蜗杆外径计算公式
蜗轮蜗杆计算
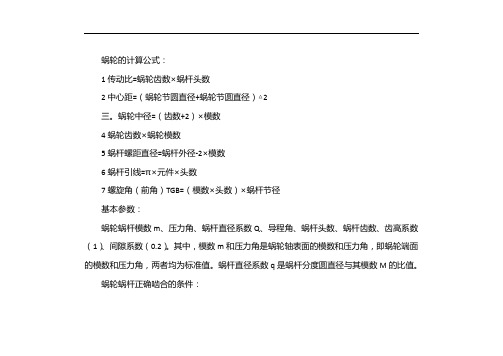
蜗轮的计算公式:1传动比=蜗轮齿数×蜗杆头数2中心距=(蜗轮节圆直径+蜗轮节圆直径)△2三。
蜗轮中径=(齿数+2)×模数4蜗轮齿数×蜗轮模数5蜗杆螺距直径=蜗杆外径-2×模数6蜗杆引线=π×元件×头数7螺旋角(前角)TGB=(模数×头数)×蜗杆节径基本参数:蜗轮蜗杆模数m、压力角、蜗杆直径系数Q、导程角、蜗杆头数、蜗杆齿数、齿高系数(1)、间隙系数(0.2)。
其中,模数m和压力角是蜗轮轴表面的模数和压力角,即蜗轮端面的模数和压力角,两者均为标准值。
蜗杆直径系数q是蜗杆分度圆直径与其模数M的比值。
蜗轮蜗杆正确啮合的条件:在中间平面,蜗杆和蜗轮的模数和压力角分别相等,即蜗轮端面的模数等于蜗杆轴线的模数,即标准值。
蜗轮端面的压力角应等于蜗杆的轴向压力角和标准值,即==M。
当蜗轮的交角一定时,必须保证蜗轮和蜗杆的螺旋方向一致。
蜗轮结构通常用于在两个交错轴之间传递运动和动力。
蜗轮相当于中间平面上的齿轮和齿条,蜗杆和螺钉的形状相似。
分类这些系列大致包括:1。
Wh系列蜗轮减速器:wht/whx/whs/whc2;CW系列蜗轮减速器:CWU/CWS/cwo3;WP系列蜗轮减速器:WPA/WPS/WPW/WPE/wpz/wpd4;TP系列包络蜗轮减速器:TPU/TPS/TPA/tpg5;PW型平面双包环面环面蜗杆减速器;另外,根据蜗杆的形状,蜗杆传动可分为圆柱蜗杆传动、环形蜗杆传动和斜蜗杆传动。
[1]组织特征1该机构比交错斜齿轮机构具有更大的传动比。
2两轮啮合齿面间存在线接触,其承载能力远高于交错斜齿轮机构。
三。
蜗杆传动相当于螺旋传动,即多齿啮合传动,传动平稳,噪音低。
4当蜗杆的导程角小于啮合齿间的等效摩擦角时,该机构具有自锁性能,可以实现反向自锁,即只有蜗杆可以驱动蜗轮,而不能驱动蜗轮。
起重机械采用自锁蜗杆机构,其反向自锁性能能起到安全防护作用。
蜗杆计算公式
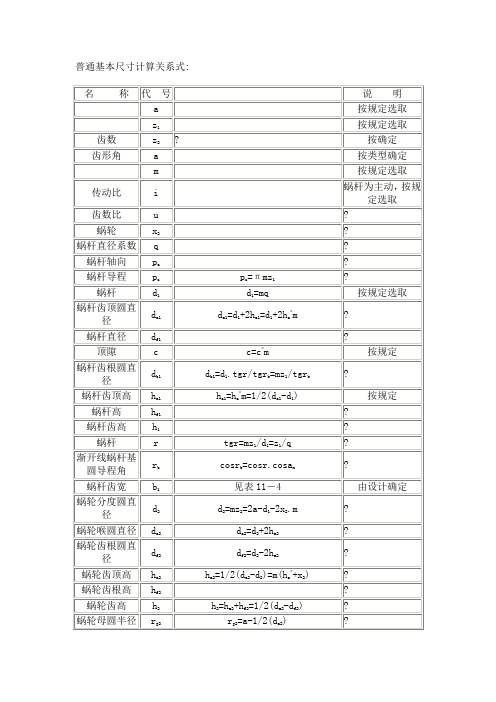
d2'=d2
b1
见表11-4
由设计确定
蜗轮分度圆直径
d2
d2=mz2=2a-d1-2x2.m
?
蜗轮喉圆直径
da2
da2=d2+2ha2
?
蜗轮齿根圆直径
df2
df2=d2-2ha2
?
蜗轮齿顶高
ha2
ha2=1/2(da2-d2)=m(ha*+x2)
?
蜗轮齿根高
hf2
?
蜗轮齿高
h2
h2=ha2+hf2=1/2(da2-df2)
普通基本尺寸计算关系式:
名 称
代 号
说 明
a
按规定选取
z1
按规定选取
齿数
z2
?
按确定
齿形角
a
按类型确定
m
按规定选取
传动比
i
蜗杆为主动,按规定选取
齿数比
u
?
蜗轮
x2
?
蜗杆直径系数
q
?
蜗杆轴向
pa
?
蜗杆导程
pz
pz=πmz1
?
蜗杆
d1
d1=mq
按规定选取
蜗杆齿顶圆直径
da1
da1=d1+2ha1=d1+2ha*m
?
蜗杆直径
df1
?
顶隙
c
c=c*m
按规定
蜗杆齿根圆直径
db1
db1=d1.tgr/tgrb=mz1/tgrb
?
蜗杆齿顶高
ha1
ha1=ha*m=1/2(da1-d1)
按规定
蜗杆高
蜗轮蜗杆的计算

蜗轮蜗杆的计算公司标准化编码 [QQX96QT-XQQB89Q8-NQQJ6Q8-MQM9N]蜗轮、蜗杆的计算公式:1,传动比=蜗轮齿数÷蜗杆头数2,中心距=(蜗轮节径+蜗杆节径)÷2 3,蜗轮吼径=(齿数+2)×模数 4,蜗轮节径=模数×齿数5,蜗杆节径=蜗杆外径-2×模数 6,蜗杆导程=π×模数×头数7,螺旋角(导程角)tg β=(模数×头数)÷蜗杆节径 一.基本参数:(1)模数m 和压力角α:在中间平面中,为保证蜗杆蜗轮传动的正确啮合,蜗杆的轴向模数m a1和压力角αa1应分别相等于蜗轮的法面模数m t2和压力角αt2,即 m a1=m t2=m αa1=αt2蜗杆轴向压力角与法向压力角的关系为: tgαa =tgαn /cosγ 式中:γ-导程角。
(2)蜗杆的分度圆直径d 1和直径系数q为了保证蜗杆与蜗轮的正确啮合,要用与蜗杆尺寸相同的蜗杆滚刀来加工蜗轮。
由于相同的模数,可以有许多不同的蜗杆直径,这样就造成要配备很多的蜗轮滚刀,以适应不同的蜗杆直径。
显然,这样很不经济。
为了减少蜗轮滚刀的个数和便于滚刀的标准化,就对每一标准的模数规定了一定数量的蜗杆分度圆直径d1,而把及分度圆直径和模数的比称为蜗杆直径系数q ,即: q=d1/m常用的标准模数m 和蜗杆分度圆直径d1及直径系数q ,见匹配表。
(3)蜗杆头数z 1和蜗轮齿数z 2蜗杆头数可根据要求的传动比和效率来选择,一般取z1=1-10,推荐 z1=1,2,4,6。
选择的原则是:当要求传动比较大,或要求传递大的转矩时,则z1取小值;要求传动自锁时取z1=1;要求具有高的传动效率,或高速传动时,则z1取较大值。
蜗轮齿数的多少,影响运转的平稳性,并受到两个限制:最少齿数应避免发生根切与干涉,理论上应使z2min≥17,但z2<26时,啮合区显着减小,影响平稳性,而在z2≥30时,则可始终保持有两对齿以上啮合,因之通常规定z2>28。
蜗轮蜗杆的计算
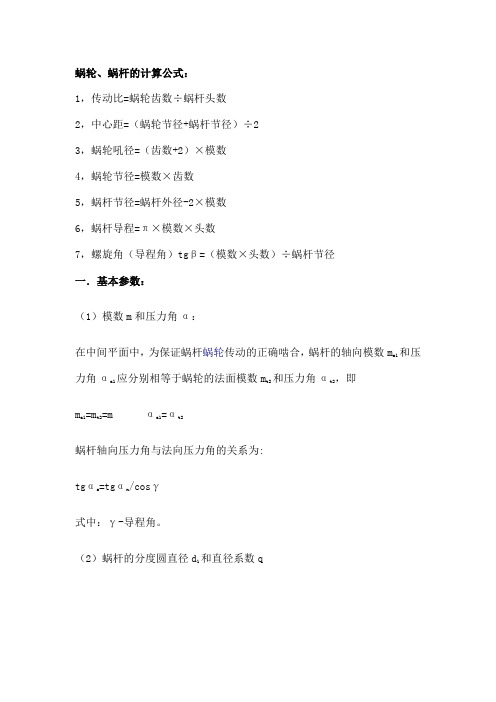
蜗轮、蜗杆的计算公式: 1,传动比=蜗轮齿数÷蜗杆头数 2,中心距=(蜗轮节径+蜗杆节径)÷2 3,蜗轮吼径=(齿数+2)×模数 4,蜗轮节径=模数×齿数 5,蜗杆节径=蜗杆外径-2×模数 6,蜗杆导程=π×模数×头数7,螺旋角(导程角)tg β=(模数×头数)÷蜗杆节径 一.基本参数:(1)模数m 和压力角α:在中间平面中,为保证蜗杆蜗轮传动的正确啮合,蜗杆的轴向模数m a1和压力角αa1应分别相等于蜗轮的法面模数m t2和压力角αt2,即 m a1=m t2=m αa1=αt2蜗杆轴向压力角与法向压力角的关系为: tgαa =tgαn /cosγ 式中:γ-导程角。
(2)蜗杆的分度圆直径d 1和直径系数q为了保证蜗杆与蜗轮的正确啮合,要用与蜗杆尺寸相同的蜗杆滚刀来加工蜗轮。
由于相同的模数,可以有许多不同的蜗杆直径,这样就造成要配备很多的蜗轮滚刀,以适应不同的蜗杆直径。
显然,这样很不经济。
为了减少蜗轮滚刀的个数和便于滚刀的标准化,就对每一标准的模数规定了一定数量的蜗杆分度圆直径d1,而把及分度圆直径和模数的比称为蜗杆直径系数q,即:q=d1/m常用的标准模数m和蜗杆分度圆直径d1及直径系数q,见匹配表。
(3)蜗杆头数z1和蜗轮齿数z2蜗杆头数可根据要求的传动比和效率来选择,一般取z1=1-10,推荐 z1=1,2,4,6。
选择的原则是:当要求传动比较大,或要求传递大的转矩时,则z1取小值;要求传动自锁时取z1=1;要求具有高的传动效率,或高速传动时,则z1取较大值。
蜗轮齿数的多少,影响运转的平稳性,并受到两个限制:最少齿数应避免发生根切与干涉,理论上应使z2min≥17,但z2<26时,啮合区显着减小,影响平稳性,而在z2≥30时,则可始终保持有两对齿以上啮合,因之通常规定z2>28。
另一方面z2也不能过多,当z2>80时(对于动力传动),蜗轮直径将增大过多,在结构上相应就须增大蜗杆两支承点间的跨距,影响蜗杆轴的刚度和啮合精度;对一定直径的蜗轮,如z2取得过多,模数m 就减小甚多,将影响轮齿的弯曲强度;故对于动力传动,常用的范围为z2≈28-70。
蜗轮蜗杆计算
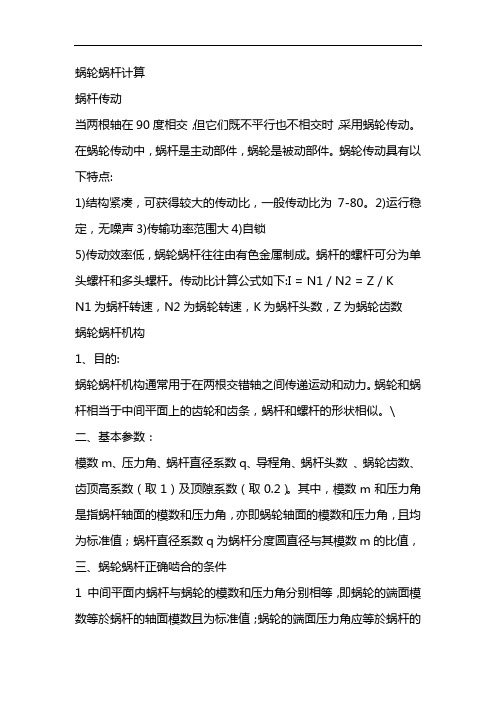
蜗轮蜗杆计算蜗杆传动当两根轴在90度相交,但它们既不平行也不相交时,采用蜗轮传动。
在蜗轮传动中,蜗杆是主动部件,蜗轮是被动部件。
蜗轮传动具有以下特点:1)结构紧凑,可获得较大的传动比,一般传动比为7-80。
2)运行稳定,无噪声3)传输功率范围大4)自锁5)传动效率低,蜗轮蜗杆往往由有色金属制成。
蜗杆的螺杆可分为单头螺杆和多头螺杆。
传动比计算公式如下:I = N1 / N2 = Z / KN1为蜗杆转速,N2为蜗轮转速,K为蜗杆头数,Z为蜗轮齿数蜗轮蜗杆机构1、目的:蜗轮蜗杆机构通常用于在两根交错轴之间传递运动和动力。
蜗轮和蜗杆相当于中间平面上的齿轮和齿条,蜗杆和螺杆的形状相似。
\ 二、基本参数:模数m、压力角、蜗杆直径系数q、导程角、蜗杆头数、蜗轮齿数、齿顶高系数(取1)及顶隙系数(取0.2)。
其中,模数m和压力角是指蜗杆轴面的模数和压力角,亦即蜗轮轴面的模数和压力角,且均为标准值;蜗杆直径系数q为蜗杆分度圆直径与其模数m的比值,三、蜗轮蜗杆正确啮合的条件1 中间平面内蜗杆与蜗轮的模数和压力角分别相等,即蜗轮的端面模数等於蜗杆的轴面模数且为标准值;蜗轮的端面压力角应等於蜗杆的轴面压力角且为标准值,即m2 当蜗轮蜗杆的交错角为时,还需保证,而且蜗轮与蜗杆螺旋线旋向必须相同。
四、几何尺寸计算与圆柱齿轮基本相同,需注意的几个问题是:蜗杆导程角()是蜗杆分度圆柱上螺旋线的切线与蜗杆端面之间的夹角,与螺杆螺旋角的关系为,蜗轮的螺旋角,大则传动效率高,当小於啮合齿间当量摩擦角时,机构自锁。
引入蜗杆直径系数q是为了限制蜗轮滚刀的数目,使蜗杆分度圆直径进行了标准化m一定时,q大则大,蜗杆轴的刚度及强度相应增大;一定时,q小则导程角增大,传动效率相应提高。
蜗杆头数推荐值为1、2、4、6,当取小值时,其传动比大,且具有自锁性;当取大值时,传动效率高。
与圆柱齿轮传动不同,蜗杆蜗轮机构传动比不等於,而是,蜗杆蜗轮机构的中心距不等於,而是。
蜗轮蜗杆的计算
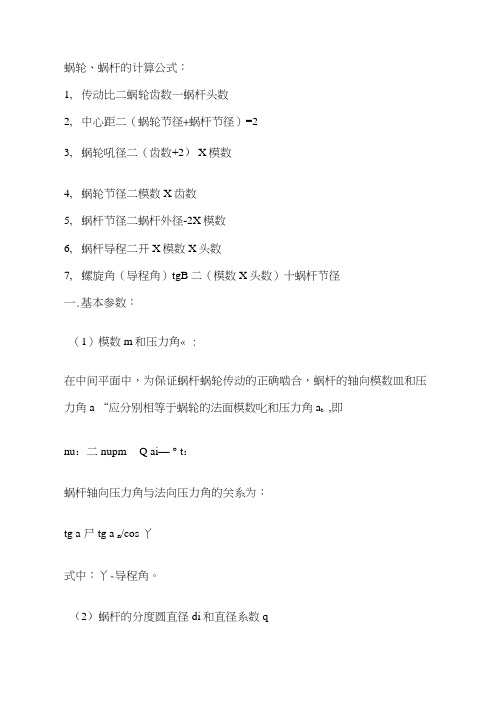
蜗轮、蜗杆的计算公式:1,传动比二蜗轮齿数一蜗杆头数2,中心距二(蜗轮节径+蜗杆节径)=23,蜗轮吼径二(齿数+2) X模数4,蜗轮节径二模数X齿数5,蜗杆节径二蜗杆外径-2X模数6,蜗杆导程二开X模数X头数7,螺旋角(导程角)tgB二(模数X头数)十蜗杆节径一.基本参数:(1)模数m和压力角« :在中间平面中,为保证蜗杆蜗轮传动的正确啮合,蜗杆的轴向模数皿和压力角a “应分别相等于蜗轮的法面模数叱和压力角a t:,即nu:二nupm Q ai— ° t:蜗杆轴向压力角与法向压力角的关系为:tg a 尸tg a n/cos 丫式中:丫-导程角。
(2)蜗杆的分度圆直径di和直径系数q为了保证蜗杆与蜗轮的正确啮合,要用与蜗杆尺寸相同的蜗杆滚刀來加工蜗轮。
由于相同的模数,可以有许多不同的蜗杆直径,这样就造成要配备很多的蜗轮滚刀,以适应不同的蜗杆直径。
显然,这样很不经济。
为了减少蜗轮滚刀的个数和便于滚刀的标准化,就对每一标准的模数规定了一定数量的蜗杆分度圆直径",而把及分度圆直径和模数的比称为蜗杆直径系数q,即:q=dl/m常用的标准模数m和蜗杆分度圆直径dl及直径系数q,见匹配表。
(3)蜗杆头数N和蜗轮齿数比蜗杆头数可根据要求的传动比和效率来选择,一般取zl = l-10,推荐zl=1, 2, 4, 6o选择的原则是:当要求传动比较大,或要求传递大的转矩时,则zl取小值;要求传动自锁时取zl = l:要求具有高的传动效率,或高速传动时,则zl取较大值。
蜗轮齿数的多少,影响运转的平稳性,并受到两个限制:最少齿数应避免发生根切与干涉,理论上应使z2min^l7,但z2<26时,啮合区显着减小, 影响平稳性,而在z2N30时,则可始终保持有两对齿以上啮合,因之通常规定z2>28o另一方面z2也不能过多,当z2>80时(对于动力传动),蜗轮直径将增大过多,在结构上相应就须增大蜗杆两支承点间的跨距,影响蜗杆轴的刚度和啮合精度;对一定直径的蜗轮,如z2取得过多,模数m 就减小我多,将影响轮齿的弯曲强度;故对于动力传动,常用的范围为z2~28-70。
蜗轮蜗杆计算

蜗轮蜗杆计算蜗轮蜗杆传动蜗轮蜗杆传动用于两轴交叉成90度,但彼此既不平行又不相交的情况下,通常在蜗轮传动中,蜗杆是主动件,而蜗轮是被动件。
蜗轮蜗杆传动有如下特点:1)结构紧凑、并能获得很大的传动比,一般传动比为7-80。
2) 工作平稳无噪音3) 传动功率范围大4)可以自锁5)传动效率低,蜗轮常需用有色金属制造。
蜗杆的螺旋有单头与多头之分。
传动比的计算如下:I=n1/n2=z/Kn1-蜗杆的转速n2-蜗轮的转速K-蜗杆头数Z-蜗轮的齿数蜗轮及蜗杆机构一、用途:蜗轮蜗杆机构常用来传递两交错轴之间的运动和动力。
蜗轮与蜗杆在其中间平面内相当於齿轮与齿条,蜗杆又与螺杆形状相似。
2、基本参数:模量m,压力角,蜗杆直径系数Q,导程角,蜗杆头数,蜗轮齿数,齿顶系数取1,间隙系数取0.2。
其中模量m和压力角为蜗杆轴面模量和压力角,即蜗轮轴面模量和压力角,均为标准值;蜗杆直径系数q 为蜗杆分度圆直径与其模量M之比,3、蜗轮与蜗杆正确啮合的条件1. 蜗杆和蜗轮在中间平面的模量和压力角分别相等,即蜗轮端面模量与蜗杆轴面模量相等,为标准值;蜗轮端面压力角应与蜗杆轴面压力角相等,为标准值,即M2. 当蜗轮交错角为时,必须保证蜗轮与蜗杆的螺旋方向一致。
4、几何尺寸的计算与圆柱齿轮基本相同蜗杆导度角()是蜗杆分度圆柱上螺旋的切线与蜗杆端面的夹角。
超前角与螺杆角的关系为:蜗轮螺旋角大时,传动效率高;当它小于啮合齿间的等效摩擦角时,该机构锁住自己。
引入蜗杆直径系数q是为了限制蜗杆滚刀的数量和标准化蜗杆分度圆的直径。
当m固定时,q越大,蜗杆轴的刚度和强度越大;当q较小时,超前角增大,传动效率相应提高。
蜗杆头数的推荐值为1,2,4,6。
当值小时,传动比大,具有自锁性能;当值大时,传输效率高。
与圆柱齿轮传动不同,蜗轮机构的传动比不等于,但蜗轮机构的中心距离不等于,但。
在蜗轮蜗杆传动中,可根据啮合点K(平行于螺旋线的切线)的方向和方向,并画出垂直于蜗轮轴的速度矢量三角形,确定蜗轮转动方向的判断方法;也可以通过“左手握着右旋蜗杆,右手握着左旋蜗杆,四个拇指”来判断。
涡轮蜗杆的技术公式
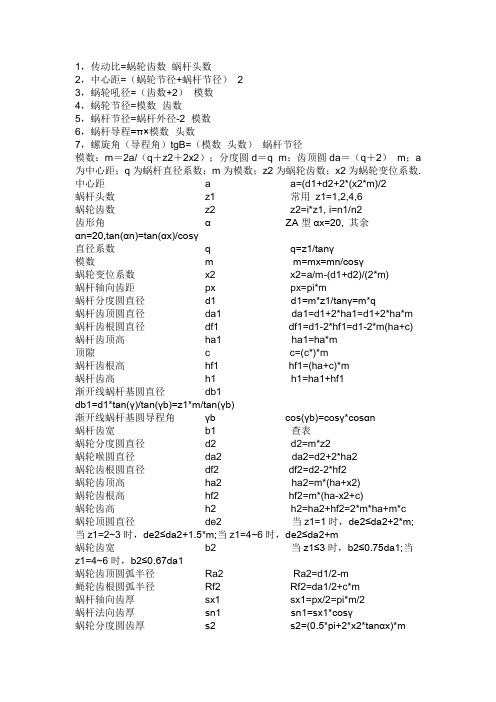
1,传动比=蜗轮齿数÷蜗杆头数2,中心距=(蜗轮节径+蜗杆节径)÷23,蜗轮吼径=(齿数+2)×模数4,蜗轮节径=模数×齿数5,蜗杆节径=蜗杆外径-2×模数6,蜗杆导程=π×模数×头数7,螺旋角(导程角)tgB=(模数×头数)÷蜗杆节径模数:m=2a/(q+z2+2x2);分度圆d=q×m;齿顶圆da=(q+2)×m;a 为中心距;q为蜗杆直径系数;m为模数;z2为蜗轮齿数;x2为蜗轮变位系数. 中心距 a a=(d1+d2+2*(x2*m)/2蜗杆头数z1 常用z1=1,2,4,6蜗轮齿数z2 z2=i*z1, i=n1/n2齿形角α ZA型αx=20, 其余αn=20,tan(αn)=tan(αx)/cosγ直径系数q q=z1/tanγ模数m m=mx=mn/cosγ蜗轮变位系数x2 x2=a/m-(d1+d2)/(2*m)蜗杆轴向齿距px px=pi*m蜗杆分度圆直径d1 d1=m*z1/tanγ=m*q蜗杆齿顶圆直径da1 da1=d1+2*ha1=d1+2*ha*m 蜗杆齿根圆直径df1 df1=d1-2*hf1=d1-2*m(ha+c) 蜗杆齿顶高ha1 ha1=ha*m顶隙 c c=(c*)*m蜗杆齿根高hf1 hf1=(ha+c)*m蜗杆齿高h1 h1=ha1+hf1渐开线蜗杆基圆直径db1db1=d1*tan(γ)/tan(γb)=z1*m/tan(γb)渐开线蜗杆基圆导程角γb cos(γb)=cosγ*cosαn蜗杆齿宽b1 查表蜗轮分度圆直径d2 d2=m*z2蜗轮喉圆直径da2 da2=d2+2*ha2蜗轮齿根圆直径df2 df2=d2-2*hf2蜗轮齿顶高ha2 ha2=m*(ha+x2)蜗轮齿根高hf2 hf2=m*(ha-x2+c)蜗轮齿高h2 h2=ha2+hf2=2*m*ha+m*c蜗轮顶圆直径de2 当z1=1时,de2≤da2+2*m;当z1=2~3时,de2≤da2+1.5*m;当z1=4~6时,de2≤da2+m蜗轮齿宽b2 当z1≤3时,b2≤0.75da1;当z1=4~6时,b2≤0.67da1蜗轮齿顶圆弧半径Ra2 Ra2=d1/2-m蝇轮齿根圆弧半径Rf2 Rf2=da1/2+c*m蜗杆轴向齿厚sx1 sx1=px/2=pi*m/2蜗杆法向齿厚sn1 sn1=sx1*cosγ蜗轮分度圆齿厚s2 s2=(0.5*pi+2*x2*tanαx)*m蜗杆节圆直径d1' d1'=d1+2*x2*m 蜗轮节圆直径d2' d2'=d2。
【方案】蜗轮蜗杆的计算.doc
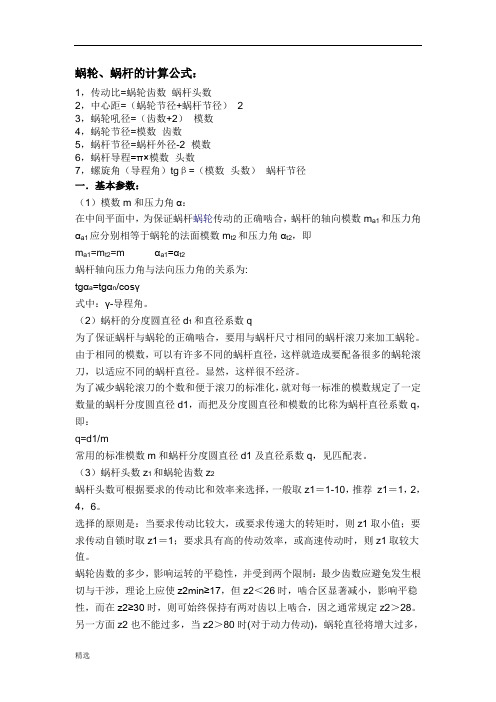
蜗轮、蜗杆的计算公式:1,传动比=蜗轮齿数÷蜗杆头数2,中心距=(蜗轮节径+蜗杆节径)÷23,蜗轮吼径=(齿数+2)×模数4,蜗轮节径=模数×齿数5,蜗杆节径=蜗杆外径-2×模数6,蜗杆导程=π×模数×头数7,螺旋角(导程角)tgβ=(模数×头数)÷蜗杆节径一.基本参数:(1)模数m和压力角α:在中间平面中,为保证蜗杆蜗轮传动的正确啮合,蜗杆的轴向模数m a1和压力角αa1应分别相等于蜗轮的法面模数m t2和压力角αt2,即m a1=m t2=mαa1=αt2蜗杆轴向压力角与法向压力角的关系为:tgαa=tgαn/cosγ式中:γ-导程角。
(2)蜗杆的分度圆直径d1和直径系数q为了保证蜗杆与蜗轮的正确啮合,要用与蜗杆尺寸相同的蜗杆滚刀来加工蜗轮。
由于相同的模数,可以有许多不同的蜗杆直径,这样就造成要配备很多的蜗轮滚刀,以适应不同的蜗杆直径。
显然,这样很不经济。
为了减少蜗轮滚刀的个数和便于滚刀的标准化,就对每一标准的模数规定了一定数量的蜗杆分度圆直径d1,而把及分度圆直径和模数的比称为蜗杆直径系数q,即:q=d1/m常用的标准模数m和蜗杆分度圆直径d1及直径系数q,见匹配表。
(3)蜗杆头数z1和蜗轮齿数z2蜗杆头数可根据要求的传动比和效率来选择,一般取z1=1-10,推荐z1=1,2,4,6。
选择的原则是:当要求传动比较大,或要求传递大的转矩时,则z1取小值;要求传动自锁时取z1=1;要求具有高的传动效率,或高速传动时,则z1取较大值。
蜗轮齿数的多少,影响运转的平稳性,并受到两个限制:最少齿数应避免发生根切与干涉,理论上应使z2min≥17,但z2<26时,啮合区显著减小,影响平稳性,而在z2≥30时,则可始终保持有两对齿以上啮合,因之通常规定z2>28。
另一方面z2也不能过多,当z2>80时(对于动力传动),蜗轮直径将增大过多,在结构上相应就须增大蜗杆两支承点间的跨距,影响蜗杆轴的刚度和啮合精度;对一定直径的蜗轮,如z2取得过多,模数m就减小甚多,将影响轮齿的弯曲强度;故对于动力传动,常用的范围为z2≈28-70。
蜗轮蜗杆的计算
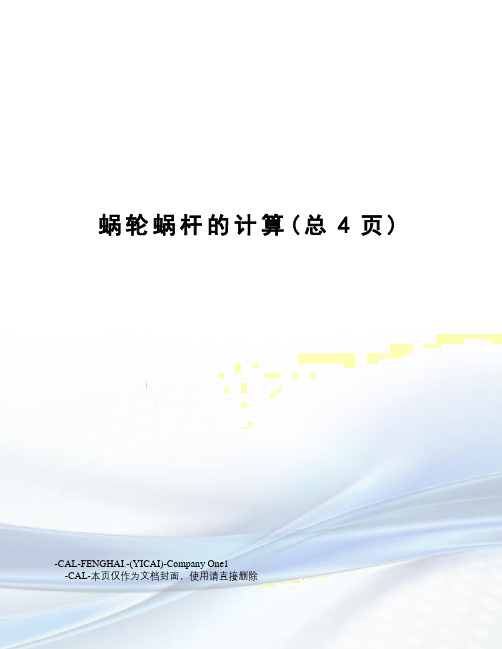
蜗轮蜗杆的计算(总4页) -CAL-FENGHAI.-(YICAI)-Company One1-CAL-本页仅作为文档封面,使用请直接删除蜗轮、蜗杆的计算公式:1,传动比=蜗轮齿数÷蜗杆头数2,中心距=(蜗轮节径+蜗杆节径)÷2 3,蜗轮吼径=(齿数+2)×模数 4,蜗轮节径=模数×齿数5,蜗杆节径=蜗杆外径-2×模数 6,蜗杆导程=π×模数×头数7,螺旋角(导程角)tg β=(模数×头数)÷蜗杆节径 一.基本参数:(1)模数m 和压力角α:在中间平面中,为保证蜗杆蜗轮传动的正确啮合,蜗杆的轴向模数m a1和压力角αa1应分别相等于蜗轮的法面模数m t2和压力角αt2,即 m a1=m t2=m αa1=αt2蜗杆轴向压力角与法向压力角的关系为: tgαa =tgαn /cosγ 式中:γ-导程角。
(2)蜗杆的分度圆直径d 1和直径系数q为了保证蜗杆与蜗轮的正确啮合,要用与蜗杆尺寸相同的蜗杆滚刀来加工蜗轮。
由于相同的模数,可以有许多不同的蜗杆直径,这样就造成要配备很多的蜗轮滚刀,以适应不同的蜗杆直径。
显然,这样很不经济。
为了减少蜗轮滚刀的个数和便于滚刀的标准化,就对每一标准的模数规定了一定数量的蜗杆分度圆直径d1,而把及分度圆直径和模数的比称为蜗杆直径系数q ,即: q=d1/m常用的标准模数m 和蜗杆分度圆直径d1及直径系数q ,见匹配表。
(3)蜗杆头数z 1和蜗轮齿数z 2蜗杆头数可根据要求的传动比和效率来选择,一般取z1=1-10,推荐 z1=1,2,4,6。
选择的原则是:当要求传动比较大,或要求传递大的转矩时,则z1取小值;要求传动自锁时取z1=1;要求具有高的传动效率,或高速传动时,则z1取较大值。
蜗轮齿数的多少,影响运转的平稳性,并受到两个限制:最少齿数应避免发生根切与干涉,理论上应使z2min≥17,但z2<26时,啮合区显着减小,影响平稳性,而在z2≥30时,则可始终保持有两对齿以上啮合,因之通常规定z2>28。
蜗轮蜗杆计算

蜗轮的计算公式:1传动比=蜗轮齿数×蜗杆头数2中心距离=(蜗轮节圆直径+蜗轮节圆直径)△23.蜗轮的螺距直径=(齿数+ 2)×模数4个蜗轮齿×蜗轮模块5蜗杆螺距直径=蜗杆外径-2×模数6蠕虫导线=π×成分×头数7螺旋角(前角)TGB =(模数×头数)×蜗杆螺距直径基本参数:蜗杆组件m,压力角,蜗杆直径系数Q,导程角,蜗杆头数,蜗杆齿数,齿高系数(1)和间隙系数(0.2)。
其中,模数m和压力角是蜗轮轴表面的模数和压力角,即蜗轮端面的模量和压力角,两者均为标准值。
蜗杆直径系数q是蜗杆分度圆直径与其模量M的比值。
正确啮合蜗轮和蜗杆的条件:在中间平面中,蜗杆和蜗轮的模量和压力角分别相等,即,蜗轮端面的模量等于蜗杆轴线的模量,即标准值。
蜗轮端面的压力角应等于轴向压力角和蜗杆的标准值,即== M.当蜗轮的交角固定时,蜗轮与蜗杆的螺纹方向必须一致。
蜗轮蜗杆结构通常用于在两个交错轴之间传递运动和动力。
蜗轮与中间平面上的齿轮和齿条等效,蜗轮和螺杆的形状相似。
分类这些系列大致包括:1. Wh系列蜗轮减速机:wht / whx / whs / whc2;CW系列蜗轮减速机:CWU / CWS / cwo3;WP系列蜗轮减速机:WPA / WPS / WPW / WPE / wpz / wpd4;TP 系列包络蜗轮减速机:TPU / TPS / TPA / tpg5;PW型平面双包络环形蜗杆减速机;另外,根据蜗杆的形状,蜗杆驱动器可分为圆柱蜗杆驱动器,环形蜗杆驱动器和斜蜗杆驱动器。
[1]组织特征该机构的传动比大于交错斜齿轮机构的传动比。
2.两个齿轮的啮合齿面之间在线接触,其承载能力远高于交错斜齿轮机构。
3.蜗杆传动相当于螺旋传动,即多齿啮合传动,传动平稳,噪音低。
当蜗杆的超前角小于啮合齿之间的等效摩擦角时,该机构具有自锁性能,可以实现反向自锁,即只有蜗杆可以驱动蜗轮,而不能驱动蜗轮。
蜗杆参数计算

普通圆柱蜗杆传动几何尺寸计算3. 蜗杆传动精度等级国标对蜗杆、蜗轮和蜗杆传动规定12个精度等级,第1级精度最高,第12级精度最低。
按照公差对传动性能的主要保证作用,可分为三个公差组,分别规定传动精度、工作平稳性精度和接触精度;各公差组中又规定若干项公差。
根据使用要求不同,允许各公差组选用不同的精度等级组合,但在同一公差组中,各项公差应保持相同的精度等级。
蜗杆和配对蜗轮的精度等级一般取为相同,也允许不相同。
蜗杆和蜗轮的加工方法和应用场合不同,可选不同精度等级。
蜗杆传动精度选择4. 蜗杆传动效率和自锁(1) 效率与齿轮传动的效率类似,蜗杆传动的功率损失主要包括:1)啮合损失;2)搅动润滑油的油阻损失;3)轴承的摩擦损失。
闭式蜗杆传动的效率η为:η=η1η2η3式中:η1——啮合效率;η2——搅油效率(一般为0.95-0.99);η3——轴承效率(对滚动轴承取0.99,对滑动轴承取0.98-0.99)。
蜗杆传动的效率主要取决于啮合效率。
蜗杆传动的啮合效率可以参照螺旋副的效率进行计算。
对于减速蜗杆(蜗杆主动):对于增速蜗杆(蜗轮主动):式中:ρv——当量摩擦角,其值与蜗杆蜗轮的材料组合、齿面精度和相对滑动速度等有关。
表中的相对滑动速度,v1为蜗杆节圆处的圆周速度。
从蜗杆传动的啮合效率中可以看出,导程角γ是影响啮合效率的重要参数,而导程角γ又与蜗杆头数有直接关系。
(2) 自锁在减速蜗杆传动中,蜗杆可以带动蜗轮旋转而蜗轮不能带动蜗杆旋转称为自锁。
其自锁条件与螺纹副的自锁条件相同,即:导程角γ≤ρv。
自锁蜗杆传动效率〈0.5。
设计蜗杆传动时,需要预估传动的效率,可以参考以下数值确定。
蜗轮蜗杆参数计算公式

蜗轮蜗杆参数计算公式
蜗轮蜗杆传动是一种常见的减速传动方式,其传动比可以较大,传动效率也较高,因此在机械传动中得到广泛应用。
蜗轮蜗杆传动的参数计算需要考虑许多因素,包括蜗轮和蜗杆的几何尺寸、材料性质、工作环境等。
下面是蜗轮蜗杆传动的参数计算公式:
1.蜗杆的公称直径
蜗杆的公称直径是指蜗杆中心线与蜗杆螺旋线之间的距离,通常用d表示。
蜗杆的公称直径可以根据以下公式计算:
d=mz
其中,m为模数,z为蜗杆的齿数。
2.蜗杆的导程
蜗杆的导程是指蜗杆螺旋线每圈的长度,通常用p表示。
蜗杆的导程可以根据以下公式计算:
p=πd
其中,d为蜗杆的公称直径。
3.蜗杆的螺旋角
蜗杆的螺旋角是指蜗杆螺旋线与蜗杆中心线的夹角,通常用α表示。
蜗杆的螺旋角可以根据以下公式计算:
tanα=p/πd
其中,p为蜗杆的导程,d为蜗杆的公称直径。
4.蜗轮的齿数
蜗轮的齿数是指蜗轮上的齿数,通常用z表示。
蜗轮的齿数可以根据以下公式计算:
z=(πd)/m
其中,d为蜗杆的公称直径,m为模数。
5.蜗轮的模数
蜗轮的模数是指蜗轮齿形的尺寸参数,通常用m表示。
蜗轮的模数可以根据以下公式计算:
m=(πd)/z
其中,d为蜗杆的公称直径,z为蜗轮的齿数。
以上是蜗轮蜗杆传动的参数计算公式,需要根据具体的传动要求和工作环境进行选择和计算。
蜗轮蜗杆的计算

蜗轮、蜗杆的计算公式:1,传动比=蜗轮齿数÷蜗杆头数2,中心距=(蜗轮节径+蜗杆节径)÷ 2 3,蜗轮吼径=(齿数+2)×模数4,蜗轮节径=模数×齿数5,蜗杆节径=蜗杆外径-2×模数6,蜗杆导程=π×模数×头数为了减少蜗轮滚刀的个数和便于滚刀的标准化,就对每一标准的模数规定了一定数量的蜗杆分度圆直径d1,而把及分度圆直径和模数的比称为蜗杆直径系数q,即:q=d1/m常用的标准模数m和蜗杆分度圆直径d1及直径系数q,见匹配表。
(3)蜗杆头数z1和蜗轮齿数z2蜗杆头数可根据要求的传动比和效率来选择,一般取z1=1-10,推荐z1=1,2,4,6。
选择的原则是:当要求传动比较大,或要求传递大的转矩时,则z1取小值;要求传动自锁时取z1=1;要求具有高的传动效率,或高速传动时,则z1取较大值。
蜗轮齿数的多少,影响运转的平稳性,并受到两个限制:最少齿数应避免发生根切与干涉,理论上应使z2min≥17,但z2<26时,啮合区显着减小,影响平稳性,而在z2≥30时,则可始终保持有两对齿以上啮合,因之通常规定z2>28。
另一方面z2也不能过多,当z2>80时(对于动力传动),蜗轮直径将增大过多,在结构上相应就须增大蜗杆两支承点间的跨距,影响蜗杆轴的刚度和啮合精度;对一定直径的蜗轮,如z2取得过多,模数m就减小甚多,将影响轮齿的弯曲强度;故对于动i=n1/n2=z2/z1 =u式中:n1 -蜗杆转速;n2-蜗轮转速。
减速运动的动力蜗杆传动,通常取5≤u≤70,优先采用15≤u≤50;增速传动5≤u≤15。
普通圆柱蜗杆基本尺寸和参数及其与蜗轮参数的匹配表。
2 蜗杆传动变位的特点蜗杆传动变位变位蜗杆传动根据使用场合的不同,可在下述两种变位方式中选取一种。
1)变位前后,蜗轮的齿数不变(z2 '=z2),蜗杆传动的中心距改变(a '≠a),如图9-8a、c所示,其中心距的计算式如下:a '=a+x2m=(d1+d2+2x2m)/22)变位前后,蜗杆传动的中心距不变(a '=a),蜗轮齿数发生变化(z2'≠z2),如图9-8d、e所示,z2' 计算如下:因a'=a则z2' =z2-2x2蜗杆传动变位:3 普通圆柱蜗杆传动的几何尺寸计算普通圆柱蜗杆传动基本几何尺寸计算关系式:。
计算四吼公式

计算四吼公式
1、传动比=蜗轮齿数÷蜗杆头数
2、中心距=(蜗轮节径+蜗杆节径)÷2
3、蜗轮吼径=(齿数+2)×模数
4、蜗轮节径=模数×齿数
5、蜗杆节径=蜗杆外径-2×模数
6、蜗杆导程=π×模数×头数
7、螺旋角(导程角)tgB=(模数×头数)÷蜗杆节径
蜗杆导程=π×模数×头数
模数=分度圆直径/齿数
头数是说螺杆上螺旋线的条数;
模数是指螺杆上螺旋线的大小,也就是模数越大螺杆上的螺旋线就越“柱装”(东北话,就是比较大,比较结实)
直径系数是指螺杆的粗细。
模数:齿轮的分度圆是设计、计算齿轮各部分尺寸的基准,而齿轮分度圆的周长=πd=z p,于是得分度圆的直径
d=z p/π
由于在上式中π为一无理数,不便于作为基准的分度圆的定位。
为了便于计算,制造和检验,现将比值p/π人为地规定为一些简单
的数值,并把这个比值叫做模数(module),以m表示。
模数m是决定齿轮尺寸的一个基本参数。
齿数相同的齿轮模数大,则其尺寸也大。
为了便于制造,检验和互换使用,齿轮的模数值已经
标准化了。
- 1、下载文档前请自行甄别文档内容的完整性,平台不提供额外的编辑、内容补充、找答案等附加服务。
- 2、"仅部分预览"的文档,不可在线预览部分如存在完整性等问题,可反馈申请退款(可完整预览的文档不适用该条件!)。
- 3、如文档侵犯您的权益,请联系客服反馈,我们会尽快为您处理(人工客服工作时间:9:00-18:30)。
蜗杆外径计算公式
蜗杆是一种常见的传动装置,具有简单、紧凑、高效、传动比大等优点。
在设计和制造蜗杆时,其外径的计算是非常重要的。
以下是蜗杆外径计算公式:
1. 蜗杆外径D的计算公式:
D = (Pd2/2π) + 2a + k
其中,P为蜗杆的模数,d为蜗杆的节圆直径,a为蜗杆的齿宽,k为蜗杆的端面距离。
2. 蜗轮外径D1的计算公式:
D1 = d + 2(m + a)/sinβ
其中,d为蜗杆的节圆直径,m为蜗杆的模数,a为蜗杆的齿宽,β为蜗杆与蜗轮的螺旋角。
3. 螺旋角β的计算公式:
tanβ = (π/2m)*tanφ
其中,φ为蜗杆和蜗轮的压力角。
以上是蜗杆外径计算公式,可以根据具体的蜗杆设计需求进行计算和应用。
- 1 -。