制动主缸的设计计算资料
制动主缸文档
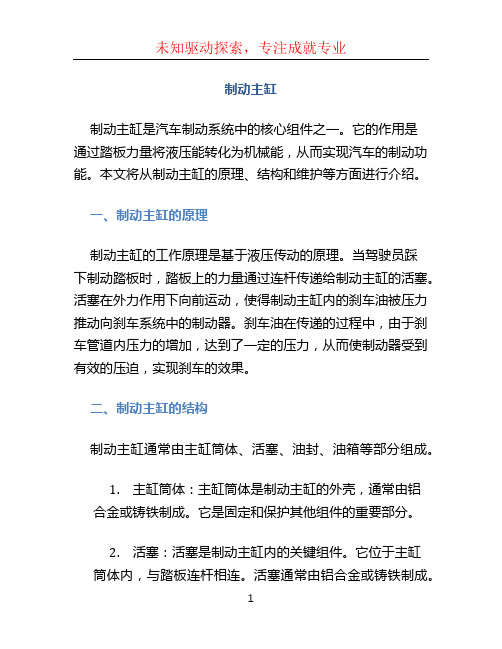
制动主缸制动主缸是汽车制动系统中的核心组件之一。
它的作用是通过踏板力量将液压能转化为机械能,从而实现汽车的制动功能。
本文将从制动主缸的原理、结构和维护等方面进行介绍。
一、制动主缸的原理制动主缸的工作原理是基于液压传动的原理。
当驾驶员踩下制动踏板时,踏板上的力量通过连杆传递给制动主缸的活塞。
活塞在外力作用下向前运动,使得制动主缸内的刹车油被压力推动向刹车系统中的制动器。
刹车油在传递的过程中,由于刹车管道内压力的增加,达到了一定的压力,从而使制动器受到有效的压迫,实现刹车的效果。
二、制动主缸的结构制动主缸通常由主缸筒体、活塞、油封、油箱等部分组成。
1.主缸筒体:主缸筒体是制动主缸的外壳,通常由铝合金或铸铁制成。
它是固定和保护其他组件的重要部分。
2.活塞:活塞是制动主缸内的关键组件。
它位于主缸筒体内,与踏板连杆相连。
活塞通常由铝合金或铸铁制成。
当踏板力量作用于活塞时,活塞会向前移动,从而起到推动刹车油的作用。
3.油封:油封是防止刹车油泄漏的重要组件。
它位于活塞和主缸筒体之间,防止刹车油从活塞周围泄漏出去。
4.油箱:油箱是存储刹车油的部分。
它通常位于主缸筒体的一侧,用于储存供制动主缸使用的刹车油。
油箱通常具有透明的标尺,方便驾驶员观察刹车油的余量。
三、制动主缸的维护为了保证制动主缸的正常运行和延长其使用寿命,以下几点维护工作需要特别注意:1.定期检查刹车油的水分含量:刹车油容易吸湿,过高的水分含量会降低刹车系统的工作效率。
因此,定期检查刹车油的水分含量,并及时更换刹车油,是保持制动主缸正常运行的重要措施。
2.注意刹车油的品质:选择合适的刹车油并定期更换是非常重要的。
刹车油的品质直接关系到制动主缸的工作效果和系统的安全性。
3.检查主缸密封圈和油封:定期检查主缸密封圈和油封的磨损情况。
如果发现有磨损或泄漏迹象,应及时更换。
4.注意制动踏板的力量传递:制动踏板与制动主缸通过连杆连接,确保连杆的稳固性和顺畅的传动是保证制动主缸正常工作的重要条件。
制动主缸的结构与工作原理

第三阶段:继续推动活塞,来自第二压力 腔的液压作用到第二活塞上产生的反作用 力加上逐渐增大的第二回位弹簧抗力之和 大于第一回位弹簧的抗力,使第一回位弹 簧被压缩,第一腔也开始建压。
工作状态
Page 6
• 补偿孔式主缸工作过程(3):
泄压状态:当制动踏板 松开后,在两个回位弹 簧的作用下,活塞迅速 回退,这时在压力腔容 易形成真空。为了消除 真空,必须让供油腔内 的制动液快速地补充到 压力腔。这时通过活塞 上的过油孔制动液由供 油腔进入到压力腔,使 制动回路压力降低。
自然状态
Page 5
• 补偿孔式主缸工作过程(2):
建压状态: 第一阶段:来自第一活塞的推力推动第一、 二活塞组件向前运动,主皮碗唇边将两个 补偿孔封闭。
第二阶段:继续推动活塞,因第二回位弹 簧抗力小于第一回位弹簧,故先被压缩, 第二压力腔先建压。此时第一压力腔内的 制动液未被压缩,故第一腔没有液压。
• 第一活塞限位底座与调节螺杆之间可以相对运动,第一活组件的高度直接影响第二腔的死行程。
Page 4
一、制动主缸的工作原理
• 补偿孔式主缸工作过程(1):
自由(非工作)状态: 主皮碗位于补偿孔和供油 孔之间,压力腔和供油腔 通过这两个孔相连,主缸 没有油压输出。
?第一活塞限位底座与调节螺杆之间可以相对运动第一活塞在推力的作用下压缩回位弹簧向前运动调节螺杆起辅助导向作用?第一活塞组件的高度直接影响第二腔的死行程
制动主缸的结构与工作原理
一、制动主缸的结构 • 补偿孔式主缸结构
Page 2
• 主缸死行程定义(补偿孔式):
Page 3
• 主缸第一活塞组件结构:
泄压状态
Page 7
机械制造专业毕业论文--汽车制动器设计
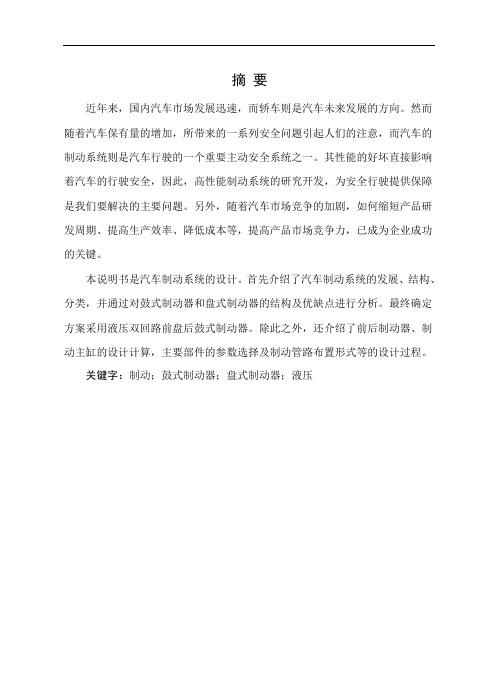
摘要近年来,国内汽车市场发展迅速,而轿车则是汽车未来发展的方向。
然而随着汽车保有量的增加,所带来的一系列安全问题引起人们的注意,而汽车的制动系统则是汽车行驶的一个重要主动安全系统之一。
其性能的好坏直接影响着汽车的行驶安全,因此,高性能制动系统的研究开发,为安全行驶提供保障是我们要解决的主要问题。
另外,随着汽车市场竞争的加剧,如何缩短产品研发周期、提高生产效率、降低成本等,提高产品市场竞争力,已成为企业成功的关键。
本说明书是汽车制动系统的设计。
首先介绍了汽车制动系统的发展、结构、分类,并通过对鼓式制动器和盘式制动器的结构及优缺点进行分析。
最终确定方案采用液压双回路前盘后鼓式制动器。
除此之外,还介绍了前后制动器、制动主缸的设计计算,主要部件的参数选择及制动管路布置形式等的设计过程。
关键字:制动;鼓式制动器;盘式制动器;液压AbstractIn recent years, the domestic automobile market is growing rapidly, and the car is in the direction of the automotive future development. With the increase of car ownership, however, brought about by a series of security issues attract attention, the car's braking system is one of the vehicle driving is an important active safety systems. Whose performance directly affects the safety of car driving, high-performance braking system research and development, provide protection for safe driving we have to solve the problem. In addition, as the auto market competition intensifies, how to shorten the product development cycle, increase productivity, reduce costs, improve market competitiveness has become a key to business success.This manual is car braking system design. First introduced the development of automotive braking systems, structure, classification, and to analyze the structure and the advantages and disadvantages of drum brakes and disc brakes. Finalized program Qianpanhougu brake hydraulic double-loop. In addition, the front and rear brakes, brake master cylinder design calculations, the major components of the parameter selection and arrangement of the brake pipe of the design process.Key words: braking; brake drum; brake disc; hydroid pressure目录第1章绪论 (5)1.1 制动系统设计的意义 (5)1.2 制动系统研究现状 (5)1.3 本次制动系统应达到的目标 (6)1.4 本次制动系统设计要求 (6)第2章制动系统方案论证分析与选择 (7)2.1 制动器形式方案分析 (7)2.1.1 鼓式制动器 (7)2.1.2 盘式制动器 (10)2.2 制动驱动机构的结构形式选择 (11)2.2.1 简单制动系 (11)2.2.2 动力制动系 (12)2.2.3 伺服制动系 (14)2.3 液压分路系统的形式的选择 (14)2.3.1 II型回路 (15)2.3.2 X型回路 (15)2.3.3 其他类型回路 (15)2.4 液压制动主缸的设计方案 (16)第3章制动系统设计计算 (18)3.1 制动系统主要参数数值 (18)3.1.1 相关主要技术参数 (18)3.1.2 同步附着系数的分析 (19)3.2 制动器有关计算 (20)3.2.1 确定前后轴制动力矩分配系数β (20)3.2.2 制动器制动力矩的确定 (20)3.2.3 后轮制动器的结构参数与摩擦系数的选取 (21)3.2.4 前轮盘式制动器主要参数确定 (22)3.3 制动器制动因数计算 (23)3.3.1 前轮盘式制动效能因数 (23)3.3.2 后轮鼓式制动器效能因数 (23)3.4 制动器主要零部件的结构设计 (24)第4章液压制动驱动机构的设计计算 (28)4.1 后轮制动轮缸直径与工作容积的设计计算 (28)4.2 前轮盘式制动器液压驱动机构计算 (29)4.3 制动主缸与工作容积设计计算 (30)4.4 制动踏板力与踏板行程 (31)4.4.1 制动踏板力F (31)p4.4.2 制动踏板工作行程 (32)第5章制动性能分析 (33)5.1 制动性能评价指标 (33)5.2 制动效能 (33)5.3 制动效能的恒定性 (33)5.4 制动时汽车的方向稳定性 (33)5.5 制动器制动力分配曲线分析 (34)5.6 制动距离S (36)5.7 摩擦衬片(衬块)的磨损特性计算 (36)5.8 驻车制动计算 (39)第6章总论 (40)参考文献 (41)第1章绪论1.1制动系统设计的意义汽车是现代交通工具中用得最多,最普遍,也是最方便的交通运输工具。
制动器的设计计算

制动器的设计计算制动器是用来减速和停止运动物体的一种装置。
在设计制动器时,需要考虑以下几个因素:制动力的大小、制动距离的要求、制动器材料的选型、热力学效应以及制动器的结构设计等等。
首先,要确定所需的制动力大小。
制动力是指制动器施加在运动物体上的力,它的大小决定了物体的减速度和停止的时间。
根据实际需求和应用场景,可以通过以下公式计算制动力:制动力=质量×减速度其中,质量是指运动物体的质量,减速度是要达到的减速度。
根据这个制动力,可以选择适当的制动器结构和材料。
其次,要确定制动距离的要求。
制动距离是指从开始制动到停止的距离,它的大小决定了制动器制动的效果和占用的空间。
制动距离可以通过以下公式计算:制动距离=初始速度²/(2×减速度)其中,初始速度是运动物体开始制动时的速度,减速度是物体的减速度。
根据这个制动距离,可以调整制动器结构和制动参数的设计。
然后,要选择适当的制动器材料。
制动器材料需要具备一定的强度、硬度和耐磨性,以保证制动效果和使用寿命。
常见的制动器材料包括金属、陶瓷和复合材料等。
选择合适的材料还需要考虑制动温度的影响,因为制动过程中会产生大量的热量,可能导致制动器材料的热膨胀、软化或者燃烧。
最后,要进行制动器的结构设计。
制动器的结构设计包括选择合适的制动器类型(如摩擦制动器、液力制动器和电磁制动器等),确定制动器的安装位置和方式,设计制动器的摩擦面积和接触面形状等。
结构设计需要考虑制动器的尺寸、重量和安装方便性,以保证制动器能够稳定可靠地工作。
在制动器设计的过程中,还需要考虑一些其他的因素,如制动器的可靠性、维修性以及制动器和运动物体之间的适配性。
制动器的设计是一个综合考虑各种因素的过程,需要进行合理的计算和模拟分析,并结合实际的试验验证。
制动主缸综合性能测试系统设计

De s i g n o f Aut o mo t i v e Br a ke Ma s t e r Cy l i nd e r Co m pr e he n s i v e
Pe r f o r ma n c e Te s t S y s t e m
Q u e B i a o , L u Y i , H u X i a o f e n g , L u o Z a i , F a n We i j u n
Ke y wo r ds: Br ak e ma s t e r c y l i nd e r ,Co m pr e h e n s i v e p e r f o r man c e ,Te s t s y s t e m
1 前 言
汽 车 制 动 主 缸 是 液 压 制 动 系 统 中 的 核 心 部
.
试 验测试 .
制动 主 缸 综合 性 能 测试 系统设 计
★
阙 飚 陆 艺 - 胡 晓峰 罗 哉 1 范伟 军 2
( 1 . 中 国计量 学 院 ; 2 . 杭州 沃镭科技 有 限公 司)
【 摘要 】 针对 目 前 我国制动主缸性能检测设备测试项 目不全面的问题 , 设计 了一套以计算机为控制核心 . 并 采用
a u t o ma t i c a l l y.Te s t r e s u hs i nd i c at e t h a t t e s t f u nc t i o ns o f t h i s s y s t e m s a t i s ie f s c r i t e r i a r e q ui r e me n t ,t e s t r e s u l t s o f a l l t e s t i t e ms a r e a c c e p t a bl e i n a ce r t a i n de g r ee o f c on id f e n c e.
制动器设计-计算说明书
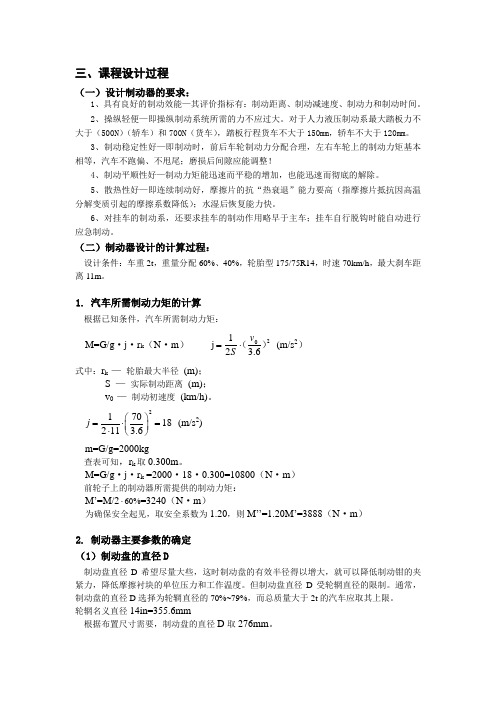
三、课程设计过程(一)设计制动器的要求:1、具有良好的制动效能—其评价指标有:制动距离、制动减速度、制动力和制动时间。
2、操纵轻便—即操纵制动系统所需的力不应过大。
对于人力液压制动系最大踏板力不大于(500N )(轿车)和700N (货车),踏板行程货车不大于150mm ,轿车不大于120mm 。
3、制动稳定性好—即制动时,前后车轮制动力分配合理,左右车轮上的制动力矩基本相等,汽车不跑偏、不甩尾;磨损后间隙应能调整!4、制动平顺性好—制动力矩能迅速而平稳的增加,也能迅速而彻底的解除。
5、散热性好—即连续制动好,摩擦片的抗“热衰退”能力要高(指摩擦片抵抗因高温分解变质引起的摩擦系数降低);水湿后恢复能力快。
6、对挂车的制动系,还要求挂车的制动作用略早于主车;挂车自行脱钩时能自动进行应急制动。
(二)制动器设计的计算过程:设计条件:车重2t ,重量分配60%、40%,轮胎型175/75R14,时速70km/h ,最大刹车距离11m 。
1. 汽车所需制动力矩的计算根据已知条件,汽车所需制动力矩:M=G/g ·j ·r k (N ·m ) 206.321j )(v S ⋅=(m/s 2) 式中:r k — 轮胎最大半径 (m);S — 实际制动距离 (m);v 0 — 制动初速度 (km/h)。
217018211 3.6j ⎛⎫=⋅= ⎪⋅⎝⎭(m/s 2) m=G/g=2000kg查表可知,r k 取0.300m 。
M=G/g ·j ·r k =2000·18·0.300=10800(N ·m )前轮子上的制动器所需提供的制动力矩:M ’=M/2⋅60%=3240(N ·m )为确保安全起见,取安全系数为1.20,则M ’’=1.20M ’=3888(N ·m )2. 制动器主要参数的确定(1)制动盘的直径D制动盘直径D 希望尽量大些,这时制动盘的有效半径得以增大,就可以降低制动钳的夹紧力,降低摩擦衬块的单位压力和工作温度。
制动主缸设计计算

特点: 1、结构简 单; 2、工作时 主皮碗每次都 必须经过补偿 孔,会减少主 皮碗的使用寿 命。
2018年8月16日 7
中心阀式双腔制动主缸
1)工作原理 ABS对制动器压力通常以每秒钟15次的频率进行调节。通过调节制动器的压力变化, 保持轮胎与路面之间的摩擦力,实现可控制的停车。装有ABS的车辆的制动踏板与传统制 动系统的踏板有不同感觉。在ABS起作用时,踏板快速脉动而呈现出对脚的持续不断冲击, 直至停车或ABS关闭为止。这种脉动是对制动器调节压力的反映,不同车型的ABS,其脉动 的强弱是不同的,这是由于在压力调节装置内采用了阻尼阀的缘故。 2)耐高压 由于ABS系统中液压泵的作用,使制动系统的制动液压发生波动,正是这种作用使制 动主缸内的液压产生波动,且活塞同时发生相对移动,其液压的变化频率可达每秒15次左 右,液压可达20Mpa高压,对于补偿孔式主缸,当活塞相对缸体移动时,由于高压的作用, 在补偿孔和回油孔处就会发生密封皮碗的过度磨损或切削现象,这样就会造成制动主缸失 效,从而造成制动失效, 3)装配有ABS/ESP的车辆,制动系统中应采用中心阀式制动主缸,克服了以上不足,从而 提高了制动系统的安全可靠性,所以在ABS系统中不应配用补偿孔式主缸。 4)结构复杂,成本高,可靠性较补偿孔式要高。
产品设计
制动主缸 贮液罐
2018年8月16日 1
助力器、制动主缸的设计
Байду номын сангаас
设计条件 1、整车参数已确定 2、制动系统参数中的制动器参数、踏板参数已确定。 3、制动系统的工作压力已确定 设计依据:GB12676、GB7258 已知条件: 1、标准规定:踏板力: 踏板行程:设计2≺120mm,要求≺150mm 无真空时的踏板力: 2、制动分泵的直径和行程 3、制动踏板的踏板比: 4、发动机提供的真空度: 计算方法 1、由分泵的直径和行程、标准规定的踏板行程,确定制动主缸的缸径和行程 2、由工作压力、制动主缸直径、踏板力,确定真空助力器的有效作用面积: 3、确定真空助力器采用的形式、选择产品结构。 4、对于有补偿孔的串联制动主缸,轮制动器的排量应足够,以保证在压力小于1MPa情 况下,第一活塞上的主皮碗能完全移过补偿孔。 复核 细化计算,确定产品的结构、性能参数。
毕业设计制动系设计计算说明书
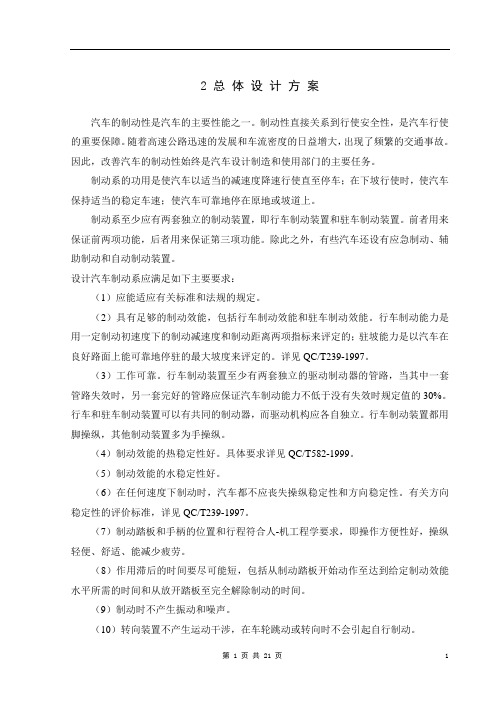
2.4.2 制动原理和工作过程
图 2-2
要使行使中的汽车减速,驾驶员应踩下制动踏板,通过推杆和主缸活塞,使主缸内 的油液在一定压力下流入轮缸,并通过两个轮缸活塞推动两制动蹄绕支撑销转动,上端 向两边分开而其摩擦片压紧在制动鼓的内圆面上。这样,不旋转的制动蹄就对旋转的制 动鼓作用一个摩擦力矩,其方向与车轮旋转方向相反。制动鼓将该力矩传到车轮后,由 于车轮与路面间有附着作用,车轮对路面作用一个向前的周缘力,同时路面也对车轮作 用一个向后的反作用力,即制动力。制动力由车轮经车桥和悬架传给车架和车身,迫使 整个汽车产生一定的减速度。制动力越大,制动减速度越大。当放开制动踏板时,复位 弹簧即将制动蹄拉回复位,摩擦力矩和制动力消失,制动作用即行终止。
第 5 页 共 21 页
5
第 6 页 共 21 页
6
3 制动系主要参数确定
3.1 CS1028 皮卡车型的基本参数
空 汽车质量 前 轴荷分配 质心高度 轴 距 后 轴 轴
载
满
载
1625kg 850kg 775kg 0.52m 2.7m 0.37m
2325kg 920kg 1405kg 0.57m
Ff 1 Ff
0.565
空载条件: Ff 1 8630.3 N
Ff 2 4109.7 N
Ff 1 Ff
0.677
前、后制动器制动力分配的比例影响到汽车制动时方向稳定性和附着条件利用程 度。要确定 值首先就要选取同步附着系数 0 。一般来说,我们总是希望前轮先抱死 ( 0 ) 。 根据有关文献推荐以及我国道路条件, 车速不高, 所以本车型选取 0 0.6 。 为保证汽车制动时的方向稳定性和有足够的附着系数利用率,ECE 的制动法规规 定,在各种载荷条件下,轿车在 0.15 q 0.8,其他汽车在 0.15 q 0.3 的范围内,前 轮应先抱死;在车轮尚未抱死的情况下,在Байду номын сангаас0.15 0.8 的范围内,必须满足 q 0.1 0.85( 0.2)
制动器的设计计算资料
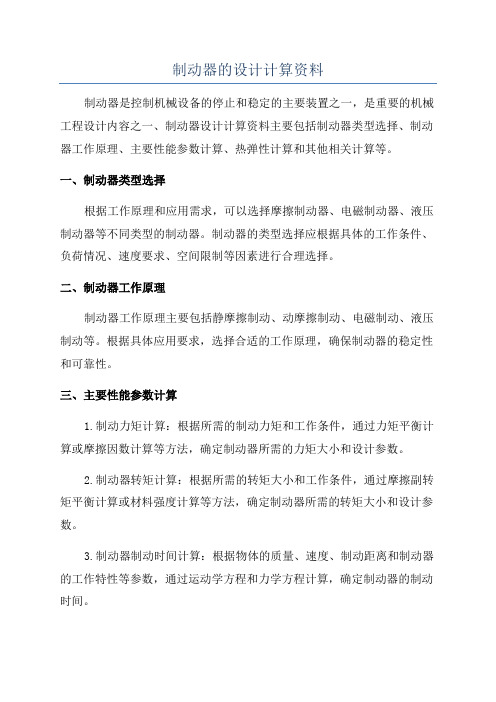
制动器的设计计算资料制动器是控制机械设备的停止和稳定的主要装置之一,是重要的机械工程设计内容之一、制动器设计计算资料主要包括制动器类型选择、制动器工作原理、主要性能参数计算、热弹性计算和其他相关计算等。
一、制动器类型选择根据工作原理和应用需求,可以选择摩擦制动器、电磁制动器、液压制动器等不同类型的制动器。
制动器的类型选择应根据具体的工作条件、负荷情况、速度要求、空间限制等因素进行合理选择。
二、制动器工作原理制动器工作原理主要包括静摩擦制动、动摩擦制动、电磁制动、液压制动等。
根据具体应用要求,选择合适的工作原理,确保制动器的稳定性和可靠性。
三、主要性能参数计算1.制动力矩计算:根据所需的制动力矩和工作条件,通过力矩平衡计算或摩擦因数计算等方法,确定制动器所需的力矩大小和设计参数。
2.制动器转矩计算:根据所需的转矩大小和工作条件,通过摩擦副转矩平衡计算或材料强度计算等方法,确定制动器所需的转矩大小和设计参数。
3.制动器制动时间计算:根据物体的质量、速度、制动距离和制动器的工作特性等参数,通过运动学方程和力学方程计算,确定制动器的制动时间。
4.制动器制动压力计算:根据制动器的工作特性、制动力矩和材料强度等参数,通过流体力学原理和弹性力学原理计算,确定制动器所需的制动压力。
四、热弹性计算在制动器工作过程中,由于摩擦产生的热量会引起制动器温升,并且制动器会受热膨胀的影响。
为确保制动器的稳定性和可靠性,需要进行热弹性计算,包括热传导计算、热膨胀计算和热应力计算等。
五、其他相关计算除了上述主要计算外,还需要进行其他相关的计算,如制动器的材料选择和强度计算、制动器的寿命估算和可靠性分析等。
总之,制动器的设计计算资料包括制动器类型选择、制动器工作原理、主要性能参数计算、热弹性计算和其他相关计算等内容。
制动器的设计应根据具体的工作条件和要求,经过合理的计算和分析,确保制动器的性能稳定和可靠性,满足机械设备的工作要求。
制动主缸缸径标准
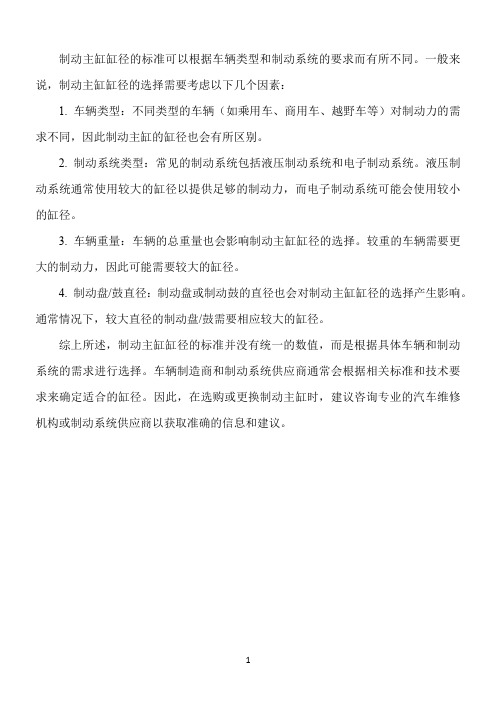
制动主缸缸径的标准可以根据车辆类型和制动系统的要求而有所不同。
一般来说,制动主缸缸径的选择需要考虑以下几个因素:
1. 车辆类型:不同类型的车辆(如乘用车、商用车、越野车等)对制动力的需求不同,因此制动主缸的缸径也会有所区别。
2. 制动系统类型:常见的制动系统包括液压制动系统和电子制动系统。
液压制动系统通常使用较大的缸径以提供足够的制动力,而电子制动系统可能会使用较小的缸径。
3. 车辆重量:车辆的总重量也会影响制动主缸缸径的选择。
较重的车辆需要更大的制动力,因此可能需要较大的缸径。
4. 制动盘/鼓直径:制动盘或制动鼓的直径也会对制动主缸缸径的选择产生影响。
通常情况下,较大直径的制动盘/鼓需要相应较大的缸径。
综上所述,制动主缸缸径的标准并没有统一的数值,而是根据具体车辆和制动系统的需求进行选择。
车辆制造商和制动系统供应商通常会根据相关标准和技术要求来确定适合的缸径。
因此,在选购或更换制动主缸时,建议咨询专业的汽车维修机构或制动系统供应商以获取准确的信息和建议。
1。
制动主缸综合性能测试系统设计

制动主缸综合性能测试系统设计制动主缸测试是评估汽车制动系统性能的重要手段之一。
在制动主缸测试中,主要测试其制动力的准确性、装配质量及机械健康状况,表现在推力、回弹力、密封性、最大制动力等指标上。
因此,制动主缸综合性能测试系统的设计显得尤为重要。
一、测试系统的设计要求设计制动主缸测试系统要符合以下要求:(1)高度自动化:系统应尽可能自动化,减少操作人员操作过程中的干预,提高测试的可重复性和稳定性。
(2)高精度:测试系统应具备高精度传感器和高精度采样器,以确保测试数据的准确性。
(3)高可靠性:为了确保测试数据质量,测试系统应具备高度可靠性,能够长时间运转且不出现误差。
(4)高效:测试系统的测试速度应快,以节约时间和成本。
二、测试系统的设计1、软件设计测试系统的软件主要负责驱动数据采集器,采集测试装置的实时数据,并将采集的数据进行处理,以产生测试结果。
测试结果包括制动主缸推力、回弹力、密封性、最大制动力等指标。
在处理数据时,还需要考虑数据的精度,以确保测试结果的准确性。
为了提高测试过程的自动化,在软件中应设置测试参数、自动运行和自动计算等功能。
2、硬件设计测试系统的硬件包括传感器、数据采集器、计算机等。
其中,测力传感器应与测试系统坐标系对应,以确保有对应的力的标准方向;数据采集器通常选用高灵敏度和高精度的传感器,以确保数据的准确性和稳定性;计算机应配置高性能硬件设备,以确保数据的稳定性和速度。
3、测试棚在设计测试棚时,应考虑到测试数据的稳定性和准确性。
测试棚应该能够保证良好的光照和通风,以确保测量结果的准确性。
同时,测试棚应该有条件控制环境温度和湿度等因素的影响,以确保测试过程的稳定。
在测试棚的设计中,还应该考虑主缸的安装固定和测试人员的操作空间。
4、测试数据的处理测试完成后,应对测试数据进行处理和分析,以得到重要的测试指标信息,如最大制动力、密封性、回弹力等参数。
同时,还可以根据这些数据得到关于主缸性能的评估报告,以提供给制动系统设计人员参考。
制动器的设计计算资料

§3 制动器的设计计算3.1制动蹄摩擦面的压力分布规律从前面的分析可知,制动器摩擦材料的摩擦系数及所产生的摩擦力对制动器因数有很大影响。
掌握制动蹄摩擦面上的压力分布规律,有助于正确分析制动器因数。
在理论上对制动蹄摩擦面的压力分布规律作研究时,通常作如下一些假定:(1)制动鼓、蹄为绝对刚性;(2)在外力作用下,变形仅发生在摩擦衬片上;(3)压力与变形符合虎克定律。
1.对于绕支承销转动的制动蹄如图29所示,制动蹄在张开力P 作用下绕支承销点转动张开,设其转角为,则蹄片上某任意点A 的位移AB 为 AB =A O '·θ∆由于制动鼓刚性对制动蹄运动的限制,则其径向位移分量将受压缩,径向压缩为AC AC =AB COS β即 AC =A O 'θ∆COS β从图29中的几何关系可看到A O 'COS β=D O '=O O 'Sin ϕAC =O O 'Sin ϕθ∆⋅ 因为θ∆⋅'O O 为常量,单位压力和变形成正比,所以蹄片上任意一点压力可写成 q=q 0Sin ϕ (36)亦即,制动器蹄片上压力呈正弦分布,其最大压力作用在与O O '连线呈90°的径向线上。
2.浮式蹄在一般情况下,若浮式蹄的端部支承在斜支座面上,如图30所示,则由于蹄片端部将沿支承面作滚动或滑动,它具有两个自由度运动,而绕支承销转动的蹄片只有一个自由度的运动,因此,其压力分布状况和绕支承销转动的情况有所区别。
现分析浮式蹄上任意一点A 的运动情况。
今设定蹄片和支座面之间摩擦足够大,制动蹄在张开力作用下,蹄片将沿斜支座面上作滚动,设Q 为其蹄片端部圆弧面之圆心,则蹄片上任意一点A 的运动可以看成绕Q 作相对转动和跟随Q 作移动。
这样A 点位移由两部分合成:相对运动位移AB 和牵连运动位移BC ,它们各自径向位移分量之和为AD (见图30)。
AD =AB COS β+BC COS(ϕ-α)根据几何关系可得出AD =(θ∆·OQ +BC Sin α) Sin ϕ+BC COS αCOS ϕ式中θ∆为蹄片端部圆弧面绕其圆心的相对转角。
制动主缸设计
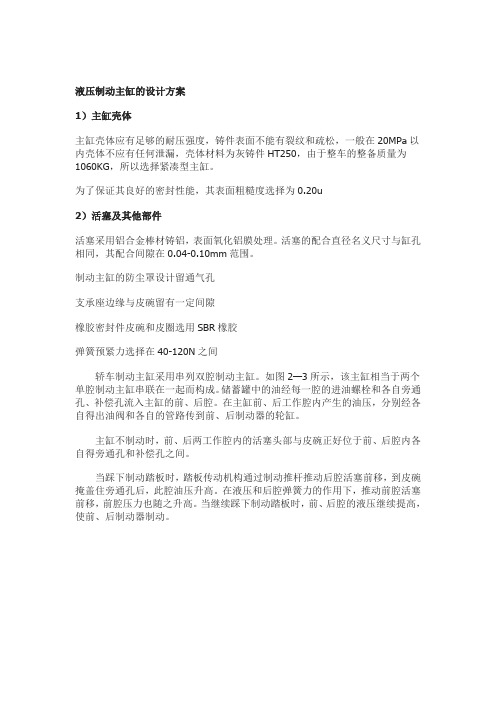
液压制动主缸的设计方案1)主缸壳体主缸壳体应有足够的耐压强度,铸件表面不能有裂纹和疏松,一般在20MPa以内壳体不应有任何泄漏,壳体材料为灰铸件HT250,由于整车的整备质量为1060KG,所以选择紧凑型主缸。
为了保证其良好的密封性能,其表面粗糙度选择为0.20u2)活塞及其他部件活塞采用铝合金棒材铸铝,表面氧化铝膜处理。
活塞的配合直径名义尺寸与缸孔相同,其配合间隙在0.04-0.10mm范围。
制动主缸的防尘罩设计留通气孔支承座边缘与皮碗留有一定间隙橡胶密封件皮碗和皮圈选用SBR橡胶弹簧预紧力选择在40-120N之间轿车制动主缸采用串列双腔制动主缸。
如图2—3所示,该主缸相当于两个单腔制动主缸串联在一起而构成。
储蓄罐中的油经每一腔的进油螺栓和各自旁通孔、补偿孔流入主缸的前、后腔。
在主缸前、后工作腔内产生的油压,分别经各自得出油阀和各自的管路传到前、后制动器的轮缸。
主缸不制动时,前、后两工作腔内的活塞头部与皮碗正好位于前、后腔内各自得旁通孔和补偿孔之间。
当踩下制动踏板时,踏板传动机构通过制动推杆推动后腔活塞前移,到皮碗掩盖住旁通孔后,此腔油压升高。
在液压和后腔弹簧力的作用下,推动前腔活塞前移,前腔压力也随之升高。
当继续踩下制动踏板时,前、后腔的液压继续提高,使前、后制动器制动。
图2—3 制动主缸工作原理图撤出踏板力后,制动踏板机构、主缸前、后腔活塞和轮缸活塞在各自的回位弹簧作用下回位,管路中的制动液在压力作用下推开回油阀流回主缸,于是解除制动。
若与前腔连接的制动管路损坏漏油时,则踩下制动踏板时,只有后腔中能建立液压,前腔中无压力。
此时在液压差作用下,前腔活塞迅速前移到活塞前端顶到主缸缸体上。
此后,后缸工作腔中的液压方能升高到制动所需的值。
若与后腔连接的制动管路损坏漏油时,则踩下制动踏板时,起先只有后缸活塞前移,而不能推动前缸活塞,因后缸工作腔中不能建立液压。
但在后腔活塞直接顶触前缸活塞时,前缸活塞前移,使前缸工作腔建立必要的液压而制动。
汽车制动主缸原理及失效案例分析

汽车制动主缸原理及失效案例分析汽车制动主缸是制动系统管路中重要零部件之一,作用是将自外界输入的机械能转换成液压能,从而液压能通过管路再输给制动轮缸。
制动主缸主要分为三类:补偿孔式、中心阀式和柱塞式。
制动主缸功能失效将会导致整个制动系统失去作用,从而造成汽车制动力减弱或丧失。
标签:压力;制动主缸;侧向力;密封作用1 制动主缸的工作原理帕斯卡定律:定义:根据静压力基本方程(p=p0+ρgh),盛放在密闭容器内的液体,其外加压强p0发生变化时,只要液体仍保持其原来的静止状态不变,液体中任一点的压强均将发生同样大小的变化。
这就是说,在密闭容器内,施加于静止液体上的压强将以等值同时传到各点。
这就是帕斯卡原理,或称静压传递原理。
制动主缸利用帕斯卡原理将真空助力器的输出力转化为液压输出到制动管路;将机械力转化为液压力过程。
2 制动主缸的类型特点2.1 补偿孔式主缸,不能承受高的压力冲击,因为它的第一密封圈位于扩张孔的后面,高的压力冲击会使密封圈脱落,同样,它的制动液流动能力也非常有限。
2.2 中心阀式主缸,结构较复杂,能满足ABS和ESP的要求,是这些年的主流。
2.3 柱塞式主缸,结构作了很大的改进,总长度缩短(节省空间),全行程更大,皮碗改为固定在缸体槽内,不再随活塞一起运动,缸体内部结构较复杂,加工难度偏大,能同时满足ABS和ESP的要求,耐久性提高,事故安全性更高。
3 常见失效案例分析3.1 柱塞式制动主缸3.1.1 失效模式失效现象为制动力减弱,制动液报警灯点亮,检查发现储液壶制动液不足。
确认制动主缸发现活塞偏磨、密封圈磨损导致配合不严泄漏。
3.1.2 失效机理助力器回位弹簧在安装后存在一定的初始压缩量,此状态下弹簧侧向力较大,一般在24N以上。
(如图1)助力器弹簧侧向力Fv导致初始状态时助力器输出推杆发生偏斜,偏斜的推杆与主缸活塞接触不同轴,在制动时输出推杆轴向力产生部分侧向分力,推杆轴向力Fa越大产生的侧向分力越大,从而产生的偏转力矩Mh越大,造成主缸活塞运动不同心与内壁发生严重摩擦,最终导致活塞、皮碗磨损。