节能搅拌反应器的应用
理想混合连续搅拌釜式反应器(CSTR)
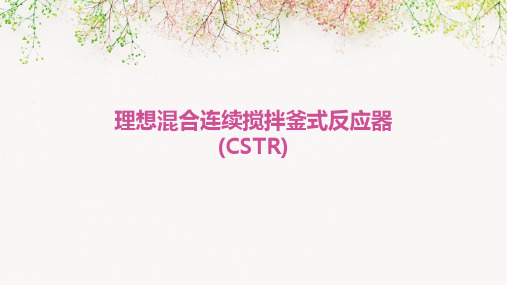
理想混合状态
物料在反应器内达到完全混合,不存在浓度和温度 的梯度分布。
反应器内各点的物料性质(如浓度、温度等)完全 相同,且随时间保持不变。
在理想混合状态下,反应器的性能达到最优,反应 效率和产物质量得到保证。
03
CSTR反应器的数学模型
物料平衡方程
进入反应器的物料流量与离开 反应器的物料流量相等,即输 入等于输出。
用于连续加入反应物和排出产物,实现连续化生产 。
工作流程
01
02
03
04
物料进入
反应物通过进料口连续加入反 应器内。
充分混合
在搅拌装置的作用下,物料在 反应器内充分混合,达到浓度 和温度的均匀分布。
反应进行
在适宜的反应条件下,物料在 反应器内进行化学反应。
产物排出
反应完成后,产物通过出料口 连续排出反应器。
100%
平均停留时间
表示物料在反应器内的平均停留 时间,影响反应器的生产能力和 产品质量。
80%
停留时间分布曲线
通过实验测定,可直观反映反应 器内物料的停留时间分布情况。
转化率与选择性
转化率
表示原料在反应器内转化为产 品的程度,是衡量反应器性能 的重要指标。
选择性
表示在给定转化率下,生成目 标产物的能力,反映反应器的 选择性能。
THANK YOU
感谢聆听
缺点与挑战
能耗较高
连续搅拌过程需要消耗大量能量,导致CSTR反应器的能耗相对较 高。
设备复杂度高
CSTR反应器结构复杂,涉及搅拌、传热、传质等多个过程,设备 设计、制造和维护难度较大。
放大效应
在将实验室规模的CSTR反应器放大至工业生产规模时,可能会遇到 放大效应问题,影响反应器的性能和产物质量。
搅拌式生物反应器(bilfinger型)标准操作规程

搅拌式生物反应器(bilfinger型)标准操作规程搅拌式生物反应器(bilfinger型)标准操作规程搅拌式生物反应器(bilfinger型)是一种常用于生物工程领域的设备,用于培养微生物、细胞和酶等生物体的生长和代谢过程。
为了确保反应器的正常运行和实验的准确性,制定一套标准的操作规程是非常重要的。
下面是搅拌式生物反应器(bilfinger型)的标准操作规程。
1. 准备工作a. 检查反应器的设备和配件是否完好无损,确保所有连接口和阀门处于关闭状态。
b. 清洗反应器和配件,使用适当的清洗剂和工具,彻底清除残留物和污垢。
c. 检查反应器的传感器和控制系统是否正常工作,确保温度、压力和pH等参数的准确测量和控制。
2. 培养基的制备a. 根据实验需求,准备适当的培养基,确保培养基的成分和浓度符合实验要求。
b. 使用无菌技术,将培养基倒入反应器中,确保反应器内部的环境无菌。
3. 微生物或细胞的接种a. 根据实验需求,选择适当的微生物或细胞进行接种。
b. 使用无菌技术,将微生物或细胞接种到反应器中,确保接种过程无菌。
4. 反应器的运行a. 启动搅拌器和加热系统,确保培养基的均匀搅拌和恒定温度。
b. 根据实验需求,调节搅拌速度和温度,确保反应器内的环境适合微生物或细胞的生长和代谢。
c. 定期监测和记录反应器内的温度、pH、溶氧度和压力等参数,确保实验的准确性和稳定性。
d. 根据实验需求,添加适量的营养物质和辅助剂,促进微生物或细胞的生长和代谢。
5. 反应结束和清洗a. 根据实验需求,确定反应的结束时间。
b. 关闭搅拌器和加热系统,停止培养基的搅拌和加热。
c. 使用无菌技术,将反应器内的培养基和微生物或细胞转移到适当的容器中,进行后续处理。
d. 清洗反应器和配件,使用适当的清洗剂和工具,彻底清除残留物和污垢。
e. 检查反应器的设备和配件是否完好无损,确保所有连接口和阀门处于关闭状态。
搅拌式生物反应器(bilfinger型)的标准操作规程对于实验的准确性和稳定性至关重要。
搅拌式生物反应器的原理
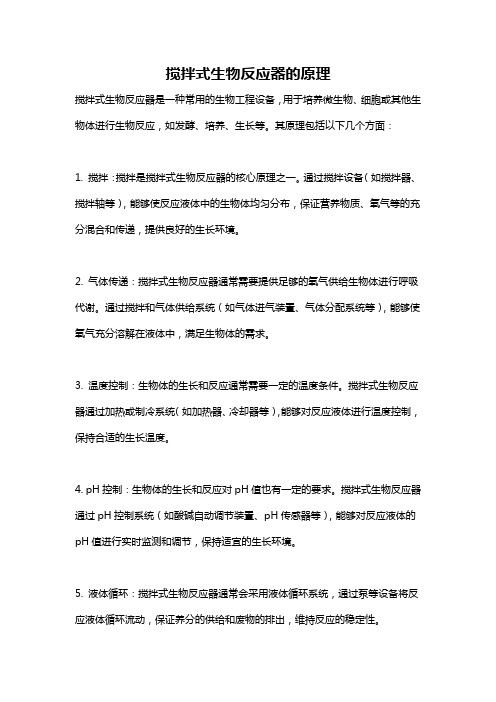
搅拌式生物反应器的原理
搅拌式生物反应器是一种常用的生物工程设备,用于培养微生物、细胞或其他生物体进行生物反应,如发酵、培养、生长等。
其原理包括以下几个方面:
1. 搅拌:搅拌是搅拌式生物反应器的核心原理之一。
通过搅拌设备(如搅拌器、搅拌轴等),能够使反应液体中的生物体均匀分布,保证营养物质、氧气等的充分混合和传递,提供良好的生长环境。
2. 气体传递:搅拌式生物反应器通常需要提供足够的氧气供给生物体进行呼吸代谢。
通过搅拌和气体供给系统(如气体进气装置、气体分配系统等),能够使氧气充分溶解在液体中,满足生物体的需求。
3. 温度控制:生物体的生长和反应通常需要一定的温度条件。
搅拌式生物反应器通过加热或制冷系统(如加热器、冷却器等),能够对反应液体进行温度控制,保持合适的生长温度。
4. pH控制:生物体的生长和反应对pH值也有一定的要求。
搅拌式生物反应器通过pH控制系统(如酸碱自动调节装置、pH传感器等),能够对反应液体的pH值进行实时监测和调节,保持适宜的生长环境。
5. 液体循环:搅拌式生物反应器通常会采用液体循环系统,通过泵等设备将反应液体循环流动,保证养分的供给和废物的排出,维持反应的稳定性。
总体来说,搅拌式生物反应器通过搅拌、气体传递、温度控制、pH控制和液体循环等原理,提供适宜的生长环境和条件,促进微生物、细胞或其他生物体的生长和反应。
反应器搅拌器的用途
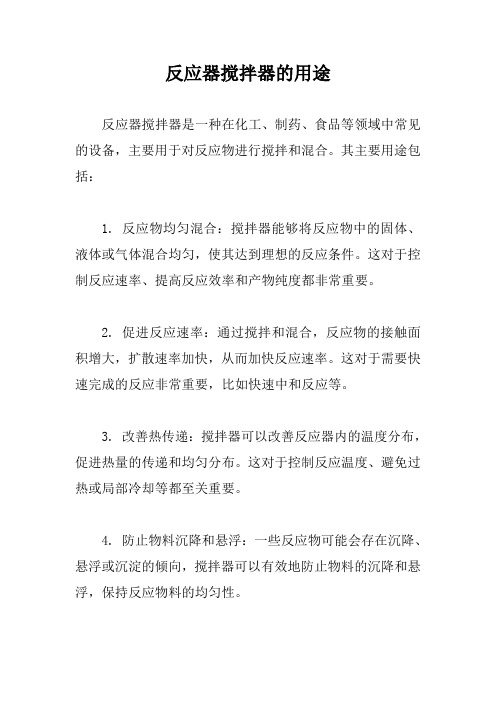
反应器搅拌器的用途
反应器搅拌器是一种在化工、制药、食品等领域中常见的设备,主要用于对反应物进行搅拌和混合。
其主要用途包括:
1. 反应物均匀混合:搅拌器能够将反应物中的固体、液体或气体混合均匀,使其达到理想的反应条件。
这对于控制反应速率、提高反应效率和产物纯度都非常重要。
2. 促进反应速率:通过搅拌和混合,反应物的接触面积增大,扩散速率加快,从而加快反应速率。
这对于需要快速完成的反应非常重要,比如快速中和反应等。
3. 改善热传递:搅拌器可以改善反应器内的温度分布,促进热量的传递和均匀分布。
这对于控制反应温度、避免过热或局部冷却等都至关重要。
4. 防止物料沉降和悬浮:一些反应物可能会存在沉降、悬浮或沉淀的倾向,搅拌器可以有效地防止物料的沉降和悬浮,保持反应物料的均匀性。
5. 排除质量梯度:在某些情况下,反应物料可能存在质量梯度,例如浓度变化、固体颗粒大小分布等。
搅拌器能够减小或排除质量梯度,使得反应获得更加一致的产物。
总而言之,反应器搅拌器在化工生产中扮演着非常重要的角色,通过搅拌和混合,它能够实现反应物料的均匀性、速率控制和温度分布的改善,提高反应效率和产物质量。
各种反应器特点优缺点及应用
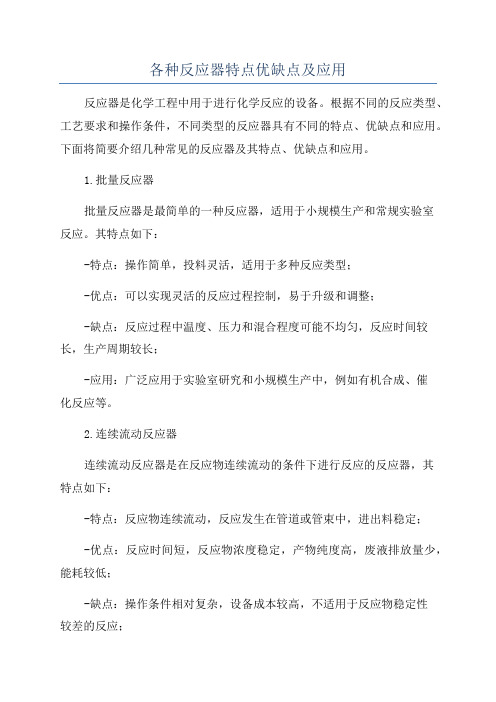
各种反应器特点优缺点及应用反应器是化学工程中用于进行化学反应的设备。
根据不同的反应类型、工艺要求和操作条件,不同类型的反应器具有不同的特点、优缺点和应用。
下面将简要介绍几种常见的反应器及其特点、优缺点和应用。
1.批量反应器批量反应器是最简单的一种反应器,适用于小规模生产和常规实验室反应。
其特点如下:-特点:操作简单,投料灵活,适用于多种反应类型;-优点:可以实现灵活的反应过程控制,易于升级和调整;-缺点:反应过程中温度、压力和混合程度可能不均匀,反应时间较长,生产周期较长;-应用:广泛应用于实验室研究和小规模生产中,例如有机合成、催化反应等。
2.连续流动反应器连续流动反应器是在反应物连续流动的条件下进行反应的反应器,其特点如下:-特点:反应物连续流动,反应发生在管道或管束中,进出料稳定;-优点:反应时间短,反应物浓度稳定,产物纯度高,废液排放量少,能耗较低;-缺点:操作条件相对复杂,设备成本较高,不适用于反应物稳定性较差的反应;-应用:广泛应用于底物稳定性较好的化学反应,如合成化学和催化反应等。
3.管式反应器管式反应器是一种连续流动反应器,具有管状结构,反应物在管内流动进行反应。
其特点如下:-特点:反应物在直管中流动,具有较大的接触面积和较高的传热效率;-优点:反应时间短,反应速度快,能够实现高温反应和高压反应;-缺点:管内积垢和堵塞的问题较突出,操作不够灵活,难以对反应过程进行调控;-应用:广泛应用于有机合成、聚合反应、氧化反应等。
4.搅拌式反应器搅拌式反应器是一种常见的批量反应器,其特点如下:-特点:反应物在搅拌器的作用下进行混合和反应;-优点:能够实现较好的混合程度,反应均匀,温度、压力和浓度控制相对容易;-缺点:能耗较高,产物分布不均匀,反应速率受到混合效果的影响;-应用:广泛应用于有机合成、聚合反应、酯化反应等。
5.固定床反应器固定床反应器是将催化剂固定在固体床上进行反应的反应器-特点:催化剂固定,反应物流经固体床进行反应;-优点:反应过程相对稳定,操作简单,可以持续生产较长时间;-缺点:反应物质传质受到限制,催化剂活性容易降低,床层温度不易均匀;-应用:广泛应用于催化反应,如重油加氢、氯化反应等。
CSTR 反应器
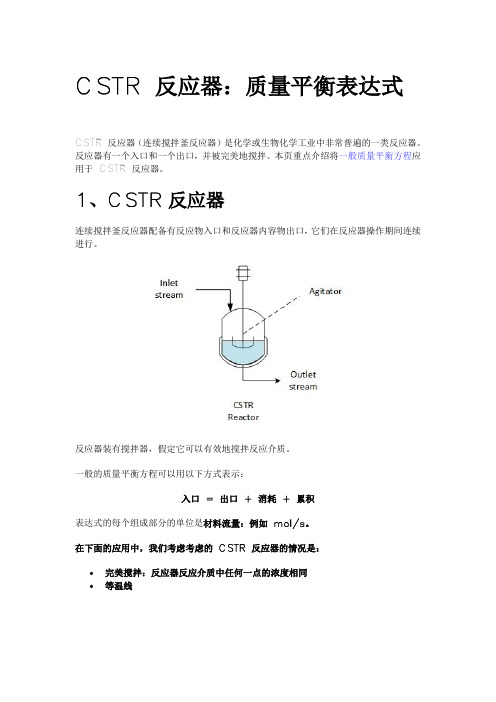
CSTR 反应器:质量平衡表达式CSTR 反应器(连续搅拌釜反应器)是化学或生物化学工业中非常普遍的一类反应器。
反应器有一个入口和一个出口,并被完美地搅拌。
本页重点介绍将一般质量平衡方程应用于CSTR 反应器。
1、CSTR反应器连续搅拌釜反应器配备有反应物入口和反应器内容物出口,它们在反应器操作期间连续进行。
反应器装有搅拌器,假定它可以有效地搅拌反应介质。
一般的质量平衡方程可以用以下方式表示:入口= 出口+ 消耗+ 累积表达式的每个组成部分的单位是材料流量:例如mol/s。
在下面的应用中,我们考虑考虑的CSTR 反应器的情况是:•完美搅拌:反应器反应介质中任何一点的浓度相同•等温线2. CSTR反应器完全搅拌并处于稳定状态:物料平衡让我们假设反应物 A 和 B 被引入反应器。
反应A +B =C +D生成 C 和D。
入口处只有 A 和B,但在出口流中我们可以发现 A 和 B 未反应,而 C 和D。
与在反应发生时浓度始终变化的间歇式和半间歇式反应器相反,CSTR 反应器具有在稳态下运行的特性,这意味着在入口和出口之间找到平衡,可以防止积累(正或负)在反应器中。
稳态意味着:dnA/dt = dnB/dt = dnC/dt = dnD / dt = 0除了反应器处于稳定状态外,反应体积不会随时间变化,这意味着我们可以直接使用材料平衡方程中的体积V。
将反应器完全搅拌的事实也有助于表达反应物和产物的消耗/产生,因为它可以表示为反应速度与体积(r'V) 和浓度的乘积。
完全搅拌意味着:[A]reactor = [A]out[B]reactor = [B]out[C]reactor = [C]out[D]reactor = [D]out每个组分的质量平衡将如下(r'是消耗速度,r是形成速度):反应性AQ输入*[A]输入= Q输出*[A]输出 + r' A .V + 0反应BQ in *[B] in = Q out *[B] out + r' B .V + 0产品C0 = Q输出*[C]输出+ r C .V + 0产品D0 = Q输出*[D]输出+ r D .V + 03. CSTR反应器搅拌完美且处于稳定状态:反应速度反应速度系统可以由上述方程表示如下:r' A = (Q in .[A] in - Q out *[A] out )/Vr' B = (Q in .[B] in - Q out *[B] out )/Vr C =Q输出*[C]输出/Vr D = Q输出*[D]输出/V这些是稳态CSTR 的特征方程。
搅拌反应器原理

搅拌反应器原理在化学工程领域,搅拌反应器是一种常见的反应器类型。
它通过搅拌装置将反应物混合均匀,并提供良好的热质传递,从而实现化学反应的进行。
本文将介绍搅拌反应器的原理、结构和应用。
一、搅拌反应器的原理搅拌反应器的原理是利用搅拌装置对反应物进行混合,从而增加反应速率,提高反应效果。
搅拌装置通常由搅拌桨、轴和驱动装置组成。
搅拌桨的形式可以有螺旋桨、螺帽桨、葉轮桨等多种形式,根据不同的反应条件和需求选择合适的搅拌桨。
搅拌反应器在反应过程中起到了以下几个重要作用:1. 将反应物混合均匀:搅拌装置能够将液体或固体反应物充分混合,使其达到均一的反应条件,从而提高反应速率。
2. 促进质量传递:搅拌反应器中的搅拌装置通过不断搅动,能够促进反应物质量的传递,加速反应速率。
3. 保持温度均匀:搅拌反应器中的搅拌装置还可以通过增加液体的对流传热,保持反应器内温度均匀,防止反应物发生局部过热或过冷的现象。
二、搅拌反应器的结构搅拌反应器通常由反应容器、搅拌装置、加热或冷却装置、进料口、出料口等组成。
1. 反应容器:反应容器通常是由耐酸碱或耐高温材料制成,如玻璃或不锈钢。
根据反应物的性质和反应条件的要求,选择合适的反应容器材料。
2. 搅拌装置:搅拌装置是搅拌反应器中最重要的部分,它能够将反应物搅拌均匀。
搅拌装置的形式多种多样,根据反应物的性质和反应条件的要求选择合适的搅拌装置。
3. 加热或冷却装置:加热或冷却装置能够提供和控制反应过程中的温度。
常见的加热方式包括电炉、水浴、油浴等,冷却方式可以包括外部循环冷却水或使用冷凝器等。
4. 进料口和出料口:进料口用于将反应物加入反应器中,出料口用于取出反应产物或样品。
三、搅拌反应器的应用搅拌反应器广泛应用于化工、制药、食品等领域,常见的应用包括溶解、中和、酯化、聚合等反应过程。
搅拌反应器具有以下优点:1. 可控性强:搅拌反应器可以通过调节搅拌速度、温度等参数来控制反应速率和反应效果。
CSTR反应器
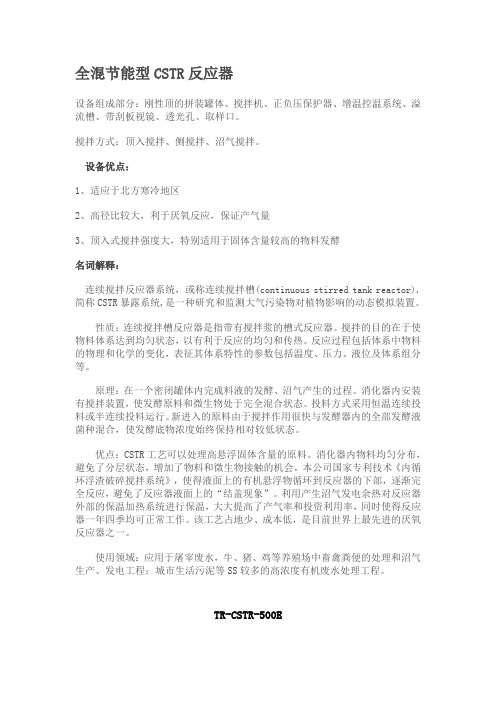
全混节能型CSTR反应器设备组成部分:刚性顶的拼装罐体、搅拌机、正负压保护器、增温控温系统、溢流槽、带刮板视镜、透光孔、取样口。
搅拌方式:顶入搅拌、侧搅拌、沼气搅拌。
设备优点:1、适应于北方寒冷地区2、高径比较大,利于厌氧反应,保证产气量3、顶入式搅拌强度大,特别适用于固体含量较高的物料发酵名词解释:连续搅拌反应器系统,或称连续搅拌槽(continuous stirred tank reactor),简称CSTR暴露系统,是一种研究和监测大气污染物对植物影响的动态模拟装置。
性质:连续搅拌槽反应器是指带有搅拌浆的槽式反应器。
搅拌的目的在于使物料体系达到均匀状态,以有利于反应的均匀和传热。
反应过程包括体系中物料的物理和化学的变化,表征其体系特性的参数包括温度、压力、液位及体系组分等。
原理:在一个密闭罐体内完成料液的发酵、沼气产生的过程。
消化器内安装有搅拌装置,使发酵原料和微生物处于完全混合状态。
投料方式采用恒温连续投料或半连续投料运行。
新进入的原料由于搅拌作用很快与发酵器内的全部发酵液菌种混合,使发酵底物浓度始终保持相对较低状态。
优点:CSTR工艺可以处理高悬浮固体含量的原料。
消化器内物料均匀分布,避免了分层状态,增加了物料和微生物接触的机会。
本公司国家专利技术《内循环浮渣破碎搅拌系统》,使得液面上的有机悬浮物循环到反应器的下部,逐渐完全反应,避免了反应器液面上的“结盖现象”。
利用产生沼气发电余热对反应器外部的保温加热系统进行保温,大大提高了产气率和投资利用率,同时使得反应器一年四季均可正常工作。
该工艺占地少、成本低,是目前世界上最先进的厌氧反应器之一。
使用领域:应用于屠宰废水,牛、猪、鸡等养殖场中畜禽粪便的处理和沼气生产、发电工程;城市生活污泥等SS较多的高浓度有机废水处理工程。
TR-CSTR-500ETR-CSTR-500/F适用原料种类:所有类型畜禽粪便、屠宰场垃圾、酒糟及糟液、生物柴油垃圾、厨房垃圾、废弃油脂、食品加工厂垃圾、乳液加工厂垃圾、其它可消化有机废弃物。
简述搅拌式反应设备的结构组成

简述搅拌式反应设备的结构组成搅拌式反应设备是一种常用的化工设备,广泛应用于化学反应、混合和溶解等工艺过程中。
它由多个组成部分构成,包括反应器、搅拌器、加热器、冷却器、传感器、控制系统等。
下面将对搅拌式反应设备的结构组成进行详细介绍。
一、反应器反应器是搅拌式反应设备的核心部件,用于容纳反应物质进行化学反应。
反应器通常由壳体、进料口、出料口、搅拌器支承构架等组成。
壳体一般采用耐腐蚀的材料,如不锈钢、玻璃钢等。
进料口和出料口的位置通常根据反应物质的性质和反应过程的要求进行设计。
搅拌器支承构架用于支撑搅拌器,并能够调节搅拌器的位置和角度。
二、搅拌器搅拌器是搅拌式反应设备中起到搅拌和混合作用的部件。
它通常由搅拌轴、搅拌叶片和搅拌电机等组成。
搅拌轴一般采用耐腐蚀的材料,如不锈钢、玻璃钢等。
搅拌叶片的形状和数量根据反应过程的要求进行设计,常见的搅拌叶片有桨叶、锚叶、螺旋叶等。
搅拌电机用于驱动搅拌轴旋转,其功率和转速根据反应物质的性质和反应过程的要求进行选择。
三、加热器和冷却器加热器和冷却器是搅拌式反应设备中用于控制反应温度的部件。
加热器通常采用电加热、蒸汽加热或导热油加热等方式进行加热。
冷却器通常采用冷却水或制冷剂进行冷却。
加热器和冷却器的设计和选择需要考虑反应物质的热敏性和反应过程的热平衡。
四、传感器传感器是搅拌式反应设备中用于监测反应过程的部件。
常见的传感器有温度传感器、压力传感器、流量传感器等。
这些传感器可以实时监测反应过程中的温度、压力、流量等参数,并将其传输给控制系统进行处理和控制。
五、控制系统控制系统是搅拌式反应设备中用于控制和调节反应过程的部件。
它由计算机、PLC控制器、触摸屏等组成。
控制系统可以根据传感器的反馈信号,实时调节反应器的温度、压力、搅拌速度等参数,以实现反应过程的自动化控制。
搅拌式反应设备的结构组成主要包括反应器、搅拌器、加热器、冷却器、传感器和控制系统。
这些组成部分相互协作,实现了反应过程的控制和调节,提高了生产效率和产品质量。
CSTR反应器关键技术的应用实例

CSTR反应器关键技术的应用实例首先介绍CSTR。
CSTR是一种反应器形式,是连续搅拌反应器。
我们知道现在市面的厌氧反应器,主要处理两类物质:废水、固废。
废水我们都知道厌氧反应器有UASB、IC 、EGSB等很多各种花式变样的反应器类型。
但是这些反应器在用于固废处理的过程中,都遇到了固含量太高,没办法实现分离的问题。
因此在对于厌氧消化系统中,反而是最原始的80年代最早期,早于UASB的全混式搅拌反应器,CSTR 更适用于固体废弃物处理,实现了介质的充分接触反应。
污泥啊,废渣等都是在反应器内充分反应后,出液直接通过固液分离系统分离就可以了。
固态厌氧消化具有什么特点呢,为什么需要用固态厌氧消化,这个我们就需要和他同类的处理技术相比较了。
所有的处理技术都是以以下两点为出发点的:1.是否能实现有效的减量:湿物质总体积的减量,也就是含水量;干物质含量的减量;2.是否能实现能耗平衡,就是自持处理,这块涉及了初建投资和后期收益。
之前的污泥污泥干化、脱水技术都是在于减少污泥总体积,而目前有很多分解技术,也都是利用热、化学、热+化学、电等手段去减少固废(污泥、废渣等)的干物质量,而这些很热的分解技术,都是以尽量降低初建投资占地,投资成本,实现更好的减量为目的进行处理的。
这样的技术成本相对较高,后期收益较低。
而我们的厌氧消化技术则具有:1资源化利用高效,提供可直接利用的高品位沼气;2与好氧处理相比,不需要通风动力,运行成本低;3产物可再利用,用于土壤调理剂;4弱化蛋白质之间的作用力,引起污泥絮解体,提高污泥降解率及脱水性能。
这就是一个常规的厌氧消化系统,带沼气净化及CHP热电联产。
固废及污泥的厌氧消化有2类,主要是根据不同的温度范围划分的——高温厌氧和中温厌氧。
我们通常所说35-37度的就是中温厌氧。
在国内普遍采用的也都是中温厌氧消化系统较多,我们白龙港的污水厂,那出了名的8个蛋就是。
我们这里主要要介绍的是高温厌氧CSTR 反应器。
化学工程学中的反应器设计与优化

化学工程学中的反应器设计与优化反应器是化学工程学中至关重要的设备,用于进行化学反应以转化原料为所需产品。
合理的反应器设计与优化能够显著提高反应效率、降低能耗、优化产物选择以及改进产品质量。
在本文中,我将向大家介绍一些常见的反应器设计原则和优化方法,以及它们在化学工程中的应用。
1. 反应器设计原则在进行反应器设计之前,首先需要明确反应的特性以及实验结果。
以下是一些反应器设计的基本原则:1.1 反应动力学:了解反应速率、反应转化率以及副产物生成情况,以便选择合适的反应机制和工艺。
1.2 热平衡:确保反应温度在合适的范围内,避免副反应的产生或催化剂失活。
1.3 高选择性:通过选择合适的反应条件和控制反应物的浓度,提高目标产物的选择性。
1.4 良好的传质与传热性能:保证反应物和热量在反应器中的传递有效,并减少质量传递的限制。
2. 反应器类型及应用根据反应物的性质和反应条件的不同,化学工程中常见的反应器类型包括:2.1 批量反应器:适用于小规模反应或需要对反应物进行处理的情况。
2.2 连续流动反应器:适用于大规模生产或连续反应过程的情况,具有较高的反应效率。
2.3 固定床反应器:适用于气体相反应和吸附过程,常见于催化剂反应。
2.4 搅拌槽反应器:适用于液态反应,可通过搅拌来提高传质和传热性能。
3. 反应器的优化方法为了提高反应器效率并降低生产成本,反应器的优化成为研究重点。
以下是一些常见的反应器优化方法:3.1 流程模拟与优化:通过建立反应动力学模型和流程模拟软件,优化反应物的流程和条件,以达到最佳操作参数。
3.2 催化剂的选择和改进:通过催化剂的优化选择或制备新的催化剂,提高反应选择性和活性。
3.3 反应体积的优化:优化反应器的尺寸和体积,以提高反应效率并降低能耗。
3.4 传热与传质性能的改进:改善反应器的传热和传质性能,提高反应速率和选择性。
3.5 投料方式的优化:选择合适的投料方式,确保反应物的均匀分布和充分混合。
压电搅拌技术
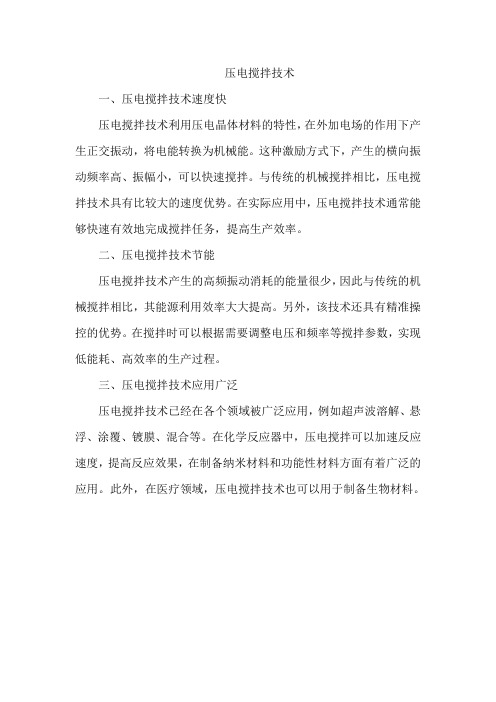
压电搅拌技术
一、压电搅拌技术速度快
压电搅拌技术利用压电晶体材料的特性,在外加电场的作用下产生正交振动,将电能转换为机械能。
这种激励方式下,产生的横向振动频率高、振幅小,可以快速搅拌。
与传统的机械搅拌相比,压电搅拌技术具有比较大的速度优势。
在实际应用中,压电搅拌技术通常能够快速有效地完成搅拌任务,提高生产效率。
二、压电搅拌技术节能
压电搅拌技术产生的高频振动消耗的能量很少,因此与传统的机械搅拌相比,其能源利用效率大大提高。
另外,该技术还具有精准操控的优势。
在搅拌时可以根据需要调整电压和频率等搅拌参数,实现低能耗、高效率的生产过程。
三、压电搅拌技术应用广泛
压电搅拌技术已经在各个领域被广泛应用,例如超声波溶解、悬浮、涂覆、镀膜、混合等。
在化学反应器中,压电搅拌可以加速反应速度,提高反应效果,在制备纳米材料和功能性材料方面有着广泛的应用。
此外,在医疗领域,压电搅拌技术也可以用于制备生物材料。
搅拌罐式反应器原理

搅拌罐式反应器原理搅拌罐式反应器是一种广泛应用于化学工程领域的反应器,其原理基于搅拌罐内的物质混合和化学反应。
本文将详细介绍搅拌罐式反应器的原理、结构和应用。
一、搅拌罐式反应器的原理搅拌罐式反应器是一种连续反应器,其反应原理基于物质在搅拌罐内的混合和化学反应。
在反应器中,搅拌器将反应物混合并保持均匀,从而促进化学反应的进行。
同时,反应器内的温度、压力和pH 值等参数也会对反应速率和反应产物的选择性产生影响。
搅拌罐式反应器的混合原理是通过搅拌器的旋转和液体的流动来实现的。
搅拌器的旋转可以使反应物之间产生剪切力和湍流,从而增加反应物之间的接触面积,促进反应物的反应。
液体的流动则可以使反应物在反应器内均匀分布,避免反应物在反应器中的局部堆积和形成死区,从而保证反应的均匀性。
除了混合原理外,搅拌罐式反应器的反应原理还与反应物的物理性质、化学反应的类型以及反应器的操作条件等因素有关。
例如,当反应物为液体时,反应器的操作条件可以调节温度、压力和pH值等参数来影响反应速率和反应选择性。
当反应物为气体时,反应器的操作条件可以调节反应器内的气体流速和压力等参数来影响反应速率和反应选择性。
二、搅拌罐式反应器的结构搅拌罐式反应器的结构一般包括反应器本体、搅拌器、加料装置、温度控制装置、压力控制装置、pH控制装置等组成。
下面将详细介绍每个部分的结构和功能。
1. 反应器本体:反应器本体一般由容器、进出口管道、排放装置等组成。
容器一般为圆柱形或球形,内壁光滑,表面光洁,以便于反应物的混合和流动。
进出口管道一般安装在反应器的顶部和底部,用于加入反应物和排放反应产物。
排放装置一般是一个阀门或泵,用于控制反应产物的排放。
2. 搅拌器:搅拌器是搅拌罐式反应器的核心部件,其作用是将反应物混合并保持均匀,从而促进化学反应的进行。
搅拌器的结构一般包括旋转轴、搅拌叶片、驱动装置等。
搅拌叶片的形状和数量可以根据不同的反应类型和反应条件进行设计。
超声波搅拌反应器工作原理

超声波搅拌反应器工作原理超声波搅拌反应器是一种利用超声波作为能量源进行物质混合、催化反应和溶解等过程的装置。
它通过将电能转换为超声波能量,使液体中的分子发生剧烈振动和撞击,从而实现混合反应的目的。
其工作原理主要包括超声波的产生、传播和作用三个方面。
超声波的产生是通过超声波发生器完成的。
超声波发生器中的压电陶瓷片受到电压激励后,会发生压电效应,即在电场的作用下发生形变。
当电场频率与陶瓷片的固有频率相同时,陶瓷片会发生共振,产生高频振动,从而产生超声波。
超声波的传播是通过超声波换能器和反应器中的介质完成的。
超声波换能器是将发生器产生的电能转换为超声波能量的装置,它包括压电陶瓷片和金属震荡片。
当陶瓷片振动时,金属震荡片也会跟随振动,将电能转换为机械能,进而产生超声波。
超声波通过换能器的震动传递到反应器中的液体介质中,液体介质中的分子受到超声波的作用而发生振动和撞击。
超声波的作用是通过超声波的剧烈振动和撞击来实现的。
当超声波传播到液体介质中时,超声波能量会使液体中的分子发生高频振动。
这种振动可以增加分子之间的碰撞频率和能量,从而促进物质的混合和反应。
同时,超声波的剧烈振动也可以破坏液体中的大分子聚集体,使其分散为更小的颗粒,提高反应效率。
此外,超声波还可以改变液体介质的物理性质,如粘度、表面张力等,从而影响反应的进行。
总的来说,超声波搅拌反应器利用超声波的产生、传播和作用来实现物质的混合、反应和溶解等过程。
通过超声波的剧烈振动和撞击,可以提高反应速率和效果,减少反应时间和能量消耗。
超声波搅拌反应器在化学、生物、医药等领域具有广泛的应用前景,为实现高效、节能、环保的反应过程提供了一种新的技术手段。
化工搅拌器的设计

1绪论1.1 搅拌器的概述1.1.1搅拌器的应用范围机械搅拌反应器适用于各种物性(如粘度、密度)和各种操作条件(温度、压力)的反应过程,广泛应用于合成材料、合成纤维、合成橡胶、医药、农药、化肥、染料、涂料、食品、冶金、废水处理等行业。
如实验室的搅拌反应器可小至数十毫升,而污水处理、湿法冶金、磷肥等工业大型反应器的容积可达数千立方米。
除用作化学反应器和生物反应器外,搅拌反应器还可大量用于混合、分散、溶解、结晶、萃取、吸收或解吸、传热等操作。
搅拌反应器由搅拌容器和搅拌机两大部分组成。
搅拌容器包括筒体、换热元件及内构件。
搅拌器、搅拌轴、及其密封装置、传动装置等统称为搅拌机。
1.1.2搅拌器的工作原理通常搅拌装置由作为原动机的马达(电动、风动或液压),减速机与其输出轴相连的搅拌抽,和安装在搅拌轴上的叶轮组成减速机体通过一个支架或底板与搅拌容器相连。
当容器内部有压力时,搅拌轴穿过底板进入容器时应有一个密封装置,常用填料密封或机械密封。
通常马达与密封均外购,研究的重点是叶轮。
叶轮的搅拌作用表现为“泵送”和涡流”,即产生流体速度和流体剪切,前者导至全容器中的回流,介质易位,防止固体的沉淀并产生对换热热管束 (如果有)的冲刷;剪切是一种大回流中的微混合,可以打碎气泡或不可溶的液滴,造成“均匀”。
1.1.3化工反应中的搅拌设备根据搅拌器叶轮的形状可以分成直叶桨式、开启涡轮式、推进式、圆盘涡轮式、锚式、螺带式、螺旋式等}根据处理的掖体牯度不同可以分为低粘度液搅拌器。
低粘度液搅拌器,如:三叶推进式、折叶桨叶,6直叶涡轮式、超级混合叶轮式 HR 100,HV 100等;中高粘度液搅拌器如:锚式、螺杆叶轮式、双螺旋螺带叶轮型,MR 205,305超混合搅拌器等等。
1.2化工搅拌器的适应条件和构造1.2.1化工搅拌器的适应条件搅拌加速传热和传质,在化工设备中广泛运用。
化工搅拌器的作用使化工生产中的液体充分混合,以满足化学反应能够最大程度的进行,该设备可以代替手动搅拌对人体有毒或对皮肤有伤害的化工原料减少对人体的危害,同时通过电动机带动轴加速搅拌,提高生产率。
搅拌反应器中颗粒完全离底悬浮的临界转速

搅拌反应器中颗粒完全离底悬浮的临界转速搅拌反应器是一种常见的工业设备,广泛应用于化工、制药、冶金、食品等领域。
在搅拌反应器中,将物料通过搅拌器搅拌,使得反应物充分混合,从而实现反应的发生及产物的生成。
因此,搅拌器的性能对反应器的效率、安全性及产物质量均有着重要的影响。
在搅拌反应器中,随着搅拌速度的增加,颗粒会逐渐脱离容器底部,形成悬浮状态,这种现象称为颗粒的离底悬浮。
当搅拌速度 d 达到一定值时,颗粒能够完全离底悬浮,不再接触容器底部,此时的搅拌速度称为临界转速 nc。
在实际工业生产中,了解临界转速的大小非常重要,可以为反应器的设计、操作及维护提供依据。
临界转速的大小与多种因素有关,如颗粒大小、密度、形状等。
一般来说,颗粒较大、密度较大、形状较圆滑的颗粒,临界转速较低;而颗粒较小、密度较小、形状较不规则的颗粒,临界转速较高。
此外,液体的物理性质和容器的几何形状也会对临界转速产生影响。
在实际工程中,可以通过实验来测定临界转速。
常用的实验方法有两种,一种是观察颗粒的变化,另一种是通过转速调节法测定临界转速。
首先介绍观察颗粒的变化法。
在操作过程中,加入一个颜色比较鲜艳的指示剂,使得颗粒的离底悬浮状态更加明显。
然后,在逐渐增加搅拌速度的过程中,观察颗粒状态的变化,当颗粒完全离底悬浮时,记录此时的搅拌速度作为临界转速。
其次介绍转速调节法。
在操作过程中,通过调节搅拌器的转速,使得颗粒从完全沉降到完全离底悬浮的过渡状态更加平滑。
具体实验步骤如下:(1)将反应容器放置在搅拌反应器内,加入追踪颜色剂和适量的颗粒样品;(2)将搅拌器转速逐步增加,直到颗粒开始离底悬浮,记录此时的转速 v1;(4)将搅拌器的转速稍微降低,使得颗粒从完全离底悬浮到完全沉降的过渡过程更加平滑,将此时的转速记录为临界转速 nc。
通过实验,可以得到临界转速与颗粒物理性质、液体物理性质及容器形状等因素的关系,可以为搅拌反应器的设计和运行提供重要的参考依据。
cstr混合方式 -回复

cstr混合方式-回复什么是cstr混合方式?CSTR,即完全搅拌反应器,是一种化工生产中常用的反应器类型。
它被广泛应用于液相和气液相反应过程中,特别适用于高速转化反应和连续操作模式。
CSTR混合方式的主要特点是在反应器内部,通过机械搅拌或气体的循环使反应物在整个反应过程中保持均匀混合状态。
这种混合方式的优点在于能够提供良好的反应速度和高产品产率。
CSTR混合方式的工作原理是将反应物通过进料管道输送到反应器内部,然后在反应器内进行搅拌或循环使反应物均匀混合。
反应过程中,反应物在反应器内停留的时间相对较短,因此可以进行连续生产。
在CSTR混合方式中,反应物的浓度和产物的浓度在反应器内部是均匀分布的,反应速率常常受到温度和浓度的影响。
对于CSTR混合方式,有几个关键参数需要考虑。
首先是反应速度常数k,它可以通过实验测定得到。
k值越大,反应速度越快。
其次是反应物的浓度C,它决定了反应速率。
当反应物的浓度较高时,反应速率较快。
此外,还需要考虑反应器的体积V,体积越大,反应物停留的时间越长,反应物的转化率也会相应增加。
CSTR混合方式的优点之一是能够适应不同反应物和反应条件的需求。
它可以用于液相反应和气液相反应,并且很容易进行规模化生产。
此外,CSTR混合方式还具有稳定的反应过程和良好的产品质量控制能力。
然而,CSTR混合方式也存在一些局限性。
由于反应物在反应器内的停留时间较短,可能导致反应转化率较低。
此外,由于反应物在反应器内部均匀分布,不同组分的物质可能会发生竞争反应,从而降低了所需产物的选择性。
针对CSTR混合方式的局限性,在实际应用中可以采取一些措施进行改进。
例如,可以通过调节反应物的进料量和反应器的体积,以使反应物停留的时间延长,从而提高反应物的转化率。
此外,还可以通过添加催化剂或控制反应物的浓度来改善所需产物的选择性。
总而言之,CSTR混合方式在化工生产中具有广泛的应用前景。
它通过机械搅拌或气体循环的方式,保证了反应物在反应过程中的均匀混合状态,提供了良好的反应速率和高产率。
- 1、下载文档前请自行甄别文档内容的完整性,平台不提供额外的编辑、内容补充、找答案等附加服务。
- 2、"仅部分预览"的文档,不可在线预览部分如存在完整性等问题,可反馈申请退款(可完整预览的文档不适用该条件!)。
- 3、如文档侵犯您的权益,请联系客服反馈,我们会尽快为您处理(人工客服工作时间:9:00-18:30)。
图 1 反应器结构示意图 来自 ・5 0・ 安 徽 冶 金 科 技 职 业 学 院 学 报
2 0 1 4年第 3期
2 生物反应器重新设计情况
2 . 1 对生 物反应器 装 置重 新设 计
2 . 2 . 3 桨 叶弧形 结 构
叶 片的弧 形 结构 和相 应 半 径 。通过 几 何 形状 保证 浆 叶前端 受到 冲击较 小 , 中心部 分形成 一股很 强 的 向下 的力 推 动 液 体 流动 。叶 片 的弧形 从 中心 由不规则 的 2 4 。 转到 1 2 。 。叶 片 的弧形 结构 可增 强
。
搅拌 功率 计算 公式 如下 :
P =N P・ P・ Ⅳ3・ d
均匀 , 达到中和、 酸解完全反应 的目的。 2 . 2 对搅拌 装置重 新设 计 固液悬浮是借助搅拌装置的作用 , 使固体颗粒 悬浮 在液体 中 , 形成 固液 混合 物 或悬 浮液 。均匀悬 浮的主要控制因素是循环速率及湍流强度 , 其中容 积循环速率( 即搅拌流量 ) 又是最主要 的因素。搅 拌流量计算公式如下 :
收稿日期 : 2 0 1 4-0 5-0 1
l : J j / l 料管 2 简体 3 : 上搅拌浆叶 耐} i } 拌轴 s - . - F 搅拌浆叶 礅 料阀
作者简介: 高志林 ( 1 9 6 3 一) , 男, 安 徽淮南 人 , 安徽丰 原马鞍 山生 物化学有 限公 司总经理 , 工程师。
1 . 1 生物反应 器装 备 结构 不合 理
主要体现在结构尺寸较小 , 装备和搅拌选型不 合理。装 备 容 器 直 径 在 2 0 0 0 m m、 高度 在 3 4 0 0 m m, 高径比在 1 . 7 , 装填容积为 1 0 m , 料液装填量 较小。搅拌装置采用斜叶桨式搅拌 , 该桨叶直径与 容器内径之 比为 0 . 4 , 转速为 6 0 r / m i n 一 7 0 r / m i n , 配备的电机为 7 . 5 k W, 单位体积能耗为 0 . 7 5 k W /
在中和、 酸解过程中采用 的生物反应器装备为 普通型结构形式 , 该装备在使用过 程中 , 存在物料 混合不均匀 、 能耗大、 结垢严重 等问题。通过对 反 应器、 搅拌装置重新设计 , 提 高反应器 内壁及搅 拌
器的加工精度 , 经使用验证 , 提高 了产 品质量和生 产效率 , 降低能耗 和装置结垢现象 , 提高 了公司经 济效 益 。
后, 加入硫酸( H : S O ) 产生复分解反应 ( 即酸解 ) ,
钙盐晶体 中包夹 有机酸钙盐 , 检测分析包 夹量为
0 . 5 %, 说明物料反应不完全。原因与装备结构不 合理有关系。
1 . 3 生物反 应器 结垢 严重
生成溶解度极小的硫酸钙盐 , 过滤后得 到纯度更高
的有机 酸溶液 。
V o 1 . 2 4 . N o . 3
J u 1 .2 O 1 4
节 能 搅 拌 反 应 器 的 应 用
高志林
( 安徽马鞍 山丰原生物化学有限公 司 安徽马鞍 山 2 4 3 0 0 0 )
摘 要 : 针对发酵有机酸在中和、 酸解过程中出 现混 合不均匀、 能 耗大、 结 垢严重的问 题, 通过设备使用、 工艺 过程检测和
装置运行一段时问后 , 在容器 内壁、 接管和搅
拌等处有大量的无机钙盐和有机钙盐沉积 , 沉淀厚 度平均为 4 m m, 部分管道上结垢成不规则块状, 形 状如石钟乳 。不易清洗垢质 , 对设备存在一定的损 坏作 用 。 1 . 4 原 生物反 应器 结构 形式 示意 图
1 原生物反应器现状
分析 , 找 出了存在 问题的原 因。对反应器 、 搅拌装置重新设计 。 提 高反应 器内壁及搅拌 器的加 工精度 , 经使 用验证 。 提 高 了产 品质量和生产效率 。 降低能耗和装置结垢现 象, 提 高了公司经济效益 。
关键 司: 发酵有机酸; 节能; 搅拌反应器; 应用
中图分类号 : T Q 9 2 1 : T S 2 0 3 文 献标 识码 : B 文章编 号 : 1 6 7 2- 9 9 9 4 ( 2 0 1 4 ) 0 3- 0 0 4 9- 0 2
第2 4卷 第 3期
2 0 1 4年 7月
安 徽 冶 金 科 技 职 业 学 院 学 报
J o u ms a o f An h u i Vo c a t i o n a l Co l l e g e o f Me t a ] l u r g y a n d T e c h n o l o g y
叶片强度 , 防止 叶片变形 。
根据反应固体颗粒易沉淀的现象 , 对反应器结 构重新设计 , 容 器直径 在 4 0 0 0 I T I I T I 、 高 度在 5 6 0 0 1 1 1 1 1 1 范 围 内, 高 径 比在 1 . 4之 间 , 装 填 容 积 为 7 0 m。 减小 容器 的高径 比 , 便 于 固体 颗粒 的悬 浮 , 降低容器 内混合 不均 匀度 , 可 确保 液体 与 固体 混合
的有机酸发生 中和反应 , 生成溶解度极小的有机酸
钙盐 , 过 滤 后 得 到 有 机 酸 钙 盐 。有 机 酸 钙 盐 调 浆
对发酵有机酸在中和、 酸解过程中产生的固体 颗粒悬浮液上 、 下部分取样检测 , 上部固液 比平均
为4 9 . 8 %, 下部 固液 比平均为 5 4 . 6 %, 混合不均 匀 。有机 酸钙 盐加 入硫 酸产 生 复分解反应 后 , 硫 酸
发酵有机酸在食品 、 饮料、 医药 、 化工、 洗涤剂 等领域应用十分广泛 。经发酵后的有机酸液体中,
m , 能耗偏 高 。
1 . 2 料液 混合 不均 匀
除含有主要产物有机酸外 , 还含有纤维 、 菌体 、 有机 杂酸等杂质。通过加人碳 酸钙 ( C a C O 。 ) 与溶液 中