蜗杆传动的强度计算
蜗杆传动的强度计算、效率、润滑和热平衡计算
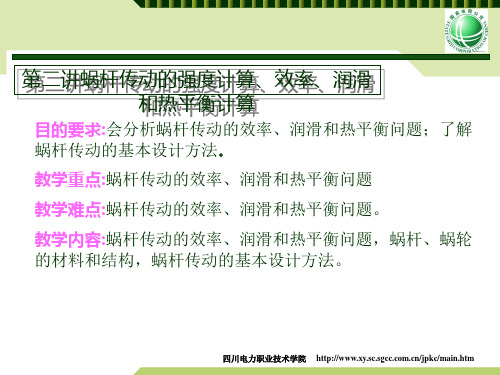
四川电力职业技术学院
/jpkc/main.htm
2.蜗轮结构
整体式:直径较小(小于100mm)的青铜蜗轮或铸铁蜗轮 组合式:直径较大(大于100mm)的青铜蜗轮,齿圈用青 铜,而轮齿用价格较低的铸铁或钢制造 。(三种 情况) (1) 压配式 齿圈和轮芯用过盈配合联接
四川电力职业技术学院
ห้องสมุดไป่ตู้
/jpkc/main.htm
一、蜗杆传动的强度计算 1.蜗杆传动的受力分析
四川电力职业技术学院
/jpkc/main.htm
Ft1 Fa 2 Fa1 Ft 2 T2 T1i1
2T1 d1 2T2 d2
Fr1 Fr 2 Ft 2tg
式中 T1 、T2——蜗杆、蜗轮传递的转矩(N· mm); d1、 d2——蜗杆、蜗轮分度圆直径(mm) α ——蜗杆轴面压力角(°); η1 ——传动效率。
四川电力职业技术学院
/jpkc/main.htm
(2) 螺栓联接式 (3) 镶铸式
四川电力职业技术学院
/jpkc/main.htm
(1)整体式
(2)压配式
(3)螺纹联接式
(4)镶铸式
四川电力职业技术学院
/jpkc/main.htm
2、蜗杆、蜗轮所受各力方向的判定: (1) 圆周力Ft的方向: 主动件的圆周力方向与 其啮合点的速度方向相反;从动件的圆周力方向 与其啮合点的速度方向相同。 (2) 径向力Fr的方向:由啮合点沿径向指向各 自的轮心。 (3) 轴向力Fa的方向: 当蜗杆为主动件时,仍 可用“主动轮左(右)手定则”判定蜗杆的轴向 力方向:用右手四指沿右旋蜗杆(左旋用左手) 转动方向环绕,则大拇指的指向即为蜗杆轴向力 Fa1的方向。从动蜗轮所受的轴向力与蜗杆圆周 力方向相反。
机械设计基础-蜗杆传动的强度计算
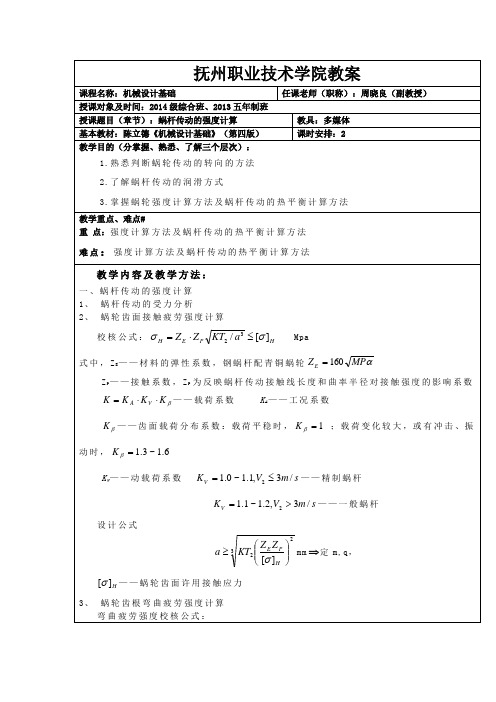
润滑油量适当浸油深度 ;
1/3蜗轮外径——上置式蜗杆,润滑较差,但搅油损失小
i个蜗杆齿高——下(侧)置式蜗杆,润滑较好,但搅油损失大
3、蜗杆传动热平衡计算
蜗杆传动效率较低,摩擦发热较大,温升较高,过高的温度使润滑油稀释,粘度下降,啮合时从齿面间被稀释,会加剧磨损和胶合。所以蜗杆传动设计要进行热平衡计算。
教学后记:
教研室主任意见:
教学方法:采用多媒体教学(动画演示运动),结合教具,提高学生的学习兴趣。
课程作业或思考题:
1、蜗杆传动的润滑方法?2、蜗杆传动的涡轮转动方向的判断方式?3、蜗杆传动为什么要进行热平衡计算?
参考资料或常用网址:韩玉成.机械设计基础.北京.电子工业出版社;庄宿涛.成都.西南交通大学出版社;徐刚涛.北京.高等教育出版社;http//
抚州职业技术学院教案
课程名称:机械设计基础
任课老师(职称):周晓良(副教授)
授课对象及时间:2014级综合班、2013五年制班
授课题目(章节):蜗杆传动的强度计算
教具:多媒体
基本教材:陈立德《机械设计基础》(第四版)
课时安排:2
教学目的(分掌握、熟悉、了解三个层次):
1.熟悉判断蜗轮传动的转向的方影响系数
——载荷系数KA——工况系数
——齿面载荷分布系数:载荷平稳时, ;载荷变化较大,或有冲击、振动时,
KV——动载荷系数 ——精制蜗杆
——一般蜗杆
设计公式
mm 定m,q,
——蜗轮齿面许用接触应力
3、蜗轮齿根弯曲疲劳强度计算
弯曲疲劳强度校核公式:
2.了解蜗杆传动的润滑方式
3.掌握蜗轮强度计算方法及蜗杆传动的热平衡计算方法
蜗轮蜗杆扭矩计算公式
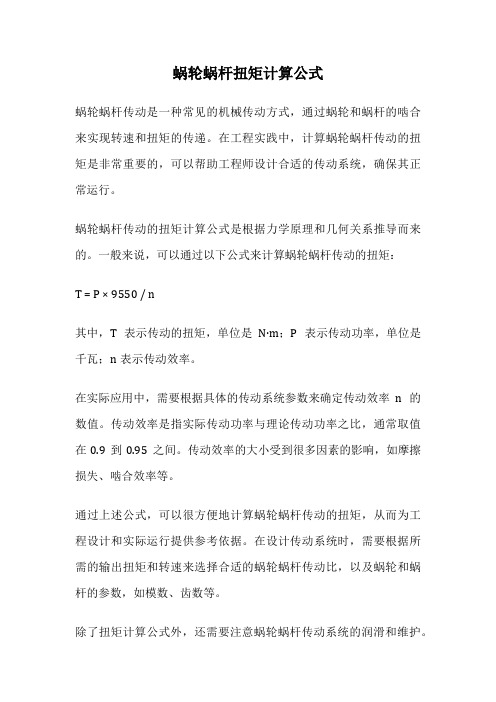
蜗轮蜗杆扭矩计算公式
蜗轮蜗杆传动是一种常见的机械传动方式,通过蜗轮和蜗杆的啮合来实现转速和扭矩的传递。
在工程实践中,计算蜗轮蜗杆传动的扭矩是非常重要的,可以帮助工程师设计合适的传动系统,确保其正常运行。
蜗轮蜗杆传动的扭矩计算公式是根据力学原理和几何关系推导而来的。
一般来说,可以通过以下公式来计算蜗轮蜗杆传动的扭矩:
T = P × 9550 / n
其中,T表示传动的扭矩,单位是N·m;P表示传动功率,单位是千瓦;n表示传动效率。
在实际应用中,需要根据具体的传动系统参数来确定传动效率n的数值。
传动效率是指实际传动功率与理论传动功率之比,通常取值在0.9到0.95之间。
传动效率的大小受到很多因素的影响,如摩擦损失、啮合效率等。
通过上述公式,可以很方便地计算蜗轮蜗杆传动的扭矩,从而为工程设计和实际运行提供参考依据。
在设计传动系统时,需要根据所需的输出扭矩和转速来选择合适的蜗轮蜗杆传动比,以及蜗轮和蜗杆的参数,如模数、齿数等。
除了扭矩计算公式外,还需要注意蜗轮蜗杆传动系统的润滑和维护。
良好的润滑可以减小传动系统的摩擦损失,提高传动效率,延长传动件的使用寿命。
定期检查传动系统的工作状态,及时更换磨损严重的传动件,可以保证传动系统的正常运行。
总的来说,蜗轮蜗杆传动扭矩的计算是工程设计和运行中的重要一环,只有合理计算和选择扭矩,才能确保传动系统的安全可靠性。
在实际应用中,需要结合具体情况进行计算和设计,以获得最佳的传动效果。
蜗杆计算公式教程
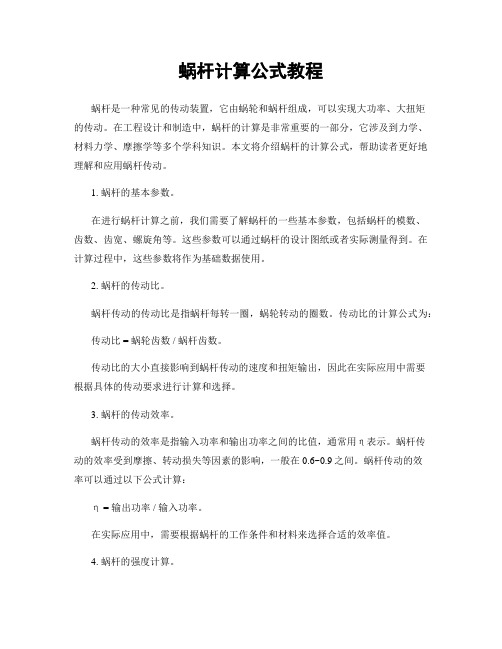
蜗杆计算公式教程蜗杆是一种常见的传动装置,它由蜗轮和蜗杆组成,可以实现大功率、大扭矩的传动。
在工程设计和制造中,蜗杆的计算是非常重要的一部分,它涉及到力学、材料力学、摩擦学等多个学科知识。
本文将介绍蜗杆的计算公式,帮助读者更好地理解和应用蜗杆传动。
1. 蜗杆的基本参数。
在进行蜗杆计算之前,我们需要了解蜗杆的一些基本参数,包括蜗杆的模数、齿数、齿宽、螺旋角等。
这些参数可以通过蜗杆的设计图纸或者实际测量得到。
在计算过程中,这些参数将作为基础数据使用。
2. 蜗杆的传动比。
蜗杆传动的传动比是指蜗杆每转一圈,蜗轮转动的圈数。
传动比的计算公式为:传动比 = 蜗轮齿数 / 蜗杆齿数。
传动比的大小直接影响到蜗杆传动的速度和扭矩输出,因此在实际应用中需要根据具体的传动要求进行计算和选择。
3. 蜗杆的传动效率。
蜗杆传动的效率是指输入功率和输出功率之间的比值,通常用η表示。
蜗杆传动的效率受到摩擦、转动损失等因素的影响,一般在0.6~0.9之间。
蜗杆传动的效率可以通过以下公式计算:η = 输出功率 / 输入功率。
在实际应用中,需要根据蜗杆的工作条件和材料来选择合适的效率值。
4. 蜗杆的强度计算。
蜗杆的强度计算是蜗杆设计中最重要的一部分,它涉及到蜗杆的受力分析、材料力学等知识。
蜗杆的强度可以通过以下公式进行计算:蜗杆的齿面接触应力σH = (2T) / (πdLb)。
其中,T为蜗杆的扭矩,d为蜗杆的分度圆直径,Lb为蜗杆的齿宽。
蜗杆的齿面接触应力必须小于蜗杆材料的许用应力,否则会导致蜗杆的断裂。
此外,蜗杆的齿根弯曲应力、蜗杆的齿面弯曲应力等也需要进行计算和分析,以保证蜗杆在工作时不会发生破坏。
5. 蜗杆的热量计算。
蜗杆传动在工作时会产生一定的摩擦热量,因此需要进行热量计算,以确定蜗杆的冷却方式和散热能力。
蜗杆的热量计算可以通过以下公式进行:Q = (τμ) / (2πn)。
其中,Q为单位时间内的摩擦热量,τ为摩擦力矩,μ为摩擦系数,n为转速。
机械设计基础自测题-第六章概念
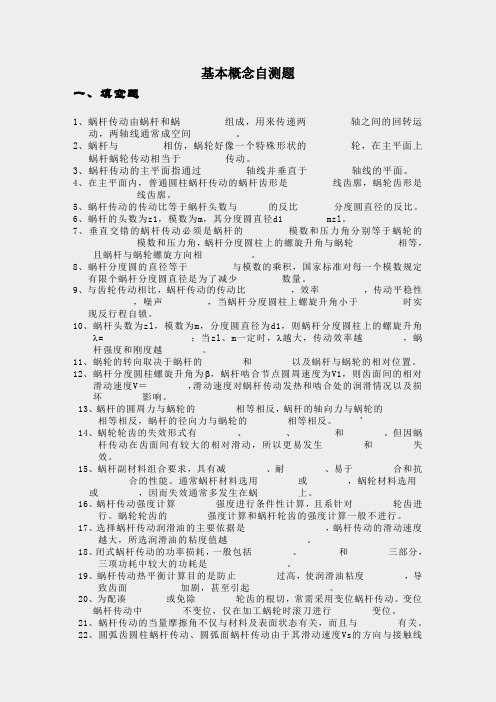
基本概念自测题一、填空题1、蜗杆传动由蜗杆和蜗__________组成,用来传递两__________轴之间的回转运动,两轴线通常成空间__________。
2、蜗杆与__________相仿,蜗轮好像一个特殊形状的__________轮,在主平面上蜗杆蜗轮传动相当于__________传动。
3、蜗杆传动的主平面指通过__________轴线并垂直于__________轴线的平面。
4、在主平面内,普通圆柱蜗杆传动的蜗杆齿形是__________线齿廓,蜗轮齿形是__________线齿廓。
5、蜗杆传动的传动比等于蜗杆头数与_______的反比________分度圆直径的反比。
6、蜗杆的头数为z1,模数为m,其分度圆直径d1__________mzl。
7、垂直交错的蜗杆传动必须是蜗杆的__________模数和压力角分别等于蜗轮的__________模数和压力角,蜗杆分度圆柱上的螺旋升角与蜗轮__________相等,且蜗杆与蜗轮螺旋方向相___________。
8、蜗杆分度圆的直径等于__________与模数的乘积,国家标准对每一个模数规定有限个蜗杆分度圆直径是为了减少__________数量。
9、与齿轮传动相比,蜗杆传动的传动比__________,效率__________,传动平稳性__________,噪声__________,当蜗杆分度圆柱上螺旋升角小于__________时实现反行程自锁。
10、蜗杆头数为zl,模数为m,分度圆直径为d1,则蜗杆分度圆柱上的螺旋升角λ=____________________;当zl、m一定时,λ越大,传动效率越_________,蜗杆强度和刚度越_________。
11、蜗轮的转向取决于蜗杆的_________和_________以及蜗杆与蜗轮的相对位置。
12、蜗杆分度圆柱螺旋升角为β,蜗杆啮合节点圆周速度为V1,则齿面间的相对滑动速度V=_________,滑动速度对蜗杆传动发热和啮合处的润滑情况以及损坏_________影响。
单位内部认证机械设计基础考试练习题及答案2_2023_背题版
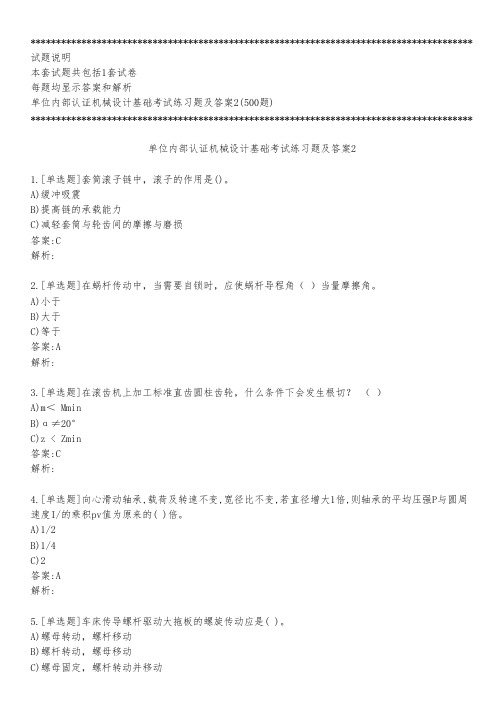
***************************************************************************************试题说明本套试题共包括1套试卷每题均显示答案和解析单位内部认证机械设计基础考试练习题及答案2(500题)***************************************************************************************单位内部认证机械设计基础考试练习题及答案21.[单选题]套筒滚子链中,滚子的作用是()。
A)缓冲吸震B)提高链的承载能力C)减轻套筒与轮齿间的摩擦与磨损答案:C解析:2.[单选题]在蜗杆传动中,当需要自锁时,应使蜗杆导程角( )当量摩擦角。
A)小于B)大于C)等于答案:A解析:3.[单选题]在滚齿机上加工标准直齿圆柱齿轮,什么条件下会发生根切? ( )A)m< MminB)α≠20°C)z < Zmin答案:C解析:4.[单选题]向心滑动轴承,载荷及转速不变,宽径比不变,若直径增大1倍,则轴承的平均压强P与圆周速度I/的乘积pv值为原来的( )倍。
A)1/2B)1/4C)2答案:A解析:5.[单选题]车床传导螺杆驱动大拖板的螺旋传动应是( )。
A)螺母转动,螺杆移动6.[单选题]对带的疲劳强度影响较大的应力是( )。
A)紧边拉应力B)离心应力C)弯曲应力答案:C解析:7.[单选题]V带带轮材料一般选用( )。
A)碳钢调质B)合金钢C)铸铁答案:C解析:8.[单选题]毛坯是采用铸铁还是钢来制造,主要取决于()。
A)链条的线速度B)传递的圆周力C)链轮的转速答案:A解析:9.[单选题]钢是含碳量( )铁碳合金。
A)低于2%B)高于2%C)低于5%答案:A解析:10.[单选题]在单向间歇运动机构中,( )可以获得不同转向的间歇运动。
A)槽轮机构B)棘轮机构C)不完全齿轮机构答案:B解析:11.[单选题]( )键适于定心精度要求高、传递载荷大的轴、毂动或静联接。
蜗杆蜗轮强度计算
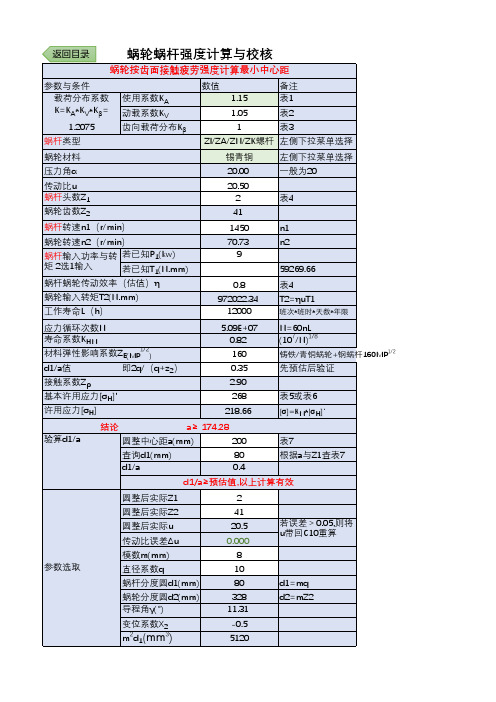
当N<105时,取N=105;
当N>25x107时,取N=25x107
器
油 泵
说明: 由于材料与结构原因,蜗杆螺旋齿部分强度总是高于蜗轮轮齿强度,所有
失效经常发生在蜗轮上,一般只校核计算蜗轮。 校核计算的一般顺序:按表预估传动效率η,预估d1/a,按齿面接触疲劳强
度计算最小中心距——按参数匹配表选取参数——验证d1/a与η——若不合理 则将计算值带回重算,直至d1/a与η验证合格——以齿根弯曲疲劳强度校核— —校核蜗杆刚度——热平衡核算。
m2d1(mm3)
2 41 20.5 0.000 8 10 80 328 11.31 -0.5 5120
若误差>0.05,则将 u带回C10重算
d1=mq d2=mZ2
验算效率
滑动速度Vs(m/s)
6.19
Vs=πd1n1/60000cosγ
当量摩擦角φv
1.1687
atan(fv)表8
传动效率η
文档信息 编写:图惜 参考:《机械设计——第八版》——蒲良贵、纪名刚
《机械设计手册——第五版第三卷》——成大先 2018.7.30
附录1 常用蜗杆材料
材料
15Cr/20Cr
热处理
渗碳淬火
硬度
≥45HRC
用途
40/45/40Cr 淬火 ≥45HRC 高速或重载
40/45 调质 200~300HBS 不重要的低速中载
备注
氮化处理后55~62HRC
附录1 常用蜗轮材料
材料
铸造锡青铜
耐磨性
好
价格
高
实用滑动速度Vs ≥3
用途
重要传动
抗胶合能力
强
抗点蚀能力
差
史上最好用机械计算与非标选型—蜗轮蜗杆强度计算与校核
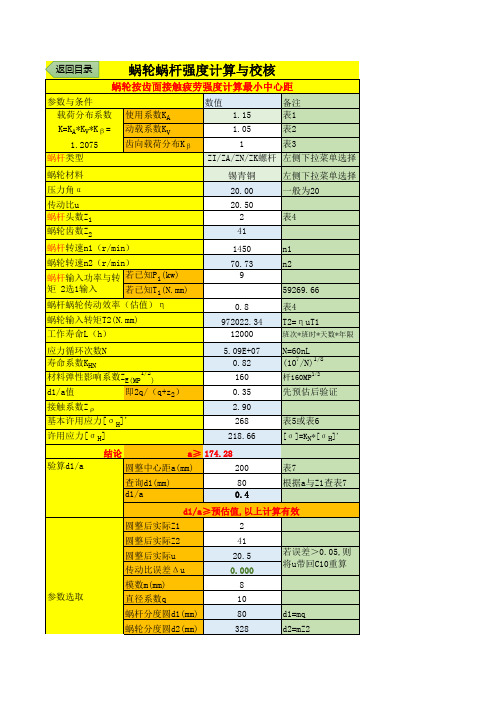
n1 n2
59269.66 表4 T2=ηuT1
班次*班时*天数*年限
应力循环次数N
寿命系数KHN 材料弹性影响系数ZE(MP1/2)
d1/a值
即2q/(q+z2)
接触系数Zρ
基本许用应力[σH]'
许用应力[σH]
5.09E+07 0.82 160 0.35 2.90 268 218.66
验算d1/a
蜗轮材料
铸造方法
单侧工作
双侧工作
铸锡青铜 砂型铸造
40
29
ZCuSn10P1 金属模铸造
56
40
铸锡锌铅青铜 砂型铸造
26
22
ZCuSnSPB5Zn5 金属模铸造
32
26
铸铝铁青铜 砂型铸造
80
57
ZCuAl10Fe3 金属模铸造
90
64
灰铸铁
HT150砂型铸造 40
28
HT200砂型铸造 48
34
返回目录
蜗轮蜗杆强度计算与校核
蜗轮按齿面接触疲劳强度计算最小中心距
参数与条件 载荷分布系数 K=KA*KV*Kβ= 1.2075
蜗杆类型
使用系数KA 动载系数KV 齿向载荷分布Kβ
数值 1.15
备注 表1
1.05
表2
1
表3
ZI/ZA/ZN/ZK螺杆 左侧下拉菜单选择
蜗轮材料
压力角α
传动比u 蜗杆头数Z1 蜗轮齿数Z2
均取206GPa I=πdf14/64 [y]=d1/1000
热平衡核算(闭式蜗轮蜗杆)
箱体表面传热系数αd=8.15~17.45
17.00
蜗轮蜗杆计算
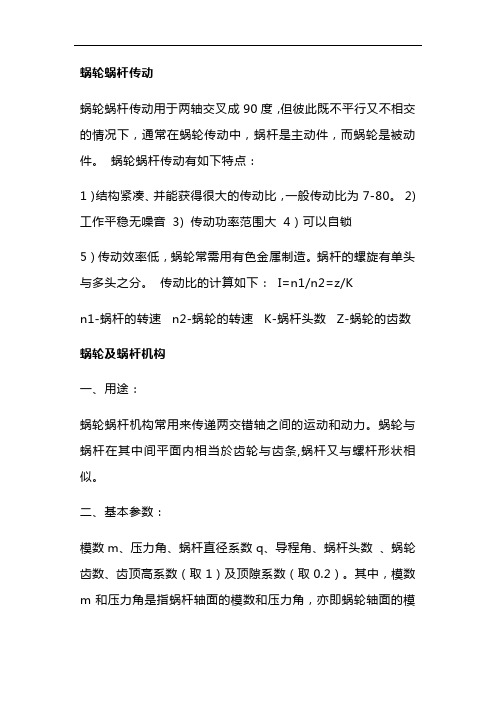
蜗轮蜗杆传动蜗轮蜗杆传动用于两轴交叉成90度,但彼此既不平行又不相交的情况下,通常在蜗轮传动中,蜗杆是主动件,而蜗轮是被动件。
蜗轮蜗杆传动有如下特点:1)结构紧凑、并能获得很大的传动比,一般传动比为7-80。
2) 工作平稳无噪音3) 传动功率范围大4)可以自锁5)传动效率低,蜗轮常需用有色金属制造。
蜗杆的螺旋有单头与多头之分。
传动比的计算如下:I=n1/n2=z/Kn1-蜗杆的转速 n2-蜗轮的转速 K-蜗杆头数 Z-蜗轮的齿数蜗轮及蜗杆机构一、用途:蜗轮蜗杆机构常用来传递两交错轴之间的运动和动力。
蜗轮与蜗杆在其中间平面内相当於齿轮与齿条,蜗杆又与螺杆形状相似。
二、基本参数:模数m、压力角、蜗杆直径系数q、导程角、蜗杆头数、蜗轮齿数、齿顶高系数(取1)及顶隙系数(取0.2)。
其中,模数m和压力角是指蜗杆轴面的模数和压力角,亦即蜗轮轴面的模数和压力角,且均为标准值;蜗杆直径系数q为蜗杆分度圆直径与其模数m的比值,三、蜗轮蜗杆正确啮合的条件1 中间平面内蜗杆与蜗轮的模数和压力角分别相等,即蜗轮的端面模数等於蜗杆的轴面模数且为标准值;蜗轮的端面压力角应等於蜗杆的轴面压力角且为标准值,即m2 当蜗轮蜗杆的交错角为时,还需保证,而且蜗轮与蜗杆螺旋线旋向必须相同。
四、几何尺寸计算与圆柱齿轮基本相同,需注意的几个问题是:蜗杆导程角()是蜗杆分度圆柱上螺旋线的切线与蜗杆端面之间的夹角,与螺杆螺旋角的关系为,蜗轮的螺旋角,大则传动效率高,当小於啮合齿间当量摩擦角时,机构自锁。
引入蜗杆直径系数q是为了限制蜗轮滚刀的数目,使蜗杆分度圆直径进行了标准化m一定时,q大则大,蜗杆轴的刚度及强度相应增大;一定时,q小则导程角增大,传动效率相应提高。
蜗杆头数推荐值为1、2、4、6,当取小值时,其传动比大,且具有自锁性;当取大值时,传动效率高。
与圆柱齿轮传动不同,蜗杆蜗轮机构传动比不等於,而是,蜗杆蜗轮机构的中心距不等於,而是。
蜗轮蜗杆的设计计算
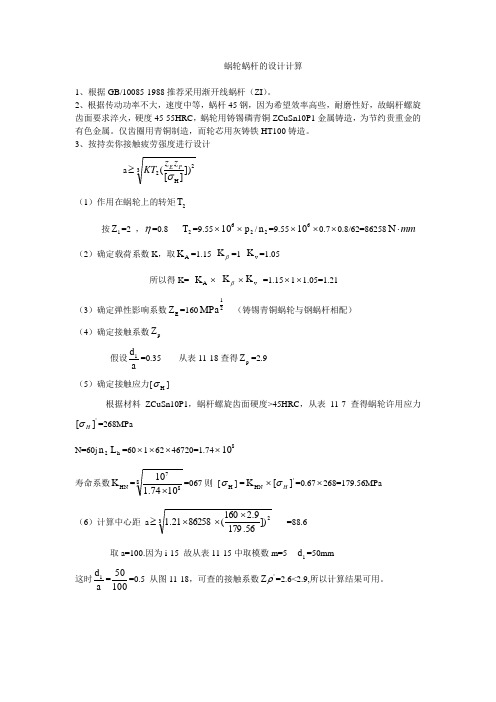
蜗轮蜗杆的设计计算1、根据GB/10085-1988推荐采用渐开线蜗杆(ZI )。
2、根据传动功率不大,速度中等,蜗杆45钢,因为希望效率高些,耐磨性好,故蜗杆螺旋 齿面要求淬火,硬度45-55HRC ,蜗轮用铸锡磷青铜ZCuSn10P1金属铸造,为节约贵重金的有色金属。
仅齿圈用青铜制造,而轮芯用灰铸铁HT100铸造。
3、按持卖你接触疲劳强度进行设计a ≥32H 2])][(σP E z z KT (1)作用在蜗轮上的转矩2T按1Z =2 ,η=0.8 2T =9.55⨯610⨯2p /2n =9.55⨯610⨯0.7⨯0.8/62=86258mm ⋅N(2)确定载荷系数K ,取A K =1.15 βK =1 v K =1.05所以得K= A K ⨯ βK ⨯v K =1.15⨯1⨯1.05=1.21(3)确定弹性影响系数E Z =16021MPa (铸锡青铜蜗轮与钢蜗杆相配)(4)确定接触系数p Z假设ad 1=0.35 从表11-18查得p Z =2.9 (5)确定接触应力[H σ]根据材料ZCuSn10P1,蜗杆螺旋齿面硬度>45HRC ,从表11-7查得蜗轮许用应力'][H σ=268MPaN=60j 2n h L =60⨯1⨯62⨯46720=1.74⨯810寿命系数HN K =8871074.110⨯=067则 [H σ] =HN K ⨯'][H σ=0.67⨯268=179.56MPa (6)计算中心距 a ≥32])56.1799.2160(8625821.1⨯⨯⨯ =88.6 取a=100.因为i-15 故从表11-15中取模数m=5 1d =50mm 这时a d 1=10050=0.5 从图11-18,可查的接触系数'Z ρ=2.6<2.9,所以计算结果可用。
4、蜗杆蜗轮的主要参数(1)蜗杆:轴向齿距Pa=15.7得直径系数q=10 齿顶园直径a1d =60,齿根圆f1d =38,分度圆导角r=11 18 36 ,蜗杆轴向齿厚Sa=5π/2=7.85mm(2)蜗轮齿数2Z =31 变位系数2x =-0.500 验算传动比i=2Z /1Z =31/2=15.5 误差为15155.15-=3.33%,在允许范围内,所以可行。
蜗杆与蜗轮主要参数及几何计算
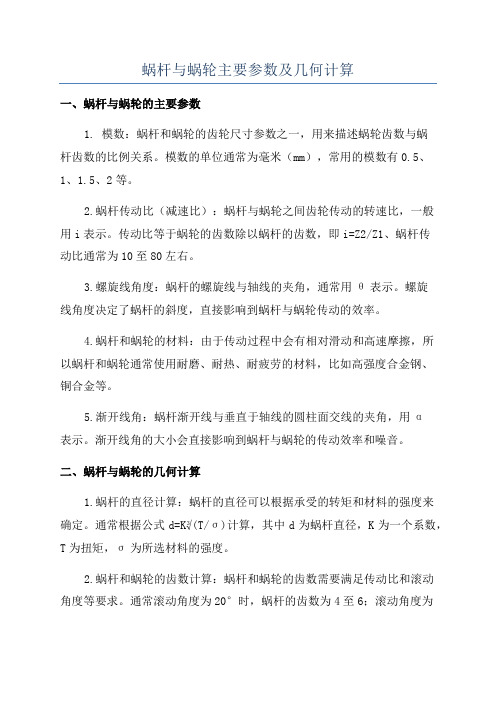
蜗杆与蜗轮主要参数及几何计算一、蜗杆与蜗轮的主要参数1. 模数:蜗杆和蜗轮的齿轮尺寸参数之一,用来描述蜗轮齿数与蜗杆齿数的比例关系。
模数的单位通常为毫米(mm),常用的模数有0.5、1、1.5、2等。
2.蜗杆传动比(减速比):蜗杆与蜗轮之间齿轮传动的转速比,一般用i表示。
传动比等于蜗轮的齿数除以蜗杆的齿数,即i=Z2/Z1、蜗杆传动比通常为10至80左右。
3.螺旋线角度:蜗杆的螺旋线与轴线的夹角,通常用θ表示。
螺旋线角度决定了蜗杆的斜度,直接影响到蜗杆与蜗轮传动的效率。
4.蜗杆和蜗轮的材料:由于传动过程中会有相对滑动和高速摩擦,所以蜗杆和蜗轮通常使用耐磨、耐热、耐疲劳的材料,比如高强度合金钢、铜合金等。
5.渐开线角:蜗杆渐开线与垂直于轴线的圆柱面交线的夹角,用α表示。
渐开线角的大小会直接影响到蜗杆与蜗轮的传动效率和噪音。
二、蜗杆与蜗轮的几何计算1.蜗杆的直径计算:蜗杆的直径可以根据承受的转矩和材料的强度来确定。
通常根据公式d=K∛(T/σ)计算,其中d为蜗杆直径,K为一个系数,T为扭矩,σ为所选材料的强度。
2.蜗杆和蜗轮的齿数计算:蜗杆和蜗轮的齿数需要满足传动比和滚动角度等要求。
通常滚动角度为20°时,蜗杆的齿数为4至6;滚动角度为15°时,蜗杆的齿数为6至9、齿数的具体计算可以根据所选的传动比和齿轮的模数来确定。
3. 蜗轮的直径计算:蜗轮的直径需要根据滚动角度和蜗杆直径来确定。
一般来说,蜗轮的直径大于或等于蜗杆的直径。
可以根据公式d2 =d1 + 2mcosα 计算,其中d2为蜗轮的直径,d1为蜗杆的直径,m为模数,α为渐开线角。
4.蜗杆传动比的计算:蜗杆传动比等于蜗轮的齿数除以蜗杆的齿数。
根据所选的传动比和蜗杆的齿数,可以计算出蜗轮的齿数。
以上是蜗杆与蜗轮的主要参数和几何计算的介绍,这些参数和计算方法的正确选择和应用,能够保证蜗杆与蜗轮传动的效率和可靠性。
在实际应用中,还需要考虑到摩擦和磨损等因素,选择适当的润滑方式和材料,以提高传动的效率和寿命。
蜗轮蜗杆传动承载能力计算(精选)
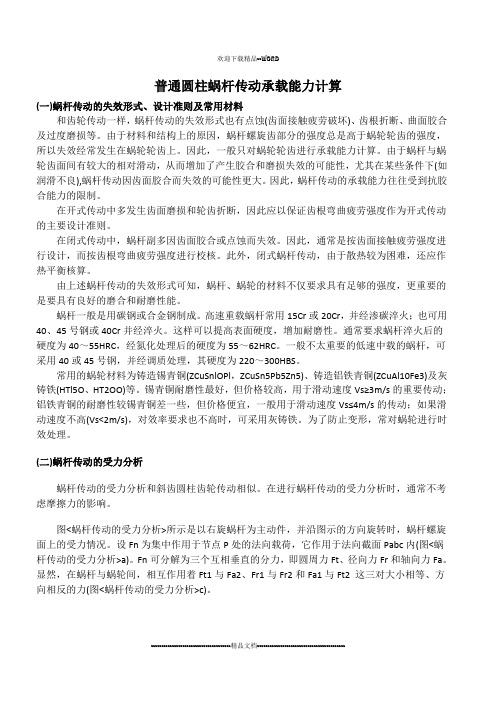
普通圆柱蜗杆传动承载能力计算(一)蜗杆传动的失效形式、设计准则及常用材料和齿轮传动一样,蜗杆传动的失效形式也有点蚀(齿面接触疲劳破坏)、齿根折断、曲面胶合及过度磨损等。
由于材料和结构上的原因,蜗杆螺旋齿部分的强度总是高于蜗轮轮齿的强度,所以失效经常发生在蜗轮轮齿上。
因此,一般只对蜗轮轮齿进行承载能力计算。
由于蜗杆与蜗轮齿面间有较大的相对滑动,从而增加了产生胶合和磨损失效的可能性,尤其在某些条件下(如润滑不良),蜗杆传动因齿面胶合而失效的可能性更大。
因此,蜗杆传动的承载能力往往受到抗胶合能力的限制。
在开式传动中多发生齿面磨损和轮齿折断,因此应以保证齿根弯曲疲劳强度作为开式传动的主要设计准则。
在闭式传动中,蜗杆副多因齿面胶合或点蚀而失效。
因此,通常是按齿面接触疲劳强度进行设计,而按齿根弯曲疲劳强度进行校核。
此外,闭式蜗杆传动,由于散热较为困难,还应作热平衡核算。
由上述蜗杆传动的失效形式可知,蜗杆、蜗轮的材料不仅要求具有足够的强度,更重要的是要具有良好的磨合和耐磨性能。
蜗杆一般是用碳钢或合金钢制成。
高速重载蜗杆常用15Cr或20Cr,并经渗碳淬火;也可用40、45号钢或40Cr并经淬火。
这样可以提高表面硬度,增加耐磨性。
通常要求蜗杆淬火后的硬度为40~55HRC,经氮化处理后的硬度为55~62HRC。
一般不太重要的低速中载的蜗杆,可采用40或45号钢,并经调质处理,其硬度为220~300HBS。
常用的蜗轮材料为铸造锡青铜(ZCuSnlOPl,ZCuSn5Pb5Zn5)、铸造铝铁青铜(ZCuAl10Fe3)及灰铸铁(HTl5O、HT2OO)等。
锡青铜耐磨性最好,但价格较高,用于滑动速度Vs≥3m/s的重要传动;铝铁青铜的耐磨性较锡青铜差一些,但价格便宜,一般用于滑动速度Vs≤4m/s的传动;如果滑动速度不高(Vs<2m/s),对效率要求也不高时,可采用灰铸铁。
为了防止变形,常对蜗轮进行时效处理。
(二)蜗杆传动的受力分析蜗杆传动的受力分析和斜齿圆柱齿轮传动相似。
塑料蜗杆蜗轮强度计算公式

塑料蜗杆蜗轮强度计算公式塑料蜗杆蜗轮是一种常见的传动装置,它由蜗杆和蜗轮两部分组成,通常用于工业设备和机械设备中。
在设计和制造塑料蜗杆蜗轮时,强度计算是非常重要的一环,它可以帮助工程师确定蜗杆蜗轮的承载能力和使用寿命,确保其在工作过程中不会出现断裂或变形等问题。
本文将介绍塑料蜗杆蜗轮强度计算的相关公式和方法。
塑料蜗杆蜗轮的强度计算公式主要包括静态强度计算和疲劳强度计算两部分。
静态强度计算是指在静止或稳态工况下,蜗杆蜗轮所能承受的最大载荷。
而疲劳强度计算则是指在动态工况下,蜗杆蜗轮所能承受的循环载荷和振动载荷。
下面将分别介绍这两部分的计算公式和方法。
首先是静态强度计算。
塑料蜗杆蜗轮的静态强度可以通过以下公式进行计算:σ = Pd / (b m Y)。
其中,σ为蜗杆蜗轮的应力,P为传动力,d为蜗杆蜗轮的分度圆直径,b为蜗杆蜗轮的宽度,m为模数,Y为弯曲强度系数。
在进行静态强度计算时,需要首先确定传动力P,然后根据蜗杆蜗轮的几何参数,计算出蜗杆蜗轮的应力σ。
在计算过程中,需要考虑蜗杆蜗轮的材料强度和几何形状对其强度的影响,以确保蜗杆蜗轮在正常工作条件下不会发生破坏。
其次是疲劳强度计算。
塑料蜗杆蜗轮在工作过程中会受到循环载荷和振动载荷的影响,因此需要进行疲劳强度计算,以确定蜗杆蜗轮的使用寿命。
疲劳强度可以通过下面的公式进行计算:S = (K σa^m) / (Nf Y)。
其中,S为疲劳强度,K为材料常数,σa为应力幅值,m为材料指数,Nf为循环次数,Y为表面质量系数。
在进行疲劳强度计算时,需要确定材料的疲劳参数K和m,然后根据应力幅值和循环次数,计算出蜗杆蜗轮的疲劳强度S。
通过疲劳强度计算,可以预测蜗杆蜗轮的使用寿命,并采取相应的措施,延长其使用寿命。
除了以上的强度计算公式外,还需要考虑蜗杆蜗轮的材料选择、表面处理和加工工艺等因素对其强度的影响。
在设计和制造塑料蜗杆蜗轮时,需要综合考虑这些因素,以确保蜗杆蜗轮具有足够的强度和使用寿命。
蜗杆蜗轮传动设计计算
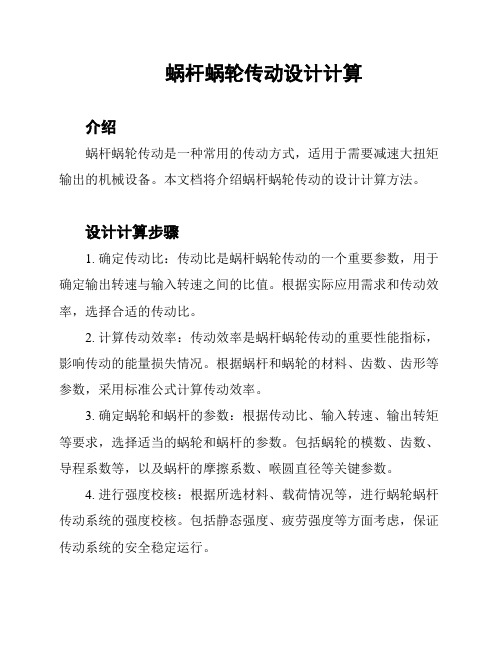
蜗杆蜗轮传动设计计算介绍蜗杆蜗轮传动是一种常用的传动方式,适用于需要减速大扭矩输出的机械设备。
本文档将介绍蜗杆蜗轮传动的设计计算方法。
设计计算步骤1. 确定传动比:传动比是蜗杆蜗轮传动的一个重要参数,用于确定输出转速与输入转速之间的比值。
根据实际应用需求和传动效率,选择合适的传动比。
2. 计算传动效率:传动效率是蜗杆蜗轮传动的重要性能指标,影响传动的能量损失情况。
根据蜗杆和蜗轮的材料、齿数、齿形等参数,采用标准公式计算传动效率。
3. 确定蜗轮和蜗杆的参数:根据传动比、输入转速、输出转矩等要求,选择适当的蜗轮和蜗杆的参数。
包括蜗轮的模数、齿数、导程系数等,以及蜗杆的摩擦系数、喉圆直径等关键参数。
4. 进行强度校核:根据所选材料、载荷情况等,进行蜗轮蜗杆传动系统的强度校核。
包括静态强度、疲劳强度等方面考虑,保证传动系统的安全稳定运行。
设计计算示例以一个减速器设计为例,输入转速为1000 rpm,输出扭矩为5000 Nm,要求传动比为10。
假设蜗杆材料为45号钢,蜗轮材料为ZCuSn10Pb1。
1. 计算传动效率:传动效率 = (传动比 x 蜗杆效率 x 蜗轮效率)/ 100%,根据实际参数计算传动效率为80%。
2. 确定蜗轮和蜗杆的参数:蜗轮模数 m = (输出扭矩 x 1000)/ (传动比 x 输入转速 x 齿数) = (5000 x 1000)/ (10 x 1000 x 100) = 5 mm;蜗杆摩擦系数μ = 0.1,喉圆直径 d = (输出扭矩 x 输入转速)/ ( x 传动比 x 齿数x μ) = (5000 x 1000)/ ( x 10 x 20 x 0.1) = 8 mm。
3. 进行强度校核:根据蜗杆和蜗轮的尺寸、材料强度等参数,进行静态强度和疲劳强度的校核。
确保蜗杆蜗轮传动系统的强度满足设计要求。
结论本文档介绍了蜗杆蜗轮传动的设计计算步骤,并以一个减速器设计为例进行了示例计算。
蜗杆传动的强度计算讲解
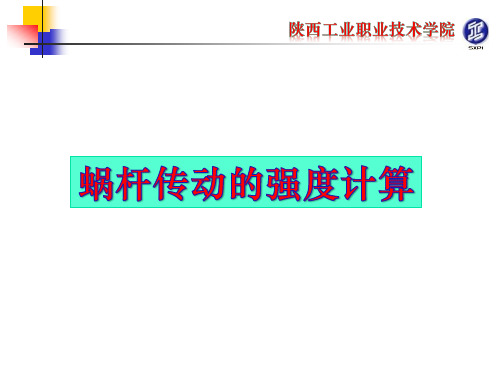
蜗杆齿面硬度 ≤45HRC
46(32) 58(42) 32(24) 41(32)
ZCuSn10Pb1
ZCuSn5Pb5Zn5
ZCuAl10Fe3 HT150
砂模 砂模
112(91) 40
蜗杆齿面硬度 >45HRC 磨光或抛光 58(40) 73(52) 40(30) 51(40) 140(116) 50
手,四指弯曲与主动轮转向一致,大拇
指伸直指向轴向力方向。
二、蜗轮齿面接触疲劳强度计算 近似按齿条与斜齿圆柱齿轮啮合传动计算 校核式 设计式
KT2 H 500 2 2 H m d1 z2
500 m d1 z KT2 2 H
2 2
“500”——钢对青铜,钢对铸铁
K 1.1 ~ 1.3
铸锡青铜蜗轮的许用接触应力/MPa
铸造 方法 滑动速度 [σH]
蜗轮材料
蜗杆齿面硬度 ≤350HBW 180 200
110 135
vs(m/s)
ZCuSn10Pb1 ZCuSn5Pb5 Zn5
>45HRC 200 220
125 150
砂模 金属模
砂模 金属模
≤12 ≤25
一、轮齿受力分析
作用点:节点C 大小:略去摩擦力
Ft1 2T1 d1 Fa 2 Fa1 Ft 2 2T2 d 2 Fr1 Fr 2 Ft 2 tg
方向判断:
主动轮Ft1与v1反向;从动轮Ft2与v2
同向;Fr 指向各自轮心; 主动轮Fa1:左旋用左手,右旋用右
90
75
钢经淬火
①
HT200,HT150
HT150
渗碳钢
调质或 淬火钢
蜗轮蜗杆传动承载能力计算
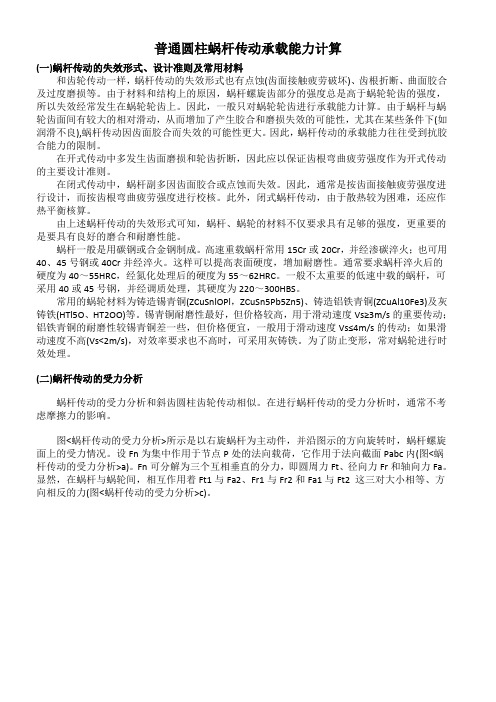
普通圆柱蜗杆传动承载能力计算(一)蜗杆传动的失效形式、设计准则及常用材料和齿轮传动一样,蜗杆传动的失效形式也有点蚀(齿面接触疲劳破坏)、齿根折断、曲面胶合及过度磨损等。
由于材料和结构上的原因,蜗杆螺旋齿部分的强度总是高于蜗轮轮齿的强度,所以失效经常发生在蜗轮轮齿上。
因此,一般只对蜗轮轮齿进行承载能力计算。
由于蜗杆与蜗轮齿面间有较大的相对滑动,从而增加了产生胶合和磨损失效的可能性,尤其在某些条件下(如润滑不良),蜗杆传动因齿面胶合而失效的可能性更大。
因此,蜗杆传动的承载能力往往受到抗胶合能力的限制。
在开式传动中多发生齿面磨损和轮齿折断,因此应以保证齿根弯曲疲劳强度作为开式传动的主要设计准则。
在闭式传动中,蜗杆副多因齿面胶合或点蚀而失效。
因此,通常是按齿面接触疲劳强度进行设计,而按齿根弯曲疲劳强度进行校核。
此外,闭式蜗杆传动,由于散热较为困难,还应作热平衡核算。
由上述蜗杆传动的失效形式可知,蜗杆、蜗轮的材料不仅要求具有足够的强度,更重要的是要具有良好的磨合和耐磨性能。
蜗杆一般是用碳钢或合金钢制成。
高速重载蜗杆常用15Cr或20Cr,并经渗碳淬火;也可用40、45号钢或40Cr并经淬火。
这样可以提高表面硬度,增加耐磨性。
通常要求蜗杆淬火后的硬度为40~55HRC,经氮化处理后的硬度为55~62HRC。
一般不太重要的低速中载的蜗杆,可采用40或45号钢,并经调质处理,其硬度为220~300HBS。
常用的蜗轮材料为铸造锡青铜(ZCuSnlOPl,ZCuSn5Pb5Zn5)、铸造铝铁青铜(ZCuAl10Fe3)及灰铸铁(HTl5O、HT2OO)等。
锡青铜耐磨性最好,但价格较高,用于滑动速度Vs≥3m/s的重要传动;铝铁青铜的耐磨性较锡青铜差一些,但价格便宜,一般用于滑动速度Vs≤4m/s的传动;如果滑动速度不高(Vs<2m/s),对效率要求也不高时,可采用灰铸铁。
为了防止变形,常对蜗轮进行时效处理。
(二)蜗杆传动的受力分析蜗杆传动的受力分析和斜齿圆柱齿轮传动相似。
蜗杆传动的几何参数和尺寸计算
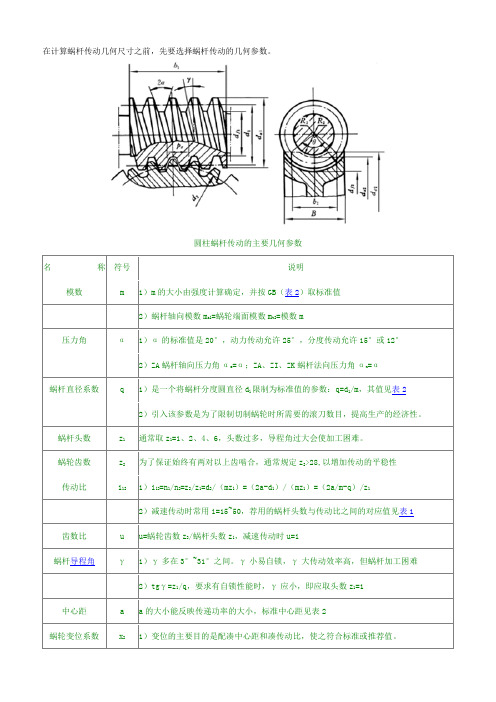
径d1/mm
m2d1/mm3
蜗杆头数z1
直径系数q
蜗杆分度圆导程角γ
蜗轮齿数z2
蜗轮变位系数x2
40
1
18
18
1
18.00
3°10′47″
62
0
50
82
0
40
1.25
20
31.25
1
16.00
3°34′35″
49
-0.500
50
22.4
35
17.92
3°11′38″
62
0.040
63
62
0.440
-0.1
≥(10.5+ )m
0.5
≥(12.5+0.1 )m
1.0
≥(13+0.1 )m
表1蜗杆头数z1与蜗轮齿数z2的荐用值
i=z2/z1
z1
z2
5
6
29~31
7~15
4
29~61
14~30
2
29~61
29~82
1
29~82
往上
表2普通圆柱蜗杆基本尺寸和参数及其与蜗轮参数的匹配
中心距a/mm
模数m/mm
传动比
i12
1)i12=n1/n2=z2/z1=d2/(mz1)=(2a-d1)/(mz1)=(2a/m-q)/z1
2)减速传动时常用i=15~50,荐用的蜗杆头数与传动比之间的对应值见表1
齿数比
u
u=蜗轮齿数z2/蜗杆头数z1,减速传动时u=i
蜗杆导程角
γ
1)γ多在3°~31°之间。γ小易自锁,γ大传动效率高,但蜗杆加工困难
(-0.100)
- 1、下载文档前请自行甄别文档内容的完整性,平台不提供额外的编辑、内容补充、找答案等附加服务。
- 2、"仅部分预览"的文档,不可在线预览部分如存在完整性等问题,可反馈申请退款(可完整预览的文档不适用该条件!)。
- 3、如文档侵犯您的权益,请联系客服反馈,我们会尽快为您处理(人工客服工作时间:9:00-18:30)。
三、蜗杆传动的强度计算
1、蜗轮齿面接触疲劳强度计算,由赫其公式(Hertz )按主平面内斜齿轮与齿条啮合进行强度计算
H n E H L KF Z ][σρσ≤=∑
Fn ——法向载荷(N );L ——接触线长度(注意蜗杆蜗轮接触线是倾斜的,并计入重合度);∑ρ——综合曲率半径;Z E ——材料弹性线数,对钢蜗杆↔配青铜蜗轮αMP Z E 160=,代入蜗杆传动有关参数,并化简得 校核公式:H P E H a KT Z Z ][/32σσ≤⋅= Mpa
式中,Z E ——材料的弹性系数,钢蜗杆配青铜蜗轮αMP Z E 160=
Z P ——接触系数,Z P 为反映蜗杆传动接触线长度和曲率半径对接触强度的影响系数 βK K K K V A ⋅⋅=——载荷系数
K A ——工况系数
βK ——齿面载荷分布系数:1=βK ——载荷平稳
6.1~3.1=βK ——载荷变化较大,或有冲击、振动时 K V ——动载荷系数 s m V K V /3,1.1~0.12≤=——精制蜗杆
s m V K V /3,2.1~1.12>=——一般蜗杆
设计公式:32
2][⎪⎪⎭⎫ ⎝
⎛≥H P E Z Z KT a σmm ⇒定m,q ,
H ][σ——蜗轮齿面许用接触应力
(1)当蜗轮材料为铸铁或高强度青铜,ασMP B 300≥——失效形式为胶合(不属于疲劳失效),∴许用应力H ][σ与应力循环次数N 无关。
(2)若蜗轮材料ασMP B 300<(锡青铜)——失效形式为点蚀,H ][σ与应力循环次数N 有关。
OH HN H K ][][σσ= OH ][σ——基本许用接触应力
HN K ——接触强度寿命系数,8
710N
K HN =,N 为应力循环次数,h L jn N 260=,n 2
为蜗轮转速(r/min ),L h 为蜗轮总工作时数h ,j 为每转一圈每个轮齿啮合次数。
2、蜗轮齿根弯曲疲劳强度计算
齿根折断一般发生在Z 2>90,及开式传动中,∴在闭式传动中弯曲强度计算作为校核计算对于重载传动,通过计算还可差别由于轮齿的弯曲变形量引起的轮齿弹性变形量是否过大而影响蜗杆传动的平稳性。
同样由于主平面内蜗杆蜗轮——相当于齿条与斜齿轮啮合,所以,将蜗轮看成斜齿轮,由斜齿轮齿根弯曲应力计算公式得: 斜齿数:βεβεσY Y Y Y m d b KT Y Y Y Y m b KF Sa Fa n
Sa Fa n t F 2222222222== b 2——蜗轮齿弧长,γθ
πcos 36012︒=d b ,θ为蜗轮齿宽角
γcos m m n =为法面模数
Y Sa2——齿根应力修正系数在F ][σ中考虑。
εY ——弯曲疲劳强度重合度系数,εY =0.667
βY ——螺旋角影响系数,取︒-=1201γβY
将上述参数代入得弯曲疲劳强度校核公式:
F Fa F Y Y m d d KT ][cos 53.12212σγ
σβ≤= Y Fa2——蜗轮齿形系数,按当量齿数γ322cos Z Z V =及变位系数X 2,查图
F ][σ——蜗轮轮齿许用弯曲应力
Fn oF F K ⋅=][][σσ
oF ][σ——蜗轮基本许用应力(计入齿根应力修正系数Y Fa2),
弯曲应力脉动循环oF ][σ;弯曲应力对称(双侧工作)循环oF ][1-σ 设计公式:βσγY Y Z KT d m Fa F
22212][cos 53.1≥ mm 3 ⇒定m 、d 1、q 四、蜗杆的刚度计算
目的:防止弹性变形过大而造成蜗杆蜗轮不能正确啮合,加剧齿面磨损
计算模型:简支梁 集中载荷:2121r t F F P +=
蜗杆最大挠度:][483
2121y L EI F F y r t ≤'+=
刚度条件: 许用最大挠度:1000
][1d y = I ——蜗杆的截面惯性矩,644
1
f d I π=,
1f d ——蜗杆齿根圆直径(mm ),L ——支承跨距(mm )
五、普通圆柱蜗杆传动精度等级及其选择
按GB10089-88
高 → 低
精度等级 1,2,…,6,7,8,9,10,11,12
远景 常用
6级——中等精度机床分度机构(插齿机、滚、齿机),读数装置精密传动机构V 2>5m/s 7级——适于一般精度要求的动力传动,中等速度(V 2<7m/s )
8级——短时工作低速传动(V 2≤3m/s )
9级——低速、低精度,简易机构中。