The stress corrosion cracking II
高考英语专项复习《阅读理解议论文》高考真题汇总

高考英语专项复习《阅读理解议论文》高考真题汇总2023年高考真题Passage 1【2023年全国乙卷】If you want to tell the history of the whole world, a history that does not privilege one part of humanity, you cannot do it through texts alone, because only some of the world has ever had texts, while most of the world, for most of the time, has not. Writing is one of humanity’s later achievements, and until fairly recently even many literate (有文字的) societies recorded their concerns not only in writing but in things.Ideally a history would bring together texts and objects, and some chapters of this book are able to do just that, but in many cases we simply can’t. The clearest example of this between literate and non-literate history is perhaps the first conflict, at Botany Bay, between Captain Cook’s voyage and the Australian Aboriginals. From the English side, we have scientific reports and the captain’s record of that terrible day. From the Australian side, we have only a wooden shield (盾) dropped by a man in flight after his first experience of gunshot. If we want to reconstruct what was actually going on that day, the shield must be questioned and interpreted as deeply and strictly as the written reports.In addition to the problem of miscomprehension from both sides, there are victories accidentally or deliberately twisted, especially when only the victors know how to write. Those who are on the losing side often have only their things to tell their stories. The Caribbean Taino, the Australian Aboriginals, the African people of Benin and the Incas, all of whom appear in this book, can speak to us now of their past achievements most powerfully through the objects they made: a history told through things gives them back a voice. When we consider contact (联系) between literate and non-literate societies such as these, all our first-hand accounts are necessarily twisted, only one half of a dialogue. If we are to find the other half of that conversation, we have to read not just the texts, but the objects.12. What is the first paragraph mainly about?A. How past events should be presented.B. What humanity is concerned about.C. Whether facts speak louder than words.D. Why written language is reliable.13. What does the author indicate by mentioning Captain Cook in paragraph 2?A. His report was scientific.B. He represented the local people.C. He ruled over Botany Bay.D. His record was one-sided.14. What does the underlined word “conversation” in paragraph 3 refer to?A. Problem.B. History.C. Voice.D. Society.15. Which of the following books is the text most likely selected from?A. How Maps Tell Stories of the WorldB. A Short History of AustraliaC. A History of the World in 100 ObjectsD. How Art Works Tell Stories2023年名校模拟题Passage 1(2023·山东·山东省实验中学校考二模)Danone Portugal introduced a new yogurt named Juntos. For every pack of yogurt that a person bought, he would donate yogurt to a family in need. Danone had done its research. Increasingly, people say they want to buy from brands that give them a sense of purpose. Surely a yogurt that helped the needy would be appealing. But Juntos was a failure. Despite sinking millions into a marketing campaign, Danone pulled Juntos from the market only months after it was launched. Now the same product is simply marketed as a tasty yogurt.What happened? To find the reason behind Juntos’ failure, Lawrence Williams and his colleagues did an experiment where they showed people some products and asked these people to pick one option. They reminded some to focus on the “purposeful and valuable” aspect while others were told to “enjoy themselves” and focus on “delight and pleasure.” They found that participants who prioritized meaning preferred the less expensive product when compared with people who put pleasure in the first place.So why were meaning-seekers cheaping out? Lawrence Williams asked participants to explain their decision-making to find out. He learned that meaning-oriented people were not thinking about how the product they might buy could bring meaning to their lives. Instead, they were occupied with what else they could do with their money.I am all for people making wise and strategic financial choices. But cheap products can create many problems. Inexpensive options often do not last as long as the higher-end ones. As a result, we shop more often, which is ultimately worse for our wallets. Plus, that spending pattern can do a greater damage to the environment. Thanks in part to fast fashion, people buy 60 percent more clothing today than they did 15 years ago. The fashion industry alone emits more greenhouse gases than international flights and maritime (海洋的) shipping combined.So before you dive into your wallet for some deals, try not to fix only on what you are spending or saving. Think carefully about what you are buying, too.1.What is the main reason for the failure of Juntos?A.It ignored marketing strategies.B.It priced itself relatively high.C.It lacked a particularly good taste.D.It focused on delight and pleasure. 2.What can be inferred about meaning seekers?A.They frequent high-end stores.B.They think products extend their lives. C.They hesitate to make decisions.D.They make more purchases with money. 3.How is Paragraph 4 mainly developed?A.By giving some examples.B.By listing numbers and data.C.By explaining reasons.D.By making some comparisons.4.Which is the most suitable title for the text?A.Innovation: a Product’s Life B.To Buy or not to BuyC.Meaning seekers or Quality-pursuers D.Fast Fashion: a Hit to Your WalletPassage 2(2023·山东淄博·统考三模)There is no universally accepted age that is considered old among or within societies. Often disagreements exist as to what age a society may consider old and what members in that society of that age and older may consider old. Moreover, biologists are not in agreement about the existence of an internal biological cause foraging.In general the social status of an age group is related to its effective influence in its society, which is associated with that group’s function in productivity. In agricultural societies the elderly have a status of respectability. Their life experiences and knowledge are regarded as valuable, especially in preliterate (尚无文字的) societies where knowledge is orally transmitted. The range of activities in these societies allows the elderly to continue to be productive members of their communities.In industrialized nations, although in certain fields old age is still considered significant, particularly in the political field, older people are increasingly being forced into retirement before their productive years are over, causing problems in their psychological adaptations to old age. Retirement is not regarded unfavorably in all instances, but its economic limitations tend to further remove older people from the range of influence and raise problems in the extended use of leisure time and housing. As a consequence, financial preparation for retirement has become an increased concern for individuals and society.Familial relationships tend to be the focus of the elderly’s attention. However, the tendency for young people in industrialized countries to be highly mobile has forced older people to decide whether to move to keep up with their families or to remain in neighborhoods which also change, altering their familiar patterns of activity. Although most older people do live within an hour from their closest child, industrialized societies are faced with formulating programs to accommodate increasing numbers of older people who function independently of their families. Adult education programs are beginning to close the generation gap; however, as each successive generation reaches old age, bringing with it its particular tendencies and preferences, new problems arise requiring new social accommodations.5.What counts for the elderly in agricultural societies?A.Their status of respectability.B.Their value in productivity.C.Their rich knowledge in education.D.Their extraordinary ability to work. 6.What can we learn about the elderly’s retirement from Paragraph 3?A.It has faded the elderly worries.B.It means the end of productive ability.C.It is considered beneficial in all distances.D.It influences the elderly psychologically and financially.7.What does the underlined word “formulating” in Paragraph 4 mean?A.Planning.B.Changing.C.Extending.D.Canceling.8.Where is this text probably taken from?A.A personal journal.B.A science research.C.A social issue review.D.A community brochure.Passage 3(2023·河南郑州·统考模拟预测)Some experts have been concerned lately about robots leaving humans behind, taking our jobs and possibly a lot more, as in sci-fi films. Christ of Koch, a famous neuroscientist (神经学家), has suggested a novel method. To keep up with the machines, we should increase our brainpower with brain implants (植人物).Koch notes that brain implants are already helping the paralyzed or people unable to move control computers and robots, and they are being explored for the treatment of mental disorders. Future implants could help us download huge amounts of information instantly, he says, so we can learn “novel skills and facts without even trying”. “Another exciting aspect,” Koch says, “is combining two or more brains into a single conscious mind by direct neuron-to-neuron links.” Koch calls for a “crash program” in brain technologies to make us smarter.But Koch ignores the obvious facts that bad persons can hack (侵入) into our smartphones and laptops. What if hackers could attack our brains? They may be able to spy on, change or control the memories of people implanted with brain devices. What’s more, we are nowhere close to being able to strengthen the brain in the manner that Koch imagines. Scientists have been experimenting with neuro-technologies for mental illness for more than half a century, and they have little to show for it.Koch genuinely feared that science, far from addressing our problems, might exacerbate them. The use of robots in the workshop, for example, could cause mass unemployment. Do we just count the immediate job losses—without measuring any other potential positive effect on the economy? Despite losing some jobs to robots in the short term, the increase in productivity will help our overall economy grow faster, which, in turn, will create more, higher quality jobs than we had before.The future is not as scary as we think. Perhaps we’ve got serious problems on our hands, and we have a lot of work to do to settle them. Brain implants are not the answer.9.What leads to Koch’s optimism about future brain implants?A.The great advance in AI research.B.Their application in medical fields.C.The breakthrough in surgical techniques.D.Their easy adaptation to the human body.10.How does the author feel about Koch’s “crash program” in brain technologies?A.Disapproving.B.Unconcerned.C.Favorable.D.Excited. 11.What does the underlined word “exacerbate” in paragraph 4 mean?A.Avoid.B.Worsen.C.Reduce.D.Answer. 12.What’s the best title for the text?A.Are Brain Implants at Risk of Hacker Attack?B.Will Robots Take the Place of Humans in Future?C.Will Brain Implants Let the Disabled Live Normally?D.Do We Need Brain Implants to Keep Up with Robots?Passage 4(2023·山西·校联考模拟预测)What do you want from life? Perhaps you want to spend more time with your family, or get a more secure job, or improve your health. But why do you want those things? Chances are that your answer will come down to one thing: Happiness.Yet there is some evidence that too much pursuit of happiness is associated with a greater risk of depression. Modern conceptions of happiness are primarily practical, focusing on what we might call the techniques of happiness. The concern is not what happiness is, but instead on how to get it.But maximizing pleasure isn’t the only option. Every human life, even the most fortunate, is filled with pain. Painful loss, painful disappointments, the physical pain of injury or sickness, and the mental pain of long-suffering boredom, loneliness, or sadness. Pain is an unavoidable consequence of being alive. All the good things in life involve suffering. Writing a novel, running a marathon, or giving birth all cause suffering in pursuit of the final, joyous result.There are other factors as well. In the eyes of Aristotle, we get happiness by exercising our uniquely human capabilities to think and reason. But thinking and reasoning are as much social activities as they are individual. Happiness requires others; it is not an emotional state so much as it is the excellence of the relations we cultivate with other people.But even that cannot guarantee happiness. Aristotle recognised that our happiness is hostage (人质)to fortune. Events beyond any individual’s control—war, poverty, and global pandemics—will often make happiness impossible. Happiness is not a mental state that can be permanently won, but instead it’s a practice which we hone(磨练), imperfectly, in circumstances only partly of our making.Recognizing this will not secure a good life, but it will avoid the illusory(虚幻的)hope of permanent contentment. No life worth living should meet the only standard. Instead, aim with Aristotle to embrace those faults and to flower in spite of them.13.Where can you find negative effects of focusing too much on “happiness”?A.In paragraph 2.B.In paragraph 3.C.In paragraph 4.D.In paragraph 5.14.How does the author prove that pain is an unavoidable result of being alive?A.By making comparisons.B.By analyzing causes.C.By giving examples.D.By telling stories.15.What is Aristotle’s view on happiness?A.Happiness is a stable emotional state.B.Good personal relationships lead to happiness.C.Taking part in social activities guarantees happiness.D.Happiness promotes independent thinking and reasoning.16.What is the text mainly about?A.Happiness is what humans pursue forever.B.Happiness lies in the process of pursuing it.C.Our pursuit of happiness may be imperfect.D.Depression and happiness are equally important.Passage 5(2022·广东佛山·统考模拟预测)One of the oldest metaphors (隐喻) for human interaction with technology is the relationship of master and slave. Aristotle imagined that technology could replace slavery if machine became automated. Marx and Engels saw things differently. “Masses of laborers are daily and hourly enslaved by the machine,” they wrote in the Communist Manifesto.Today, computers often play both roles. Nicholas Carr, in his new book The Glass Cage: Automation and Us, takes a stand on whether such technology imprisons or liberates its users. We are increasingly engaged, he argues, but the invisibility of our high-tech traps gives us the ‘image of freedom’. He describes doctors who rely so much on decision-assistance software that they overlook signals that are not obvious from patients.All of this has obvious implications for the use of technology in classrooms: When do technologies free students to think about more interesting and complex questions, and when do they destroy the very cognitive (认知) capacities that they are meant to improve? The effect of spell check and AutoCorrect software is an example. Psychologists have found the act of forming a word in your mind strengthens your capacity to remember it. When a computer automatically corrects a spelling mistake, we’re no longer forced to form the correct spelling in our minds.This might not seem very important. The process of word formation is not just supplementing spelling skills, it’s also destroying students. When students find themselves without automated spelling assistance, they don’t face the prospect of freezing to death, as the Inuits did when their GPS malfunctioned, but they’re more likely to make errors. This creates a vicious cycle: The more we use the technology, the more we need to use it in all circumstances. Suddenly, our position as masters of technology starts to seem more insecure.17.What did Marx and Engels think of the machine?A.It did the boring daily work for people.B.It failed to free people from being enslaved.C.It gave people more time to enjoy themselves.D.It was the result of the development of technology.18.Which of the following is Nicholas Carr most likely to agree with?A.Technology is a guarantee of freedom.B.Doctors should stay away from technology.C.Too much involvement with technology may be risky.D.Some decision-assistance software needs improving.19.What does the underlined word “this” in paragraph4 refer to?A.Students being unable to spell words correctly.B.Spell check helping students remember more words.C.Students depending too much on spelling software.D.Spellcheck destroying students’ cognitive capacities.20.Which of the following might be the best title of the passage?A.Is technology making people stupid or not?B.Which areas are most affected by technology?C.Are people satisfied with the advancement of technology?D.Why shouldn’t technology be employed in the classroom?Passage 6(2022·湖北·校联考模拟预测)When I stepped into the Samcheong Park Library in Seoul, I saw the future. The simple building had a nice selection of books and a cafe where readers could enjoy coffee while gazing at the leaves outside. It was specifically designed without any latest technology.“What’s so innovative about that?” a librarian in Toronto asked when I showed her pictures. I Innovation to her meant digital technology, like 3D printers. “Why couldn’t they both be innovative?” I asked.We are constantly told that innovation is the most important force in our economy, without which we would be left behind. But that fear of missing out has led us to fall into the false trappings of innovation over truly innovative ideas that may be simpler and more effective. This mindset implies that if you just buy the new thing, you have innovated! Each year, businesses and individuals run around like broken toy robots, trying to figure out their strategy for the latest buzzword equipment.At best, this is a waste of resources. Devices are bought, used and abandoned, as the technology’s capabilities fall short of its promise. But at its worst, this approach can truly cause damage. Schools cut field trips to purchase tablets with few proven benefits. Companies thatapplied AI into hiring have actually strengthened gender and racial prejudices.True innovation isn’t just some magic devices. It is a continuing process of reflection and reassessment, which often means adopting “old” ideas and tools in a new context, or even returning to methods that worked in the past. Adjusted properly, these rearview (后视的) innovations have proved as transformative as novel technologies.Look no farther than the streets of New York, which have been redesigned recently to accommodate cyclists with car-free zones. The idea isn’t new. It was created half a century ago, with the aim of bringing cities back to their residents. And while e-reader sales have been exploding, Penguin just announced it would publish tiny printed books, an ideal solution for a market demanding both convenience and physicality.21.How does the author like about the Samcheong Park Library in Seoul? A.Unexceptional.B.Boring.C.Refreshing.D.Old-fashioned.22.What’s the main idea of Paragraph 3?A.Innovation is important for the growth of economy.B.The public has misread the meaning of innovation.C.The true meaning of innovation is to buy new things.D.Truly innovative ideas shouldn’t be simple and effective.23.What does the writer agree with about innovation?A.Wasting resources are a must for innovation.B.Magic devices encourage innovation.C.Innovation should be human-centered.D.The power of technology is undervalued.24.What is the writing purpose of the text?A.To convince people of the true meaning of innovation.B.To show that future lies in returning to the past.C.To introduce some best ideas about innovation.D.To stress the important role innovation plays in economy.Passage 7(2022·湖北·校联考模拟预测)A measure in the House’s $ 2 trillion economic bill would require states to cut greenhouse gas emissions (排放) promising rewards for transportation departments that post reductions and “consequences” for those that don’t.Peter A.DeFazio, chairman of the Transportation Committee, said the proposal is designed to push states to act. “We’re going to give them very large motivation to actually make those meaningful targets and deliver on those targets,” he said. According to the proposal, states that cut emissions could get a $ 1 billion pot of money and potentially receive other bonus funding fromthe federal government. The bill doesn’t spell out potential consequences for not reducing emissions, leaving the decision to national transportation officials. Experts say they could include barriers to accessing highly prized grant funds (拨款).Much of the attention on cutting emissions from the transport industry-the nation’s largest emitter of greenhouse gases-has focused on the adoption of electric vehicles by putting money in charging factories and supporting battery-powered cars. The new measure sides with environmental advocates who argue the nation can’t battle a changing climate without changing how Americans move around. Environmentalists say the nation’s changing to electric vehicles probably won’t happen quickly enough to limit temperature rises unless Americans can be convinced to drive less, and that would mean building new networks focused on walking, cycling and transit (运输).Opposition to the emission measure is deep-seated. The heads of five western state transportation departments wrote a letter to Capitol’s committee last month saying the proposal would harm rural areas because options such as heavy-traffic pricing are not well-suited to places which are populated in few people, and it doesn’t make sense to target those state agencies when there are multiple reasons that influence emissions, including fuel economy standards for cars and local decisions about where to build stores and homes.Kevin DeGood, a transportation researcher, said basic construction shape how people can get around. “It is funny that the state transportation departments suggest in the letter that they do not deeply influence greenhouse gas emissions from the transportation industry,” he said.25.How does the government provide motivation?A.By praising.B.By punishing.C.By financing.D.By restricting.26.What is an intended result of the bill?A.Greatly changed climate.B.More convenient stores.C.Stable fuel economy standards.D.Eco-friendly transport system.27.Why did some states mention heavy-traffic pricing?A.To oppose the emission measure.B.To introduce solutions to emission.C.To call for attention to rural areas.D.To list several reasons for emission. 28.What’s Kevin’s attitude towards the letter in paragraph 4?A.Supportive.B.Disapproving.C.Shocked.D.Confident.Passage 8(2023·四川成都·成都七中校考模拟预测)Thanks to in-depth reporting by The Wall Street Journal, we now know that Facebook has long been aware its product Instagram has harmful effects on the mental health of many adolescent users. Young girls, in particular, struggle withtheir body image thanks to a constant stream of photos and videos showing beautiful bodies that users don’t think they can attain.While the information the journal covered is essential and instructive, it does not tell the whole story. Deep down, this is not an Instagram problem; it’s a people problem. Understanding that distinction can make the difference between a failed attempt to contain a teen’s interest in an addictive app and successfully addressing the underlying problem leading to mental distress caused by Instagram.Critics were quick to shame Facebook for sitting on the data and not releasing it to researchers or academics who asked for it. Others criticize the social media giant for not using the research to create a safer experience for its teen users. The anger, while understandable, is misplaced.While I’m reluctant to defend Facebook, I’m not sure it’s reasonable to blame the company for refusing to give data that would hurt its business. Have you ever binge-watched a Netflix series? I assure you it wasn’t a healthy endeavor. You were inactive, likely did nothing productive, mindlessly snacked and didn’t go outside for fresh air. It is an objectively harmful use of time to stare at a TV or laptop for a full weekend. Should we respond by shaming Netflix for not alerting us to how damaging an addictive product can be?While it’s reasonable to say Instagram makes esteem issues worse, it is almost impossible to believe it causes them in the first place. You create your own experiences on social media. For the most part, you choose which accounts to follow and engage. If you’re already vulnerable to insecurities and self-sabotage (自损) — as many teens are — you will find accounts to obsess over. And this isn’t a new phenomenon.Before social media, there were similar issues fueling self-esteem issues. Whether the target be magazines, movies or television shows depicting difficult-to-attain bodies, there has been a relatively steady chorus of experts noting the damage new media could cause young viewers.Self-esteem issues have an underlying cause — one that’s independent of social media use. Instagram merely enhances those feelings because it provides infinitely more access to triggers than older forms of media. It’s more worthwhile to address those underlying factors rather than to attack Facebook.29.What does the author think of the criticisms against Instagram?A.They address the mental pain caused by Instagram.B.They are not directed at the fundamental problem.C.They are only based on the data released by Facebook.D.They are effective in changing teens’ interest in addictive apps.30.Why is Netflix mentioned?A.To defend why Facebook is to blame.B.To show Netflix does more harm to teens.C.To suggest the critics’ remarks are not to the point.D.To compare the criticisms against it and Facebook.31.Why is the Instagram problem essentially a “people problem”?A.People have a tendency to feel insecure online.B.People are keen on making up their self-profile.C.It is human nature to get addicted to social media.D.Users decide on their experiences on social media.32.What is the passage mainly about?A.The fierce criticism faced by Facebook.B.The harmful impact of Instagram on teenagers.C.The alarming online habits of teenagers worldwide.D.The root of mental sufferings caused by Instagram.Passage 9(2023·广东韶关·统考二模)Many of us seem to have lives that follow a certain path. From kindergarten all the way to marriage, every stage of our lives seems to be preset. Although this works well for many people, according to British motivational philosopher Jay Shetty, there is no “right” schedule to live our lives by.A few months ago, a video of Shetty’s speech Before You Feel Pressure went viral on the Internet across the world. In the video, he sends an important message that we should think “outside of the path” and have the courage to follow our hearts. Shetty adds that, we don’t have to get stressed and put ourselves in a race with our peers or judge our lives based on others. Everything in life happens according to our time, our clocks.In his inspiring speech, Shetty points out that UK author J. K. Rowling got her famous Harry Potter series published at age 32, after being turned down by 12 publishers. Shetty also mentions that Chinese businessman Jack Ma didn’t even start the Alibaba Group until he was 35 and US actor Morgan Freeman didn’t get his big break until he was 52 years old.We shouldn’t let anyone rush us. As Albert Einstein once said, “Not everything that counts can be counted, and not everything that’s counted truly counts. ”The key to staying on our own tracks is to be patient and embrace our own passions. In Australian nurse Bronnie Ware’s best-selling book, she recorded the regrets of her dying patients, and the top one on the list was, “I wish l had the courage to live a life true to myself, not the one others expected of me.” Indeed, we are all unique in our personalities and gifts, and there’s no perfect fit for all. We should listen to our inner voices and unlearn what the world has taught us.“It is important to allow people to go back to being self-aware of their own interests, needs and concerns”, Shetty told National Geographic. “It’s disconnecting from what ‘makes sense’ to what actually moves you and what makes sense internally.”33.What is many people’s life path like according to Paragraph 1?。
基于有限元法的V型缺口平板应力集中系数研究
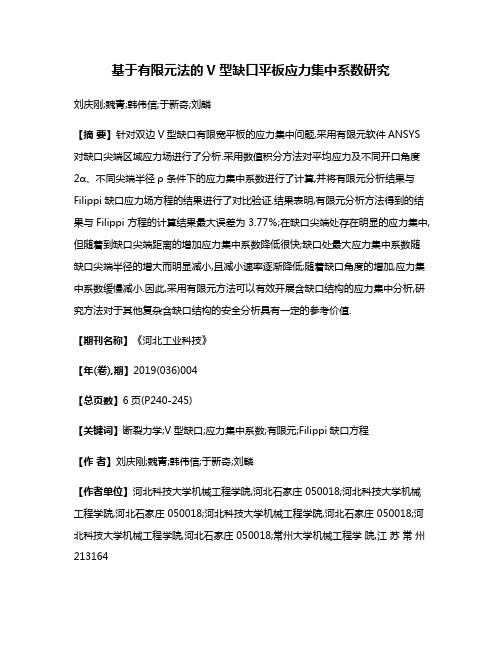
基于有限元法的V型缺口平板应力集中系数研究刘庆刚;魏青;韩伟信;于新奇;刘麟【摘要】针对双边V型缺口有限宽平板的应力集中问题,采用有限元软件ANSYS 对缺口尖端区域应力场进行了分析.采用数值积分方法对平均应力及不同开口角度2α、不同尖端半径ρ 条件下的应力集中系数进行了计算,并将有限元分析结果与Filippi缺口应力场方程的结果进行了对比验证.结果表明,有限元分析方法得到的结果与Filippi方程的计算结果最大误差为3.77%;在缺口尖端处存在明显的应力集中,但随着到缺口尖端距离的增加应力集中系数降低很快;缺口处最大应力集中系数随缺口尖端半径的增大而明显减小,且减小速率逐渐降低;随着缺口角度的增加,应力集中系数缓慢减小.因此,采用有限元方法可以有效开展含缺口结构的应力集中分析,研究方法对于其他复杂含缺口结构的安全分析具有一定的参考价值.【期刊名称】《河北工业科技》【年(卷),期】2019(036)004【总页数】6页(P240-245)【关键词】断裂力学;V型缺口;应力集中系数;有限元;Filippi缺口方程【作者】刘庆刚;魏青;韩伟信;于新奇;刘麟【作者单位】河北科技大学机械工程学院,河北石家庄 050018;河北科技大学机械工程学院,河北石家庄 050018;河北科技大学机械工程学院,河北石家庄 050018;河北科技大学机械工程学院,河北石家庄 050018;常州大学机械工程学院,江苏常州213164【正文语种】中文【中图分类】TH114缺口会引起应力集中,因此缺口部位是各类航空器、机械装置、建筑结构中的薄弱环节,其强度问题需要予以格外重视。
因此,为了保障含缺口结构的安全性,自20世纪初期含缺口结构的应力、应变问题得到固体力学领域研究人员的重视,并逐渐形成了“缺口力学”这一固体力学的分支。
在缺口力学领域,国内外学者以V型缺口为研究对象做了大量研究。
早期,研究人员的研究工作主要集中在含缺口结构应力场的解析解方面。
酸性硫酸根离子介质中奥氏体不锈钢的应力腐蚀行为研究
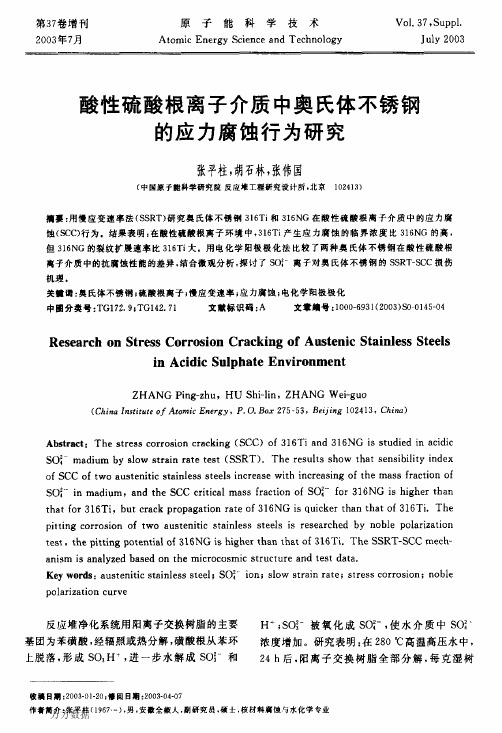
~n·自mfH#∞m…×…“-## ∞H”*#~#mHn4#n*E#,“口*
“#
"≈SSRT#%∞}日口#E¨#&t H×#%#H∞MB镕#(III&^#*m^ 一《*¥Fm*≈%^#)W&T№。&M M∞mⅡ《WT rM≈目Ⅵ』|m F№#ⅫB 镕#m"¨一m*Ⅱ,*“mnWⅧ#8Ⅲm ,一目』。』E+¨¨4∞一rⅫE☆*∞i,j。 B々#H*#№^☆*∞t。,。自』。&o~1 n■自☆n,&mⅨc№镕#&M^m“m ^“#M【l**自…8&十目自自&月Ⅱn №”%¨JE(¨8 do于{#日‰Lm{r
2试验镕}
I)十目s(×镕***F 3】6¨n SSRI
w(s(X,~I'∞5口o…000 R& &十I#自*{sKMl**n J。。℃pH~
52
g*n
1F’ )№I 6 nFiKRm#洲*fW]}自∞☆*目 自& 1|H盯nⅡ *★*Ⅻ3lg∽(目t
Aloo℃F、},H自3 7∞(ⅫW)~19 5口500
H+;s0;一被氧化成sO:一,使水介质中SO;‘ 浓度增加。研究表明:在280℃高温高压水中, 24 h后.阳离子交换树脂全部分解,每克湿树
收藕日期:2003—01-20}惨回日期:2003—04-07
作者筒介 万:方张平数柱据(1967一).男,安徽全椒人,副研究员.硕士.核材料腐蚀与水化学专业
ZHANG Ping-zhu,HU Shi—lin.ZHANG Wei—guo (ChinaInstitute ofAtomicEnergy。P.oBox 275—53,Beijing 102413.China)
Abstract:The stress corrosion cracking(SCC)of 316Ti and 316NG is studied in acidic
腐蚀及防蚀理论

M2+水化及不动态皮膜破坏
腐蚀初期阶段 Fe → Fe2+ + eO2 + 2H2O + 4e- → 4OH-
← 隙间腐蚀 的 初 期 阶段
Material : Nickel alloy (Hastelloy C4) Part : Bolts and nuts of agitator (1year)
M(n+x)+ +
☞电话电池(Electrochemical Cell)內的电子消磨反 应 ☞代表性的有卤族元素
Xn- + x e还原反应式 + Cl2 3 e2 Cl+
x
eFe2+
X(n+x)
2 e-
※ 氧化,还原反应通常会同时发生,两级电荷形成均衡 (氧化) 2Na+ + 2 e2Na
(还原)
2Cl-
局部腐蚀(Localized Corrosion)
④ 应力腐蚀开裂 (Stress Corrosion Cracking)
⑤ 氢腐蚀 (Hydrogen Attack) ⑥ 腐蚀疲劳(Corrosion Fatigue) ⑦ 导航仪腐蚀 (Cavitations Corrosion) ⑧ 电偶腐蚀 (Galvanic Corrosion)
4H2O : 酸化第二鐵
水
腐蚀环境的特性
环境
腐蚀程度
比较
海岸地方
都市环境 山间地方
100 (基准)
20 ~ 30 10 ~ 20
盐分
产业公害物质
※ 上记表是一般的统计资料或都市环境(包含工业地带)时,酸性雨等的影响腐蚀程 度更为严重的增加的趋势
海洋环境的主要腐蚀因子
ED2013-3112-ACCELERATED STRESS CORROSION CRACK INITIATION OF ALLOY 690 AND

ACCELERATED STRESS CORROSION CRACK INITIATION OF ALLOY 690 AND ALLOY 600 IN HIGH TEMPERATURE HYDROGENATED WATERTyler Moss, Gary S. WasUniversity of Michigan; 2355 Bonisteel Blvd.; Ann Arbor, MI 48109-1204ABSTRACTThe objective of this study is to quantitatively determine the susceptibility to crack initiation of Alloy 690. Due to the long incubation time of crack initiation in Alloy 690, accelerated testing was carried out by increasing the test temperature. Accelerated cracking tests are typically conducted at temperatures up to 360°C, and any further increase of the temperature would mean entering the supercritical water phase. However, it is unclear if the mechanism for cracking in supercritical water is the same as in subcritical water. If the mechanism of cracking is the same in supercritical and subcritical water, then the activation energy for cracking in CERT testing should also be the same. To determine if there is a consistent mechanism across the critical point, alloys 690 and 600 were subjected to interrupted constant extension rate tensile tests between 320°C and 450°C and at strain rates of 3x10-7 s-1 and 5x10-8 s-1. All experiments were conducted at constant electrochemical potential from the Ni/NiO boundary in the NiO stable regime by controlling the overpressure of hydrogen on the vessel feed water. Cracking susceptibility was quantified by measuring the crack length, density, crack length per unit area, and depth on the gauge surface of tensile samples. Alloy 600 was first used to confirm that there was not a mechanism change for crack initiation by straining tensile bars at a strain rate of 3x10-7 s-1, and it was found that the activation energy for cracking in supercritical and subcritical water was comparable at 147±14 kJ/mol and 132±16 kJ/mol respectively. In order to induce measureable intergranular cracking of Alloy 690, tensile bars were subjected to a room temperature pre-strain of 20% and tested at a slower strain rate of 5x10-8 s-1 to a strain of 7% in water between 320 and 450°C. Using this method, crack initiation was measured with an activation energy of 85±17 kJ/mol on Alloy 690 without a change in the cracking behavior across the critical temperature.Keywords: Nickel Alloys, Crack Initiation, Supercritical Water, Alloy 600, Alloy 690INTRODUCTIONAlloy 600 was originally used in pressurized water reactors (PWRs) due to its mechanical properties, fatigue resistance, and resistance to chloride-induced stress corrosion cracking (SCC). However, over the last 30 years intergranular SCC has presented itself as a problem in many pressure boundary components made of Alloy 600. Alloy 690 has been utilized in many of the replacement components and has been shown to be highly resistant to stress corrosion cracking, especially crack initiation, in laboratory and operating reactor settings. Its resistance is high enough that in temperature--accelerated experiments up to 360°C very little SCC initiation has been observed [1, 2, 3]. Assessing crack initiation susceptibility requires additional accelerating factors such as lowering the strain rate during constant extension rate tensile (CERT) testing, imposing a pre-strain, and increasing the temperature into the supercritical regime. While crack initiation of Alloy 690 has been difficult to study due to very long initiation times, there have been a few studies using accelerated testing methods. Simultaneous exposures of U-bend samples of each alloy have been conducted by many researchers without successfully initiating cracks in Alloy 690 [1, 2, 3]. Using deaerated pure supercritical water as an accelerating environment, Teysseyre and Was were able to initiate intergranular cracks on Alloy 690 between 360 and 500°C [4]. They found that the activation energy for crack initiation of Alloy 690 was 87 kJ/mol by measuring the depth of cracking over thetemperature range. However, the cracking resistance of Alloy 690 prevented study of lower temperatures in subcritical water.The purpose of this study is to further assess the susceptibility to SCC initiation of Alloy 690 and Alloy 600. Experiments were conducted in both subcritical and supercritical water to accelerate the cracking behavior and to determine the temperature relationship for crack initiation of Alloys 690 and 600. The environment for all of the experiments was controlled to be in the NiO stable regime in close proximity to the Ni/NiO boundary. This required mapping of the location of the Ni/NiO boundary in supercritical water. Crack initiation of Alloy 690 was further accelerated by conducting CERT experiments at a slow strain rate on samples that had a prior 20% tensile strain imposed.EXPERIMENTAL PROCEDUREMaterialsTwo nickel-based alloys, 690 and 600, were used for this study. Both alloys are in the mill annealed condition. The Alloy 690 heat had an average grain size of 40 μm with discontinuous M23C6carbides precipitated along the grain boundaries. The Alloy 600 heat had an average grain size of 60 μm with no carbides along the grain boundaries. Both alloys contained titanium nitride particles ranging from 5-10 μm in diameter dispersed in the matrix. The chemical compositions of both alloys are presented in Table I.Samples were machined into SCC bars that are 38 mm long with threaded ends with the tensile axis oriented in the rolling direction. The gage section has a diameter of 2 mm and a length of 20.5 mm. The machined samples were mechanically polished using standard metallographic techniques and then electropolished in perchloric acid (10% HClO4) and methanol (CH3OH) solution maintained at -30°C, applying 30 V for 30 s to obtain a mirror finish. Some of the Alloy 690 samples were pre-strained at room temperature at a strain rate of 1x10-5 s-1 to 20% strain. To determine the oxidation of nickel in the test environment, 1 cm by 1.5 cm strips of 99.99% pure nickel foil were also used in the electropolished condition.Supercritical Water SystemsCERT testing and exposures were performed in the multi-specimen supercritical water (MSCW) and single-specimen supercritical water (SSCW) systems in the high temperature corrosion laboratory at the University of Michigan. The MSCW has a 4 L water capacity and can hold up to four CERT specimens and eight corrosion coupons. The setup has a flowing water loop with external water columns that can accept gas additions. The loop consists of the vessel which is made of Inconel 625, two high-pressure liquid chromatography pumps, a set of two pre-heaters, and a back pressure regulator. The water is pressurized by the pumps and heated to supercritical temperatures before it enters the vessel. From the vessel the water flows through a tube in tube heat exchanger and is chilled before reaching the BPR. The water then flows through several sensors that measure its conductivity and dissolved oxygen content. Finally it is fed through an ion exchanger before entering the main column again. The amount of dissolved hydrogen is controlled by using an overpressure of hydrogen in the glass water column when below 25 psi. To achieve pressures above 25 psi, a portable stainless steel tank replaces the glass water columns for both systems. Tensile samples were strained using a stepping motor in the constant displacement rate condition. The crosshead displacement was measured using a linear variable differential transformer (LVDT) with a displacement resolution of 0.5 µm.Exposures and CERT ExperimentsIt was first necessary to determine the dissolved hydrogen concentration required to control the ECP to be a fixed distance from the Ni/NiO boundary. Exposures of pure nickel foil coupons were conducted for 72hours at a variety of dissolved hydrogen concentrations and temperatures. The dissolved hydrogen was determined by fixing the overpressure of hydrogen in the room temperature feed water and calculating the dissolved hydrogen via Henry’s Law. The thickness of the oxide film formed was determined by using nuclear reaction analysis (NRA) to measure the oxygen on the surface. The analysis was conducted with an 850 keV deuterium beam with the detector at an angle of 150° from the incident beam. The amount of oxygen present on the surface was determined by integrating the 16O(d,p1)17O peak and taking a ratio to the integrated charge. The results of this examination was used to determine the environmental conditions used in CERT testing.CERT experiments were performed in one of the two flowing water loops described earlier. Experiments were performed at temperatures between 320°C and 450°C in pure hydrogenated water. The flow rate was set at 40 mL/min and the conductivity was maintained to be under 0.1 µS/cm on the inlet and outlet by resin ion exchange filters. To measure the temperature dependence of crack initiation for Alloy 600, samples were strained in the MSCW at a strain rate of 3x10-7 s-1 to 8% strain. Additional CERT tests were conducted on Alloy 600 in the SSCW at a strain rate of 3x10-7 s-1 to 2% strain to avoid a saturation in the crack density in supercritical water. To measure the temperature dependence of crack initiation for Alloy 690, samples were pre-strained at room temperature to 20% then further strained in the MSCW at a strain rate of 5x10-8 s-1 to 7% strain in the water environments. To determine the effect of pre-strain, Alloy 690 was strained with and without pre-strain at 450°C and 425°C with a strain rate of 5x10-8 s-1 to 7%. To determine the effect of strain rate, Alloy 600 was strained at 320°C with strain rates of 3x10-7s-1and 5x10-8 s-1 to 8% strain. After removal from the autoclave, samples were examined by scanning electron microscopy (SEM) to characterize the cracking on the gauge section. Crack density, crack length, and crack length per unit area were measured.Confidence intervals for the activation energy for cracking in CERT testing were determined by calculating the error of the measurement and then propagating that error to the fit through simulation. The error of the crack length per unit area measurement was found using the method developed by Alexandreanu and Was [5]. The cracking was modeled as a binomial distribution where the standard deviation of the density is defined as,()(1) where σp is the standard deviation, N is the number of measured grain boundaries, and p is the fraction of cracked boundaries. The standard deviation of the average length measurement is defined as,(2)where σm is the error in the length measurement of a single crack and M is the number of cracks. The error in the length measurement of a single crack was found to be 0.2 μm. Because the length per unit area is equal to the product of the density and the average length, the uncertainty from the length and density measurements was propagated to the length per unit area measurement. The 95% confidence intervals for the activation energy were simulated by assuming that the uncertainty of the crack length per unit area followed a normal distribution for each data point. For each temperature the value was randomly generated following the normal distribution and a fit was calculated from the generated data. This process was repeated 100 times and the standard distribution of the fits was calculated; after 30 iterations the standard deviation did not vary by more than 1 kJ/mol. The 95% confidence interval was calculated by taking the P = 0.05 quantile of the fit standard deviation which was done by multiplying the standard deviation by 1.96.RESULTSExposure of pure nickel coupons was a quick method of determining the stability of nickel in subcritical and supercritical water. Optical examination of the coupons after exposure clearly showed whether or not NiO was stable by examining the surface of the sample. If NiO was stable the samples were black and if Ni was stable the surface retained the electropolished finish. A more quantitative examination using NRA was conducted and spectra such as those shown in Figure 1a were collected from the reaction of deuterium with oxygen. Figure 1b shows the ratio of counts from the 16O(d,p1)17O peak to the integrated charge collected on each sample as a function of the dissolved hydrogen concentration and exposure temperature. Exposure conditions below 0.001 counts/µC were considered to be Ni stable and above that were NiO stable. Figure 2 shows a summary of the exposed conditions as a function of dissolved hydrogen and temperature. Filled in black squares correspond with conditions where NiO was stable and open black squares are where Ni was stable. The data from subcritical water fits very well to exposure data from Attanasio and Morton shown by the red line [6]. However, the extrapolation of the boundary from the subcritical water does not match the exposure data. The measured location of the boundary in supercritical water is shifted to higher concentrations of dissolved hydrogen. It is not yet known if the higher hydrogen concentrations also correspond to lower than expected ECP since the fugacity has not been measured.Results of CERT tests for Alloy 690 and Alloy 600 are presented in Table II. For all samples of Alloy 600, the gauge surfaces exhibited significant amounts of intergranular cracking. The gauge surfaces of Alloy 600 tested at 320, 360, 400, and 425°C to 8% strain are shown in Figure 3. It is clear from the micrographs that cracking is temperature dependent with cracking severity increasing with temperature. The temperature dependence is strong enough that the cracking begins to saturate at temperatures in the supercritical water regime. Cracking saturation was observed when almost all of the grain boundaries normal to the tensile axis cracked, which was up to 35% of the total available grain boundaries at 450°C. To avoid cracking saturation, samples of Alloy 600 were strained to 2% instead of 8% in supercritical water to provide for a more accurate estimation of activation energy. Intergranular cracking was observed on Alloy 690, but to far lesser extent than Alloy 600. For example, the crack density at 320°C with a strain rate of 5x10-8 s-1 of Alloy 690 was ~30 cracks/mm2 whereas Alloy 600 had a crack density of ~1311 cracks/mm2. The observed cracking in Alloy 690 was a mixture of transgranular and intergranular cracks, but it appears that the transgranular cracks were primarily in the oxide layer. Transgranular cracks were observed to penetrate up to 200 nm in Alloy 690 strained at 400°C, which was on the same scale as the oxide layer thickness. Figure 4 shows examples of the extent of cracking in samples tested at 400°C and 320°C. For the purpose of measuring the crack density and length, only intergranular cracks were counted. In subcritical water the transgranular cracking diminished and the main mode was intergranular cracking. It also appeared that intergranular cracking mostly occurred on sections of grain boundaries where there was no surface carbide coverage. Cracks were seen to terminate at carbides and cracks greater than 1μm were not observed to traverse carbides. When cracks did intersect carbides they tended to migrate to transgranular and arrest.The intergranular crack length per unit area, crack density, and crack length are plotted for Alloy 600 samples strained to 8% and 2% at a strain rate of 3x10-7 s-1 in Figure 5a and pre-strained Alloy 690 which was strained in water to 7% at 5x10-8s-1in Figure 5b. The cracking behavior follows an Arrhenius relationship with temperature without a change in slope at the critical point for Alloy 690. Alloy 600 showed a break at the critical point because the samples were strained to two different total strains to avoid cracking saturation, 8% and 2%. The effect of pre-strain on Alloy 690 and lowering the strain rate on Alloy 600 is shown in Figure 6. The acceleration factor was calculated by taking the ratio of the cracking severity between the testing conditions. The pre-strained Alloy 690 sample showed an increased crack length per unit area and density by factors of 3.9 and 3.6 respectively, but only increases the length by a factor of 1.5 when compared to the sample that was not pre-strained. A similar situation wasobserved for Alloy 600 when the strain rate was changed. A lower strain rate increased the crack length per unit area and density by factors of 6.6 and 6.2 respectively, but did not increase the crack length.DISCUSSIONThe SCC initiation severity is clearly temperature dependent. Crack length per unit area as a function of 1/T is shown for each alloy condition in Figure 7. The crack length per unit area increases in a nonlinear fashion with temperature following an Arrhenius relationship which can be described as:(3) where Q is the activation energy for crack initiation in CERT testing. Fits for the activation energy were performed by a nonlinear robust fit regression following the Arrhenius relationship in GraphPad Prism©.The activation energy for crack initiation in CERT testing with 95% confidence intervals for each alloy is shown in Figure 7. Alloy 600 shows activation energies of 132±16 kJ/mol in subcritical water for samples strained to 8%, and 147±14 kJ/mol in supercritical water for samples strained to 2%. These two values agree well with each other and are well within the range of crack growth data activation energies in subcritical water, ranging from 80 to 220 kJ/mol [7]. They are also in agreement with the activation energy for crack initiation of Alloy 600 measured by Richey and Morton who measured 140±33 kJ/mol [8]. Alloy 690 has an activation energy for crack initiation of 85±17 kJ/mol. This is outside the range of what is seen for the crack initiation for Alloy 600 in this study, which may indicate a different mechanism is responsible for initiation. However, it has also been reported by Etien et al. that cold work and different heats of material can affect the activation energy for crack initiation [9]. Etien et al. measured a value of 103±18 kJ/mol for high temperature annealed Alloy 600, which covers the same range as the Alloy 690 measured in this evaluation. The activation energy for Alloy 690 crack initiation measured by crack depth in CERT specimens was found by Teysseyre and Was to be 87 kJ/mol, which is in very good agreement with this the value in this study. The activation energy may also be affected by the prior cold work, which has been observed in CERT testing of Alloy 600 by Rebak, Xia, and Szklarska-Smialowska [10]. However, it is important to consider how the activation energies are obtained. There is a good deal of scatter in the measures of the activation energy for cracking, which may partially be caused by the variety of testing methodologies used and different definitions of what crack initiation is. Many of the sources for crack initiation of Alloy 600 are taken from constant load time-to-failure data. Richey and Morton used in situ detection by direct current potential drop to measure the initiation time of cracks in samples exposed while under a constant load [8]. It is unclear if the differences in experiment methodology have an effect on the measured activation energy. While CERT straining is very fast and can be used to compare between equivalent macroscopic strains, it can lead to somewhat uncontrolled mechanical conditions in growing cracks and causes mechanical damage that is not representative of the stress state seen in reactors. By measuring cracks on the gauge surface of the tensile bar in SEM, this study may be including cracks that would not have grown into cracks that could have been measurable by DCDP or failed a specimen in constant load. As a result, it is not clear if the activation energies measured in this study are directly comparable to those from the literature for crack initiation. However, the testing methodology employed in this study is self-consistent, which allows comparison of the activation energy measurements across the subcritical-supercritical water boundary and between Alloy 690 and Alloy 600.The cracking severity in terms of crack length per unit area across the supercritical-subcritical water boundary suggests that the accelerating testing method is consistent with a single mechanism for cracking. The activation energies for Alloy 600 strained in supercritical and subcritical water are within the error of the measurement. The Alloy 690 crack initiation behavior showed no sharp change in the activation energy as it crossed the supercritical-subcritical boundary. Because Alloy 690 could be testedat a single condition over the entire temperature range, it is a better indication of whether there would be a change in the mechanism.CONCLUSIONS1.The location of the Ni/NiO boundary is shifted to higher dissolved hydrogen concentrations insupercritical water, possibly due to a change in the fugacity coefficient.2.The activation energy of crack initiation in CERT testing of Alloy 600 does not change across thecritical temperature (within experimental error), implying that the mechanism for crack initiation does not change from subcritical to supercritical water.3.The activation energy for Alloy 690 is lower than that measured for Alloy 600, potentiallysuggesting a different crack initiation mechanism.ACKNOWLEDGEMENTSThe authors would like to acknowledge support provided by the Electric Power Research Institute under contract EP-P35621 specifically the guidance provided by Tiangan (TG) Lian, and the help provided by Alexander Flick in the laboratory.REFERENCES[1] Materials Reliability Program (MRP), Resistance to Primary Water Stress Corrosion Cracking of Alloys 690, 52, and 152 in Pressurized Water Reactors (MRP-111), EPRI, Palo Alto, CA: 2004. 1009801.[2] K. Smith, A. Klein, P. Saint-Paul, and J. Blanchet, “Inconel 690 A Material with Improved Corrosion Resistance for PWR Steam Generator Tubes,” Proceedings of the Second International Symposium on Environmental Degradation of Materials in Nuclear Power Systems—Water Reactors, Monterey, California, September 9-12, 1985.[3] M.G. Angell, S.J. Allan, and G.P. Airey, “The Effect of Primary Coolant Zinc Additions on the SCC Behavior of Alloy 600 and 690,” Proceedings of the Ninth International Symposium on Environmental Degradation of Materials in Nuclear Power Systems—Water Reactors, Newport Beach, California, Aug. 1-5, 1999.[4] S. Teysseyre, G.S. Was, “Stress Corrosion Cracking of Austenitic Alloys in Supercritical Water,” Corrosion, 6(12), 1100-1116, 2006.[5] B. Alexandreanu, G.S. Was, “A priori determination of the sampling size for grain-boundary character distribution and grain-boundary degradation analysis,” Philosophical Magazine A, 81(8), 1951-1965, 2001.[6] S.A. Attanasio, D.S. Morton, “Measurement of the Nickel/Nickel Oxide Transition in Ni-Cr-Fe Alloys and Updated Data and Correlations to Quantify the Effect of Aqueous Hydrogen on Primary Water SCC,” Proceedings of the Eleventh International Symposium on Environmental Degradation of Materials in Nuclear Power Systems—Water Reactors, Stevenson, WA, Aug. 10-14, 2003.[7] R.W. Staehle, J.A. Gorman, “Progress in Understanding and Mitigating Corrosion on the Secondary Side of PWR Steam Generators,” Proceedings of the Tenth International Symposium on Environmental Degradation of Materials in Nuclear Power Systems—Water Reactors, Houston, TX, Aug. 5-9, 2001.[8] E. Richey, D. S. Morton, M. K. Schurman, “SCC Initiation Testing of Nickel-Based Alloys Using in situ Monitored Uniaxial Tensile Specimens,” Proceedings of the Twelfth International Symposium on Environmental Degradation of Materials in Nuclear Power Systems—Water Reactors, Salt Lake City, UT, Aug. 14-18, 2005.[9] R.A. Etien, E. Richey, D.S. Morton, J. Eager, “SCC Initiation Testing of Alloy 600 in High Temperature Water,” Proceedings of the Fifteenth International Symposium on Environmental Degradation of Materials in Nuclear Power Systems—Water Reactors, Colorado Springs, CO, Aug. 7-11, 2011.[10] R.B. Rebak, Z. Xia, Z Szklarska-Smialowska, “Effect of Temperature and Cold Work on the Crack Growth Rate of Alloy 600 in Primary Water,” Corrosion Science, 51(9), 689-697, 1995.Table I. Alloy Composition (Weight Percent)(a) (b)Figure 1. (a) Example of nuclear reaction analysis data taken from two samples tested at 450°C with 380 and 290cc/kg dissolved hydrogen. (b) Oxygen content on the surface of Ni coupons as a function of temperature and dissolved hydrogen concentration.Figure 2. Summary of Ni coupon exposures to determine the location of the Ni/NiO boundary insupercritical water in terms of temperature and dissolved hydrogen concentration. Open squares indicate no oxide formation and filled squares indicate conditions where oxide was found. Subcritical data was obtained from Attanasio and Morton [6].00.0050.010.0150.020.025320°C 360°C 400°C 425°C 450°C C o u n t s i n O x y g e n P e a k /C h a r g e (#/µC )Hydrogen Concentration (cc/kg)Air Formed FilmFigure 3. Representative micrographs of the gauge surface of Alloy 600 after CERT testing at the Ni/NiO boundary with a strain rate of 3x10-7 s-1 to 8% plastic strain.Figure 4. Representative micrographs of the gauge surface of Alloy 690 after CERT testing at the Ni/NiO boundary with a strain rate of 5x10-7 s -1 to 7% plastic strain with 20% pre-strain in air.(a) (b)Figure 5. The crack length per unit area, crack density, and crack length for (a) Alloy 600 samplesstrained to 8% and 2% at a strain rate of 3x10-7 s -1 and (b) 20% pre-strained Alloy 690 which was strained in water to 7% at 5x10-8 s -1.1011021031041051001011021031040.00120.00130.00140.00150.00160.0017C r a c k L e n g t h / U n i t A r e a (µm /m m 2)C r a c kD e n s i t y (#/m m 2)Average Crack Length (µm)1/T (K -1)4503504005003001011021031041051001011021031040.00120.00130.00140.00150.00160.0017C r a c k L e n g t h / U n i t A r e a (µm /m m 2)C r a c kD e n s i t y (#/m m 2)Average Crack Length (µm)1/T (K -1)Temperature (°C)450350400500300Figure 6. Effect of 20% pre-strain on Alloy 690 and lowering the strain rate on Alloy 600.Figure 7. Activation energy with 95% confidence intervals for crack initiation of Alloy 690 and Alloy 600 in supercritical and subcritical water tested over the temperature range from 320°C to 425°C.1234567891020% Pre-Strainvs.No Pre-strain 5x10s ,vs.3x10-7 s -1,A c c e l e r a t i o n F a c t o r1011021031041050.00120.00130.00140.00150.00160.0017C r a c k L e n g t h / U n i t A r e a (µm /m m 2)1/T (K -1)Temperature (°C)450350400500300。
腐蚀介绍和酸性环境选材ISO 15156-2009分享
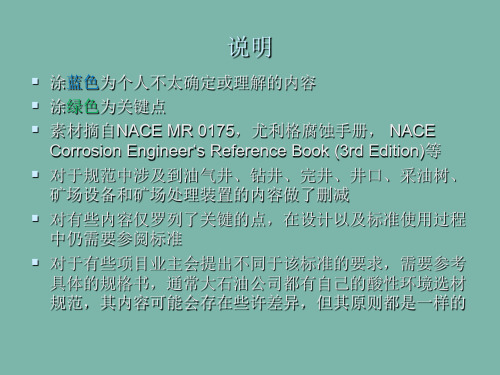
一 CRACKING AND CORROSION
CRACKING:开裂,只要有裂纹源,裂纹会扩展,扩展
速率有时会很快,不能通过增加腐蚀裕量来解决消除,在 含硫化氢的酸性环境中,通常开裂起着主导因素。该环境 中H2S对腐蚀起着主导作用,水是引起腐蚀的必要条件, CO2存在会促进腐蚀,究其本质也是应力腐蚀,即使在无 外加应力情况下也是因氢压引起,详见对HB的分析,见下 图(f).
SOHIC(stress-oriented hydrogen-induced cracking)应
力导向性氢致开裂 SCC(stress corrosion cracking) 应力腐蚀开裂 HSC(hydrogen stress cracking)氢应力开裂 SZC(soft-zone cracking)软区开裂 SWC(Step-wise cracking)阶梯裂纹 CRA( Corrosion-resistant alloy)耐蚀合金 HRC(Rockwell hardness)洛氏硬度 HBW (Brinell hardness) 布氏硬度 HV (Vickers hardness) HZC(Heat-affected zone) 热影响区 SOUR SERVICE: exposure to oilfield environments that contain sufficient H2S to cause cracking of materials by the mechanisms addressed by this part of ISO 15156
说明
涂蓝色为个人不太确定或理解的内容 涂绿色为关键点 素材摘自NACE MR 0175,尤利格腐蚀手册, NACE
Corrosion Engineer‘s Reference Book (3rd Edition)等 对于规范中涉及到油气井、钻井、完井、井口、采油树、 矿场设备和矿场处理装置的内容做了删减 对有些内容仅罗列了关键的点,在设计以及标准使用过程 中仍需要参阅标准 对于有些项目业主会提出不同于该标准的要求,需要参考 具体的规格书,通常大石油公司都有自己的酸性环境选材 规范,其内容可能会存在些许差异,但其原则都是一样的
ASTM A 790-09 无缝与焊接铁素体-奥氏体不锈钢管

Designation:A790/A790M–09Standard Specification forSeamless and Welded Ferritic/Austenitic Stainless Steel Pipe1This standard is issued under thefixed designation A790/A790M;the number immediately following the designation indicates the year of original adoption or,in the case of revision,the year of last revision.A number in parentheses indicates the year of last reapproval.A superscript epsilon(´)indicates an editorial change since the last revision or reapproval.1.Scope*1.1This specification2covers seamless and straight-seam welded ferritic/austenitic steel pipe intended for general corro-sive service,with particular emphasis on resistance to stress corrosion cracking.These steels are susceptible to embrittle-ment if used for prolonged periods at elevated temperatures.1.2Optional supplementary requirements are provided for pipe when a greater degree of testing is desired.These supplementary requirements call for additional tests to be made and,when desired,one or more of these may be specified in the order.1.3Appendix X1of this specification lists the dimensions of welded and seamless stainless steel pipe as shown in ANSI B36.19.Pipe having other dimensions may be furnished provided such pipe complies with all other requirements of this specification.1.4The values stated in either inch-pound units or SI units are to be regarded separately as standard.Within the text,the SI units are shown in brackets.The values stated in each system are not exact equivalents;therefore,each system must be used independently of the bining values from the two systems may result in nonconformance with the specifi-cation.The inch-pound units shall apply unless the M desig-nation of this specification is specified in the order.N OTE1—The dimensionless designator NPS(nominal pipe size)has been substituted in this standard for such traditional terms as nominal diameter,size,and nominal size.2.Referenced Documents2.1ASTM Standards:3A370Test Methods and Definitions for Mechanical Testing of Steel ProductsA923Test Methods for Detecting Detrimental Intermetallic Phase in Duplex Austenitic/Ferritic Stainless SteelsA941Terminology Relating to Steel,Stainless Steel,Re-lated Alloys,and FerroalloysA999/A999M Specification for General Requirements for Alloy and Stainless Steel PipeE213Practice for Ultrasonic Testing of Metal Pipe and TubingE309Practice for Eddy-Current Examination of Steel Tu-bular Products Using Magnetic SaturationE381Method of Macroetch Testing Steel Bars,Billets, Blooms,and ForgingsE426Practice for Electromagnetic(Eddy-Current)Exami-nation of Seamless and Welded Tubular Products,Austen-itic Stainless Steel and Similar AlloysE527Practice for Numbering Metals and Alloys in the Unified Numbering System(UNS)2.2ANSI Standards:4B1.20.1Pipe Threads,General PurposeB36.10Welded and Seamless Wrought Steel PipeB36.19Stainless Steel Pipe2.3SAE Standard:5SAE J10862.4Other Standard:6SNT-TC-1A Personal Qualification and Certification in Nondestructive Testing2.5AWS StandardA5.9Corrosion-Resisting Chromium and Chromium-Nickel Steel Welding Rods and Electrodes3.Terminology3.1Definitions—For definitions of terms used in this speci-fication refer to Terminology A941.1This specification is under the jurisdiction of ASTM Committee A01on Steel, Stainless Steel and Related Alloys and is the direct responsibility of Subcommittee A01.10on Stainless and Alloy Steel Tubular Products.Current edition approved Aug.1,2009.Published September2009.Originally approved st previous edition approved in2008as A790/A790M–08a.2For ASME Boiler and Pressure Vessel Code applications see related Specifi-cation SA–790in Section II of that Code.3For referenced ASTM standards,visit the ASTM website,,or contact ASTM Customer Service at service@.For Annual Book of ASTM Standards volume information,refer to the standard’s Document Summary page on the ASTM website.4Available from American National Standards Institute(ANSI),25W.43rd St., 4th Floor,New York,NY10036,.5Available from Society of Automotive Engineers(SAE),400Commonwealth Dr.,Warrendale,PA15096-0001,.6Available from American Society for Nondestructive Testing(ASNT),P.O.Box 28518,1711Arlingate Ln.,Columbus,OH43228-0518,.*A Summary of Changes section appears at the end of this standard. Copyright©ASTM International,100Barr Harbor Drive,PO Box C700,West Conshohocken,PA19428-2959,United States.4.Ordering Information4.1Orders for material under this specification should include the following,as required,to describe the desired material adequately:4.1.1Quantity (feet,[metres],or number of lengths),4.1.2Name of material (ferritic/austenitic steel pipe),4.1.3Process (seamless or welded),4.1.4Grade (see Table 1),4.1.5Size (NPS designator or outside diameter and sched-ule number of average wall thickness),4.1.6Length (specific or random)(see Section 11),4.1.7End finish (section on ends of Specification A 999/A 999M ),4.1.8Optional requirements (product analysis,Section 9;hydrostatic test or nondestructive electric test,Section 14),4.1.9Test report required (section on certification of Speci-fication A 999/A 999M ),4.1.10Specification designation,and4.1.11Special requirements and any supplementary require-ments selected.5.General Requirements5.1Material furnished under this specification shall con-form to the applicable requirements of the current edition of Specification A 999/A 999M unless otherwise provided herein.6.Materials and Manufacture6.1Manufacture :6.1.1The pipe shall be made by the seamless or an automatic welding process,with no addition of filler metal in the welding operation.6.1.2At the manufacturer’s option,pipe may be either hot-finished or cold-finished.6.1.3The pipe shall be pickled free of scale.When bright annealing is used,pickling is not necessary.6.2Discard —A sufficient discard shall be made from each ingot to secure freedom from injurious piping and undue segregation.6.3Unless otherwise stated in the order,all pipe shall be furnished in the heat-treated condition as shown in Table 1.TABLE 1Heat TreatmentUNS Designation Type A Temperature °F [°C]QuenchS312001920–2010[1050–1100]Rapid cooling in water S312601870–2010[1020–1100]Rapid cooling in air or water S315001800–1900[980–1040]Rapid cooling in air or water S318031870–2010[1020–1100]Rapid cooling in air or water S320031850–2050[1010–1120]Rapid cooling in air or water S321011870[1020]Quenched in water or rapidly cooled by other meansS322021870–1975[1020–1080]Rapid cooling in air or water S3220522051870–2010[1020–1100]Rapid cooling in air or water S3230423041700–1920[925–1050]Rapid cooling in air or water S325061870–2050[1020–1120]Rapid cooling in air or water S325201975–2050[1080–1120]Rapid cooling in air or water S3*******1900[1040]min Rapid cooling in air or water S327071975–2050[1080–1120]Rapid cooling in air or water S3275025071880–2060[1025–1125]Rapid cooling in air or water S327601960–2085[1070–1140]Rapid cooling in air or water S328081920–2100[1050–1150]Rapid cooling in air or water S3*******1700–1750[925–955]Rapid cooling in air or water S329061870–2100[1020–1150]Rapid cooling in air or water S329501820–1880[990–1025]Air coolS332071905–2085[1040–1140]Rapid cooling in water or by other meansS392741920–2060[1025–1125]Rapid cooling in air or water S392771975–2155[1080–1180]Rapid cooling in air or waterACommon name,not a trademark,widely used,not associated with any one producer.329is na AISInumber.6.3.1For seamless pipe,as an alternate to final heat treat-ment in a continuous furnace or batch-type furnace,immedi-ately following hot forming while the temperature of the pipes is not less than the specified minimum solution treatment temperature,pipes shall be individually quenched in water or rapidly cooled by other means,except for UNS S32950,which shall be air cooled.6.3.2If the purchaser desires pipe without heat treatment subsequent to welding,the purchase order shall specify the following condition:6.3.2.1No final heat treatment of pipe fabricated from plate that has been heat treated as required by Table 1for the particular grade is required,provided a sample of that heat of finished pipe or material representative of that heat of pipe as a prolongation of the weld passes the Test Methods A 923Method B or C (See Note 2),including base metal,weld metal,and heat affected zone per heat.Each pipe supplied under this requirement shall be stenciled with the suffix “HT-O.”6.3.2.2For materials not listed in Table 3of Test Methods A 923,the HT-O provision does not apply.N OTE 2—The Test Methods A 923test method (B or C)is at the manufacturer’s option,unless otherwise specified by the purchaser.7.Chemical Composition7.1The steel shall conform to the chemical requirements as prescribed in Table 2.8.Heat Analysis8.1An analysis of each heat of steel shall be made by the steel manufacturer to determine the percentages of the ele-ments specified.9.Product Analysis9.1At the request of the purchaser’s inspector,an analysis of one billet or one length of flat-rolled stock from each heat,or two pipes from each lot,shall be made by the manufacturer.A lot of pipe shall consist of the following number of lengths of the same size and wall thickness from any one heat of steel:NPS Designator Lengths of Pipe in Lot Under 2400or fraction thereof 2to 5,incl 200or fraction thereof 6and over100or fraction thereof9.2The results of these analyses shall be reported to the purchaser or the purchaser’s representative and shall conform to the requirements specified in Section 7.9.3If the analysis of one of the tests specified in 8.1or 9.1does not conform to the requirements specified in Section 7,an analysis of each billet or pipe from the same heat or lot may be made,and all billets or pipe conforming to the requirements shall be accepted.10.Tensile and Hardness Properties10.1The material shall conform to the tensile and hardness properties prescribed in Table 3.TABLE 2Chemical Requirements AUNS Designa-tion B Type CC Mn P S Si Ni Cr Mo N CuOthersS312000.030 2.000.0450.030 1.00 5.5–6.524.0–26.0 1.20–2.000.14–0.20......S312600.030 1.000.0300.0300.75 5.5–7.524.0–26.0 2.5–3.50.10–0.300.20–0.80W0.10–0.50S315000.030 1.20–2.000.0300.030 1.40–2.00 4.2–5.218.0–19.0 2.50–3.000.05–0.10......S318030.030 2.000.0300.020 1.00 4.5–6.521.0–23.0 2.5–3.50.08–0.20......S320030.030 2.000.0300.020 1.00 3.0–4.019.5-22.5 1.50–2.000.14–0.20......S321010.040 4.0–6.00.0400.030 1.00 1.35–1.7021.0–22.00.10–0.800.20–0.250.10–0.80...S322020.030 2.000.0400.010 1.00 1.00–2.8021.5–24.00.450.18–0.26......S3220522050.030 2.000.0300.020 1.00 4.5–6.522.0–23.0 3.0–3.50.14–0.20......S3230423040.030 2.500.0400.040 1.00 3.0–5.521.5–24.50.05–0.600.05–0.200.05–0.60...S325060.030 1.000.0400.0150.90 5.5–7.224.0–26.0 3.0–3.50.08–0.20...W0.05–0.30S325200.030 1.50.0350.0200.80 5.5–8.024.0–26.0 3.0–5.00.20–0.350.5–3.00...S3*******0.04 1.500.0400.030 1.00 4.5–6.524.0–27.0 2.9–3.90.10–0.25 1.50–2.50...S327070.030 1.500.0350.0100.50 5.5–9.526.0–29.0 4.0–5.00.30–0.50 1.0Co0.5–2.0S3275025070.030 1.200.0350.0200.80 6.0–8.024.0–26.0 3.0–5.00.24–0.320.5...S327600.051.000.0300.0101.006.0–8.024.0–26.03.0–4.00.20–0.300.50–1.00W0.50–1.0040min DS328080.0301.100.0300.0300.507.0–8.227.0–27.90.80–1.200.30–0.40...W2.10–2.50S3*******0.08 1.000.0400.0300.75 2.5–5.023.0–28.0 1.00–2.00.........S329060.0300.80–1.500.0300.0300.80 5.8–7.528.0–30.0 1.50–2.600.30–0.400.80...S329500.030 2.000.0350.0100.60 3.5–5.226.0–29.0 1.00–2.500.15–0.35......S332070.030 1.500.0350.0100.80 6.0–9.029.0–33.0 3.0–5.00.40–0.60 1.0S392740.030 1.000.0300.0200.80 6.0–8.024.0–26.0 2.5–3.50.24–0.320.20–0.80W1.50–2.50S392770.0250.800.0250.0020.806.5–8.024.0–26.03.0–4.00.23–0.331.20–2.00W 0.8–1.2AMaximum,unless a range or minimum is indicated.Where ellipses (...)appear in this table,there is no minimum and analysis for the element need not be determined or reported.BNew designation established in accordance with Practice E 527and SAE J 1086.CCommon name,not a trademark,widely used,not associated with any one producer.329is na AISI number.D%Cr +3.33%Mo +163%N.11.Lengths11.1Pipe lengths shall be in accordance with the following regular practice:11.1.1Unless otherwise agreed upon,all sizes from NPS 1⁄8to and including NPS 8are available in a length up to 24ft (see Note 3)with the permissible range of 15to 24ft (see Note 3).Short lengths are acceptable and the number and minimum length shall be agreed upon between the manufacturer and the purchaser.N OTE 3—This value applies when the inch-pound designation of this specification is the basis of purchase.When the M designation of this specification is the basis of purchase,the corresponding metric value(s)shall be agreed upon between the manufacturer and purchaser.11.1.2If definite cut lengths are desired,the lengths re-quired shall be specified in the order.No pipe shall be less than the specified length and no more than 1⁄4in.[6mm]over it.11.1.3No jointers are permitted unless otherwise specified.TABLE 3Tensile and Hardness RequirementsUNS Designation TypeATensile Strength,min,ksi [MPa]Yield Strength,min,ksi [MPa]Elongation in 2in.or 50mm,min,%Hardness,max HBW HRC S3*******[690]65[450]25280...S3*******[690]65[450]25......S3150092[630]64[440]3029030S3180390[620]65[450]2529030S3200390[620]65[450]2529030S32101t #0.187in.[5.00mm]101[700]77[530]30290...t >0.187in.[5.00mm]94[650]65[450]30290...S3220294[650]65[450]3029030S32205220595[655]65[450]2529030S32304230487[600]58[400]2529030S3250690[620]65[450]1830232S32520112[770]80[550]25310...S32550255110[760]80[550]1529731S32707133[920]101[700]2531834S327502507116[800]80[550]1530032S32760B 109[750]80[550]25300...S3*******[800]80[550]1531032S3290032990[620]70[485]2027128S32906Wall below 0.40in.[10mm]116[800]94[650]2530032Wall 0.40in.[10mm]and above 109[750]80[550]2530032S3*******[690]70[480]2029030S33207Wall below0.157in.(4mm)138[950]112[770]1533636Wall 0.157in.(4mm)and above 123[850]101[700]1533636S39274116[800]80[550]1531032S39277120[825]90[620]2529030ACommon name,not a trademark,widely used,not associated with any one producer.329is na AISI number.BPrior to A 790/A 790M –04,the tensile strength value for UNS 32760was 109–130ksi [750–895MPa].12.Workmanship,Finish,and Appearance12.1Thefinished pipes shall be reasonably straight and shall have a workmanlikefinish.Imperfections may be re-moved by grinding,provided the wall thicknesses are not decreased to less than that permitted,in the Permissible Variations in Wall Thickness Section of Specification A999/ A999M.13.Mechanical Tests Required13.1Transverse or Longitudinal Tension Test—One tension test shall be made on a specimen for lots of not more than100 pipes.Tension tests shall be made on specimens from2pipes for lots of more than100pipes.13.2Mechanical Testing Lot Definition—The term lot for mechanical tests applies to all pipe of the same nominal size and wall thickness(or schedule)that is produced from the same heat of steel and subjected to the samefinishing treatment as defined as follows:13.2.1Where the heat treated condition is obtained,consis-tent with the requirements of 6.3,in a continuous heat treatment furnace or by directly obtaining the heat treated condition by quenching after hot forming,the lot shall include all pipe of the same size and heat,heat treated in the same furnace at the same temperature,time at heat,and furnace speed or all pipe of the same size and heat,hot formed and quenched in the same production run.13.2.2Wherefinal heat treatment is obtained,consistent with the requirements of6.3,in a batch-type heat-treatment furnace equipped with recording pyrometers and automatically controlled within a50°F[30°C]or smaller range,the lot shall be the larger of(a)each200ft[60m]or fraction thereof or(b) that pipe heat treated in the same batch furnace charge. 13.2.3Where thefinal heat treatment is obtained,consistent with the requirements of6.3,in a batch-type heat-treatment furnace not equipped with recording pyrometers and automati-cally controlled within a50°F[30°C]or smaller range,the term lot for mechanical tests applies to the pipe heat treated in the same batch furnace charge,provided that such pipe is of the same nominal size and wall thickness(or schedule)and is produced from the same heat of steel.13.3Flattening Test—For pipe heat treated in a batch-type furnace,flattening tests shall be made on5%of the pipe from each heat-treated lot.For pipe heat treated by the continuous process,or by direct quenching after hot forming,this test shall be made on a sufficient number of pipes to constitute5%of the lot,but in no case less than two lengths of pipe.13.3.1For welded pipe with a diameter equal to or exceed-ing NPS10,a transverse guided face bend test of the weld may be conducted instead of aflattening test in accordance with the method outlined in the steel tubular product supplement of Test Methods and Definitions A370.The ductility of the weld shall be considered acceptable when there is no evidence of cracks in the weld or between the weld and the base metal after bending.Test specimens from5%of the lot shall be taken from the pipes or test plates of the same material as the pipe, the test plates being attached to the end of the cylinder and welded as a prolongation of the pipe longitudinal seam.13.4Hardness Test—Brinell or Rockwell hardness tests shall be made on specimens from two pipes from each lot(see13.2).14.Hydrostatic or Nondestructive Electric Test14.1Each pipe shall be subjected to the nondestructive electric test or the hydrostatic test.The type of test to be used shall be at the option of the manufacturer,unless otherwise specified in the purchase order.14.2The hydrostatic test shall be in accordance with Speci-fication A999/A999M,except that the value for S to be used in the calculation of the hydrostatic test pressure shall be equal to50%of the specified minimum yield strength of the pipe.14.3Nondestructive Electric Test:Nondestructive electric tests shall be in accordance with Practices E213or E309.14.3.1As an alternative to the hydrostatic test,and when specified by the purchaser,each pipe shall be examined with a nondestructive test in accordance with Practices E213or E309.Unless specifically called out by the purchaser,the selection of the nondestructive electric test will be at the option of the manufacturer.The range of pipe sizes that may be examined by each method shall be subject to the limitations in the scope of the respective practices.14.3.1.1The following information is for the benefit of the user of this specification:14.3.1.2The reference standards defined in14.3.1.3-14.3.1.5are convenient standards for calibration of nondestruc-tive testing equipment.The dimensions of these standards should not be construed as the minimum size imperfection detectable by such equipment.14.3.1.3The ultrasonic testing(UT)can be performed to detect both longitudinally and circumferentially oriented de-fects.It should be recognized that different techniques should be employed to detect differently oriented imperfections.The examination may not detect short,deep,defects.14.3.1.4The eddy-current testing(ET)referenced in this specification(see Practice E426)has the capability of detect-ing significant discontinuities,especially the short abrupt type.14.3.1.5A purchaser interested in ascertaining the nature (type,size,location,and orientation)of discontinuities that can be detected in the specific application of these examinations should discuss this with the manufacturer of the tubular product.14.4Time of Examination—Nondestructive testing for specification acceptance shall be performed after all mechani-cal processing,heat treatments,and straightening operations. This requirement does not preclude additional testing at earlier stages in the processing.14.5Surface Condition:14.5.1All surfaces shall be free of scale,dirt,grease,paint, or other foreign material that could interfere with interpretation of test results.The methods used for cleaning and preparing the surfaces for examination shall not be detrimental to the base metal or the surfacefinish.14.5.2Excessive surface roughness or deep scratches can produce signals that interfere with the test.14.6Extent of Examination:14.6.1The relative motion of the pipe and the transducer(s), coil(s),or sensor(s)shall be such that the entire pipe surface is scanned,except as in14.6.2.14.6.2The existence of end effects is recognized and the extent of such effects shall be determined by the manufacturer and,if requested,shall be reported to the purchaser.Other nondestructive tests may be applied to the end areas,subject to agreement between the purchaser and the manufacturer. 14.7Operator Qualifications—The test unit operator shall be certified in accordance with SNT-TC-1A,or an equivalent recognized and documented standard.14.8Test Conditions:14.8.1For eddy-current testing,the excitation coil fre-quency shall be chosen to ensure adequate penetration yet provide good signal-to-noise ratio.14.8.2The maximum eddy-current coil frequency used shall be as follows:On specified walls up to0.050in.—100KHz maxOn specified walls up to0.150in.—50KHz maxOn specified walls over0.150in.—10KHz max14.8.3Ultrasonic—For examination by the ultrasonic method,the minimum nominal transducer frequency shall be 2.00MHz and the maximum nominal transducer size shall be 1.5in.If the equipment contains a reject noticefilter setting, this shall remain off during calibration and testing unless linearity can be demonstrated at that setting.14.9Reference Standards—Reference standards of conve-nient length shall be prepared from a length of pipe of the same grade,size(NPS,or outside diameter and schedule or wall thickness),surfacefinish and heat treatment condition as the pipe to be examined.14.9.1For Ultrasonic Testing,the reference ID and OD notches shall be any one of the three common notch shapes shown in Practice E213,at the option of the manufacturer.The depth of each notch shall not exceed121⁄2%of the specified nominal wall thickness of the pipe or0.004in.,whichever is greater.The width of the notch shall not exceed twice the depth.Notches shall be placed on both the OD and ID surfaces.14.9.2For Eddy-Current Testing,the reference standard shall contain,at the option of the manufacturer,any one of the following discontinuities:14.9.2.1Drilled Hole—The reference standard shall con-tain three or more holes equally spaced circumferentially around the pipe and longitudinally separated by a sufficient distance to allow distinct identification of the signal from each hole.The holes shall be drilled radially and completely through the pipe wall,with care being taken to avoid distortion of the pipe while drilling.One hole shall be drilled in the weld,if visible.Alternately,the producer of welded pipe may choose to drill one hole in the weld and run the calibration standard through the test coils three times with the weld turned at120°on each pass.The hole diameter shall vary with NPS as follows:NPS Designator Hole Diameter0.039in.[1mm]above1⁄2to11⁄40.055in.[1.4mm]above11⁄4to20.071in.[1.8mm]above2to50.087in.[2.2mm]above50.106in.[2.7mm]14.9.2.2Transverse Tangential Notch—Using a round tool orfile with a1⁄4-in.[6.4-mm]diameter,a notch shall befiled or milled tangential to the surface and transverse to the longitu-dinal axis of the pipe.Said notch shall have a depth not exceeding121⁄2%of the specified nominal wall thickness of the pipe or0.004in.[0.102mm],whichever is greater.14.9.2.3Longitudinal Notch—A notch0.031in.or less in width shall be machined in a radial plane parallel to the tube axis on the outside surface of the pipe to have a depth not exceeding121⁄2%of the specified wall thickness of the pipe or0.004in.,whichever is greater.The length of the notch shall be compatible with the testing method.More or smaller reference discontinuities,or both,may be used by agreement between the purchaser and the manufac-turer.14.10Standardization Procedure:14.10.1The test apparatus shall be standardized at the beginning and end of each series of pipes of the same size (NPS or diameter and schedule or wall thickness,grade,and heat treatment condition),and at intervals not exceeding4h. More frequent standardization may be performed at the manu-facturer’s option or may be required upon agreement between the purchaser and the manufacturer.14.10.2The test apparatus shall also be standardized after any change in test system settings,change of operator,equip-ment repair,or interruption due to power loss,process shut-down,or when a problem is suspected.14.10.3The reference standard shall be passed through the test apparatus at the same speed and test system settings as the pipe to be tested.14.10.4The signal-to-noise ratio for the reference standard shall be21⁄2to1or greater.Extraneous signals caused by identifiable causes such as dings,scratches,dents,straightener marks,and so forth shall not be considered noise.The rejection amplitude shall be adjusted to be at least50%of full scale of the readout display.14.10.5If upon any standardization,the rejection amplitude has decreased by29%(3dB)of peak height from the last standardization,the pipe since the last calibration shall be rejected.The test system settings may be changed or the transducer(s),coil(s),or sensor(s)adjusted and the unit restan-dardized.But all pipe tested since the last acceptable standard-ization must be retested for acceptance.14.11Evaluation of Imperfections:14.11.1Pipes producing a signal equal to or greater than the lowest signal produced by the reference standard(s)shall be identified and separated from the acceptable pipes.The area producing the signal may be reexamined.14.11.2Such pipes shall be rejected if the test signal was produced by imperfections that cannot be identified or was produced by cracks or crack-like imperfections.These pipes may be repaired per Sections12and13.To be accepted,a repaired pipe must pass the same non-destructive test by which it was rejected,and it must meet the minimum wall thickness requirements of this specification.14.11.3If the test signals were produced by visual imper-fections such as:(1)scratches,(2)surface roughness,(3)dings, (4)straightener marks,(5)cutting chips,(6)steel diestamps,(7)stop marks,or(8)pipe reducer ripple.The pipe may be accepted based on visual examination,provided the imperfec-tion is less than0.004in.[0.1mm]or121⁄2%of the specified wall thickness(whichever is greater).14.11.4Rejected pipe may be reconditioned and retested providing the wall thickness is not decreased to less than that required by this or the product specification.The outside diameter at the point of grinding may be reduced by the amountso removed.To be accepted,retested pipe shall meet the test requirement.14.11.5If the imperfection is explored to the extent that it can be identified as non-rejectable,the pipe may be accepted without further test providing the imperfection does not en-croach on the minimum wall thickness.15.Repair by Welding15.1For welded pipe of size NPS6or larger with a specified wall thickness of0.188in.[4.8mm]or more,weld repairs made with the addition of compatiblefiller metal may be made to the weld seam with the same procedures specified for plate defects in the section on Repair by Welding of Specification A999/A999M.15.2Weld repairs of the weld seam shall not exceed20%of the seam length.15.3Except as allowed by15.3.1,weld repairs shall be made only with the gas tungsten-arc welding process using the same classification of barefilter rod qualified to the most current AWS Specification A5.9as the grade of pipe being repaired as given in Table4.15.3.1Subject to approval by the purchaser,it shall be permissible for weld repairs to be made with the gas tungsten-arc welding process using afiller metal more highly alloyed than the base metal,if needed for corrosion resistance or other properties.15.4Pipes that have had weld seam repairs withfiller metal shall be identified with the symbol“WR”and shall be so stated and identified on the certificate of tests.Iffiller metal other than that listed in Table4is used,thefiller metal shall be identified on the certificate of tests.15.5Weld repairs shall be completed prior to any heat treatment.16.Product Marking16.1In addition to the marking prescribed in Specification A999/A999M,the marking shall include the manufacturer’s private identifying mark and whether the pipe is seamless or welded.If specified in the purchase order,the marking for pipe larger than NPS4shall include the weight.17.Keywords17.1duplex stainless steel;ferritic/austenitic stainless steel; seamless steel pipe;stainless steel pipe;steel pipe;welded steel pipeSUPPLEMENTARY REQUIREMENTSFOR PIPE REQUIRING SPECIAL CONSIDERATION One or more of the following supplementary requirements shall apply only when specified in the purchase order.The purchaser may specify a different frequency of test or analysis than is provided in the supplementary requirement.Subject to agreement between the purchaser and manufacturer, retest and retreatment provisions of these supplementary requirements may also be modified.S1.Product AnalysisS1.1For all pipe over NPS5there shall be one product analysis made of a representative sample from one piece for each ten lengths or fraction thereof from each heat of steel. S1.2For pipe smaller than NPS5there shall be one product analysis made from ten lengths per heat of steel or from10% of the number of lengths per heat of steel,whichever number is smaller.S1.3Individual lengths failing to conform to the chemical requirements specified in Section7shall be rejected.S2.Transverse Tension TestsS2.1There shall be one transverse tension test made from one end of10%of the lengths furnished per heat of steel.This applies only to pipe over NPS8.S2.2If a specimen from any length fails to conform to the tensile properties specified that length shall be rejected.S3.Flattening TestS3.1Theflattening test of Specification A999/A999M shall be made on a specimen from one end or both ends of each pipe.Crops ends may be used.If this supplementary require-ment is specified,the number of tests per pipe shall also be specified.If a specimen from any length fails because of lack of ductility prior to satisfactory completion of thefirst step of theflattening test requirement,that pipe shall be rejected subject to retreatment in accordance with Specification A999/ A999M and satisfactory retest.If a specimen from any length of pipe fails because of a lack of soundness that length shall be rejected,unless subsequent retesting indicates that the remain-ing length is sound.S4.Etching TestsS4.1The steel shall be homogeneous as shown by etching tests conducted in accordance with the appropriate portions of Method E381.Etching tests shall be made on a cross section TABLE4Pipe and Filler Metal SpecificationPipe Filler MetalUNS Designation AWS A5.9Class UNS Designation S31803ER2209S39209S32205ER2209S39209S31200ER2553S39553。
焊接冷裂纹
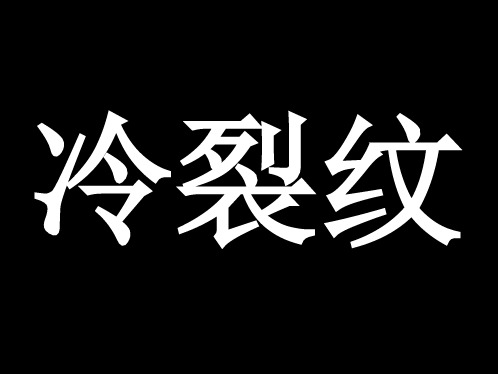
拘束度
焊接接头根部间隙产生单位长度的弹性位移 时,单位长度焊缝上所承受的力。
L 两端被固定 的对接接头
假定焊缝冷却结束时,根部间隙产生了单位长度 的弹性位移,则应变为:
h
1
L
焊缝对母材产 生的拉伸应力为:
E0
E0 L
单位长度母材上所承受的力与单位长度焊缝 上所承受的力相等,即拘束度R为:
I. 钢种的淬硬倾向
钢种的淬硬倾向主要决定于化学成 分,板厚、焊接工艺及冷却条件等也有 影响。钢种的淬硬倾向越大,冷裂倾向 越大。
• 脆硬的片M组织 • 淬硬会产生较多的晶格缺陷
焊接时,近缝区加热温度高,A晶 粒严重长大,在焊后快速冷却条件下, 粗大的A就转变为粗大的M。这种脆硬 的M组织易于裂纹的萌生及裂纹的扩展。
氢、组织和应力三者对冷 裂纹的影响是非常复杂的。
R / ×1000N(mm·mm)-1
20
氢
HD=4~5mL/100g
15
t8/5=8~9s
Ceq: IIW
10
应
组织
力
5
0.3
0.4
0.5
Ceq
Ceq
C
Mn 6
Cr
Mo V 5
Cu Ni 15
4.4.2 冷裂纹敏感指数
PC
Pcm
适用范围:
1) 合金元素含量 wt%
C Si Mn Cu Ni Cr Mo V Ti Nb B
0.07~
~ 0.4~
~
~
~
~
~
~
~
~
0.22 0.6 1.4 0.5 1.20 1.2 0.7 0.12 0.05 0.04 0.005
焊接专业英语词汇学习汇总

焊接方面的1. 保护气体shielding gas2。
变形deformation3. 波浪变形buckling distortion4. 补焊repair welding5。
残余应力residual—stress6。
层状撕裂Lamellar Tear7. 插销试验Implant Test8. 常规力学性能convention mechanics performance9. 超声波探伤ultrasonic inspection10. 衬垫焊welding with backing11. 船形焊fillet welding in the flat position 12。
磁粉探伤magnetic particle inspection 13。
粗滴过渡globular transfer14。
脆性断裂brittlement fracture15。
淬火vt. quench n. ~ing16. 错边变形dislocating distortion17. 搭接lap welding18。
打底焊backing welding19. 单道焊single—pass welding20. 单面焊welding by one side21. 导电嘴wire guide ;contact tube22。
等离子弧焊plasma welding23。
低合金钢low alloy steel24. 点焊spot welding25. 电弧动特性dynamic characteristic26. 电弧焊electric arc welding27。
电弧静特性static characteristic28。
电极electrode29. 电流current30. 电压voltage31。
电源power supply;power source32. 电阻焊resistance welding33. 调修correct34. 定位焊tack welding35. 短路过渡short circuiting transfer36。
高级封坯抗渗剂安全数据表说明书
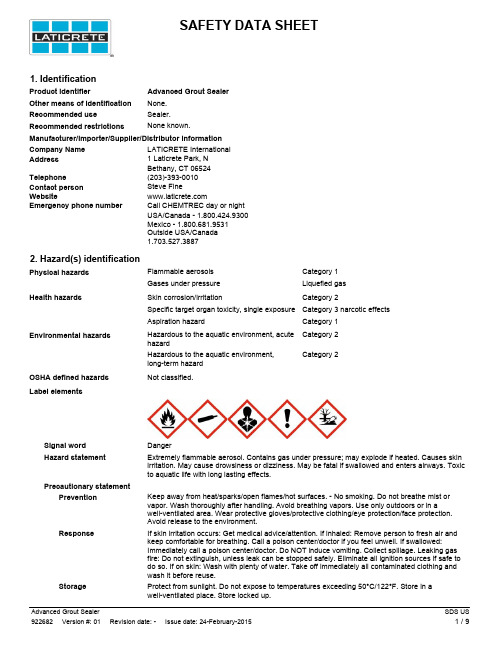
SAFETY DATA SHEET1. IdentificationProduct identifier Advanced Grout SealerOther means of identification None.Recommended use Sealer.Recommended restrictions None known.Manufacturer/Importer/Supplier/Distributor informationCompany Name LATICRETE InternationalAddress 1 Laticrete Park, NBethany, CT 06524Telephone(203)-393-0010Contact person Steve FineWebsite Emergency phone number Call CHEMTREC day or nightUSA/Canada - 1.800.424.9300Mexico - 1.800.681.9531Outside USA/Canada1.703.527.38872. Hazard(s) identificationFlammable aerosolsCategory 1Physical hazardsGases under pressureLiquefied gasSkin corrosion/irritationCategory 2Health hazardsSpecific target organ toxicity, single exposureCategory 3 narcotic effectsAspiration hazardCategory 1Hazardous to the aquatic environment, acuteCategory 2Environmental hazardshazardHazardous to the aquatic environment,Category 2long-term hazardNot classified.OSHA defined hazardsLabel elementsSignal word DangerHazard statement Extremely flammable aerosol. Contains gas under pressure; may explode if heated. Causes skinirritation. May cause drowsiness or dizziness. May be fatal if swallowed and enters airways. Toxicto aquatic life with long lasting effects.Precautionary statementPrevention Keep away from heat/sparks/open flames/hot surfaces. - No smoking. Do not breathe mist orvapor. Wash thoroughly after handling. Avoid breathing vapors. Use only outdoors or in awell-ventilated area. Wear protective gloves/protective clothing/eye protection/face protection.Avoid release to the environment.Response If skin irritation occurs: Get medical advice/attention. If inhaled: Remove person to fresh air andkeep comfortable for breathing. Call a poison center/doctor if you feel unwell. If swallowed:Immediately call a poison center/doctor. Do NOT induce vomiting. Collect spillage. Leaking gasfire: Do not extinguish, unless leak can be stopped safely. Eliminate all ignition sources if safe todo so. If on skin: Wash with plenty of water. Take off immediately all contaminated clothing andwash it before reuse.Storage Protect from sunlight. Do not expose to temperatures exceeding 50°C/122°F. Store in awell-ventilated place. Store locked up.DisposalDispose of contents/container in accordance with local/regional/national/international regulations.Hazard(s) not otherwise classified (HNOC)May displace oxygen and cause rapid suffocation.3. Composition/information on ingredientsMixtures64742-48-960 - 80Naphtha (petroleum),hydrotreated heavy CAS number %Chemical name 106-97-810 - 20Butane 74-98-610 - 20PropaneProprietary < 2Partially Fluorinated Acrylic Copolymer 123-86-4< 2n-Butyl acetate Composition commentsAll concentrations are in percent by weight unless ingredient is a gas. Gas concentrations are in percent by volume.4. First-aid measuresInhalation Move into fresh air and keep at rest. If breathing stops, provide artificial respiration. Get medical attention if any discomfort continues.Skin contactFlush thoroughly with water for at least 15 minutes. Wash skin with soap and water. Get medical attention if irritation develops and persists.Frostbite: Do not remove clothes, but flush with copious amounts of lukewarm water. Call an ambulance and continue to flush during transportation to hospital.Eye contact Flush thoroughly with water for at least 15 minutes. Remove contact lenses, if present and easy to do. Get medical attention immediately.IngestionImmediately rinse mouth and drink plenty of water. Keep person under observation. If person becomes uncomfortable take to hospital along with these instructions. Get medical attention if symptoms occur.Most importantsymptoms/effects, acute and delayedSkin irritation. Irritation of nose and throat. Irritating to mucous membranes. Droplets of the product aspirated into the lungs through ingestion or vomiting may cause a serious chemical pneumonia. Exposure to rapidly expanding gas or vaporizing liquid may cause frostbite ("cold burn"). Very high exposure can cause suffocation from lack of oxygen.Indication of immediatemedical attention and special treatment needed Treat symptomatically.General informationEnsure that medical personnel are aware of the material(s) involved, and take precautions to protect themselves.5. Fire-fighting measuresSuitable extinguishing media Extinguish with alcohol-resistant foam, carbon dioxide or dry powder.Unsuitable extinguishing mediaDo not use a solid water stream as it may scatter and spread fire.Specific hazards arising from the chemicalDuring fire, gases hazardous to health may be formed. Solvent vapors may form explosive mixtures with air.Special protective equipment and precautions for firefighters Selection of respiratory protection for firefighting: follow the general fire precautions indicated in the workplace. Self-contained breathing apparatus and full protective clothing must be worn in case of fire.Fire fightingequipment/instructions In case of fire and/or explosion do not breathe fumes. Wear full protective clothing, including helmet, self-contained positive pressure or pressure demand breathing apparatus, protective clothing and face mask. Move containers from fire area if you can do it without risk.General fire hazardsExtremely flammable aerosol - contents under pressure. Aerosol containers can explode when heated, due to excessive pressure build-up. The product is extremely flammable, and explosive vapor/air mixtures may be formed even at normal room temperatures. Gas may travel considerable distance to a source of ignition and flash back. May form explosive mixtures with air.6. Accidental release measuresPersonal precautions,protective equipment and emergency proceduresExtinguish all ignition sources. Avoid sparks, flames, heat and smoking. Ventilate. Do not breathe mist or vapor. Avoid contact with skin and eyes. Local authorities should be advised if significant spillages cannot be contained. Stay upwind. Do not touch damaged containers or spilled material unless wearing appropriate protective clothing. Keep people away from and upwind of spill/leak.Ventilate closed spaces before entering. Use personal protection recommended in Section 8 of the SDS.Methods and materials for containment and cleaning upELIMINATE all ignition sources (no smoking, flares, sparks or flames in immediate area). Stop the flow of material, if this is without risk. Prevent entry into waterways, sewers, basements or confined areas. Keep combustibles (wood, paper, oil, etc.) away from spilled material. This product is miscible in water.Large Spills: Dike the spilled material, where this is possible. Following product recovery, flush area with water. Cover with plastic sheet to prevent spreading. Absorb spillage with non-combustible, absorbent material.Small Spills: Clean surface thoroughly to remove residual contamination.Never return spills in original containers for re-use.Environmental precautionsPrevent further leakage or spillage if safe to do so. Do not contaminate water.7. Handling and storagePrecautions for safe handlingWash thoroughly after handling. Avoid prolonged exposure. Avoid contact with skin, eyes and clothing. Do not breathe mist or vapor. The product is extremely flammable. May form explosive mixtures with air. Ground container and transfer equipment to eliminate static electric sparks. Do not handle or store near an open flame, heat or other sources of ignition. Contents under pressure.Do not puncture. Do not expose to electric current or heat. Take precautionary measures against static discharges. All equipment used when handling the product must be grounded. Usenon-sparking tools and explosion-proof equipment. Use only in well-ventilated areas. Handle and open container with care.Conditions for safe storage,including any incompatibilitiesKeep away from heat, sparks and open flame. Store in cool place. Keep in a well-ventilated place.Keep container tightly closed. Keep in an area equipped with sprinklers. Keep this material away from food, drink and animal feed. Use care in handling/storage. Keep away from sources of ignition - No smoking.8. Exposure controls/personal protectionOccupational exposure limitsUS. OSHA Table Z-1 Limits for Air Contaminants (29 CFR 1910.1000)Value Type ComponentsPEL400 mg/m3Naphtha (petroleum),hydrotreated heavy (CAS 64742-48-9)100 ppm PEL 710 mg/m3n-Butyl acetate (CAS 123-86-4)150 ppm PEL1800 mg/m3Propane (CAS 74-98-6)1000 ppmUS. ACGIH Threshold Limit Values Value Type ComponentsSTEL 1000 ppm Butane (CAS 106-97-8)STEL 200 ppm n-Butyl acetate (CAS 123-86-4)TWA150 ppmUS. NIOSH: Pocket Guide to Chemical Hazards Value Type ComponentsTWA1900 mg/m3Butane (CAS 106-97-8)800 ppmUS. NIOSH: Pocket Guide to Chemical Hazards Value Type ComponentsTWA400 mg/m3Naphtha (petroleum),hydrotreated heavy (CAS 64742-48-9)100 ppm STEL 950 mg/m3n-Butyl acetate (CAS 123-86-4)200 ppm TWA710 mg/m3150 ppm TWA1800 mg/m3Propane (CAS 74-98-6)1000 ppmBiological limit values No biological exposure limits noted for the ingredient(s).Exposure guidelines Follow standard monitoring procedures.Appropriate engineering controlsExplosion proof exhaust ventilation should be used. Use process enclosures, local exhaustventilation, or other engineering controls to control airborne levels below recommended exposure limits. Use explosion-proof equipment. Provide easy access to water supply or an emergency shower.Individual protection measures, such as personal protective equipmentEye/face protectionWear goggles/face shield.Skin protectionHand protectionWear protective gloves. Be aware that the liquid may penetrate the gloves. Frequent change is advisable. Suitable gloves can be recommended by the glove supplier.OtherWear appropriate chemical resistant clothing. Wear appropriate chemical resistant gloves.Protective shoes or boots. Structural firefighters protective clothing provides limited protection in fire situations ONLY; it is not effective in spill situations. Wear chemical protective equipment that is specifically recommended by the Personal Protective Equipment manufacturer.Respiratory protectionIf engineering controls do not maintain airborne concentrations below recommended exposure limits (where applicable) or to an acceptable level (in countries where exposure limits have not been established), an approved respirator must be worn. Use a NIOSH/MSHA approved air purifying respirator as needed to control exposure. Consult with respirator manufacturer todetermine respirator selection, use, and limitations. Use positive pressure, air-supplied respirator for uncontrolled releases or when air purifying respirator limitations may be exceeded. Follow respirator protection program requirements (OSHA 1910.134 and ANSI Z88.2) for all respirator use. In case of inadequate ventilation or risk of inhalation of vapors, use suitable respiratory equipment.Thermal hazards Wear appropriate thermal protective clothing, when necessary.General hygiene considerationsHandle in accordance with good industrial hygiene and safety practice. Wash hands before breaks and immediately after handling the product. When using, do not eat, drink or smoke. Launder contaminated clothing before reuse. Remove and isolate contaminated clothing and shoes.9. Physical and chemical propertiesAppearanceCompressed liquefied gas.Physical state Liquid.Form Aerosol liquid.Color Clear.OdorSolvent.Odor threshold Not available.pHNo data available.Melting point/freezing point Not applicable.Initial boiling point and boiling range Not available.Flash point < -0.4 °F (< -18.0 °C)Evaporation rate Not applicable.Flammability (solid, gas)Flammable gas.Upper/lower flammability or explosive limitsFlammability limit - lower(%)1.8 % v/v Flammability limit - upper (%)9.5 % v/v Explosive limit - lower (%)Not available.Explosive limit - upper (%)Not available.Vapor pressure Not available.Vapor density Not available.Relative density 0.817Solubility(ies)Solubility (water)Insoluble in water.Partition coefficient (n-octanol/water)Not available.Auto-ignition temperature Not available.Decomposition temperature Not available.ViscosityNot available.Other informationVOC (Weight %)1.5 g Ozone/g product10. Stability and reactivityReactivity The product is non-reactive under normal conditions of use, storage and transport.Chemical stability Stable under normal temperature conditions. Heat may cause the containers to explode.Possibility of hazardous reactionsHazardous polymerization does not occur.Conditions to avoid Heat, sparks, flames, elevated temperatures. Pressurized container: Must not be exposed for temperatures above 50°C.Incompatible materials Strong oxidizing agents. Strong acids.Hazardous decomposition productsThermal decomposition or combustion may liberate carbon oxides and other toxic gases or vapors.11. Toxicological informationInformation on likely routes of exposureInhalationVapors/aerosol spray may irritate the respiratory system.Skin contact Causes skin irritation.Eye contact May cause eye irritation on direct contact.IngestionIngestion may cause irritation and malaise.Symptoms related to thephysical, chemical andtoxicological characteristics Skin irritation. Irritation of nose and throat. Irritating to mucous membranes.Information on toxicological effectsAcute toxicity May cause discomfort if swallowed.Test ResultsComponentsSpeciesButane (CAS 106-97-8)LC50Rat Inhalation Acute 658 mg/l, 4 HoursNaphtha (petroleum), hydrotreated heavy (CAS 64742-48-9)LD50Rabbit Dermal Acute > 2000 mg/kg LC50RatInhalation > 4.96 mg/l, 4 HoursTest Results ComponentsSpecies LD50RatOral > 5000 mg/kgPropane (CAS 74-98-6)LC50RatInhalation Acute 1355 mg/lSkin corrosion/irritation Causes skin irritation.Serious eye damage/eye irritationMay cause eye irritation.Respiratory or skin sensitizationRespiratory sensitizationNot classified.Skin sensitization Not a skin sensitizer.Germ cell mutagenicity Not classified.CarcinogenicityNot classified.OSHA Specifically Regulated Substances (29 CFR 1910.1001-1050)Not listed.Reproductive toxicityNot classified.Specific target organ toxicity -single exposureMay cause drowsiness or dizziness.Specific target organ toxicity -repeated exposure Not classified.Aspiration hazard May be fatal if swallowed and enters airways.Further informationDroplets of the product aspirated into the lungs through ingestion or vomiting may cause a serious chemical pneumonia. Organic solvents may be absorbed into the body by inhalation and cause permanent damage to the nervous system, including the brain.12. Ecological informationEcotoxicityToxic to aquatic life with long lasting effects.ComponentsTest ResultsSpeciesNaphtha (petroleum), hydrotreated heavy (CAS 64742-48-9)Aquatic IC50Algae <= 10 mg/l, 72 hours Algae EC50Crustacea <= 10 mg/l, 48 hours Daphnia LC50Fish<= 10 mg/l, 96 hoursFishPersistence and degradability No data is available on the degradability of this product.Bioaccumulative potentialNo data available for this product.Partition coefficient n-octanol / water (log Kow)Butane (CAS 106-97-8) 2.89Propane (CAS 74-98-6)2.36n-Butyl acetate (CAS 123-86-4)1.78Mobility in soil No data available.Mobility in general The product is insoluble in water.Other adverse effectsNo data available.13. Disposal considerationsDisposal instructionsDispose of this material and its container at hazardous or special waste collection point. Do not incinerate sealed containers. Do not allow this material to drain into sewers/water supplies.Dispose in accordance with all applicable regulations.Hazardous waste code Waste codes should be assigned by the user based on the application for which the product was used.Waste from residues / unused productsDispose of in accordance with local regulations.Contaminated packaging Dispose of in accordance with local regulations. Empty containers should be taken to an approvedwaste handling site for recycling or disposal. Do not puncture or incinerate even when empty. 14. Transport informationDOTUN1950UN numberAerosolsUN proper shipping nameTransport hazard class(es)2.1Class-Subsidiary risk2.1Label(s)Not applicable.Packing groupEnvironmental hazardsYesMarine pollutantRead safety instructions, SDS and emergency procedures before handling.Special precautions for user306Packaging exceptionsNonePackaging non bulkNonePackaging bulkIATAUN1950UN numberAerosolsUN proper shipping nameTransport hazard class(es)2.1Class-Subsidiary risk2.1Label(s)Not applicable.Packing groupYesEnvironmental hazards10LERG CodeRead safety instructions, SDS and emergency procedures before handling.Special precautions for userIMDGUN1950UN numberAEROSOLSUN proper shipping nameTransport hazard class(es)2.1Class-Subsidiary risk2.1Label(s)Not applicable.Packing groupEnvironmental hazardsYesMarine pollutantF-D, S-UEmSRead safety instructions, SDS and emergency procedures before handling. Read safety Special precautions for userinstructions, SDS and emergency procedures before handling.Not available.Transport in bulk according toAnnex II of MARPOL 73/78 andthe IBC CodeGeneral information IATA classification is not relevant as the material is not transported by air.15. Regulatory informationUS federal regulations This product is a "Hazardous Chemical" as defined by the OSHA Hazard CommunicationStandard, 29 CFR 1910.1200.All components are on the U.S. EPA TSCA Inventory List.This material contains one or more substances which requires export notification under TSCASection 12(b) and 40 CFR Part 707 Subpart D:Partially Fluorinated Acrylic CopolymerPMN Number: P-08-0643TSCA Section 12(b) Export Notification (40 CFR 707, Subpt. D)Regulated.OSHA Specifically Regulated Substances (29 CFR 1910.1001-1050)Not listed.CERCLA Hazardous Substance List (40 CFR 302.4)Butane (CAS 106-97-8)LISTEDn-Butyl acetate (CAS 123-86-4)LISTEDPropane (CAS 74-98-6)LISTEDSuperfund Amendments and Reauthorization Act of 1986 (SARA)Hazard categories Immediate Hazard - YesDelayed Hazard - NoFire Hazard - YesPressure Hazard - YesReactivity Hazard - NoSARA 302 Extremely hazardous substanceNot listed.SARA 311/312 HazardouschemicalYesSARA 313 (TRI reporting)Not regulated.Other federal regulationsClean Air Act (CAA) Section 112 Hazardous Air Pollutants (HAPs) ListNot regulated.Clean Air Act (CAA) Section 112(r) Accidental Release Prevention (40 CFR 68.130)Butane (CAS 106-97-8)Propane (CAS 74-98-6)Safe Drinking Water Act(SDWA)Not regulated.US state regulations This product does not contain a chemical known to the State of California to cause cancer, birthdefects or other reproductive harm.US. Massachusetts RTK - Substance ListButane (CAS 106-97-8)Naphtha (petroleum), hydrotreated heavy (CAS 64742-48-9)n-Butyl acetate (CAS 123-86-4)Propane (CAS 74-98-6)US. New Jersey Worker and Community Right-to-Know ActButane (CAS 106-97-8)Naphtha (petroleum), hydrotreated heavy (CAS 64742-48-9)n-Butyl acetate (CAS 123-86-4)Propane (CAS 74-98-6)US. Pennsylvania Worker and Community Right-to-Know LawButane (CAS 106-97-8)Naphtha (petroleum), hydrotreated heavy (CAS 64742-48-9)n-Butyl acetate (CAS 123-86-4)Propane (CAS 74-98-6)US. Rhode Island RTKButane (CAS 106-97-8)n-Butyl acetate (CAS 123-86-4)Propane (CAS 74-98-6)US. California Proposition 65Not Listed.International InventoriesCountry(s) or region Inventory name On inventory (yes/no)*Australian Inventory of Chemical Substances (AICS)No AustraliaDomestic Substances List (DSL)No CanadaNon-Domestic Substances List (NDSL)No CanadaInventory of Existing Chemical Substances in China (IECSC)No ChinaEuropean Inventory of Existing Commercial Chemical Substances (EINECS)NoEuropeEuropean List of Notified Chemical Substances (ELINCS)Yes EuropeInventory of Existing and New Chemical Substances (ENCS)No JapanCountry(s) or region Inventory nameOn inventory (yes/no)*Existing Chemicals List (ECL)NoKorea New Zealand InventoryNo New Zealand Philippine Inventory of Chemicals and Chemical Substances (PICCS)No Philippines*A "Yes" indicates this product complies with the inventory requirements administered by the governing country(s).A "No" indicates that one or more components of the product are not listed or exempt from listing on the inventory administered by the governing country(s).Toxic Substances Control Act (TSCA) InventoryNoUnited States & Puerto Rico16. Other information, including date of preparation or last revisionIssue date 24-February-2015Revision date -Version #01NFPA ratings1References HSDB® - Hazardous Substances Data BankRegistry of Toxic Effects of Chemical Substances (RTECS)DisclaimerThe information in this (M)SDS was obtained from sources which we believe are reliable but cannot guarantee. Additionally, your use of this information is beyond our control and may be beyond our knowledge. Therefore, the information is provided without any representation or warranty express or implied.。
塑胶类英语词汇大全

废料粉碎机---scrap grinder顶出板,脱模板---stripper plate应力龟裂---stress cracking环境应力龟裂试验---environmental stress cracking test行程,衝程---stroke注道,注道料---sprue注道衬套,浇口衬套---sprue bush成形压力,模製压力---molding pressure成形温度,模製温度---molding temperature成形循环,成形週期---molding cycle成形时间,模製时间---molding time成形收缩,模压收缩---mold shrinkage, molding shrinkage窄浇口,限制形浇口---restricted gate剪切强度,抗剪强度---shear strength增亮剂---brightening agent,optical brightener,optical whitening agent 加速试验---accelerated test加速老化---accelerated ageing塑性变形---plastic deformation塑性流动---plastic fiow翘曲---warp(ing),warpage抗臭氧性---ozone resistance抗臭氧试验---ozone resistance test耐天侯性---weatherability,weather resistance耐光性---light resistance,light fastness天侯老化试验---weathering test耐酸性---acid resistance耐衝击性---impact resistance褪色---fading,discoloration耐蚀性---corrosion resistance拉桿,导柱---tie-bar拉桿间距---tie-bar distance多模穴模具---multi-cavity mold双色射出成形---double-shot molding超音(声)波镶嵌---ultrasonic inserting超音(声)波焊接---ultrasonic welding顶出,脱模---ejection顶出组合---ejector顶出板---ejector plate,knock-out plate顶出桿,脱模桿---knock-out bar,ejector rod无光面---dull surface低压射出成形法---low pressure injection molding硬度计---durometer电镀---electroplating,electrodeposition电铸模具---electroformed mold公差,容差---tolerance冷料---cold slug冷料井,冷料窝---cold slug well回程销,覆归销---surface pin冷热骤变试验---thermal shock test热应力龟裂---thermal stress cracking,TSC 侧向浇口---side gate侧向模蕊(心型)销---side draw pin砂磨---sanding喷砂,打砂---sand blast修饰,涂饰,打光---finishing自断浇口,剪切浇口---shear gate紫外线---ultraviolet, UV紫外线稳定剂---UV stabilizer紫外线吸收剂---UV absorber压花---embossing压花机---embossing machine喷霜,起霜---blooming exudation鯊皮斑---shark skin射出压力---injection pressure射出成形---injection molding射出成形机---injection molding machine 射出成形模具---injection mold射出装置---injection unit射出速度---injection speed射出喷嘴,注料嘴---injection nozzle射出容量---machine shot capacity射出率(量)---injection rate煮沸试验---boiling test充填不足,缺料---short shot手动模具---hand mold,loose mold手动油压机---hand press缩窝,凹孔---shrinkage pool衝击试验---inpact test衝击强度---impact strength烧结法,粉铸法---sintering烧结成形法---sinter molding模板---mold plate注射,射料---shot硅橡胶---silicone rubber真空成形---vacuum forming珠光顏料---pearlescent pigment浸渍涂装---dip coating人造皮革---artificial leather嵌件---insert嵌件销---insert pin气胀真空成形---air assist forming空气隙---air gap空气顶出---air ejection永久伸长---permanent elongation,tension set永久变形---permanent set,permanent deformation蚀刻,侵蚀---etching应力---stress应力鬆弛---stress relaxation应力龟裂---stress cracking应力集中---stress concentration应力断裂,应力破坏---stress rupture应力.应变曲线---stress-strain curve应力.应变图---stress-strain diagram托板,模板---retainer plate硬度---hardness合模机构---mold clamping mechanism合模力,闭模力---locking force,clamping force开模力---mold opening force悬臂梁---cantilever beam润滑剂---lubricant模具---mold,Tools,T ooling模温度控制器---mold temperature controller模具尺寸---mold size加热管套(料筒)---heating cylinder加热板---heating plate凸轮---cam玻璃纤维---glass fiber,fibrous glass玻璃纤维强化热塑塑胶---fiber glass reinforced thermoplastics,FRTP,glass fiber reinforced thermoplasitcs,GRTP玻璃纤维强化塑胶---glass fiber reinforced plastics,GRP,fiber galss reinforced plastics,FRP.感光聚合物---photopolymer,photo-sensitive polymer镜面抛光---mirror polishing龟裂---cracking龟裂---crack颗粒料---granule石墨---graphite石墨纤维---graphite fiber间隙, 隙距---clearance模蕊,蕊片,蕊线,蕊孔---core成孔销,模蕊销---core pin成孔销托板---core pin platephenolic resin 酚醛树脂plastic 塑胶polyacrylic acid 聚丙烯酸PAPpolyamide 耐龙PA polybutyleneterephthalate 聚对苯二甲酸丁酯PBT polycarbonate 聚碳酸酯PC polyethyleneglycol 聚乙二醇PFG polyethyleneoxide 聚氧化乙烯PEO polyethyleneterephthalate 聚乙醇对苯PETP polymetylmethacrylate 聚甲基丙烯酸甲酯PMMA polyoxymethylene 聚缩醛POMpolyphenylene oxide 聚硫化亚苯polyphenyleneoxide 聚苯醚PPO polypropylene 聚丙烯PPpolystyrene 聚苯乙烯PS polytetrafluoroethylene 聚四氟乙烯PTFE polytetrafluoroethylene 聚四氟乙烯polythene 聚乙烯PEpolyurethane 聚氨基甲酸酯PU polyvinylacetate 聚醋酸乙烯PVAC polyvinylalcohol 聚乙烯醇PVApolyvinylbutyral 聚乙烯醇缩丁醛PVB polyvinylchloride 聚氯乙烯PVC polyvinylfuoride 聚氟乙烯PVF polyvinylidenechloride 聚偏二氯乙烯PVDC prepolymer 预聚物silicone resin 矽树脂thermoplastic 热塑性thermosetting 热固性thermosetting plastic 塑胶unsaturated polyester 不饱和聚酯树脂入水:gate进入位:gate location水口形式:gate type大水口:edge gate细水口:pin-point gate水口大小:gate size转水口:switching runner/gate唧嘴口径:sprue diameter流道: runner热流道:hot runner,hot manifold热嘴冷流道: hot sprue/cold runner唧嘴直流: direct sprue gate圆形流道:round(full/half runner流道电脑分析:mold flow analysis流道平衡:runner balance热嘴:hot sprue热流道板:hot manifold发热管:cartridge heater探针: thermocouples插头:connector plug插座:connector socket密封/封料:seal运水:water line喉塞:line lpug喉管:tube塑胶管:plastic tube快速接头:jiffy quick connector plug/socker 模具零件:mold components三板模:3-plate mold二板模:2-plate mold边钉/导边:leader pin/guide pin边司/导套:bushing/guide bushing中托司:shoulder guide bushing中托边L:guide pin顶针板:ejector retainner plate托板:support plate螺丝:screw管钉:dowel pin开模槽:ply bar scot内模管位:core/cavity inter-lock顶针:ejector pin司筒:ejector sleeve司筒针:ejector pin推板:stripper plate缩呵:movable core,return core core puller 扣机(尼龙拉勾):nylon latch lock斜顶:lifter模胚(架):mold base上内模:cavity insert下内模:core insert行位(滑块):slide镶件:insert压座/斜鸡:wedge耐磨板/油板:wedge wear plate压条:plate撑头: support pillar唧嘴:sprue bushing挡板:stop plate定位圈:locating ring锁扣:latch扣鸡:parting lock set推杆:push bar栓打螺丝:S.H.S.B顶板:eracuretun活动臂:lever arm分流锥:spure sperader水口司:bush垃圾钉:stop pin隔片:buffle弹弓柱:spring rod弹弓:die spring中托司:ejector guide bush中托边:ejector guide pin镶针:pin销子:dowel pin波子弹弓:ball catch喉塞: pipe plug锁模块:lock plate斜顶:angle from pin斜顶杆:angle ejector rod尼龙拉勾:parting locks活动臂:lever arm复位键、提前回杆:early return bar气阀:valves斜导边:angle pin术语:terms承压平面平衡:parting surface support balance模排气:parting line venting回针碰料位:return pin and cavity interference模总高超出啤机规格:mold base shut hight顶针碰运水:water line interferes withejector pin料位出上/下模:part from cavith (core) side模胚原身出料位:cavity direct cut on A-plate,core direct cut on B-plate. 不准用镶件:Do not use (core/cavity) insert用铍铜做镶件:use beryllium copper insert初步(正式)模图设计:preliinary (final) mold design反呵:reverse core弹弓压缩量:spring compressed length稳定性好:good stability,stable强度不够:insufficient rigidity均匀冷却:even cooling扣模:sticking热膨胀:thero expansion公差:tolorance铜公(电极):copper electrodecompre sion molding压缩成型flash mold溢流式模具plsitive mold挤压式模具split mold分割式模具cavity型控母模core模心公模taper锥拔leather cloak仿皮革shiver饰纹flow mark流痕welding mark溶合痕post screw insert螺纹套筒埋值self tapping screw自攻螺丝striper plate脱料板piston活塞cylinder汽缸套chip细碎物handle mold手持式模具encapsulation molding低压封装成型、射出成型用模具two plate两极式(模具)well type蓄料井insulated runner绝缘浇道方式hot runner热浇道runner plat浇道模块valve gate阀门浇口band heater环带状的电热器spindle阀针spear head刨尖头slag well冷料井cold slag冷料渣air vent排气道welding line熔合痕eject pin顶出针knock pin顶出销return pin回位销反顶针sleave套筒stripper plate脱料板insert core放置入子runner stripper plate浇道脱料板guide pin导销eject rod (bar)(成型机)顶业捧subzero深冷处理three plate三极式模具runner system浇道系统stress crack应力电裂orientation定向sprue gate射料浇口,直浇口nozzle射嘴sprue lock pin料头钩销(拉料杆) slag well冷料井side gate侧浇口edge gate侧缘浇口tab gate搭接浇口film gate薄膜浇口flash gate闸门浇口slit gate缝隙浇口fan gate扇形浇口dish gate因盘形浇口diaphragm gate隔膜浇口ring gate环形浇口subarine gate潜入式浇口tunnel gate隧道式浇口pin gate针点浇口Runner less无浇道(sprue less)无射料管方式long nozzle延长喷嘴方式sprue浇口;溶渣。
13Cr和超级13Cr不锈钢在CaCl2完井液中的腐蚀行为研究

华中科技大学硕士学位论文摘要本论文研究的主要目的是为了弄清13Cr钢和超级13Cr不锈钢在含有CO2的完井液盐水环境中,温度、盐水浓度和应变对其SCC的影响,研究溶解氧与醋酸含量对SCC的影响以及试样在有无应变条件下的腐蚀电化学行为之间的区别。
论文采用了四点弯曲法、U形环试验、表面分析方法和电化学测试技术(主要是恒电位极化、快/慢动电位极化和电化学噪声)主要讨论了温度、应变、溶解氧含量和醋酸对两种金属材料在有应变和无应变条件下的腐蚀行为的影响。
13Cr不锈钢的研究结果表明:13Cr不锈钢在不除氧的33wt%CaCl2盐水中,在100℃和150℃主要产生均匀腐蚀和点蚀。
在除氧的33wt%CaCl2盐水中,在100℃和150℃主要产生均匀腐蚀和裂纹。
醋酸的加入加速了13Cr不锈钢的均匀腐蚀,且随着其浓度的增加腐蚀速率增加;在不除氧条件下醋酸能加速点蚀发展,而在除氧条件下有抑制裂纹发展的趋势。
体系温度提高同样促进了13Cr不锈钢的腐蚀速率。
电化学试验的结果和挂片试验的结果相一致,通过电化学噪声证实了在研究条件下13Cr钢将在很短的时间内萌发点蚀。
超级13Cr不锈钢的研究结果表明:醋酸能够提高超级13Cr钢在不除氧33wt% CaCl2盐水中的SCC敏感性;但是,在除氧条件下醋酸却能降低超级13Cr钢的SCC 敏感性。
SEM形貌图显示超级13Cr钢在33wt% CaCl2盐水中1.0MPa CO2和150℃条件下为沿晶型SCC。
超级13Cr钢在除氧33wt% CaCl2盐水中1.0MPa CO2和150℃条件下,当醋酸存在时,钝化能力显著降低。
恒电位极化和动电位极化曲线测试结果证实了超级13Cr钢SCC起源于第二个活化-钝化转化区的阳极溶解。
关键词:13Cr不锈钢,超级13Cr不锈钢,完井液,CO2,SCC,溶解氧,醋酸华中科技大学硕士学位论文AbstractThe purpose of this work was to clarify the effect of temperature, brine concentration, dissolved O2, acetic acid and the strain on SCC, and the difference in corrosion electrochemical behavior between specimens with and without stress for 13Cr and super 13Cr stainless steels in completion fluids containing CO2. The effects were investigated by using the four-point bend test, U-bend test, the surface analysis and electrochemical measurements (potentiostatic polarization, potentiodynamic polarization and electrochemistry noise).The study results for 13Cr stainless steel showed that in 33% CaCl2brine with no deoxidization, 13Cr stainless steel mainly suffered general corrosion and pitting corrosion both at 100℃and 150℃; however, in 33% CaCl2 brine with deoxidization, 13Cr stainless steel mainly suffered general corrosion and cracks both at 100℃and 150℃. The adding of acetic acid could accelerate the general corrosion and the general corrosion rate increase with the enhancement of the acetic acid concentration. And the pitting corrosion was overspreaded by the adding of the acetic acid concentration in 33% CaCl2brine with no deoxidization, but the cracks was restrained by the adding of the acetic acid concentration in 33% CaCl2brine with deoxidization. The corrosion rate was also accelerated by the system temperature. The results of electrochemistry test were consistent with the exposure experiment results, and the pitting corrosion bourgeon of 13Cr stainless steel under the test condition in short time was confirmed by electrochemistry noise spectrum.The results for super 13Cr stainless steel showed that acetic acid increased the stress corrosion cracking susceptivity of super 13Cr stainless steel in 33wt% CaCl2 brine at 150℃and 1.0MPa CO2 under no deaerated condition, but it reduced the SCC susceptivity under deaerated condition. SEM morphology showed that SCC of super 13Cr stainless steel was intergranular cracking mode in the 33wt% CaCl2brine at 150℃and 1.0MPa CO2. The passivate ability of super 13Cr stainless steel was weakened in the deaerated 33wt% CaCl2华中科技大学硕士学位论文brine at 150℃and 1.0MPa CO2especially presence of acetic acid. The results of potentiostatic polarization and potentiodynamic polarization experiments demonstrated that the cracking is initiated by the anodic dissolution in the secondary active-passive transition region.Keyword: 13Cr stainless steel, super 13Cr stainless steel, completion fluid,CO2, SCC, dissolved oxygen, acetic acid华中科技大学硕士学位论文目录摘要 ..................................................................................................................(I) ABSTRACT.................................................................................................... (II) 1绪论1.1前言 (1)1.2金属材料的SCC (2)1.3不锈钢SCC研究现状 (9)1.4课题的提出、意义及研究内容与目的 (15)2 实验装置和方法2.1实验材料 (17)2.2实验介质 (20)2.3实验装置 (21)2.4实验方法 (24)2.5实验分析 (25)3 13CR钢在含CO2完井液中的腐蚀行为3.1温度和应变对13C R不锈钢腐蚀行为的影响 (26)3.2溶解氧和醋酸对13C R不锈钢腐蚀行为的影响 (29)3.313C R钢腐蚀表面分析结果 (29)3.413C R不锈钢腐蚀电化学行为 (31)3.5本章结论 (34)4 超级13CR钢在完井液中的SCC4.1溶液盐浓度对超级13C R不锈钢SCC的影响 (36)华中科技大学硕士学位论文4.2应变对超级13C R钢SCC的影响 (36)4.3温度对超级13C R不锈钢SCC的影响 (38)4.4体系溶解氧和醋酸含量对超级13C R钢SCC的影响 (39)4.5试样表面分析结果 (40)4.6超级13C R钢电化学测试 (45)4.7讨论 (49)4.8结论 (50)5 总结与创新5.1 本文主要结论 (51)5.2本文创新点 (52)致谢 (53)参考文献 (54)附录1 攻读硕士学位期间发表学术论文目录 (59)华中科技大学硕士学位论文1 绪论1.1 前言金属腐蚀遍及国民经济和国防建设的各个领域,危害十分严重[1]。
Chapter 4-corrosion under stress

一、应力腐蚀断裂的特征
具备三条件:敏感材料,特定环境和拉伸应力。 如锅炉钢在碱液中的“碱脆”;低碳钢在硝酸 盐中的“硝脆”,奥氏体不锈钢在含氯离子液 中的“氯脆”;黄铜在氨气中的“氨脆”。
5
敏感材料
certain alloys从金到钛、锆,几乎所有金属的 合金在特定环境中都有某种应力腐蚀敏感性。 纯金属不会发生应力腐蚀开裂。 99.99%Fe在硝酸盐溶液中难以开裂,含0.04%C 即可发生硝脆。
11
二、应力腐蚀开裂的特征
1.典型的滞后破坏
2.裂纹分为晶间型、穿晶型和混合型
3.裂纹扩展速度比均匀腐蚀快约106倍 4.SCC开裂是一种低应力的脆性断裂
12
1.SCC是典型的滞后破坏
应力腐蚀断裂是一种典型的滞后破坏,需经 一定时间的裂纹形核、裂纹亚临界扩展,最 终达到临界尺寸,发生失稳断裂。 存在一个孕育期90%(裂纹成核),裂纹 扩展期(成核到临界尺寸),快速断裂期。
6
7
特定介质
某种合金的应力腐蚀开裂只是对特定介质敏感。 通常合金对引起应力腐蚀的环境是惰性的,表 面往往存在钝化膜。这种特定的环境并不要大 量存在才造成应力腐蚀。如空气中少量的氨气, 甚至鼻子感觉不出就会造成黄铜的氨脆。 材料与环境的交互作用反映在电位上就是SCC 一般发生在活化-钝化或钝化-过钝化的过渡 区电位范围,即钝化膜不完整的电位区间
28
Chloride Attack: Waste water with a high chloride content caused rapid corrosion of this stainless steel mixing valve.
29
Ammonia Attack :A few parts per million of ammonia in boiler feed water caused failure of this bronze valve.
STRESS-CORROSION MONITORING DEVICE AND EVALUATION

专利名称:STRESS-CORROSION MONITORING DEVICEAND EVALUATION OF DETERIORATIONDEGREE OF PENETRATING MEMBER发明人:DEBITSUDO HOOKU ROOTEI,デビッド ホークローティ,DEBITSUDO ANSONII EDEN,デビッドアンソニー エデン申请号:JP特願平6-17865申请日:19940117公开号:JP特開平7-72110A公开日:19950317专利内容由知识产权出版社提供专利附图:摘要:PURPOSE: To monitor the local corrosion of a structural member penetrating a reactor vessel by exposing the electrodes of an electrochemical sensor together with a through member to electrolyte to form an electrochemical detecting cell so that the deterioration of the wall can be evaluated with a voltage/current signal arising in a signal conductor. CONSTITUTION: A through pipe 32 is a conductor subjected to stresscorrosion in operating a nuclear reactor, a part of which is located at a reactor vessel and subjected to chemical action by stress, cooling material or electrolyte 50 according to temperature and pressure conditions. The wall of the through pipe 32 may be corrode and crack and so the proceeding degree of corrosion is evaluated. For the evaluation of corrosion, chemical reaction giving influence to the through pipe 32 is electrically detected. A cell in an electrochemical sensor 64 has an operating electrode and a reference electrode, both of which are arranged in areas on the wall 82 of the pipe 32 to be monitored to make response to corrosion in the respective areas. A signal line 92 symbolizes an electric potential, a potential level and the dispersion degree of a current flowing in the electrolyte 50. The signal shows the level of corrosion and the degree of stress corrosion cracking.申请人:WESTINGHOUSE ELECTRIC CORP ,ウエスチングハウス・エレクトリック・コーポレイション地址:アメリカ合衆国、ペンシルベニア州、ピッツバーグ、ゲイトウェイ・センター(番地なし)国籍:US代理人:加藤 紘一郎 (外2名)更多信息请下载全文后查看。
M-TP-710 Material and Equipment Standard for Thermal Insulation 保温

MATERIAL AND EQUIPMENT STANDARDFORTHERMAL INSULATIONORIGINAL EDITIONDEC. 1997This standard specification is reviewed andupdated by the relevant technical committee onFeb. 2003. The approved modifications areincluded in the present issue of IPS.This Standard is the property of Iranian Ministry of Petroleum. All rights are reserved to the owner. Neither whole nor any part of this document may be disclosed to any third party, reproduced, stored in any retrieval system or transmitted in any form or by any means without the prior written consent of the Iranian Ministry of Petroleum.0. INTRODUCTIONThis Standard consists of nine parts as follows:Part I: Mineral Fiber Preformed Pipe Thermal Insulation.Part II: Mineral Fiber Block and Board Thermal Insulation.Part III: Mineral Fiber Blanket and Blanket Type Pipe Thermal Insulation.Part IV: Calcium Silicate Preformed Block and Pipe Thermal Insulation.Part V: Cellular Glass/Foam Glass Thermal Insulation.Part VI: Cork board and Cork pipe Thermal Insulation.Part VII: Spray-Applied Rigid Cellular Polyurethane (PUR) and Polyisocyanurate (PIR) Thermal Insulation.Part VIII: Preformed Rigid-Cellular Polyurethane (PUR) and Polyisocyanurate (PIR) Thermal Insulation.Part IX: Miscellaneous Materials to be Used with Thermal Insulation.Parts I through V are categorized as Hot Thermal Insulation whereas Parts VI, VII and VIII are classified as Cold Thermal Insulation.Note:Cellular glass/foam glass hot thermal insulation may also be used as cold thermal insulation detail of which has been given in volume one.PART IMINERAL FIBER PREFORMED PIPETHERMAL INSULATIONThis Standard is the property of Iranian Ministry of Petroleum. All rights are reserved to the owner. Neither whole nor any part of this document may be disclosed to any third party, reproduced, stored in any retrieval system or transmitted in any form or by any means without the prior written consent of the Iranian Ministry of Petroleum.CONTENTS : PAGE No.1. SCOPE (2)2. REFERENCES (2)3. DEFINITIONS AND TERMINOLOGY (2)4. UNITS (3)5. MATERIALS AND MANUFACTURE (3)6. GENERAL PROPERTIES (3)7. CHEMICAL COMPOSITION (4)8. PHYSICAL PROPERTIES (5)9. SHAPES, SIZES AND DIMENSIONS (6)10. DIMENSIONAL TOLERANCES (6)11. WORKMANSHIP (6)12. SAMPLING (7)13. INSPECTION AND REJECTION (7)14. PACKAGING AND MARKING (7)15. STORAGE (8)APPENDICES:APPENDIX A ORDERING INFORMATION (9)1. SCOPE1.1 This Standard specification covers the minimum requirements for composition, sizes, dimensions, physical properties, inspection, packaging and marking of mineral wool preformed pipe insulation for use on pipe surfaces up to 600°C. If insulation is to be used at higher temperature the actual temperature limits shall be as agreed upon between the manufacturer and the Company.1.2 For satisfactory performance, properly installed protective vapor barriers shall be used in low-temperature applications to prevent movement of moisture through or around the insulation towards the colder surface.Note:This standard specification is reviewed and updated by the relevant technical committee on Feb. 2003. The approved modifications by T.C. were sent to IPS users as amendment No. 1 by circular No. 191 on Feb. 2003. These modifications are included in the present issue of IPS.2. REFERENCESThroughout this Standard the following dated and undated standards/codes are referred to. These referenced documents shall, to the extent specified herein, form a part of this standard. For dated references, the edition cited applies. The applicability of changes in dated references that occur after the cited date shall be mutually agreed upon by the Company and the Vendor. For undated references, the latest edition of the referenced documents (including any supplements and amendments) applies.ASTM (AMERICAN SOCIETY FOR TESTING AND MATERIALS)C 585 "Practice for Inner and Outer Diameters of Rigid Thermal Insulationfor Nominal Sizes of Pipe and Tubing (NPS System)"C 390 "Criteria for Sampling and Acceptance of Preformed ThermalInsulation Lots"C 356 "Test Method for Linear Shrinkage of Preformed High TemperatureThermal Insulation Subjected to Soaking Heat"C 335 "Test Method for Steady State Heat Transfer Properties ofHorizontal Pipe Insulation"C 547C 871 "Test Methods for Chemical Analysis of Thermal InsulationMaterials for Leachable Chloride, Fluoride, Silicate, and SodiumIons"C 692 "Test Methods for Evaluating the Influence of Thermal InsulationWicking-Type on the External Stress Corrosion Cracking Tendencyof Austenitic Stainless Steel"C11043. DEFINITIONS AND TERMINOLOGYJacketA form of facing applied over insulation. It may be integral with the insulation, or field applied using sheet materials.Mineral fiberInsulation composed principally of fibers manufactured from rock, slag, or glass with or without binders.Pipe insulationInsulation in a form suitable for application to cylindrical surfaces.Rock woolMineral fiber produced from naturally occurring igneous rock.Slag woolMineral fiber produced from steel mill slag.Soaking heatA test condition in which the specimen is completely immersed in an atmosphere maintained at a controlled temperature.Water-vapor-permeabilityThe time rate of water-vapor transmission through unit area of flat material of unit thickness induced by unit vapor pressure difference between two specific surfaces, under specified temperature and humidity condition.4. UNITSThis Standard is based on International System of Units (SI), except where otherwise specified.5. MATERIALS AND MANUFACTURE5.1 CompositionThe mineral fiber preformed thermal insulation for pipes shall be manufactured from mineral fiber substances such as rock or slag from a molten state into fibrous form and shall be made rigid with organic binder. The binder shall be phenolic or manufacturer Standard.5.2 Jacket (facing)The pipe insulation may be jacketed or plain as will be specified by the purchaser, if jacketed, the type of jacket to be aluminum foil or kraft paper as is specified by the Purchaser.6. GENERAL PROPERTIESThe mineral fiber preformed pipe insulation shall have the general properties as follows:6.1 Insulation shall have suitable resistance to sunlight in order to minimize shrinkage below the limit specified in Clause 8.1 and have as low water vapor permeability as possible.6.2 It shall be non-combustible and shall be resistant to vermins and fungus, be free from objectionable odors, and shall not react with process chemicals present.6.3 The insulation shall be asbestos free and shall have not health hazard in case of contact or during labor working.6.4 The insulation shall have only traces of corrosive materials; e.g. water-soluble chlorides which attack stainless steels or alkalinity which attacks aluminum jacketing.7. CHEMICAL COMPOSITION7.1 Chemical composition for major constituent of mineral fiber preformed pipe insulating materials shall be as following when tested by spectrometric methods:SiO2= 30 - 45 weight %Al2O3= 8 - 15 weight %TiO2= 2 - 4 weight %Fe2O3= 2.5 max. weight %CaO = 30 - 35 weight %MgO = 6 - 12 weight %Na2O = 0 - 1 weight %K2O = 0 – 1 weight %P2O5= 0 - 1 weight %Water soluble chloride: Approximately 6 mg/kg when tested in accordance with ASTM C871.7.2 If water-soluble chloride content of the insulation material exceeds the amount specified in the chemical composition above, sufficient amounts of sodium silicate (Na2SiO3) inhibitor shall be added to the insulation material. Acceptable proportion of sodium plus silicate ions to the chlorides ions as found by leaching from the insulation when tested in accordance with ASTM Test Method C871 shall be in accordance with Fig. 1.1.With reference to Fig. 1.1 the minimum allowable value of sodium plus silicate will be 50 ppm when tested in accordance with ASTM Test Method C692, providing leachable (water soluble) chloride be higher than 10 mg per kg of insulation material.7.3 The pH of leach water shall be measured, in accordance with ASTM Test Methods C871, and shall be greater than 7.0 but not greater than 11.7 at 25°C.Cl ppmACCEPTABILITY OF INSULATION MATERIAL ON THE BASIS OF THE PLOT POINTSOF THE Cl AND THE (Na+SiO3) ANALYSISFig. 1.18. PHYSICAL PROPERTIESThe physical properties of mineral fiber preformed pipe insulation shall be as follows:8.1 Linear ShrinkageLinear shrinkage for length shall be maximum 2% after soaking heat and tested in accordance with ASTM Test Method C356 at manufacturer’s temperature limit.8.2 DensityThe minimum density shall be agreed between purchaser and manufacturer. As a reference the value 48 Kg/m3 for the temperature up to 450o C and 96 Kg/m3 for the temperature up to 650o C should be used in accordance with ASTM test method C302.8.3 Thermal ConductivityMaximum thermal conductivity value shall be 0.065 W/mK at 200°C and 0.073 w/mK up to 450o C in accordance with ASTM Test Method C335.8.4 Water Vapor SorptionWater vapor sorption shall be minimum 5% by weight in accordance with ASTM test method C1104.9. SHAPES, SIZES AND DIMENSIONS9.1 The mineral fiber preformed pipe insulation shall be supplied as hollow cylinders, split lengthwise on one or both sides of the cylindrical axis (depending on Company request) and shall be furnished in sections or segments in a length of 1 meter unless otherwise agreed between company and manufacturer.9.2 The minimum and maximum thickness shall be specified by the Company but in no case shall be less than 13 mm.9.3 Thicknesses greater than 150 mm may be furnished in multiple layers.9.4 Dimensional standard of inner and outer diameter of insulation for nominal pipe size shall be in accordance with ASTM C585.10. DIMENSIONAL TOLERANCES10.1 The average measured length and thickness of any individual section or segment shall not differ from the specified dimensions by more than the following:DIMENSION TOLERANCELength Thickness±3mm±3%(see 9.2 for minimum thickness)10.2 When installed on the pipe of the specified size, sections shall fit snugly and shall have tight longitudinal and circumferential joints.11. WORKMANSHIPThe insulation shall not have visible defects that will adversely affect its installation or service quality.12. SAMPLINGThe insulation shall be sampled for the purpose of tests in accordance with criteria ASTM C390. 13. INSPECTION AND REJECTION13.1 Inspection13.1.1 The manufacturer and/or supplier shall be responsible for carrying out the tests and inspections required by this Standard specification, using his own or other reliable facilities, and he shall maintain complete records of all such tests and inspections. Such records shall be available for review by the Purchaser. The manufacturer and/or supplier shall furnish to the Purchaser a certificate of inspection stating that each lot has been sampled, tested, and inspected in accordance with this Standard specification and has been found to meet the requirements specified.13.1.2 The supplier shall afford the Purchaser’s inspector all reasonable facilities necessary to satisfy that the material is being produced and furnished in accordance with this Standard specification. Such inspections in no way relieve the manufacturer and/or supplier of his responsibilities under the term of this Standard specification.13.1.3 The Purchaser reserves the right to perform any inspections set forth in this Standard specification where such inspections are deemed necessary to assure that supplies and services comform to the prescribed requirements.13.1.4 The Purchaser’s inspector shall have access to the material subject to inspection for the purpose of witnessing the selection of the samples. The preparation of the test pieces, and the performance of the test(s). For such tests, the inspector shall have the right to indicate the pieces from which the samples will be taken in accordance with the provisions of this Standard specification.13.2 Rejection13.2.1 If the inspection of the sample shows failure to conform to the requirements of this Standard specification, a second sample from the same lot shall be tested and the results of this retest averaged with the result of the original test.13.2.2 Upon retest as described in 13.2.1 failure to conform to this Standard specification shall constitute grounds for rejection.13.2.3 In case of rejection, the manufacturer or supplier shall have the right to reinspect the rejected lot and resubmit the lot for inspection after removal of that portion of the lot not conforming to the specified requirement.14. PACKAGING AND MARKING14.1 Packaging14.1.1 Unless otherwise specified by the Purchaser, the mineral fiber preformed pipe insulation shall be packaged in manufacturer’s standard commercial container approved by the Purchaser and considering the following:14.1.2 Overseas consignments shall be packed in double-corrugated cartons incorporating weather proof paper because of greater handling involved and possibly of exposure to wet conditions. If the size of sections exceeds the practical size for cartons, wooden or strong mesh crates may be used.14.1.3 Mineral fiber preformed pipe insulations materials shall not be unpacked at site until is required for use.14.1.4 Stacking of packed mineral fiber preformed pipe insulation during transportation shall be in accordance with the manufacturer’s recommendation.14.2 Marking14.2.1 Unless otherwise agreed between purchaser and manufacturer and/or supplier, containers shall be marked as follows:- purchase order No.;- name and type of material;- thickness of insulation and pipe size in case of pipe insulation;- quantity of material in the container;- date of manufacturing;- supplier’s name;- origin of manufacturing;- destination.15. STORAGE15.1 The insulation shall be stored in a dry atmosphere under cover and inspected at interval not exceeding three months.15.2 Cartons shall be stored end up and be stacked no more than three high.APPENDICESAPPENDIX AORDERING INFORMATIONThe following information shall be supplied with purchase order:a) The number and date of this IPS Standard,b) the dimension of the sections required,c) the finish required,d) the maximum service temperature to which the product will be subjected,e) a note of any adverse condition in the environment of insulation or special requirements,f) density.PART IIMINERAL FIBER BLOCK AND BOARDTHERMAL INSULATIONThis Standard is the property of Iranian Ministry of Petroleum. All rights are reserved to the owner. Neither whole nor any part of this document may be disclosed to any third party, reproduced, stored in any retrieval system or transmitted in any form or by any means without the prior written consent of the Iranian Ministry of Petroleum.CONTENTS : PAGE No.1. SCOPE (12)2. REFERENCES (12)3. DEFINITIONS AND TERMINOLOGY (12)4. UNITS (13)5. MATERIAL AND MANUFACTURE (13)6. GENERAL PROPERTIES (13)7. CHEMICAL COMPOSITION (14)8. PHYSICAL PROPERTIES (15)9. SIZE OF BOARD AND SLAB (16)10. DIMENSIONAL TOLERANCES (16)11. WORKMANSHIP (16)12. SAMPLING (17)13. INSPECTION AND REJECTION (17)14. PACKAGING AND MARKING (17)15. STORAGE (18)APPENDICES:APPENDIX A ORDERING INFORMATION (19)1. SCOPE1.1 This Standard specification covers the minimum requirements for chemical composition, dimensions, physical properties, inspection, packaging and marking of rigid and semi-rigid mineral fiber block and board thermal insulation for use on surfaces up to 540°C. If the insulation is to be used at higher temperatures the actual temperature limits shall be as agreed upon between the manufacturer and Company.1.2 For satisfactory performance, properly installed protective vapor barriers must be used in low temperature application to prevent movement of moisture through or around the insulation towards the colder surface.2. REFERENCESThroughout this Standard the following dated and undated standards/codes are referred to. These referenced documents shall, to the extent specified herein, form a part of this standard. For dated references, the edition cited applies. The applicability of changes in dated references that occur after the cited date shall be mutually agreed upon by the Company and the Vendor. For undated references, the latest edition of the referenced documents (including any supplements and amendments) applies.ASTM (AMERICAN SOCIETY FOR TESTING AND MATERIALS)C 177 "Test Method for Steady-State Heat Flux Measurementsand Thermal Transmission Properties by Means of theApparatus"Guarded-Hot-PlateC 356 "Test Method for Linear Shrinkage of Preformed HighTemperature Thermal Insulation Subjected to SoakingHeat"C 390 "Criteria for Sampling and Acceptance of PreformedThermal Insulation Lots"C 411 "Hot-Surface Performance of High Temperature ThermalInsulation"C 553 "Test Method for Mineral Fiber Blanket and Felt Insulation"C 692 "Test Method for Evaluating the Influence of Wicking-TypeThermal Insulations on the External Stress CorrosionCrackin Tendency of Austenitic Stainless Steel"C 871 "Test Methods for Chemical Analysis of Thermal InsulationMaterial for Leachable Chloride, Fluoride, Silicate, andIons"sodiumBSI (BRITISH STANDARD INSTITUTION)BS 3958: Part 5 "Thermal Insulating Materials Part 5: Specification forBonded man-made Mineral Fiber Slabs"BS 2972 "Methods of Test for Inorganic Thermal InsulatingMaterials"3. DEFINITIONS AND TERMINOLOGYBlock InsulationSemi-rigid insulation formed into sections, rectangular both in plan and cross section, usually 90-120 cm long, 15-60 cm wide and 2.5-15 cm thick.BoardRigid or semi-rigid insulation formed into sections, rectangular both in plan and cross section, usually more than 120 cm long, 60-75 cm wide and up to 10 cm thick.Mineral fiber (Mineral wool)Insulation composed principally of fibers manufactured from rock, slag, or glass with or without binders.Rock woolMineral fiber produced from naturally occurring igneous rock.SlabSee definition for block.Slag woolMineral fiber produced from steel mill slag.Soaking heatA test condition in which the specimen is completely immersed in an atmosphere maintained at a controlled temperature.Vapor barrierA vapor check with water vapor permeance not exceeding 0.067 g/(s MN), when tested in accordance with BS 2972.4. UNITSThis Standard is based on International System of Units (SI), except were otherwise specified.5. MATERIAL AND MANUFACTUREThe mineral fiber preformed block and board thermal insulation shall be manufactured from mineral substances such as rock or slag processed from a molten state into fibrous form. The boards shall not contain non-fibrous pieces of these materials that have any dimensions exceeding 10 mm. Mineral fiber preformed block and board insulation shall be rigid or semi-rigid material composed of mineral fibers with or without binder.6. GENERAL PROPERTIESThe mineral fiber preformed block and board thermal insulation shall have general properties as follows:6.1 Insulation shall have suitable resistance to sunlight in order to minimize shrinkage bellow the limit specified in 8.1 and have as low water permeability as specified in 8.5.6.2 It shall be non-combustible and shall be resistant to vermins and fungus, be free fromobjectionable odors, and shall not react with process chemicals present.6.3 The insulation shall be asbestos free and shall have not health hazard in case of contact or during labor working.6.4 The insulation shall have only traces of corrosive materials; i.e. water soluble chloride, which attacks stainless steels or alkalinity which attacks aluminum jacketing.7. CHEMICAL COMPOSITION7.1 Optimum chemical composition for major constituent of mineral fiber preformed block and board thermal insulation shall be as follows, when tested by spectrometric methods.SiO2= 30 - 45 weight %Al2O3= 8 - 15 weight %TiO2= 2 - 4 weight %Fe2O3= 2.5 max. weight %CaO = 30 - 35 weight %MgO = 6 - 12 weight %Na2O = 0 - 1 weight %K2O = 0 - 1 weight %P2O5= 0 - 1 weight %Water soluble chloride: Approximately 6 mg/kg when tested in accordance with ASTM C-871.7.2 If water-soluble chloride content of the insulation material exceeds the amount specified in the chemical composition above, sufficient amount of sodium silicate (Na2SiO3) inhibitor shall be added to the insulation material. Acceptable proportion of sodium plus silicate ions to the chloride ions as found by leaching from the insulation when tested in accordance with ASTM Test Method C 871 shall be in accordance with Fig. 2.1.With reference to Fig. 2.1 the minimum allowable value of sodium plus silicate will be 50 ppm when tested in accordance with ASTM Test Method C-692, providing leachable (water soluble ) chloride be higher than 10 mg per kg of insulation material.7.3 The pH of leach water shall be measured, in accordance with ASTM Test Methods C871, and shall be greater than 7.0 but not greater than 11.7 at 25°C .Cl ppmACCEPTABILITY OF INSULATION MATERIAL ON THE BASIS OF THE PLOT POINTS OF THECl AND THE (Na+SiO3) ANALYSISFig. 2.18. PHYSICAL PROPERTIESThe physical properties of mineral fiber preformed block and board insulation shall be as follows:8.1 Linear ShrinkageLinear shrinkage for length shall be maximum 2% after soaking heat and tested in accordance with ASTM Test Method C-356 at manufacturer’s temperature limit.8.2 Thermal ConductivityMaximum thermal conductivity value shall be 0.065 w/mk at 200°C when tested in accordance with ASTM Test Method C 177.8.3 Temperature of UseWhen tested in accordance with ASTM Test Method C411 at the intended use temperature, insulation for use above ambient shall show no physical changes that adversely affect its service qualities.8.4 Bulk DensityDensity of the block and board mineral fiber thermal insulation shall be 300 kg/m³ maximum and variation from the specified density shall not exceed ±15%.8.5 Moisture Absorption (water vapor)When tested in accordance with ASTM C553 insulation for use below ambient temperature shall gain no more than 1% volume.8.6 Recovery after CompressionWhen tested in accordance with BS 3958: Part 5 the recovery after compression shall be not less than 95% of the original thickness.9. SIZE OF BOARD AND SLAB9.1 The length and width of Board and slab shall be as per manufacturer’s standard dimension unless otherwise agreed between Company and manufacturer.9.2 The thickness of board and slab shall be specified by the Purchaser (see Appendix A "ordering information"). However the thickness shall be within the range of 25 to 100 mm in 13 mm increments.10. DIMENSIONAL TOLERANCESThe average measured length, width, and thickness of the board and slab thermal insulation shall not differ from the dimension specified by more than the following:DIMENSION TOLERANCE IN mmLength Width Thickness ±١٢±6 +6 -311. WORKMANSHIPThe insulation shall not have visible defects that will adversely affect its service qualities.12. SAMPLINGThe insulation shall be sampled for the purpose of tests in accordance with Test Method ASTM C390.13. INSPECTION AND REJECTION13.1 Inspection13.1.1 The manufacturer and/or supplier shall be responsible for carrying out all the tests and inspections required by this Standard specification, using his own or other reliable facilities, and he shall maintain complete records of all such tests and inspections. Such records shall be available for review by the Purchaser. The manufacturer and/or supplier shall furnish to the Purchaser a certificate of inspection stating that each lot has been sampled, tested, and inspected in accordance with this Standard specification and has been found to meet the requirements specified.13.1.2 The supplier shall afford the Purchaser’s inspector all reasonable facilities necessary to satisfy that the material is being produced and furnished in accordance with this Standard specification. Such inspections in no way relieve the manufacturer and/or supplier of his responsibilities under the term of this Standard specification.13.1.3 The Purchaser reserves the right to perform any inspections set forth in this Standard specification where such inspections are deemed necessary to assure that supplies and services comform to the prescribed requirements.13.1.4 The Purchaser’s inspector shall have access to the material subject to inspection for the purpose of witnessing the selection of the samples. The preparation of the test pieces, and the performance of the test(s). For such tests, the inspector shall have the right to indicate the pieces from which the samples will be taken in accordance with the provisions of this Standard specification.13.2 Rejection13.2.1 If the inspection of the sample shows failure to conform to the requirements of this Standard specification, a second sample from the same lot shall be tested and the results of this retest averaged with the result of the original test.13.2.2 Upon retest as described in 13.2.1 failure to conform to this Standard specification shall constitute grounds for rejection.13.2.3 In case of rejection, the manufacturer or supplier shall have the right to reinspect the rejected lot and resubmit the lot for inspection after removal of that portion of the lot not conforming to the specified requirement.14. PACKAGING AND MARKING14.1 Packaging14.1.1 Unless otherwise specified by the Purchaser, the mineral fiber block and board thermal insulation shall be packaged in manufacturer’s standard commercial container approved by the Purchaser and considering the following:14.1.2 Overseas consignments shall be packed in double-corrugated cartons incorporating weather proof paper because of greater handling involved and possibly of exposure to wet conditions. If the size of sections exceeds the practical size for cartons, wooden or strong mesh crates may be used.14.1.3 Mineral fiber block and board insulations materials shall not be unpacked at site until is required for use.14.1.4 Stacking of packed mineral fiber block and board insulation during transportation shall be in accordance with the manufacturer’s recommendation.14.2 Marking14.2.1 Unless otherwise agreed between purchaser and manufacturer and/or supplier, containers shall be marked as follows:- purchase order No.;- name and type of material;- sizes of thermal insulation;- quantity of material in the container;- date of manufacturing;- supplier’s name;- origin of manufacturing;- destination.15. STORAGE15.1 The insulation shall be stored in a dry atmosphere under cover and inspected at interval not exceeding three months.15.2 Cartons shall be stored end up and be stacked no more than three high.APPENDICESAPPENDIX AORDERING INFORMATIONThe following information shall be supplied with the order:a) The number and date of this IPS Standard,b) the dimension of thermal insulation required,c) the maximum temperature to which the insulation will be subjected,d) the density of thermal insulation,e) a note of any other special requirements or properties that the material shall have inaddition to this Standard.。
关于基普乔格破2的作文英文

The Breakthrough of Kipchoge: Beating theTwo-Hour MarathonIn the annals of sports history, few achievements have captivated the world's attention as much as EliudKipchoge's groundbreaking feat of running a marathon in less than two hours. This remarkable milestone not only marked a new era in endurance running but also served as a testament to the unwavering determination and relentless training of an athlete who pushed the boundaries of human possibility.Kipchoge's journey to this remarkable feat was anything but conventional. He had to overcome numerous challenges, including doubts from critics who questioned whether the two-hour barrier was even achievable. Yet, through a meticulous training program and a meticulous approach to race strategy, Kipchoge defied the odds and emerged victorious.His success is not just about breaking a record, but also about breaking barriers. His feat challenges what we believe is possible, pushing us to reimagine what we consider achievable in our own lives. His story is aninspiration to us all, reminding us that with enough dedication and perseverance, we can overcome any obstacle and achieve our dreams.Kipchoge's achievement is also a testament to the power of teamwork and collaboration. He did not achieve this feat alone; he had a team of coaches, support staff, and sponsors who believed in him and helped him every step of the way. This underscores the importance of having a support system in our lives, one that believes in us and helps us when times are tough.Moreover, Kipchoge's feat highlights the importance of setting ambitious goals. By aiming for something that seemed unattainable, he was able to push himself beyond his limits and achieve something truly remarkable. This serves as a reminder to us all to aim high and never settle for mediocrity.In conclusion, Eliud Kipchoge's breaking of the two-hour marathon barrier is not just a sports milestone, but also a symbol of human potential and determination. His story is an inspiration to us all, showing us that with enough dedication, perseverance, and ambition, we canachieve anything we set our minds to. His feat reminds us that there are no limits to what we can achieve, only the limits we place on ourselves.**基普乔格破2:马拉松的新纪元**在体育历史的长河中,很少有像埃鲁德·基普乔格以不到两小时完成马拉松这样的成就能够吸引全世界的目光。
API653模拟考题
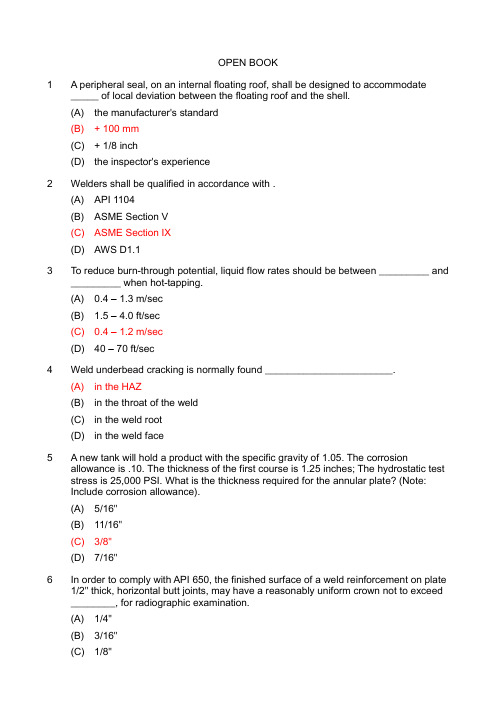
OPEN BOOK1 A peripheral seal, on an internal floating roof, shall be designed to accommodate_____ of local deviation between the floating roof and the shell.(A) the manufacturer's standard(B) + 100 mm(C) + 1/8 inch(D) the inspector's experience2 Welders shall be qualified in accordance with .(A) API 1104(B) ASME Section V(C) ASME Section IX(D) AWS D1.13 To reduce burn-through potential, liquid flow rates should be between _________ and_________ when hot-tapping.(A) 0.4 – 1.3 m/sec(B) 1.5 – 4.0 ft/sec(C) 0.4 – 1.2 m/sec(D) 40 – 70 ft/sec4 Weld underbead cracking is normally found _______________________.(A) in the HAZ(B) in the throat of the weld(C) in the weld root(D) in the weld face5 A new tank will hold a product with the specific gravity of 1.05. The corrosionallowance is .10. The thickness of the first course is 1.25 inches; The hydrostatic test stress is 25,000 PSI. What is the thickness required for the annular plate? (Note:Include corrosion allowance).(A) 5/16"(B) 11/16"(C) 3/8"(D) 7/16"6 In order to comply with API 650, the finished surface of a weld reinforcement on plate1/2" thick, horizontal butt joints, may have a reasonably uniform crown not to exceed ________, for radiographic examination.(A) 1/4"(B) 3/16"(C) 1/8"(D) 1/16"7 What is the design thickness for the first course of a new tank 60’ tall, with a fill heightof 58’ and a diameter of 80’4”? The material of construction is A516M 485. Specific gravity of .6(A) .097(B) .416(C) 28.1(D) .2818 What is the hydrostatic test shell thickness of the tank in question 7?(A) .416(B) .281(C) .117(D) .5009 To what thickness should the tank in question 8 be constructed?(A) .281”(B) .416”(C) .500”(D) 1.00”10 If the first course of a new tank is 12.5 mm and the design metal temperature is -7℃,what is the material group?(A) Group I(B) Group II(C) Group III(D) Group IV11 What is the maximum reinforcement on a vertical butt joint, if the plate is .625 in.thick?(A) 3/32”(B) 1/8”(C) 3/16”(D) 1/4”12 Ultrasonic acceptance standards, in accordance with API 650, shall be ______.(A) ASME Section VIII(B) ASME Section V(C) ASME Section XI(D) Agreed upon by the purchaser and the manufacturer13 A material Test Report shows the following chemistries:C:0.15% Cr:1.25% V:0.02% Ni:0.35%Mn:0.20% Mo:1.00% Si:0.53% Cu:0.01%What is the approximate CE of this material using the formula supplied in RP 577?(A) 0.35(B) 0.7(C) 0.9(D) 0.5514 From the above CE number, what should typically be done after welding this steel?(A) no PWHT(B) preheating(C) PWHT(D) preheat and PWHT15 What is the minimum dimension for a shell ring replacement piece or segment?(A) The actual area requiring renewal, plus 6" on all four surrounding sides.(B) 12" or 12 times the "t" of the replacement plate, whichever is greater.(C) 10% of the individual ring segment involved.(D) 20% of the individual ring segment involved.16 The periphery of the insert plates shall have a _________ tapered transition to thethickness of the adjacent shell plates when it used.(A) 1 : 3(B) 1 : 4(C) Round corner smoothly to avoid stress concentration.(D) None of the above.17 Butt welded annular plates shall be required for ____________.(A) When purchaser required.(B) When bottom shell course of material Gr.IV to VI.(C) When shell course thickness above 25mm.(D) When the tank diameter above 100ft.18 What is the fin height for a new tank whose diameter is 150', first course 5/8”,the shellmaterial is A-36?(A) 40.9’(B) 400'(C) The tank strapping company win report, not an inspection problem(D) Not enough information to calculate19 A weld with a nominal thickness of 1.5 inch is to be radiographed using a film side holeIQI. The IQI designation should be:(A) 25(B) 30(C) 35(D) Both a and b are acceptable?20 The most common measure of weldability and hot cracking of stainless steel is the_________.(A) bend test(B) ferrite number(C) Charpy V-notch number(D) hydrogen number21 F numbers are assigned to electrodes based on their ______________.(A) alloy(B) chemistry(C) usability characteristics(D) flux coating22 The allowable unsharpness for a material that is 2" thick is:(A) .015(B) .020(C) .040(D) .030(E) Unsharpness is not allowed in any ASME Code23 A hole-type IQI is observed on a RT film for an aluminum weld. The IQI body is placedacross the weld, but the lead letter "F" and the l.D. markers are not in the area ofinterest. Per ASME V, this condition is:(A) Acceptable as shown(B) Unacceptable - wrong placement for aluminum welds(C) Unacceptable - hole IQI's cannot be used on this material(D) Unacceptable - hole type IQI's cannot be used across the weld when a film-sideset-up is used.24 After repairing of shell to bottom weld, reexamine the repaired welds and a minimumof___________.(A) 75mm in defective side.(B) 150mm in defective side.(C) 75mm in both sides of defect.(D) 150mm in both sides of defect.25 A new tank will hold a product with the specific gravity of 1.05; The corrosionallowance is .1 0; Thethicknessofthefirstcourseisl.25inches; Hydrostatictest stress25,000 PSI. What is the thickness required for the annular plate? (Note: lncludecorrosion allowance).(A) 5/16”(B) 11/16"(C) 3/8"(D) 7/16"The following applies to quest ions 26 through 31 below:An inspection is performed on an AST 24' tall, 22' fill height, 94' diameter, waterstorage service, earth foundation. There is one area of general internal corrosion on the south side of the shell 20" wide and 20" in vertical length. There is evidence ofbottom settlement.26 Calculate the minimum thickness of the first course based on product alone.(A) 1.175"(B) 1.000"(C) 0.551"(D) 0.219"27 Calculate the minimum thickness for the third course, if each course is 4' in height.(A) .122"(B) .100"(C) .275"(D) .300"28 Calculate the "L” length for an area of general corrosion found 10' from the bottom onthe south side of the shell, T2=.125".(A) 40”(B) 12.68”(C) 6.80”(D) 11.75”29 There are three pits aligned vertically on the north side of the tank, in the first course.The diameter of the pits are 1.250", 1 ", and .500" in length along a vertical line 8" long.Note: Assume pit depth of slightly less than one-half of the minimum acceptable tank shell thickness, exclusive of the corrosion allowance.(A) Because the pits are aligned vertically no repair is required(B) Scattered pits may be ignored(C) If the pit is round, it may be ignored(D) A repair is required30 Three circumferentially scattered pits are located on the west side of the tank 18" fromthe bottom. The pits measure .500", ,477" and .732" in diameter. Note: Assume pitdepth of one-half of the minimum acceptable tank shell thickness, exclusive of thecorrosion allowance.(A) Because the pits are scattered circumferentially no repair is required(B) All pits may be ignored(C) If the pit is round, it may be ignored(D) A repair is required31 A bulge is found on the tank floor, the diameter of the bulge is 30". What is themaximum permissible height for the bulge?(A) 11.1"(B) .460"(C) .962"(D) 1.11 "32 The general Brinell Hardness limit for 5CR-Mo steels is:(A) 200(B) 225(C) 241(D) 25033 At what temperatures does SE-797 provide guidelines for measuring the thickness ofmaterials using the contact pulse-echo method?(A) Not to exceed 93° F(B) Not to exceed 200° C(C) Not to exceed 200° F(D) Not to exceed 100°C34 A weld will be radiographed using a source-side wire IQI. The weld is 3/8" thick with1/16" reinforcement on both sides. What ASTM IQI set will be required?(A) Set A(B) Set B(C) Set C(D) Set D(E) (A) and (D)35 If a WPS is qualified using a base material that is 9" thick, the correct base metalthickness range shown in the WPS should be:(A) 3/16"-12" thick(B) 1/16"-14" thick(C) 3/16"-18" thick(D) 3/16"-9.9" thic(E) 3/16"-maximum to be welded36 A welding procedure is qualified on P5A to P5A steel. This WPS is then qualified toweld on:(A) P5A - P4 steels(B) P5A - P5B steels(C) P4 - P4 steels(D) All of the above37 The radiographic density through an IQI is measured at 2.6 with a densitometer usinggamma RT. The allowable density through the weld will be, if no shim is used.(A) 2.0-4.0(B) 1.8-4.0(C) 2.21 - 3.38(D) 2.0-2.9938 Which of the following is an essential variable for the GMAW process?(A) Wire diameter(B) Travel speed(C) Interposes temperature(D) Electrical characteristics (short arc to spray or vice-versa)(E) Groove design39 One of the procedural requirements for MT examination that must be addressed is:(A) Magnetizing time(B) Developer application(C) Type of particles, wet or dry(D) (A) and (B) above40 A 4T hole on a 20 IQI has a diameter of:(A) .80”(B) .043”(C) .080”(D) .070”QUESTIONS ( 41 ~ 50 ) are based on WPS/PQR SAW-1, attached:41 The deposited weld metal thickness range listed on the WPS:(A) is correct as shown(B) is incorrect - should be 3/16” - 2” max.(C) should be 4” max.(D) none of the above42 The joint design shown on the WPS:(A) must be qualified by the PQR(B) is acceptable as shown(C) must be re-qualified if an open root joint will be used(D) should be qualified with a backing strip instead of weld metal43 An essential variable that has not been addressed on both the WPS and PQR is:(A) QW-404.36(B) QW-403.9(C) QW-403.13(D) all of the above44 The pipe diameter range listed on the WPS:(A) is acceptable as shown(B) is incorrect - plate does not qualify for pipe(C) should be >24” O.D.(D) should be shown as > 2 7/8” O.D.45 Post-weld heat treatment as shown on the WPS/PQR is:(A) incorrect, as all codes require PWHT in this thickness(B) i ncorrect, as the PQR should be PWHT’d(C) incorrect as the WPS should specify required PWHT of production welds(D) none of the above46 The tension test results shown on the PQR are:(A) acceptable as shown(B) unacceptable due to insufficient width of specimens(C) unacceptable due to insufficient number of specimens(D) unacceptable because multiple specimens cannot be used in this thickness ofplate coupon47 The bend test results shown on the PQR are:(A) acceptable as shown(B) unacceptable due to insufficient number of specimens(C) unacceptable due to wrong type of bend test specimen(D) unacceptable due to wrong size of specimen48 The tension test results shown on the PQR are:(A) sufficiently strong to meet the Code(B) too weak to meet the Code(C) 1.5% over the rated base metal tensile strength, and therefore, do not meet theCode(D) unacceptable because the results look “bogus”49 The PQR:(A) does not need to be signed(B) must be signed to be “Code legal”(C) must be signed by the President of the Company(D) none of the above50 An essential variable that is addressed on the WPS but not addressed on the PQR is:(A) QW 404.25(B) QW 406.1(C) QW 407(D) QW 404.34CLOSE BOOK1 In case of conflict between API-12C, API-650 and API-653 standards involving"in-service" AST's, which of the three codes will govern?(A) API-12C(B) API-650(C) API-6532 Which of the following have the ultimate responsibility for complying with API-653standard provisions?(A) On-site Inspector(B) Contractor Involved(C) Owner/operator of equipment(D) Relevant State or Federal Agency3 Internal pressures inside tanks may vary. Which of the following pressures representthe maximum amount and is still considered to be atmospheric storage?(A) 3 oz. psig(B) 1.0 lb. psig(C) 1.5 lb. psig(D) 2.5 lb. Psig4 What is the joint efficiency of a lap riveted joint with one (1) row of rivets?(A) 45%(B) 60%(C) 75%(D) 80%5 All prior reported brittle fracture tank failures have occurred under which of thefollowing conditions/situations?(A) Atmospheric temperature of 20℉or lower.(B) During a hydro test where the test water was 50°F or colder.(C) Shortly after erection, following a repair/alteration, first cold weather filling orchange to lower temperature service.(D) Where a testing medium other than water was used.6 Prior to examination, each adjacent surface shall be cleaned within at least ______ ofthe area to be examined.(A) 1”(B) 1.5”(C) 2”(D) 3”7 The procedure qualification test is used to determine:(A) The skill of the welder(B) That the proposed production weldment is capable of having the requiredproperties(C) The corrosion –resistance(D) None of the above8 A welding electrode has the marking E-6010. The “1” marking indicates:(A) Flat position only(B) Horizontal position only(C) All positions(D) Only good for heat treated welds9 May a welder who is qualified using a double-groove weld, make a single V-grooveweld without backing?(A) Yes(B) No(C) Not enough information provided(D) Yes, because backing is not an essential variable for a welder10 What is the maximum defect permitted on the convex surface of a welder qualificationbend test after bending , except for corner cracks and corrosion resistant weldoverlay?(A) 1/4 inch(B) 1/8 inch(C) 1/16 inch(D) 3/16 inch(E) No defects are allowed11 When external UT measurements are used to determine a rate of general, uniformcorrosion (relevant to shell integrity) which of the following values cannot beexceeded?(A) 10 years maximum(B) 20 years maximum(C) 5 years (after commissioning), or at 5 year intervals (where corrosion rate is notknown).(D) Five years or RCA/4N, whichever is more.12 What primary factor determines the interval between internal and externalinspections?(A) Jurisdictional regulations(B) Tank service history, unless special reasons indicate an earlier inspection isrequired.(C) Known (or suspected) corrosion activity of product.(D) Change of service to a product with a specific gravity 10% higher than priorstored product.13 Which of the areas described below are considered to be the "critical zone" involvingtank bottom repair?(A) Within the annular ring, within 12" of shell, or within 12" of inside edge of annularplate ring.(B) Any area where 3–plate laps are located(C) Within 36" (measured vertically) from any shell penetration above.(D) Within 3" from the shell on the bottom plates14 Select the minimum number of "t" measurements required (along the circumference ofany proposed "hot-tap" nozzle location):(A) One (1) on horizontal centerline (3" from edge) on each side of proposed shellopening cut.(B) Four (4)(C) Eight (8)(D) Establishment of both a minimum and average "t" over the entire nozzleinstallation area.15 What type of contour cut (if any) and what degree of bevel (if any) is required on thenozzle "barrel" end that is to be joined to shell during a "hot-tap".(A) No contour cut required, 30° outside bevel.(B) No contour cut required, 45° outside bevel.(C) Cut to shell contour and outside beveled for full penetration attachment weld.(D) No contour cut required. 1/8" corner radius (minimum).16 A common weld defect encountered with the GMAW-S welding process is:(A) LOP(B) slag(C) LOF(D) cracking17 From the above CE number, what should typically be done after welding this steel?(A) no PWHT(B) preheating(C) PWHT(D) preheat and PWHT18 A typical test for hardenability is the ___________.(A) bend test(B) Rockwell test(C) Jominy Bar test(D) Charpy V-notch test19 NDE examiners should be qualified to ______ when specified by the referencingcode.(A) ASME XII(B) API 570(C) SNT-TC-1A(D) API 51020 A welder continuity log should be maintained to allow verification that each welder hasutilized each welding process within a _______ period.(A) one yea(B) 3 month(C) 2 year(D) six month21 Each pass of the UT transducer should overlap the previous pass by _____% of thetransducer dimension.(A) 1%(B) 5%(C) 10%(D) 15%22 Metals with a high coefficient of thermal expansion are more susceptible to:(A) transverse cracking(B) lack of fusion(C) warpage and distortion(D) linear porosity23 A film density of 1.0 will allow _______% of light through to the film.(A) 1%(B) 10%(C) 0.01%(D) 0.001%24 How does preheating carbon steel tend to reduce hydrogen-induced delayedcracking?(A) eliminates SCC(B) prevents carbon migration(C) slows the cooling rate – prevents martensite formation(D) makes the grains grow so they won’t crack25 GMAW can be used in 3 distinct modes of transfer. The coolest or fastest freezing ofthese transfers is:(A) spray(B) short circuiting(C) pulse-spray(D) globular26 When reconstructing tank shells with a material "t" exceeding 1.50", what minimumpre-heat is specified?(A) No preheat required, if air temperature exceeds 70℉.(B) 200℉.(C) 225℉.(D) 300℉.27 In re-erecting a tank shell, what length "sweep-board" and what are maximumallowable values for weld seam peaking?(A) 0.50" (1/2") with 36" horizontal sweep board?(B) 0.25" (1/4") on verticals; 0.50" (1/2") on horizontal with 36" board(C) 0.75" (3/4") with 48" board.(D) 1.00" (1") with 48" board.28 Welding procedure Specs (WPS) are established in Section 11 of API-653.Welders/operators must be qualified in accordance with which of the codes listed.(A) AWS(B) Section V ASME(C) Section VIII ASME(D) Section IX ASME29 API-653 (Section 12) requires greater radiographic examination of tank shell weldsthan does API-650. Relevant to new or repaired vertical joints in existing shell plates, how many radiographs are required?(A) Twice those required by API-650.(B) API 650 requirements plus one (1) in every joint.(C) One (1) for each welder or operator involved on each ring.(D) Two (2) for each welder or operator involved on each ring for all platethicknesses.30 According to API 650, which of the following types of connections shall be stressrelieved?(A) All nozzles(B) All Group I, II, III or IIIA opening connections less than 12 inches(C) All Group IV, IVA, V or VI opening connections requiring reinforcement(D) All connections requiring reinforcement31 Upon completion, the roof of a tank designed to be gas tight shall be tested by whichone of the following methods?(A) Magnetic particle testing of all welds(B) Application of internal air pressure not exceeding the weight of the roof platesand applying a solution suitable for the detection of leaks .(C) Penetrant testing the weld joints(D) Visual inspection of the weld joints32 Each welder making welds on a tank shall be certified by the _______.(A) erection/fabrication manufacturer(B) purchaser(C) Nuclear Regulatory Commission(D) certified inspector33 Per API 650, external floating roof deck plates having support leg or other rigidpenetrations closer than ____ inches to lap weld seams must be full fillet welded not less than 2 inches on 10 inch centers.(A) 6(B) 12(C) 14(D) 1834 Upon completion of welding of the new tank bottom, the welds shall be inspected bywhich one of the following methods?(A) Radiographs(B) Vacuum or air pressure(C) Penetrant testing(D) Hammer testing35 The maximum reinforcement thickness for vertical butt joints, less than or equal to1/2" thick is .(A) 1/16"(B) 1/8"(C) 3/32"(D) 3/16"36 What designation is used to indicate the IQI is on the film side?(A) an “F”(B) an “E”(C) a “D”(D) an “FS”37 A wire IQI shall be placed ___________ the weld, with the wires _________ to theweld.(A) Adjacent to, perpendicular(B) Adjacent to, parallel(C) only perpendicular(D) none of the above38 The location markers required by ASME V are required __________________.(A) be written with a sharpie pen(B) be vibra-etched(C) appear as radiographic images(D) both A & B, above39 What are materials of prime concern for brittle fracture(A) Aluminum(B) 300 Series SS(C) Low alloy steels(D) Nickel base alloys40 Which condition is the highest corrosion rate of atmospheric corrosion(A) Marine environments(B) Industrial environments(C) Inland locations(D) Dry rural environments41 What have been effective for underground structures in preventing MIC(A) Wrapping(B) Proper application of biocides(C) Cathodically protecting(D) a&c42 What is frequently used to estimate soil corrosivity(A) Measuring the structure to soil potential(B) Cathodic protection(C) Soil resistivity(D) pH43 What element of the alloy has a major affect on Cl-SCC resistance(A) Ni(B) Cr(C) Mo(D) Cu44 What alloys are more resistant for Caustic Stress Corrosion Cracking at 200℃(A) PWHT’d Carbon steel(B) Low alloy steels(C) 300 Series SS(D) Nickel base alloys45 Which is susceptible to Cl-SCC(A) 400SS(B) 316SS(C) Carbon steel(D) C27646 Annular bottom plates shall have a radial width that provides at least _____inchesbetween the inside of the shell and any lap-welded joint in the remainder of thebottom.(A) 10(B) 30(C) 24(D) 1847 The maximum acceptable undercutting of the base metal for vertical butt joints is ___inch.(A) 3/32(B) 1/8(C) 1/64(D) 3/6448 A double-welded butt weld is ______.(A) a joint between two abutting parts lying in approximately the same plane(B) a joint between two abutting parts lying in approximately the same plane that iswelded from both sides(C) a joint between two overlapping members in which the overlapping edges ofboth members are welded with fillet welds(D) a fillet weld whose size is equal to the thickness of the thinner joined member49 Openings in tank shells larger than required to accommodate an NPS _____ inchflanged or threaded nozzle shall be reinforced.(A) one(B) two(C) three(D) four50 The acceptability of welds examined by radiography shall be judged by the standardsin .(A) ASME Section V, Division 7(B) ASME Section IX, Paragraph QW-191(C) ASME Section VIII, Division 1, Paragraph UW-51(b)(D) API 110451 When bottom annular plates are required by paragraph 3.5.1 of API 650, the radialjoints shall be radiographed. For single welded butt joints using a backup bar, one spot radiograph shall be taken on _____ percent of the radial joints.(A) 10(B) 30(C) 50(D) 10052 Annular bottom plates must extend a minimum of _______ inches outside the tankshell.(A) 1 1/2(B) 2(C) 3(D) 453 The maximum operating temperature for tanks constructed to API 650 (not includingappendices) is _______.(A) 500℉(B) 500℃(C) 200℉(D) 200℃54 Who is responsible for compliance with the API 650 standards?(A) Manufacturer(B) Purchaser(C) State Inspector(D) API 653 Inspector55 A new tank is under construction. How many radiographs are required on the firstcourse vertical welds if the shell is 35 mm thick?(A) One radiograph shall be taken in every vertical joint(B) 100% of the vertical joint(C) Two radiographs shall be taken in the vertical joint(D) No radiographs required56 All bottom plates shall have a minimum nominal thickness of _____ inch, exclusive ofany corrosion allowance specified by the purchaser for the bottom plates.(A) 3/8(B) .250(C) .516(D) .32557 Repairs of defects shall not be attempted on a tank that is filled with _____ or on atank that has contained ____ until the tank has been emptied, cleaned and gas freed in a safe manner.(A) nitrogen(B) oil(C) water(D) grain58 Misalignment in completed vertical joints over 5/8" shall not exceed what percentageof the plate thickness?(A) 25% with a maximum of 1/16"(B) 2% with a maximum of 3/64"(C) 5% with a maximum of 3/8"(D) 10% with a maximum of 1/8"59 Reinforcing plates of shell penetrations shall be given a(n) ________ test, inaccordance with API Standard 650.(A) diesel(B) air(C) stress(D) gas60 Column-based clip-guides shall be welded to the tank bottom to prevent __________.(A) internal erosion(B) structural uplifting(C) lateral movement of column bases(D) lateral expansion and contraction61 The most common method used for monitoring underground structures is to measure(A) The structure to soil potential(B) Salts(C) Soil resistivity(D) pH62 Cl-stress corrosion cracking usually occurs at metal temperatures(A) Above about 60℉(15℃)(B) Above about 120℉(49℃)(C) Above about 140℉(60℃)(D) Below about 140℉(60℃)63 Atmospheric Corrosion becomes more severe at metal temperatures between(A) 10℉(-12℃) and 350℉(175℃),(B) 100℉(38℃) and121℉(49℃),(C) 250℉(121℃) and 350℉(175℃),(D) 212℉(100℃) and 250℉(121℃)64 If the WPS shows a single "Vee" groove is to be used and the PQR was qualified witha double "Vee" groove:(A) The WPS can be used without re-qualification(B) The WPS must be requalified(C) The PQR must be retested(D) The WPS must be modified to show the correct joint65 A common root pass welding defect is:(A) Porosity(B) Lack of penetration(C) Tungsten inclusion(D) Overlap66 A welding electrode is marked E8018. The first two digits mean that the electrode has:(A) 80 kg weld strength(B) 80 psi stress(C) 80,000 ksi tensile strength(D) 80,000 psi tensile strength67 The primary difference between GMAW and FCAW is:(A) The wire feeder used(B) The gas used(C) The wire used(D) The power source used68 Per ASME IX a welding operator may be qualified by:(A) Test plates (bend tests)(B) Production weld radiograph(C) Radiography of a test pipe(D) (A) and (B) above(E) ALL of the above69 An ASME magnetic particle field indicator is made up of how many "PIE" sectionsfurnace brazed together?(A) 2(B) 4。
秘鲁大冒险2 英语作文
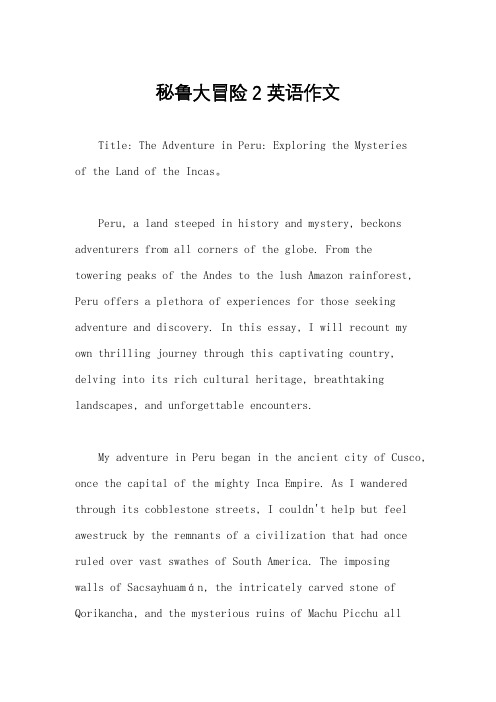
秘鲁大冒险2 英语作文Title: The Adventure in Peru: Exploring the Mysteriesof the Land of the Incas。
Peru, a land steeped in history and mystery, beckons adventurers from all corners of the globe. From thetowering peaks of the Andes to the lush Amazon rainforest, Peru offers a plethora of experiences for those seeking adventure and discovery. In this essay, I will recount my own thrilling journey through this captivating country, delving into its rich cultural heritage, breathtaking landscapes, and unforgettable encounters.My adventure in Peru began in the ancient city of Cusco, once the capital of the mighty Inca Empire. As I wandered through its cobblestone streets, I couldn't help but feel awestruck by the remnants of a civilization that had once ruled over vast swathes of South America. The imposingwalls of Sacsayhuamán, the intricately carv ed stone of Qorikancha, and the mysterious ruins of Machu Picchu allserved as reminders of the ingenuity and craftsmanship of the Inca people.But it wasn't just the historical sites that captivated me; it was also the natural beauty of Peru that left me spellbound. Trekking through the Andes, I was treated to stunning vistas of snow-capped peaks, crystal-clear lakes, and verdant valleys. The air was crisp and invigorating, and with each step, I felt a deep sense of connection to the land and its people.One of the highlights of my journey was exploring the Amazon rainforest, often referred to as the "lungs of the Earth." Teeming with life in every corner, the Amazon is home to an incredible array of flora and fauna, from colorful macaws and playful monkeys to elusive jaguars and giant anacondas. Guided by knowledgeable local experts, I embarked on treks through dense jungle, cruised along winding rivers, and even spent a night in a remote eco-lodge, falling asleep to the symphony of the rainforest.Of course, no visit to Peru would be complete withoutindulging in its culinary delights. From hearty stews and grilled meats to exotic fruits and fiery ceviche, Peruvian cuisine is a tantalizing fusion of indigenous ingredients and Spanish, African, and Asian influences. Whether sampling street food in bustling markets or dining in gourmet restaurants, I savored every mouthful, each dish a celebration of Peru's diverse cultural heritage.But perhaps the most memorable aspect of my journey was the warmth and hospitality of the Peruvian people. Everywhere I went, I was greeted with smiles and kindness, whether from humble farmers in the highlands or artisans in bustling cities. Despite the language barrier, I found that laughter and gestures were universal languages, bridging the gap between cultures and forging connections that transcended words.As I reflect on my adventure in Peru, I am filled with a profound sense of gratitude and wonder. In the span of just a few weeks, I had experienced more than I ever thought possible – traversing ancient ruins, communing with nature, savoring exotic flavors, and forgingmeaningful connections with people from all walks of life. Peru had welcomed me with open arms and left an indelible mark on my heart, reminding me of the boundless beauty and magic that awaits those willing to embark on the journey of a lifetime.。
SAE-AMS-QQ-A-200-11-1997-R2007.pdf
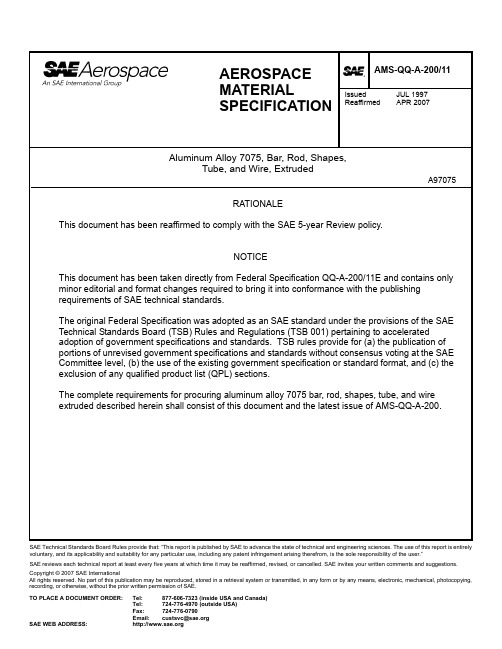
SAE Technical Standards Board Rules provide that: “This report is published by SAE to advance the state of technical and engineering sciences. The use of this report is entirely voluntary, and its applicability and suitability for any particular use, including any patent infringement arising therefrom, is the sole responsibility of the user.”SAE reviews each technical report at least every five years at which time it may be reaffirmed, revised, or cancelled. SAE invites your written comments and suggestions.Copyright © 2007 SAE InternationalAll rights reserved. No part of this publication may be reproduced, stored in a retrieval system or transmitted, in any form or by any means, electronic, mechanical, photocopying,recording, or otherwise, without the prior written permission of SAE.TO PLACE A DOCUMENT ORDER:Tel: 877-606-7323 (inside USA and Canada)Tel: 724-776-4970 (outside USA)Aluminum Alloy 7075, Bar, Rod, Shapes,Tube, and Wire, ExtrudedA97075RATIONALEThis document has been reaffirmed to comply with the SAE 5-year Review policy.NOTICEThis document has been taken directly from Federal Specification QQ-A-200/11E and contains only minor editorial and format changes required to bring it into conformance with the publishing requirements of SAE technical standards.The original Federal Specification was adopted as an SAE standard under the provisions of the SAE Technical Standards Board (TSB) Rules and Regulations (TSB 001) pertaining to accelerated adoption of government specifications and standards. TSB rules provide for (a) the publication of portions of unrevised government specifications and standards without consensus voting at the SAE Committee level, (b) the use of the existing government specification or standard format, and (c) the exclusion of any qualified product list (QPL) sections.The complete requirements for procuring aluminum alloy 7075 bar, rod, shapes, tube, and wire extruded described herein shall consist of this document and the latest issue of AMS-QQ-A-200.AEROSPACE MATERIALSPECIFICATIONAMS-QQ-A-200/11Issued JUL 1997 ReaffirmedAPR 20071.SCOPE AND CLASSIFICATION:1.1Scope:This specification covers the specific requirements for aluminum alloy 7075 bar, rod, shapes, tube, and wire produced by extrusion.1.2Classification:1.2.1Tempers: Bar, rod, shapes, tube, and wire are classified in the following tempers as specified(See6.2): O,T6, T62, T6510, T6511, T73, T73510, or T73511. Definitions of tempers arespecified in AMS-QQ-A-200.1.2.2Tubing: Tubing shall be additionally classified as follows:Type DescriptionI-Tubing extruded from hollow billets using die and mandrel (SeeAMS-QQ-A-200).II-Tubing extruded from solid billets using a porthole or spiderdie or similar tooling (See AMS-QQ-A-200) 1/.1/ Type II tubing is not commonly available from the producers.2.APPLICABLE DOCUMENTS:See AMS-QQ-A-200.3.REQUIREMENTS: 3.1Chemical Composition:The chemical composition shall conform to the requirements specified in Table I.3.2Mechanical Properties:3.2.1Mechanical Properties of Material as Supplied: Mechanical properties of as-supplied material shall, in the longitudinal (extrusion) direction, conform to property requirements specified in Table II, except as exempted in AMS-QQ-A-200.TABLE I. Chemical Composition 1/ElementPercentMinimum Maximum Zinc5.16.1Magnesium 2.1 2.9Copper 1.2 2.0Chromium 0.180.28Iron --0.50Silicon--0.40Manganese --0.30Titanium--0.20Other Elements, each --0.05Other Elements, total 2/--0.15AluminumRemainder1/Analysis shall routinely be made only for the elements specifically mentioned in Table I. If, however, thepresence of other elements is indicated or suspected in amounts greater than the specified limits, furtheranalysis shall be made to determine that these elements are not present in excess of specified limits.2/The sum of those "Others" metallic elements 0.010percent or more each, expressed to the second decimal before determining the sum.3.2.2Mechanical Properties After Heat Treatment: In addition to conforming to the requirements of3.2.1, materials identified in the following paragraphs shall, after having been heat-treated to other tempers also identified therein, have properties in the longitudinal (extrusion) direction conforming to those specified in Table II, as applicable.TABLE II. Mechanical PropertiesTemperThickness, (bar and shapes); diameter,(rod and wire); wall thickness, (tube)InchesArea Square Inches TensileStrengthMinimum ksi Yield Strength at 0.2 percent Offset or at extension indicatedElongation in2 inches or 4times D 1/Minimum percent Minimum ksi Extension under load inch perinch O AllAll 2/2/--10T6, T62 3/, Up to 0.249, incl All 78.070.00.0088 7T6510 and 0.250to 0.499, incl All 81.073.00.0090 7T6511 4/0.500to 2.999, inclAll 81.072.00.0090 73.000to 4.499, incl Up thru 2081.071.00.0088 73.000to 4.499, incl Over 20 thru 3278.070.00.0088 64.500to 5.000, incl Up thru 3278.068.00.0086 6T73,0.062to 0.249, incl Up thru 2068.058.00.0076 7T73510,0.250to 1.499, incl Up thru 2570.061.00.0079 8T73511 4/ 1.500to 2.999, incl Up thru 2569.059.00.0077 83.000to 4.499, incl Up thru 2068.057.00.0075 73.000to 4.499, inclOver 20 thru 3265.055.00.007371/D represents specimen diameter.2/No minimum required. Maximum tensile and yield strengths shall be 40.0 ksi and 24.0 ksi, respectively.3/Material in the T62 temper is not available from material producers.4/For stress-relieved tempers, the characteristics and properties, other than those specified, may differ somewhat from the corresponding characteristics and properties of the material in the basic temper.3.2.2.1Material in the O Temper: Material in the O temper, without the subsequent imposition of cold work or forming operations, shall, after proper solution heat treatment and artificial aging,develop the properties specified in Table II for the T62 temper. Material in the O temper, without the subsequent imposition of cold work or forming operations, shall be capable of being solution heat-treated and overaged (stabilized) to the properties specified for the T73 temper. Such capability shall be demonstrated when specified (See 6.2).3.2.2.2Material in the T6, T6510, T6511, T73, T73510, and T73511 Tempers: Material in the T6, T6510, T6511, T73, T73510, and T73511 tempers, without the subsequent imposition of cold work or forming operations, shall be capable of being solution heat-treated and artificially aged or overaged, as applicable, to the properties specified for the T62 and T73 tempers. Such capability shall be demonstrated when specified (See 6.2).3.3Internal Defects:When specified (See 6.2), bar, rod, tube, and shapes shall be ultrasonically inspected (SeeAMS-QQ-A-200). Acceptance limits shall be as specified in Table III. The technique for inspection of tube shall be as agreed upon by the procuring activity and the contractor (See 6.2).3.4Resistance to Stress-Corrosion Cracking:Material supplied in the T73, T73510, and T73511 tempers shall exhibit no evidence of stress-corrosion cracking when subjected to the test specified in 4.2. Sampling frequency shall be in accordance with AMS-QQ-A-200.TABLE III. Ultrasonic Discontinuity Acceptance Limits 1/Thickness, (bar and shapes); diameter(rod); wall thickness, (tube);inches 2/Maximum weightper piece poundsMaximum width to thicknessratio 3/Discontinuityclass 4/0.500 to 1.49960010 to 1B 1.500 and over60010 to 1A1/Discontinuities in excess of those listed in Table III may be allowed subject to approval of the procuring activity, if it is established that they will be removed by machining or that they are in noncritical areas.2/The thickness of any element of a shape shall be deemed to be the smallest dimension of that element, and the discontinuity class applicable to that particular thickness shall apply to that element of the shape.3/Not applicable to rod and tube.4/Discontinuity class limits are defined in MIL-STD-2154.3.4.1Lot Acceptance Criteria for Stress-Corrosion Cracking: Resistance to stress-corrosion cracking foreach inspection lot of 7075-T73, T73510, and T73511 material shall be established by testing the previously selected tensile test specimens to the following criteria:Determine electrical conductivity and tensile properties.If the conductivity is below 38.0 percent International Annealed Copper Standard (IACS), thematerial is considered unsatisfactory and must be reprocessed, regardless of property level.If the conductivity is 40.0 percent IACS or higher and tensile properties meet the minimum values specified herein, the material is considered to be satisfactory.If conductivity is 38.0 through 39.9 percent IACS, if tensile properties meet the minimum limitsspecified herein, and if the yield strength does not exceed the specified minimum by more than11.9 ksi, the material is considered to be satisfactory.If conductivity is 38.0 through 39.9 percent IACS and the yield strength exceeds the specifiedminimum value by 12.0 ksi or more, the material is considered suspect.When material is considered suspect, it may either be given additional second step aging or be reprocessed.3.5Marking:In addition to the marking required by AMS-QQ-A-200, material in the T6, T6510, T6511, T73,T73510, and T73511 tempers shall be identified by an inspection lot number marked in at least one location on each piece.4.QUALITY ASSURANCE PROVISIONS:See AMS-QQ-A-200 and the following:4.1Mechanical Tests After Heat Treatment:4.1.1Material in the O Temper: From material in the O temper, an additional number of specimens,equal to that required by AMS-QQ-A-200, shall be taken and tested after solution heat treatment and artificial aging to determine compliance with 3.2.2.1 relative to the T62 temper. Whenspecified (See 6.2), from material in the O temper, a number of specimens, equal to that required by AMS-QQ-A-200, shall be taken and tested after solution heat treatment and over-aging todetermine compliance with 3.2.2.1 relative to the T73 temper.4.1.2Material in Tempers Other Than O: When specified (See 6.2), from material in a temper other thanthe O temper, an additional number of specimens, equal to that required by AMS-QQ-A-200, shall be taken and tested after the appropriate solution heat treatment and aging treatment to determine compliance with 3.2.2.2.4.2Stress-Corrosion Cracking Test:Specimens shall be selected from 7075-T73, -T73510, and -T73511 material, 0.750 inch and greater in thickness, in a manner which will permit application of the specified tensile stress in the short-transverse direction with respect to grain flow. Specimens shall be stressed in tension in the short-transverse direction and held at constant strain. The stress level shall be 75 percent of the specified longitudinal yield strength. The specimens shall be subjected to the stress-corrosion test specified in AMS-QQ-A-200, the exposure duration to be 20 days. It is the responsibility of the contractor that test results be recorded, identified as to inspection lot, and maintained.4.3Electrical Conductivity Testing:Conductivity measurements shall be made prior to tensile testing on samples selected from the extruded 7075-T73, -T73510, and -T73511 material, to determine compliance with 3.4.1. For all material in the thickness range of 0.500 through 1.500 inches, conductivity measurements shall be made at the approximate center of the section thickness on a plane parallel to the longitudinalcenterline of the extrusion. For material over 1.500 inches in thickness, the conductivity shall be measured on the test coupon surface which is closest to the center of the extrusion thickness and ona plane parallel to the extrusion surface. For extruded sections of non-constant cross-sectionaldimensions, conductivity measurements shall be made at the center of the section possessing the greatest cross-sectional thickness. For material 0.101 through 0.499 inch in thickness, theconductivity shall be determined on the subsurface after removal of approximately 10 percent of the thickness from one surface. For material up through 0.100 inch in thickness, the conductivity shall be measured on the surface of the tensile test specimen. For curved surfaces, the conductivity shall be measured on a machined flat spot; however, for small sizes of tubes, a cut-out portion may be flattened and the conductivity determined on the surface.5.PREPARATION FOR DELIVERY:See AMS-QQ-A-200.6.NOTES:6.1Intended Use:This alloy is intended for use where high strength is required, and where good resistance to general corrosion is not important. The T6510 and T73510 tempers are intended primarily to provideextruded material with low residual stresses and consequent minimum distortion during machining.The T6511 and T73511 tempers are straightened T6510 and T73510 material respectively and may have unknown residual stresses and may or may not distort during machining. The T73, T73510, and T73511 tempers provide resistance to stress corrosion.6.2Properties After Heat Treatment:Mechanical properties and corrosion properties, where applicable, are certified for the temper of material supplied. The producer’s capability demonstration is not evidence that user-treated material conforms to property requirements of a given temper. Frequently, user-heat-treated material may develop a lower level of properties, especially if any cold, warm, or hot work is introduced prior to solution heat treatment. The user should be held responsible for demonstrating that his processing will yield properties meeting requirements.6.3Ordering Data:Purchasers should select the preferred options permitted herein and include the followinginformation in procurement documents:Title, number, and date of this specification.Form, quantity, and temper required (See 1.2.1).Dimensions required.Requirements for sizes not specifically covered (See AMS-QQ-A-200).Special end use requirements.Which, if any, demonstrations of heat treatability are to be performed where such demonstrations are optional (See 3.2.2.1 and 3.2.2.2).Whether ultrasonic inspection of material is required (See 3.3). Method of inspection of tubing,where applicable. Requirements for sizes, maximum weights, and discontinuityclasses not coveredin Table III.Selection of applicable levels of preservation, packaging, and packing (See AMS-QQ-A-200).6.4Product produced and marked to the requirements of AMS-QQ-A-200/11 also meets therequirements of QQ-A-200/11E. Product produced and marked to the requirements ofQQ-A-200/11E also meets the requirements of AMS-QQ-A-200/11.6.5The properties listed in 3.2.1 are exactly the same as QQ-A-200/11, Revision E. These propertieshave not been substantiated in accordance with the AMS Manual for Preparation of Aerospace Specifications.PREPARED UNDER THE JURISDICTION OF AMS COMMITTEE "D"。