浅谈催化裂化装置中分馏塔塔顶压力
催化裂化吸收稳定流程说明
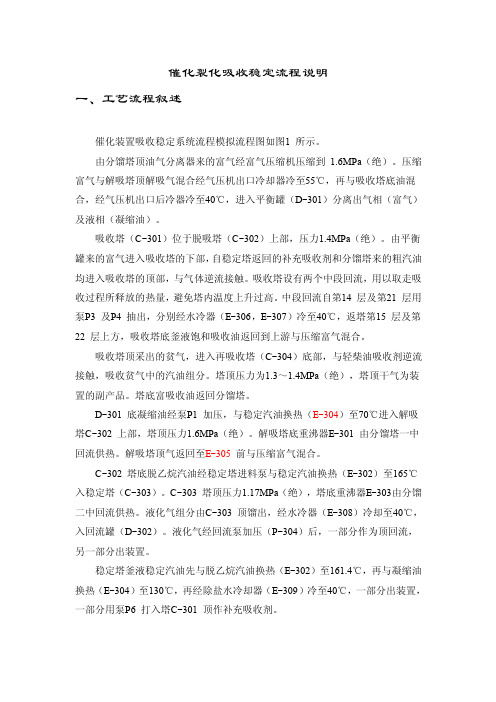
催化裂化吸收稳定流程说明一、工艺流程叙述催化装置吸收稳定系统流程模拟流程图如图1 所示。
由分馏塔顶油气分离器来的富气经富气压缩机压缩到1.6MPa(绝)。
压缩富气与解吸塔顶解吸气混合经气压机出口冷却器冷至55℃,再与吸收塔底油混合,经气压机出口后冷器冷至40℃,进入平衡罐(D-301)分离出气相(富气)及液相(凝缩油)。
吸收塔(C-301)位于脱吸塔(C-302)上部,压力1.4MPa(绝)。
由平衡罐来的富气进入吸收塔的下部,自稳定塔返回的补充吸收剂和分馏塔来的粗汽油均进入吸收塔的顶部,与气体逆流接触。
吸收塔设有两个中段回流,用以取走吸收过程所释放的热量,避免塔内温度上升过高。
中段回流自第14 层及第21 层用泵P3 及P4 抽出,分别经水冷器(E-306,E-307)冷至40℃,返塔第15 层及第22 层上方,吸收塔底釜液饱和吸收油返回到上游与压缩富气混合。
吸收塔顶采出的贫气,进入再吸收塔(C-304)底部,与轻柴油吸收剂逆流接触,吸收贫气中的汽油组分。
塔顶压力为1.3~1.4MPa(绝),塔顶干气为装置的副产品。
塔底富吸收油返回分馏塔。
D-301 底凝缩油经泵P1 加压,与稳定汽油换热(E-304)至70℃进入解吸塔C-302 上部,塔顶压力1.6MPa(绝)。
解吸塔底重沸器E-301 由分馏塔一中回流供热。
解吸塔顶气返回至E-305 前与压缩富气混合。
C-302 塔底脱乙烷汽油经稳定塔进料泵与稳定汽油换热(E-302)至165℃入稳定塔(C-303)。
C-303 塔顶压力1.17MPa(绝),塔底重沸器E-303由分馏二中回流供热。
液化气组分由C-303 顶馏出,经水冷器(E-308)冷却至40℃,入回流罐(D-302)。
液化气经回流泵加压(P-304)后,一部分作为顶回流,另一部分出装置。
稳定塔釜液稳定汽油先与脱乙烷汽油换热(E-302)至161.4℃,再与凝缩油换热(E-304)至130℃,再经除盐水冷却器(E-309)冷至40℃,一部分出装置,一部分用泵P6 打入塔C-301 顶作补充吸收剂。
催化裂化提高汽油收率操作分析

催化裂化提高汽油收率操作分析摘要:通过对催化裂化装置操作调整的分析,改善操作,有效提高汽油收率。
关键词:催化裂化;操作调整;汽油收率催化裂化装置的汽油是原油进提升管经过裂化反应,通过分馏塔组分切割,再经过吸收稳定精馏分离而出来的。
下面通过对装置操作调整分析,确定怎样来提高汽油收率。
本文从反应再生系统,分馏系统,吸收稳定系统三个方面的操作调整,分析对汽油收率的影响。
1.反应再生系统的操作1.1 反应温度催化裂化反应是吸热反应,反应温度升高有利于裂化反应的进行,由于我们反应温度一般投自动控制,提高反应温度的同时再生滑阀开大,增加催化剂循环量,增加催化剂活性中心,增加反应深度。
则提高反应温度,汽油收率增加。
但当反应温度提至很高时,热裂化反应趋于重要,汽油组分开始减少,干气组分明显增多。
表1 反应温度与汽油收率图1 反应温度与汽油收率由表1和图1中可以看出,其他条件不变时,提高反应温度,汽油收率增加.反应温度在504℃时,汽油收率最高。
505℃时,汽油收率开始下降,干气收率增加。
1.2急冷介质在反应温度不变情况下,提高汽油收率另一种手段就是在提升管反应部分喷入急冷介质,提高剂油比和反应深度,减少二次裂化和热裂化,从而提高汽油收率。
急冷介质一般用粗汽油或者水或者两者混合。
但急冷介质的喷入会影响系统的油气分压,分流塔产品质量的控制需相应调整。
1.3 再生温度本装置再生器采用重叠式两段再生型式。
两个再生器重叠布置,一段再生位于二段再生上面。
一再贫氧、CO部分燃烧;二再富氧再生、CO完全燃烧。
催化裂化反应所需热量是通过再生器内完全再生的热催化剂提供的,所以再生温度的高低也直接影响催化剂循环量的大小。
再生温度高则催化剂循环量降低,反应的催化剂活性中心减少,反应深度降低,汽油收率降低。
表2 再生温度与汽油收率图2再生温度与汽油收率由表2与图2可以看出其他条件不变时,汽油收率随再生温度升高而降低,但当再生温度降至670℃以下后,再生器烧焦效果变差,再生器稀相出现尾燃。
炼油催化裂化分馏塔顶腐蚀原因分析及对策
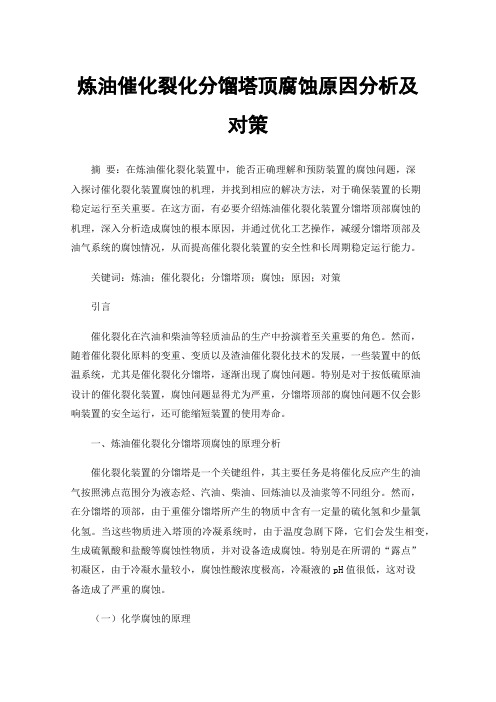
炼油催化裂化分馏塔顶腐蚀原因分析及对策摘要:在炼油催化裂化装置中,能否正确理解和预防装置的腐蚀问题,深入探讨催化裂化装置腐蚀的机理,并找到相应的解决方法,对于确保装置的长期稳定运行至关重要。
在这方面,有必要介绍炼油催化裂化装置分馏塔顶部腐蚀的机理,深入分析造成腐蚀的根本原因,并通过优化工艺操作,减缓分馏塔顶部及油气系统的腐蚀情况,从而提高催化裂化装置的安全性和长周期稳定运行能力。
关键词:炼油;催化裂化;分馏塔顶;腐蚀;原因;对策引言催化裂化在汽油和柴油等轻质油品的生产中扮演着至关重要的角色。
然而,随着催化裂化原料的变重、变质以及渣油催化裂化技术的发展,一些装置中的低温系统,尤其是催化裂化分馏塔,逐渐出现了腐蚀问题。
特别是对于按低硫原油设计的催化裂化装置,腐蚀问题显得尤为严重,分馏塔顶部的腐蚀问题不仅会影响装置的安全运行,还可能缩短装置的使用寿命。
一、炼油催化裂化分馏塔顶腐蚀的原理分析催化裂化装置的分馏塔是一个关键组件,其主要任务是将催化反应产生的油气按照沸点范围分为液态烃、汽油、柴油、回炼油以及油浆等不同组分。
然而,在分馏塔的顶部,由于重催分馏塔所产生的物质中含有一定量的硫化氢和少量氯化氢。
当这些物质进入塔顶的冷凝系统时,由于温度急剧下降,它们会发生相变,生成硫氰酸和盐酸等腐蚀性物质,并对设备造成腐蚀。
特别是在所谓的“露点”初凝区,由于冷凝水量较小,腐蚀性酸浓度极高,冷凝液的pH值很低,这对设备造成了严重的腐蚀。
(一)化学腐蚀的原理将常压渣油加热至200℃后,引入提升管反应器的下部喷嘴,通过蒸汽雾化将其分散成微粒,然后进入提升管内。
在提升管内,与来自再生器的高温催化剂发生接触,随后汽化并进行反应。
有机硫化物在高温下分解成酸性H2S和RSH等化合物,随着反应油气一起进入分馏塔。
电脱盐过程未能完全去除的无机盐类会在高温下熔化、水解,有机氯化物也会在高温下分解生成HCl。
H2S和HCl会在水蒸汽结雾时溶解其中,产生强烈的化学腐蚀。
催化裂化装置工艺条件一览表

一、催化裂化装置主要工艺指标
1、反应再生单元
序号工艺指标名称单位仪表位号控制范围
1
重油提升管出口温度
℃
TRCA22101A
500~530
2
出管芳烃提升口温度烃芳提升管出口温度
℃℃
TRCA22101B TRCA22101B
440~480(低硫)480~530(高硫)
3
反应压力
50±20
10
液位T22201A
%
LC22201
20
±50
11
T22201B液位
%
LC22202
50±20
12
V22203A液位
%
LICA2220
50±20
13
V22203B液位
%
LICA2220
50±20
14
电脱盐罐温度
℃
110~140
15
电脱盐罐压力
Mpa
0.8~1.5
16
电脱盐罐电场强
kv/cm
15
过热蒸气温度
℃
TIC22461
380~410
16
汽外取热包压力
MPa
PRA22421
3.5~4.1
17
省煤器上水温度
℃
TI22468
>122
18
外取热汽包液位
%
LRC22421
50±20
2、分馏单元
序号
工艺指标名称
单位
仪表位号
控制范围
1
重油分馏塔塔顶
℃
TRCA2220
120~150
2
芳烃分馏塔塔顶
90~130
认真分析 开拓思路 催化装置稳定塔顶压力偏低的异常操作得到解决

认真分析开拓思路稳定塔顶压力偏低的异常操作得到解决——王军刘龙脱科峰一、概述催化装置吸收稳定系统自从2008年5月份改造后,稳定塔顶压力一段时间一直处于偏低状态,虽然采取了一系列传统的操作调整手段,但是效果仍然不佳,长时间稳定塔顶压力补压热旁路控制调节阀处于全开,付线阀也处于全开状态,但压力仍然偏离工艺指标控制值,压力很低。
泄压压力控制调节阀不凝气阀一直处于关闭状态,这种操作现象的存在,造成液态烃质量不合格,液态烃中的C5含量超标。
C2含量由于溶解于液相中很难排出而超标,这样一来,液态烃的脱前总硫含量大大上升,使得液态烃的后续脱硫装置符合大大增加,液态烃脱后硫含量超标,碱液单耗猛增,超标那段时间,每天消耗新鲜碱液使正常稳定工况下的5倍,同时也直接影响了聚丙烯装置的平稳生产。
针对这种操作异常现象,我们认真分析,及时采取了行之有效的措施,使得稳定塔顶压力偏低的问题得到解决,平稳了操作,保证了液态烃质量,减低了碱液单耗,有力的保证了装置的安全、平稳、高效、长周期运行。
二、稳定塔顶压力偏低的弊端a)稳定系统操作波动大,对装置的安全生产造成很大威胁。
b)液态烃质量波动不合格,液态烃中的C5、C2含量超标。
c)液态烃脱后硫含量超标,新鲜碱单耗大大超标。
d)液化气质量直接影响聚丙烯装置的平稳生产,不利于聚合反应的进行三、稳定塔顶压力偏低的原因分析1.改造缺陷2008年5月份对原稳定塔顶回流罐(V302)进行了放大,但改造时是利旧了原气压机出口油气分离器(V301)作为改造后的稳定塔顶回流罐(V302),由于原设备接口少的现状,所以在配值工艺管线时将原从稳定塔顶回流罐顶接入的补压线接口并在了液态烃管线一并进入回流罐内的液层,这样一来,在操作中虽有大量的热态液态烃进入回流罐补压但由于是和冷态的液态烃混合并且进入液层,从而造成大量的热态液态烃不能在回流罐及时很好的汽化进入气相达到补压的效果,致使稳定塔顶压力偏低。
C2含量由于溶解于液相中很难排出而超标。
催化裂化的装置简介及工艺流程
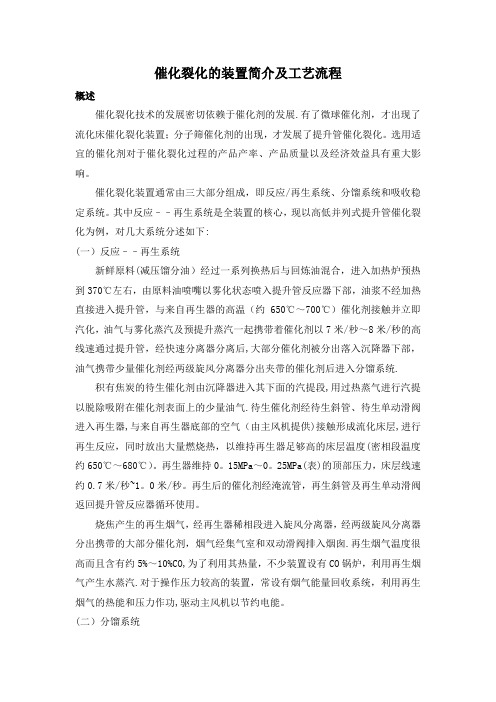
催化裂化的装置简介及工艺流程概述催化裂化技术的发展密切依赖于催化剂的发展.有了微球催化剂,才出现了流化床催化裂化装置;分子筛催化剂的出现,才发展了提升管催化裂化。
选用适宜的催化剂对于催化裂化过程的产品产率、产品质量以及经济效益具有重大影响。
催化裂化装置通常由三大部分组成,即反应/再生系统、分馏系统和吸收稳定系统。
其中反应––再生系统是全装置的核心,现以高低并列式提升管催化裂化为例,对几大系统分述如下:(一)反应––再生系统新鲜原料(减压馏分油)经过一系列换热后与回炼油混合,进入加热炉预热到370℃左右,由原料油喷嘴以雾化状态喷入提升管反应器下部,油浆不经加热直接进入提升管,与来自再生器的高温(约650℃~700℃)催化剂接触并立即汽化,油气与雾化蒸汽及预提升蒸汽一起携带着催化剂以7米/秒~8米/秒的高线速通过提升管,经快速分离器分离后,大部分催化剂被分出落入沉降器下部,油气携带少量催化剂经两级旋风分离器分出夹带的催化剂后进入分馏系统.积有焦炭的待生催化剂由沉降器进入其下面的汽提段,用过热蒸气进行汽提以脱除吸附在催化剂表面上的少量油气.待生催化剂经待生斜管、待生单动滑阀进入再生器,与来自再生器底部的空气(由主风机提供)接触形成流化床层,进行再生反应,同时放出大量燃烧热,以维持再生器足够高的床层温度(密相段温度约650℃~680℃)。
再生器维持0。
15MPa~0。
25MPa(表)的顶部压力,床层线速约0.7米/秒~1。
0米/秒。
再生后的催化剂经淹流管,再生斜管及再生单动滑阀返回提升管反应器循环使用。
烧焦产生的再生烟气,经再生器稀相段进入旋风分离器,经两级旋风分离器分出携带的大部分催化剂,烟气经集气室和双动滑阀排入烟囱.再生烟气温度很高而且含有约5%~10%CO,为了利用其热量,不少装置设有CO锅炉,利用再生烟气产生水蒸汽.对于操作压力较高的装置,常设有烟气能量回收系统,利用再生烟气的热能和压力作功,驱动主风机以节约电能。
催化裂化操作指南(分馏与稳定)解读
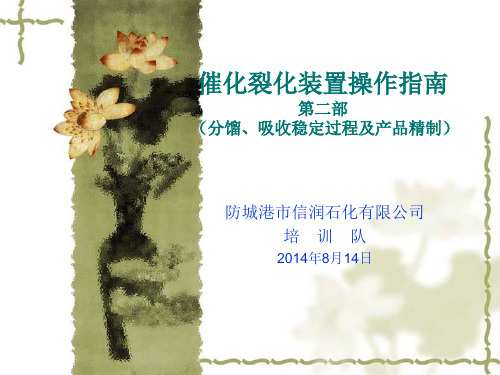
分馏过程
一、设备检查 1、塔器 (1)分馏塔 首次运行的分馏塔,必须逐层检查所有塔盘,确认按图纸正确安装; 如溢流口尺寸、堰高和塔盘水平度等。 对所有浮阀进行检查,确认清洁,活动自如;所有塔盘紧固件安装正 确、紧固;所有分布器安装定位正确,分布孔畅通。 每层塔盘和降液管清洁,顶循、中段、柴油等抽出槽和抽出口清洁无 杂物,集油箱焊缝完好,不泄漏。 底部脱过热段折流板(人字档板)等均坚固,焊缝完好,所有固定螺 栓均已经锤击或被点焊。 塔底搅拌蒸汽分布器、支撑等完好;油浆过滤器及其附件清洁,固定 或焊接牢固。 塔内设备检查完成后,应马上安装人孔,安排专人现场负责该项工作。
分馏过程
档板或园盘型档板,进入油气与260-360℃循环油浆逆流接触、换热、 冼涤,油气被冷却,将油气中夹带的催化剂细枌冼涤下来,防止其污染 上部的测线产品,堵塞上部塔盘。 (2)全塔过剩热量大 分馏塔进料是过热度很高的反应油气(480-510 ℃ ),塔顶是低温 (100-130 ℃ )气体,其他产品均以液态形式离开分馏塔。在整个分 馏过程中有大量的过剩热量需要移出。所以系统有大量的冷换设备和热 水器。 (3)产品分馏要求较容易满足 油品分馏难易程度可用相邻馏分50%馏出温度差值来衡量。差值越大, 馏分间相对挥发度越大,就越容易分离。催化分馏塔除塔顶为粗汽油外 还有轻柴油、重柴油、回炼油三个侧线组分。催化裂化各侧线组分50% 馏出温度值较大,馏分容易分离,所以产品分馏要求容易满足。
分馏过程
(5)轻污油系统 分馏、吸收稳定部分轻油设备(换热器、泵、过滤器、采样器等) 在停工或检修时存有少量的轻油,通过污油系统自流至地下轻污油罐, 用污油泵送出装置。 (6)重污油系统 装置内重油设备在停工或检修时存有少量的重油,通过重污油系统 送出装置。 5、事故处理流程 (1)富气放火炬流程 开工时提升管反应器已经进油,但富气压缩机还没有启动,在此期 间产生的富气从分馏塔顶油气分离器引出经富气放空管道排放至火炬系 统。正常生产中富气压缩机因故障紧急停机,则启用富气放火炬系统。 (2)汽油紧急排放流程 当分馏塔顶油气分离罐粗汽油液位突然升高,用正常方法处理不及 时,有汽油进入富气压缩机的危险时,可启用汽油紧急放空(粗汽油泵 入口管排放到轻污油罐)。
催化裂化装置分馏系统工艺分析
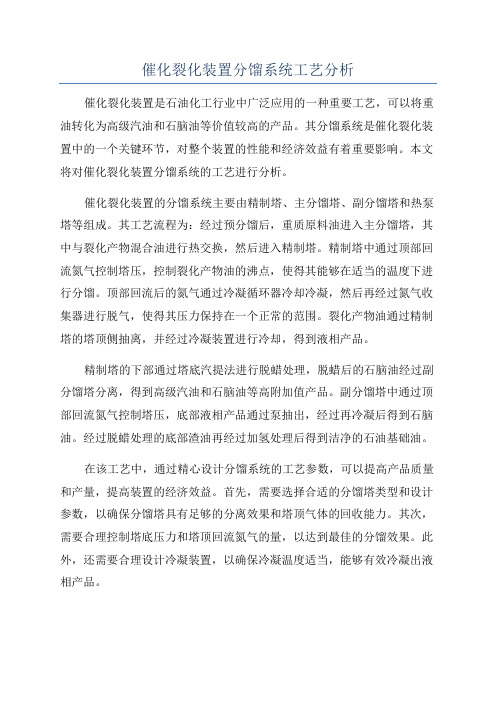
催化裂化装置分馏系统工艺分析催化裂化装置是石油化工行业中广泛应用的一种重要工艺,可以将重油转化为高级汽油和石脑油等价值较高的产品。
其分馏系统是催化裂化装置中的一个关键环节,对整个装置的性能和经济效益有着重要影响。
本文将对催化裂化装置分馏系统的工艺进行分析。
催化裂化装置的分馏系统主要由精制塔、主分馏塔、副分馏塔和热泵塔等组成。
其工艺流程为:经过预分馏后,重质原料油进入主分馏塔,其中与裂化产物混合油进行热交换,然后进入精制塔。
精制塔中通过顶部回流氮气控制塔压,控制裂化产物油的沸点,使得其能够在适当的温度下进行分馏。
顶部回流后的氮气通过冷凝循环器冷却冷凝,然后再经过氮气收集器进行脱气,使得其压力保持在一个正常的范围。
裂化产物油通过精制塔的塔顶侧抽离,并经过冷凝装置进行冷却,得到液相产品。
精制塔的下部通过塔底汽提法进行脱蜡处理,脱蜡后的石脑油经过副分馏塔分离,得到高级汽油和石脑油等高附加值产品。
副分馏塔中通过顶部回流氮气控制塔压,底部液相产品通过泵抽出,经过再冷凝后得到石脑油。
经过脱蜡处理的底部渣油再经过加氢处理后得到洁净的石油基础油。
在该工艺中,通过精心设计分馏系统的工艺参数,可以提高产品质量和产量,提高装置的经济效益。
首先,需要选择合适的分馏塔类型和设计参数,以确保分馏塔具有足够的分离效果和塔顶气体的回收能力。
其次,需要合理控制塔底压力和塔顶回流氮气的量,以达到最佳的分馏效果。
此外,还需要合理设计冷凝装置,以确保冷凝温度适当,能够有效冷凝出液相产品。
此外,还需要注意操作控制的安全性和稳定性。
对于分馏系统来说,要注意控制好分馏温度和压力的变动,以防止分馏塔内发生过热、过压等异常情况。
在日常操作中,要注意监控分馏系统的各个关键参数,及时发现问题并进行调整和处理。
综上所述,催化裂化装置分馏系统是催化裂化装置中一个重要的工艺环节。
通过合理设计和精心操作,可以提高产品的质量和产量,提高装置的经济效益。
但需要注意操作的安全性和稳定性,及时处理和解决问题。
催化裂化装置分馏塔顶及其冷却系统腐蚀分析与控制
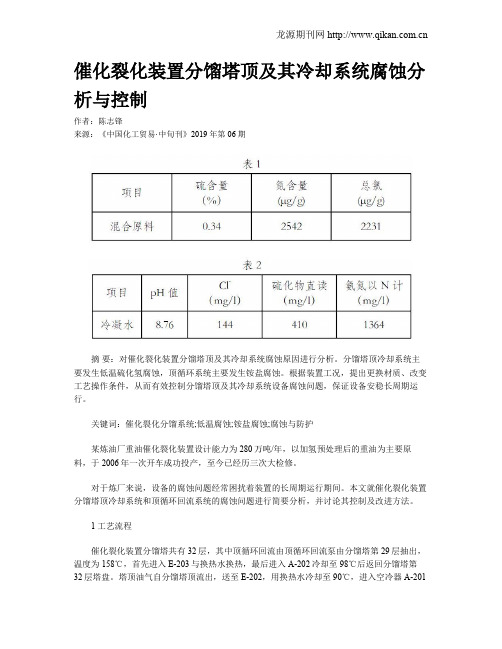
催化裂化装置分馏塔顶及其冷却系统腐蚀分析与控制作者:陈志锋来源:《中国化工贸易·中旬刊》2019年第06期摘要:对催化裂化装置分馏塔顶及其冷却系统腐蚀原因进行分析。
分馏塔顶冷却系统主要发生低温硫化氢腐蚀,顶循环系统主要发生铵盐腐蚀。
根据装置工况,提出更换材质、改变工艺操作条件,从而有效控制分馏塔顶及其冷却系统设备腐蚀问题,保证设备安稳长周期运行。
关键词:催化裂化分馏系统;低温腐蚀;铵盐腐蚀;腐蚀与防护某炼油厂重油催化裂化装置设计能力为280万吨/年,以加氢预处理后的重油为主要原料,于2006年一次开车成功投产,至今已经历三次大检修。
对于炼厂来说,设备的腐蚀问题经常困扰着装置的长周期运行期间。
本文就催化裂化装置分馏塔顶冷却系统和顶循环回流系统的腐蚀问题进行简要分析,并讨论其控制及改进方法。
1 工艺流程催化裂化装置分馏塔共有32层,其中顶循环回流由顶循环回流泵由分馏塔第29层抽出,温度为158℃,首先进入E-203与换热水换热,最后进入A-202冷却至98℃后返回分馏塔第32层塔盘。
塔顶油气自分馏塔顶流出,送至E-202,用换热水冷却至90℃,进入空冷器A-201冷却至60℃后进入一级油气分离器D-201A分离,分离后的粗汽油一部分送入塔顶作为冷回流,一部分与不凝气经油气后冷器E-215冷却至43℃一起进入二级油气分离器D-201B。
2 腐蚀概况装置在第三运行周期内,分馏塔顶冷却系统和塔顶循环系统换热器多次发生管束穿孔泄露,并且塔顶循环泵结盐严重。
严重影响了装置的正常生产,进而影响到设备安稳长周期运行。
2.1 顶循环系统顶循环--换热水换热器E-203共有六台,两台串联为一组,三组并联运行,管程介质为换热水,材质原为10号钢,壳程介质为塔顶循环,材质为16MnR。
装置在第三周期运行期间经常发生管束穿孔泄露,堵管率较高,其中E-203B堵管40根,检修时拆解发现管束腐蚀严重,管外壁布满大量褐色腐蚀产物,除去腐蚀产物,经过打磨,管束出现深浅不一的凹坑。
中级催化裂化装置操作工考试题库含答案

中级催化裂化装置操作工考试题库含答案1、分馏塔顶回流返塔流量( ),粗汽油干点降低。
A、减少B、不变C、增加D、无法确定答案:C2、吸收剂应具有较好的选择性,即对原料气中的产品组分()的吸收能力强。
A、C1、C2B、C2、C3C、C3、C4D、C4、C5答案:C3、换热器扫线时,要将进、出口阀( ),放空阀( )。
A、关闭,关闭B、关闭,打开C、打开,打开D、打开,关闭答案:B4、引循环水进装置时循环水压力不得低于()。
A、0.2MPaB、0.3MPaC、0.4MPaD、0.5MPa答案:C5、油浆发生严重泄漏时,如果泄漏点周围操作人员无法靠前,应关闭管线(),尽量减小可燃物质的泄漏。
A、上下游阀门B、泄漏点阀门C、泵出口阀门D、远端切断阀门答案:D6、属于内取热器缺点的是()A、操作弹性小B、设备投资大C、布置合理D、尺寸紧凑答案:A7、在保证柴油凝点和闪点合格的情况下,通过( )汽油干点可以提高轻柴油收率。
A、降低B、保持C、提高D、不确定答案:A8、再吸收塔液位失灵导致干气带轻柴油的处理方法是( )。
A、降低贫吸收油量,液控阀失灵改副线,液面失灵联系仪表修理B、降低贫吸收油量,提高富吸收油量C、提高贫吸收油量,降低富吸收油量D、提高贫吸收油量,液控阀失灵改副线,液面失灵联系仪表修理答案:A9、视在功率:在具有电阻和电抗的交流电路中,电压有效值与电流有效值的乘积称为视在功率,用英立字母()表示,单位为伏安(V.A)表示。
A、SB、PC、WD、R答案:A10、外取热器与内取热器相比,不属于外取热器缺点的是( )。
A、增加投资费用B、增加维护费用C、能有效控制再生器温度D、增加了阀门和管道答案:C11、随着反应的降量,相应( )各段回流,以免回流泵抽空,开大塔底搅拌蒸汽。
A、降低B、提高C、不变D、无法确定答案:A12、下列哪项不是外取热器泄漏的主要原因( )。
A、催化剂长时间冲刷B、水循环倍率过低C、进入外取热器催化剂不均D、再生温度波动答案:D13、当回炼油泵抽空时,下列操作正确的是( )。
关于催化裂化装置主分馏塔工艺模拟的若干思考

关于催化裂化装置主分馏塔工艺模拟的若干思考摘要:催化裂化是石油二次加工的主要方法之一,是在热和催化剂的作用下使重质油发生裂化反应,转变为裂化气、汽油和柴油等的过程。
主要反应有分解、异构化、氢转移、芳构化、缩合、生焦等,相较于热裂化,催化裂化轻质油产率高汽油辛烷值高,柴油安定性较好,并副产富含烯烃的液化气。
主分馏塔在催化裂化装置中的职能是把反应油气分别分离成液化气、汽油、柴油等产品。
本文首先阐述了催化裂化装置主分馏塔的特点及其工作原理,其次提出了催化裂化装置主分馏塔工艺模拟策略。
关键词:催化裂化装置主分馏塔工艺模拟在催化裂化装置中,主分馏塔属于对产品进行分离的核心单元,因实际中牵涉各种温位能量的综合利用,优化主分馏塔的设计与操作参数时将会加剧装置的能耗,所以必须准确的进行主分馏塔的模拟,以防止催化裂化装置能耗的大量消耗。
我国在主分馏塔工艺模拟方面的研究工作目前还很少,尤其是主分馏塔模拟计算中还有各种问题未得到解决,比如反应油气组成的预测、热力学方法的选择等。
本文主要以催化裂化装置主分馏塔的特点及其工作原理为切入点,对催化裂化装置主分馏塔工艺模拟策略进行了分析。
1.催化裂化装置主分馏塔的特点及其工作原理1.1特点首先,主分馏塔的进料主要是存在催化剂粉尘的过热催化裂化反应油气,实际存在脱过热和洗涤粉尘的油浆换热段,也就是我们所说的脱过热段,并不包括提馏段;其次,主分馏塔存在较大的余热量,实际涵盖了油浆循环、一中循环回流、二中循环回流(或回炼油循环)、顶循环回流,从而使主分馏塔整体上达到热平衡;再有,可以有效控制产品质量;另外,不会有太高的系统压降要求;脱过热段主要任务是通过油浆及时冷却反应油气防止出现结焦情况,并且全面清理反应油气夹带的催化剂粉尘,通常存在八到十层人字挡板。
可见,催化裂化装置主分馏塔的模拟策略和一般的分馏塔有着很大的差别。
1.2工作原理分馏塔的原理是利用了液体的饱和蒸汽压的不同而实现液态物质的分离。
催化裂化中的分馏塔汽提塔
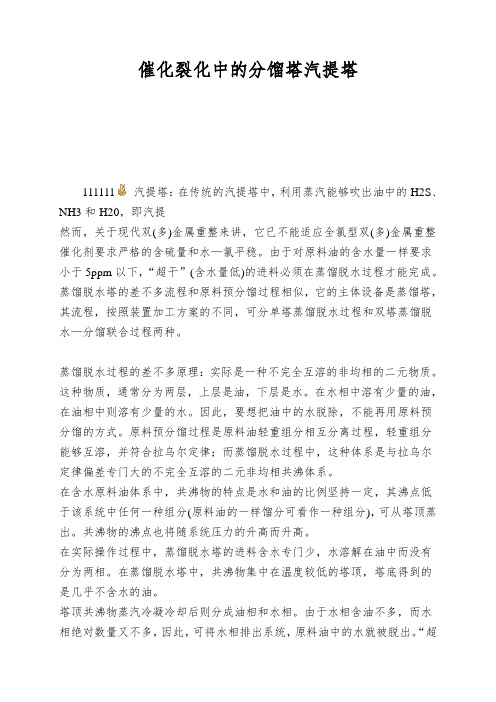
催化裂化中的分馏塔汽提塔111111汽提塔:在传统的汽提塔中,利用蒸汽能够吹出油中的H2S、NH3和H20,即汽提然而,关于现代双(多)金属重整来讲,它已不能适应全氯型双(多)金属重整催化剂要求严格的含硫量和水—氯平稳。
由于对原料油的含水量一样要求小于5ppm以下,“超干”(含水量低)的进料必须在蒸馏脱水过程才能完成。
蒸馏脱水塔的差不多流程和原料预分馏过程相似,它的主体设备是蒸馏塔,其流程,按照装置加工方案的不同,可分单塔蒸馏脱水过程和双塔蒸馏脱水—分馏联合过程两种。
蒸馏脱水过程的差不多原理:实际是一种不完全互溶的非均相的二元物质。
这种物质,通常分为两层,上层是油,下层是水。
在水相中溶有少量的油,在油相中则溶有少量的水。
因此,要想把油中的水脱除,不能再用原料预分馏的方式。
原料预分馏过程是原料油轻重组分相互分离过程,轻重组分能够互溶,并符合拉乌尔定律;而蒸馏脱水过程中,这种体系是与拉乌尔定律偏差专门大的不完全互溶的二元非均相共沸体系。
在含水原料油体系中,共沸物的特点是水和油的比例坚持一定,其沸点低于该系统中任何一种组分(原料油的一样馏分可看作一种组分),可从塔顶蒸出。
共沸物的沸点也将随系统压力的升高而升高。
在实际操作过程中,蒸馏脱水塔的进料含水专门少,水溶解在油中而没有分为两相。
在蒸馏脱水塔中,共沸物集中在温度较低的塔顶,塔底得到的是几乎不含水的油。
塔顶共沸物蒸汽冷凝冷却后则分成油相和水相。
由于水相含油不多,而水相绝对数量又不多,因此,可将水相排出系统,原料油中的水就被脱出。
“超干”的重整进料自塔底排出。
塔顶回流罐中的油相,做为全回流打回塔顶,以保持塔顶的适宜温度和顺利蒸出水。
事实上,蒸馏脱水塔中,与水形成共沸物的组分是最轻的组分,有的装置为提升装置的有效加工能力,把重整原料分成轻石脑油和重石脑油,由于轻石脑油具有较高的辛烷值,可直截了当做汽油调合组分,只把重石脑油进行催化重整。
那个过程也能够合在蒸馏脱水系统中进行,由于需要的塔板数较多,通常由两个蒸馏塔来完成。
催化裂化吸收塔顶温和顶压的关系
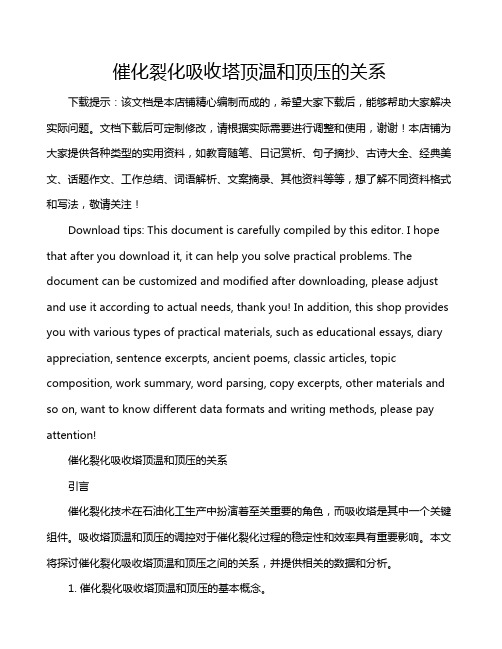
催化裂化吸收塔顶温和顶压的关系下载提示:该文档是本店铺精心编制而成的,希望大家下载后,能够帮助大家解决实际问题。
文档下载后可定制修改,请根据实际需要进行调整和使用,谢谢!本店铺为大家提供各种类型的实用资料,如教育随笔、日记赏析、句子摘抄、古诗大全、经典美文、话题作文、工作总结、词语解析、文案摘录、其他资料等等,想了解不同资料格式和写法,敬请关注!Download tips: This document is carefully compiled by this editor. I hope that after you download it, it can help you solve practical problems. The document can be customized and modified after downloading, please adjust and use it according to actual needs, thank you! In addition, this shop provides you with various types of practical materials, such as educational essays, diary appreciation, sentence excerpts, ancient poems, classic articles, topic composition, work summary, word parsing, copy excerpts, other materials and so on, want to know different data formats and writing methods, please pay attention!催化裂化吸收塔顶温和顶压的关系引言催化裂化技术在石油化工生产中扮演着至关重要的角色,而吸收塔是其中一个关键组件。
浅谈催化裂化装置中分馏塔塔顶压力
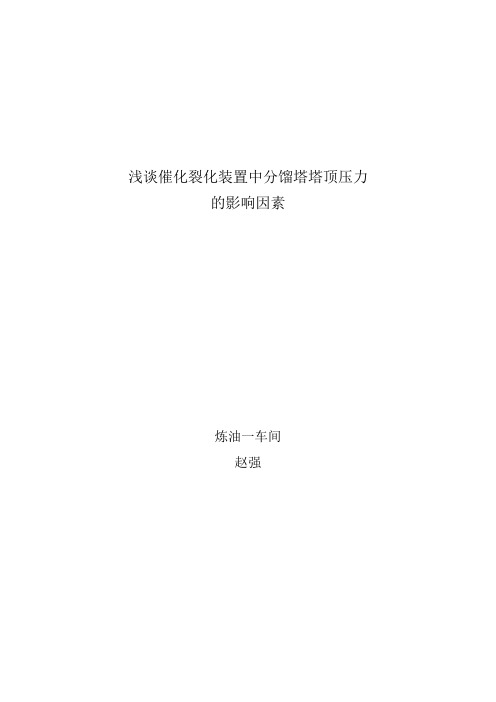
浅谈催化裂化装置中分馏塔塔顶压力的影响因素炼油一车间赵强浅谈催化裂化装置中分馏塔塔顶压力的影响因素赵强(乌石化炼油厂一车间)前言:催化裂化分馏塔的主要任务是将来自反应系统的高温油气脱过热后,根据各组分沸点的不同切割为富气、汽油、柴油、回炼油和油浆等,通过温度,压力,回流量等工艺因素控制,保证各馏分质量合格。
关键词:催化裂化,分馏塔,压力,汽油,柴油,回炼油,油浆一 基本情况介绍:蜡油催化裂化装置近期在生产过程中,分馏塔顶压力一直不好控制,从原来的115kPa 下降到113kPa 在到现在的110kPa ,如图(一),分馏塔顶压力月平均111111.5112112.5113113.5114114.5115115.51月份2月份3月份4月份5月份6月份图1 2008年1月份到6月份在我装置生产过程中,分馏塔顶压力要控制在105kPa 到135kPa 之间,从上述据上看分馏塔的压力都在正常控制压力之内,但是在近期的观察中,发现分馏塔顶压力一直在降低。
在催化裂化装置中分馏塔顶压力是控制各侧线流出产品质量的重要参数,分流塔顶压力的过高或过低都会使产品的质量受到很大影响,当分馏塔顶压力过低时,粗汽油的干点就会升高,而柴油的终馏点却会降低;当分馏塔塔顶压力过高则反之。
而汽油的干点说明了汽油在发动机中蒸发完全的程度,这个温度过高,说明重质成分过多,其结果是降低发动机的功率和经济性,因此我们要控制好分馏塔的压力。
二原因分析:影响分馏塔顶压力的主要原因有以下几点:原料的性质,反应温度,反应压力,催化剂的活性,分馏塔顶的温度,分馏塔的中部温度,塔底的气相温度,分馏塔的顶部及各中部回流量,气压机的转速,塔顶的安全阀,以及Dg400,Dg200阀的开度等因素,下面从原料性质,分馏塔中部温度,分馏塔底汽相温度3个方面来分析分馏塔顶压力。
2.1 在催化裂化装置中,分馏塔顶的压力来源于原料裂解之后经过分馏塔的各中段回流和塔顶回流之后的不凝气体,这些气体是通过高温催化剂和原料的相互接触使原料裂解而生成的,所以分馏塔的压力和原料的性质,催化剂的活性,反应温度都有关系,下面就是6月15日到6月17日之间原料性质和反应温度的变化情况;原料性质变化情况罐位初馏点℃5% 10% 50% 90% 终馏点℃残碳密度5号285 320 340 420 505 555 0.17 881.66号277 344 360 435 521 --- 0.21 882.97号270 325 345 430 515 570 0.12 881.7反应温度变化情况6月15日6月16日6月17日反应温度塔顶压力反应温度塔顶压力反应温度塔顶压力1点485113485113489111 3点485113485113489110 5点485113484113487110 7点485114484113487109 9点485113484113487110 11点484113483112488111 13点484113483113487108 15点484112487114481109 17点482114488113481109 19点483113489113482111 21点484113489111482110 23点486113489111480110平均值484.3333113.0833485.8333112.6667485109.8333这个表格中从6月15日的19点钟到6月16日的15点钟是5号罐裂解,6月16日17点到6月17日13点是6号罐裂解,6月17日以后的7号罐裂解从上边两个表的数据来看,在6月15日到17日之间,近似的把催化剂的活性看成是一定的,分馏塔顶的压力和原料的5%点有着密切的关系,当原料的5%点从5号罐320℃上升到6号罐344℃再到7号罐的325℃,反应温度从485℃改变到489℃然后在回到480℃的情况下分馏塔顶的压力从113kPa 下降到了111kPa再到110kPa,在反应温度的变化是随着原料性质的变化而变化的情况下,反应压力却一直保持在172 kPa,从这些数据来看分馏塔顶的压力和原料的性质有这直接的关系。
催化裂化中的分馏塔汽提塔.doc
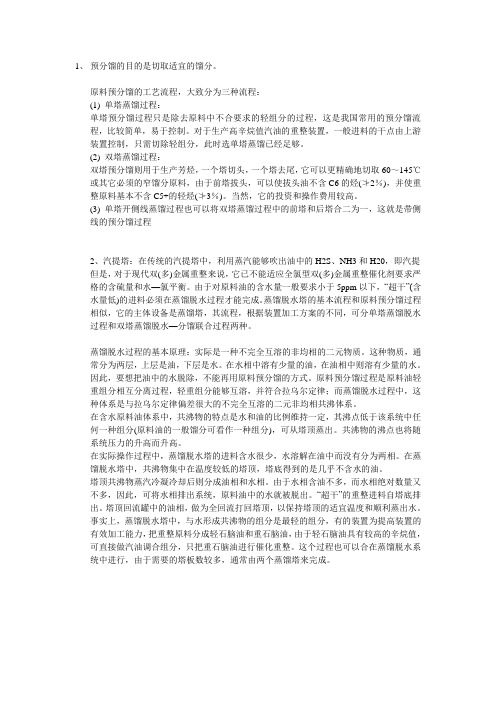
1、预分馏的目的是切取适宜的馏分。
原料预分馏的工艺流程,大致分为三种流程:(1) 单塔蒸馏过程:单塔预分馏过程只是除去原料中不合要求的轻组分的过程,这是我国常用的预分馏流程,比较简单,易于控制。
对于生产高辛烷值汽油的重整装置,一般进料的干点由上游装置控制,只需切除轻组分,此时选单塔蒸馏已经足够。
(2) 双塔蒸馏过程:双塔预分馏则用于生产芳烃,一个塔切头,一个塔去尾,它可以更精确地切取60~145℃或其它必须的窄馏分原料,由于前塔拔头,可以使拔头油不含C6的烃(≯2%),并使重整原料基本不含C5+的轻烃(≯3%)。
当然,它的投资和操作费用较高。
(3) 单塔开侧线蒸馏过程也可以将双塔蒸馏过程中的前塔和后塔合二为一,这就是带侧线的预分馏过程2、汽提塔:在传统的汽提塔中,利用蒸汽能够吹出油中的H2S、NH3和H20,即汽提但是,对于现代双(多)金属重整来说,它已不能适应全氯型双(多)金属重整催化剂要求严格的含硫量和水—氯平衡。
由于对原料油的含水量一般要求小于5ppm以下,“超干”(含水量低)的进料必须在蒸馏脱水过程才能完成。
蒸馏脱水塔的基本流程和原料预分馏过程相似,它的主体设备是蒸馏塔,其流程,根据装置加工方案的不同,可分单塔蒸馏脱水过程和双塔蒸馏脱水—分馏联合过程两种。
蒸馏脱水过程的基本原理:实际是一种不完全互溶的非均相的二元物质。
这种物质,通常分为两层,上层是油,下层是水。
在水相中溶有少量的油,在油相中则溶有少量的水。
因此,要想把油中的水脱除,不能再用原料预分馏的方式。
原料预分馏过程是原料油轻重组分相互分离过程,轻重组分能够互溶,并符合拉乌尔定律;而蒸馏脱水过程中,这种体系是与拉乌尔定律偏差很大的不完全互溶的二元非均相共沸体系。
在含水原料油体系中,共沸物的特点是水和油的比例维持一定,其沸点低于该系统中任何一种组分(原料油的一般馏分可看作一种组分),可从塔顶蒸出。
共沸物的沸点也将随系统压力的升高而升高。
催化裂化两器压力控制

一、沉降器压力控制正常操作:正常工况下的沉降器压力采用分馏塔顶压力控制富气压缩机组的转速来控制的。
此时,富气压缩机入口放火炬大、小阀均处于关闭状态,同时富气压缩机组反喘振控制系统中,用调节反飞动量来避免富气压缩机组喘振。
影响因素:1、提升管总进料量的变化,总进料量增加,压力上升。
2、原料油组份的变化,原料易裂解,反应压力上升。
3、反应温度变化,反应温度上升,反应压力上升。
4、反应汽提蒸汽量变化,增加汽提蒸汽量,反应压力上升。
5、原料油带水,反应压力明显上升。
6、分馏塔底液面变化,影响分馏塔上部负荷变化,而使反应压力随着变化,负荷过大,则反应压力高。
分馏塔液面超高,造成液封,反应压力上升。
要特别注意,不允许此情况发生。
7、急冷剂量大,反应压力上升。
8、气压机吸入压力的变化,气压机吸入压力上升,反应压力上升。
(如反喘振量变化,气压机故障等)。
9、分馏塔顶蝶阀开度变化。
10、污汽油回炼量变化。
11、分馏塔顶油气分离器液面超高,反应压力急剧上升。
12、分馏塔顶回流及冷回流量变化。
13、当气压机组由汽轮机调节机组转速时,装置内的中压蒸汽压力及流量变化影响气压机转速,导致反应压力的变化。
14、分馏塔顶油气冷却效果变化,冷却效果好,反应压力下降。
15、吸收塔冲塔使富吸收油大量带汽油至分馏塔,使反应压力上升。
停工调节方法:1、两器烘器阶段,通过遥控设在沉降器顶的放空阀控制沉降器压力,其目的是控制两器升温速度。
2、建立汽封至两器流化试验阶段,用分馏塔顶压力控制分馏塔顶出口油气管道上的蝶阀保证反应压力平稳。
3、反应进油后至启动富气压缩机前,采用分馏塔顶压力控制压缩机入口放火炬小阀(微调),配以遥控压缩机入口放火炬大阀(粗调),保证反应压力平稳。
4、汽轮机调速器故障,若汽轮机调速器故障,则将调速器于固定位置,使机组处于恒速运行状态,采用分馏塔顶压力和富气压缩机组反喘振调节系统组成低选,控制气压机出口循环线上的反喘振调节阀,同时投用控制放火炬小阀以保证反应压力的平稳。
中压加氢裂化装置分馏塔的控制及流程优化方法
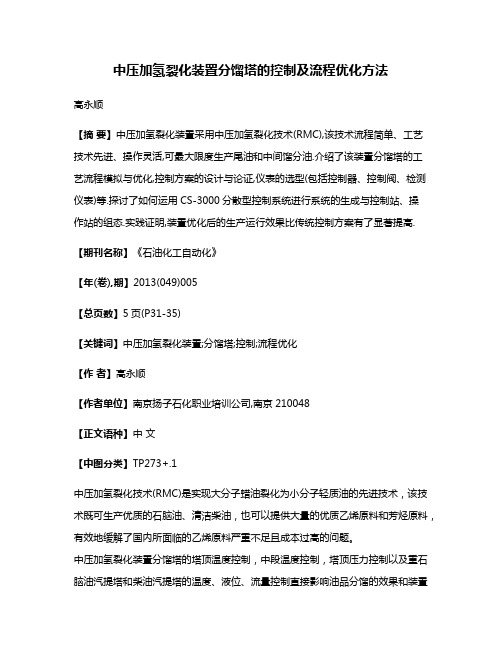
中压加氢裂化装置分馏塔的控制及流程优化方法高永顺【摘要】中压加氢裂化装置采用中压加氢裂化技术(RMC),该技术流程简单、工艺技术先进、操作灵活,可最大限度生产尾油和中间馏分油.介绍了该装置分馏塔的工艺流程模拟与优化,控制方案的设计与论证,仪表的选型(包括控制器、控制阀、检测仪表)等.探讨了如何运用CS-3000分散型控制系统进行系统的生成与控制站、操作站的组态.实践证明,装置优化后的生产运行效果比传统控制方案有了显著提高.【期刊名称】《石油化工自动化》【年(卷),期】2013(049)005【总页数】5页(P31-35)【关键词】中压加氢裂化装置;分馏塔;控制;流程优化【作者】高永顺【作者单位】南京扬子石化职业培训公司,南京210048【正文语种】中文【中图分类】TP273+.1中压加氢裂化技术(RMC)是实现大分子蜡油裂化为小分子轻质油的先进技术,该技术既可生产优质的石脑油、清洁柴油,也可以提供大量的优质乙烯原料和芳烃原料,有效地缓解了国内所面临的乙烯原料严重不足且成本过高的问题。
中压加氢裂化装置分馏塔的塔顶温度控制,中段温度控制,塔顶压力控制以及重石脑油汽提塔和柴油汽提塔的温度、液位、流量控制直接影响油品分馏的效果和装置的安全运行,因而对装置的控制方案和工艺流程进行系统性的优化是很有必要的。
Aspen软件可对装置的工艺流程进行模拟并对控制指标进行系统性优化,计算出安全生产条件下的各项工艺指标,解决生产中的瓶颈问题(分馏质量与产量之间)。
1.1 流程说明中压加氢裂化装置分馏塔的工艺流程如图1所示,分馏塔进料加热炉为4路进料,设有49层塔盘,塔底用过热蒸汽汽提。
340 ℃的脱硫油进入产品分馏塔第8层塔盘,分馏塔设有2个侧线塔,分别为重石脑油汽提塔和轻柴油汽提塔,用于生产重石脑油和轻柴油。
1.2 控制要求1) 分馏塔塔顶油气温度控制。
分馏塔塔顶油气经空冷器冷却至40 ℃后进入分馏塔顶回流罐进行气液分离,界位控制在50%。
催化裂化装置主分馏塔工艺模拟与分析

分馏塔每层塔板有其各自负荷性能图 , 由于篇幅所 限在此仅做出一层具有代表性的理论板的负荷性能 图 , 见图 2 。由于舌形塔板的雾沫夹带线远离淹塔 线 , 塔板的适宜传质操作区又很狭窄 , 为了清晰的 表明操作点的位置 , 塔板的负荷性能图均略去雾沫 夹带线 。
取一典型塔板 , 利用 Aspen Plus 模拟的物流数据 、 物性参数进行水力学核算 , 结果见表 3 。 412 塔板负荷性能图
舌形塔板属于气液并流喷射型塔板 , 其负荷性 能图与普通塔板不同 , 是以液相流量和动能因子表 示适宜的传质操作区[4 ] 。
· 99 0 · 化 工 进 展 2003 年第 22 卷
(3) 粗汽油的干点与柴油的初馏点标定值相差 20 ℃, 模拟值相差 18158 ℃, 重叠较大 , 说明塔 的分离效果不佳 , 在柴油抽出板与一中回流之间增 加理论板或轻柴油汽提塔增加塔板均可改善分离效 果 。通过模拟计算 , 前一种方法增加 5 层理论板 , 温度重叠减小 2155 ℃; 增加 10 层理论板 , 温度重
催化裂化主分馏塔塔径为 318 m , 共有塔板 37 层 。
分馏塔上部设 30 层固舌形塔板 , 分离作用完 全在此段内 。采用固舌形塔板的优点在于处理能力 大 , 液面梯度较小 , 液层较低 , 塔板压降小 , 有利 于提高富气压缩机的入口压力 , 降低压缩比 , 节省 能耗 。
分馏塔底部设有脱过热段 , 采用 7 层人字形换 热板 。其主要任务是使上升的过热油气温度降到饱 和温度以便于精馏 , 同时将进料中的高沸点油浆和
催化裂化装置动态机理模型:Ⅲ.催化剂流动和压力系统
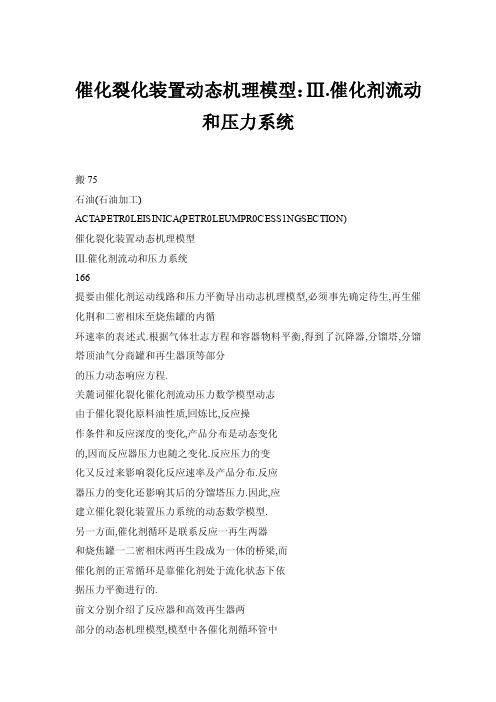
催化裂化装置动态机理模型:Ⅲ.催化剂流动和压力系统搬75石油(石油加工)ACTAPETR0LEISINICA(PETR0LEUMPR0CESS1NGSECTION)催化裂化装置动态机理模型Ⅲ.催化剂流动和压力系统166提要由催化剂运动线路和压力平衡导出动志机理模型,必须事先确定待生,再生催化荆和二密相床至烧焦罐的内循环速率的表述式.根据气体壮志方程和容器物料平衡,得到了沉降器,分馏塔,分馏塔顶油气分商罐和再生器顶等部分的压力动态响应方程.关麓词催化裂化催化剂流动压力数学模型动志由于催化裂化原料油性质,回炼比,反应操作条件和反应深度的变化,产品分布是动态变化的,因而反应器压力也随之变化.反应压力的变化又反过来影响裂化反应速率及产品分布.反应器压力的变化还影响其后的分馏塔压力.因此,应建立催化裂化装置压力系统的动态数学模型.另一方面,催化剂循环是联系反应一再生两器和烧焦罐一二密相床两再生段成为一体的桥梁,而催化剂的正常循环是靠催化剂处于流化状态下依据压力平衡进行的.前文分别介绍了反应器和高效再生器两部分的动态机理模型,模型中各催化剂循环管中催化剂循环速率(循环量)的大小,不但与两器压差有关,还受催化剂藏量的影响.在以往的催化裂化稳态数学模型中,一般不考虑两器压力平衡和催化剂的流动,即使动态模型也很少涉及,但对于经常处于动态过程中的实际工业装置,压力平衡是至关重要的.本文讨论两器压力平衡和再生器压力,沉降器压力的动态变化规律,以及与反应压力有关的分馏塔,分馏塔顶气液分离罐和富气压缩机等部分的压力变化.1压力平衡催化剂在反应一再生蔺器间,烧焦罐与二密相床间正常循环,遵循"推动力一阻力"这一基本关系式,可以推导出待生催化剂和再生催化剂外循环速率及催化剂内循环速率的表达式.1.1待生线路的压力平衡由待生线路的压力平衡,可以得到待生催化剂循环速率为:式中K一(沉降器稀相静压+沉降器过渡段静压+待生斜管蓄压)一(再生器稀相静压+稀相管静压)(2)在操作过程中,可以简单地视为常数;——沉降器顶压力',Pa;——再生器顶压力,Pa;——汽提段藏量,kg;n——汽提段平均截面积,m;H——烧焦罐藏量,t}n——烧焦罐截面积,m;g——重力加速率,9.807m/s;——待生斜管中催化剂平均视密度,kg/m;,——待生滑阀阀芯面积,m;——待生滑阀开度,;——待生斜管中催化剂流动阻力系数m/kg.收稿日期:1帅7一O4—25*通讯联系人,』魇石油(石油加工)第]4卷1.2再生线路的压力平衡在建立稳态数学模型或稳态关系计算中,再生催化剂循环速率与待生催化剂循环速率是相同的,但在动态过程中,二者就不一定相等.由再生线路的压力平衡,可以得到再生催化剂循环速率为:(3)式中K=(再生器稀相静压+再生器过渡段静压+再生斜管蓄压)一(沉降器稀相静压+提升管静压+预提升段压降)(4)在操作过程中,可以简单地视为常数;——二密相床藏量,t;n——二密相床平均截面积,m.;Ppipe,rg2——再生斜管中催化剂平均视密度, kg/m;——再生滑阀阀芯面积,m.;z——再生滑阀开度,;^——再生斜管中催化剂流动阻力系数,m/kg;F.——总原料油流量,kg/s;.——油汽流经提升管的流动阻力系数,l/kg?121.1.3内循环线路的压力平衡在内循环线路的压力平衡.可以得到两再生段间催化剂内循环速率为Gcc1一式中丘一(再生器过渡段静压+内循环管蓄压)一(粗旋压降+稀相管压降)(6)在操作过程中,可以简单地视为常数; P.——内循环斜管中催化剂平均视密度,kg/m;——内循环滑阀阀芯面积,121;z——内循环滑阀开度,;.——内循环管中催化剂流动阻力系数,m/kg.2压力系统动态响应方程催化裂化装置操作压力不高,气体可视为理想气体,则有pV=nR7'(7)当容器体积和温度丁恒定时,则有訾=?窑㈣盂可.面'8J对容器作物料平衡,即可由通过容器的物料摩尔流率得到压力动态响应方程.2.1沉降器压力动态响应方程对沉降器作物料平衡一[富气+汽油+柴油+回炼油+回炼油浆+汽提蒸汽+雾化和预提升蒸汽一沉降器出口反应油汽(含水蒸气)](9)上式中各项物料单位均为kmol/s;R——气体常数,Pa?m/kmol?K;户——沉降器压力,Pa;了1,——沉降器平均温度,K;,——沉降器容积,m..沉降器各进出物料摩尔流率为富气=YGIx=1-.~,a(1O)汽油一F(11)柴油=YDix-1~.(12)回炼油一面?丽DI(13)回炼油一面.(13油浆=?(14)汽提蒸汽一(15)提升管出口蒸汽一一警…)沉降器出口反应油汽一是,/户(户e一户一△户h)(17)式中——与沉降器顶油汽管线,分馏塔气体流动阻力有关的常数;Fw.——汽提蒸汽流量,kg/s;A——分馏塔顶压力,Pa;●,●●●●●●第3期催化裂化装置动态机理模型LXp"——分馏塔塔板液体静压,P;D.——回炼油浆回炼比,D.一回炼油浆/(户A一△m)——沉降器至分馏塔塔顶流动新鲜原料.阻力,Pa;在确定回炼油和油浆生成量时.简单地假定MW,MWN,MWo,MWh.和——富气,生成的回炼油和油浆的比例与进反应器的回炼油汽油,柴油,回炼油和油浆的平均相对分子质量;和回炼油装的比例相同. D——回炼油回炼比,D一回炼油/新鲜将以上各式代入式(9).得到反应沉降器顶原料;压力动态响应模型d—p.a:墨』『丝+盟++.—旦_+墨苎.]一-ILMW哪.MWN.MWD.MWhD1+D2.yD1+D2J!!±!!±!l82.2分馏塔压力动态响应方程2.2.1分馏塔塔下段压力动态模型反应油汽进入催化裂化主分馏塔后,从分馏塔底至顶依次被分离成油浆,回炼油,柴油和(汽油+气体+水蒸气).为了简化分析,将主分馏塔分成上下两段:(1)从柴油和回炼油抽出板中间至塔底油浆抽出为塔下段.流入物流为反应油汽,流出物流为油浆和回炼油及流至塔上段的流出物流.(2)从柴油和回炼油抽出板至塔顶为塔上段.流入物流为塔下段来的流出物流,流出物流为柴油和从塔顶出去的(汽油+气体+水蒸气).基本假定:(1)每段压力按集中化参数建立模型,即各段压力均一,段间压降为后段塔板压降;(2)忽略塔内回流流量和循环回流流量的影响,忽略塔顶冷回流的影响}(3)柴油,回炼油和油浆均以液体形式抽出,其体积与气体体积相比可忽略不计,在建立压力动态模型时认为这几个物流进入各塔段后即冷凝为液体.对塔下段作物料平衡,应用式(8),得到塔下段压力的动态响应方程訾一{[沉降器出口反应油汽(含水蒸气)一回炼油一油浆]一(进出塔下段和塔上段之间的物料流量Qb))(19)式中各项物料单位均为kmol/s;pb——塔下段压力,Pa;——塔下段气相温度,K;——塔下段容积,m;进出塔下段和塔上段之间的物料包括富气, 汽油,柴油和水蒸气,流量按下式计算'..................................一Qb:矗.√pb(户b—A一△)(20)式中.——取决于塔上段塔板流动阻力的常数;A——塔上段压力,Pa;Ap——塔上段塔板静压,Pa;P一户一△p——塔上段流动阻力,Pa.将式(12),(14),(17)和(20)代入式(19),得訾一一?91…I一Fo921)}(2】)2.2.2分馏塔塔上段压力动态模型对塔上段作物料平衡,得到塔上段压力P的动态响应方程dp,一等[进出塔下段和塔上段之间的物料流量Q.柴油流量一塔顶至塔顶油汽分离罐的物料流量Q](22)式中各项物料单位均为kmol/sP——塔顶压力,Pa;丁——塔顶气相温度,K;——塔上段容积,m.塔顶至塔顶油汽分离罐的物料包括富气,汽油和水蒸气,流量按下式计算36石油(石油加工)第l4卷一 (23)式中——取决于塔顶至油汽分离罐上冷凝冷却器流动阻力的常数;(一户)——塔顶至油汽分离罐上冷凝冷却器流动阻力,Pa.将式(12),(2o)和(23)代入式(22),得P——塔顶油汽分离罐压力,Pa;孥:一Y删olx-_~.p.卜i},2.3分馏塔顶油气分离罐压力动态模型V——油汽分离罐容积,121.对油汽分离罐中的气体作物料平衡,假定粗气压机的入口富气流量与气压机进出口压力,汽汽油和水蒸气至油汽分离罐后即刻冷凝成液体,轮机转速有关,而汽轮机蒸汽流量直接影响其转对气体体积量影响可忽略不计.应用式(8),得速,油汽分离罐气体出口至气压机入口压降较小到油汽分离罐压力P的动态响应方程可视为常数,因而气压机入口流量可表示为=[(塔顶至油汽分离罐的物料流Q一.f(V)√户一户(26)量Q一粗汽油流量一污水量)一(至气压机式中户一一t——气压机排气压力,Pa; 的富气流量Q)](25)V——汽轮机蒸汽流量?kg/s.式中各项物料单位均为kmol/s;将式(11),(15),(16),(23)和(26)代入式p——油汽分离雏压力,Pa;(25),得——油汽分离罐温度,K;一:一y丽xIx-1一k~J(V)](27)2.4再生器压力动态模型由于使用co助燃剂,烧焦罐中烧焦反应表主风从烧焦罐底部和二密相床进入再生器,示为焦炭燃烧生成cO和HO,烟气从再生器顶离C+O.一一cO:开,进入废热锅炉和烟气回收系统,然后排入H+{o一-'Ho大气.应用式(8),对再生器稀相段和过渡段作压力其中碳燃烧反应时气体为等分子反应;而氢燃烧平衡时,每反应一个氢原子,多产生1/4个分子的气一罐产生的烟气+二密相床墨:烧较烧焦罐出口处氢已几乎螂烧警风'流过再恚烧焦罐烟气量+4(1裔㈣双动滑阀的烟气量](28)………+)…式中各项物料单位均为kmol/s;二密相床中只有碳的燃烧反应,因而是等气体分一一再生器顶压力,Pa;子反应,即烟气量与二密相风量相同T——再生器顶温度,K;二密相烟气量一V(3O)——再生器稀相段和过渡段气相容积,流经再生器双动滑阀的烟气总量为.m3.烟气排出量一1.5789×1oz√垒羔女,kmol/s(31)式中mwfl——烟气平均相对分子质量d~阀孔孔径,m;Z——双动滑阀开度,;Ca——流量系数,为阀孔孔径和滑阀第3期催化裂化装置动态机理模型37开度的函数;y——膨胀系数,为阀孔孔径和滑阀开度的函数;z——孔板上游烟气压缩系数,再生器出口处烟气的z≈1;——双动滑阀后的压力,P丑,随烟气流量变化而有所改变烟气排出量户=户+(烟气排出量).(32)户一——大气压力,Pa;n——烟道气流动阻力系数,Pa?s/kmol.将式(32)代入式(31),得到烟气排出量与再生器顶压力,滑阀开度,烟道气流动阻力的关系将上面各式代入式(28),并且假设再生器顶则再生器顶压力的动态方程为温度与烧焦罐出口温度相差一个定值aT,(K),d户出×+一~lCscGc.tn一(33)(34)2罗雄瓣,裒曩,林世雄.石油(石油加工),1998,14(2){参考文献611罗雄瓣,裒曩.林世雄.石油(石油加工),1998,14(1);3林世雄主编石油炼制工程(下册)?第二版-北京:石油工34业出版社,1988DYNAMICM0DELING0FFLUIDCA TALYTICCRACKINGUNITⅢ.CatalystTransportSystemandPressureSystem LuoXionglinYuanPuLinShixiong(Uni~dtyofPetroleum,&枷102200) AbstractTheformulawereobtainedtocalculatethespent,regeneratedcatalysttransportrate andthecatalysttranspo~ratefromthesecondstageoftheregeneratortothebottomofthefirstwhic hmustbedeterminedbeforethedynamicmodelingoftheFCCU,accordingtothebalanceofpre ssure. Thepressuredynamictransientequationsforseparatoratthetopoftheriserreactor,mainfracti ona-tor,separator{orgasandgasolineandregeneratorwereproposedonthebasisoftheequationof state foridealgasandthechangeofmolecularratesthroughthevessels.KeywordsFCCU,catalysttransport,pressure,model,dynamic。
加氢裂化装置分馏岗位操作参数调节

加氢裂化装置分馏岗位操作参数调节(一)脱硫化氢塔C201-烃类含量,对其下脱硫化氢塔的主要目的是减少反应生成油中硫化氢和C5游的分馏设备不须考虑硫化氢的腐蚀问题。
当塔的操作压力恒定时,塔的操作温-烃类分压降低,而液相中度是一重要参数。
若塔顶温度低时,气相中硫化氢、C5-烃类含量就会增加,回流至下部,造成塔底硫化氢和轻烃含量高,的硫化氢、C5+汽化,增加塔顶冷凝负荷和影响下游的操作。
若塔顶温度过高,就会有大量C5P201负荷。
所以正确的操作温度应是即不太高也不太低,尽可能按设计条件来操作。
A、操作参数调节1、进料温度提高进料温度,可以提高塔进料口以上气相负荷,有助于脱除硫化氢、水和轻烃。
但是增大了塔顶冷凝器的负荷和塔顶回流量,过高的烃、蒸汽和液体流率也会导致塔液泛。
进料温度由热低分油温度和冷低分油经1401-E-102换后温度来共同决定的。
塔进料温度的高低表示低分油带进塔的热量大小。
进料温度过高,增加塔的操作负荷;温度太低,加氢生成油脱硫化氢不完全,严重时会导致柴油腐蚀不合格。
2.塔顶温度S,同时汽提出少量的水、轻烃(液D201的作用主要是脱除加氢生成油中的H2化气组分),轻烃去吸收脱吸塔。
提高塔顶温度也就提高了硫化氢汽提塔全塔温+进入回流罐,使塔顶度,易于脱除硫化氢,但较高的塔顶温度会导致较多的C5冷凝负荷增大。
所以塔顶温度要按照操作指标严格控制。
塔顶回流方式为部分回流。
当塔顶温度过高或过低时,可以通过适当改变回流量来调节。
塔顶温度是通过温控调节器1402-TIC0101与塔顶回流量调节器1402-FIC0101串级控制来保证塔顶温度恒定。
4. 塔顶压力高的操作压力不利于硫化氢的脱除,增加了塔顶冷凝负荷。
塔的操作压力必须是能将D201的排放气体压入C205,最高的塔压不应高于塔顶安全阀定压。
压力过低,塔顶挥发量过大,使回流量过大;C201塔底油也不易压入C202,不利于下游系统平稳操作。
塔的操作压力由设于D201处的1402-PIC0201来调节,正常操作期间操作压力应保持稳定。
- 1、下载文档前请自行甄别文档内容的完整性,平台不提供额外的编辑、内容补充、找答案等附加服务。
- 2、"仅部分预览"的文档,不可在线预览部分如存在完整性等问题,可反馈申请退款(可完整预览的文档不适用该条件!)。
- 3、如文档侵犯您的权益,请联系客服反馈,我们会尽快为您处理(人工客服工作时间:9:00-18:30)。
浅谈催化裂化装置中分馏塔塔顶压力
的影响因素
炼油一车间
赵强
浅谈催化裂化装置中分馏塔塔顶压力
的影响因素
赵强
(乌石化炼油厂一车间)
前言:催化裂化分馏塔的主要任务是将来自反应系统的高温油气脱过热后,根据各组分沸点的不同切割为富气、汽油、柴油、回炼油和油浆等,通过温度,压力,回流量等工艺因素控制,保证各馏分质量合格。
关键词:催化裂化,分馏塔,压力,汽油,柴油,回炼油,油浆
一 基本情况介绍:
蜡油催化裂化装置近期在生产过程中,分馏塔顶压力一直不好控制,从原来的115kPa 下降到113kPa 在到现在的110kPa ,如图(一),
分馏塔顶压力月平均
111
111.5112112.5113113.5114114.5115115.5
1月份
2月份
3月份
4月份
5月份
6月份
图1 2008年1月份到6月份
在我装置生产过程中,分馏塔顶压力要控制在105kPa 到135kPa 之间,从上述据上看分馏塔的压力都在正常控制压力之内,但是在近期的观察中,发现分馏塔顶压力一直在降低。
在催化裂化装置中分馏塔顶压力是控制
各侧线流出产品质量的重要参数,分流塔顶压力的过高或过低都会使产品的质量受到很大影响,当分馏塔顶压力过低时,粗汽油的干点就会升高,而柴油的终馏点却会降低;当分馏塔塔顶压力过高则反之。
而汽油
的干点说明了汽油在发动机
中蒸发完全的程度,这个温度过高,说明重
质成分过多,其结果是降低发动机的功率和
经济性,因此我们要控制好分馏塔的压力。
二原因分析:
影响分馏塔顶压力的主要原因有以下几点:原料的性质,反应温度,反应压力,催化剂的活性,分馏塔顶的温度,分馏塔的中部温度,塔底的气相温度,分馏塔的顶部及各中部回流量,气压机的转速,塔顶的安全阀,以及Dg400,Dg200阀的开度等因素,下面从原料性质,分馏塔中部温度,分馏塔底汽相温度3个方面来分析分馏塔顶压力。
2.1 在催化裂化装置中,分馏塔顶的压力来源于原料裂解之后经过分馏塔的各中段回流和塔顶回流之后的不凝气体,这些气体是通过高温催化剂和原料的相互接触使原料裂解而生成的,所以分馏塔的压力和原料的性质,催化剂的活性,反应温度都有关系,下面就是6月15日到6月17日之间原料性质和反应温度的变化情况;
原料性质变化情况
罐位初馏点℃5% 10% 50% 90% 终馏点℃残碳密度
5号285 320 340 420 505 555 0.17 881.6
6号277 344 360 435 521 --- 0.21 882.9
7号270 325 345 430 515 570 0.12 881.7
反应温度变化情况
6月15日6月16日6月17日
反应温度塔顶压力反应温度塔顶压力反应温度塔顶压力1点485113485113489111 3点485113485113489110 5点485113484113487110 7点485114484113487109 9点485113484113487110 11点484113483112488111 13点484113483113487108 15点484112487114481109 17点482114488113481109 19点483113489113482111 21点484113489111482110 23点486113489111480110平均值484.3333113.0833485.8333112.6667485109.8333
这个表格中从6月15日的19点钟到6月16日的15点钟是5号罐裂解,6月16日17点到6月17日13点是6号罐裂解,6月17日以后的7号罐裂解
从上边两个表的数据来看,在6月15日到17日之间,近似的把催化剂的活性看成是一定的,分馏塔顶的压力和原料的5%点有着密切的关系,当原料的5%点从5号罐320℃上升到6号罐344℃再到7号罐的325℃,反应温度从485℃改变到489℃然后在回到480℃的情况下分馏塔顶的压力从113kPa 下降到了111kPa再到110kPa,在反应温度的变化是随着原料性质的变化而变化的情况下,反应压力却一直保持在172 kPa,从这些数据来看分馏塔顶的压力和原料的性质有这直接的关系。
2.2 分馏塔顶的压力不仅只和原料性质、反应操作有关系,它还和分馏塔的操作有关系,下边是分馏塔在生产操作中的一些基本数据:
7号罐TR203 (℃) TRC101 (℃) TR211 (℃) PR210 ( kPa) 1点236 485 367 113
3点234 485 364 113
5点236 485 366 113
7点238 485 368 114
9点235 485 367 113
11点230 485 363 112
13点230 485 362 112
6月15日7号罐分馏塔底气相温度和分馏塔顶压力的变化趋势
从上表中看到在反应温度不变的情况下,分馏塔底汽相温度和中部温度在7点中升高时候,分馏塔顶压力也随之升高,在11点和13点下降的时候分馏塔顶的压力也随之降低。
2.3 分馏塔的操作能够直接影响分馏塔顶的压力,但影响分馏塔顶压力的因素还有很多,如气压机的转速忽高忽低使得分馏塔顶压力不稳,分馏塔顶安全阀失灵,在规定的压力下没有能够起跳,在没有达到规定压力下突然起跳,Dg400和Dg 200火炬阀的失灵开启,大油气线上电动阀的自动关闭或开启,冷凝器的泄露,空冷风机的运转情况,D210液面的高低,D501的压油,C302底部压油都会影响分馏塔顶的压力。
三结论:
经过以上分析,原料的性质,反应温度,反应压力,催化剂的活性,分馏塔顶的温度,分馏塔的中部温度,塔底的气相温度,分馏塔的顶部及各中部回流量,气压机的转速,塔顶的安全阀,以及Dg400,Dg200阀的开度等因素都会对分馏塔顶压力造成影响,而在中些因素中原料性质,反应温度,反应压力对分馏塔顶的压力影响最大,还有分馏塔底汽相温度,和分馏塔的中部温度,顶部温度都可以影响分馏塔顶的压力。
参考文献:
炼油厂一车间蜡油催化裂化装置操作规程,中国石油乌鲁木齐石化公司,2007年1月1日
催化裂化装置技术问答,中国石油化工出版社,2007年6月化工原理(第二版)上册,化工工业出版社
流化催化裂化,中国石化出版社,2008年1月。