Quality Report1
品质改善报告范文3篇

品质改善报告范文3篇Quality improvement report model汇报人:JinTai College品质改善报告范文3篇前言:报告是按照上级部署或工作计划,每完成一项任务,一般都要向上级写报告,反映工作中的基本情况、工作中取得的经验教训、存在的问题以及今后工作设想等,以取得上级领导部门的指导。
本文档根据申请报告内容要求展开说明,具有实践指导意义,便于学习和使用,本文档下载后内容可按需编辑修改及打印。
本文简要目录如下:【下载该文档后使用Word打开,按住键盘Ctrl键且鼠标单击目录内容即可跳转到对应篇章】1、篇章1:品质改善报告模板(通用版)2、篇章2:品质改善报告样本(常用版)3、篇章3:品质改善报告模板篇章1:品质改善报告模板(通用版)我于12月1日正式成为东方CJ顾客中心商谈7组组员,成为正式员工已有3个月左右的日子,在最近的1个多月里,我的情况不敬如人意,已经犯下了多次商谈错误,并且被领导谈话教育。
在此,辜负了领导及同事对于我的信任,深表歉意。
在这段时间里,我进行了深刻的反思,归根结底主要问题出在以下2点:1.对工作态度的散漫由于在起初的2个月里没有犯下致命错误,并且成为正式员工已有一段时间,造成了自满的情绪,忽略了自己的不足点,所以在工作中,缺少主动性,对我组老员工提出的建议也是听过算数,没有认真思考并加以改善。
随着工作态度的下降,业务看的少了,对工作的关心程度,参与度也少了,在商谈中抱着侥幸的心理去应对。
导致了QA成绩下降,犯下商谈员错误等一系列问题。
2.对工作失去热情在工作了一段时间后,渐渐发觉每天的工作就是重复接听电话,也没有空余的时间来调节自己,与同事之间缺乏沟通交流。
每天上班变的枯燥乏味起来,对商谈产生了抗拒的心理。
改进目标通过总结以上两点问题,改变自己对工作态度上的散漫,提高自己对工作的职业操守。
争取在以后的工作中提高自己的QA成绩,重新得到领导和同事的信任。
服装英文验货报告范文

服装英文验货报告范文Clothing Quality Inspection Report.1. Introduction.This comprehensive quality inspection report aims to assess the conformity and quality of the clothing items under review. The inspection covers various aspects of the garments, including material, stitching, fit, and overall appearance. The report is conducted to ensure that the products meet the specified requirements and standards.2. Material Evaluation.The clothing items were inspected for the type of material used. The fabric was checked for its thickness, texture, and colorfastness. The inspection revealed that the majority of the items were made from high-quality cotton blend, which provided both comfort and durability. However, a few items showed slight variations incolorfastness, which might affect their longevity.3. Stitching Quality.The stitching was evaluated for its uniformity, tightness, and overall durability. The inspection teamnoted that the majority of the garments had neatly done stitching, with no loose threads or uneven patches. However, a few garments exhibited minor stitching issues, such as skipped stitches or uneven thread tension, which could potentially affect their durability.4. Fit and Design.The fit and design of the clothing items were also inspected. The items were measured to ensure they adheredto the specified size chart. Additionally, the cut and styling of the garments were assessed for their attractiveness and comfort. Overall, the inspectionrevealed that the majority of the items fitted well andwere designed to complement a wide range of body types.5. Packaging and Labeling.The packaging and labeling of the clothing items were also inspected. The items were checked for proper packaging, ensuring they were protected during transit. Additionally, the labels were inspected for accuracy, including size, material, and care instructions. The inspection revealedthat the packaging and labeling were generally satisfactory, with minor inconsistencies noted in a few cases.6. Conclusion.Overall, the clothing items under review exhibited good quality and conformed to the specified requirements. However, minor issues were identified in a few areas, such as colorfastness and stitching quality. It is recommended that these issues be addressed to ensure the highestquality standards are maintained. Additionally, attention should be paid to ensuring consistency in packaging and labeling to enhance the overall customer experience.7. Recommendations.To further improve the quality of the clothing items, the following recommendations are suggested:Conduct regular quality checks throughout the production process to identify and address any issues early on.Invest in high-quality materials to ensure durability and colorfastness.Train stitchers regularly to maintain consistent stitching quality.Implement strict quality control measures during packaging and labeling to ensure accuracy and consistency.By implementing these recommendations, it is expected that the quality of the clothing items will be further enhanced, providing a superior customer experience.8. Future Outlook.With the continuous evolution of fashion trends and consumer preferences, it is crucial to stay updated with the latest industry standards and best practices. The manufacturer should aim to innovate and improve their products to meet the changing needs of the market. By focusing on quality, comfort, and style, the manufacturer can ensure that their clothing items remain competitive in the market and continue to satisfy their customers.In conclusion, this quality inspection report provides a detailed assessment of the clothing items under review. While the majority of the items exhibited good quality, minor issues were identified that need to be addressed. By implementing the recommended measures, the manufacturer can ensure the highest quality standards are maintained, providing a superior customer experience.。
QC Report.ppt
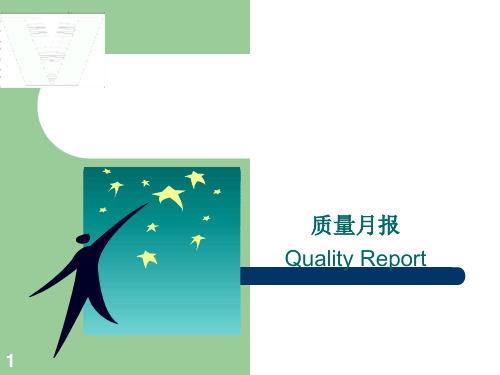
2、塑件 (1)塑件本月共生产 46种规格,共112897 只。 三、成品 (1)本月出成品灯管共 15 批 9种规格 240290 只
(其中螺旋管234689只),合格出货8批,总数36142 只,其余均为特采。环灯出货5801,其中有1697只为特 采。 四、客户反馈 本月客户投诉6次;退货5批,退货总数22745。 五、异常或特采 本月特采5批,开出异常通知7次,得到回复2次。
18
比华集团(金山厂) VIVA Group (Jinshan)
以往质量改善的追踪 Ameliorate Pursue
一、上次会议的追踪(见质量会议待办事项) 1、掉粉问题 。螺旋灯未有效改善。环灯有改善
但带来光通量下降的问题。(暂未完全证实光通 量的下降与此有关 2、光参数的不符合,未有效改善 二、质保课反馈事项的整改 1、反馈的环灯和螺旋灯的掉粉问题有所改善, 目前在实验中。
P P M ?<?LS L 68965.52
P P M ?>?U S L
*
P P M ?T otal
68965.52
1300 1400
E xp. Within P erformance
P P M ?<?LS L 92234.92
P P M ?>?U S L
*
P P M ?T otal
92234.92
24
比华集团(金山厂)
VIVA Group (Jinshan)
会议决议事项
Decision Proceeding
本事项品质周会使用,见《质量会议待办事项》
3
比华集团(金山厂) VIVA Group (Jinshan)
英文版qc报告

英文版qc报告QC ReportReport title: Quality Control ReportDate: [Enter date]Report prepared by: [Enter name]1. Introduction:The purpose of this Quality Control (QC) report is to provide an overview of the quality control measures taken during the specified time period. This report aims to evaluate the effectiveness of the quality control procedures implemented and identify areas for improvement.2. Objective:The main objective of the QC report is to assess the quality standards and ensure that they are in compliance with predetermined criteria. It also aims to identify any deviations or anomalies that may have occurred and analyze their root causes.3. Quality Control Procedures:a. Inspection: The inspection process involved the thorough examination of raw materials, work in progress, and finished products. The inspection team conducted random checks to ensure adherence to quality standards.b. Testing: Samples from each batch were tested for various quality parameters such as strength, stability, and functionality. This was carried out using validated testing methods andequipment.c. Documentation: Complete documentation of all quality control processes was maintained, including inspection reports, test results, and any corrective actions taken.4. Results and Analysis:a. Conformance rate: The overall conformance rate for the specified time period was [enter percentage], indicating that [enter percentage] of the products met the predetermined quality criteria.b. Deviations: [Enter number] deviations were identified during the inspection process. The most common deviations were [enter details]. The root causes of these deviations were found to be [enter causes].c. Corrective Actions: Immediate corrective actions were taken to address the identified deviations. These included [enter details of corrective actions].d. Trends and Patterns: An analysis of the QC data revealed certain trends and patterns, suggesting potential areas for improvement. These trends will be further investigated to enhance the overall quality control processes.5. Conclusion:In conclusion, the quality control measures implemented during the specified time period were effective in ensuring a high level of product quality. The identified deviations were promptly addressed, and corrective actions were taken. The analysis of QC data highlighted areas for improvement, which will be considered for future quality control enhancements.6. Recommendations:Based on the findings of this QC report, the following recommendations are proposed for improvements:a. Increase the frequency of random inspections.b. Conduct comprehensive training sessions for the production team to ensure better adherence to quality standards.c. Review and update quality control procedures based on the identified trends and patterns.This completes the English version of the QC report.。
质量分析报告的英文

质量分析报告的英文Quality Analysis Report1. IntroductionThe purpose of this report is to provide a detailed analysis of the quality of a product or process. Quality analysis plays a crucial role in ensuring the delivery of high-quality products or services, identifying areas for improvement, and maintaining customer satisfaction. This report will outline the methodology used for quality analysis, present the findings, and provide recommendations for enhancing quality.2. MethodologyTo conduct the quality analysis, a combination of quantitative and qualitative methods was employed. The quantitative analysis involved collecting data on various quality metrics such as defect rates, customer complaints, and customer satisfaction scores. This data was then analyzed to identify trends, patterns, and areas of concern. The qualitative analysis involved conducting interviews with key stakeholders, such as customers, employees, and suppliers, to gatherinsights on their perceptions of quality and any potential issues.3. FindingsBased on the analysis conducted, the following key findings were identified:3.1. Defect RatesThe defect rates for the product were found to be higher than industry standards. This indicates a potential problem in the manufacturing process or the quality of raw materials used.3.2. Customer ComplaintsA significant number of customer complaints were observed, particularly relating to product reliability, durability, and customer service. This suggests that there may be systemic quality issues affecting customer satisfaction.3.3. Supplier PerformanceThe analysis revealed that certain suppliers consistently provided lower-quality materials, resulting in higher defect rates. This highlights the need for closer monitoring and evaluation of suppliers to ensure consistent quality.3.4. Employee FeedbackDuring interviews with employees, it was found that they lacked adequate training and resources to produce high-quality products. This points to the importance of providing ongoing training and support to improve employee competencies and ensure quality control measures are effectively implemented.4. RecommendationsBased on the findings of the quality analysis, the following recommendations are proposed for enhancing quality:4.1. Process ImprovementEvaluate and improve the manufacturing process to identify and eliminate potential sources of defects. This includes conducting root cause analysis, implementing quality control tools such as Six Sigma, and ensuring proper control measures are in place.4.2. Supplier Evaluation and CollaborationEstablish a robust supplier evaluation process to identify and select reliable suppliers. Regularly monitor their performance and collaborate with them to address quality concerns and establish clear quality standards.4.3. Employee Training and DevelopmentInvest in comprehensive training programs to enhance employee competencies and provide them with the necessary skills and knowledge to produce high-quality products. Continuous improvement initiatives, such as Lean manufacturing, can also be implemented to foster a culture of quality excellence.4.4. Customer Feedback and EngagementActively seek and analyze customer feedback to identify any recurring issues and address them promptly. Engage with customers through surveys, focus groups, or direct interactions to gain insights into their expectations and incorporate them into the quality improvement process.5. ConclusionQuality analysis plays a vital role in ensuring the continuous improvement and delivery of high-quality products or services. By identifying areas of improvement, addressing systemic quality issues, and engaging key stakeholders, organizations can enhance their overall quality performance and maintain customer satisfaction. The recommendations provided in this report aim to guide the organization towards achieving these objectives.。
Quality Inspection Report
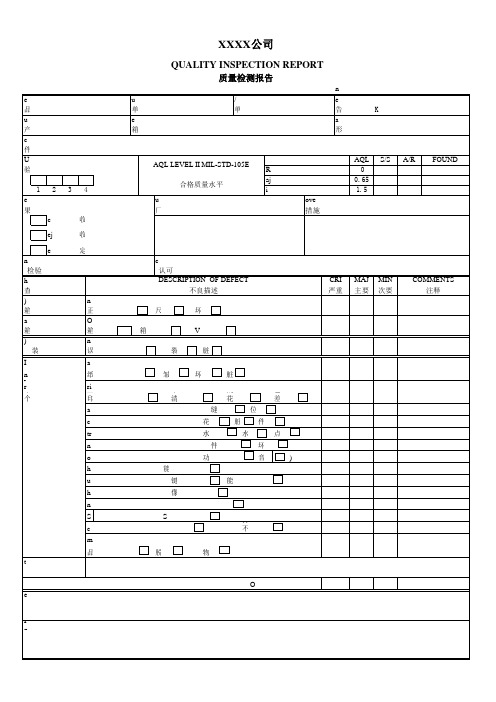
AQL LEVEL II MIL-STD-105E 合格质量水平 Supplier comments 工厂意见
AQL CRI(严重问题) 0 Major(主要问题) 0.65 Minor(次要问题) 1.5 Improvements action 改善措施
S/S
A/R
FOUND
Accept Reject Pending Ister carton 外箱 Carton drop test 外箱跌落测试 II )Package 包装 III ) Individual product 单个产品
FOUND
OMMENTS 注释
CRI 严重
MAJ 主要
MIN 次要
COMMENTS 注释
Incorrect software version 软件版本错误
Small or loose part, material inside the unit. Others 其它 TOTAL General comments: 注释:
Inspector's comment:检验员评述总结:
接收 拒收 待定 Acknowledged by 认可人 DESCRIPTION OF DEFECT 不良描述 Incorrect shipping mark,size,damaged 不正确的唛头 尺寸 损坏 Outer carton,inner carton,PVC damage 外箱损坏 内箱损坏 PVC损坏 Incorrect Package method,tear,dirt 错误的包装方法 破裂 脏 Label and decals on product in incorrect position,wrinkled,damaged,soiled 贴纸位置不正确 丝印: 内容错误 Scratch ,dirt mark, miss part Stress mark, flow mark, sink, stain Any parts broken or damaged No function(no picture, no sound) The function INT Button no function/INT The picture blurred USB cable defect Screw tight,loose 产品内有小件 功能时有时无 按键无功能 图像模糊 USB线不良 螺丝打滑 松脱 杂物 打不到位 功能时有时无 起皱 不清晰 刮花 夹水纹 部件破裂 无功能(无图 损坏 脏 刮花 有缝隙 脏 缩水 损坏 无音 ) 错位 漏件 污点 色差 Printing on product: wrong content, unclear, scratch, different color Gap or mismatch between mate parts
(外出)品质报告中英文
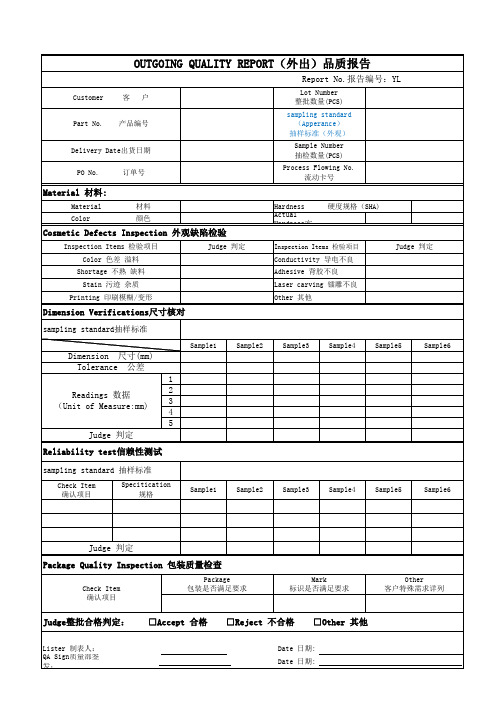
Judge 判定
Color 色差 溢料
Conductivity 导电不良
Shortage 不熟 缺料
Adhesive 背胶不良
Stain 污迹 杂质
Laser carving 镭雕不良
Printing 印刷模糊/变形
Other 其他
Dimension Verifications尺寸核对
OUTGOING QUALITY REPORT(外出)品质报告
Report No.报告编号:YL
Customer 客 户
Lot Number 整批数量(PCS)
Part No. 产品编号
sampling standard (Apperance)
抽样标准(外观)
Delivery Date出货日期
Sample Number 抽检数量(PCS)
PO No.
订单号
Process Flowing No. 流动卡号
Material 材料:
Material
材料
Color
颜色
Cosmetic Defects Inspection 外观缺陷检验
Hardness Actual
Hardness实
硬度规格(SHA)
Inspection Items 检验项目
Package 包装是否满足要求
Mark 标识是否满足要求
Other 客户特殊需求详列
Judge整批合格判定: □Accept 合格 □Reject 不合格 □Other 其他
Lister 制表人: QA Sign质量部签
发:
Date 日期: Date 日期:
sampling standard抽样标准
2019年英文,品质检验报告-优秀word范文 (10页)
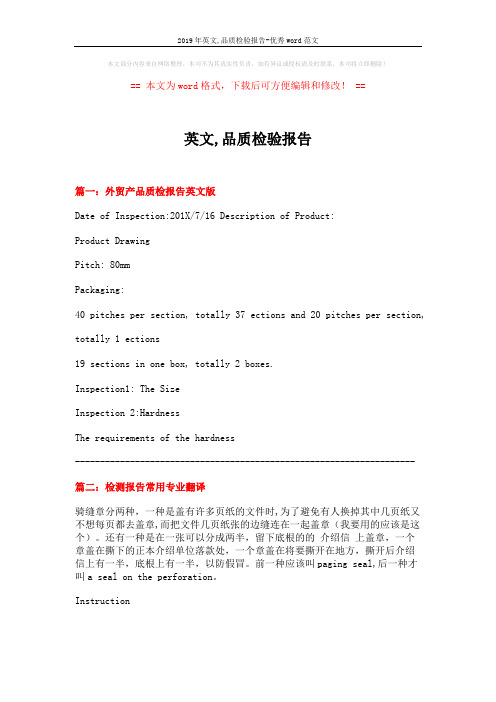
本文部分内容来自网络整理,本司不为其真实性负责,如有异议或侵权请及时联系,本司将立即删除!== 本文为word格式,下载后可方便编辑和修改! ==英文,品质检验报告篇一:外贸产品质检报告英文版Date of Inspection:201X/7/16 Description of Product:Product DrawingPitch: 80mmPackaging:40 pitches per section, totally 37 ections and 20 pitches per section, totally 1 ections19 sections in one box, totally 2 boxes.Inspection1: The SizeInspection 2:HardnessThe requirements of the hardness-------------------------------------------------------------------- 篇二:检测报告常用专业翻译骑缝章分两种,一种是盖有许多页纸的文件时,为了避免有人换掉其中几页纸又不想每页都去盖章,而把文件几页纸张的边缝连在一起盖章(我要用的应该是这个)。
还有一种是在一张可以分成两半,留下底根的的介绍信上盖章,一个章盖在撕下的正本介绍单位落款处,一个章盖在将要撕开在地方,撕开后介绍信上有一半,底根上有一半,以防假冒。
前一种应该叫paging seal,后一种才叫a seal on the perforation。
Instruction1. the report is invalid when there is no ‘special stamp for inspection report’ or inspection organization stamp.----- 报告无‘检验报告专用章’ 或检验单位公章无效。
产品质量不合格整改报告范文

产品质量不合格整改报告范文(中英文实用版)**Product Quality Non-Compliance Rectification Report Template** ---**Executive Summary:**In response to the recent product quality inspection, our company has identified several non-compliance issues that require immediate attention and rectification.This report outlines the specific areas of non-compliance, the potential causes, and the proposed corrective actions to address these issues and ensure future compliance.---**Introduction:**Recently, our company"s product quality has not met the required standards, which has affected customer satisfaction and the company"s reputation.We have conducted a thorough investigation into the matter and are committed to taking necessary actions to rectify the issues and improve our product quality.---**Non-Compliance Issues:**Upon inspection, we found several non-compliance issues, including:1.**Dimensional T olerances:** The product dimensions varied significantly from the specified requirements.2.**Material Composition:** The materials used did not meet the required specifications.3.**Surface Defects:** The product surface had visible defects, such as scratches and dents.4.**Functional Testing:** The product failed several functional tests, indicating potential performance issues.---**Root Cause Analysis:**To address the non-compliance issues, we have conducted a root cause analysis to identify the underlying problems.The analysis revealed the following potential causes:1.Inadequate Quality Control Procedures: There were gaps in our quality control processes, leading to oversight in critical areas.2.Insufficient Training: Some of our staff members may not have had adequate training on quality standards and inspection techniques.3.Supply Chain Issues: The materials provided by our suppliers did not meet the required specifications.4.Equipment Maintenance: Some of our production equipment may not have been properly maintained, affecting product quality.---**Proposed Corrective Actions:**To rectify the non-compliance issues, we have developed thefollowing corrective actions:1.Strengthen Quality Control: We will revise and strengthen our quality control procedures to ensure compliance in all aspects of production.2.Employee Training: We will provide additional training to our staff on quality standards and inspection techniques.3.Supplier Management: We will reevaluate our supplier relationships and implement stricter quality control measures for incoming materials.4.Equipment Maintenance: We will establish a regular maintenance schedule for our production equipment to ensure optimal performance.---**Conclusion:**We acknowledge the importance of product quality and are committed to taking immediate and effective actions to rectify the non-compliance issues.We will continuously monitor and evaluate our production processes to ensure ongoing compliance and improve customer satisfaction.---**中文摘要:**针对近期产品质量检查,我们公司发现了几项需要立即关注和整改的非符合性问题。
品质类术语英文缩写
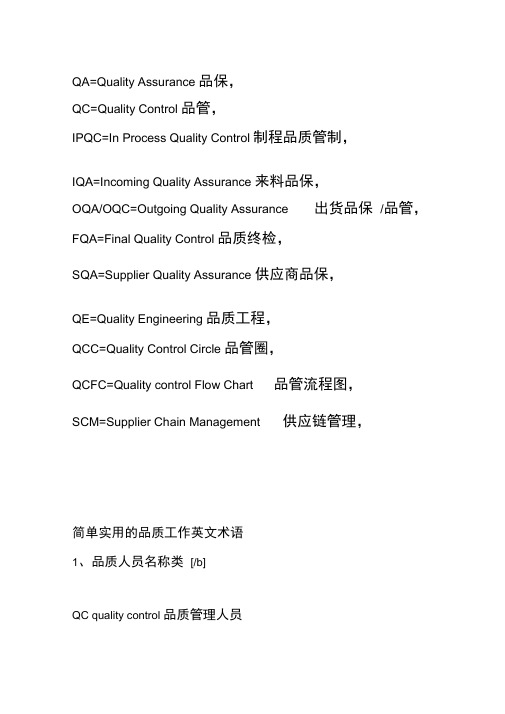
QA=Quality Assurance 品保,QC=Quality Control 品管,IPQC=In Process Quality Control 制程品质管制,IQA=Incoming Quality Assurance 来料品保,OQA/OQC=Outgoing Quality Assurance 出货品保/品管,FQA=Final Quality Control 品质终检,SQA=Supplier Quality Assurance 供应商品保,QE=Quality Engineering 品质工程,QCC=Quality Control Circle 品管圈,QCFC=Quality control Flow Chart 品管流程图,SCM=Supplier Chain Management 供应链管理,简单实用的品质工作英文术语1、品质人员名称类[/b]QC quality control 品质管理人员FQC final quality control 终点品质管制人员IPQC in process quality control 制程中的品质管制人员OQC output quality control 最终出货品质管制人员IQC incoming quality control 进料品质管制人员TQC total quality control 全面质量管理POC passage quality control 段检人员QA quality assurance 质量保证人员OQA output quality assurance 出货质量保证人员QE quality engineering 品质工程人员[b]2 、品质保证类[/b]FAI first article inspection 新品首件检查FAA first article assurance 首件确认TVR tool verification report 模具确认报告3B 3B 模具正式投产前确认CP capability index 能力指数CPK capability index of process 模具制程能力参数SSQA standardized supplier quality 合格供应商品质评估OOBA out of box audit 开箱检查QFD quality function deployment 品质机能展开FMEA failure model effectiveness analysis 失效模式分析8 disciplines 8 项回复内容FA final audit 最后一次稽核CAR corrective action request 改正行动要求corrective action report 改正行动报告[b]3、FQC 运作类[/b]AQL Acceptable Quality Level 运作类允收品质水准S/S Sample size 抽样检验样本大小ACC Accept 允收REE Reject 拒收CR Critical 极严重的MAJ Major 主要的MIN Minor 轻微的AOQ Average Output Quality 平均出厂品质AOQL Average Output Quality Level 平均出厂品质Q/R/S Quality/Reliability/Service 品质/可靠度服务MIL-STDMilitary-Standard 军用标准S I-S IV Special I-Special IV 特殊抽样水准等级P/N Part Number 料号L/N Lot Number 特采AOD Accept On Deviation 特采UAI Use As It 首件检查报告FPIR First Piece Inspection Report 百万分之一PPM Percent Per Million 批号制程统计品管专类SPC Statistical Process Control 统计制程管制SQC Statistical Quality Control 统计品质管制R Range 全距AR Averary Range 全距平均值UCL Upper Central Limit 管制上限管制下限LCL Lower Central LimitMAX Maximum 最大值MIN Minimum 最小值GRR Gauge Reproducibility&Repeatability 量具之再制性及重测性判断量可靠与否DIM Dimension 尺寸DIA Diameter 直径FREQ Frequency 频率N Number 样品数[b]4 、其它品质术语类[/b]QCC Quality Control Circle 品质圈QIT Quality Improvement Team 品质改善小组PDCA Plan Do Check Action 计划执行检查总结ZD Zero Defect 零缺点QI Quality Improvement 品质改善QP Quality Policy 目标方针TQM Total Quality Management 全面品质管理MRB Material Reject Bill 退货单LQL Limiting Quality Level 最低品质水准RMA Return Material Audit 退料认可QAN Quality Amelionrate Notice 品质改善活动ADM Absolute Dimension Measuremat 全尺寸测量QT Quality Target 品质目标7QCTools 7 Quality Controll Tools 品管七大手法[b]5 、通用之件类[/b]ECN Engineering Change Notes 工程变更通知(供应商)ECO Engineering Change Order 工程改动要求(客户)PCN Process Change Notice 工序改动通知PMP Product Management Plan 生产管制计划SIP Specification In Process 制程检验规格SOP Standard Operation Procedure 制造作业规范IS Inspection Specification 成品检验规范BOM Bill Of Material 物料清单PS Package Specification 包装规范SPEC Specification 规格DWG Drawing 图面[/size]。
质量报告英文简写
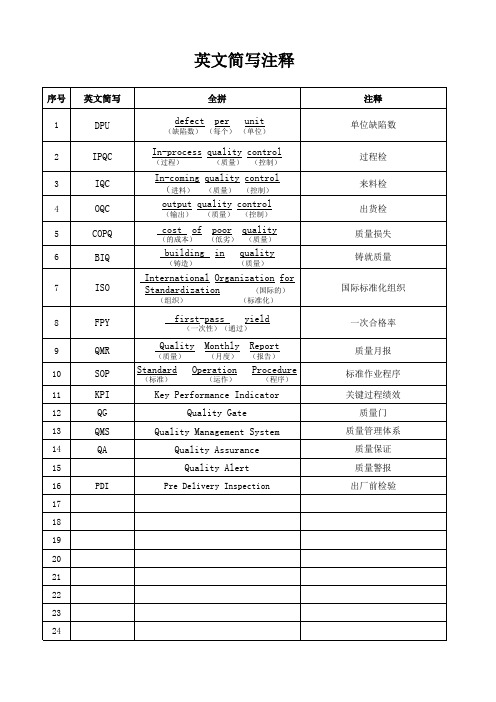
In-process quality control
(过程)
(质量) (控制)
In-coming quality control (进料) (质量) (控制)
output quality control
(输出) (质量) (控制)
cost of poor quality
(的成本) (低劣) (质量)
building in quality
(铸造)
(质量)
International Organization for
Standardization
(国际的)
(组织)
(标准化)
first-pass yield
(一次性)(通过)
Quality Monthly
(质量)
(月度)
Standard Operation
(标准)
(运作)
Report
(报告)
Procedure
(程序)
Key Performance Indicator
Quality Gate
Quality Management System
Quality ery Inspection
注释 单位缺陷数
英文简写注释
序号
1
2
3 4 5 6
7
8
9 10 11 12 13 14 15 16 17 18 19 20 21 22 23 24
英文简写
全拼
DPU
defect per unit
(缺陷数) (每个) (单位)
IPQC IQC OQC COPQ BIQ
ISO
FPY QMR SOP KPI QG QMS QA
过程检 来料检 出货检 质量损失 铸就质量
水土保持工程质量评定报告范文

水土保持工程质量评定报告范文英文回答:Water and soil conservation engineering quality assessment report is an important document that evaluates the quality of a project. It provides an overview of the project, assesses its compliance with relevant standards and regulations, and identifies any deficiencies or areas for improvement.In my experience, a comprehensive quality assessment report should include the following sections:1. Introduction: This section provides background information about the project, including its purpose, location, and scope. It also outlines the objectives of the assessment and the criteria used to evaluate the project.2. Methodology: This section describes the methods and techniques used to assess the project's quality. It mayinclude site visits, inspections, interviews with stakeholders, and analysis of relevant documents and data.3. Findings: This section presents the findings of the assessment. It highlights the strengths and weaknesses of the project, identifies any non-compliance with standards or regulations, and suggests areas for improvement.4. Recommendations: This section provides recommendations for improving the project's quality. It may include specific actions to address deficiencies, suggestions for additional monitoring or evaluation, and recommendations for future projects.5. Conclusion: This section summarizes the key findings and recommendations of the assessment. It emphasizes the importance of quality in water and soil conservation engineering and highlights the benefits of implementing the recommended improvements.中文回答:水土保持工程质量评定报告是评估工程质量的重要文件。
产品质量证明书及出厂检验报告

产品质量证明书及出厂检验报告英文回答:Certificate of Product Quality and Factory Inspection Report。
As the manufacturer of your high-quality products, we take great pride in ensuring that every item meets our stringent quality standards. To provide you with peace of mind, we are pleased to offer the following documentation:Certificate of Product Quality verifies that your products have been rigorously tested and meet or exceed industry specifications. Our quality control team conducts thorough inspections throughout the manufacturing process, from raw materials to finished goods. This certificate serves as a guarantee of the product's quality and performance.Factory Inspection Report provides a detailed accountof the inspection process conducted at our manufacturing facility. This report includes observations made by our independent inspectors, who assess our production processes, equipment, and quality control systems. It also verifiesour compliance with industry regulations and environmental standards.These documents provide irrefutable evidence of the exceptional quality of our products and our commitment to customer satisfaction. By providing you with this documentation, we hope to foster confidence in our brandand strengthen our partnership.中文回答:产品质量证明书及出厂检验报告。
品质报告总结英语范文

IntroductionThis quality report aims to provide a comprehensive summary of the performance and outcomes of our recent quality assurance initiatives. The report covers various aspects, including product quality, process efficiency, customer satisfaction, and compliance with regulatory standards. By analyzing these key areas, we aim to identify strengths, areas for improvement, and strategies for continuous enhancement.Product QualityOur products have consistently met or exceeded the established quality standards. The following highlights the key findings:- Material Quality: The raw materials used in the production process were of high quality, ensuring the durability and reliability of our products.- Manufacturing Process: The manufacturing process was optimized to minimize defects and ensure consistent quality across all units.- Final Product Inspection: Our rigorous quality control measures resulted in a defect rate of less than 1%, which is significantly lower than the industry average.Process EfficiencyEfficiency is a critical factor in maintaining high-quality standards. The following points highlight our process efficiency:- Automation: The introduction of automated systems has reduced the likelihood of human error and improved production speed.- Supply Chain Management: Streamlined supply chain processes have minimized lead times and reduced costs.- Continuous Improvement: Regular process audits and feedback loops have enabled us to identify bottlenecks and implement corrective actions promptly.Customer SatisfactionCustomer satisfaction is a top priority for our organization. The following data reflects the level of customer satisfaction:- Feedback Scores: Our customers have given us an average feedback score of 4.5 out of 5, indicating high levels of satisfaction.- Repeat Business: A significant percentage of our customers have returned for repeat purchases, which underscores the quality andreliability of our products.- Service Quality: Our customer service team has received positive feedback for their responsiveness and helpfulness.Compliance with Regulatory StandardsCompliance with regulatory standards is non-negotiable. The following highlights our compliance status:- Regulatory Audits: We have successfully passed all regulatory audits conducted by external agencies, including ISO 9001, ISO 14001, and OHSAS 18001.- Documented Processes: Our quality management system is well-documented, ensuring that all processes are in line with regulatory requirements.- Employee Training: Regular training sessions have been conducted to ensure that our employees are aware of and adhere to all relevant regulations.Areas for ImprovementDespite the achievements mentioned above, there are still areas where we can improve:- Product Development: Enhancing the design and functionality of our products to meet the evolving needs of the market.- Employee Training: Providing further training to employees to ensure they are up-to-date with the latest quality standards and best practices.- Market Research: Conducting more extensive market research to identify potential areas of improvement and new market opportunities.ConclusionIn conclusion, our quality report highlights a strong performance across various dimensions, including product quality, process efficiency, customer satisfaction, and compliance with regulatory standards. However, we remain committed to continuous improvement and are actively workingon addressing the identified areas for enhancement. By doing so, we aim to maintain our position as a leading provider of high-quality products and services in the industry.。
Quality_reviw_质量报告
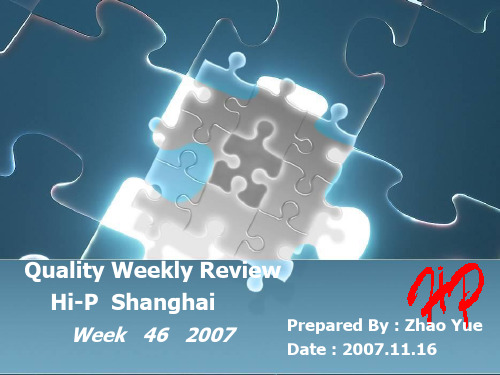
W37
W38
W39
W40
W41
LAR%
W42
Target%
W43
W44
W45
W46
Customer Quality Report
Hi-P (ShangHai) Technology
Customer LAR Breakdown(by Customer)
Week
Shipping Lots
Reject Lots LAR
Hi-P (ShangHai) Technology
Prepared By : Ye Xiang Date : 2007.11.15
Customer Quality Report
Hi-P (ShangHai) Technology
Week Shipping Lots Reject Lots
LAR Target
Return qty 700
0
63
0
2407
0
436
0
OT
FY
HS
0
31980
0
0
0
0
DPPM
5025
0
177
0
6168
0
206
0
0
0
0
Target
2800
2800
2800
2800 2800
2800
2800
2800
2800
2800 2800
6000 4000 2000
0
MT
ZT
HW
SM
PA
NK
RM
DPPM
Target
MT
10
0 100% 99.5%
质量分析报告单英文

质量分析报告单英文Quality Analysis Report FormProject Name:Date:Project Description:Section 1: Overall Quality Analysis1.1 Total Testing EffortThe total testing effort for the project was measured in terms of person-hours. A total of [X] person-hours were spent on testing activities, including test planning, test case design, test execution, and defect management.1.2 Test CoverageThe test coverage for the project was measured in terms of requirements coverage and code coverage. The requirements coverage was [X]%, indicating that [X]% of the project requirements were tested. The code coverage was [X]%, indicating that [X]% of the project code was exercised during testing.1.3 Defect DensityThe defect density for the project was calculated by dividing the total number of defects found duringtesting by the size of the project in terms of lines of code. The defect density was [X] defects per thousand lines of code, indicating the quality of the code base.Section 2: Test Execution Results2.1 Test Cases ExecutionA total of [X] test cases were executed during the testing phase. Out of these, [X] test cases passed without any issues, [X] test cases failed with defects, and [X] test cases were blocked due to test environment issues.2.2 Defect ManagementDuring the testing phase, a total of [X] defects were identified. Out of these, [X] defects were classified as critical, [X] defects as major, and [X] defects as minor. The defects were prioritized and assigned to development teams for resolution. The defect resolution rate was [X]%, indicating the effectiveness of defect management.Section 3: Test Performance3.1 Test EfficiencyThe test efficiency was measured by dividing the number of test cases executed by the total testing effort in person-hours. The test efficiency for theproject was [X] test cases per person-hour, indicating the productivity of the testing team.3.2 Test EffectivenessThe test effectiveness was measured by dividing the number of defects found during testing by the number of test cases executed. The test effectiveness for the project was [X] defects per test case, indicating the thoroughness of the testing activities.Section 4: Test Environment4.1 Test Environment SetupThe test environment was set up according to the project requirements, ensuring that all required hardware, software, and configuration settings were in place.4.2 Test Data ManagementThe test data for the project was managed effectively, ensuring that relevant and diverse data sets were available for testing. Data privacy and security measures were implemented to protect sensitive information.Section 5: Recommendations5.1 Test Process ImprovementBased on the quality analysis results, it is recommended to review and improve the test processfor future projects. This may include enhancing the test planning phase, improving test case design techniques, and implementing a more robust defect management process.5.2 Test AutomationConsidering the size and complexity of the project, it is recommended to explore test automation opportunities to improve overall testing efficiency and effectiveness. The automation of repetitive and complex test cases can reduce the testing effort while increasing test coverage.5.3 Test Environment EnhancementTo ensure better test execution and accuracy, it is recommended to enhance the test environment by upgrading hardware and software components, improving network connectivity, and addressing any identified issues with the test environment setup.Section 6: ConclusionOverall, the quality analysis results indicate the effectiveness of the testing activities conducted for the project. The identified defects were managed and resolved in a timely manner, ensuring the delivery of a high-quality product. Recommendations for process improvement, test automation, and test environmentenhancement will further enhance the testing capabilities for future projects.Prepared by:Reviewed by:Approved by:。
QC Report
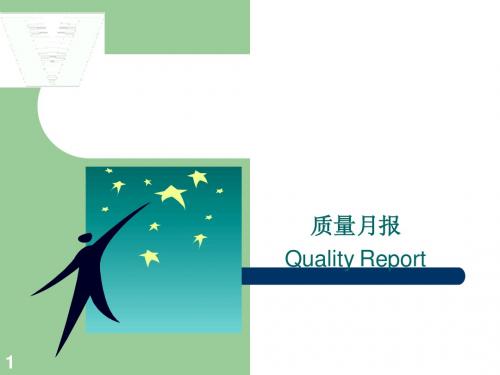
GT
W ith in O v er a ll
P o te n tia l C C C C C (W ith in ) C a p a b ility p * PL 0.4 4 PU * pk 0.4 4 C pk 0.4 4
O v e ra ll C a p a b ility Pp PPL PPU P pk C pm * 0.4 4 * 0.4 4 *
O v e ra ll P e rf o rm a n ce ?< ?LS L * ?> ?U S L 2 1 3 3 1 8 .1 3 ?T o ta l 2 1 3 3 1 8 .1 3
12
比华集团(金山厂) 比华集团(金山厂) VIVA Group (Jinshan)
制程能力分析 Capability Analysis
18
比华集团(金山厂) 比华集团(金山厂) VIVA Group (Jinshan)
以往质量改善的追踪 Ameliorate Pursue 一,上次会议的追踪(见质量会议待办事项) 1,掉粉问题 .螺旋灯未有效改善.环灯有改善 但带来光通量下降的问题.(暂未完全证实光通 量的下降与此有关 2,光参数的不符合,未有效改善 二,质保课反馈事项的整改 1,反馈的环灯和螺旋灯的掉粉问题有所改善, 目前在实验中.
19
比华集团(金山厂) 比华集团(金山厂) VIVA Group (Jinshan)
5
比华集团(金山厂) 比华集团(金山厂) VIVA Group (Jinshan)
质量状况报告 Quality Status Report
二,制程 1,灯管 (1)本月共生产SP灯管74129只,成品率 79.13%.环灯成品7988,成品率65.1%. (2)各制程品质状况见图表
供应商品质要求合约
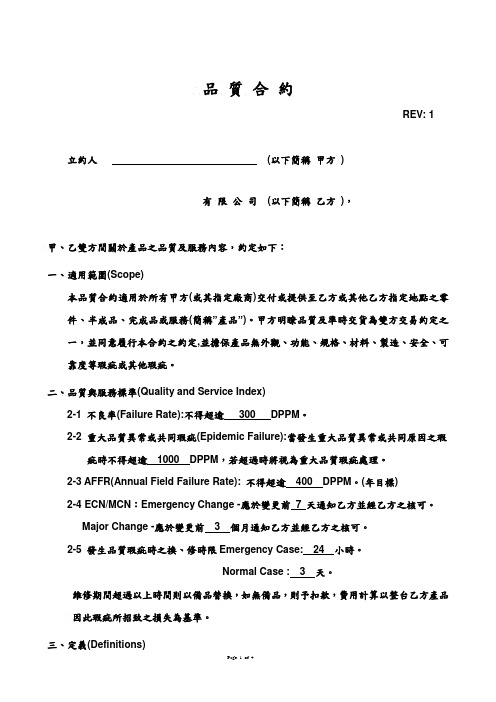
品質合約REV: 1 立約人(以下簡稱甲方)有限公司(以下簡稱乙方),甲、乙雙方間關於產品之品質及服務內容,約定如下:一、適用範圍(Scope)本品質合約適用於所有甲方(或其指定廠商)交付或提供至乙方或其他乙方指定地點之零件、半成品、完成品或服務(簡稱”產品”)。
甲方明瞭品質及準時交貨為雙方交易約定之一,並同意履行本合約之約定,並擔保產品無外觀、功能、規格、材料、製造、安全、可靠度等瑕疵或其他瑕疵。
二、品質與服務標準(Quality and Service Index)2-1 不良率(Failure Rate):不得超逾300 DPPM。
2-2 重大品質異常或共同瑕疵(Epidemic Failure):當發生重大品質異常或共同原因之瑕疵時不得超逾1000 DPPM,若超過時將視為重大品質瑕疵處理。
2-3 AFFR(Annual Field Failure Rate): 不得超逾400 DPPM。
(年目標)2-4 ECN/MCN:Emergency Change -應於變更前7 天通知乙方並經乙方之核可。
Major Change -應於變更前 3 個月通知乙方並經乙方之核可。
2-5 發生品質瑕疵時之換、修時限Emergency Case: 24 小時。
Normal Case : 3 天。
維修期間超過以上時間則以備品替換,如無備品,則予扣款,費用計算以整台乙方產品因此瑕疵所招致之損失為基準。
三、定義(Definitions)3-1 DPPM:指產品(零件)瑕疵數量/每百萬。
3-2 不良率(Failure Rate):指在乙方或乙方其他指定地點發現產品有外觀上或功能上之損壞、瑕疵。
3-3重大品質異常或共同瑕疵(Epidemic Failure):指產品發生相同性原因之瑕疵,瑕疵率超逾2-2所定比例者。
3-4 AFFR(Annual Field Failure Rate):指在乙方指定區域(Fields)內所發現之產品瑕疵損壞比例(採累計式)。
品质指标名词解释.
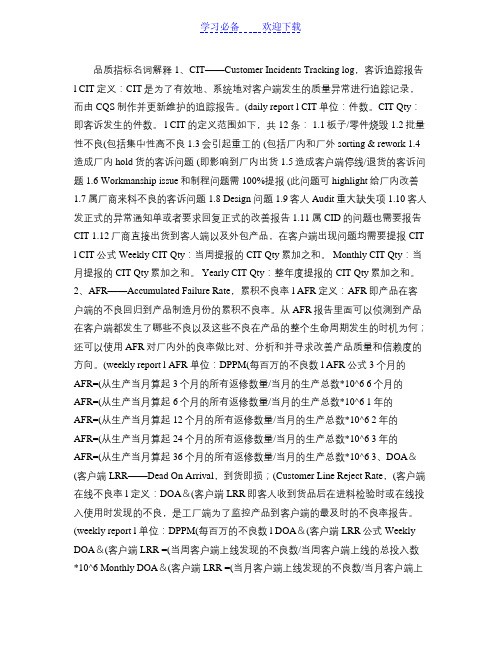
品质指标名词解释 1、CIT——Customer Incidents Tracking log,客诉追踪报告l CIT定义:CIT是为了有效地、系统地对客户端发生的质量异常进行追踪记录,而由CQS制作并更新维护的追踪报告。
(daily report l CIT单位:件数。
CIT Qty:即客诉发生的件数。
l CIT的定义范围如下,共12条: 1.1板子/零件烧毁 1.2批量性不良(包括集中性高不良 1.3会引起重工的 (包括厂内和厂外sorting & rework 1.4造成厂内hold货的客诉问题 (即影响到厂内出货 1.5造成客户端停线/退货的客诉问题 1.6 Workmanship issue和制程问题需100%提报 (此问题可highlight给厂内改善1.7属厂商来料不良的客诉问题 1.8 Design 问题 1.9客人Audit重大缺失项 1.10客人发正式的异常通知单或者要求回复正式的改善报告 1.11属CID的问题也需要报告CIT 1.12厂商直接出货到客人端以及外包产品,在客户端出现问题均需要提报CIT l CIT公式 Weekly CIT Qty:当周提报的CIT Qty累加之和。
Monthly CIT Qty:当月提报的CIT Qty累加之和。
Yearly CIT Qty:整年度提报的CIT Qty累加之和。
2、AFR——Accumulated Failure Rate,累积不良率 l AFR定义:AFR即产品在客户端的不良回归到产品制造月份的累积不良率。
从AFR报告里面可以侦测到产品在客户端都发生了哪些不良以及这些不良在产品的整个生命周期发生的时机为何;还可以使用AFR对厂内外的良率做比对、分析和并寻求改善产品质量和信赖度的方向。
(weekly report l AFR 单位:DPPM(每百万的不良数 l AFR公式 3个月的AFR=(从生产当月算起3个月的所有返修数量/当月的生产总数*10^6 6个月的AFR=(从生产当月算起6个月的所有返修数量/当月的生产总数*10^6 1年的AFR=(从生产当月算起12个月的所有返修数量/当月的生产总数*10^6 2年的AFR=(从生产当月算起24个月的所有返修数量/当月的生产总数*10^6 3年的AFR=(从生产当月算起36个月的所有返修数量/当月的生产总数*10^6 3、DOA&(客户端LRR——Dead On Arrival,到货即损;(Customer Line Reject Rate,(客户端在线不良率 l 定义:DOA&(客户端LRR即客人收到货品后在进料检验时或在线投入使用时发现的不良,是工厂端为了监控产品到客户端的最及时的不良率报告。
- 1、下载文档前请自行甄别文档内容的完整性,平台不提供额外的编辑、内容补充、找答案等附加服务。
- 2、"仅部分预览"的文档,不可在线预览部分如存在完整性等问题,可反馈申请退款(可完整预览的文档不适用该条件!)。
- 3、如文档侵犯您的权益,请联系客服反馈,我们会尽快为您处理(人工客服工作时间:9:00-18:30)。
劉逸鴻
熊曉強 熊曉強
唐鐳
2004/12/10
2004/11/10 2004/12/10 2004/12/10
open
close open open
Defect Description
Initial Test 14
1 3 3 1 3 1
1 1 1 1 1
Corrective Actions--Please Separate Short and Long Term Actions
12 DP00*5
13 ME08 14 ME08 15 CO03 16 BP02 17 DP00 18 DP00 19 DP00 20 DP00 21 CO01 22 US01 23 DP00 24 DP00 25 PW00 26 DP12 27
CH11 PIN脚插弯 U8空焊 U8空焊
CN22 PIN脚插弯 误判 误判
D30坏件 U32坏件 D30坏件
误判 CN502 短路
Final Assembly Data
Item 1 2 3 4 5 6 7
DP00 PW00 ME08 CO03 SY00 CO01 HD01
CB01 BP02 US01 DP12 留样
Yield 91.0%
ID No.
AH4BMC0019E AH4BMC001ZK AH4BMC007KW AH4BMC00274 AH4BMC002LX AH4BMC001SM AH4BMC00BNH AH4BMC001X1 AH4BMC004V8 AH4BMC00M0W AH4BMC00L8V
Root Cause
11/11
Item 11/11
1 2 3 4 5 6 7 8 9 10 11
Quantity Inspected 346
Description CO01 SY00 CO01 HD01 CB01 ME08 CO03 DP00 CO03 DP00 DP00
PC92 Sub-Assembly Data
Quantity Defective 31
AH4BMC001N9 AH4BMC0075S AH4BMC0078M AH4BMC0066T AH4BMC0052G
U26壞件(第一次開機作業員不正常關機 造成51CODE資料丟失)
1.要求作業員看電流完全掉下來後再關機 2.下Build時先烘烤smc(24小時)後再使用 3.請RD分析
AH4BMC007BE CN4001位移(GSM吸著位置不對造成) 從新做 Feeder Teach
AH4BMC00ADG CN6001位移(手擺件放位不對)
加強對作業員的教育訓練,下Build改為袋裝入料,改用機器著裝
AH4BMC00496 U8空焊(印刷下錫不良)
修改鋼板(現用0.15 下Build後會該0.13)
AH4BMC0001X U5201壞件
AH4BMC0066T U26壞件
AH4BMC00W30 U26壞件
AH4BMC00N40 U26壞件
AH4BMC00N74 R671撞件
AH4BMC00MHK U9空焊
AH4BMC00M85 PE在分析中
AH4BMC00KZ3 PE在分析中
AH4BMC00MN9 PE在分析中
AH4BMC000R4 PE在分析中
AH4BMC006HT PE在分析中
AH4BMC0008V 留樣
Run-InDateFra bibliotekTotal
Owner
Due Date Close Date
Status
Prority
Quantity built before Short or Long Term Corrective Actions Implemented
AOI cover
ICT cover S/A COVER