FMEA范例(DFMEA)--离合主缸
车辆白车身DFMEA分析范例

车身工程中心编制人:新严重度新频度新探测度新风险顺序数1零部件无法安装1车身数据未符合边界要求5按《白车身孔位描述书》和《零部件边界条件确认表》进行数据检查152车身无法焊装、车身运动干涉、车身异响、用户抱怨1三维数据检查未全面检查、运动校核未考虑实车精度、相关零部件未考虑到位5按《白车身自相关检查表》和《车身运动件运动校核检查表》进行数据校核6303整车外观效果差,无法满足客户需求,影响销售4设计间隙、面差不合理;装调不到位;公差分配不合理;定位方式设置不合理6参照相关车型合理设置DTS定义值,合理设置公差,合理设置定位方式6144数模校核,定位方案确定车身4增加模具费用,增加整车成本,影响利润1设计结构时未考虑后期开发车型的共用性5编制车身开发模块化说明,预先设计拓展车型结构方案6305零部件冲压起皱,翻边开裂,尖角争料,产品结构弱,易变形,尖角拉延破裂冲压负角,件拉延开裂,模具上修边刃口强度不足,影响车身性能5冲压SE分析未到位,钣金结构不合理4按《白车身SE审查报告》进行反馈及数模修改,合理设计钣金结构6120SE分析车身/制造6车身焊接操作性差,工人抱怨、生产率低,焊接效果差,影响车身性能5焊装SE分析未到位,钣金结构不合理4按《白车身SE审查报告》进行反馈及数模修改,合理设计钣金结构,合理布置焊点位置及层次2407车身电泳底漆厚度不均匀、部分区域未充分覆盖底漆、车身锈蚀、影响整车寿命5涂装SE分析未到位,钣金结构不合理4按《白车身SE审查报告》进行反馈及数模修改,合理设计钣金结构,保证涂装效果2408总装件无法安装;车身总装操作性差,工人抱怨、生产率低;零部件维修操作性差5总装SE分析未到位未分析可维修性4按《白车身SE审查报告》进行反馈及数模修改,合理设计钣金结构,合理考虑安装操作空间,进行安装虚拟验证2409影响用户乘车舒适性,影响内部载货空间,用户抱怨3未合理设计钣金结构,钣金侵占内部空间6进行CAE分析,在保证车身性能、安装结构的前提下尽量增大内部空间,可对比标杆设计7126初期确定目标值,后期按照执行,尽量加大内部空间车身/整车10影响用户乘车舒适性,影响内部装卸货方便性,用户抱怨3未合理设计钣金结构,未按人机要求设计6按人机要求设计数据,在保证车身性能、安装结构的前提下尽量改善,可对比标杆设计6108方案阶段确定各相关尺寸,保证后期数据满足要求。
系统总成DFMEA分析范例

系统:H06后视镜总成设计责任:子系统:关键日期:部件:车辆项目:团队:镜面曲率半径选择错误由于车门数据的改变,造成主机厂提供的线框数据中镜面位置不正确后视镜应满足GB15084-2013规定的反射率(≥80%)镜面太暗驾驶员看后视野时不清晰7●镜面反射率选择错误后视镜应满足GB15084-2013规定的(平均SR误差≤12.5%)镜面变形驾驶员看后视野时感觉不舒服7●镜面烤弯变形要求无未预期的风噪风噪过大或难听用户感觉刺耳不舒适3外形造型不好或镜壳与背盖间隙过大后视镜应耐腐蚀后视镜内金属件锈蚀后视镜内部零件外观不良2材料选择或表面处理不当在高温作用下,后视镜零部件(如塑料件、电机等)产生变形后视镜功能减弱或丧失(如镜面移位、不可调节/折叠、抖动等)6材料选择不合理在低温作用下,后视镜零部件(如塑料件、镜面等)产生开裂、变形等后视镜功能减弱或丧失(如镜面松动、不可调节/折叠、抖动等)6材料选择不合理部件/功能后视镜应满足GB15084-2013规定的视野视野范围小于国标GB15084-2013规定整车视野不合格或视野有盲区,不能上国家目录8●设计 FMEA H06后视镜应耐高温、低温和高湿度环境潜在失效模式失效的潜在影响严重度分级失效的潜在原因/机制在高温高湿度环境下,后视镜零部件(如塑料件、镜面等)产生开裂、变形等后视镜功能减弱或丧失(如镜面松动、不可调节/折叠、抖动等)6材料选择不合理后视镜应能耐冷热冲击在高温低温交变冲击的环境下,后视镜零部件(如塑料件、镜面等)产生开裂、变形等后视镜功能减弱或丧失(如镜面松动、不可调节/折叠、抖动等)6材料选择不合理镜杆应与镜臂牢固连接镜杆和镜臂配合和设计数据不符。
1:后视野模糊 。
2:后视镜镜壳与背盖,主镜和广角镜,镜头与镜臂之间的配合间隙不能满足要求。
6镜杆和镜臂配合设计不合理后视镜镜头能可靠折叠且折叠力适中镜头折叠力过大或过小折叠力过大:有外力撞击时不易折叠;折叠力过小:行车时易抖动7●下支座定位柱弹簧工作压力过大或过小对电调总成:电调镜面的手动调节力过小行车时镜头易抖动而使后视野模糊5电机选型不当,其承载力过小镜面托板分总成拔脱力过小或感觉到横向空程镜面易脱落或抖动,无镜面或后视野模糊7托板与电机卡簧配合不合理镜头应能经受反复折叠而保持折叠功能镜头反复折叠后有空程或折叠力明显下降,行车时镜头易抖动后视镜使用一段时间后,行车时镜头易抖动视野模糊4下镜臂的凹槽与支座上的凸台直接接触,在镜头折叠时被磨损电机工作及卡止时噪声可接受电调后视镜调节噪声过大用户感觉刺耳不舒适3调节电机选型不当6数模转换误差导致数据设计失误6车身冲压件存在反弹主机厂对后视镜装配的外观效果不满意镜面能够稳定连接在镜壳中,并能进行各方向的最小8度的调节支座分总成与车身安装后外观效果应良好后视镜安装在车身上后,上下支座与车身存在断差、间隙、错位等温、低温和高湿度环境6●支座安装尺寸错误电机与基板/广角镜壳装配完好电机与基板/广角镜壳配合安装孔径不正确电机无法安装6电机安装孔径比基板/广角镜壳安装孔大基板和广角镜壳准确定位广角镜壳与镜杆相对位置偏差广角镜头与其他相配合的零件配合间隙失控6广角镜头和镜杆没有自动找正结构基板和镜杆准确定位基板与镜杆相对位置偏差主镜头与其他相配合的零件配合间隙失控6基板和镜杆没有自动找正结构镜壳与托板在调节到极限角度时有干涉电机选择不合理为镜面提供电动调节功能使用一定时间后电机调节功能失效驾驶员无法利用镜面调节开关控制镜面4电机选择不合理配的外观效果不满意主镜面调节角度在各个方向均达到8度以上主镜面分总成调节角度不够有的驾驶员看不到符合法规要求的视野5车身安装后外观效果应良好上后,上下支座与车身存在断差、间隙、错位等FMEA 号:准备人员:FMEA 日期:根据GB15084-2013规定选择曲率半径:1.主镜面/SR1200+300。
变速器dfmea范例

异响,和损坏
其它组件。使 不能回位到空 用寿命满足整 档
不能换档
8
车要求
换档器总成弹簧力 偏小
根据换档力,类 比设计合适的弹 簧力
3
道路试验
2 48
跳、脱档
变速器功能部 分失效
7
锁止弹簧力偏小
根据换档力,类 比设计合适的弹 3 道路试验 簧力
2 42
系统:
子系统:
√ 项目
部件:变速器总成 1700100
功能
要求
潜在失效模式
失效模式的 潜在后果
潜在失效模式及后果分析
严重度
分 类
潜在失效起因/机理
现有设计 控制预防 发生率 控制探测
共 9 页,
第6页
措施结果
探测 RPN
建议措施
职责/目标完 成日期
采取的措施完
率
成日期
严 重 度
发 生 率
探 测 度
RPN
选档重,选换档 不到位
用户不接受
7
选换档支架
支承换档拉索总 成
系统:
子系统:
√
型号年/项 目: 项目
部件:变速器总成 1700100
功能
要求
潜在失效模式
失效模式的 潜在后果
潜在失效模式及后果分析
设计责任: 307项 目组
严重度
分 类
潜在失效起因/机理
现有设计 控制预防 发生率 控制探测
共 9 页,
第4页
编制:
措施结果
探测 RPN
建议措施
职责/目标完 成日期
采取的措施完
共 9 页,
第5页
编制:
措施结果
探测 RPN
DFMEA(设计FMEA)与 PFMEA(过程FMEA)简介范文

DFMEA(设计FMEA)与PFMEA(过程FMEA)简介何谓FMEAFMEA是一组系统化的活动,其目的是:ν发现、评价产品/过程中潜在的失效及其后果。
νν找到能够避免或减少这些潜在失效发生的措施。
书面总结上述过程。
ν为确保客户满意,这是对设计过程的完善。
νFMEA发展历史ν虽然许多工程技术人员早已在他们的设计或制造过程中应用了FMEA这一分析方法。
但首次正式应用FMEA技术则是在六十年代中期航天工业的一项革新。
FMEA的实施ϖ由于不断追求产品质量是一个企业不可推卸的责任,所以应用FMEA技术来识别并消除潜在隐患有着举足轻重的作用。
对车辆回收的研究结果表明,全面实施FMEA能够避免许多事件的发生。
ϖ虽然FMEA的准备工作中,每项职责都必须明确到个人,但是要完成FMEA还得依靠集体协作,必须综合每个人的智能。
例如,需要有设计、制造、装配、售后服务、质量及可靠性等各方面的专业人才。
ϖ及时性是成功实施FMEA的最重要因素之一,它是一个“事前的行为”,而不是“事后的行为”,为达到最佳效益,FMEA必须在设计或过程失效模式被无意纳入设计产品之前进行。
事前花时间很好地进行综合的FMEA分析,能够容易、低成本地对产品或过程进行修改,从而减轻事后修改的危机。
ϖϖ FMEA能够减少或消除因修改而带来更大损失的机会。
适当的应用FMEA是一个相互作用的过程,永无止境。
ϖDFMEA(设计FMEA)简介ν设计潜在FMEA是由“设计主管工程师/小组”早期采用的一种分析技术,用来在最大范围内保证已充份的考虑到并指明各种潜在失效模式及与其相关的起因/机理。
ν应评估最后的产品以及每个与之相关的系统、子系统和零部件。
ν FMEA以其最严密的形式总结了设计一个零部件、子系统或系统时,一个工程师和设计组的设计思想(其中包括,根据以往的经验和教训对一些环节的分析)。
ν这种系统化的方法与一个工程师在任何设计过程中正常经历的思维过程是一致的,并使之规范化、文件化。
DFMEA设计范例
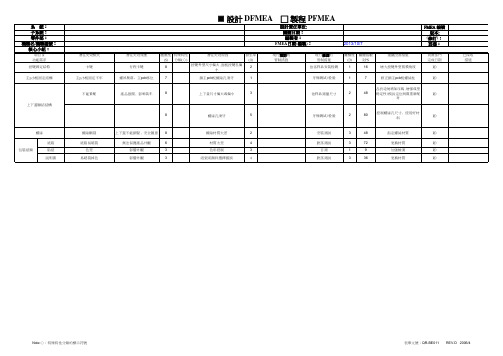
建議改善措施 增大按键外型拔模角度
牙规测试/检验
1
7
修正鎖主pcb板螺絲柱
負責部門 完成日期
RD
RD
產品張開﹐影响装车
8
上下盖尺寸偏大或偏小
3
各折边处增加压线.增强成型
依样品測量尺寸
2
48 稳定性/模具定位间隙重新配
RD
对
8
螺絲孔滑牙
5
牙规测试/检验
2
80
控制螺絲孔尺寸﹐使用好材 料
RD
螺絲斷裂
紙箱易破裂 色差
FMEA 編號 版本:
(修訂): 頁碼:
潛在失效效應 行程卡键
螺丝脱落,主pcb移位
嚴重度 特殊特性 (S) 分類(◇)
8
潛在失效原因
按键外型尺寸偏大.面板按键孔偏 小
發生率 (O)
2
7
鎖主pcb板螺絲孔滑牙
1
現行預防的 管制措施
現行檢測的 管制措施
依客样品安装检测
難檢度 關鍵指數
(D)
RPN
1
16
MEA □ 製程 PFMEA
A
1 of 1
嚴重度 發生率 難檢度 RPN (S) (O) (D)
Note:◇:特殊特性分類的標示符號
表單文號:QR-BE011 REV.D 2006/4
易破裂掉色
上下蓋不能鎖緊﹐安全隱患 8
無法保護產品外觀
6
影響外觀
3
影響外觀
3
螺絲材質太差
2
材質太差
4
色彩控制
3
紙張或顏料選擇錯誤
4
安裝測試
3
48
指定螺絲材質
RD
DFMEA范例

计工具(8)
蜡设备和规定 程师和装配 供3个额外的
汽车耐久性
的蜡
部门
通气孔(防
试验T-
0X 11 15 错)
118(7)
0X 12 15
7
空间不够,
容不下喷头
4 喷头作业的 4 112 利用辅助设计 车身工程师 评价显示充分 7 2 4 56
图样评定(4)
模型
和装配部门 的可进入空间
汽车耐久性
和喷头,增加 0X 11 15 0X 12 15
图
-
系统
X 子系统
潜在失效模式及后果分析
部件 01.03/车身密封 ⑵ 设计责任 车身工程部
⑶
(设计FMEA)
车型年/车辆类型 199X/狮牌 4门/旅行车 ⑸ 关键日期 9X年 03 01 ⑹ 核心小组 T.芬德-轿车产品开发部、切利得斯-制造部、J.福特-总装厂 (Dalton,Fraser, Henley 总装厂)
FMEA 编号 1234 ⑴ 共 1 页,第 1 页
编制人 泰特-X6412-车身工程师
⑷
FMEA 日期(原始)0X 07 22 0X 09 14 ⑺
⑻
项目
⑼
功能
要求
严
潜在失效模式
失效潜在影响
重 度
分 类
S
失效潜在 起因
探
现行设计 控制 预
频 度
现行设计 控制 探
测 度
RPN
防
O
测
D
建议措施
责任及目标 完成日期
性试验
蚀试验
程师
结果(1481号
不够 以及最佳实
T-118(7)
0X 09 03 试验),显示
液压泵DFMEA范例
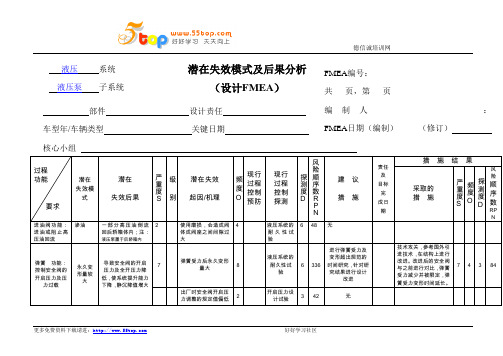
德信诚培训网过程功能要求潜在失效模式潜在失效后果严重度S级别潜在失效起因/机理频度O现行过程控制预防现行过程控制探测探测度D风险顺序数RPN建议措施责任及目标完成日期措施结果采取的措施严重度S频度O探测度D风险顺序数RPN进油阀功能:进油或阻止高压油回流渗油一部分高压油倒流回后轿箱体内;注:液压泵置于后轿箱内2 使用磨损,会造成阀体成阀座之间间隙过大4 液压系统的耐久性试验6 48 无弹簧功能:控制安全阀的开启压力及压力过载永久变形量较大导致安全阀的开启压力及全开压力降低,使系统提升能力下降,静沉降值增大7弹簧受力后永久变形量大8液压系统的耐久性试验6 336进行弹簧受力及变形超出规范的时间研究,针对研究结果进行设计改进技术攻关,参考国外引进技术,在结构上进行改进。
改进后的安全阀与之前进行对比,弹簧受力减少并被限定,弹簧受力变形时间延长。
7 4 3 84出厂时安全阀开启压力调整的规定值偏低2开启压力设计试验3 42 无潜在失效模式及后果分析(设计FMEA)FMEA编号:共页,第页编制人:FMEA日期(编制)(修订)液压系统液压泵子系统部件设计责任年车型年/车辆类型关键日期年核心小组柱塞与缸体功能:柱塞在缸体内作往复运动,完成吸油与压油工作过程泄漏压油量减少,输出压力降低3 使用磨损,会造成阀体成阀座之间间隙过大2 液压系统的耐久性试验6 36 无偏心轮与柱塞架功能:偏心轮带动柱塞架作往复运动卡死柱塞架碎裂使柱塞不能完成吸油和压油8 在重载荷时,油温过高,易出现偏心轮在衬套内卡死造成柱塞架碎裂。
6 台架试验8 384 柱塞架材料试验,寻找提高材料韧性并价格合适的材料……经过试验设计及对比试验结果,选定新材料。
结果使强度好于之前的设计。
8 4 3 96偏心轴衬功能:偏心轮通过偏心轴衬,带动柱塞架往复运动磨损快由于偏心轴衬磨损,使活塞行程缩短,压油量减少。
3 偏心轴衬为铜衬套,材质及加工达不到设计要求时,磨损过快,长期使用时也会使轴衬磨损量增大4 8 96 无以下是关于XX系统XX子系统的车门部件的设计FMEA的例子左前车门H8HX-0000-A·上、下车·保护乘员免受天气、噪声侧碰撞的影响车门附件视镜、门锁、门铰链及门窗升降器等的固定支撑·为外观项目提供适当的表面·喷漆和软内饰车门内板下部腐蚀车门寿命降低,导致:·因漆面长期生锈,使顾客对外观不满·使车门内附件功能降低7 车门内板保护蜡上边缘规定得太低6 整车耐久性试验7 294 增加实验室强化腐蚀试验根据试验结果(1481号试验),上边缘规范增加125cm7 2 2 287 蜡层厚度规定不足 4 整车耐久性试验同上7 196 增加实验室强化腐蚀试验对蜡层厚度进行实验设计(DOE)结合观察和试验验证蜡的上边缘-试验结果(1481号试验)表明要求的厚度是充分的。
FMEA手册上的完整案例(DFMEA)

R DP
N 3 30
3 30
3 30
角落设计使得喷 涂设备无法覆盖 所有需喷涂区域
车门板之间空间 不够,容不下喷 头
5 用非功能喷头进 7 175 利用正式量产喷 车身工程部和总 基于试验结果:在 5 1 1 5
行设计辅助调查;
腊设备和特定的 装厂
受影响的区域增加3
整车耐久性试验
标要求不够
(#31268)
T-118(7)
以及最佳实
践
(BP3455)
探R 测P 度N D
建议措施
7 105 增加实验室加速 腐蚀试验
7 105 增加实验室强化 腐蚀试验
对蜡层厚度进行 实验设计(DOE)
蜡的配方规定得 行业标准
不当
MS-1893
2 理化实验室实验- 5 报告NO1265; 整车耐久性试验 T-118(7)
50 无
职责和目标 完成日期
实施结果
采取的措施 完成日期
SO
泰特-车身工程 根据试验结果(4- 5 2
师
484号试验)上边缘
2008-9-03
规范增加125mm。
2008-09-03
泰特-车身工程 试验结果(4-484号 5 2
师
试验)表明要求的
2008-9-03
厚度是充分的。
2008-9-03
J.Smthye 车身 实验设计表明规定 5 2 设计工程师 的厚度变差在25%范 2008-10-18 围内可以接受。
饰板的完整 间,5年 不生锈、 腐蚀
锈,使顾客对 外观不满 ②损害车门内 附Βιβλιοθήκη 件严重 度
分 类
潜在失效原因
S
设计FMEA(DFMEA)

三、DFMEA是一項活頁文件,在設計階段應完成制訂,並且在生產階段時持續修訂,DFMEA要考慮易製性和易裝性,因此必須靠製程管製法找出設計弱點。
四、DFMEA首先要利用QFD,將顧客需求轉成設計規格,使用功能方塊圖,利用流程方式,將各另組件間的功能關係(輸出、輸入)連貫起來,接著再使用結構樹,將另件層、組件層與系統層依序劃分,作為DFMEA制訂之依據。
2.潛在效應分析
失效模式產生後對功能之影響性,效應分析必須從另件失效後一直探討至產品之影響性,必須要 有整體性,故是一項term work。 嚴重度:失效模式發生後,對本身、上一層組件或顧客之影響程度。要降低嚴重度,唯有透過設計變更。
3.潛在失效原因
失效原因是一項設計弱點的指標,設計弱點的結果就是失效模式。 發生度:失效原因發生之可能機率。透過設計變更,可以降低發生度。
3.在設計發展階段,增加失效模式和系統效應分析的次數。
4.提供另一項分析方法,幫助設計者進行有效的驗證規劃。
5.根據對顧客需求的影響性,列出失效模式的排序,並按序改善。
6.提供一項改善方案,可以減少矯正與追查的活動。
7.提供更好的參考資料,協助現場解決問題,評估設計變更和發展進一步的設計。
6.嚴重度在9分及10分者,不論RPN之分數,應優 先改進,接著依RPN之高低逐項改善,改進步驟依降低嚴重度,發生度與難檢度之順利進行。
難檢度:失效模式及失效原因被偵測出之能力(在另組件生產之前)。為降低難檢度,適當的設計管制措施必須加以改進。
5.RPN
6.矯正措施
j增加設計驗證或確認,可以降低難檢度。
【最新2018】dfmea范例-word范文模板 (3页)

本文部分内容来自网络整理,本司不为其真实性负责,如有异议或侵权请及时联系,本司将立即删除!== 本文为word格式,下载后可方便编辑和修改! ==dfmea范例篇一:发电机DFMEA范例潜在失效模式及后果分析(设计FMEA)_____________系统 FMEA编号:_____________子系统页码:__第 _1 _ 页共 __10 _ 页_____________零组件: _发电机总成 _设计责任:编制者:主管工程师:______ 车型年度/车辆类型:___________关健日期:____ _____ FMEA日期:编制:修订:_____________系统 FMEA编号:_____________子系统页码:__第 _2 _ 页共 __10 _ 页 _____________零组件: _发电机总成 _ 设计责任:汽配技术部编制者: _____ 车型年度/车辆类型:___ _________关健日期:__________ FMEA日期:_____________系统 FMEA编号:_____________子系统页码:__第 _3 _ 页共 __10 _ 页 _____________零组件:_ 定子总成 _ 设计责任:汽配技术部编制者:_____车型年度/车辆类型:____________关健日期:____201X.9.6 ______ FMEA日期:编制:13.08.25 修订:13.09. 12_____________系统 FMEA编号:_____________子系统页码:__第 _4 _ 页共 __10 _ 页 _____________零组件: _ 定子铁芯 _ 设计责任:汽配技术部编制者:_____车型年度/车辆类型:____________关健日期:____201X.9.6 ______ FMEA日期:编制:13.08.25 修订:13.09. 12潜在失效模式及后果分析(设计FMEA)_____________系统 FMEA编号:_____________子系统页码:__第 _5 _ 页共 __10 _ 页 _____________零组件:_ 转子总成 _ 设计责任:汽配技术部编制者:_____车型年度/车辆类型:____________关健日期:____201X.9.6 ______ FMEA日期:编制:13.08.25 修订:13.09. 12篇二:DFMEA 案例XXXX有限公司系统子系统潜在失效模式及后果分析(设计FMEA)FMEA编号:共页,第页制人:部件设计责任编车型年/车辆类型关键日期 FMEA日期(编制)(修订)核心小组设计潜在失效模式及后果分析DFMEA 第 1 页共 2 页设计潜在失效模式及后果分析DFMEA 第 2 页共 2 页篇三:DFMEA_案例潜在失效模式及后果分析FMEA编号:共页,第页编。
发电机DFMEA范例

潜在失效模式及后果分析(设计FMEA)_____________系统 FMEA编号:_____________子系统页码:__第 _1 _ 页共 __10 _ 页_____________零组件: _发电机总成 _ 设计责任:编制者:主管工程师: ______ 车型年度/车辆类型:__ _________ 关健日期:____ _____ FMEA日期:编制:修订:_____________系统 FMEA编号:_____________子系统页码:__第 _2 _ 页共 __10 _ 页_____________零组件: _发电机总成 _ 设计责任:汽配技术部编制者: _____ 车型年度/车辆类型:___ _________ 关健日期:____ ______ FMEA日期:_____________系统 FMEA编号:_____________子系统页码:__第 _3 _ 页共 __10 _ 页_____________零组件:_ 定子总成 _ 设计责任:汽配技术部编制者: _____车型年度/车辆类型:____________ 关健日期:____2013.9.6 ______ FMEA日期:编制:13.08.25 修订:13.09. 12_____________系统 FMEA编号:_____________子系统页码:__第 _4 _ 页共 __10 _ 页_____________零组件: _ 定子铁芯 _ 设计责任:汽配技术部编制者: _____车型年度/车辆类型:____________ 关健日期:____2013.9.6 ______ FMEA日期:编制:13.08.25 修订:13.09. 12潜在失效模式及后果分析(设计FMEA)_____________系统 FMEA编号:_____________子系统页码:__第 _5 _ 页共 __10 _ 页_____________零组件:_ 转子总成 _ 设计责任:汽配技术部编制者: _____车型年度/车辆类型:____________ 关健日期:____2013.9.6 ______ FMEA日期:编制:13.08.25 修订:13.09. 12潜在失效模式及后果分析(设计FMEA)_____________系统 FMEA编号:_____________子系统页码:__第 _6 _ 页共 __10 _ 页_____________零组件: _ 转子总成 _ 设计责任:汽配技术部编制者: _____车型年度/车辆类型:____________ 关健日期:____2013.9.6 ______ FMEA日期:编制:13.08.25 修订:13.09. 12潜在失效模式及后果分析(设计FMEA)_____________系统 FMEA编号:_____________子系统页码:__第 _7 _ 页共 __10 _ 页_____________零组件:_ 调节器 _ 设计责任:汽配技术部编制者: _____车型年度/车辆类型:____________ 关健日期:____2013.9.6 ______ FMEA日期:编制:13.08.25 修订:13.09. 12潜在失效模式及后果分析(设计FMEA)_____________系统 FMEA编号:_____________子系统页码:__第 _8 _ 页共 __10 _ 页_____________零组件: _ 整流桥 _ 设计责任:汽配技术部编制者: _____车型年度/车辆类型:____________ 关健日期:____2013.9.6 ______ FMEA日期:编制:13.08.25 修订:13.09. 12潜在失效模式及后果分析(设计FMEA)_____________系统 FMEA编号:_____________子系统页码:__第 _9 _ 页共 __10 _ 页_____________零组件: _ 前端盖 _ 设计责任:汽配技术部编制者: _____车型年度/车辆类型:____________ 关健日期:____2013.9.6 ______ FMEA日期:编制:13.08.25 修订:13.09. 12潜在失效模式及后果分析(设计FMEA)_____________系统 FMEA编号:_____________子系统页码:__第 _10 _ 页共 __10 _ 页_____________零组件: _ 后端盖 _ 设计责任:汽配技术部编制者: _____车型年度/车辆类型:____________ 关健日期:____2013.9.6 ______ FMEA日期:编制:13.08.25 修订:13.09. 12。
系统总成DFMEA分析范例

系统:H06后视镜总成设计责任:子系统:关键日期:部件:车辆项目:团队:镜面曲率半径选择错误由于车门数据的改变,造成主机厂提供的线框数据中镜面位置不正确后视镜应满足GB15084-2013规定的反射率(≥80%)镜面太暗驾驶员看后视野时不清晰7●镜面反射率选择错误后视镜应满足GB15084-2013规定的(平均SR误差≤12.5%)镜面变形驾驶员看后视野时感觉不舒服7●镜面烤弯变形要求无未预期的风噪风噪过大或难听用户感觉刺耳不舒适3外形造型不好或镜壳与背盖间隙过大后视镜应耐腐蚀后视镜内金属件锈蚀后视镜内部零件外观不良2材料选择或表面处理不当在高温作用下,后视镜零部件(如塑料件、电机等)产生变形后视镜功能减弱或丧失(如镜面移位、不可调节/折叠、抖动等)6材料选择不合理在低温作用下,后视镜零部件(如塑料件、镜面等)产生开裂、变形等后视镜功能减弱或丧失(如镜面松动、不可调节/折叠、抖动等)6材料选择不合理部件/功能后视镜应满足GB15084-2013规定的视野视野范围小于国标GB15084-2013规定整车视野不合格或视野有盲区,不能上国家目录8●设计 FMEA H06后视镜应耐高温、低温和高湿度环境潜在失效模式失效的潜在影响严重度分级失效的潜在原因/机制在高温高湿度环境下,后视镜零部件(如塑料件、镜面等)产生开裂、变形等后视镜功能减弱或丧失(如镜面松动、不可调节/折叠、抖动等)6材料选择不合理后视镜应能耐冷热冲击在高温低温交变冲击的环境下,后视镜零部件(如塑料件、镜面等)产生开裂、变形等后视镜功能减弱或丧失(如镜面松动、不可调节/折叠、抖动等)6材料选择不合理镜杆应与镜臂牢固连接镜杆和镜臂配合和设计数据不符。
1:后视野模糊 。
2:后视镜镜壳与背盖,主镜和广角镜,镜头与镜臂之间的配合间隙不能满足要求。
6镜杆和镜臂配合设计不合理后视镜镜头能可靠折叠且折叠力适中镜头折叠力过大或过小折叠力过大:有外力撞击时不易折叠;折叠力过小:行车时易抖动7●下支座定位柱弹簧工作压力过大或过小对电调总成:电调镜面的手动调节力过小行车时镜头易抖动而使后视野模糊5电机选型不当,其承载力过小镜面托板分总成拔脱力过小或感觉到横向空程镜面易脱落或抖动,无镜面或后视野模糊7托板与电机卡簧配合不合理镜头应能经受反复折叠而保持折叠功能镜头反复折叠后有空程或折叠力明显下降,行车时镜头易抖动后视镜使用一段时间后,行车时镜头易抖动视野模糊4下镜臂的凹槽与支座上的凸台直接接触,在镜头折叠时被磨损电机工作及卡止时噪声可接受电调后视镜调节噪声过大用户感觉刺耳不舒适3调节电机选型不当6数模转换误差导致数据设计失误6车身冲压件存在反弹主机厂对后视镜装配的外观效果不满意镜面能够稳定连接在镜壳中,并能进行各方向的最小8度的调节支座分总成与车身安装后外观效果应良好后视镜安装在车身上后,上下支座与车身存在断差、间隙、错位等温、低温和高湿度环境6●支座安装尺寸错误电机与基板/广角镜壳装配完好电机与基板/广角镜壳配合安装孔径不正确电机无法安装6电机安装孔径比基板/广角镜壳安装孔大基板和广角镜壳准确定位广角镜壳与镜杆相对位置偏差广角镜头与其他相配合的零件配合间隙失控6广角镜头和镜杆没有自动找正结构基板和镜杆准确定位基板与镜杆相对位置偏差主镜头与其他相配合的零件配合间隙失控6基板和镜杆没有自动找正结构镜壳与托板在调节到极限角度时有干涉电机选择不合理为镜面提供电动调节功能使用一定时间后电机调节功能失效驾驶员无法利用镜面调节开关控制镜面4电机选择不合理配的外观效果不满意主镜面调节角度在各个方向均达到8度以上主镜面分总成调节角度不够有的驾驶员看不到符合法规要求的视野5车身安装后外观效果应良好上后,上下支座与车身存在断差、间隙、错位等FMEA 号:准备人员:FMEA 日期:根据GB15084-2013规定选择曲率半径:1.主镜面/SR1200+300。
集成声卡芯片DFMEA分析范例

6
电容来料不良、污 染、焊接桥接
2
IQC检查、QC外观 检验
6
设计人员对ALC 655 datasheet未认真核 对造成原理图错误
9
原理图评审,样 板调测、中试
PCB layout
数字、模拟地未隔离、 EMI超标 未采用单点接地措施 信号干扰
6
layout工程师没有 数字、模拟地的区 分概念/布线粗心
难 检R 度 PN D
建议控制措施
行动结果
责任者/目标完
R
成日
已采取的行动 S O D P
N
2 28
N/A
将EMC对电容layout
2
70
要求列入 PCB Checklist中,评审
时重点检查
付纪忠 2008-3-20
已列入 checklist中供 7 2 2 28 评审参考
2 28
N/A
1 12
N/A
将CD-GND要求加入模 1 54 块checklist中;加
强设计人员培训
张建明 2008.3.15
已列入 checklisBiblioteka 中;621
12
3
将LAYOUT要求加入设
计规范、checklist
72
中,列入PCB评审重 点检查项目,加强培
训宣导,增加ICT测
试
张建明/付纪 忠
2008.3.15
将LAYOUT要求 加入设计规范 、checklist 中,列入PCB评 6 审重点检查项 目,加强培训 宣导
1
3 18
4 48 N/A
1 28 N/A
建立连接器器标准 1 56 库,在库中增加3D图
或图片标识 安排专人对版本控制 管理,制定软件版本 8 144 管理规范或使用说明 书 定时更新驱动程序
汽车音响编码器设计DFMEA范例

RPN 本体刷子折弯角度3度设计错误2参考同类型成熟产品的设计本体刷子角度1.用专业的3D和2D软件对信号输出进行模拟试验;2.用测试盒对信号进行检测336无波动盘五金片与塑胶面角度设计错误2参考同类型成熟产品的设计波动盘五金片与塑胶面的角度1.用专业的3D和2D软件对信号输出进行模拟试验;2.用测试盒对信号进行检测336无波动盘五金片与塑胶面落差设计过大31、参考同类型成熟产品的设计;2、在图面上规定五金片与塑胶面落差值1.用高度规测试落差值的大小,2.组装成品测试信号472无本体信号输出A、B、C脚设计错误2根据客户提供的规格书进行设计信号输出脚1.图纸评审;2.用测试盒对信号进行检测336无本体刷子折弯角度3度设计错误2参考同类型成熟产品的设计本体刷子角度1.用专业的3D和2D软件对信号输出进行模拟试验;2.用测试盒对信号进行检测330无波动盘五金片与塑胶面角度设计错误2参考同类型成熟产品的设计波动盘五金片与塑胶面的角度1.用专业的3D和2D软件对信号输出进行模拟试验;2.用测试盒对信号进行检测330无波动盘五金片毛刺过大31、参考同类型成熟产品的设计;2、在图面上规定五金片毛刺大小1.用二次元测试毛刺大小,2.组装成品测试信号460无波动盘五金片格子同心度过大31、参考同类型成熟产品的设计;2、在图面上规定五金片同心度大小1.用菲林检测五金片同心度的大小,2.用测试盒对信号进行检测460无波动盘五金片与塑胶面落差过大31、参考同类型成熟产品的设计;2、在图面上规定五金片与塑胶面落差值1.用高度规测试落差值的大小,2.组装成品测试信号460无音量无法调大、调小无功能、无法完成调节,客户不满意6▲调节功能下降,影响客户使用,客户不满意探测度D潜在失效模式潜在失效后果潜在失效起因/机理现行设计控制- 预防建议措施现行设计控制- 探测功能要求严重度S级别频度O设计FMEA表系统潜在失效模式及后果 FMEA编号编码器子系统(设计FMEA)部件 RE1103编码器设计责任工程1部编制人 批准人车型年/车辆类型关键日期 FEMA日期(编制)(修订)核心小组详见多功能小组任命单措施结果采取的措施S O D RPN责任及目标完成日期调节音量不连续5本体五金毛刺面选择错误21、参考同类型成熟产品的设计; 1.产品设计成不对称型,2.塑胶模及五金冲压模按防保要求设计220无本体刷子自由高度偏低31、参考同类型成熟产品的设计;2、在图面上规定刷子的自由高度 1.用专业的3D和2D软件对信号输出进行模拟试验;2.组装成品做寿命测试460无波动盘五金片格子数设计错误2依客户提供的规格书上的脉冲数设计 1.图纸评核;2.用测试盒对信号进行检测330无波动盘定位齿数设计错误2依客户提供的规格书上的定位数设计 1.图纸评核;2.用测试盒对信号进行检测330无波动盘定位齿不均匀2参考同类成熟产品设计波动盘齿高的公差1、定位齿测试;2、旋转手感检测540无波动盘与轴套配合部位间隙过小3查公差等极表,选择合理的公差等极1.用专业的3D和2D软件对波动盘与轴套进行模拟试验;2.旋转手感检测448无波动盘与轴套配合部位同心度偏差大3参考同类成熟产品设计波动盘的同心度 1.用专业的3D和2D软件对波动盘进行模拟试验;2.旋转手感检测448无轴套与波动盘配合部位同心度大3参考同类成熟产品设计轴套的同心度 1.用专业的3D和2D软件对轴套进行模拟试验;2.旋转手感检测448无弹片苞点对称度差3参考同类成熟产品设计弹片苞点的对称度旋转手感检测560无弹片苞点的荷重力偏大5参考同类成熟产品设计弹片荷重力大小1、荷重力测试;2、旋转力矩测试5100无弹片苞点设计过小4参考同类成熟产品设计弹片苞点的大小1.用专业的3D和2D软件对弹片苞点与波动盘定位槽进行模拟;2.旋转力矩测试448无弹片厚度设计过厚3参考同类成熟产品设计弹片厚度旋转力矩测试448无弹片自由高度设计过度3参考同类成熟产品设计弹片自由高度 1.用专业的3D和2D软件对弹片工作高度进行模拟;2.旋转力矩测试336无44▲产品旋转周时,音量调节无法达到客户需求的效果。
DFMEA程序文件

版本A1說新發行明提案審查核准新產品開發試作階段,利用 FMEA 不良模式與效應分析事先提出預防措施,從而降低設計過程失效風險,使產品的品質和交期滿足客戶要求.所有新產品在開發設計初期均適用。
3.1設計FMEA 制訂:研發工程師;3.2設計 FMEA審查:新產品開發小組研(發工程師、品保部及其它部門相關人員組成) 。
;3.3設計FMEA 核準:研發部部門主管。
4.1 FMEA:Failure Mode and Effective Analysis ,失效模式及有效性分析;DFMEA:Design Failure Mode and Effective Analysis設,計失效模式及有效性分析 ;4.2 失效4.2.1在規定條件下(環境、操作、時間等)不能完成既定功能;4.2.2在規定條件下,產品參數值不能維持在規定的上下限之間。
4.2.3 產品在工作範圍內,導致零組件如破裂、斷裂等正常規範以外之異常現象均屬之。
4.3 系統:此處專指 FMEA 之對象物,或者為零件之某部位、或者為零件、或者為組合、或者為總成、或者為機構…。
4.3.1 子系統:系統之構成件,如零件之對組合,組合之對總成等,為上游工程(前製程)狀態。
5.1研發工程師負責召集各相關單位人員由(各單位指派)成立新產品開發小組; 5.2研發工程師負責制定 DFMEA計劃開,發小組成員的職責並負責小組活動的安排;5.3.DFMEA 表製作說明 :5.3.1 DFMEA 編號:設計 FMEA 表編號原則參照工程部編碼原則由工程文管統一編碼。
5.3.2 零組件名稱:填入想要分析設計之產品名稱及其零件名稱。
5.3.3設計責任者:填入設計擔當者名稱或者設計小組名稱,也可是協力廠名稱。
5.3.4 制定日期:填入最初 DFMEA被完成日期。
5.3.5 生效日期:填入 DFMEA發佈日期。
該日期不能超過開始計劃生產日期。
5.3.6修改日期:填入最初 DFMEA被完成日期。
电子燃油泵系统 DFMEA 范本.

潜在失效模式及后果分析(设计DFMEA)99新秀电子燃油泵系统进油板组合子系统FMEA编号:RLSP005-2009 进油板零件DZRYB001.00.01.01设计责任部门:产品开发部页码:共 25 页第 1 页车型年/车辆类型:关键日期:2009.10.9 编制者XXX主要参与人XXX、XXX、XXX、XXX、XX日期(编制):2009.10.6(修订):潜在失效模式及后果分析(设计DFMEA)99新秀电子燃油泵系统进油板组合子系统FMEA编号:RLSP005-2009 销钉零件DZRYB001.00.01.02设计责任部门:产品开发部页码:共 25 页第 2 页车型年/车辆类型:关键日期: 2009.10.9 编制者XXX潜在失效模式及后果分析(设计DFMEA)99新秀电子燃油泵系统外壳装配子系统FMEA编号:RLSP005-2009 叶轮零件DZRYB001.00.02.01设计责任部门:产品开发部页码:共 25 页第 3 页车型年/车辆类型:关键日期: 2009.10.6 编制者XXX潜在失效模式及后果分析(设计DFMEA)99新秀电子燃油泵系统出油板组合子系统FMEA编号:RLSP005-2009 轴承(大)零件DZRYB001.00.02.02.01设计责任部门:产品开发部页码:共 25 页第 4 页车型年/车辆类型:关键日期: 2009.10.9 编制者XXX主要参与人XXX、XXX、XXX、XXX、XX日期(编制):2009. 10.6(修订):潜在失效模式及后果分析(设计DFMEA)99新秀电子燃油泵系统出油板组合子系统FMEA编号:RLSP005-2009 出油板零件DZRYB001.00.02.02.02设计责任部门:产品开发部页码:共 25 页第 5 页车型年/车辆类型:关键日期:2009.10.9 编制者XXX主要参与人XXX、XXX、XXX、XXX、XX日期(编制):2009. 10.6(修订)潜在失效模式及后果分析(设计DFMEA)99新秀电子燃油泵系统外壳组合子系统FMEA编号:RLSP005-2009 电枢组件零件DZRYB001.00.02.03设计责任部门:产品开发部页码:共 25 页第 6 页车型年/车辆类型:关键日期:2009.10.9 编制者XXX主要参与人XXX、XXX、XXX、XXX、XX日期(编制):2009. 10.6(修订)潜在失效模式及后果分析(设计DFMEA)99新秀电子燃油泵系统磁瓦装配子系统FMEA编号:RLSP005-2009 磁瓦弹性夹零件DZRYB001.00.02.04.02设计责任部门:产品开发部页码:共 25 页第 8 页车型年/车辆类型:关键日期: 2009.10.9 编制者XXX主要参与人XXX、XXX、XXX、XXX、XX日期(编制):2009.10.6(修订)潜在失效模式及后果分析(设计DFMEA)99新秀电子燃油泵系统连接器组合子系统FMEA编号:RLSP005-2009 止动器零件DZRYB001.00.02.04.03.01.01设计责任部门:产品开发部页码:共 25 页第 9 页车型年/车辆类型:关键日期: 2009.10.9 编制者XXX主要参与人XXX、XXX、XXX、XXX、XX日期(编制):2009.10.7(修订)潜在失效模式及后果分析(设计DFMEA)99新秀电子燃油泵系统连接器组合子系统FMEA编号:RLSP005-2009 单向阀弹簧零件DZRYB001.00.02.04.03.01.02设计责任部门:产品开发部页码:共 25 页第 10 页车型年/车辆类型:关键日期:2009.10.9 编制者XXX主要参与人XXX、XXX、XXX、XXX、XX日期(编制):2009.10.7(修订)潜在失效模式及后果分析(设计DFMEA)99新秀电子燃油泵系统连接器组合子系统FMEA编号:RLSP005-2009 单向阀头组件零件DZRYB001.00.02.04.03.01.03设计责任部门:产品开发部页码:共 25 页第 11 页车型年/车辆类型:关键日期: 2009.10.9 编制者XXX主要参与人XXX、XXX、XXX、XXX、XX日期(编制):2009.10.7(修订)潜在失效模式及后果分析(设计DFMEA)99新秀电子燃油泵系统连接器组合子系统FMEA编号:RLSP005-2009 连接器件零件DZRYB001.00.02.04.03.01.04设计责任部门:产品开发部页码:共 25 页第 12 页车型年/车辆类型:关键日期:2009.10.9 编制者XXX主要参与人XXX、XXX、XXX、XXX、XX日期(编制):2009.10.7(修订)潜在失效模式及后果分析(设计DFMEA)99新秀电子燃油泵系统连接器组合子系统FMEA编号:RLSP005-2009 金属板零件DZRYB001.00.02.04.03.01.05设计责任部门:产品开发部页码:共 25 页第 13 页车型年/车辆类型:关键日期: 2009.10.9 编制者XXX主要参与人XXX、XXX、XXX、XXX、XX日期(编制):2009.10.7(修订)潜在失效模式及后果分析(设计DFMEA)99新秀电子燃油泵系统连接器组合子系统FMEA编号:RLSP005-2009 安全阀弹簧零件DZRYB001.00.02.04.03.01.05设计责任部门:产品开发部页码:共 25 页第 14 页车型年/车辆类型:关键日期:2009.10.9 编制者XXX主要参与人XXX、XXX、XXX、XXX、XX日期(编制):2009.10.7(修订)潜在失效模式及后果分析(设计DFMEA)99新秀电子燃油泵系统轴承固定架装配子系统FMEA编号:RLSP005-2009 右接线片零件DZRYB001.00.02.04.03.02.01 设计责任部门:产品开发部页码:共 25 页第 15 页车型年/车辆类型:关键日期: 2009.10.9 编制者XXX主要参与人XXX、XXX、XXX、XXX、XX日期(编制):2009.10.7(修订)潜在失效模式及后果分析(设计DFMEA)99新秀电子燃油泵系统轴承固定架装配子系统FMEA编号:RLSP005-2009 右电感组件零件DZRYB001.00.02.04.03.02.01 设计责任部门:产品开发部页码:共 25 页第 16 页车型年/车辆类型:关键日期: 2009.10.9 编制者XXX主要参与人XXX、XXX、XXX、XXX、XX日期(编制):2009.10.7(修订)潜在失效模式及后果分析(设计DFMEA)99新秀电子燃油泵系统轴承固定架装配子系统FMEA编号:RLSP005-2009 右碳刷接线片零件DZRYB001.00.02.04.03.02.03 设计责任部门:产品开发部页码:共 25 页第 17 页车型年/车辆类型:关键日期: 2009.10.9 编制者XXX主要参与人XXX、XXX、XXX、XXX、XX日期(编制):2009.10.7(修订)潜在失效模式及后果分析(设计DFMEA)99新秀电子燃油泵系统轴承固定架装配子系统FMEA编号:RLSP005-2009 左接线片零件DZRYB001.00.02.04.03.02.04 设计责任部门:产品开发部页码:共 25 页第 18 页车型年/车辆类型:关键日期: 2009.10.9 编制者XXX主要参与人XXX、XXX、XXX、XXX、XX日期(编制):2009.10.7(修订)潜在失效模式及后果分析(设计DFMEA)99新秀电子燃油泵系统轴承固定架装配子系统FMEA编号:RLSP005-2009 左电感组件零件DZRYB001.00.02.04.03.02.06 设计责任部门:产品开发部页码:共25 页第 19 页车型年/车辆类型:关键日期:2009.10.9 编制者XXX主要参与人XXX、XXX、XXX、XXX、XX日期(编制):2009.10.8(修订)潜在失效模式及后果分析(设计DFMEA)99新秀电子燃油泵系统轴承固定架装配子系统FMEA编号:RLSP005-2009左碳刷接线片零件DZRYB001.00.02.04.03.02.06 设计责任部门:产品开发部页码:共 25 页第 20 页车型年/车辆类型:关键日期: 2009.10.9 编制者XXX主要参与人XXX、XXX、XXX、XXX、XX日期(编制):2009.10.8(修订)潜在失效模式及后果分析(设计DFMEA)99新秀电子燃油泵系统轴承固定架组合子系统FMEA编号:RLSP005-2009 碳刷弹簧零件DZRYB001.00.02.04.03.02.07设计责任部门:产品开发部页码:共25 页第 21 页车型年/车辆类型:关键日期: 2009.10.9 编制者 XXX主要参与人XXX、XXX、XXX、XXX、XX日期(编制):2009.10.8(修订)潜在失效模式及后果分析(设计DFMEA)99新秀电子燃油泵系统轴承固定架组合子系统FMEA编号:RLSP005-2009 碳刷零件DZRYB001.00.02.04.03.02.08设计责任部门:产品开发部页码:共 25 页第 22 页车型年/车辆类型:关键日期: 2009.10.9 编制者XXX主要参与人XXX、XXX、XXX、XXX、XX日期(编制):2009.10.8(修订)潜在失效模式及后果分析(设计DFMEA)99新秀电子燃油泵系统轴承固定架组合子系统FMEA编号:RLSP005-2009 轴承固定架零件DZRYB001.00.02.04.03.02.09设计责任部门:产品开发部页码:共 25 页第 23 页车型年/车辆类型:关键日期: 2009.10.9 编制者XXX主要参与人XXX、XXX、XXX、XXX、XX日期(编制):2009.10.8(修订)潜在失效模式及后果分析(设计DFMEA)99新秀电子燃油泵系统轴承固定架组合子系统FMEA编号:RLSP005-2009 轴承(小)零件DZRYB001.00.02.04.03.02.09-1 设计责任部门:产品开发部页码:共 25 页第 24 页车型年/车辆类型:关键日期: 2009.10.9 编制者XXX主要参与人XXX、XXX、XXX、XXX、XX日期(编制):2009.10.8(修订)潜在失效模式及后果分析(设计DFMEA)99新秀电子燃油泵系统外壳组合子系统FMEA编号:RLSP005-2009 外壳零件DZRYB001.00.02.04.03.03设计责任部门:产品开发部页码:共 25 页第25 页车型年/车辆类型:关键日期: 2009.10.9 编制者XXX潜在失效模式及后果分析(设计DFMEA)99新秀电子燃油泵系统磁瓦组合子系统FMEA编号:RLSP005-2009 磁瓦零件DZRYB001.00.02.04.01 设计责任部门:产品开发部页码:共 25 页第 7 页车型年/车辆类型:关键日期: 2009.10.9 编制者XXX主要参与人XXX、XXX、XXX、XXX、XX。
设计FMEA案例 - 传动轴滑动密封DFMEA分析编写过程

整车有 缺陷 动力传动 有缺陷
发动机 传动器 有缺陷 离合器
驱动轴 有缺陷
有失效功能的整车系统结构
齿轮 有缺陷
案例——产品系统FMEA
第一步
系统结构与系统单元
传动器壳体 发动机 中间轴
车身
动力传动 汽车
离合器*
传动器
主轴/从动轴
输入轴总成 油封* 润滑材料*
……
…… …… * 外协件
输入轴总成
后果 无法保证有利于 环境且功能可靠 的运行 失效模式 无法通过油封达 到符合功能要求 的密封 缺陷原因 无法保证油封的 油膜结构
产品系统 FMEA
滑动油封
后果 失效模式 无法保证油封的 油膜结构 缺陷原因 滑动面磨损
设计FMEA (基于组件的系统FMEA)
无法通过油封达 到符合功能要求 的密封
传动器系统结构
案例——产品系统FMEA
功能与功能结构
第二步
车身 …… 发动机 …… 离合器*
保证传递/切断发动机与 传动器间的驱动功率
…… …… …… ……
汽车
保证符合 产品建议 书要求的 无故障/ 经济行驶
传动系统
保证汽车 的驱动 ……
……
传动器 保证有利于环境且无 故障的运行 保证各档位的扭矩变 换/转速变换 …… ……
未符合功能/无间隙地 安装油封
[滑动油封]
滑动面磨损
[输入轴总成] [传动器]
未保证有利于 环境且功能可 靠的运行
[滑动油封]
未确保油封的 油膜结构
通过油封未达到 符合功能的密封
[离合器*]
产生振动
[输入轴总成]
通过油封未达到 无渗漏的密封
前轮毂轴承DFMEA分析范例

系统FMEA 编号:子系统第 页共 页零部件
设计责任人:编制日期: 车
关键日期:
修订日期:
核心小组:
潜在设计失效模式和后果分析(DFMEA)
底盘 制动前轮毂轴承
系统FMEA 编号:子系统第 页共 页零部件
设计责任人:编制日期: 车
关键日期:
修订日期:
核心小组:
潜在设计失效模式和后果分析(DFMEA)
底盘
制动前轮毂轴承
承早期失效
内不能正常运行,甚至引起其他部件的功能,车辆异响,顾客
不满意
统共 页零部件
设计责任人:编制日期: 车
关键日期:
修订日期:
核心小组:
制动前轮毂轴承
统共 页零部件
设计责任人:编制日期: 车
关键日期:
修订日期:
核心小组:
制动前轮毂轴承
统共 页零部件
设计责任人:编制日期: 车
关键日期:
修订日期:
核心小组:
制动前轮毂轴承
统共 页零部件
设计责任人:编制日期: 车
关键日期:
修订日期:
核心小组:
制动前轮毂轴承
统共 页零部件
设计责任人:编制日期: 车
关键日期:
修订日期:
核心小组:
制动前轮毂轴承
统共 页零部件
设计责任人:编制日期: 车
关键日期:
修订日期:
核心小组:
制动前轮毂轴承。
电子燃油泵系统DFMEA范本

(D)
(RI
固定磁瓦
发牛塑性 变形
因磁瓦装 得不牢固 而松动
5
材料选用不 当。
2
根据类 似产品 选材经 验
设计评审
3
30
无
几何尺寸设 计不当。
3
以往设 计经验
2
30
无
FMEA编号:RLSP005-2009页码:共25页第9页
编制者XXX
日期(编制):2009.10.7(修订)
功能
潜在失 效模式
设计责任部门:产品开发部
页码:共25页第10页
车型年/车辆类型:
关键日期:2009.10.9
编制者XXX
主要参与人XXX XXX XXX XXX XX
日期(编制):2009.10.7(修订)
功能
潜在失 效模式
潜在失 效后果
^严 重 度
(S)
级 别
潜在失效 起因/机理
频 度
现行 设计 控制 预防
现行设 计控制 探测
潜在失 效后果
^严 重 度
(S)
级 别
潜在失效 起因/机理
频 度
现行 设计 控制 预防
现行设 计控制 探测
探
测 度
(D)
风险 顺序 数
RPN
建议 措施
责任及目 标
完成的日 期
措施结果
采取的 措施
严重 度
(S)
频 度
(0)
探 测 度
(D)
(RI
和单向阀 头组件形 运动副
发牛塑性 变形
单向阀失 去密封性
易磨损
产品寿合 缩短
5
设计的产品 要求的含油 里太低
材质要求不 当