一种工件材料去除仿真的方法
铣削平面的常用方法
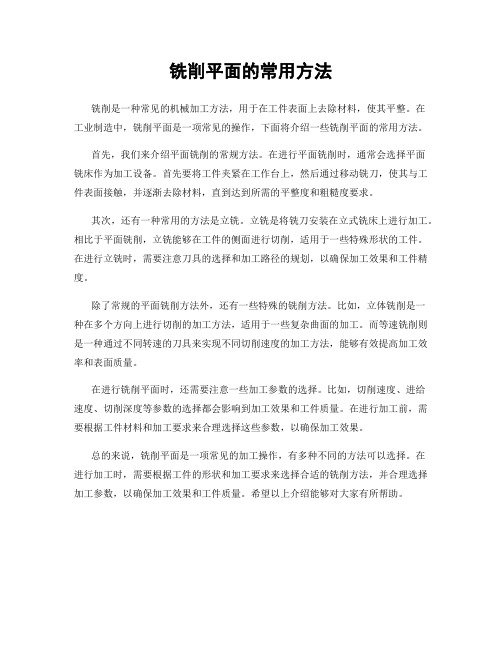
铣削平面的常用方法
铣削是一种常见的机械加工方法,用于在工件表面上去除材料,使其平整。
在
工业制造中,铣削平面是一项常见的操作,下面将介绍一些铣削平面的常用方法。
首先,我们来介绍平面铣削的常规方法。
在进行平面铣削时,通常会选择平面
铣床作为加工设备。
首先要将工件夹紧在工作台上,然后通过移动铣刀,使其与工件表面接触,并逐渐去除材料,直到达到所需的平整度和粗糙度要求。
其次,还有一种常用的方法是立铣。
立铣是将铣刀安装在立式铣床上进行加工。
相比于平面铣削,立铣能够在工件的侧面进行切削,适用于一些特殊形状的工件。
在进行立铣时,需要注意刀具的选择和加工路径的规划,以确保加工效果和工件精度。
除了常规的平面铣削方法外,还有一些特殊的铣削方法。
比如,立体铣削是一
种在多个方向上进行切削的加工方法,适用于一些复杂曲面的加工。
而等速铣削则是一种通过不同转速的刀具来实现不同切削速度的加工方法,能够有效提高加工效率和表面质量。
在进行铣削平面时,还需要注意一些加工参数的选择。
比如,切削速度、进给
速度、切削深度等参数的选择都会影响到加工效果和工件质量。
在进行加工前,需要根据工件材料和加工要求来合理选择这些参数,以确保加工效果。
总的来说,铣削平面是一项常见的加工操作,有多种不同的方法可以选择。
在
进行加工时,需要根据工件的形状和加工要求来选择合适的铣削方法,并合理选择加工参数,以确保加工效果和工件质量。
希望以上介绍能够对大家有所帮助。
金属切削中的材料去除机制与切削力分析

金属切削中的材料去除机制与切削力分析金属切削是一种常见的加工方法,广泛应用于制造业。
了解金属切削中的材料去除机制和切削力分析对于提高切削效率和工件质量至关重要。
本文将介绍金属切削中的材料去除机制和切削力分析的基本原理及相关实验方法。
一、材料去除机制在金属切削过程中,材料被切削刀具与工件之间的相对运动剪断。
这种剪断过程可以通过两种机制来解释,分别是塑性变形机制和断裂机制。
1. 塑性变形机制塑性变形机制是指金属在切削过程中由于受到外力作用而发生塑性形变。
切削刀具在刀尖与工件接触处施加力量,引起金属产生应力。
当应力超过金属的屈服应力时,金属开始发生塑性变形。
在切削区域,沿着切削刃前进的方向,材料被产生的压力推到一侧,形成一个切削薄层。
这个薄层随着刀具的运动而不断切削下去。
2. 断裂机制断裂机制是指在切削过程中,当切削力超过材料内部的强度极限时,材料会发生断裂。
如果金属的韧性较差或者切削速率较高,断裂机制会变得更加明显。
二、切削力分析切削力分析是评估切削过程中的切削力大小和方向的方法。
准确分析切削力可以帮助我们优化加工参数和改进切削刀具设计。
1. 切削力的组成切削力包括主切削力、法向切削力和切向切削力三个方向的力。
主切削力是指切削过程中与刀具主切削方向相对的力,通常为刀具前进方向上的力。
法向切削力是指与工件外表面垂直的力,切向切削力是指与工件表面平行的力。
切削力的大小和方向会直接影响到加工过程的稳定性和加工表面的质量。
2. 切削力分析的实验方法目前,常用的方法有两种:实验方法和数值仿真方法。
实验方法是通过使用专门的切削力测试设备,在实际切削过程中测量切削力的大小和方向。
这些设备通常包括力传感器、加速度计和数据采集装置。
实验方法的优点是直接测量,准确度较高,但需要较昂贵的测试设备。
数值仿真方法是使用计算机模拟的方法预测切削力大小和方向。
通过建立切削力模型和材料去除模型,在数值仿真软件中进行计算。
数值仿真方法可以快速预测不同切削参数和切削刀具对切削力的影响,但是结果的准确性取决于模型的精度和计算方法的选取。
铣削加工加工方法
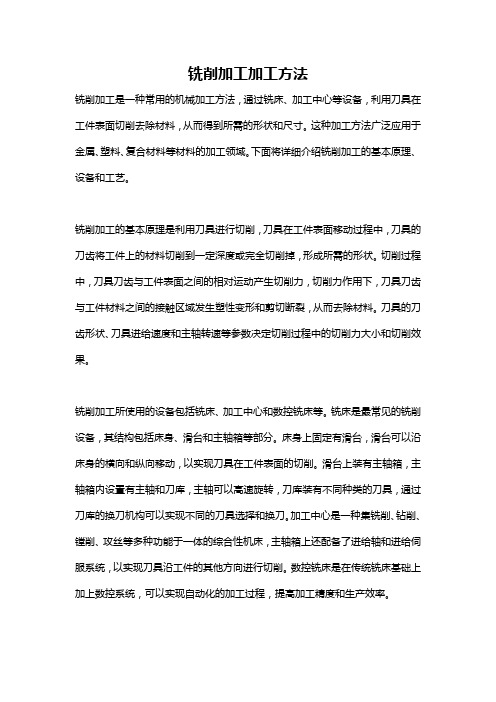
铣削加工加工方法铣削加工是一种常用的机械加工方法,通过铣床、加工中心等设备,利用刀具在工件表面切削去除材料,从而得到所需的形状和尺寸。
这种加工方法广泛应用于金属、塑料、复合材料等材料的加工领域。
下面将详细介绍铣削加工的基本原理、设备和工艺。
铣削加工的基本原理是利用刀具进行切削,刀具在工件表面移动过程中,刀具的刀齿将工件上的材料切削到一定深度或完全切削掉,形成所需的形状。
切削过程中,刀具刀齿与工件表面之间的相对运动产生切削力,切削力作用下,刀具刀齿与工件材料之间的接触区域发生塑性变形和剪切断裂,从而去除材料。
刀具的刀齿形状、刀具进给速度和主轴转速等参数决定切削过程中的切削力大小和切削效果。
铣削加工所使用的设备包括铣床、加工中心和数控铣床等。
铣床是最常见的铣削设备,其结构包括床身、滑台和主轴箱等部分。
床身上固定有滑台,滑台可以沿床身的横向和纵向移动,以实现刀具在工件表面的切削。
滑台上装有主轴箱,主轴箱内设置有主轴和刀库,主轴可以高速旋转,刀库装有不同种类的刀具,通过刀库的换刀机构可以实现不同的刀具选择和换刀。
加工中心是一种集铣削、钻削、镗削、攻丝等多种功能于一体的综合性机床,主轴箱上还配备了进给轴和进给伺服系统,以实现刀具沿工件的其他方向进行切削。
数控铣床是在传统铣床基础上加上数控系统,可以实现自动化的加工过程,提高加工精度和生产效率。
铣削加工的基本工艺包括刀具选择、刀具装夹、工件装夹、刀具路径规划和切削参数设置等。
刀具的选择要根据工件材料和加工要求进行,包括刀具的材料、刀齿形状和刀具直径等。
刀具的装夹要保证刀具牢固固定,以防止在切削过程中的脱落和振动。
工件的装夹要保持工件的稳定位置,以保证加工质量。
刀具路径规划是根据工件形状和加工要求确定刀具的移动轨迹,一般包括顺铣、逆铣和横向铣削等方式。
切削参数的设置是根据工件材料和加工要求确定切削速度、进给速度和切削深度等参数,以保证切削过程中的切削力和加工效果。
常用金属切削加工方法
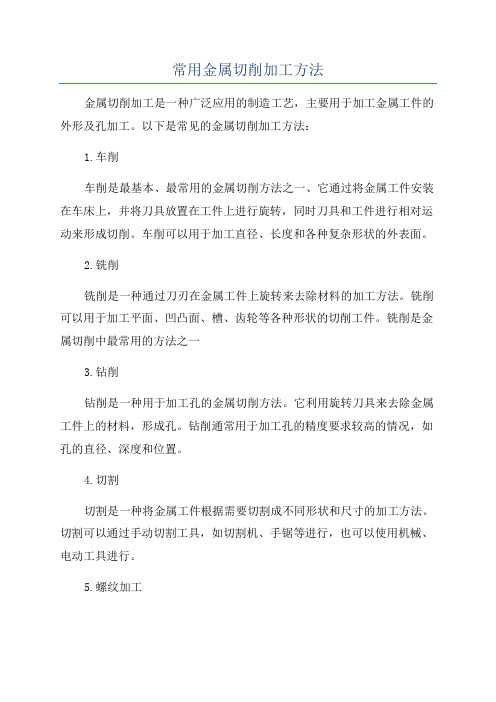
常用金属切削加工方法金属切削加工是一种广泛应用的制造工艺,主要用于加工金属工件的外形及孔加工。
以下是常见的金属切削加工方法:1.车削车削是最基本、最常用的金属切削方法之一、它通过将金属工件安装在车床上,并将刀具放置在工件上进行旋转,同时刀具和工件进行相对运动来形成切削。
车削可以用于加工直径、长度和各种复杂形状的外表面。
2.铣削铣削是一种通过刀刃在金属工件上旋转来去除材料的加工方法。
铣削可以用于加工平面、凹凸面、槽、齿轮等各种形状的切削工件。
铣削是金属切削中最常用的方法之一3.钻削钻削是一种用于加工孔的金属切削方法。
它利用旋转刀具来去除金属工件上的材料,形成孔。
钻削通常用于加工孔的精度要求较高的情况,如孔的直径、深度和位置。
4.切割切割是一种将金属工件根据需要切割成不同形状和尺寸的加工方法。
切割可以通过手动切割工具,如切割机、手锯等进行,也可以使用机械、电动工具进行。
5.螺纹加工螺纹加工是一种用于制造螺纹的金属切削方法。
它通过旋转工件并将刀具沿着螺纹轴向移动来形成螺纹。
螺纹加工主要用于加工螺纹螺栓、螺母等紧固件。
6.刨削刨削是一种将金属工件上的材料去除形成平坦表面的加工方法。
它使用刨床或刨床类似的设备,在金属工件上移动刀具,同时刀具和工件进行相对运动来去除材料。
7.磨削磨削是一种通过磨料颗粒进行切削的金属加工方法。
它利用磨料颗粒对金属工件进行切削和抛光,以获得更高的加工精度和表面质量。
磨削通常用于加工高硬度材料、特殊形状的工件和表面要求较高的工件。
8.拉削拉削是一种通过用切削刀具在金属工件上施加压力来形成加工面的金属切削方法。
拉削通常用于加工薄壁筒体、轴类工件和螺旋面。
9.剪切剪切是一种通过在金属工件上施加剪力来将其切成两部分的金属加工方法。
剪切通常用于切割金属板材、金属板和金属带。
10.冲压冲压是一种通过在金属工件上施加压力来将其切割成所需形状的金属加工方法。
冲压通常用于大规模、高效率的批量生产,可以加工出复杂的形状和细节。
基于OpenGL的数控铣削材料去除过程动态仿真

第 3 期 ( 第 1 2期 ) 总 4 20 0 7年 6月
机 械 工 程 与 自 动 化
M ECHANI CAL ENGI NEERI NG & AUT0M AT1 0N
N o. 3
J n u .
文 章 编 号 :6 26 1 (0 70 —0 30 17 —4 3 2 0 ) 30 3— 3
司开 发的非常优 秀的开放式 三维图形 软件 库 , 其实质是 种 图形 与硬件 的接 口。它提供 一 系列 的三维 图 形单 元 、图形变换 函数 以及外部设 备访 问函数等 ,在处理建 模 、变换 、光线 、色 彩 、动 画等方面具有 很好 的性 能 。 Op n e GI 独立于硬件 、 口系统 和操作 系统 ,能在各种 窗 平 台下工作 ,许 多计 算机公 司把 O e GI 集成 到各 种 pn 窗 口和操作 系统 中。VC + MF ( 软基础 类库 )包 +中 C 微 含 了强大的基于 Wid w n o s的应用框 架 ,提 供 了丰 富 的 窗 口和事件 管理 函数 , 利用 MF C调用 Op n 函数 可 e GI 以较方便 地实现数控铣 削材料去 除过程的 动态仿 真 。
基 于 Op n e GL 的数控 铣 削材 料 去 除过 程 动 态仿 真
黄 静 ,刘 小 明 ,柴 苍 修
40 7) 3 0 0 ( 汉 理 工 大 学 机 电工 程 学 院 , 湖北 武 汉 武
摘 要 : 用 Op n 利 e GL提 供 的强 大 三 维 图 形 开 发 功 能 和 Vi a C + 程 环 境 , 用 可 以 控 制 精 度 的 Z ma s l+编 u 采 — p算 法 , 较 简 便 地 实 现 了数 控 铣 削 材 料 去 除 过 程 的 动 态仿 真 。
VERICUT的数控仿真加工及改进办法分析

VERICUT的数控仿真加工及改进办法分析VERICUT 是一种数控机床仿真软件,它可以对数控加工过程进行实时仿真和分析,以便于寻找潜在的错误或问题,并进行改进。
本文将对该软件的数控仿真加工及改进办法进行分析。
VERICUT 能够模拟数控机床的实际加工过程,从而可以检查刀具路径、加工时间、材料去除率和工件形状等相关方面。
具体的仿真流程可以概括为以下几个步骤:1. 导入 CAD 模型并进行设备模拟。
在这个步骤中,用户需要导入模型数据以及设备参数,例如夹具、刀具、工艺参数等。
2. 编辑加工数据并进行仿真。
在这个步骤中,用户可以编辑加工过程中的相关参数,例如刀具轨迹、刀具直径、加工深度等,并在软件界面中进行仿真。
3. 评估仿真结果并进行优化。
在这个步骤中,用户需要评估仿真结果以确定是否存在问题或优化机会,例如材料去除率是否满足要求、工件表面质量是否达到预期等。
如果存在问题,用户就需要重新编辑加工数据和进行仿真直至结果合理为止。
虽然 VERICUT 已经可以提供较为完整的数控仿真加工方案,但仍然存在一些改进办法可以进一步优化其性能。
1. 提高仿真精度。
如果要在 VERICUT 中进行高精度仿真,需要考虑诸如刀具检测、变形模拟、加工瞬时处理等方面的问题。
其中,变形模拟是解决机械变形和刀具变形的重要方法。
同时,为了更加准确地模拟材料去除过程,还需考虑材料的物理性质和机床控制命令等。
2. 提高仿真效率。
在进行大规模仿真时,需要针对各类场景性能进行优化,例如利用类似于并行计算和图像压缩的技术提高仿真效率,以便于实现更快速的仿真结果。
3. 增强人机交互性。
虽然软件提供了种类繁多的仿真参数编辑视图,但依然有很多选择并不明显,这导致了用户需要进行更多的实验测试,增加了使用成本。
因此,提高人机交互性,加强反馈功能等措施可以帮助用户快速找到关键性能,提高效率。
总之,通过对 VERICUT 的数控仿真加工及改进办法进行分析,我们可以发现优化仿真性能、提高仿真精度和效率、巩固人机交互性等方面的改进建议,这些措施将有助于让该软件更好地服务于广大客户和用户,提高仿真效率和成本控制。
切削加工过程与残余应力仿真研究
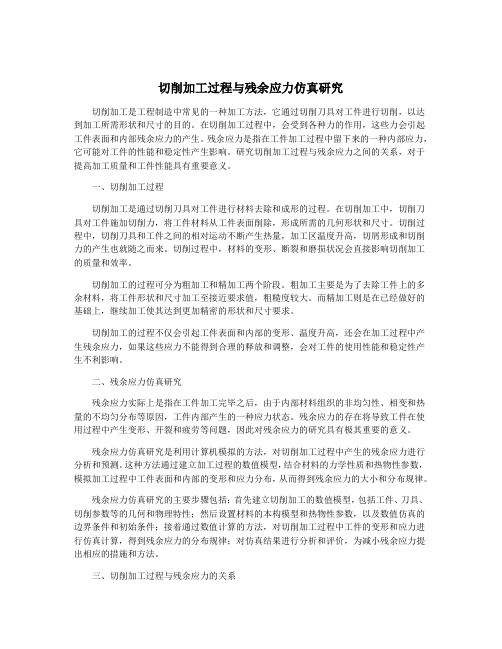
切削加工过程与残余应力仿真研究切削加工是工程制造中常见的一种加工方法,它通过切削刀具对工件进行切削,以达到加工所需形状和尺寸的目的。
在切削加工过程中,会受到各种力的作用,这些力会引起工件表面和内部残余应力的产生。
残余应力是指在工件加工过程中留下来的一种内部应力,它可能对工件的性能和稳定性产生影响。
研究切削加工过程与残余应力之间的关系,对于提高加工质量和工件性能具有重要意义。
一、切削加工过程切削加工是通过切削刀具对工件进行材料去除和成形的过程。
在切削加工中,切削刀具对工件施加切削力,将工件材料从工件表面削除,形成所需的几何形状和尺寸。
切削过程中,切削刀具和工件之间的相对运动不断产生热量,加工区温度升高,切屑形成和切削力的产生也就随之而来。
切削过程中,材料的变形、断裂和磨损状况会直接影响切削加工的质量和效率。
切削加工的过程可分为粗加工和精加工两个阶段。
粗加工主要是为了去除工件上的多余材料,将工件形状和尺寸加工至接近要求值,粗糙度较大。
而精加工则是在已经做好的基础上,继续加工使其达到更加精密的形状和尺寸要求。
切削加工的过程不仅会引起工件表面和内部的变形、温度升高,还会在加工过程中产生残余应力,如果这些应力不能得到合理的释放和调整,会对工件的使用性能和稳定性产生不利影响。
二、残余应力仿真研究残余应力实际上是指在工件加工完毕之后,由于内部材料组织的非均匀性、相变和热量的不均匀分布等原因,工件内部产生的一种应力状态。
残余应力的存在将导致工件在使用过程中产生变形、开裂和疲劳等问题,因此对残余应力的研究具有极其重要的意义。
残余应力仿真研究是利用计算机模拟的方法,对切削加工过程中产生的残余应力进行分析和预测。
这种方法通过建立加工过程的数值模型,结合材料的力学性质和热物性参数,模拟加工过程中工件表面和内部的变形和应力分布,从而得到残余应力的大小和分布规律。
残余应力仿真研究的主要步骤包括:首先建立切削加工的数值模型,包括工件、刀具、切削参数等的几何和物理特性;然后设置材料的本构模型和热物性参数,以及数值仿真的边界条件和初始条件;接着通过数值计算的方法,对切削加工过程中工件的变形和应力进行仿真计算,得到残余应力的分布规律;对仿真结果进行分析和评价,为减小残余应力提出相应的措施和方法。
基于SPH法的钢轨打磨单颗磨粒磨削仿真

基于SPH法的钢轨打磨单颗磨粒磨削仿真商维;王文健;郭俊;刘启跃【摘要】为研究钢轨打磨过程中材料的去除机理,采用光滑粒子流体动力学(SPH)的方法,仿真模拟钢轨打磨过程中单颗磨粒的切削过程,分析单颗磨粒几何形状、切削深度、负前角对打磨磨削过程中切削力、切削力比的变化规律及工件材料应力、变形情况的影响.结果表明:由于单颗磨粒的推挤作用,工件材料流动后形成毛刺和磨屑,而棱锥形磨粒可以获得较好的磨削加工表面;切削力随磨粒切削深度的增加而增大;磨粒负前角增大时,切削力和切削力比都随之增大,且负前角越大磨屑呈越明显的锯齿状.【期刊名称】《金刚石与磨料磨具工程》【年(卷),期】2016(036)003【总页数】7页(P54-59,64)【关键词】钢轨打磨;SPH法;磨粒几何形状;负前角;切削深度【作者】商维;王文健;郭俊;刘启跃【作者单位】西南交通大学,牵引动力国家重点实验室摩擦学研究所,成都610031;西南交通大学,牵引动力国家重点实验室摩擦学研究所,成都610031;西南交通大学,牵引动力国家重点实验室摩擦学研究所,成都610031;西南交通大学,牵引动力国家重点实验室摩擦学研究所,成都610031【正文语种】中文【中图分类】U216;TG58由于车轮与钢轨之间剧烈的相互作用,钢轨表面容易出现各种损伤,如波浪型磨耗、轨面擦伤、轨面剥离、轨侧严重磨损、裂纹以及轨头压溃等[1]。
钢轨打磨技术可以有效地控制和改善钢轨表面状况,延长钢轨的使用寿命[2]。
针对钢轨打磨技术,国内外取得了一定的研究成果。
智少丹等[3]建立了磨粒与钢轨接触的几何模型和受力模型,分析了磨粒切削深度与打磨功率的关系,证明了基于磨粒模型预测打磨砂轮性能的可行性。
张青等[4]建立了钢轨打磨三维热弹性有限元模型,分析了不同车速、不同砂轮转速及不同数量打磨磨头对钢轨表面温度的影响。
KANEMATSU等[5]分析了不同磨石对钢轨打磨效率的影响,得到比现有磨石打磨性能更好的七种磨石。
分层去除材料引起的加工变形规律的仿真研究

Z A G Q—e g C E G Ja , U Nn H N if , H N n X i n u g
(h n ogA r utrl ahn r R sac stt, nnCt, h n ogPoic 5 0 0 C ia S ad n g c l a M c ie eerhI tueJ a i S ad n rv e2 0 1 ,hn ) i u y ni i y n
[ bta t nmoenar utrl q imet n ei epr n f tr gpoes ahnn n fh i poes g A src]I d r g cl a e u i u p n a dvhc a s l t maua ui rcs,m c ii i o eo tema rcsi c n gs n n
m eho s t d .Be a e t e c tngpr c s i a d da i e r n e,a d c n r a h v r ih r c so nd lw ura e r u n s c us h uti o e sng h swi e a ptv a g n a e c ey h g p e ii n a o s fc o gh es , i a s a m p ra trl n ma hie y m a u a t i g tc oog tply n i o t n o e i c n r n f curn e hn l y.I u tn n c ti g,d fr ai n c u e emo a fmae i li n f e om to a s d by r v lo tra s o e o
[ 关键词 ]A ss有 限元 法; ny ; 材料去除 ; 加工 变形 [ 中图分 类号 ] H12 T 2 [ 文献标志码 ] B [ 文章编号]17 — 122 1)8 0 6 — 4 6 3 34 ( 20 — 0 3 0 0
机械加工中的材料去除理论研究

机械加工中的材料去除理论研究随着工业的发展和科技的进步,机械加工在制造业中扮演着重要的角色。
机械加工的过程包括材料去除,也就是通过切削、磨削、抛光等方式,将原材料加工成所需形状和尺寸的零件。
在机械加工中,材料去除理论是研究和指导机械加工过程的基础,其重要性不可忽视。
材料去除理论研究的核心是切削力和切削过程,这是实现高效、精确机械加工的关键。
切削力是指在切削过程中作用在切削工具和工件之间的力。
切削力的大小和方向直接影响到切削过程中材料的去除情况,因此需要对切削力进行准确的预测和控制。
根据材料去除理论研究的成果,工程师可以选择合适的切削工艺参数,优化加工路径,提高加工效率和质量。
材料去除理论的研究不仅涉及到切削力,还包括切削热、切削振动等相关问题。
切削热是在切削过程中由于摩擦和塑性变形引起的热量。
切削热的积累会导致刀具和工件的热变形,甚至使切削刃快速磨损,影响加工质量和工具寿命。
因此,研究切削热与切削参数、刀具材料等的关系,对于提高机械加工的稳定性和可靠性至关重要。
此外,材料去除理论研究还包括切削振动的分析与控制。
切削振动是指在切削过程中切削力和切削系统的共振引起的不稳定运动。
切削振动会导致加工表面粗糙、工具损伤,甚至引起操作人员的身体不适。
因此,通过研究切削振动的机理和控制方法,可以改善机械加工的稳定性和质量。
机械加工中的材料去除理论研究不仅包括实验研究,还有理论模型的建立和仿真分析。
利用先进的数值模拟技术,可以对切削过程中的各种因素进行模拟和优化。
通过建立物理模型和数学模型,可以探究切削力、切削热、切削振动等的规律,并为实际加工过程的优化和改进提供指导。
此外,材料去除理论研究还包括新材料和新工艺的探索。
随着科学技术的不断进步,新的材料和新的工艺不断涌现,对于机械加工而言,如何高效去除这些新材料成为一个新的研究方向。
通过对材料力学行为、切削机理和刀具材料等方面的研究,可以为新材料的机械加工提供理论和技术支持。
平面磨床的工件材料去除率研究
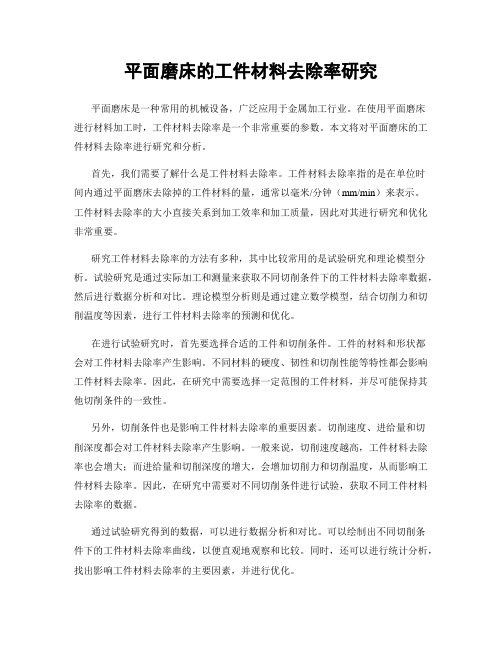
平面磨床的工件材料去除率研究平面磨床是一种常用的机械设备,广泛应用于金属加工行业。
在使用平面磨床进行材料加工时,工件材料去除率是一个非常重要的参数。
本文将对平面磨床的工件材料去除率进行研究和分析。
首先,我们需要了解什么是工件材料去除率。
工件材料去除率指的是在单位时间内通过平面磨床去除掉的工件材料的量,通常以毫米/分钟(mm/min)来表示。
工件材料去除率的大小直接关系到加工效率和加工质量,因此对其进行研究和优化非常重要。
研究工件材料去除率的方法有多种,其中比较常用的是试验研究和理论模型分析。
试验研究是通过实际加工和测量来获取不同切削条件下的工件材料去除率数据,然后进行数据分析和对比。
理论模型分析则是通过建立数学模型,结合切削力和切削温度等因素,进行工件材料去除率的预测和优化。
在进行试验研究时,首先要选择合适的工件和切削条件。
工件的材料和形状都会对工件材料去除率产生影响。
不同材料的硬度、韧性和切削性能等特性都会影响工件材料去除率。
因此,在研究中需要选择一定范围的工件材料,并尽可能保持其他切削条件的一致性。
另外,切削条件也是影响工件材料去除率的重要因素。
切削速度、进给量和切削深度都会对工件材料去除率产生影响。
一般来说,切削速度越高,工件材料去除率也会增大;而进给量和切削深度的增大,会增加切削力和切削温度,从而影响工件材料去除率。
因此,在研究中需要对不同切削条件进行试验,获取不同工件材料去除率的数据。
通过试验研究得到的数据,可以进行数据分析和对比。
可以绘制出不同切削条件下的工件材料去除率曲线,以便直观地观察和比较。
同时,还可以进行统计分析,找出影响工件材料去除率的主要因素,并进行优化。
理论模型分析是另一种常用的研究方法。
通过建立数学模型,可以预测和优化工件材料去除率。
在建立数学模型时,需要考虑多种因素,如切削力、切削温度、刀具磨损等。
这些因素之间的关系非常复杂,需要综合考虑。
通过建立合理的数学模型,可以预测出不同切削条件下的工件材料去除率,并提供优化方案。
粗糙度 加工方法

粗糙度加工方法粗糙度是指物体表面的粗糙程度或不光滑程度。
在制造和加工过程中,粗糙度是一个重要的参数,需要控制在一定的范围内,以满足特定的功能和需求。
下面我将介绍一些常见的粗糙度加工方法。
1. 铣削:铣削是一种常见的粗糙度加工方法,通过切削工具在工件上进行走刀运动,去除不需要的材料,从而形成所需的形状和尺寸。
铣削可以实现高效的精细加工,其粗糙度通常可以控制在比较小的范围内。
2. 研磨:研磨是一种常用的粗糙度加工方法,通过磨料与工件表面的相对运动,去除表面的不规则凸起,使得工件表面变得更加光滑。
研磨既可以手动进行,也可以借助机械设备实现。
不同的研磨工艺和磨料的选择可以实现不同的粗糙度要求。
3. 抛光:抛光是一种通过在工件表面施加力和磨料的相对运动来改善表面质量的加工方法。
抛光可以进一步降低工件表面的粗糙度,提高表面的光滑度和亮度。
抛光通常需要使用特殊的设备和磨料,针对不同的材料和粗糙度要求选择合适的抛光工艺。
4. 拉削:拉削是一种通过金属刀具和工件之间的相对运动来加工工件表面的方法。
通常情况下,拉削可以实现高精度、高效率的加工,具有较低的表面粗糙度。
5. 电火花加工:电火花加工是一种通过电脉冲放电来去除工件表面材料的加工方法。
通过电极与工件之间的电脉冲放电,工件表面的材料可以被腐蚀和去除,从而改善表面的质量和粗糙度。
电火花加工可以实现较高的加工精度和表面质量。
除了上述介绍的几种常见的粗糙度加工方法,还有许多其他的方法,如喷砂、化学处理等。
这些加工方法根据具体的应用需求和工件的材料特性选择合适的方法,以实现所需的粗糙度要求。
需要注意的是,不同的加工方法和工艺参数对粗糙度的影响是不同的,需要根据具体情况进行调整和优化。
此外,在加工过程中,还需要严格控制设备、工具和刀具的质量,以保证加工的稳定性和一致性。
通过合理的加工方法和精细的工艺控制,可以实现满足不同应用需求的粗糙度要求。
切削过程中材料去除机制及切屑形态演化研究

切削过程中材料去除机制及切屑形态演化研究切削是一种常见的机械加工方法,通过在工件上施加切削力,去除材料以形成所需的形状和尺寸。
然而,在切削过程中,材料的去除机制以及切屑的形态演化是一个复杂而关键的问题。
研究这些问题不仅有助于深入理解切削过程的本质,还能够指导切削工艺的优化和刀具的设计。
在切削过程中,材料的去除主要通过切削刀具与工件的相对运动来完成。
刀具与工件之间形成一定的切削角,并施加一定的切削力。
切削刀具的刀尖与工件表面相交,形成一个刀尖接触区域。
在这个接触区域内,切削角与切削力共同作用下,材料开始发生塑性变形和切削磨损,从而被去除。
材料的去除机制可分为切削剪切和切削破碎两种。
切削剪切是指材料沿着刀具刃口形成的剪切面上的原子间滑动和轧制,最终导致材料的断裂。
在切削过程中,切削剪切是主要的去除机制。
在搬运切屑的同时,切削刀具也会受到一定的摩擦磨损。
切削剪切的具体机理涉及塑性变形、切削力分析以及刀具与工件接触面的应力分布等方面,仍然是切削研究的重要课题。
切削破碎是指材料在切削过程中发生裂纹和破碎,从而被去除。
切削破碎主要发生在脆性材料或强脆性材料的加工中。
在加工过程中,由于切削刀具的剧烈冲击或高应力作用下,材料发生裂纹、破碎或剥落,并随着切削过程的进行而脱离工件表面。
切削破碎的研究对于脆性材料的切削加工具有重要的指导意义。
切削过程中形成的切屑是切削去除过程的副产品,除了研究切削机理外,研究切屑形态演化也是切削研究的重要内容之一。
切屑的形态与切削工艺参数、材料性质以及刀具性能都密切相关。
切屑可以分为连续切屑、不连续切屑和层状切屑三种形态。
连续切屑具有光滑的表面和较大的形变能,是切削过程中的预期形态。
而不连续切屑和层状切屑通常是由于材料的脆性或切削参数不当引起的,会导致切削过程的变动和不稳定,影响加工质量和效率。
切削过程中材料的去除机制和切屑形态演化的研究一直是学术界关注的热点。
通过对切削剪切和切削破碎的研究,可以优化切削工艺参数、提高刀具的设计和材料的加工性能。
机器人恒力磨抛材料去除研究

2021年2月第49卷第4期机床与液压MACHINETOOL&HYDRAULICSFeb.2021Vol 49No 4DOI:10.3969/j issn 1001-3881 2021 04 007本文引用格式:李晓炜,饶巍林.机器人恒力磨抛材料去除研究[J].机床与液压,2021,49(4):31-36.LIXiaowei,RAOWeilin.Researchonmaterialremovalofroboticconstant⁃forcegrindingandpolishing[J].MachineTool&Hydraulics,2021,49(4):31-36.收稿日期:2020-09-16基金项目:福建省自然科学基金(2018J05099)作者简介:李晓炜(1985 ),男,硕士,讲师,研究方向为工业机器人应用技术㊁新能源技术㊂E-mail:389976373@qq com㊂机器人恒力磨抛材料去除研究李晓炜,饶巍林(福建工程学院机械与汽车工程学院,福建福州350118)摘要:针对传统机器人-砂带磨抛工件时材料去除量难以定量控制的问题,结合Preston磨削经验公式与赫兹弹性接触理论,将法向磨抛力㊁砂带速度㊁工件进给速度3个工艺参数作为变量,建立机器人恒力磨抛的材料去除深度模型;然后进行硬件选型,搭建机器人恒力磨抛实验平台;最后以上述3个工艺参数为变量设计了机器人恒力磨抛单因素实验,实验结果较好验证了该材料去除深度模型的准确性㊂关键词:工业机器人;Preston方程;恒力控制;材料去除模型中图分类号:TP242 2ResearchonMaterialRemovalofRoboticConstant⁃forceGrindingandPolishingLIXiaowei,RAOWeilin(SchoolofMechanical&AutomotiveEngineering,FujianUniversityofTechnology,FuzhouFujian350118,China)Abstract:Aimingattheproblemthatitisdifficulttoquantitativelycontrolthematerialremovalamountduringtraditionalrobotic⁃sandbeltgrindingandpolishing,combinedwiththePreston sempiricalgrindingformulaandHertzflexibilitycontacttheory,thema⁃terialremovaldepthmodeloftheroboticconstant⁃forcegrindingandpolishingwasestablishedinwhichthenormalgrindingforce,abra⁃sivebeltspeedandworkpiecefeedrateweretakenasvariables.Thehardwareswereselectedandtheexperimentalplatformofroboticconstant⁃forcegrindingandpolishingwasbuilt.Takingtheabovethreeprocessparametersasvariables,thesinglefactorexperimentoftheroboticconstant⁃forcegrindingandpolishingwasdesigned.Theexperimentalresultsverifytheaccuracyofthematerialremovaldepthmodel.Keywords:Industrialrobot;Prestonequation;Constant⁃forcecontrol;Materialremovalmodel0㊀前言随着先进制造技术的发展,工件的再处理再加工过程中,越来越多使用具有冷态㊁高效㊁万能的砂带磨削工艺[1-4],特别随着机器人技术的普及,机器人拥有的重复定位精度较高,能够保证加工的精度和一致性的特点,使得越来越多的工业机器人被运用于磨抛领域[1,5-6]㊂而当工业机器人夹持着工件在砂带上进行磨抛作业时,砂带磨抛作为一种弹性加工工艺,在其打磨过程中不易对材料去除量进行准确控制,预测准确度仍不够精确是砂带磨抛中长期以来的关键问题[7-8]㊂对此,研究人员进行了大量试验,探讨砂带磨抛过程精确的材料去除深度预测[9],研究材料去除深度的相关性分析[10],相关结果表明砂带磨削的材料去除深度主要与磨削过程的工艺参数如接触压力㊁砂带速度㊁进给速度等因素有关[11-12]㊂北京航空航天大学刘斐等人[13]研究了砂带张紧对接触轮变形和磨削深度的影响,采用弹性力学平面问题的复变函数解法,根据Hammann经验公式建立了一种机器人砂带磨削深度仿真和预测模型,研究过程中设定砂带线速度㊁砂带宽度恒定,仅研究不同工件进给速率下,不同的接触应力与实际磨削深度之间的关系;华中科技大学的吴昌林等[14]在自主研发的数控抛光机床基础上研究铝合金车轮磨抛问题,在假设抛光工具与铝合金车轮表面的接触服从椭圆赫兹接触的前提下,利用Preston方程推导材料去除深度模型;HE等[15]以磨削压力为重点研究对象,同时考虑了接触体的结合特征以及砂带弹性接触轮的材料特性,总结出砂带磨削过程中接触压力对钢轨材料去除的影响规律㊂综上,本文作者将运用弹性接触理论以及Pres⁃ton经验方程,结合法向磨抛力㊁砂带速度㊁工件进给速度3个变量推导机器人磨抛时的材料去除深度模型,并通过实验平台进行打磨实验来验证其准确性㊂1 材料去除深度模型建立1 1㊀基于Preston方程的分析Preston方程是广泛运用于磨削加工中的经验方程[16]㊂此方程用于描述砂带磨抛过程中工件的加工时间与单位磨抛接触面积内的材料去除率与各工艺参数之间的定量函数关系,如下式所示:Δz=ʏt0Kpfvdt(1)式中:Δz为磨抛过程中的材料去除量体积;t为打磨时间;Kp为Preston常数;f为砂带与工件之间的接触面压力;v为砂带磨粒与工件的相对运动速度㊂设上述磨抛过程中单位接触面积为ΔS,单位面积上的压力为p,H为材料单位面积上的近似磨抛深度,结合式(1)则可得到式(2):H=ΔzΔS=ʏt0KpfvdtΔS(2)对式(2)求时间微分可将其表达为磨抛区域内某一点在时间dt内的材料去除深度dH,可表示为dHdt=Kppv(3)式(3)仅适用于定点打磨加工,并不能描述工件被动态地直线移动打磨㊂在实际磨抛加工过程中是动态移动的,即打磨工具与工件之间有一个相对移动速度㊂设在时间段t内,砂带磨抛过程中在工件表面的相对移动距离为L,即可得到工件进给速度vg表达式:dLdt=vg(4)将式(4)代入式(3),可得被加工材料在一定压力下磨抛时,材料表面磨抛区域上某点的材料去除深度dH与工件进给距离dL之间的量化关系式:dHdL=Kpvpvg(5)1 2㊀机器人砂带磨抛材料去除深度模型推导由于砂带与承载砂带的接触轮都具有弹性特征,弹性物体在一定压力下发生接触时,会产生一定形状的接触区域㊂根据弹性接触理论[17],当被加工圆柱形棒料沿着机器人基坐标z轴方向向下压向砂带时,被加工工件表面与砂带表面在接触后产生的接触面近似椭圆㊂图1为磨抛时在工件与砂带产生的接触区域所建立的o-xyz坐标系,y轴指向砂带接触轮轴向方向,x轴与工件移动方向平行,法向压力Fn与z轴平行,o为接触区域的中心,椭圆长半轴a与x轴平行,椭圆短半轴b与y轴平行㊂图1㊀在接触区域所建立的o-xyz坐标系在接触区域中心压力最大,当越向接触区域边缘靠近时,压力越小,其压力分布如式(6):p(x,y)=pmax1-xaæèçöø÷2-ybæèçöø÷2(6)式中:pmax为磨抛接触区域中心处压力㊂根据椭圆表达式对接触区域的压力进行积分,可得到作用于整个磨抛接触区域内的磨抛法向压力Fn的大小,如式(7)所示:Fn=∬p(x,y)dxdy=23πabpmax(7)由于在实验平台中磨抛法向接触力Fn是可调变量,由此可求得磨抛区域中心压力pmax:pmax=3Fn2πab(8)为了获得磨抛接触区域的最大材料去除深度,建立图2所示接触区域的o-xy坐标系㊂在o-xy坐标系中设点A1(-x,d)㊁点A2(x,d),假设磨抛过程中以恒力Fn进行㊂当产生弹性接触区域后,取线段A1A2为研究对象,从A1移动到A2的磨抛轨迹与x轴平行㊂由理论分析可知,恒力磨抛过程中,由于区域内存在不同压力分布,这样便造成接触区域内不同位置的材料去除量是不同的,在A1A2线段里的材料去除量是该轨迹内所有点的材料去除量的累加㊂图2㊀椭圆接触区域o-xy坐标系结合式(5)㊁式(6)㊁式(8),可对A1到A2线段区域内的材料去除量进行积分,从而得到该线段区㊃23㊃机床与液压第49卷域的材料去除深度表达式(9):H(y)=2ʏd03KpFn(vs+vg)2vgπab1-x2a2-y2b2dx(9)其中:vs为砂带速度;vg为工件进给速度㊂根据椭圆表达式可得d的长度为d=1-y2b2æèçöø÷a2(10)接触所形成椭圆的长短半轴a㊁b可由下式确定:a=3k2αk()FnπE∗A+B()éëêêùûúú1/3b=3αk()FnkπE∗A+B()éëêêùûúú1/3ìîíïïïï(11)其中:1E∗=1-a21E1+1-a22E2(12)A+B=121R1+1R2+1R∗1+1R∗2æèçöø÷(13)B-A=121R1-1R∗1æèçöø÷2+1R2-1R∗2æèçöø÷2+éëêê21R1-1R∗1æèçöø÷1R2-1R∗2æèçöø÷cos2βùûúú1/2(14)εk()=1+0 6A+B()(15)k=1 034BAæèçöø÷0 64(16)式中:a1㊁a2分别为磨抛砂带弹性接触轮㊁工件的泊松比;E1㊁E2㊁E∗分别为砂带接触轮㊁工件的弹性模量以及二者相对弹性模量;A㊁B分别为砂带接触轮与工件于接触点的相对曲率;ε(k)为第二类椭圆积分;R1㊁R∗1为砂带接触轮在接触中心点的曲率半径;R2㊁R∗2为工件在接触中心点的曲率半径;β为砂带接触轮与工件在接触点处的曲率半径所在法面的夹角㊂综上,对式(9)进行计算并化简可得A1到A2磨抛轨迹沿x轴方向的材料去除深度模型H(y)=3KpFn(vs+vg)vgb-3KpFn(vs+vg)vgb3y2(17)分析式(17)可知:A1到A2磨抛轨迹的材料去除深度模型为二次抛物线型,同理整个磨抛接触区域都满足此表达式㊂在磨抛加工中,材料去除最大深度是个极其重要的参数,它决定了材料的最终去除深度㊂由式(9)可知H(y)在原点(0,0)处便取得最大材料去除深度值,并且由于工件移动速度vg远小于砂带线速度vs,这里直接忽略工件移动速度vg,得到如下磨抛最大材料去除深度值:Hmax=3KpFnvsvgb(18)将式(11)中的短半轴b表达式代入式(18)可得最终表达式:Hmax=3KpvsF2/3nvgkπE∗(A+B)3α(k)æèçöø÷1/3(19)从式(19)中能得出恒力磨抛过程中的材料最大去除深度除了与砂带㊁砂带接触轮以及被加工工件的固有属性有关,还与常数Kp㊁砂带磨削线速度vs㊁法向磨抛力Fn成正比,与工件本身的进给速度vg成反比㊂1 3㊀Preston常数的理论推导常数Kp是一个包含了众多关于磨抛固有影响因素的集合㊂为了能够满足式(19)的建立,需要求得Kp㊂现对常数Kp进行推导㊂根据式(8),设磨抛区域面积为ΔS,结合之前的磨抛区域压力分布式分别对x㊁y进行积分可得到施加的法向磨抛压力Fn,综合分析可以得到关系式(20):Δz=Kpvt∬ΔSp(x,y)dxdy=KpvtFn(20)设材料去除量的质量为Δm,密度为ρ,由于Δz=Δm/ρ,将其代入式(20)则可得出下式:Δz=Δmρ=KpvtFn(21)由于工件移动速度vg远小于砂带线速度vs,同理忽略工件移动速度vg,使用砂带速度vs代替砂带磨粒与工件的瞬时相对运动速度v:Kp=ΔmρvsFnt(22)至此,得到了Preston常数Kp的表达式㊂2 机器人恒力磨抛实验与分析2 1㊀实验平台的搭建所搭建的机器人实验平台如图3所示,主控端为工控机(型号为研华IPC⁃510,运行Windows操作系统),被控端为KUKA工业机器人(KUKAKR900sixx),力检测单元为安装在机器人末端的力传感器,其型号为美国DeltaIP60(F/TSensor)㊂图3㊀机器人实验平台㊃33㊃第4期李晓炜等:机器人恒力磨抛材料去除研究㊀㊀㊀2 2㊀试验法求Preston常数所建立的材料去除深度模型中的Preston常数Kp是包含了诸多因素的集合,需要在实际工况中确定㊂根据式(22)可知,为了获得Kp,磨抛实验需要5个参数㊂其中材料去除量的质量Δm可以通过工件磨抛前的质量m1减去磨抛后的质量m2计算获得即(m1-m2),工件磨抛前后的质量通过电子秤(精度:0 001g)称量;工件材料密度可通过查询资料获得;砂带运动速度vs㊁磨抛法向压力Fn㊁磨抛过程时间t这3个因素需要在实验中取不同水平,进而获得不同组参数组合㊂实验场景示意如图4所示㊂图4㊀实验场景示意因素水平如表1所示㊂表1㊀实验因素水平水平因素vs/(m㊃s-1)Fn/Nt/s1551021010153151520㊀㊀设计的正交表如表2所示,进行实验并记录数据,然后按照式(22)求出Kp,最后计算出9次实验中Kp的平均值作为最终结果㊂此实验平台的Pres⁃ton常数Kp=1 644ˑ10-8㊂表2㊀正交表及实验数据记录试验号因素vs/(m㊃s-1)Fn/Nt/sΔm/gKp/(10-8)Kp/(10-8)155100.0311.56121010150.3811.61831515200.6101.7294510200.1311.66551015100.2021.7176155150.1371.5587515150.1441.6368105200.1361.73891510100.1851.5771.6442 3㊀材料去除深度模型实验验证及分析根据上一小节所确定的此机器人磨抛实验平台的Preston常数Kp,现设计实验验证材料去除深度模型的准确性㊂在实验中,被加工工件均为45钢圆柱形棒料(密度ρ=7 85g/cm3,半径为15mm),砂带号为240㊂根据实验材料与磨抛机属性,设定相应参数;磨抛橡胶接触轮半径为25mm,加工半径为15mm的45号钢圆柱形棒料,故R1=0 025m,R∗1=+¥,R2=+¥,R∗2=0 015m;根据查阅相关资料两者的弹性模量分别是E1=109Pa㊁E2=209000GPa,泊松比分别为a1=0 47㊁a2=0 269㊂打磨场景如图5所示㊂图5㊀机器人夹持棒料打磨场景设计单因素打磨实验,工艺参数值如表3所示㊂每组实验完成后,便对圆柱形45钢棒料进行材料去除深度测量,测量工具为千分尺(精度:0 01mm)㊂测量示意如图6所示,图中所示为垂直于45钢圆柱形棒料轴线的横截面,R为圆柱形棒料的直径,打磨深度H通过直径R减去千分尺测量的读数获得㊂每组分别测量3次,并估读到0 001mm,求其平均值作为最后结果,实验数据记录如表3所示㊂将表3中材料去除深度实验数据绘制成散点图,并与建立的材料去除深度模型仿真计算曲线进行对比,如图7所示㊂㊃43㊃机床与液压第49卷表3㊀工艺参数组及实验数据记录序号Fn/Nvs/(m㊃s-1)vg/(mm㊃s-1)H/mm序号Fn/Nvs/(m㊃s-1)vg/(mm㊃s-1)H/mm序号Fn/Nvs/(m㊃s-1)vg/(mm㊃s-1)H/mm15520.4131310511.195255520.362210520.5721410520.4532651020.586315520.9161510530.3342751520.913420521.2241610540.1592852021.126551020.71717101012.2242910520.5546101021.10518101021.34730101021.0277151021.76319101030.63231101521.6358201022.13420101040.41332102022.014951521.14621101512.8173315520.62810101521.57222101521.45434151021.71611151522.12823101531.22235151522.01412201522.56724101540.83636152022.823图6㊀材料去除深度测量示意㊀㊀在图7中,通过观察对比实验数据散点分布与仿真曲线具有一致性;在9-12号实验组中,实际打磨深度偏离仿真值较大,分析其原因是随着法向力Fn与砂带线速度vs的增大,两者作用使得实验平台出现较大机械振动,出现砂带磨粒破碎或掉落,造成材料去除率下降㊂在图8中,当固定法向力Fn=10N,观察对比实验数据散点分布与仿真曲线具有较好拟合度㊂在图9中,当工件进给速度固定为较小值2mm/s时,实验数据与仿真曲线基本重合㊂㊀㊀图7㊀固定vg=2mm/s㊀㊀㊀㊀㊀㊀㊀图8㊀固定法向力Fn=10N㊀㊀㊀㊀㊀图9㊀固定vg=2mm/s㊀㊀现对36组实验数据进行处理及结果评价,将表3中的测量结果与仿真结果的差值设为新的测量值xi,按照下式计算测量值的平均值x:x=1nðxi(23)36组数据的平均值x为0 006mm,再按照有限测量次数的标准偏差公式(24)求出36组测量数据的标准偏差ss=ð(xi-x)2n-1(24)经过计算,36组实验数据的标准偏差s为0 142mm㊂现采用t检验法[18]对实验结果进行显著性差异检验,如式(25):t=x-μsn(25)其中实验结果置信度设为95%,标准值μ设定为0,经过计算得出t计算=0 254㊂通过对t分布值表的查阅,其中置信度为95%㊁测定次数n=40的t值为2 021(t表=2 021),由此可得出:t计算<t表(26)根据对比结果和对比t检验法的判断标准可知:实验结果与仿真结果之间不存在显著性差异,证明了机器人砂带磨抛材料去除深度模型的准确性㊂3 结论结合Preston磨削经验公式与赫兹弹性接触理论,针对传统机器人-砂带磨抛工件时的材料去除量难以进行定量控制的问题,将法向磨抛力㊁砂带速度㊁工件进给速度3个工艺参数作为变量,建立了机器人恒力磨抛的材料去除深度模型㊂搭建了机器人恒力磨抛实验平台,并进行实验验证,采用t值检验法分析实㊃53㊃第4期李晓炜等:机器人恒力磨抛材料去除研究㊀㊀㊀验数据可知,所建立的机器人砂带磨抛材料去除深度模型可较好地表示实际的机器人-砂带磨抛材料时的去除深度㊂综上,文中内容为机器人砂带磨抛材料去除模型提供了一定的理论与指导㊂参考文献:[1]黄云.砂带磨削技术的研究现状和发展方向简介[J].金刚石与磨料磨具工程,2020,40(3):1-4.HUANGY.Briefintroductionofresearchstatusanddevel⁃opmentdirectionofbeltgrindingtechnology[J].Diamond&AbrasivesEngineering,2020,40(3):1-4.[2]黄云,黄智.现代砂带磨削技术及工程应用[M].重庆:重庆大学出版社,2009.[3]肖贵坚,张友栋,黄云,等.基于灰色关联法的航发叶片机器人砂带磨削精度控制技术[J].航空制造技术,2020,63(9):63-70.XIAOGJ,ZHANGYD,HUANGY,etal.Roboticbeltgrindingaccuracycontroltechnologyofaero⁃enginebladebasedongreycorrelationmethod[J].AeronauticalManu⁃facturingTechnology,2020,63(9):63-70.[4]穆煜.磨抛机器人关键技术研究[D].北京:北京理工大学,2017.MUY.Studyonthekeytechnologyofpolishingrobot[D].Beijing:BeijingInstituteofTechnology,2017.[5]刘涛雄,刘骏.人工智能㊁机器人与经济发展研究进展综述[J].经济社会体制比较,2018(6):172-178.LIUTX,LIUJ.Aliteraturereviewonartificialintelli⁃gence,roboticsandeconomicdevelopment[J].ComparativeEconomicandSocialSystems,2018(6):172-178.[6]ZHANGH,PANZX.Roboticmachining:materialremovalratecontrolwithaflexiblemanipulator[C]//Proceedingsof2008IEEEConferenceonRobotics,AutomationandMechatronics.Chengdu:IEEE,2008:30-35.[7]黄云,黄智.砂带磨削的发展及关键技术[J].中国机械工程,2007,18(18):2263-2267.HUANGY,HUANGZ.Developmentandkeytechnologiesofabrasivebeltgrinding[J].ChinaMechanicalEngineer⁃ing,2007,18(18):2263-2267.[8]程继发.钢轨砂带打磨磨粒微观接触与材料去除理论研究[D].北京:北京交通大学,2019.CHENGJF.Theoreticalstudyonmicroscopiccontactofgrainsandmaterialremovalforrailgrindingusingabrasivebelt[D].Beijing:BeijingJiaotongUniversity,2019.[9]母焰.恒力砂带磨抛材料去除理论与实验研究[D].长春:吉林大学,2017.MUY.Thetheoreticalandexperimentalresearchonthema⁃terialremovalofconstantforceabrasivebeltgrindingandpolishing[D].Changchun:JilinUniversity,2017.[10]阮玉镇,金福江.机器人砂带磨削材料去除深度模型研究[C]//第30届中国过程控制会议论文集.昆明:中国自动化学会,2019.[11]KHELLOUKIA,RECHJ,ZAHOUANIH.Micro⁃scalein⁃vestigationonbeltfinishingcuttingmechanismsbyscratchtests[J].Wear,2013,308(1/2):17-28.[12]WANGW,YUNC.Apathplanningmethodforroboticbeltsurfacegrinding[J].ChineseJournalofAeronautics,2011,24(4):520-526.[13]刘斐,王伟,王雷,等.接触轮变形对机器人砂带磨削深度的影响[J].机械工程学报,2017,53(5):86-92.LIUF,WANGW,WANGL,etal.Effectofcontactwheel sdeformationoncuttingdepthforroboticbeltgrinding[J].JournalofMechanicalEngineering,2017,53(5):86-92.[14]吴昌林,丁和艳,陈义.铝合金车轮CNC机械抛光材料去除深度建模方法研究[J].中国机械工程,2009,20(21):2558-2562.WUCL,DINGHY,CHENY.ResearchonmodelingmethodofmaterialremovaldepthinCNCmechanicalpol⁃ishingforaluminumalloywheel[J].ChinaMechanicalEngineering,2009,20(21):2558-2562.[15]HEZ,LIJY,LIUYM,etal.Investigatingtheeffectsofcontactpressureonrailmaterialabrasivebeltgrindingperformance[J].TheInternationalJournalofAdvancedManufacturingTechnology,2017,93(1/2/3/4):779-786.[16]韩晓露,王家忠,弋景刚,等.基于Preston方程的反射杯抛磨工艺参数研究[J].机床与液压,2018,46(14):12-16.HANXL,WANGJZ,YIJG,etal.StudyonpolishingprocessingparametersofreflectivecupbasedonPrestonequation[J].MachineTool&Hydraulics,2018,46(14):12-16.[17]樊文刚,刘月明,王文玺,等.基于弹性赫兹接触的钢轨砂带打磨材料去除建模研究[J].机械工程学报,2018,54(15):191-198.FANWG,LIUYM,WANGWX,etal.Researchonmod⁃elingmethodofmaterialremovalforrailgrindingbyabra⁃sivebeltbasedonelastichertziancontact[J].JournalofMechanicalEngineering,2018,54(15):191-198.[18]李卫国,运泽健,张师,等.基于粗糙集理论的t检验广域保护区域划分方法[J].电力系统保护与控制,2019,47(19):122-130.LIWG,YUNZJ,ZHANGS,etal.Partitionmethodoft-testwide⁃areaprotectionareabasedonroughsettheory[J].PowerSystemProtectionandControl,2019,47(19):122-130.(责任编辑:张艳君)㊃63㊃机床与液压第49卷。
论述一种机械加工方法

论述一种机械加工方法引言机械加工方法是一种通过机械设备和工具对工件进行材料去除、形状修复和表面加工的加工技术。
它在制造业中占据着重要的地位,广泛应用于各个领域,如汽车制造、航空航天、电子设备等。
本文将详细论述一种常见的机械加工方法,以期更好地了解其原理、特点和适用范围。
车削加工方法车削加工方法是一种通过旋转切削刀具,将工件上的材料进行去除的机械加工技术。
该方法适用于各种形状的工件,包括圆柱形、锥面形、球面形等。
车削加工方法主要分为经济车削和数控车削两种方式。
经济车削经济车削是一种传统的机械加工方法,其通过手动操作车削工具,沿着工件轴向进行切削。
这种方法操作简单,成本低廉,适用于小批量或单件加工。
经济车削的切削速度较慢,而且需要熟练的操作工才能保证加工质量。
数控车削数控车削是一种采用数控系统来控制车床操作的机械加工方法。
相比于经济车削,数控车削具有更高的自动化程度和加工精度。
数控车床通过事先编程,可以实现复杂形状的加工,且能够快速切削,提高生产效率。
此外,由于数控车削使用机械手臂等自动装置进行操作,因此能够减少人工操作对加工质量的影响,提高工作环境的安全性。
车削加工方法的特点车削加工方法有以下几个特点:1. 广泛适用性:车削加工方法适用于各种金属和非金属材料的加工。
无论是硬度高的钢材还是柔软的塑料,都可以通过车削加工方法进行加工。
2. 高精度加工:车削加工方法具有较高的加工精度。
数控车削更是可以实现微米级的加工精度,满足了许多高精度加工需求。
3. 加工效率高:与其他加工方法相比,车削加工方法具有较高的加工效率。
特别是数控车削,可以通过事先编程,实现自动化的连续加工,大大提高了生产效率。
4. 灵活性强:车削加工方法具有较高的灵活性。
由于切削刀具可根据不同的加工要求进行更换,所以可以加工出各种不同形状的工件。
车削加工方法的应用车削加工方法在制造业中有广泛的应用,包括但不限于以下几个领域:1. 汽车制造:车削加工方法在制造汽车零部件中起着重要作用,如发动机曲轴、活塞、齿轮等。
一种工件材料去除仿真的方法
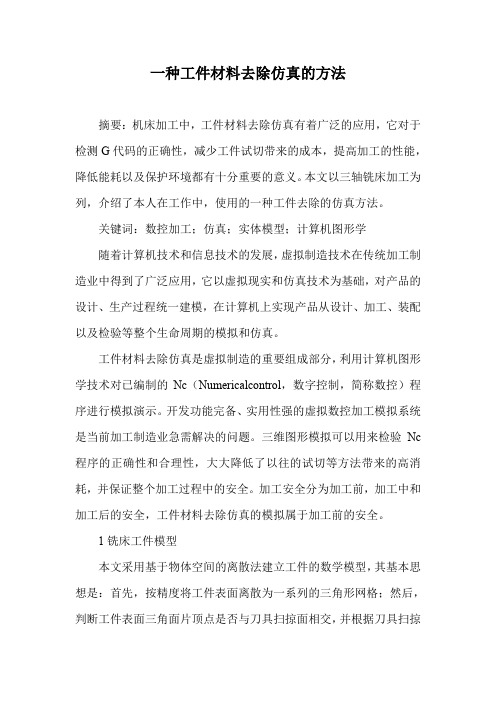
一种工件材料去除仿真的方法摘要:机床加工中,工件材料去除仿真有着广泛的应用,它对于检测G代码的正确性,减少工件试切带来的成本,提高加工的性能,降低能耗以及保护环境都有十分重要的意义。
本文以三轴铣床加工为列,介绍了本人在工作中,使用的一种工件去除的仿真方法。
关键词:数控加工;仿真;实体模型;计算机图形学随着计算机技术和信息技术的发展,虚拟制造技术在传统加工制造业中得到了广泛应用,它以虚拟现实和仿真技术为基础,对产品的设计、生产过程统一建模,在计算机上实现产品从设计、加工、装配以及检验等整个生命周期的模拟和仿真。
工件材料去除仿真是虚拟制造的重要组成部分,利用计算机图形学技术对已编制的Nc(Numericalcontrol,数字控制,简称数控)程序进行模拟演示。
开发功能完备、实用性强的虚拟数控加工模拟系统是当前加工制造业急需解决的问题。
三维图形模拟可以用来检验Nc 程序的正确性和合理性,大大降低了以往的试切等方法带来的高消耗,并保证整个加工过程中的安全。
加工安全分为加工前,加工中和加工后的安全,工件材料去除仿真的模拟属于加工前的安全。
1铣床工件模型本文采用基于物体空间的离散法建立工件的数学模型,其基本思想是:首先,按精度将工件表面离散为一系列的三角形网格;然后,判断工件表面三角面片顶点是否与刀具扫掠面相交,并根据刀具扫掠面修改各三角片顶点值,其中重点是根据刀具路径计算刀具扫掠面;最后,对三角网格进行真实感渲染。
基于三角网格的物体空间离散法己经比较成熟,并且也已经被成功应用于数控仿真的实现中。
具体来说,本文假定毛胚(待加工工件)为长方体,将毛坯的6个面分别进行离散。
上表面是待加工表面,是毛坯离散化的关键,将其离散为均匀点阵,形成的三角网格,形状规则,排列有序,便于三角网格的快速检索。
同理,工件的下表面由于也存在着加工的可能性(如通孔的加工),将工件的下边面采用上表面同样的方法进行离散,对于工件的侧面,采用四边形网格的方法,原因是,实际加工中用四边形网格和三角形网格在表示工件侧面上具有同等的精度,并且四边形网格的数量比三角形网格要少的多。
机械加工中的材料去除率研究

机械加工中的材料去除率研究机械加工是制造工业中常见的一项工艺,它实现了对材料的去除和形状加工。
其中,材料去除率是衡量机械加工效率的重要指标之一。
本文将从材料去除率的定义和计算方法入手,探讨机械加工中影响材料去除率的因素,以及一些提高材料去除率的策略。
一、材料去除率的定义和计算方法材料去除率是指在一定时间内材料的质量损失,通常用单位时间内去除的材料质量来表示。
它可以反映机械加工效率的高低,影响加工成本和产能。
计算材料去除率的方法有多种,其中常用的是根据机械加工前后工件的重量差来计算。
例如,若加工前后工件的重量差为Δm,加工时间为Δt,则材料去除率R 可以表示为R=Δm/Δt。
二、影响材料去除率的因素1. 切削速度切削速度是指刀具在单位时间内与工件相对运动的速度。
它是影响材料去除率的重要因素之一。
一般来说,切削速度越大,材料去除率越高。
然而,过高的切削速度可能导致刀具磨损加剧和变形,影响加工质量。
2. 切削深度切削深度是指刀具在单次切削过程中进入工件的深度。
切削深度的增加会显著提高材料去除率,但也会增加机械振动、刀具磨损和切割力等问题。
因此,选择合适的切削深度对于提高材料去除率至关重要。
3. 进给速度进给速度是指工件在单位时间内相对于刀具的移动速度。
合理选择进给速度可以帮助控制材料去除率,太快的进给速度可能导致刀具过早磨损,太慢的进给速度则会影响加工效率。
4. 刀具材料和几何形状刀具的材料和几何形状对材料去除率有着重要影响。
硬度高、耐磨性好的刀具材料可以延长刀具的使用寿命,提高材料去除率。
而合理的刀具几何形状可以获得更好的切削效果,进而提高材料去除率。
5. 切削液切削液的使用对机械加工中的材料去除率也有一定影响。
切削液可以降低切削温度、减少切削力和磨损,从而提高材料去除率。
此外,切削液还可以冷却和润滑切削过程,保证加工质量。
三、提高材料去除率的策略1. 优化切削参数合理选择切削速度、切削深度和进给速度等切削参数,可以最大程度地提高材料去除率。
材料去除函数

材料去除函数材料去除是现代工业中一项非常基础的处理工艺,常常用于对工件表面进行修整或是改善其表面质量。
这项工艺就需要依靠材料去除函数来实现。
本文将着重介绍材料去除函数的相关知识。
材料去除函数是一个用来描述工具在扫描工件表面时所去除的材料量的函数。
它可以根据工具的运动状态、表面形貌以及材料物性等多种因素来计算并控制材料的去除量。
总的来说,材料去除函数不仅仅是一个简单的数学表达式,而是一个综合了多个学科知识的丰富模型。
下面是具体的步骤:第一步:工具选择首先需要根据材料的物性以及工件表面的硬度等特征来选定合适的工具。
一般情况下,以切削刃直接接触工件表面的切削工具和钻孔工具都是常用的材料去除工具,而且会根据工件表面的具体形态和曲率来选择不同的工具尺寸。
第二步:扫描函数设计接下来需要根据工件表面的形貌等条件来设计一个合理的扫描函数。
具体来说,扫描函数需要考虑工件表面的形状曲率、工具尖端的位置信息以及工具切削面的几何形状等因素。
不同的扫描函数会导致材料去除效果的差异。
第三步:数学模型建立在确定了扫描函数之后,需要根据材料的物性以及工具的运动状态等因素来建立一个完备的材料去除模型。
这个模型可以描述材料去除量与工具位置、运动速度和表面形态等相关关系。
一般情况下,材料去除模型都会采用复杂的数学公式和计算方法。
第四步:参数校正完成以上三个步骤之后,还需要进行一些实验验证和参数校正的工作。
这个过程可以帮助我们更准确地计算材料去除量,并且提高材料去除的质量。
具体来说,就是在模型的基础上根据实验数据对模型参数进行校正,以提高模型的精度和可靠性。
总结材料去除函数的设计和使用是一个基础而又复杂的工作。
需要我们在工具选择、扫描函数设计、数学模型建立和参数校正四个方面进行全面的考虑和实践。
只有这样,我们才能够成功地实现对工件表面的材料去除,满足现代工业对制造质量和效率不断提升的要求。
减材制造的原理和应用

减材制造的原理和应用1. 引言减材制造(Subtractive Manufacturing)是一种基于物质逐渐去除的制造工艺,通过将工件从初始块件中逐步去除物质来得到最终形状的产品。
本文将介绍减材制造的原理、技术和应用领域。
2. 原理减材制造的原理是通过机器工具或激光切割、铣削等加工方法,从初始块件中削减或去除材料,来实现最终产品的制造。
主要的原理包括:2.1 机器工具加工利用机器工具如铣床、车床等进行切削、打孔、铣削等加工工艺,去除多余材料,达到所需形状的目的。
2.2 激光切割采用激光束对工件进行烧蚀或熔化,然后通过气流或水流等方式将烧蚀的材料去除,从而实现产品的制造。
3. 技术减材制造涉及多种技术,以下是其中几种常见的技术:3.1 数控加工数控加工是一种自动控制技术,通过预先编程的指令,实现对加工设备进行精确控制,实现高精度的加工效果。
3.2 烧蚀加工利用激光束或电火花进行烧蚀加工,通过高温烧蚀或熔化工件表面的材料,然后通过气流或液流将烧蚀的材料去除,从而实现产品的制造。
3.3 数字化设计与建模利用计算机辅助设计(CAD)软件进行三维建模,将设计好的产品模型输入到减材制造设备中进行加工。
4. 应用领域减材制造技术在各个领域都有广泛的应用,以下是几个常见的应用领域:4.1 航空航天航空航天领域对产品的轻量化和高精度要求较高,减材制造技术能够满足这些需求,因此在航空航天领域得到广泛应用。
4.2 汽车制造汽车制造中,减材制造技术可以用于制造复杂的汽车零部件,例如引擎缸体、制动器等。
4.3 医疗领域减材制造技术在医疗领域有广泛的应用,例如制造人工关节、植入物等。
4.4 工业制造减材制造技术可以用于制造各种工业机械设备的零部件,例如齿轮、减速器等。
5. 优势和挑战减材制造技术有以下优势:•高度灵活性:可以制造复杂形状的产品,满足多样化的需求。
•资源节约:减少了材料的浪费。
•精度高:可以制造高精度的产品。
- 1、下载文档前请自行甄别文档内容的完整性,平台不提供额外的编辑、内容补充、找答案等附加服务。
- 2、"仅部分预览"的文档,不可在线预览部分如存在完整性等问题,可反馈申请退款(可完整预览的文档不适用该条件!)。
- 3、如文档侵犯您的权益,请联系客服反馈,我们会尽快为您处理(人工客服工作时间:9:00-18:30)。
一种工件材料去除仿真的方法
作者:陈阁
来源:《无线互联科技》2014年第10期
摘要:机床加工中,工件材料去除仿真有着广泛的应用,它对于检测G代码的正确性,减少工件试切带来的成本,提高加工的性能,降低能耗以及保护环境都有十分重要的意义。
本文以三轴铣床加工为列,介绍了本人在工作中,使用的一种工件去除的仿真方法。
关键词:数控加工;仿真;实体模型;计算机图形学
随着计算机技术和信息技术的发展,虚拟制造技术在传统加工制造业中得到了广泛应用,它以虚拟现实和仿真技术为基础,对产品的设计、生产过程统一建模,在计算机上实现产品从设计、加工、装配以及检验等整个生命周期的模拟和仿真。
工件材料去除仿真是虚拟制造的重要组成部分,利用计算机图形学技术对已编制的NC (Numerical Control,数字控制,简称数控)程序进行模拟演示。
开发功能完备、实用性强的虚拟数控加工模拟系统是当前加工制造业急需解决的问题。
三维图形模拟可以用来检验NC程序的正确性和合理性,大大降低了以往的试切等方法带来的高消耗,并保证整个加工过程中的安全。
加工安全分为加工前,加工中和加工后的安全,工件材料去除仿真的模拟属于加工前的安全。
1 铣床工件模型
本文采用基于物体空间的离散法建立工件的数学模型,其基本思想是:首先,按精度将工件表面离散为一系列的三角形网格;然后,判断工件表面三角面片顶点是否与刀具扫掠面相交,并根据刀具扫掠面修改各三角片顶点值,其中重点是根据刀具路径计算刀具扫掠面;最后,对三角网格进行真实感渲染。
基于三角网格的物体空间离散法己经比较成熟,并且也已经被成功应用于数控仿真的实现中。
具体来说,本文假定毛胚(待加工工件)为长方体,将毛坯的6个面分别进行离散。
上表面是待加工表面,是毛坯离散化的关键,将其离散为均匀点阵,形成的三角网格,形状规则,排列有序,便于三角网格的快速检索。
同理,工件的下表面由于也存在着加工的可能性(如通孔的加工),将工件的下边面采用上表面同样的方法进行离散,对于工件的侧面,采用四边形网格的方法,原因是,实际加工中用四边形网格和三角形网格在表示工件侧面上具有同等的精度,并且四边形网格的数量比三角形网格要少的多。
在毛坯离散化的过程中,离散精度(网格节点密度)的选择,影响着毛坯的显示质量。
但是精度提高,又必然会影响效率,仿真的效率和精度两者互相制约,为此需要根据仿真具体情况(毛坯大小、加工工艺)寻找一个合适的值。
为了简化计算,同时根据实际使用中的经验,
本文采用将工件离散为边长1mm的正方形网格,再将正方形网格分为两个相等的三角形,图1为50×50的网格,用于工件上、下表面的离散。
2 算法实现
整个算法分为工件模型初始化,切除运算和模型绘制三个部分实现,以下是具体描述。
2.1 初始化工作
包括工件模型的初始化和刀具模型初始化,工件模型的初始化,按照本文第一部分的方法建立工件的数学模型,将毛坯表面离散为密度合适的均匀网格节点;对于刀具模型,由于刀具模型在加工过程中,形状没有改变,因此采用简单的几何体进行描述。
2.2 工件切除运算
机床数控系统对NC代码进行插补处理,在程序起点和终点之间进行数据点的密化,最终得到的刀具运动轨迹均为连一系列连续的微小直线段,如图2中的线段。
图中球头刀沿着轨迹移动,设轨迹的起点和终点坐标分别为。
球头刀沿刀位轨迹移动所扫掠过的立体空间称为刀具扫描体;刀具扫掠面就是刀具表面在空间运动过程中形成的包络面;刀具扫掠域就是刀具移动时刀具扫掠面在平面的投影。
为了简化计算,首先将刀具一次运动生成的扫掠面投影到平面,这样可以快速找到此次刀具运动切除工件模型的范围,只对该区域进行计算,减少了计算量。
判断毛坯表面节点是否被加工,首先要判断毛坯节点是否位于刀具扫掠域中。
如图2所示,图中矩形为刀具扫掠域包围的矩形,为在平面内的投影,刀具扫掠域分为三个部分,起始和终止部分为半圆形,中间矩形部分。
:
包围矩形是指能包围扫掠域的最小矩形。
采用两步判别网格点,第一步是粗判,判断网格点是否落在扫掠域的包围矩形中;如果网格点落在扫掠域的包围矩形中,则进一步判断网格点与扫掠域之间的关系,从而确定网格点是否被切除,这样可以大大减少计算量,提高判断效率。
首先判断网格点是否位于刀具扫掠域包围矩形中,刀具扫掠域包围矩形的数学表达式为(的取值范围,其中为刀具半径):
只有位于刀具扫掠域包围矩形内的网格点才进一步判断它是否位于刀具扫掠域中。
刀具运动方向为:
则刀具扫掠域数学表达式为:
循环遍历工件上包围矩形内的离散网格点,判断每一个节点与刀具扫掠域的关系。
如果网格点位于刀具扫掠域中,则对该点做继续判断。
铣削加工中材料去除的过程就是毛坯网格点数据修改的过程,即工件上离散网格点的向坐标值根据刀具扫掠面改变的过程。
本文实现了三种刀具(球头刀、立铣刀和环形刀)的切除运算。
下面以球头刀为例,介绍刀具扫掠面的方程。
图2中球头刀扫掠面是一个空间规则的曲面,分为三部分,其中起始部分和终止部分均为球面,中间部分为一个半径为的半圆柱面。
假设为刀具扫掠面上任意一点,点位于起始部分满足方程:
点位于终止部分时满足方程:
刀具扫掠面中间圆柱面满足方程:
在一次刀具运动过程中,循环遍历工件上切除区域内的每一个离的点,根据工件上的点在刀具扫掠面在平面投影的位置的不同,采用不同的方程,解出值,该值即为刀具本次切除后工件上表面在该点的值,从而确定在某一时刻,工件模型的状态。
2.3 模型绘制
有了工件模型的三维模型数据,就可以对数据进行渲染,由于数控系统是运行在linux系统下,因此采用OpenGL图形库对数据模型进行渲染,将网格数据转化为三角片,调用OpenGL绘制函数进行绘制。
为了增强显示效果,本文使用了OpenGL自带的光照模型,启用光照后,需要计算工件模型切除后的每个三角片的法线值,否则工件切除后,根本看不出工件是否被切除。
因此在工件切除过程中,除了要修改每个被切除离散点的Z值外,还要修改与该离散点相关的三角片的法线值。
以球头刀切除算法为例,被切除离散点的法线方向分为起始部分,中间部分和终止部分,其中,起始部分和终止部分离散点的法线方向指向刀具扫掠面的球面的球心,中间部分离散点的法线方向指向球心运动的线段。
3 算法优化
采用上述算法,对刀具运动以及工件做切除运算,并集成到数控系统中,发现整个运算占用很高的系统资源,特别是CPU的使用率很高,在一次进行大量的切除运算时,会有模拟卡住的现象。
为了降低CPU的使用率,并增加仿真的流畅性,需要对仿真算法进行优化。
本文以绘制模型的优化为例,介绍本人工作中使用的优化方法,经过分析CPU使用率较高的情
况,发现主要瓶颈在绘制模型的复杂性上,因此,简化绘制模型是首选的方法,也是本文采用的方法。
在实际的加工中,很多离散网格(其中包括公面且三角片的法向量相等的网格)可以合并为一个网格,合并网格后,减少了三角片的数量,对于工件的复杂部分,仍然使用较多的三角片绘制,网格合并效果见图3。
这样处理,很大程度上减少了CPU的使用,提高了仿真系统的流畅性。
采用简单合并网格的方法,仿真效率提高了,但是出现了新的问题,就是在某些视角下,相邻网格间会有隐隐约约的虚线,影响了显示效果,对于这个问题,发现是某些离散点位于三角片的边上,也就是不是所有的离散点都只位于三角片的顶点上(如图4中间红色的顶点)。
对于这个问题,需要修正这样的点,方法是增加一个网格,如图5所示,这样所有的顶点都在三角片的顶点上,没有顶点在三角片的边上。
经过优化,显示效果得到了较好的改善,加工后的工件模型显示效果如图6所示。
4 总结
本文介绍了一种工件切除的实时仿真方法,本文介绍的内容是本人在工作工使用的方法,由于涉及到保密问题,本文只是粗略的讲解了理论方面的知识,没有写核心问题的解决方法和相关代码细节的实现。
[参考文献]
[1]王占礼.面向虚拟制造的数控加工仿真技术研究.吉林大学.2007.
[2]周静.数控仿真三维建模与系统实现.南京理工大学.2005.
[3]张新宇.基于网格的三维造型和处理技术研究.浙江大学.2004.
[4]马志艳.面向数控加工仿真的增强现实关键技术研究.华中科技大学.2007.
[5]张岩.曲面三角网格表示的数据结构优化研究.大连理工大学.2006.。