BH908T-C-HITE, 规格书,Datasheet 资料
MLX90808_Chinese

版本 001
3901090808
1/8
数08据年手0册2 月
MLX90808
集成绝对压力传感器
目录
1 原理图 ..........................................................................................................1 2 产品概述.......................................................................................................1 3 最大绝对额定值............................................................................................3 4 规电学参数 ...................................................................................................3 5 诊断特性.......................................................................................................4 6 细节概述.......................................................................................................4 7 独特特性.......................................................................................................5 8 应用信息.......................................................................................................5 9 编程和校正 ...................................................................................................6
产品规格书

不锈钢面发蓝色光 方(圆)形按钮
CANNY ELEVATOR CO., LTD.
第 6 页 共 42 页
乘客电梯
[2] 销售 & 生产 2.1 销售 & 生产开始
销售 : 2015 年 4 月 开始生产:2015 年 4 月生产 设计 & 制造场所:康力工厂 2.2 生产周期 以工厂运营中心数据实施,非标及特殊另行商议。
22 平层精度
±5mm(包括防震橡胶和钩环弹簧的挠度)
CANNY ELEVATOR CO., LTD.
第 7 页 共 42 页
乘客电梯
KLKS(新凌燕)
序号 23 24 25 26
参数名称
紧急停层时的平均减 速度
轿厢内噪音(一定时 间运行中) 层站(一定时间运行 中) 起居室噪音(一定时 间运行中)
KLKS-P14-CO96 KLKS-P14-CO105 KLKS-P14-CO120 P14―――额定载客人数 14 人标准轿厢 60―――额定速度 1.0m/s
CANNY ELEVATOR CO., LTD.
第 4 页 共 42 页
乘客电梯
KLKS(新凌燕)
(4)能量回馈技术(选配) 高纯净度的再生能量,卸下电网重担保持电梯机房正常“体温”,延长电梯寿命,消减谐波污染,净
化电网环境提高运行舒适性,实现完美驾驭。
1.4.2 品质电梯,优化生活 康力 KLKS(新凌燕)小机房乘客电梯充分体现康力电梯
召唤可直接安装在墙壁表面,因为其后的盒子被取消,因此只需开一个Φ30mm 的墙孔即可安装。
54字高红色 10"STNLED点阵 LCD液晶
不锈钢面发红色光 方(圆)形按钮
不锈钢面发蓝色光 方(圆)形按钮
Series 8, 建议用户名为:电子蒸煮烘箱CSG656BS7B用户手册说明书

Series 8, Built-in compact oven with steam function, 60 x 45 cm, Stainless steelCSG656BS7BIncluded accessories1 x grid, 1 x universal pan, punched, size XL, 1 x steam container, unpunched, size SOptional accessoriesHEZ617000 Pizza pan, enamelled, HEZ625071 Grill tray, anthracite enamelled, HEZ631070 Baking tray, enamelled, HEZ632070 Multipurpose pan, enamelled, HEZ636000 Glass pan, HEZ638D18 1 telescopic rail, full ext, 45cm, steam, HEZ660050 Cover Strip,HEZ660060 Strip, HEZ664000 Baking and roasting grid (steam), HEZ915003 Glass roasting dish, 5,4 L, HEZ36D163 Steam container, unpunched, size S, HEZ36D163G Steam container, punched, size S, HEZ530000 Half tray, HEZ531010 Baking tray, non-stick ceramic coated, HEZ532010 Universal pan, non-stick ceramic coated The compact steam oven with hot air function: lets you combine gentle cooking with the power of hot air.• Steam function: for gentle, healthy food preparation.• Added steam: your foods turn out crispy on the outside and juicy on the inside.• 4D Hotair: even heat distribution for perfect results.• TFT touchdisplay: clearly shows text and images, for easy and intuitive oven control.• EcoClean Direct: easy cleaning thanks to a coating that breaks down grease while you bake.Technical DataInstallation type: ......................................................................Built-in Door opening: ....................................................................Drop down Min. required niche size for installation (HxWxD): 450-455 x 560-568 x 550 mmDimensions: ........................................................455 x 594 x 548 mm Dimensions of the packed product (HxWxD): .....530 x 660 x 690 mm Control Panel Material: ................................................Stainless steel Door Material: ............................................................................Glass Net weight: ..............................................................................33.8 kg Length of electrical supply cord: ..........................................150.0 cm EAN code: (4242005125920)Fuse protection: ...........................................................................16 A Voltage: ...............................................................................220-240 V Frequency: ...........................................................................50; 60 Hz Plug type: .....................no plug (electrical connection by electrician) Number of cavities (2010/30/EC): . (1)Usable volume (of cavity) - NEW (2010/30/EC): ...........................47 l Energy efficiency rating: ..................................................................A+ Energy consumption per cycle conventional (2010/30/EC): ........0.73 kWh/cycleEnergy consumption per cycle forced air convection (2010/30/EC):0.61 kWh/cycleEnergy efficiency index (2010/30/EC): .....................................81.3 % Included accessories: ...............1 x grid, 1 x universal pan, 1 x steam container, punched, size S, 1 x steam container, punched, size XL, 1 x steam container, unpunched, size SSeries 8, Built-in compact oven with steam function, 60 x 45 cm, StainlesssteelCSG656BS7BThe compact steam oven with hot air function: lets you combine gentle cooking with the power of hot air.Design- 3x 2,5“-TFT colour and graphics display with direct touch function - Bosch control wheel- Drop down door, SoftClose, SoftOpen- 3 shelf positions- Straight bar handleFeatures- Home Connect ready- Digital temperature display with proposal- Actual temperature display Heating-up indicator- Control panel lock- Automatic safety switch off Residual heat indicator Start button Door contact switch- Location of water tank: Outside cavity- BoschAssist- Electronic clock timer- LED light, Light on/off when oven door opened/closed- Water tank empty indicator- Integral cooling fanCleaning- EcoClean Direct : ceiling, back panel, side liners- EcoClean Direct programme- Full glass inner doorProgrammes/functions- Compact steam oven with 12 main functions heating methods: 4D Hotair, Hotair Gentle, conventional top and bottom heat, conventional heat Gentle, Hotair grilling, full width variable grill, half width grill, pizza function, bottom heat, low temperature cooking, plate warming, keep warm- Additional functions:- Descaling programme- Drying function autom. boiling point detectionAccessories- Fast pre-heating function- 1 x steam container, punched, size S, 1 x steam container, punched, size XL, 1 x steam container, unpunched, size S, 1 x grid, 1 x universal panPerformance/technical information- Energy efficiency rating (acc. EU Nr. 65/2014): A+- Energy consumption per cycle in conventional mode:0.73 kWh- Energy consumption per cycle in fan-forced convection mode:0.61 kWh- Number of cavities: Main cavity Heat source: electrical Cavity volume:47 litre capacity- Temperature range 30 °C - 250 °C - 1 l Water tank- Power cord length 150 cm Cable length- Nominal voltage: 220 - 240 V- Appliance dimension (hxwxd): 455 mm x 594 mm x 548 mm- Please refer to the dimensions provided in the installation manualSeries 8, Built-in compact oven with steam function, 60 x 45 cm, Stainless steelCSG656BS7B。
6N137SD,6N137SD,6N137SD,HCPL2631SD,HCPL2631SD,HCPL2631SD,6N137,6N137S, 规格书,Datasheet 资料

8 1
8 1
8 1
Truth Table (Positive Logic)
Input
Enable
H
H
L
H
H
L
L
L
H
NC
L
NC
Output L H H H L H
©2005 Fairchild Semiconductor Corporation 6N137, HCPL2601, HCPL2611, HCPL2630, HCPL2631 Rev. 1.0.8
Dual Channel
VE = 0.5V
IEL
Low Level Enable Current VCC = 5.5V, VE = 0.5V
IEH
High Level Enable Current VCC = 5.5V, VE = 2.0V
VEH High Level Enable Voltage VCC = 5.5V, IF = 10mA
V EL
Low Level Enable Voltage VCC = 5.5V, IF = 10mA(3)
Min.
5.0
2.0
Typ.* Max. Unit
1.8
V
1.4 1.75
V
60
pF
-1.4Βιβλιοθήκη mV/°C710
mA
10
15
9
13
mA
14
21
-0.8 -1.6 mA
-0.6 -1.6 mA
V
0.8
Symbol
IFL IFH VCC VEL VEH TA N
Parameter Input Current, Low Level Input Current, High Level Supply Voltage, Output Enable Voltage, Low Level Enable Voltage, High Level Low Level Supply Current Fan Out (TTL load)
CG2145MS,CG2800MS,CG75MS,CG75LTR,CG2800LTR,CG2600LTR,CG2470L,CG75L, 规格书,Datasheet 资料

CG/CG2 Series
CG/CG2 Series
Description
Littelfuse highly reliable CG/CG2 Series GDTs provide a high degree of surge protection in a small size ideal for board level circuit protection. GDTs function as switches which dissipate a minimum amount of energy and therefore handle currents that far surpass other types of transient voltage protection. Their gas-filled, rugged ceramic metal construction make them well suited to adverse environments. The CG/CG2 series comes in a variety of forms including surface mount, core, straight and shaped leads, to serve a variety of mounting methods.
AGENCY FILE NUMBER
Agency Approvals
AGENCY
& &
2 Electrode GDT Graphical Symbol
The CG Series (75-110V) is ideal for protection of test and communication equipment and other devices in which low voltage limits and extremely low arc voltages are required. The CG2 Series (145V-1000V) is ideal for protecting equipment where higher voltage limits and holdover voltages are necessary.
TSOP34838;中文规格书,Datasheet资料

IR Receiver Modules for Remote Control SystemsMECHANICAL DATAPinning for TSOP348.., TSOP344..:1 = OUT, 2 = GND, 3 = V SPinning for TSOP322.., TSOP324..:1 = OUT, 2 = V S , 3 = GNDFEATURES•Very low supply current•Photo detector and preamplifier in one package •Internal filter for PCM frequency •Improved shielding against EMI •Supply voltage: 2.5 V to 5.5 V•Improved immunity against ambient light •Insensitive to supply voltage ripple and noise•Material categorization: For definitions of compliance please see /doc?99912DESCRIPTIONThese products are miniaturized receivers for infrared remote control systems. A PIN diode and a preamplifier are assembled on a lead frame, the epoxy package acts as an IR filter.The demodulated output signal can be directly decoded by a microprocessor. The TSOP348.., TSOP322.. are compatible with all common IR remote control data formats. The TSOP324.., TSOP344.. are optimized to suppress almost all spurious pulses from energy saving fluorescent lamps but will also suppress some data signals.This component has not been qualified according to automotive specifications.BLOCK DIAGRAMAPPLICATION CIRCUITPARTS TABLECARRIER FREQUENCY STANDARD APPLICATIONS(AGC2)VERY NOISY ENVIRONMENTS(AGC4)PINNING1 = OUT,2 = GND,3 = V S1 = OUT,2 = V S ,3 = GND1 = OUT,2 = GND,3 = V S1 = OUT,2 = V S ,3 = GND30 kHz TSOP34830TSOP32230TSOP34430TSOP3243033 kHz TSOP34833TSOP32233TSOP34433TSOP3243336 kHz TSOP34836TSOP32236TSOP34436TSOP3243638 kHz TSOP34838TSOP32238TSOP34438TSOP3243840 kHz TSOP34840TSOP32240TSOP34440TSOP3244056 kHzTSOP34856TSOP32256TSOP34456TSOP32456Note•Stresses beyond those listed under “Absolute Maximum Ratings” may cause permanent damage to the device. This is a stress rating only and functional operation of the device at these or any other conditions beyond those indicated in the operational sections of this specification is not implied. Exposure to absolute maximum rating conditions for extended periods may affect the device reliability.TYPICAL CHARACTERISTICS (T amb = 25 °C, unless otherwise specified)Fig. 1 - Output Active Low Fig. 2 - Pulse Length and Sensitivity in Dark AmbientABSOLUTE MAXIMUM RATINGSPARAMETER TEST CONDITIONSYMBOLVALUE UNIT Supply voltage V S - 0.3 to + 6V Supply current I S 3mA Output voltage V O - 0.3 to (V S + 0.3)V Output current I O 5mA Junction temperature T j 100°C Storage temperature range T stg - 25 to + 85°C Operating temperature range T amb- 25 to + 85°C Power consumption T amb ≤ 85 °C P tot 10mW Soldering temperaturet ≤ 10 s, 1 mm from caseT sd260°CELECTRICAL AND OPTICAL CHARACTERISTICS (T amb = 25 °C, unless otherwise specified)PARAMETER TEST CONDITION SYMBOLMIN.TYP.MAX.UNIT Supply current E v = 0, V S = 3.3 V I SD 0.270.350.45mA E v = 40 klx, sunlightI SH 0.45mA Supply voltage V S 2.55.5V Transmission distance E v = 0, test signal see fig. 1,IR diode TSAL6200,I F = 250 mA d 45m Output voltage low I OSL = 0.5 mA, E e = 0.7 mW/m 2,test signal see fig. 1V OSL 100mV Minimum irradiance Pulse width tolerance:t pi - 5/f 0 < t po < t pi + 6/f 0,test signal see fig. 1E e min.0.10.25mW/m 2Maximum irradiance t pi - 5/f 0 < t po < t pi + 6/f 0,test signal see fig. 1E e max.30W/m 2DirectivityAngle of half transmissiondistanceϕ1/2± 45degE eV O V VFig. 3 - Output Function Fig. 4 - Output Pulse Diagram Fig. 5 - Frequency Dependence of Responsivity Fig. 6 - Sensitivity in Bright AmbientFig. 7 - Sensitivity vs. Supply Voltage DisturbancesFig. 8 - Sensitivity vs. Electric Field DisturbancesEV O V V OL0.00.20.40.60.81.01.20.70.9 1.1 1.3f/f 0 - Relative Frequency16925E /E - R e l. R e s p o n s i v i t y e m i n.eFig. 9 - Max. Envelope Duty Cycle vs. Burst Length Fig. 10 - Sensitivity vs. Ambient TemperatureFig. 11 - Relative Spectral Sensitivity vs. WavelengthFig. 12 - Horizontal DirectivityFig. 13 - Sensitivity vs. Supply VoltageSUITABLE DATA FORMATThese products are designed to suppress spurious output pulses due to noise or disturbance signals. Data and disturbance signals can be distinguished by the devices according to carrier frequency, burst length and envelope duty cycle. The data signal should be close to the band-pass center frequency (e.g. 38 kH z) and fulfill the conditions in the table below.When a data signal is applied to the IR receiver in the presence of a disturbance signal, the sensitivity of the receiver is reduced to insure that no spurious pulses are present at the output. Some examples of disturbance signals which are suppressed are:•DC light (e.g. from tungsten bulb or sunlight)•Continuous signals at any frequency•Strongly or weakly modulated noise from fluorescent lamps with electronic ballasts (see figure 14 or figure 15)Fig. 14 - IR Signal from Fluorescent Lampwith Low ModulationFig. 15 - IR Signal from Fluorescent Lampwith High ModulationNote•For data formats with short bursts please see the datasheet for TSOP323.., TSOP325.., TSOP343.., TSOP345..0101520Time (ms)16920I R S i g n a l50101520Time (ms)16921I R S i g n a l5TSOP322.., TSOP348..TSOP324.., TSOP344..Minimum burst length10 cycles/burst 10 cycles/burst After each burst of lengtha minimum gap time is required of10 to 70 cycles ≥ 10 cycles 10 to 35 cycles ≥ 10 cycles For bursts greater thana minimum gap time in the data stream is needed of 70 cycles > 4 x burst length35 cycles> 10 x burst lengthMaximum number of continuous short bursts/second 18001500Recommended for NEC code yes yes Recommended for RC5/RC6 code yes yes Recommended for Sony codeyes no Recommended for Thomson 56 kHz codeyes yes Recommended for Mitsubishi code (38 kHz, preburst 8 ms, 16 bit)yes no Recommended for Sharp codeyesyesSuppression of interference from fluorescent lampsMost common disturbance signals are suppressedEven extreme disturbance signals are suppressedPACKAGE DIMENSIONS in millimetersLegal Disclaimer Notice VishayDisclaimerALL PRODU CT, PRODU CT SPECIFICATIONS AND DATA ARE SU BJECT TO CHANGE WITHOU T NOTICE TO IMPROVE RELIABILITY, FUNCTION OR DESIGN OR OTHERWISE.Vishay Intertechnology, Inc., its affiliates, agents, and employees, and all persons acting on its or their behalf (collectively,“Vishay”), disclaim any and all liability for any errors, inaccuracies or incompleteness contained in any datasheet or in any other disclosure relating to any product.Vishay makes no warranty, representation or guarantee regarding the suitability of the products for any particular purpose or the continuing production of any product. To the maximum extent permitted by applicable law, Vishay disclaims (i) any and all liability arising out of the application or use of any product, (ii) any and all liability, including without limitation special, consequential or incidental damages, and (iii) any and all implied warranties, including warranties of fitness for particular purpose, non-infringement and merchantability.Statements regarding the suitability of products for certain types of applications are based on Vishay’s knowledge of typical requirements that are often placed on Vishay products in generic applications. Such statements are not binding statements about the suitability of products for a particular application. It is the customer’s responsibility to validate that a particular product with the properties described in the product specification is suitable for use in a particular application. Parameters provided in datasheets and/or specifications may vary in different applications and performance may vary over time. All operating parameters, including typical parameters, must be validated for each customer application by the customer’s technical experts. Product specifications do not expand or otherwise modify Vishay’s terms and conditions of purchase, including but not limited to the warranty expressed therein.Except as expressly indicated in writing, Vishay products are not designed for use in medical, life-saving, or life-sustaining applications or for any other application in which the failure of the Vishay product could result in personal injury or death. Customers using or selling Vishay products not expressly indicated for use in such applications do so at their own risk and agree to fully indemnify and hold Vishay and its distributors harmless from and against any and all claims, liabilities, expenses and damages arising or resulting in connection with such use or sale, including attorneys fees, even if such claim alleges that Vishay or its distributor was negligent regarding the design or manufacture of the part. Please contact authorized Vishay personnel to obtain written terms and conditions regarding products designed for such applications.No license, express or implied, by estoppel or otherwise, to any intellectual property rights is granted by this document or by any conduct of Vishay. Product names and markings noted herein may be trademarks of their respective owners.Material Category PolicyVishay Intertechnology, Inc. hereb y certifies that all its products that are identified as RoHS-Compliant fulfill the definitions and restrictions defined under Directive 2011/65/EU of The European Parliament and of the Council of June 8, 2011 on the restriction of the use of certain hazardous substances in electrical and electronic equipment (EEE) - recast, unless otherwise specified as non-compliant.Please note that some Vishay documentation may still make reference to RoHS Directive 2002/95/EC. We confirm that all the products identified as being compliant to Directive 2002/95/EC conform to Directive 2011/65/EU.分销商库存信息: VISHAYTSOP34838。
NCP1521ASNT1G,NCP1521ASNT1G,NCP1521UEVB, 规格书,Datasheet 资料

Stresses exceeding Maximum Ratings may damage the device. Maximum Ratings are stress ratings only. Functional operation above the Recommended Operating Conditions is not implied. Extended exposure to stresses above the Recommended Operating Conditions may affect device reliability. 1. Maximum electrical ratings are defined as those values beyond which damage to the device may occur at TA = 25°C. 2. According to JEDEC standard JESD22-A108B.
A
= Assembly Location
Y
= Year
W
= Work Week
G
= Pb-Free Package
(Note: Microdot may be in either location)
ORDERING INFORMATION
Device
Package
Shipping
NCP1521ASNT1G TSOP-5 3000/Tape & Reel (Pb-Free)
Eff (%)
NCP1521
100 90
80
70
Vout = 3.3 V
60
Vin = 4.2 V
TA = 25°C
管道规格书资料

一、管道等级代号说明管道等级代号采用下列三个单元字符组成×××第三单元,表示相同的公称压力和类似的或相同的基本材料下变化的顺序号第二单元,表示基本材料第一单元,表示法兰的公称压力第一单元法兰公称压力的数值1.0——表示法兰公称压力为1.0MPa1.6——表示法兰公称压力为1.6MPa2.0——表示法兰公称压力为2.0MPa2.5——表示法兰公称压力为2.5MPa4.0——表示法兰公称压力为4.0MPa5.0——表示法兰公称压力为5.0MPa6.3——表示法兰公称压力为6.3MPa10.0——表示法兰公称压力为10.0MPa16.0——表示法兰公称压力为16.0MPa第二单元基本材料的符号为英文字母A——碳钢10、20、20R、20G、B3F、Q235-A、Q235-AFB——16Mn、16MnRC——15CrMo、12CrMoD——铸铁、可锻铸铁E——合金钢F——衬里(橡胶衬里、非金属衬里等)G——1¼Cr½Mo、5Cr½Mo(1Cr5Mo)K——1Cr18Ni9Ti、0Cr18Ni10TiL——铝M——蒙乃尔合金N——镍P——塑料管(PVC、PE、PP)R——玻璃钢X——镀锌其他字母预留第三单元由数字符号表示变化的顺序号,表示适用介质的不同、腐蚀裕量的不同、管件或阀门的选择有较大的不同。
按流水号顺序,无特殊含义。
二、三维配管软件常用缩写词1. 端面代码对照表2. 阀门代码对照表3. 管件代码对照表三、管道分支表HEADER 主管B BOSS(HCOUPL)接缘(单头管箍)W WELD 焊接RT REDUCING TEE 异径三通BW BRANCH WELD 补强焊接T TEE 等径三通四、管道规格书项目设计时需填写管道规格书,管道规格书分首页和副页。
首页按项目实际需要列入所需等级及应用的介质代号和介质名称,填写操作条件。
在副页中将对应的管道等级列出,并按项目实际需要填写设计温度和设计压力。
长城电源技术规格书说明书

电源技术规格书(客户承认书)SPECIFICATION FOR APPROV AL客户/ CUSTOMER: 光电显示客户物料号/CUSTOMER NO.:长城型号/ MODEL NO.: XSP200WV42B长城料号/ P/N .: 5171915电源版本/ POWER REV.: V01日期/ DATE: 2020.02.27客户确认签字,盖章后请回传一份承认书给我司。
Please return to us on copy of “SPECIFICATION FOR APPROV AL”with your approved signature.中国长城科技集团股份有限公司电源事业部China Greatwall Technology Group Co., LTD. Power Supply Division深圳宝安区石岩镇宝石东路长城工业园Great wall Industry Park, Baoshi East Rd, Shiyan Country, Baoan, ShenzhenTEL: 0755--29519374 / 26639997 FAX: 0755--29519395/power变更记录目录总则 (2)1 电气特性 (2)1.1输入特性 (2)1.1.1输入基本特性 (2)1.1.2输入保护特性 (2)1.2 输出特性 (2)1.2.1输出基本特性 (2)1.2.2输出保护特性 (3)1.2.3负载/温度曲线图&负载/输入电压曲线图 (3)2 环境 (4)3 电磁兼容性 (4)4 安规 (4)5 可靠性 (4)6 特殊要求 (4)7 外观结构 (5)7.1电源尺寸 (5)7.2标签图 (6)8 包装 (6)8.1电源净重 (6)8.2包装图 (6)8.3包装运输实验 (7)9条形码label说明 (7)10 使用注意事项 (8)10.1开箱检查 (8)10.2使用原则 (8)10.3安全注意事项 (8)11 产品保修 (8)11.1保修期限 (8)11.2维修范围 (8)11.3限制条款 (9)12 备注 (9)总则该款产品为AC转DC电源,90~264Vac交流输入,单路直流隔离输出,输出总功率168W,通过CCC、CE、UL认证,符合欧盟RoHS指令。
FOD3120,FOD3120SDV,FOD3120SD,FOD3120TV,FOD3120V,FOD3120T,FOD3120SV,FOD3120TS, 规格书,Datasheet 资料

Symbol TSTG TOPR TJ TSOL
IF(AVG) IF(PEAK)
f VR IO(PEAK) VCC – VEE
VO(PEAK) tR(IN), tF(IN)
PDI PDO
Parameter
Storage Temperature
Operating Temperature
Junction Temperature
Symbol
Parameter
Installation Classifications per DIN VDE 0110/1.89 Table 1
For Rated Mains Voltage < 150Vrms
For Rated Mains Voltage < 300Vrms
For Rated Mains Voltage < 450Vrms
FOD3120 — High Noise Immunity, 2.5A Output Current, Gate Drive Optocoupler
October 2009
FOD3120 High Noise Immunity, 2.5A Output Current, Gate Drive Optocoupler
VO Low Low Transition High
©2003 Fairchild Semiconductor Corporation
FOD3120 Rev. 1.17.0
2
芯天下--/
FOD3120 — High Noise Immunity, 2.5A Output Current, Gate Drive Optocoupler
Stresses exceeding the absolute maximum ratings may damage the device. The device may not function or be operable above the recommended operating conditions and stressing the parts to these levels is not recommended. In addition, extended exposure to stresses above the recommended operating conditions may affect device reliability. The absolute maximum ratings are stress ratings only.
Hiteco自动换刀电主轴快速使用说明接线端子型2014-9-28

压力 管径(外 X 内) 6bar Ø6x4
6bar Ø4x2.5
6bar Ø6x4
注意,非常重要!!电主轴通电旋转的时候进气口 2 必须要通气!
4
意大利 HITEC 海铁克自动换刀电主轴快速安装指南 (2) 气动图:请参看 Hiteco 电主轴使用手册第 4.4 节
1 工厂压缩空气提供 2 5 微米过滤 3 0.1 微米过滤 4 压力调节开关 5 松拉刀压缩空气提供 单稳 两位 5 通电磁阀 6 快卸阀(防止单稳 5V-2P 电磁阀泄漏) 7 压力调节开关 8 刀柄清洁压吹气提供 单稳 两位 1 通 电磁阀
意大利 HITEC 海铁克自动换刀电主轴快速安装指南 - 新电主轴第一次上电旋转之前,请确保执行以下步骤。
安装电主轴的面板,要求平面度不大于 0.02mm,表面粗糙度不大于 Ra 1.6。
注意锁紧螺丝的长度,锁紧螺丝旋转到位后,锁紧螺丝头端和 T 型槽底部必须留有空隙。
进入到电主轴的压缩空气必须经过干燥和不大于 0.5 微米的过滤,并且含油量小于每立方米 1 毫克。 确保电主轴上 Ø4 的那个空气接头已经通入并保持 6Bar 的压缩空气,观察并确保电主轴头端旋转部分和非旋转部分之间的空隙有轻微空气流出(此 状态表示气密封工作正常) 按照电主轴铭牌上的参数表设置电主轴参数,注意确保一下参数设置正确:额定电压,额定频率,最大电流,最大频率。 设置 PWM 开关频率为 8 kHz. 根据刀具的尺寸设置相应的电主轴转速(具体设置数值参看使用说明书 6.8 节).
系统发出拉刀指令 电主轴下降,准备纳入刀柄
停止电主轴锥面清洁吹气(电主轴离抓刀位置20mm的时候停止此吹气 )
电主轴继续下降, 直至拉刀位置
松刀电磁阀停止供气
NO
CD74HCT390M96,CD74HCT390M96E4,CD74HC390M96E4,CD74HC390M96G4,CD74HCT390E, 规格书,Datasheet 资料

16 Ld SOIC
CD74HC390M96
-55 to 125
16 Ld SOIC
CD74HCT390E
-55 to 125
16 Ld PDIP
CD74HCT390M
-55 to 125
16 Ld SOIC
CD74HCT390MT
-55 to 125
16 Ld SOIC
CD74HCT390M96
-55 to 125
73
Maximum Junction Temperature . . . . . . . . . . . . . . . . . . . . . . . 150oC
Maximum Storage Temperature Range . . . . . . . . . .-65oC to 150oC
Maximum Lead Temperature (Soldering 10s) . . . . . . . . . . . . . 300oC
For VI < -0.5V or VI > VCC + 0.5V . . . . . . . . . . . . . . . . . . . . . .±20mA DC Output Diode Current, IOK
For VO < -0.5V or VO > VCC + 0.5V . . . . . . . . . . . . . . . . . . . .±20mA DC Output Source or Sink Current per Output Pin, IO
3 (13) nQ0
4 (12) nCP1
GND = 8 VCC = 16
÷5
IP1001,IP1001TR,IP1001,IP1001TR, 规格书,Datasheet 资料

• 3.3V to 12V input voltage 1•20A maximum load capability, with no derating up to T PCB = 90°C • 5 bit DAC settable, 0.925V to 2V output voltage range 2•Configurable down to 3.3Vin & up to 3.3Vout with simple external circuit 3•200kHz or 300kHz nominal switching frequency •Optimized for very low power losses •Over & undervoltage protection •Adjustable lossless current limit•Internal features minimize layout sensitivity *•Very small outline 14mm x 14mm x 3mmFull Function Synchronous Buck Power BlockIntegrated Power Semiconductors, Control IC & PassivesThe iP1001 is a fully optimized solution for high current synchronous buck applications requiring up to 20A.The iP1001 is optimized for single-phase applications, and includes a full function fast transient response PWM control, with an optimized power semiconductor chip-set and associated passives, achieving benchmark power density. Very few external components are required, including output inductor, input & output capacitors.Further range of operation to 3.3Vin can be achieved with the addition of a simple external boost circuit, and operation up to 3.3Vout can be achieved with a simple external voltage divider.iPOWIR technology offers designers an innovative board space-saving solution for applications requiring high power densities. iPOWIR technology eases design for applications where component integration offers benefits in performance and functionality. iPOWIR technology solutions are also optimized internally for layout,heat transfer and component selection.DescriptioniP1001 Power BlockFeatures* Although, all of the difficult PCB layout and bypassing issues have been addressed with the internal design of the iPOWIR block, proper layout techniques should be applied for the design of the power supply board. There are no concerns about unwanted shutdowns common to switching power supplies, if operated as specified. TheiPOWIR block will function normally, but not optimally without any additional input decoupling capacitors. Input decoupling capacitors should be added at Vin pin for stable and reliable long term operation. No additional bypassing is required on the Vdd pin. See layout guidelines in datasheet for more detailed information.PD - 94336c05/20/03iP1001 1iP1001Absolute Maximum Ratings Recommended Operating ConditionsElectrical Specifications @ VDD = 5V & TPCB0°C - 90°C (Unless otherwise specified)All specifications @ 25°C (unless otherwise specified) 2 3iP1001Electrical Specifications (continued)Notes :1 For Vin less than 4.5V requires external 5V DD supply.2 Can be modified to operate up to 3.3V OUT , outside of DAC settable range. See Design Guidelines on how to setoutput voltage greater than 2V.3 See design guidelines.4 See Fig.5 for Recommended Operating Area4iP1001Fig 1. Power Loss vs CurrentFig 2. Safe Operating Area (SOA) vs T PCBAdjusting the Power Loss and SOA curves for different operating conditionsTo make adjustments to the power loss curves in Fig. 1, multiply the normalized value obtained from the curves in Figs. 3,or 4 by the value indicated on the power loss curve in Fig. 1. If multiple adjustments are required, multiply all of the normalized values together, then multiply that product by the value indicated on the power loss curve in Fig. 1. The resulting product is the final power loss based on all factors.To make adjustments to the SOA curve in Fig. 2, determine the maximum allowed PCB temperature in Fig. 2 at the required operating current. Then, add the correction temperature from the normalized curves in Figs. 3 or 4 to find the final maximum allowable PCB temperature. When multiple adjustments are required, add all of the temperatures together, then add the sum to the PCB temperature indicated on the SOA graph to determine the final maximum allowable PCB temperature based on all factors.Note: If input voltage <5Vin nominal operation is required then first see Fig. 5 for maximum current capability limit.Operating Conditions for the examples below:Output Current = 20A Input Voltage = 7VOutput Voltage = 2.5VAdjusting for Maximum Power Loss:(Fig. 1)Maximum power loss =5 W(Fig. 3)Normalized power loss for output voltage ≈1.14(Fig. 4)Normalized power loss for input voltage ≈0.89Adjusted Power Loss = 5W x 0.89 x 1.14 ≈ 5.07WAdjusting for SOA Temperature:(Fig. 2)SOA PCB Temperature = 90°C(Fig. 3)Normalized SOA PCB Temperature for output voltage ≈ -4.5°C (Fig. 4)Normalized SOA PCB Temperature for input voltage ≈ 4°C Adjusted SOA PCB Temperature = 90°C + 4°C -4.5°C ≈ 89.5°CGuaranteed Performance Curves0.00.51.01.52.02.53.03.54.04.55.002468101214161820Output Current (A)P o w e r L o s s (W )2468101214161820220102030405060708090100110120130PCB Temperature (°C)O u t p u t C u r r e n t (A ) 5iP1001Fig 4. Normalized Power Loss vs V INFig 3. Normalized Power Loss vs V OUTFig 5. Recommended Operating AreaFor 200kHz frequency setting there will be a 10% power loss reduction and a positive PCB temperature adjustment of 3°C.Typical Performance CurvesOutput Voltage (V)05101520250.91.21.51.82.12.42.73.03.3Input Voltage (V)SOA PCB Temperature Adjustmentltage (°C)SOA PCB Temperature Adjustmentltage (°C)P o w e r L o s s (N o r m a l i z e d )P o w e r L o s s (N o r m a l i z e d )Output Voltage (V)L o a d C u r r e n t (A )0.880.941.001.061.121.181.241.301.360.91.3 1.72.1 2.5 2.93.3-13-11-9-6-4-20240.830.860.890.910.940.971.00345678910111201234566iP1001D4 D3 D2 D1 D0 OUTPUTVOLTAGE(V)0 0 0 0 0 2.00 0 0 0 0 1 1.95 0 0 0 1 0 1.90 0 0 0 1 1 1.85 0 0 1 0 0 1.80 0 0 1 0 1 1.75 0 0 11 0 1.70 0 0 1 1 1 1.65 0 1 0 0 0 1.60 0 1 0 0 1 1.55 0 1 0 1 0 1.50 0 1 0 1 1 1.45 0 1 1 0 0 1.40 0 1 1 0 1 1.35 0 1 1 1 0 1.30 0 1 1 1 1 Shutdown* 1 0 0 0 0 1.275 1 0 0 0 1 1.250 1 0 0 1 0 1.225 1 0 0 1 1 1.200 1 0 1 0 0 1.175 1 0 1 0 1 1.150 1 0 1 1 0 1.125 1 0 1 1 1 1.100 1 1 0 0 0 1.075 1 1 0 0 1 1.050 1 1 0 1 0 1.025 1 1 0 1 1 1.000 1 1 1 0 0 0.975 1 1 1 0 1 0.950 1 1 1 1 0 0.925 1 1 1 1 1Shutdown** Shutdown : Upon receipt of the shutdown code (per VID code table above), both FET s are turned OFF and the output is discharged as the undervoltage protection is activated.Table 1. VID Code Table 2Fig 6. Overcurrent adjustment settings using R LIM7iP1001Table 2. Pin DescriptioniP100189iP1001Fig 8. Recommended PCB Footprint (Top View)NCNC NC NC NC NC NCNC NC NCNC NCNC NC NC NC NC NC NC NC NC NC NCNC NC NCNCNC NC NC NC NCNC NCNCENABLEPGOOD D0D1D2D3D4 V DDV SWPGNDPGNDV ING N D SSGND FREQ ILIMV FNC V FSiP1001iP1001 User’s Design GuidelinesThe iP1001 is a 20A power block that consists of optimized power semiconductors, PWM control and its associated passive components. It is based on a synchronous buck topology and offers an optimized solution where space, efficiency and noise caused by stray parasitics are of concern. The iP1001 com-ponents are integrated in a ball grid array (BGA) pack-age where the electrical and thermal conduction is accomplished through solder balls. FUNCTIONAL DESCRIPTIONVINThe standard iP1001 operating input voltage range is 5V to 12V. The input voltage can also be easily configured to run at voltages down to 3.3V.FREQThe PWM control is pseudo current mode. The ESR of the output filter capacitor is used for current sens-ing and the output voltage ripple developed across the ESR provides the PWM ramp signal.iP1001 offers two switching frequency settings, 200kHz and 300kHz. At a given setting the switching frequency will remain relatively constant indepen-dent of load current.VDD(+5V bias)An external 5V bias supply is required to operate the iP1001. In applications where input voltages are lower than 4.5V, and where 5V is not available, aspecial boost circuit is required to supply VDD with 5V(as shown in the reference design). Soft Start, VDDUndervoltage LockoutWhen VDD rises above 4.2V a soft start is initiated byramping the maximum allowable current limit. The ramp time is typically 1.8ms. An external capacitor can be added across the current limit resistor from ILIM to PGND to provide up to 5ms ramp time. Select the capacitor according to the 10nf/ms rule. PGOODThe PGOOD comparator constantly monitors VFfor undervoltage. A 5% drop in output voltage can cause PGOOD to go low. PGOOD pin is internally pulled-up to VDDthrough a 100K, 5% resistor. If it is desired to use the PGOOD signal to enable another stage using iP1001, then it is recommended to filter and buffer PGOOD to prevent transients appearing at the output from pulling PGOOD low.OVP (Output Overvoltage Protection)If the overvoltage trip 2.25V threshold is reached, the OVP is triggered, the circuit is shutdown and the bottom FET is latched on discharging the output filter capacitor. Pulling ENABLE low resets the latch. The overvoltage trip threshold is scaled accordingly, if output voltages greater than 2V are set through voltage dividers.UVP (Output Undervoltage Protection)The Output Undervoltage Protection trip threshold is fixed at 0.8V. If ENABLE is pulled up and VFis below 0.8V for a duration of 10-20ms, the PWM will be in a latched state, with the bottom FET latched on, and will not restart until ENABLE is recycled.DAC Converter (D0-D4)The output voltage is programmed through a 5-bit DAC (see the VID code in table 1). The output volt-age can be programmed from 0.925V to 2V. To elimi-nate external resistors, the DAC pins are internally pulled up. To set for output voltages above 2V, the DAC must be set to 2V and a resistor divider,R3 & R4 (see Fig 10.), is used. The values of the resistors are selected using equation 1.Equation 1 : Vout = VFx (1 + R3/R4)where VFis equal to the DAC settingand R4 is recommended to be ~1kΩTable 3 - iP1001 Operating Truth Table10 11iP1001DESIGN PROCEDUREInductor SelectionThe inductor is selected according to the following expression.L = V OUT x (1-D) / (fsw x ∆I L )where, D = VOUT/ VINV OUT is the output voltage in Volts,fsw is the switching frequency in kHz,∆I L is the output inductor ripple current.The inductor value should be selected from 0.8µH to 2.0µH range.Output Capacitor SelectionUse tantalum or POSCAP type capacitors for iP1001.Selection of the output capacitors depends on several factors.•Low effective ESR for ripple and load transient requirements.•Stability.To support the load transients and to stay within a specified voltage dip ∆V due to the transients, ESR selection should satisfy the following equation:R ESR ≤ ∆V/∆Iwhere, ∆I is the transient load stepIf output voltage ripple is required to be maintained at specified levels then, the following expression should be used to select the output capacitors.R ESR ≤ V p-p / ∆I Lwhere, V p-p is the peak to peak output voltage ripple.The value of the output capacitor ESR zero frequency also determines stability. The value of the ESR zero frequency is calculated by the expression:R ESR = 1 / (2π x f ESR x C OUT )A 470µF POSCAP capacitor has a maximum 35m Ωof ESR which provides 9.7kHz zero frequency.The ESR zero frequency must be set below 12kHz.This value is calculated assuming the capacitor datasheet maximum ESR value.Example:To determine the amount of capacitance to meet a 30mVp-p output ripple, with 4A inductor current ripple requirement.The calculated ESR will be = 30mV/4A =7.5m Ω. This will require 5 x 470uF POSCAP capacitors. The total ESR will result in a 9.7kHz zero frequency.For stable operation:• Set the resonant frequency f o of the output inductor and capacitor between 2kHz and 4kHz.The resonant frequency is calculated using the following expression:f o = 1/ (2π x (√LC))• Select the output inductor value between 0.8µHto 2.0µH and the output capacitance between 1880µF (4x 470µF) and 5600µF (12x470µF)• Set the minimum output ripple voltage to begreater than 0.5% of the output voltage. Select the capacitor by ESR and by voltage rating rather than capacitance.External Input Capacitor SelectionThe switching currents impose RMS current requirements on the input capacitors. The following expression allows the selection of the input capacitors, based on the input RMS current:I RMS = I LOAD x ( √D x (1-D))where, D = V OUT /V IN12iP1001Application IssuesSetting V OUT above 2VIn certain applications where the output voltage is required to be set higher than the maximum DAC code setting of 2V, it is possible to use an external resistive voltage divider which, for accuracy, needs to have 1% or better tolerance. The switching frequency should be set at 200kHz by connecting the FREQ pin to V DD . Also, the output voltage should never be set higher than 3.3V with a V IN minimum of 5V, or 2.5V with a V IN minimum of 3.3V. The DAC code should be set to 2V and the following equation used to select the resistors:V OUT = V F x (1 + R3/R4)See the reference design for reference designators.Note that the impedance at V F is 180K Ω ±35%. It is recommended that R3 be calculated assuming a value of 1k Ω for R4. Connect V FS to V F and GNDS to PGND.Duty Cycle D = V OUT / V IN >50%For duty cycles >50% the switching frequency should be set at 200kHz. 300kHz switching frequency can be selected if the output is less than 2V and the duty cycle is <50%.For duty cycles >50%, add external compensation ramp from the Vsw terminal of the iP1001 device as shown in the reference design through R9 resistor and C21 capacitor (Fig 10a.). For optimum perfor-mance maintain a RC time constant of approximately 5µs. 13iP1001For stable and noise free operation of the whole power system it is recommended that the designer uses to the following guidelines.1. Follow the layout scheme presented in Fig.9.Make sure that the output inductor L1 is placed as close to the iP1001 as possible to prevent noise propagation that can be caused by switching of power at the switching node V SW , to sensitive circuits.2. Provide a mid-layer solid ground with connections to the top layer through vias. The two PGND pads of the iP1001 also need to be connected to the same ground plane through vias.3. Do not connect SGND pins of the iP1001 to PGND.4. To increase power supply noise immunity, place input and output capacitors close to one another, as shown in the layout diagram. This will provide short high current paths that are essential at the ground terminals.Fig 9. iP1001 suggested layout5. Although there is a certain degree of V IN bypassing inside the iP1001, the external input decoupling capacitors should be as close to the device as possible.6. In situations where the load is located at an appreciable distance from the iP1001 block, it is recommended that at least one or two capacitors be placed close to the iP1001 to derive the V F signal.7. The V F connection to the output capacitors should be as short as possible and should be routed as far away from noise generating traces as possible.8. V FS & GNDS pins need to be connected at the load for remote sensing. If remote sensing is not used connect V FS to V F and GNDS to PGND.9. Refer to IR application note AN-1029 to determine what size vias and what copper weight and thickness to use when designing the PCB.Layout GuidelinesInput TerminalLoad T erminalV OUTOutput Caps (C OUT )Input Caps (C IN )V INPGNDV SWOutput Inductor (L 1)PGNDiP1001 BlockiP1001The schematics in Fig.10a & 10b and complete Bill of Materials in Table 4 are provided as a reference design to enable a preliminary evaluation of iP1001. They represent a simple method of applying the iP1001 solution in a synchronous buck topology. Fig. 10a shows the implementation for <5VIN nominal applications, and Fig. 10b shows theimplementation for 5VIN - 12VINnominalapplications.The connection pins are provided through the solder balls on the bottom layer of the package. A total power supply solution is presented with the addition of inductor L1 and the output capacitors C11-C14. Input capacitors C1-C10 are for bypassing in the5VIN - 12VINapplication, but only C1-C3 are requiredfor <5VIN applications (refer to the BOM for values).Switches 1-5 of SW1 are used to program the output voltage. Refer to the VID table provided in this datasheet for the code that corresponds to the desired output voltage. Resistors R2 & R4 need to be removed for operation at standard VID levels (0.925V - 2.0V, leave R3 = 0Ω). Switch 8 of SW1 enables the output when floating (internally pulledhigh). The 5V VDD power terminal and input powerterminals are provided as separate inputs. They can be connected together if the application requires only 5V nominal input voltage.The reference design also offers a higher output voltage option for greater than 2.0V, up to 3.3V. For output voltages above 2V, the DAC setting must be set to 2V, and then select resistors R3 & R4 per Equation 1 on page 10 for the desired output volt-age. Remove R5 and connect VF to VFSthrough R2,where R2=0Ω. In this case, GNDS should be refer-enced to PGND. Tighter regulation can be achieved by using resistors with less than 1% tolerance. For Vin < 5V and Vout > 2V, the frequency select pin (FREQ) must be set to 200kHz (connected to VDD).For applications with VIN < 5V and where there is noauxiliary 5V available, connections JP2 and JP3 must be provided in order to enable the boost cir-cuit. This will provide 5V VDD necessary for theiP1001 internal logic to function. The boost circuit will convert 3.3V input voltage to 5V, to power theVDD , and will provide enough power to supply theinternal logic for up to five iP1001 power blocks.iP1001 Reference Design 14 15iP1001Fig 10a. - Reference Design Schematic For <4.5V INFig 10b. - Reference Design Schematic For 5V IN - 12V IN Nominal16iP1001Table 4 - Reference Design Bill of MaterialsIRDCiP1001-A (For operation <4.5V IN )Designator Value Part TypeFootprint Mfr.Mfr. P/N C1, C3, C5100uFCapacitor, 6.3V, 20%, X5R1812TDK C4532X5R0J107MT C2, C4, C6, C7, C8, C9, C10, C15-Not Installed---C11, C12, C13, C14470uFCapacitor, 6.3V, 20%, Tantalum 7343Sanyo 6TPB470M C16, C190.100uF Capacitor, 50V, 10%, X7R 1206Novacap 1206B104K500N C17, C1810.0uF Capacitor, 16V, 10%, X5R 1210TDK C3225X5R1C106KT C20 1.00uF Capacitor, 10V, 10%, X7R 0805MuRata GRM40X7R105K010C2147.0pF Capacitor, 50V, 5%, C0G 1206MuRata GRM42-6C0G470J050AD140V Schottky Diode, 40V, 2.1AD-64International Rectifier 10MQ040NJP1, JP2, JP3-Test Point -Samtec TSW-102-07-LS JP1-1, JP2-1, JP3-1-Shunt-Samtec SNT-100-BKT L1 1.06uHInductor, 16A, 20%, Ferrite SMT Panasonic ETQP6F1R1BFA L222uH Inductor, 0.68A, 20%, FerriteSMT Sumida CR43-220R10:Resistor, 0:Jumper 2716Isotek Corp SMT-R000R2-For <2Vout, Not installed For >2Vout, Resistor, 0:Jumper SMT --R3-For <2Vout, Resistor, 0: Jumper For >2Vout see formula for valueSMT --R4-For <2Vout, Not installed For >2Vout recommend 1k :see formula for detailSMT --R5-For <2Vout, Resistor, 0: JumperFor >2Vout, Not installed 1206PanasonicERJ-8GEY0R00R60:Resistor, 0:Jumper 1206--R7340k :Resistor, 340k :, 1%340k : sets for 20A limit.See ILIM formula for other values1206ROHMMCR18EZHF3403R8100k :Resistor, 100k :, 5%1206ROHM MCR18EZHJ104R991k :Resistor, 91k :, 5%1206ROHM MCR18EZHJ913SW1-8-position DIP switchSMT C&K Components SD08H0SKTP1, TP3-Not Installed ---TP2, TP4, TP5-Test Point-Keystone1502-2U1-Power BlockSSBGA14mmx14mm International RectifieriP1001U2-IC, Step-Up DC-DC Converter, 0.5A8uMAX MaximMAX1675EUAIRDCiP1001-B (For operation 5V IN to 12V IN )DesignatorValuePart TypeFootprint Mfr.Mfr. P/NC1 C2 C3 C4 C5 C6 C7 C8 C9 C1010.0uF Capacitor, 25V, 10%, X5R 1812MuRata GRM43-2X5R106K25A C11 C12 C13 C14470uF Capacitor, 6.3V, 20%, Tantalum7343Sanyo 6TPB470M C160.100uFCapacitor, 50V, 10%, X7R1206Novacap1206B104K500NC15, C17, C18, C19, C20, C21-Not Installed---D140V Schottky Diode, 40V, 2.1AD-64International Rectifier10MQ040NJP1, JP2, JP3-Not Installed ---JP1-1, JP2-1, JP3-1-Not Installed---L1 1.06uH Inductor, 16A, 20%, FerriteSMT PanasonicETQP6F1R1BFAL2-Not Installed ---R10:Resistor, 0:Jumper 2716Isotek CorpSMT-R000R2-For <2Vout, Not installed For >2Vout, Resistor, 0:Jumper SMT --R3-For <2Vout, Resistor, 0: Jumper For >2Vout see formula for valueSMT --R4-For <2Vout, Not installed For >2Vout recommend 1k :see formula for detailSMT --R5-For <2Vout, Resistor, 0: JumperFor >2Vout, Not installed 1206PanasonicERJ-8GEY0R00R60:Resistor, 0:Jumper 1206--R7340k :Resistor, 340k :, 1%340k : sets for 20A limit.See ILIM formula for other values1206ROHM MCR18EZHF3403R8, R9-Not Installed ---SW1-8-position DIP switchSMT C&K ComponentsSD08H0SK TP1 TP2 TP4 TP5-Test Point -Keystone1502-2TP3-Not Installed---U1-Power Block SSBGA14mmx14mmInternational RectifieriP1001U2-Not Installed---17iP1001iPOWIR Technology products:AN-1028: Recommended Design, Integration and Rework Guidelines for International Rectifier’s iPOWIR Technology BGA PackagesThis paper discusses the assembly considerations that need to be taken when mounting iPOWIR BGA’s on printed circuit boards. This includes soldering, pick and place, reflow, inspection, cleaning and reworking recommendations.AN-1029: Optimizing a PCB Layout for an iPOWIR Technology DesignThis paper describes how to optimize the PCB layout design for both thermal and electrical performance.This includes placement, routing, and via interconnect suggestions.AN-1030: Applying iPOWIR Products in Your Thermal EnvironmentThis paper explains how to use the Power Loss and SOA curves in the data sheet to validate if theoperating conditions and thermal environment are within the Safe Operating Area of the iPOWIR product.。
BH产品规格书模板
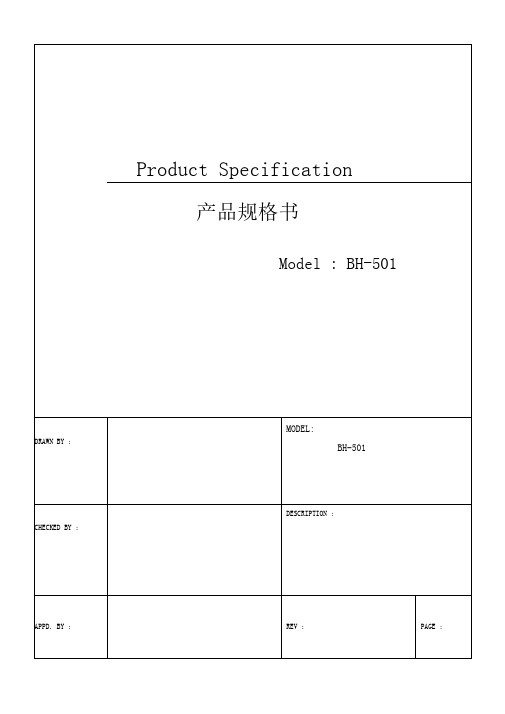
音量增加
短按音量加键
/
/
在通话或音乐播放状态,按加键将 增加耳机音量,按着加键不放,可 快速增加音量。
Con diti on
指示灯
1
开机
蓝灯长亮1秒
2
配对
监灯、红灯交替闪烁
3
等连接
蓝灯每秒闪一下
4
待机
蓝灯2秒闪1下
8
低电
红灯有节奏快闪
9
充电中
红灯长亮
10
充电完成
红灯熄火
10)常规功能
功能
操作
LED状
态
提示音
功能详细描述
开机
关机状态,按住多功
能键3S
蓝灯每秒闪
一下
有提示音
.
关机
开机状态,按住多功
能键5S
NOMINAL
LIMIT
UNIT
a)
LOW BATTERY WARNING VOLTAGE
报警电压
3.5
3.45---3.55
V
b)
AUTO POWER OFF VOLTAGE
关机电压
3.3
2.25---3.35
V
6)CHARGE CURRENT (AT STANDARD INPUT VOLTAGE)充电电流测试
DESCRIPTION
NOMINAL
LIMIT
UNIT
a) ST-BY TIME待机时间
300
-
b)TALK TIME通话时间
8
-
H
c)MAX CHARGE TIME最大充电时间
XMTA9018T温控仪说明书

XMTA9018T温控仪说明书一、概述:温度仪表厂专业生产智能温控仪表,该仪表由单片机控制,具有热电阻、热电偶、电压、电流等多种信号自由输入,十种报警方式,手动自动切换,主控方式除常规两位式外,在传统PID控制算法基础上,结合模糊控制理论创建了新的人工智能调节 PID控制算法,在各种不同的系统上,经仪表自整定的参数大多数能得到满意的控制效果,具有无超调,抗扰动性强等特点。
此外仪表还具有良好的人机界面,仪表能根据设置自动屏蔽不相应的参数项,使用户更觉简洁易接受。
二、主要技术指标:1、本误差:≤士0.5%F.S士1个字,士0.3%F.S士1个字。
2、补偿误差:≤士2.0℃。
3、采样周期:0.5秒。
4、控制周期:继电器输出与阀位控制时的控制周期为2~120秒可调,其它为2秒。
5、报警输出回差(不灵敏区):0.5或5。
6、继电器触点输出:AC250V/5A(阻性负载)或AC250V/0.3A(感性负载)。
7、驱动可控硅脉冲输出:幅度≥3V,宽度=50uS的过零或移相触发脉冲(共阴)。
8、驱动固态继电器信号输出:驱动电流≥15mA,电压≥9V。
9、连续PID调节模拟量输出:0~10mA(负载500±2002),4-20mA (负载250±1002),或0-5V(负载≥100kΩ),1~5V(负载≥100k2)。
10、电源:AC85V~242V(开关电源),50/60Hz,或其它特殊定货。
11、工作环境:温度0~50.0℃,相对湿度不大于85%的无腐蚀性气体及无强电磁T扰的场所。
三、参数及状念改直方法:1、第一设置区上电后,按SET键约3秒,仪表进入第一设置区,仪表将按参数代码1~23依次在上显示窗显示参数符号,下显示窗显示其参数值,此时分别按4、V、A三键可调整参数值,长按V或A可快速加或减,调好后按SET键确认保存数据,转到下一参数继续调完为止,长按SET将快捷退出,也可按SET+4直接退出。
PA83M,PA83M883, 规格书,Datasheet 资料
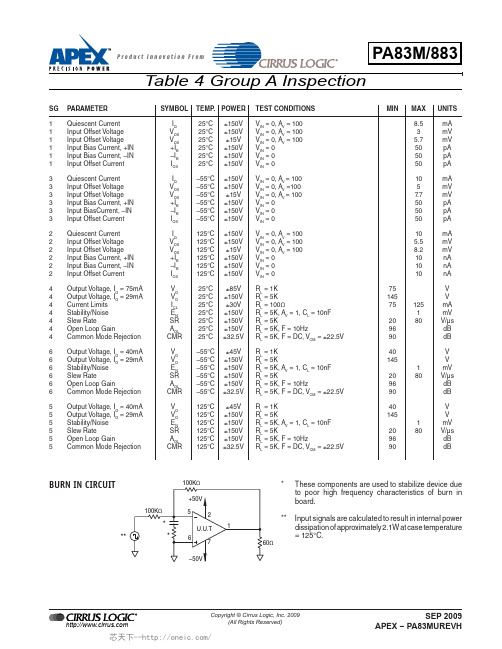
SG PARAMETER SYMBOL TEMP. POWER TEST CONDITIONS MIN MAX UNITS 1 Quiescent Current I Q 25°C ±150V V IN = 0, A V = 1008.5 mA 1 Input Offset Voltage V OS 25°C ±150V V IN = 0, A V = 100 3 mV 1 Input Offset Voltage V OS 25°C ±15V V IN = 0, A V = 100 5.7 mV 1 Input Bias Current, +IN +I B 25°C ±150V V IN = 0 50 pA 1 Input Bias Current, –IN –I B 25°C ±150V V IN = 0 50 pA 1 Input Offset Current I OS 25°C ±150V V IN = 050 pA 3 Quiescent Current I Q –55°C ±150V V IN = 0, A V = 100 10 mA 3 Input Offset Voltage V OS –55°C ±150V V IN = 0, A V =100 5 mV 3 Input Offset Voltage V OS –55°C ±15V V IN = 0, A V = 100 7.7 mV 3 Input Bias Current, +IN +I B –55°C ±150V V IN = 0 50 pA 3 Input BiasCurrent, –IN –I B –55°C ±150V V IN = 0 50 pA 3 Input Offset Current I OS –55°C ±150V V IN = 050 pA 2 Quiescent Current I Q 125°C ±150V V IN = 0, A V = 100 10 mA 2 Input Offset Voltage V OS 125°C ±150V V IN = 0, A V = 100 5.5 mV 2 Input Offset Voltage V OS 125°C ±15V V IN = 0, A V = 100 8.2 mV 2 Input Bias Current, +IN +I B 125°C ±150V V IN = 0 10 nA 2 Input Bias Current, –IN –I B 125°C ±150V V IN = 0 10 nA 2 Input Offset Current I OS 125°C ±150V V IN = 010 nA 4 Output Voltage, I O = 75mA V O 25°C ±85V R L = 1K 75 V 4 Output Voltage, I O = 29mA V O 25°C ±150V R L = 5K 145 V 4 Current Limits I CL 25°C ±30V R L = 100Ω75 125 mA 4 Stability/Noise E N 25°C ±150V R L = 5K, A V = 1, C L = 10nF 1 mV 4 Slew RateSR 25°C ±150V R L = 5K20 80 V/µs 4 Open Loop GainA OL 25°C ±150V R L = 5K, F = 10Hz96 dB 4 Common Mode Rejection CMR 25°C±32.5VR L = 5K, F = DC, V CM = ±22.5V 90 dB 6 Output Voltage, I O = 40mA V O –55°C ±45V R L = 1K 40 V 6 Output Voltage, I O = 29mA V O –55°C ±150V R L = 5K145 V 6 Stability/Noise E N –55°C ±150V R L = 5K, A V = 1, C L = 10nF 1 mV 6 Slew RateSR –55°C ±150V R L = 5K20 80 V/µs 6 Open Loop GainA OL –55°C ±150V R L = 5K, F = 10Hz96 dB 6 Common Mode Rejection CMR –55°C ±32.5V R L = 5K, F = DC, V CM = ±22.5V 90 dB 5 Output Voltage, I O = 40mA V O 125°C ±45V R L = 1K 40 V 5 Output Voltage, I O = 29mA V O 125°C ±150V R L = 5K145 V 5 Stability/Noise E N 125°C ±150V R L = 5K, A V = 1, C L = 10nF 1 mV 5 Slew RateSR 125°C ±150V R L = 5K20 80 V/µs 5 Open Loop GainA OL 125°C ±150V R L = 5K, F = 10Hz96 dB 5Common Mode RejectionCMR125°C ±32.5VR L = 5K, F = DC, V CM = ±22.5V90dBBURN IN CIRCUIT***These components are used to stabilize device due to poor high frequency characteristics of burn in board.** Input signals are calculated to result in internal powerdissipation of approximately 2.1W at case temperature = 125°C.2 PA83MUCONTACTING CIRRUS LOGIC SUPPORTFor all Apex Precision Power product questions and inquiries, call toll free 800-546-2739 in North America. For inquiries via email, please contact apex.support@.International customers can also request support by contacting their local Cirrus Logic Sales Representative.To find the one nearest to you, go to IMPORTANT NOTICECirrus Logic, Inc. and its subsidiaries ("Cirrus") believe that the information contained in this document is accurate and reliable. However, the information is subject to change without notice and is provided "AS IS" without warranty of any kind (express or implied). Customers are advised to obtain the latest version of relevant information to verify, before placing orders, that information being relied on is current and complete. All products are sold subject to the terms and conditions of sale supplied at the time of order acknowledgment, including those pertaining to warranty, indemnification, and limitation of liability. No responsibility is assumed by Cirrus for the use of this information, including use of this information as the basis for manufacture or sale of any items, or for infringement of patents or other rights of third parties. This document is the property of Cirrus and by furnishing this information, Cirrus grants no license, express or implied under any patents, mask work rights, copyrights, trademarks, trade secrets or other intellectual property rights. Cirrus owns the copyrights associated with the information contained herein and gives con-sent for copies to be made of the information only for use within your organization with respect to Cirrus integrated circuits or other products of Cirrus. This consent does not extend to other copying such as copying for general distribution, advertising or promotional purposes, or for creating any work for resale.CERTAIN APPLICATIONS USING SEMICONDUCTOR PRODUCTS MAY INVOLVE POTENTIAL RISKS OF DEATH, PERSONAL INJURY, OR SEVERE PROP-ERTY OR ENVIRONMENTAL DAMAGE (“CRITICAL APPLICATIONS”). CIRRUS PRODUCTS ARE NOT DESIGNED, AUTHORIZED OR WARRANTED TO BE SUITABLE FOR USE IN PRODUCTS SURGICALLY IMPLANTED INTO THE BODY, AUTOMOTIVE SAFETY OR SECURITY DEVICES, LIFE SUPPORT PROD-UCTS OR OTHER CRITICAL APPLICATIONS. INCLUSION OF CIRRUS PRODUCTS IN SUCH APPLICATIONS IS UNDERSTOOD TO BE FULLY AT THE CUS-TOMER’S RISK AND CIRRUS DISCLAIMS AND MAKES NO WARRANTY, EXPRESS, STATUTORY OR IMPLIED, INCLUDING THE IMPLIED WARRANTIES OF MERCHANTABILITY AND FITNESS FOR PARTICULAR PURPOSE, WITH REGARD TO ANY CIRRUS PRODUCT THAT IS USED IN SUCH A MANNER. IF THE CUSTOMER OR CUSTOMER’S CUSTOMER USES OR PERMITS THE USE OF CIRRUS PRODUCTS IN CRITICAL APPLICATIONS, CUSTOMER AGREES, BY SUCH USE, TO FULLY INDEMNIFY CIRRUS, ITS OFFICERS, DIRECTORS, EMPLOYEES, DISTRIBUTORS AND OTHER AGENTS FROM ANY AND ALL LIABILITY, INCLUDING ATTORNEYS’ FEES AND COSTS, THAT MAY RESULT FROM OR ARISE IN CONNECTION WITH THESE USES.Cirrus Logic, Cirrus, and the Cirrus Logic logo designs, Apex Precision Power, Apex and the Apex Precision Power logo designs are trademarks of Cirrus Logic, Inc. All other brand and product names in this document may be trademarks or service marks of their respective owners.。
BH使用说明书

欢迎您选用捷益达公司不间断电源产品,并在此向您致谢!在安装使用银雁BH-F系列UPS前,请您仔细阅读本使用手册。
并请妥善保存本使用手册以备参考。
为了确保产品具有高可靠的品质,捷益达公司均严格测试每一台银雁UPS,所有机器部件都符合捷益达品质控制标准。
为了保障您的合法利益,请您务必在购机之日起一个月内将保修卡回执寄回深圳市捷益达电子有限公司客户服务中心,我们将为您建立用户档案,并使您能及时享受到捷益达公司源源不断的服务和支持。
适用型号:BH10S-F、BH20S-F、BH30S-F、BH60S-F、BH100S-F单相输入/单相输出BH10L-F、BH20L-F、BH30L-F、BH60L-F、BH100L-F单相输入/单相输出BH100L31-F三相输入/单相输出BH10L-F/RM、BH20L-F/RM、BH30L-F/RM、BH60L-F/RM、1.概述 (1)1.1产品简介1.2工作原理1.3整机描述2.安装与操作 (14)2.1开箱和检查2.2 安装环境2.3连接市电2.4外接电池的连接2.5开机测试2.6电池充电2.7连接负载2.8关机2.9冗余并机(选件)3.安全说明 (23)4.使用注意事项和日常维护 (24)4.1日常使用4.2使用注意事项4.3日常的维护5.网络化管理 (26)6.常见状态、故障及处理 (28)6.1常见状态6.2常见故障及处理7.技术指标 (30)8.售后服务 (37)注意:为了保障您的正常权益,请您在您的UPS正常使用后,将保修卡寄回捷益达公司!。
(仅供参考)钢芯铝绞线技术规格书

大张线微联改造工程技术规格书电力电缆及铝绞线大秦铁路股份有限公司大同电务段二〇一六年十一月1技术规格共同条款1.1工程概况大张线阳高等四站计算机联锁改造工程共分四座车站,分别为阳高站、罗文皂站、永嘉堡站及西湾堡站。
电力主材、设备(甲控)涉及箱式变电站、高压电力电缆、钢芯铝绞线等。
1.2设备、器材的一般规定1.2.1使用环境条件(1)环境温度:极端最高温度40℃,极端最低温度-40℃(2)空气相对湿度:日平均值不大于95% ,月平均值不大于90%。
(3)最大风速:30m/s(4)覆冰厚度:15mm1.2.2试验电压值各种电器设备、器材的实验电压值应按GB311.1进行修正。
1.2.3控制电压各种电气设备、器材的回路电压,采用如下标准值:(1)控制回路:DC220V(DC110V)或AC220V(2)保护回路:DC220V(DC110V)或AC220V(3)信号及显示回路:DC220V(DC110V)或AC220V在上述标准值的80%~120%范围内,各种电气设备、器材应能保证可靠动作。
1.2.4涂色所有电气设备、器材喷涂的颜色应按标准颜色及喷涂工艺进行,并取得招标人的同意。
1.2.5标志各设备、器材均应有铭牌,铭牌的内容按中华人民共和国有关标准确定。
2YJV22-8.7/15kV系列交联聚乙烯铠装铜芯高压电缆2.1总则(1)本技术规格书仅适用于本次所采购的交流额定电压10kV以下绝缘电力电缆的订货。
(2)本技术规格书的内容包括遵循的标准和电缆使用条件、构造及及其技术要求、试验项目和方法、验收规则、标志、包装。
(3)本技术规格书中凡标明参数数值的,是作为特别强调,其他未标明的均应执行相关GB、IEC和DL标准。
(4)本技术规格书是本次电缆采购最低要求,投标人所提供的电缆各项技术指标均不得低于本技术规格书要求。
2.2引用标准电缆应满足或高于下面列出的规范和标准的最新版本的要求。
如果几种规范和标准适用于同一情况,则应遵循最为严格的规范。