温度,时间,压力对某某塑料成型的影响
pa66成型参数
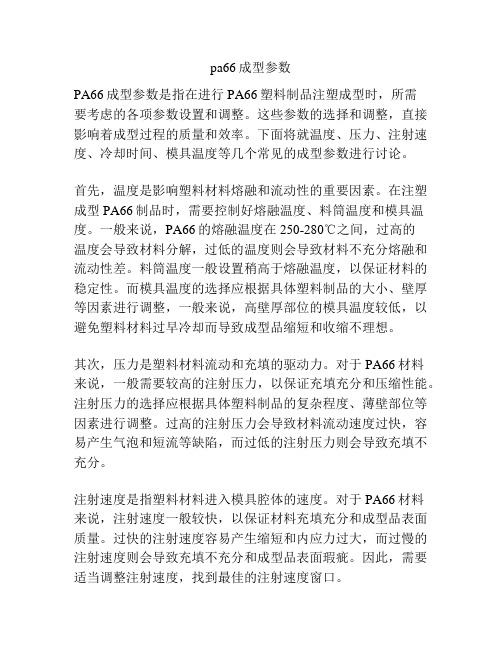
pa66成型参数PA66成型参数是指在进行PA66塑料制品注塑成型时,所需要考虑的各项参数设置和调整。
这些参数的选择和调整,直接影响着成型过程的质量和效率。
下面将就温度、压力、注射速度、冷却时间、模具温度等几个常见的成型参数进行讨论。
首先,温度是影响塑料材料熔融和流动性的重要因素。
在注塑成型PA66制品时,需要控制好熔融温度、料筒温度和模具温度。
一般来说,PA66的熔融温度在250-280℃之间,过高的温度会导致材料分解,过低的温度则会导致材料不充分熔融和流动性差。
料筒温度一般设置稍高于熔融温度,以保证材料的稳定性。
而模具温度的选择应根据具体塑料制品的大小、壁厚等因素进行调整,一般来说,高壁厚部位的模具温度较低,以避免塑料材料过早冷却而导致成型品缩短和收缩不理想。
其次,压力是塑料材料流动和充填的驱动力。
对于PA66材料来说,一般需要较高的注射压力,以保证充填充分和压缩性能。
注射压力的选择应根据具体塑料制品的复杂程度、薄壁部位等因素进行调整。
过高的注射压力会导致材料流动速度过快,容易产生气泡和短流等缺陷,而过低的注射压力则会导致充填不充分。
注射速度是指塑料材料进入模具腔体的速度。
对于PA66材料来说,注射速度一般较快,以保证材料充填充分和成型品表面质量。
过快的注射速度容易产生缩短和内应力过大,而过慢的注射速度则会导致充填不充分和成型品表面瑕疵。
因此,需要适当调整注射速度,找到最佳的注射速度窗口。
冷却时间是指在注塑成型后,待塑料制品充分冷却后方可取出的时间。
对于PA66材料来说,冷却时间的设置应根据制品的大小、壁厚等因素进行调整。
一般来说,冷却时间应保证充分冷却,避免成型品过早脱模和形变。
同时,冷却时间也不能过长,以免生产效率低下。
因此,需要通过试模和调整实际生产中的冷却时间。
除了以上几个常见的成型参数外,还有一些其它的因素也会对成型质量产生影响,如保压时间、保压力、模具开合速度等。
在实际生产中,需要根据具体塑料制品的要求和生产经验进行设置和调整。
注塑成型五大要素调机

注塑成型五大要素调机注塑成型是一种重要的塑料加工方法,广泛应用于各个领域。
在注塑成型过程中,调机是非常关键的环节,它直接影响到成品的质量和生产效率。
本文将介绍注塑成型的五大要素以及如何进行调机。
一、温度调控温度调控是注塑成型中必不可缺的一项要素。
合理的温度调控可以保证塑料原料的熔融状态,使其能够顺利进入模具中进行成型。
温度过低会导致塑料无法完全熔化或熔化不均匀,从而出现不良品;而温度过高则容易造成模具磨损或塑料变质。
因此,在调机过程中,需要根据具体的塑料种类和注塑机型号来合理设置温度,确保塑料的熔融状态处于最佳范围。
二、压力调控压力调控是注塑成型过程中另一个重要的要素。
通过调整注塑机的压力大小,可以控制塑料在模具中的流动速度和压实程度。
如果压力过小,塑料可能无法填充整个模具腔道,导致成品缺陷;而压力过大则容易造成模具损坏或超出产品要求的尺寸。
因此,在调机时需要根据产品要求和模具设计来合理设置压力,保证塑料能够在模具中达到理想的充填状态。
三、速度调控速度调控也是注塑成型中需要特别注意的要素。
注塑机的进料速度、射胶速度和回退速度等都需要在调机过程中进行合理设置,以确保塑料在模具中的流动和充填能够按照预定的要求进行。
不同的塑料种类和产品要求可能需要不同的速度设置,因此在调机时需要仔细研究产品的特点和要求进行相应设置。
四、冷却调控冷却调控是注塑成型中一个重要但常常被忽视的要素。
在塑料完成充填、压实后,需要进行冷却来使其固化成型。
冷却过程对成品的质量有着很大的影响,因此需要合理设置冷却时间和冷却介质的温度。
如果冷却不足,塑料可能会在脱模时变形或容易受到外界环境的影响;而过度冷却则可能导致产品表面出现气泡、翘曲等问题。
因此,在调机时需要根据具体情况合理控制冷却时间和温度,确保成品能够达到最佳的冷却效果。
五、保压调控保压调控是注塑成型过程中需要特别注意的一项要素。
在注塑机射胶结束后,需要进行一段时间的保压来确保产品在模具中的密实度和尺寸稳定性。
注塑机调机必备--成型条件五要素
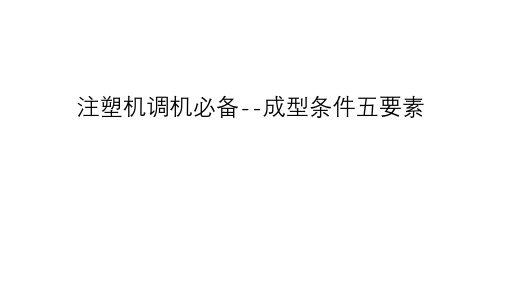
4.冷却时间 定义: 产品冷却固化而脱模后又不致于发生变形所需的时间
作用: (1)让制品固化 (2)防止制品变形
设定原则: (1)冷却时间是周期时间的重要组成部分,在保证制品质量的前提 下尽可能使其短. (2)冷却时间因熔体的温度,模具温度,产品大小及厚度而定.
5.滞留时间
定义:指注塑工艺中塑料树脂在注塑机中注射装置滚筒中的驻留时间(通常以分钟或秒计算)。换言之, 滞留时间也即塑料树脂从滚筒料斗仓口移动到喷嘴尖端的时间。滞留时间长就会导致塑料分解,塑料流动性增强, 塑料的性能发生变化。
4.缓冲量
定义: 螺杆注塑完拮,并不希望把螺杆中头部的熔料全部射出,还希望留一些.形成一个祭料量,此料量即为缓冲量. 作用: (1)防止螺杆头部与喷嘴接触发生机械破坏事故. (2)控制注射量的重复精度 设定原则: (1)缓冲量不宜过大,也不宜过小,过大,会使得余料过多,造成压力损失及原料降解,过小,则达不到缓冲之目的. (2)缓冲量的确定,一般取3~5mm为宜.
2.背压(塑化压力)
定义: 塑料在塑化过程建立在熔腔中的压力 .在塑料熔融、塑化过程中,熔料不断移向料筒前端(计量室内), 且越来越多,逐渐形成一个压力,推动螺杆向后退。为了阻止螺杆后退过快,确保熔料均匀压实,需要给螺 杆提供一个反方向的压力,这个反方向阻止螺杆后退的压力称为背压 。 作用: (1)提高熔体的比重. (2)使熔体塑化均匀. (3)使熔体中含气量降低.提高塑化质量 设定原则: (1)背压的调整应考虑塑料原料的性质. (2)背压的调整应参考制品的表观质量和尺寸精度 这种压力的大小是可以通过液压系统中的溢流阀来调整的。 在注射中,塑化压力的大小是随螺杆的设计、制品质量的要求以及塑料的种类不同而需要改变的,如果说这 些情况和螺杆的转速都不变,则增加塑化压力会加强剪切作用,即会提高熔体的温度,但会减小塑化的效率, 增大逆流和漏流,增加驱动功率。 此外,增加塑化压力常能使熔体的温度均匀,色料的混合均匀和排出熔体中的气体。 一般塑成型中的压力曲线操作中,塑化压力的决定应在保证制品质量优良的前提下越低越好,其具体数值是 随所用的塑料的品种而异的,但通常很少超过20公斤/平方厘米。 采用高背压有利于色料的分散和塑料的融化,但却同时延长了螺杆回缩时间,降低了塑料纤维的长度,增加 了注塑机的压力,因此背压应该低一些,一般不超过注塑压力的20%。
注塑机作业中的成型温度对塑料性能的影响

注塑机作业中的成型温度对塑料性能的影响注塑机在塑料制品加工中起着至关重要的作用。
其中,成型温度是影响塑料性能的关键因素之一。
本文将探讨注塑机作业中成型温度对塑料性能的影响,并提出相应的解决方案。
一、成型温度对塑料性能的影响1.熔融温度在注塑过程中,塑料需要被加热到足够的熔融温度才能进行成型。
如果温度过低,会导致塑料无法完全熔化,从而引起成型品表面出现瑕疵;如果温度过高,可能会降低塑料的分子量,从而降低其力学性能。
2.冷却速率成型温度的变化会影响注塑机的冷却速率,进而影响塑料制品的凝固过程。
过快的冷却速率会导致制品内部产生应力,从而影响其物理性能和尺寸稳定性。
而过慢的冷却速率则可能导致制品的收缩率增大,造成尺寸偏差。
3.热历程成型温度的控制还影响塑料的热历程,即塑料在加热、成型和冷却过程中的温度变化。
适当控制热历程可以使塑料分子链得到充分的定向,并有利于提高制品的力学性能和表面质量。
二、解决方案与实践1.温度控制系统的优化为了确保注塑机成型温度的准确控制,可以优化温度控制系统。
首先,确保传感器能够准确测量注塑机不同部位的温度,以便对熔融温度和冷却温度进行精确调节。
其次,采用先进的温度控制器,增加温度的稳定性和控制精度。
2.合理选择塑料材料不同种类的塑料对成型温度的敏感度各不相同。
在选择塑料材料时,需要考虑其熔融温度范围和热变形温度。
合理选择塑料材料可以更好地匹配注塑机的成型温度要求,提高塑料制品的质量。
3.优化注塑工艺参数除了控制成型温度以外,还需要优化注塑工艺参数。
例如,通过调节注塑机的注射速度、保压时间和冷却时间等参数,以达到最佳的成型温度和冷却速率。
合理调整工艺参数可以避免塑料受热时间过长或过短,从而影响塑料的性能。
4.检测与改进对于注塑机作业中的成型温度影响塑料性能的问题,通过定期检测和改进来提高工艺的稳定性和可靠性。
及时发现和解决温度控制不准确、冷却不均匀等问题,以确保塑料制品的质量。
三、结论注塑机作业中的成型温度对塑料性能有着显著影响。
模压成型的压力和温度设定对产品质量的影响

模压成型的压力和温度设定对产品质量的影响
模压成型是一种常用的工艺过程,特别适用于塑料制品的生产。
在模压成型过程中,压力和温度的设定是非常关键的因素,对最终产品的质量有着重要影响。
首先,压力是模压成型过程中的主要控制参数之一。
通过调整模具的开合速度和压力大小,可以有效地控制原料在模具中的填充情况。
适当的压力可以确保原料充分填充模具的每个角落,避免产品出现空洞或瘤状缺陷。
同时,合适的压力还可以帮助原料与模具表面更好地接触,从而提高产品的表面光洁度和精度。
其次,温度设定也是影响产品质量的重要因素之一。
在模压成型过程中,原料需要在一定温度范围内进行加热,使其塑性达到最佳状态,有利于成型和流动。
适当的温度可以保证产品表面光滑、无瑕疵,同时还可以减少产品的收缩率和内部应力,提高产品的尺寸稳定性和力学性能。
此外,压力和温度两者之间的配合也至关重要。
通常情况下,适当增加压力的同时需相应提高温度,以保证原料能够充分流动并填充模具。
过高或过低的温度都会导致产品质量下降,如温度过高可能导致产品烧结或变形,温度过低则可能导致产品表面粗糙或开裂。
因此,在模压成型过程中需要综合考虑压力和温度的互相作用,以获得最佳的成型效果和产品质量。
总的来说,模压成型的压力和温度设定是影响产品质量的重要因素,合理的压力和温度设定可以提高产品的成型精度、表面质量和力学性能,从而满足客户的各种需求。
在生产实践中,运用科学的方法和经验总结,不断优化压力和温度的设定参数,将有助于提高生产效率、降低成本,实现模压成型生产的良性循环发展。
1。
注塑成型过程中的影响因素

注塑成型过程中的影响因素注塑成型是一门工程技术,它所涉及的内容是将塑料变化为有用并能保持原有性能的制品。
注射成型的紧要工艺条件是影响塑化流动和冷却的温度,压力和相应的各个作用时间。
一、温度掌控1、料筒温度注射模塑过程需要掌控的温度有料筒温度、喷嘴温度和模具温度等。
前两个温度重要影响塑料的塑化和流动,而后一种温度重要是影响塑料的流动和冷却。
每一种塑料都具有不同的流动温度,同一种塑料,由于来源或牌号不同,其流动温度及分解温度是有差别的,这是由于平均分子量和分子量分布不同所致,塑料在不同类型的注射机内的塑化过程也是不同的,因而选择料筒温度也不相同。
2、喷嘴温度喷嘴温度通常是略低于料筒zui高温度的,这是为了防止熔料在直通式喷嘴可能发生的“流涎现象”。
喷嘴温度也不能过低,否则将会造成熔料的早凝而将喷嘴堵死,或者由于早凝料注入模腔而影响制品的性能。
3、模具温度模具温度对制品的内在性能和表观质量影响很大。
模具温度的高处与低处决议于塑料结晶性的有无、制品的尺寸与结构、性能要求,以及其它工艺条件(熔料温度、注射速度及注射压力、模塑周期等)。
二、压力掌控注塑过程中压力包括塑化压力和注射压力两种,并直接影响塑料的塑化和制品质量。
1、塑化压力(背压)采纳螺杆式注射机时,螺杆顶部熔料在螺杆转动后退时所受到的压力称为塑化压力,亦称背压。
这种压力的大小是可以通过液压系统中的溢流阀来调整的。
在注射中,塑化压力的大小是随螺杆的转速都不变,则加添塑化压力时即会提高熔体的温度,但会减小塑化的速度。
此外,加添塑化压力常能使熔体的温度均匀,色料的混合均匀和排出熔体中的气体。
一般操作中,塑化压力的决议应在保证制品质量优良的前提下越低越好,其实在数值是随所用的塑料的品种而异的,但通常很少超过20公斤/厘米。
2、注射压力在当前生产中,几乎全部的注射机的注射压力都是以柱塞或螺杆顶部对塑料所施的压力(由油路压力换算来的)为准的。
注射压力在注塑成型中所起的作用是,克服塑料从料筒流向型腔的流动阻力,予以熔料充模的速率以及对熔料进行压实。
模具温度对注塑成型的影响

模具温度对注塑成型的影响模具温度是注塑成型中最重要的变量——无论注塑何种塑料,必须保证形成模具表面基本的湿润。
一个热的模具表面使塑料表面长时间保持液态,足以在型腔内形成压力。
如果型腔填满而且在冻结的表皮出现硬化之前,型腔压力可将柔软的塑料压在金属上,那么型腔表面的复制就高。
另一方面,如果在低压下进入型腔的塑料暂停了,不论时间多短,那么它与金属的轻微接触都会造成污点,有时被称为浇口污斑。
对于每一种塑料和塑胶件,存在一个模具表面温度的极限,超过这个极限就可能出现一种或更多不良影响(例如:组件可以溢出毛边)。
模具温度更高意味着流动阻力更小。
在许多注塑机上,这自然就意味着更快流过浇、浇口和型腔,因为所用的注塑流动控制阀并不纠正这个改变,填充更快会在浇道和型腔内引起更高的有效压力。
可能造成溢料毛边。
由于更热的模型并不冻结那些在高压形成之前进入溢料边区域的塑料,熔料可在顶出杆周围溢料毛边并溢出到分割线间隙内。
这表明需要有良好的注射速率控制,而一些现代化的流动控制编程器也确实可以做到这点。
通常,模具温度的升高会减少塑料在型腔晨有冷凝层,使熔融材料在型腔内更易于流动,从而获得更大的零件重量和更好的表面质量。
同时,模具温度的提高还会使零件张力强度增加。
•模具的保温方法许多模具,尤其是工程用的热塑性塑料,在相对较高的温度下运行,如80摄氏度或176华氏度。
如果模具没有保温,流失到空气和注塑机上的热量可以很容易地与射料缸流失的一样多。
所以要将模具与机板隔热,如果可能,将模具的表面隔热。
如果考虑用热流道模具,尝试减少热道部分和冷却了的注塑件之间的热量交换。
这样的方法可以减少能量流失和预热时间。
一、塑模温度控制【一】温度控制必要性(1)温度控制对成形性之目的及作为成形品外观,材料物理性质,成形循环等,受模仁温度之影响,颇为显著。
一般成型情况,模仁温度保持于较低,可以提高射出次数较为理想,但与成形品形状(模仁构造)及成品材料种类有关之成形循环亦寄赖于必需提高模仁充填之温度。
pvc 在一定压力下的变形

pvc 在一定压力下的变形
PVC(聚氯乙烯)是一种常用的塑料材料,它在一定温度和压力下会发生变形。
PVC的变形行为受到温度、压力、时间和材料成分的影响。
1.热塑性材料:PVC是一种热塑性材料,这意味着它在受热时会软化,而在冷却后会重新硬化。
因此,在一定温度范围内,PVC可以被塑形成各种不同的形状。
这个温度范围通常称为PVC的熔点或玻璃化温度。
2.压力变形:当PVC受到外部压力作用时,它会发生压力变形。
这种变形通常表现为PVC的体积缩小或形状改变。
PVC的抗压性取决于材料的类型和成分,以及施加的压力大小。
3.弹性恢复:一旦外部压力解除,PVC通常会在一定程度上恢复原状。
这是因为PVC是一种具有一定弹性的材料。
4.时间效应:PVC的变形也可能受到时间的影响,即长时间受到压力作用可能会导致持久的变形。
要理解PVC在一定压力下的变形行为,需要考虑材料的温度、压力、时间和负荷大小。
这些因素都会影响PVC的变形特性,因此在设计和使用PVC制品时,需要充分考虑这些因素,以确保其性能和可持续性。
塑胶成型的五大要素

塑胶成型的五大要素塑胶成型这件事情,就像是在厨房做一道美味佳肴,需要掌握好几个关键要素才能做出好产品。
今天我们就来聊聊这五个要素,保证说得通俗易懂,让大家一听就明白!温度可是个大boss!就像煮饭一样,火候太大会糊,太小又煮不熟。
塑胶成型时的温度控制也是这个道理,要是温度不对,塑料就会闹脾气。
温度太高,塑料会变得跟糊糊似的,做出来的东西歪歪扭扭;温度太低,塑料又会变得特别倔强,根本不听话,跟石头似的难以成型。
压力这个要素,就像是给面团揉面时的力道。
力道太大,面团都给你挤扁了;力道太小,面团又不能充分混合。
塑胶成型时的压力也是这个道理,压力要是掌握不好,产品要么密度不均,要么表面会起泡,就像发霉的馒头一样难看。
时间控制简直就是个艺术!就像煮鸡蛋,三分钟是溏心,五分钟是半熟,七分钟是全熟。
塑胶成型的时间也得掌握得恰到好处,时间太短,里面还没熟透呢;时间太长,又会把塑料给憋坏了,搞不好还会变色,那可就尴尬了。
说到速度,这可真是个有意思的要素。
想象一下,你在倒果汁,倒得太快会溅得到处都是,倒得太慢又浪费时间。
塑胶成型的速度也是这样,注塑速度要是太快,塑料会像受惊的小兔子一样乱窜;速度太慢,又会影响生产效率,而且容易在产品表面留下难看的痕迹。
冷却这个要素,就像是刚出炉的面包需要晾一会儿才能切。
塑胶制品也需要适当的冷却时间,要是冷却不当,产品就会变形,就像晒太阳晒蔫了的塑料花一样难看。
冷却时间太短,产品会变形;太长,又会影响生产效率。
这五个要素之间还特别爱搞对象,它们互相之间都有着千丝万缕的关系。
就像温度和压力是一对好搭档,温度高了,压力就得适当调整;时间和速度又是一对,速度快了,时间自然要跟着变。
在实际生产中,这五个要素就像是在演奏一首交响乐,每个要素都是一件乐器,必须协调一致才能奏出美妙的音乐。
要是哪个要素走调了,整个产品就会变得不伦不类。
有趣的是,不同的塑料材料对这五个要素的要求还不一样。
有的塑料特别娇气,温度稍微高一点点就会变质;有的塑料倒是挺耐造,温度范围可以放宽一些。
注塑工艺参数对塑料产品成型的影响
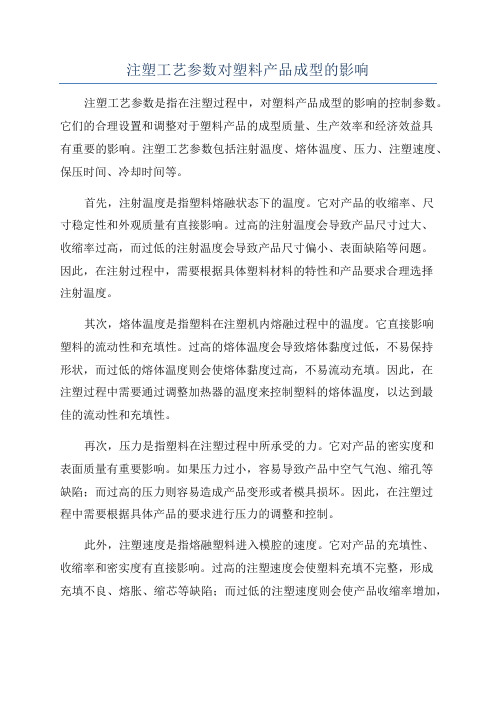
注塑工艺参数对塑料产品成型的影响注塑工艺参数是指在注塑过程中,对塑料产品成型的影响的控制参数。
它们的合理设置和调整对于塑料产品的成型质量、生产效率和经济效益具有重要的影响。
注塑工艺参数包括注射温度、熔体温度、压力、注塑速度、保压时间、冷却时间等。
首先,注射温度是指塑料熔融状态下的温度。
它对产品的收缩率、尺寸稳定性和外观质量有直接影响。
过高的注射温度会导致产品尺寸过大、收缩率过高,而过低的注射温度会导致产品尺寸偏小、表面缺陷等问题。
因此,在注射过程中,需要根据具体塑料材料的特性和产品要求合理选择注射温度。
其次,熔体温度是指塑料在注塑机内熔融过程中的温度。
它直接影响塑料的流动性和充填性。
过高的熔体温度会导致熔体黏度过低,不易保持形状,而过低的熔体温度则会使熔体黏度过高,不易流动充填。
因此,在注塑过程中需要通过调整加热器的温度来控制塑料的熔体温度,以达到最佳的流动性和充填性。
再次,压力是指塑料在注塑过程中所承受的力。
它对产品的密实度和表面质量有重要影响。
如果压力过小,容易导致产品中空气气泡、缩孔等缺陷;而过高的压力则容易造成产品变形或者模具损坏。
因此,在注塑过程中需要根据具体产品的要求进行压力的调整和控制。
此外,注塑速度是指熔融塑料进入模腔的速度。
它对产品的充填性、收缩率和密实度有直接影响。
过高的注塑速度会使塑料充填不完整,形成充填不良、熔胀、缩芯等缺陷;而过低的注塑速度则会使产品收缩率增加,尺寸不稳定。
因此,在注塑过程中需要通过调整注塑机的注射速度来控制注塑速度,以达到产品质量要求。
保压时间是指塑料在注塑过程中保持一定压力的时间。
它对产品的密实度、尺寸稳定性和缺陷情况有直接影响。
保压时间过长会使产品收缩率过大,尺寸偏大;保压时间过短则会导致产品尺寸偏小、表面缺陷等问题。
因此,在注塑过程中需要根据具体产品的要求和塑料材料的特性进行保压时间的调整和设定。
最后,冷却时间是指塑料在注塑过程中冷却的时间。
它对产品的尺寸稳定性、变形和序列产能有重要影响。
常用注塑工艺参数

常用注塑工艺参数注塑工艺参数是指在注塑成型过程中需要设置的各项参数,包括料筒温度、注塑压力、注射速度、保压时间、冷却时间等。
这些参数的设置将直接影响到注塑成型的质量和效率。
下面是一些常用的注塑工艺参数。
1.料筒温度:注塑过程中需保持一定的料筒温度,一般分为上料区、加热区和冷却区。
上料区用于将塑料原料加热至熔融状态,一般设置较低的温度,避免原料在上料过程中过度熔化或变质。
加热区用于将熔融状态的塑料加热至合适的注射温度,一般设置较高的温度。
冷却区用于降低热塑性塑料的温度,避免注射后的产品变形或变色。
2.注塑压力:注塑压力是指注射机在注塑成型过程中对塑料熔融物体所施加的压力。
注塑压力既影响塑料的熔融和注射速度,也影响充填过程中的背压。
一般情况下,注塑压力应根据产品的尺寸、结构和塑料的性质进行调整,以保证产品的充填性能和尺寸精度。
3.注射速度:注射速度是指注射机将塑料熔融物体注射到模具中的速度。
注射速度的快慢将直接影响到产品的充填性能和尺寸精度。
一般情况下,注射速度应根据产品的尺寸、壁厚和注塑机的规格进行调整,以保证产品的充填性能和表面质量。
4.保压时间:保压时间是指在注射和充填完成后,继续对模具施加一定的保压力和时间,使产品保持充填状态直到冷却和固化完全。
保压时间一般根据产品的尺寸、壁厚和注塑机的规格进行调整,以保证产品的密实度和尺寸精度。
5.冷却时间:冷却时间是指产品在模具中冷却和固化的时间。
冷却时间应根据产品的尺寸、壁厚和冷却条件进行调整,以保证产品冷却和固化完全,并避免产品变形和缩水现象的发生。
6.模具温度:模具温度是指模具加热系统对模具进行加热的温度。
模具温度应根据产品的尺寸、壁厚和塑料的性质进行调整,以保证产品的表面质量和尺寸精度。
7.射胶量:射胶量是指每次注射时注塑机所注入模具中的塑料量。
射胶量一般根据产品的尺寸、壁厚和注塑机的规格进行调整,以保证产品的充填性能和表面质量。
8.背压:背压是指在注射过程中,注塑机对塑料熔融物体施加的压力。
影响塑胶成型的主要工艺参数

影响塑胶成型的主要工艺参数
塑胶成型是一种广泛应用于工业生产中的制造工艺,它的质量和效率受到许多不同的工艺参数的影响。
以下是影响塑胶成型的主要工艺参数:
1. 温度
温度是影响塑胶成型的最重要的参数之一。
在制造过程中,塑料必须被加热到足够的温度,以便它可以变得柔软并且可以被塑形。
但是,如果温度过高,就会导致塑料熔化或者烧焦。
因此,必须控制好温度,确保在正确的范围内。
2. 压力
压力是塑胶成型中另一个重要的参数。
在制造过程中,塑料必须被注入到模具中,并且需要足够的压力才能填充模具中的所有空间。
如果压力不够,就会导致模具中存在空隙或者气泡,从而影响制品质量。
3. 时间
时间也是影响塑胶成型的一个关键参数。
在注塑过程中,塑料需要一定的时间才能充分地填充模具,并且需要一定的时间来冷却和固化。
如果时间不够,就会导致制品出现缺陷或者变形。
4. 模具设计
模具设计是影响塑胶成型质量的另一个重要因素。
模具必须被设计成能够完全填充并且允许塑料流动的形状。
此外,模具应该被设计成易于拆卸和清洁,以便能够快速地进行生产。
5. 塑料类型
不同类型的塑料对于成型过程有不同的要求。
例如,一些塑料需要更高的温度和压力才能被成型,而另一些则需要更少的时间来冷却和固化。
因此,在选择塑料时必须考虑到它们的特性和成型要求。
总之,以上这些工艺参数都对塑胶成型有着重要的影响。
在生产过程中必须仔细控制这些参数,并且根据需要进行调整,以确保生产出高质量的制品。
影响塑胶成型的主要工艺参数
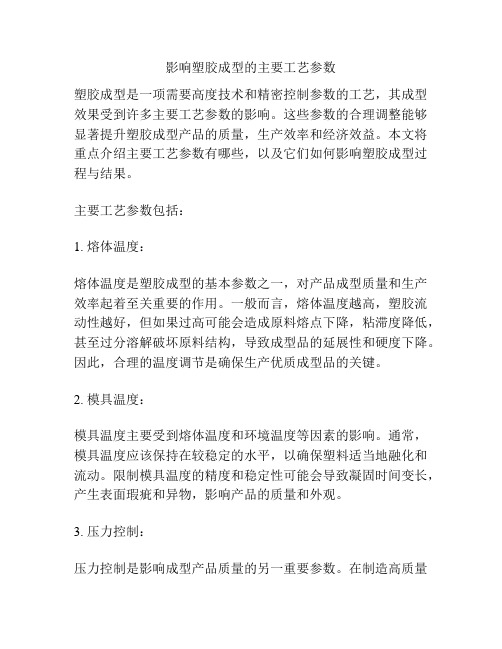
影响塑胶成型的主要工艺参数塑胶成型是一项需要高度技术和精密控制参数的工艺,其成型效果受到许多主要工艺参数的影响。
这些参数的合理调整能够显著提升塑胶成型产品的质量,生产效率和经济效益。
本文将重点介绍主要工艺参数有哪些,以及它们如何影响塑胶成型过程与结果。
主要工艺参数包括:1. 熔体温度:熔体温度是塑胶成型的基本参数之一,对产品成型质量和生产效率起着至关重要的作用。
一般而言,熔体温度越高,塑胶流动性越好,但如果过高可能会造成原料熔点下降,粘滞度降低,甚至过分溶解破坏原料结构,导致成型品的延展性和硬度下降。
因此,合理的温度调节是确保生产优质成型品的关键。
2. 模具温度:模具温度主要受到熔体温度和环境温度等因素的影响。
通常,模具温度应该保持在较稳定的水平,以确保塑料适当地融化和流动。
限制模具温度的精度和稳定性可能会导致凝固时间变长,产生表面瑕疵和异物,影响产品的质量和外观。
3. 压力控制:压力控制是影响成型产品质量的另一重要参数。
在制造高质量的塑料部件的过程中,要保证合适的压力,以确保塑料适当定位并填充全部空间。
压力过大会导致产品变形、沉降和缩放,而过小则会影响填充时间和产品外观质量等问题。
4. 塑胶流量速度和时间:塑料流量速度和时间也是成型过程的关键参数因素之一。
如果速度过高,可能会产生熔态的塑料物料,导致产生空隙和变形、熔料的正常填充和降低表面质量等缺陷,而速度过慢则会导致产品脆性等问题。
5. 锁模力:锁模力是实现整个成型过程的一个关键参数。
如果锁模力不足,会导致在填充时模具会发生形变,产生喷漏或剪切破裂痕迹等问题。
相反,过高的锁模力也可能导致模具损坏,降低模具的使用寿命等问题。
综合来看,合理的工艺参数调节和控制,不仅仅可以提高生产效率,更重要的是可以生产出高质量的成型品,为塑胶成型行业的未来增添更多的发展潜力和机会。
除上述主要工艺参数外,还有一些其他的参数也会影响到塑胶成型的生产效果和产量,例如:6. 压力传感器与控制系统:在塑胶成型过程中,主要通过压力传感器和控制系统来控制和监视各个节点的压力变化。
塑料成形特性介绍
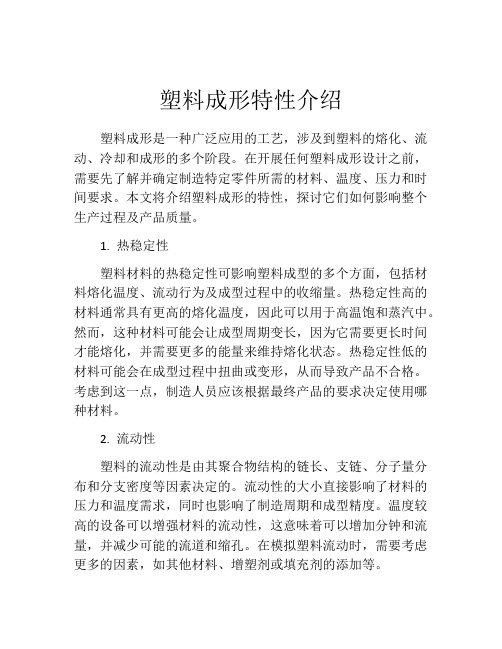
塑料成形特性介绍塑料成形是一种广泛应用的工艺,涉及到塑料的熔化、流动、冷却和成形的多个阶段。
在开展任何塑料成形设计之前,需要先了解并确定制造特定零件所需的材料、温度、压力和时间要求。
本文将介绍塑料成形的特性,探讨它们如何影响整个生产过程及产品质量。
1. 热稳定性塑料材料的热稳定性可影响塑料成型的多个方面,包括材料熔化温度、流动行为及成型过程中的收缩量。
热稳定性高的材料通常具有更高的熔化温度,因此可以用于高温饱和蒸汽中。
然而,这种材料可能会让成型周期变长,因为它需要更长时间才能熔化,并需要更多的能量来维持熔化状态。
热稳定性低的材料可能会在成型过程中扭曲或变形,从而导致产品不合格。
考虑到这一点,制造人员应该根据最终产品的要求决定使用哪种材料。
2. 流动性塑料的流动性是由其聚合物结构的链长、支链、分子量分布和分支密度等因素决定的。
流动性的大小直接影响了材料的压力和温度需求,同时也影响了制造周期和成型精度。
温度较高的设备可以增强材料的流动性,这意味着可以增加分钟和流量,并减少可能的流道和缩孔。
在模拟塑料流动时,需要考虑更多的因素,如其他材料、增塑剂或填充剂的添加等。
3. 填充特性填充是在塑料成形过程中常用的技术,可以将金属、纤维和其他颗粒状材料加入到聚合物基质中,以改善其机械性能和/或外观。
填充物颗粒的形状、大小和分布都会对材料的流动性、成型收缩率、机械性能和外观等特征产生影响。
测试填充物分布和形态的方法包括密度测试、高分辨率显微镜照片等。
4. 尺寸稳定性由于塑料成型过程中的温度梯度、冷却速率和工具设计的缩孔,塑料制件的尺寸稳定性成为一个很大的问题。
缩孔可以在成型后形成不和模具内壁接触的部分。
尺寸稳定性通常是通过测量长期的材料缩合量来衡量。
成型后的产品要经过冷却和排气才能尽可能地缩小空气在部件内的含量。
调节温度、加压和时间等参数来达到最佳的成形效果。
5. 加工稳定性有些材料很容易出现成形不良和双色/三色成型等问题,这些问题可能会使材料变形、变色或形成瑕疵因此,在选择材料的时,需要特别注意它的加工稳定性。
pet和pbt成型条件

pet和pbt成型条件PET和PBT成型条件一、引言PET(聚对苯二甲酸乙二醇酯)和PBT(聚对苯二甲酸丁二醇酯)是常用的工程塑料,广泛应用于各个领域。
为了获得高质量的PET和PBT制品,成型条件起着关键作用。
本文将重点介绍PET和PBT的成型条件。
二、PET的成型条件1. 温度控制PET的成型温度一般在240℃-280℃之间。
过高的温度会导致热分解,影响制品质量;过低的温度则会导致熔体流动性较差,难以充填模具。
因此,在PET的成型过程中,需要精确控制温度,确保在合适的范围内。
2. 压力控制PET的成型压力一般在80MPa-140MPa之间。
过高的压力可能导致模具开裂或变形,同时也会增加设备的能耗;过低的压力则会导致制品表面不光滑、翘曲等问题。
因此,在PET的成型过程中,需要根据具体情况调整压力,以保证制品质量。
3. 冷却控制PET的成型过程中,冷却是非常重要的一环。
合理的冷却可以使PET迅速凝固,避免制品变形和收缩。
一般来说,冷却时间应占整个成型周期的三分之一左右。
此外,还可以通过调整冷却介质的温度和流速来控制制品的冷却效果。
4. 料筒温度控制PET的成型过程中,料筒温度的控制也非常重要。
料筒温度过高会导致PET在料筒中降解,影响制品质量;料筒温度过低则会影响熔体的流动性。
因此,在PET的成型过程中,需要根据具体的PET牌号和成型要求,合理调整料筒温度。
三、PBT的成型条件1. 温度控制PBT的成型温度一般在230℃-270℃之间。
过高的温度会导致材料降解,产生气泡、烧焦等问题;过低的温度则会导致材料流动性差,难以填充模具。
因此,在PBT的成型过程中,需要准确控制温度,确保在合适的范围内。
2. 压力控制PBT的成型压力一般在60MPa-120MPa之间。
过高的压力会导致模具变形、开裂等问题;过低的压力则会导致制品表面质量不好。
因此,在PBT的成型过程中,需要根据具体情况调整压力,以保证制品质量。
温度,时间,压力对某某塑料成型的影响

温度,时间,压力对某某塑料成型的影响时间、压力、温度对聚丙烯塑料成型的影响2008081 模具081前言聚丙烯是通用塑料中用量较大的品种之一,具有密度小,刚性好,耐挠曲,耐化学腐蚀,绝缘性好等优点。
它的不足之处是低温冲击性能较差、易老化、成型收缩率大。
通过改性可以改善聚丙烯的低温冲击性能、成型收缩和热老化性能。
使聚丙烯的使用范围大辐度扩大,在很多场合取代传统的工程塑料。
聚丙烯原料来源充足,价格便宜,因而近年来在塑料改性行业中聚丙烯改性占据首位,成为改性塑料的主要品种,越来越受到人们的重视。
聚丙烯简介聚丙烯,英文名称:Polypropylene分子式:C3H6nCAS简称:PP由丙烯聚合而制得的一种热塑性树脂。
按甲基排列位置分为等规聚丙烯(isotaeticPolyProlene)、无规聚丙烯(atacticPolyPropylene)和间规聚丙烯(syndiotaticPolyPropylene)三种。
成型特性1.结晶料,湿性小,易发生融体破裂,长期与热金属接触易分解。
2.流动性好,但收缩范围及收缩值大,易发生缩孔。
凹痕,变形。
3.冷却速度快,浇注系统及冷却系统应缓慢散热,并注意控制成型温度,料温低温高压时容易取向,模具温度低于50度时,塑件不光滑,易产生熔接不良,流痕,90度以上易发生翘曲变形。
4.塑料壁厚须均匀,避免缺胶,尖角,以防应力集中。
注塑模工艺条件:注塑机选用:对注塑机的选用没有特殊要求。
由于PP具有高结晶性。
需采用注射压力较高及可多段控制的电脑注塑机。
锁模力一般按3800t/m2来确定,注射量20%-85%即可。
干燥处理:如果储存适当则不需要干燥处理。
熔化温度:PP的熔点为160-175℃,分解温度为350℃,但在注射加工时温度设定不能超过275℃。
熔融段温度最好在240℃。
模具温度:模具温度50-90℃,对于尺寸要求较高的用高模温。
型芯温度比型腔温度低5℃以上。
注射压力:采用较高注射压力(1500-1800bar)和保压压力(约为注射压力的80%)。
关于温度、时间以及压力对聚乙烯PE的注塑成型的影响

关于温度、时间以及压力对聚乙烯PE的注塑成型的影响模具081班方毅20081018随着聚乙烯(PE)在市场上的应用越来越广,而且对它的研究也越来越深入。
所以我们来谈谈聚乙烯在加工工艺中温度、时间以及压力对它的影响。
首先,了解聚乙烯材料。
聚乙烯英文名称:polyethylene ,简称PE,是乙烯经聚合制得的一种热塑性树脂。
在工业上,也包括乙烯与少量α-烯烃的共聚物。
聚乙烯无臭,无毒,手感似蜡,具有优良的耐低温性能(最低使用温度可达-70~-100℃),化学稳定性好,能耐大多数酸碱的侵蚀(不耐具有氧化性质的酸),常温下不溶于一般溶剂,吸水性小,电绝缘性能优良,但聚乙烯对于环境应力(化学与机械作用)是很敏感的,耐热老化性差。
聚乙烯的性质因品种而异,主要取决于分子结构和密度。
超高分子量聚乙烯的强度非常高,可以用来做防弹衣。
纯度99%以上的乙烯在催化剂四氯化钛和一氯二乙基铝存在下,在压力0.1-0.5MPa和温度65-75℃的汽油中聚合得到HDPE的淤浆。
经醇解破坏残余的催化剂、中和、水洗,并回收汽油和未聚合的乙烯,经干燥、造粒得到产品。
我国研制的一种聚乙烯材料,超过四十度时完全融化,低于十五度时完全凝固。
这是由于物体熔化吸热,凝固放热。
在温度较低时,聚乙烯材料凝固放热,使室温不至于太低。
而温度较高时,材料熔化吸热,使室温保持在一个较低的水平。
其次,我们来了解一下温度、时间、压力对PE塑料的成型工艺上的影响。
第一、塑料的成型工艺1)冷却时释放出的热量大,要充分冷却,高模温成型时注意冷却时间的控制;2)熔态与固态时的比重差大,成型收缩大,易发生缩孔、气孔,要注意保压压力的设定;3)模温低时,冷却快,结晶度低,收缩小,透明度高。
结晶度与塑件壁厚有关,塑件壁厚大时冷却慢结晶度高,收缩大,物性好,所以结晶性塑料应按要求必须控制模温;4)各向异性显著,内应力大,脱模后未结晶折分子有继续结晶化的倾向,处于能量不平衡状态,易发生变形、翘曲,应适当提高料温和模具温度,中等的注射压力和注射速度。
注塑工艺的五大要素

注塑工艺的五大要素
一、温度:注塑过程中的温度控制是非常重要的,温度的不同会影响到熔融状态的塑料流动性、填充性和稳定性。
在注塑模具中,塑料熔融后会注入到模具腔中进行冷却成型,温度的控制可以影响到产品的尺寸和表面质量。
如果温度过高,塑料容易炭化或分解,而温度过低则会导致产品尺寸收缩不够。
二、压力:注塑过程中的压力控制也非常关键,它可以影响到塑料的流动性和填充性。
在注塑过程中,塑料会受到注塑机的压力作用被挤压入模具腔中,同时也可以起到排除空气、充实模具腔的作用。
过高或过低的压力都会影响到产品的质量和尺寸。
三、流速:流速是指塑料在注塑过程中的流动速度,它直接影响到塑料充实模具腔的速度和填充性。
流速过快会导致塑料在模具腔中的充实不充分,从而产生缩孔、短射等缺陷;而流速过慢则会导致模具腔中塑料的熔融温度过高,容易损坏模具。
四、冷却时间:冷却时间指的是塑料在模具腔中冷却固化的时间,这个时间对于产品的尺寸、收缩率和密度等都有着重要影响。
适当的冷却时间可以使产品充分固化,从而保证其尺寸稳定性和表面质量。
五、卸模时间:卸模时间指的是产品在模具中冷却固化后,从模具中取出的时间。
如果卸模时间过早,产品可能还没有完全固化就会变形或损坏;而如果卸模时间过晚,产品可能会粘附在模具上,难以取出。
因此,合理的卸模时间对于产品的成型质量和模具的使用寿命都是非常重要的。
总结起来,注塑工艺的五大要素包括温度、压力、流速、冷却时间和卸模时间,它们在注塑过程中相互关联、相互作用,对于产品的质量、尺
寸和表面质量都有着重要的影响。
注塑工艺的优化和控制需要综合考虑以上要素,以实现最佳的成型效果。
塑料成型工艺参数对产品质量的影响实验心得

塑料成型工艺参数对产品质量的影响实验心得
1. 温度:温度是塑料成型的重要参数,对产品的物理性能、表面质量以及尺寸稳定性都有影响。
如果温度过高,可能导致材料熔化不均匀,产生气泡或烧焦的现象;如果温度过低,则可能导致成型件不完整或收缩不足。
因此,合适的温度范围对于保证产品质量非常重要。
2. 压力:压力是保证塑料充填和充实的重要参数。
适当的压力可以确保塑料在模具中充填均匀,并充实到预定的位置,避免产生缩孔和其他缺陷。
不同的成型工艺有不同的压力要求,需要进行适当的调整。
3. 时间:成型时间直接影响到产品形状的准确性和尺寸的稳定性。
过长或过短的时间都可能导致产品质量不稳定、尺寸变化或翘曲等问题。
因此,需要根据具体材料和产品要求来调整成型时间。
4. 冷却系统:冷却是保证产品质量的关键环节。
合理的冷却系统可以确保成型件在模具中完全固化和收缩,避免变形和内应力的产生。
因此,冷却时间和温度的控制非常重要。
总的来说,塑料成型工艺参数的调整对产品质量有重要影响。
合理调整温度、压力、时间和冷却系统,可以确保产品的物理性能、表面质量和尺寸稳定性。
在实际操作中,还需要结合具体的材料和产品要求,进行综合考虑和优化调整。
- 1、下载文档前请自行甄别文档内容的完整性,平台不提供额外的编辑、内容补充、找答案等附加服务。
- 2、"仅部分预览"的文档,不可在线预览部分如存在完整性等问题,可反馈申请退款(可完整预览的文档不适用该条件!)。
- 3、如文档侵犯您的权益,请联系客服反馈,我们会尽快为您处理(人工客服工作时间:9:00-18:30)。
时间、压力、温度对聚丙烯塑料成型的影响
2008081 模具081
前言
聚丙烯是通用塑料中用量较大的品种之一,具有密度小,刚性好,耐挠曲,耐化学腐蚀,绝缘性好等优点。
它的不足之处是低温冲击性能较差、易老化、成型收缩率大。
通过改性可以改善聚丙烯的低温冲击性能、成型收缩和热老化性能。
使聚丙烯的使用范围大辐度扩大,在很多场合取代传统的工程塑料。
聚丙烯原料来源充足,价格便宜,因而近年来在塑料改性行业中聚丙烯改性占据首位,成为改性塑料的主要品种,越来越受到人们的重视。
聚丙烯简介
聚丙烯,英文名称:Polypropylene
分子式:C3H6nCAS
简称:PP由丙烯聚合而制得的一种热塑性树脂。
按甲基排列位置分为等规聚丙烯(isotaeticPolyProlene)、无规聚丙烯(atacticPolyPropylene)和间规聚丙烯(syndiotaticPolyPropylene)三种。
成型特性
1.结晶料,湿性小,易发生融体破裂,长期与热金属接触易分解。
2.流动性好,但收缩范围及收缩值大,易发生缩孔。
凹痕,变形。
3.冷却速度快,浇注系统及冷却系统应缓慢散热,并注意控制成型温度,料温低温高压时容易取向,模具温度低于50度时,塑件不光滑,易产生熔接不良,流痕,90度以上易发生翘曲变形。
4.塑料壁厚须均匀,避免缺胶,尖角,以防应力集中。
注塑模工艺条件:
注塑机选用:对注塑机的选用没有特殊要求。
由于PP具有高结晶性。
需采用注射压力较高及可多段控制的电脑注塑机。
锁模力一般按3800t/m2来确定,注射量20%-85%即可。
干燥处理:如果储存适当则不需要干燥处理。
熔化温度:PP的熔点为160-175℃,分解温度为350℃,但在注射加工时温度设定不能超过275℃。
熔融段温度最好在240℃。
模具温度:模具温度50-90℃,对于尺寸要求较高的用高模温。
型芯温度比型腔温度低5℃以上。
注射压力:采用较高注射压力(1500-1800bar)和保压压力(约为注射压力的80%)。
大概在全行程的95%时转保压,用较长的保压时间。
注射速度:为减少内应力及变形,应选择高速注射,但有些等级的PP和模具不适用(出现气泡、气纹)。
如刻有花纹的表面出现由浇口扩散的明暗相间条纹,则要用低速注射和较高模温。
流道和浇口:流道直径4-7mm,针形浇口长度1-1.5mm,直径可小至0.7mm。
边形浇口长度越短越好,约为0.7mm,深度为壁厚的一半,宽度为壁厚的两倍,并随模腔内的熔流长度逐肯增加。
模具必须有良好的排气性,排气孔深0.025mm-0.038mm,厚1.5mm,要避免收缩痕,就要用大而圆的注口及圆形流道,加强筋的厚度要小(例如是壁厚的50-60%)。
均聚PP制造的产品,厚度不能超过3mm,否则会有气泡(厚壁制品只能用共聚PP)。
熔胶背压:可用5bar熔胶背压,色粉料的背压可适当调高。
制品的后处理:为防止后结晶产生的收缩变形,制品一般需经热水浸泡处理。
时间,温度,压力的分析
1.时间对成型的影响
注射成型时间越长,收缩率越小。
但当浇口凝封后,再延长注射时间不但不起作用,反而容易引起浇口附近产生裂纹等缺陷。
其次,加热时间不宜过长,否则会发生分解,灼伤
再者,在热塑性塑料注射成型中,制品在模腔内的冷却时间对制品成型收缩率的影响因树脂种类、制品壁厚、料温、模温和结晶方式等不同而异。
模内冷却时间长能使收缩率减小。
对于非结晶型塑料影响不大。
但对于结晶型塑料,若冷却时间过长,结晶得到充分进行,结晶度高,成型收缩率就会增大。
但是一般来说,冷却时间过长,冷却可均匀进行。
当模具内的制品得以充分固化,因而成型收缩率小。
即:温度对收缩率的影响大于结晶对收缩率的影响。
2.压力对成型的影响
提高注塑压力有利于熔料的充模,由于PE的流动性很好,因此除薄壁细长制品外,应该精良选择较低的注射压力,一般采用较高注射压力(1500-1800bar)和保压压力(约为注射压力的80%)。
大概在全行程的95%时转保压,用较长的保压时间。
形状简单。
壁后较大的塑件,注射压力可以低些,反之则高。
其次,较高的成型压力使模腔内的制品密度大,收缩减小,特别是保压阶段的压力和保压时间对制品收缩产生的影响更大。
也可以说模腔内材料压力越高,弹性恢复越大,因此收缩率越小。
但是,不适当地增大成型压力,会引起成型后的制品存在较大的残留内应力,导
致以后制品的变形、开裂。
即使对于同一制品,模腔内树脂的压力在各部分也不一致,所以收缩也会有所不同,严重时也会导致以后制品的变形、开裂。
3.温度对成型的影响
物料熔体温度与模腔内熔体的充注状态和冷却方式等有密切的关系。
成型收缩是这些状态综合的体现。
随物料的种类、制品形状、模具温度、树脂温度、制品壁厚和浇口大小等不同,熔体温度对成型收缩的影响有很大差异,甚至会出现完全相反的情况。
PP的熔点为
160-175℃,分解温度为350℃,但在注射加工时温度设定不能超过275℃。
熔融段温度最好在240℃。
模具温度50-90℃,对于尺寸要求较高的用高模温。
型芯温度比型腔温度低5℃以上。
一般情况下,料温越高,制品的收缩就越大。
但随料温的增加,物料的熔体粘度下降,在不改变注塑压力的情况下,模腔内的压力损失就会减小,进入模腔的料流压力增高,不但抵消了熔体温度升高的影响,反而使制品收缩率减小(但当模具温度较低时,成型收缩率稍有增大的倾向)。
PP类树脂,当熔体温度较低时,料流方向的收缩率比垂直于料流方向的大。
而且随着熔体温度的上升,其差值减小。
结论
正确选择注射成型工艺的参数为保证塑料熔体在成为良好塑件的必要条件。
扩大浇口横截面或调低注射速度都是可选择的措施.另外,提高模具温度,也能减缓与型腔表面接触的树脂的冷却速率,这对防止在充填初期形成表面硬化皮,也具有良好的效果. 提高模具温度并使模具温度均匀,提高树脂温度或采用退火方法予以消除应力。
通过对热塑性塑料在注射成型过程中常见缺陷及其产生原因的分析, 我们可以清楚的知道,对于制品的某一缺陷有可能是多方面因素综合影响,我们应当对存在的问题逐一查找其原因并耐心纠正;特别是在调整工艺时,最好一次只改变一个条件,假如把时间,温度,压力一起调节,则容易造成混乱和误解.。