qualification of hvac and water system
Validation、Verification、Qualification的区别

Validation、Verification、Qualification的区别制药都离不开GMP,而GMP总是少不了确认和验证。
那么确认和验证到底有什么区别?要搞清楚这个问题,就必须要理解三个词Validation,Qualification 和Verification的英语原意。
不过在讲解这三个词之前,请想象一下如果一个正在学中文的外国朋友问你:“街”、“道”和“路”有什么区别您如何回答呢?我们理解“Verification”、“Qualification”和“Validation”可能就像外国人理解“街”,“道”和“路”的区别,可能永远达不到那种“只可意会不可言传”的境界。
Verification这个词来自于英语的Verify。
意思是“to find out a fact or statements…etc. is true去核实一个事实或说法是真实的”,也就是查验(check)的意思。
其隐含的意义是“已经有某个事实或说法存在”,而这个动作就是找出这个事实或说法是真实的。
举个例子,我们可以说:“请verify张三是不是一个GMP审核员”。
这个动作的隐含前提是已经有“张三是GMP审核员”的说法存在了。
制药界对这个词的翻译重要性尚没有共同认可。
目前最贴切的翻译是“确证”。
Qualification这个词制药界的朋友都非常熟识,来自于Qualify,一直被公认翻译为"确认"。
可是估计很少有人真正理解Qualify是什么意思。
其原意是指"to pass an exam or meet the standards of something", 即"达到了一定的标准,从而能够做某种事情"。
设备的Qualification是其原意的延伸,即某个设备达到了一定的标准,可以被用来做某个预定的生产步骤。
Qualification的过程一定要有"预定的标准"。
确认、再确认

Qualification, Requalification - frequent Obscurities确认、再确认常见的疑问ECA GMP新闻2013年10月2日1、总则有关确认、再确认及监测经常会被搞混,尤其是在GMP环境下使用不同的ISO惯用语,因此以下对于这三个词进行解释并以水系统为例进行举例说明。
根据GMP的大体定义:确认:确保新的设备、厂房或是即将使用的设备满足既定用途再确认:保证在变更或是给定周期的周期性设备评估内设备仍处于合格的状态监测:对于设备或者系统的监督,可以是连续的、也可以是间断的但是对于再确认而言需要更详细的解释,严格上来说,再确认在欧盟附录十五中并没有被提及。
但是再验证是有相关描述的,而确认常被理解为验证的一部分,再确认也是必须的,并没有设定的时间标准,但须规定实施定期的再确认。
这些并不是需要满足基本要求,而是与系统相关并要基于风险评估。
很多情况下,再确认是3-5年。
以注射剂全自动灯检系统为例,一般是1-2年。
很重要的是,再确认不要被理解成验证工作的重复。
经常的,在设备没有变更的范畴内,没必要进行新的测试或测量。
再确认就是常规操作的一个数据回顾。
因此,质量相关设备、质量标准参数及一段时期内设备变更及偏差会被分析到。
对于台账的分析也是评估的一部分,还有GMP审查员不会认为年度质量回顾可代替再确认。
The terms qualification, requalification and monitoring are often mixed up, especially if the somewhat different language from ISO standards is used in the GMP environment.Therefore, the three terms will be explained in the following and then differentiated one from the other by way of the examples watersystem and clean room.General definitions according to GMP:Qualification: ensuring in the case of new equipment/facilities or equipment entering into service that they serve their intended purposeRequalification*: ensuring that the equipment is still in the qualified state after a change AND periodical assessment of eqipment within defined time intervalsMonitoring: supervision of equipment or a system - this can be performed continuously or discontinuouslyBut the topic of requalification* needs to be considered in more detail. Strictly speaking, requalification is not mentioned in Annex 15 of the EU Guidelines to Good Manufacturing Practice which is the guidance document for qualification in Europe. But revalidation is described (e.g. article 45) and since qualification is considered to be a subset of validation, a requalification also is required. There is no setting of time standards. But it should be stipulated when a periodically recurring requalification has to be carried out. These requirements should not be taken and met on a general basis but system-related and risk-based. In many cases this is every 3 to 5 years. But in the case of a fully automated system for the visual inspection of parenterals for example, it could be scheduled already every 1 to 2 years. It is very important that this requalification is not understood as a repetition of qualification. Usually, no new tests or measurements are necessary insofar as the equipment concerned was not changed. Here, requalification is rather a review of data from routine operation. Hence, the quality-related equipment or specification parameters are to be considered and analysed as well as the changes in the equipment and the deviations that took place in the period considered. An analysis of the logbook should also bepart of this evaluation. The document should end with a conclusion that informs about the equipment's state: equipment still is considered to be qualified: Yes / No. By the way, GMP inspectors don't consider the annual product review (APR) as substitute for the requalification.2、制药用水为例在确认中,确认和验证这两个词经常被理解的很模糊。
中英文-固体制剂仿制药研发流程

compared with the RLD product.生产一小批经 研究开发 的药品 ,并根 据制成 品规范 对其进 行 测试,这 包括药 品杂质 分布评 估,和 对照药 物 进行比对 ,进行 溶出曲 线研究 。 ⑤ Place the DP on accelerated stability study (up to 3 months) to evaluate the stability of the
API and excipients and
③ API characterization and qualification, including chemical and physical properties
corresponding analytical methods 建立可接 受的原 料药及 辅料标 准和
分析方法 能指示 稳定性 。
3)Vendor qualification, including full testing on the first three lots of CCS. 供应商资 格认证 ,包括 容器密 封系 统前三批 次的测 试
Note: CCS which has been used in FDA approved drugs is highly recomm end ed
1 Drug Packaging Insert Study to obtain basic information about RLD, such a s 通 过对 对照药 物的 包材以 内成分 的分 析,获 取有 关该对 照 药物 的基本 信息 ① Components in the formulation 处方成份 ② BE information 生物等效性信息 ③ Etc.其它
制药系统英文简写
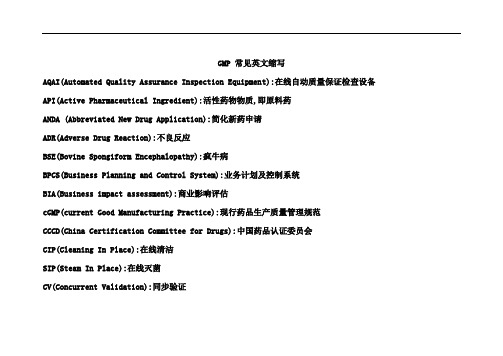
GMP 常见英文缩写AQAI(Automated Quality Assurance Inspection Equipment):在线自动质量保证检查设备API(Active Pharmaceutical Ingredient):活性药物物质,即原料药ANDA (Abbreviated New Drug Application):简化新药申请ADR(Adverse Drug Reaction):不良反应BSE(Bovine Spongiform Encephalopathy):疯牛病BPCS(Business Planning and Control System):业务计划及控制系统BIA(Business impact assessment):商业影响评估cGMP(current Good Manufacturing Practice):现行药品生产质量管理规范CCCD(China Certification Committee for Drugs):中国药品认证委员会CIP(Cleaning In Place):在线清洁SIP(Steam In Place):在线灭菌CV(Concurrent Validation):同步验证CDER( Center for Drug Evaluation and Research):药品研究与评价中心COA(Certificate Of Analysis):分析报告单CFR(Code of Federal Regulation):美国联邦法规CDC(Centers for Disease Control and Prevention):疾病预防控制中心COS/ CEP( Certificate of Suitability for European Pharmacopeia):欧洲药典适用性证书CCD(Certification Committee for Drugs):药品认证管理中心CPMP(Committee for Proprietary Medicinal Products):欧洲专利药品委员会CTD(Common Technical Document): 通用技术文件CDC( Centers for Disease Control and Prevention):疾病预防控制中心GMP(Good Manufacturing Practice): 药品生产质量管理规范TQC(Total Quality Control),TQM(Total Quality Management):全面质量管理EU(European Union):欧洲联盟EFPIA(European Federation of Pharmaceutical Industries Associations):欧洲制药工业协会联合会MHW(Ministry of Health and Welfare,Japan):日本厚生省JPMA(Japan Pharmaceutical Manufacturers Association):日本制药工业协会FDA(US Food and Drug Administration):美国食品与药品管理局PRMA(Pharmaceutical Research and Manufacturers of America):美国药物研究和生产联合会WHO(World Health Organization):世界卫生组织IFPMA(International Federation of Pharmaceutical Manufacturers Associations): 国际制药工业协会联合会PDCA(Plan,Do,Check,Action):计划,执行,检查,处理QA(Quality Assurance):质量保证QC(Quality Control):质量控制QS(Quality System):质量体系QM(Quality Management):质量管理SOP(Standard Operating Procedure):标准操作规程SMP(Standard Management Procedure):标准管理程序SOR(Standard Operating Record):标准操作记录GEP(Good Engineering Practice):工程设计规范HVAC(Heating Ventilation and Air Conditioning):空调净化系统HEPA(High Efficiency Particulate air Filter):高效空气过滤器DQ(Design Qualification):设计确认IQ(Installation Qualification):安装确认OQ(Operational Qualification):运行确认PQ(Performance Qualification):性能确认OOS(Out-Of-Specification):检验不合格;超标PFDS(Process Flow Diagrams):工艺流程图MRA(cMutual Reognition Agreements):现场检查多边认同协议DMF( Drug Master File): EDMF(European Drug Master File)欧盟药物主文件EDQM(European Directorate for Quality Medicines): 欧洲药品质量管理局ORA(Office of Regulatory Affairs):药政事务办公室GGPs( Good Guidance Practices):优良指南规范MOA(Method Of Analysis):分析方法VMP(Validation Master Plan):验证主计划VP(Validation Protocol):验证方案MSDS(Material Safety Data Sheet):物料安全技术说明书NDA (New Drug Application):新药申请OTC(Over-the-counter):非处方INN(International Nonproprietary Name):国际非专有名称USP(the united state pharmacopeia):美国药典NF(National Formulary):美国国家药品集GAP(Good Agricultural Practice):中药材种植管理规范GCP(Good Clinical Practice):药物临床试验质量管理规范GLP(Good Laboratory Practice):药物实验室管理规范GSP(Good Supply Practice):药品经营质量管理规范GUP(Good Use Practice):药品使用质量管理规范PMF(Plant Master File); SMF(Site Master File):工厂主文件EDL(List of Essential Drugs ):基本药物目录PI(Package Insert):说明书PCT( Patent Cooperation Treaty):专利合作条约PPAC(Patent Protection Association of China):中国专利保护协会PIC( Person In Charge):负责人PDS(Pharmaceutical Development Services):整体新药研发机构SPC(Summary of Product Characteristics):产品特性摘要SAL(Sterility Assurance Level)无菌保证水平原料药 API,Active Pharmaceutical Ingredient,美国焊接学会 AWS,American Welding Society生物耗氧量 BOD,Biochemical Oxygen Demand菌落数 CFU,Colony Forming Units关键运行参数 COD,Critical Operating Data化学耗氧量 COD设计确认 DQ,Design Qualification增强设计审核 EDR,Enhanced Design Review工厂验收测试 FAT,Factory Acceptance Test良好自动化质量规范 GAMP,Good Automated Manufacturing Practice 良好工程规范 GEP ,Good Engineering Practice生产质量规范 GMP,Good Manufacturing Practice输入输出 IO,Input/Output安装确认 IQ,Installation Qualification运行确认 OQ ,Operational Qualification氧化还原电势 ORP,Oxidation-Reduction Potential管道和仪表工艺流程图 P&ID,Piping and Instrumentation Diagrams可编程序逻辑控制器 PLC ,Programmable Logic Controller性能确认 PQ ,Performance Qualification在系统或系统主要元件交付到现场之前的检查和测试 PDI,Pre-Delivery Inspection 工艺流程图 PFD,Process Flow Diagrams聚偏氟乙稀 PVDF,Polyvinylidene Fluoride聚四氟乙烯 PTFE,Polytetrafluoroethylene聚丙烯 PP,Polypropylene反渗透 RO,Reverse Osmosis电去离子 EDI,ElectroDeIonization标准操作程序 SOP,Standard Operating Procedure现场验收测试 SAT ,Site Acceptance Test用户技术要求说明 URS,User Requirement Specification 总有机碳 TOC,Total Organic Carbon注射用水 WFI ,Water For Injection。
WHO指南 附件8 非无菌产品空调系统指南翻译

目录1 Introduction 简介 (2)2 Scope 范围 (2)3 Glossary 术语 (2)4 Premises 厂房 (4)5 Design of HVAC systems and components 空调系统和组件的设计 (6)6 Full fresh air systems and recirculation systems 全新风系统和再循环系统 (8)7 Air filtration, airflow direction and pressure differentials 空气过滤、气流方向和压差 (8)8 Temperature and relative humidity 温度和相对湿度 (10)9 Dust, vapour and fume control 粉尘、蒸汽和烟雾控制 (10)10 Protection of the environment 环境保护 (11)11 Commissioning 试运行 (11)12 Qualification 确认 (11)13 Maintenance 维护 (12)1 Introduction介绍略2 Scope范围These guidelines focus primarily on GMP for the design, qualification, management and maintenance of HVAC systems in facilities for the manufacture of non-sterile dosage forms.They are intended to complement the guidelines on GMP for pharmaceutical products and should be read in conjunction with the parent guide. The additional standards addressed in these guidelines should therefore be considered supplementary to the general requirements set out in the main principles guide (4).该指南主要适用于非无菌制剂生产设施中空调系统GMP方面的设计、确认、管理和维护。
HVAC的概念HVAC-cn

DEFINE THE CRITICAL ONES 定义关键项
DEFINE WHERE MANUFACTURE 定义制造地点 DEFINE WHO MANUFACTURE 定义制造者
ISOLATOR 隔离的区域 DEDICATED AREA 指定的区域 COMMON AREA 公共的区域 MACHINES – PERSONNEL 机器-人员
IT IS INTENDED TO CONTROL THE AIR HUMIDITY AND KEEP THE AIR CLEAN 控制空气湿度,保持洁净
“IT IS INTENDED TO KEEP THE AIR CLEAN” 用来保证空气洁净
TRAINING SESSION
6
HVACs DESIGN 设计
TRAINING SESSION
TEMPERATURE CONTROL DEHUMIDIFICATION 温度控制,除湿
5
HVACs DESIGN 设计
HEATING VENTILATING AIR CONDITIONING
IT IS INTENDED TO CONTROL THE TEMPERATURE OF THE AIR 用来控制空气温度 IT IS INTENDED TO GUARANTEE BOTH AIR CHANGES IN ROOMS AND PRESSURE DIFFERENTIALS AMONGST ROOMS. 保证房间的换气 和压差
步骤步骤步骤步骤weighing称量mixing混合filling填充packaging包装criticalones定义关键项productionprocess生产过程生产过程生产过程生产过程trainingsessionprotectoperators保护产品和操作人员productcontaminationcross产品污染交差productdegradation产品降解airtreatment空气处理空气处理空气处理空气处理filters过滤器过滤器过滤器过滤器overpressure正压正压正压正压dehumidification除湿除湿除湿除湿segregation隔离temperaturecontroldehumidification温度控制除湿hvacsdesign设计trainingsessionhvacsdesign设计airhumidityairclean控制空气湿度保持洁净guaranteebothairchangespressuredifferentialsamongstrooms
(2021年整理)ISPE指南目录

(完整)ISPE指南目录编辑整理:尊敬的读者朋友们:这里是精品文档编辑中心,本文档内容是由我和我的同事精心编辑整理后发布的,发布之前我们对文中内容进行仔细校对,但是难免会有疏漏的地方,但是任然希望((完整)ISPE指南目录)的内容能够给您的工作和学习带来便利。
同时也真诚的希望收到您的建议和反馈,这将是我们进步的源泉,前进的动力。
本文可编辑可修改,如果觉得对您有帮助请收藏以便随时查阅,最后祝您生活愉快业绩进步,以下为(完整)ISPE指南目录的全部内容。
ISPE指南按系列分类的目录清单:GAMP5GAMP 5: A Risk-Based Approach to Compliant GxP Computerized SystemsGAMP 5: 保证GXP计算机系统符合性的基于风险的方法GAMP Good Practice GuidesA Risk-Based Approach to Calibration Management (Second Edition)基于风险的校正管理方法(第二版)A Risk-Based Approach to Electronic Records and Signatures基于风险的电子记录和签名方法A Risk—Based Approach to GxP Compliant Laboratory ComputerizedSystems (Second Edition)基于风险的GXP符合性实验室计算机化系统方法(第二版)A Risk—Based Approach to GxP Process Control Systems (SecondEdition)基于风险的GXP工艺控制体系方法(第二版)A Risk-Based Approach to Operation of GxP Computerized Systems -A Companion Volume to GAMP 5基于风险的GXP计算机系统操作方法——-GAMP 5姊妹篇A Risk-Based Approach to Regulated Mobile Applications基于风险的移动APP管理方法A Risk-Based Approach to Testing of GxP Systems (Second Edition)基于风险的GXP系统检测方法(第二版)Electronic Data Archiving电子数据归档Global Information Systems Control and Compliance全球信息系统控制和符合性IT Infrastructure Control and ComplianceIT基础设施控制和符合性Legacy Systems遗留系统Manufacturing Execution Systems – A Strategic and Program Management Approach生产执行系统—策略和编程管理方法GAMP Good Practice Guides Under Development制订中的GAMP GPGISPE Baseline Pharmaceutical Engineering Guides for New and Renovated FacilitiesISPE基准:新设施和创新型设施药品工程指南Volume 1: Active Pharmaceutical Ingredients (Second Edition) - Revision to Bulk Pharmaceutical Chemicals卷1:活性药物成分(第二版)---对散装药用化学品的修订Volume 2: Oral Solid Dosage Forms (Second Edition)卷2:口服固体制剂(第二版)Volume 3: Sterile Product Manufacturing Facilities (Second Edition)卷3:无菌药品生产设施(第二版)Volume 4: Water and Steam Systems (Second Edition)卷4:水和蒸汽系统(第二版)Volume 5: Commissioning and Qualification卷5:调试和确认Volume 6: Biopharmaceutical Manufacturing Facilities (Second Edition)卷6:生物药品生产设施(第二版)Volume 7: Risk—Based Manufacture of Pharmaceutical Products (Risk—MaPP)卷7:基于风险的药品生产(风险MAPP)Baseline Guides Under Development制订中的基准指南ISPE GuidesISPE Guide: Science and Risk-Based Approach for the Delivery of Facilities, Systems, and EquipmentISPE指南:基于风险的设施、系统和设备传送科学方法ISPE Guide: Biopharmaceutical Process Development and ManufacturingISPE指南:生物药品工艺开发和生产(新出版)ISPE Guides Under Development在制订中的ISPE指南ISPE Good Practice Guides 优良规范指南ISPE Good Practice Guide: Applied Risk Management for Commissioning and QualificationISPE GPG:在调试和确认中应用风险管理ISPE Good Practice Guide: Approaches to Commissioning and Qualification of Pharmaceutical Water and Steam Systems (Second Edition)ISPE GPG:药用水和蒸汽系统调试和确认方法(第二版)(新出)ISPE Good Practice Guide: Assessing the Particulate Containment Performance of Pharmaceutical Equipment (Second Edition)ISPE GPG:制药设备颗粒密闭性能的评估(第二版)ISPE Good Practice Guide: Booklet LabelsISPE GPG:书册标签ISPE Good Practice Guide: Clinical Supply SystemsISPE GPG:临床补给系统(新出)ISPE Good Practice Guide: Cold Chain ManagementISPE GPG:冷链管理ISPE Good Practice Guide: Comparator ManagementISPE GPG:对照组管理ISPE Good Practice Guide: Development of Investigational Therapeutic Biological ProductsISPE GPG:临床前治疗用生物产品开发ISPE Good Practice Guide: Good Engineering PracticeISPE GPG:优良工程规范ISPE Good Practice Guide: Harmonizing the Definition and Use of Non—Investigational Medicinal Products (NIMPs)ISPE GPG:协调非临床前药品的定义和使用ISPE Good Practice Guide: Heating, Ventilation, and Air Conditioning (HVAC)ISPE GPG:HVACISPE Good Practice Guide: Interactive Response TechnologyISPE GPG:互动反馈技术ISPE Good Practice Guide: MaintenanceISPE GPG:维护ISPE Good Practice Guide: Ozone Sanitization of Pharmaceutical Water SystemISPE GPG:制药用水系统的臭氧消毒ISPE Good Practice Guide: Packaging, Labeling, and Warehousing FacilitiesISPE GPG:包装、贴标和仓储设计ISPE Good Practice Guide: Process GasesISPE GPG:工艺用气ISPE Good Practice Guide: Project Management for the Pharmaceutical IndustryISPE GPG:制药行业的项目管理ISPE Good Practice Guide: Quality Laboratory FacilitiesISPE GPG:质量化验室设施ISPE Good Practice Guide: Technology Transfer (Second Edition)ISPE GPG:技术转移(第二版)(新出)ISPE Good Practice Guides Under Development制订中的ISPE GPGPQLI Guides 药品质量生命周期实施指南PQLI Overview Good Practice GuidePQLI概览GPGProduct Quality Lifecycle Implementation (PQLI) from Concept to Continual ImprovementPart 1: Product Realization using QbD, Concepts and Principles从概念到持续改进的药品质量生命周期实施(PQLI)第一部分:利用质量源于设计(QbD)实现实现,概念和原则Product Quality Lifecycle Implementation (PQLI) from Concept to Continual ImprovementPart 2: Product Realization using QbD, Illustrative Example从概念到持续改进的药品质量生命周期实施(PQLI)第二部分:利用质量源于设计(QbD)实现实现,实例解说Product Quality Lifecycle Implementation (PQLI) from Concept to Continual ImprovementPart 3: Change Management System as a Key Element of a Pharmaceutical Quality System 从概念到持续改进的药品质量生命周期实施(PQLI)第三部分:药品质量体系关键要素变更管理Product Quality Lifecycle Implementation (PQLI) from Concept to Continual ImprovementPart 4: Process Performance and Product Quality Monitoring System (PP&PQMS)从概念到持续改进的药品质量生命周期实施(PQLI)第四部分:工艺性能和药品质量监测体系(PP&PQMS)ISPE PQLI Guides Under Development制订中的ISPE PQLI指南。
药学英语--欧盟GMP第四卷(最新英文原版)

EudraLexThe Rules Governing Medicinal Products in the European UnionVolume 4EU Guidelines toGood Manufacturing PracticeMedicinal Products for Human and Veterinary UsePart IChapter 1 Quality ManagementPrincipleThe holder of a Manufacturing Authorisation must manufacture medicinal products so as to ensure that they are fit for their intended use, comply with the requirements of the Marketing Authorisation and do not place patients at risk due to inadequate safety, quality or efficacy. The attainment of this quality objective is the responsibility of senior management and requires the participation and commitment by staff in many different departments and at all levels within the company, by the company‟s suppliers and by the distributors. To achiev e the quality objective reliably there must be a comprehensively designed and correctly implemented system of Quality Assurance incorporating Good Manufacturing Practice, Quality Control and Quality Risk Management. It should be fully documented and its effectiveness monitored. All parts of the Quality Assurance system should be adequately resourced with competent personnel, and suitable and sufficient premises, equipment and facilities. There are additional legal responsibilities for the holder of the Manufacturing Authorisation and for the Qualified Person(s).The basic concepts of Quality Assurance, Good Manufacturing Practice, Quality Control and Quality Risk Management are inter-related. They are described here in order to emphasise their relationships and their fundamental importance to the production and control of medicinal products.Quality Assurance1.1 Quality Assurance is a wide-ranging concept, which covers all matters, which individually or collectively influence the quality of a product. It is the sum total of the organised arrangements made with the objective of ensuring that medicinal products are of the quality required for their intended use. Quality Assurance therefore incorporates Good Manufacturing Practice plus other factors outside the scope of this Guide.The system of Quality Assurance appropriate for the manufacture of medicinal products should ensure that:(i) medicinal products are designed and developed in a way that takes account of the requirements of Good Manufacturing Practice;(ii) production and control operations are clearly specified and Good Manufacturing Practice adopted;(iii) managerial responsibilities are clearly specified;(iv) arrangements are made for the manufacture, supply and use of the correct starting and packaging materials;(v) all necessary controls on intermediate products, and any other in-process controls and validations are carried out;(vi) the finished product is correctly processed and checked, according to the defined procedures; (vii) medicinal products are not sold or supplied before a Qualified Person has certified that each production batch has been produced and controlled in accordance with the requirements of the Marketing Authorisation and any other regulations relevant to the production, control and release of medicinal products;(viii) satisfactory arrangements exist to ensure, as far as possible, that the medicinal products are stored, distributed and subsequently handled so that quality is maintained throughout their shelf life;(ix) there is a procedure for Self-Inspection and/or quality audit, which regularly appraises the effectiveness and applicability of the Quality Assurance system.Good Manufacturing Practice for Medicinal Products (GMP)1.2 Good Manufacturing Practice is that part of Quality Assurance which ensures that products are consistently produced and controlled to the quality standards appropriate to their intended use and as required by the Marketing Authorisation or product specification.Good Manufacturing Practice is concerned with both production and quality control. The basic requirements of GMP are that:(i) all manufacturing processes are clearly defined, systematically reviewed in the light of experience and shown to be capable of consistently manufacturing medicinal products of the required quality and complying with their specifications;(ii) critical steps of manufacturing processes and significant changes to the process are validated; (iii) all necessary facilities for GMP are provided including:• a ppropriately qualified and trained personnel;• adequate premises and space;• suitable equipment and services;• correct materials, containers and labels;• approved procedures and instructions;• suitable storage and transport;(iv) instructions and procedures are written in an instructional form in clear and unambiguous language, specifically applicable to the facilities provided;(v) operators are trained to carry out procedures correctly;(vi) records are made, manually and/or by recording instruments, during manufacture which demonstrate that all the steps required by the defined procedures and instructions were in fact taken and that the quantity and quality of the product was as expected. Any significant deviations are fully recorded and investigated;(vii) records of manufacture including distribution which enable the complete history of a batch to be traced, are retained in a comprehensible and accessible form;(viii) the distribution (wholesaling) of the products minimises any risk to their quality;(ix) a system is available to recall any batch of product, from sale or supply;(x) complaints about marketed products are examined, the causes of quality defects investigated and appropriate measures taken in respect of the defective products and to prevent reoccurrence. Quality Control1.3 Quality Control is that part of Good Manufacturing Practice which is concerned with sampling, specifications and testing, and with the organisation, documentation and release procedures which ensure that the necessary and relevant tests are actually carried out and that materials are not released for use, nor products released for sale or supply, until their quality has been judged to be satisfactory.The basic requirements of Quality Control are that:(i) adequate facilities, trained personnel and approved procedures are available for sampling, inspecting and testing starting materials, packaging materials, intermediate, bulk, and finished products, and where appropriate for monitoring environmental conditions for GMP purposes; (ii) samples of starting materials, packaging materials, intermediate products, bulk products and finished products are taken by personnel and by methods approved by Quality Control;(iii) test methods are validated;(iv) records are made, manually and/or by recording instruments, which demonstrate that all the required sampling, inspecting and testing procedures were actually carried out. Any deviations are fully recorded and investigated;(v) the finished products contain active ingredients complying with the qualitative and quantitative composition of the Marketing Authorisation, are of the purity required, and are enclosed within their proper containers and correctly labelled;(vi) records are made of the results of inspection and that testing of materials, intermediate, bulk, and finished products is formally assessed against specification. Product assessment includes a review and evaluation of relevant production documentation and an assessment of deviations from specified procedures;(vii) no batch of product is released for sale or supply prior to certification by a Qualified Person that it is in accordance with the requirements of the relevant authorisations;(viii) sufficient reference samples of starting materials and products are retained to permit future examination of the product if necessary and that the product is retained in its final pack unless exceptionally large packs are produced.Product Quality Review1.4 Regular periodic or rolling quality reviews of all licensed medicinal products, including export only products, should be conducted with the objective of verifying the consistency of the existing process, the appropriateness of current specifications for both starting materials and finished product to highlight any trends and to identify product and process improvements. Such reviews should normally be conducted and documented annually, taking into account previous reviews, and should include at least:(i) A review of starting materials including packaging materials used in the product, especially those from new sources.(ii) A review of critical in-process controls and finished product results.(iii) A review of all batches that failed to meet established specification(s) and their investigation.(iv) A review of all significant deviations or non-conformances, their related investigations, and the effectiveness of resultant corrective and preventative actions taken.(v) A review of all changes carried out to the processes or analytical methods.(vi) A review of Marketing Authorisation variations submitted/granted/refused, including those for third country (export only) dossiers.(vii) A review of the results of the stability monitoring programme and any adverse trends. (viii) A review of all quality-related returns, complaints and recalls and the investigationsperformed at the time.(ix) A review of adequacy of any other previous product process or equipment corrective actions. (x) For new marketing authorisations and variations to marketing authorisations, a review of post-marketing commitments.(xi) The qualification status of relevant equipment and utilities, e.g. HV AC, water, compressed gases, etc.(xii) A review of any contractual arrangements as defined in Chapter 7 to ensure that they are up to date.The manufacturer and marketing authorisation holder should evaluate the results of this review, where different, and an assessment made of whether corrective and preventative action or any revalidation should be undertaken. Reasons for such corrective actions should be documented. Agreed corrective and preventative actions should be completed in a timely and effective manner. There should be management procedures for the ongoing management and review of these actions and the effectiveness of these procedures verified during self- inspection. Quality reviews may be grouped by product type, e.g. solid dosage forms, liquid dosage forms, sterile products, etc. where scientifically justified.Where the marketing authorisation holder is not the manufacturer, there should be a technical agreement in place between the various parties that defines their respective responsibilities in producing the quality review. The Qualified Person responsible for final batch certification together with the marketing authorisation holder should ensure that the quality review is performed in a timely manner and is accurate.Quality Risk Management1.5 Quality risk management is a systematic process for the assessment, control, communication and review of risks to the quality of the medicinal product. It can be applied both proactively and retrospectively.1.6 The quality risk management system should ensure that:- the evaluation of the risk to quality is based on scientific knowledge, experience with the process and ultimately links to the protection of the patient- the level of effort, formality and documentation of the quality risk management process is commensurate with the level of riskExamples of the processes and applications of quality risk management can be found inter alia in Annex 20.CHAPTER 2 PERSONNELPrincipleThe establishment and maintenance of a satisfactory system of quality assurance and the correct manufacture of medicinal products relies upon people. For this reason there must be sufficient qualified personnel to carry out all the tasks which are the responsibility of the manufacturer. Individual responsibilities should be clearly understood by the individuals and recorded. All personnel should be aware of the principles of Good Manufacturing Practice that affect them and receive initial and continuing training, including hygiene instructions, relevant to their needs. General2.1 The manufacturer should have an adequate number of personnel with the necessary qualifications and practical experience. The responsibilities placed on any one individual should not be so extensive as to present any risk to quality.2.2 The manufacturer must have an organisation chart. People in responsible positions should havespecific duties recorded in written job descriptions and adequate authority to carry out their responsibilities. Their duties may be delegated to designated deputies of a satisfactory qualification level. There should be no gaps or unexplained overlaps in the responsibilities of those personnel concerned with the application of Good Manufacturing Practice.Key Personnel2.3 Key Personnel include the head of Production, the head of Quality Control, and if at least one of 1 these persons is not responsible for the duties described in Article 51 of Directive 2001/83/EC , the Qualified Person(s) designated for the purpose. Normally key posts should be occupied by full-time personnel. The heads of Production and Quality Control must be independent from each other. In large organisations, it may be necessary to delegate some of the functions listed in 2.5, 2.6 and 2.7.2.4 The duties of the Qualified Person(s) are fully described in Article 51 of Directive 2001/83/EC, and can be summarised as follows:(a) for medicinal products manufactured within the European Community, a Qualified Person must ensure that each batch has been produced and tested/checked in accordance with the directives and the marketing authorisation ;(b) for medicinal products manufactured outside the European Community, a Qualified Person must ensure that each imported batch has undergone, in the importing country, the testing specified in paragraph 1 (b) of Article 51;(c) a Qualified Person must certify in a register or equivalent document, as operations are carried out and before any release, that each production batch satisfies the provisions of Article 51.The persons responsible for these duties must meet the qualification requirements laid down in Article 493 of the same Directive, they shall be permanently and continuously at the disposal of the holder of the Manufacturing Authorisation to carry out their responsibilities. Their responsibilities may be delegated, but only to other Qualified Person(s).2.5 The head of the Production Department generally has the following responsibilities:i. to ensure that products are produced and stored according to the appropriate documentation in order to obtain the required quality;ii. to approve the instructions relating to production operations and to ensure their strict implementation;iii. to ensure that the production records are evaluated and signed by an authorised person before they are sent to the Quality Control Department;iv. to check the maintenance of his department, premises and equipment;v. to ensure that the appropriate validations are done;vi. to ensure that the required initial and continuing training of his department personnel is carried out and adapted according to need.2.6 The head of the Quality Control Department generally has the following responsibilities:i. to approve or reject, as he sees fit, starting materials, packaging materials, and intermediate, bulk and finished products;ii. to evaluate batch records;iii. to ensure that all necessary testing is carried out;iv. to approve specifications, sampling instructions, test methods and other Quality Control procedures;v. to approve and monitor any contract analysts;vi. to check the maintenance of his department, premises and equipment;vii. to ensure that the appropriate validations are done;viii. to ensure that the required initial and continuing training of his department personnel is carried out and adapted according to need.Other duties of the Quality Control Department are summarised in Chapter 6.2.7 The heads of Production and Quality Control generally have some shared, or jointly exercised, responsibilities relating to quality. These may include, subject to any national regulations:— the authorisation of written procedures and other documents, including amendments;— the monitoring and control of the manufacturing environment;— plant hygiene;— process validation;— training;— the approval and monitoring of suppliers of materials;— the approval and monitoring of contract manufacturers;— the designation and monitoring of storage conditions for materials and products;— the retention of records;— the monitoring of compliance with the requirements of Good Manufacturing Practice;— the inspection, investigation, and taking of samples, in order to monitor factors which may affect product quality.Training2.8 The manufacturer should provide training for all the personnel whose duties take them into production areas or into control laboratories (including the technical, maintenance and cleaning personnel), and for other personnel whose activities could affect the quality of the product.2.9 Besides the basic training on the theory and practice of Good Manufacturing Practice, newly recruited personnel should receive training appropriate to the duties assigned to them. Continuing training should also be given, and its practical effectiveness should be periodically assessed. Training programmes should be available, approved by either the head of Production or the head of Quality Control, as appropriate. Training records should be kept.2.10 Personnel working in areas where contamination is a hazard, e.g. clean areas or areas where highly active, toxic, infectious or sensitising materials are handled, should be given specific training.2.11 Visitors or untrained personnel should, preferably, not be taken into the production and quality control areas. If this is unavoidable, they should be given information in advance, particularly about personal hygiene and the prescribed protective clothing. They should be closely supervised.2.12 The concept of Quality Assurance and all the measures capable of improving its understanding and implementation should be fully discussed during the training sessions. Personnel Hygiene2.13 Detailed hygiene programmes should be established and adapted to the different needs within the factory. They should include procedures relating to the health, hygiene practices and clothing of personnel. These procedures should be understood and followed in a very strict way by every person whose duties take him into the production and control areas. Hygiene programmes should be promoted by management and widely discussed during training sessions.2.14 All personnel should receive medical examination upon recruitment. It must be the manufacturer‟s responsibility t hat there are instructions ensuring that health conditions that can be of relevance to the quality of products come to the manufacturer‟s knowledge. After the first medical examination, examinations should be carried out when necessary for the work and personal health.2.15 Steps should be taken to ensure as far as is practicable that no person affected by an infectious disease or having open lesions on the exposed surface of the body is engaged in the manufacture of medicinal products.2.16 Every person entering the manufacturing areas should wear protective garments appropriate to the operations to be carried out.2.17 Eating, drinking, chewing or smoking, or the storage of food, drink, smoking materials or personal medication in the production and storage areas should be prohibited. In general, any unhygienic practice within the manufacturing areas or in any other area where the product might be adversely affected, should be forbidden.2.18 Direct contact should be avoided between the operator‟s hands and the exposed product as well as with any part of the equipment that comes into contact with the products.2.19 Personnel should be instructed to use the hand-washing facilities.2.20 Any specific requirements for the manufacture of special groups of products, for example sterile preparations, are covered in the annexes.CHAPTER 3 PREMISES AND EQUIPMENTPrinciplePremises and equipment must be located, designed, constructed, adapted and maintained to suit the operations to be carried out. Their layout and design must aim to minimise the risk of errors and permit effective cleaning and maintenance in order to avoid cross- contamination, build up of dust or dirt and, in general, any adverse effect on the quality of products.PremisesGeneral3.1 Premises should be situated in an environment which, when considered together with measures to protect the manufacture, presents minimal risk of causing contamination of materials or products.3.2 Premises should be carefully maintained, ensuring that repair and maintenance operations do not present any hazard to the quality of products. They should be cleaned and, where applicable, disinfected according to detailed written procedures.3.3 Lighting, temperature, humidity and ventilation should be appropriate and such that they do not adversely affect, directly or indirectly, either the medicinal products during their manufacture and storage, or the accurate functioning of equipment.3.4 Premises should be designed and equipped so as to afford maximum protection against the entry of insects or other animals.3.5 Steps should be taken in order to prevent the entry of unauthorised people. Production, storage and quality control areas should not be used as a right of way by personnel who do not work in them.Production Area3.6 In order to minimise the risk of a serious medical hazard due to cross-contamination, dedicated and self contained facilities must be available for the production of particular medicinal products, such as highly sensitising materials (e.g. penicillins) or biological preparations (e.g. from live micro-organisms). The production of certain additional products, such as certain antibiotics, certain hormones, certain cytotoxics, certain highly active drugs and non-medicinal products should not be conducted in the same facilities. For those products, in exceptional cases, the principle of campaign working in the same facilities can be accepted provided that specific precautions are taken and the necessary validations are made. The manufacture of technicalpoisons, such as pesticides and herbicides, should not be allowed in premises used for the manufacture of medicinal products.3.7 Premises should preferably be laid out in such a way as to allow the production to take place in areas connected in a logical order corresponding to the sequence of the operations and to the requisite cleanliness levels.3.8 The adequacy of the working and in-process storage space should permit the orderly and logical positioning of equipment and materials so as to minimise the risk of confusion between different medicinal products or their components, to avoid cross-contamination and to minimise the risk of omission or wrong application of any of the manufacturing or control steps.3.9 Where starting and primary packaging materials, intermediate or bulk products are exposed to the environment, interior surfaces (walls, floors and ceilings) should be smooth, free from cracks and open joints, and should not shed particulate matter and should permit easy and effective cleaning and, if necessary, disinfection.3.10 Pipework, light fittings, ventilation points and other services should be designed and sited to avoid the creation of recesses which are difficult to clean. As far as possible, for maintenance purposes, they should be accessible from outside the manufacturing areas.3.11 Drains should be of adequate size, and have trapped gullies. Open channels should be avoided where possible, but if necessary, they should be shallow to facilitate cleaning and disinfection.3.12 Production areas should be effectively ventilated, with air control facilities (including temperature and, where necessary, humidity and filtration) appropriate both to the products handled, to the operations undertaken within them and to the external environment.3.13 Weighing of starting materials usually should be carried out in a separate weighing room designed for that use.3.14 In cases where dust is generated (e.g. during sampling, weighing, mixing and processing operations, packaging of dry products), specific provisions should be taken to avoid cross- contamination and facilitate cleaning.3.15 Premises for the packaging of medicinal products should be specifically designed and laid out so as to avoid mix-ups or cross-contamination.3.16 Production areas should be well lit, particularly where visual on-line controls are carried out.3.17 In-process controls may be carried out within the production area provided they do not carry any risk for the production.Storage Areas3.18 Storage areas should be of sufficient capacity to allow orderly storage of the various categories of materials and products:starting and packaging materials, intermediate, bulk and finished products, products in quarantine, released, rejected, returned or recalled.3.19 Storage areas should be designed or adapted to ensure good storage conditions. In particular, they should be clean and dry and maintained within acceptable temperature limits. Where special storage conditions are required (e.g. temperature, humidity) these should be provided, checked and monitored.3.20 Receiving and dispatch bays should protect materials and products from the weather. Reception areas should be designed and equipped to allow containers of incoming materials to be cleaned where necessary before storage.3.21 Where quarantine status is ensured by storage in separate areas, these areas must be clearly marked and their access restricted to authorised personnel. Any system replacing the physicalquarantine should give equivalent security.3.22 There should normally be a separate sampling area for starting materials. If sampling is performed in the storage area, it should be conducted in such a way as to prevent contamination or cross-contamination.3.23 Segregated areas should be provided for the storage of rejected, recalled or returned materials or products.3.24 Highly active materials or products should be stored in safe and secure areas.3.25 Printed packaging materials are considered critical to the conformity of the medicinal product and special attention should be paid to the safe and secure storage of these materials.Quality Control Areas3.26 Normally, Quality Control laboratories should be separated from production areas. This is particularly important for laboratories for the control of biologicals, microbiologicals and radioisotopes, which should also be separated from each other.3.27 Control laboratories should be designed to suit the operations to be carried out in them. Sufficient space should be given to avoid mix-ups and cross-contamination. There should be adequate suitable storage space for samples and records.3.28 Separate rooms may be necessary to protect sensitive instruments from vibration, electrical interference, humidity, etc.3.29 Special requirements are needed in laboratories handling particular substances, such as biological or radioactive samples.Ancillary Areas3.30 Rest and refreshment rooms should be separate from other areas.3.31 Facilities for changing clothes, and for washing and toilet purposes should be easily accessible and appropriate for the number of users. Toilets should not directly communicate with production or storage areas.3.32 Maintenance workshops should as far as possible be separated from production areas. Whenever parts and tools are stored in the production area, they should be kept in rooms or lockers reserved for that use.3.33 Animal houses should be well isolated from other areas, with separate entrance (animal access) and air handling facilities.Equipment3.34 Manufacturing equipment should be designed, located and maintained to suit its intended purpose.3.35 Repair and maintenance operations should not present any hazard to the quality of the products.3.36 Manufacturing equipment should be designed so that it can be easily and thoroughly cleaned. It should be cleaned according to detailed and written procedures and stored only in a clean and dry condition.3.37 Washing and cleaning equipment should be chosen and used in order not to be a source of contamination.3.38 Equipment should be installed in such a way as to prevent any risk of error or of contamination.3.39 Production equipment should not present any hazard to the products. The parts of the production equipment that come into contact with the product must not be reactive, additive or absorptive to such an extent that it will affect the quality of the product and thus present any hazard.。
WHO验证指南(2016版)解读
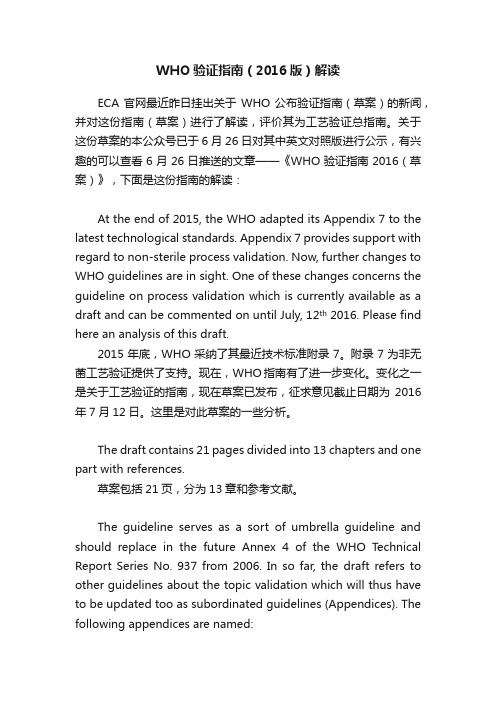
WHO验证指南(2016版)解读ECA官网最近昨日挂出关于WHO公布验证指南(草案)的新闻,并对这份指南(草案)进行了解读,评价其为工艺验证总指南。
关于这份草案的本公众号已于6月26日对其中英文对照版进行公示,有兴趣的可以查看6月26日推送的文章——《WHO验证指南2016(草案)》,下面是这份指南的解读:At the end of 2015, the WHO adapted its Appendix 7 to the latest technological standards. Appendix 7 provides support with regard to non-sterile process validation. Now, further changes to WHO guidelines are in sight. One of these changes concerns the guideline on process validation which is currently available as a draft and can be commented on until July, 12th 2016. Please find here an analysis of this draft.2015年底,WHO采纳了其最近技术标准附录7。
附录7为非无菌工艺验证提供了支持。
现在,WHO指南有了进一步变化。
变化之一是关于工艺验证的指南,现在草案已发布,征求意见截止日期为2016年7月12日。
这里是对此草案的一些分析。
The draft contains 21 pages divided into 13 chapters and one part with references.草案包括21页,分为13章和参考文献。
The guideline serves as a sort of umbrella guideline and should replace in the future Annex 4 of the WHO Technical Report Series No. 937 from 2006. In so far, the draft refers to other guidelines about the topic validation which will thus have to be updated too as subordinated guidelines (Appendices). The following appendices are named:该指南是类似伞样的指南,将来会替代2006年WHO技术报告第937号中的附录4。
空调净化系统运行确认1
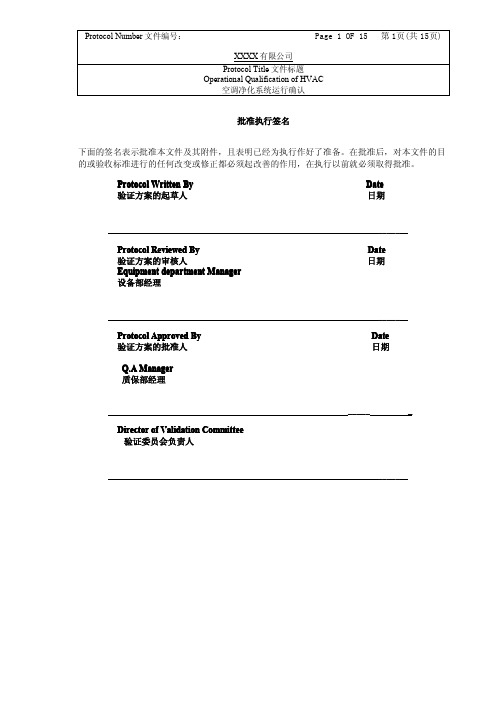
Operational Qualification of HVAC空调净化系统运行确认批准执行签名下面的签名表示批准本文件及其附件,且表明已经为执行作好了准备。
在批准后,对本文件的目的或验收标准进行的任何改变或修正都必须起改善的作用,在执行以前就必须取得批准。
Protocol Written By Date验证方案的起草人日期_____Protocol Reviewed By Date验证方案的审核人日期E quipment department Manager设备部经理_____ Protocol Approved By Date验证方案的批准人日期Q.A Manager质保部经理______ Director of V alidation C ommittee验证委员会负责人_____Operational Qualification of HVAC空调净化系统运行确认目录1范围 (3)2目的 (3)3背景 (3)4介绍 (3)5参考书目 (4)6责任方及其责任 (4)7系统说明 (5)8检验程序 (5)8.1测试用仪器仪表的校准 (5)8.2单机试运转 (5)8.3系统联合试运转 (5)8.4室内风速和风速不均匀度、风量的测定及房间换气次数的计算 (6)8.5静压差的测定 (7)8.6高效过滤器的检漏及过滤效率的测定 (8)8.7气流组织及流线平行性 (10)8.8室内温湿度测定 (11)8.9室内噪声的测定 (12)8.10照度和照度均匀度的测定 (13)8.11表面导静电性能的测定 (14)8.12自净时间的测定 (15)8.13侵入粒子的测定 (15)9验收标准 (15)10附件 (15)附件1签名确认清单附件2验证检验设备和材料附件3单机试运转记录(通风机、水泵)附件4系统联合试运转记录(系统风量的测定)附件5系统联合试运转记录(防倒灌措施确认)附件6室内风速和风速不均匀度、风量的测定及房间换气次数的计算附件7静压差测定附件8高效过滤器的检漏记录附件9气流组织及流线平行性附件10温湿度测试记录附件11室内噪声的测定附件12光照度的确认附件13表面导电性能的测定附件14自净时间的测定记录附件15侵入粒子的测定记录附件16文件偏差日志附件17文件偏差记录Operational Qualification of HVAC空调净化系统运行确认1范围本运行确认方案将会在XXXX有限公司的空调净化系统上实施。
VMP

3
Validation Master Plan
验证总计划 VMP should cover the following activities:
(验证总计划应包括以下各项)
1.
Qualification of facilities and supply systems
– Plant , workshop, etc. – HVAC, water, etc.
13
6.
Function of Representative from R & D 研发部门的责任
Responsible for defining the process (new product or process) to be validated and for providing technical assistance to the validation team by defining specifications, limits, and manufacturing methods.
equipment and/or instrument
4
Validation Master Plan
验证总计划 4. Cleaning validation (CLV)
– Such as for bioreactors or fermentors, chromatographic
columns, etc.
7
Validation Team Members
验证小组人员的组成 The validation team should be consist of the following members: 1. Quality Assurance (QA) Department 2. Quality Control Laboratory 3. Engineering (Utilities) 4. Equipment Calibration/Maintenance 5. Production/manufacturing 6. Product Research and Development 7. Packaging Department
世界卫生组织HVAC非无菌制药指南(中英对照)WHO_937
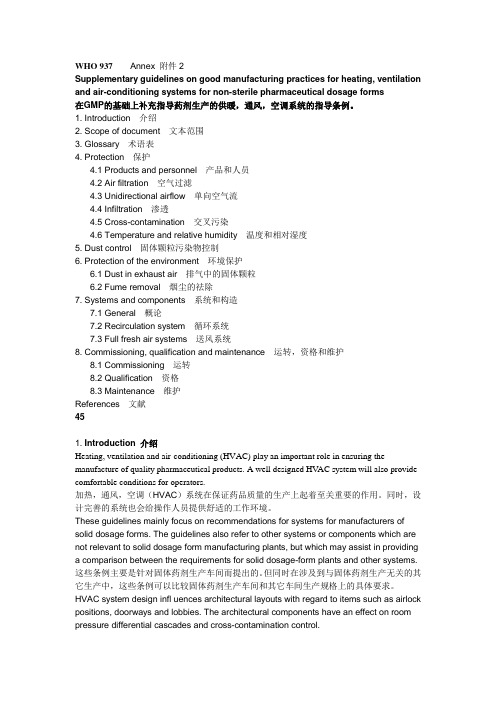
WHO 937 Annex 附件2Supplementary guidelines on good manufacturing practices for heating, ventilation and air-conditioning systems for non-sterile pharmaceutical dosage forms在GMP的基础上补充指导药剂生产的供暖,通风,空调系统的指导条例。
1. Introduction 介绍2. Scope of document 文本范围3. Glossary 术语表4. Protection 保护4.1 Products and personnel 产品和人员4.2 Air filtration 空气过滤4.3 Unidirectional airflow 单向空气流4.4 Infiltration 渗透4.5 Cross-contamination 交叉污染4.6 Temperature and relative humidity 温度和相对湿度5. Dust control 固体颗粒污染物控制6. Protection of the environment 环境保护6.1 Dust in exhaust air 排气中的固体颗粒6.2 Fume removal 烟尘的祛除7. Systems and components 系统和构造7.1 General 概论7.2 Recirculation system 循环系统7.3 Full fresh air systems 送风系统8. Commissioning, qualification and maintenance 运转,资格和维护8.1 Commissioning 运转8.2 Qualification 资格8.3 Maintenance 维护References 文献451. Introduction 介绍Heating, ventilation and air-conditioning (HVAC) play an important role in ensuring the manufacture of quality pharmaceutical products. A well designed HV AC system will also provide comfortable conditions for operators.加热,通风,空调(HVAC)系统在保证药品质量的生产上起着至关重要的作用。
ISPE HVAC(翻译版)国际制药工程协会对空调系统的基准指南
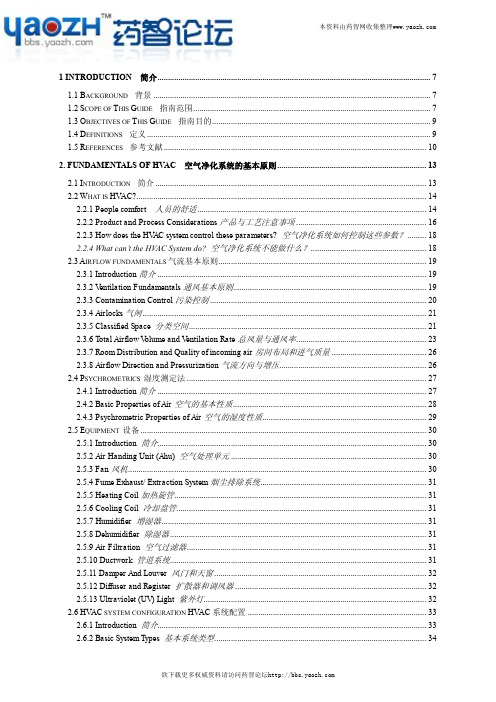
WHO发布《使用不同方法—包括HBEL—建立清洁验证限度指南》!
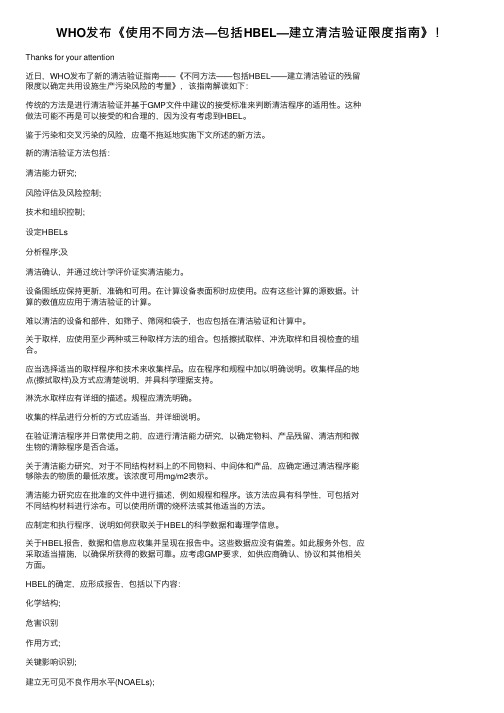
WHO发布《使⽤不同⽅法—包括HBEL—建⽴清洁验证限度指南》!Thanks for your attention近⽇,WHO发布了新的清洁验证指南——《不同⽅法——包括HBEL——建⽴清洁验证的残留限度以确定共⽤设施⽣产污染风险的考量》,该指南解读如下:传统的⽅法是进⾏清洁验证并基于GMP⽂件中建议的接受标准来判断清洁程序的适⽤性。
这种做法可能不再是可以接受的和合理的,因为没有考虑到HBEL。
鉴于污染和交叉污染的风险,应毫不拖延地实施下⽂所述的新⽅法。
新的清洁验证⽅法包括:清洁能⼒研究;风险评估及风险控制;技术和组织控制;设定HBELs分析程序;及清洁确认,并通过统计学评价证实清洁能⼒。
设备图纸应保持更新,准确和可⽤。
在计算设备表⾯积时应使⽤。
应有这些计算的源数据。
计算的数值应应⽤于清洁验证的计算。
难以清洁的设备和部件,如筛⼦、筛⽹和袋⼦,也应包括在清洁验证和计算中。
关于取样,应使⽤⾄少两种或三种取样⽅法的组合。
包括擦拭取样、冲洗取样和⽬视检查的组合。
应当选择适当的取样程序和技术来收集样品。
应在程序和规程中加以明确说明。
收集样品的地点(擦拭取样)及⽅式应清楚说明,并具科学理据⽀持。
淋洗⽔取样应有详细的描述。
规程应清洗明确。
收集的样品进⾏分析的⽅式应适当,并详细说明。
在验证清洁程序并⽇常使⽤之前,应进⾏清洁能⼒研究,以确定物料、产品残留、清洁剂和微⽣物的清除程序是否合适。
关于清洁能⼒研究,对于不同结构材料上的不同物料、中间体和产品,应确定通过清洁程序能够除去的物质的最低浓度。
该浓度可⽤mg/m2表⽰。
清洁能⼒研究应在批准的⽂件中进⾏描述,例如规程和程序。
该⽅法应具有科学性,可包括对不同结构材料进⾏涂布。
可以使⽤所谓的烧杯法或其他适当的⽅法。
应制定和执⾏程序,说明如何获取关于HBEL的科学数据和毒理学信息。
关于HBEL报告,数据和信息应收集并呈现在报告中。
这些数据应没有偏差。
如此服务外包,应采取适当措施,以确保所获得的数据可靠。
ISO 22519:2019《纯化水和注射用水预处理和生产系》(中英文对照)
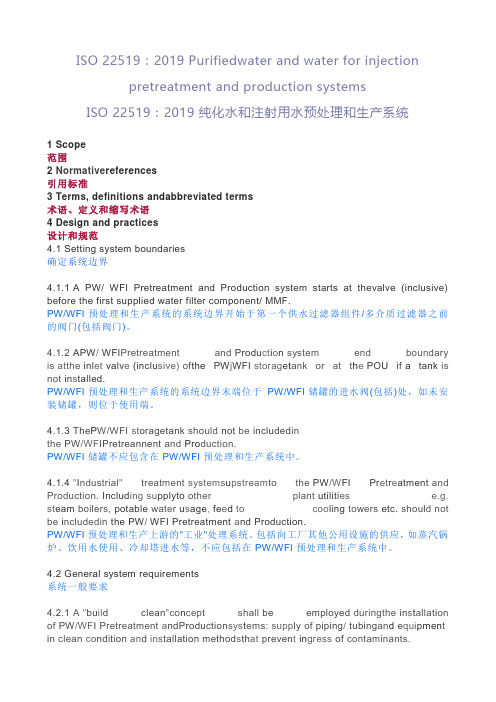
ISO 22519:2019 Purifiedwater and water for injectionpretreatment and production systemsISO 22519:2019 纯化水和注射用水预处理和生产系统1 Scope范围2 Normative references引用标准3 Terms, definitions andabbreviated terms术语、定义和缩写术语4 Design and practices设计和规范4.1 Setting system boundaries确定系统边界4.1.1 A PW/ WFI Pretreatment and Production system starts at thevalve (inclusive) before the first supplied water filter component/ MMF.PW/WFI 预处理和生产系统的系统边界开始于第一个供水过滤器组件/多介质过滤器之前的阀门(包括阀门)。
4.1.2 APW/ WFI Pretreatment and Produ ct i o n system end boundary is at the inl et valv e (inclu sive) of the PW j WFI storag e t ank or at t h e POU i f a tank is not in s talled.PW/WFI 预处理和生产系统的系统边界末端位于PW/WFI 储罐的进水阀(包括)处,如未安装储罐,则位于使用端。
4.1.3 The P W/WFI st oragetank should not be included inthe PW/WF IPretreannent and Pro duction.PW/WFI 储罐不应包含在 PW/WFI 预处理和生产系统中。
维生素产品年度验证总计划范例(中英文)

V ALIDATION DOCUMENT验证文件Validation Master Plan for the First Phase20XX年验证总计划Document No./ 文件编号:VD01001Issue No./版本号: 1Issue Date/颁发日期:20XX年12月28日Written by/起草人:TValidation Manager /验证经理Signed/签名: Date/日期:年月日Authorized by/授权人:RTechnical Director/技术总监Signed/签名: Date/日期:年月日Document check/审核DistributionQA Validation archive (Completed original) QA验证档案(完整的原件)Technical Director (Copy) 技术总监(复印件)Engineering Manager (Copy) 维修经理(复印件)QC Manager (Copy) QC经理(复印件)Production Manager (Copy) 生产经理(复印件)QA Manager (Copy) QA经理(复印件)Packing Manager (Copy) 包装经理(复印件)Validation Manager (Copy) 验证经理(复印件)Commercial Manager (Copy) 商务经理(复印件)Production Director (Copy) 生产总监(复印件)Table of Content/目录1Purpose/目的 (6)2Summary/概述 (6)2.1 Company introduction and summary of fist stage project / 公司及一期工程项目概述 (6)2.2 Scope/验证范围 (6)2.3 Validation Policy /验证方针 (6)3Validation Organizational Chart and Personnel Responsibilities/验证组织结构及人员职责 (7)3.1 Organizational Chart/组织结构图 (7)3.2 Validation Committee/验证委员会 (7)3.3 Validation/Qualification Team/验证小组 (7)3.4 Responsibilities/职责: (7)3.4.1 Responsibilities of Validation Committee/验证委员会职责 (7)3.4.2 Responsibilities of Validation Team/验证小组职责: (8)3.4.3 All Departmental Managers/所有部门经理职责 (9)3.5 Training /验证培训 (9)4The Writing and Approval of Validation Plan, Protocol and Report/验证计划、方案、报告的起草审批程序 (9)5Documentation/文件 (9)5.1 Content/文件范围 (9)5.1.1Validation Plan/验证计划 (9)5.1.2Validation Protocol/验证方案 (10)5.1.3Validation Report/验证报告 (10)5.1.4Validation Certificate/验证证书 (10)5.2 Format/文件格式 (10)5.3 Validation Document numbering/验证文件的编号 (12)5.4 Validation/Qualification Archiving验证/确认归档 (12)6Validation Implementation/验证实施 (12)6.1 Safety and Health/安全与健康 (12)6.2 Validation Classification and Applicable Scope / 本次验证所用到的验证分类与适用范围.. 126.2.1Prospective Validation / 前验证 (12)6.2.2Concurrent Validation/同步验证 (13)6.2.3Revalidation/再验证 (13)6.3 Validation Implementation/验证的实施 (13)6.4 Validation Project Collection/本次验证的项目汇总 (13)6.4.1Analytical Methods Validation/分析方法学 (14)6.4.2Facilities/设施 (14)6.4.3Instruments and equipments/仪器设备 (14)6.4.4Process/工艺 (15)6.4.5Equipment Cleaning/设备清洁 (16)6.4.6Computerized system/计算机化系统 (16)6.5 Schedule/本次验证的时间计划安排 (17)6.5.1First Phase/第一阶段 (17)6.5.2Second phase/第二阶段 (18)6.5.3Third phase/第三阶段 (19)6.5.4Fourth phase第四阶段 (19)7Validation Method and Acceptance Criteria/验证方法和可接受标准 (20)7.1 URS/用户需求标准 (20)7.2 Analytical methods validation/分析方法学验证 (20)7.3 Facilities Validation/厂房设施、仓库设施的验证 (21)7.3.1Design Qualification/设计确认 (21)7.3.2Installation Qualification/安装确认 (21)7.3.3Operational Qualification/运行确认 (22)7.4 Validation of Clean Rooms and Air-conditioning System/洁净车间、空调系统的验证 (22)7.4.1Design Qualification/设计确认 (22)7.4.2Installation Qualification/安装确认 (22)7.4.3Operational Qualification运行确认 (23)7.4.4Performance Qualification/性能确认 (24)7.5 Purified water system validation/纯化水系统验证 (25)7.5.1Design Qualification/设计确认 (25)7.5.2Installation Qualification/安装确认 (25)7.5.3Operational Qualification/运行确认: (25)7.5.4Performance Qualification/性能确认 (26)7.6 Compressed air system validation/压缩空气系统验证 (27)7.6.1Design Qualification/设计确认 (27)7.6.2Installation Qualification/安装确认 (27)7.6.3Operational Qualification/运行确认 (28)7.6.4Performance Qualification/性能确认 (28)7.7 Instruments and equipments validations/仪器设备验证 (28)7.7.1Design Qualification/设计确认 (28)7.7.2Installation Qualification/安装确认 (29)7.7.3Operational Qualification/运行确认 (29)7.7.4Performance Qualification/性能确认 (30)7.8 Equipment cleaning validation/设备清洁验证 (30)7.8.1Establishment of cleaning procedure/建立清洁规程 (31)7.8.3Validation of sampling method/验证取样方法 (31)7.8.4Confirmation of Chemical Residue/确定化学残留量 (31)7.8.5Confirmation of microbes residue/确定微生物残留量 (31)7.8.6Expiry Date of Cleaned Equipment/确定清洁设备的存放有效期 (32)7.9 Process Validation/生产工艺验证 (32)7.9.1Preconditions/验证先决条件 (32)7.9.2Validation Method/验证方法 (32)7.10 Validation of Computerized System/计算机化系统验证 (32)7.10.1Hardware/硬件 (33)7.10.2Operational System/操作系统 (33)7.10.3Firmware/生产或支持设备使用的固件 (33)7.10.4Commercial system/商业化系统 (33)7.10.5Configurable software package/可配置软件包 (33)8Deviations and change control/偏差处理及变更控制 (33)9History of Change /文件变更及历史 (34)10References/参引 (34)11Annex/附录 (34)1Purpose/目的This Validation Master Plan (VMP) describes the V alidation and Qualification activities that will be undertaken at Tripardus Pharmaceuticals Ltd. at first phase before start-up. It summarizes the company’s Validation intentions, philosophy, policy, project, plan, and approach and acceptance criteria.本验证总计划(VMP)描述了瑞博德制药有限公司新建的一期工程在启用前应该进行的验证和确认活动,概括地阐述验证目的、原则、方针、项目、计划、方法和可接受标准等。
常用制药及GMP英文缩写
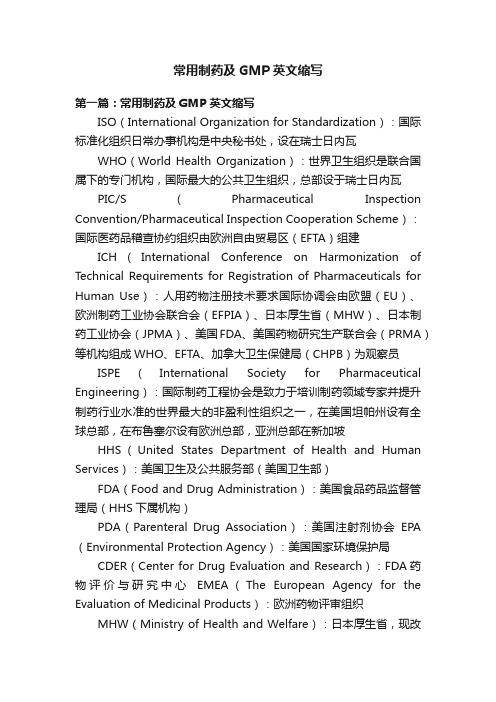
常用制药及GMP英文缩写第一篇:常用制药及GMP英文缩写ISO(International Organization for Standardization):国际标准化组织日常办事机构是中央秘书处,设在瑞士日内瓦WHO(World Health Organization):世界卫生组织是联合国属下的专门机构,国际最大的公共卫生组织,总部设于瑞士日内瓦PIC/S(Pharmaceutical Inspection Convention/Pharmaceutical Inspection Cooperation Scheme):国际医药品稽查协约组织由欧洲自由贸易区(EFTA)组建ICH(International Conference on Harmonization of Technical Requirements for Registration of Pharmaceuticals for Human Use):人用药物注册技术要求国际协调会由欧盟(EU)、欧洲制药工业协会联合会(EFPIA)、日本厚生省(MHW)、日本制药工业协会(JPMA)、美国FDA、美国药物研究生产联合会(PRMA)等机构组成WHO、EFTA、加拿大卫生保健局(CHPB)为观察员ISPE(International Society for Pharmaceutical Engineering):国际制药工程协会是致力于培训制药领域专家并提升制药行业水准的世界最大的非盈利性组织之一,在美国坦帕州设有全球总部,在布鲁塞尔设有欧洲总部,亚洲总部在新加坡HHS(United States Department of Health and Human Services):美国卫生及公共服务部(美国卫生部)FDA(Food and Drug Administration):美国食品药品监督管理局(HHS下属机构)PDA(Parenteral Drug Association):美国注射剂协会EPA (Environmental Protection Agency):美国国家环境保护局CDER(Center for Drug Evaluation and Research):FDA药物评价与研究中心EMEA(The European Agency for the Evaluation of Medicinal Products):欧洲药物评审组织MHW(Ministry of Health and Welfare):日本厚生省,现改为厚生劳动省MHLW(Ministry of Health, Labor and Welfare),负责医疗卫生和社会保障的主要部门 D&B(Dun & Bradstreet):邓白氏公司DUNS(DataUniversal Numbering System):邓白氏公司提供的唯一的公司代号,用于信用评级等在SMF文件中会用到GMP(Good Manufacturing Practice):药品良好生产规范cGMP(Current Good Manufacture Practices):动态药品生产管理规范,即现行的GLP(Good Laboratory Practice):药物非临床研究质量管理规范,及优良实验室规范GSP(Good Supplying Practice):药品经营质量管理规范,及良好的药品供应规范GAP(Good Agricultural Practice for Chinese Crude Drugs):中药材生产质量管理规范GDP(Good Documentation Practice):良好文件管理GEP (Good Engineering Practice):工程设计规范GAMP(Good Automated Manufacturing Practice):优良自动化生产规范USP(united states pharmacopeia):美国药典EP (European Pharmacopeia):欧洲药典JP(Japanese Pharmacopoeia):日本药典CFR(Code of Federal Regulations):美国联邦法律CFR 21 Part 11(Code of Federal Registry Part11):联邦法规法律标题21第11部分CEP/COS(Certificate of Suitability to the monographs of European Pharmacopoeia):欧洲药典适应性认证证书CEP认证,COS证书CTD(Common Technical Document):国际注册用常规技术文件CTD文件是国际公认的文件编写格式,用来制作一个向药品注册机构递交的结构完善的注册申请文件EHS(Environment、Health、Safety):环境-健康-安全管理体系HACCP(Hazard Analysis and Critical Control Point):(保健食品)危害分析和关键控制点REACH(REGULATION concerning the Registration, Evaluation, Authorization and Restriction of Chemicals):欧盟规章《化学品注册、评估、许可和限制》,欧盟建立的,并于2007年6月1日起实施的化学品监管体系 ICH-Q1A:新原料药和制剂的稳定性试验ICH-Q1B:稳定性试验:新原料药和制剂的光稳定性试验ICH-Q1C:稳定性试验:新剂型的要求ICH-Q1D:新原料药和制剂的稳定性试验的括号法和矩阵法设计ICH-Q1E:稳定性数据的评价ICH-Q1F:气候带Ⅲ和Ⅳ注册申请的稳定性数据 ICH-Q2A:分析步骤验证:正文ICH-Q2B:分析步骤验证:方法学ICH-Q3A:原料药中的杂质 ICH-Q3B:新制剂中的杂质ICH-Q3C:杂质;残留溶剂的指导原则 ICH-Q4:药典ICH-Q4A:药典的同一化ICH-Q4B:各地区使用的药典正文评估和建议ICH-Q5A:来源于人或动物细胞系的生物技术产品的病毒安全性评价ICH-Q5B:生物技术产品的质量:rDNA衍生蛋白质产品生产细胞的表达构建体分析ICH-Q5C:生物技术产品的质量:生物制品/生物技术产品的稳定性试验ICH-Q5D:用于生物技术产品及生物制品生产的细胞基质的来源和鉴定 ICH-Q5E:生物技术产品/生物制品在工艺变更时的可比性ICH-Q6A:质量标准新原料药和制剂的检测以及可接受标准:化学物质ICH-Q6B:质量标准:生物技术产品及生物制品的检测方法和可接受标准ICH-Q7:原料药良好制造规范(ICH-Q7A的新版)ICH-Q7A:原料药的GMP规范 ICH-Q8:药物研发指南 ICH-Q9:质量风险管理ICH-Q10(PQS):药物质量体系QA(Quality Assurance):质量保证QC(Quality Control):质量控制QRM(Quality Risk Management):质量风险管理IPC (InproceicsQuality Control):制程品质控制/中控OOS(Out of Specification):检验结果超标 OOT(Out of Trend):超趋势结果OOL(Out of Limit):超出极限的结果,如温湿度等OOE (Out of Expectation):超期望结果SAL(SterilityAssuranceLevel):无菌保证水平灭菌后微生物的存活概率的负对数,要求≥6SAL=−lg存活率=F0D−lgN0D值:杀灭90%的微生物所需要的时间,D值越大,微生物死亡越难,D值与细菌的耐热性成正比Z值:指灭菌时间减少到原来的10%所需要升高的温度或是相同的灭菌时间内杀死99%的微生物所需要提高的温度F值:为一定温度下,给定Z值所产生的灭局效果与参比温度T0下给定Z值所产生的灭菌效果相同时所相当的时间F值用于干热灭菌F0值:为一定温度下,Z值为10℃产生的灭菌效果与120℃,Z 值为10℃时产生的灭菌效果相当的时间,t分钟内的灭菌效果相当于120℃下灭菌F0分钟的效果F0被称为标准灭菌时间,用于热压灭菌LRV:除菌过滤的对数下降值LRV=lgN0-lgN SOP(Standard Operation Procedure):标准操作规程 DMF(Drug Master File):药品主文件 SMF(Site Master File):工厂主文件URS(User Requirement Specification):用户需求标准FS (Functional Specification):功能标准DS(Design Specification):设计标准 DQ(Design Qualification):设计确认IQ(Installation Qualification):安装确认OQ(Operational Qualification):运行确认PQ(Performance Qualification):性能确认 RQ(Requalification):再确认CAPA(Corrective Action & Preventive Action):纠正预防系统,Q10的四大要素之一QbD(Quality byDesign):质量源于设计COA(Certificate of Analysis):分析证书/检验报告书/检验报告单 BPR(Batch Production Record):批生产记录API(Active Pharmaceutical Ingredients):药物活性成分,通常指的原料药 PMC(Product Material Control):生产物料控制PC 生产控制;MC物料控制CMC(Chemistry and manufacture control):生产和化学控制APR(Annual Products Review):年度质量回顾 KPI(Key Performance Indicators):关键业绩指标P&ID(Piping and Instrument Diagram):工艺管道仪表流程图 PFD(Process Flow Diagram):工艺流程图 UFD(Utility Flow Diagram):公用工程流程图CIP(Cleaning in Place):原位清洗(全自动,如针剂配制系统)WIP(Washing in Place):在线清洁(半自动,需要手动的拆卸,如流化床)SIP(Sterilization in Place):在线灭菌WFI (Water for Injection):注射用水HVAC(Heating Ventilation Air Conditioning):供热空气调节净化系统 HEPA(High Efficiency Particulate Air Filter):高效过滤器DOP:为邻苯二甲酸二辛酯,HEPA检漏用的气溶胶PAO:聚-α-烯烃,HEPA检漏用的气溶胶 IBC(IntermediateBulkContainer):中型散装容器BFS(Blowing Filling and Sealing):吹-灌-封PAT (Process Analytical Technology):过程分析技术PLC (Programmable Logic Controller):可编程逻辑控制CPP (Critical Process Parameters):关键工艺参数FBD(Fluid Bed Dryer):流化床AHU(Air Handling Unit):空气处理单元SAT (SiteAcceptance T est):现场验收测试 FAT(Factory Acceptance Test):工厂验收测试第二篇:GMP英文缩写1.AQAI(Automated Quality Assurance Inspection Equipment):在线自动质量保证检查设备 2.API(Active Pharmaceutical Ingredient):活性药物物质即原料药 3.ANDA(Abbreviated New Drug Application):简化新药申请 4.ADR(Adverse Drug Reaction):不良反应5.BSE(Bovine Spongiform Encephalopathy):疯牛病6.BPCS(Business Planning and Control System):业务计划及控制系统7.BIA(Business impact assessment): 商业影响评估8.cGMP(current Good Manufacturing Practice):现行药品生产质量管理规范 CD(China Certification Committee for Drugs):中国药品认证委员会10.CIP(Cleaning In Place):在线清洁11.CV(Concurrent Validation):同步验证12.CDER(Center for Drug Evaluation and Research): 药品研究与评价中心13.COA(Certificate Of Analysis):分析报告单14.CFR(Code of Federal Regulation):(美国)联邦法规15.CDC(Centers for Disease Control and Prevention):疾病预防控制中心16.COS / CEP(Certificate of Suitability for European Pharmacopeia):欧洲药典适用性证书D(Certification Committee for Drugs):药品认证管理中心18.CPMP(Committee for Proprietary Medicinal Products): 欧洲专利药品委员会19.CTD(Common Technical Document):通用技术文件20.CDC(Centers for Disease Control and Prevention): 疾病预防控制中心21.GMP(Good Manufacturing Practice):药品生产质量管理规范22.ICH(International Conference on Harmonization of Technical Requirements for Registration ofPharmaceuticals for Human Use):人用药品注册技术要求国际协调会 23.EU(European Union):欧洲联盟24.EFPIA(European Federation of Pharmaceutical Industries Associations):欧洲制药工业协会联合会25.MHW(Ministry of Health and Welfare,Japan):日本厚生省26.JPMA(Japan Pharmaceutical Manufacturers Association):日本制药工业协会27.FDA(US Food and Drug Adminiistration):美国食品与药品管理局28.PRMA(Pharmaceutical Research and Manufacturers of America):美国药物研究和生产联会29.WHO(World Health Organization):世界卫生组织30.IFPMA(International Federation of Pharmaceutical Manufacturers Associations):国际制药工业协会联合会31.TQC(Tota lQuality Control),TQM(Total Quality Management): 全面质量管理32.PDCA(Plan,Do,Check,Action):计划执行检查处理33.QA(Quality Assurance):质量保证 34.QC(Quality Control):质量控制 35.QS(Quality System):质量体系36.QM(Quality Management): 质量管理37.SOP(Standard Operating Procedure): 标准操作规程38.SMP(Standard Management Procedure):标准管理程序39.SOR(Standard Operating Record): 标准操作记录 40.GEP(Good Engineering Practice):工程设计规范41.HVAC(Heating Ventilation and Air Conditioning):空调净化系统42.DQ(Design Qualification):设计确认43.IQ(Installation Qualification):安装确认44.OQ(Operational Qualification):运行确认 45.PQ(Performance Qualification):性能确认46.OOS(Out-Of-Specification):检验结果偏差,有别于偏差47.PFDS(Process Flow Diagrams):工艺流程图48.MRA(cMutual Reognition Agreements): 现场检查多边认同协议 49.DMF(Drug Master File):药物主文件50.EDMF(European Drug Master File)欧盟药物主文件51.EDQM(European Directorate for Quality Medicines): 欧洲药品质量管理局 52.ORA(Office of Regulatory Affairs):药政事务办公室53.GGPs(Good Guidance Practices): 优良指南规范54.MOA(Method Of Analysis):分析方法 55.VMP(Validation Master Plan):验证主计划 56.VP(Validation Protocol):验证方案57.MSDS(Material Safety Data Sheet):物料安全技术说明书58.NDA(New Drug Application):新药申请59.OTC(Over-the-counter):非处方60.INN(International Nonproprietary Name):国际非专有名称P(the united state pharmacopeia): 美国药典62.NF(National Formulary):(美国)国家药品集63.GAP(Good Agricultural Practice):中药材种植管理规范64.GCP(Good Clinical Practice):药物临床试验质量管理规范65.GLP(Good Laboratory Practice):药物实验室管理规范66.GSP(Good Supply Practice):药品经营质量管理规范67.GUP(Good Use Practice):药品使用质量管理规范 68.SM(Starting Material):起始物料69.PMF(Plant Master File);SMF(Site Master File):工厂主文件70.EDL(List of Essential Drugs): 基本药物目录 71.PI(Package Insert):说明书72.PCT(Patent Cooperation Treaty): 专利合作条约73.PPAC(Patent Protection Association of China):中国专利保护协会 74.PIC(Person In Charge):负责人75.PDS(Pharmaceutical Development Services):整体新药研发机构 76.SPC(Summary of Product Characteristics):产品特性摘要第三篇:GMP常见英文缩写(本站推荐)GMP常见英文缩写AQAI(Automated Quality Assurance Inspection Equipment):在线自动质量保证检查设备 API(Active Pharmaceutical Ingredient):活性药物物质,即原料药 ANDA(Abbreviated New Drug Application):简化新药申请ADR(Adverse Drug Reaction):不良反应BSE(BovineSpongiform Encephalopathy):疯牛病BPCS(Business Planning and Control System):业务计划及控制系统 BIA(Business impact assessment): 商业影响评估cGMP(current Good Manufacturing Practice):现行药品生产质量管理规范 CCCD(China Certification Committee for Drugs):中国药品认证委员会CIP(Cleaning In Place):在线清洁CV(Concurrent Validation):同步验证CDER(Center for Drug Evaluation and Research): 药品研究与评价中心COA(Certificate Of Analysis):分析报告单CFR(Code of Federal Regulation):(美国)联邦法规CDC(Centers for Disease Control and Prevention):疾病预防控制中心COS/ CEP(Certificate of Suitability for European Pharmacopeia):欧洲药典适用性证书 CCD(Certification Committee for Drugs):药品认证管理中心CPMP(Committee for Proprietary Medicinal Products): 欧洲专利药品委员会 CTD(Common Technical Document):通用技术文件CDC(Centers for Disease Control and Prevention): 疾病预防控制中心 GMP(Good Manufacturing Practice):药品生产质量管理规范ICH(International Conference on Harmonization of Technical Requirements for Registration of Pharmaceuticals for Human Use):人用药品注册技术要求国际协调会 EU(European Union):欧洲联盟EFPIA(European Federation of PharmaceuticalIndustries Associations):欧洲制药工业协会联合会MHW(Ministry of Health and Welfare,Japan):日本厚生省JPMA(Japan Pharmaceutical Manufacturers Association):日本制药工业协会 FDA(US Food and Drug Adminiistration):美国食品与药品管理局PRMA(Pharmaceutical Research and Manufacturers ofAmerica):美国药物研究和生产联合会WHO(World Health Organization):世界卫生组织IFPMA(International Federation of Pharmaceutical Manufacturers Associations): 国际制药工业协会联合会TQC(Total Quality Control),TQM(Total Quality Management): 全面质量管理PDCA(Plan,Do,Check,Action):计划,执行,检查,处理QA(Quality Assurance):质量保证QC(Quality Control):质量控制QS(Quality System):质量体系 QM(Quality Management): 质量管理SOP(Standard Operating Procedure): 标准操作规程SMP(Standard Management Procedure):标准管理程序SOR(Standard Operating Record): 标准操作记录GEP(Good Engineering Practice):工程设计规范HVAC(Heating Ventilation and Air Conditioning):空调净化系统DQ(Design Qualification):设计确认IQ(Installation Qualification):安装确认OQ(Operational Qualification):运行确认PQ(Performance Qualification):性能确认OOS(Out-Of-Specification):检验不合格;超标 PFDS(Process Flow Diagrams):工艺流程图MRA(cMutual Reognition Agreements): 现场检查多边认同协议 DMF(Drug Master File): EDMF(European Drug Master File)欧盟药物主文件EDQM(European Directorate for Quality Medicines): 欧洲药品质量管理局 ORA(Office of Regulatory Affairs):药政事务办公室GGPs(Good Guidance Practices): 优良指南规范MOA(Method Of Analysis):分析方法VMP(Validation Master Plan):验证主计划VP(Validation Protocol):验证方案MSDS(Material Safety Data Sheet):物料安全技术说明书NDA(New Drug Application):新药申请OTC(Over-the-counter):非处方INN(International Nonproprietary Name)国际非专有名称USP(the united state pharmacopeia): 美国药典NF(National Formulary):(美国)国家药品集GAP(Good Agricultural Practice):中药材种植管理规范GCP(Good Clinical Practice):药物临床试验质量管理规范 GLP(Good Laboratory Practice):药物实验室管理规范GSP(Good Supply Practice):药品经营质量管理规范 GUP(Good Use Practice):药品使用质量管理规范 SM(Starting Material):起始物料PMF(Plant Master File);SMF(Site Master File):工厂主文件EDL(List of Essential Drugs): 基本药物目录 PI(Package Insert):说明书PCT(Patent Cooperation Treaty): 专利合作条约PPAC(Patent Protection Association of China):中国专利保护协会 PIC(Person In Charge):负责人PDS(Pharmaceutical Development Services): 整体新药研发机构 SPC(Summary of Product Characteristics):产品特性摘要第四篇:英文缩写GM(General Manager)总经理VP(Vice President)副总裁FVP(First Vice President)第一副总裁AVP(Assistant Vice President)副总裁助理CEO(Chief Executive Officer)首席执行官COO(Chief Operations Officer)首席运营官CFO(Chief Financial Officer)首席财务官CTO(Chief Technology Officer)首席技术官HRD(Human Resource Director)人力资源总监OD(Operations Director)运营总监MD(Marketing Director)市场总监OM (Operations Manager)运作经理PM(Production Manager生产经理、Product Manager产品经理、Project Manager项目经理)注:这里面变化比较多,要结合谈话时的背景来判断究竟是指哪种身份)BM(Branch Manager)部门经理DM(District Manager)区域经理RM(Regional Manager)区域经理President 总裁Vice-President 副总裁Assistant VP 副总裁助理Executive Marketing Director 市场行政总监General Manager 总经理Branch Manager部门经理Product Manager 产品经理Project Manager 项目经理Regional Manager 区域经理Production Manager 生产经理Transportation Manager 运输经理Applications Programmer 应用软件程序员Computer Operator 电脑操作员Computer Operations Supervisor 电脑操作主管Hardware Engineer 硬件工程师Computer T echnician 电脑技术MIS Manager 管理信息系统部经理Developmental Engineer 开发工程师Operations Analyst 操作分析Director of Information Services 信息服务主管LAN Administrator 局域网管理员Systems Analyst 系统分Manager of Network Administration 网络管理经理Systems Engineer 系统工程师Product Support Manager 产品支持经理Systems Programmer 系统程序员VP Sales 销售副总裁VP Marketing 市场副总裁Senior Account Manager 高级客户经理Telemarketing Director 电话销售总监Sales Administrator 销售主管Telemarketer 电话销售员Regional Sales Manager 地区销售经理Tele-Interviewer 电话调查员Regional AccountManager 地区客户经理Salesperson 销售员Sales Representative 销售代表Merchandising Manager 采购经理Sales Manager 销售经理Marketing Consultant 市场顾问Sales Executive 销售执行者Marketing Assistant 市场助理Sales Assistant 销售助理Marketing and Sales Director 市场与销售总监Retail Buyer 零售采购员Market Research Analyst 市场调查分析员Manufacturer’s Representative 厂家代Purchasing Agent 采购代理Assistant Account Executive 客户管理助理Marketing Manager 市场经理Advertising Manager 广告经理Marketing Intern 市场实习Advertising Coordinator 广告协调员Marketing Director 市场总监Advertising Assistant 广告助理Account Manager 客户经理Account Representative 客户代表Accounting Payable Clerk 应付帐款文员Accounting Assistant 会计助理Accounting Manager 会计经理AccountsReceivable Clerk 应收帐款文员Accounting Clerk 会计文员Certified Public Accountant 注册会计师Senior Accountant 高级会计Chief Financial Officer 首席财务官Audit Manager 审计经理Collections Officer 收款负责人Auditor 审计师Junior Accountant 初级会计Loan Administrator 贷款管理员Management Accountant 管理会计Billing Clerk 票据文员Billing Supervisor 票据管理员Bookkeeper 档案管理Staff Auditor 审计员Bookkeeping Clerk 档案管理助理Budget Analyst 预算分析Tax Accountant 税务会计Credit Analyst 信用分析Credit Manager 信用管理经理Vice-President of Administration and Finance 财务行政副总裁Financial Analyst 财务分析Vice-President of Finance 财务副总裁Financial Consultant 财务顾问Financial Manager 财务经理Financial Planner 财务计划员VP HR 人力资源副总裁Assistant VP HR 人力资源副总裁助理HR Director 人力资源总监Compensation &Benefit Manager 薪酬福利经理Staffing Manager 招聘经理Training Manager 培训经理Benefits Coordinator 员工福利协调员Employer Relations Representative 员工关系代表Payroller 工资专员Training Coordinator 培训协调Training Specialist 培训专员HR Supervisor(Training)培训主管Vice-President of Administration 行政副总裁Administrative Director 行政总监Office Manager 办公室经理File Clerk 档案管理员Administration Assistant 行政助理Receptionist 接待员General Office Clerk 办公室文员Secretary 秘书Order Entry Clerk 订单输入文员Operator 接线员Typist 打字员公司部门:总公司Head Office分公司Branch Office营业部Business Office人事部 Personnel Department人力资源部 Human Resources Department总务部 General Affairs Department财务部General Accounting Department销售部 Sales Department国际部International Department广告部 Advertising Department企划部Planning Department研发部 Research and Development Department(R&D)秘书室 Secretarial Pool销售相关名词:KA:Key Accounts(原:主要客户)大卖场,大型连锁DM:DeliverMessageDirectMail 宣传单张POP:Point of the purchase(原:据点上的购买)店头广告PDCA:Plan,Do,Check,Action 计划、实施、检核、措施为管理循环的简称4PS:Product,Price,Place,Promotion 行销组合4p(产品价格通路促销)4CS:Consumer needs,Costs,Convienience,Communication行销组合4c(顾客需求顾客接受的成本便利性沟通)MINI:Mininum 小SWOT:trength,Weakness,Opportunity,Threat(优势弱势机会问题)为内外环境分析的一个工具USP:Unique Special Point 独特点FAB:Feature,Advantage,Benefit 产品特性,利益,功效推销法POD:Product Of Difference 产品的卖点SP:Sales Promotion 促销AD:Advertisement 广告NP:News Paper 报纸杂志PR:Public Relation 公共关系Store Check:Store Audit(偏于量的终端调查)终端调查,铺市率调查(可见度)FGD:Focus Group Discuss 座谈会(市调一种)Outdoor:户外GRP: Gross Rating Point(媒介用语)毛评点;总收视点3A:Avalible,Able,Adsire买得到,买得起,乐得买A&U:Attitude and Usage 消费态度和行为(市场调查)TG:端架SKU:单品CPM:每一百万个使用者会有几次抱怨(Complaint per Million)CRM:客户关系管理(Customer Relationship Management)JIT: 即时管理(Just In Time)KM:知识管理(Knowledge Management)LTC:最小总成本法(Least Total Cost)LUC:最小单位成本(Least Unit Cost)SO:订单(Sales Order)销售中的4P:产品(Product)、价格(Price)、通路(Place)、促销(Promotion)销售中的4C:消费者(Consumer)、成本(Cost)、方便(Convenience)、Inventory Control Manager 库存管理经理Regional Manager 区域经理Executive Marketing Director 市场行政总监Warehouse Manager 仓库经理Manager(Non-Profit and Charities)非盈利性慈善机构管理Cashier 出纳员Buyer 采购员Clerk/Receptionist 职员/接待员Civil Engineer 土木工程师Clerk Typist & Secretary 文书打字兼秘书Marketing Representative 销售代表Simultaneous Interpreter 同传公司英文标识总公司Head Office分公司Branch Office 营业部Business Office人事部 Personnel Department人力资源部Human Resources Department 总务部General Affairs Department财务部General Accounting Department 销售部Sales Department 促销部Sales Promotion Department 国际部 International Department 出口部Export Department进口部Import Department 公共关系Public Relations Department 广告部Advertising Department 企划部Planning Department 产品开发部Product Development Department 研发部Research and Development Department(R&D)艺术类词汇:服装设计师Fashion Designer电影摄制助理Film Production Assistant画面设计师Graphic Designer 装饰设计师Interior Designer制片协调员Production Coordinator男演员/女演员Actor/Actress艺术总监Art Director舞蹈教练Choreographer喜剧演员Comedian舞蹈家 Dancer摄影师 Photographer服务行业词汇: 办案员Case Worker城市规划者Urban Planner临床医学家Therapist社会工作者Social Worker心理学家Psychologist客户服务经理 Customer Service Manager客户服务代表 Customer Service Representative健康俱乐部经理Health Club Manager厨师Chef美容师Cosmetologist发型师Hairstylist 教育词汇:校长Principal外语教师 Foreign Language Teacher银行词汇:工商银行 ICBC: Industrial and Commercial Bank of China中国银行 BOC: Bank of China建设银行CCB: China Construction Bank农业银行ABOC: Agriculture Bank of China交通银行BOCM: Bank of Communication招商银行CMB: China Merchant Bank民生银行 CMBC: China Minsheng Banking Group,.Ltd光大银行 CEB: China Everbright Bank华夏银行 Huaxia Bank中信银行 ChinaCitic Bank广东发展银行Guangdong Development Bank深圳发展银行Shenzhen Development Bank上海浦东发展银行SPDB: Shanghai Pudong Development Bank兴业银行 CIB: China Industrial Bank Co., Ltd.MPV是指多用途汽车(multi-Purpose Vehicles),从源头上讲,MPV是从旅行轿车逐渐演变而来的,它集旅行车宽大乘员空间、轿车的舒适性、和厢式货车的功能于一身,一般为单厢式结构,即多用途车。
Product Quality Review 产品质量回顾

Product Quality Review 产品质量回顾1.4 Regular periodic or rolling quality reviews of all licensed medicinal prod ucts, including export only products, should be conducted with the objective of ver ifying the consistency of the existing process, the appropriateness of current spec ifications for both starting materials and finished product to highlight any trends and to identify product and process improvements. Such reviews should normally be conducted and documented annually, taking into account previous reviews, and should include at least:定期对所有批准的医药产品包括出口产品进行质量回顾,进行回顾的目标是确认原辅料和成品现有工艺的稳定性,现有质量标准的适用性,强调趋势,产品鉴别和工艺优化。
应进行年度的质量回顾并记录,结合先前的回顾,至少包括以下几点:(i) A review of starting materials including packaging materials used in the p roduct, especially those from new sources.该产品所用到的所有原辅料和包装材料的回顾,特别是来源于新供应商。
(ii) A review of critical in-process controls and finished product results. 关键中控检测和成品检测结果的回顾。
WHO非无菌制剂暖通空调GMP指南:第二部分

自2006年WHO发布第一版非无菌制剂暖通空调系统GMP指南,后于2010年、2011年、2015年、2016年、2017年分别发布五版征求意见稿,结构与收录内容几经变更,WHO药物制剂规格专家委员会(ECSPP)于2017年10月第51次会议上商定,非无菌制剂的暖通空调系统指南修订稿将被收录于GMP第一部分。
2018年2月发布《非无菌制剂暖通空调系统GMP指南:第二部分》,在征求公众意见后,将会考虑补充收录。
据WHO发布的修订时间表,2018年5月进行第一次意见整合与评审,2018年7月进行药品和检查工具GXP的讨论,于2018年8月进行第二次公示咨询。
现将此文件进行翻译,希望可以为国内药企进行WHO的GMP验证时提供参考。
若翻译内容有不当之处,还望不吝赐教。
GOOD MANUFACTURING PRACTICES FOR HEATING, VENTILATION AND AIR-CONDITIONING SYSTEMS FOR NON-STERILE PHARMACEUTICAL DOSAGE FORMS: PART 2非无菌制剂暖通空调系统GMP:第二部分INTERPRETATION OF PART 1 – GMP FOR HVAC SYSTEMS第一部分说明-暖通空调系统GMPContents 目录Section 1 and 2. Introduction and Scope第一、二节简介与范围Section 3. Glossary第三节术语Section 4. Premises第四节厂房Section 5. Design of HVAC systems and components第五节暖通空调系统和部件的设计Section 6. Full fresh air and recirculation systems第六节全新风及再循环系统Section 7. Air filtration, airflow direction and pressure differentials第七节空气过滤、气流方向和压差Section 8. Temperature and relative humidity第八节温度和相对湿度Section 9. Dust, vapour and fume control第九节粉尘、蒸汽和烟雾控制Section 10. Protection of the environment第十节环境保护Section 11. Commissioning第十一节试车Section 12. Qualification第十二节确认Section 13. Maintenance第十三节维护Section 1 and 2 : Introduction and Scope第一、二节简介与范围This document represents Part 2 of the HVAC systems guidelines. It contains non-binding examples, drawings, technical representations and interpretation in support of Part 1 of the HVAC systems guidelines.本文件代表第二部分的暖通空调系统指南。
制药厂设备维护部门经常发生的十个GMP问题

This categorization system is detailed in the ISPE Baseline Guideline on Qualification and Commissioning, Volume 5, Impact Assessment. The Direct, Indirect, No Impact and Safety categories are sometimes referred to as the D.I.N.S. system. 设备的这种分类体系在国际制药工程协会的《确认和调试基本指南》中第五卷“影响评估”中有详细说 明。上述设备的四种分类体系也简称为 D.I.N.S.体系。
5. Scheduling maintenance activities
安排维护活动
As consultants to the industry, we often see hybrid management systems within maintenance departments. 作为顾问,我们通常会发现企业维护部门使用的是混合管理系统(纸质管理系统和计算机系统)。
Let’s face it –maintenance staff would rather watch 15 hours of snail racing on TV than complete paperwork. It’s hard enough to get them to complete maintenance records, let alone Change Control forms. Yet simple maintenance activities such as changing filters or adding lubricant can dramatically impact product quality. 事实上,维护人员更愿意看 15 个小时的蜗牛赛跑节目,而不是完成纸质文件。维护人员很难完成维护记 录,更不用说变更控制表单了。然而简单的维护工作,例如换装过滤器或添加润滑油,都可能对产品质 量造成很大影响。
- 1、下载文档前请自行甄别文档内容的完整性,平台不提供额外的编辑、内容补充、找答案等附加服务。
- 2、"仅部分预览"的文档,不可在线预览部分如存在完整性等问题,可反馈申请退款(可完整预览的文档不适用该条件!)。
- 3、如文档侵犯您的权益,请联系客服反馈,我们会尽快为您处理(人工客服工作时间:9:00-18:30)。
Validation
Part 1. General overview on qualification and validation Part 2. Qualification of HVAC and water systems Part 3. Cleaning validation
Part 4. Analytical method validation Part 5. Computerized system validation
Influenced by the type of facility and level of protection See also ISO 14644 for methods of testing Requalification, and change control
8.2.18 – 8.2.20, 8.2.9
OOS results recorded
Design Condition
Normal Operating Range
8.2.12 – 8.2.15
Operating Range - Validated Acceptance Criteria
Validation
|
Slide 11 of 48
August 2006
Acceptance criteria and limits defined in design stage Design conditions, normal operating ranges, operating ranges, alert and action limits
8.2.5 – 8.2.11
See also full guidelines on "Validation" in WHO TRS, No. 937, 2005, Annex 4
Risk based approach for HVAC qualification
8.2.1
Validation
|
Slide 8 of 48
Supplementary Training Modules on Good Manufacturing Practice
Validation
WHO Technical Report Series, No. 937, 2006. Annex 4.
Validation
|
Slide 1 of 48
August 2006
Qualification of HVAC and water systems
Part 2
WHO Technical Report Series, No. 937, 2006. Annex 4. Appendix 1 and 2
Validation | Slide 3 of 48 August 2006
|
Slide 12 of 48
August 2006
HVAC
Qualification (4)
Typical parameters to be included in qualification (based on risk assessment):
Temperature Relative humidity Supply, return and exhaust air quantities
Validation
|
Slide 15 of 48
August 2006
HVAC
Qualification (7)
Tests performed according to protocols and procedures for the tests
Results recorded and presented in report (source data kept) Traceability, e.g. devices and standards used, calibration records; and conditions specified
HVAC
Objectives
To understand key issues in – commissioning, – qualification and – maintenance of HVAC and Water systems
8.
Validation
|
Slide 4 of 48
August 2006
IQ – Verify installation
– E.g. relevant components, ducting, filters, controls, monitors, sensors, etc. – Includes calibration where relevant
Validation
Maximum time interval
6 months or 12 months depending on Class
Test procedure* and key aspects
Particle counter. Readings and positions
Air pressure difference
HVAC
Qualification – examples of aspects to consider
DQ – Design of the system, URS
– (e.g. components, type of air treatment needed, materials of construction)
―
programme and records
August 2006
Validation
|
Slide 5 of 48
HVAC
Commissioning
Precursor to qualification
Includes setting up, balancing, adjustment and testing of entire HVAC system to ensure it meets requirements in URS and capacity Acceptable tolerances for parameters Training of personnel
Part 6. Qualification of systems and equipment Part 7. Non sterile product process validation
Validation
|
Slide 2 of 48
August 2006
Supplementary Training Modules on Good Manufacturing Practice
8.2.2 – 8.2.5
Validation | Slide 9 of 48 August 2006
HVAC
Qualification (3)
Direct impact components and critical parameters should be included Non-critical systems and components are subjected to Good Engineering Practices (GEP)
August 2006
HVAC
Qualification (2)
Described in a Validation Master Plan (VMP) VMP to include the nature and extent of tests, and protocols DQ, IQ, OQ, and PQ Risk analysis to determine critical and non-critical parameters, components, subsystems and controls
Validation | Slide 10 of 48 August 2006
HVAC
Design conditions and normal operating ranges set to achievable limits
ACTION LIMIT ALERT LIMIT ALERT LIMIT ACTION LIMIT
O&M manuals, schematic drawings, protocols, reports
8.1.2, 8.1.3, 8.1.6
Validation
|
Slide 7 of 48
August 2006
HVAC
Qualification
Validation is an extensive exercise Qualification of the HVAC system is one component in the overall approach that covers premises, systems/utilities, equipment, processes, etc.
Validation
|
Slide 16 of 48
August 2006
HVAC
Schedule of tests to demonstrate continuing compliance
Test Parameter
Particle count test
Objective
Verifies cleanliness
Manuals Operating procedures
Instructions for performance control, monitoring and records Maintenance instructions and records