粉末冶金新技术在烧结齿轮中的应用
粉末冶金齿轮设计简介
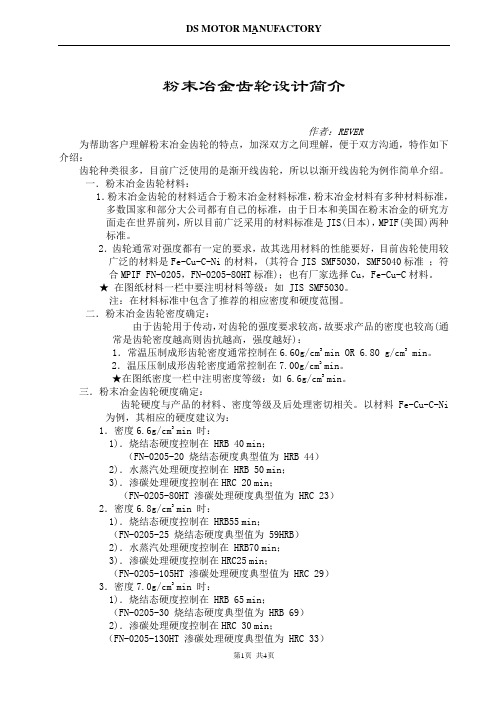
粉末冶金齿轮设计简介
作者:REVER
为帮助客户理解粉末冶金齿轮的特点,加深双方之间理解,便于双方沟通,特作如下介绍:
齿轮种类很多,目前广泛使用的是渐开线齿轮,所以以渐开线齿轮为例作简单介绍。
一.粉末冶金齿轮材料:
1.粉末冶金齿轮的材料适合于粉末冶金材料标准,粉末冶金材料有多种材料标准,多数国家和部分大公司都有自己的标准,由于日本和美国在粉末冶金的研究方
面走在世界前列,所以目前广泛采用的材料标准是JIS(日本),MPIF(美国)两种
标准。
2.齿轮通常对强度都有一定的要求,故其选用材料的性能要好,目前齿轮使用较广泛的材料是Fe-Cu-C-Ni的材料,(其符合JIS SMF5030,SMF5040标准;符
合MPIF FN-0205,FN-0205-80HT标准);也有厂家选择Cu,Fe-Cu-C材料。
★在图纸材料一栏中要注明材料等级:如 JIS SMF5030。
注:在材料标准中包含了推荐的相应密度和硬度范围。
二.粉末冶金齿轮密度确定:
由于齿轮用于传动,对齿轮的强度要求较高,故要求产品的密度也较高(通常是齿轮密度越高则齿抗越高,强度越好):
1.常温压制成形齿轮密度通常控制在6.60g/cm3 min OR 6.80 g/cm3 min。
2.温压压制成形齿轮密度通常控制在7.00g/cm3 min。
★在图纸密度一栏中注明密度等级:如 6.6g/cm3 min。
三.粉末冶金齿轮硬度确定:
齿轮硬度与产品的材料、密度等级及后处理密切相关。以材料Fe-Cu-C-Ni 为例,其相应的硬度建议为:
1.密度6.6g/cm3 min 时:
粉末冶金材料的应用
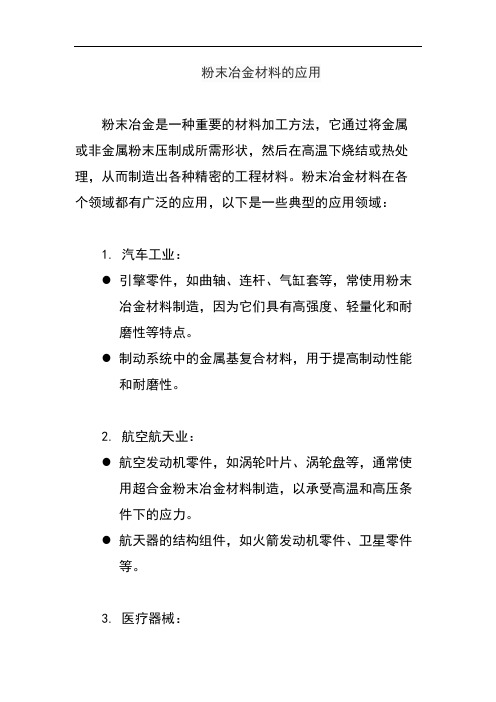
粉末冶金材料的应用
粉末冶金是一种重要的材料加工方法,它通过将金属或非金属粉末压制成所需形状,然后在高温下烧结或热处理,从而制造出各种精密的工程材料。粉末冶金材料在各个领域都有广泛的应用,以下是一些典型的应用领域:
1. 汽车工业:
●引擎零件,如曲轴、连杆、气缸套等,常使用粉末
冶金材料制造,因为它们具有高强度、轻量化和耐
磨性等特点。
●制动系统中的金属基复合材料,用于提高制动性能
和耐磨性。
2. 航空航天业:
●航空发动机零件,如涡轮叶片、涡轮盘等,通常使
用超合金粉末冶金材料制造,以承受高温和高压条
件下的应力。
●航天器的结构组件,如火箭发动机零件、卫星零件
等。
3. 医疗器械:
●人工关节、牙科植入物和医用工具等医疗器械中,
粉末冶金材料常用于制造耐腐蚀、生物相容性好的部件。
4. 电子和电气工程:
●电子电路板上的金属化连接器、封装材料和导电粘
合剂中常使用粉末冶金材料。
●用于磁性元件、电感器和传感器的软磁材料,如铁
氧体粉末。
5. 工具和刀具:
●刀片、铣刀、钻头、齿轮和锯片等切削工具常使用
粉末冶金材料制造,因为它们具有高硬度、耐磨性和耐热性。
●硬质合金(碳化钨等)用于制造切削刀具。
6. 磁性材料:
●用于电机、变压器、传感器和磁盘驱动器的永磁体
材料。
●电感线圈和电子元件的软磁材料。
7. 能源产业:
●用于太阳能电池和燃料电池的材料。
●用于储能系统中的电池材料。
总的来说,粉末冶金材料在制造业中发挥着重要作用,因为它们具有高度可控性、高精度和多种定制化特性,可以满足各种应用的要求。由于粉末冶金材料的广泛适用性和优越性能,它们在现代工程和科学领域中扮演着不可或缺的角色。
粉末冶金工艺在复杂零件制备中的应用

粉末冶金工艺在复杂零件制备中的应用
粉末冶金工艺是一种重要的金属材料加工技术,通过将金属粉末压制成形,然后进行高温烧结,从而制造出各种复杂的零件。粉末冶金工艺具有成本低、生产效率高、能耗低等优点,因此在复杂零件制备中有广泛的应用。
首先,粉末冶金工艺可以制备出具有复杂形状和内部结构的零件。传统的加工方法可能会受到几何形状的限制,而粉末冶金工艺可以灵活地调整粉末的成型方式,从而制造出各种复杂形状的零件,如内孔、螺纹、齿轮等。这些零件在一些特殊的工程领域中得到广泛应用,例如航空航天、汽车制造等。
其次,粉末冶金工艺可以制备出具有多种材料组成的零件。在一些特殊的工程要求中,需要零件具有复合材料的特性,而传统的加工方法难以实现。而粉末冶金工艺可以将不同材料的粉末混合在一起,并且可以通过控制烧结参数,使各种材料之间充分结合,从而制备出具有复合材料特性的零件。
再次,粉末冶金工艺可以制备出具有高精度和精细的表面特性的零件。粉末冶金工艺可以通过控制粉末的尺寸和形状以及烧结参数等,使得零件的尺寸和形状精度高,表面粗糙度小,从而满足一些对零件的高精度要求。同时,粉末冶金工艺还可以制备出具有特殊功能表面的零件,例如具有疏水、疏油、耐磨等特性的表面。
最后,粉末冶金工艺可以实现批量生产,并且可以高效利用材料。粉末冶金工艺可以将金属粉末高效压制成形,同时可以通
过粉末的再利用,减少材料的浪费。由于粉末冶金工艺的工艺稳定性好,生产效率高,因此可以实现批量生产,满足大规模生产的需求。
总之,粉末冶金工艺在复杂零件制备中具有重要的应用价值。通过粉末冶金工艺,可以制备出具有复杂形状和内部结构的零件,具有多种材料组成的零件,具有高精度和精细的表面特性的零件,并且可以实现批量生产并高效利用材料。粉末冶金工艺的应用在提高零件质量和生产效率,推动工业发展等方面发挥着重要的作用。粉末冶金工艺在复杂零件制备中的应用已经广泛涉及到各个领域,包括航空航天、汽车制造、机械加工等等。下面从几个方面继续介绍粉末冶金工艺的应用。
粉末冶金齿轮

粉末冶金齿轮
引言
粉末冶金是一种常用于制造高强度、高精度和复杂形状的
金属零件的方法。齿轮是粉末冶金应用领域的重要组成部分之一。本文将介绍粉末冶金齿轮的制造工艺、优势以及应用领域。
制造工艺
粉末冶金齿轮的制造工艺主要包括粉末制备、成型、烧结
和后处理四个步骤。下面将对每个步骤进行详细介绍。
1. 粉末制备
粉末冶金齿轮的制备通常使用球磨机来对金属粉末进行球磨,以确保粉末的细度和均匀性。球磨过程中,金属粉末与球磨介质在球磨罐中不断摩擦和碰撞,从而使金属粉末的颗粒尺寸逐渐减小。一般来说,金属粉末的粒径在10-200微米之间。
2. 成型
成型是指将粉末冶金齿轮所需的粉末填充到模具中,并施
加压力来形成所需的形状。成型方法通常包括冷压成型和注射成型两种。
•冷压成型是将金属粉末放入模具中,然后通过机械
压力将粉末压实,得到所需形状的零件。这种方法适用于
制造密度较低的齿轮。
•注射成型是指将金属粉末与有机粘结剂混合后,注
入到注射成型机中,通过高压将粉末注入模具中,然后经
过固化和去除粘结剂,得到所需形状的零件。
3. 烧结
在成型后,通过烧结过程,将填充在模具中的粉末在高温
下进行烧结,使粉末颗粒之间发生扩散,相互结合,从而形成致密的零件。烧结温度一般在金属材料的熔点以下进行,以保持粉末的形状稳定。烧结后的零件具有较高的密度和机械强度。
4. 后处理
烧结后的齿轮还需要进行加工和处理才能达到所需的精度
和表面质量。后处理工艺包括精加工、磨削、热处理和表面处理等。精加工和磨削可以使齿轮的尺寸和形状更精确;热处理可以提高齿轮的硬度和耐磨性;表面处理可以增加齿轮的表面硬度和耐腐蚀性。
粉末冶金工艺在生产中的应用

粉末冶金工艺在生产中的应用
粉末冶金工艺是一种利用金属或非金属粉末作为原料,通过成型和烧结等工艺制造零部件的方法。在工业生产中,粉末冶金工艺被广泛应用于制造各种金属零部件,具有许多独特的优势和特点。
粉末冶金工艺可以实现材料的高效利用。在传统的加工方法中,通常需要大量的原材料来制造零部件,而粉末冶金工艺可以将原材料直接制成粉末,避免了材料的浪费。此外,粉末冶金工艺还可以实现材料的高纯度和均匀性,提高了零部件的质量和性能。
粉末冶金工艺可以制造复杂形状的零部件。由于粉末可以在成型过程中填充到任何形状的模具中,并且可以在高温下烧结成固体,因此粉末冶金工艺可以制造出各种复杂形状的零部件,包括内部结构复杂的零部件,这是传统加工方法无法实现的。
粉末冶金工艺还可以实现批量生产,提高生产效率。在粉末冶金工艺中,可以通过一次成型和一次烧结来制造大量相同或类似的零部件,避免了传统加工方法中需要逐个加工的繁琐过程,大大提高了生产效率。
粉末冶金工艺还可以制造具有特殊性能的材料。通过粉末冶金工艺可以制备出各种合金材料,包括高强度、耐磨、耐腐蚀等特殊性能的材料,满足了不同领域对材料性能的需求。
总的来说,粉末冶金工艺在工业生产中具有广泛的应用前景。随着
科技的不断进步和工艺的不断完善,粉末冶金工艺将更好地满足各种行业对高质量、高效率、特殊性能材料的需求,推动着工业制造的发展。
粉末冶金工艺在生产中的应用具有独特优势,为各行业提供了更多可能性。随着工艺的不断创新和完善,相信粉末冶金工艺将在未来得到更广泛的应用,并为工业生产带来更多的发展机遇。
粉末冶金新技术-烧结

11
与传统的粉末冶金工艺相比,SPS工艺的特点是:
• 粉末原料广泛:各种金属、非金届、合金粉末,特别是 活性大的各种粒度粉末都可以用作SPS 烧结原科。
• 成形压力低:SPS烛结时经充分微放电处理,烧结粉末表 面处于向度活性化状态.为此,其成形压力只需要冷压烧 结的l/10~1/20。
8
SPS烧结原理示意图
9
SPS原理是利用强脉冲电流加在粉末颗粒上产生的诸多 有利于快速烧结的效应: 1)由于脉冲放电产生的放电冲击波以及电子、离子在电场
中反方向的高速流动, 可使粉末吸附的气体逸散, 粉末表 面的起始氧化膜在一定程度上可被击穿, 使粉末得以净 化、活化;
10
2)由于脉冲是瞬间、断续、高频率发生, 在粉末颗粒未接触 部位产生的放电热, 以及粉末颗粒接触部位产生的焦耳热, 都大大促进了粉末颗粒原子的扩散, 其扩散系数比通常热 压条件下的要大得多,而达到粉末烧结的快速化;
粉末冶金新技术
烧结新技术
1
三、烧结新技术 在普通烧结技术的基础上,通过改进加 热源、施加外力等作用在较短的时间里 使粉体致密化的过程,主要有微波烧结 技术和电火花烧结技术等。
2
1.微波烧结技术 微波烧结是通过被烧结粉体吸收微波,将电磁
粉末冶金齿条的热膨胀性能研究与改进

粉末冶金齿条的热膨胀性能研究与改进
摘要:
粉末冶金齿条广泛应用于机械传动系统中,其热膨胀性能是保证齿轮传动精度和可靠性的重要因素。本文采用实验方法研究了不同粉末冶金齿条在高温条件下的热膨胀性能,并提出了改进的方法,以提高其热膨胀性能。实验结果表明,通过适当的调整原料配比和处理工艺,可以明显改善粉末冶金齿条的热膨胀性能。这些研究成果对于提高齿轮传动的可靠性和使用寿命具有重要意义。
引言:
粉末冶金技术是一种制造工艺,通过将金属粉末经过成型和烧结等工序制备成零件。齿轮作为机械传动系统中重要的组成部分,粉末冶金齿条因其具有精密性和高效性而受到广泛应用。然而,在高温条件下,粉末冶金齿条的热膨胀性能可能会受到限制,进而影响其精度和可靠性。因此,研究和改进粉末冶金齿条的热膨胀性能具有重要意义。
1. 实验方法
1.1 实验设计
我们在实验中选择了不同配方的粉末冶金齿条进行测试,以探究不同成分对其热膨胀性能的影响。同时,我们采用了常见的测试方法,如热膨胀系数测试和热膨胀动态曲线测量等,来评估粉末冶金齿条在高温条件下的热膨胀性能。
1.2 实验结果
实验结果表明,在不同温度下,粉末冶金齿条的热膨胀性能存在差异。具体而言,随着温度的升高,粉末冶金齿条的热膨胀系数逐渐增大。此外,不同原料配比和处理工艺对粉末冶金齿条的热膨胀性能也具有显著影响。某些成分的变化可导致齿条材料的热膨胀性能显著改善。
2. 改进方法
2.1 原料配比优化
根据实验结果,我们可以通过调整粉末冶金齿条的原料配比,以优化其热膨胀
性能。例如,适当增加或减少某些成分的用量,以控制热膨胀系数的变化。此外,在选择原料时,应注意选择具有低热膨胀系数的材料,以提高整体热膨胀性能。
粉末冶金螺旋齿轮成形工艺
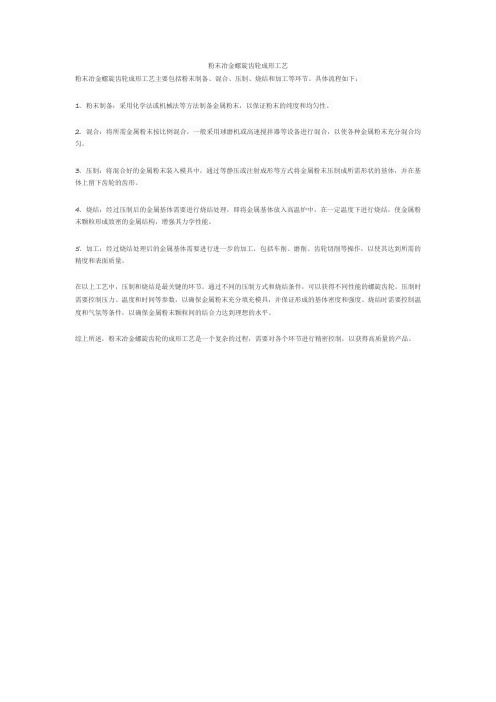
粉末冶金螺旋齿轮成形工艺
粉末冶金螺旋齿轮成形工艺主要包括粉末制备、混合、压制、烧结和加工等环节。具体流程如下:
1. 粉末制备:采用化学法或机械法等方法制备金属粉末,以保证粉末的纯度和均匀性。
2. 混合:将所需金属粉末按比例混合,一般采用球磨机或高速搅拌器等设备进行混合,以使各种金属粉末充分混合均匀。
3. 压制:将混合好的金属粉末装入模具中,通过等静压或注射成形等方式将金属粉末压制成所需形状的基体,并在基体上留下齿轮的齿形。
4. 烧结:经过压制后的金属基体需要进行烧结处理,即将金属基体放入高温炉中,在一定温度下进行烧结,使金属粉末颗粒形成致密的金属结构,增强其力学性能。
5. 加工:经过烧结处理后的金属基体需要进行进一步的加工,包括车削、磨削、齿轮切削等操作,以使其达到所需的精度和表面质量。
在以上工艺中,压制和烧结是最关键的环节。通过不同的压制方式和烧结条件,可以获得不同性能的螺旋齿轮。压制时需要控制压力、温度和时间等参数,以确保金属粉末充分填充模具,并保证形成的基体密度和强度。烧结时需要控制温度和气氛等条件,以确保金属粉末颗粒间的结合力达到理想的水平。
综上所述,粉末冶金螺旋齿轮的成形工艺是一个复杂的过程,需要对各个环节进行精密控制,以获得高质量的产品。
粉末冶金齿轮材料进展_FrancisHanejko2010

1 概述
齿轮是用于在平行或垂直于原来施加力的方向 传递扭矩与运动的机械部件 。 利用几何形状不同的 齿轮(直齿 , 螺旋齿 , 锥齿等)可使齿轮的噪声最小化 或使齿轮承载的扭矩特性最大化 。 由于对齿轮功率
密度与寿命的要求增高 , 促进了改进材料与材料生 产工艺的发展[ 1] 。 图 1 示铸锻齿轮材料与其极限抗 拉强度和其最大弯曲应力的关系曲线图 。
在粉末冶金中 , 合金化的方法有预混合法 , 扩散 合金化法及完全预合金化法 。图 2 示在粉末冶金零 件生产中使用的合金化方法 。最常用的合金化方法 是预先将各种合金化元素 、石墨粉及压制用润滑剂 混合于基粉铁粉中 。这种方法的好处是 , 能保持纯 铁粉固有的高压缩性 , 而且能够使用各种合金化元 素 。对预混合法的一项改进是扩散粘结的或部分合 金化的 材料(FD 材料)。 这种材 料的独 特之 处在 于 , 除石墨外 , 所有合金化元素都是通过热处理被粘 结在纯铁粉颗粒上 。其优势是 , 减少偏聚与压缩性 高 。扩散合金化粉的不足之处在于材料的生产成本 较高 , 这是因为其需要增加运送和热处理 。通过熔 化与雾化可生产完全均一的合金 ;可是 , 这样合金化 的铜与镍会降低铁粉的压缩性 。 用钼作为主要合金 化元素时 , 可使压缩性的下降最小化 , 而且生产的粉 末冶金零件显微组织均一和增高压缩性[ 8] 。 最后 , 可利用预合金化粉与额外添加的镍与铜(混合合金) 获得较高的烧结态与热处理态强度 。
粉末冶金齿条的材料选择与性能对比

粉末冶金齿条的材料选择与性能对比
在现代工业生产中,粉末冶金技术广泛应用于齿轮、齿条等零件的制造中。粉
末冶金齿条具有高精度、高耐磨和优异的力学性能等特点,因此在机械制造和汽车工业等领域得到了广泛的应用。粉末冶金齿条的性能主要取决于其材料的选择。本文将对粉末冶金齿条的材料选择及其性能进行详细的对比分析。
在粉末冶金齿条的材料选择方面,常见的材料包括铁基、铜基和镍基材料。这
些材料具有不同的化学成分和物理性能,适用于不同的应用场景。
首先,铁基材料是制造粉末冶金齿条常用的材料之一。铁基材料具有较高的强
度和硬度,同时具备良好的耐磨性能。常见的铁基材料包括高碳素钢、合金钢和不锈钢等。高碳素钢具有优异的硬度和耐磨性,适用于制造高负荷和高速运转的齿条。合金钢具有较高的韧性和抗疲劳性能,在高强度应用场景中表现出色。不锈钢具有抗腐蚀能力强的特点,在潮湿和腐蚀性环境下具有较好的耐久性。铁基材料广泛用于机械制造领域,特别是汽车和摩托车行业。
其次,铜基材料是另一种常见的粉末冶金齿条材料。铜基材料具有良好的导热
性和导电性,同时具备较高的塑性和可加工性。常见的铜基材料包括铜合金和青铜等。铜合金具有较高的抗腐蚀性和耐磨性能,在一些特殊应用场景中表现出色。青铜具有良好的耐磨性和自润滑性能,适用于制造高速和高载荷齿条。铜基材料通常用于制造电气设备和电子产品等领域。
最后,镍基材料在一些特殊应用场景中也被用于粉末冶金齿条的制造。镍基材
料具有优异的耐高温和耐腐蚀性能,适用于高温和腐蚀环境下的工作条件。常见的镍基材料包括镍铝合金和镍铁合金等。镍铝合金具有较高的耐磨性和高温强度,广泛用于航空航天和能源领域。镍铁合金具有较高的硬度和强度,适用于制造高负荷和高速运转的齿条。
用对研法提高粉末冶金齿轮的精度
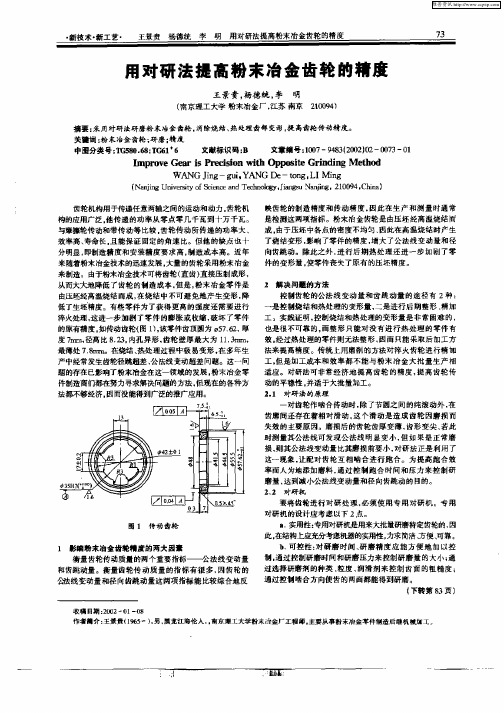
也是很不可靠 的, 而整形 只能 对没 有进行热 处理 的零件 有
效 , 过热处理的零件则无法整 形 , 经 因而只能采取后加 工方 法来提高精度 。传统 上用 磨削的方法对 淬火齿 轮进行 精加 工, 但是加工成本 和效率 都不 能与粉末 冶金 大批 量生产 相 适应 。对研法可非常 经济地 提高 齿轮 的精度 , 高齿轮 传 提 动的平稳性 , 并适于大批 量加工 。
2 1 对研 法 酌原 理 .
一
对齿轮作啮合 传动时 , 了节圆之 间的纯 滚动外 , 除 在
齿廓 问还 存在着相对 滑动 , 个滑 动是 造成 齿轮 因磨 损而 这 失效 的主要原 因。磨损后 的齿轮齿厚 变薄 , 齿形 变尖 , 若此 时测量其公法线可发 现公法 线 明显 变小 , 如果 是正常 磨 但 损 , 其公法线变动量 比其磨 损前要小 , 研法正是利 用 了 则 对 这一现象 , 让配对 齿 轮互 相 啮合进 行跑合 。为提 高跑合 效 率而人 为地 添加磨料 , 过控制 跑舍 时间和 压力来 控制 研 通 磨量 , 达到减小公法线变动量和径 向齿跳动 的 目的 。
2 2 对研 机 .
重
一 一
●
一
一
蘧
\
\0 5x 。
7
ቤተ መጻሕፍቲ ባይዱ
要将齿轮进行 对研 处理 , 必须使 用专 用对研 机 。专 用 对研机 的设计应考虑 以下 2. 。 a 实用性 : . 专用对研机是用来大批量研磨特定齿轮的, 因 此 力求简洁 、 、 方便 可靠。 b 可控性 : . 对研 磨 时间 、 磨精 度应 能 方便 地加 以控 研 制, 通过控制研磨时 间和研磨 压力来 控制研 磨量 的大小 ; 通 过选择研磨剂 的种类 、 度 、 粒 润滑 荆来控制 齿 面 的粗 糙度 ; 通过控制啮合 方向使齿 的两 面都能得到研磨。
粉末冶金非圆齿轮的能耗与资源消耗分析

粉末冶金非圆齿轮的能耗与资源消耗分析
摘要:粉末冶金是一种将金属粉末制备成所需产品的加工技术,具有材料利用率高、生产效率高、成型制件精度高等优点。本文将对粉末冶金非圆齿轮的能耗与资源消耗进行分析,以寻找优化工艺和减少能耗的途径。
1. 引言
随着现代工业的发展和对产品性能的不断追求,传动机械作为一个重要的领域也得到了快速发展。作为传动机械的重要部件之一,齿轮的制造工艺对产品质量和性能起着至关重要的作用。粉末冶金作为一种新型的制造工艺,具有一定的优势,但在能耗和资源消耗方面仍有改进的空间。
2. 粉末冶金非圆齿轮的制造工艺
粉末冶金非圆齿轮的制造工艺主要包括原料粉末制备、混合、成型、烧结和后处理等步骤。原料粉末制备是整个过程的基础,混合是将各种粉末按照一定比例混合均匀,成型是将混合粉末按照预定的形状制作成所需产品,烧结是在高温下使粉末颗粒相互结合,形成致密的制件,后处理则是对烧结制件进行加工和处理。
3. 粉末冶金非圆齿轮的能耗分析
3.1 原料粉末制备过程的能耗
原料粉末的制备过程包括矿石的选矿、粉碎和筛分等步骤。在这个过程中,能耗主要包括电力消耗和燃料消耗。选矿过程中需要采用磁选、选金、浮选等方法进行,这些方法需要消耗大量的电力。粉碎和筛分过程中,常常需要使用破碎机、颚式破碎机等设备,这些设备也需要消耗大量的电力。为了减少能耗,可以采用先进的制粉技术,如干法球磨、振动磨等,以提高能源利用效率。
3.2 混合过程的能耗
混合过程是将各种原料按照一定比例混合均匀的过程,其能耗主要来自于混合
设备的运行。目前常用的混合设备有双轴强制式混合机和单轴螺旋式混合机,这些设备运行时需要消耗电力或燃料。为了减少能耗,可以优化混合设备的结构,提高混合效率,减少混合时间,从而降低能耗。
粉末冶金齿轮

粉末冶金齿轮设计简介
作者:REVER
为帮助客户理解粉末冶金齿轮的特点,加深双方之间理解,便于双方沟通,特作如下介绍:
齿轮种类很多,目前广泛使用的是渐开线齿轮,所以以渐开线齿轮为例作简单介绍。
一.粉末冶金齿轮材料:
1.粉末冶金齿轮的材料适合于粉末冶金材料标准,粉末冶金材料有多种材料标准,多数国家和部分大公司都有自己的标准,由于日本和美国在粉末冶金的研究方
面走在世界前列,所以目前广泛采用的材料标准是JIS(日本),MPIF(美国)两种
标准。
2.齿轮通常对强度都有一定的要求,故其选用材料的性能要好,目前齿轮使用较广泛的材料是Fe-Cu-C-Ni的材料,(其符合JIS SMF5030,SMF5040标准;符
合MPIF FN-0205,FN-0205-80HT标准);也有厂家选择Cu,Fe-Cu-C材料。
★在图纸材料一栏中要注明材料等级:如 JIS SMF5030。
注:在材料标准中包含了推荐的相应密度和硬度范围。
二.粉末冶金齿轮密度确定:
由于齿轮用于传动,对齿轮的强度要求较高,故要求产品的密度也较高(通常是齿轮密度越高则齿抗越高,强度越好):
1.常温压制成形齿轮密度通常控制在6.60g/cm3 min OR 6.80 g/cm3 min。
2.温压压制成形齿轮密度通常控制在7.00g/cm3 min。
★在图纸密度一栏中注明密度等级:如 6.6g/cm3 min。
三.粉末冶金齿轮硬度确定:
齿轮硬度与产品的材料、密度等级及后处理密切相关。以材料Fe-Cu-C-Ni 为例,其相应的硬度建议为:
1.密度6.6g/cm3 min 时:
粉末冶金齿轮设计指南(二)2024
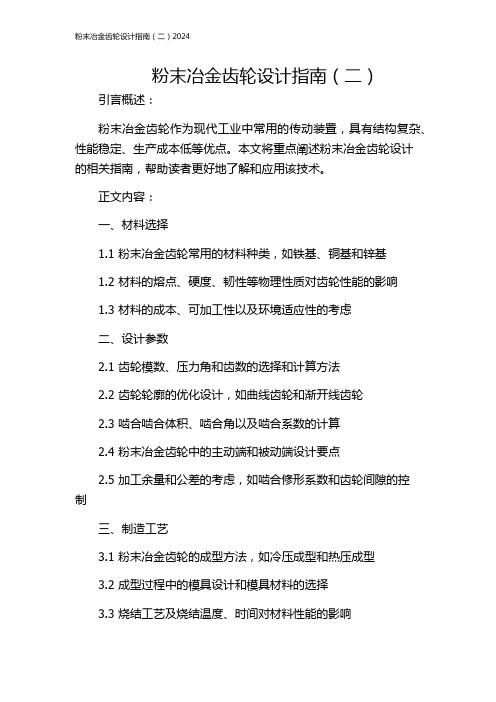
粉末冶金齿轮设计指南(二)引言概述:
粉末冶金齿轮作为现代工业中常用的传动装置,具有结构复杂、性能稳定、生产成本低等优点。本文将重点阐述粉末冶金齿轮设计
的相关指南,帮助读者更好地了解和应用该技术。
正文内容:
一、材料选择
1.1 粉末冶金齿轮常用的材料种类,如铁基、铜基和锌基
1.2 材料的熔点、硬度、韧性等物理性质对齿轮性能的影响
1.3 材料的成本、可加工性以及环境适应性的考虑
二、设计参数
2.1 齿轮模数、压力角和齿数的选择和计算方法
2.2 齿轮轮廓的优化设计,如曲线齿轮和渐开线齿轮
2.3 啮合啮合体积、啮合角以及啮合系数的计算
2.4 粉末冶金齿轮中的主动端和被动端设计要点
2.5 加工余量和公差的考虑,如啮合修形系数和齿轮间隙的控
制
三、制造工艺
3.1 粉末冶金齿轮的成型方法,如冷压成型和热压成型
3.2 成型过程中的模具设计和模具材料的选择
3.3 烧结工艺及烧结温度、时间对材料性能的影响
3.4 粉末冶金齿轮的后续热处理工艺
3.5 表面处理工艺选用及其效果评价
四、性能测试与分析
4.1 粉末冶金齿轮的力学性能测试方法,如强度和韧性测试
4.2 粉末冶金材料的疲劳寿命和耐磨性能测试
4.3 齿轮啮合特性的仿真模拟及分析
4.4 脱落和磨损机理研究
4.5 齿轮传动系统的振动和噪声测试与分析
五、优化和改进
5.1 齿形修正技术和齿尖强化处理的应用
5.2 材料和工艺的改进以提高齿轮的性能
5.3 粉末冶金齿轮设计的新技术趋势
5.4 齿轮设计中的可靠性和寿命评估
5.5 粉末冶金齿轮制造过程的质量控制方法和标准
总结:
粉末冶金在汽车零件上的应用

粉末冶金在汽车零件上的应用
粉末冶金在汽车零件上有着广泛的应用。由于粉末冶金具有节能、节材、节力、环保、近净成形、个性化等多项优点,使得汽车中的许多关键零部件都采用了这种工艺。
在汽车发动机中,粉末冶金零件主要用于气缸、气阀、曲轴、连杆、活塞杆等关键部件的制造。这些零件使用粉末冶金工艺可以一次成型,减少切削加工,节约成本。此外,粉末冶金零件的强度和性能也得到了显著提高,可以满足发动机高强度、高效率的工作需求。
在变速器中,粉末冶金零件主要用于行星齿轮架等部件的制造。通过粉末冶金工艺,可以制造出具有高精度和复杂形状的零件,提高了变速器的传动效率和稳定性。
在底盘系统中,粉末冶金零件可用于制造制动器和离合器等关键部件。粉末冶金零件的高耐磨性和高耐疲劳性能可以显著提高制动器和离合器的使用寿命和可靠性。
此外,粉末冶金还可以用于制造汽车座椅系统中的金属件、门锁系统中的金属件以及车身系统中的一些金属连接件等。
总体而言,粉末冶金技术在汽车零部件制造中发挥了重要作用,不仅提高了零部件的性能和可靠性,还有助于降低汽车的整体制造成本。随着汽车工业的发展和环保要求的提高,粉末冶金技术在汽车零件上的应用前景将更加广阔。
粉末冶金原理-烧结
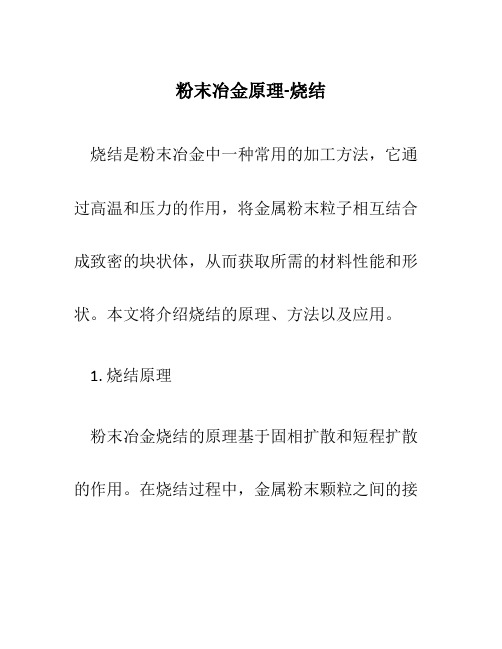
粉末冶金原理-烧结
烧结是粉末冶金中一种常用的加工方法,它通过高温和压力的作用,将金属粉末粒子相互结合成致密的块状体,从而获取所需的材料性能和形状。本文将介绍烧结的原理、方法以及应用。
1. 烧结原理
粉末冶金烧结的原理基于固相扩散和短程扩散的作用。在烧结过程中,金属粉末颗粒之间的接
触面发生原子间的扩散,使得粒子之间形成更强
的结合力,从而实现粉末的聚结。
烧结过程中,首先是金属粉末颗粒之间的接触,原子开始扩散。随着温度的升高,扩散速率也随
之增加。当粉末颗粒之间的接触点扩散到一定程
度后,开始形成颗粒之间的原子键合。键合的形
成使得颗粒间的结合力增强,同时形成新的晶体
结构或弥散态结构。
2. 烧结方法
2.1 传统烧结
传统烧结是指采用外加热源和压力来实现烧结过程。该方法通常包括以下几个步骤:
1.装料:将金属粉末和所需添加剂按照一定
比例混合,并形成一定的装料形状,如坯料或颗粒。
2.预压:将装料放入模具中,并施加一定的
压力,使装料初步固结成形。
3.高温烧结:将装料放入烧结炉中,在一定的温度下暴露一段时间,使装料中的金属粉末
颗粒扩散、晶粒长大并结合。
4.冷却:烧结完成后,将烧结块从炉中取出,经过冷却以稳定材料结构。
5.表面处理:根据需求,对烧结块进行加工、修整和处理,以得到最终所需的形状和表面特性。
2.2 反应烧结
反应烧结是指在烧结过程中引入化学反应,利用固相反应进行金属粉末的结合。相较于传统烧结,反应烧结可以实现更高的烧结温度,加快晶粒生长和结合的速度。
反应烧结的具体步骤包括:
1.装料:将金属粉末和反应剂按照一定比例
- 1、下载文档前请自行甄别文档内容的完整性,平台不提供额外的编辑、内容补充、找答案等附加服务。
- 2、"仅部分预览"的文档,不可在线预览部分如存在完整性等问题,可反馈申请退款(可完整预览的文档不适用该条件!)。
- 3、如文档侵犯您的权益,请联系客服反馈,我们会尽快为您处理(人工客服工作时间:9:00-18:30)。
粉末冶金新技术在烧结齿轮中的应用
烧结齿轮的性能与粉末冶金工艺密切相关,不同工艺和技术路线生产的齿轮,性能差异很大,而粉末冶金技术的发展促进了烧结齿轮性能的提高和尺寸的稳定。文章作者根据其多年从事粉末冶金齿轮生产与科研的实践经验分析和评述了近年来发展起来的温压成形、高速成形、烧结硬化、高温烧结、熔渗和齿轮表面致密化等技术及其在齿轮制造中的应用,采用温压成形、高速成形、烧结硬化、高温烧结或溶渗等新技术配合表面数字化,可望同时实现高密度、低成本和高精度的齿轮生产。
作为传动系统重要零件的齿轮,一般都是通过机械加工法制成的。但是随着汽车工业的发展,对齿轮等零件的要求越来越高,在成本、交货日期和噪音等方面机加工齿轮难以满足要求;而粉末冶金则是项能制造形状复杂零件的技术,可以节料、节能、省工、优质,适合大批量生产,能满足汽车工业对零部件的要求。因此,粉末冶金工业与汽车工业密切相关。在美国,铁基粉末冶金零件的市场有70%以上属于汽车市场;而在国内,远未达到这个比例,据中国机协粉末冶金专业委员会2004年3月的统计,国内粉末冶金行业的汽车市场仅占19%。
对于汽车和其他工业而言,粉末冶金是生产高强度和形状复杂齿轮的有效工艺。目前,通过使用高性能的粉末成形、烧结和特殊的后加工,粉末冶金工艺已经可以生产出密度超过7.5 g/cm3的齿轮。这些技术的使用,已经成功地替代了机加工或其他方法加工的零件。粉末冶金工艺的成功,使机械工程师设计高性能和较低成本的零件成为可能。目前在汽车上使用的齿轮零件有同步器齿毂、离合器齿毂等,随着汽车工业的发展,必将对粉末冶金工业提出更高的要求。本文将从粉末冶金材料工艺和齿轮表面致密化等方面探讨粉末冶金工业的最新进展及其在齿轮生产中的应用,为机械工程师在设计齿轮时提供参考。
齿轮作为重要的传动零件,在汽车上起着关键的作用。齿轮的密度、硬度等与材料的性能及制备工艺息息相关。先进的压形技术提高了粉末压坯的密度,改进了粉末冶金制品的性能;同时,零件的尺寸精度可以获得提高,形状也可以更加复杂。温压技术的致密化主要通过在温压温度下铁粉颗粒的加工硬化速率降低和程度减轻,以及铁粉颗粒塑性变形阻力减小来实现的。此外,在成形过程中的颗粒重新排列,也可以使密度提高D]。目前已经制备出抗拉强度达1 500 MPa的烧结铁基零件。Ford汽车公司已将质量达1.2 kg的温压流体变速涡轮毂用在发动机上。温压工艺的关键在于以较低的成本制造出高性能的铁基粉末冶金零件,为汽车的零部件在性能与成本之间找到一个较佳的结合点。温压的优势在于:压坯密度和烧结密度高,压坯强度高,脱模压力低,弹性后效小。
瑞典开发了高速压制的工艺。这种工艺的开发使高密度和超过5 kg的大型粉末冶金零件的开发成为可能,它使粉末能在20 ms以内被压缩,而且在300 ms内多次压制还可以进一步提高密度。高速压制作为大批量的生产方法可以突破目前粉末冶金的局限性。传统压制成形要求高的成形压力,而成形压力又受到压机吨位的限制,高速压制则不受此限制。基于预合金化和扩散合金化的粉末密度可以达到7.4~7.7g/cm3,这种新型的制造技术最近引入到了粉末冶金行业。高速压制的致密化主要通过由液压控制的冲锤产生的强烈冲击波来实现,冲锤的质量和压制时的速度决定了冲击功的大小和致密化程度。由于采用液压控制,安全性能较高。通过合适的工艺控制,可以避免非轴向的反弹引起压坯的微观缺陷。
烧结硬化是将粉末冶金的烧结与提高材料性能的淬火热处理工序合二为一,以降低成本。烧结硬化工艺可以省去烧结后热处理工序,同时可以获得高强度和高硬度的性能,从而降低生产成本。此外,淬火时会产生高的残余内应力并且使零件发生变形,给控制零件尺寸公差带来困难。烧结硬化工艺,由于烧结后的冷却速度远低于淬火的冷却速度,因而可以使变形减少到最小。因此烧结硬化工艺适用于难以处理的大型以及形状复杂的零件。烧结硬化钢一般用来制造中高密度零件。一般情况下,烧结硬化铁粉的主要合金元素有钼、锰、铬、
铜和镍等。含有这些合金元素的材料具有足够高的淬透性,在烧结冷却期间能够淬硬。烧结硬化后合金金相组织多为马氏体,此外还有少量的细珠光体、贝氏体和残余奥氏体;根据烧结温度和时间的不同,可能还有少量的富镍区。根据烧结的实际条件和零件的具体要求,适当调配化学成分,在冷却后可以得到要求的硬度和性能。目前已经有大量的烧结硬化齿轮开始应用于汽车等传动机构上。与传统的工艺相比,它降低了生产成本,但是没有降低任何使用性能。这些齿轮的尺寸精度高,噪音低,强度高,耐磨性和耐腐蚀好。宁波东睦(NBTM)公司的齿轮(见图3),通过烧结硬化,密度大于7.0 g/cm3,经过回火处理后硬度大于HRC40。与传统方法相比成本降低1O%,且减小了淬火变形的危险。
高温烧结是提高强度的一项重要措施。通过高温烧结,可以使一部分氧化物还原、提高原子的扩散速率和增加成分均匀性,可以使孔隙充分球化和孔隙间距更大(见图4),适合于新型粉末冶金材料例如高速钢、不锈钢和高温合金等。这样,可提高零件的密度、机械性能、轴向/旋转弯曲疲劳强度、耐蚀性和物理性能。
熔渗是在烧结过程中将其他材料(对于铁基烧结件而言主要是铜)熔化并在毛细管和重力的作用下渗入烧结坯内,以提高零件的密度和性能。一般情况下,原材料费用较高,熔渗时铜向骨架基体中扩散和生成大量液相,尺寸变化较大。
粉末冶金工艺生产的齿轮具有良好的力学性能、尺寸精度和表面粗糙度,且适用于大批量生产,因而具有良好的性价比,这是烧结齿轮能赢得汽车工业认可的重要原因。由于粉末冶金传统工艺技术的限制,烧结齿轮密度较低,影响了齿轮的性能。温压成形、高速成形、烧结硬化、高温烧结、熔渗、HVC粉末成形和齿轮表面致密化等技术在烧结齿轮中的应用解决了密度较低、尺寸精度和力学性能达不到规定要求的问题。从目前的技术发展来看,烧结齿轮要达到全致密不存在技术障碍,尺寸变化也完全可以达到可控的程度。但是成本也是考虑烧结齿轮的一个重要因素。生产烧结齿轮真正困难的是同时达到高密度、低成本和高精度。