射出成形模具试模作业SOP
试模作业指导书

试模作业指导书一、试模的定义用模具加工零件时,在最初阶段,工艺不稳定,这个时候试加工一批零件,并调整工艺参数,使出模后的零件能达到设计的要求,这个过程叫做试模。
二、试模前的注意事项1. 了解模具的有关资料:最好能取得模具的设计图面,详予分析,并约得模具技师参加试模工作。
2. 先在工作台上检查其机械配合动作:要注意有否刮伤,缺件及松动等现象,模向滑板动作是否确实,水道及气管接头有无泄漏,模具之开程若有限制的话也应在模上标明。
以上动作若能在挂模前做到的话,就可避免在挂模时发现问题,再去拆卸模具所发生的工时浪费。
3. 当确定模具各部动作得宜后,就要选择适合的试模射出机,在选择时应注意(a)射出容量(b)导杆的宽度(c)最大的开程(d)配件是否齐全等。
一切都确认没有问题后则下一步骤就是吊挂模具,吊挂时应注意在锁上所有夹模板及开模之前吊钩不要取下,以免夹模板松动或断裂以致模具掉落。
模具装妥后应再仔细检查模具各部份的机械动作,如滑板、顶针、退牙结构及限制开关等之动作是否确实。
并注意射料嘴与进料口是否对准。
下一步则是注意合模动作,此时应将关模压力调低,在手动及低速的合模动作中注意看及听是否有任可不顺畅动作及异声等现象。
4. 提高模具温度:依据成品所用原料之性能及模具之大小选用适当的模温控制机将模具之温度提高至生产时所须的温度。
待模温提高之后须再次检视各部份的动作,因为钢材因热膨胀之后可能会引起卡模现象,因此须注意各部的滑动,以免有拉伤及颤动的产生。
5.若工厂内没有推行实验计划法则,我们建议在调整试模条件时一次只能调整一个条件,以便区分单一条件变动对成品之影响。
6.依原料不同,对所采用的原枓做适度的烘烤。
7.试模与将来量产尽可能采用同样的原料。
8.勿完全以次料试模,如有颜色需求,可一并安排试色。
9.内应力等问题经常影响二次加工,应于试模后待成品稳定后即加以二次加工模具在慢速合上之后,要调好关模压力,并动作几次,查看有无合模压力不均等现象,以免成品产生毛边及模具变形。
射出成型作业标准

制订日期:年月日
版次
规格
制订单位:制造部生技组
核准
审核
制订
标准工时
个/HR
变更记事
成型机台
符号
变更内容
成
型
条
件
使用
材料
材质
干燥
成品
净重
g/个
颜色
重量
毛重
g/个
周期时间(秒)
人工时间(秒)
冷却时间(秒)
料管温度℃
HN
H1
H2
H3
H4
H5
H6
控制
方式
TIME
V-P
切换
mm
模具
mm
中
子
动作
开模前
模具温度℃
秒
终速
降压时间
型闭压力
开模压力
注意事项
射出机作业标准
文件编号:
PR-018-02-A0
保压
③
kg/cm²
㎜
㎜
秒
秒
秒
回转速
%
回转压
kg/cm²
射出长度㎜/秒
背
压
kg/cm²
松退
押
出
戾限㎜
计量
%
料量
㎜
sec
㎜
后退%
型
开
闭
低速
低速
染
色
机
色
母
编号
前进⑴%
1→2切换㎜
1→2切换㎜
比例
切换
2→3切换㎜
取出开始㎜
料量时间
出限㎜
接触
终速
热
胶
道
迟延时间
秒
注塑厂模具试模及验收作业指引

注塑厂模具试模及验收作业指引1、目的为了保证修改模、新模、试模效果良好,控制模具质量使生产顺利进行。
2、适用范围适用于注塑成型和工模修模组。
3、定义3.1模具试模:控制产品各类缺陷,试出各项存在影响问题,找出解决方案。
4、职责4.1注塑部:负责模具请修、试模、试样、并跟踪返修到位。
4.2班长:负责根据现场生产的要求安排修模作业。
4. 3工艺组长:负责跟踪修模、试模结果及报告填写与最终结果确认。
5、工作程序4.1 模具请修作业4.1.1 正在机台上生产的模具请修流程5. L1.1生产中出现料件不良,如镶件断、划伤、飞边、毛刺、滑块卡死、压模等不能正常工作时,班长及时上报课长处,同时课长决定是否先生产或立即修模。
若判定为立即修模模具,由班长填写模具请修单,送课长或部门经理处审核,同时在IH内下模,附上不良样板及经审核的修模单一起送到工模部。
生产中模具一般在12H间修好,并由课长或班长负责跟踪。
5.1.1.2工模部将模具修好后连同“试模通知单”一并送往注塑部,模具组长签收。
模具组长签收到机台修模、试模单时应及时安排班长或技术人员试模,班长将重新写首件,将修模后料件送于PQC处确认修模结果,OK即可正常生产,NG则通知工模返修到好为止。
5.1.2生产完模具请修5.1.2.1模具订单批量生产完,班长下模送于模房,应附有该模的“生产记录单”和尾板料件。
模具保养员接收模具后,应仔细查看“生产记录单”是否填写规范、工整,并确认是修模还是保养。
若保养模,则保养后上模架;若需修模,模具保养员应根据“生产记录单”上所记录的问题开出“模具请修单”和不良料件,送于模具组长或课长、经理处审核,保养员再将模具及时送于工模修模组,模具组长随后将审核好的“模具请修单”连同修模料件一并送于工模(”模具请修单”的填写:编号、时间、机型、料件名称、送修时间、完成时间、修模内容)。
模具送到工模,保养员应做好详细的送模记录,并由工模签名。
成型试模作业指导书

成型试模作业指导书英力集团SV Group英力电子科技(昆山)有限公司SHINY VACUUM TECHNOLOGY(KUNSHAN)CO.,LTD.真准电子(昆山)有限公司CHUPOND ELECTRONICS TECHNOLOGY(KUNSHAN)CO.,LTD文件名称:成型试模作业指导书文件编号: YL-W-2003版本 : A发行日期:2014/8/28修订履历1目的: 规范试模作业程序,提升试模效率,提升试模检讨能力,减少试模次数。
2范围:成型车间3职责:试模技术员4准备工作:4.1手套,白布,清洗剂,水桶,风枪,机械手治具(测试),切料头治具(测试),试模条件(试模册),卡尺等。
4.2参加人员:注塑技术员,厂内工程,模具厂技术员,客户RD。
5试模步骤:5.1 上模前,点检模具定位环,锁模块,限位开关,强制回位螺丝大小,水嘴内孔型号是否统一,水嘴外孔避空是否够大,水嘴孔与压块是否有干涉,吊环孔检查,灌嘴是否固定、是否与定位圈同心,顶针板孔是否合理,模具○顶○基是否标示,各水路是否标示,模脚处锁压块位置是否避空过小等等。
5.2 模具电路配套定位是否合理,气阀定位是否合理实用等。
5.3 上模参照《成型课上模作业指导书》。
5.4 接水路,在接水时确认是否通畅,或有无一通二现象,检查模仁是否渗水。
5.5 开模,即检查模具滑动部件有无弹簧,有无定位或限位,滑块有无耐磨块,耐磨块、行位有无油槽等等。
5.6 检查PL面有无排气槽,排气块等。
5.7 顶出是否顺畅,异声,斜销有无油槽,较大的顶针上须开油槽和排气。
5.8 确认模具中心大面积靠破的空当处有无开排气井等。
5.9 除四支模具导柱外,公母模模坯四边有无凸凹定位装置。
5.10 合模时模具有无异常响声。
5.11 调机,输入之前的试模条件,参照《成型课开机作业指导书》调机。
5.12 新模调机,以“慢--快--慢”模式设定成型条件,分段先射出到料头,进胶点,再射到产品大小的95%,再将产品射满、但不饱模的状况下,确认保压转换位置,再以从小到大递增的次序设定保压压力,禁止因压力过大撑涨模。
试模SOP

試模SOP 試模SOP
澆道黏模改善對策 項目 原因 1.射出壓力太高 機器 2.填料過飽 3. 澆道波司(SPRUE BUSHING) 與 (NOZZLE) 射料嘴(NOZZLE)之配合不正 1.澆道過大 2.澆道冷卻不夠 3.澆道脫模角不夠 模具 4.澆道內表面不光滑或有倒模脫角 5.澆道外孔有損壞 6.無澆道環銷(SNATCH PIN) 對策 1.降低射出壓力 2.降低射出劑量時間及速度 3.重新調整其配合 1.修改模具 2.延長冷卻時間或降低冷卻溫度 3.修改模具增加角度 4.檢修模具 5.檢修模具 6.加設抓銷材料原料溫度過高降低 原料溫度
試模SOP 試模SOP
黑點改善對策 項目 原因 1.原料過熱部份附著料管管裹 對策 1.徹底空射 2.拆除料管清理 3.降低原料溫度 機器 2.射入模內時產生焦斑(BURNING MARK)料管內有使原料過熱的死角 4.減短加熱時間 5.降低射出壓力入速度,酌降關模壓力 檢查射嘴與料管間接觸面.,有無間隙或 腐蝕現象
試模SOP 試模SOP
成型制程過程中的不良狀況
1.黑點 黑點 2.黑紋 黑紋 3.產品不完整 產品不完整 4.縮水 縮水 5.產品粘模 產品粘模 6.澆道粘模 澆道粘模 7.溢料毛邊 溢料毛邊
8.開模時頂出產品拉傷 拉白 開模時頂出產品拉傷,拉白 開模時頂出產品拉傷 9.結合線 結合線 10.流紋 流紋 11.銀絲 氣瘡 銀絲&氣 銀絲 12.產品表面不光澤 產品表面不光澤 13.產品變形 產品變形 14.產品內孔有氣泡 產品內孔有氣泡
提出問題點進行原因分析,分析出原因後再由改善單位提報改善對策及完成時間由業務工程 師進行追蹤.
b.試模後尺寸部份檢討
(1).產品的重點尺寸(圖面上有標示之尺寸) (2).CPK尺寸(圖面上有特殊標示或與客戶協商之尺寸) 造成尺寸NG的原因有二,首先是模具尺寸是否有做到模具設計值,因此我們必須檢查模具 量測報告,報告上之量測尺寸是否與模具設計值相符.其次就是确認成型條件的問題,而成型條 件包括機台以及周邊設備的設定以及人員的因素.成型條件一定後,產品尺寸還不合格,就要考 慮修改模具設計值.
射出成型现场实用手册

PC+ABS: 含玻纖材料: POM:塑鋼
Polyoxymethylene , polyacetal
03'01'04
模具簡介-兩板模
03'01'04
兩板模運作原理
"A" Plate
Standard Two Plate Mold
Sprue Bushing
Ejector Plate
Support Plate
內部加強肋厚度
03'01'04
成型品設計的原則-肉厚
一般肉厚建議需均勻
肉厚不均容易造成縮水.產生內應力.變形
能否有效均勻分散衝擊作用力 構造強度是否充分
03'01'04
資料來源
Tom‘s 硬體指南 公用資料夾 實用塑膠模具學-全華出版社 射出成型現場實用技術手冊 3C產業材料暨精密塑膠射出加工技術交 流會
03'01'04
塑膠射出製程
將粒狀的ABS塑膠樹脂倒入機器中,並 熔化這些樹脂,然後將其注入模具中以 形成塑膠零件。
03'01'04
塑膠射出製程
射出場必須用到許 多模具架來存放塑 膠射出模具。
03'01'04
塑膠射出製程
射出機器將塑膠熔化後注入模具中。等 到塑膠冷卻並從模具中取出時,便可得 到塑膠成品。
03'01'04
塑膠射出製程
工作人員正在進 行品管檢查。檢 查的重點是射出 品的品質。在這 個步驟中,工作 人員必須確定射 出品完全符合規 格。
试模标准动作流程
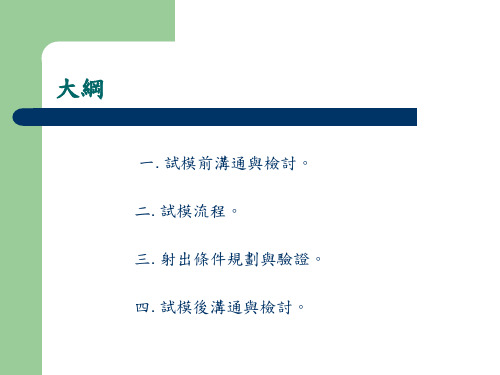
射膠行程計量
100*10 12.56*1.06*0.8 *0.8+3(殘量)
=(1000/10.68)*0.8+3 ≒ 77(mm)
樹脂 PP
樹脂比重*射出效率 0.73
PE
0.71
PS
0.91
ABS 0.85 * 射出效率一般以80%計
樹脂 AS PA PC PMMA
樹脂比重*射出效率 0.99 0.97 1.06 1.06
【附圖F】
依照產品結構和塑料特性、 外觀要求設定模溫機溫度。
【附圖G】 公、母模仁四角點。
【附圖H】
量測四角點溫度 ,確定溫度是否達到要求,並可由 此得知溫度分佈是否平均。
【附圖I】
檢查頂針、斜銷、滑塊、 導銷等滑配機構是否有異 常和拉模痕。
2-3-1 射膠行程預估計算方法
射膠行程計量(mm)=
2-4 短射
找出模具澆道至澆口的極限位置。 依照產品結構設定各個流動軌跡位置。 找出因注澆而產生的應力、變形、噴痕、流痕、焦化、
光澤不均、頂白、縮水、毛邊等不良現象是如何產生。 將短射過程之成品以數位相機拍攝存檔。(附圖J)
【附圖J】 短射成品。
三、射出條件規劃與驗證
依據短射程序找出中壓及中速值。 依據短射程序找出何處有包風現象,再來制定分幾
依據前述觀念要求模具廠作對的修改。
4-1 試模記錄
試模完立即量測公、母模四角點溫度,並加以記錄。 (附圖M)
記錄料管溫度。 (附圖N) 記錄成型條件。 (附圖O) 記錄試模過程之問題點及改善對策。
【附圖M】 公、母模仁四角點。
【附圖N】 記錄料管溫度於模具生產履歷表內。
【附圖O】 記錄成型條件於模具生產履歷表內。
模具生产流程SOP

模具生产流程作业规范
1.总则
1.1制定目的
为规范模具始作、试模、模具修正、承认、量产得以顺利进行,有效进行资源整合利用,使之有章可循,特制定本规范。
1.2适用范围
本公司制作与量产之所有模具。
1.3权责单位及职能
(1)模具技术营业部:
1、模具制作之提出、报价、试模安排、模具承认、模具履历表建立;
2、模具结构检讨、试模跟踪、试模问题点及改善对策建立及跟踪、试模指
导书;
3、试模条件表建立、部品2D图面CHECK;
(2)品质部:
1、注塑及后加工检查标准书建立;
2、生产过程中品质督导、不良状况分析并制定相关改善措施会同其它部门、
品质问题点与客户交涉;
3、建立相关品质记录表单及报告表单、返工事件处理;
(3)生产技术部:
1、注塑及后加工作业指导书、材料明细表、机种注塑资料清单;
2、样品制作跟踪、部品(客户)承认、样板(业体)制作确认;
3、PV、PR、LPP、DPP生产跟进、问题点处理、对策建立、跟踪
4、生产流程规划、生产仕样建立、生产所需之其它文件制作;
5、技术问题与客户进行交涉;
6、生产使用工、治具制作及确认;
(4)营业部:
1、生产及交货计划、内部P/O管理;
2、模具外发管理、外发加工管理、交货及客服;。
射出作业指导书

页次:3
制定部门:研发部 制定日期:2004 年 10 月 16 日
射出作业指导书
文件编号: 版 次: 修订日期:
5.7.1 射出速度, 料管温度――减少 5.7.2 射出压力, 射嘴及前段温度――减少 5.7.3 螺杆转速――减少 5.8 黑点及杂质之处理方法 5.8.1 检查原料 5.8.2 料管温度――减少 5.8.3 射嘴及前段温度――减少 5.8.4 螺杆转速――减少 6.0 相关表单: 6.1 首件, 末件检查记录表(RD-001-01) 6.2 射出作业点检表(RD-001-02) 6.3 射出巡检日报表(RD-001-03) 6.4 射出站检片点检表(RD-001-04) 6.5 射出制程参数表(附件一) 6.6 模温测量记录表(RD-001-05)
射出作业指导书
文件编号: 版 次: 修订日期:
1.0 目的:规范射出所属之作业流程.
2.0 设备: 2.1 原料干燥除湿机 2.2 射出成型机 2.3 机械手 2.4 电控模温机 2.5 离子风扇 2.6 框架及台车 2.7 输送带
3.0 原物料: 3.1 塑料原料 3.2 去渍油 3.3 老紫液 3.4 化妆棉 3.5 工业酒精 4.0 作业说明: 4.1 作业流程
塑胶原料 塑胶原料
烘 烘料 料
射出成型 射出成型
取 取出 出
强 化 站 强 化 站
插 插框 框
折折
Hale Waihona Puke 片 片吹 吹净 净4.2 烘料前准备 4.2.1 请参照射出制程参数表(附件),作原料选择. 4.2.2 用工业擦试纸将塑胶原料之外袋擦拭干净. 4.2.3 将塑胶原料外袋拆开,检视袋内塑胶原料有无异物,毛屑掺杂等.
页次:4
4.3 烘料 4.3.1 将塑胶原料置入干燥除湿机置料桶内, 并确实锁紧桶盖. 4.3.2 若塑胶原料为 PMMA, 则以除湿温度 180℃干燥温度 90℃ ~100℃之温度烘料四至六小时.
试模作业规范
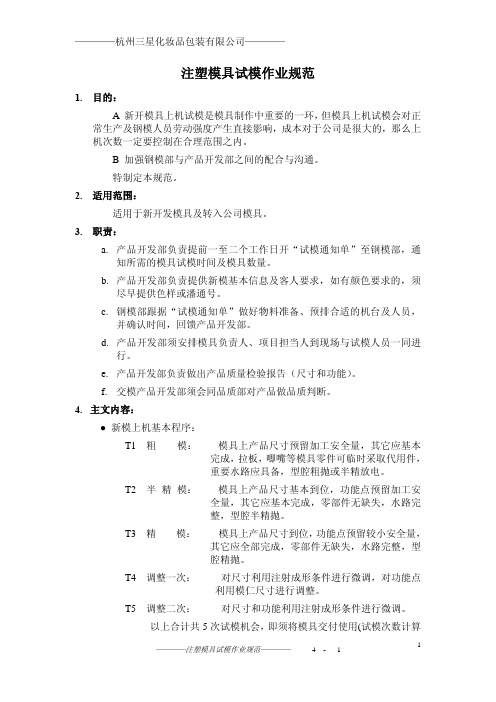
注塑模具试模作业规范1.目的:A 新开模具上机试模是模具制作中重要的一环,但模具上机试模会对正常生产及钢模人员劳动强度产生直接影响,成本对于公司是很大的,那么上机次数一定要控制在合理范围之内。
B 加强钢模部与产品开发部之间的配合与沟通。
特制定本规范。
2.适用范围:适用于新开发模具及转入公司模具。
3.职责:a.产品开发部负责提前一至二个工作日开“试模通知单”至钢模部,通知所需的模具试模时间及模具数量。
b.产品开发部负责提供新模基本信息及客人要求,如有颜色要求的,须尽早提供色样或潘通号。
c.钢模部跟据“试模通知单”做好物料准备、预排合适的机台及人员,并确认时间,回馈产品开发部。
d.产品开发部须安排模具负责人、项目担当人到现场与试模人员一同进行。
e.产品开发部负责做出产品质量检验报告(尺寸和功能)。
f.交模产品开发部须会同品质部对产品做品质判断。
4.主文内容:●新模上机基本程序:T1 粗模:模具上产品尺寸预留加工安全量,其它应基本完成,拉板,唧嘴等模具零件可临时采取代用件,重要水路应具备,型腔粗抛或半精放电。
T2 半精模:模具上产品尺寸基本到位,功能点预留加工安全量,其它应基本完成,零部件无缺失,水路完整,型腔半精抛。
T3 精模:模具上产品尺寸到位,功能点预留较小安全量,其它应全部完成,零部件无缺失,水路完整,型腔精抛。
T4 调整一次:对尺寸利用注射成形条件进行微调,对功能点利用模仁尺寸进行调整。
T5 调整二次:对尺寸和功能利用注射成形条件进行微调。
以上合计共5次试模机会,即须将模具交付使用(试模次数计算方法依“新开模奖惩制度”标准执行) 。
● 新模上机基本条件:a.. 信息:产品开发部负责提供产品材料、产品颜色及后续加工方式。
b. 产品开发部送试的模具应具备:1. 排气已经开好。
2. 滑块已经定位。
3. 水嘴已经接好并确认不漏水。
4. 各配件应齐全,模具详细资料,特别是共用模座,应确认清楚相关配件)。
试模作业指导书

试模作业指导书一、背景介绍试模是指在生产制造过程中,为了验证产品设计的可行性和制造工艺的合理性,通过制作模具并进行模具试模操作,以检验产品的尺寸精度、装配性能、工艺可行性等方面的要求。
试模作业是模具制造过程中的重要环节,对于确保产品质量和生产效率具有重要意义。
二、试模作业的目的试模作业的目的是通过模具试模操作,验证产品设计和制造工艺的可行性,检验产品的尺寸精度、装配性能、工艺可行性等方面的要求,为后续的批量生产提供参考和指导。
三、试模作业的步骤1. 准备工作在进行试模作业之前,需要进行以下准备工作:- 确定试模的目的和要求,明确试模的检验内容和标准。
- 准备试模所需的模具、产品零件、材料和工具等。
- 清洁模具和试模设备,确保其表面干净,并进行必要的润滑和保养。
2. 模具安装将模具安装到试模设备上,确保模具安装牢固、稳定,并能够正常运行。
根据模具的结构和特点,进行相应的模具调整和校正,确保模具能够正常开合、顺畅运行。
3. 试模操作根据试模的目的和要求,进行相应的试模操作。
具体步骤如下:- 将产品零件放入模具中,进行装配操作。
检查产品零件的装配性能和尺寸精度,确保产品能够正常装配和使用。
- 进行模具开合操作,观察模具的开合情况和动作是否正常。
检查模具的开合间隙、顶出装置等,确保模具能够正常开合、顺畅运行。
- 进行注塑操作,将熔融的塑料材料注入模具中,形成产品零件。
观察注塑过程中的温度、压力、流动性等参数,检验产品的工艺可行性。
- 进行冷却和顶出操作,使产品零件冷却固化,并从模具中顶出。
检查产品零件的尺寸精度、表面质量等,确保产品符合设计要求。
- 进行模具开合、顶出、冷却等操作的调整和优化,以达到最佳的试模效果。
4. 试模结果分析根据试模操作的结果,进行相应的分析和评估。
对试模中出现的问题进行记录和总结,找出问题的原因,并进行相应的改进和优化措施。
根据试模结果,评估产品设计和制造工艺的可行性,为后续的批量生产提供参考和指导。
注塑射出成形的各阶段操作设定重点,收藏了

注塑射出成形的各阶段操作设定重点,收藏了注塑汇国内专注注塑业咨询培训服务,致力于注塑业的降本增效疫情以后,注塑行业向何处走?固体塑料的塑化阶段料缸温度及喷嘴温度(1)由第一段(入料处)到第三段(喷嘴前)逐渐升温,每段温度设定值约相差5~10℃,逐步将塑料加热到适当的加工温度,各种塑料有其不同的加工温度。
(2)对低黏度的塑料,为避免在机座后退时造成漏料,通常可将喷嘴温度设定成第三段温度或略低一些(约5℃),但太低将会造成冷料,在射出时易生流痕。
对高黏度的塑料,其设定值可高于第三段温度约5~10℃,射出时可用于将流道系统加热。
(3)熔胶因螺杆旋转而摩擦生热,常导致在第三段熔胶温度高于加热器的设定值,一般甚至可高出15~30℃,因此应避免温度设定太高产生热劣解。
螺杆背压螺杆背压一般约3~10kg/cm2,背压设定的目的主要是抵住螺杆,当进料时塑料输送到螺杆前端,产生熔胶压力而使螺杆缓慢后退。
若螺杆背压大,则塑料自入料口被输送到螺杆前端,所经历的时间较长,因此塑化程度较完全,气体较不易进入,但在螺杆前端产生的熔胶压力也较大,容易在机座后退时造成漏料。
反之!若螺杆背压小,则塑料自入料口被输送到螺杆前端,所经历的时间较短,因此塑化程度较不完全,且气体较易进入。
固体塑料的塑化阶段由于螺杆在进料过程中因熔胶室的增压而后退,因此后面进入的塑料所历经的螺杆长度将变短,对塑料的熔化能力将会发生不足的现象,若因此使未完全熔化的胶粒进入熔胶室而成悬浮状,将严重影响产品质量。
因此随着进料行程的进行,螺杆的后退速度应渐缓,且必须使后进的胶料能在螺沟内有足够的时间熔化。
为达此目的,螺杆背压应随着进料行程的进行而渐增,而螺杆转速应渐减。
螺杆转速•螺杆转速rpm快,则吃料量多,剪切热也较高,但若太快也可能造成塑料分子的剪断•参有玻纤的塑料,若螺杆转速太快,会将玻纤剪断,造成物性降低•随着进料行程的进行,为使后进的胶料能在螺沟内有足够的时间熔化,螺杆转速应渐减。
试模操作流程标准规范

试模操作流程试模主要分四部分:(1)试模前模具的检查(2)试模前的准备工作和调试(3)试模时的注意事项(4)试模后模具的检收一、试模前模具的检查模具做好后,需要对模具进行试模前的检查,以发现模具设计和制造中的问题,以便及时纠正,其具体步骤如下:(1)注塑模的外观检查1.成型零件、浇注系统等与熔料接触的表面应光滑、平整、无塌坑、伤痕等缺陷。
2.模具的闭合行程,安装于机器的各配合部位尺寸、脱模方式、开模距离、模具工件要求等应符合设备的相关条件。
3.模具上应有生产号和合模标志,各种接头、阀门、附件、备件应齐全。
4.各滑动零件的配合间隙应符合要求,起止位置定位正确,镶件紧固应紧固牢靠。
5.对于注塑腐蚀性较强的注塑模,其模具型腔的表面应镀铬和防腐处理。
6.模具的外观部分不应当有锐角,大、中型模具应有起吊用的吊孔、吊环。
7.互相接触的承压零件,应有合理的承压面积和承压方式,避免直接承受挤压。
8.模具的稳定性良好,有足够强度,工作时应受力匀衡,行动平稳。
(2)模具的空运转检查模具安装好后,必须经过空运转检查,经便进一步发现问题,进而解决问题。
1.将模具缓缓合拢,合模后各结合面均应接触紧密,不得出现间隙。
2.开模时顶出脱模机构应保证顺利脱模,以便取出塑件和浇注系统废料。
3.活动型芯,顶出及导向部分等运动时应滑动平稳、灵活、动作协调可靠。
4.检查各锁紧机构、应能可靠、稳妥地锁紧,各紧固件不得有任何松动现象。
5.各气动、液动控制系统动作正确,不泄漏、不产生过大振动,各阀门工作正常。
6.冷却系统的水路应畅通,不漏水,各种控制阀门控制正常。
二,试模前的准备工作及调试试模是为了检查模具制作的质量好坏,能否生产出合格产品来。
1.试模前,应检查所用原料是否符合要求,不符合要求的应进行处理或更换;欲试之原料先行干燥,PE、PP、POM不需干燥其余均要,利用新料试才标准。
2.模具挂上中心孔要对准锁模力以总顿数的1/3即可,如射出时分模面不是因射压太高之关系起毛边,可渐渐增加锁模顿数直到不起毛边为至如此做法可增长模具使用寿命。
QI-RD-014 (A1)立式射出成型机作业规范

□文件变更内容: 新增Management representative 管理代表Approve 核准Review 主管审核Establish制定二 范围:Scope:适应本公司相关技术人员和成型作业员。
三 权责:Responsibility:3.1工程部对相关技术文件的补充及修正,并负责设备的维护与维修。
四 定义:Glossary:无五作业内容:Content of Operation:5.1 成型机:5.1.1 按其结构可分为:A.卧式机(主要是成型一些无镶件的胶件)B.立式机(成型镶件产品有它独有的优点)5.1.2 立式成型机的结构(参见图一、图二):图一 图二5.1.35.1.4 立式成型机的型号及其规格:控制面油压表 料斗 固定块.接近开关 关模慢速调安全电眼 紧急回升开关油压马达电机 电磁换向阀 哥林电热高压油座缸 射缸模缸 上模板 自动关模下模板 螺杆 油箱冷却水2 射出成型相关专业名词说明:5.2.1 塑胶原料须经下列条件才能由射出成型机将胶料射入模腔内成型5.2.1.1 温度(电热温度)控制5.2.1.2 压力(总压、射出一次压力、二次压力、关模低压、背压)控制5.2.1.3 射出时间(射出时间、冷却时间、低压时间、顶出时间)控制5.2.1.4 射出速度控制5.2.1.5 射出料量(一次料量、二次料量)控制5.2.2 电热:可分为上、中、下节温度,控制不同的塑胶原料加热温度皆不同,对于PVC 料 ,一般为150℃~200℃.温度必须达到塑胶塑化之温度,方可射出加料, 否则,可对螺杆造成损伤。
5.图三 图四5.2.3 压力控制:机器的压力控制由液压系统来控制和完成,其动作压力可分为总压力、低压、射出一次压力(即一次压)、射出二次压力(即二次压),各射出压力大小及注意点如下。
5.2.3.1 总压力:射出成型机关模压力(即锁模压力),其大小须视模具大小而定,一般固定点機臺型號料桿直徑射出重量開模行程最小模厚最大開距35T(鎖模力) 28 cm 58g 280mm 100 mm 460 mm 15T(鎖模力)25cm38g140mm40mm230mm模具(如D-SUB)设定压力约为80~100KG,活动模具(如SR 模)设定压力 约为50~70KG,其最高压力不超过110KG 以上,以免造成机台损伤。
SOPZS12试模作业指导书

文件修订履历1目的确保试模操作正确,防止不正当操作造成人身伤害和模具或机器的损坏提高试模效率及试模有效性2范围适用于试模流程3安全3.1 开机前安全要求3.1.1 进入工作岗位时需穿戴好工作服、工作鞋,特殊情况下:如拆卸注塑机射嘴.拆卸注塑机螺杆时要戴好防护眼镜;如上下模具要戴好安全帽。
3.1.2 节假日后第一班开机时,要检查设备有否漏电,检查冷却水系统是否堵塞和滴漏。
3.1.3 机筒加热升温时,要同时开机筒冷却水。
冬季寒冷时,车间温度较低,应先点动开启油泵,未发现异常现象时再开车空转10~15min后正常生产。
3.1.4 检查注塑机各滑轨部位,并给各润滑点加油。
3.2 生产过程的安全要求3.2.1 机筒温度达到工艺要求以后,要恒温15分钟才进行螺杆动作的操作。
3.2.2 操作必须使用安全门,如安全门行程开关失灵时不准开机,严禁不使用安全门(罩)操作。
3.2.3 安放模具、嵌件时要稳准可靠,合模过程中发现异常应立即停机排除故障。
3.2.4 机器修理或较长时间修理模具时,必须将注塑机的料筒温度设置为保温状态或者关闭。
3.2.5 清理模具中残料或制品时要用铜质等软金属材料。
3.2.6 运转设备的电器、液压及转动部份的各种盖板、防护罩等盖好、安好、固定螺栓旋紧。
3.2.7 身体进到模具开档内,一定要关闭设备马达或电源。
维修人员修机时,操作者不准脱岗。
3.2.8 避免在模具打开时,用注射座撞击定模,以免造成定模模具损伤。
3.2.9 对空注射有困难时,应停止操作,注意通知邻近人员避开危险区,检查温度是否正常。
3.2.10 发现设备、模具异常、及时通知维修人员检修。
3.2.11 试模中用于清洗螺杆的废料要严格处理,一定要等料完全冷却后才能放进废料袋。
用于擦模具的废布要单独处理。
3.3 停机后安全要求3.3.1 停机前要使用PP料或其它不易分解的材料清洗注塑机的螺杆。
3.3.2 停机后将机器手动合模至低压位置,及时关闭马达电源开关。
试模作业指导书

5.0附件:无。
6.0参考文件:
6.1上下模作业指导书 WI-PD-004
4.4.7手动测试出合理成形条件后,再开半自动进行试作,约试作20模后再观察产品状况及注塑运作状况。
4.4.8在试作过程中,如果出现顶针因模温逐步升高而后退慢或不后退现象,是个别顶针或斜顶不顺畅所致。观察有无多胶及烧针现象,如不后退完或无强制复位功能,切不可合模,以免烧顶针、斜顶或撞伤前模。
4.4.9在试作过程中,如在开模或顶针顶出时出现声响,可视为前后模分开时或产品顶出时不平衡不正常而产生之声音,此情况必有顶白、拉伤、变形、尺寸变化等异常现象。此时必须观察产品顶白或拉伤、变形之处,作上标记。若需要提交样品,可先喷脱模剂试作样品,但不良样品及现场作业状况做模人员务必清楚,作为日后改进重点。
4.4.10在试作过程中产品出现缩水异常现象时,首先分析产品结构是否复杂,流道及浇口大小位置是否合理。若改进缩水,必须考虑会不会导致产品筋位及柱子粘膜。若成形条件调整改进困难连喷脱模剂都必须无法啤出样品,可要求做模人员及时调整处理。
4.4.11在试作过程中,对注塑一模出多穴或形状结构不同部品的情况,必须通过分段射出了解浇口是否平均,浇口形状及位置是否合理。若不平均,会出现成形困难、顾此失彼现象。若需先试出样品,可分穴分次成形先将样品制出,列出浇口大小形状位置,方便做模人员后续改进。
4.4试模过程
4.4.1根据“制样通知单”试作要求知会注塑课做模人员及品质课QE到现场一同开始试模。
4.4.2开始试模前,如是首次试模的注塑,必先看成品图纸或客供样品来预设成形条件,并对前后模喷上脱膜剂,预防第一模就粘模。
4.4.3如是再次试模的注塑,使用同等规格型号的成形机台,且将前一次试模报告作为试作依据,前一次试作的样品作为参考,方可开始试作。
试模作业指导书

模具试模打样作业指导书1、目的规范试模2、责任部门项目组、成型试模、品质部、3、记录《委外申请单》《模具检查表》《成型条件表》《模具整改表》《试模报价单》《试模送货单》《产品测数报告》4、文件和物品产品图原料物性表客户产品要求&DFM装配样品&上次试模样品&卡尺5、步骤5.1、按生产PO提前一周订购试模胶料,订购单需注明原料供应商提供原料物性表。
特殊原料客户提供,跟催营业部门提前将原料安排回厂,同时请客户提供相应的原料物性表。
5.2、制作《委外申请单》,委外试模或生产需提起2~3天预约机台。
5.3、按《模具检查表》《模具整改表》和钳工在合模前比对模具特征是否存在漏加工。
现场和钳工组长调试水、电、油是否正常运作。
现场确认模具外部接头和试模机台是否匹配。
现场验证顶出动作、滑块动作、油缸动作顺畅。
确认完毕后签字确认。
5.4、依据签字确认后的《模具检查表》《模具整改表》开物品放行条,并安排车辆拉模。
5.5、注塑机台确认:1.确认机台顶棍位置及直径是否符合。
2.确认机台对模具炮嘴是否存在漏胶。
3.确认机台运水是否符合模具及产品调整需求。
4.确认料斗是否清洗干净,做颜色产品需注意。
5.确认机台能正常升温制定:确认:批准:6.确认机台已过料洗机,射出胶料无黑点、混色、异物。
7.确认机台安排做前后模温差,调整变形。
5.6、啤机上确认模具动作:1.模具在啤机上顶出动作确认是否存在顶出异响。
2.油缸确认滑块动作。
3.热流道温控箱正常控制温度和射胶,油封正常开启和关闭,时序控制正常按步骤开启和关闭。
4.确认顶针、斜顶、滑块行程开合到位,符合产品取件要求。
5.确认模具开模顺序和动作是否到位。
6.三板模确认水口取件符合机械手取件要求。
5.7、产品走胶确认:1.产品调试10%、30%、60%、98%不同位置的走水样本。
2.调试高速高压样品验证模具研配效果并保留注明留给生产组修改模具。
3.射胶位置调整到样品98%时切换成保压,调整保压压力和速度查看产品外观。
射出成型注塑机安全操作规程 安全操作规程 岗位作业指导书 岗位操作规程

××××有限公司标准安全操作规程文件编号:XXX-XXX-XXX射出成型注塑机安全操作规程编制:审核:批准:版本:受控状态:20××年10月10日发布20××年10月10日实施标准、完整的Word版文档,下载后可根据实际工作情况适当修改,自由编辑,适合相关行业人员参考,实际使用请删除本行文字。
射出成型注塑机安全操作规程程序文件规定了射出成型注塑机安全操作的方法,以达到使设备状况良好正常运转、高效、优质、低耗和安全生产;避免对环境造成污染。
1适用范围注塑车间所有注塑机。
2规程内容2.1工作人员工作前必须穿戴好防护用具(手套、工作鞋、工作帽等)。
2.2当前后安全门和安全护罩开启时,绝对禁止操作机器设备。
2.3前后安全门亚克力板损坏时,应立即维修货更换。
2.4机器在正常运转时,绝对禁止让身体的任何部位进入模具区域固定护罩内。
2.5人员进入修模或进入机台里面时,必须按下红色紧急停止开关或停止马达。
2.6由于料管是高温度及高电压的缘故,绝对禁止接触射出部分及料管、电热、盖板。
2.7在射出保护罩或电热盖板被拆除时,绝对禁止操作机器。
2.8当料桶被拆除时,绝对禁止将手和铁块杆入进料口。
2.9操作工必须严格培训,并由车间考核确认后方可操作。
2.10操作过程必须按照正确流程作业。
2.11若操作中有紧急状况时,请按下机台操作面板上的红色紧急开关按钮,自己无法处理必须立即上报机修或相关负责人。
2.12在设备不明原因停止工作时,应立即将急停按钮按下,然后通知班长初步查找原因,不要私自对设备操作,更不要进入设备工作区操作或者观看。
2.13设备投入工作前必须确认压缩气压压力值是否在0.5-0.6MPA。
2.14严禁在设备工作区域堆放易燃易爆物品。
2.15工作前必须确认循环水阀门打开,确认地面清洁,无积水,并对吸料机产生的灰尘进行清理。
2.16工作完毕后必须清理工作区卫生,清理机台下漏水、机身灰尘、油污等。
- 1、下载文档前请自行甄别文档内容的完整性,平台不提供额外的编辑、内容补充、找答案等附加服务。
- 2、"仅部分预览"的文档,不可在线预览部分如存在完整性等问题,可反馈申请退款(可完整预览的文档不适用该条件!)。
- 3、如文档侵犯您的权益,请联系客服反馈,我们会尽快为您处理(人工客服工作时间:9:00-18:30)。
射出成型模具試模作業SOP (流程)
目錄
1.目的
2.適用範圍
3.試模作業流程與檢核項目
4.潛在模具生產性和可靠度問題檢測方法
5.試模異常問題點真因驗證及對策方法
6.塑膠模具試模Check List
7.产品试模工程条件卡
1.目的:
1-1減少Try & Error 之次數,縮短模具開發時間。
1-2確保模具開發品質與量產性。
1-3提供經驗傳承,減少對老師傅的依賴度。
1-4做為模具廠、成型廠與產品負責人溝通的橋樑。
1-5新進人員之教育訓練用教材。
1-6選定最佳成型模式及條件。
2.適用範圍:
2-1 凡R&D負責開發之產品及模具均適用。
2-2 配合R&D產品開發之協力廠商亦須參考遵循。
3. 試模作業流程與檢核項目:
4. 潛在模具生產性和可靠度問題檢測方法:
5. 試模異常問題點真因驗證及對策方法
(設定在成品尺寸上限之狀況下或正常成型條件壓力及速度增加10%之狀況下)。