KK8028C-005中文资料
V8A02解决方案用户手册V2.1

V8A02解决方案用户手册V2.1目录1. 文档说明 (6)1.1版本说明 (6)1.2专有名词 (6)2. 方案简介 (8)2.1方案概述 (8)2.2 功能特点 (8)2.2.1 支持DVI数据源输入 (8)2.2.2 支持宽屏等多种DVI输入分辨率 (8)2.2.3 发送卡超大带载 (8)2.2.4 功能强大的配套软件 (8)2.2.5 智能在线检测 (8)2.2.6 高刷新频率 (8)2.2.7 高灰度等级 (9)2.2.8 支持各种像素类型 (9)2.2.9 灵活支持各种模组 (9)2.2.10 多样的端口设置功能 (9)2.2.11箱体色度调整 (9)2.2.12 逐点校正功能 (9)2.2.13 集成测试功能 (9)2.2.14 联机配置数据 (9)2.2.15 智能维修 (10)2.2.16 环路备份功能 (10)2.2.17 在线升级固件安全可靠 (10)2.2.18 支持低电压输入 (10)2.2.19 配备指示灯及控制面板接口 (10)2.2.20 支持远距离传输 (10)2.2.21 支持音频传输及电源控制 (10)2.2.22 提供完整的二次开发接口 (10)2.2.24 支持内建PWM恒流 (10)2.2.25 支持低亮度高保真 (10)2.3产品清单 (11)3. 应用概述 (12)3.1 典型应用 (12)3.2 环路备份 (13)3.3 多发送卡 (14)4. 功能详解 (15)4.1 模组支持能力 (15)4.1.1 模组行、列数1~128以内任意 (16)4.1.2 模组数据类型 (16)4.1.3 模组内每扫描串移长度 (17)4.1.4 虚拟模组LED灯点位置多种排列方式 (17)4.2 箱体连接设置 (17)4.2.1 箱体内模组级联方式 (17)4.2.2 端口扩展 (18)4.2.3 端口对开 (19)4.2.4 端口逆序 (20)4.2.5 端口偏移 (20)4.2.6 箱体带载高度、宽度 (20)4.2.7 箱体显示起始的行、列位置 (21)4.2.8 箱体无信号输入时显示内容设置 (21)4.2.9 箱体级联数量 (21)4.2.10 箱体色度调整 (21)4.2.11 箱体逐点色度校正 (22)4.2.12 箱体测试功能 (22)4.3 屏体参数调节 (23)4.3.1 多个LED屏设置 (23)4.3.3 虚拟LED屏的实效果 (24)4.3.4 LED屏亮度调节 (25)4.3.5 LED屏对比度调节 (26)4.3.6 LED屏色温调节 (26)4.3.7 关闭LED屏显示 (27)4.3.8 锁定LED屏内容 (27)4.3.9 LED屏环境监控 (27)4.4 显示性能参数说明 (30)4.4.1 灰度等级 (30)4.4.2 刷新频率 (31)4.4.3 亮度效率 (31)4.4.4 最小OE (31)4.5 发送卡带载 (31)4.6 在线检测 (34)4.7 系统升级 (34)4.8 智能维修 (36)4.8.1 接收卡更换 (36)4.8.2模组替换 (37)5. 使用说明 (39)5.1 连接硬件 (39)5.1.1 发送卡安装方法 (39)5.1.2 接收卡安装方法 (39)5.1.3 多功能卡安装方法 (39)5.2 安装软件 (40)5.2.1 配置要求 (40)5.2.2 安装步骤 (40)5.3 系统设置 (40)5.3.1 显卡设置 (40)5.3.2系统设置 (43)6. 附录 (55)6.1 设备推荐型号 (55)6.1.1 DVI复制器 (55)6.2 选用线缆清单 (55)6.2.1 HDMI转DVI线缆 (55)6.2.2 音频线 (56)6.2.3 双绞线 (56)6.2.4 光纤 (56)1. 文档说明1.1版本说明版本日期说明V2.0 2013-01-09 升级自1.71版本V2.1 2013-07-15 新增接收卡产品1.2专有名词以下是本文中使用的专用术语及解释,便于读者更好的理解文章内容。●软件一系列按照特定顺序组织的计算机数据和指令的集合,本文中特指在计算机上运行的应用软件。
莫克8口无管理以太网开关产品说明书
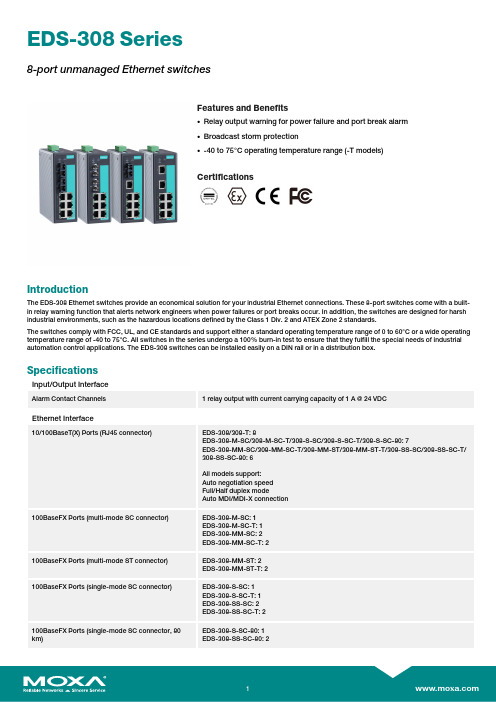
EDS-308Series8-port unmanaged Ethernet switchesFeatures and Benefits•Relay output warning for power failure and port break alarm •Broadcast storm protection•-40to 75°C operating temperature range (-T models)CertificationsIntroductionThe EDS-308Ethernet switches provide an economical solution for your industrial Ethernet connections.These 8-port switches come with a built-in relay warning function that alerts network engineers when power failures or port breaks occur.In addition,the switches are designed for harsh industrial environments,such as the hazardous locations defined by the Class 1Div.2and ATEX Zone 2standards.The switches comply with FCC,UL,and CE standards and support either a standard operating temperature range of 0to 60°C or a wide operating temperature range of -40to 75°C.All switches in the series undergo a 100%burn-in test to ensure that they fulfill the special needs of industrial automation control applications.The EDS-308switches can be installed easily on a DIN rail or in a distribution box.SpecificationsInput/Output InterfaceAlarm Contact Channels1relay output with current carrying capacity of 1A @24VDCEthernet Interface10/100BaseT(X)Ports (RJ45connector)EDS-308/308-T:8EDS-308-M-SC/308-M-SC-T/308-S-SC/308-S-SC-T/308-S-SC-80:7EDS-308-MM-SC/308-MM-SC-T/308-MM-ST/308-MM-ST-T/308-SS-SC/308-SS-SC-T/308-SS-SC-80:6All models support:Auto negotiation speed Full/Half duplex modeAuto MDI/MDI-X connection100BaseFX Ports (multi-mode SC connector)EDS-308-M-SC:1EDS-308-M-SC-T:1EDS-308-MM-SC:2EDS-308-MM-SC-T:2100BaseFX Ports (multi-mode ST connector)EDS-308-MM-ST:2EDS-308-MM-ST-T:2100BaseFX Ports (single-mode SC connector)EDS-308-S-SC:1EDS-308-S-SC-T:1EDS-308-SS-SC:2EDS-308-SS-SC-T:2100BaseFX Ports (single-mode SC connector,80km)EDS-308-S-SC-80:1EDS-308-SS-SC-80:2Standards IEEE802.3for10BaseTIEEE802.3u for100BaseT(X)and100BaseFXIEEE802.3x for flow controlOptical Fiber800Typical Distance4km5km40km80kmWavelen-gthTypical(nm)130013101550TX Range(nm)1260to13601280to13401530to1570 RX Range(nm)1100to16001100to16001100to1600Optical PowerTX Range(dBm)-10to-200to-50to-5 RX Range(dBm)-3to-32-3to-34-3to-34 Link Budget(dB)122929 Dispersion Penalty(dB)311Note:When connecting a single-mode fiber transceiver,we recommend using anattenuator to prevent damage caused by excessive optical power.Note:Compute the“typical distance”of a specific fiber transceiver as follows:Linkbudget(dB)>dispersion penalty(dB)+total link loss(dB).DIP Switch ConfigurationEthernet Interface Port break alarmSwitch PropertiesMAC Table Size2kbitsPacket Buffer Size768KProcessing Type Store and ForwardPower ParametersInput Current EDS-308/308-T:0.07A@24VDCEDS-308-M-SC/S-SC Series,308-S-SC-80:0.12A@24VDCEDS-308-MM-SC/MM-ST/SS-SC Series,308-SS-SC-80:0.15A@24VDC Connection1removable6-contact terminal block(s)Operating Voltage9.6to60VDCInput Voltage Redundant dual inputs,12/24/48VDCReverse Polarity Protection SupportedOverload Current Protection SupportedPhysical CharacteristicsHousing MetalIP Rating IP30Dimensions53.6x135x105mm(2.11x5.31x4.13in)Weight790g(1.75lb)Installation DIN-rail mounting,Wall mounting(with optional kit) Environmental LimitsOperating Temperature Standard Models:-10to60°C(14to140°F)Wide Temp.Models:-40to75°C(-40to167°F) Storage Temperature(package included)-40to85°C(-40to185°F)Ambient Relative Humidity5to95%(non-condensing)Standards and CertificationsHazardous Locations ATEX,Class I Division2EMI CISPR32,FCC Part15B Class AMaritime DNV-GLEMC EN55032/24Vibration IEC60068-2-6EMS IEC61000-4-2ESD:Contact:6kV;Air:8kVIEC61000-4-3RS:80MHz to1MHz:20V/mIEC61000-4-4EFT:Power:2kV;Signal:1kVIEC61000-4-5Surge:Power:2kV;Signal:2kVIEC61000-4-6CS:10VIEC61000-4-8PFMFSafety UL508,UL60950-1,CSA C22.2No.60950-1 Shock IEC60068-2-27Freefall IEC60068-2-32MTBFTime255,528hrsStandards MIL-HDBK-217FWarrantyWarranty Period5yearsDetails See /warrantyPackage ContentsDevice1x EDS-308Series switchInstallation Kit1x cap,plastic,for SC fiber port2x cap,plastic,for SC fiber port(-SC models)2x cap,plastic,for ST fiber port(-ST models) Documentation1x quick installation guide1x warranty cardDimensionsOrdering InformationModel Name 10/100BaseT(X)PortsRJ45Connector100BaseFX PortsMulti-Mode,SCConnector100BaseFX PortsMulti-Mode,STConnector100BaseFX PortsSingle-Mode,SCConnectorOperating Temp.EDS-3088–––0to60°CEDS-308-T8–––-40to75°C EDS-308-M-SC71––0to60°CEDS-308-M-SC-T71––-40to75°C EDS-308-MM-SC62––0to60°CEDS-308-MM-SC-T62––-40to75°C EDS-308-MM-ST6–2–0to60°CEDS-308-MM-ST-T6–2–-40to75°C EDS-308-S-SC7––10to60°CEDS-308-S-SC-T7––1-40to75°C EDS-308-SS-SC6––20to60°CEDS-308-SS-SC-T6––2-40to75°C EDS-308-S-SC-807––10to60°CEDS-308-SS-SC-806––20to60°C Accessories(sold separately)Power SuppliesDR-120-24120W/2.5A DIN-rail24VDC power supply with universal88to132VAC or176to264VAC input byswitch,or248to370VDC input,-10to60°C operating temperatureDR-452445W/2A DIN-rail24VDC power supply with universal85to264VAC or120to370VDC input,-10to50°C operating temperatureDR-75-2475W/3.2A DIN-rail24VDC power supply with universal85to264VAC or120to370VDC input,-10to60°C operating temperatureMDR-40-24DIN-rail24VDC power supply with40W/1.7A,85to264VAC,or120to370VDC input,-20to70°Coperating temperatureMDR-60-24DIN-rail24VDC power supply with60W/2.5A,85to264VAC,or120to370VDC input,-20to70°Coperating temperatureWall-Mounting KitsWK-46Wall-mounting kit,2plates,8screws,46.5x66.8x1mmRack-Mounting KitsRK-4U19-inch rack-mounting kit©Moxa Inc.All rights reserved.Updated Jan30,2019.This document and any portion thereof may not be reproduced or used in any manner whatsoever without the express written permission of Moxa Inc.Product specifications subject to change without notice.Visit our website for the most up-to-date product information.。
Atmel CryptoAuthentication

Application Note Single-Wire and I2C Interfaces Seamless DebuggingUsing Saleae Logic AnalyzerATSHA204A, ATECC108A, and ATECC508A Prerequisites●Hardware PrerequisitesAtmel® AT88CK490 or AT88CK590 Demo-Evaluation Board orAtmel AT88CK101-() KitSaleae Logic Analyzer●Software PrerequisitesAtmel Crypto Evaluation Studio (ACES)IntroductionThe purpose of this document is to help the user gain a better understanding of how to use the Atmel CryptoAuthentication™ ATSHA204A, ATECC108A, and ATECC508A devices (crypto device) with the Saleae Logic Analyzer. The Saleae Logic Analyzer is a powerful tool to debug and evaluate the commands coming to and from these devices. The tool supports both the standard I2C and the Atmel Single-Wire Interface (SWI) protocols.The goal of this application note is to:●Understand the bus interfaces of the crypto device using the Saleae LogicAnalyzer.●Develop and debug with the crypto device using the Saleae Logic Analyzer. SummaryThe Saleae Logic Analyzer provides an in depth tool to quickly develop and debug integration of the crypto device into a customer’s system. The bus decoding allows for easy understanding of all bus traffic to the crypto device. By reducing the development time, the Saleae Logic Analyzer greatly reduces the cost of adding the crypto device.CryptoAuthentication for Single-Wire and I 2C Interfaces Seamless Debugging Using SaleaeLogic Analyzer [APPLICATION NOTE]Atmel-8847B-CryptoAuth-SWI-I2C-Seamless-Debugging-Saleae-Logic-Analyzer-ApplicationNote_08201521.Saleae Logic AnalyzerOn load of the analyzer, either 8 or 16 channels will display depending on the analyzer used. Protocol specific settings are located on the far right under the heading, Analyzers .Figure 1-1.Channels and Protocol SettingsThe crypto device supports either a Single-Wire Interface (SWI) or I 2C Interface depending on the P/N. ●SWI — Supported through the use of a DLL library. Use version 1.1.16 or greater. This version comes with support on Win, LNX, and IOS.●I 2C — Supported by the use of the built-in I 2C interface that is included in the Saleae download.3CryptoAuthentication for Single-Wire and I 2C Interfaces Seamless Debugging Using SaleaeLogic Analyzer [APPLICATION NOTE]Atmel-8847B-CryptoAuth-SWI-I2C-Seamless-Debugging-Saleae-Logic-Analyzer-ApplicationNote_0820152.Single-Wire Interface (SWI)Use the SWI DLL library version 1.1.16 or greater.1.Copy the DLL into the Saleae LLC\Analyzers directory on the user’s PC. Once the driver has been copied to the correct folder, the Atmel SWI option will appear and be listed in the Analyzer drop-down options. The SWI Analyzer has three display modes:Token Byte Packet (as described in the datasheet)Figure 2-1.Atmel SWI Option2.Select the Atmel SWI Analyzer from the list. 3.After selecting Atmel SWI Analyzer , rename the channel when prompted, 4.Select the Falling Edge Trigger option and start sampling. Using ACES, select a command and send it to the device. For an overview of the ACES tool, please see “Using ACES Application Note”. This will cause the bus to become active and the Analyzer will trigger on the first falling edge and data line.In the screen shot below, the Wake command has been captured followed by Wake Status Read. The Wake command is a special token designed to wake the device and reset the watchdog timer.Figure 2-2.Wake Command Followed by Wake Status ReadEnlargement ofthe Analyzerpull-down options.CryptoAuthentication for Single-Wire and I 2C Interfaces Seamless Debugging Using SaleaeLogic Analyzer [APPLICATION NOTE]Atmel-8847B-CryptoAuth-SWI-I2C-Seamless-Debugging-Saleae-Logic-Analyzer-ApplicationNote_0820154The token view displays each logic bit which is made up of seven bits on the wire. Each group of seven bits is encoded either as a Logic 1 or Logic 0 as follows:●A Logic 1 is one low bit followed by six high bits. ● A Logic 0 is one low bit followed by one high bit, then by one low bit, and then by four high bits.Figure 2-3.Token View Figure 2-4.Logic BitsThe byte view builds on the token view by combining eight tokens into a single byte. This view allows for easy matching of information on the data bus to the command set defined in the datasheet. The byte view istransmitted with the less significant bit first.Figure 2-5.BytesThe packet view further builds on the byte view by ordering the data into logic packets based on the datasheet definition. This allow for quick and easy review of the commands without the need to reference the datasheet.Figure 2-6.Packets0x880x045CryptoAuthentication for Single-Wire and I 2C Interfaces Seamless Debugging Using SaleaeLogic Analyzer [APPLICATION NOTE]Atmel-8847B-CryptoAuth-SWI-I2C-Seamless-Debugging-Saleae-Logic-Analyzer-ApplicationNote_0820153.I 2C InterfaceThe crypto device supports an I 2C interface that is directly supported by the Saleae tool.1.To configure the Analyzer for I 2C , select the I2C option from the Analyzer drop-down list and follow the configuration guide.Figure 3-1.I2C Analyzer Option 2.Select the clock and data channels that will be used for the I2C bus. Different encoding options can also be selected. The crypto device uses the default 8-bit encoding.Figure 3-2.Clock and Data Channels Enlargement ofthe Analyzerpull-down options.CryptoAuthentication for Single-Wire and I 2C Interfaces Seamless Debugging Using SaleaeLogic Analyzer [APPLICATION NOTE]Atmel-8847B-CryptoAuth-SWI-I2C-Seamless-Debugging-Saleae-Logic-Analyzer-ApplicationNote_0820156 3.Next, the Update Channel Names dialog box will be prompted to rename the channels to reflect SCL andSDA. This is an optional step, but helps when analyzing more then one bus at a time.Figure 3-3.Update Channel Names 4.Now that the analyzer is configured, set-up the trigger settings. The Saleae has a One Shot trigger thatcan be triggered on either the falling or rising edge of the SCL channel. The bus is normally held high;therefore, setting a falling edge trigger is recommended.Figure 3-4.Trigger Settings7CryptoAuthentication for Single-Wire and I 2C Interfaces Seamless Debugging Using SaleaeLogic Analyzer [APPLICATION NOTE]Atmel-8847B-CryptoAuth-SWI-I2C-Seamless-Debugging-Saleae-Logic-Analyzer-ApplicationNote_0820155.Once the analyzer has been started, execute a command in order to generate data on the bus.Figure 3-5.Execute a Command After the Analyzer has been triggered, it will collect the waveform information and display it in the viewer. The first token shown is the ATSHA204 Wake.Figure 3-6.First Token — ATSHA204 WakeThe Wake command is a special command that is required to wake-up the device. The command consists of a I 2C Start event followed by a long period of Logic 0 on the SDA line, then followed a Stop event.Figure 3-7.Wake CommandCryptoAuthentication for Single-Wire and I 2C Interfaces Seamless Debugging Using SaleaeLogic Analyzer [APPLICATION NOTE]Atmel-8847B-CryptoAuth-SWI-I2C-Seamless-Debugging-Saleae-Logic-Analyzer-ApplicationNote_0820158After a Wake command, an optional Read can be performed to read the status of the crypto device as shown in the waveform below. After the Read command is issued, the device will send four bytes of data (1-count, 1-data, and 2-CRC).Figure 3-8.Read WaveformThe Saleae tool supports a variety of display options for the I 2C interface including Binary, Hex, and ASCII to help quickly and easily evaluate the data. It can be selected by clicking the Configuration button next to the analyzer of interest on the right.Figure 3-9.Display Options4.Revision HistoryX X X X X XAtmel Corporation 1600 Technology Drive, San Jose, CA 95110 USA T: (+1)(408) 441.0311F: (+1)(408) 436.4200| © 2015 Atmel Corporation. / Rev.: Atmel-8847B-CryptoAuth-SWI-I2C-Seamless-Debugging-Saleae-Logic-Analyzer-ApplicationNote_082015.Atmel ®, Atmel logo and combinations thereof, Enabling Unlimited Possibilities ®, CryptoAuthentication ™, and others are registered trademarks or trademarks of Atmel Corporation in U.S. and other countries. Other terms and product names may be trademarks of others.DISCLAIMER: The information in this document is provided in connection with Atmel products. No license, express or implied, by estoppel or otherwise, to any intellectual property right is granted by this document or in connection with the sale of Atmel products. EXCEPT AS SET FORTH IN THE ATMEL TERMS AND CONDITIONS OF SALES LOCATED ON THE ATMEL WEBSITE, ATMEL ASSUMES NO LIABILITY WHATSOEVER AND DISCLAIMS ANY EXPRESS, IMPLIED OR STATUTORY WARRANTY RELATING TO ITS PRODUCTS INCLUDING, BUT NOT LIMITED TO, THE IMPLIED WARRANTY OF MERCHANTABILITY, FITNESS FOR A PARTICULAR PURPOSE, OR NON-INFRINGEMENT. IN NO EVENT SHALL ATMEL BE LIABLE FOR ANY DIRECT, INDIRECT, CONSEQUENTIAL, PUNITIVE, SPECIAL OR INCIDENTAL DAMAGES (INCLUDING, WITHOUT LIMITATION, DAMAGES FOR LOSS AND PROFITS, BUSINESS INTERRUPTION, OR LOSS OF INFORMATION) ARISING OUT OF THE USE OR INABILITY TO USE THIS DOCUMENT, EVEN IF ATMEL HAS BEEN ADVISED OF THE POSSIBILITY OF SUCH DAMAGES. Atmel makes no representations or warranties with respect to the accuracy or completeness of the contents of this document and reserves the right to make changes to specifications and products descriptions at any time without notice. Atmel does not make any commitment to update the information contained herein. Unless specifically provided otherwise, Atmel products are not suitable for, and shall not be used in, automotive applications. Atmel products are not intended,authorized, or warranted for use as components in applications intended to support or sustain life.SAFETY-CRITICAL, MILITARY, AND AUTOMOTIVE APPLICATIONS DISCLAIMER: Atmel products are not designed for and will not be used in connection with any applications where the failure of such products would reasonably be expected to result in significant personal injury or death (“Safety-Critical Applications”) without an Atmel officer's specific written consent. Safety-Critical Applications include, without limitation, life support devices and systems, equipment or systems for the operation of nuclear facilities and weapons systems.Atmel products are not designed nor intended for use in military or aerospace applications or environments unless specifically designated by Atmel as military-grade. Atmel products are not designed nor intended for use in automotive applications unless specifically designated by Atmel as automotive-grade.。
SE8025TC说明书V2
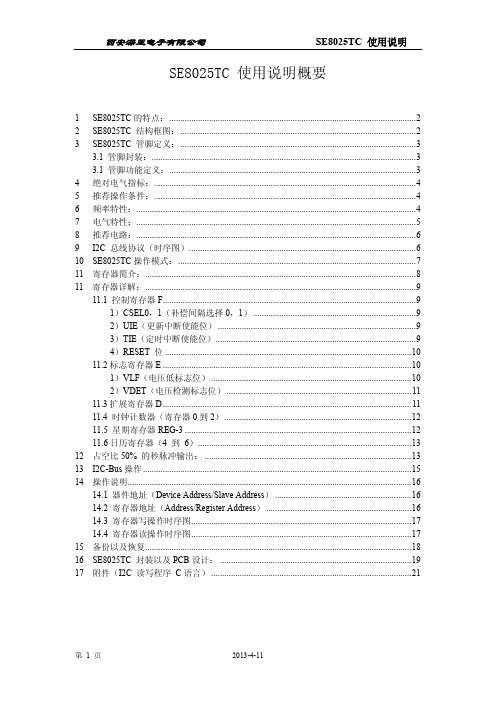
SE8025TC 使用说明
SE8025TC 使用说明概要
1 2 3 SE8025TC 的特点: ................................................................................................................ 2 SE8025TC 结构框图: ........................................................................................................... 2 SE8025TC 管脚定义: ........................................................................................................... 3 3.1 管脚封装:........................................................................................................................ 3 3.1 管脚功能定义:................................................................................................................ 3 绝对电气指标:..............................................................................................................
802说明书
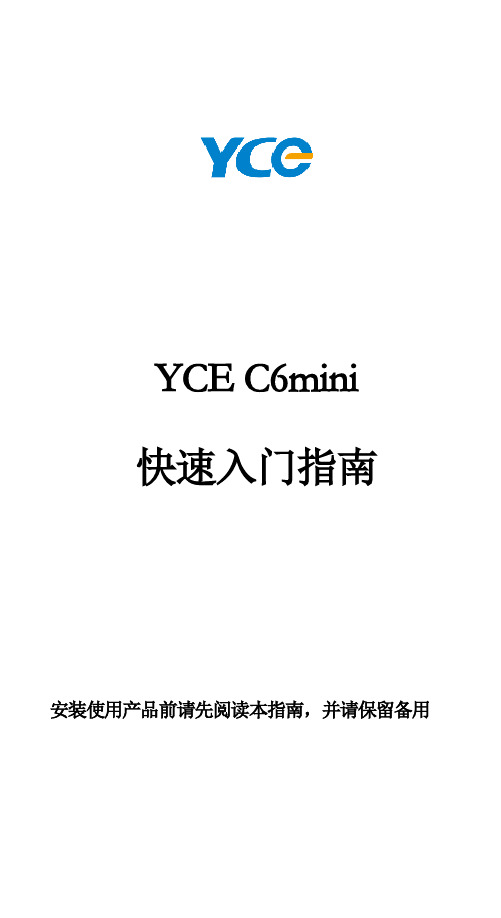
YCE C6mini快速入门指南安装使用产品前请先阅读本指南,并请保留备用欢迎使用YCE手机!感谢您选择本公司数字移动电话。
POMP C6mini是由强大团队倾情打造,为您提供高品质的移动通信和娱乐体验。
●您可以通过阅读本手册,全面地了解本智能手机的使用,领略其完善的功能和简洁的操作方法。
使用手机前,请仔细阅读全部安全注意事项和本用户手册,以确保安全和正确使用。
●本用户手册中所用的插图仅作为示意用图,可能与手机有所不同,请以你的手机为准。
●本手册中描述的某些服务和功能取决于网络和预定服务。
●收发信息、上传和下载、进行同步和使用定位服务等可能会产生其他费用。
如欲避免产生额外费用,请选择合适的实际收费计划。
有关详细信息,请联系服务运营商。
安全警告和注意事项将手机放在儿童和宠物等接触不到的地方。
以防可能吞下小零件导致窒息或发生危险。
安全开机,当禁止使用手机或手机的使用会引起干扰或危险时,请不要开机。
请遵守当地的所有相关法律法规。
请使用双手驾驶汽车。
开车时使用手机应首先考虑交通安全。
所有的无线设备都可能受到干扰,从而影响性能。
在医疗或卫生保健机构可能会使用对无线频率敏感的设备。
在飞机上应关机。
请遵守任何的相关的限制规定。
无线设备会对飞机产生干扰。
在加油站或靠近燃料、化学制剂的地方,请不要使用手机。
注意:●您的手机只能使用本公司指定的电池和充电器。
使用其它的产品可能会造成电池漏液、过热、爆裂和起火。
●请使用220V交流电。
使用其它电压会引起漏电、起火和对手机及充电器的损坏。
●禁止短路充电器,否则会引起触电、冒烟和对充电器的损坏。
●请不要在电源线损坏的情况下使用充电器,否则会导致起火和触电。
●请不要拆卸或改装充电器,否则会导致人身伤害、触电、起火和充电器损坏。
●拔插头时要抓住充电器,拉电源线会损坏电线,引起触电和起火。
●手机、电池和充电器无防水性能,请勿在浴室等高湿度的地方使用,同样也要避免被雨淋湿。
●用柔软的干布清洁手机、电池和充电器。
NCR RealPOS 80硬件用户手册说明书

NCR RealPOS 80 hardware user ManualNCR RealPOS 80Release 1.0Hardware User's GuideB005-0000-1440Issue Av Table of ContentsChapter 1: Product OverviewIntroduction...........................................................................................1-1 Cabinet.............................................................................................1-2Configurations................................................................................1-4Integrated Terminal...................................................................1-4Integrated Terminal w/Cash Drawer.....................................1-5Left/Right Configurability.......................................................1-6 Serial Number/Model Number Label...............................................1-7Features..................................................................................................1-8 Processor Board..............................................................................1-84-Port USB Daughter Card............................................................1-9ATX Riser Card...............................................................................1-9Front Control Panel......................................................................1-10Storage Media...............................................................................1-10Power Supply................................................................................1-11Operating Systems.......................................................................1-11UPS.................................................................................................1-11 Power Management............................................................................1-12 Definitions of the states involved...............................................1-13 Operator Displays...............................................................................1-17 5964 12.1-Inch Touch Screen.......................................................1-17Features.....................................................................................1-175942 12.1-INCH Color LCD.........................................................1-197452-K309/K404 9-Inch Monochrome CRT..............................1-207452-K419 15-Inch Color CRT.....................................................1-20NCR 5982 5-Inch LCD Display...................................................1-21 NCR 5953 12.1-Inch DynaKey...........................................................1-22viNCR 5952 10.4-Inch DynaKey...........................................................1-23NCR 5932 Keyboards.........................................................................1-24109-Key USB Keyboard...............................................................1-24Features.....................................................................................1-25115-Key PS/2 Big Ticket Keyboard............................................1-2668-Key PS/2 POS Keyboard........................................................1-27Features.....................................................................................1-27NCR 5972 2x20 Remote Customer Display.....................................1-31Features..........................................................................................1-31NCR 5973 2x20 International VFD Customer Display..................1-32Features..........................................................................................1-32Printers.................................................................................................1-33NCR 7158 Printer..........................................................................1-33NCR 7162 Printer..........................................................................1-34NCR 7194 Printer..........................................................................1-34NCR 7167 Printer..........................................................................1-35NCR 7197 Printer..........................................................................1-35System Configuration Diagrams......................................................1-36Chapter 2: Hardware InstallationIntroduction...........................................................................................2-1Installation Restrictions.................................................................2-1Installing the Integration Tray............................................................2-2Installing the Keyboard........................................................................2-3PS/2 Keyboard/Mouse Cable Connections...............................2-5Dual Port Keyboard/Mouse Installation................................2-5Mouse Installation Restriction..................................................2-5Installing the Integrated Operator Display.......................................2-6Operator Display Cable Connections........................................2-10Installing an NCR 5964 12.1-inch Touch LCD.....................2-10Installing a 5942 12.1-Inch LCD Monitor..............................2-13viiInstalling the Integrated Customer Display....................................2-14 Installing the Transaction Printer.....................................................2-16 Printer Cable Connections...........................................................2-18USB Installation........................................................................2-18RS-232 Installation w/Power from Powered USB..............2-19 Installing an NCR 5972 Remote Customer Display.......................2-20 Customer Display Cable Connections.......................................2-21 Installing an NCR 5973 Remote Customer Display.......................2-22 Customer Display Cable Connections.......................................2-23 Installing a 5953 DynaKey.................................................................2-24 Installing a 5952 DynaKey.................................................................2-25 Installing a Secondary CRT Display (Dual Display)......................2-26 Installing the Hardware...............................................................2-26Supported Configurations......................................................2-26Supported Configurations by Operating System................2-27Supported Hardware Configurations...................................2-27Installing the Displays.............................................................2-28Configuring the Software for Dual Display..............................2-29 Installing an NCR 5982 5-Inch Operator Display...........................2-30 Installing the PCI LCD Board (5952-K052)................................2-31Connecting the 5982 Display to the Terminal......................2-32 Installing a Cash Drawer...................................................................2-33 Installing a Second Cash Drawer...........................................2-33Chapter 3: SetupIntroduction...........................................................................................3-1 Entering Setup Using a Keyboard......................................................3-1 How to Select Menu Options..............................................................3-1 Restoring Factory Settings...................................................................3-2 Special DynaKey Keypad Mode.........................................................3-2 Normal DynaKey Keypad Operating Mode..............................3-4viiiDisabling Resources..............................................................................3-5BIOS Default Values.............................................................................3-5Main Menu......................................................................................3-5Advanced Menu.............................................................................3-8Security Menu...............................................................................3-12Power Menu..................................................................................3-12Boot Sequence...............................................................................3-12Chapter 4: Operating System RecoveryIntroduction...........................................................................................4-1Prerequisites....................................................................................4-1Connecting an External Backpack CD-ROM Drive...................4-2Updating Procedures.....................................................................4-3Completing the OS Installation (Windows 2000)..................4-5Completing the OS Installation (Windows NT 4.0)..............4-5Completing the OS Installation (Windows EXe)...................4-6Completing the OS Installation (DOS)....................................4-6Gold Disk Contents...............................................................................4-7NCR 7456/58 Windows 2000 Operating System RecoverySoftware (LPIN: D370-0536-0100).................................................4-7Installed Software:.....................................................................4-7Software Drivers.........................................................................4-8Special Settings...........................................................................4-8Recommendation.......................................................................4-9NCR 7456/58 Windows NT 4.0 Operating SystemRecovery Software (LPIN: D370-0564-0100)............................4-10Installed Software:...................................................................4-10Software Drivers.......................................................................4-10Special Settings.........................................................................4-11Recommendation.....................................................................4-12ix NCR RealPOS 80/80c Windows XPe Operating SystemRecovery Software (LPIN: D370-0570-0100).............................4-13Installed Software:...................................................................4-13Software Drivers.......................................................................4-13Special Settings.........................................................................4-14Recommendation.....................................................................4-14 OS Recovery from a Larger Disk Image..........................................4-15Chapter 5: BIOS Updating ProceduresIntroduction...........................................................................................5-1 Prerequisites....................................................................................5-1Connecting an External Backpack CD-ROM Drive...................5-2Updating Procedures.....................................................................5-3 BIOS Crisis Recovery............................................................................5-5 Recovery Procedures......................................................................5-6 Cable/Connector Pin-Out Information.............................................5-9Chapter 6: Memory DumpGeneral Memory Dump Information.................................................5-1 BIOS Requirements........................................................................5-1Disk Format.....................................................................................5-1Supported Operating Systems......................................................5-2Summary of Operating Systems..............................................5-3Prerequisites....................................................................................5-3Windows XP/2000.....................................................................5-4Windows NT...............................................................................5-5 DOS Memory Dump Specifics............................................................5-6 Dump Process Overview...............................................................5-6Restrictions and Limitations.........................................................5-6Performing the Memory Dump....................................................5-9Configuring the Terminal.........................................................5-9xDump Procedure........................................................................5-9Tunes/Tones.............................................................................5-10Moving the Files to Hard Disk and Reassembling..............5-12Flow Chart.................................................................................5-13Memory Dump Assembler..........................................................5-14Appendix A: Retail Keyboard Key Layouts68-Key Keyboard..................................................................................A-1DynaKey.........................................................................................A-4Special DynaKey Keypad Mode.............................................A-4Normal DynaKey Keypad Operating Mode.........................A-65932 USB Keyboard.......................................................................A-7 Appendix B: Feature KitsAppendix C: CablesPrinter Cables.......................................................................................C-1Scanner Cables......................................................................................C-37872 or 7875 Scanner/Scale (RS-232)..........................................C-37872 or 7875 Scanner/Scale (Powered USB)..............................C-37892 Scanner (Powered RS-232)..................................................C-37882 Scanner (Powered RS-232)..................................................C-47837 Scanner (Powered RS-232)..................................................C-4Display Cables......................................................................................C-5VGA Display, Mono......................................................................C-5VGA Display, Color......................................................................C-5CRT AC Power Extension............................................................C-55982 5-Inch LCD............................................................................C-65953 DynaKey................................................................................C-65953 DynaKey w/Insert...............................................................C-6Wedge Keyboard Y-Cable............................................................C-7xi5972 VFD Customer Display (Powered RS-232).......................C-7DVI to DVI for 5964.......................................................................C-7PS/2 - RS-232 & Power for 5964..................................................C-8Wedge Keyboard Adapter...........................................................C-812.1-Inch LCD Aux Power Cable................................................C-8Cash Drawer Cables............................................................................C-9 Dual Cash Drawer, Y-Cable.........................................................C-9Cash Drawer, Extension Cable....................................................C-9 Ethernet Communications Cable.......................................................C-9 Keyboard Cables................................................................................C-10 PS/2 Keyboard Extension..........................................................C-10PS/2 Y-Cable................................................................................C-10 Signature Capture/Electronic Payment Terminal Cable.............C-11 5945/5992 EPT (RS-232 w/Power)...........................................C-115942 12V Power Cable.................................................................C-11 IDE Cables...........................................................................................C-12 IDE Interface Cable (3-Connector)............................................C-12IDE Interface Cable (2-Connector)............................................C-12 Compact Flash Power Cable.............................................................C-12 Power Cables......................................................................................C-13 AC Power......................................................................................C-13Appendix D: Memory MapDOS Considerations............................................................................D-2 Non-TAPS DOS Environment.....................................................D-3TAPS DOS Environment..............................................................D-3This is a “Table of Contents preview” for quality assuranceThe full manual can be found at /estore/catalog/ We also offer free downloads, a free keyboard layout designer, cable diagrams, free help andsupport. : the biggest supplier of cash register and scale manuals on the net。
MA801_MA802_A9

6. 存储器组织................................................................................................... 19
7. 数据指针寄存器(DPTR)................................................................................ 23 8. 系统时钟 ...................................................................................................... 24
2012/11 version A9
2
MA801_MA802 1 中央处理器 MA801_MA802 8K 字节 Flash ROM ━ ISP 存储空间可以选择 1.0KB, 2.0KB 或 3.0KB ━ 用于 Flash 存储器访问的两级代码保护 ━ Flash 写/擦除周期: 20,000 ━ Flash 数据保留时间: 在 25℃下 100 年 片上 256 字节暂存 RAM 中断控制器 ━ 7 个中断源,4 级优先级 ━ 两个外部中断输入,INT0 和 INT1 两个 16 位定时/计数器, Timer 0 和 Timer 1. ━ Timer 0/1 可以选择 X12 模式 可编程的 16 位计数/定时阵列(PCA) 支持 2 通道 PWM ━ 捕获模式 ━ 16 位软件定时器模式 ━ 高速输出模式 ━ 8 位 PWM 模式 增强型 UART (S0) ━ 帧错误检测 ━ 自动地址识别 8 位 ADC ━ 可编程吞吐率达到 100 ksps ━ 8 通道单端输入 主/从 SPI 串行接口 可编程看门狗定时器,由 CPU 或上电一次使能。 在 20 脚封装下最多 15 个 GPIO。 ━ 可以配置成双向口,推挽输出,漏极开路和仅输入 多种电源控制模式:空闲模式和掉电模式 ━ 所有中断可以唤醒空闲模式 ━ 2 个源可以唤醒掉电模式 低压侦测器:对于 MA801 是 VDD 3.7V ,对于 MA802 是 VDD 2.4V 工作电压范围 Operating voltage range: ━ MA801: 4.5V~5.5V, 要求 Flash 写操作最小是 4.5V (ISP/IAP) ━ MA802: 2.4V~3.6V, 要求 Flash 写操作最小是 2.7V (ISP/IAP) 工作频率范围: 25MHz(最大) ━ MA801: 0 – 25MHz @ 4.5V – 5.5V ━ MA802: 0 – 12MHz @ 2.4V – 3.6V and 0 – 25MHz @ 2.7V – 3.6V 时钟源 ━ 外部晶振模式和内置 RC 振荡器 (IRCO, 6MHz) 工作温度: ━ 工业级 (-40℃ to +85℃)* 封装类型: ━ PDIP20: MA801AE/MA802AE ━ SOP20: MA801AS/MA802AS ━ TSSOP20: MA801AT/MA802AT
SC802_08资料
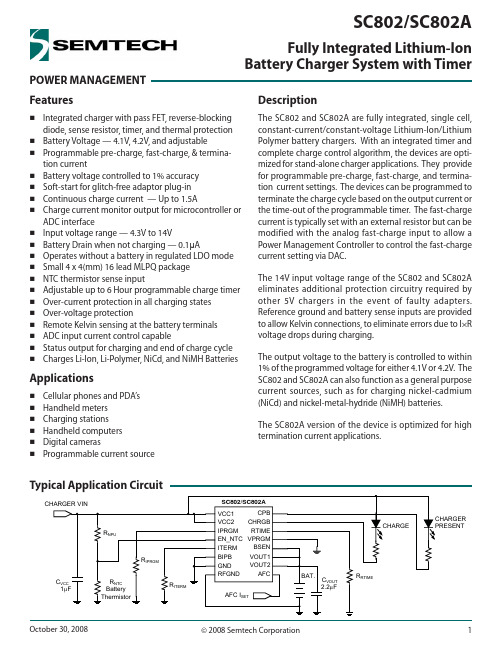
POWER MANAGEMENT Fully Integrated Lithium-Ion Battery Charger System with TimerFeaturesIntegrated charger with pass FET, reverse-blocking diode, sense resistor, timer, and thermal protection Battery Voltage — 4.1V, 4.2V, and adjustableProgrammable pre-charge, fast-charge, & termina-tion currentBattery voltage controlled to 1% accuracy Soft-start for glitch-free adaptor plug-in Continuous charge current — Up to 1.5ACharge current monitor output for microcontroller or ADC interfaceInput voltage range — 4.3V to 14VBattery Drain when not charging — 0.1μAOperates without a battery in regulated LDO mode Small 4 x 4(mm) 16 lead MLPQ package NTC thermistor sense inputAdjustable up to 6 Hour programmable charge timer Over-current protection in all charging states Over-voltage protectionRemote Kelvin sensing at the battery terminals ADC input current control capableStatus output for charging and end of charge cycle Charges Li-Ion, Li-Polymer, NiCd, and NiMH BatteriesApplicationsCellular phones and PDA’s Handheld meters Charging stations Handheld computers Digital camerasProgrammable current sourceDescriptionThe SC802 and SC802A are fully integrated, single cell, constant-current/constant-voltage Lithium-Ion/Lithium Polymer battery chargers. With an integrated timer and complete charge control algorithm, the devices are opti-mized for stand-alone charger applications. They provide for programmable pre-charge, fast-charge, and termina-tion current settings. The devices can be programmed to terminate the charge cycle based on the output current or the time-out of the programmable timer. The fast-charge current is typically set with an external resistor but can be modified with the analog fast-charge input to allow a Power Management Controller to control the fast-charge current setting via DAC.The 14V input voltage range of the SC802 and SC802A eliminates additional protection circuitry required by other 5V chargers in the event of faulty adapters. Reference ground and battery sense inputs are provided to allow Kelvin connections, to eliminate errors due to I×R voltage drops during charging.The output voltage to the battery is controlled to within 1% of the programmed voltage for either 4.1V or 4.2V. The SC802 and SC802A can also function as a general purpose current sources, such as for charging nickel-cadmium (NiCd) and nickel-metal-hydride (NiMH) batteries.The SC802A version of the device is optimized for high termination current applications.Typical Application CircuitPin Confi gurationMarking InformationOrdering InformationDevicePackageSC802IMLTRT (1)(2)MLP16 SC802AIMLTRT (1)(2)MLP16 SC802EVB (3)Evaluation Board SC802AEVB (3)Evaluation BoardNotes:(1) Available in tape and reel only. A reel contains 3,000 devices.(2) Available in lead-free package only. Device is WEEE and RoHScompliant.(3) Specify the part number when ordering.802yywwyyww = datecode802A yywwyyww = datecodeExceeding the above specifi cations may result in permanent damage to the device or device malfunction. Operation outside of the parametersspecifi ed in the Electrical Characteristics section is not recommended.NOTES:(1) VCC1 and VCC2, and VOUT1 and VOUT2, must be connected, and will be referred to collectively as VCC and VOUT, respectively. All referencesto V VCC , V VOUT , I VCC , and I VOUT refer to the common node voltage and total current of VCC1 and VCC2, and VOUT1 and VOUT2, respectively.(2) Tested according to JEDEC standard JESD22-A114-B.(3) Operating voltage is the input voltage at which the charger is guaranteed to begin operation. Maximum operating voltage is the maximumVsupply as defi ned in EIA/JEDEC Standard Number 78, paragraph 2.11.(4) Calculated from package in still air, mounted to 3 x 4.5(in), 4 layer FR4 PCB with thermal vias under the exposed pad per JESD51 standards.Absolute Maximum RatingsVCC1, VCC2, EN_NTC (V) . . . . . . . . . . . . . . . . . . . -0.3 to +14.0VOUT1, VOUT2, RTIME(V) . . . . . . . . . . . . . . . . . -0.3 to +6.0BIPB, CPB, CHRGB (V) . . . . . . . . . . . . . . . . . . . . . -0.3 to +6.0 IPRGM, ITERM, AFC (V) . . . . . . . . . . . . . . . . . . . . -0.3 to +6.0 VPRGM, BSEN (V) . . . . . . . . . . . . . . . . . . . . . . . . . -0.3 to +6.0REFGND to GND (V) . . . . . . . . . . . . . . . . . . . . . . . -0.3 to +0.3VOUT Short to GND (1) . . . . . . . . . . . . . . . . . . . . . . Continuous ESD Protection Level (2)(kV) . . . . . . . . . . . . . . . . . . . . . . . . . . . . 2Recommended Operating ConditionsAmbient Temperature Range (°C) . . . . . . . . -40 < T A < +85VCC Operating Voltage (1)(3) (V) . . . . . . . . 4.3 < V VCC1,2 < 6.5Thermal InformationThermal Resistance, Junction to Ambient (4) (°C/W) . . . . 50Maximum Junction Temperature (°C) . . . . . . . . . . . . . . +150Storage Temperature Range (°C) . . . . . . . . . . . . -65 to +150Peak IR Refl ow Temperature (10s to 40s) (°C) . . . . . . . +260Test Conditions: V VCC = 5.00V (1), V VOUT = 3.70V unless specifi ed. Typ values at 25°C. Min and Max at -40°C < T A < 85°C, unless specifi ed.ParameterSymbolConditions MinTypMaxUnitsVCC UVLO Rising Threshold VT UVLOR 3.74.0 4.3V VCC UVLO Hysteresis VT UVLOH 40mVVCC OVP Rising Threshold VT OVPR 6.5 6.87.5V VCC OVP Falling Threshold VT OVPF 6.16.57.1V VCC OVP HysteresisVT OVPH VT OVPR - VT OVPF200300500mVOperating CurrentICC DISV EN_NTC = 0V, CHRGB, CPB off 2.6mAICC CHG V EN_NTC = 0.5 × V VCC , CHRGB, CPB off 1 2.4 3.5ICC LDOLDO Mode, CHRGB, CPB off 81623Battery Leakage Current (sum of I VOUT and I BSEN )ILeak BAT V VCC = 0V, V VOUT = V BSEN = 4.5V0.12μA Regulated VoltageV CV-HI V VPRGM = V VCC 4.16 4.20 4.24VV CV_LOV VPRGM = 0V4.06 4.10 4.14REFGND Output Accuracy V VOUT_RGND V VOUT_RGND = V VOUT - V CV n , V REFGND = 30mV223038mV REFGND CurrentI REFGNDV REFGND = 0V35μA Electrical CharacteristicsParameterSymbolConditionsMin TypMax UnitsAdjust Mode Feedback Voltage V ADJMF VPRGM = External Divider, 4.2V ≤ VCC ≤ 6.5V3.0VAdjust Mode VPRGM Shunt Resis-tanceR VPGMSHAdjust Mode, V VPRGM = 0.1V0.515kΩAdjust Mode Threshold Voltage VT ADJM V VOUT - V BSEN 50250420mV SC802 Pre-Charge Current I PREQ R ITERM = 3.01kΩ748290mA SC802 Termination Current I TERMQ R ITERM = 3.01kΩ35.54249.5mA SC802 Fast-Charge Current I FastQ R IPRGM = 3.01kΩ, V VOUT = 3.8V 450500550mA SC802 AFC Fast-Charge Current I FQ_ADJ R IPRGM = 3.01kΩ, V AFC = 0.75V200240280mA SC802A Pre-Charge Current I PREQA R ITERM = 976Ω135145160mA SC802A Termination Current I TERMQA R ITERM = 976Ω135145160mA SC802A Fast-Charge Current I FastQA R IPRGM = 1.78kΩ, R ITERM = 976Ω, V VOUT = 3.8V740800860mA SC802A AFC Fast-Charge Current I FQ_ADJA R IPRGM = 1.78kΩ, R ITERM = 976Ω, V AFC = 0.75V, V VOUT = 3.8V310367430mA I PROG Regulated Voltage V IPRGM 1.44.5 1.6V V VOUT Pre-charge Threshold (2)VT PreQ measured at VOUT pins 2.7 2.8 2.9V V VOUT Re-charge Threshold (3)VT ReQ V CV (at BSEN) - V BSEN-FDBK70100140mV Over Temperature ShutdownT OT-R Hysteresis = 10°C 150°CEN_NTC ThresholdsVT NTC_DISDisable (Falling)0.5<1 1.1V RT NTC_HFNTC Hot (Falling), tested at V VCC = 5V 283032%RT NTC_CR NTC Cold (Rising), tested at V VCC = 5V 727578%RT NTC_EN Charger Enable, tested at V VCC = 5V 849092%VT NTC_HYSHot/Cold threshold hysteresis, tested at V VCC = 5V50mVTimer Disable Threshold VT TIMER V RTIME < VT TIMER Disables Timer 0.71 1.1V Internal Timer Select VT INTTS VCC-V RTIME < VT INTTS selects internal timer 1.5VExternal RTIME VoltageV RTIME RTIME tied through 36.5kΩ to GND 1.4 1.5 1.6VPre-Charge Fault Time-out T PreQFRTIME tied through 36.5kΩ to GND50minRTIME tied to VCC-35%45+35Charge Complete Time-outT QCOMPRTIME tied through 36.5kΩ to GND3.3hrRTIME tied to VCC-35%3+35Electrical Characteristics (continued)ParameterSymbolConditionsMin TypMaxUnitsCHRGB Charge LED On V CHRGB Load = 5mA 0.51V CHRGB Charge LED OFF I CHRGB Leakage Current, V = 5V1μA CPB LED On V CPB Load = 5mA 0.51V CPB LED OffI CPB Leakage Current, V = 5V1μABIPB, VPRGM InputsV IH 1.8VV IL0.4Electrical Characteristics (continued)Notes:(1) Electrical Characteristics apply for V VIN = 4.75V to 5.25V, but are tested only at V VIN = 5.00V, unless noted.(2) Pre-charge threshold is applied directly at VOUT for any setting of V CV , whether 4.1V or 4.2V fi xed, or Adjust Mode.(3) Re-charge threshold is relative to V CV as measured at BSEN. For either of the fi xed output voltage settings, V BSEN is compared directly tothe programmed CV regulation voltage. In Adjust Mode, V BSEN is compared to the Adjust Mode feedback voltage, V ADJMF . So the re-charge threshold at the battery is VT ReQ × V CV / V BSEN-FDBK .Typical CharacteristicsOutput Current (SC802) versus R IPRGM00.511.520.751 1.52 2.533.544.555.56.57R IPRGM (k ) C u r r e n t (A )I FQ501001502002500.81.52.53.54.568.51011.8514R ITERM (k )C u r r e n t (m A )I PQI TERM024681020406080T i m e -o u t (h r s )T PreQT QCOMPR RTIME(k ) 0100200300400500600700100080060050045030025020010054Output Current (mA)D r o p o u t V o l t a g e (m V )33.23.43.63.844.24.40255075100125150175200225t (minutes)V O L T A G E (V )0.10.20.30.40.50.6C U R R E N T (A )V VOUTI VOUTV CHRGBOutput Current (SC802) versus R ITERMDrop-out Voltage versus Output CurrentTime-out versus Output R RTIMEBattery Charge Profi leΩΩΩPin DescriptionsPin #Pin Name Pin Function1BSEN Battery voltage sense pin — Connect to battery terminal to Kelvin sense battery voltage, to a resistor divider network for adjustable output voltage, or to VOUT otherwise. Do not leave this pin fl oating.2VPRGM Selectable voltage program pin — Logic low = 4.1V; Logic high = 4.2V; Resistor = adjustable.3IPRGM Charger current program pin in fast-charge mode — Requires a resistor to ground to program fast-charge current.4ITERM Selection for current termination and pre-charge current — Requires a resistor to ground to pro-gram pre-charge and termination current.5REFGND Reference ground — Allows Kelvin connection to battery negative terminal. 6GND Ground7EN_NTC Combined device enable/disable and NTC input pin — Logic high enables device; logic low dis-ables device. Analog voltages between 0.3×VVCCand 0.75×VVCCenable the NTC function.8BIPB Battery In Place Bar (BIPB) — selects Charge/LDO mode. BIPB = Low selects charge mode. BIPB = High selects LDO mode which disables Pre-Charge and timer functions9AFC Analog fast-charge setting — Connect to DAC for analog control of fast-charge current value. Connect to VCC to disable AFC. Do not leave open.10CHRGB Open drain charger status pin — The output is active low when the charger is on and IVOUT> ITERM. The CHRGB output switches to high impedance when IVOUT< ITERM. This pin can sink 10mA.11CPB Open Drain Charger present indicator — The output is active low when the VVCCexceeds VTUVLOR. This pin can sink 10mA.12RTIME Programmable timer input pin — Connect to VCC to select the internal time-out of 3hrs. Connect an external resistor to ground to program the timeout period. Connect to ground to disable the timer.13VCC1Supply pin — Connect to adaptor power and to VCC2. (1) 14VCC2Supply pin — Connect to adaptor power and to VCC1. (1) 15VOUT1Charger output — Connect to battery and to VOUT2. (2) 16VOUT2Charger output — Connect to battery and to VOUT1. (2)T ThermalPad Pad is for heatsinking purposes — The thermal pad is not connected internally. Connect exposed pad to ground plane using multiple vias.Notes:(1) VCC1 and VCC2 must be connected. VCC1 and VCC2 will be referred to collectively as VCC. All references to VVCC and IVCCrefer to the commonnode voltage and total current of VCC1 and VCC2.(2) VOUT1 and VOUT2 must be connected. VOUT1 and VOUT2 will be referred to collectively as VOUT. All references to VVOUT and IVOUTrefer to thecommon node voltage and total current of VOUT1 and VOUT2.Block DiagramVCCBIPBBSENAFCEN-NTCRTIM CPB CHRGB REFGNDVPRGM GNDGeneral OperationThe SC802 and SC802A can be confi gured independently with respect to fast-charge and termination current, output voltage, timing, and operation with and without a battery (LDO mode). A typical charging cycle is described in this section. Details on alternate applications and output programmability are covered in subsequent sec-tions. Wherever the SC802 and SC802A descriptions are the same, the part will be referred to as the SC802/A.The charging cycle begins when the adapter is plugged in. The SC802/A performs glitch fi ltering on the VCC input and initiates a charge cycle when V VCC > VT UVLOR . The CPB and CHRGB signals turn on the charger LED’s. If the battery voltage is less than 2.8V, the SC802/A will charge the output with the pre-charge current. When the battery voltage exceeds 2.8V, the SC802/A enters fast-charge or Constant Current (CC) regulation. When the battery voltage reaches its fi nal value, the charger enters Constant Voltage (CV) regulation. The CV regulation output voltage, (V CV ), can be programmed to fixed values V CV-HI = 4.2V, V CV-LO = 4.1V, or programmed to any voltage V CV-ADJ using the available Adjust Mode. In CV regulation the battery accepts decreasing current until the output current (I VOUT ) reaches the programmed termination current, designated (I TERM ).When I VOUT < I TERM , an event known as charge termination, the CHRGB status indicator turns off, but the SC802/A continues to hold the battery in CV regulation until the timer cycle is completed. At this point the charger enters the monitor state where the output remains off until V VOUT drops by VT ReQ , nominally 100mV, and a new charge cycle is initiated.Termination CurrentWhen the battery reaches the CV voltage (V CV ), the charger transitions from a constant current source to a constant voltage source. The current through the battery begins to decrease while the voltage remains constant until the current decreases below the programmed termination current set by the ITERM pin resistance to ground. Upon termination, the SC802/A will turn off the CHRGB status indicator. If the timer is enabled, the output will remain in CV regulation until the timer cycle is complete. If the timer is disabled, then the output will turn off as soon as the termination current level is reached. The terminationcurrent is programmed according to the following equations. 88R 5.1I ITERMTERM u (SC802)97R 5.1I ITERMTERM u(SC802A)The termination current is programmable up to 67mA for the SC802, and up to 150mA for the SC802A.Pre-ChargePre-charge regulation is automatically enabled when the battery voltage is below the pre-charge threshold, VT PreQ , nominally 2.8V. Pre-charge is required to precondition the battery for fast-charging, and to limit the power dis-sipation in the charger. The pre-charge current value, I PQ , is determined by the ITERM pin resistance to ground. The pre-charge current is programmable from 10mA to 125mA with the SC802, and up to 150mA with the SC802A. The pre-charge current is given by the following equations. 88R 8.2I ITERMPQ u (SC802) 97R 5.1I ITERMPQ u(SC802A)If the charge timer is enabled, a pre-charge timer is also enabled. If the pre-charge time exceeds 1/4 of the pro-grammed total charge time, the charger will turn off and a pre-charge fault will be indicated by blinking the CHRGB status indicator. This fault is cleared when the charger is disabled (by grounding the EN_NTC pin), or the VCC input voltage is cycled, or the output voltage rises above 2.8V.Fast-ChargeFast-charge or CC regulation is active when the battery voltage is above VT PreQ and less than V CV , the fi nal fl oat charge voltage of the battery. The fast-charge current can be set to a maximum of 1.5A and is selected by the program resistor on the IPRGM pin. The voltage on this pin represents the current through the battery. It enables a microprocessor via an Analog-to-Digital Converter (ADC) to monitor battery current by sensing the voltageApplications InformationApplications Information (continued)on the IPRGM pin. The fast-charge current is given by the following equations. 1000R 5.1I IPRGM FQ u (SC802)TERM IPRGMFQ I 3.01000R 5.1I u u(SC802A)Note that for a given program resistor the current throughthe battery in CV regulation can be determined by replac-ing 1.5 with the actual voltage on the IPRGM pin in the equations. In the case of the SC802A, the I TERM term applies only prior to termination (while CHRGB is low), and should be excluded following termination. The CC current can also be modified by applying an analog voltage to the AFC pin as described in the next section.Analog Fast-ChargeMany applications require more than one current setting for fast-charge. This feature is included in the SC802/A by using the AFC function. When the AFC pin is connected to VCC the SC802/A operates as described in the previous section. When the AFC pin is driven by an analog voltage between 0 and 1.5V the SC802/A automatically uses this pin voltage to set the maximum fast-charge current setting according to the following equation. 1000R V I IPRGMAFCAFQ u (SC802)TERM IPRGMAFCAFQ I 3.01000R V I u u(SC802A)Monitor StateWhen a charge cycle is completed, the SC802/A output turns off and the device enters monitor state. If the voltage of the battery falls below the re-charge voltage of V CV − VT ReQ , nominally 100mV below V CV , the charger will clear the charge timer and re-initiate a charge cycle. The maximum current drain from the battery during monitor state is less than 1μA over temperature. The status of the charger output as a function of BIPB, timer status, and I VOUT in the following table.Output StateBIPBTimerI VOUTOn High N/A N/A OnLowt < T QCOMPN/A Off Low t > T QCOMP N/AOff LowDisabled< I TERMCharge TimerThe timer in the SC802/A provides protection in the event of a faulty battery, and maximizes charging capacity. Connect the RTIME pin to VCC to select the internally programmed timer, and to GND to disable the timer. Connecting a resistor between the RTIME pin and GND will program the total charge complete time T QCOMP according to the following equation.R RTIME (kΩ) = T QCOMP (hours) x 12.5 (kΩ/hour)The timer is programmable over the range of two to six hours. The internal timer selection provides a charge time of three hours. The SC802/A automatically turns off the output when the charge timer times out, and then enters the Monitor State. A re-charge cycle resets and restarts the timer.Note that the CHRGB fault indication blink rate is a func-tion of the timer setting, whether externally programmed or set internally. When the timer is disabled, the blink rate is the same as if the timer were internally set.EN_NTC InterfaceThe EN_NTC pin is the interface to a battery pack temper-ature sensing Negative Temperature Coefficient (NTC) thermistor. It can be used to suspend charging if the battery pack temperature is outside of a safe-to-charge range. The EN_NTC interface also serves as a charger disable or NTC–unconditional enable input.The recommended EN_NTC network is a fixed-value pullup resistor (designated R NPU ) from the EN_NTC pin to the VCC pins, and the battery pack NTC thermistor (desig-nated R NTC ) from the EN_NTC pin to ground. In this con-fi guration, shown in the Typical Application Circuit onpage 1, an increasing battery temperature produces a decreasing NTC pin voltage, designated V EN_NTC .When V EN_NTC is greater than the high (cold) threshold (but below the Charger Enable threshold) or less than the low (hot) threshold (but above the Disable threshold), the charge cycle is suspended, turning off the output. This suspends but does not reset the charge timer, and indi-cates a charging fault by blinking the CHRGB status indi-cator. Hysteresis is provided for both high and low NTC thresholds to avoid chatter at the NTC temperature fault thresholds. When V EN_NTC returns to the Temperature-OK-to-Charge range, the charge timer resumes, CHRGB is asserted (pulled low), the charging output is enabled, and the charge cycle continues. The timer will expire when the output on-time exceeds the timer setting, regardless of how long it has been disabled due to an NTC fault.All EN_NTC input thresholds are proportional to the VCC pin voltage (V VCC ). When the recommended external NTC circuit is used, the external EN_NTC pin voltage is also proportional to V VCC , varying with the thermistor resis-tance. This ensures that all EN_NTC thresholds are insensi-tive to V VCC . The ratiometric hot and cold thresholds are given by the parameters RT NTC_HF and RT NTC_CR . V EN_NTC between RT NTC_HF ×V VCC and RT NTC_CR ×V VCC indicates the battery temperature is safe to charge, and enables charg-ing. See the following table.EN_NTC Pin Ratiometric Thresholds% of V VCCRangeV EN_NTC Ratiometric ThresholdsRT NTC_EN = 90%Charger Enable NTC Cold FaultRT NTC_CR = 75% NTC Temperature-OK-to-Charge RT NTC_HF = 30% NTC Hot Fault RT NTC_DIS = 1VCharger DisableWhen V EN_NTC < 1V approximately, the SC802/A charger is disabled. This allows the system controller to asynchro-nously disable or reset the device by pulling EN_NTC to ground, using for example an n-channel FET. When dis-abled, the charger is turned off , the charge timer is reset,Applications Information (continued)and CHRGB is turned off (high). The behavior of CPB diff ers between the SC802 and SC802A when the device is disabled. See the Status Indicators section.Charger Enable is selected when the battery (along with the thermistor) is removed, determined by the NTC pin exceeding RT NTC_EN × V VCC , nominally 90% of the VCC pin voltage. Charger Enable behaves identically to NTC safe-to-charge. Charger Enable also provides a convenient means to operate the SC802/A in applications without a battery thermistor, without requiring a passive resistor network to obtain 50% of V VCC . Connect EN_NTC directly to VCC, or via a pullup resistor if it will be necessary to disable the charger by pulling EN_NTC to ground.The response of the SC802/A to an EN_NTC pin voltage above the NTC Cold Fault threshold (but below RT NTC_EN ) or below the low NTC Hot Fault threshold (but above VT NTC_DIS ) is the same. Therefore the EN_NTC network can be confi gured with the battery pack thermistor between EN_NTC and VCC, and a fi xed resistor between EN_NTC and ground, reversing the designation of the hot and cold thresholds. This confi guration may be used to disable the charger when the battery pack is removed.For detailed design guidance for ratiometric NTC inter-faces, including thermistor selection guidelines, see the Semtech Application Note AN–PM–0801, NTC Thermistor Network Design for Ratiometric Thresholds .Status IndicatorsThere are two status indicator outputs on the SC802/A — CHRGB (Charge) and CPB (Charger Present). These outputs are open drain n-channel MOSFET drivers suit-able for driving LEDs directly. The following table defi nes each output state.Applications Information (continued)Status IndicatorON (active low)OFF (inactive high)BlinkingCPB UVLO < V VCC < OVPPower Not GoodXCHRGBI OUT > I TERM I OUT < I TERM (1)Pre-charge or NTC fault(1) Output remains on when timer is enabled and t < T QCOMP .The CPB output can be used as a VCC–valid detector. When V VCC is between the UVLO and OVP thresholds the CPB output is low. In the SC802, the CPB output refl ects the voltage of the VCC input regardless of the voltage V EN_NTC . In the SC802A, the CPB output becomes inactive (high) when the charger is disabled, regardless of V VCC .The CHRGB output signifi es the charging status. When I VOUT > I TERM , CHRGB is driven low. CHRGB is high when I VOUT < I TERM . The CHRGB output is latched during the charge cycle when the output current is less than I TERM . This latch is reset when the battery enters a re-charge cycle, or if BIPB, EN_NTC, or VCC are toggled. The CHRGB indicator operates the same way in both charging and LDO modes.The five fault conditions detected by the SC802/A are input under-voltage, input over-voltage, NTC temperature fault, maximum die over-temperature (OT) fault, and pre-charge timeout. The status indicator states for these fault conditions are shown in the following table.FaultCPBCHRBVCC UVLO or VCC OVP OFF OFF NTC Fault ON Blinking Pre-Charge Time-outON Blinking TJ > 150ºCOFFOFFConfi guring the Output Voltage to the BatteryV CV Fixed ModeThe battery voltage is set by the VPRGM pin in fi xed mode and externally in the adjust mode. If VPRGM is logic high the output voltage is set to 4.2V. If this pin is logic low the output voltage will be set to 4.1V. For a value other than 4.1V or 4.2V a resistor divider is required.V CV Adjust ModeV CV Adjust Mode permits confi guring the SC802/A for V CV other than 4.1V or 4.2V. In V CV Adjust Mode the CV regula-tion voltage is set by an external resistor divider. The SC802/A Adjust Mode schematic is shown in Figure 1. The SC802/A provides the capability, via the VPRGM pin, to disconnect the external feedback resistor divider when the charging source is removed, to reduce current drain from the battery through the resistor network. Connect the external resistor divider between the VOUT pins andFigure 1. V CV Adjust Mode programming.the VPRGM pin with the divider tap connected to the BSEN pin to utilize this feature. The Adjust Mode CV regulation voltage is set by the following equation.0.3R R 1V LO ADJ HI ADJ ADJ CV u ¸¸¹·¨¨©§ To ensure detection of V CV Adjust Mode, R ADJ–HI should beat least 130kΩ. The capacitor across R ADJ–HI in the feedback network provides zero-pole frequency compensation for stability. Place the zero according to the following equa-tion to ensure stability.kHz10021C R ADJ HI ADJ u Su In V CV Adjust Mode, V CV–ADJ must satisfy V VCC > V CV–ADJ + 150mV to ensure regulation. If V VCC approaches V CV–ADJ , V CV–ADJ will drop out such that V CV–ADJ will be approximately V VCC – 150mV.LDO ModeThe SC802/A can operate with or without a battery. If the battery is not in place the device can enter LDO Mode. The input pin BIPB is used to switch the SC802/A from charger mode to LDO mode. If this pin is driven logic high the device will be in LDO mode, if it is logic low it will be in the charger mode. The BIPB pin should never be left fl oat-ing. It should be tied through pull-up or pull-down resis-tors when connected to a high impedance control pin or it can be connected directly to the VCC pin or GND.In LDO Mode the SC802/A will function as a low dropout voltage regulator. The EN_NTC pin functions remain active, and the status indicators are active, including the CHRGB indicator. The timer is inactive. The output remains enabled even when I VOUT < I TERM . The output voltage can be set to 4.1V, 4.2V or externally set by a resistor divider, with a current limit equal to I FQ . The pre-charge threshold is ignored.Remote Kelvin Sensing at the BatteryKelvin sensing of both the positive and negative terminals of the battery is available on the SC802/A. The BSEN pin provides the positive sensing voltage feedback to the CV amplifi er and should be connected as close to the batterypositive terminal as possible. The REFGND pin should be Kelvin connected to the negative terminal of the battery. This provides maximum fl exibility in PCB layout. This also results in a greater accuracy in sensing the battery voltage at the battery terminals. When laying out the PCB the designer should route the BSEN pin directly to the battery terminal connections. (For Adjust Mode, the high-side resistor should be connected directly to the battery termi-nal connections.) In LDO mode, as in Charging mode, the BSEN pin must sense the output voltage, so BSEN should never be left unconnected.Over-Current and Max Temperature ProtectionOver-current protection is inherent in all modes of opera-tion. When the device is in charge-mode (BIPB=low) the output is current limited to either the pre-charge current limit value or the fast-charge current limit value depend-ing on V VOUT . When the device is in LDO mode (BIPB = high) the output current is limited to the fast-charge current limit. Maximum die temperature protection is provided on the SC802/A. This feature allows the SC802/A to operate with maximum power dissipation by disabling the output current when the die temperature reaches the over temperature limit. The device will then operate as a pulse charger in extreme power dissipation applications, delivering the maximum allowable output current while regulating the internal die temperature to a safe level.Capacitor SelectionLow cost, low ESR ceramic capacitors such as the X5R and X7R dielectric material types are recommended. The VOUT pin capacitance range is typically 1μF to 4.7μF, but C VOUT can be as large as desired to accommodate the required input capacitors of regulators connected directly to the battery terminal. The VCC pin input capacitor C VCC is typically between 0.1μF to 1μF , but larger values will not degrade performance. Capacitance must be evaluated at the expected bias voltage (V CV for C VOUT , the expected VCC supply regulation voltage for C VCC ), rather than the zero-volt capacitance rating.Applications Information (continued)。
中文48250092

十进制 十六进 字长 原文 地址 制地址
866 868 870 872 362 364 366 368 2 2 2 2
脉冲输入1 脉冲输入2 脉冲计量数量 电流报警: 0 : 无报警 1 : 电流 2 : 线电压 3: 正向总有功功率 4: 正向总无功功率 5: 视在功率 6: 频率 7 : 感性功率因数 8 :电流谐波畸变率 thd I 9 : 电压谐波畸变率thd U 10 :中性线电流 In 11 : 运行时间 12 : 相电压V 13 :中性线电流谐波畸变率 thd In 14 :中性线电压谐波畸变率thd V 15 :负向总有功功率 16 : 负向总无功功率 17 : 容性总功率因数 电流超限报警 0 : 无报警 1 : 电流 2 : 线电压 3: 正向总有功功率 4: 正向总无功功率 5: 视在功率 6: 频率 7 : 感性功率因数 8 :电流谐波畸变率 thd I 9 : 电压谐波畸变率thd U 10 :中性线电流 In 11 : 运行时间 12 : 相电压V 13 :中性线电流谐波畸变率 thd In 14 : 中性线电压谐波畸变率thd V 15 : 负向总有功功率 16 : 负向总无功功率 17 : 容性总功率因数 输入/输出个数 低位:输入个数 高位:输出个数 输入/输出状态 0位 : 输入1状态 (0 =开, 1 = 合) 1位 : 输入2状态 (0 =开, 1 = 合) 2位 : 输入3状态 (0 =开, 1 = 合) 3位: 输入4状态 (0 =开, 1 = 合) 4位: 输入5状态 (0 =开, 1 = 合) 5位: 输入6状态 (0 =开, 1 = 合) 15位: 输出1状态 (0 =开, 1 = 合) 16位: 输出2状态 (0 =开, 1 = 合) 17位: 输出3状态 (0 =开, 1 = 合) 18位: 输出4状态 (0 =开, 1 = 合) 19位: 输出5状态 (0 =开, 1 = 合) 20位: 输出6状态 (0 =开, 1 = 合)
802说明书
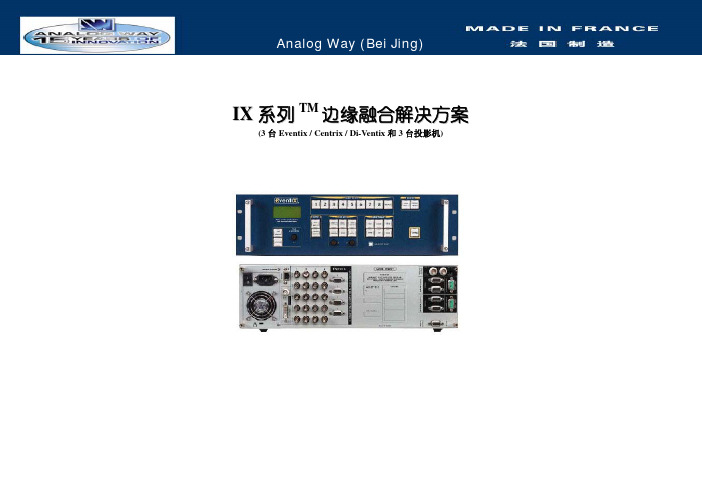
Analog Way (Bei Jing)
效果: 切换,画中画,淡入淡出,字幕,擦除
- SDTV(15KHz):SDI,YUV, 分量信号,S.VIDEO, 复合视频 NTSC/PAL
用户控制: 前面板配置齐全 - 4 行显示 LCD,直观的菜单显示,可以完成输入输出设置和图象控制。 - 高质量按钮: - 输入选择 - 用户可控排序转换效果 - 图象切换 - 冻结图象画面 - LOGO,图象&画中画水平&垂直位置调整 可通过远程控制台或提供的软件进行完全控制。
Analog Way (Bei Jing)
技术参数:
8 路通用视频输入: ·复合视频
NTSC=15.735KHz/60Hz PAL/SECAM=15.625KHz/50Hz ·S.VIDEO(Y/C) ·分量视频(YUV) 525L/625L ·RGB/S(TTL 或 0.3V Analog) RGsB(SOG:0.3V Analog ) ·计算机信号(RGBHV,RGB/S,RGsB):PC,MAC,工作站。 自动同步锁定及标定分辨率从 640*480 到 1600*1280(最高到 110Hz 的刷新率)。 ·HDTV:分量(HD YUV 3 级同步) 1080i/60Hz,720p/60Hz,480p/60Hz ·选配: - SDI-4:2:2(10 bit) - DVI 最高至 UXGA
特点:
·主输出&预览输出的混合模式 ·内置矩阵模式:8 路输入到 2 路定标输出 ·8 路通用输入(可高至 UXGA,Video,HDTV)
802说明书
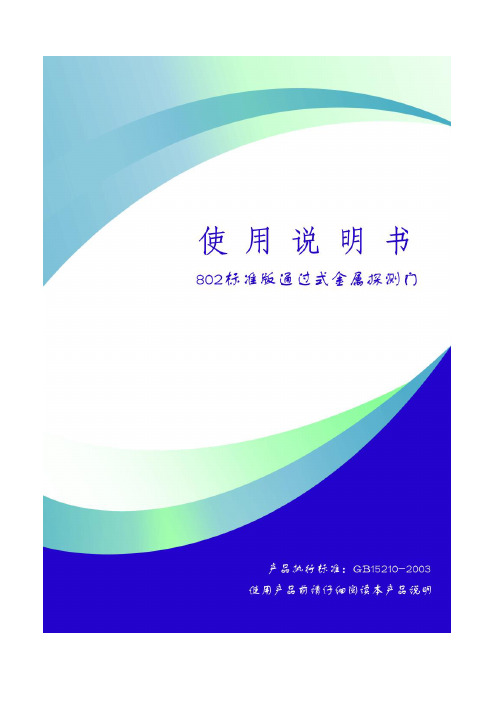
目录前言 (1)产品概述 (2)产品性能 (2)部件介绍 (3)安装说明 (4)显示面板说明 (5)参数设置 (5)操作简图 (9)物件探测调节 (10)装箱清单 (10)技术参数 (11)注意事项 (12)常见故障及解决办法 (12)干扰说明 (13)前言首先,感谢你购买本公司的金属探测门!!!本说明书对本产品进行了充分的描述与说明,在使用本产品前,您可以花一小段时间来阅读本说明书,这样您可以更了解本产品的性能,更好的去操作,同时您也能看到本产品更好的性能。
金属探测门可以应用于机场,监狱,考场,工厂等场所,对通过的人体进行准确检测身上是否携带金属物品。
本说明书对通过式金属探测门的安装与使用进行了详细的说明。
适用对象为使用产品客户,了解产品潜在客户等群体。
注意:本公司有权对本说明书及产品进行变更,如有变更,恕不另行通知。
本说明书编制过程中力求内容的准确和完善,但不保证本说明书没有任何错误或漏失,若有错误与缺失之处,欢迎来电赐教,我们将把您的意见作为修正参考意见之一。
- 1 -- 2 -我公司生产的802标准版通过式金属探测门采用了国际先进技术,专门用于对人身上隐藏的金属及合金物品的探测防范,它安全性高,适用性强,灵敏度高,探测范围广,抗外界干扰能力强,能够全天智能工作,并可以声光同时报警,在质量,效果,技术上均达到了世界领先水平,它可以调节灵敏度,最高精确探测可以小到曲形别针大小的金属物,并可以区分人体隐藏的具体位置,用户还可以根据金属的大小,体积,重量等进行灵敏度的设置,以排除钥匙,首饰,皮带金属扣而产生的误报警,而且本产品还可以防止贵重物品的流失,如海关,生产重金属工厂,私人毫宅等地方,都可以购买本产品作为一道安全防护。
因此安装本公司生产的通过式金属探测门是你英明的选择!◆ 六个探测区域:6个相互重叠的探测区域划分,准确判断金属物品的位置。
◆ 报警区域指示:在门的两边或主机箱有与人体等高的报警部位指示灯,配和声音,一目了然,大大提高工作效率。
20-COMM-H RS485 HVAC 适配器固件版本 2.009 发行说明书

Release Note 20-COMM-H RS485 HVAC Adapter Firmware Revision 2.009This release note describes major revision 2, minor revision 9 of firmware for 20-COMM-H RS485 HV AC adapters.IntroductionThe following information is included in this document: EnhancementsThis section describes enhancements provided in this revision of firmware.•Added support for PowerFlex 750-Series drives (PowerFlex 753 and PowerFlex 755) in all three modes of operation (Modbus RTU, FLN P1, and Metasys N2) with the following limitations: –Does not support Chinese, Japanese, and Korean languages.–Cannot access drive DPI port 7 and higher.•Added support for PowerFlex 700VC drives in all three modes of operation (Modbus RTU, FLN P1, and Metasys N2).•Added new Parameter 33 - [RTU Memory Map]. This parameter sets the register mapping that the adapter uses when the adapter operates in the ‘Modbus RTU’ mode. The settings for this parameter are:–‘0’ (Legacy), the default setting, which provides Modbus register mapping that conforms to the Modbus standard specification, which is typically used by PowerFlex 7-Class drives.–‘1’ (PF4-Class) which provides Modbus register mapping that matches the register mapping used by PowerFlex 4-Class drives. This mapping reduces the programming time required for PowerFlex 7-Class drives when they are used on a network consisting mainly of PowerFlex 4-Class. For details of this register mapping, see Appendix C in the PowerFlex 4 Drive User Manual, publication 22A-UM001.Important:The register mapping provided with setting ‘1’ does not pass configured Datalinks through the adapter. Therefore, they are ignored.Topic Page Enhancements 1Corrected Anomalies 2Determining Firmware Revision 2Updating the Firmware 4Restrictions 7Compatible Revisions 8Rockwell Automation Support 8Product Satisfaction Return 8220-COMM-H RS485 HVAC Adapter Firmware Revision 2.009Corrected Anomalies There are no anomalies corrected in this revision of firmware.Determining Firmware Revision This section describes procedures to determine the firmware revision of your 20-COMM-H RS485 HV AC adapter.Using the LCD HIMUsing DriveExplorer Lite/Full Softwareunch DriveExplorer software.ing a 1203-USB or 1203-SSS converter, go online with the drive thatis connected to the adapter.3.In the DriveExplorer treeview, select the 20-COMM-H Modbus RTUadapter (see Figure 1).4.Click the information icon to display the adapter Properties screen.5.The ‘Revision’ field shows the present revision of the adapter firmware(for example, 2.008).TIP: When selecting the 20-COMM-H adapter using DriveExplorer Lite or Full software, version 5.01 or later, the adapter firmware revision is also shown in the right pane of the DriveExplorer window.20-COMM-H RS485 HVAC Adapter Firmware Revision 2.0093Figure 1 DriveExplorer Window with Information Icon and Device Properties Using DriveExecutive Softwareunch DriveExecutive software.ing a 1203-USB or 1203-SSS converter, go online with the drive thatis connected to the adapter.3.In the DriveExecutive treeview, select the 20-COMM-H adapter (see Figure 2).4.Click the information iconto display the adapter Properties screen.5.The ‘Revision’ field shows the present revision of the adapter firmware(for example, 2.008).Figure 2 DriveExecutive Window with Information Icon and Device Properties420-COMM-H RS485 HVAC Adapter Firmware Revision 2.009Updating the Firmware This section describes procedures to update the adapter firmware. Flash kitsfor drives, communication adapters, and peripherals are provided on the Allen-Bradley Web Updates site at /support/abdrives/webupdate . Updating can be performed using a 1203-USB or 1203-SSS converter. For information about how to connect to your drive, see their respective User Manual. They can be viewed/downloaded on the Literature Library website at .Installing the Flash Kit1.Go to the Allen-Bradley Web Updates site at /support/abdrives/webupdate and install the flash kit for the20-COMM-H adapter, which also automatically installs theControlFLASH software on your computer.2.You are now ready to use DriveExplorer, DriveExecutive,ControlFLASH or HyperTerminal software to update the adapter. See the respective section below and follow the ing DriveExplorer Lite/Full Software to Update Firmware1.With the Flash Kit installed (see Installing the Flash Kit ), launchDriveExplorer software.ing a 1203-USB or 1203-SSS converter, go online with the drive thatis connected to the adapter.3.In the DriveExplorer treeview, select the 20-COMM-H adapter.4.Click the information icon(see Figure 1) to display the adapterProperties screen.5.On the 20-COMM-H Properties screen, click the Details tab.Important:This update may cause the adapter parameters to revert totheir default values. You may want to save yourconfiguration using DriveExplorer software or the HIMCopyCat feature before updating.6.Click Flash Update to start the update.7.Select ‘2.009.xx’ from the list of available updates.8.Click Next >.9.Follow the remaining screen prompts until the update procedurecompletes and displays the new firmware revision 2.009.ATTENTION: Risk of permanent equipment damage exists. Once an update has been started, do not remove power from the drive until after the download has completed and the adapter MOD status indicator startsflashing green. If power is removed before this occurs, the adapter may be permanently damaged. An adapter that has been damaged in this way cannot be repaired.20-COMM-H RS485 HVAC Adapter Firmware Revision 2.0095Using DriveExecutive Software to Update Firmware1.With the Flash Kit installed (see Installing the Flash Kit), launchDriveExecutive software.ing a 1203-USB or 1203-SSS converter, go online with the drive thatis connected to the adapter.3.In the DriveExecutive treeview, select the 20-COMM-H adapter.4.Click the information icon(see Figure 2) to display the adapterProperties screen.5.On the 20-COMM-H Properties screen, click the Component Detailstab.Important:This update may cause the adapter parameters to revert to their default values. You may want to save yourconfiguration using DriveExecutive software or the HIMCopyCat feature before updating.6.Click Flash Update to start the update.7.Select the 20-COMM-H from the list of available devices.8.Click Next >.9.Select ‘2.009.xx’ from the list of available updates.10.Click Next >.11.Follow the remaining screen prompts until the update procedurecompletes and displays the new firmware revision 2.009.Using ControlFLASH Software to Update Firmware1.With the Flash Kit installed (see Installing the Flash Kit on page4),choose Start > (All) Programs > Flash Programming Tools >ControlFLASH to launch the ControlFLASH software.2.On the ControlFLASH Welcome screen, click Next >.3.Choose the appropriate 20-COMM-H update from the list of availableupdates for the mode (RTU, N2 or FLN P1) in which the adapter is set.4.Click Next >.Important:This update may cause the adapter parameters to revert to their default values. You may want to save yourconfiguration using the HIM CopyCat feature, orDriveExplorer or DriveExecutive software before updating.5.Expand the treeview for the communication path you are using, andselect the drive icon that represents the drive with the 20-COMM-H adapter you are updating.6.Click OK.7.If the Multiple Assemblies Found window appears, select‘Port X - 20-COMM-H’ from the list and click OK. If this window does620-COMM-H RS485 HVAC Adapter Firmware Revision 2.0098.With the Firmware Revision window displayed, select ‘2.009.xx’ fromthe list of available updates.9.Click Next >.10.Follow the remaining screen prompts until the update procedurecompletes and displays the new firmware revision 2.009.Using HyperTerminal Software to Update Firmware1.With the Flash Kit installed (see Installing the Flash Kit on page 4),launch HyperTerminal software.ing a 1203-USB or 1203-SSS converter, go online with the drive thatis connected to the adapter.3.Set the adapter network protocol rotary switch to either the ‘N2’ or ‘P1’position before proceeding.Important:If the ‘N2’ or ‘P1’ setting is different from what the adapterswitch was previous set to, you must power cycle the drive.4.Press Enter until the main menu appears.5.In the main menu, press ‘3’ to flash upgrade.6.Press the number key that corresponds to the ‘20-COMM-H’ in the list.7.Press ‘Y’ (for Yes) to update the firmware.The terminal program will start displaying the letter ‘C’. This signals the Xmodem protocol that the download may proceed. You then have one minute to start the transfer.8.From the Transfer menu, choose Send File to display the Send Filescreen.a.Click Browse.b.Navigate to the flash file located in C:\Program Files\ControlFLASH\0001\0078\1F00.Main Menu - Enter Number for Selection1> Display Setup Parameters2> Display Event Queue3> Flash Upgrade ATTENTION: Risk of injury or equipment damage exists. When youperform an update, the drive will fault if it is receiving control I/O from the adapter. Verify that the drive has stopped safely or is receiving control I/O from an alternate source before beginning an update.20-COMM-H RS485 HVAC Adapter Firmware Revision 2.0097c.In the Select File to Send window list, select the‘20-COMM-H_2_009_03_AppV2_N2P1_NewHdr.bin’ file.d.Click Open.This file name now appears in the Filename box in the Send Filescreen.e.From the Protocol pull-down menu, choose ‘Xmodem’.f.Click Send.A dialog box appears and reports the update progress. Whencomplete, a ‘Flash Complete’ message appears. Press any key tocontinue.Important:Keep the adapter powered for 15 seconds after theoperation has completed or until the adapter MOD statusindicator starts flashing green.TIP: To cancel the flash update at any time, press Ctrl-X.9.Repeat steps 4 through 8 for the‘20-COMM-H_2_009_05_ComboNewHdr.bin’ file.10.Repeat steps 4 through 8 for the‘20-COMM-H_2_001_02_BootNewHdrV2.bin’ file.11.After the firmware update successfully completes, set the adapternetwork protocol rotary switch to the desired mode (RTU, N2 or P1) inwhich you want to operate the adapter.Important:Changing to a new rotary switch position requires you topower cycle the drive.12.Press Enter to return to the main menu.Restrictions For PowerFlex 753 and PowerFlex 755 Drives, these restrictions apply:•The Reference and Feedback words are internally scaled 1:32 to allow arange of 0 to 650.00 Hz.•32-bit floating point parameters are mapped as follows:–Datalinks are mapped as Little Endian (that is, Low/High wordordering).–User In/Out registers are mapped as Big Endian (that is, High/Lowword ordering).–Direct DPI parameters are mapped as Big Endian (that is, High/Lowword ordering).–This mapping structure also applies to PowerFlex 700VC driveswhich use 32-bit Datalinks.U.S.Allen-BradleyDrivesTechnicalSupport-Tel:(1)262.512.8176,Fax:(1)262.512.2222,Email:*****************,Online:/support/abdrivesCompatible Revisions To use this revision of firmware, update your tools and devices as needed.Rockwell AutomationSupport Rockwell Automation provides technical information on the web to assist you in using our products. At , youcan find technical manuals, a knowledge base of Frequently AskedQuestions (FAQs), technical and application notes, sample code and links to software service packs, and a MySupport feature that you can customize to make the best use of these tools.Rockwell Automation also provides complimentary phone support for drives, communication adapters, and peripherals. If you experience a problem with a device, please see the information in its User Manual. For further help in getting your device operational, contact a Customer Support representative.For an additional level of technical phone support for installation, configuration, and troubleshooting, TechConnect Support programs are available. For more information, contact your local distributor, a Rockwell Automation representative, or visit . Product Satisfaction Return Rockwell Automation tests all products to ensure that they are fully operational when shipped from the manufacturing facility. However, if your product is not functioning and needs to be returned, follow the steps below. Tool/DeviceVersion Required DriveExplorer Lite/Full software4.01 or later DriveExecutive software3.01 or later PowerFlex 7-Class driveall versions compatible LCD HIMall versions compatible RSLinx Classic software 2.43 or laterUnited States (1) 262.512.8176Monday – Friday, 7am – 6pm CST Outside United States Please contact your local Rockwell Automation representative for any technical support issues.United States Contact your distributor. You must provide a Customer Support case number (see phone number above to obtain one) to your distributor to complete the return process.Outside United States Contact your local Rockwell Automation representative for the return procedure.。
PCB Model 482C05 Four-channel, ICP Sensor Signal C
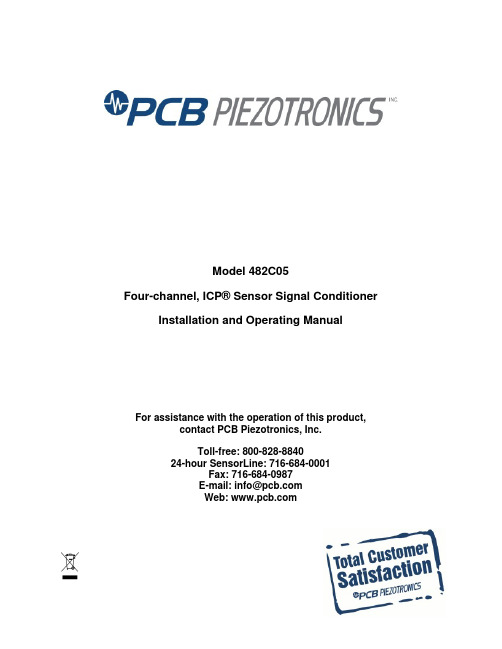
Model 482C05Four-channel, ICP® Sensor Signal Conditioner Installation and Operating ManualFor assistance with the operation of this product,contact PCB Piezotronics, Inc.Toll-free: 800-828-884024-hour SensorLine: 716-684-0001Fax: 716-684-0987E-mail:************Web: Repair and MaintenancePCB guarantees Total Customer Satisfaction through its “Lifetime Warranty Plus” on all Platinum Stock Products sold by PCB and through its limited warranties on all other PCB Stock, Standard and Special products. Due to the sophisticated nature of our sensors and associated instrumentation, field servicing and repair is not recommended and, if attempted, will void the factory warranty.Beyond routine calibration and battery replacements where applicable, our products require no user maintenance. Clean electrical connectors, housings, and mounting surfaces with solutions and techniques that will not harm the material of construction. Observe caution when using liquids near devices that are not hermetically sealed. Such devices should only be wiped with a dampened cloth—never saturated or submerged.In the event that equipment becomes damaged or ceases to operate, our Application Engineers are here to support your troubleshooting efforts 24 hours a day, 7 days a week. Call or email with model and serial number as well as a brief description of the problem. CalibrationRoutine calibration of sensors and associated instrumentation is necessary to maintain measurement accuracy. We recommend calibrating on an annual basis, after exposure to any extreme environmental influence, or prior to any critical test.PCB Piezotronics is an ISO-9001 certified company whose calibration services are accredited by A2LA to ISO/IEC 17025, with full traceability to SI through N.I.S.T. In addition to our standard calibration services, we also offer specialized tests, including: sensitivity at elevated or cryogenic temperatures, phase response, extended high or low frequency response, extended range, leak testing, hydrostatic pressure testing, and others. For more information, contact your local PCB Piezotronics distributor, sales representative, or factory customer service representative. Returning EquipmentIf factory repair is required, our representatives will provide you with a Return Material Authorization (RMA) number, which we use to reference any information you have already provided and expedite the repair process. This number should be clearly marked on the outside of all returned package(s) and on any packing list(s) accompanying the shipment.Contact InformationPCB Piezotronics, Inc.3425 Walden Ave.Depew, NY14043 USAToll-free: (800) 828-884024-hour SensorLine: (716) 684-0001General inquiries: ************Repair inquiries: ***********For a complete list of distributors, global offices and sales representatives, visit our website, .Safety ConsiderationsThis product is intended for use by qualified personnel who recognize shock hazards and are familiar with the precautions required to avoid injury. While our equipment is designed with user safety in mind, the protection provided by the equipment may be impaired if equipment is used in a manner not specified by this manual.Discontinue use and contact our 24-Hour Sensorline if:∙Assistance is needed to safely operate equipment∙Damage is visible or suspected∙Equipment fails or malfunctionsFor complete equipment ratings, refer to the enclosed specification sheet for your product.Definition of Terms and SymbolsThe following symbols may be used in this manual:DANGERIndicates an immediate hazardoussituation, which, if not avoided, mayresult in death or serious injury.CAUTIONRefers to hazards that could damage the instrument.NOTEIndicates tips, recommendations and important information. The notes simplify processes and containadditional information on particular operating steps.The following symbols may be found on the equipment described in this manual:This symbol on the unit indicates that high voltage may be present. Use standard safety precautions to avoid personal contact with this voltage.This symbol on the unit indicates that the user should refer to the operating instructions located in the manual.This symbol indicates safety, earth ground.PCB工业监视和测量设备 - 中国RoHS2公布表PCB Industrial Monitoring and Measuring Equipment - China RoHS 2 Disclosure Table部件名称有害物质铅 (Pb)汞(Hg)镉(Cd) 六价铬 (Cr(VI)) 多溴联苯 (PBB) 多溴二苯醚 (PBDE)住房O O O O O O PCB板X O O O O O 电气连接器O O O O O O 压电晶体X O O O O O 环氧O O O O O O 铁氟龙O O O O O O 电子O O O O O O 厚膜基板O O X O O O 电线O O O O O O 电缆X O O O O O 塑料O O O O O O 焊接X O O O O O 铜合金/黄铜X O O O O O 本表格依据 SJ/T 11364 的规定编制。
Recom RAC05-K 5W 单输出 AC DC 电源说明书

5 Watt 1“ x 1“Single OutputAC/DC ConverterE224736DescriptionThe RAC05-K series are ultra-compact AC/DC power supply modules in lightweight fully-encapsulated plastic casing. Beside safety approvals for industrial and IT solutions IEC60950-1 and UL62368-1, the units meet EN55032-“B“ limits without any external components. Integrated fusing as well as electrical protections against short circuit and over voltage are on board. With their excellent efficiency over the entire load range including light load standby conditions, these power modules are especially suitable for IOT applications and control equipment.FeaturesRAC05-K UL62368-1 certifiedCSA C22.2 No. 62368-1-14 certified IEC/EN60950-1 certified IEC/EN62368-1 certified EN61204-3 compliant CB-ReportSpecifications (measured @ ta= 25°C, nominal input voltage (115/230VAC), full load and after warm-up)BASIC CHARACTERISTICSParameterCondition Min.Typ.Max.Internal Input Filter Pi Type Input Voltage Range (2)85VAC 120VDC264VAC 370VDC Input Current 115VAC 230VAC250mA 100mA Inrush Currentcold start115VAC 230VAC15A 30ANo load Power Consumption 264VAC75mWInput Frequency Range 47Hz 63HzMinimum Load 0%Power Factor 115VAC 230VAC0.60.45Start-up Time 20msRise Time 8msHold-up time115VAC 230VAC12ms 60msInternal Operating Frequency 130kHzOutput Ripple and Noise (3)20MHz BW3.3Vout, 5Voutothers60mVp-p1% of Voutcontinued on next pageSelection GuidePart Input Output Output Efficiency Max. Capacitive Number Voltage Range Voltage Current typ. (1) L oad [VAC] [VDC] [mA] [%] [µF]RAC05-3.3SK 85-264 3.3 1515 76 6000RAC05-05SK 85-264 5 1000 80 6000RAC05-12SK 85-264 12 416 81 1500RAC05-15SK 85-264 15 333 82 1000RAC05-24SK 85-264 24 210 84 330Notes:Note1: Efficiency is tested at 25°C with constant resistant mode at full load and 230VACNotes:Note2: The products were submitted for safety files at AC-Input operation. Refer to …Line Derating“ Note3: Measurements are made with a 0.1μF MLCC & 10μF E-cap in parallel across output. (low ESR)Model NumberingS ingle OutputOutput VoltageRAC05-__ SKSpecifications (measured @ Ta= 25°C, nominal input voltage (115/230VAC), full load and after warm-up)Specifications (measured @ Ta= 25°C, nominal input voltage (115/230VAC), full load and after warm-up)ENVIRONMENTALParameterConditionValueOperating Temperature Range @ natural convection 0.1m/sfull load-25°C to +50°C refer to …Derating Graph“-25°C to +70°CMaximum Case Temperature 230VAC+90°C Temperature Coefficient 0.05%/K Operating Altitude 3000mOperating Humidity non-condensing20% to 90% RH Design Lifetime 115VAC/60Hz and full load at +25°C 136 x 10³ hours MTBF according to MIL-HDBK-217F, G.B.+25°C +50°C>450 x 10³ hours >250 x 10³ hoursPollution Degree PD2Vibration10-500Hz, 2G 10min./1cycle, period 60min. each along x,y,z axes continuned on next pageREGULATIONSParameterConditionValueOutput Accuracy ±1.0% typ.Line Regulation ±0.5% typ.Load Regulation 1.0% typ.Transient Response25% load step changerecovery time4.0% max.500μsPROTECTIONSParameterType ValueInternal Input Fuse (4)T1A, slow blowShort Circuit Protection (SCP)Hiccup, automatic restart Over Voltage Protection (OVP)125% - 195%, latch off mode Over Current Protection (OCP)150% - 195%, hiccup modeOver Voltage Category (OVC)OVC II Class of Equipment Class II Isolation Voltage I/P to O/P , I/P to Case and O/P to Casetested for 1 minute tested for 3 seconds 3kVAC 4kVAC Isolation Resistance I/P to O/PIsolation Voltage 500VDC1G W min.Isolation Capacitance 100kHz/0.1V100pF max.Insulation Grade reinforced Leakage Current0.25mA max.Notes:Note4: Refer to local safety regulations if input over-current protection is also requiredSpecifications (measured @ Ta= 25°C, nominal input voltage (115/230VAC), full load and after warm-up)SAFETY AND CERTIFICATIONSCertificate Type (Safety)Report / File NumberStandard Audio/Video, information and communication technology equipment - Safety requirementsE224736UL62368-1, 2nd Edition: 2014CSA C22.2 Nr. 62368-1-14, 2nd Edition: 2014 Information Technology Equipment, General Requirements for Safety (CB Scheme)E491408-A2-CB-1IEC60950-1:2005, 2nd Edition: + A2:2013Information Technology Equipment, General Requirements for Safety EN60950-1:2006 + A2:2013Audio/Video, information and communication technology equipment - Safety requirements (CB Scheme)OFF-4787889086-1IEC62368-1:2014, 2nd EditionAudio/Video, information and communication technology equipment - Safety requirements EN62368-1: 2014 + A11:2017EAC RU-AT.03.67361TP TC 004/020, 2011RoHS2+RoHS 2011/65/EU + AM2015/863EMC ComplianceConditionsStandard / CriterionLow-voltage power supplies DC output - Part 3: Electromagnetic compatibility EN61204-3: 2000, Class B ESD Electrostatic discharge immunity test±8kV Air; ±4kV Contact EN61000-4-2: 2009, Criteria BRadiated, radio-frequency, electromagnetic field immunity test 10V/m, 80MHz-1GHz 3V/m, 1.5GHz-2GHz 1V/m, 2GHz-2.7GHz EN61000-4-3: 2006 + A2, 2010, Criteria AFast Transient and Burst Immunity AC In Port: ±2.0kV EN61000-4-4: 2012, Criteria B Surge ImmunityAC In Port (L-N): ±1.0kV DC Output Port: ±0.5kV EN61000-4-5: 2014, Criteria B Immunity to conducted disturbances, induced by radio-frequency fields AC and DC Power Port: 10VEN61000-4-6: 2014, Criteria A Power Magnetic Field Immunity 50Hz, 1A/m EN61000-4-8: 2010, Criteria A Voltage Dips and InterruptionsVoltages Dips: >95%Voltage Dips: 30%Interruptions: >95%EN61000-4-11: 2004, Criteria B EN61000-4-11: 2004, Criteria C EN61000-4-11: 2004, Criteria CVoltage Fluctuations and Flicker in Public Low-Voltage Systems <=16A per phaseEN61000-3-3: 2013(5)-25-202040507060801001008060409070503020100O u t p u t L o a d [%]Ambient Temperature [°C]Derating Graph(@ Chamber and natural convection 0.1m/s)1008060409070503020100O u t p u t L o a d [%]Input Voltage [VAC]8590110135160185210235264Notes:Note5: No derating required for the specified DC-input rangeNotes:Note6: If output is connected to GND, please contact RECOM tech support for adviceLine DeratingSpecifications (measured @ Ta= 25°C, nominal input voltage (115/230VAC), full load and after warm-up)PACKAGING INFORMATIONParameter Type Value Packaging Dimension (LxWxH)tube530.0 x 27.5 x 25.6mm Packaging Quantity18pcs Storage Temperature Range-40°C to +85°C Storage Humidity non-condensing20% to 90% RHThe product information and specifications may be subject to changes even without prior written notice.The product has been designed for various applications; its suitability lies in the responsibility of each customer. The products are not authorized for use in safety-critical applications without RECOM’s explicit written consent. A safety-critical application is an application where a failure may reasonably be expected to endanger or cause loss of life, inflict bodily harm or damage property. The applicant shall indemnify and hold harmless RECOM, its affiliated companies and its representatives against any damage claims in connection with the unauthorizeduse of RECOM products in such safety-critical applications.。
保安电源快切MFC5208装置说明书
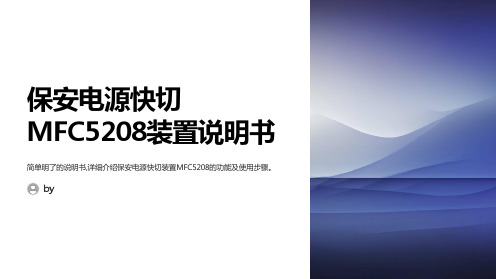
注意事项和警告
安全操作
请严格遵守装置说明,确保安全操 作。操作时请远离高压电源,避免 触电伤害。
环境要求
装置仅适用于室内使用,请远离潮 湿环境和易燃易爆物品。
维护保养
定期检查装置状态,确保所有连接 牢固。如发现异常,请立即停机并 联系专业人员。
禁止拆解
请勿私自拆解或修改装置,以免造 成人身伤害或设备损坏。
技术参数
220V
电源电压
交流220伏输入
50Hz
频率
50赫兹交流电
3A
10ms
额定电流
最大3安培输出电流
切换速度
最快10毫秒内切换
保安电源快切MFC5208装置采用高速固态继电器,可以在非常短的时间内切换电 源路径,以确保关键负载不会在电源切换过程中断电。该装置可靠性高,使用寿命 长,适合应用于医疗设备、金融系统等场景。
电池检测
应定期检测电池组的电压和容 量,及时更换已老化或损坏的 电池组。
专业维修
如出现故障或异常情况,请立 即停止使用并联系专业维修人 员进行检修。请勿私自拆解。
电磁兼容性
电磁辐射
该装置采用先进的电磁屏蔽设计,可有效抑制外部电磁干扰,确保稳定可靠的工作性能。
防雷保护
内置专业级的防雷电路,可承受较强的电磁脉冲冲击,确保设备在恶劣环境下也能安全208具有快速切断保安电源的功能,可 在发生故障时瞬时切断电源,避免危险情况 的发生。
全面的监控功能
设备配备多种指示灯和监控信号输出,可实 时监测电源工作状态,及时发现故障。
灵活的接口设计
MFC5208支持多种输入电源和输出信号连 接,可根据现场需求灵活配置,满足不同场景 的应用。
外形尺寸和重量
康多机械钥匙切割机 XC-002 用户手册说明书

CONDOR Mechanical Key Cutting MachineXC-002User ManualTABLE OF CONTENTS1)SAFETY PRECAUTIONS AND WARNINGS-----------------------------------------01 2)GENERAL INFORMATION-------------------------------------------02 2.1BRIEF INTRODUCTION---------------------------------------------------02 2.2CHARACTERISTICS------------------------------------------------------02 3)PRODUCT PACKAGING CHECKLIST----------------------------------------------03 4)OVERVIEW4.1 SCHEMATIC------------------------------------------------------06 4.2 SPECIFICATIONS AND PARAMETERS-----------------------------------------07 4.3 MAIN COMPONENTS AND FUNCTION INSTRUCTION----------------------08 5)MACHINE INSTALLATION AND PREPARATION5.1 INSTALLING THE MAIN HANDLE--------------------------------------------15 5.2 INSTALLING THE SUB HANDLE---------------------------------------------16 5.3 INSTALLING AND REMOVING PROBE/CUTTER---------------------------175.4 CLAMP INSTALLATION---------------------------------------------------185.5 PROBE/CUTTER HEIGHT LEVEL ADJUSTMENT----------------------------195.6 ROTATION ADJUSTMENT----------------------------------------------------20 6)OPERATING INSTRUCTIONS6.1 KEY ALIGNMENT--------------------------------------------------21 6.2 SELECTION RULES OF CLAMP SIDES----------------------------------22 7)MAINTENANCE-----------------------------------------------------23 8)WARRANTY AND AFTER SALESSERVICE-----------------------------------------24 9)APPENDIX--------------------------------------------------------------251.SAFETY PRECAUTIONS AND WARNINGSTo prevent personal injury or machine damage, users should carefully observe the instructions in this operation manual and adopt following safety precautions:●Always operate the machine under a safe condition.●Place the machine on a horizontal surface, which should be firmenough to carry.●Do not explore the machine to the direct sunlight, or place the machinein any wet, oily, or dusty area.●Please keep the machine clean and dry, and maintain at least 30cmdistance to the wall for ventilation.●Please wear the safety glasses that meets ANSI standard.●Keep clothing, hair, hands, tools, test equipment, etc. away from allmoving parts.●Do not leave the machine while it is operating, and someonespecifically for monitoring is also required.●Do not place any object on the machine during running.●Must connect to the grounded power outlet, please do not use thepower outlet if it is broken, loosen or with substandard power.●Please unplug the machine during maintenance or it is idle.●Immediately shut down the machine if any exception occurs. The powerswitch locates near the power cord connector, at the lower rear part ofthe machine.●Please place the machine out of the reach of children.2.GENERAL INFORMATION2.1 BRIEF INTRODUCTION1Thank you for choosing CONDOR XC-002 Mechanical Key Cutting Machine. XC-002 Mechanical Key Cutting Machine is a professional device. It enables locksmiths to copy and process keys more efficiently and accurately for vehicles or civil use. The careful reading of this manual before use is a quite crucial precondition for safety. For occasional reference, please keep this user manual properly.2.2 CHARACTERISTICSCONDOR XC-002 Mechanical Key Cutting Machine contains following characteristics:●Ergonomic design provides better user experience●Aluminum-casting body make it more reliable and durable●Adjustable high-speed motor ensures the stability and fluency ofoperation.●Built-in indicator lights make the height level adjustment easier●Cross rail guarantees the accuracy●Supporting track and dimple cutting, that can process special keys ●More key types are available because of 4-side rotary clamp23. PRODUCT PACKAGING CHECKLISTThe whole package covers all following items, if missing, please contact your dealer.Main body1 Key machine bodyUpper rubber mat1Temporarily carry lightitemsMulti-functionalclamp1Key carrier, can rotates infour sides Key alignment blockblade 1Use in key alignment2.5mm cutter (Ø2.5ר6×40L ) 1Available for most mechanical keys1.5mm cutter (Ø1.5ר6×40L )1Available for elaboratecuttingTracer(Ø 1.5ר 2.5ר 6×45L)1 The tool for detection3Main handle1Control the height of tracer and cutter Sub-handle1Control the position ofworking bench Power cord(1.5m)1Connect to power outlet (Chinese Standard)Power cord(1.5m) (optional )Connect to power outlet(British Standard)Power cord(1.5m) (optional )Connect to power outlet (European Standard)Power cord(1.5m) (optional )Connect to power outlet (American Standard)Brush1 For clean2.5mm Allen wrench1Tool for the installation oftracer and cutter 4mm Allen wrench1Tool to tighten the clampProduct packagingchecklist1 Product DeliveryInspection Certificate Product Packaging checkUser manual1Machine installation and operating instruction4Note :★ For the product improvement, color, design and structure may be different, please in kind prevail.★ The cutter should be replaced timely to maintain the cutting effectiveness. ★ Please use 3A fuse.4. OVERVIEW4.1 SCHEMATICMain handleIndicator lightfor height level adjustment CutterRotation speed adjuster Key tighten knob Cutting bench Storage box Sub-handle Micro-adjusterTracer Sub-clamp Limitation knob 1Limitation knob 2 Main clamp54.2 SPECIFICATIONS AND PARAMETERSInput Voltage 220VACInput Frequency 50HzPower Consumption 200WMotor Rotation SpeedMAX 10000rpm 1st gear,6000rpm 2nd gear,8000rpmMotor Torque 1st gear,torque 0.4N 2nd gear,torque 0.3NWorking Temperature 0~50℃Humidity 10~90% Travel of Spindle 27mmTravel of Cutting Bench Horizontal:38mm Vertical:50mmDecibel 77dBNet Weight 23KGGross Weight 28KGMachine Dimension L 298mm×W 445mm×H 525mm Package Dimension L 595mm×W 550mm×H 375mm6MACHINE DIMENSION 525mm298mm445mm7PACKAGE DIMENSION4.3 MAIN COMPONENTS AND FUNCTION INSTRUCTION4.3.1 SUB-HANDLEEnsure cutting bench’s horizontal movement is in a specified area.84.3.2 MAIN HANDLE1)Pull or push the handle up and down to adjust the height of tracer andcutter. When releasing the handle, tracer will back to the original position.2)Tighten the handle in the clockwise direction can fix the position oftracer and cutter.3)The operation strength should be proper to avoid damage.94.3.3 ROTATION SPEED ADJUSTERThere are four gears to control rotation speed - neutral, OFF, 1 and 2, respectively, means motor turnoff, standby, low speed and high speed four running modes.4.3.4 INDICATOR LIGHT OF HEIGHT LEVEL ADJUSTMENT1)If the heights of tracer and cutter are the same, two indicator lights willbe both on when tracer and cutter’s tops have contacted with the clamp by main handle.2)If trace is higher than cutter, the left indicator light will be on, means“Lower”.3)If trace is lower than cutter, the right indicator light will be on, means“Raise”.104.3.5 MICRO-ADJUSTERIt is used to adjust the height of tracer, until its top is at the same height level as cutter’s.(Clockwise rotating will raise the tracer and counterclockwise will lower it)114.3.6 CUTTING BENCHThe sliding base is for the horizontal movement of clamp.(The maximum slide distance is 38mm laterally and 50mm longitudinally.) 4.3.7 CLAMPThis is the key carrier (the left one is sub-clamp for original key and the right one is main clamp for key blank). Four sides A, B, C and D are rotary, and each of them has the place for key alignment. Please select the corresponding side in terms of key type and bitting.NOTE: When cutting, the side of both two clamps must be the same.124.3.8 KEY TIGHTNESS KNOBPut the original key and key blank into clamp spot and tighten, that to ensure the position shifting will not happen during the process. Please first loosen knobs, and then both clamps should be turn to the same side,4.3.9 LIMITATION KNOB1)Knob 1 on the left is used to adjust cutting bench’s left and rightmoving. When this knob is tightened, bench can only move backwards and forwards.Knob 2 on the right is used to adjust cutting bench’s sliding range. When this knob is tightened, the distance of bench’s left-to-right sliding is limited.134.3.10 STORAGE BOXTo place tracer, cutter, key blank, brunch and other materials and tools.4.3.11 POWER CONTROL MODULEThe power connector, fuse and power switch are all located at the lower back of the machine.1)Insert the power cord into left port, then link to the grounded poweroutlet.2)When switch the power to “ON”, machine enters into “Standby”mode.3)To replace the fuse, please remove the box first, then change a new oneand put the box back.14★Please use 3A fuse.★When the machine is idle or maintaining, please turn off the power and unplug the power outlet.155.MACHINE INSTALLATION AND PREPARATION5.1 INSTALLING MAIN HANDLE1)Insert the bottom of main handle into installing hole, which is by theright side of the machine body. Then cover the screw cap and rotate thehandle clockwise until tightened.2)If fully tightened, the main handle should be fix at a certain positionand unable to move up or down.3)If rotate the handle 180 degrees counterclockwise, the height of tracerand cutter can be changed freely.165.2 INSTALLING SUB-HANDLE4)Insert the bottom of sub-handle into the installing hole, which is by theleft side of the machine body. Put on the protective bushing and then plug in the lower bearing bore to avoid moving. Cover the screw cap and rotate the handle clockwise until tightened.175.3 INSTALLING AND REMOVING PROBE/CUTTER1)The left one is tracer and the right one is cutter. Put the tracer andcutter into the hole and to the top limit position. Then use 2.5mm Allen wrench to turn the lock screw clockwise respectively till the tracer and cutter are both tightened.NOTE: When using 1.5mm cutter and 2.5mm cutter, tracer and cutter must select the top with the same diameter for processing.182)Insert the wrench into the hole, turn the lock screw counterclockwise,and then remove trace and cutter.5.4 CLAMP INSTALLATIONAim the bump (A1: underneath the clamp) at the cutting bench’s groove (A2), push toward the left until A1 and A2 (shown above) are fully overlapped. Then use 4mm Allen wrench to tighten the screw.195.5 PROBE/CUTTER HEIGHT LEVEL ADJUSTMENT1)When the installation finished, push the main handle.If the tracer is higher than cutter, the indicator light on the left will turn on.2)If the tracer is lower than cutter, the indicator light on the right will turnon.203)According to the signal of indicator light, rotate the Micro-adjusteruntil tracer and cutter’s tops have both touched the clamp. In other words, they are at the same height. Then two indicator lights will on, adjustment finished.NOTE:During the height level adjustment, main clamp and sub-clamp must at the same side.5.6 ROTATION SPEED ADJUSTMENTRotation adjustment knob locates at the right side of the machine. There are two gears to control the rotating speed of motor.211)When the adjuster is at the neutral gear, motor stays at “Turnoff” mode; when it points to “OFF”, the light will be on, means the machine is ready to work2) When the adjuster points to “1”, the motor rotates at a low speed, about 6000rpm; when it points to “2”, the rotation speed is higher, about 8000rpm.226.OPERATING INSTRUCTIONS6.1 KEY ALIGNMENTThere are two ways to align the key: shoulder alignment and headalignment1)Shoulder alignment as shown belowAdjustment line2)The position of head alignment as shown below, and 1, 2, 3 are theblock blades for different key types.23246.2 SELECTION RULES OF CLAMP SIDESKey TypeSchemaClamp sideIllustration2 Track ExternalA/B1)The key type available for side A and D are thesame, please make the selection according to the cutting depth.2)When cutting dimple key, please use the specific cutter.A/C4 Track ExternalA/DA/DChannel TrackA/DA/BA/C4 Track InternalA/D25Dimple A/D7.MAINTENANCE●Before cutting, please use a brush to clean up the operating area. Sinceinclusions may cause corrosion or damages, and would eventuallyimpact the accuracy of key cutting.●Do not use any oily product or detergent to clean the components,because it may also lead to some damages or corrosion.●Neither direct water rinse nor wet cloth wipe can be used on machine.Otherwise, electric leakage or metal rustiness will probably happen.●Under no circumstance can cleaning equipment be used for operatingarea, such as air gun, blower etc. It is to avoid inclusions blowing intothe machine and raise the unsafety of daily use.268.WARRANTY AND AFTER SALES SERVICECONDOR XC-002 contains one-year warranty and the start date of period is subject to invoice; if with no invoice or has lost, then the daterecorded by manufacturer shall prevail.★Following circumstances are not included in free maintenance:●The malfunction caused by the operation not followed with usermanual.●The malfunction and damage caused by unauthorized repairs andalteration.●The malfunction caused by fall, crash or improper voltage.●Damage due to force majeure.●Long time used in harsh places or vehicles, or the failure and damagecaused by ship carrying.●The malfunction arisen from everyday use, such as dirt or normal lossesof shell and protective shield is excluded either.To achieve more information about product’s after sales service and technical support, please contact dealer or scan the QR code below, andfollow Xhorse official account (WeChat ID: SZ-Xhorse).27XhorseAll rights reserved. Without permission, all copies or transmissions of any parts of this publication by any individuals or organizations in any ways are forbidden. Due to the continuous improvement, the content in this manual is subject to change without prior notice.289.APPENDIX29。
M80287资料

Y
Y
Protected Mode Operation Completely Conforms to the M80286 Memory Management and Protection Mechanisms Directly Extends M80286 10 Instruction Set to Trigonometric Logarithmic Exponential and Arithmetic Instructions for All Datatypes 8 x 80-Bit Individually Addressable Numeric Register Stack 6 8 10 MHz Military Temperature Range b 55 C to a 125 C (TC)
CKM
I
RESET
I
D15–D0 BUSY ERROR PEREQ
I O O O O
PEACK
I
NPRD NPWR NPS1 NPS2
I I I
CMD1 CMD0
I
CLK286
I
S1 S0 COD INTA HLDA READY VSS VCC 2
I
I I I I
M80287Байду номын сангаас
Once in protected mode all references to memory for numerics data or status information obey the M80286 memory management and protection rules giving a fully protected extension of the M80286 CPU In the protected mode M80286 20 numerics software is also completely compatible with M8086 20 and M8088 20 The M80287 has two operating modes similar to the two modes of the M80286 When reset M80287 is in the real address mode It can be placed in the protected virtual address mode by executing the SETPM ESC instruction The M80287 cannot be switched back to the real address mode except by reset In the real address mode the M80286 M80287 is completely software compatible with M8086 M8087 and M8088 M8087 Once in protected mode all references to memory for numerics data or status information obey the M80286 memory management and protection rules giving a fully protected extension of the M80286 CPU In the protected mode M80286 M80287 numerics software is also completely compatible with M8086 M8087 and M8088 M8087
卡达克Z885支持指南说明书
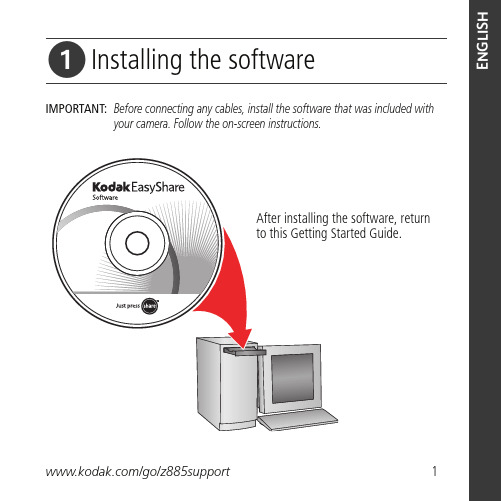
ᕡInstalling the software IMPORTANT: Before connecting any cables, install the software that was included with/go/z885support1ᕢLoading the batteries(rechargeable)non-rechargeable)ᕣ(non-rechargeable)/go/z885support 3ᕤSetting the language, date/time21to change.OK to accept.OK (press)21to change.OK to accept.Language:Date/Time:ᕥTaking a picture/videoPress the Shutter buttoncompletely down and release.To stop recording, press theShutter button again./go/easysharecenter/go/z885support5EᕦOK During playback to pause or play.During playback to adjust the volume.During playback to play at 2X speed; press again for 4X.During playback to reverse at 2X speed; press again for 4X.Play.ᕧTransferring pictures/videos/go/z885supportᕨKeep learning about your camera!• the extended user’s guide• interactive troubleshooting and repairs • interactive tutorials • FAQs• downloads • accessories• printing information • product registrationCongratulations! You have:• set up your camera • taken pictures• transferred pictures to your computerKeep learning!Finish reading this book, so you can take and share your best pictures!Self-timer/Burst button3Self-timer/Video light8Speaker4On/Off button9Microphone5Flash button 10Lens/go/easysharecenter/go/z885support 9E N G L I OK/4-way arrows 13DC-In (3V), for optional AC adapter4LCD/Info button 14Share button 5Delete button15Menu button 6Wide angle button 16Review button7Telephoto button 17Battery compartment 8Strap post18Battery door 9Slot for optional SD or MMC card19Tripod socket10SD or MMC card (sold separately)20Dock connector1Doing more with your cameraUsing optical zoomUse optical zoom to get up to 5X closer to your subject. Optical zoom is effective when the lens is no closer than 24 in. (60 cm) to the subject or 7.9 in. (20 cm) in Close-up mode. You can change optical zoom before and during video recording.1Use the LCD to frame your subject.2Press Telephoto (T) to zoom in. Press Wide Angle (W) to zoom out.The zoom indicator shows zoom status.3Take the picture or video.NOTE: In Video mode, the zoom indicator changes and only the optical zoom range appears.W T D10/go/easysharecenterDoing more with your cameraUsing the self-timerUse the self-timer when you want to be included in a picture, or to ensure a steady Shutter button press., or press the Shutter button completely down.Use the same procedure to use the self-timer in Video mode, but:■Turn the Mode dial to Video .■Press the Shutter button completely down.NOTE: The video stops when no storage space remains. Only the 2- and 10-second options are available invideo mode.• Once for a 10-second delay (so you have time to get into the scene)• Again for a 2-second delay (for a steady, auto-shutter release on a tripod)• Again for 2-shot (one picture taken after 10 seconds and another pictureIn most Still modes, press the Self-timer/Burst button :Doing more with your cameraUsing burst1In most Still modes, press the Self-timer/Burst button.NOTE: Burst is unavailable in Portrait, Night Portrait, Night Landscape, Backlight, Fireworks, and Panorama.2Press the Shutter button halfway to focus and set exposure.3Press the Shutter button completely down and hold it to take pictures.The camera stops taking pictures when you release the Shutter button, when the pictures are taken, or when there is no more storage space.NOTE: During quickview, you can delete all pictures in the burst series. To delete selectively, do so in Review(see page 21).ModeIcon Description Purpose FirstBurst Camera takes up to 5 pictures while the Shutter button is pressed.Capture an expected event.Example:A person swinging agolf club.Last BurstCamera takes up to 30 pictures while the Shutter button is pressed. When the Shutter button is released, only the last 5 pictures are saved.Capture an eventwhen the precisetiming is uncertain.Example:A child blowing outbirthday candles.Press the button repeatedly to scroll through flash modes (see Flash modes below).The current flash mode appears in the LCDDoing more with your cameraCapture modesCapture modeFor Smart Scene General picture taking. When the Shutter button is pressedhalfway, faces are detected, the scene is analyzed, and the bestsettings are applied. Pictures are taken in Auto mode if the Scene(SCN) mode cannot be determined.P, M More creative control. Program and Manual modes.High ISO People in low-light scenes indoors using a higher ISO.Digital Image Stabilization Minimizing the effects of camera shake and subject movement.Scene Point-and-shoot simplicity when taking pictures under specialconditions. (See page 15.)Video Capturing video with sound. (See page 4.)FavoritesViewing favorite pictures. Choose the mode that best suitsyour subjects and surroundings.Mode dialP/M ISO SCNDoing more with your cameraScene modes1Turn the Mode dial to Scene .2Press to display Scene mode descriptions.NOTE: If the mode description turns off before you finish reading it, press OK.3Press OK to choose a Scene mode.Using camera HelpDoing more with your cameraUnderstanding the picture-taking icons In Smart Scene mode—no buttons pressed Picture size Pictures/time remaining Storage location Low battery Zoom: Camera modeFlashwide digitaltelephoto Self-timer/BurstDate stampAlbum name Framing marksFraming grid2Working with pictures/videosIf you press the W button while at 1X, the view changes from single-picture to multi-up thumbnails.Cropping pictures1Press the Review button, then to find apicture.2Press the Menu button, then tohighlight Crop. Press the OK button.3Press Telephoto (T) to zoom in, ortomove the crop box. Press OK.4Follow the screen prompts.The picture is cropped. The original is saved. (Cropped pictures cannot be cropped again.)■Press the Menu button to exit the menu.Treturn to 1X.OKPicture Cropped pictureWorking with pictures/videosViewing thumbnails (multi-up)1Press the Review button.2Press the Zoom Wide Angle (W) button to changefrom single-picture view to multi-up thumbnails.3Press Telephoto (T) to return to single-picture view.■Press the Review button to exit Review.Using Kodak Perfect Touch technologyKodak Perfect Touch technology helps ensure better, brighter pictures.1Press the Review button, then to find a picture.2Press the Menu button, then to highlight Perfect Touch tech.Press the OK button.The enhancement is previewed in a split screen. Press to view other parts of the picture.3Press OK. Follow the screen prompts to replace the original picture or to save the enhanced picture as a new one.NOTE: You cannot enhance previously enhanced or panorama pictures, or videos.■Press the Menu button to exit the menu.Working with pictures/videos Editing videosMaking a picture from a videoYou can choose a single frame from a video, then make a picture suitable for printing.1Press the Review button, then to find a video.2Press the Menu button, thentohighlight Make Picture. Press the OK button.3Press to navigate through video frames.4Press OK to select a video frame, then press.5Follow the screen prompts.A picture is created. (The original video is saved.) Trimming a videoYou can delete an unwanted portion from the beginning or end of a video.Press the Review button, thento find a video.Press the Menu button, then tohighlight Edit Video. Press the OK button.Choose Trim, then press OK.Follow the screen prompts.The video is trimmed. (You can save it as a new video orreplace the original.)Video PictureWorking with pictures/videosUsing sound tagsYou can add a unique sound/message (up to 1 minute long) to your picture. Only one tag can be applied to each picture. You cannot add a sound tag to a video.Recording a sound tag1Press the Review button, thento find a picture.2Press the Menu button, thento highlight Sound Tag. Press the OK button.3Choose Record, then press OK.4Follow the screen prompts.The sound tag is applied to your picture.■Press the Menu button to exit the menu.Playing a sound tag1Press the Review button, thento find a tagged picture.2Press to play the sound tag.3Press to adjust the volume.4Press OK to pause or replay the sound tag duringplayback.ReviewOKWorking with pictures/videosDeleting pictures/videos1Press the Review button.2Press to find a picture/video.3Press the Delete button.4Follow the screen prompts.NOTE: After you delete a picture/video, the next picture/video (overlaidwith the Delete menu with the Undo Delete option) appears. Ifthere are no more pictures/videos, the Delete menu on a blankscreen appears. See Using the undo delete feature for moreinformation.Using the undo delete featureIf you accidentally delete a picture or video, use Undo Delete to retrieve it. This feature is available only immediately after you delete a picture/video in Review mode. The Undo Delete option appears.1Press to highlight Undo Delete.2Press OK.The deleted picture/video (overlaid with the Delete menu) appears.■Select Exit to exit the Delete menu.3Solving camera problemsFor step-by-step product support, visit /go/z885support and select Interactive Troubleshooting & Repairs.Camera problemsIf...Try one or more of the followingCamera does not turn on/off.■Install new batteries (page2).■Charge rechargeable batteries.■Remove the battery, then reinsert or replace it.Stored pictures are corrupted.■Retake pictures. Do not remove card while the Ready light is blinking.Keep rechargeable batteries charged.■Transfer the pictures to the computer (page6), format the SD/MMC card in the camera. (Press the Menu button, choose Setup and find Format).Formatting deletes all pictures/videos, including protected files.Removing the card during formatting may damage the card.Short battery life with Kodak Ni-MH rechargeable digital camera batteries.■Wipe the contacts with a clean, dry cloth before loading batteries in the camera.■Limit the following activities that quickly deplete battery power: reviewing pictures/videos on the LCD; and excessive use of the flash.■Use the Refresh feature on your camera dock series 3 or printer dock series 3.4AppendixImportant safety instructionsCAUTION:Do not disassemble this product; there are no user-serviceable parts inside. Refer servicing to qualified service personnel. Do not expose this product to liquid, moisture, or extreme temperatures. Kodak AC adapters and battery chargers are intended for indoor use only. The use of controls, adjustments, or procedures other than those specified herein may result in exposure to shock and/or electrical or mechanical hazards. If the LCD breaks, do not touch the glass or liquid. Contact Kodak customer support.■The use of an accessory that is not recommended by Kodak may cause fire, electric shock, or injury.■Use only a USB-certified computer. Contact your computer manufacturer if you have questions.■If using this product in an airplane, observe all instructions of the airline.■When removing the battery, allow it to cool; it may be hot.■Read and follow all warnings and instructions supplied by the battery manufacturer.■Use only batteries approved for this product to avoid risk of explosion.■Keep batteries out of the reach of children.■Do not allow batteries to touch metal objects, including coins. Otherwise, a battery may short circuit, discharge energy, become hot, or leak.■Do not disassemble, install backward, or expose batteries to liquid, moisture, fire, or extreme temperature.■Remove the battery when the product is stored for an extended period of time. In the unlikely event that battery fluid leaks inside the product, contact Kodak customer support.■In the unlikely event that battery fluid leaks onto your skin, wash immediately with water and contact your local health provider. For additional health-related information, contact your local Kodak customer support.■Dispose of batteries according to local and national regulations.■Do not charge non-rechargeable batteries.For more information on batteries, see /go/batterytypesAppendixUpgrading your software and firmwareDownload the latest versions of the software included on the Kodak EasyShare software CD and the camera firmware (the software that runs on the camera). See /go/z885downloads.Additional care and maintenance■If the camera has been subjected to inclement weather or you suspect water has gotten inside the camera, turn off the camera and remove the batteries and card. Allow components to air-dry for at least 24 hours before using the camera again.■Blow gently on the lens or LCD to remove dust and dirt. Wipe gently with a soft, lint-free cloth or an untreated lens-cleaning tissue. Do not use cleaning solutions unless designed specifically for camera lenses.Do not allow chemicals, such as suntan lotion, to contact painted surfaces.■Service agreements are available in some countries. Contact a dealer of Kodak products for more information.For digital camera disposal or recycling information, contact your local authorities. In the US, visit the Electronics Industry Alliance Web site at or visit /go/z885support.WarrantyKodak warrants Kodak consumer electronic products and accessories (“Products”), excluding batteries, to be free from malfunctions and defects in both materials and workmanship for one year from the date of purchase. Retain the original dated sales receipt. Proof of the date of purchase will be required with any request for warranty repair.Limited warranty coverageWarranty service is only available from within the country where the Products were originally purchased. You may be required to ship Products, at your expense, to the authorized service facility for the country where the Products were purchased. Kodak will repair or replace Products if they fail to function properly during the warranty period, subject to any conditions and/or limitations stated herein. Warranty service will include all labor as well as any necessary adjustments and/or replacement parts. If Kodak is unable to repair or replace a Product, Kodak will, at its option, refund the purchase price paid for the Product provided the Product has been returned to Kodak along with proof of the purchase price paid. Repair, replacement, or refund of the purchase price are the sole remedies under the warranty. If replacement parts are used in making repairs, those parts may be remanufactured, or may contain remanufactured materials. If it is necessary to replace the entire Product, it may be replaced with a remanufactured Product. Remanufactured Products, parts and materials are warranted for the remaining warranty term of the original Product, or 90 days after the date of repair or replacement, whichever is longer.Appendix LimitationsThis warranty does not cover circumstances beyond Kodak's control. This warranty does not apply when failure is due to shipping damage, accident, alteration, modification, unauthorized service, misuse, abuse, use with incompatible accessories or attachments (such as third party ink or ink tanks), failure to follow Kodak's operation, maintenance or repacking instructions, failure to use items supplied by Kodak (such as adapters and cables), or claims made after the duration of this warranty. Kodak makes no other express or implied warranty for this product, and disclaims the implied warranties of merchantability and fitness for a particular purpose. In the event that the exclusion of any implied warranty is ineffective under the law, the duration of the implied warranty will be one year from the purchase date or such longer period as required by law. The option of repair, replacement, or refund is Kodak's only obligation. Kodak will not be responsible for any special, consequential or incidental damages resulting from the sale, purchase, or use of this product regardless of the cause. Liability for any special, consequential or incidental damages (including but not limited to loss of revenue or profit, downtime costs, loss of the use of the equipment, cost of substitute equipment, facilities or services, or claims of your customers for such damages resulting from the purchase, use, or failure of the Product), regardless of cause or for breach of any written or implied warranty is expressly disclaimed.Your rightsSome states or jurisdictions do not allow exclusion or limitation of incidental or consequential damages, so the above limitation or exclusion may not apply to you. Some states or jurisdictions do not allow limitations on how long an implied warranty lasts, so the above limitation may not apply to you. This warranty gives you specific rights, and you may have other rights which vary from state to state or by jurisdiction.Outside the United States and CanadaIn countries other than the United States and Canada, the terms and conditions of this warranty may be different. Unless a specific Kodak warranty is communicated to the purchaser in writing by a Kodak company, no warranty or liability exists beyond any minimum requirements imposed by law, even though defect, damage, or loss may be by negligence or other act.FCC compliance and advisoryKodak EasyShare z885 zoom digital cameraThis equipment has been tested and found to comply with the limits for a Class B digital device, pursuant toPart 15 of the FCC Rules. These limits are designed to provide reasonable protection against harmfulinterference in a residential installation.This equipment generates, uses, and can radiate radio frequency energy and, if not installed or used inaccordance with the instructions, may cause harmful interference to radio communications. However, there isno guarantee that interference will not occur in a particular installation.AppendixIf this equipment does cause harmful interference to radio or television reception, which can be determined by turning the equipment off and on, the user is encouraged to try to correct the interference by one or more of the following measures: 1) reorient or relocate the receiving antenna; 2) increase the separation between the equipment and the receiver; 3) connect the equipment to an outlet on a circuit different from that to which the receiver is connected; 4) consult the dealer or an experienced radio/TV technician for additional suggestions.Any changes or modifications not expressly approved by the party responsible for compliance could void the user’s authority to operate the equipment. Where shielded interface cables have been provided with the product or specified additional components or accessories elsewhere defined to be used with the installation of the product, they must be used in order to ensure compliance with FCC regulation.Australian C-tickCanadian DOC statement DOC Class B ComplianceThis Class B digital apparatus complies with Canadian ICES-003.Observation des normes-Classe BCet appareil numérique de la classe B est conforme à la norme NMB-003 du Canada.Waste Electrical and Electronic Equipment labelingVCCI Class B ITEIn the European Union, do not discard this product as unsorted municipal waste. Contact your local authorities or go to /go/recycle for recycling program information.N137Appendix Korean Class B ITEChinese RoHSEastman Kodak CompanyRochester, NY 14650Eastman Kodak Company, 2007Kodak, EasyShare, and Perfect Touch are trademarks of Eastman Kodak Company.4J6180_en。
802协议打包下载
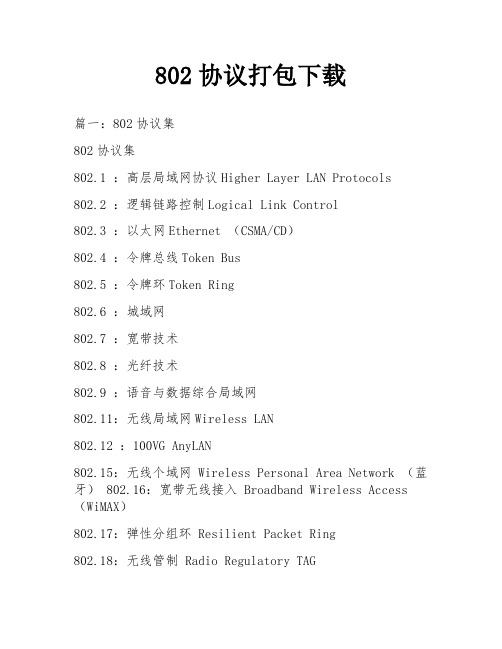
802协议打包下载篇一:802协议集802协议集802.1 :高层局域网协议Higher Layer LAN Protocols802.2 :逻辑链路控制Logical Link Control802.3 :以太网Ethernet (CSMA/CD)802.4 :令牌总线Token Bus802.5 :令牌环Token Ring802.6 :城域网802.7 :宽带技术802.8 :光纤技术802.9 :语音与数据综合局域网802.11:无线局域网Wireless LAN802.12 :100VG AnyLAN802.15:无线个域网 Wireless Personal Area Network (蓝牙) 802.16:宽带无线接入 Broadband Wireless Access (WiMAX)802.17:弹性分组环 Resilient Packet Ring802.18:无线管制 Radio Regulatory TAG802.19:共存 Coexistence TAG802.20:移动宽带无线接入 Mobile Broadband Wireless Access (MBWA) 802.21:媒质无关切换 Media Independent Handoff----------------------------------------------------------------------------------------------------------------------------------------------------------------IEEE802 协议是一种物理协议,因为有以下多种子协议,把这些协议汇集在一起就叫802协议集。
IEEE是电气和电子工程师协会(Institute of Electrical and Electronics Engineers)的简称,IEEE组织主要负责有关电子和电气产品的各种标准的制定。
- 1、下载文档前请自行甄别文档内容的完整性,平台不提供额外的编辑、内容补充、找答案等附加服务。
- 2、"仅部分预览"的文档,不可在线预览部分如存在完整性等问题,可反馈申请退款(可完整预览的文档不适用该条件!)。
- 3、如文档侵犯您的权益,请联系客服反馈,我们会尽快为您处理(人工客服工作时间:9:00-18:30)。
TECHNICAL DATA
SIMPLE MELODY GENERATOR
KK 8028-XX
DESCRIPTION
The KK 8028 is a CMOS LSI chip which electronically plays a prearranged melody. Selection of melody start signal is possible by mask option: orders specification suffix "L" indicate Level Hold Mode, and suffix "S" indicate One Shot Mode. The Universal version (as One Shot or Level Hold Mode) is possible also (suffix "U").
ABSOLUTE MAXIMUM RATINGS (Ta = 25o C)
Characteristic Symbol Value Unit
DC Supply Voltage V CC – V SS -0.3 ~ 3.5 V Input Voltage V IN V SS – 0.3 ~ V CC – 0.3
V
Operating Temperature T opr -20 ~ +65 o C Storage Temperature
T stg
-55 ~ +125
o
C
ELECTRICAL CHARACTERISTICS (T a = 25o C, V CC = 1.5V ; unless otherwise specified)
Characteristic Symbol Test Condition Min Typ Max Unit
Operating Voltage V CC
1.3 1.5 3.3 V
Supply Current
Stand-by
I S 0.1 1
Operating I CC Output open 60 µA
Output Drive Current I OH V CC =1.3V, V O =0.8V 0.6 1.5 mA Output Sink Current I OL V CC =1.3V, V O =0.5V
0.6
1.5
mA
Frequency Stability ∆F/F F OSC (1.6V) - F OSC (1.3V)
12 %
F OSC (1.3V)
APPLICATION CIRCUITS
LEVEL HOLD
ONE SHOT
TO-92 ONE SHOT OR LEVEL HOLD MODE CHIP FORM
FOR SPEAKER FOR PIEZO
50Ω
AVAILABLE SONG LIST
NEW EXT No. SONG LIST SEC
KK8028C-001 For Elise 13
KK8028C-002 Staff WRK
KK8028C-003 Happy
Birthday 13 KK8028C-004 Jingle Bell 12
KK8028C-005 It’s Small World 21
KK8028C-006 3 Children Song 13
KK8028C-007 Cuocoo
Waltz 10 KK8028C-008 London Bridge is Falling Down 16
KK8028C-009 Trainis Running Fast 11
KK8028C-010 Love Me Tender Love Me True 38
KK8028C-011 Love
Story 23 KK8028C-012 Old McDonald Had a Farm 25
KK8028C-013 Jingle Bell/Santa Claus Is Coming to Town/
We Wish You a Merry X'mas
28
KK8028C-014 You are My Sunshine 12
KK8028C-015 Santa Claus is Coming To Town 20
KK8028C-016 Silent
Night 26 KK8028C-017 Twinkle Twinkle Little Star 14
KK8028C-053 Car
Alarm
PAD LAYOUT
NOTE:Substrate is connected to V CC.
PAD LOCATION
Pad No. Designation X Y Description
Input
1 MT -445 -445
Start
Melody
2 BD 445 -435 Melody Output 1
3 BDN 445 145 Melody Output 2
4 V CC44
5 295 Positive Power Supply
5 V SS445 445 Negative Power Supply
Pad
Test
6 OSC -445 -282
Pad
Test
7 TEST -445 -169
• TO-92。