气液相反应器本类型与结构
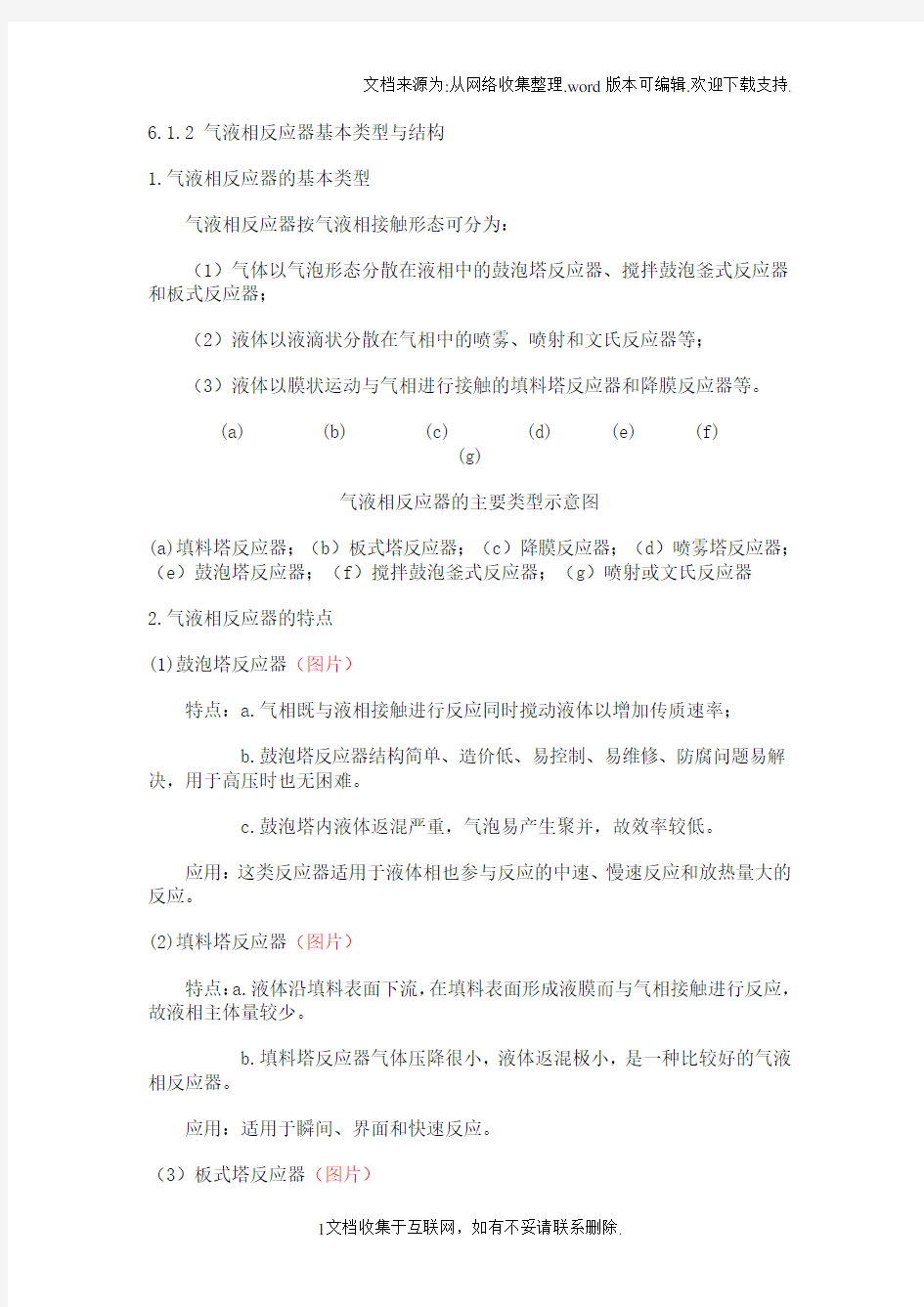

6.1.2 气液相反应器基本类型与结构
1.气液相反应器的基本类型
气液相反应器按气液相接触形态可分为:
(1)气体以气泡形态分散在液相中的鼓泡塔反应器、搅拌鼓泡釜式反应器和板式反应器;
(2)液体以液滴状分散在气相中的喷雾、喷射和文氏反应器等;
(3)液体以膜状运动与气相进行接触的填料塔反应器和降膜反应器等。
(a) (b) (c) (d) (e) (f)
(g)
气液相反应器的主要类型示意图
(a)填料塔反应器;(b)板式塔反应器;(c)降膜反应器;(d)喷雾塔反应器;(e)鼓泡塔反应器;(f)搅拌鼓泡釜式反应器;(g)喷射或文氏反应器
2.气液相反应器的特点
(1)鼓泡塔反应器(图片)
特点:a.气相既与液相接触进行反应同时搅动液体以增加传质速率;
b.鼓泡塔反应器结构简单、造价低、易控制、易维修、防腐问题易解决,用于高压时也无困难。
c.鼓泡塔内液体返混严重,气泡易产生聚并,故效率较低。
应用:这类反应器适用于液体相也参与反应的中速、慢速反应和放热量大的反应。
(2)填料塔反应器(图片)
特点:a.液体沿填料表面下流,在填料表面形成液膜而与气相接触进行反应,故液相主体量较少。
b.填料塔反应器气体压降很小,液体返混极小,是一种比较好的气液相反应器。
应用:适用于瞬间、界面和快速反应。
(3)板式塔反应器(图片)
特点:a.板式塔反应器中的液体是连续相而气体是分散相,借助于气相通过塔板分散成小气泡而与板上液体相接触进行化学反应;
b.能在单塔中直接获得极高的液相转化率;
c.板式塔反应器的气液传质系数较大,可以在板上安置冷却或加热元件,以适应维持所需温度的要求;
d.但是板式塔反应器具有气相流动压降较大和传质表面较小等缺点。
应用:板式塔反应器适用于快速及中速反应。
(4)膜反应器(图片)
特点:a.通常借助管内的流动液膜进行气液反应,管外使用载热流体导入或导出反应热。
b.降膜反应器还具有压降小和无轴向返混的优点。
c.由于降膜反应器中液体停留时间很短,
d.降膜管的安装垂直度要求较高,液体成膜和均匀分布是降膜反应器的关键,工程使用时必须注意。
应用:降膜反应器可用于瞬间、界面和快速反应,它特别适用于较大热效应的气液反应过程;不适用于慢反应;也不适用于处理含固体物质或能析出固体物质及粘性很大的液体。
(5)喷雾塔反应器(图片)
特点:a.液体以细小液滴的方式分散于气体中,气体为连续相,液体为分散相,
b.具有相接触面积大和气相压降小等优点。
c.具有持液量小和液侧传质系数过小,气相和液相返混较为严重的缺点。
应用:适用于瞬间、界面和快速反应,也适用于生成固体的反应。
(6)搅拌鼓泡釜式反应器(图片)
特点:a.反应器内气体能较好地分散成细小的气泡,增大气液接触面积。
b.反应器内液体流动接近全混流,同时能耗较高。
反应器选型与设计 一、反应器类型 反应器设备种类很多,按结构型式分,大致可分为釜式反应器、管式反应器、塔式反应器、固定床反应器、流化床反应器等。 釜式反应器: 反应器中物料浓度和温度处处相等,并且等于反应器出口物料的浓度和温度。物料质点在反应器内停留时间有长有短,存在不同停留时间物料的混合,即返混程度最大。应器内物料所有参数,如浓度、温度等都不随时间变化,从而不存在时间这个自变量。 优点:适用范围广泛,投资少,投产容易,可以方便地改变反应内容。 缺点:换热面积小,反应温度不易控制,停留时间不一致。绝大多数用于有液相参与的反应,如:液液、液固、气液、气液固反应等。 管式反应器 ①由于反应物的分子在反应器内停留时间相等,所以在反应器内任何一点上的反应物浓度和化学反应速度都不随时间而变化,只随管长变化。 ②管式反应器具有容积小、比表面大、单位容积的传热面积大,特别适用于热效应较大的反应。 ③由于反应物在管式反应器中反应速度快、流速快,所以它的生产能力高。
④管式反应器适用于大型化和连续化的化工生产。 ⑤和釜式反应器相比较,其返混较小,在流速较低的情况下,其管内流体流型接近与理想流体。 ⑥管式反应器既适用于液相反应,又适用于气相反应。用于加压反应尤为合适。固定床反应器 固定床反应器的优点是:①返混小,流体同催化剂可进行有效接触,当反应伴有串联副反应时可得较高选择性。②催化剂机械损耗小。③结构简单。 固定床反应器的缺点是:①传热差,反应放热量很大时,即使是列管式反应器也可能出现飞温(反应温度失去控制,急剧上升,超过允许范围)。②操作过程中催化剂不能更换,催化剂需要频繁再生的反应一般不宜使用,常代之以流化床反应器或移动床反应器。固定床反应器中的催化剂不限于颗粒状,网状催化剂早已应用于工业上。目前,蜂窝状、纤维状催化剂也已被广泛使用。 1. 4 流化床反应器 (1)流化床反应器的优点 ①由于可采用细粉颗粒,并在悬浮状态下与流体接触,流固相界面积大(可高 16400m2/m3),有利于非均相反应的进行,提高了催化剂的利用率。 达3280 ~ ②由于颗粒在床内混合激烈,使颗粒在全床内的温度和浓度均匀一致,床层 400/(2)],全床热容量大,热稳定性高,这与内浸换热表面间的传热系数很高[200 ~
反应釜搅拌器选型方法规范 反应釜搅拌器一个好的选型方法最好具备两个条件,一是选择结果合理,一是选择方法简便,而这两点却往往难以同时具备。 由于液体的粘度对搅拌状态有很大的影响,所以根据反应釜内搅拌介质粘度大小来选型是一种基本的方法。几种典型的搅拌器都随粘度的高低而有不同的使用范围。随粘度增高的各种搅拌器使用顺序为推进式、涡轮式、浆式、锚式和螺带式等,这里对推进式的分得较细,提出了大容量液体时用低转速,小容量液体时用高转速。这个选型图不是绝对地规定了使用浆型的限制,实际上各种浆型的使用范围是有重叠的,例如浆式由于其结构简单,用挡板可以改善流型,所以在低粘度时也是应用得较普遍的。而涡轮式由于其对流循环能力、湍流扩散和剪切力都较强,几乎是应用最广的一种浆型。 根据搅拌过程的目的与搅拌器造成的流动状态判断该过程所适用的浆型,这是一种比较合用的方法。由于苏联的浆型选择有其本国的习惯,所以与我国常用浆型并不尽相同。 推荐浆型是把浆型分成快速型与慢速型两类,前者在湍流状态操作,后者在层流状态操作。选用时根据搅拌目的及流动状态来决定浆型及挡板条件,流动状态的决定要受搅拌介质的粘度高低的影响。 其使用条件比较具体,不仅有浆型与搅拌目的,还有推荐的介质粘度范围、搅拌转速范围和槽的容量范围。 提出的选型表也是根据反应釜搅拌的目的及搅拌时的流动状态来选型,它的优点还在于根据不同搅拌过程的特点划分了浆型的使用范围,使得选型更加具体。比较上述表可以看到,选型的根据和结果还是比较一致的。下面对其中几个主要的过程再作些说明。 低粘度均相液体混合,是难度最小的一种搅拌过程,只有当容积很大且要求混合时间很短时才比较困难。由于推进式的循环能力强且消耗动力少,所以是最合用的。而涡轮式因其动力消耗大,虽有高的剪切能力,但对于这种混合的过程并无太大必要,所以若用在大容量液体混合时,其循环能力就不足了。
釜式反应器 Tank Reactor 釜式反应器的学习任务 1、了解釜式反应器的基本结构、特点及工业应用。 2、掌握各类釜式反应器的计算。 3、了解釜式反应器的热稳定性。 4、掌握釜式反应器的操作技能。 项目一釜式反应器的结构 釜式反应器又称: 槽型反应器或锅式反应器一种低高径比的圆筒形反应器,用于实现液相单相反应过程和液液、气液、液固、气液固等多相反应过程。 反应器内常设有搅拌(机械搅拌、气流搅拌等)装置。在高径比较大时,可用多层搅拌桨叶。在反应过程中物料需加热或冷却时,可在反应器壁处设置夹套,或在器内设置换热面,也可通过外循环进行换热。 操作时温度、浓度容易控制,产品质量均一。在化工生产中,既可适用于间歇操作过程,又可用于连续操作过程;可单釜操作,也可多釜串联使用;但若应用在需要较高转化率的工艺要求时,有需要较大容积的缺点。通常在操作条件比较缓和的情况下,如常压、温度较低且低于物料沸点时,釜式反应器的应用最为普遍。 一、釜式反应器基本结构 釜式反应器的基本结构主要包括: 反应器壳体、搅拌装置、密封装置、换热装置、传动装置。 壳体结构:一般为碳钢材料,筒体皆为圆筒型。釜式反应器壳体部分的结构包括筒体、底、盖(或称封头)、手孔或人孔、视镜、安全装置及各种工艺接管口等。封头;反应釜的顶盖,为了满足拆卸方便以及维护检修。 平面形:适用于常压或压力不高时; 碟形:应用较广。 球形:适用于高压场合; 椭圆形:应用较广。 锥形:适用于反应后物料需要分层处理的场合。 手孔、人孔:为了检查内部空间以及安装和拆卸设备内部构件。 视镜: 观察设备内部物料的反应情况,也作液面指示用。 工艺接管: 用于进、出物料及安装温度、压力的测定装置。
化学化工学院 化工专业课程设计 设计题目:管式反应器设计 化工系
化工专业课程设计——设计文档质量评分表(100分) 评委签名: 日期:
目录 绪论 .........................................................错误!未定义书签。1设计内容与方法介绍..........................................错误!未定义书签。 反应器设计概述............................................错误!未定义书签。 设计内容..................................................错误!未定义书签。 生产方法介绍..............................................错误!未定义书签。 反应器类型特点............................................错误!未定义书签。 反应器选择及操作条件说明..................................错误!未定义书签。2工艺计算....................................................错误!未定义书签。 主要物性数据..............................................错误!未定义书签。 计算,确定管长,主副反应收率.............................错误!未定义书签。 管数计算..................................................错误!未定义书签。3压降计算公式................................................错误!未定义书签。4催化剂用量计算..............................................错误!未定义书签。5换热面积计算................................................错误!未定义书签。6反应器外径计算..............................................错误!未定义书签。7壁厚计算....................................................错误!未定义书签。 8 筒体封头计算................................................错误!未定义书签。9管板厚度计算................................................错误!未定义书签。10设计结果汇总...............................................错误!未定义书签。11设计小结...................................................错误!未定义书签。
表6-1 反应器选型一览表表6-2 压缩机选型一览表 名称类型数 量 个 型号 重 量 t 功率 Kw 价格/万 元 异构化循环压缩机凝汽透平驱动 的离心式压缩 机 2 BCL406/A 14. 3 5000 名称 数量/ 台类型尺寸/mm 温度 /℃ 压力 /MPa 封头形式材料 重量/ Kg 价格/万 元 异构化反 应器1 Packin ox焊板 式 Φ4000*13000420 1.2 标准椭圆 型封头 06Cr25 Ni20S3 1008 36238.2 异构化分 离器1 FA-701 -1/2 Φ4000*13000 175 0.8 标准椭圆 形风头 06Cr25 Ni20S3 1008 36238.2
编号型号类型 内径 /mm 列管 管数/ 根 管程 数 换热 面积 /㎡ 材料 重量/ Kg 价格/ 万元管长 /mm 列管规格 /mm 排列方式管程壳程 E101 BEM600-0.345-28.8-1.27/19-1Ⅰ管板式635 1270 Φ19X2正三角形310 1 28.8 碳钢碳钢1549 18.3 E102 BEM200-0.345/3.3-6.5-2.4/19-2Ⅰ管板式203.2 2438.4 Φ19X2正三角形46 2 6.5 碳钢碳钢354 6.0 E103 BEM200-0.345-2.3-1.2/19-4Ⅰ管板式203.2 1219.2 Φ19X2正三角形33 4 2.3 碳钢碳钢214 4.9 E104 BEM200-0.345-9.8-4.6/19-2Ⅰ管板式203.2 4267.2 Φ19X2正三角形39 2 9.8 碳钢碳钢465.7 6.0 E105 BEM200-0.345/1.03-3.1-1.2/19-2Ⅰ管板式203.2 1219.2 Φ19X2正三角形46 2 3.1 碳钢碳钢228.6 5.1 E106 BEM200-0.345/4.4-3.1-1.2/19-1Ⅰ管板式177.8 1219.2 Φ19X2正三角形46 1 3.1 碳钢碳钢233.9 5.2 E107 BEM200-0.345-3.2-1.2/19-1Ⅰ管板式203.2 1219.2 Φ19X2正三角形47 1 3.2 碳钢碳钢244.6 5.1
反应器选型与设计完结版 This manuscript was revised by the office on December 10, 2020.
反应器选型与设计 一、反应器类型 反应器设备种类很多,按结构型式分,大致可分为釜式反应器、管式反应器、塔式反应器、固定床反应器、流化床反应器等。 釜式反应器: 反应器中物料浓度和温度处处相等,并且等于反应器出口物料的浓度和温度。物料质点在反应器内停留时间有长有短,存在不同停留时间物料的混合,即返混程度最大。应器内物料所有参数,如浓度、温度等都不随时间变化,从而不存在时间这个自变量。优点:适用范围广泛,投资少,投产容易,可以方便地改变反应内容。 缺点:换热面积小,反应温度不易控制,停留时间不一致。绝大多数用于有液相参与的反应,如:液液、液固、气液、气液固反应等。 管式反应器 ①由于反应物的分子在反应器内停留时间相等,所以在反应器内任何一点上的反应物浓度和化学反应速度都不随时间而变化,只随管长变化。 ②管式反应器具有容积小、比表面大、单位容积的传热面积大,特别适用于热效应较大的反应。 ③由于反应物在管式反应器中反应速度快、流速快,所以它的生产能力高。 ④管式反应器适用于大型化和连续化的化工生产。 ⑤和釜式反应器相比较,其返混较小,在流速较低的情况下,其管内流体流型接近与理想流体。 ⑥管式反应器既适用于液相反应,又适用于气相反应。用于加压反应尤为合适。 固定床反应器 固定床反应器的优点是:①返混小,流体同催化剂可进行有效接触,当反应伴有串联副反应时可得较高选择性。②催化剂机械损耗小。③结构简单。 固定床反应器的缺点是:①传热差,反应放热量很大时,即使是列管式反应器也可能出现飞温(反应温度失去控制,急剧上升,超过允许范围)。②操作过程中催化剂不能更换,催化剂需要频繁再生的反应一般不宜使用,常代之以流化床反应器或移动床反应器。固定床反应器中的催化剂不限于颗粒状,网状催化剂早已应用于工业上。目前,蜂窝状、纤维状催化剂也已被广泛使用。 1. 4 流化床反应器 (1)流化床反应器的优点 ①由于可采用细粉颗粒,并在悬浮状态下与流体接触,流固相界面积大(可高达 16400m2/m3),有利于非均相反应的进行,提高了催化剂的利用率。 3280 ~ ②由于颗粒在床内混合激烈,使颗粒在全床内的温度和浓度均匀一致,床层 400/(2)],全床热容量大,热稳定性高,这些都与内浸换热表面间的传热系数很高[200 ~ 有利于强放热反应的等温操作。这是许多工艺过程的反应装置选择流化床的重要原因之一。 流化床内的颗粒群有类似流体的性质,可以大量地从装置中移出、引入,并可以在两个流化床之间大量循环。这使得一些反应—再生、吸热—放热、正反应—逆反应等反应耦合过程和反应—分离耦合过程得以实现。使得易失活催化剂能在工程中使用。 (2)流化床反应器的缺点
反应器结构及工作原理图解 小7:这里给大家介绍一下常用的反应器设备,主要有以下类型:①管式反应器。由长径比较大的空管或填充管构成,可用于实现气相反应和液相反应。②釜式反应器。由长径比较小的圆筒形容器构成,常装有机械搅拌或气流搅拌装置,可用于液相单相反应过程和液液相、气液相、气液固相等多相反应过程。用于气液相反应过程的称为鼓泡搅拌釜(见鼓泡反应器);用于气液固相反应过程的称为搅拌釜式浆态反应器。③有固体颗粒床层的反应器。气体或(和)液体通过固定的或运动的固体颗粒床层以实现多相反应过程,包括固定床反应器、流化床反应器、移动床反应器、涓流床反应器等。④塔式反应器。用于实现气液相或液液相反应过程的塔式设备,包括填充塔、板式塔、鼓泡塔等(见彩图)。 一、管式反应器 一种呈管状、长径比很大的连续操作反应器。这种反应器可以很长,如丙烯二聚的反应器管长以公里计。反应器的结构可以是单管,也可以是多管并联;可以是空管,如管式裂解炉,也可以是在管内填充颗粒状催化剂的填充管,以进行多相催化反应,如列管式固定床反应器。通常,反应物流处于湍流状态时,空管的长径比大于50;填充段长与粒径之比大于100(气体)或200(液体),物料的流动可近似地视为平推流。
分类: 1、水平管式反应器 由无缝钢管与U形管连接而成。这种结构易于加工制造和检修。高压反应管道的连接采用标准槽对焊钢法兰,可承受1600-10000kPa压力。如用透镜面钢法兰,承受压力可达10000-20000kPa。
2、立管式反应器 立管式反应器被应用于液相氨化反应、液相加氢反应、液相氧化反应等工艺中。
3、盘管式反应器 将管式反应器做成盘管的形式,设备紧凑,节省空间。但检修和清刷管道比较困难。
反应器选型与设计完结 版 Company number【1089WT-1898YT-1W8CB-9UUT-92108】
反应器选型与设计一、反应器类型 反应器设备种类很多,按结构型式分,大致可分为釜式反应器、管式反应器、塔式反应器、固定床反应器、流化床反应器等。 釜式反应器: 反应器中物料浓度和温度处处相等,并且等于反应器出口物料的浓度和温度。物料质点在反应器内停留时间有长有短,存在不同停留时间物料的混合,即返混程度最大。应器内物料所有参数,如浓度、温度等都不随时间变化,从而不存在时间这个自变量。 优点:适用范围广泛,投资少,投产容易,可以方便地改变反应内容。 缺点:换热面积小,反应温度不易控制,停留时间不一致。绝大多数用于有液相参与的反应,如:液液、液固、气液、气液固反应等。 管式反应器 ①由于反应物的分子在反应器内停留时间相等,所以在反应器内任何一点上的反应物浓度和化学反应速度都不随时间而变化,只随管长变化。 ②管式反应器具有容积小、比表面大、单位容积的传热面积大,特别适用于热效应较大的反应。 ③由于反应物在管式反应器中反应速度快、流速快,所以它的生产能力高。 ④管式反应器适用于大型化和连续化的化工生产。 ⑤和釜式反应器相比较,其返混较小,在流速较低的情况下,其管内流体流型接近与理想流体。 ⑥管式反应器既适用于液相反应,又适用于气相反应。用于加压反应尤为合适。
固定床反应器 固定床反应器的优点是:①返混小,流体同催化剂可进行有效接触,当反应伴有串联副反应时可得较高选择性。②催化剂机械损耗小。③结构简单。 固定床反应器的缺点是:①传热差,反应放热量很大时,即使是列管式反应器也可能出现飞温(反应温度失去控制,急剧上升,超过允许范围)。②操作过程中催化剂不能更换,催化剂需要频繁再生的反应一般不宜使用,常代之以流化床反应器或移动床反应器。固定床反应器中的催化剂不限于颗粒状,网状催化剂早已应用于工业上。目前,蜂窝状、纤维状催化剂也已被广泛使用。 1. 4 流化床反应器 (1)流化床反应器的优点 ①由于可采用细粉颗粒,并在悬浮状态下与流体接触,流固相界面积大(可 16400m2/m3),有利于非均相反应的进行,提高了催化剂的利用率。 高达3280 ~ ②由于颗粒在床内混合激烈,使颗粒在全床内的温度和浓度均匀一致,床层与内浸换热表面间的传热系数很高[200 400/(2)],全床热容量大,热稳定性高, ~ 这些都有利于强放热反应的等温操作。这是许多工艺过程的反应装置选择流化床的重要原因之一。 流化床内的颗粒群有类似流体的性质,可以大量地从装置中移出、引入,并可以在两个流化床之间大量循环。这使得一些反应—再生、吸热—放热、正反应—逆反应等反应耦合过程和反应—分离耦合过程得以实现。使得易失活催化剂能在工程中使用。 (2)流化床反应器的缺点
6.1.2 气液相反应器基本类型与结构 1.气液相反应器的基本类型 气液相反应器按气液相接触形态可分为: (1)气体以气泡形态分散在液相中的鼓泡塔反应器、搅拌鼓泡釜式反应器和板式反应器; (2)液体以液滴状分散在气相中的喷雾、喷射和文氏反应器等; (3)液体以膜状运动与气相进行接触的填料塔反应器和降膜反应器等。 (a) (b) (c) (d) (e) (f) (g) 气液相反应器的主要类型示意图 (a)填料塔反应器;(b)板式塔反应器;(c)降膜反应器;(d)喷雾塔反应器;(e)鼓泡塔反应器;(f)搅拌鼓泡釜式反应器;(g)喷射或文氏反应器 2.气液相反应器的特点 (1)鼓泡塔反应器(图片) 特点:a.气相既与液相接触进行反应同时搅动液体以增加传质速率; b.鼓泡塔反应器结构简单、造价低、易控制、易维修、防腐问题易解决,用于高压时也无困难。 c.鼓泡塔内液体返混严重,气泡易产生聚并,故效率较低。 应用:这类反应器适用于液体相也参与反应的中速、慢速反应和放热量大的反应。
(2)填料塔反应器(图片) 特点:a.液体沿填料表面下流,在填料表面形成液膜而与气相接触进行反应,故液相主体量较少。 b.填料塔反应器气体压降很小,液体返混极小,是一种比较好的气液相反应器。 应用:适用于瞬间、界面和快速反应。 (3)板式塔反应器(图片) 特点:a.板式塔反应器中的液体是连续相而气体是分散相,借助于气相通过塔板分散成小气泡而与板上液体相接触进行化学反应; b.能在单塔中直接获得极高的液相转化率; c.板式塔反应器的气液传质系数较大,可以在板上安置冷却或加热元件,以适应维持所需温度的要求; d.但是板式塔反应器具有气相流动压降较大和传质表面较小等缺点。 应用:板式塔反应器适用于快速及中速反应。 (4)膜反应器(图片) 特点:a.通常借助管内的流动液膜进行气液反应,管外使用载热流体导入或导出反应热。 b.降膜反应器还具有压降小和无轴向返混的优点。 c.由于降膜反应器中液体停留时间很短, d.降膜管的安装垂直度要求较高,液体成膜和均匀分布是降膜反应器的关键,工程使用时必须注意。 应用:降膜反应器可用于瞬间、界面和快速反应,它特别适用于较大热效应的气液反应过程;不适用于慢反应;也不适用于处理含固体物质或能析出固体物质及粘性很大的液体。 (5)喷雾塔反应器(图片) 特点:a.液体以细小液滴的方式分散于气体中,气体为连续相,液体为分散相, b.具有相接触面积大和气相压降小等优点。
化学反应器分类及其特点 This model paper was revised by the Standardization Office on December 10, 2020
化学反应器的分类及特点 秦财德 (中南大学、化学化工学院、化工1002班) 摘要: 反应器的应用始于古代,制造陶器的窑炉就是一种原始的反应器。近代工业中的反应器形式多样。化学反应器,用于实现液相单相反应过程和液液、气液、液固、气液固等多相反应过程。器内常设有搅拌(机械搅拌、气流搅拌等)装置。本文主要介绍化学反应器的分类和特点 关键词:化学反应器特点典型反应 现在的化工反应器在向高精端方向发展,在化工反应中处于主要地位,化学反应器是化学反应的载体,是化工研究、生产的基础,是决定化学反应好坏的重要因素之一,因此反应器的设计、选型是十分重要的。反应器的种类很多,设计和选型很重要,座椅应该按照实际情况来设计制造。 一.釜式反应器 (一)反应器的简介 一种低高径比的圆筒形反应器,用于实现液相单相反应过程和液液、气液、液固、气液固等多相反应过程。器内常设有搅拌(机械搅拌、气流搅拌等)装置。在高径比较大时,可用多层搅拌桨叶。在反应过程中物料需加热或冷却时,可在反应器壁处设置夹套,或在器内设置换热面,也可通过外循环进行换热。 (二)反应器的特点
反应器中物料浓度和温度处处相等,并且等于反应器出口物料的浓度和温度。物料质点在反应器内停留时间有长有短,存在不同停留时间物料的混合,即返混程度最大。反应器内物料所有参数,如浓度、温度等都不随时间变化,从而不存在时间这个自变量。 优点:适用范围广泛,投资少,投产容易,可以方便地改变反应内容。 缺点:换热面积小,反应温度不易控制,停留时间不一致。绝大多数用于有液相参与的反应,如:液液、液固、气液、气液固反应等。 (三)典型反应: 在等温间歇反应器中进行乙酸乙酯皂化反应: CH 3COOC 2 H 5 +NaOH CH 3 COONa+ C 2 H 5 OH 二.管式反应器 (一)反应器的简介 管式反应器一种呈管状、长径比很大的连续操作反应器。这种反应器可以很长,如丙烯二聚的反应器管长以公里计。反应器的结构可以是单管,也可以是多管并联;可以是空管,如管式裂解炉,也可以是在管内填充颗粒状催化剂的填充管,以进行多相催化反应,如列管式固定床反应器。通常,反应物流处于湍流状态时,空管的长径比大于50;填充段长与粒径之比大于100(气体)或200(液体),物料的流动可近似地视为平推流.(二)反应器的特点 (1)由于反应物的分子在反应器内停留时间相等,所以在反应器内任何一点上的反应物浓度和化学反应速度都不随时间而变化,只随管长变化。
毕业论文题目管式反应器操作与控制 专业应用化工生产技术年级 姓名 指导教师 定稿日期:2013年 5月 25日
目录 一、管式反应器的概述 (1) 二、管式反应器的特点 (2) 三、管式反应器的分类 (3) 四、管式反应器的日常维护 (5) 五、管式反应器故障分析及处理 (5) 六、关于管式反应器的计算 (7) 七、管式反应器生产实例 (12) 八、相关习题 (15) (一)判断题 (15) (二)选择题 (15) (三)填空题 (15) (四)问答题 (15) (五)参考答案 (15) 结语 (16) 参考文献 (16) 致谢 (17)
管式反应器操作与控制 一、管式反应器的概述 管式反应器是一种呈管状、长径比很大的连续操作反应器。 这种反应器可以很长,如丙烯二聚的反应器管长以公里计。反应器的结构可以是单管,也可以是多管并联;可以是空管,如管式裂解炉,也可以是在管内填充颗粒状催化剂的填充管,以进行多相催化反应,如列管式固定床反应器。通常,反应物流处于湍流状态时,空管的长径比大于50;填充段长与粒径之比大于100(气体)或200(液体),物料的流动可近似地视为平推流。 管式反应器返混小,因而容积效率(单位容积生产能力)高,对要求转化率较高或有串联副反应的场合尤为适用。此外,管式反应器可实现分段温度控制。其主要缺点是,反应速率很低时所需管道过长,工业上不易实现。
二、管式反应器的特点 1、反应物的分子在反应器内停留时间相等,反应器内任何一点上的反应物浓度和化学反应速度都不随时间而变化,只随管长变化。 2、管式反应器的单位反应器体积具有较大的换热面,特别适用于热效应较大的反应。 3、由于反应物在管式反应器中返混小,反应速度快,流速快,所以它的生产率高。 4、管式反应器适用于大型化和连续化的化工生产。 5、和釜式反应器相比较,其返混较小,在流速较低的情况下,其管内流体流型接近于理想置换流。 6、反应器内各处的浓度未必相等,反应速率随空间位置而变化; 7、由于径向具有严格均匀的速度分布,也就是在径向不存在浓度变化,所以反应速率随空间位置的变化将只限于轴向。 8、理想管式反应器的反应结果唯一地由化学反应动力学所确定。 9、结构简单紧凑,强度高,抗腐蚀强,抗冲击性能好,使用寿命长,便于检修。
管式反应器的概述 管式反应器是一种呈管状、长径比很大的连续操作反应器。这种反应器可以很长,如丙烯二聚的反应器管长以公里计。反应器的结构可以是单管,也可以是多管并联;可以是空管,如管式裂解炉,也可以是在管内填充颗粒状催化剂的填充管,以进行多相催化反应,如列管式固定床反应器。通常,反应物流处于湍流状态时,空管的长径比大于50;填充段长与粒径之比大于100(气体)或200(液体),物料的流动可近似地视为平推流。 管式反应器的特点 1、反应物的分子在反应器内停留时间相等,反应器内任何一点上的反应物浓度和化学反应速度都不随时间而变化,只随管长变化。 2、管式反应器的单位反应器体积具有较大的换热面,特别适用于热效应较大的反应。 3、由于反应物在管式反应器中返混小,反应速度快,流速快,所以它的生产率高。 4、管式反应器适用于大型化和连续化的化工生产。 5、和釜式反应器相比较,其返混较小,在流速较低的情况下,其管内流体流型接近于理想置换流。 6、反应器内各处的浓度未必相等,反应速率随空间位置而变化; 7、由于径向具有严格均匀的速度分布,也就是在径向不存在浓度变化,所以反应速率随空间位置的变化将只限于轴向。 8、理想管式反应器的反应结果唯一地由化学反应动力学所确定。 9、结构简单紧凑,强度高,抗腐蚀强,抗冲击性能好,使用寿命长,便于检修。 管式反应器的分类 管式反应器按结构可分为:直管式、U型管式、盘管式和多管式 1、直管式:结构简单,处理量小,可用作多管式反应器的实验装置
2、U型管式: 3、盘管式 4、多管式: 多管式反应器按管道的连接方式的不同,把管式反应器分为多管串联管式反应器和多管并联管式反应器。
反应器选型与设计完结版Newly compiled on November 23, 2020
反应器选型与设计一、反应器类型 反应器设备种类很多,按结构型式分,大致可分为釜式反应器、管式反应器、塔式反应器、固定床反应器、流化床反应器等。 釜式反应器: 反应器中物料浓度和温度处处相等,并且等于反应器出口物料的浓度和温度。物料质点在反应器内停留时间有长有短,存在不同停留时间物料的混合,即返混程度最大。应器内物料所有参数,如浓度、温度等都不随时间变化,从而不存在时间这个自变量。优点:适用范围广泛,投资少,投产容易,可以方便地改变反应内容。 缺点:换热面积小,反应温度不易控制,停留时间不一致。绝大多数用于有液相参与的反应,如:液液、液固、气液、气液固反应等。 管式反应器 ①由于反应物的分子在反应器内停留时间相等,所以在反应器内任何一点上的反应物浓度和化学反应速度都不随时间而变化,只随管长变化。 ②管式反应器具有容积小、比表面大、单位容积的传热面积大,特别适用于热效应较大的反应。 ③由于反应物在管式反应器中反应速度快、流速快,所以它的生产能力高。 ④管式反应器适用于大型化和连续化的化工生产。 ⑤和釜式反应器相比较,其返混较小,在流速较低的情况下,其管内流体流型接近与理想流体。 ⑥管式反应器既适用于液相反应,又适用于气相反应。用于加压反应尤为合适。 固定床反应器
固定床反应器的优点是:①返混小,流体同催化剂可进行有效接触,当反应伴有串联副反应时可得较高选择性。②催化剂机械损耗小。③结构简单。 固定床反应器的缺点是:①传热差,反应放热量很大时,即使是列管式反应器也可能出现飞温(反应温度失去控制,急剧上升,超过允许范围)。②操作过程中催化剂不能更换,催化剂需要频繁再生的反应一般不宜使用,常代之以流化床反应器或移动床反应器。固定床反应器中的催化剂不限于颗粒状,网状催化剂早已应用于工业上。目前,蜂窝状、纤维状催化剂也已被广泛使用。 1. 4 流化床反应器 (1)流化床反应器的优点 ①由于可采用细粉颗粒,并在悬浮状态下与流体接触,流固相界面积大(可高达 16400m2/m3),有利于非均相反应的进行,提高了催化剂的利用率。 3280 ~ ②由于颗粒在床内混合激烈,使颗粒在全床内的温度和浓度均匀一致,床层 与内浸换热表面间的传热系数很高[200~400/(2)],全床热容量大,热稳定性高,这些都有利于强放热反应的等温操作。这是许多工艺过程的反应装置选择流化床的重要原因之一。 流化床内的颗粒群有类似流体的性质,可以大量地从装置中移出、引入,并可以在两个流化床之间大量循环。这使得一些反应—再生、吸热—放热、正反应—逆反应等反应耦合过程和反应—分离耦合过程得以实现。使得易失活催化剂能在工程中使用。 (2)流化床反应器的缺点 ①气体流动状态与活塞流偏离较大,气流与床层颗粒发生返混,以致在床层轴向没有温度差及浓度差。加之气体可能成大气泡状态通过床层,使气固接触不良,使反应的转化率降低。因此流化床一般达不到固定床的转化率。
第九章反应器设计 9.1 概述 (1) 9.2反应器的分类和结构特点 (3) 9.3 发酵罐设计与分析 (6) 9.5 其他反应器 (14) 9.1 概述 生物反应器是指一个能为生物反应提供适宜的反应条件,以实现将原料转化为特定产品的设备,是生物技术产业化的核心。 生物反应器设计的主要内容包括:(1)反应器选型,即根据生产工艺要求、反应及物料的特性等因素,确定反应器的操作方式、结构类型、传递和流动方式等;(2)设计反应器结构,确定各种结构参数,即确定反应器的内部结构及几何尺寸、搅拌器形式、大小及转速、换热方式及换热面积等;(3)确定工艺参数及其控制方式,如温度、压力、pH、通气量、底物浓度、进料的浓度、流量和温度等。生物反应器设计的基本要求: (1)避免将必须蒸汽灭菌的部件与其它部件直接相连; (2)法兰应尽量少; (3)尽可能采用焊接连接,焊接部位要充分抛光; (4)避免产生凹陷和裂缝; (5)设备各部件能分别进行灭菌; (6)反应器的接口处用蒸汽封口; (7)阀门要易清洗,易使用,易灭菌; (8)反应器内易保持一定正压; (9)为便于清洗,反应器主体部分应尽量简单。 反应器的设计以及工程放大,主要采用数学模型法,即利用数学模型来分析、研
究生化反应过程中的现象和规律,即用数学语言表达过程中各种变量之间的关系。 数学模型的建立:以生物反应器为研究对象,将其中的生化反应过程分解为生化反应、传递过程及流体流动与混合等子过程,并分别进行研究,通过物料衡算和热量衡算将各子过程的相关参数进行关联和偶合,即对动力学方程、物料衡算及热量衡算式联立求解,从而得到所研究的生化反应过程规律的解析表达形式。另一方面,由于生化反应过程极为复杂,往往对过程的机理研究得不透彻或有些问题尚不清楚,在这种情况下,就必须结合一定的经验模型,即在一定条件下由实验数据进行数学关联并拟合而得到的模型。
学习任务卡
化学反应过程与设备 小组成员: 任务:A0101乙酸丁酯反应器型式及反应器材质的选择 任务点0101-1 合成乙酸丁酯的反应原理及其工业生产方法 C4H9OH+CH3COOH→CH3COOC4H9+H2O 由乙酸与正丁醇在硫酸存在下酯化而得。将丁醇、乙酸和硫酸按比例投入酯化釜,在120℃进行酯化,经回流脱水,控制酯化时的酸值在0.5以下,所得粗酯经中和后进入蒸馏釜,经蒸馏、冷凝、分离进行回流脱水,回收醇酯,最后在126℃以下蒸馏而得产品。生产工艺有连续法及间歇法,视生产规模不同而定。原料消耗定额:乙酸(98%)540kg/t、正丁醇650kg/t。 任务点0101-2 乙酸丁酯、原料、催化剂的物理、化学性质
正丁醇物化性质 英文名称: butyl alcohol;1-butanol 别名: 丁醇分子式: C4H10O;CH3(CH2)3OH 分子量: 74.12 熔点: -88.9℃沸点:117.25 相对密度: d(20,4)=0.8908;蒸汽压: 35℃(蒸汽压: 0.82kPa/25℃) 溶解性: 微溶于水,溶于乙醇、醚多数有机溶剂 稳定性: 稳定外观与性状: 无色透明液体,具有特殊气味危险标记: 7(易燃液体)临界压力(MPa): 4.90 饱和蒸气压: 0.82(25℃) 折射率(n20D )1.3993,闪点:35℃(闭口),40℃(开口) 自燃点365℃,粘度:2.95mPa.s(20℃) 张力:24.6mN/m(20℃) 20℃时在水中的溶解度7.7%(重量),水在正丁醇中的的溶解度20.1%(重量)。 用途:用于制取酯类、塑料增塑剂、医药、喷漆,以及用作溶剂。也是多种涂料的溶剂和制增塑剂邻苯二甲酸二丁酯(见邻苯二甲酸酯)的原料,也用于制造丙烯酸丁酯、醋酸丁酯、乙二醇丁醚以及作为有机合成中间体和生物化学药的萃取剂,还用于制造表面活性剂 催化剂:浓硫酸 纯硫酸是一种无色油状液体。常用的浓硫酸中H2SO4的质量分数为 98.3%,其密度为1.84g/cm-3,其物质的量浓度为18.4mol/L。硫酸是一种高沸点难挥发的强酸,易溶于水,能以任意比与水混溶。浓硫酸溶解时放出大量的热,因此浓硫酸稀释时应该“酸入水,沿器壁,慢慢倒,