580万年原油常减压蒸馏装置工艺设计
化工课程设计(原油常减压蒸馏装置常压塔工艺设计)

广东石油化工学院课程设计520万吨/年原油常减压蒸馏装置常压塔工艺设计学院:专业:班级:学生:学号:指导教师:完成时间:年月日至年月日广东石油化工学院化学工程与工艺专业设计任务书1.设计题目: 520 万吨/年原油常减压蒸馏装置常压塔工艺设计2. 学生完成全部设计之期限: 2014 年 11 月 12 日3. 设计之原始数据: (另给)4. 计算及说明部分内容: (设计应包括的项目)一、总论1.概述;2.文献综述;3.设计任务依据;4.主要原材料;5.其他二、工艺流程设计1. 原料油性质及产品性质;2. 工艺流程;3. 塔器结构;4.环保措施三、常压蒸馏塔工艺计算1. 工艺参数计算;2. 操作条件的确定;3. 蒸馏塔各点温度核算;4. 蒸馏塔汽液负荷计算四、常压蒸馏塔尺寸计算1. 塔径计算;2. 塔高计算五、常压蒸馏塔水力学计算六、车间布置设计1. 车间平面布置方案;2. 车间平面布置图;3. 常压蒸馏塔装配图七、参考资料5. 绘图部分内容: (明确说明必绘之图)(1) 原油常减压蒸馏装置工艺流程图(2) 主要塔器图(3) 常压蒸馏塔汽液负荷分布图(4) 常压蒸馏塔装配图6. 发出日期: 2011 年 11 月 7 日设计指导教师:完成任务日期: 年月 10 日学生签名:化学工程与工艺课程设计520万吨/年原油常减压蒸馏装置常压塔工艺设计基础数据一. 原油的一般性质阿曼原油,20d= 0.8552;特性因数 K=12.2 含硫石蜡-中间基原油4二. 原油实沸点蒸馏数据三. 产品方案及产品性质四. 设计处理量: 250+学号×10万吨/年, 开工:8000小时/年。
五. 汽提水蒸汽采用过热水蒸汽: 420℃, 0.4MPa(表)六. 可采用二段汽化流程,设3个中段循环回流; 过汽化油为2~4%(重)。
七.原油平衡蒸发数据(由产品体积收率数据代替原油实沸蒸馏数据换算).目录第一章总论 (1)1.1 概述 (1)1.1.1 设计基础 (1)1.1.2 设计方案 (2)1.1.3 生产规模 (2)1.1.4 工艺技术路线 (2)1.1.5 工艺技术特点 (3)1.2 文献综述:常减压蒸馏技术现状 (3)1.2.1 国外蒸馏装置技术现状及发展趋势 (3)1.2.2 国内蒸馏装置技术现状 (4)1.3 课程设计任书 (5)1.4 主要原材料 (5)1.5 其他 (6)1.5.1 “三废”综合利用 (6)1.5.2 交通运输及综合利用 (6)1.5.3 节能措施 (6)第二章工艺流程设计 (7)2.1 原料油性质及产品性质 (7)2.1.1 原油的一般性质 (7)2.1.2 原料油处理量 (7)2.1.3 原油实沸点蒸馏数据 (7)2.1.4 原油平衡蒸发数据 (8)2.1.5 产品性质 (8)2.2 工艺流程 (8)2.2.1 工艺流程 (8)2.3 塔器结构 (10)2.4 环保措施 (11)2.4.1 污染源分析 (11)2.4.2 废气处理 (12)2.4.3 废水处理 (12)2.4.4 噪声防护 (13)第三章常压蒸馏塔工艺设计 (14)3.1 工艺参数计算 (14)3.1.1 体积平均沸点体t (14)3.1.2 恩氏蒸馏90%~10%斜率 (15)3.1.3 立方平均沸点 (15)3.1.4 中平均沸点 (15)3.1.5 特性因数K (16)3.1.6 相对分子质量: (16)3.1.7 平衡蒸发温度 (16)3.1.8 临界温度和临界压力 (17)3.1.9 焦点温度和焦点压力 (17)3.2 原油和产品的有关性质参数计算汇总 (17)3.3 操作条件的确定 (18)3.3.1 汽提蒸汽用量 (18)3.3.2 塔板型式和塔板数 (19)3.3.3 操作压力 (21)3.3.4 汽化段温度 (21)3.3.5 塔底温度 (24)3.3.6 塔顶及各侧线温度的假设与回流热分配 (24)3.4 蒸馏塔各点温度核算 (25)3.4.1 重柴油抽出板(第34块)温度校核 (25)3.4.2 轻柴油抽出板和航空煤油抽出板温度 (27)3.4.3 塔顶温度的校正 (27)3.5 全塔汽、液负荷分布图 (28)第四章 常压蒸馏塔尺寸计算 (30)4.1 塔的直径的计算 (30)4.1.1 塔径的初算 (30)4.1.2 计算适宜的气速Wa (31)4.1.3 计算气相空间截面积 (31)4.1.4 降液管内流体流速, Vd (31)4.1.5 计算降液管面积 (31)4.1.6 塔横截面积Ft 的计算 (32)4.1.7 采用的塔径D 及空塔气速W (32)4.2 塔高的计算 (32)4.3 塔板布置, 浮阀、溢流堰及降液管的计算 (33)4.3.1 浮阀型式 (33)4.3.2 临界阀孔流速 (33)4.3.3 开孔率 (33)4.4 浮阀数 (33)4.5 溢流堰及降液管的决定 (34)4.5.1 降液管 (34)4.5.2 溢流堰 (34)4.5.3 进口受液盘 (34)4.5.4 进口堰 (34)4.5.5 降液管停留时间 (34)4.5.6 降液管内流体流速, Vd (35)4.5.7 降液管底缘距塔板的高度 (35)第五章常压蒸馏塔水力计算 (35)5.1 塔板总压力降 (35)5.1.1 干板压力降△Pd (35)5.1.2 表面张力的压力降△Po (36)5.1.3 气体通过塔板上液层的压力降△PL (36)5.1.4 气体通过一块塔板的总压力降△Pt (36)5.2 雾沫夹带 (36)5.3 泄漏 (37)5.4 淹塔 (37)5.5 降液管超负荷 (38)5.6 适宜操作区和操作线 (38)5.6.1 雾沫夹带量线 (38)5.6.2 淹塔界线 (39)5.6.3 降液管超负荷界线 (40)5.6.4 泄漏线 (40)5.6.5 液相负荷下限线 (40)5.6.6 操作线 (41)5.6.7 适宜操作区和操作线 (41)第六章车间布置图 (42)6.1 车间平面布置方案 (42)6.2 车间平面布置图 (42)6.2.1 工艺条件 (42)6.2.2 安全性 (43)6.2.3 经济性 (43)6.3 常压蒸汽塔装配图 (43)第七章参考文献 (44)第一章总论1.1 概述1.1.1 设计基础原油在常压条件下呈液态的复杂的烃类混合物。
常减压蒸馏装置工艺流程

常减压蒸馏装置工艺流程嘿,咱来说说常减压蒸馏装置工艺流程哈。
我跟你讲,有一回我去一个化工厂参观,就看到了那个庞大的常减压蒸馏装置。
那天我一进工厂,就被那个高高的装置给吸引住了。
哇,那家伙,就像一个巨大的钢铁怪物。
我好奇地跟着导游往前走,听他介绍这个神奇的装置。
导游说,首先呢,原油从外面运进来,就像一群调皮的小孩子,急着要去玩耍。
这些原油被送到一个大罐子里,这个罐子就像一个大游泳池,让原油在里面安静一会儿。
然后呢,原油就被泵送到加热炉里。
加热炉就像一个大火炉,把原油加热得滚烫滚烫的。
我看着那红红的火焰,心里想,这原油得被烤成啥样啊。
不过导游说,这是为了让原油里面的不同成分分开。
加热后的原油就进入了蒸馏塔。
这个蒸馏塔可高了,就像一个巨大的烟囱。
原油在里面慢慢地上升,就像坐电梯一样。
随着温度的降低,不同的成分就会在不同的高度凝结下来。
就像一群小伙伴,各自找到了自己的位置。
比如说,最轻的汽油最先凝结,然后是煤油、柴油啥的。
这些不同的成分就被分别收集起来,送到不同的地方去加工。
我看着那些管道里流出来的各种液体,觉得好神奇啊。
有一次,导游让我们靠近一点看蒸馏塔的顶部。
哇,那里冒出一股白色的蒸汽,就像一朵白云。
导游说,这是一些最轻的气体,它们会被收集起来,或者烧掉,不能让它们随便跑出去污染空气。
从那以后,我就对常减压蒸馏装置的工艺流程有了深刻的印象。
这玩意儿虽然看起来很复杂,但是真的很厉害。
它能把原油变成各种各样有用的东西,就像一个魔法工厂。
嘿嘿。
原油预处理和原油蒸馏—原油常减压蒸馏工艺流程

减一 减二 减三
减底渣油
原油常减压蒸馏
三段蒸馏 原油加工流程方案中有三个蒸馏塔, 常减压蒸馏塔前面再设一个初馏塔(闪蒸塔、闪蒸罐)
初 馏 塔 电脱盐罐
原油
常 压 塔
常压炉
粗汽油
航空煤油
减
轻柴油
压
塔
重柴油
减压炉
减一 减二 减三
减底渣油
三段汽化 常减压流程
原油常减压蒸馏
230~240℃
轻汽油
汽油
煤油 轻柴油 重柴油
➢ 减压塔
原油常减压蒸馏
原油预处理过程中只用一个精馏塔;
初 馏 塔
电脱盐罐
原油
常压炉
重整原料
航空煤油
常
压 塔
轻柴油 减 压
塔
重柴油
常底油
减压炉
润滑油 石蜡 沥青
原油常减压蒸馏
原油的常减压蒸馏,有两个精馏塔,经过了两次汽化;
初 馏 塔 电脱盐罐
原油
常 压 塔
常压炉
粗汽油
航空煤油
减
轻柴油
压
塔
重柴油
减压炉
拔头油
常渣
360~370℃
里面有宝贵的润滑油 馏分和二次加工原料
>350℃
低温下得到高沸点馏份 (<600 ℃)
原油常减压蒸馏
轻汽油
拔头油
常渣
汽油
煤油 405~410℃
轻柴油 重柴油
减压塔顶抽真空系统:
冷凝器
抽真空
回流罐
冷却器
产品罐
➢ 润滑油 ➢ 催化裂化原料
去焦化、丙烷脱沥青等
课程:石油炼制的运行与操控
知识点:原油常减压工艺流程
原油常减压蒸馏ppt课件
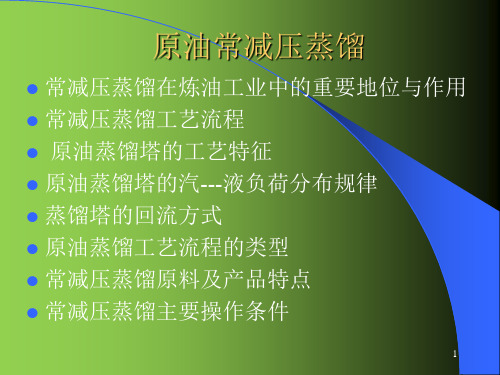
9
常减压蒸馏主要操作条件
常压塔 温度:原油经换热后达到300℃左右,进入常压 加热炉,原油被加热到360~380℃进入常压塔 进行蒸馏。塔顶100~130 ℃,常一线(煤油) 200 ℃左右,常二线(柴油)280 ℃左右,常 三线(重柴油)340 ℃左右。 压力:塔顶在0.1~0.16Mpa下操作。
范围分离成不同的馏分。 炼油其他装置的原料均由蒸馏提供原料。
2
常减压蒸馏工艺流程
3
原油蒸馏塔的工艺特征
1、复合塔 2、汽提塔和汽提段 3、全塔热平衡 4、恒分子回流的假定完全不适用
4
原油蒸馏塔的汽---液负荷分布规律
5
蒸馏塔的回流方式
1、塔顶回流 冷回流 热回流 循环回流 2、中段循环回流
10
减压塔 温度:常压塔底油 350℃左右进入减压加热炉,
被加热到380~400℃进入减压塔进行蒸馏。 压力:减压塔顶残压一般在20~60mmHg。
11
减压塔的工艺特点
塔顶和塔底缩径 一般使用填料 燃料型减压塔有2—3个侧线 润滑油型减压塔有4—5个侧线
12
“干式”减压特点
塔顶残压在10—20mmHg 一般在塔底不注水蒸汽 塔用填料 炉管扩径 大直径低速转油线 燃料型减压塔使用该技术
6
原油蒸馏工艺流程的类型
我国原油蒸馏工艺流程按炼油 厂类型不同,可大致分为燃料 型、燃料---润滑油型二大类。 (一)燃料型 (二)燃料—润滑油型
7
常减压蒸馏原料及产品特点
原油在进入常减压蒸馏装置前,首先进行脱盐脱水。 在常压塔得到:
常压塔顶:石脑油(汽油馏分):
原油常减压蒸馏

原油常减压蒸馏
编辑ppt
6
原油蒸馏工艺流程的类型
我国原油蒸馏工艺流程按炼油 厂类型不同,可大致分为燃料 型、燃料---润滑油型二大类。 (一)燃料型 (二)燃料—润滑油型
编辑ppt
7
常减压蒸馏原料及产品特点
原油在进入常减压蒸馏装置前,首先进行脱盐脱水。 在常压塔得到:
常压塔顶:石脑油(汽油馏分):
因为辛烷值低可以作为溶剂油;催化重整原料;
压力:塔顶在0.1~0.16Mpa下操作。
编辑热炉,
被加热到380~400℃进入减压塔进行蒸馏。 压力:减压塔顶残压一般在20~60mmHg。
编辑ppt
11
减压塔的工艺特点
塔顶和塔底缩径 一般使用填料 燃料型减压塔有2—3个侧线 润滑油型减压塔有4—5个侧线
编辑ppt
12
“干式”减压特点
塔顶残压在10—20mmHg 一般在塔底不注水蒸汽 塔用填料 炉管扩径 大直径低速转油线 燃料型减压塔使用该技术
编辑ppt
13
常一线:航空煤油(煤油):
根据原油性质不同,生产不同的煤油。
常二线:柴油 一般生产0#柴油 常三线:重柴油:20#重柴油
编辑ppt
8
在减压塔得到:
馏分范围为(350~500℃)的蜡油
1、在不同的侧线得到各个馏分,作为生产润 滑油原料。或将各个馏分混合,特点:凝 固点高,分子量大,作为:催化裂化原料, 加氢裂化原料。
常减压蒸馏装置工艺流程图

减压渣油出装置 减压渣油出装置
3
中国石油华东设计院
4.1常减压蒸馏装置—工艺流程
4
中国石油华东设计院
4.1常减压蒸馏装置—工艺流程
5
中国石油华东设计院
注水 注氨 注缓蚀剂
常压塔
常一中油泵
常二中油泵 初底油自常压炉来
汽提蒸汽
常压塔顶回流罐
常压塔顶产品罐
常压汽提塔
含硫污水 ห้องสมุดไป่ตู้压塔顶回流泵
含硫污水
常顶产品油泵
常一线油泵 气提蒸汽
常二线油泵 汽提蒸汽
常三线油泵 常四线油泵
常底油泵
2
常顶不凝气
常顶油至轻烃回收部分 常顶一级油出装置 常一线油出装置 常二线油出装置
常三线油出装置 常四线油去减压塔 常底油至减压炉
中国石油华东设计院
4.1常减压蒸馏装置—工艺流程
蒸汽 减顶气 减顶油出装置
常压渣油自常压部分来
减顶真空泵
减顶油泵 含油污水
减顶油罐 减顶水泵
汽提蒸汽
减一线及一中泵 减二线及二中泵
减三线及三中泵 洗涤油泵
燃料油 燃料气 减压炉
减压塔
减压渣油泵
减一线油出装置
4.1常减压蒸馏装置—工艺流程图
脱盐排水
电脱盐罐
电脱盐罐
净化水
注水 注氨 注缓蚀剂
含硫污水 初顶油泵
初侧油泵
原油自罐区来
原油泵
初馏塔
初底油泵
1
常压炉
初顶不凝气 初顶油至轻烃回收部分 初侧油至常压塔
初底油至常压塔 燃料油 燃料气
中国石油华东设计院
常减压蒸馏装置—工艺流程图.ppt

常压塔
注水 注氨 注缓蚀剂
常压塔顶回流罐
常压塔顶产品罐
常顶不凝气
常顶循油泵 含硫污水 初侧油自初馏塔来 常压汽提塔 含硫污水 常顶油至轻烃回收部分 常压塔顶回流泵 常顶产品油泵
常顶一级油出装置
常一线油出装置 常一中油泵
常一线油泵
常二中油泵
气提蒸汽
常二线油出装置
初底油自常压炉来 常二线油泵
汽提蒸汽
汽提蒸汽 常三线油出装置
常三线油泵 常四线油去减压塔 常四线油泵 常底油至减压炉
常底油泵
1
中国石油华东设计院
4.1常减压蒸馏装置—工艺流程
2
中国石油华东设计院
4.1常减压蒸馏装置—工艺流程
初顶不凝气
初顶油至轻烃回收部分
初侧油至常压塔
3
中国石油华东设计院
4.1常减压蒸馏装置—工艺流程
4
中国石油华东设计院
4.1常减压蒸馏装置—工艺流程
初顶不凝气 注水 注氨 注缓蚀剂
含硫污水
初顶油至轻烃回收部分
初顶油泵
脱盐排水
电脱盐罐
电脱盐罐 初侧油至常压塔
初侧油泵
净化水
初底油至常压塔
燃料油 燃料气
原油自罐区来
原油泵
初馏塔
初底油泵
常压炉
5
中国石油华东设计院
400万吨年常减压蒸馏装置工艺设计

400万吨年常减压蒸馏装置工艺设计常减压蒸馏装置是一种常用的化工设备,用于对原料进行分离和提纯。
本文将介绍一种设计容量为400万吨年的常减压蒸馏装置的工艺设计。
首先,我们需要确定装置的原料和产品。
假设我们的装置用于石油精炼,原料是原油,产品是石油衍生品,如汽油、柴油和液化石油气等。
接下来,我们需要进行原料的预处理。
原油中含有杂质和不同碳链长度的烃类化合物,需要通过脱盐、脱水和脱硫等工艺步骤进行预处理。
这些步骤将有助于提高蒸馏塔的效率和避免设备的腐蚀。
然后,我们需要设计蒸馏塔的结构。
常减压蒸馏装置通常由多个塔组成,包括原料预热塔、主分馏塔和精馏塔等。
每个塔都有不同的功能和操作条件。
例如,原料预热塔用于将原料加热到合适的温度,以便进入主分馏塔进行分离。
在主分馏塔中,原料将经历不同温度的塔板,每个塔板上都有一定的压力和温度。
通过调节供料量、回流比和冷凝器温度等操作参数,可以实现不同组分的分离。
高沸点组分将在底部的液相中收集,而低沸点组分将在顶部的气相中收集。
精馏塔用于进一步提纯分离出的不同组分。
它通常会有更多的塔板和较低的操作压力和温度。
最后,产品将通过冷凝器冷却,并收集在不同的收集装置中。
收集的产品可以进一步处理或直接用作市售产品。
在整个装置的设计过程中,需要进行多次的热力学计算和模拟。
这些计算将帮助我们确定塔板数目、操作参数、回流比和冷凝温度等设计参数。
总之,400万吨年的常减压蒸馏装置的工艺设计需要根据原料和产品的特性进行合理的塔结构和操作参数的选择。
通过热力学计算和模拟,可以优化装置的设计,实现高效的分离和提纯过程。
继续写相关内容,1500字为了确保400万吨年常减压蒸馏装置的高效运行和优化设计,还需要考虑以下几个方面:首先是热能供应和回收利用。
蒸馏过程需要大量的热能来提供蒸汽和加热原料。
为了降低能耗和运行成本,装置需要考虑热能的供应和回收利用。
一种常见的做法是利用余热回收系统和换热器来回收废热,并将其用于加热原料或生成蒸汽。
原油常减压蒸馏工艺流程毕业设计

The wild and wacky world of continuous vacuum distillation of crude oil is like a magical potion-making process happening right before our eyes! Picture this: a distillation column is like a giant wizard's cauldron, where the crude oil gets heated and starts to bubble and sizzle, releasing its magical vapors. But here's the twist - instead of using a regular old stove, we bring in the vacuum to work its mysterious powers and lower the boiling points of the oil's differentponents. This allows us to separate out the various magical ingredients without them getting too hot and turning into a gooey mess. And to make sure we get the perfect potion, the distillation column is stacked with all sorts of special trays and packing materials to work their enchanting spells and enhance the separation process. It's like a wild and wonderful chemistry experiment, right in the heart of the industrial world!连续真空蒸馏原油的野生和疯狂的世界,就像一个神奇的制药过程在我们眼前发生!想象一下:蒸馏柱就像一个巨大的法师的炉子,原油在那里被加热,并开始发泡和喷发,释放出它的神奇蒸汽。
原油的常减压蒸馏工艺

原油的常减压蒸馏工艺1. 你知道原油的常减压蒸馏工艺是多么神奇的过程吗?就好像一场华丽的魔法表演!比如在工厂里,原油就像一个等待被雕琢的宝贝,进入常减压蒸馏装置,然后奇妙的变化就开始啦!2. 嘿,想不想了解一下原油的常减压蒸馏工艺呀?这可绝对不是一般的操作哦!就如同厨师精心烹饪一道大餐,每一步都至关重要,原油在这里被精心处理着,太厉害啦!3. 原油的常减压蒸馏工艺,那可是相当重要的环节啊!你能想象没有它我们的生活会变成什么样吗?就好比没有了阳光,世界都会暗淡许多呀!像在那些大型工厂里,这个工艺让原油焕发新生!4. 哇哦,原油的常减压蒸馏工艺真的太有意思啦!这不就是给原油来一次华丽大变身嘛!比如看着原油从一种状态变成各种有用的产品,真的超有成就感的!5. 你难道不好奇原油的常减压蒸馏工艺到底是怎么回事吗?这简直就是工业领域的一颗璀璨明星啊!就好像一个精彩的故事,原油在这里演绎着属于它的传奇!6. 哎呀呀,原油的常减压蒸馏工艺真的不容小觑呀!这可是让原油实现价值的关键一步呢!就如同千里马遇到了伯乐,原油在这里被发掘出无限潜力,厉害吧!7. 嘿,告诉你哦,原油的常减压蒸馏工艺超神奇的!你想想看,原油进去后出来好多不同的东西,这不就跟变魔术一样嘛!比如那些工厂里忙碌的场景,就是这场魔术的舞台!8. 哇,原油的常减压蒸馏工艺真的是太牛啦!这简直就是打开原油宝藏的钥匙啊!就好像探险家找到了宝藏的入口,兴奋又期待,在这个工艺中,原油的秘密被一点点揭开!9. 你可别小看了原油的常减压蒸馏工艺呀!这可是关乎我们生活的重要一环呢!就像盖房子的基石,没有它可不行!看看那些大型设备,都在为这个工艺努力工作着呢!10. 原油的常减压蒸馏工艺,真的是非常非常重要啊!没有它,好多东西都没法生产出来呢!这就像是一个不可或缺的伙伴,默默地为我们的生活贡献着,太厉害啦!我的观点结论:原油的常减压蒸馏工艺是极其重要且充满魅力的,它让原油实现了华丽的转变,为我们的生活带来了各种不可或缺的产品,真的是一项伟大的工艺!。
原油常压蒸馏工艺设计
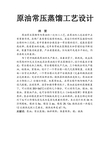
原油常压蒸馏工艺设计摘要原油常压蒸馏作为原油的一次加工工艺,在原油加工总流程中占有重要作用,在炼厂具有举足轻重的地位,其运行的好坏直接影响到后续的加工过程。
其中重要的分离设备—常压塔的设计,是能否获得高收率、高质量油的关键。
近年来常减压蒸馏技术和管理经验不断创新,装置节能消耗显著,产品质量提高。
但与国外先进水平相比,仍存在较大的差距。
为了更好地提高原油的生产能力,本着投资少,能耗低,效益高的思想对印尼贝兰纳克混合原油进行常压蒸馏设计。
设计的基本方案是:常压塔采取三侧线,常压塔塔顶生产汽油,三个侧线分别生产煤油,轻柴油,重柴油。
设计了一个常压塔一段汽化蒸馏装置,此装置由一台管式加热炉,一个常压塔以及若干台换热器(完善的换热流程应达到要求:充分利用各种余热;换热器的换热强度较大;原油流动压力降较小。
)冷凝冷却器、机泵等组成,在常压塔外侧为侧线产品设汽提塔。
流程简单,投资和操作费用较少。
原油在这样的蒸馏装置下,可以得到350-360℃以前的几个馏分,可以用作汽油、煤油、轻柴油、重柴油产品,也可分别作为重整化工(如轻油裂解)等装置的原料。
蒸余的塔底重油可作钢铁或其它工业的燃料。
在某些特定的情况下也可以作催化裂化或加氢裂化装置的原料。
本次设计共用34块浮阀塔板,塔距0.8m,塔径3.6m,塔高28.12m.换热流程一共通过12次换热达到工艺要求,换热效率是67.1%。
关键词:原油;常压蒸馏;物料衡算;热量衡算;塔;换热目录摘要1目录2前言1第一章产品方案及工艺流程5 1.1产品方案5 1.2工艺流程5第二章工艺计算及说明7 2.1设计数据72.1.1 已知数据72.1.2 原油的实沸点及窄馏分数据7 2.2原油实沸点蒸馏曲线的绘制8 2.3常压塔工艺计算92.3.1 各产品的恩氏蒸馏数据和实沸点数据的换算92.3.2 产品的有关数据计算112.3.3 物料衡算132.3.4 确定塔板数和汽提蒸汽用量142.3.5 操作压力162.3.6 汽化段温度172.3.7 塔底温度182.3.8 塔顶及侧线温度的假设与回流热的分配182.3.9 侧线及塔顶温度的校核19 2.4全塔气、液相负荷分布21第三章塔的设计及水力学计算30 3.1塔板的操作条件30 3.2塔板间距初选30 3.3塔径初算30 3.4浮阀数及开孔率的计算32 3.5溢流堰及降液管的决定32 3.6水力学计算33 3.7塔板上的适宜操作区和负荷上下限34第四章塔的内部工艺结构37 4.1板式塔的内部工艺结构37 4.2塔高H39第五章换热流程设计40 5.1换热流程计算405.1.1初馏塔之前的换热流程405.1.2 一、二路原油同时与重油(一次)换热45 5.2热量利用率计算45常压塔计算结果46符号表47前言背景我国炼油工业经过50多年的发展,到21世纪初期,已经形成281Mt/a的原油加工能力,生产的汽油、煤油、柴油、润滑油等石油产品基本满足的国民经济的发展和人民生活的需要。
原油常减压蒸馏的工艺流程
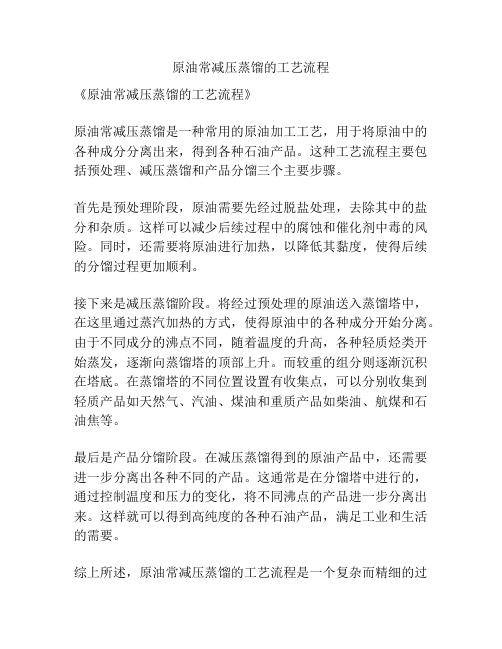
原油常减压蒸馏的工艺流程
《原油常减压蒸馏的工艺流程》
原油常减压蒸馏是一种常用的原油加工工艺,用于将原油中的各种成分分离出来,得到各种石油产品。
这种工艺流程主要包括预处理、减压蒸馏和产品分馏三个主要步骤。
首先是预处理阶段,原油需要先经过脱盐处理,去除其中的盐分和杂质。
这样可以减少后续过程中的腐蚀和催化剂中毒的风险。
同时,还需要将原油进行加热,以降低其黏度,使得后续的分馏过程更加顺利。
接下来是减压蒸馏阶段。
将经过预处理的原油送入蒸馏塔中,在这里通过蒸汽加热的方式,使得原油中的各种成分开始分离。
由于不同成分的沸点不同,随着温度的升高,各种轻质烃类开始蒸发,逐渐向蒸馏塔的顶部上升。
而较重的组分则逐渐沉积在塔底。
在蒸馏塔的不同位置设置有收集点,可以分别收集到轻质产品如天然气、汽油、煤油和重质产品如柴油、航煤和石油焦等。
最后是产品分馏阶段。
在减压蒸馏得到的原油产品中,还需要进一步分离出各种不同的产品。
这通常是在分馏塔中进行的,通过控制温度和压力的变化,将不同沸点的产品进一步分离出来。
这样就可以得到高纯度的各种石油产品,满足工业和生活的需要。
综上所述,原油常减压蒸馏的工艺流程是一个复杂而精细的过
程。
通过这个过程,原油中的各种成分可以被有效地分离出来,得到各种优质的石油产品。
这对于石油行业的发展和石油产品的质量提升具有重要意义。
常减压蒸馏装置设计
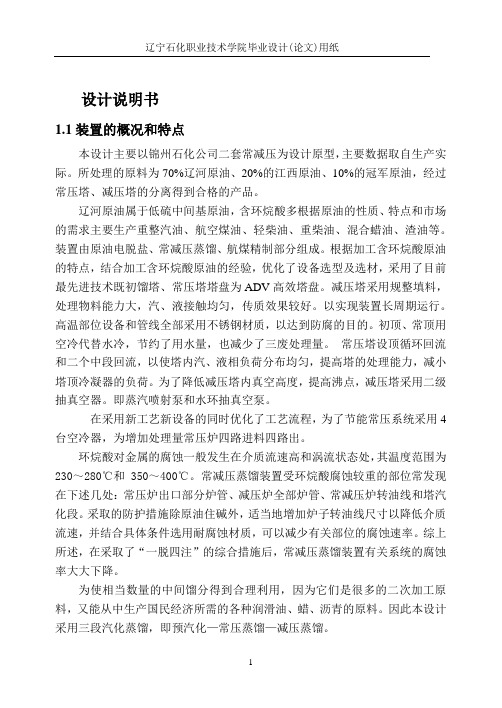
设计说明书1.1装置的概况和特点本设计主要以锦州石化公司二套常减压为设计原型,主要数据取自生产实际。
所处理的原料为70%辽河原油、20%的江西原油、10%的冠军原油,经过常压塔、减压塔的分离得到合格的产品。
辽河原油属于低硫中间基原油,含环烷酸多根据原油的性质、特点和市场的需求主要生产重整汽油、航空煤油、轻柴油、重柴油、混合蜡油、渣油等。
装置由原油电脱盐、常减压蒸馏、航煤精制部分组成。
根据加工含环烷酸原油的特点,结合加工含环烷酸原油的经验,优化了设备选型及选材,采用了目前最先进技术既初馏塔、常压塔塔盘为ADV高效塔盘。
减压塔采用规整填料,处理物料能力大,汽、液接触均匀,传质效果较好。
以实现装置长周期运行。
高温部位设备和管线全部采用不锈钢材质,以达到防腐的目的。
初顶、常顶用空冷代替水冷,节约了用水量,也减少了三废处理量。
常压塔设顶循环回流和二个中段回流,以使塔内汽、液相负荷分布均匀,提高塔的处理能力,减小塔顶冷凝器的负荷。
为了降低减压塔内真空高度,提高沸点,减压塔采用二级抽真空器。
即蒸汽喷射泵和水环抽真空泵。
在采用新工艺新设备的同时优化了工艺流程,为了节能常压系统采用4台空冷器,为增加处理量常压炉四路进料四路出。
环烷酸对金属的腐蚀一般发生在介质流速高和涡流状态处,其温度范围为230~280℃和350~400℃。
常减压蒸馏装置受环烷酸腐蚀较重的部位常发现在下述几处:常压炉出口部分炉管、减压炉全部炉管、常减压炉转油线和塔汽化段。
采取的防护措施除原油住碱外,适当地增加炉子转油线尺寸以降低介质流速,并结合具体条件选用耐腐蚀材质,可以减少有关部位的腐蚀速率。
综上所述,在采取了“一脱四注”的综合措施后,常减压蒸馏装置有关系统的腐蚀率大大下降。
为使相当数量的中间馏分得到合理利用,因为它们是很多的二次加工原料,又能从中生产国民经济所需的各种润滑油、蜡、沥青的原料。
因此本设计采用三段汽化蒸馏,即预汽化—常压蒸馏—减压蒸馏。
常减压蒸馏装置常压塔工艺设计
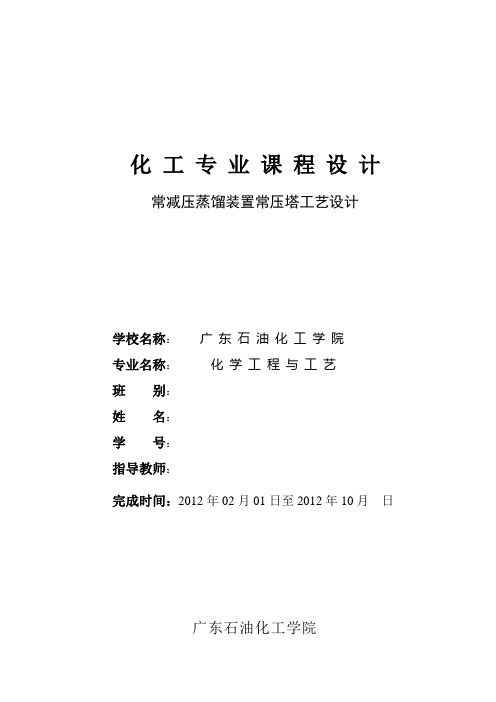
化工专业课程设计常减压蒸馏装置常压塔工艺设计学校名称:广东石油化工学院专业名称:化学工程与工艺班别:姓名:学号:指导教师:完成时间:2012年02月01日至2012年10月日广东石油化工学院课程设计说明书设计名称:化工专业课程设计题目:530万吨/年原油常减压蒸馏装置设计常压分馏塔工艺设计学生:学号:班别:专业:化学工程与工艺指导教师:日期:2012 年02 月20 日广东石油化工学院化学工程与工艺专业设计任务书2012 年9 月30 日批准系主任谢颖发给学生1.设计题目: 原油常减压蒸馏装置工艺设计2. 学生完成全部设计之期限: 2013 年10 月20 日3. 设计之原始数据: (另给)4. 计算及说明部分内容: (设计应包括的项目)一、总论1.概述;2.文献综述;3.设计任务依据;4.主要原材料;5.其他二、工艺流程设计1. 原料油性质及产品性质;2. 生产方案;3.工艺流程;4. 蒸馏塔类型、塔器结构;5.环保措施三、常压蒸馏塔工艺计算1. 工艺参数计算;2. 物料平衡计算;3.操作条件的确定;4. 蒸馏塔各点温度核算;5. 蒸馏塔汽液负荷计算四、常压蒸馏塔尺寸计算1. 塔径计算;2. 塔高计算五、常压蒸馏塔水力学计算六、车间布置设计1. 车间平面布置方案;2. 车间平面布置图;3. 常压蒸馏塔装配图七、参考资料5. 绘图部分内容: (明确说明必绘之图)(1) 原油常减压蒸馏装置工艺流程图(2) 车间平面布置图(3) 常压蒸馏塔装配图插图: 主要塔器图, 蒸馏塔汽液负荷分布图, 计算草图等.6. 发出日期: 2013 年9 月30 日设计指导教师:完成任务日期: 2013 年10 月日学生签名:石油化工生产技术课程设计原油常减压蒸馏装置工艺设计基础数据1、原油的一般性质大庆原油,204d= 0.8587;特性因数K=12.32、原油实沸点蒸馏数据表1 大庆原油实沸点蒸馏及窄馏分性质数据馏分号沸点范围/℃占原油(质)/% 密度(20℃)/g·cm-3运动粘度/ mm2·s-1凝点/℃闪点(开)/℃折射率每馏分累计20℃50℃100℃20Dn70Dn1 初~112 2.98 2.98 0.7108 ————— 1.3995 —2 112~156 3.15 6.13 0.7461 0.89 0.64 ——— 1.4172 —3 156~195 3.22 9.35 0.7699 1.27 0.89 —-65 — 1.4350 —4 195~225 3.25 12.60 0.7958 2.03 1.26 —-41 78 1.4445 —5 225~257 3.40 16.00 0.8092 2.81 1.63 —-24 — 1.4502 —6 257~289 3.40 19.46 0.8161 4.14 2.26 —-9 125 1.4560 —7 289~313 3.44 22.90 0.8173 5.93 3.01 — 4 — 1.4565 —8 313~335 3.37 26.27 0.8264 8.33 3.84 1.73 13 157 1.4612 —9 335~355 3.45 29.72 0.8348 — 4.99 2.07 22 —— 1.445010 355~374 3.43 33.15 0.8363 — 6.24 2.61 29 184 — 1.445511 374~394 3.35 36.50 0.8396 —7.70 2.86 34 —— 1.447212 394~415 3.55 40.05 0.8479 —9.51 3.33 38 206 — 1.451513 415~435 3.39 43.44 0.8536 —13.3 4.22 43 —— 1.456014 435~456 3.88 47.32 0.8686 —21.9 5.86 45 238 — 1.464115 456~475 4.05 51.37 0.8732 ——7.05 48 —— 1.467516 475~500 4.52 55.89 0.8786 ——8.92 52 282 — 1.469717 500~525 4.15 60.04 0.8832 ——11.5 55 —— 1.4730 渣油>525 39.96 100.0 0.9375 ———41①———3、产品方案及产品性质4. 设计处理量: 250+学号×10万吨/年, 开工:8000小时/年。
常减压蒸馏装置常压塔工艺设计分解
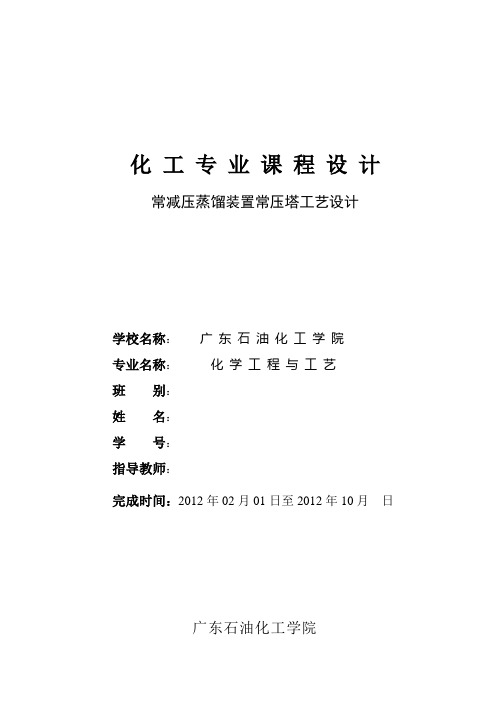
化工专业课程设计常减压蒸馏装置常压塔工艺设计学校名称:广东石油化工学院专业名称:化学工程与工艺班别:姓名:学号:指导教师:完成时间:2012年02月01日至2012年10月日广东石油化工学院课程设计说明书设计名称:化工专业课程设计题目:530万吨/年原油常减压蒸馏装置设计常压分馏塔工艺设计学生:学号:班别:专业:化学工程与工艺指导教师:日期:2012 年02 月20 日广东石油化工学院化学工程与工艺专业设计任务书2012 年9 月30 日批准系主任谢颖发给学生1.设计题目: 原油常减压蒸馏装置工艺设计2. 学生完成全部设计之期限: 2013 年10 月20 日3. 设计之原始数据: (另给)4. 计算及说明部分内容: (设计应包括的项目)一、总论1.概述;2.文献综述;3.设计任务依据;4.主要原材料;5.其他二、工艺流程设计1. 原料油性质及产品性质;2. 生产方案;3.工艺流程;4. 蒸馏塔类型、塔器结构;5.环保措施三、常压蒸馏塔工艺计算1. 工艺参数计算;2. 物料平衡计算;3.操作条件的确定;4. 蒸馏塔各点温度核算;5. 蒸馏塔汽液负荷计算四、常压蒸馏塔尺寸计算1. 塔径计算;2. 塔高计算五、常压蒸馏塔水力学计算六、车间布置设计1. 车间平面布置方案;2. 车间平面布置图;3. 常压蒸馏塔装配图七、参考资料5. 绘图部分内容: (明确说明必绘之图)(1) 原油常减压蒸馏装置工艺流程图(2) 车间平面布置图(3) 常压蒸馏塔装配图插图: 主要塔器图, 蒸馏塔汽液负荷分布图, 计算草图等.6. 发出日期: 2013 年9 月30 日设计指导教师:完成任务日期: 2013 年10 月日学生签名:石油化工生产技术课程设计原油常减压蒸馏装置工艺设计基础数据1、原油的一般性质大庆原油,204d= 0.8587;特性因数K=12.32、原油实沸点蒸馏数据表1 大庆原油实沸点蒸馏及窄馏分性质数据馏分号沸点范围/℃占原油(质)/% 密度(20℃)/g·cm-3运动粘度/ mm2·s-1凝点/℃闪点(开)/℃折射率每馏分累计20℃50℃100℃20Dn70Dn1 初~112 2.98 2.98 0.7108 ————— 1.3995 —2 112~156 3.15 6.13 0.7461 0.89 0.64 ——— 1.4172 —3 156~195 3.22 9.35 0.7699 1.27 0.89 —-65 — 1.4350 —4 195~225 3.25 12.60 0.7958 2.03 1.26 —-41 78 1.4445 —5 225~257 3.40 16.00 0.8092 2.81 1.63 —-24 — 1.4502 —6 257~289 3.40 19.46 0.8161 4.14 2.26 —-9 125 1.4560 —7 289~313 3.44 22.90 0.8173 5.93 3.01 — 4 — 1.4565 —8 313~335 3.37 26.27 0.8264 8.33 3.84 1.73 13 157 1.4612 —9 335~355 3.45 29.72 0.8348 — 4.99 2.07 22 —— 1.445010 355~374 3.43 33.15 0.8363 — 6.24 2.61 29 184 — 1.445511 374~394 3.35 36.50 0.8396 —7.70 2.86 34 —— 1.447212 394~415 3.55 40.05 0.8479 —9.51 3.33 38 206 — 1.451513 415~435 3.39 43.44 0.8536 —13.3 4.22 43 —— 1.456014 435~456 3.88 47.32 0.8686 —21.9 5.86 45 238 — 1.464115 456~475 4.05 51.37 0.8732 ——7.05 48 —— 1.467516 475~500 4.52 55.89 0.8786 ——8.92 52 282 — 1.469717 500~525 4.15 60.04 0.8832 ——11.5 55 —— 1.4730 渣油>525 39.96 100.0 0.9375 ———41①———3、产品方案及产品性质表2 产品产率及其性质产品沸点范围产率相对密度恩氏蒸馏数据, ℃名称℃%(重) 204d初10% 30% 50% 70% 90% 终重整原料初~130 4.27 0.7200 42 67 74 86 102 114 127航空煤油130~230 8.86 0.7720 138 158 167 177 191 215 226轻柴油230~320 10.84 0.8210 238 245 252 270 285 291 313重柴油320~360 6.65 0.8305 326 331 333 336 339 344 353重油>360 69.38 0.90504. 设计处理量: 250+学号×10万吨/年, 开工:8000小时/年。
1.5油田原油常压蒸馏装置工艺设计

1.5油田原油常压蒸馏装置工艺设计1.5油田原油常压蒸馏装置工艺设计摘要设计一套年处理量为1.5Mt/a大港原油加工装置,由于原料中轻组分不多,所以原油蒸馏装置采用二段汽化,设计常压塔,减压塔。
设计中采用水蒸气汽提方式, 并确定汽提水蒸汽用量;由于浮阀塔操作弹性大,本设计采用浮阀塔。
原油蒸馏在炼油厂是原油首先要通过的加工装置。
一般包括预处理系统(原油电脱盐)、常压分馏系统、减压分馏系统、注剂系统、轻烃回收系统(加工轻质原油且达到经济规模时一般设置轻烃回收系统)等。
常压蒸馏就是在常压下对原油进行加热、气化、分馏和冷凝。
如此得到各种不同沸点范围的石油馏分。
常减压蒸馏是指在常压和减压条件下,根据原油中各组分的沸点不同,把原油“切割”成不同馏分的工艺过程。
关键词:原油常压蒸馏,大港原油加工装置,原油“切割”目录前言 (1)第一章常减压蒸馏1.1 常减压蒸馏技术现状 (2)1.2 节能措施 (3)第二章工艺流程设计2.1 原料油性质及产品性质 (4)2.1.1 原料油性质 (4)2.1.2 产品性质 (5)2.2 工艺流程 (5)2.3 塔器结构 (6)2.4 环保措施 (6)2.4.1 污染源分析 (6)2.4.2 废气处理 (7)2.4.3 废水处理 (7)2.4.4 噪声防护 (8)第三章工艺计算3.1 原料及产品的有关参数的计算 (10)3.2 工艺流程的确定根据与流程的叙述 (11)3.2.1 切割方案及性质 (11)3.2.2 汽提蒸汽用量 (12)3.2.3 操作压力 (14)3.2.4 汽化段温度 (14)3.3 蒸馏塔各点温度核算 (16)3.3.1 塔底温度 (16)3.3.2 塔顶及各侧线温度的假设与回流热分配 (16)3.3.3 侧线及塔顶温度的校核 (17)第四章常压蒸馏塔尺寸计算4.1 塔径的计算 (20)4.1.1 塔径的初算 (20)4.1.2计算出Wmax后再计算适宜的气速Wa (20)4.1.3 计算气相空间截面积 (21)4.1.4 降液管内流体流速Vd (21)4.1.5 计算降液管面积 (21)4.1.6 塔横截面积Ft的计算 (21)4.1.7 采用的塔径D及空塔气速W (22)4.2 塔高的计算 (22)第五章水力学衡算5.1 塔板布置,浮阀、溢流堰及降液管的计算 (23)5.2 塔的水力学计算 (24)5.2.1 塔板总压力降 (25)5.2.2 雾沫夹带 (25)5.2.3 泄漏 (26)5.2.4 淹塔 (27)5.2.5 降液管超负荷 (27)5.2.6 适宜操作区和操作线 (27)结论 (29)参考文献 (30)致谢 (31)前言石油是一种主要由碳氢化合物组成的复杂混合物。
- 1、下载文档前请自行甄别文档内容的完整性,平台不提供额外的编辑、内容补充、找答案等附加服务。
- 2、"仅部分预览"的文档,不可在线预览部分如存在完整性等问题,可反馈申请退款(可完整预览的文档不适用该条件!)。
- 3、如文档侵犯您的权益,请联系客服反馈,我们会尽快为您处理(人工客服工作时间:9:00-18:30)。
580万/年原油常减压蒸馏装置工艺设计 (年处理量250+33*10=580万吨/年) 一. 总论
1.1概述 石油加工是国民经济的主要产业以及国民经济的支柱产业之一,在国民经济中有着重要的地位。石油产品应用在国民经济中的各行各业,涉及到民用以及军用。石油已是一个国家懒以生存产品,是一个国家能否兴旺发达的有力支柱。 目前,国际原油供不应求,价格高居不下,原油供应紧张,并由原油所引发起不少主要产油地区的不稳定。我国是一个人口大国,石油的需求在近年来尤其紧张,并随着经济的发展,市场需求越来越大,石油产品利润很高。 本设计是以大港原油为加工原油,采用常减压蒸馏装置蒸馏加工(580万吨/年)原油,而分离出以汽油,煤油,轻柴油,重柴油以及重油为主要产品的各种油产品。本方法简单实用,处理量大,技术成熟,是目前国内外处理原油最主要的方法。
1.2文献综述 本设计是以课程设计、化工设计为基础,以课程中指导老师给出的数据为依据,参考《化工原理》、《化工设计》、《石油练制工艺学》、《石油化工工艺计算图表》《工程制图》等资料。采用原油常减压蒸馏装置工艺设计以生产重整原油,煤油,轻柴油,重柴油,重油等产品。所采用的方法是目前国内外最实用,最普遍,最成熟的原油加工方法。适用国内大中小企业等使用。
1.3设计任务依据 所设计任务是以指导老师给出的原油数据为依据。 所设计的设备参数是以一些权威书籍为参考。
1.4主要原材料 本设计主要的原材料主要有大港原油、水、电 1.5其它
本设计应设计应用在一些交通运输方便,市场需求大的附近。同时,生产过程中应与环境相给合,注重“三废”的处理,坚持国家可持续发展的战略,坚持和谐发展的道路,与时俱进。同时应注意到,废品只是一种放在待定时间与空间中的原材料,在另一些场所,它们又是一种原材料,因而,在生产过程中,应把“三废”综合利用。 2、1 工艺参数计算 2、1、1 原料及产品的有关参数的计算 以下的转换计算均以重整原料为例,其它产品仅写出计算结果。 (1) 根据提供的原油实沸点蒸馏数据,常压下的平衡蒸发数据作出实沸点曲线和常压下的原油平衡蒸发曲线,见图2-1 (2) 体积平均沸点,tv
重整原料: 879399106118100.65vt (3)恩氏蒸馏90%-10% 斜率
重整原料:118870.38759010k (4)立方平均沸点 tc 由《工艺计算图表》图2—1查得体积平均沸点校正值为:-1.8℃ 重整原料tc=100.6-1.8=98.8℃ (5)中平均沸点, t(中): 由图表集图2-1-1查得体积平均沸点校正值为-2.2℃, 故: 汽油, t(中)=t(体)-2.2℃=98.8-2.2=98.4℃ (6)特性因数 K: 由图表集图2-1-2查得: 汽油 K=11.58。 (7)分子量 M: 由图表集图2-1-2查得: 汽油 M=96. (8)平衡蒸发温度 由图表集图2-2-3及图2-2-4计算出汽油平衡蒸发100%温度为109℃。 (9)临界温度, tkp: 由图表集图2-3-7和图2-3-8查得: 汽油 tkp=275℃。 (10)临界压力, Pkp: 由图表集图2-3-9查得: 汽油Pkp=3.26MPa。 (11)焦点温度, tF 由图表集图2-2-19查得, 汽焦点温度为307℃。 (12)焦点压力, PF 由图表集图2-2-18查得, 汽焦点压力为4.52MPa。 表2 油品的有关性质参数计算汇总 油品名称 密 度 d204 比重指数oAPI 特性因 数 K 分子量 M
平衡蒸发温度 ℃ 临界参数 焦点参数
0 % 100% 温度℃ MPa 温度℃ MPa 汽油 0.7342 59.2 11.58 96 109 275 3.26 307 4.52 煤油 0.7909 47.2 11.9 158 164 371 2.31 408.1 4.51 轻柴 0.8406 42.3 12.12 219 247 442 1.94 461.4 2.39 重柴 0.8450 41.8 12.62 305 340.8 497 1.38 506.8 1.58 重油 0.9200 21.2 12.1 290 原油 0.7342 32 12
2、1、2产品收率及物料平衡
物料平衡可参考同一原油丶同一产品方案的生产数据确定。确定后列出物料平衡表。如不能取得实标生产数据, 可根据实沸点数据来确定。 如表1所示, 相邻两个产品是互相重叠的, 即实沸点蒸馏(tH-tL)是负值。通常相邻两个产品的实沸点就在这一重叠值的一半处, 因此可取tH和tL之间的中点温度作为这两个馏分的切割温度, 按切割温度, 可以从原油的实沸点曲线得出各产品的收率。决定年开工天数后, 即可作出常压塔的物料平衡表, 如表3所示。表3中没有考虑到损失, 在实标生产中通常取(气体+损失)约占原油的0.5%。 注: tH为相邻两馏分重馏分实沸点的0%点温度; tL为相邻两馏分轻馏分实沸点的100%点温度。 表3 物料平衡表(按每年开工330天计) 油 品 产 率,% 处 理 量 或 产 量 体积 质量 104t/Y t/D kg/h kmol/h 原 油 100 100 280 7576 350000
产 品
汽油 5.0 4.2 11.76 266 14700 153 煤油 10.4 9.4 26.32 505 32900 208.2 轻柴油 14 13.5 37.8 524 47250 215.8 重柴油 5.9 5.7 15.96 730 19950 65.4 重油 64.7 67.2 188.16 5551 235200
2、1、3.汽提蒸汽用量
侧线产品及塔底重油都用过热水蒸汽汽提, 使用的是温度420℃, 压力0.3MPa的过热水蒸汽。 汽提水蒸汽用量与需要汽提出来的轻组分含量有关。在设计中可参考经验数据选择汽提蒸汽用量。 表4 汽提水蒸气用量 油品 质量分数 Kg/h Kmol/h 一线煤油 3 98.7 5.5 二线轻柴油 3 1417.5 78.75 三线重柴油 2.8 558.6 31 塔底重油 2 4704 261.3 合计 7667 425.9 2、2 操作条件的确定 2、2、1 决定塔板数、塔顶压力和塔板压力降 (1)根据《塔的工艺计算》表1-3决定塔板数如下: 汽油──煤油段 9层(考虑一线生产航煤) 煤油──轻柴油段 6层 轻柴油──重柴油段 6层 重柴油──汽化段 3层 塔底汽提段 4层 全塔用两个中段回流, 每个用3层换热塔板, 共6层, 全塔塔板总数为34层。 (2)分馏塔计算草图
(3) 操作压力 取塔顶产品罐压力为: 0.131MPa。塔顶采用两级冷凝冷却流程图。取塔顶空冷器压力降为0.01MPa, 使用一个管壳式后冷器, 壳程压力降取0.0171MPa, 故塔顶压力=0.13+0.01+0.017=0.1571MPa (绝)。 取每层浮阀塔板压力降为0.00051MPa (4mmHg), 则推算常压塔各关键部位的压力如下: (单位为MPa) 塔顶压力 0.157 一线抽出板(第9层)上压力 0.161 二线抽出板(第18层)上压力 0.166 三线抽出板(第27层)上压力 0.170 汽化段压力(第30层下) 0.172 取转油线压力降为0.0351MPa, 则 加热炉出口压力=0.172+0.035=0.2071MPa (4)汽化段温度 ①汽化段中进料的汽化率与过汽化率 取过汽化率为进料的2%(质)(经验值为2~4)或2.06%(体), 则过汽化油量为7000kg/h, 要求进料在汽化段的汽化率为: eF=(5.0+10.4+14+5.9+2.06)%=37.29%(体) ②汽化段油气分压 汽化段中各物料的流量如下: 汽油 153kmol/h 煤油 20832kmol/h 轻柴油 215.8kmol/h 重柴油 65.4kmol/h 过汽化油 23.3kmol/h 油气量合计 665.5kmol/h 其中过汽化油的分子量取300, 水蒸汽261kmol/h(塔底汽提)。由此计算得过汽化段的油气分压为: 0.172×665.5/(665.5+261)=0.124MPa ③汽化段温度的初步求定 汽化段温度应该是在汽化段油气分压0.124MPa之下汽化37.29%(体)的温度, 为此需要作出在0.124MPa下的原油平衡汽化曲线, 见图1中的曲线4。在不具备原油的临界参数与焦点参数而无法作出原油的P-T-e相图的情况下, 曲线4可用简化法求定: 由图1可得到原油在常压下的实沸点曲线与平衡汽化曲线的交点为310℃。将此交点温度换算成在0.124MPa压力下的温度为315℃。过该交点作垂直于横座标的直线A, 在A线上找到315℃之点, 过此点作平行于原油常压平衡汽化曲线2的线4, 即为原油在0.124MPa下的平衡汽化曲线。 由曲线4可查得当eF为37.29%(体)时的温度为350℃, 此即欲求的汽化段温度tF。此tF是由相平衡关系求得, 还需对它进行校核。 ④tF的校核 校核的目的是看tF要求下的加热炉出口温度是否合理。校核的方法是作绝热闪蒸过程的热平衡计算以求得炉出口温度。 当汽化率eF=37.29%(体), tF=350℃, 进料在汽化段中的焓hF计算如表8所示。 表8 进料带入汽化段的热量QF(P=0.172MPa, t=350℃)
物料 焓,Kj/kg 热量,kJ/h 汽相 液相
汽油 1146 1146×14700=16.85×106 煤油 1134 1147×32900=37.31×106 轻柴油 1126 1130×47250=53.18×106 重柴油 1121 1122×19950=22.37×106 过汽化油 ~1109 1109×7000=7.76×106 重油 877 877×235200=206.27×106 合计 QF=343.7×106 hF=343.7×106/350000=982.12kJ/kg 再求出原油在加热炉出口条件下的热焓ho, 按前述方法作出原油在炉出口