铝制品生产工艺流程图
铝箔工艺流程图

铝箔工艺流程图铝箔工艺流程图铝箔是制造包装材料的常见材料之一,具有轻巧、耐腐蚀、易成型等优点,广泛应用于食品包装、药品包装、电子电气等领域。
下面是一个铝箔工艺的流程图,以便更好地了解铝箔的制作过程。
1. 原料选择:首先选择适合的铝合金材料,其中常用的铝合金有1000系列、3000系列和8000系列。
2. 熔炼:将选好的铝合金材料加入到铝熔炉中进行熔炼,使其达到适当的熔点。
3. 铸材:将熔化好的铝合金浇入铸模中,将其冷却成所需的板材。
4. 加热:将铸好的板材放入加热炉中进行加热处理,使其达到适当的软化温度。
5. 轧制:将加热后的板材放入轧机中进行轧制,逐渐减小板材的厚度,使其成为所需的薄铝板。
6. 再热:将轧制后的薄铝板放入再热炉中进行再次加热处理,使其达到适当的软化温度。
7. 再轧:将再热后的薄铝板放入再一次轧机中进行再次轧制,继续减小板材的厚度,使其成为所需的更薄的铝箔。
8. 淬火:将再次轧制后的铝箔通过水淬或气淬等方式进行淬火处理,使其获得适当的硬度和强度。
9. 铣剪:将淬火后的铝箔进行铣剪,将其切割成所需的尺寸。
10. 表面处理:对铝箔进行表面处理,如抛光、喷涂等,以提高其外观质量和耐腐蚀性能。
11. 检测:对铝箔进行各项质量检测,包括厚度、硬度、表面质量等方面。
12. 包装:将合格的铝箔进行包装,以便于运输和储存。
以上就是铝箔的工艺流程图。
通过以上的工艺流程,铝箔可以获得理想的性能和外观质量。
同时,不同的工艺条件和要求也会有所差异,上述流程仅为一般情况下的铝箔制作流程。
随着技术的进步和市场的需求,铝箔的生产工艺也在不断发展和改进,以更好地满足各种应用领域的需求。
电解铝生产工艺流程图

电解铝生产工艺流程图电解铝是通过电解氧化铝溶解于熔融的氟化铝溶液中制取铝金属的一种工艺。
下面是电解铝的生产工艺流程图:首先,将原油经过破碎、磨细后,与石灰石、食盐等混合物一起煅烧成氧化铝。
然后,经过浮选、提纯等工艺进行提纯,得到纯度较高的氧化铝粉末。
接下来,将氧化铝粉末与氟化铝等物料混合,放入电解槽中。
电解槽由炭块阳极、炭块阴极和浸没在熔融的氟化铝溶液中的铝槽中构成。
阳极是铝板制成的,而阴极是由石墨或钢制成的,两者之间隔着一定距离,形成电解贞。
然后,在电解槽中注入熔融的氟化铝溶液,使其溶解成低温电解质。
在施加过电流的条件下,氧化铝在阳极被还原成氧气并释放,而金属铝在阴极上被电解析出来,并沉积在铝槽底部。
随着电流的流动,阴极上的铝层逐渐增厚,最后达到一定厚度后,可以抽取出来,经过过滤、除杂、浇铸等工艺处理,得到纯度较高的铝锭。
在整个过程中,需要注意调节电解槽中的氟化铝浓度、温度、电流密度等参数,以保证电解反应正常进行。
此外,废气处理也是必不可少的环节,以减少对环境的污染。
电解铝生产工艺流程图如下:原油|↓破碎、磨细|↓煅烧|↓氧化铝粉末|↓浮选、提纯|↓纯度较高的氧化铝粉末|↓与氟化铝等物料混合|↓放入电解槽|↓注入熔融的氟化铝溶液|↓电解贞形成|↓施加过电流|↓氧化铝被还原为氧气并释放,金属铝被电解析出并沉积在铝槽底部|↓抽取、过滤、除杂、浇铸等处理|↓纯度较高的铝锭通过电解铝的生产工艺,可以高效、环保地制取出纯度较高的铝金属,满足人们对于铝材的需求。
同时,电解铝工艺还可以循环利用氧化铝废料,减少对资源的消耗。
铝型材工艺流程

各车间生产工艺流程图
挤压生产工艺流程图:
铝棒、模具、盛料筒加温 挤压 风冷淬火(水冷) 检验 (牵引)中断
拉伸矫直 检验 成品锯切 检验 装框时效 送至下道工序
喷涂生产工艺流程图
隔热穿条生产工艺流程图
隔热型材分型材检验 → 分料(分为A 、B 组) → A 组开齿 →
穿条 → B 组开齿 → 复合 → 检验 → 滚压 →
检验 → 定尺锯切 → 清洁 → 检验 → 包装入库
坯料检验 水洗 水 洗 上 排 预水洗 除油 水 洗 中和 水洗 碱蚀 水 洗 纯水洗 无铬钝化 水洗 水洗 上线 无铬化检验 下 排 烘 干 沥 干 吹 尘 喷粉 固 化 下线 包 装
成品检验。
从铝土矿制备铝的工艺流程图NaAlO2溶液Al(OH)

2000
中国原铝表观消费变化
1700 消费量 消费增速 1296
1950 45% 40% 35% 30% 25%
1500
1000 710 500 340 Source : KTIC 0 2000年 2002年 2004年 2006年 2008年 2010年
5.【知识提升】 某混合物A,含有KAl(SO4)2、 Al2O3、 CaCO3,在一定条件下可实现下图所示的物质之间转 化:
据此回答下列问题: (1) I、II 、III、IV四步中对于溶液和沉淀的分离采取的方法是 __________。 (2) 根据上述框图反应关系,写出下列B、C、D、E所含物质的 化学式: 固体B_______ ;沉淀C_______ 沉淀D_______;溶液E_______。
——从铝土矿制备铝的工艺流程图
NaOH溶液 溶解 铝土矿
主要成分Al2O3,还有部 分杂质Fe2O3,SiO2等
过滤
过量 二氧化碳
NaAlO2溶液 过滤
Al(OH)3
灼烧
降低氧化 铝熔融温 度
冰晶石
Al2O3 熔融 电解 Al
流 程 甲
过量烧碱
硅铝酸盐沉淀 和Fe2O3
滤液 NaAlO2
滤液FeCl3 通入过量的CO2
滤液 NaHCO3
铝土矿
流 程 过量盐酸 乙
和 AlCl3
过量 烧碱
Fe(OH)3
沉淀 Al(OH)3↓
通入过 量的CO2
灼烧 灼烧 氧 化 铝
SiO2
滤液 NaAlO2
沉淀 Al(OH)3↓ 滤液 NaHCO3
铝板、不锈钢、门窗加工全过程图解

韦xx加工厂学习总结经过将近一个月的xxx学习,从中也学到有很多有关板材加工相关的知识。
北京京湘联科技有限公司主要从事钣金加工及喷涂工事智能门窗制造等业务,针对金属薄板(京湘联工厂主要是对冷板、铝板、镀锌板和不锈钢板)一种综合冷加工工艺,包括一系列的剪、冲/切/复合、折、焊接、铆接、拼接、成型等。
一般完成一次板材加工入库需要几个过程,工厂技术部收到现场发来的板材加工图以后:技术部对加工图的深化、下料——剪板机剪板(剪板料)——刨槽机刨槽——数控冲床切边、冲孔——折弯机折弯板材——对成型板材组装、辅助焊接、打磨——喷涂前处理——喷涂板材——喷涂检测,包装入库。
一:技术部对加工图的深化,下料工厂技术部收到工地现场发来的各板材加工图,然后对加工图的进一步深化,包括对板材投影面的展开、计算面积(用做后期预算)以及对加工板材的数控编程,就可以下料了。
为了更好的节约原材料,编程时要合理的选择板材的拼接图使几张要加工的板材拼接起来符合原材料的常规尺寸。
在数控冲床的编程时,应当选择合理的换模次序,其一般原则是:先圆孔后方孔,先小孔后大孔、先中间后外形。
同时一套模具在选用以后,出于缩短加工时间的考虑,应该完成其在这个零件上的所有需要加工的型孔。
在合理选择换模次序的同时也应该选取模具的最佳走刀路线,以减少空行程,提高生产效率,并保证机床安全可靠的运行,一般每个不同的工件必须独立编程。
在对加工图深化的过程中要参照常用板材来进行选板、计算。
如下表1:二:剪板机剪板(剪板料)数控剪板机(下图1)是借于运动的上刀片和固定的下刀片,采用合理的刀片间隙,对各种厚度的金属板材施加剪切力,使板材按所需要的尺寸断裂分离,一般采用脚踏或按钮操纵进行单次或连续剪切金属。
数控剪板机可分为:脚踏式(人力)、机械数控剪板机式、液压摆式数控剪板机等。
数控剪板机常用来剪裁直线边缘的板料毛坯。
剪切工艺应能保证被剪板料剪切表面的直线性和平行度要求,并尽量减少板材扭曲,以获得高质量的工件。
铝合金制作及安装工艺流程图

北京庭凯门窗工程有限公司
工序名称
成品检验
产品型号、名称
工艺文件
编号
页
数
共13页
第12页
产品部位
名称
框、中梃、扇
工序号
12
设备
名称
编号
型号
工装模具
名称
编号
工装定位基准
工序工时定额
工人等级
材料
工序技术标准
操作要点
检测方法及量具
序号
内容
允差
内容
方法
量检具名称
1
按产品标准出厂逐项检验
必须按标准逐项检验
3
1型口宽度偏差
±0.4
首件要检查,合格后再批量加工
用游标卡尺测量
游标卡尺
4
1型口位置偏差
±0.4
首件要检查,合格后再批量加工
用游标卡尺测量
游标卡尺
角度尺
更改状态
更改单号
签字
日期
更改状态
更改单号
签字
日期
描图
审核
设计
标准化
校对
批准
企业名称
北京庭凯门窗工程有限公司
工序名称
钻执手孔
产品型号、名称
工艺文件
编号
注意避免拐角处胶条脱槽
更改状态
更改单号
签字
日期
更改状态
更改单号
签字
日期
描图
审核
设计
标准化
校对
批准
企业名称
北京庭凯门窗工程有限公司
工序名称
框扇装配
产品型号、名称
工艺文件
编号
页
数
共13页
铝型材加工工艺流程
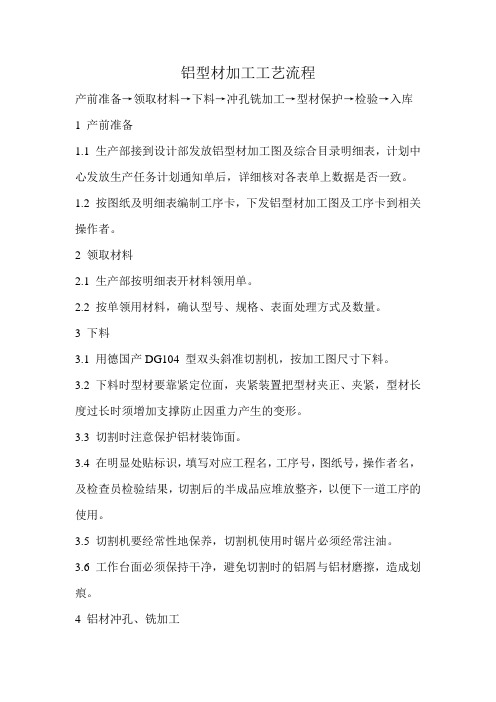
铝型材加工工艺流程产前准备→领取材料→下料→冲孔铣加工→型材保护→检验→入库1 产前准备1.1 生产部接到设计部发放铝型材加工图及综合目录明细表,计划中心发放生产任务计划通知单后,详细核对各表单上数据是否一致。
1.2 按图纸及明细表编制工序卡,下发铝型材加工图及工序卡到相关操作者。
2 领取材料2.1 生产部按明细表开材料领用单。
2.2 按单领用材料,确认型号、规格、表面处理方式及数量。
3 下料3.1 用德国产DG104 型双头斜准切割机,按加工图尺寸下料。
3.2 下料时型材要靠紧定位面,夹紧装置把型材夹正、夹紧,型材长度过长时须增加支撑防止因重力产生的变形。
3.3 切割时注意保护铝材装饰面。
3.4 在明显处贴标识,填写对应工程名,工序号,图纸号,操作者名,及检查员检验结果,切割后的半成品应堆放整齐,以便下一道工序的使用。
3.5 切割机要经常性地保养,切割机使用时锯片必须经常注油。
3.6 工作台面必须保持干净,避免切割时的铝屑与铝材磨擦,造成划痕。
4 铝材冲孔、铣加工4.1 冲孔使用国产XCT-1100A 型冲床,冲孔前接上电源开关让设备空转无异常后开始安装冲压模具。
4.2 模具须专业人员安装,安装时调整上下模间隙,用废料进行试冲合格后开始冲压。
4.3 铝材冲孔后,切口必须平整、光滑。
4.4 冲孔过程中,应时常检查上模中的料落是否退出,模具是否松动,如有问题必须做好相应措施解决。
4.5 铣加工使用国产ZX32 钻铣床或德国产加工中心,按加工图进行加工,注意保护装饰面。
4.6 在明显处贴标识,填写对应工程名,工序号,图纸号,操作者名,及检查员检验结果。
5 型材保护5.1 铝材擦拭干净后进行贴膜保护,贴在铝材上的塑料膜两端的超出部分不宜过长,以免浪费。
5.2 贴膜后的铝材应光滑,不能有皱痕与裂口。
5.3 贴膜完毕,应按要求堆放。
6 检验6.1 核对各工序有无漏加工,检验员有无漏检,标识上有无漏项。
6.2 按加工图检验,不合格品返修,返修仍达不到图纸要求的报废。
铝制品生产工艺流程
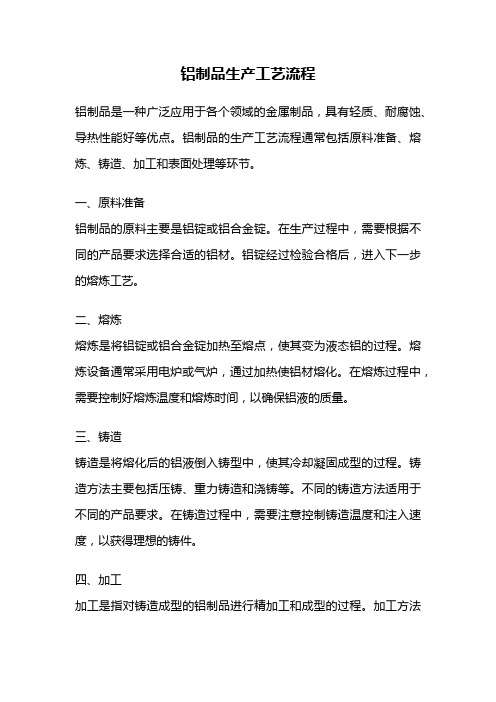
铝制品生产工艺流程铝制品是一种广泛应用于各个领域的金属制品,具有轻质、耐腐蚀、导热性能好等优点。
铝制品的生产工艺流程通常包括原料准备、熔炼、铸造、加工和表面处理等环节。
一、原料准备铝制品的原料主要是铝锭或铝合金锭。
在生产过程中,需要根据不同的产品要求选择合适的铝材。
铝锭经过检验合格后,进入下一步的熔炼工艺。
二、熔炼熔炼是将铝锭或铝合金锭加热至熔点,使其变为液态铝的过程。
熔炼设备通常采用电炉或气炉,通过加热使铝材熔化。
在熔炼过程中,需要控制好熔炼温度和熔炼时间,以确保铝液的质量。
三、铸造铸造是将熔化后的铝液倒入铸型中,使其冷却凝固成型的过程。
铸造方法主要包括压铸、重力铸造和浇铸等。
不同的铸造方法适用于不同的产品要求。
在铸造过程中,需要注意控制铸造温度和注入速度,以获得理想的铸件。
四、加工加工是指对铸造成型的铝制品进行精加工和成型的过程。
加工方法主要包括冷加工和热加工。
冷加工主要是通过机械加工、切割、冲压等方式对铝制品进行加工;热加工则是通过热处理、热轧、锻造等方式对铝制品进行加工。
加工过程中需要根据产品要求进行精确的加工操作,以保证产品的质量和尺寸精度。
五、表面处理表面处理是对铝制品进行防腐蚀、装饰和改善物理性能的过程。
常见的表面处理方法有阳极氧化、电镀、喷涂等。
阳极氧化是将铝制品放入含有电解液的槽中,通过电流作用使其表面形成一层氧化膜,增加其耐蚀性和装饰性。
电镀是将铝制品放入电解槽中,通过电流作用使其表面镀上一层金属,提高其表面硬度和耐磨性。
喷涂是将涂料喷涂在铝制品表面,增加其装饰性和防腐蚀性。
铝制品的生产工艺流程包括原料准备、熔炼、铸造、加工和表面处理等环节。
每个环节都需要严格控制工艺参数和操作要求,以确保产品的质量和性能。
铝制品作为一种重要的金属制品,在各个领域都有着广泛的应用前景。
随着科技的不断发展和工艺的不断完善,铝制品的生产工艺也在不断改进和创新,以满足市场的需求。
铝的生产工艺流程

铝的生产工艺流程
铝的生产工艺流程通常包括以下几个步骤:
1. 选矿:从铝矿石中提取出富含氧化铝的矿石,如赤铁矾。
2. 粉碎和研磨:将矿石破碎并加入水或酸进行磨碎,使之成为粉末状。
3. 酸浸:将研磨后的矿石与稀硫酸或盐酸等酸性液体混合,使氧化铝溶解,并滤去未溶解的杂质。
4. 沉淀和过滤:通过加入氢氧化钠、氢氧化铝或其他沉淀剂,使溶液中的氧化铝沉淀下来,然后通过过滤将沉淀物分离出来。
5. 熔炼和电解:将沉淀物经过干燥和煅烧后,放入铝电解槽中,用电流通过电解槽,使氧化铝还原成金属铝。
同时,利用电解液中有盐酸等溶解的杂质被阳极板吸附,净化电解液。
6. 精炼:对产生的铝液进行精炼处理,如去除杂质和调整合金成分。
7. 铸造和加工:将精炼后的铝液浇铸成铝锭或铝型材,经过冷却和固化后,进行加工成所需的铝制品。
此外,铝的生产过程中还有一些附加步骤,如处理废水和废气的环保措施,以及回收再利用铁、铜和其他有价值的材料。
铝合金生产流程

铝型材生产流程一、铝合金型材生产流程图一、产品设计篇根据客户的来样或者来图,由专业的技术人员进行对接,讨论型材的最优化设计方案,并组织公司人员进行评审,出具标准图纸后双方签字确认。
二、模具篇 根据使用需求详细了解开模产品参数,如:规格尺寸、力学性能等、形态结构(产品规格尺寸、结构的难易程度会直接影响开模定制的成本投入);根据以上了解,技术人员开始出具模具设计图纸,以及技术参数; 1、模具加工工艺流程图模具:平流模客户沟通来图/来样 图纸评审标准图绘制 客户确认开模通知 图纸批准 图纸发放模具:分流模三、熔铸篇铝棒的质量是直接影响整个产品质量的首要一环。
为了确保铝棒的质量达到国际先进水平,从设备的投入,工艺的优化和材料的确挑选,我公司作出如下工作:1、好的产品质量首先要有先进的设备作为基础,我公司配备具有自动加料、电磁搅拌功能的先进节能环保铝棒熔铸炉、深井式热顶铸棒机和铝棒均质炉。
使用在线除气、净化系统;全线采用PLC控制系统。
2、合金化学成分的合理性直接影响挤压性能及产品力学性能。
为了确保合金成分的合理配比,我公司引进德国电磁波光谱仪严格控制化学成份,多次进行成份复验。
3、铝锭的来源:选用国内外优质的A00铝锭,分别来自国内十大铝厂以及加拿大、澳大利亚等国进口。
4、现生产各种规格铝棒:∮101、∮120、∮152、∮178、∮254等多种规格。
5、铝锭融化温度为750℃,均质温度为570℃。
(一)、对比优点:选用先进设备、优质原料、独特工艺和先进的检测设备。
选用优质纯铝锭(99.7% A00 AL)作为原料,配备具有自动加料、电磁搅拌功能的先进节能环保铝棒熔铸炉、深井式热顶铸棒机和铝棒均质炉。
使用在线除气、净化系统;全线采用PLC控制系统。
引进德国的电磁波光谱仪严格控制化学成份。
何为均质以及均质的好处:铸锭均匀化,可以消除铸锭残余应力,提高塑性,改善加工性能,提高挤压制品的掠夺速度及表面质量。
电解铝工艺流程图

电解铝工艺流程图电解铝工艺是制取纯铝的一种重要方法,其工艺流程图如下:一、原料准备在电解铝工艺中,主要原料是氧化铝,可以通过氢氧化铝的煅烧和铝矿的氧化得到。
首先将氟化铝作为助熔剂加入氧化铝中,形成氟化铝溶液。
然后将铝矿破碎、研磨成粉末,与氧化铝混合,放入电解槽中。
二、电解槽装配电解槽是制取铝的关键设备,它由钢制而成,内部涂有特殊陶瓷材料。
电解槽装配时,首先安装阳极,阳极是由导电碳材料制成的。
然后装配阴极,阴极是由碳素砖砌筑而成的。
最后,将电解槽密封,启动电解设备。
三、电解过程在电解过程中,首先通过电解设备给电解槽提供恒定的电流。
电流进入电解槽,阳极上的氧化铝会发生还原反应,生成金属铝,同时释放出氧气。
金属铝沉积在阴极上,逐渐形成铝块。
释放的氧气会在液面上方形成气泡,并随着氢气一起排出电解槽。
四、收集铝液电解槽中的铝液会不断地积累,需要定期进行收集。
收集铝液时,首先关闭电流,然后用特殊工具将铝液从电解槽中舀取出来。
收集到的铝液会经过离心等处理,除去杂质,得到纯净的铝液。
五、铝液处理收集到的铝液中可能含有一些杂质,需要进行处理。
首先,将铝液加热至液态,然后通过过滤和沉淀等方法去除杂质。
经过处理后的铝液就是纯度较高的铝液。
六、铝液铸造处理后的铝液可以进行铸造。
铸造的方法有很多种,常见的有连铸法和半连铸法。
在连铸法中,将铝液倒入长方形的铝模中,使其形成长方形的铝坯。
在半连铸法中,将铝液倒入铸造机器中,通过旋转和振动将其形成铝坯。
七、铝坯加工铝液铸造成坯体后,需要进行加工。
首先,将铝坯送入轧机中,通过轧制将其变成薄板或薄带。
然后,对薄板进行拉伸、剪切、冲孔等工艺,得到所需的铝产品。
最后,对铝产品进行表面处理,如阳极氧化、喷涂等,提高产品的质量和耐腐蚀性能。
八、成品检验制取出的铝产品需要经过严格的检验,确保其质量符合要求。
成品检验主要包括外观检查、尺寸检测、化学成分分析等。
合格的铝产品即可包装、入库。
以上是电解铝工艺的主要流程。
铝门窗生产工艺流程图
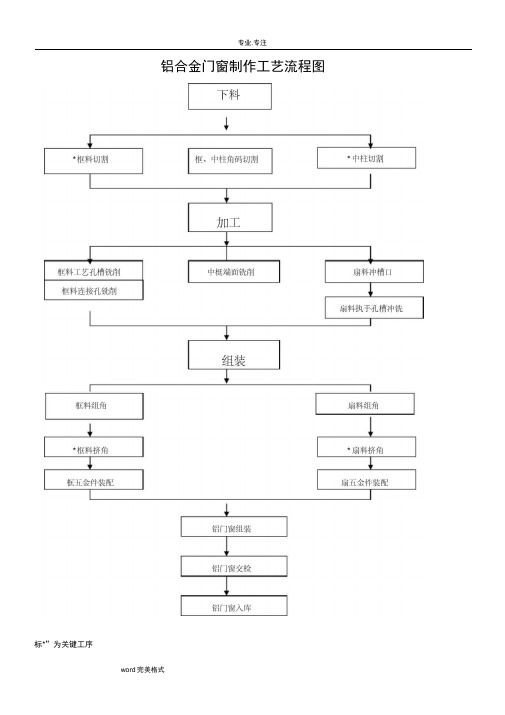
铝合金门窗制作工艺流程图标*”为关键工序(一)、下料(关键工序)A、工序流程:*为关键工序B、操作方法1、领料后仔细确认下料加工单和优化单材料与实物一致。
2、确认下料方式(90°或45°或异型)3、确认型材放置方向是否正确。
4、根据不同的型材选择不同的工装卡具。
5、根据不同的型材调整锯片的进给速度和冷却剂的喷射量。
6、45°下料时应仔细测量料高,如果安装模具要经锯床水平台面与料的最高点做料高,不许单独测量原材料的料高(测料高采用游标卡尺,至少3点,以平均值为准)7、下料时必须严格执行首检制,确认无误后方可成批下料(由工艺员、质检员、班长认可并做好首检记录),并且在下料过程中要进行抽检。
&主操手和副操手应互检,每次调整尺寸或角度,副操手应复合尺寸和角度,防止批量尺寸或角度出现错误,9、角码要根据不同的型材试装后,方可成批下料,样窗及私人窗,如果没有订购角码,可自行配制,应以间隙不大于0.2为准。
工程用角码一定按设计要求提角码料切割。
10、工件的数量应以生产部下发的下料单或班长经书面形式提供的数量为准,确保数量无误(生产部或班长签字为准)。
11、尺寸:框料0—— +0.5 ;扇料—0.5 —— 0.。
12、下完料后要及时清除腔内的铝屑(用压缩空气吹,但是要注意安全),要按照不同的规格,标明尺寸/数量,分类码放整齐,不同规格不能混放,转到下道工序时要办好交接记录(填好工艺卡片)。
13、合格下料转到下道工序后,下料任务单由下料工签字后交组长保存,以便查阅。
14、需交接班时,应有记录,并作好交接手续。
由于交接不当而出现的问题由交接双方负同责15、检查方法:检查首件记录、现场抽查、按照批量3%抽查且不少于5根。
C、质量控制点:1、型材下料后的长度L±0.52、角度偏差一10 'D、检验标准:下料长度L±0.5,角度偏差—10 ',型材不得夹伤和变形,切口平整,不准缺角或留有断E、基本要求:1、人员要求:经过机械设备操作规程的培训,考核合格,熟悉本职工作的所有程序。