精益生产10个原则
精益生产12原则
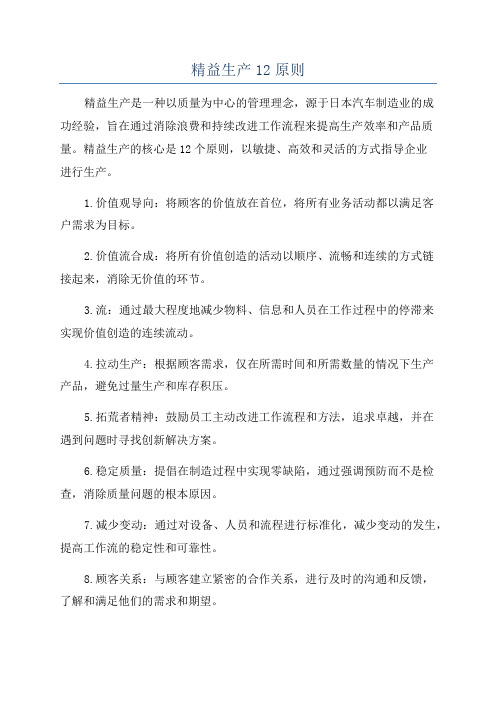
精益生产12原则精益生产是一种以质量为中心的管理理念,源于日本汽车制造业的成功经验,旨在通过消除浪费和持续改进工作流程来提高生产效率和产品质量。
精益生产的核心是12个原则,以敏捷、高效和灵活的方式指导企业进行生产。
1.价值观导向:将顾客的价值放在首位,将所有业务活动都以满足客户需求为目标。
2.价值流合成:将所有价值创造的活动以顺序、流畅和连续的方式链接起来,消除无价值的环节。
3.流:通过最大程度地减少物料、信息和人员在工作过程中的停滞来实现价值创造的连续流动。
4.拉动生产:根据顾客需求,仅在所需时间和所需数量的情况下生产产品,避免过量生产和库存积压。
5.拓荒者精神:鼓励员工主动改进工作流程和方法,追求卓越,并在遇到问题时寻找创新解决方案。
6.稳定质量:提倡在制造过程中实现零缺陷,通过强调预防而不是检查,消除质量问题的根本原因。
7.减少变动:通过对设备、人员和流程进行标准化,减少变动的发生,提高工作流的稳定性和可靠性。
8.顾客关系:与顾客建立紧密的合作关系,进行及时的沟通和反馈,了解和满足他们的需求和期望。
9.员工发展:鼓励员工参与决策和改进,并提供培训和培养机会,激励员工的自我发展和职业成长。
10.合作伙伴关系:与供应商建立长期的合作伙伴关系,共同寻求质量提升和工艺改进的可能。
11.持续改进:不断寻求改进的机会,在每个层面和每个环节上追求卓越和最佳实践。
12.健康安全:确保员工的安全和健康,并提供良好的工作环境和条件,以最大程度地保护员工的福祉。
这些原则共同构成了精益生产的核心理念和指导原则,可以帮助企业实现高效、高质量和可持续发展的生产,从而提高竞争力和客户满意度。
虽然这些原则主要针对生产领域,但它们也可以应用于其他领域,如服务业和管理领域。
实现精益生产的14项管理原则
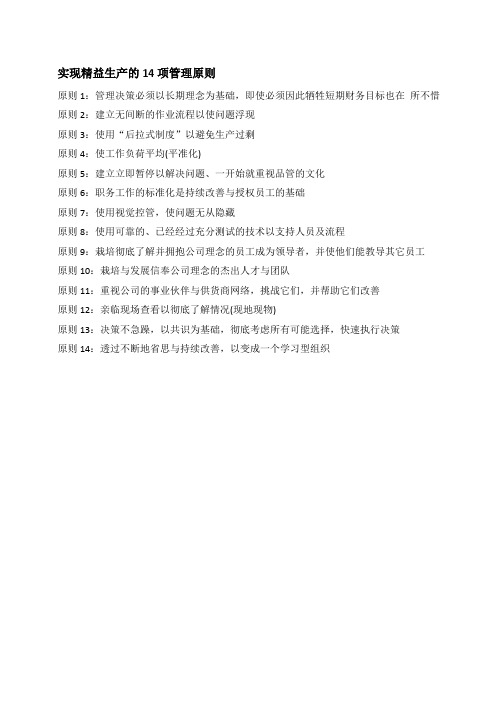
实现精益生产的14项管理原则
原则1:管理决策必须以长期理念为基础,即使必须因此牺牲短期财务目标也在所不惜原则2:建立无间断的作业流程以使问题浮现
原则3:使用“后拉式制度”以避免生产过剩
原则4:使工作负荷平均(平准化)
原则5:建立立即暂停以解决问题、一开始就重视品管的文化
原则6:职务工作的标准化是持续改善与授权员工的基础
原则7:使用视觉控管,使问题无从隐藏
原则8:使用可靠的、已经经过充分测试的技术以支持人员及流程
原则9:栽培彻底了解并拥抱公司理念的员工成为领导者,并使他们能教导其它员工
原则10:栽培与发展信奉公司理念的杰出人才与团队
原则11:重视公司的事业伙伴与供货商网络,挑战它们,并帮助它们改善
原则12:亲临现场查看以彻底了解情况(现地现物)
原则13:决策不急躁,以共识为基础,彻底考虑所有可能选择,快速执行决策
原则14:透过不断地省思与持续改善,以变成一个学习型组织。
精益生产方案

精益生产方案一、引言在当今竞争激烈的市场环境下,企业需要不断寻求提高效率和降低成本的方法。
精益生产是一种有效的管理方法,旨在通过最小化浪费和优化价值流程,提高生产效率。
本文将介绍精益生产的概念、原则和实施步骤,并结合实际案例分析其应用。
二、精益生产的概念精益生产是一种基于质量管理和生产效率的方法,最早由丰田汽车公司引入。
它的核心理念是在生产过程中消除浪费和降低成本,以提高生产效率和产品质量。
精益生产强调以客户为中心,追求价值流程的流畅与高效。
三、精益生产的原则1. 客户价值:确定产品或服务对客户产生价值的要素,消除无效的步骤和过程。
2. 价值流程:优化价值流程,使生产活动与客户需求高度匹配,减少浪费。
3. 流程流畅:消除生产流程中的瓶颈与障碍,提高整体生产效率。
4. 拉动生产:根据客户需求,通过有效的生产计划和物料管理,减少库存和生产周期。
5. 持续改进:通过员工参与和良好的反馈机制,不断优化生产流程和提升产品质量。
四、精益生产的实施步骤1. 价值流程分析:明确生产过程中的价值和浪费,进行价值流程图绘制,找出改进的重点。
2. 浪费消除:根据价值流程图,针对每一环节中的浪费因素进行改进,例如减少等待、运输和工具调整时间。
3. 流程流畅化:优化各个环节之间的协调与衔接,消除瓶颈,避免过程中的等待和停滞。
4. 拉动生产模式:根据客户需求进行生产计划,避免过度生产和库存积压。
5. 基于数据的改进:建立有效的数据收集与分析机制,通过实时监控和数据反馈,持续改进生产流程和产品质量。
五、案例分析:精益生产在某电子制造公司的应用某电子制造公司在实施精益生产方案后,取得了显著的成效。
首先,通过价值流程分析,公司确定了各个环节中的浪费因素,例如生产计划不准确和生产线停机时间较长。
然后,公司采取了一系列措施,包括改进生产计划系统,提高生产线设备的稳定性和可维护性,以及加强员工培训和激励措施。
这些改进措施的实施使得产品生产周期缩短了20%,生产效率提高了30%。
精益生产十大防错原理

精益生产十大防错原理早在三十年前,精益生产出现在我们的生活中,它推动了企业朝精益生产模式发展,把无效的费用和工作减少,保证高质量产品及时准确地提供服务。
精益生产有十大防错原则,在企业对精益生产进行实践中,其中的防错原则起到了重要作用。
第一,安全第一,应遵循安全认证的要求。
企业应保证设备的安全,只有在认证后的安全状态下才能进行生产,以确保操作安全,减少可能出现的危险和损失。
第二,事前计划,应在生产前进行计划,考虑设备和人员的分配,以及原料的使用,有效地预防错误和风险,提高生产效率。
第三,预防式的管理,应坚持以预防的方式来管理,确保质量,降低报废率和废品,实现精益生产的目标。
第四,细节设计,要进行细节的设计,准确的信息的分析,对产品质量的控制,以及生产过程的准确控制。
第五,持续改善,要不断改进生产过程,实现质量管理,减少费用和时间,提高生产效率和质量,实现持续发展。
第六,精益模式,要使用精益模式,根据客户需求进行产品设计,提高产品质量,延长生产周期,提高客户满意度。
第七,技术设施,必须认真设计机械和电气设施,确保精准的技术指标,提供质量安全的产品服务。
第八,新技术,要不断引入新技术以提高生产效率和质量,保证产品的可靠性和可靠性,以满足客户的需求。
第九,系统流程,要实现系统化的流程,针对生产环节和生产过程,制定标准化的规则,并利用信息技术来进行控制,确保生产过程稳定、可靠。
最后,必须建立质量管理体系,确保质量的准确性和可靠性。
要建立完善的质量保证体系,把质量管理作为一项长期的立足点,重视质量的检验和改善,确保产品质量的稳定。
精益生产的十大防错原则在企业实施精益生产时起到关键作用。
它不仅可以运用安全、有效地发挥作用,而且还可以确保产品质量的稳定,有效地满足客户需求。
企业在实施精益生产时应该认真贯彻这十大防错原则,以保证产品质量,争取更完美的实践成果。
精益生产管理手册
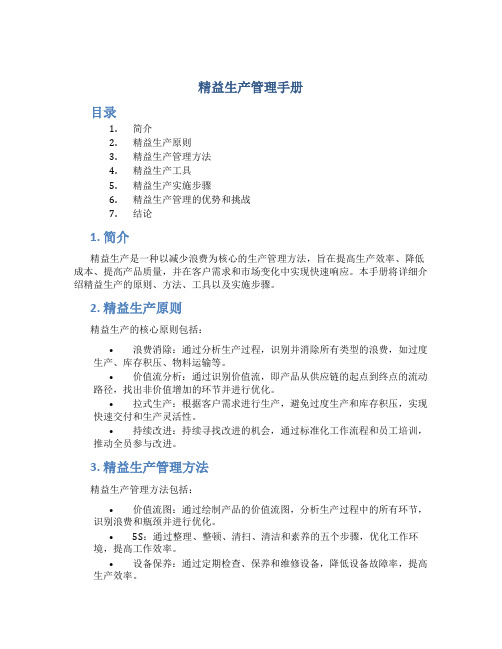
精益生产管理手册目录1.简介2.精益生产原则3.精益生产管理方法4.精益生产工具5.精益生产实施步骤6.精益生产管理的优势和挑战7.结论1. 简介精益生产是一种以减少浪费为核心的生产管理方法,旨在提高生产效率、降低成本、提高产品质量,并在客户需求和市场变化中实现快速响应。
本手册将详细介绍精益生产的原则、方法、工具以及实施步骤。
2. 精益生产原则精益生产的核心原则包括:•浪费消除:通过分析生产过程,识别并消除所有类型的浪费,如过度生产、库存积压、物料运输等。
•价值流分析:通过识别价值流,即产品从供应链的起点到终点的流动路径,找出非价值增加的环节并进行优化。
•拉式生产:根据客户需求进行生产,避免过度生产和库存积压,实现快速交付和生产灵活性。
•持续改进:持续寻找改进的机会,通过标准化工作流程和员工培训,推动全员参与改进。
3. 精益生产管理方法精益生产管理方法包括:•价值流图:通过绘制产品的价值流图,分析生产过程中的所有环节,识别浪费和瓶颈并进行优化。
•5S:通过整理、整顿、清扫、清洁和素养的五个步骤,优化工作环境,提高工作效率。
•设备保养:通过定期检查、保养和维修设备,降低设备故障率,提高生产效率。
•产能平衡:根据市场需求和生产能力,调整生产线的平衡,提高生产效率和产品质量。
•Just-In-Time (JIT) 生产:根据客户需求精确控制物料、零部件和成品的库存,避免过度生产和库存积压。
•持续改进:通过持续的改进活动,提高工作流程、生产效率和产品质量。
4. 精益生产工具精益生产使用多种工具来支持管理和改进活动,包括:•流程图:用于描述生产过程中的各个步骤和环节。
•Gantt 图:用于规划和跟踪项目进度。
•帕累托图:用于识别主要问题和优先解决。
•5W1H 分析:通过回答问题谁、何时、何地、为什么、如何和多少来分析问题的根本原因。
•根本原因分析:通过追溯问题的根本原因,找到解决问题的有效措施。
•PDCA 循环:通过计划、执行、检查和行动的循环,持续改进工作流程和活动。
精益生产十大原则
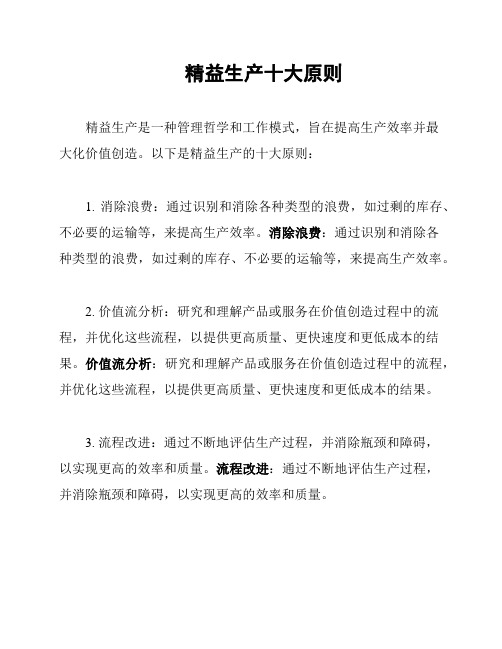
精益生产十大原则精益生产是一种管理哲学和工作模式,旨在提高生产效率并最大化价值创造。
以下是精益生产的十大原则:1. 消除浪费:通过识别和消除各种类型的浪费,如过剩的库存、不必要的运输等,来提高生产效率。
消除浪费:通过识别和消除各种类型的浪费,如过剩的库存、不必要的运输等,来提高生产效率。
2. 价值流分析:研究和理解产品或服务在价值创造过程中的流程,并优化这些流程,以提供更高质量、更快速度和更低成本的结果。
价值流分析:研究和理解产品或服务在价值创造过程中的流程,并优化这些流程,以提供更高质量、更快速度和更低成本的结果。
3. 流程改进:通过不断地评估生产过程,并消除瓶颈和障碍,以实现更高的效率和质量。
流程改进:通过不断地评估生产过程,并消除瓶颈和障碍,以实现更高的效率和质量。
4. 标准化工作:确保每个工作岗位都有明确的工作标准和操作方法,以提高工作质量和一致性。
标准化工作:确保每个工作岗位都有明确的工作标准和操作方法,以提高工作质量和一致性。
5. 持续改进:通过鼓励员工提出改进建议并实施这些建议,不断地改进生产过程和工作方法。
持续改进:通过鼓励员工提出改进建议并实施这些建议,不断地改进生产过程和工作方法。
6. 团队合作:建立一个积极的团队合作环境,鼓励员工之间的互相支持和协作。
团队合作:建立一个积极的团队合作环境,鼓励员工之间的互相支持和协作。
7. 可视化管理:使用可视化工具和技术,如看板、图表等,帮助员工和管理层更好地了解生产状况和问题,并及时做出调整。
可视化管理:使用可视化工具和技术,如看板、图表等,帮助员工和管理层更好地了解生产状况和问题,并及时做出调整。
8. 质量优先:将质量放在首位,确保产品和服务符合客户的期望,并尽量减少缺陷和错误。
质量优先:将质量放在首位,确保产品和服务符合客户的期望,并尽量减少缺陷和错误。
9. 减少变动:尽量避免频繁的变动和调整,以保持生产过程的稳定性和可控性。
减少变动:尽量避免频繁的变动和调整,以保持生产过程的稳定性和可控性。
精益生产10个原则
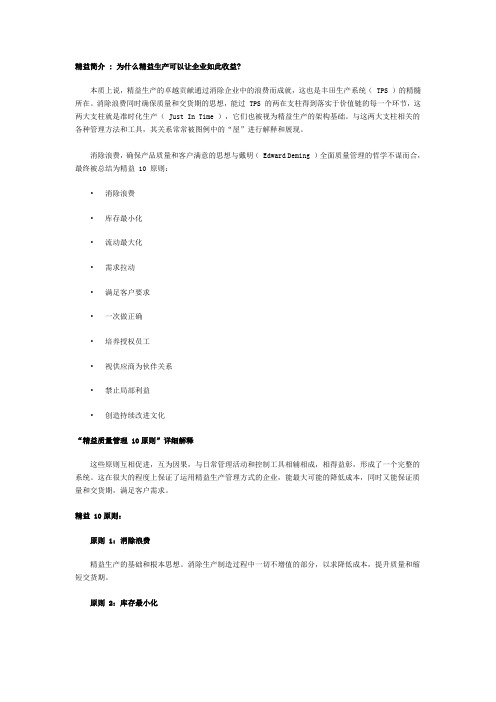
精益简介 : 为什么精益生产可以让企业如此收益?本质上说,精益生产的卓越贡献通过消除企业中的浪费而成就,这也是丰田生产系统( TPS )的精髓所在。
消除浪费同时确保质量和交货期的思想,能过 TPS 的两在支柱得到落实于价值链的每一个环节,这两大支柱就是准时化生产( Just In Time ),它们也被视为精益生产的架构基础。
与这两大支柱相关的各种管理方法和工具,其关系常常被图例中的“屋”进行解释和展现。
消除浪费,确保产品质量和客户满意的思想与戴明( Edward Deming )全面质量管理的哲学不谋而合,最终被总结为精益 10 原则:•消除浪费•库存最小化•流动最大化•需求拉动•满足客户要求•一次做正确•培养授权员工•视供应商为伙伴关系•禁止局部利益•创造持续改进文化“精益质量管理 10原则”详细解释这些原则互相促进,互为因果,与日常管理活动和控制工具相辅相成,相得益彰,形成了一个完整的系统。
这在很大的程度上保证了运用精益生产管理方式的企业,能最大可能的降低成本,同时又能保证质量和交货期,满足客户需求。
精益 10原则:原则 1:消除浪费精益生产的基础和根本思想。
消除生产制造过程中一切不增值的部分,以求降低成本,提升质量和缩短交货期。
原则 2:库存最小化库存是 7 大浪费之一。
库存占用资金和场地,并掩盖了企业经营管理中的大量问题,精益生通过不断降低库存,暴露问题,解决问题后再降低库存的循环不断降低库存量。
原则 3:流动最大化让物流和加工过程快速流动起来,以最短的生产周期应对市场变化。
原则 4:需求拉动不再依靠预测来生产,而根据客户的需求来生产,尽可能最迟将客户的需求导入生产环节以提升准确性。
当客户需求的时候才生产。
原则 5:满足客户要求了解客户的正真需求,满足顾客在质量、交货、服务、价格等方面的需求。
原则 6:一次做正确生产的每个环节确保提供的都是合格品,每一步骤都作工确,而不是最后校正。
在制造过程中坚持“不制造、不传递、不接受”不合格品的“三不”原则。
精益生产的定义
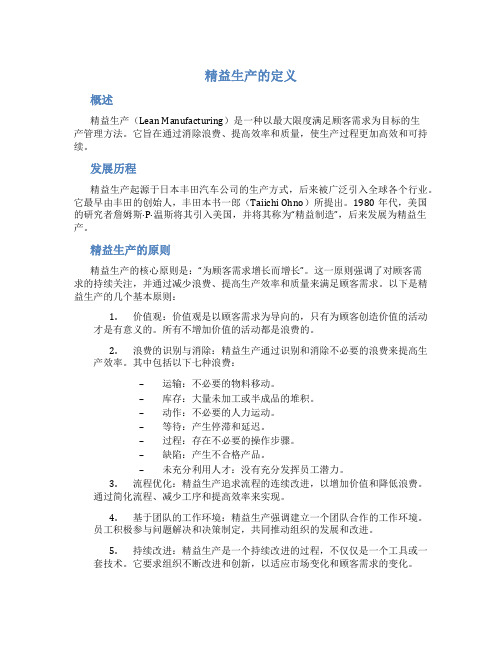
精益生产的定义概述精益生产(Lean Manufacturing)是一种以最大限度满足顾客需求为目标的生产管理方法。
它旨在通过消除浪费、提高效率和质量,使生产过程更加高效和可持续。
发展历程精益生产起源于日本丰田汽车公司的生产方式,后来被广泛引入全球各个行业。
它最早由丰田的创始人,丰田本书一郎(Taiichi Ohno)所提出。
1980年代,美国的研究者詹姆斯·P·温斯将其引入美国,并将其称为“精益制造”,后来发展为精益生产。
精益生产的原则精益生产的核心原则是:“为顾客需求增长而增长”。
这一原则强调了对顾客需求的持续关注,并通过减少浪费、提高生产效率和质量来满足顾客需求。
以下是精益生产的几个基本原则:1.价值观:价值观是以顾客需求为导向的,只有为顾客创造价值的活动才是有意义的。
所有不增加价值的活动都是浪费的。
2.浪费的识别与消除:精益生产通过识别和消除不必要的浪费来提高生产效率。
其中包括以下七种浪费:–运输:不必要的物料移动。
–库存:大量未加工或半成品的堆积。
–动作:不必要的人力运动。
–等待:产生停滞和延迟。
–过程:存在不必要的操作步骤。
–缺陷:产生不合格产品。
–未充分利用人才:没有充分发挥员工潜力。
3.流程优化:精益生产追求流程的连续改进,以增加价值和降低浪费。
通过简化流程、减少工序和提高效率来实现。
4.基于团队的工作环境:精益生产强调建立一个团队合作的工作环境。
员工积极参与问题解决和决策制定,共同推动组织的发展和改进。
5.持续改进:精益生产是一个持续改进的过程,不仅仅是一个工具或一套技术。
它要求组织不断改进和创新,以适应市场变化和顾客需求的变化。
实施精益生产的关键步骤要成功实施精益生产,组织需要采取一系列关键步骤:1.指定目标:设定明确的目标和指标,以推动改进工作的进行。
这些目标应该与顾客需求和组织的战略一致。
2.流程分析:对组织的生产流程进行详细分析,识别出存在的浪费和瓶颈,并确定改进的重点。
精益生产与精益思想

精益生产与精益思想简介精益生产与精益思想是一种管理理念和方法论,旨在通过优化生产过程,减少浪费,提高效率和质量。
这一概念最早由日本丰田汽车公司引入,并在世界范围内得到推广和应用。
随着全球制造业的发展,越来越多的企业开始关注精益生产和精益思想,以提升竞争力。
精益生产的原则精益生产的核心原则是“以价值为导向,消除浪费”。
以下是精益生产的几个重要原则:1.价值流:精益生产强调产品或服务的价值流动,并通过分析价值流,消除不必要的环节和浪费。
2.价值流映射:通过绘制价值流地图,将产品或服务的价值流程可视化,便于理解和分析。
3.流程稳定:精益生产追求稳定的生产流程,稳定的流程可以提高生产效率和质量。
4.拉动式生产:精益生产鼓励以客户需求为导向进行生产,避免过度生产和库存积压。
5.零缺陷:精益生产追求零缺陷的产品和服务,通过改进生产过程和培养员工的质量意识,实现质量的持续改进。
精益思想的应用精益思想不仅适用于生产领域,也可以在其他领域得到应用,如服务业、项目管理等。
以下是精益思想在不同领域的应用:1.精益服务:在服务业中,精益思想可以用于优化服务流程,减少等待时间和不必要的操作,提高服务效率和顾客满意度。
2.精益项目管理:在项目管理中,精益思想可以帮助团队识别并消除项目中的浪费,提高项目的执行效率和交付质量。
3.精益物流:在物流领域,精益思想可以应用于供应链管理,通过优化物流流程,减少库存和运输时间,降低成本,提高响应能力。
4.精益办公:在办公环境中,精益思想可以应用于提高效率和减少浪费。
例如,通过优化工作流程,减少会议时间和不必要的工作步骤,提高工作效率。
精益生产的工具和方法精益生产使用了许多工具和方法来辅助实施和改进。
以下是一些常用的精益生产工具和方法:1.5S整理法:通过整理、整顿、清扫、清洁和素养,创建整洁的工作环境,提高工作效率和质量。
2.Kanban看板系统:使用看板系统来控制生产流程,提高生产的可视性和管理效率。
【推荐下载】精益生产持续改善的十大原则介绍
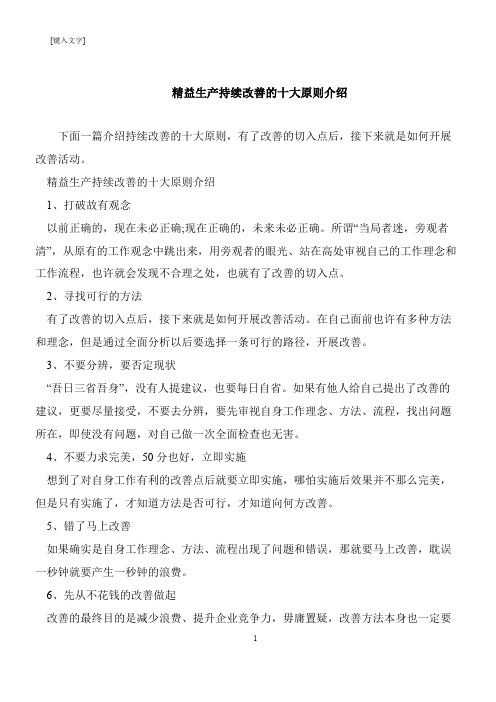
[键入文字]
精益生产持续改善的十大原则介绍
下面一篇介绍持续改善的十大原则,有了改善的切入点后,接下来就是如何开展改善活动。
精益生产持续改善的十大原则介绍
1、打破故有观念
以前正确的,现在未必正确;现在正确的,未来未必正确。
所谓“当局者迷,旁观者清”,从原有的工作观念中跳出来,用旁观者的眼光、站在高处审视自己的工作理念和工作流程,也许就会发现不合理之处,也就有了改善的切入点。
2、寻找可行的方法
有了改善的切入点后,接下来就是如何开展改善活动。
在自己面前也许有多种方法和理念,但是通过全面分析以后要选择一条可行的路径,开展改善。
3、不要分辨,要否定现状
“吾日三省吾身”,没有人提建议,也要每日自省。
如果有他人给自己提出了改善的建议,更要尽量接受,不要去分辨,要先审视自身工作理念、方法、流程,找出问题所在,即使没有问题,对自己做一次全面检查也无害。
4、不要力求完美,50分也好,立即实施
想到了对自身工作有利的改善点后就要立即实施,哪怕实施后效果并不那么完美,但是只有实施了,才知道方法是否可行,才知道向何方改善。
5、错了马上改善
如果确实是自身工作理念、方法、流程出现了问题和错误,那就要马上改善,耽误一秒钟就要产生一秒钟的浪费。
6、先从不花钱的改善做起
改善的最终目的是减少浪费、提升企业竞争力,毋庸置疑,改善方法本身也一定要
1。
精益生产的定义

精益生产的定义什么是精益生产?精益生产是一种管理理念和生产方法,旨在通过最大程度地减少资源浪费,以实现高效生产和提供价值给客户。
精益生产的核心原则是通过不断改善流程,消除浪费,提高生产效率和质量。
这一理念最初起源于丰田汽车公司的生产体系,后来被广泛应用于其他行业和领域。
精益生产的目标精益生产的主要目标是实现以下几点:1.提高生产效率:通过消除浪费,优化流程,提高生产效率和生产率。
2.降低成本:通过减少废品和不必要的生产成本,实现成本的最小化。
3.提高产品质量:通过改进生产过程和流程控制,提高产品质量和稳定性。
4.提高客户满意度:通过及时交付高质量的产品,提高客户满意度和忠诚度。
精益生产的原则精益生产遵循一些核心原则,其中包括:1.价值:专注于为客户创造价值,只集中精力和资源在对客户有意义的活动上。
2.价流:优化价值流动,消除所有形式的浪费,确保产品/服务按需求流动。
3.拉动:基于客户需求拉动生产,避免过度生产和库存积压。
4.流程改进:不断改进生产过程,强调团队合作和持续学习。
5.标准化:建立标准化工作流程和操作规程,确保质量和稳定性。
精益生产的实践精益生产的实践方法包括:1.价值流分析:分析整个价值流,识别不必要的步骤和浪费。
2.5S整理法:通过整理、整顿、清扫、清洁、标准化等步骤,改善工作环境和效率。
3.持续改进:建立改进文化和机制,鼓励员工提出改进建议和参与改进活动。
4.精益供应链管理:与供应商建立紧密合作关系,实现供应链的高效协同和配合。
精益生产的应用范围精益生产不仅适用于制造业,也适用于服务业和其他领域。
在制造业中,精益生产可以帮助企业提高生产效率、降低成本、改善质量;在服务业中,精益生产可以帮助企业提高服务效率、提升客户体验、降低服务成本。
总结精益生产是一种重要的管理理念和生产方法,其核心目标是通过最大程度地减少浪费,实现高效生产和提供价值给客户。
精益生产的原则和实践方法可以帮助企业提高生产效率、降低成本、改善质量,从而获得持续竞争优势。
精益生产方式JIT学习

精益生产方式JIT学习简介精益生产(Just-In-Time,JIT)是一种高效的生产管理方式,其最大的特点是在工作流程中实现无浪费和按需生产。
JIT管理方法的核心是避免库存的积压,使得生产过程能够实现高效的物流流转和精确的生产规划。
本文将介绍精益生产方式JIT的原理、特点和实施步骤,旨在帮助读者了解和应用这一管理方法。
精益生产的原理精益生产的原理是通过精确的生产规划和及时的物流流转,使得产品按需生产、按需供应,并且在整个生产过程中尽量减少浪费。
精益生产采用了以下几个重要原则:1.零库存原则:JIT管理方法的核心是尽量避免库存的积压。
通过减少库存数量,可以降低库存成本以及库存导致的浪费。
2.小批量生产原则:JIT生产方式强调按需生产,避免大规模的批量生产。
通过小批量生产,可以减少库存积压,提高生产灵活性和响应速度。
3.平衡生产原则:JIT管理方法追求工作流程的平衡,即避免在生产过程中出现瓶颈现象。
通过平衡各个工作环节,可以降低生产过程中的等待和停顿,并提高生产效率。
4.追求零缺陷原则:JIT生产方式注重质量管理,追求零缺陷的生产过程。
通过严格的质量控制,可以减少不良品率,提高产品质量。
精益生产的特点精益生产方式JIT有以下几个特点:1.短交付周期:JIT生产方式强调按需生产,使得产品能够及时交付给客户。
通过缩短交付周期,可以提高客户满意度。
2.降低库存成本:JIT管理方法避免库存的积压,减少库存数量,从而降低库存成本。
3.精确生产规划:JIT生产方式通过精确的生产规划,使得生产过程高效有序。
可以提前预测客户需求,合理安排生产计划。
4.提高生产效率:JIT管理方法追求工作流程的平衡,避免瓶颈现象,从而提高生产效率。
5.强调质量管理:JIT生产方式注重质量管理,追求零缺陷的生产过程。
通过提高产品质量,减少不良品率。
精益生产的实施步骤要实施精益生产方式JIT,可以按照以下步骤进行:1.优化供应链:通过优化供应链,确保原材料的及时供应、产品的及时交付。
精益生产原则

精益生产原则精益生产是一种管理方法,旨在通过减少浪费和提高效率,实现生产过程的优化和改进。
以下是一些精益生产的原则。
1. 价值流分析:了解产品或服务在整个价值流中的流程,从而识别出哪些步骤是为顾客创造价值的,哪些是浪费的。
2. 一件流:通过减少库存和流程中的等待时间,实现产品或服务从开始到结束的流畅流动。
此原则帮助消除瓶颈和阻碍生产效率的因素。
3. 按需生产:根据客户需求进行生产,避免生产过剩和库存积压的问题。
这可以通过实施精准的订单预测和及时的供应链管理来实现。
4. 持续改进:不断寻求改进的机会,并在实践中测试新的方法和技术。
持续改进是精益生产的核心原则,它要求员工参与到改进过程中,并提供他们的想法和建议。
5. 人员发展:提供培训和发展机会,使员工能够掌握所需的技能和知识,以更好地支持精益生产的实施。
这包括培训员工使用新的工具和技术,以及培养团队合作和问题解决能力。
6. 质量控制:确保产品或服务的质量符合顾客的要求和期望。
这可以通过实施严格的质量控制流程和采用持续改进的方法来实现。
7. 参与式管理:鼓励员工参与到决策和问题解决过程中。
精益生产认为员工是组织中最重要的资源,他们应该被赋予责任和自主权,以推动改进和增加价值。
通过遵循以上原则,组织可以实现生产过程的精益化,提高效率、降低成本、提供高质量的产品和服务。
精益生产不仅适用于制造业,也可以应用于服务行业和其他领域,以提升组织的竞争力和可持续发展。
精益生产原则是由丰田汽车公司首先提出,后来被广泛应用于制造业和服务业。
它的核心思想是通过消除浪费和优化价值流程,提高生产效率和质量,以实现持续改进和客户满意度。
首先,精益生产强调进行价值流分析。
这意味着通过对生产流程的详细了解,找出哪些步骤创造了真正的价值,哪些步骤是浪费的。
通过识别和减少浪费,企业可以改善效率并降低成本。
这种分析可以从供应链的开始直到产品交付的整个过程中进行。
其次,精益生产强调"一件流"的理念。
精益生产体系与运营管理
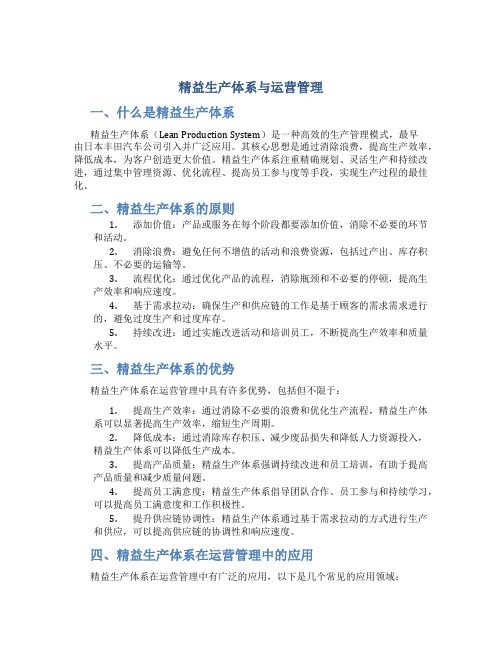
精益生产体系与运营管理一、什么是精益生产体系精益生产体系(Lean Production System)是一种高效的生产管理模式,最早由日本丰田汽车公司引入并广泛应用。
其核心思想是通过消除浪费,提高生产效率,降低成本,为客户创造更大价值。
精益生产体系注重精确规划、灵活生产和持续改进,通过集中管理资源、优化流程、提高员工参与度等手段,实现生产过程的最佳化。
二、精益生产体系的原则1.添加价值:产品或服务在每个阶段都要添加价值,消除不必要的环节和活动。
2.消除浪费:避免任何不增值的活动和浪费资源,包括过产出、库存积压、不必要的运输等。
3.流程优化:通过优化产品的流程,消除瓶颈和不必要的停顿,提高生产效率和响应速度。
4.基于需求拉动:确保生产和供应链的工作是基于顾客的需求需求进行的,避免过度生产和过度库存。
5.持续改进:通过实施改进活动和培训员工,不断提高生产效率和质量水平。
三、精益生产体系的优势精益生产体系在运营管理中具有许多优势,包括但不限于:1.提高生产效率:通过消除不必要的浪费和优化生产流程,精益生产体系可以显著提高生产效率,缩短生产周期。
2.降低成本:通过消除库存积压、减少废品损失和降低人力资源投入,精益生产体系可以降低生产成本。
3.提高产品质量:精益生产体系强调持续改进和员工培训,有助于提高产品质量和减少质量问题。
4.提高员工满意度:精益生产体系倡导团队合作、员工参与和持续学习,可以提高员工满意度和工作积极性。
5.提升供应链协调性:精益生产体系通过基于需求拉动的方式进行生产和供应,可以提高供应链的协调性和响应速度。
四、精益生产体系在运营管理中的应用精益生产体系在运营管理中有广泛的应用,以下是几个常见的应用领域:1.生产计划与调度:基于精益生产体系的原则,制定合理的生产计划并进行调度,确保生产任务的顺利完成。
2.库存管理:通过精益生产体系的原则,优化库存管理,避免库存积压和过度库存,降低库存成本。
JIT精益生产的基本知识

JIT精益生产的基本知识一、什么是JIT精益生产?JIT(Just-in-Time)精益生产是一种生产管理方法,旨在实现以最少的库存、最小的费用和最高的效率来满足客户需求。
其核心思想是在生产的每一步都不浪费时间、劳力和资源,以实现高效的生产流程。
二、JIT精益生产的原理1.零库存原则:JIT强调减少库存量,只在需要的时候才进行生产,有效降低库存成本和过剩库存的风险。
2.及时生产:产品在需要的时候才开始生产,以减少库存积压和生产周期,提高生产效率。
3.拉动生产:JIT通过“拉动式生产”,以客户需求为导向,根据实际订单推动生产,避免过度生产和浪费。
4.持续改进:JIT倡导持续改进和优化生产流程,促进团队协作和精益生产文化的建设。
三、JIT精益生产的优势1.降低成本:减少库存和废料,提高生产效率,降低生产成本。
2.提高质量:通过减少浪费和优化生产流程,提高产品质量和客户满意度。
3.提升交付速度:JIT生产方式能够更快速地响应客户需求,提高交付速度和服务水平。
4.增强竞争力:JIT可以帮助企业提升竞争力,降低生产周期,适应市场变化,实现持续发展。
四、如何实施JIT精益生产1.建立稳定的供应链:与供应商建立稳定的合作关系,确保物料供应的稳定和及时。
2.实施流程再造:对生产流程进行优化和改进,消除浪费,提高生产效率。
3.培训员工:向员工提供JIT精益生产的培训,增强他们的生产技能和质量意识。
4.持续改进:制定并实施持续改进计划,对生产流程和产品质量进行不断改进。
五、JIT精益生产的案例分析1. 丰田汽车丰田汽车采用JIT精益生产方式,通过精细的供应链管理和及时生产,实现了高效的制造和交付,提高了产品质量和客户满意度。
2. 联想集团联想集团在生产管理中推行JIT精益生产,通过优化生产流程和降低库存,提高了生产效率和竞争力,实现了持续发展。
六、结语JIT精益生产是一种重要的生产管理方法,对企业提高效率、降低成本、提高竞争力具有重要意义。
精益生产五大原则
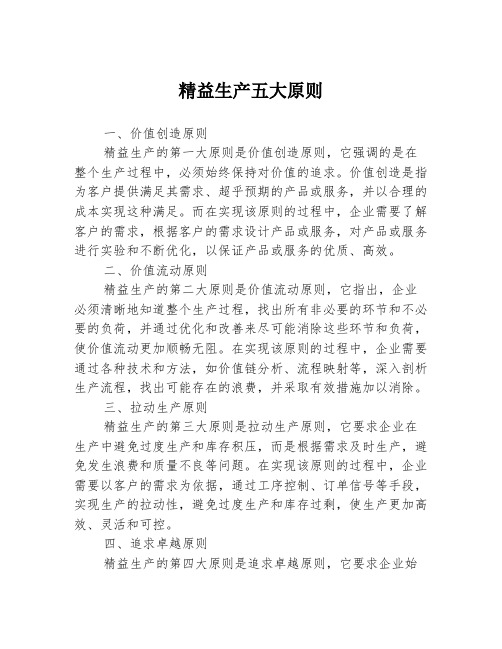
精益生产五大原则一、价值创造原则精益生产的第一大原则是价值创造原则,它强调的是在整个生产过程中,必须始终保持对价值的追求。
价值创造是指为客户提供满足其需求、超乎预期的产品或服务,并以合理的成本实现这种满足。
而在实现该原则的过程中,企业需要了解客户的需求,根据客户的需求设计产品或服务,对产品或服务进行实验和不断优化,以保证产品或服务的优质、高效。
二、价值流动原则精益生产的第二大原则是价值流动原则,它指出,企业必须清晰地知道整个生产过程,找出所有非必要的环节和不必要的负荷,并通过优化和改善来尽可能消除这些环节和负荷,使价值流动更加顺畅无阻。
在实现该原则的过程中,企业需要通过各种技术和方法,如价值链分析、流程映射等,深入剖析生产流程,找出可能存在的浪费,并采取有效措施加以消除。
三、拉动生产原则精益生产的第三大原则是拉动生产原则,它要求企业在生产中避免过度生产和库存积压,而是根据需求及时生产,避免发生浪费和质量不良等问题。
在实现该原则的过程中,企业需要以客户的需求为依据,通过工序控制、订单信号等手段,实现生产的拉动性,避免过度生产和库存过剩,使生产更加高效、灵活和可控。
四、追求卓越原则精益生产的第四大原则是追求卓越原则,它要求企业始终追求卓越,不断提升产品或服务的质量和性能,以赢得市场和客户的认可和信任。
在实现该原则的过程中,企业需要采取各种措施,如实施全员培训、持续改善、创新等,不断提高生产效率和质量水平,保证产品或服务的卓越品质。
五、持续改善原则精益生产的第五大原则是持续改善原则,它要求企业在生产过程中持续改善,不断寻求优化和提高生产效率的方法和途径。
在实现该原则的过程中,企业需要通过持续测量、监控和分析生产过程,找出各种可能存在的问题和瓶颈,并采取有效的措施改善和优化。
同时,在实施持续改善的过程中,企业需要注重员工的参与和推广,建立改善文化和管理体系。
总体而言,精益生产的五大原则是企业在生产过程中必须遵循的基本原则,它们的实施可以帮助企业不断提高生产效率和质量水平,保证产品或服务的卓越品质,提升市场竞争力。
精益生产的12条原则

精益生产的12条原则精益生产(Lean Production)是一种追求高效率、高品质和低成本的生产管理方法,其主要目标是通过消除浪费、提高工作效率和质量,为客户提供更好的产品和服务。
精益生产的理念由丰田汽车公司于20世纪80年代提出,并逐渐在全球范围内得到广泛应用。
1.客户价值:只提供符合客户期望的价值,并尽可能减少浪费。
这意味着产品和服务必须满足客户需求,并且不进行过度生产以避免存货积压。
2.流程优化:通过研究和改进生产流程,确保所有步骤和操作都能够最大限度地减少浪费和非价值增加的活动。
优化生产流程可以提高工作效率和质量。
3.持续改进:建立一个持续改进的文化,使员工不断寻找和解决问题,并优化工作流程。
这需要从高层管理到基层员工都参与进来,鼓励他们提出改进意见和建议。
4.精益文化:培养一种精益的企业文化,激发员工的创造力和积极性。
这可以通过奖励和认可优秀的员工以及提供培训和发展机会来实现。
5.标准化工作:制定规范和标准,确保所有员工按照同样的方法和标准进行工作,以减少差异性和提高质量。
标准化工作可以降低变异性和错误率。
6.小步骤改进:推行小步骤改进方法,逐步提升生产效率和质量。
这种方式可以降低改变的风险,并使改进过程更加平滑。
7.看板管理:使用看板和可视化管理方法来跟踪和管理生产过程。
这可以提供实时的信息,便于问题及时发现并进行调整。
8.应对问题:培养应对问题的能力,及时解决和处理各种生产问题,以保证生产流程的顺利进行。
这需要建立相应的反馈机制和应急预案。
9.灵活生产:根据市场需求和客户要求,实现生产过程的灵活调整。
这可以通过灵活的布局、灵活的人员安排和快速更换设备来实现。
10.停滞生产:在生产过程中实施停滞生产策略,以避免过度生产和存货积压。
停滞生产可以根据需求进行灵活调整,避免资源浪费。
11.合作共赢:与供应商和合作伙伴建立长期合作关系,共同追求共赢。
通过合作伙伴关系,可以实现资源共享、风险分担和相互支持。
精益生产12原则

精益生产12原则精益生产(Lean Manufacturing)是一种以减少浪费为核心的生产管理方法,通过从流程中剔除无价值的环节、减少无谓的工作和提高效率,以实现降低成本、提高质量和缩短交货周期的目标。
精益生产自从上世纪80年代开始兴起以来,在世界各地的制造业中得到广泛运用,并陆续发展出了许多实践方法和工具。
以下是精益生产的十二个原则:1.1价值流:价值流是指产品或服务在生产过程中经历的所有流程、活动和环节。
借助价值流图,企业可以清晰地了解到价值流中的各个环节以及其价值贡献程度,从而对生产过程进行优化。
2.流程化:流程化是指通过将工作流程划分为多个简单、标准化、连续流动的步骤,以最大程度地消除时间浪费和资源浪费,提高生产效率。
3.拉动生产:拉动生产是指根据实际需求,按需生产,而不是按计划或者按库存量进行生产。
企业应该在接收订单后再进行生产,以确保产品的交付及时。
4.零库存:零库存是指通过减少库存量来减少浪费。
企业应该尽量减少在生产和供应链过程中的库存,以避免过度投资、浪费资源和增加生产风险。
5.标准化工作:标准化工作是指通过制定标准化的工作流程、工作标准和作业指导书,确保工作可以按照预定的要求进行,减少误差和浪费。
6.设备可靠性:设备可靠性是指通过有效的维护和保养,确保生产设备的稳定运行,减少设备故障和停机时间。
7.多技能员工:多技能员工是指员工具备多种技能和能力,能够灵活应对不同的工作任务,提高生产的灵活性和效率。
8.质量控制:质量控制是指通过建立合理的质量控制体系,减少产品缺陷和废品产生。
9.持续改进:持续改进是一种管理理念,即持续地对生产过程和产品质量进行改进,以增加价值、提高效率和降低成本。
10.全员参与:全员参与是指鼓励和培养所有员工的积极参与和主动性,以推动精益生产的落地和推广。
11.合作伙伴关系:合作伙伴关系是指与供应商、客户和其他利益相关者建立良好的合作关系,共同追求利益最大化。
精益生产管理的十四个基本原则

精益生产管理的十四个基本原则一、管理决策以长期理念为基础,即使因此牺牲短期财务目标也在所不惜。
企业要有一个优先于任何短期决策的目的理念,使整个企业的运作与发展能配合着朝向这个比赚钱更重要的共同目的一一长期稳固的发展。
长期理念和历史地位的起始点应该是为客户、为社会、为企业的收益创造价值。
精益生产管理要求要每一个员工都有责任。
二、建立无间断流程以使问题浮现要求重新设计流程,使流程不仅仅是工作过程的描述。
一定要建立快速输送材料与信息的流程,使流程与员工的行为动作紧密地联结在一起。
要使整个企业文化重视流程,这是促成真正的持续改进流程及员工发展的关键。
三、实施拉式生产制度以避免生产过剩在你生产流程下游的客户有需求的时候,供应给他们正确数量的正确东西。
使在制品及库存减至最少,每项产品只维持少量存货,根据向客户实际交付的数量,经常补充存货。
按客户的需求每天进行调整在制品和存货量,而不是依靠计算机的时间表与系统来追踪已经成为浪费的存货。
四、使工作负荷水准稳定(生产均衡化),工作应该象龟兔赛跑中的乌龟一样杜绝浪费只是实现精益生产所必须做的工作的1/3o避免员工与设备的负荷过重,以避免生产安排的不均匀,也同等重要。
尽量使所有制造与服务流程的工作负荷平均化,以取代大多数公司实行的批量生产方法中经常启动、停止、启动的做法。
五、建立立即暂停以解决问题,从一开始就重视品质管理的文化为顾客提供的品质决定着你的定价。
你要想收益高,首先需要品质好。
为了提高品质,应该使用所有能够确保产品品质的现代方法。
想一想,我们的方法是不是能够确保产品品质?使生产设备具有发现问题及一发现问题就停止生产的能力。
在企业中设立支持快速解决问题的制度和监督检测。
在企业文化中融入发生问题时立即暂停或减缓速度、就地改进质量以提升长期生产力的概念。
在工作场所中的任何地方都使用稳定、可重复的方法,以维持流程的可预测性、规律的运作时间,以及规律的产出。
到一定时间时, 应该汲取对流程的累积学习心得,把“现在”的最佳实务进行标准化,让员工对于标准提出有创意的改进意见,把这些见解纳入精益生产管理新标准中。
- 1、下载文档前请自行甄别文档内容的完整性,平台不提供额外的编辑、内容补充、找答案等附加服务。
- 2、"仅部分预览"的文档,不可在线预览部分如存在完整性等问题,可反馈申请退款(可完整预览的文档不适用该条件!)。
- 3、如文档侵犯您的权益,请联系客服反馈,我们会尽快为您处理(人工客服工作时间:9:00-18:30)。
精益简介 : 为什么精益生产可以让企业如此收益?
本质上说,精益生产的卓越贡献通过消除企业中的浪费而成就,这也是丰田生产系统( TPS )的精髓所在。
消除浪费同时确保质量和交货期的思想,能过 TPS 的两在支柱得到落实于价值链的每一个环节,这两大支柱就是准时化生产( Just In Time ),它们也被视为精益生产的架构基础。
与这两大支柱相关的各种管理方法和工具,其关系常常被图例中的“屋”进行解释和展现。
消除浪费,确保产品质量和客户满意的思想与戴明( Edward Deming )全面质量管理的哲学不谋而合,最终被总结为精益 10 原则:
•消除浪费
•库存最小化
•流动最大化
•需求拉动
•满足客户要求
•一次做正确
•培养授权员工
•视供应商为伙伴关系
•禁止局部利益
•创造持续改进文化
“精益质量管理 10原则”详细解释
这些原则互相促进,互为因果,与日常管理活动和控制工具相辅相成,相得益彰,形成了一个完整的系统。
这在很大的程度上保证了运用精益生产管理方式的企业,能最大可能的降低成本,同时又能保证质量和交货期,满足客户需求。
精益 10原则:
原则 1:消除浪费
精益生产的基础和根本思想。
消除生产制造过程中一切不增值的部分,以求降低成本,提升质量和缩短交货期。
原则 2:库存最小化
库存是 7 大浪费之一。
库存占用资金和场地,并掩盖了企业经营管理中的大量问题,精益生通过不断降低库存,暴露问题,解决问题后再降低库存的循环不断降低库存量。
原则 3:流动最大化
让物流和加工过程快速流动起来,以最短的生产周期应对市场变化。
原则 4:需求拉动
不再依靠预测来生产,而根据客户的需求来生产,尽可能最迟将客户的需求导入生产环节以提升准确性。
当客户需求的时候才生产。
原则 5:满足客户要求
了解客户的正真需求,满足顾客在质量、交货、服务、价格等方面的需求。
原则 6:一次做正确
生产的每个环节确保提供的都是合格品,每一步骤都作工确,而不是最后校正。
在制造过程中坚持“不制造、不传递、不接受”不合格品的“三不”原则。
原则 7:培养授权员工
全面培训员工解决问题的技巧和方法,充分授权给有能力的员工,全员参与问题解决。
原则 8:禁止局部利益
打破条块分割,不强调某一部门或单位的利益而注重整体利益,依据产品价值实现整体利益最大化。
原则 9:视供应商为伙伴
与供应商发展战略伙伴关系。
增强彼此信任关系。
与供应商共同探讨供应、质量等问题,让供应商参与产品设计和开发,缩短开发周期。
形成新形式下的供应链竞争力。
原则 10:创造持续改进文化
持续改进是精益生产的灵魂。
不断改进,创造持续改进得公司文化,追求尽善尽美。