原则对策注意事项 1.无科学根据DATA之解析对策
2.以偏盖全之解析对策
3.增加不必要成本之解析对策
4.以变更设计改善制程变异之改善对策 5.变化点分析不明确之解析对策 6.无回馈标准之解析对策 7.无再现之解析对策
8.无三现之解析对策
9.无制程面、流出面检讨之解析对策 10.五层分析内容不连续解析对策
一.没有科学根据DATA 问题点:常发生的直觉判断 焊接强度不足 对策:加锡 正确吗? 焊接器件不粘锡 对策:焊接温度提升10度 没问题吗?
思 考:加锡/提高烙铁温度10度如何得来的? 直觉+经验≠事实 100个直觉或经验不如1个数据
分析方法:科学的根据=实验数据 有实验的数据才能决定新的标准. 要去试验出加锡及温度提高10度是最好的作业条件.
三现五原则讲义
前
一.背景
言
1.品质是企业生存的基本条件. 2.品质经常发生异常.成本损失大. 3.品质不良,操作人员总是认为是品管部门的责任. 4.不良解析经常找不到真因.
二.基本想法
1.籍由提高三现五原则解析能力.真正改善重要的品质问题点. 2.解决问题 持续有效的解决问题 不再是问题
三现五原则-最终版

要点二
详细描述
为了确保三现五原则的有效实施,企业应重视员工的培训 与参与。这可以通过开展定期培训、提供学习资源、鼓励 员工参与决策等方式实现。此外,企业应建立良好的激励 机制,表彰在原则实施过程中表现优秀的员工,以提高员 工的积极性和参与度。通过提高员工素质和参与度,企业 可以进一步推动三现五原则的落实,实现更好的发展成果 。
持续改进与优化的实施与效果
总结词
持续改进与优化是五原则的核心目标之一,它有助于组 织不断适应变化、提高竞争力和可持续发展。
详细描述
组织需要鼓励员工不断寻求改进和优化的机会,并为其 提供必要的资源和支持。这包括制定改进计划、设立改 进团队、引入创新技术和方法等。同时,组织还需要建 立有效的绩效评估体系,以衡量改进与优化的成果并持 续改进。持续改进与优化能够提高生产效率、降低成本 、增强创新能力、提升客户满意度和增强组织竞争力。
现状反思
定期对当前的工作情况进行反思和总结,找出可以改 进的地方。
现行措施调整
根据实际情况和反馈,及时调整现行措施,以实现持 续改进的目标。
04
五原则的实施与效果
管理层的决心和承诺的实施与效果
总结词
管理层对实施五原则的决心和承诺是至关重 要的,它决定了整个组织对五原则的重视程 度和执行力。
详细描述
VS
详细描述
随着企业内外部环境的变化,三现五原则 的实施方案也应不断调整和完善。企业应 定期评估原则的执行情况,总结经验教训 ,并根据实际情况调整实施方案。此外, 企业应关注行业动态和最佳实践,不断引 入新的理念和方法,以保持原则的先进性 和有效性。
原则五:员工培训与参与
要点一
总结词
员工培训与参与是三现五原则的重要支撑,需要提高员工 素质和参与度。
品质的三现五原则
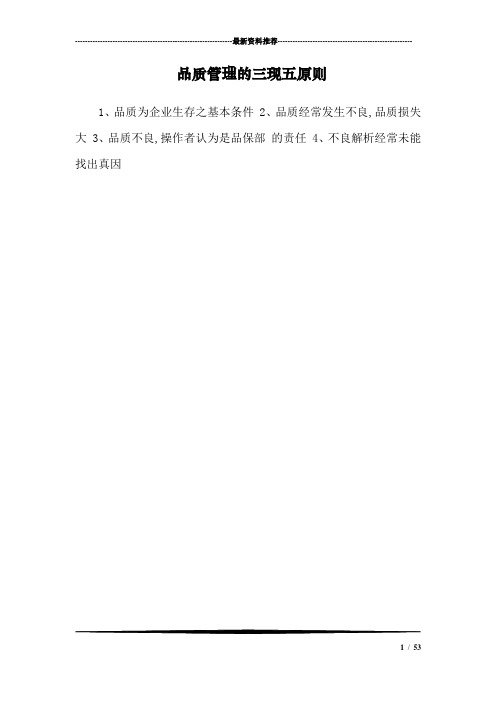
---------------------------------------------------------------最新资料推荐------------------------------------------------------品质管理的三现五原则1、品质为企业生存之基本条件2、品质经常发生不良,品质损失大3、品质不良,操作者认为是品保部的责任4、不良解析经常未能找出真因1/ 531、了解并运用三现五原则解析手法,真正改善重要品质问题2、解决问题→持续有效解决问题→不再是问题3、解决客诉品质问题挑战“零不良”---------------------------------------------------------------最新资料推荐------------------------------------------------------ 三、三现现物三现现状现场3/ 53现状把握确认项目1、机种、零件名称/号码 2、发生场所/环境/使用条件 3、发生的现象/问题 4、发生日期 5、引擎号码---------------------------------------------------------------最新资料推荐------------------------------------------------------ 现状把握确认项目6、发生件数/严重性 7、行驶里程/耐久性 8、制造日期/批重性 9、出车日期/库存性 10、不良品品质确认5/ 53现状把握确认项目11、量产中品质水准确认 12、开发阶段品质水准比对 13、设计变更履历 14、其他异常履历 15、标准确认(图面、作业、控制计划、检验标准…)---------------------------------------------------------------最新资料推荐------------------------------------------------------ 四、五原则五原则7/ 531、把握现况现状把握目的针对问题,全盘调查事实掌握变异(机遇/非机遇原因) 归纳可疑方向---------------------------------------------------------------最新资料推荐------------------------------------------------------ 1、把握现况 - 5W2H–类型、种类、受影响的部分。
三现五原则教材

为了使在调查过程中不要遗漏有用的信息和重要事实,要 多听、多看(严禁带有成见)在确认过程中尽可能地使用(3 现实主义),在进行原因分析时,要最大限度使用“特性要素 图”
现状把握举例:
1、 3、 4、 6、 机种、型号 2、 发生状况:(市场、公司内) 问题发生时的现象或(当事人的)申诉 发生年月日 5、 发生件数 对发生问题机种或是零部件的处置结果。
五原则三----对策实施
临 时 对 策 适 当 对 策 (防止恶化扩大) 永 久 对 策 (避免再发) •已流入市场处理 •库存成品处理 •半成品处理 •不良品处理 •制造面、流出 面之治本对策 •水平展开对策 •工程作业者 •进料检验者 •市场服务者 (品质通报)
对策情报传达
适当的对策(对策内容、效果预测PPA)
為什 麼之 飾條素材 五層 產生縮水 分析
2
目視檢查時 未檢查
3
無檢查基準
4
加熱不均 勻 模具損壞
5
溫度控 制損壞 未按規 定檢查
射出時素材加熱 飾條素材表 變形 面NG 模具與飾條間隙 過大
1、五層分析是三現五原則原因解析之濃縮重點內容。 2、五層分析是同說故事一樣,故事必須連貫。 3、五層分析是三現五原則單之中心思想及佈局。
不良实物
不良发生的状况, 包括使用状况 不良品发生的原 地、环境因素
五原则一--------现状把握
现状把握目的 针对问题,全盘调查事实掌握变异(机遇/非机遇原因)归纳可 疑方向 对事实的把握(现在生产的该零部件的品质状况、现象、问题 内容、发生次数、5W2H处置内容)
现状把握内容
1、问题点的概要(信息的收集、整理)例,针对部品或工程。 2、问题再现试验的结果 3、现行品的品质状况 4、发生的对象范围 5、利用绘图、图表、柱状图使问题明确化。 6、将可能想到的原因、内容,详尽的进行整理,在记录上明 确的记载。
三现五原则管理办法

1.目的
为了对发生不符合事项时能有效地解决及预防,从而使顾客满意。
2.范围
公司内部及特定要求的顾客。
3.定义
三现----现场、现时、现物。
五原则----事实把握、原因究明(五层分析)、适当对策、效果确认、回馈标准。
4.职责
质检部为发出与效果追踪的主管部门。
责任部门为原因分析与对策实施的主管部门。
5.流程图
6.程序
6.1客诉,内审不符合,制程异常,进料异常发生。
6.2质检部会同相关部门分析责任归属。
6.3质检部发出[不良对策要求书]。
6.4责任部门对不符合事项进行原因分析并会同相关部门提出暂定对策及永久对策。
6.5质检部对对策内容进行效果追踪确认。
6.6影响相关文件时须对相关文件进行修改更新。
6.7对策横向展开。
7.相关文件(无)
8.相关表单
[品质安定化推进表](附件一)
[三现五原则报告](附件二)。
三现五原则表
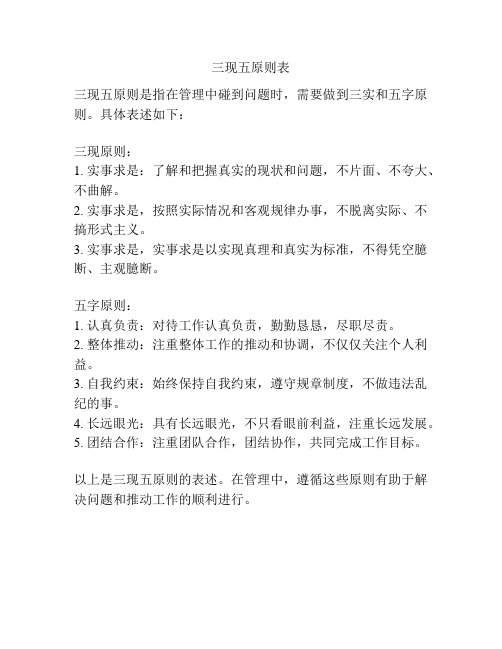
三现五原则表
三现五原则是指在管理中碰到问题时,需要做到三实和五字原则。
具体表述如下:
三现原则:
1. 实事求是:了解和把握真实的现状和问题,不片面、不夸大、不曲解。
2. 实事求是,按照实际情况和客观规律办事,不脱离实际、不搞形式主义。
3. 实事求是,实事求是以实现真理和真实为标准,不得凭空臆断、主观臆断。
五字原则:
1. 认真负责:对待工作认真负责,勤勤恳恳,尽职尽责。
2. 整体推动:注重整体工作的推动和协调,不仅仅关注个人利益。
3. 自我约束:始终保持自我约束,遵守规章制度,不做违法乱纪的事。
4. 长远眼光:具有长远眼光,不只看眼前利益,注重长远发展。
5. 团结合作:注重团队合作,团结协作,共同完成工作目标。
以上是三现五原则的表述。
在管理中,遵循这些原则有助于解决问题和推动工作的顺利进行。
三现五原则讲义

七:再現試驗證明
疑 問 點:你如何知道解析不良原因是正確的嗎? 思 考:科學的實驗是最好的證明→再現試驗。
分析方法:正向再現與反向再現
1.正向:將不良要因排除(不良條件修正)後會製 造出良品。 2.反向:以不良條件生產會製造出不良品。 若上述二向再現結果與假設違背,則肯定所解析 出之不良原因必定有偏差。 3.不良品再現
QC OK 工程表
OK OK
知識 為 不了解重點 何 新 左 手 前 不熟練 椅 未檢查 椅 檢具 背 晃 檢出力 動 未製作
標準文件
太寬鬆
設備
未規劃
2.查明原因(再現試驗、原因分析)
3.適當的對策(對策內容、對策後實際效果確認) 4.對策本案所費工時
NO 發生不良原因 對策內容 擔當 期限 蔡 正 欽 05/ 03/ 28 確認結果
三.目的:
1.交貨品質100PPM↓ 2.市場品質問題挑戰“零不良”
三現五原則
市怨編號 反應單位 反應者 K0504001 廠異編號 張 木 信 主管 管制單位 品 質 檢 查 課 承辦者 主管 尤 宏 文 游 家 齊 製 品 NY 技 術 反應日期 94 年 04 月 22 日 課 對策 單位 4PT D 指派對策者 PL
疑 問 點:1.為何會流出?為何會製造?為何設備檢不出?
2.流出面之解析對策經常被疏忽。
思
考:顧客所反應之問題必定製造面、流出面共同發生,僅
對策製造或流出面並能徹底解決問題。
分析方法:1.製造面→分析4M之變化點→真因對策。
2.流出面→a.分析製程中之流程→作業環境、作業檢
驗工程標準 b.分析檢驗之流出、出貨檢驗標準、限度 樣品、自動檢測、防呆裝置。 PS:為何會檢驗不出來。
三现五原则-现场管理

三现五原则-现场管理
三现五原则
1、三现:现场、现物、现实
2、五原则:A发生状况(现象、申诉内容、发生次数),把握事实(对零部件确认结果、原因分析、现正生产该部件品质状况);B查明原因(发生途径、问题再现试验,5个WHY的分析)C适当的对策(对策内容、效果预测)D确认效果(确认对策的实绩效果)E对源头的反馈(要落实到体系、组织标准化的内容)
现场-----解决问题要到问题发生的场所去
把现场看作问题发生的根源、管理水平提升的基石。
与其费尽心思追求制度的“完美”,不如踏踏实实搞好现场,才有“水到渠成”的效果。
现物-----对发生问题的对象进行确认
认为现场的问题往往有形有据,哪里发生了问题,对什么造成影响,都应加以明确。
“涓涓细流,汇聚成河”
不注意小事、细节,永远难以找出问题根源
现实-----依据事实和数据找出问题的根源
抛弃完全凭经验和感觉,工作中注重数据和事实。
比如发生了不良品,不是去讨论谁的责任,而是了解“不良品的数量、比率、什么样?在哪里发生?怎样发生?”事实胜于雄辩,事实胜于猜测,就是现实的意识。
品质管理三现五原则

品质管理三现五原则嘿,朋友们!今天咱们来聊聊品质管理的三现五原则,这可不像听起来那么枯燥哦。
先说说三现吧,所谓三现就是现场、现物、现实。
这就好比是破案,现场就是犯罪现场,那是所有线索的源头。
要是品质出了问题,你不到现场去,就像侦探光靠想象猜犯人一样不靠谱。
现场就像是一个充满秘密的魔法阵,每个角落都可能藏着解开品质谜题的关键。
现物呢,就是这个魔法阵里的魔法道具啦,那些产品、零部件就像是有话要说的小物件,你得仔细端详它们,就像端详宝藏一样。
而现实呢,就是要面对真实发生的情况,不要自欺欺人,别以为在办公室里瞎琢磨就能搞定品质问题,那是不可能的,这就像你想知道鱼的滋味,却只看画一样荒谬。
再来说说五原则,那可是品质管理的五大神器。
第一个原则就像是给品质问题照X光,要查明原因。
这原因啊,就像调皮的小怪兽躲在暗处,你得拿着放大镜,把它揪出来。
有时候原因可能超级复杂,就像一团乱麻,你得耐心地一点点解开。
第二个原则是要采取措施,这措施就像是超级英雄的技能。
针对那些品质小怪兽,得使出对应的绝招。
要是问题是个大恶魔,你还慢悠悠地出招,那就等着品质灾难降临吧,就像面对洪水只拿个小勺子舀水一样可笑。
第三个原则是要确认效果。
这就像是考完试看成绩一样,你得看看你那些超级英雄的招数有没有打败小怪兽。
如果没效果,那就像放了个哑炮,白忙活一场。
第四个原则是要标准化,这就像把成功的魔法咒语记录下来,让所有人都能照着做。
要是不标准化,就像每个人都按照自己的想法做菜,那做出来的味道肯定千奇百怪,品质也就乱套了。
最后一个原则是要防止再发生,这就像是给品质城堡修个坚固的城墙。
不能让那些问题小怪兽再次入侵,要是不做好防范,就像补了东墙西墙又破了,永远在救火,忙得晕头转向。
品质管理的三现五原则啊,其实就是一场和品质问题斗智斗勇的有趣游戏。
我们得像勇敢的探险家一样,在现场这个神秘的世界里,通过现物这个神奇的媒介,找到现实中的答案,再挥舞着五原则这五把宝剑,把品质管理得妥妥当当。
3即3现原则

3即3现原则
1.【问题】3即3现原则
【答案】3即3现原则整理如下,供大家学习参考。
三现原则是现场、现物、现实。
现场是解决问题要到问题发生的场所去,把现场看作问题发生的根源、管理水平提升的基石。
现实是依据事实和数据找出问题的根源。
生产管理中的五原则:
1、发生状况(现象、申诉内容、发生次数),把握事实(对零部件确认结果、原因分析、现正生产该部件品质状况)。
2、查明原因(发生途径、问题再现试验,5个WHY的分析)。
3、适当的对策(对策内容、效果预测)。
4、确认效果(确认对策的实绩效果)。
5、对源头的反馈(要落实到体系、组织标准化的内容)。
三现五原则--最终版
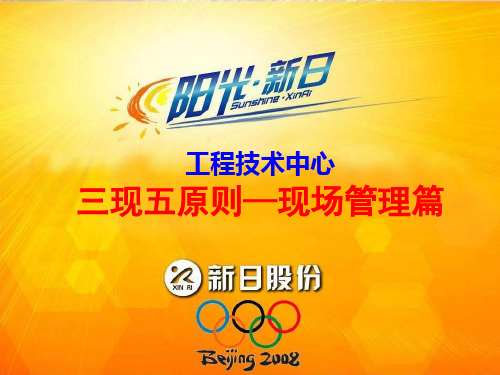
查明原因
查明原因
流出原因 问题 要因 真因
质 量 ● 创 新 ● 服 务
(流出面)
2、查明原因
WHY WHY分析 1、通过WHY、WHY的反复5次进行分析找 出真因。 2、WHY、WHY的疑问必须使之与问题现 象相关联,建立系统来进行。
质 量 ● 创 新 ● 服 务
3、WHY、WHY的分析要从问题发生的原 因(或叫硬件方面的原因)和流出 原因(又叫软件方面的原因)两方 面进行。 4、WHY、WHY分析的信息来源,基本上 是以特性要因图为基础。 5、为了说明真因,可以加入插图。
质 量 ● 创 新 ● 服 务
临时对策 适 当 对 策
(防止恶化扩大)
•已流入市场处理 •库存成品处理 •半成品处理 •不良品处理 •制造面、流出 面之治本对策 •水平展开对策
永久对策
(避免再发)
对策情报传达
质 量 ● 创 新 ● 服 务
•工程作业者 •进料检验者 •市场服务者 (品质通报)
3、采取对策
质 量 ● 创 新 ● 服 务
3.回复钱经理:已咨询技术部门,20ah配置的车型( 30A控制器)最低保障公里数在25公里,再加上目前的气候 属配置范围内正常公里数,如用户强烈可以更换(25A)控制 器;
商家表示要求技术部门的人员前往商家处实际了解 新日车和其它车的区别;建议客诉转质量部门进一 步和商家再次沟通安抚商家。
质 量 ● 创 新 ● 服 务
7、再现试验证明
疑 问 点:你如何知道解析不良原因是正确的吗? 思 考:科学的实验是最好的证明→再现试验。
分析方法:正向再现与反向再现。 1.正向:将不良要因排除(不良条件修正)后会制造 出良品。 2.反向:以不良条件生产会制造出不良品。 若上述二向再现结果与假设违背,则肯 定 所解析出之不良原因必定有偏差。 3.不良品再现。
质量管理三现五原则

2-B 查明原因(发生的途径、问题再现试验WHY WHY分析)
3 采取)适当的对策 (对策内容、效果预测PPA) 4确认(对策)效果(效果实绩) 5对(问题)源头的反馈(需落实到体制、组织的内容)
15、案例
右腕受伤
1- A 发生状况(现象、申诉内容、发生次数、5W1H处置内容)
1、发生场所:汽缸压铸NO.2生产线。 2、 发生状况:请参照右手腕受伤素描图
检验: 为何会检测不出来。
10、五层分析
意义:为什么之五层分析是一个形容 词,代表追根究底的意思,其目 的在寻求真正的原因,并不是一 次要作五次为什么分析,可以比 五次少,也可以比五次多,只要 能寻求出真正的原因。
10、五层分析
实例说明: 不良现象:踩刹车时有上、下作动感觉。
1
2
3
4
5
目视检查
为什 Drum内 未检查
3、五层分析是三现五原则单之中 心思想及布局。
11、要因 对策案例练习
1.要因:人为疏忽 对策:教育训练加强
2.要因:XX治具磨损 对策:更换新治具
3.要因:遗漏焊接 对策:后工程实施全检以确保
4.要因:半成品因台车太小不慎流入后工程 对策:台车修改加大
5.要因:修护车辆,等待时间长 对策:等待时间提供杂志阅读
1、把握现况 - 5W2H
WHERE 何地 – 记入问题发生的场所。 WHY 为什么 – 具体的内容 HOW 怎么样 – 问题是怎样发生的 HOW MANY 什么程度 – 问题发生量,
程度。
1、把握现况的填写方法
1、问题点的概要(信息的收集、整 理)。例:针对部品或工程。
2、问题再现试验的结果 3、现行品(现在生产)的品质状况 4、发生的对象范围
品质管理的三现五原则
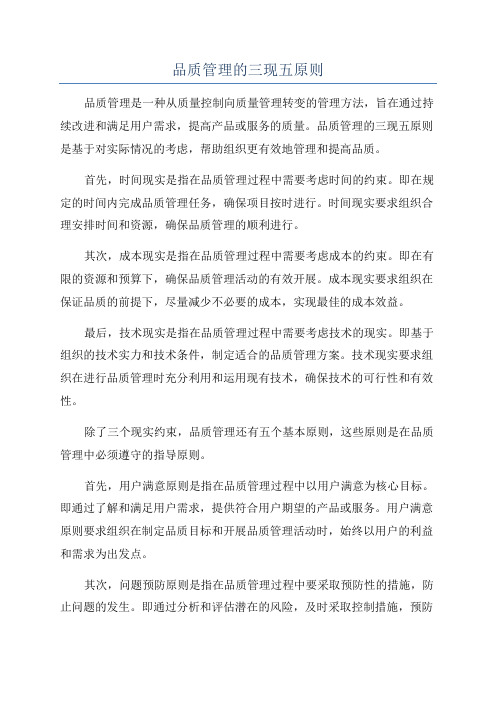
品质管理的三现五原则品质管理是一种从质量控制向质量管理转变的管理方法,旨在通过持续改进和满足用户需求,提高产品或服务的质量。
品质管理的三现五原则是基于对实际情况的考虑,帮助组织更有效地管理和提高品质。
首先,时间现实是指在品质管理过程中需要考虑时间的约束。
即在规定的时间内完成品质管理任务,确保项目按时进行。
时间现实要求组织合理安排时间和资源,确保品质管理的顺利进行。
其次,成本现实是指在品质管理过程中需要考虑成本的约束。
即在有限的资源和预算下,确保品质管理活动的有效开展。
成本现实要求组织在保证品质的前提下,尽量减少不必要的成本,实现最佳的成本效益。
最后,技术现实是指在品质管理过程中需要考虑技术的现实。
即基于组织的技术实力和技术条件,制定适合的品质管理方案。
技术现实要求组织在进行品质管理时充分利用和运用现有技术,确保技术的可行性和有效性。
除了三个现实约束,品质管理还有五个基本原则,这些原则是在品质管理中必须遵守的指导原则。
首先,用户满意原则是指在品质管理过程中以用户满意为核心目标。
即通过了解和满足用户需求,提供符合用户期望的产品或服务。
用户满意原则要求组织在制定品质目标和开展品质管理活动时,始终以用户的利益和需求为出发点。
其次,问题预防原则是指在品质管理过程中要采取预防性的措施,防止问题的发生。
即通过分析和评估潜在的风险,及时采取控制措施,预防品质问题的发生。
问题预防原则要求组织采取主动的管理方式,不仅仅局限于纠正已发生的问题,而是通过预防控制,防患于未然。
第三,连续改进原则是指在品质管理过程中要持续改进产品或服务的质量。
即通过不断地调查、分析和改进,实现产品或服务质量的持续提升。
连续改进原则要求组织采用有系统的方法,积极参与持续改进活动,使品质管理成为组织文化的一部分。
第四,全员参与原则是指在品质管理过程中要全员参与,实现全员质量意识的提升。
即通过培训和教育,激发员工对品质的认知和责任感。
全员参与原则要求组织在品质管理中形成团队合作的氛围,凝聚全体员工的力量,共同推动品质的提升。
质量管理中的三现五原则(解决问题的经典套路)

质量管理中的三现五原则(解决问题的经典套路)质量管理中的三现五原则(解决问题的经典套路)2020-08-05 17:00今天,九脑汇学院就来说⼀说质量管理中三现五原则,所谓三现即:现物、现状、现场,包含这三点,希望这份资料能对⼤家有所收获。
三现主义企业常见的缺乏“三现主义”的现象:等待⽣产现场的联系或⽣产现场对于技术、品质、资材等部门服务、指导、指⽰、供应的等待。
等待下级的汇报,任务虽已布置,但是没有检查,没有监督。
不主动去深⼊实际调查研究,掌握第⼀⼿资料,只是被动地听下级的汇报,没有核实,然后作决定或向上级汇报,瞒天过海没有可信度,出了问题,责任往下级⾝上⼀推。
注:“三现主义”的缺乏是等待中的最致命原因之⼀,严重影响⽣产现场⼯作的及时解决。
现场不要只坐在办公室决策,⽽是要⽴即赶到现场,奔赴第⼀线。
现场是⽣机勃勃的,每天都在变化,不具备正确的观察⽅法,你就没法感觉它的变化,包括异常。
现物管理的最重要的概念是“总是以事实为基础⽽⾏动”,解决问题要求你找到事实真相。
因为只有⼀个真理存在,最通⽤的⽅法是“到问题中去,并客观地观察其过程”。
观察你看不到的地⽅,这时,事实将出现。
要发现其变化的原因,仔细观察事实。
当你这样做时,隐藏的原因将会出现,这样做,你可以提⾼发现真相的能⼒。
现实解决问题需要你⾯对现实,把握事实真相。
我们需要⽤事实解决问题,⽽事实总是变化⽆常的,要抓住事实就要识别变化,理想与实际总是有很⼤的差距。
很多问题如果我们不亲临现场,不调查事实和背景原因,就不能正确认识问题。
但为什么会发⽣那样的问题呢?我们要多问⼏次“为什么”,对“现物”、“现实”进⾏确认。
五原则五原则是指从三现主义(现场、现物、现实)出发,分五个步骤来解决问题:五原则的重要思想:①从“三现主义” (现场、现物、现实)出发解决任何问题都应当最先掌握现场、现物、现实中有⽤的实际情况。
如果没有掌握实际情况。
那么,从⼀开始就⾛弯路,⾛得越远,误差越⼤,当然最终得不出真正的结论。
三现五原则--最终版
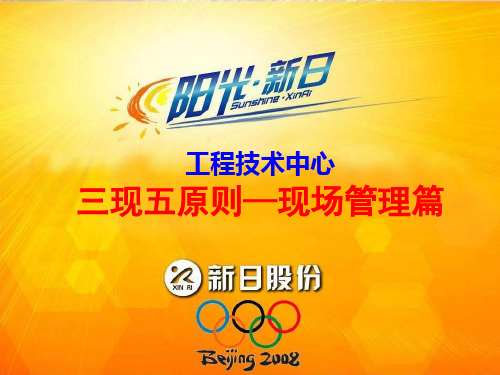
只有在 针对 才能通过观察、分析把握到 。在 我们即将讲到的“五原则”中,三现是其根本基础,离开三现,一切都 会沦为空谈。
现场
现物
现实
质 量 ● 创 新 ●● 创 新 ● 服 务
学习目的
1、了解并运用五原则解析 手法,真正改善重要品质问 题 2、把问题追溯到源头,从根本上解决问题 3、治理流程 4、制定、改善标准 5、重视“再现”,避免主观臆断或片面错断
质 量 ● 创 新 ● 服 务
WHERE 何地 – 记入问题发生的场所。 WHY 为什么 – 具体的内容 HOW 怎么样 – 问题是怎样发生的 HOW MANY 什么程度 – 问题发生量, 程度。
质 量 ● 创 新 ● 服 务
4M分析
5W分析法
查明原因
特性要因图 再现试验 NG再现 OK再现 不良再现 不良原因 (制造面)
解析对策必须手遵守三现主义
质 量 ● 创 新 ● 服 务
9、制造面、流出面未检讨
疑 问 点:1.为何会流出?为何会制造出?为何设备检不出? 2.流出面之解析对策经常被疏忽。 思 考:顾客所反应之问题必定制造面、流出面共同发生, 仅对策制造或流出面并未能彻底解决问题。
分析方法:1.制造面→分析4M之变化点→真因对策。 2.流出面→a.分析制程中之流程→作业环境、作 业检验工程标准。 b.分析检验之流出→出货检验标准、 限度样品、自动检测、防呆装置。 检验: 为何会检测不出来。
质 量 ● 创 新 ● 服 务
6、无回馈标准
疑问点:如何保证以后不会再发?或这样对策就不会再发吗? 欠缺了什么。 思 考:1.作业者不知道、不清楚、则不良问题仍然会再发生, 所以让作业者明白如何才能做良品是非常重要的。 2.
标准回馈 明确 作业者知道 如何去做 作业者正确 的去做
品质管理三现五原则

品质管理三现五原则品质管理,这可是个大学问!就像烹饪一道美味佳肴,得有精心的准备和严格的把控。
咱先来说说“三现”。
啥是“三现”?就是现场、现物、现状。
这就好比你去看病,医生总不能光听你描述就下诊断吧?他得亲自到现场,看看你的症状,摸摸你的脉象,这才叫了解现况。
搞品质管理也是一样,不能光坐在办公室里看报告,得走到实际的生产现场,亲眼看看产品,亲自感受生产的状况。
你想想,如果一个管理者只听别人说,不去现场,那能行吗?就像你要买一双鞋,只听别人说好看,自己不亲自试试,能买到合脚的吗?再说“现物”,就是实实在在的物品。
产品出了问题,光在那空想可不行,得把有问题的产品拿在手里,仔细瞧瞧,找找毛病到底出在哪。
这就像警察破案,得找到关键的物证,才能顺藤摸瓜找到真相。
“现状”就更好理解啦,就是当下的实际情况。
比如机器的运行状态、工人的操作流程,只有清楚了解这些,才能发现问题,解决问题。
接下来咱们聊聊“五原则”。
这“五原则”就像是五个武功秘籍,掌握好了,品质管理就能游刃有余。
第一个原则是“把握现状”。
这就像打仗之前要先摸清敌人的底细,知道问题到底是啥,有多严重。
不能稀里糊涂就开始行动,那不是瞎折腾嘛!第二个原则是“原因分析”。
出了问题就得找原因,不能头疼医头,脚疼医脚。
就像车子抛锚了,你得找出是发动机的问题,还是轮胎的问题,总不能随便修修就了事。
第三个原则是“对策树立”。
找到原因了,就得想办法解决。
这对策得有针对性,可不能乱出主意。
比如说房子漏雨了,你不能说在屋里打把伞就算解决问题了吧?第四个原则是“效果确认”。
对策实施了,得看看有没有效果。
这就像吃药治病,得复查看看病好了没。
要是没效果,那得赶紧调整对策。
第五个原则是“源流反馈”。
解决了一个问题,还得想想怎么防止类似的问题再次发生。
就像补了一个洞,得想想怎么不让别的地方再出现洞。
总之,品质管理的“三现五原则”就像是一套组合拳,只有把它们运用好了,才能打出漂亮的成绩。
- 1、下载文档前请自行甄别文档内容的完整性,平台不提供额外的编辑、内容补充、找答案等附加服务。
- 2、"仅部分预览"的文档,不可在线预览部分如存在完整性等问题,可反馈申请退款(可完整预览的文档不适用该条件!)。
- 3、如文档侵犯您的权益,请联系客服反馈,我们会尽快为您处理(人工客服工作时间:9:00-18:30)。
5、变化点分析不清楚
疑 问 点:以前为何不会发生不良,现在才发生? 一定是哪里有变更,变化点在哪里? 思 考:不良隐藏於变化点中。
分析方法:4M1D里寻找真因 人[Man]:人员有否更换,有否依标准作业、人员之 士气等。 机[Machine]:机器设备、镆、治、检、工具有否调 整、变更等。 料[Material]:材料有否改变、前工程流入件不良事 等。 方法[Method]: 标准有否规定?标准是否明确? 设计[Design]: 是否设计变更等。
疑 问 点:常发生的直觉判断 ~ 焊接强度不足对策:焊道加长2mm.正确吗? ~ 模温不足变形对策:模温提高10℃.没问题吗? 思 考:加长2mm、提高10℃如何得到的?
直觉+经验≠事实
100个直觉或经验不如1个数据
分析方法:科学的根据=实验数据 ~ 有实验的数据才能决定新的标准。 ~ 要去试验出焊道加长2mm及模温提高10℃是作 业最好的条件。
9、制造面、流出面未检讨
疑 问 点:1.为何会流出?为何会制造出?为何设备检不出? 2.流出面之解析对策经常被疏忽。 思 考:顾客所反应之问题必定制造面、流出面共同发生, 仅对策制造或流出面并未能彻底解决问题。 分析方法:1.制造面→分析4M之变化点→真因对策。 2.流出面→a.分析制程中之流程→作业环境、作 业检验工程标准。 b.分析检验之流出→出货检验标准、 限度样品、自动检测、防呆装置。 检验: 为何会检测不出来。
发生问题 零件号 零件名称
提出部门
日期 批准 审核 编制
日期
编制部门
批准 审核 编制
1-A 发生状况(现象、申诉内容、发生次数、5W2H处置内容)
1-B 把握事实(对零部件的确认结果、原因分析、现在正在生产的零件的品质状况)
2-A 查明原因(WHY WHY 分析) ① ② ③ ④ ⑤
2-B 查明原因(发生的途径、问题再现试验WHY WHY分析)
现场
现状把握确认项目
1、机种、零件名称/号码 2、发生场所/环境/使用条件 3、发生的现象/问题 4、发生日期 5、引擎号码
现状把握确认项目
6、 发生件数/严重性 7、 行驶里程/耐久性 8、 制造日期/批重性 9、 出车日期/库存性 10、不良品品质确认
现状把握确认项目
11、量产中品质水准确认 12、开发阶段品质水准比对 13、设计变更履历 14、其他异常履历 15、标准确认(图面、作业、控制计 划、检验标准…)
解析对策必须顾虑成本面
4、以变更设计改善制程变异
疑 问:1.变更设计就不会有问题了吗? 2.新设计有新的问题,甚或比现在的问题更严重。 3.制程中4M问题未改善,新设计就不会发生相同问题 吗? 说 明: 1.设计者之原理念不祥,不能更改设计。 2.原设计是经过耐久的验证及市场之考验,其可靠度 甚高。 3.未依图制作及未依原设计制作面产生之问题(市怨、 厂异...) 经常有闻。 4.依图面设计制作之保障。 制程变异应从制程面去改善
8、无三现
疑 问 点:有至现场去看吗?有否实车确认、实物、 实地确认? 说 明:1.杂志与资讯:未三现,可能会得到错误之 讯息,或疏略重点资讯。 2.选择性事实:三现的目的,在于针对问题, 全盘掌握事实,而未三现,可能仅知道部份 事实。 3.有三现,才能相信自己,说服别人。
解析对策必须手遵守三现主义
7、再现试验证明
疑 问 点:你如何知道解析不良原因是正确的吗? 思 考:科学的实验是最好的证明→再现试验。
分析方法:正向再现与反向再现。 1.正向:将不良要因排除(不良条件修正)后会制造 出良品。 2.反向:以不良条件生产会制造出不良品。 若上述二向再现结果与假设违背,则肯定 所解析出之不良原因必定有偏差。 3.不良品再现。
WHERE 何地 – 记入问题发生的场所。 WHY 为什么 – 具体的内容 HOW 怎么样 – 问题是怎样发生的 HOW MANY 什么程度 – 问题发生量, 程度。
1、把握现况的填写方法
1、问题点的概要(信息的收集、整 理)。例:针对部品或工程。 2、问题再现试验的结果 3决问题5原则表
记入要领
1-B 对事实的把握(对零部件的确认结果、原因分析、现在正在生产的该零部件的品质状况)
1、在确认事故发生时,也发现了 人 同样汽缸倒下来的情况,作业 人员每一次都是同样地用手把 疲劳 它扶起来(还了解到一般9个 注意 不够 里会倒1个) 2、在事故发生时,作业人员的健 睡眠不足 康状况多少都有些疲劳和睡眠 支架材料 不足的情况。 刚性 3、事故发生的频率 这种事故这一次是头一回发生, 但是根据特性要因的分析结果 材料 认为潜在的发生可能性很高。
6、无回馈标准
疑问点:如何保证以后不会再发?或这样对策就不会再发吗? 欠缺了什么。 思 考:1.作业者不知道、不清楚、则不良问题仍然会再发生, 所以让作业者明白如何才能做良品是非常重要的。 2. 标准回馈 作业者知道 作业者正确 明确 如何去做 的去做 3.作业标准四项重点:内容、手顺、时间、结果。 4.重要之标准类:作业标准、图面、零件检验标准、 QC工程表、试验规范、规章、标 准样品。 5.保证不会再发: 真因 对策 回馈标准
2、以偏概全
疑 问 点:以1、2个数据来判断,可靠吗?
思 考 点:~ 1、2个数据不能代表全部的不 良。 ~ 以偏概全可能仅会解决某比例之 不良,而不是所有的不良。 ~ 未彻底解决问题,不良会再发。
2、以偏概全
分析方法:利用品管统计学来掌握解析手法之可靠 性。问题解析与效果确认,皆可使用品 管统计手法。 1. 掌握品质的准确程度 a.平均数X b.中位数 c.众数。 2.掌握品质的均匀程度 a.全距R b.最大值最小值Max、Min c.标准差。 3. 掌握制程品质能力 a.CP值 b.CPK值
3、增加不必要成本
疑 问 点:利润很高吗?增加成本没关系吗? 说 明:1.利润=售价-成本 成本上升,自然利润降低。 2.解析对策成本面结果有三种: a.成本上升:需有上升的合理原因,需检讨合理 与不合理 b.成本不变动 c.成本下降:GOOD 3.成本上升部份由厂商吸收,虽然不影响利润,但对总体 成本仍是上升的,亦非好之对策。
四、五 原 则
五原则
1、把握现况
现状把握目的
针对问题,全盘调查事实 掌握变异(机遇/非机遇原因) 归纳可疑方向
1、把握现况 - 5W2H
– 类型、种类、受影响 的部分。 WHAT 什么 – 问题的症状,尽可能使 用图表,将问题表达清 楚。 WHEN 何时 – 记入问题发生的日期。 WHO 谁
1、把握现况 - 5W2H
临时对策
适 当 对 策
(防止恶化扩大)
永久对策
(避免再发)
•已流入市场处理 •库存成品处理 •半成品处理 •不良品处理 •制造面、流出 面之治本对策 •水平展开对策
•工程作业者 •进料检验者 •市场服务者 (品质通报)
对策情报传达
3、采取对策
1、针对发生的问题采取临时对策 与永久对策。 2、发生对策(硬件对策)流出对 策(软件对策)
实际品质水 准效果确认
4、效果确认
1、对于实行的对策,实施追踪。 2、在进行效果确认检查时,取 样数量可参考实际问题发生 率,数据方面可以灵活使用 统计手法。
5、源流回馈
•图面 •零件检验标准 •QC工程表 •作业标准 •试验规范 •限度样品
标准类反应 源流回馈
S.O.P修订
1、无科学根据数据
1、把握现况的填写方法
5、利用绘图、图表、柱状图使问 题明确化。 6、将可能想到的原因、内容,详 尽的进行整理,在记录上明确 的记载。 7、在特性要因图(鱼骨图)中, 将所有的要因全部记入。
4M分析
5W分析法 查明原因 特性要因图 NG再现 OK再现 不良再现 不良原因 (制造面)
查明原因
再现试验
查明原因
流出原因 问题 要因 真因 (流出面)
2、查明原因
WHY WHY分析 1、通过WHY、WHY的反复5次进行分析找 出真因。 2、WHY、WHY的疑问必须使之与问题现 象相关联,建立系统来进行。
2、查明原因
3、WHY、WHY的分析要从问题发生的原 因(或叫硬件方面的原因)和流出 原因(又叫软件方面的原因)两方 面进行。 4、WHY、WHY分析的信息来源,基本上 是以特性要因图为基础。 5、为了说明真因,可以加入插图。
1、品质为企业生存之基本条件 2、品质经常发生不良,品质损失大 3、品质不良,操作者认为是品保部 的责任 4、不良解析经常未能找出真因
1、了解并运用三现五原则解析 手法,真正改善重要品质问 题 2、解决问题→持续有效解决问 题→不再是问题 3、解决客诉品质问题挑战“零不良”
三、三
现
现物
三现
现状
注意力判断力
零 注意力不集中 可靠性非常低 没有注意到特别事情 没有发挥预测性、创 造性活动的能力
可靠性
0 0.9以下 0.99 至 0.99999
失败的可能性
1 1/10以上 1/100 至 1/100,000
2
3
精神活跃、意识明 快、机警
注意力较集中,视野 广阔,能做综合判断。 0.999999 在适度紧张中,作业 以上 效率高。
3 采取)适当的对策 (对策内容、效果预测PPA)
4确认(对策)效果(效果实绩) 5对(问题)源头的反馈(需落实到体制、组织的内容)
15、案例
右腕受伤
1- A
发生状况(现象、申诉内容、发生次数、5W1H处置内容)
1、发生场所:汽缸压铸NO.2生产线。 2、 发生状况:请参照右手腕受伤素描图 (由于汽缸倒下来,作业人员在准备将其扶起时, 手腕被支架给夹住了)。 3、 发生月日:SEP-21-1988 4、 发生件数:1 件。 5、 处置内容:在事故发生1 小时内,伤者被送到市内的医院急救, 接受了急救治疗。