包装时,如何防止漏装
包装漏装改善方案
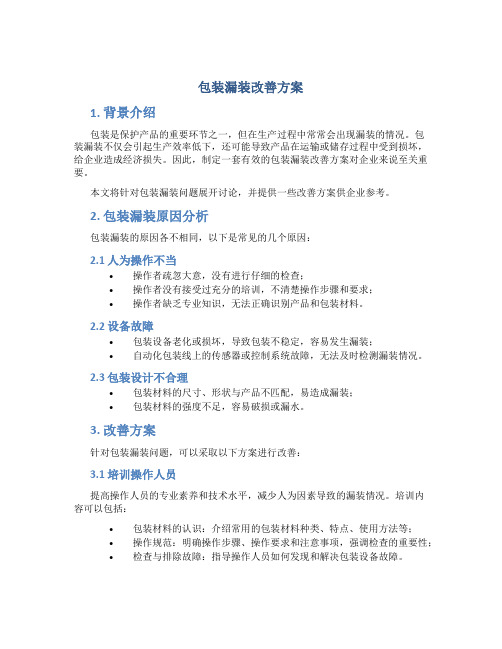
包装漏装改善方案1. 背景介绍包装是保护产品的重要环节之一,但在生产过程中常常会出现漏装的情况。
包装漏装不仅会引起生产效率低下,还可能导致产品在运输或储存过程中受到损坏,给企业造成经济损失。
因此,制定一套有效的包装漏装改善方案对企业来说至关重要。
本文将针对包装漏装问题展开讨论,并提供一些改善方案供企业参考。
2. 包装漏装原因分析包装漏装的原因各不相同,以下是常见的几个原因:2.1 人为操作不当•操作者疏忽大意,没有进行仔细的检查;•操作者没有接受过充分的培训,不清楚操作步骤和要求;•操作者缺乏专业知识,无法正确识别产品和包装材料。
2.2 设备故障•包装设备老化或损坏,导致包装不稳定,容易发生漏装;•自动化包装线上的传感器或控制系统故障,无法及时检测漏装情况。
2.3 包装设计不合理•包装材料的尺寸、形状与产品不匹配,易造成漏装;•包装材料的强度不足,容易破损或漏水。
3. 改善方案针对包装漏装问题,可以采取以下方案进行改善:3.1 培训操作人员提高操作人员的专业素养和技术水平,减少人为因素导致的漏装情况。
培训内容可以包括:•包装材料的认识:介绍常用的包装材料种类、特点、使用方法等;•操作规范:明确操作步骤、操作要求和注意事项,强调检查的重要性;•检查与排除故障:指导操作人员如何发现和解决包装设备故障。
3.2 更新包装设备购置新的包装设备,并对设备进行定期检修和维护,确保包装设备的稳定性和可靠性。
在购买新设备时,建议考虑以下因素:•自动化程度:新设备应具备高度自动化的功能,能够快速、准确地完成包装过程;•检测功能:新设备应配备漏装检测传感器,能够及时发现漏装情况并报警;•适用性:根据企业产品的特点选择合适的包装设备,确保包装效果良好。
3.3 优化包装设计重新评估包装材料的选择和设计,确保其与产品的匹配性和可靠性。
具体改善措施如下:•包装材料的选择:选择合适的包装材料,考虑材料的强度、耐磨性和防水性等因素;•尺寸设计:根据产品的尺寸和形状,合理设计包装材料的尺寸,避免漏装;•测试验证:在使用新的包装设计之前,进行充分的测试和验证,确保其稳定性和可靠性。
包装时,如何能防止漏装
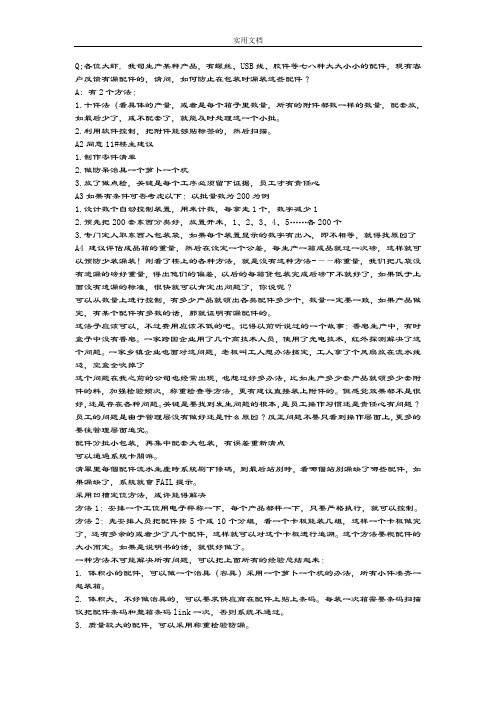
Q;各位大虾, 我司生产某种产品,有螺丝、USB线、胶件等七八种大大小小的配件,现有客户反馈有漏配件的,请问,如何防止在包装时漏装这些配件?A: 有2个方法:1.十件法(看具体的产量,或者是每个箱子里数量,所有的附件都数一样的数量,配套放,如最后少了,或不配套了,就能及时处理这一个小批。
2.利用软件控制,把附件能够贴标签的,然后扫描。
A2同意11#楼主建议1.制作零件清单2.做防呆治具一个萝卜一个坑3.放了做点检,关键是每个工序必须留下证据,员工才有责任心A3如果有条件可否考虑以下:以批量数为200为例1.设计数个自动控制装置,用来计数,每拿走1个,数字减少12.预先把200套东西分类好,放置开来,1、2、3、4、5 (200)3.专门定人取东西入包装袋,如果每个装置显示的数字有出入,即不相等,就得找原因了A4建议评估成品箱的重量,然后在设定一个公差,每生产一箱成品就过一次磅,这样就可以预防少装漏装!刚看了楼上的各种方法,就是没有这种方法-——称重量,我们把几袋没有遗漏的磅好重量,得出他们的偏差,以后的每箱货包装完成后磅下不就好了,如果低于上面没有遗漏的标准,很快就可以肯定出问题了,你说呢?可以从数量上进行控制,有多少产品就领出各类配件多少个,数量一定要一致,如果产品做完,有某个配件有多数的话,那就证明有漏配件的。
这法子应该可以,不过费用应该不低的吧。
记得以前听说过的一个故事:香皂生产中,有时盒子中没有香皂。
一家跨国企业用了几个高技术人员,使用了光电技术,红外探测解决了这个问题。
一家乡镇企业也面对这问题,老板叫工人想办法搞定,工人拿了个风扇放在流水线边,空盒全吹掉了这个问题在我之前的公司也经常出现,也想过好多办法,比如生产多少套产品就领多少套附件的料,加强检验频次,称重检查等方法,更有建议直接装上附件的。
但感觉效果都不是很好,还是存在各种问题。
关键是要找到发生问题的根本,是员工操作习惯还是责任心有问题?员工的问题是由于管理层没有做好还是什么原因?反正问题不要只看到操作层面上,更多的要往管理层面追究。
包装漏装改善方案

包装漏装改善方案包装是产品的“外衣”,不仅可以保护产品,还可以提高产品的附加值,增加产品的吸引力。
然而,在生产和运输过程中,由于各种原因,包装漏装问题时有发生。
如何改善和防止包装漏装问题,提升产品质量和客户满意度,成为企业亟待解决的难题。
一、定期检查包装设备和工艺流程包装漏装的原因可能是机械故障、操作不当、工艺流程问题等。
因此,企业需要根据实际情况,制定定期检查包装设备和工艺流程的计划,并督促相关人员认真执行。
定期检查可以发现和解决问题的根源,及时修复设备故障,改进工艺流程,确保包装的正常进行。
二、制定严格的质量控制标准为防止包装漏装问题的发生,企业需要制定严格的质量控制标准。
这包括从原材料选用、工艺流程控制、人员培训等方面进行规范化管理。
选用质量可靠的原材料,控制生产过程的每个环节,严禁使用过期包装材料,提高操作人员的技术水平和操作规范,从源头上预防包装漏装问题。
三、优化包装设计包装设计是防止漏装问题的重要环节。
首先,要选择适合产品的包装材料,确保材料的质量和可靠性。
其次,要合理设计包装结构,确保包装的稳固性和密封性。
在产品需要选用密封性较高的包装材料时,要注意包装的开口、封口、边角处的处理,避免漏装问题的发生。
此外,对于易碎、敏感产品,可以采用多层包装,增加保护层,提高包装的安全性和可靠性。
四、建立便捷的问题反馈机制五、加强员工培训和意识教育员工是企业的重要资源,他们的素质和技能直接影响到产品质量和工作效率。
为了防止包装漏装问题的发生,企业需要加强员工培训和意识教育。
通过内部培训、外部培训等渠道,提高员工的包装知识和专业技能,让他们具备良好的包装意识,避免因操作不当而导致的包装漏装问题。
此外,定期组织员工进行包装漏装案例分析和经验交流,利用集体智慧解决包装漏装问题,推动包装工作的质量持续改进。
总之,包装漏装问题的发生对企业形象和产品质量造成很大影响。
通过定期检查包装设备和工艺流程、制定严格的质量控制标准、优化包装设计、建立便捷的问题反馈机制和加强员工培训和意识教育等措施,可以有效预防和解决包装漏装问题,提升产品质量和客户满意度。
包装时,如何能防止漏装

Q;各位大虾, 我司生产某种产品,有螺丝、USB线、胶件等七八种大大小小的配件,现有客户反馈有漏配件的,请问,如何防止在包装时漏装这些配件?A: 有2个方法:1.十件法(看具体的产量,或者是每个箱子里数量,所有的附件都数一样的数量,配套放,如最后少了,或不配套了,就能及时处理这一个小批。
2.利用软件控制,把附件能够贴标签的,然后扫描。
A2同意11#楼主建议1.制作零件清单2.做防呆治具一个萝卜一个坑3.放了做点检,关键是每个工序必须留下证据,员工才有责任心A3如果有条件可否考虑以下:以批量数为200为例1.设计数个自动控制装置,用来计数,每拿走1个,数字减少12.预先把200套东西分类好,放置开来,1、2、3、4、5 (200)3.专门定人取东西入包装袋,如果每个装置显示的数字有出入,即不相等,就得找原因了A4建议评估成品箱的重量,然后在设定一个公差,每生产一箱成品就过一次磅,这样就可以预防少装漏装!刚看了楼上的各种方法,就是没有这种方法-——称重量,我们把几袋没有遗漏的磅好重量,得出他们的偏差,以后的每箱货包装完成后磅下不就好了,如果低于上面没有遗漏的标准,很快就可以肯定出问题了,你说呢?可以从数量上进行控制,有多少产品就领出各类配件多少个,数量一定要一致,如果产品做完,有某个配件有多数的话,那就证明有漏配件的。
这法子应该可以,不过费用应该不低的吧。
记得以前听说过的一个故事:香皂生产中,有时盒子中没有香皂。
一家跨国企业用了几个高技术人员,使用了光电技术,红外探测解决了这个问题。
一家乡镇企业也面对这问题,老板叫工人想办法搞定,工人拿了个风扇放在流水线边,空盒全吹掉了这个问题在我之前的公司也经常出现,也想过好多办法,比如生产多少套产品就领多少套附件的料,加强检验频次,称重检查等方法,更有建议直接装上附件的。
但感觉效果都不是很好,还是存在各种问题。
关键是要找到发生问题的根本,是员工操作习惯还是责任心有问题?员工的问题是由于管理层没有做好还是什么原因?反正问题不要只看到操作层面上,更多的要往管理层面追究。
肥料瓶装包装防漏液的方法

肥料瓶装包装防漏液的方法
肥料瓶装包装防漏液的方法有以下几种:
1. 使用密封性能好的瓶盖或塞子,确保瓶口紧密封闭,防止液体泄漏。
可以选择带有橡胶垫片的瓶盖或塞子,以增强密封性。
2. 在瓶盖或塞子上添加密封胶。
可以使用适合于肥料液体的密封胶或密封胶带,在瓶盖与瓶口之间形成有效的密封层,防止液体流出。
3. 使用包装袋或保鲜膜进行二次封装。
在将瓶盖或塞子密封后,可以将整个瓶子用塑料袋或保鲜膜包裹起来,再用胶带进行固定,以增强防漏效果。
4. 考虑使用防漏瓶装包装。
市场上有专门用于液体产品的防漏瓶装包装,其瓶盖或塞子具有更好的密封性能,可以有效防止液体泄漏。
5. 缓冲包装材料。
在瓶子外部添加一定的缓冲包装材料,如泡沫、气泡膜等,既可以增强包装的防震性能,又可以起到一定程度的防漏作用。
需要注意的是,不同类型的肥料液体可能对包装材料有不同的要求,需要根据具体情况选择合适的包装方法来防止液体泄漏。
同时,在包装后要进行必要的检查,确保防漏措施有效。
包装错漏方案
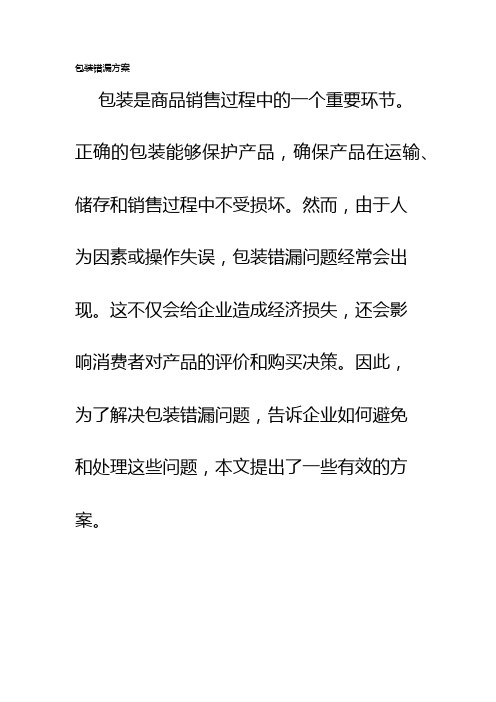
包装错漏方案包装是商品销售过程中的一个重要环节。
正确的包装能够保护产品,确保产品在运输、储存和销售过程中不受损坏。
然而,由于人为因素或操作失误,包装错漏问题经常会出现。
这不仅会给企业造成经济损失,还会影响消费者对产品的评价和购买决策。
因此,为了解决包装错漏问题,告诉企业如何避免和处理这些问题,本文提出了一些有效的方案。
第一,建立严格的品质控制体系。
包装错漏问题往往是由于生产过程中的疏忽或工人操作不当引起的。
因此,建立一个完善的品质控制体系非常重要。
这包括制定明确的包装标准、培训工人正确操作、加强检查和抽样等。
通过建立这样的体系,可以提高包装过程的准确性和可靠性,减少错漏问题的发生。
第二,采用自动化包装设备。
自动化包装设备具有高效、精确的特点,可以大大降低人为因素引起的包装错漏问题。
例如,自动化包装机器可以在运输和包装的过程中自动完成标签粘贴、装箱等操作,不仅提高了包装的质量和效率,还减少了人工操作的风险。
企业可以考虑引入这样的设备来解决包装错漏问题。
第三,加强与包装供应商的合作。
包装错漏问题有时是由于包装供应商的问题引起的。
为了避免这种情况的发生,企业应该与包装供应商建立良好的合作关系,共同制定包装标准和流程,并加强对包装供应商的管理和监督。
同时,可以与包装供应商进行定期沟通,了解他们的包装流程和设备状况,及时解决潜在的包装错漏问题。
第四,加强员工培训和意识培养。
员工是包装过程中最重要的因素之一,他们的操作水平和责任心直接影响到包装的准确性和质量。
因此,企业应该定期进行员工培训,提高他们的包装技能和质量意识。
通过培训和教育,让员工明白包装错漏问题对企业和消费者的影响,激发他们对包装质量的重视和责任感。
第五,建立快速反应机制。
尽管有了严格的品质控制体系和自动化设备,但包装错漏问题仍然可能发生。
因此,建立一个快速反应机制非常重要。
企业应该建立一个专门的团队负责处理包装错漏问题,并制定相应的处理流程和措施。
防错漏装作业方法
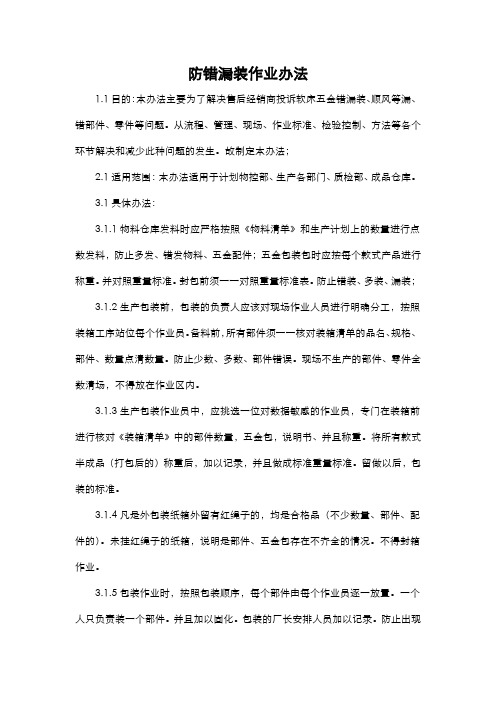
防错漏装作业办法1.1目的:本办法主要为了解决售后经销商投诉软床五金错漏装、顺风等漏、错部件、零件等问题。
从流程、管理、现场、作业标准、检验控制、方法等各个环节解决和减少此种问题的发生。
故制定本办法;2.1适用范围:本办法适用于计划物控部、生产各部门、质检部、成品仓库。
3.1具体办法:3.1.1 物料仓库发料时应严格按照《物料清单》和生产计划上的数量进行点数发料,防止多发、错发物料、五金配件;五金包装包时应按每个款式产品进行称重。
并对照重量标准。
封包前须一一对照重量标准表。
防止错装、多装、漏装;3.1.2 生产包装前,包装的负责人应该对现场作业人员进行明确分工,按照装箱工序站位每个作业员。
备料前,所有部件须一一核对装箱清单的品名、规格、部件、数量点清数量。
防止少数、多数、部件错误。
现场不生产的部件、零件全数清场,不得放在作业区内。
3.1.3 生产包装作业员中,应挑选一位对数据敏感的作业员,专门在装箱前进行核对《装箱清单》中的部件数量,五金包,说明书、并且称重。
将所有款式半成品(打包后的)称重后,加以记录,并且做成标准重量标准。
留做以后,包装的标准。
3.1.4 凡是外包装纸箱外留有红绳子的,均是合格品(不少数量、部件、配件的)。
未挂红绳子的纸箱,说明是部件、五金包存在不齐全的情况。
不得封箱作业。
3.1.5 包装作业时,按照包装顺序,每个部件由每个作业员逐一放置。
一个人只负责装一个部件。
并且加以固化。
包装的厂长安排人员加以记录。
防止出现错误后,无法追溯。
3.1.6 包装质检,在作业时。
待专门点数作业员点数完毕,封箱前,核对部件种类,部件正确性,五金包里五金数量和使用说明书,及其他标识。
进行抽查。
发现问题后。
将不良品加以隔离,并放在不合格区内。
任何员工不得擅自封箱,须待现场主管/厂长确认并补齐配件、零件后方可装箱。
3.1.7防顺风(发货床侧分左右,全发成左或右称为顺风):凡是软床的左右床侧、床头柜的上中下抽面、抽侧、抽后等产品有公母左右的。
错漏装改善措施

错漏装改善措施
错漏装是指在产品装配或包装过程中,出现错误或遗漏零部件或物品的情况。
以下是一些改善措施:
1.加强培训和教育:确保员工了解正确的装配和包装流程以及所需零部件或物品。
提供清晰的操作指南和培训材料,以减少人为错误。
2.建立质量控制体系:实施严格的质量控制措施,包括在装配和包装过程中进行检查和验证。
可以采用抽检、全检或使用自动化检测设备来确保准确性。
3.优化流程和设计:审查装配和包装流程,寻找可能导致错漏装的瓶颈或繁琐步骤。
通过简化流程、改进设计或引入防错装置来减少错误的发生。
4.使用标识和标签:为零部件和物品提供清晰的标识和标签,以便员工能够轻松识别和正确装配。
确保标签的准确性和可读性。
5.实施目视化管理:采用目视化管理工具,如看板、流程图和颜色编码,以增强对装配和包装过程的可视性和理解。
6.引入自动化技术:考虑使用自动化设备或技术来执行装配和包装任务。
自动化可以提高准确性、效率,并减少人为错误。
7.建立追溯系统:建立追溯系统,以便能够快速追踪和调查错漏装问题的根本原因。
这有助于及时采取纠正措施,并防止类似问题再次发生。
8.团队合作和沟通:鼓励团队成员之间的沟通和协作,以确保信息共享和问题及时解决。
建立开放的反馈机制,让员工能够报告潜在的问题或提出改进建议。
9.定期审查和改进:定期审查错漏装问题的发生情况,并采取持续改进的措施。
分析数据、收集反馈,以识别趋势和潜在的改进机会。
通过综合实施这些改善措施,可以有效减少错漏装的发生,提高产品质量和客户满意度。
包装和运输方式及保护措施

包装和运输方式及保护措施包装和运输是产品运输流程中非常重要的环节,能够确保产品在运输过程中不受损坏,并保持其质量和完整性。
在进行包装和选择运输方式时,需要考虑到产品的性质、尺寸、重量和运输距离等因素。
同时,还需要采取相应的保护措施,以确保产品在运输过程中的安全。
首先,包装是产品保护的第一道防线。
合理的包装可以保护产品免受外力、湿度、温度和震动等因素的影响。
针对不同类型的产品,可以采用不同的包装材料和方式。
例如,对于易碎的产品,可以使用泡沫箱或泡沫填充物来包装,以缓冲外力对产品的冲击;对于液体产品,可以使用密封的塑料瓶或桶进行包装,以防止泄漏;对于易受潮的产品,可以使用防潮袋或防潮剂进行包装,以防止潮湿。
此外,在包装过程中,可以加入适当的填充物,如泡沫、气泡膜和纸箱等,以防止产品在运输过程中晃动和碰撞。
其次,选择适当的运输方式也至关重要。
根据产品的性质和运输距离,可以选择陆运、铁运、航运或空运等不同的运输方式。
对于国内运输,陆运是常用的方式,可以采用汽车、火车或邮轮等交通工具进行运输;对于国际运输,航运和空运是常见的方式,可以选择船运、航空货运等。
在选择运输方式时,需要考虑到产品的重量、体积和安全要求,并选择合适的运输工具和舱位。
同时,还需要考虑到运输时间和成本等因素。
总之,包装和运输是产品运输流程中不可或缺的环节,对产品的保护和质量有着重要的影响。
通过采用合理的包装材料和方式,选择适当的运输方式,并采取额外的保护措施,可以有效地保护产品,确保其在运输过程中的安全和完整性。
同时,还需要注意运输人员的操作和仓储条件等因素,以确保产品的最终交付。
包装工安全操作规程

包装工安全操作规程
一、在规定区域内打包或摆放产品,随时保持通道畅通。
二、严格按产品质量要求打包,做到无错装、漏装,无包装松,包装数量要准确。
严禁将不
合格品同正品混包。
三、个人打好包的产品按同一品种,统一高度整齐叠放在中转区以便记数。
四、打包用的胶袋、草绳、封口胶放在规定的工装夹具内,不能乱扔。
五、包装过程中捡出的不良品集中放到废品车上,不滞留包装现场。
六、包装完毕自觉整理好尾数并打好包装。
清理包装现场,打扫地板。
成品输液包装安全防护措施

成品输液包装安全防护措施成品输液包装是一种用于存储和输送药物的容器,其安全防护措施至关重要。
正确的防护措施可以保证药物的质量和安全,同时也能够保护医务人员和患者的健康。
下面将介绍一些常见的成品输液包装安全防护措施。
首先,成品输液包装应该具备防漏性能。
输液包装在设计和制造过程中应该严格控制材料的质量,确保容器不会发生渗漏或破损。
这可以通过使用高质量的塑料和密封性能强的接口来实现。
此外,输液包装的开口处应该配备密封膜或保护帽,以防止污染和泄漏。
其次,成品输液包装应该具备防污染性能。
输液包装在生产过程中应该在无菌条件下进行,确保包装内部没有任何微生物污染。
同时,输液包装的外部应该配备防污染层,以防止外界的细菌和其他有害物质进入包装内部。
此外,输液包装的外包装应该具备抗菌和防水性能,以确保药物在运输和储存过程中不会受到污染。
第三,成品输液包装应该具备防光性能。
一些药物在受到光照的情况下会发生质量变化或失效,因此输液包装应该具备防光的能力。
这可以通过使用不透光的材料或涂层来实现。
此外,在储存和输送过程中,输液包装应尽量避免长时间暴露在阳光下,以防止药物的质量受到影响。
第四,成品输液包装应该具备耐压性能。
在输液过程中,包装容器需要承受一定的压力,因此输液包装应该具备足够的耐压能力。
这可以通过使用坚固的材料和加强包装结构来实现。
同时,输液包装应该经过严格的压力测试,确保能够承受输液过程中的压力变化,防止包装破裂或破损。
最后,正确的使用和处理成品输液包装也是安全防护的关键。
医务人员在使用成品输液包装之前应仔细检查包装的完整性和有效期,确保药物的质量和安全。
在使用过程中,应严格遵守操作规程,注意包装的保持和保护,避免包装受到损坏或污染。
在使用完成后,使用过的成品输液包装应该正确处理,以防止二次感染或其他安全隐患。
综上所述,成品输液包装的安全防护措施是保证药物质量和患者健康的重要环节。
正确的防护措施包括防漏性能、防污染性能、防光性能和耐压性能。
包装时,如何防止漏装

Q;各位大虾, 我司生产某种产品,有螺丝、USB线、胶件等七八种大大小小的配件,现有客户反馈有漏配件的,请问,如何防止在包装时漏装这些配件?A: 有2个方法:1.十件法(看具体的产量,或者是每个箱子里数量,所有的附件都数一样的数量,配套放,如最后少了,或不配套了,就能及时处理这一个小批。
2.利用软件控制,把附件能够贴标签的,然后扫描。
A2同意11#楼主建议1.制作零件清单2.做防呆治具一个萝卜一个坑3.放了做点检,关键是每个工序必须留下证据,员工才有责任心A3如果有条件可否考虑以下:以批量数为200为例1.设计数个自动控制装置,用来计数,每拿走1个,数字减少12.预先把200套东西分类好,放置开来,1、2、3、4、5 (200)3.专门定人取东西入包装袋,如果每个装置显示的数字有出入,即不相等,就得找原因了A4建议评估成品箱的重量,然后在设定一个公差,每生产一箱成品就过一次磅,这样就可以预防少装漏装!刚看了楼上的各种方法,就是没有这种方法-——称重量,我们把几袋没有遗漏的磅好重量,得出他们的偏差,以后的每箱货包装完成后磅下不就好了,如果低于上面没有遗漏的标准,很快就可以肯定出问题了,你说呢?可以从数量上进行控制,有多少产品就领出各类配件多少个,数量一定要一致,如果产品做完,有某个配件有多数的话,那就证明有漏配件的。
这法子应该可以,不过费用应该不低的吧。
记得以前听说过的一个故事:香皂生产中,有时盒子中没有香皂。
一家跨国企业用了几个高技术人员,使用了光电技术,红外探测解决了这个问题。
一家乡镇企业也面对这问题,老板叫工人想办法搞定,工人拿了个风扇放在流水线边,空盒全吹掉了这个问题在我之前的公司也经常出现,也想过好多办法,比如生产多少套产品就领多少套附件的料,加强检验频次,称重检查等方法,更有建议直接装上附件的。
但感觉效果都不是很好,还是存在各种问题。
关键是要找到发生问题的根本,是员工操作习惯还是责任心有问题?员工的问题是由于管理层没有做好还是什么原因?反正问题不要只看到操作层面上,更多的要往管理层面追究。
错漏装分析报告

错漏装分析报告引言本文将针对错误和遗漏的包装进行分析,并提供解决方案以减少这些问题的发生。
包装在产品销售中起着至关重要的作用,因为它不仅保护产品免受损坏,还提供了产品的识别和品牌价值的传递。
然而,错误和遗漏的包装可能会导致产品质量问题、客户投诉以及品牌形象受损等负面影响。
步骤一:制定包装规范首先,为了减少错误和遗漏的包装,制定详细的包装规范是至关重要的。
包装规范应包括以下几个方面:1.包装材料:选择适当的包装材料,确保其质量和耐久性,以防止在运输和储存过程中发生损坏。
2.包装设计:设计各个包装部件,如盒子、袋子、瓶子等,以确保产品适合包装,并能够保持其形状和完整性。
3.标识和说明:在包装上清晰地标识产品的名称、规格、使用说明和警示信息等,以便消费者正确使用产品,并提供相关的安全和法律信息。
步骤二:实施质量控制在包装过程中实施严格的质量控制是减少错误和遗漏的关键。
以下是几个关键步骤:1.检查包装材料:在使用包装材料之前,进行质量检查以确保其符合规范。
检查材料的外观、质地和强度等特征。
2.装配检查:在产品装配过程中进行检查,确保包装部件正确安装并紧固。
这包括验证标签、说明书等是否正确粘贴或放置。
3.检查包装完整性:在包装完成后,检查包装的完整性,确保没有破损、漏封或松动的包装。
步骤三:培训员工员工的培训对于减少错误和遗漏的包装至关重要。
以下是一些建议:1.包装规范培训:向员工提供关于包装规范的详细培训,确保他们了解正确的包装方法和要求。
2.质量控制培训:培训员工如何进行质量控制步骤,包括检查包装材料、装配检查和包装完整性检查等。
3.意识培训:提高员工对正确包装的重要性的意识,以及错误和遗漏包装对公司和客户的负面影响。
步骤四:建立反馈机制建立有效的反馈机制可以帮助及时发现和解决错误和遗漏包装的问题。
以下是一些建议:1.投诉管理:建立客户投诉管理系统,确保能够及时响应和处理与错误和遗漏包装相关的投诉。
2.内部反馈:鼓励员工积极报告和分享他们发现的错误和遗漏包装问题,以便及时进行纠正。
包装漏放物料改善方案

关于包装漏放/多放物料问题改善方案1:目的
杜绝包装组漏放、多放物料问题。
2:适用范围
泰博数码包装线。
3:职责权限
3.1 生产拉长负责安排人员进行加工和检验。
3.2 配料人员负责将订单物料依据投料单进行分配包装。
3.3检验人员(PQC)负责对配好物料的种类和数量100%进行检验。
4:参考文件
4.1投料单。
5:工作过程
5.1 生产线长对所要生产的物料依据投料单提供到产线配料人员。
5.2 配料人员依据投料单描述对物料进行分配包装。
5.3 包装OK物料传递到检验人员(PQC)工位进行100%全检。
6:检验人员(PQC)检验内容
6.1 依据投料单描述检验物料是否正确。
6.2 对物料种类进行清点。
6.3 对物料数量进行清点。
7:检验人员(PQC)检验方法
7.1 物料的种类和数量与投料单描述进行核对。
7.2 检验人员以口述方式进行核对物料种类和数量。
7.2.1 例如该产品共有6种物料,检验物料时要翻看物料,口中默念1、2、3、4、5、6,数量正确后方可流入下一工序。
空运货物的安全包装和防盗技术

空运货物的安全包装和防盗技术在现代物流运输中,空运已经成为一种快捷高效的货物运输方式。
然而,由于空运过程中存在一定的风险,特别是货物可能被盗或受损的风险,我们需要采取一系列的安全包装和防盗技术来保护货物的安全。
本文将讨论空运货物的安全包装和防盗技术。
一、货物包装的安全性要求在进行空运货物包装时,我们需考虑到以下几个方面的安全性要求:1. 货物保护:包装必须能够有效地保护货物,避免在运输过程中受到损坏或丢失。
2. 内部固定:包装必须能够确保货物在包装箱或包裹内部固定,避免在空运中发生移位或碰撞。
3. 适应性:包装必须根据货物的性质和尺寸进行合理设计,确保包装充分适应货物的特点。
4. 耐压性和耐冲击性:包装必须具备足够的耐压和耐冲击能力,以防止磕碰导致货物损坏。
二、安全包装的选择当选择安全包装时,我们应根据货物的性质和运输环境的特点,选择合适的包装材料和方法。
1. 箱体包装:使用强度高、耐压、耐冲击的纤维板制作的包装箱,可以提供良好的保护,适用于大型货物的包装。
2. 包裹包装:使用耐压、耐撕裂、防水的塑料袋或薄膜包装,可适用于小型货物的包装。
3. 内垫材料:在箱体或包裹包装中,应根据货物的形状和材质选择合适的内垫材料,如海绵垫、气泡垫等,以保持货物的稳定性。
4. 封装材料:采用高强度胶带或塑料封口带,确保包装的完整性,防止在运输过程中被拆包。
5. 标识标签:在包装上粘贴标识标签,详细注明货物的名称、重量、尺寸和警示信息等,以便于识别和管理。
三、防盗技术的应用除了安全包装,采用适当的防盗技术也是保护空运货物安全的重要措施。
1. GPS定位器:在货物中安装GPS定位器,可以实时追踪货物的位置,及时掌握货物的动态,有效防止货物丢失。
2. 封条:在包装箱或包裹上使用防伪封条,一旦封条被破坏,就可以发现货物被盗或被擅自拆封的情况。
3. 密封包装:使用无法轻易打开的密封包装,如密封袋、防水袋等,阻止盗贼在未被察觉的情况下窃取货物。
货物包装常见问题及解决办法

无锡市隆荣物流有限公司- 常熟物流公司, 靖江运输公司, 江阴货运公司, 常熟货运公司,
货物包装常见问题及解决办法
货物包装中常见的问题:
一、包装时应密封好,液体胶状物运输时因摇晃易飞溅、渗漏。
再用胶带加固,包装盒外多加一层包装,同时在包装内添加填充物减少碰撞。
二、纸箱多次重复使用,破旧不耐用。
因此在包装的过程中需要避免使用不具保护力的纸箱,及时更换新的包装箱。
三、不根据货物的种类和属性来包装,而是采取统一的包装,以致货物在运输的过程中发生破损、潮湿等。
此时需要注意:
1、必需在外加上有纤维袋包装,服装等软性货物和小五金等货物除用纸箱包装之外。
有防水功能最佳。
2、包装时应密封好,液体胶状物运输时因摇晃易飞溅、渗漏。
再用胶带加固,包装盒外多加一层包装,同时在包装内添加填充物减少碰撞。
3、除用普通纸箱包装外,贵重品、精密产品、易碎品、流质品、机械零件、仪器、金属制品、高比重物品以及散落容易丢失的物品等。
必需添加木架包装,加固又防挤压,保证货物平安。
4、因体积太小,小件货物零散包装。
容易导致丢失,通常使用纤袋包装。
5、未采用木架包装的较重货物必需用打包带加固。
6、小件电子产品在包装过程中需要添加防震填充物,减少碰撞。
- 1、下载文档前请自行甄别文档内容的完整性,平台不提供额外的编辑、内容补充、找答案等附加服务。
- 2、"仅部分预览"的文档,不可在线预览部分如存在完整性等问题,可反馈申请退款(可完整预览的文档不适用该条件!)。
- 3、如文档侵犯您的权益,请联系客服反馈,我们会尽快为您处理(人工客服工作时间:9:00-18:30)。
Q;各位大虾, 我司生产某种产品,有螺丝、USB线、胶件等七八种大大小小的配件,现有客户反馈有漏配件的,请问,如何防止在包装时漏装这些配件?A: 有2个方法:1.十件法(看具体的产量,或者是每个箱子里数量,所有的附件都数一样的数量,配套放,如最后少了,或不配套了,就能及时处理这一个小批。
2.利用软件控制,把附件能够贴标签的,然后扫描。
A2同意11#楼主建议1.制作零件清单2.做防呆治具一个萝卜一个坑3.放了做点检,关键是每个工序必须留下证据,员工才有责任心A3如果有条件可否考虑以下:以批量数为200为例1.设计数个自动控制装置,用来计数,每拿走1个,数字减少12.预先把200套东西分类好,放置开来,1、2、3、4、5 (200)3.专门定人取东西入包装袋,如果每个装置显示的数字有出入,即不相等,就得找原因了A4建议评估成品箱的重量,然后在设定一个公差,每生产一箱成品就过一次磅,这样就可以预防少装漏装!刚看了楼上的各种方法,就是没有这种方法-——称重量,我们把几袋没有遗漏的磅好重量,得出他们的偏差,以后的每箱货包装完成后磅下不就好了,如果低于上面没有遗漏的标准,很快就可以肯定出问题了,你说呢?可以从数量上进行控制,有多少产品就领出各类配件多少个,数量一定要一致,如果产品做完,有某个配件有多数的话,那就证明有漏配件的。
这法子应该可以,不过费用应该不低的吧。
记得以前听说过的一个故事:香皂生产中,有时盒子中没有香皂。
一家跨国企业用了几个高技术人员,使用了光电技术,红外探测解决了这个问题。
一家乡镇企业也面对这问题,老板叫工人想办法搞定,工人拿了个风扇放在流水线边,空盒全吹掉了这个问题在我之前的公司也经常出现,也想过好多办法,比如生产多少套产品就领多少套附件的料,加强检验频次,称重检查等方法,更有建议直接装上附件的。
但感觉效果都不是很好,还是存在各种问题。
关键是要找到发生问题的根本,是员工操作习惯还是责任心有问题?员工的问题是由于管理层没有做好还是什么原因?反正问题不要只看到操作层面上,更多的要往管理层面追究。
配件分批小包装,再集中配套大包装,有误差重新清点可以通過系統卡關嘛。
清單里每個配件流水生產時系統刷下條碼,到最后站別時,看哪個站別漏缺了哪些配件,如果漏缺了,系統就會FAIL提示。
采用凹槽定位方法,或许能得解决方法1:安排一个工位用电子秤称一下,每个产品都秤一下,只要严格执行,就可以控制。
方法2:先安排人员把配件按5个或10个分组,看一个卡板能装几组,这样一个卡板做完了,还有多余的或者少了几个配件,这样就可以对这个卡板进行追溯。
这个方法要视配件的大小而定。
如果是说明书的话,就很好做了。
一种方法不可能解决所有问题,可以把上面所有的经验总结起来:1. 体积小的配件,可以做一个治具(容具)采用一个萝卜一个坑的办法,所有小件凑齐一起装箱。
2. 体积大,不好做治具的,可以要求供应商在配件上贴上条码。
每装一次箱需要条码扫描仪把配件条码和整箱条码link一次,否则系统不通过。
3. 质量较大的配件,可以采用称重检验防漏。
介绍下我们曾用的的两种好方法:1.N点法;2.称重法,在电子秤上设定好产品重量范围(公差取成品中最轻的 ...这个方法好,很多公司都用这种方法控制的还是化繁为简,分工明确才行。
如果是配件包的方式,就把它当做一个制程来控制。
每天发料要控制好,一旦发现物料不一致,就说明有漏装现象。
我们打算导入成像检测系统来检测,现在也不知道效果会怎么样。
成本的话需要3W RMB 称重方法在此绝对行不通,即使你的电子秤再精密。
你以为只是装一个螺丝啊?其他配件的重量都有个误差范围,估计误差范围都远远大过那颗螺丝的重量了。
我们公司老板的要求是品质要靠设备保证,不是靠检验.此项目要是在我们公司,老板肯定要做一套自动分拣工装设备还有在衬板上按零件的模样开模,配件提前镶嵌在衬板中,也是一种防错的办法.我以前的要求是各种辅料是20件为一批,那样不容易出错,如有错误,即时就可发现,返工量会小点,包装好后,通过电子秤再秤重量(事先确定好重量的浮动标准),确保万无一实.双保险.呵呵.好多人回答哦,我們做惠普顯示器的,成品出貨時,說明書,保修卡,數據線,電源線,一堆東西,好多人說加強管理,那是屁話,作業員也不想犯錯,是人就會犯錯,流水線作業一人放一樣那也是屁話,是人就可能大意。
在流水線的末端設置稱重防呆,當然要設計的好一點,包裝想隨流水線通過時,沒有問題機器發出k!,如果有問題,就大叫NG,而且亮紅燈,這玩意是工務給安裝的,好用,稱的精度0.001kg.可以在过程的输送治具、包装的方式上着手:主要是POKAYOKE的应用。
比如螺丝的大小不一样,可以指定一个管道,只适合一种螺丝的尺寸流过,那么就起到放错的作用。
再比如,USB线/螺丝混得时候,可以在其通过的流水线路径上弄一块磁铁。
因为USB线一般是铜的,没有磁性。
而螺丝是铁的,则会被吸住。
还用,从尺寸高低着手,在流转路径上装红外线感应探头。
低于设定高度的,自然通过,包装即可。
高于设定高度的,流水线停止。
总之方法很多,看具体什么东西了。
我们是对批量不同的采取不同的方式:1. 小批量:点检就可以了。
2. 大批量:工序控制,刷barcord核对,做套板,结合称重就ok!称重法是比较好的一种方法,设置自动报警.我们现在用就是就样的方法.赞同16楼的方法:利用光电传感器。
记得本人从事的上一家公司生产汽车出风口,装配需要十几种零件,最后装配后放入检测工装,零件没有漏装的话,报警光显示为绿色,在贴上合格证,如果不是绿色那就要取下进行返工了。
当然以上是需要组装的情况,如果只是螺丝之类出厂的话,那可以将包装设计的小一点,包装好后过秤,在公差范围内则可在外包装上粘合格证等标记确认。
我们现在也存在这个漏装的问题,不过我们是装在胶袋里面,螺丝之类称重根本不可能,其实最好还是进行数量管理,像前面有位说的一样,先每种数100个或几十个,整套包装,最后如果有一种没有包完,那么前面的肯定是漏放了,不过都会影响效率。
先找专人把相关配件包装好,在最后一道工序是直接放入该配件就好,这样有专人专管,可以做到职权明确,应该可性.我们公司是采用复核制度,一个拼件员在包装上写好数量,数一遍零件放在包装箱旁,装箱人员装箱时再数一遍。
有专人不定期进行拆箱检我们公司就是这么做的、先把配套的相关材料各取100个、排好流水线、放一个批量的牌子、当100套装完以后先放下一个标示牌如果员工看到自己面前此时有剩余的零件、那么前面一百套肯定有短装、要是有零件不够也同样要全检之前100PCS、当厂线人员看到下一个批量的牌子时说明已经又流了100PCS下来!!!依此类推、一定要记得标示牌很重要!!!可以以每个时间段做为控制,之前我在一个温州人开的山寨手机厂干过几个月,经销商经常投诉有漏装附件、或者电池. 大家买山寨手机的时候留意一下,我们买的手机盒里有电池、充电器、USB连接线、耳塞、手机里面还有T卡等山寨手机经销流程如下:1.先从山寨手机加工厂出货至一级经销商(也就是某一品牌山寨手机老板),2.一级经销商要来工厂抽查或他们自己从代加工厂发货给全国各地的二级经销商.货发出后一些二级供应商投诉一级经销商说卖手机时有漏装T卡或电池等.大家知道三年前1G的T卡只少要30元一张,有是要40元.代加工的工厂老板也是温州佬,咆哮的冲我发飚要我想办法改善.我们开始想了很多办法来控制,包括称重,但是譬如像T卡漏装很难检查出来,因为T卡很轻.最后我们是以每个时间段来控制,首先物料员要全数点清电池、充电器、USB连接线、耳塞、T卡.再按配套发料,假如要出货100套,物料员就发料100套至产线包装.强调的是包装线必须是流水拉,每个员工要互检.包装过程中PQC巡检、技术员、管理员要在最后工序检查品质.到最后一个产品包完,组长要检查有无多或少装附件.如有该时间段包装产品全部返工.包完后在流程纸上记录时间、批号等,QC最后按批号抽检,如果抽检异常按时间段返工,不需要全数返工。
返工次数越多越出现新的问题.改善流程后由以前的每个月10件降为2件.说明书内要有装箱清单,封箱时和封箱后,相应的IPQC\FQC\OQC都要抽检。
有以下几种:1. 称重,比较适用流水线式生产。
2.设计包装,使包装中有对应品种的放置空间,哪个空间没放,说明漏装,适用自检及线检,比较直观。
3.作业方式改变,可把七八种东西由1个人装改为流水线式七八个人装,加强互检。
4.出货检验制订一定的抽检方案,持续实施。
防止漏装有很多方法,列举参考如下:1. 数量管理是基本原则,相互制约的部件只考虑对管理其中一种部件;2. 功能检测某些部件漏装,可以通过功能测试反映出来;3. 5S管理把无关的东西从现场移开,也是防漏的常规手段;4. 重量管理某些部件如果漏装了,重量会明显减少;5. 对比管理比高度、比重量、比颜色、比体积等也是发现漏装的一种方法6. 防错设计产品在设计阶段,考虑防错,如果装成别的部件,则放不下;7. 规则摆放将某一容易漏装的部件规则的摆放,如果某1个漏装,对比很快能发现错误;8.条码感应特别重要的部件,可以设置条码,通过扫描检验是否感应,确认是否漏装。
总之,不同的产品、部件,会有不同的方法。
首先看看是那个部分漏装的比率比较大采用流水线称重(精密电子)针对于比较中的配件如果是比较轻的,看是否采用配件模具,设计成一个拼盘,每个零件放在里面,检验的人只要发现某个格子是空的就可以判定NG将配件称重,以百或者订单数为单位,如果在最后尾数多了就说明漏装了。
或者个治具,用传感器:将每种物料放在一个盒子里,盒子口上装一个传感器(能计数的),作业指导书上规定好拿的顺序,然后要求员工执行,少拿了就报警,完工后对一下成品数个传感器计数是否一致。
要是舍不得花钱,就作业指导书上规定好拿的顺序,然后要求员工执行,后面有人复查首先,在加工线装一次作数量确认,加工完成后抽检一次,到成品线产线装入时发现附件少给予奖励,可提高员工积极性。
再是到成品抽检,4道关口任一关口出问题都能被检出来。
唯一的情况是4道关口同时出问题才有机会流入客户端。
这种机率大家想象行到吧1,定岗,定位,定量(6S要搞好)2,称重(小配件要搭配)单重要一致。
3,包装前编码,定量1.定岗定位,责任到人;2.设计放呆,一种物料一个空穴,将包装好的单个附件放置到单个的空穴内;3.完善作业指导,员工严格按照作业指导书的要求作业;4.内似的质量事故对全员做教育;5.质量处罚,对该工序的员工做相应的质量处罚;同感啊,以前也遇到同样的问题,设计了好几套方案:1. 点数法:批量大的时候很不适合,影响效率;2.称重法:可能行,但对于螺丝你就不好做了;3.工序法:每人放几样,但效果不好;4.Check list :钩钩划划,费影响效率;后来公司在包装上进行了修改:一个萝卜一个坑,效果不错。