海洋平台用锻锌钢高附着带绣环氧涂料的研究
海洋工程装备重防腐涂料的应用研究
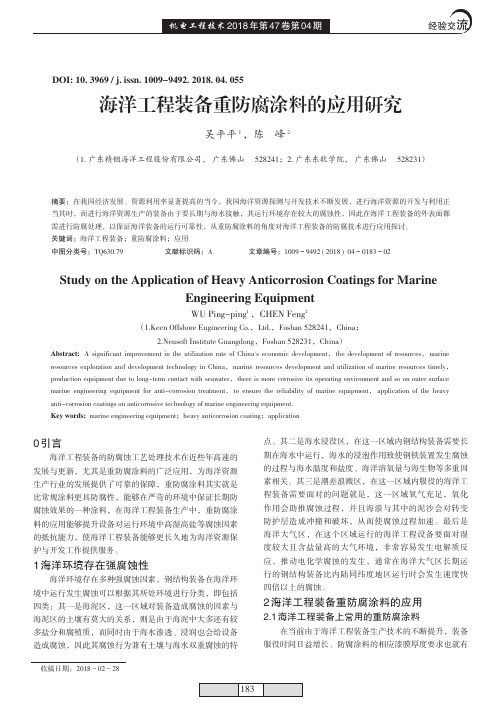
收稿日期:2018-02-28摘要:在我国经济发展、资源利用率显著提高的当今,我国海洋资源探测与开发技术不断发展,进行海洋资源的开发与利用正当其时,而进行海洋资源生产的装备由于要长期与海水接触,其运行环境存在较大的腐蚀性,因此在海洋工程装备的外表面都需进行防腐处理,以保证海洋装备的运行可靠性,从重防腐涂料的角度对海洋工程装备的防腐技术进行应用探讨。
关键词:海洋工程装备;重防腐涂料;应用中图分类号:TQ630.79文献标识码:A文章编号:1009-9492(2018)04-0183-02Study on the Application of Heavy Anticorrosion Coatings for MarineEngineering EquipmentWU Ping-ping 1,CHEN Feng 2(1.Keen Offshore Engineering Co.,Ltd.,Foshan 528241,China ;2.Neusoft Institute Guangdong ,Foshan 528231,China )Abstract:A significant improvement in the utilization rate of China's economic development ,the development of resources ,marineresources exploration and development technology in China ,marine resources development and utilization of marine resources timely ,production equipment due to long-term contact with seawater ,there is more corrosive its operating environment and so on outer surface marine engineering equipment for anti-corrosion treatment ,to ensure the reliability of marine equipment ,application of the heavy anti-corrosion coatings on anticorrosive technology of marine engineering equipment.Key words:marine engineering equipment ;heavy anticorrosion coating ;application海洋工程装备重防腐涂料的应用研究吴平平1,陈峰2(1.广东精铟海洋工程股份有限公司,广东佛山528241;2.广东东软学院,广东佛山528231)DOI:10.3969/j.issn.1009-9492.2018.04.0550引言海洋工程装备的防腐蚀工艺处理技术在近些年高速的发展与更新,尤其是重防腐涂料的广泛应用,为海洋资源生产行业的发展提供了可靠的保障,重防腐涂料其实就是比常规涂料更具防腐性,能够在严苛的环境中保证长期防腐蚀效果的一种涂料,在海洋工程装备生产中,重防腐涂料的应用能够提升设备对运行环境中高湿高盐等腐蚀因素的抵抗能力,使海洋工程装备能够更长久地为海洋资源保护与开发工作提供服务。
高固体分环氧海洋防腐蚀涂料的研究进展

高固体分环氧海洋防腐蚀涂料的研究进展1·前言防腐蚀涂料的防护作用主要有3 种: 漆膜与片层颜料的屏蔽作用、碱性或氧化性颜料的缓蚀钝化作用以及锌粉的电化学保护作用。
其中,能把水、氧以及离子等腐蚀介质隔绝的屏蔽作用最为关键。
目前常用的海洋重防腐涂料多为溶剂型涂料。
在其成膜过程中,溶剂挥发留下的针孔,会使腐蚀介质渗至膜下造成腐蚀。
所得腐蚀产物膨胀挤破涂层,使腐蚀介质得以扩散,终使涂层成片脱落失效。
需要指出的是,防护涂层即使无裂纹和针孔空隙等缺陷,腐蚀介质仍然能在一定程度上渗透涂层到达金属表面。
因此,必须提高涂膜的致密性与厚度以延长介质的渗透时间[1 - 3]。
海洋钢铁设施中常用的重防腐涂层总厚度一般要求300 ~500 μm,有的甚至要求更厚。
然而,溶剂型涂料的单道涂层仅为一百多微米,需要多道涂装才能达到规定膜厚,这就增加了施工成本,而且溶剂对工人的身体健康有损害。
面对溶剂型涂料的种种问题,科研人员正在努力开发新型防腐蚀涂料[4 - 5]。
其中,高固体分环氧涂料受到极大重视。
高固体分环氧涂料多为双组分反应固化型防腐涂料[6]。
低分子量环氧树脂、颜料、活性稀释剂及各种助剂经高速分散、研磨后,制成漆料组分,可满足特定场合需要的改性胺作固化剂组分。
环氧树脂用作成膜物质的优点是: 由于它含有大量的羟基与醚基等强极性基团,使其与底材的附着力非常好; 固化时不产生小分子副产物,体积收缩很小,因而具有良好的成膜致密性;优异的机械性能、耐化学品性能和耐腐蚀性能。
采用低分子量的树脂与活性稀释剂是为了降低施工粘度,以提高涂膜平整性与致密性。
高固体分是指: 制备与施工无需或很少量使用有机溶剂; 涂料的固含量很高,甚至达100%。
回避了有机溶剂就消除了针孔现象,提高了涂膜的抗渗性,免除了溶剂毒害。
固含量高使得单道涂层的厚度增大,适用于厚涂,从而减少了涂装费用与时间。
高固体分环氧涂料综合了高固体分与环氧树脂的优点,高固体分环氧涂料是实现厚膜化要求的最简单有效的方法,已经成为防腐涂料的研究热点,是海洋重防腐涂料的发展趋势。
海洋钻井平台防腐涂装方案(锌加系统)

海洋钻井平台防腐涂装方案(锌加系统)锌加应用在海洋钻井平台防腐涂装方案一. 普通平台防腐涂料海洋钻井平台采用的有机涂料防腐方法海上钻井平台涂料,在品种与长效船舶涂料有很多类似之处,海洋平台涂料保护的具体要求是:涂料与钢材表面及各道涂料之间有良好附着力,老化性能好,耐盐雾性能好,耐海水性能好,能形成适当弹性的涂层,满意的表面处理、油漆涂装和固化条件,以及能与阴极保护配套使用等。
又海洋平台涂装面积大,一般海洋钻井平台在100000平方米以上,而且从维修的观点,要求涂料使用周期越长越好。
涂装配套根据腐蚀部位海洋钻井平台可分三个部位:大气区、飞溅区和全浸区。
1.海洋平台大气区的涂料保护大气区是平台腐蚀较轻微的部位,比其他部位维修方便些,但比船舶与岸边的结构还是困难得多。
所选用的涂料品种亦采用高性能的。
一般的涂装配套是:道数涂层干膜厚度涂层结构1 无机锌底漆75µm 2 冷固化环氧中间漆200µm 2 丙烯酸聚氨酯面漆60µm合计5 /335µm2.海洋平台飞溅区的涂料保护飞溅区是海洋平台结构腐蚀最严重的区域,它经受海洋大气与海水浸渍的交替作用,海浪与冰块的冲击,锚链和水面飘浮物体的磨损,以及其它工作辅助船停靠的碰撞与摩擦。
而且飞溅区在维修时表面处理进行喷砂与涂装非常困难,因此平台飞溅区的涂装设计必须考虑今后维修与涂装的方便,并适当地对钢材厚度增放一定的腐蚀余量,必须采用高性能涂料。
一般的涂装配套是:道数涂层干膜厚度涂层结构1 无机锌硅酸盐底漆75µm 4 厚浆型环氧沥青涂料500µm 合计 5 /575µm3.海洋平台全浸区的涂料保护海洋平台全浸区的腐蚀速度比大气区严重,但比飞溅区要轻得多。
海洋平台全浸区一般采用阴极保护或涂料与阴极保护的联合保护,而很少单独采用涂料保护,原因是目前防锈、防污涂料使用期限最长为5-8年左右,不可能成为海洋平台永久性的保护涂层。
海洋飞溅区钢结构的防腐蚀技术分析
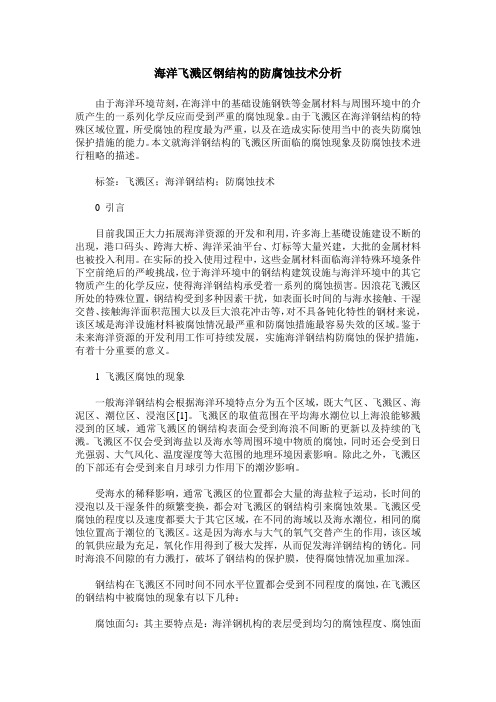
海洋飞溅区钢结构的防腐蚀技术分析由于海洋环境苛刻,在海洋中的基础设施钢铁等金属材料与周围环境中的介质产生的一系列化学反应而受到严重的腐蚀现象。
由于飞溅区在海洋钢结构的特殊区域位置,所受腐蚀的程度最为严重,以及在造成实际使用当中的丧失防腐蚀保护措施的能力。
本文就海洋钢结构的飞溅区所面临的腐蚀现象及防腐蚀技术进行粗略的描述。
标签:飞溅区;海洋钢结构;防腐蚀技术0 引言目前我国正大力拓展海洋资源的开发和利用,许多海上基礎设施建设不断的出现,港口码头、跨海大桥、海洋采油平台、灯标等大量兴建,大批的金属材料也被投入利用。
在实际的投入使用过程中,这些金属材料面临海洋特殊环境条件下空前绝后的严峻挑战,位于海洋环境中的钢结构建筑设施与海洋环境中的其它物质产生的化学反应,使得海洋钢结构承受着一系列的腐蚀损害。
因浪花飞溅区所处的特殊位置,钢结构受到多种因素干扰,如表面长时间的与海水接触、干湿交替、接触海洋面积范围大以及巨大浪花冲击等,对不具备钝化特性的钢材来说,该区域是海洋设施材料被腐蚀情况最严重和防腐蚀措施最容易失效的区域。
鉴于未来海洋资源的开发利用工作可持续发展,实施海洋钢结构防腐蚀的保护措施,有着十分重要的意义。
1 飞溅区腐蚀的现象一般海洋钢结构会根据海洋环境特点分为五个区域,既大气区、飞溅区、海泥区、潮位区、浸泡区[1]。
飞溅区的取值范围在平均海水潮位以上海浪能够溅浸到的区域,通常飞溅区的钢结构表面会受到海浪不间断的更新以及持续的飞溅。
飞溅区不仅会受到海盐以及海水等周围环境中物质的腐蚀,同时还会受到日光强弱、大气风化、温度湿度等大范围的地理环境因素影响。
除此之外,飞溅区的下部还有会受到来自月球引力作用下的潮汐影响。
受海水的稀释影响,通常飞溅区的位置都会大量的海盐粒子运动,长时间的浸泡以及干湿条件的频繁变换,都会对飞溅区的钢结构引来腐蚀效果。
飞溅区受腐蚀的程度以及速度都要大于其它区域,在不同的海域以及海水潮位,相同的腐蚀位置高于潮位的飞溅区。
海洋工程材料防腐蚀技术应用与发展趋势

海洋工程材料防腐蚀技术应用与发展趋势随着海洋工程的不断发展,海洋工程材料的防腐蚀技术也越来越重要。
在海洋环境中,海水中的氯离子、海盐、海藻等物质以及气候环境等各种因素都会造成海洋结构材料的损坏腐蚀,防腐蚀技术的应用和研究将对海洋工程的可靠性和寿命产生重要影响。
本文将从防腐蚀技术的应用和发展趋势两方面来探讨海洋工程材料防腐蚀技术的现状以及未来的趋势。
一、防腐蚀技术的应用1.金属涂层对于海洋结构的防腐蚀,金属涂层是一种常用的方法。
金属涂层的主要作用是防止海水中的氯离子、海盐等物质侵蚀结构表面。
常用的金属涂层包括锌涂层、铝涂层、不锈钢涂层等。
在实践中,锌涂层是最为常见的防腐蚀涂层,其主要原因是锌具有较高的电化学电位并且易于镀制成薄膜。
2.有机涂层有机涂层是另一种常用的海洋工程材料防腐蚀技术。
有机涂层可以覆盖在结构表面上形成一层保护膜,使其对海水等外界物质的侵蚀具有一定的防护作用。
有机涂层的主要材料包括有机硅涂料、环氧涂料、聚氨酯涂料等。
有机涂层的优点是粘附力强,可起到密封作用,但其寿命较短。
3.玻璃纤维增强塑料玻璃纤维增强塑料是目前应用较为广泛的一种防腐蚀材料。
该材料不仅具有轻质、高强度等优点,还能耐受环境的侵蚀,长期使用不会出现腐蚀损坏。
同时,玻璃纤维增强塑料还容易加工,成型灵活,可以制作成各种不同形状的部件。
这在海洋大型结构的制造中有一定的优势。
二、发展趋势1.功能性涂层传统的涂层材料主要是为了对海水侵蚀起到保护作用,而对于一些海洋结构来说,单单的防护作用已经不能满足需求。
因此,未来的发展方向将会是研究开发具有更多功能性的涂层材料,如自修复、自洁、抗污等特点,以满足海洋工程的更高要求。
2.新型防腐材料随着海洋工程的发展,新型防腐材料的研究将成为未来的一个重点。
这些材料不仅要具有优越的防腐蚀性能,还需要具备轻质、高强度、耐高温等功能,以更好地适应未来海洋工程的需求。
3.先进的材料制造技术先进的材料制造技术是未来海洋工程材料防腐蚀技术的重要保障。
海洋浪花飞溅区钢结构的防腐蚀措施

海洋浪花飞溅区钢结构的防腐蚀措施随着海洋工程的快速发展,海洋浪花飞溅区的钢结构防腐蚀问题越来越受到关注。
该区域的海洋环境复杂,包括高盐度、高湿度、海浪冲刷等,这些因素都会加速钢结构的腐蚀。
因此,为了应对这一问题,需要采取一些有效的措施进行防腐蚀处理。
首先,选择合适的材料非常关键。
钢结构的材料应该具有优良的耐腐蚀性能,例如不锈钢、镀锌钢等。
这些材料可以有效地抵抗海水的腐蚀,从而延长钢结构的使用寿命。
其次,钢结构的表面处理也非常重要。
在制造钢结构之前,应该对其表面进行清洗和打磨处理,以去除铁锈和污垢,使得涂层能够更好地附着在钢结构表面。
此外,在海洋浪花飞溅区的钢结构上,可以采用先进的涂层技术进行涂装,例如环氧树脂涂料、聚氨酯涂料等。
这些涂层具有较强的耐腐蚀性能,能够抵御海水的侵蚀,从而保护钢结构不被腐蚀。
第三,在钢结构的维护保养过程中,应该定期进行检查,并及时处理钢结构表面出现的腐蚀和损伤。
可以采用喷涂和刷涂等方式对钢结构进行维修和保养,确保其表面涂层的完整性和耐腐蚀性能。
另外,为了进一步加强钢结构的防腐蚀性能,还可以采取电化学防护等先进技术。
电化学防护是一种基于电化学反应原理的防腐蚀技术,通过外加电流使得钢结构表面被涂覆上一层保护性的氧化物膜,从而达到防腐蚀的目的。
总之,海洋浪花飞溅区钢结构的防腐蚀措施非常重要,不仅关乎钢结构的安全可靠性,还关系到海洋工程的运行效率和使用寿命。
需要采取一系列措施,从材料选择、表面处理、涂层技术和维护保养等方面综合考虑,以确保钢结构在复杂的海洋环境下能够长期安全稳定地运行。
海洋浪花飞溅区钢结构的防腐蚀措施

海洋浪花飞溅区钢结构的防腐蚀措施海洋浪花飞溅区的钢结构防腐蚀措施的重要性不可忽视。
海洋环境中的氯离子、潮湿和高湿度等因素会加速钢结构的腐蚀速度,降低其使用寿命。
采取适当的防腐蚀措施对于保护海洋浪花飞溅区的钢结构长期使用具有重要意义。
一、使用合适的材料选择适用于海洋环境的耐腐蚀性能材料是防腐蚀的首要措施。
常用的钢结构材料有不锈钢、镀锌钢、铝合金等。
不锈钢具有抗氧化、耐腐蚀的特点,适用于长期暴露在海洋环境中。
镀锌钢具有锌层的防护,可以减缓钢结构的腐蚀速度。
铝合金具有轻质、耐蚀性好的特点,也是一种常用的材料选择。
二、防护涂层在海洋浪花飞溅区的钢结构上涂覆防护涂层是常用的防腐蚀措施之一。
防护涂层可以形成一层保护层,隔绝钢结构与海水之间的接触,降低腐蚀速度。
常用的防护涂层有环氧富锌漆、有机硅涂层等。
环氧富锌漆具有优异的耐候性和抗腐蚀性能,可以长时间保护钢结构不被腐蚀。
有机硅涂层具有抗老化、抗紫外线辐射的特点,适用于暴露在恶劣海洋环境中的钢结构。
三、防腐蚀处理在对钢结构进行涂层之前,需要对其进行防腐蚀处理。
常用的防腐蚀处理方法包括除油、除锈、磷化等。
除油是指去除钢结构表面的油脂和污垢;除锈是指去除钢结构表面的锈蚀;磷化是指在钢结构表面形成一层磷酸锌、锰等化学物质的膜层,提高钢结构的抗腐蚀性能。
防腐蚀处理的目的是使钢结构表面清洁,增加涂层与钢结构的附着力,延长防腐蚀涂层的使用寿命。
四、定期检查和维护海洋浪花飞溅区的钢结构容易受到氯离子和潮湿等因素的腐蚀,因此需要定期进行检查和维护。
检查应包括钢结构表面涂层的状况、有无划伤和损坏等。
如发现问题,需要及时修补和更换涂层。
还需要定期清洗钢结构表面的污垢和盐渍,保持钢结构的清洁,防止腐蚀加剧。
海洋工程防腐涂料研究报告

海洋工程防腐涂料研究报告
海洋工程是指在海洋中进行的各种工程活动,如海底油气开采、海底电缆敷设、海洋风电场建设等。
由于海洋环境的特殊性,海洋工程的防腐保护是非常重要的。
而防腐涂料是防腐保护的主要手段之一。
海洋工程防腐涂料的研究主要涉及以下几个方面:
一、涂料的种类
海洋工程防腐涂料的种类很多,常见的有环氧涂料、聚氨酯涂料、丙烯酸涂料等。
这些涂料具有不同的特点和适用范围,需要根据具体情况选择。
二、涂料的性能
海洋工程防腐涂料的性能要求非常高,主要包括以下几个方面: 1. 耐海水腐蚀:海水中含有大量的盐分和氯离子,容易对金属材料造成腐蚀。
因此,海洋工程防腐涂料必须具有良好的耐海水腐蚀性能。
2. 耐紫外线:海洋环境中紫外线较强,容易使涂料老化、脆化,影响防腐效果。
因此,海洋工程防腐涂料必须具有良好的耐紫外线性能。
3. 耐磨损:海洋环境中波浪较大,容易对涂料造成磨损。
因此,海洋工程防腐涂料必须具有良好的耐磨损性能。
三、涂料的应用
海洋工程防腐涂料的应用需要注意以下几个方面:
1. 表面处理:在涂料施工前,需要对金属表面进行处理,如除锈、打磨等,以保证涂料与金属表面的粘结力。
2. 涂料施工:涂料施工需要注意施工环境的温度、湿度等因素,以保证涂料的质量。
3. 涂料维护:涂料施工后需要进行定期维护,如检查涂层是否有损伤、是否需要重新涂料等。
海洋工程防腐涂料的研究是非常重要的。
只有选择合适的涂料、保证涂料的性能和正确应用涂料,才能有效地保护海洋工程的安全和稳定运行。
海洋平台的腐蚀及防腐技术

海洋平台的腐蚀及防腐技术摘要:概括了海洋平台不同区域的腐蚀环境和腐蚀规律,对海洋平台重防腐涂料的选择要求及配套体系进行简要叙述。
针对海洋平台的长效防腐防护要求,介绍了几种具有长效的防腐材料和防腐技术特点,包括海洋平台热喷涂长效防腐蚀技术、加保护技术、洋平台桩腿防腐套包缚技术等,为我国对海洋平台长效防腐防护技术的研究提供参考。
关键词:海洋平台;防腐;热喷涂;锌加技术;防腐套海洋平台是一种海上大型工程结构物。
其钢结构长期处于盐雾、潮气和海水等环境中,受到海水及海生物的侵蚀,而产生剧烈的电化学腐蚀。
腐蚀严重影响海洋平台结构材料的力学性能,从而影响到海洋平台的使用安全。
而且由于海洋平台远离海岸,不能像船舶那样定期进坞维修保养,因此海洋平台的建造者及使用者都非常重视海洋平台的防腐问题。
如何对海洋平台结构进行长效防腐,以及开发研究海洋平台结构长效防腐的新材料、技术及新工艺都具有十分重要的意义。
1海洋平台的腐蚀规律1 . 1海洋环境的腐蚀区域界定海洋平台的使用环境极其恶劣,阳光暴晒、雾、浪的冲击、杂的海水体系、境温度和湿度变化及海洋生物侵蚀等使得海洋平台腐蚀速率较快。
海洋平台在不同的海洋环境下,腐蚀行为和腐蚀特点会有比较大的差异。
因此要对海洋平台结构在海洋环境中腐蚀区域的腐蚀情况进行分析和界定,才能针对性地提出有效的保护措施。
根据海洋环境、蚀特点和平均腐蚀率不同,海洋平台在海洋环境中可分为海洋大气区、飞溅区和全浸区3大区域。
为了更好地分析海洋平台钢结构的腐蚀情况,许多研究者又将飞溅区分为飞溅区和潮差区,全浸区分为海水全浸区和海底泥土区,即分成5大腐蚀区域1 . 2海洋钢结构腐蚀情况海洋大气区:海洋大气区海盐粒子使腐蚀加快,干燥表面与含盐的湿膜交替变换形成物理、学和电化学作用影响金属腐蚀。
飞溅区:在海洋环境中腐蚀最严重的部位是在平均海潮以上的飞溅区。
由于经常成潮湿表面,表面供氧充足,无海生物污损。
长时间润湿表面与短时间干燥表面的交替作用和浪花冲刷,造成物理与电化学为主的腐蚀破坏,且破坏最大。
海洋平台结构的防腐措施与维护策略研究
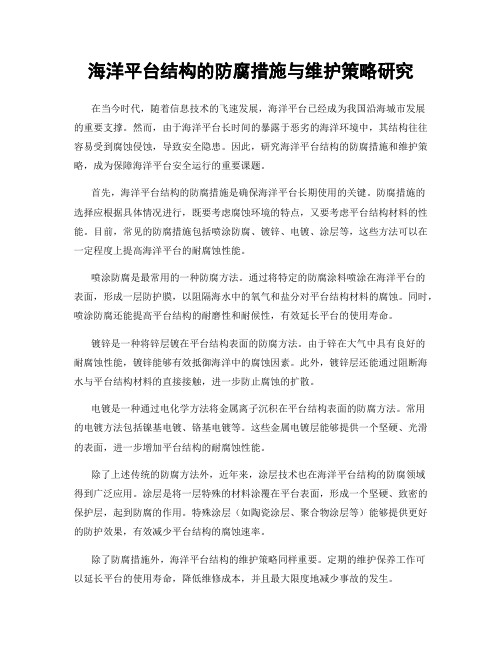
海洋平台结构的防腐措施与维护策略研究在当今时代,随着信息技术的飞速发展,海洋平台已经成为我国沿海城市发展的重要支撑。
然而,由于海洋平台长时间的暴露于恶劣的海洋环境中,其结构往往容易受到腐蚀侵蚀,导致安全隐患。
因此,研究海洋平台结构的防腐措施和维护策略,成为保障海洋平台安全运行的重要课题。
首先,海洋平台结构的防腐措施是确保海洋平台长期使用的关键。
防腐措施的选择应根据具体情况进行,既要考虑腐蚀环境的特点,又要考虑平台结构材料的性能。
目前,常见的防腐措施包括喷涂防腐、镀锌、电镀、涂层等,这些方法可以在一定程度上提高海洋平台的耐腐蚀性能。
喷涂防腐是最常用的一种防腐方法。
通过将特定的防腐涂料喷涂在海洋平台的表面,形成一层防护膜,以阻隔海水中的氧气和盐分对平台结构材料的腐蚀。
同时,喷涂防腐还能提高平台结构的耐磨性和耐候性,有效延长平台的使用寿命。
镀锌是一种将锌层镀在平台结构表面的防腐方法。
由于锌在大气中具有良好的耐腐蚀性能,镀锌能够有效抵御海洋中的腐蚀因素。
此外,镀锌层还能通过阻断海水与平台结构材料的直接接触,进一步防止腐蚀的扩散。
电镀是一种通过电化学方法将金属离子沉积在平台结构表面的防腐方法。
常用的电镀方法包括镍基电镀、铬基电镀等。
这些金属电镀层能够提供一个坚硬、光滑的表面,进一步增加平台结构的耐腐蚀性能。
除了上述传统的防腐方法外,近年来,涂层技术也在海洋平台结构的防腐领域得到广泛应用。
涂层是将一层特殊的材料涂覆在平台表面,形成一个坚硬、致密的保护层,起到防腐的作用。
特殊涂层(如陶瓷涂层、聚合物涂层等)能够提供更好的防护效果,有效减少平台结构的腐蚀速率。
除了防腐措施外,海洋平台结构的维护策略同样重要。
定期的维护保养工作可以延长平台的使用寿命,降低维修成本,并且最大限度地减少事故的发生。
首先,定期巡检是海洋平台维护的基础。
通过定期巡检,可以发现平台结构中的潜在故障,及时采取措施进行修复,避免事故的发生。
同时,做好防腐层的保护工作也是维护海洋平台的重要一环。
新型防腐蚀涂层在海洋工程中的应用研究
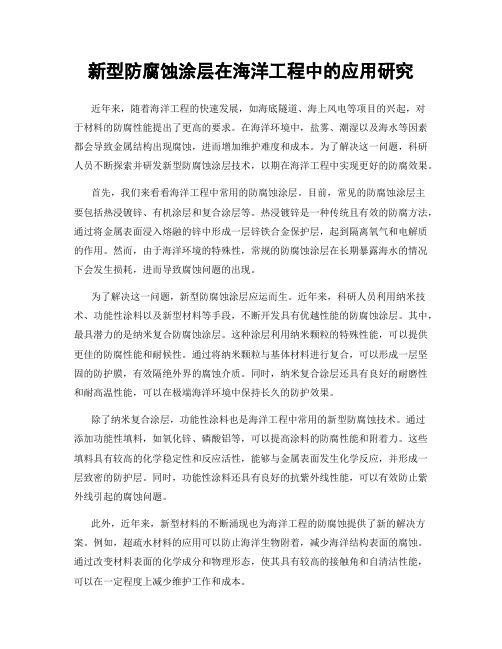
新型防腐蚀涂层在海洋工程中的应用研究近年来,随着海洋工程的快速发展,如海底隧道、海上风电等项目的兴起,对于材料的防腐性能提出了更高的要求。
在海洋环境中,盐雾、潮湿以及海水等因素都会导致金属结构出现腐蚀,进而增加维护难度和成本。
为了解决这一问题,科研人员不断探索并研发新型防腐蚀涂层技术,以期在海洋工程中实现更好的防腐效果。
首先,我们来看看海洋工程中常用的防腐蚀涂层。
目前,常见的防腐蚀涂层主要包括热浸镀锌、有机涂层和复合涂层等。
热浸镀锌是一种传统且有效的防腐方法,通过将金属表面浸入熔融的锌中形成一层锌铁合金保护层,起到隔离氧气和电解质的作用。
然而,由于海洋环境的特殊性,常规的防腐蚀涂层在长期暴露海水的情况下会发生损耗,进而导致腐蚀问题的出现。
为了解决这一问题,新型防腐蚀涂层应运而生。
近年来,科研人员利用纳米技术、功能性涂料以及新型材料等手段,不断开发具有优越性能的防腐蚀涂层。
其中,最具潜力的是纳米复合防腐蚀涂层。
这种涂层利用纳米颗粒的特殊性能,可以提供更佳的防腐性能和耐候性。
通过将纳米颗粒与基体材料进行复合,可以形成一层坚固的防护膜,有效隔绝外界的腐蚀介质。
同时,纳米复合涂层还具有良好的耐磨性和耐高温性能,可以在极端海洋环境中保持长久的防护效果。
除了纳米复合涂层,功能性涂料也是海洋工程中常用的新型防腐蚀技术。
通过添加功能性填料,如氧化锌、磷酸铝等,可以提高涂料的防腐性能和附着力。
这些填料具有较高的化学稳定性和反应活性,能够与金属表面发生化学反应,并形成一层致密的防护层。
同时,功能性涂料还具有良好的抗紫外线性能,可以有效防止紫外线引起的腐蚀问题。
此外,近年来,新型材料的不断涌现也为海洋工程的防腐蚀提供了新的解决方案。
例如,超疏水材料的应用可以防止海洋生物附着,减少海洋结构表面的腐蚀。
通过改变材料表面的化学成分和物理形态,使其具有较高的接触角和自清洁性能,可以在一定程度上减少维护工作和成本。
综上所述,新型防腐蚀涂层在海洋工程中的应用研究十分重要。
高强度防水涂料在海洋平台工程中的应用效果评估

高强度防水涂料在海洋平台工程中的应用效果评估引言海洋平台工程是指建设在海上的各种海洋资源开发、交通运输、军事防御等项目。
由于海洋环境的特殊性,海洋平台工程需要面对多样复杂的水文、气象、环境等因素的考验。
为了保证海洋平台的稳定可靠,高强度防水涂料成为海洋平台工程中重要的保护材料。
本文将对高强度防水涂料在海洋平台工程中的应用效果进行评估。
一、高强度防水涂料的基本特点高强度防水涂料具有以下基本特点:1)优异的防水性能,能够有效阻止水分渗透。
2)良好的耐候性,能够抵御海洋环境的侵蚀。
3)出色的粘结力,能够牢固粘结在基层上。
4)高耐磨性,能够承受台风、风浪等外力冲击。
5)快速施工,能够在短时间内完成涂覆。
二、高强度防水涂料在海洋平台工程中的应用1. 海洋平台的基础应用海洋平台的基础是海床的承载层,因此需要高强度防水涂料来进行防水处理。
高强度防水涂料可以有效防止海水渗透到基础中,防止腐蚀和损坏基础材料。
此外,高强度防水涂料还可以提高基础的抗风压能力,增强整个海洋平台的稳定性。
2. 海洋平台的钢结构应用海洋平台的钢结构受到海洋环境中的潮湿、高盐度、腐蚀等因素的严重侵蚀。
高强度防水涂料可以形成一层保护膜,有效防止钢结构与海水直接接触,减少腐蚀的发生。
同时,高强度防水涂料具有较高的耐候性,能够在长期的海洋环境中保持稳定的性能。
3. 海洋平台的混凝土结构应用混凝土结构在海洋平台工程中广泛应用,但由于混凝土本身的孔隙性,容易受到海水的渗透和侵蚀。
高强度防水涂料能够填充混凝土的微孔和裂缝,形成一层致密的保护层,防止水分的渗透。
同时,高强度防水涂料还具有较高的粘结力,可以牢固地粘结在混凝土表面,提高混凝土结构的耐久性。
三、1. 防水性能评估通过对高强度防水涂料进行一系列的实验和测试,可以评估其防水性能。
例如,可以进行水压试验,观察高强度防水涂料在一定水压下的防水效果。
同时还可以进行长期浸泡试验,模拟海洋环境中的长期水浸,评估高强度防水涂料的持久性能。
探讨海洋采油平台重防腐涂料技术

探讨海洋采油平台重防腐涂料技术发表时间:2017-11-22T15:47:29.633Z 来源:《防护工程》2017年第18期作者:邓绍强[导读] 随着社会的发展,我国海洋石油开采的步伐一直在不断地加快。
中海石油(中国)有限公司湛江分公司 524000 摘要:海洋环境腐蚀对海上采油平台的作用会造成钢结构强度严重下降,影响海上采油平台承载能力,影响海上采油平台大型工程项目施工,严重时甚至影响海上采油平台的安全生产,破坏海洋生态环境等严重后果,造成巨大的损失。
因此,加强海洋工程的防腐设计和防腐施工的意义重大。
本文就海洋采油平台重防腐涂料的应用现状及研发重点进行阐述。
关键词:海洋采油平台;防腐;现状;研发引言随着社会的发展,我国海洋石油开采的步伐一直在不断地加快,各种以钢结构为主的海洋开采平台成为我国石油开采的主要平台,国家也为此投入大量精力和财力,推出各种耐腐蚀的材料,加强防腐蚀技术的发展力度,但是,在海洋这样一个特有的复杂腐蚀环境下,海洋采油平台的防腐蚀工作仍然无法满足开采过程中的实际需求。
因此必须根据其发展现状对其进行更深一层次的研究,完善整个海洋工程防腐系统。
1 海洋重防腐材料的要求在海洋这样一个具有超强腐蚀性的严酷环境下,作为用以抵挡海洋防腐的重防腐涂料,必须要有能长效抵抗海洋腐蚀的性能。
首先,重防腐涂料必须要能强效依附在钢材表面,抵抗腐蚀物质的侵入,具有耐磨、耐碰、耐冲刷等物理性能。
其次,开采过程中,除去海水,盐雾、油类、各种化学品及紫外线等都具有较强的腐蚀性,防腐涂料必须要有能抵抗这些腐蚀的超强化学性能。
用于全浸区与飞溅区的防腐涂料,必须要与电化学保护系统保持良好的相容性,耐得住阴极剥落。
最后,工程所选防腐涂料在能够根据各种环境各种结构进行涂装施工的情况下,其所含有的相关物质含量必须达到国家的相关标准要求,严格依照健康、环保和安全的国家要求进行施工。
2 海洋重防腐材料应用现状浅析2.1钢结构防腐涂层系统固定和半固定在海洋中的大型钢结构构成了海洋采油平台,长期受到严重腐蚀,所以许多部位都需要进行防腐。
海洋石油平台涂装工程涂料损耗分析
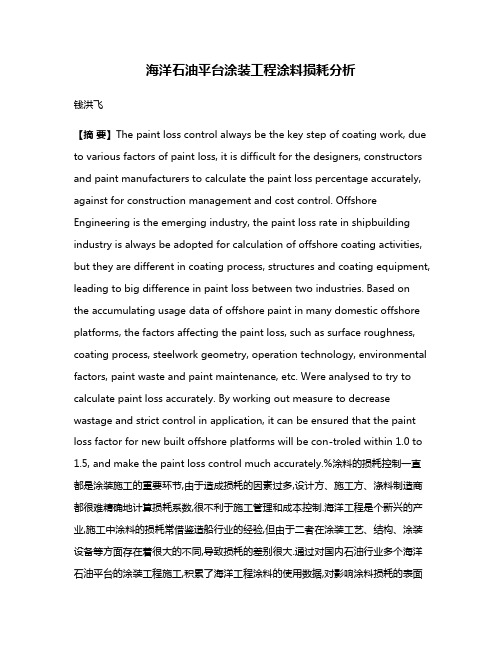
海洋石油平台涂装工程涂料损耗分析钱洪飞【摘要】The paint loss control always be the key step of coating work, due to various factors of paint loss, it is difficult for the designers, constructors and paint manufacturers to calculate the paint loss percentage accurately, against for construction management and cost control. Offshore Engineering is the emerging industry, the paint loss rate in shipbuilding industry is always be adopted for calculation of offshore coating activities, but they are different in coating process, structures and coating equipment, leading to big difference in paint loss between two industries. Based on the accumulating usage data of offshore paint in many domestic offshore platforms, the factors affecting the paint loss, such as surface roughness, coating process, steelwork geometry, operation technology, environmental factors, paint waste and paint maintenance, etc. Were analysed to try to calculate paint loss accurately. By working out measure to decrease wastage and strict control in application, it can be ensured that the paint loss factor for new built offshore platforms will be con-troled within 1.0 to 1.5, and make the paint loss control much accurately.%涂料的损耗控制一直都是涂装施工的重要环节,由于造成损耗的因素过多,设计方、施工方、涤料制造商都很难精确地计算损耗系数,很不利于施工管理和成本控制.海洋工程是个新兴的产业,施工中涂料的损耗常借鉴造船行业的经验,但由于二者在涂装工艺、结构、涂装设备等方面存在着很大的不同,导致损耗的差别很大.通过对国内石油行业多个海洋石油平台的涂装工程施工,积累了海洋工程涂料的使用数据,对影响涂料损耗的表面粗糙度、涂装方式、钢结构的几何形状、操作技术、环境因素、涂料浪费、修补等各项因素进行分析,尝试对涂料的损耗系数进行精确的统计.通过制定减少损耗的措施,在施工中严格控制,保证了新建海洋石油平台的涂料损耗系数控制在1.0 ~1.5之间,使涂料损耗达到了比较精准的控制.【期刊名称】《涂料工业》【年(卷),期】2012(042)001【总页数】4页(P71-74)【关键词】海洋石油平台;涂装工程;涂料损耗因素;损耗系数;措施【作者】钱洪飞【作者单位】中国石油集团海洋工程(青岛)有限公司,山东青岛266555【正文语种】中文【中图分类】TQ639涂装工程成本的一个控制重点和难点就是涂料的实际用量,其对涂装工程的成本影响很大,一直是施工方关注的焦点,涂料的实际用量按式(1)计算。
- 1、下载文档前请自行甄别文档内容的完整性,平台不提供额外的编辑、内容补充、找答案等附加服务。
- 2、"仅部分预览"的文档,不可在线预览部分如存在完整性等问题,可反馈申请退款(可完整预览的文档不适用该条件!)。
- 3、如文档侵犯您的权益,请联系客服反馈,我们会尽快为您处理(人工客服工作时间:9:00-18:30)。
57卷增刊1 2016年11月中国造船SHIPBUILDING OF CHINAVol.57 Special 1Nov. 2016文章编号:1000-4882 (2016) S1-0400-08海洋平台用锻锌钢高附着带绣环氧涂料的研究栾津堂\周兵i,2,张颖君2,张泽成3,杨月波2,4,邵亚薇2(1.海洋石油工程(珠海)有限公司,珠海519000; 2.哈尔滨工程大学材料科学与化学工程学院,哈尔滨150001;3.中海福陆重工有限公司,珠海519000;4.海洋石油工程液化天然气工程技术中心,天津300450)摘要以锈蚀程度为35~55%锈蚀镀锌钢片为基体,在表面制备含有不同比例磺基水杨酸(sulfosalicylacid)的环氧涂层试样。
利用附着力测试仪,测试了涂层试样的附着力。
通过电化学阻抗谱(EIS)研究了涂层试样在3.5%的NaCl溶液中的耐蚀性,并探讨了磺基水杨酸对涂层试样耐蚀性的影响机理。
从结果可见:随着磺基水杨酸含量的增加,涂层试样的附着力是先增大后减小,涂有3%磺基水杨酸涂层试样的附着力最大,浸泡3000h后仍有8.19 MPa;除浸泡初期外,磺基水杨酸含量为2%和3%时,涂层的低频阻抗摸值IZ Iy^iHz,涂层试样空隙电阻凡都是最高的,两者都保持在10n^cm2以上,电荷转移电阻况的信息没有出现,这表明涂有2%和3%磺基水杨酸的涂层耐蚀性最好。
综上所述,在综合性能(即附着力和耐蚀性的综合性能)方面,涂有3%磺基水杨酸的涂层最好。
关键词:锈蚀镀锌钢;磺基水杨酸;环氧涂层;附着力;耐蚀性中图分类号:TB304 文献标识码:A0引言钢铁的腐蚀造成了材料的极大浪费。
热浸镀锌能够有效地提高钢铁的耐腐蚀性能[1],因而广泛应 用于海洋工程及其设备设施中(如采油平台护栏所用的镀锌钢管、镀锌钢格栅板、某些设备外壳[2]),同时也需要对镀锌钢进行进一步的防腐处理(如有机涂层防护)后再使用。
但是,因为处在海洋环境 中,而且镀锌钢的表面能很低[3],使得涂层与镀锌钢的附着力并不高;使用一段时间后,涂层失去保 护功能,镀锌钢发生锈蚀。
为提高锈蚀镀锌钢构件的使用寿命,节约经济成本,这就需对锈蚀镀锌钢 构件再一次进行防腐蚀保护。
然而,目前对锈蚀镀锌钢防腐蚀保护的研宄很少,其腐蚀保护的措施主 要是有机涂层[4]。
在2011年,湖南大学的高翔等人研宄了镀锌钢表面低表面处理带锈富锌涂料[5],但 其膜层附着力夕级;在2012年,陈云等人研宄了锈蚀铁塔低表面处理涂料[6],80um厚涂层附着力为 2级,150u m厚涂层附着力为3级,这些附着力都是比较低的。
众所周知,涂层的附着力越高,涂层 与基体的结合越好,腐蚀介质越难在涂层与基体界面扩展,涂层的防腐性能就越高[7]。
因此,研宄出 一种适用于锈蚀镀锌钢的高附着涂料就十分重要。
在本文中,探讨了锈蚀镀锌钢只进行简单打磨和清洗后,获得高附着涂层的可能;并通过环氧涂 层中添加磺基水杨酸[8],就能获得低表面处理的高附着、耐蚀性优良的环氧涂料。
1实验1.1试样的制备实验所用的金属基体材料为商业镀锌钢板(镀层Zn纯度>99.99% mass%),将基体加工成尺寸为57卷增刊1栾津堂,等:海洋平台用镀锌钢高附着带锈环氧涂料的研宂40150mmx50mmx2mm的小片,放入盐雾箱进行盐雾试验获得锈蚀试样,采用网格法选取出锈蚀程度(锈 蚀面积除以整个小片的面积)为35%〜55%的锈蚀镀锌钢试样,再将试样轻轻打磨除去表面浮锈,经蒸 馏水和无水乙醇超声清洗后,置于干燥器中备用。
1.2涂料的制备选用环氧清漆涂料作为本实验的基础配方,涂料具体含量见表1。
按量称取A组分中的原料,充 分搅拌,使环氧E-44溶解在溶剂中,加入固化剂,充分搅拌0.5h后,抽真空。
将制备好的涂料静置熟 化0.5h后,均匀地涂刷到清洗后的镀锌钢片上,待板上的涂料流平后,在25°C下固化24h,然后再在 60°C下固化24h。
取出试样经漆膜干燥实验器测试为实干后待用。
表1环氧涂料具体成分单位:gComponent1%Sulfos-Varnishalicyl Acid2%Sulfos-alicyl Acid3%Sulfos-alicyl Acid4%Sulfos-alicyl AcidEpoxy E-44Mixed Solvent of2020202020Component AXylene andN-butanol1111111111 Alcohol1212121212 Sulfosalicyl Acid00.430.86 1.29 1.72Component B NX-201514141414141.3附着力测试按照国标GB/T 5210-85,采用拉开法对涂层与金属基体之间的干附着力进行测试,取完全固化的 试样以及浸泡500,1500和3000h后涂层试样进行测试,每组4个平行试样,取平均值,并进行数据分析。
1.4耐蚀性测试在本实验中,应用电化学阻抗谱(EIS)来表征涂层的耐蚀性,电化学阻抗谱测量是在Autolab PGSTAT302电化学工作站上进行的,采用经典的三电极体系。
其中,工作电极选用涂有相应涂层的试 样(测试面积为9.8 cm2),饱和Ag/AgCl电极作为参比电极,Pt作为对电极(尺寸为10mmx20mm)。
测试频率范围为105〜10-2Hz,正弦波扰动信号的振幅为20mV,腐蚀介质为3.5% NaCl溶液,测试温度 为室温:实验数据采用ZSimpWin软件进行拟合。
2结果与讨论2.1磺基水杨酸对涂层耐蚀性的影响图1分别是清漆及含有1%,2%,3%和4%磺基水杨酸涂层试样在3.5% NaCl溶液中浸泡不同时间的电 化学阻抗谱的Nyquist图和Bode图,图2是它们在3.5% NaCl溶液中的低频阻抗模值|Z|/=0.0他随浸泡时间 的变化。
从图1和图2可以看出:在刚浸泡时,涂层的|Z|/=0.0他都达到^办咖2以上。
然而,在浸泡3000h 后,清漆涂层和1%,2%,3%和4%磺基水杨酸涂层的|Z|/=0.0此分别为3.01x109D.cm2,1.03x1011Q.cm2,和^”。
乂如办咖2,|Z|/=0.0mz均随浸泡时间延长而整体呈现逐渐减小的趋势:清漆涂层的下降幅度最大,1%、4%磺基水杨酸涂层次之,2%、3%下降幅度最小;浸泡3000h后,1%、2%、3%、4%磺基水杨酸涂层的低频阻抗模值都在1011Q+cm2以上,而清漆涂层的低频阻抗模值则在 109Q+cm2,与磺基水杨酸涂层相比相差两个数量级。
这表明环氧涂层的耐蚀性随着磺基水杨酸含量的 増加先升高再下降,2%、3%磺基水杨酸涂层的耐蚀性最好,环氧清漆涂层的耐蚀性最差。
402中国造 船学术论文10Z 'fQ .c 4.0x10” 6.0X1011Z '/Q.cm 2020.02.0X108.0X 图1涂层试样在3.5% NaCl 溶液中浸泡不同时间的电化学阻抗谱的Nyquist 图和B ode 图说明:(A) (a)清漆;(B) (b) 1%磺基水杨酸涂层;(C) (c)2%磺基水杨酸涂层;(D) (d)3%磺基水杨酸涂层;(E) (e)4%磺基水杨酸涂层。
10"0"0"5*1iy Q 10"Z 10'10'v r -,z 10'^ ^ ^N i .n /…z phase angle/degree 80604020phaseangle/degree 80604020^6i ."z p h a s e a n g l e /d e g r e e806040200,10 1。
100,10 1。
^ ^ ^ ^ ^ ^ ^~i a / z op h a s e a n g l e /d e g r e eo o o o o N s r s zpha s e a n g l e /d e g r e e 80604020/°',°'0'1101,2,10'6,r 5,r 11;ES /_Z-、o d "l/57卷增刊1栾津堂,等:海洋平台用镀锌钢高附着带锈环氧涂料的研宂4030 500 1000 1500 2000 2500 3000Time/ h图2不同体系涂层试样在3.5% NaCl 溶液中的低频阻抗模值IZI m . w &随浸泡时间的变化为了更加明确地理解阻抗数据,采用ZSimpWm 软件进行拟合,其拟合采用的等效电路如图3所示。
在浸泡初期,涂层具有很好的屏蔽性能,显示纯电容的性质,只有一个时间常数,采用图3 (a )所示 的电路拟合,其中凡是腐蚀介质溶液的电阻,0。
和凡分别代表涂层电容和涂层孔隙电阻。
随着浸泡时 间的延长,电解质溶液逐渐渗透涂层达到镀锌钢基体界面,采用图3 (b )所示的电路拟合,其中0d i 和 及分别代表双电层的电容和电荷转移电阻。
其拟合结果见图4和图5。
图3电化学阻抗谱(EIS )的拟合电路:⑻一个时间常数,(b )两个时间常数图4是不同体系试样在3.5% NaCl 溶液中的J Rc 随浸泡时间的变化,凡越大表明涂层的致密性越高, 涂层的屏蔽性越好。
图4中可以看出:在浸泡的3000h 过程中,几种涂层试样的Ac 均随浸泡时间的延长 逐渐下降,涂有2%和3%磺基水杨酸涂层试样的凡除浸泡初期一直是比较高的;浸泡3000h 后,2%、3% 磺基水杨酸涂层的涂层孔隙电阻凡在以上,而1%、4%磺基水杨酸涂层的涂层孔隙电阻凡在 1010〜^^.咖2,清漆涂层的涂层孔隙电财。
则在109Q .cm 2,与2%、3%磺基水杨酸涂层相比,清漆涂 层的涂层孔隙电阻凡小了二个数量级;1%磺基水杨酸涂层的涂层孔隙电阻凡在624h 〜1464h 之间呈现先 减再増,这主要是由腐蚀产物的推积造成的。
结果表明,2%、3%磺基水杨酸涂层的致密性较高,涂层 的屏蔽性较好;而清漆涂层的致密性较低,涂层的屏蔽性较差。
■ varnish~1 % sulfosalicylic acid—a — 2% sulfosalicylic acid—3% sulfosalicylic acid—♦—4% sulfosalicylic acid z f fi I 0• 0S-G / l l z l - l o—oE o - a s z 图4不同体系涂层试样在3.5% NaCl 溶液中的涂层孔隙电阻Ac随浸泡时间的变化404中国造 船学术论文图5是不同体系涂层试样在3.5%NaCl 溶液中的%随浸泡时间的变化,一方面私越大,电荷转移越 难发生,金属越不易发生腐蚀;另一方面电荷转移电阻及出现的早晚,也说明了涂层屏蔽性能的好坏, 电荷转移电阻及出现得越晚,说明腐蚀介质渗透到金属的时间越晚,涂层的屏蔽性能越好,否则就越 差[9]。