lean manufacturing matrix
精益生产的管理方式【优质文档】

1.精益生产2.6SIGMA
1、何谓精益生产方式
Lean Production
精益生产
1960年代开始,以丰田为代表的日本汽车制造业通过实施JIT生产模式,以低成本、高质量的突出优势迅速占领美国汽车市场,引发了美日之间长达十年的汽车贸易战。 JIT——因其经营效率极限化被美国学者赞誉为“精益生产”,并对人类的生产革命产生了长远影响。
1、1978年开始质量管理小组的活动。2、QC小组累计注册数达1554个;3、为企业直接创造的经济效益达2546亿元。
QC小组在中国
群众性质量管理活动
质量管理小组的活动
干部参加劳动,工人参加管理;改革不合理的规章制度;领导干部、技术人员和工人群众三结合;
1、自检:操作者按照图样、标准、工艺、或作业指导书等文件中所规定的项目、频次的要求,对自己加工的工件进行检测。2、自分:操作者将自己加工的工件通过检测判断合格与不合格后,必须使之分别堆放。3、操作者将自己加工的合格品上打上标记。4、控制自检正确率:操作者控制自己检测的工件正确率,用以对“三自”活动的控制。
零库存
发现真正问题
大量库存造成成本高、周转困难,且看不到真正的问题在哪里
· 探求必要库存的原因 · 库存规模的合理使用 · 均衡化生产 · 设备流水化
零浪费
降低成本
“地下工厂”浪费严重,似乎无法发现、无法消除
· 整体能力协调 · 拉式生产彻底暴露问题 · 流程路线图
7个“零”目标
Lean生产模式年表
1890 - Sakichi Toyoda 获得了木制纺织的专利,由于市场竞争的压力及需要,改善 (KAIZEN) 这种哲学思想应运而生。“没有任何机器或生产流程是不可以被改善和提高的” - Sakichi Toyoda
Lean精益生产简介

Source: The Machine that Changed the World, Womack, Jones, and Roos, 1990.
© 2007 Superfactory™. All Rights Reserved. 4
Background and History
• • • • • • • • • • • • • 1574: King Henry III watches the Venice Arsenal produce finished galley ships every hour using continuous flow processes 1799: Whitney perfects the concept of interchangeable parts 1902: Sakichi Toyoda establishes the jidoka concept 1910: Ford moves into Highland Park, the “birthplace of lean manufacturing,” with continuous flow of parts 1911: Sakichi Toyoda visits the U.S. and see the Model T line for the first time 1938: JIT concept established at Toyota 1940: Consolidated Aircraft builds one B-24 bomber per day, witnessed by Ford’s Charles Sorensen, who later improves production to one B-24 per hour 1949: Taiichi Ohno promoted to shop manager at Toyota, develops “elimination of waste” concept 1951: Ohno refines TPS to include visual control, employee suggestions, TWI, batch size reduction, and kanban 1965: Toyota receives Deming Prize for Quality 1975: First English translations of TPS are drafted 1980-83: First books on TPS by American authors: Kanban and Zero Inventories 1990: Womack and Jones publish The Machine That Changed the World, becoming the definitive text creating the term “lean”, followed by Lean Thinking in 1996
精益制造 全英文.ppt

Value added 10 %
Non-value added
LEAN = ELIMINATING THE WASTES
• Overproduction • Defects (NG) • Non-value added
processing • Waiting • Excess motion • Transportation • Excess inventory • Underutilized
8
KEY CONCEPTS
• Waste Reduction • Lead Time Reduction • Variation Reduction • Product Flow • Pull of the Customer • Continuous Improvement
9
VALUE ADDED
Companies must apply the appropriate Lean principles for their industry and specific company situation.
• Something that a company does once.
Lean is NOT an end point; it is a never ending improvement process. Lean is a journey.
Shigeo Shingo
4
MANY NAMES, BUT THE SAME CONCEPT
Toyota Production System Just-In-Time
JIT/TQC/EI/TPM
One-Piece-Flow Cellular Manufacturing
精益术语 Lean Lexicon

精益术语 Lean Lexicon精益基本理念精益生产与精益公司1.Lean Production (精益生产)2.Lean Enterprise (精益企业)3.Lean Logistics (精益物流)4.Toyota Production System (丰田生产系统)5.Just-In-Time(JIT) (及时生产)增值与浪费6.Seven Wastes (七种浪费)7.Muda,Mura,Muri8.Value-Creating (增值)9.Non Value-Creating (非增值)精益改进识别价值10.Product Family Matrix (产品系列矩阵)11.Build-to-Order (按订单制造)12.Batch and Queue (批量生产)13.Demand Amplification (需求扩大)分析价值流价值流总体描述(逻辑关系)14.Spaghetti Chart (意大利面条图)15.Value Stream Mapping (价值流图)流程布局(实物——设备、物料及人)16.Process Village (加工群)时间分析(物料/设备)时间基本概念17.Value-Creating Time (增值时间)18.Non Value-Creating Time(非增值时间)19.Takt Time (节拍时间)周期时间20.Cycle Time (周期时间)21.Processing Time(加工时间)22.Machine Cycle Time(机器周期时间)23.Effective Machine Cycle Time(有效机器周期时间)24.Operator Cycle Time(操作员周期时间)Lead Time25.Production Lead Time (产品交付期)26.Order Lead Time(订单交付期)27.Order to Cash Time(订单到现金时间)库存库存基本概念28.Inventory (库存)29.Raw Materials(原材料)30.Work-in-Process(WIP)(在制品)31.Work-In-Process (在制品)32.Finished Goods(成品)标准库存33.Standard Inventory (标准库存)34.Buffer Stock (缓冲库存)35.Safety Stock(安全库存)36.Shipping Stock(装运库存)库存绩效指标37.Inventory Turns (库存周转率)设备38.Downtime (停工期)39.Changeover (换模)信息流40.信息流41.Production Control (生产控制)生产单元42.Cell (生产单元)效率43.Efficiency (效率)44.Apparent Efficiency(表面效率)与True Efficiency(真实效率)45.Total Efficiency(总效率)与Local Efficiency(局部效率)稳定价值流(生产单元[Cell]的主要参数)价值流设计46.Production Preparation Process(3P) (生产准备过程)47.Set-based Concurrent Engineering (多方案同步进行的开发工程)48.Design-In (共同设计)标准化作业(生产/作业单元)49.Work (工作)50.Standardized Work (标准化操作)51.Process Capacity Sheet(工序能力表)52.Standardized Work Combination Table(标准化操作组合表)53.Standardized Work Chart(标准化操作表)54.标准作业指导书(SOS)操作员55.Plan For Every Person (为每个人做培训计划)56.基本工序的分配方式物料57.Plan For Every Part(PFEP) (为每个产品做计划)设备58.Production Analysis Board (生产分析板)59.Total Productive Maintenance (TPM,全面生产维护)Autonomous(自主管理)60.Error-Proofing (预防差错)61.Jidoka (自动化)62.Andon (信号灯)63.Automatic Line Stop (自动停止生产线)64.Fixed-Position Stop System (固定工位来停止生产)65.Inspection (检查)现场组织66.5S67.Red Tagging (红标签)流动68.Continuous Flow (连续流)69.Flow Production (流水线生产)70.Kanban (看板)71.Pacemaker Process (定拍工序)72.A-B Control (A-B控制)73.Chaku-Chaku (一步接一步)拉动拉动基本模式74.Push Production (推动生产)75.Pull Production (拉动生产)76.Supermarket (库存超市)77.Supermarket Pull System (库存超市拉动系统)78.Fill-Up System (填补系统)79.Sequential Pull System (顺序拉动系统)80.First In, First Out (FIFO) (先进先出)81.Mixed Supermarket and Sequential Pull System(库存超市与顺序拉动混合系统)信息流(生产/作业指令)82.Pitch (单位制造时间)83.Every Product Every Interval (EPEx) (生产批次频率)均衡拉动(Level Pull)84.Heijunka (均衡化)85.Heijunka Box (生产均衡柜)bor Linearity (劳动力线性化)87.Capital Linearity (线性化的设备投资)88.right-sized tool (适度装备)89.Set-Up Reduction (减少转换时间)90.Single Minute Exchange of Die (10分钟内更换模具)追求完美精益仓库91.Cross-Dock (交叉货仓)92.物料传递员(W/S)精益物流93.Greenfield (新建工厂)精益变革基本理念94.乐于改变(Open mind to change)95.细微的改善意识96.员工参与(Employees participation)97.团队精神(Team work)98.尽管去做(Just do it)99.先创新后投资(Creativity before capital)领导100.Chief Engineer (总工程师)101.Change Agent (实施改变的领导者)组织实施102.Policy Deployment (政策实施)103.精益生产推进室(Kaizen promotion office)104.培训(Training)105.Kaizen Workshop (改善研习会)106.Gemba (现场)持续改进107.Kaizen (改善)108.Kaikaku (突破性改善)109.Plan, Do, Check, Act(PDCA) (计划,实施,检查,行动) 110.Four Ms (四M)111.Five Whys (五个“为什么”)112.A3 Report (A3报告)Labor Linearity (劳动力线性化)一种在生产工序(特别是一个生产单元)中,随着产量的变化灵活调动操作员人数的方法。
精益生产简介PPT课件

原料
成品
BATCH SIZE 周期时间
Transport Time Operation 3
Operation Time Operation 7
Rework Operation 4
Setup Operation 10
传统功能重点
工作站 (局部化) 效率
原料
操作 1
操作 2
操作 3
操作 4
成品
效率 产出 / 天
机器模型原型生产当应用补充拉系统时必须使用一般拉系统补充拉系统补充拉系统应与一般拉系统同时使用以使lead时间的变动最小从而满足发货时间的要求补充拉系统逐个部件地将需求和流程分析应用于原料战略性wip仅当需要时成品如需要的适当存货规模并与过程能力和市场需求相平衡补充拉系统在过程中建立战略性分布的部件缓冲量buffer原料通过buffer存货将供应过程与消费过程分离部件补充是根据消费与净需求的关系将来需求帮助确定buffer规模而非真实的提供原料补充循环特定部件数的拉系统循环是生产过程中的一个连续路径其中产品需求促进产品补充拉拉系统中的典型循环消费推动的生产正确产品正确数量正确时间受约束的过程存货规模部件短缺情况的减少存货减少最好是达到最小化战略性buffer战略性buffer生产线周期时间顾客预期补充信号购买指令补充信号销售指令消费消费生产线生产销售商计算补充拉系统的因素为了正确计算拉系统的规模应知道每个战略性补充循环中的每次部件中的以下数据
40.0% 35.0% 30.0% 25.0% 20.0%
Ap Ma Jun Jul Au Se Oc No De Jan Fe Ma
ry
g pt t v c
br
Operating Income % (3 Mo. Rolling)
lean精益生产术语中英文版

X 1/10 X½ X2 X½
X 1/10 X½
Goaபைடு நூலகம் : Add Value & Eliminate Waste … Relentlessly for Our Customers 目标: 减少浪费&创造价值 全心全意为客户服务
No Money 不投入更多金钱 No Space 不占用更多面积 No Manpower 不使用更多人力
Key Note from Sensei: 老师的重要提示: • To understand the above WIP definitions, go to The Genba and perform your own work towards Establishing the right WIP quantities. This is the Only way you can understand the definition. 要理解WIP定义,你需要去到现场在工作中实践正确的WIP数量。 这是让你理解这个定义的唯一方法。
Various types of WIP in our manufacturing process 生产过程中存在各种类型的WIP
1. 2. 3. 4. Standard WIP Process WIP 标准WIP 制程WIP 制程与制程间WIP
Process To Process WIP
Station To Station WIP工位与工位间WIP
9
What is Standard WIP 什么是标准WIP • WIP means INVENTORY. INVENTORY is Basically ‘bad’.
WIP就是库存。库存从根本上说是“不好”的。
Lean Manual

Introduction 手册介绍
The purpose of this manual is to provide a basic and complete knowledge and frame about Lean for all ESAB Sonia and Anita employees in order to have common sense on Lean, as well master some key tools application in their filed to improve business. 本手册目的是提供一个全面基本的精益知识与框架为Sonia与Anita的员工以便于他们可以 掌握基本的精益知识与拥有必要的了解. 特别是可以同时掌握一些核心工具的具体操作 来不断在自身业务部门改进工作 This manual includes some parts as below to systematically introduce Lean system and detailed implementation Part 1: introduce the lean program structure, key persons and relative skill need Part 2: introduce Lean concept & technique frame, as well implementation road Part 3: Introduce Lean tools applicable in various stage of whole implementation Part 4: introduce Lean tools Part 5 : introduce some key Lean tools concrete application in field 本手册包含了以下的一些章节来结构化描述精益系统的概念以及具体实施与应用 第一部分: 介绍精益项目的组织结构, 组成人员以及所需要技能 第二部分: 介绍精益的概念与技术结构, 还包括相应具体导入步骤与阶段 第三部分: 介绍在整个实施过程中的不同阶段所涉及到的方法学工具 第四部分: 介绍精益的应用工具基本内容与用途 第五部分: 介绍一些核心工具的具体实践应用方式
Lean术语
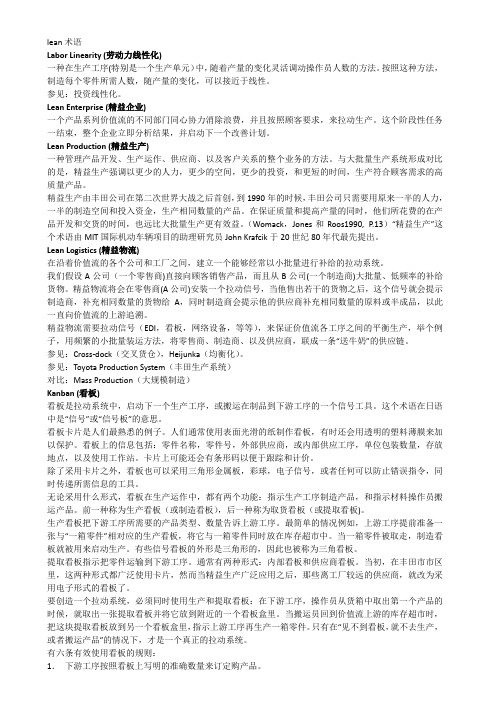
lean 术语Labor Linearity (劳动力线性化)一种在生产工序(特别是一个生产单元)中,随着产量的变化灵活调动操作员人数的方法。
按照这种方法,制造每个零件所需人数,随产量的变化,可以接近于线性。
参见:投资线性化。
Lean Enterprise (精益企业)一个产品系列价值流的不同部门同心协力消除浪费,并且按照顾客要求,来拉动生产。
这个阶段性任务一结束,整个企业立即分析结果,并启动下一个改善计划。
Lean Production (精益生产)一种管理产品开发、生产运作、供应商、以及客户关系的整个业务的方法。
与大批量生产系统形成对比的是,精益生产强调以更少的人力,更少的空间,更少的投资,和更短的时间,生产符合顾客需求的高质量产品。
精益生产由丰田公司在第二次世界大战之后首创,到1990年的时候,丰田公司只需要用原来一半的人力,一半的制造空间和投入资金,生产相同数量的产品。
在保证质量和提高产量的同时,他们所花费的在产品开发和交货的时间,也远比大批量生产更有效益。
(Womack,Jones和Roos1990, P.13)“精益生产”这个术语由MIT国际机动车辆项目的助理研究员John Krafcik于20世纪80年代最先提出。
Lean Logistics (精益物流)在沿着价值流的各个公司和工厂之间,建立一个能够经常以小批量进行补给的拉动系统。
我们假设A公司(一个零售商)直接向顾客销售产品,而且从B公司(一个制造商)大批量、低频率的补给货物。
精益物流将会在零售商(A公司)安装一个拉动信号,当他售出若干的货物之后,这个信号就会提示制造商,补充相同数量的货物给A,同时制造商会提示他的供应商补充相同数量的原料或半成品,以此一直向价值流的上游追溯。
精益物流需要拉动信号(EDI,看板,网络设备,等等),来保证价值流各工序之间的平衡生产,举个例子,用频繁的小批量装运方法,将零售商、制造商、以及供应商,联成一条“送牛奶”的供应链。
什么是lean精益生产

Traditional
process
VA
improvement
NVA NVA
Kaizen waste reduction
VA NVA
Original lead time
Minor improvement Major improvement
• Reducing value-added (VA) activities results in only minor gains • Reducing waste results in major lead time reductions
So… What’s Driving The Waste?
• Distance (plant layout) • Long set-up times • Incapable processes • Poor maintenance • Poor work methods • Lack of training • Adherence (or not) to
Don’ t make capital investments on improving VAs until the NVAs achieve equilibrium with the VAs
© 2003 Kaufman Global, LLC
11
Benefits of Lean
• The Benefits Are There For The Taking
If You Look To Technology To Save Us, We Will Be Caught From Behind, Overrun And Butchered By The Competition
© 2003 Kaufman Global, LLC
精益生产价值流图(英文版)

ENERGIZER SCHICK - HIGHLY CONFIDENTIAL - RESTRICTED FOR INTERNAL USE ONLY
4
Lean Elements
ENERGIZER SCHICK - HIGHLY CONFIDENTIAL - RESTRICTED FOR INTERNAL USE ONLY
本人刘彦1980年出生2003年毕业于兰州师范高等专科学校化学教育而后于2005年参加工作在甘肃省武威市凉州区洪祥镇陈家沟学校就职
Lean Manufacturing
Value Stream Mapping
ENERGIZER SCHICK - HIGHLY CONFIDENTIAL - RESTRICTED FOR INTERNAL USE ONLY
2
What is a Value Stream?
“All of the actions, value or non value added that are required to bring a product from concept to launch or from raw material order to delivery. . . ”
5
Value
• “What is the
willing to Pay for?”
• 3 Types of Customers:
The external end-user or paying customer
The downstream customer of any internal upstream process.
Cellular Manufacturing Rethink material storage Job/Task Combinations
Lean Manufacturing and Six Sigma

Lean Manufacturing and Six SigmaLean manufacturing and Six Sigma are two of the most popular methodologies used by businesses to improve their operations and increase efficiency. Both methodologies have their own unique approaches, but they share the same goal of reducing waste and improving quality. In this essay, we will explore the concepts of lean manufacturing and Six Sigma, their benefits, and how they can be implemented in a business.Lean manufacturing is a methodology that focuses on reducing waste and increasing efficiency in a business. The goal of lean manufacturing is to eliminate any activities that do not add value to the final product or service. This can include activities such as overproduction, waiting, excess inventory, unnecessary transportation, overprocessing, defects, and unused talent. By eliminating these wastes, businesses can reduce costs, improve quality, and increase customer satisfaction.Six Sigma, on the other hand, is a methodology that focuses on improving the quality of a product or service by reducing defects and variation. The goal of Six Sigma is to achieve a level of quality that meets or exceeds customer expectations. Six Sigma achieves this by using statistical tools and techniques to identify and eliminate the root causes of defects and reduce variation in processes. By reducing defects and variation, businesses can improve quality, reduce costs, and increase customer satisfaction.Both lean manufacturing and Six Sigma have numerous benefits for businesses. By reducing waste and increasing efficiency, lean manufacturing can help businesses save money and increase profitability. Lean manufacturing can also improve quality and customer satisfaction, which can lead to increased sales and customer loyalty. Six Sigma, on the other hand, can help businesses improve quality and reduce defects, which can lead to increased customer satisfaction and loyalty. Six Sigma can also reduce costs by eliminating the root causes of defects and reducing variation in processes.To implement lean manufacturing and Six Sigma in a business, businesses must first understand their current processes and identify areas for improvement. This can be done through process mapping, value stream mapping, and statistical analysis. Once areas forimprovement have been identified, businesses can then develop and implement strategies to reduce waste and improve quality. This can include implementing just-in-time inventory systems, improving process flow, and using statistical tools and techniques to identify and eliminate the root causes of defects.In conclusion, lean manufacturing and Six Sigma are two powerful methodologies that can help businesses improve their operations and increase efficiency. Both methodologies have their own unique approaches, but they share the same goal of reducing waste and improving quality. By implementing these methodologies, businesses can reduce costs, improve quality, and increase customer satisfaction. However, implementing these methodologies requires a thorough understanding of the business's current processes and a commitment to continuous improvement.。
Lean精益生产----06.VisMgmt可视化管理
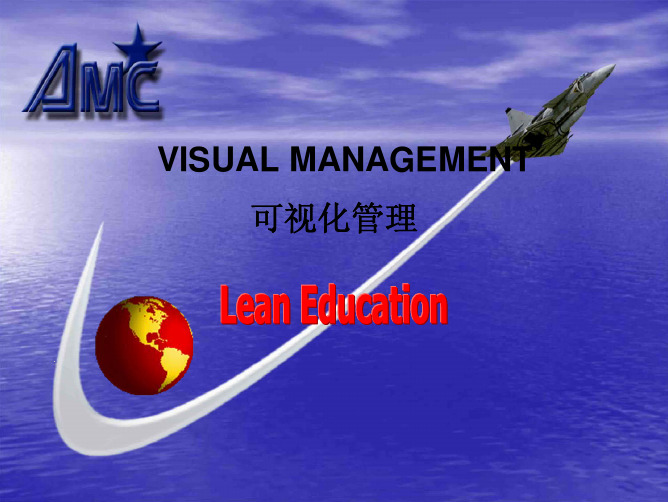
2003 Advanced Manufacturing Consultancy. All Rights reserved on printed material. No replication privileges extended
可视化管理 Visual Management
如果不告诉员工他们的努力怎样影响输出,不给权利和责任让他们去达 到他们的目标,精益生产的技术就会失去它所具有的能量。 精益工厂要求工人,经理,熟练技术雇员等对输出结果有影响的人员相 互协作。 The power of all the lean manufacturing techniques is lost without individuals motivated by work that keeps them informed about how their efforts affect the outcome and gives them the power and responsibility to reach their goals The lean factory requires a partnership among workers, managers, and skilled and technical staff in which the parties are responsible to each other for the outcome
LeanManufacturing资料精讲案例介绍
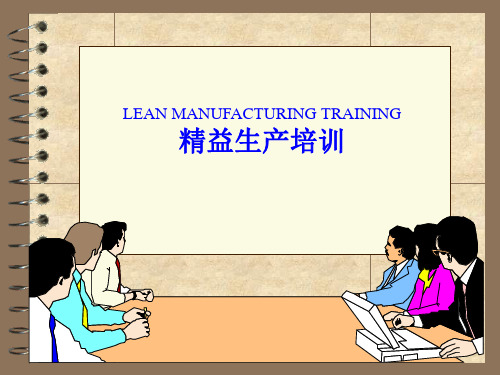
• Large batches of similar products
• Inflexible machinery
• Manufacture of goods by process
• 大批量少品种 • 工序式生产 • 设备大难组合
• Focused on total elimination of waste
The amount of human effort, time, space, tools, and inventories can typically be cut in half very quickly, and steady progress can be maintained from this point onward to cut inputs in half again within a few years.
1997 IWeek Survey of 2,900 manufacturers 1998 IWeek Survey of 2,100 additional manufacturers
Benchmark Results 定标结果
5年内生产周期时间的改进
60%
35
50% 55%的改进
30
40%
25
20
Lean -“精益”释义
精益:形容词 1: a:无肉或少肉, b:少脂肪或无脂肪 2: 不富裕 3: 在必要性,重要性,质量或成分方面稀缺 4: 文体或措词简练
同义词:薄,极瘦,过分瘦长,骨瘦如柴,瘦削的, 似 骨的,消瘦的,细长的,瘦长的
反义词: 肥胖的,多肉的,过重的,不结实的,过分 肥胖的,丰满的,粗短的,肥大的,软的
期被欧美企业纷纷采用。随着微利时代的来临, 精益生产模式成为企业竞争的有力武器
生产管理中的Lean制造
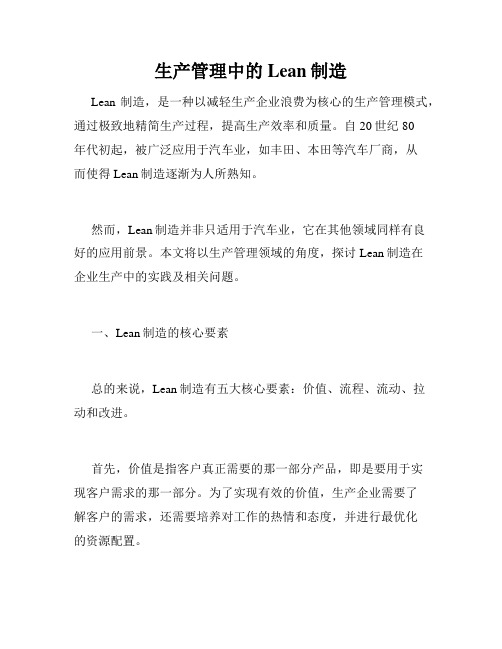
生产管理中的Lean制造Lean制造,是一种以减轻生产企业浪费为核心的生产管理模式,通过极致地精简生产过程,提高生产效率和质量。
自20世纪80年代初起,被广泛应用于汽车业,如丰田、本田等汽车厂商,从而使得Lean制造逐渐为人所熟知。
然而,Lean制造并非只适用于汽车业,它在其他领域同样有良好的应用前景。
本文将以生产管理领域的角度,探讨Lean制造在企业生产中的实践及相关问题。
一、Lean制造的核心要素总的来说,Lean制造有五大核心要素:价值、流程、流动、拉动和改进。
首先,价值是指客户真正需要的那一部分产品,即是要用于实现客户需求的那一部分。
为了实现有效的价值,生产企业需要了解客户的需求,还需要培养对工作的热情和态度,并进行最优化的资源配置。
其次,流程是指产品制造的整个流程,包括原材料采购、制造和销售等。
这个流程要具备能够使得产品制造顺利的条件,其中特别强调人工和智能技术的协作。
然后是流动,即使得产品制造流程顺畅和流畅。
充分利用分析、改进和优化技术,从而使得生产过程中不断优化并减少浪费。
在流动的过程中,还需要实施拉动生产的制度,以避免制造过程中的浪费产生。
这个制度基于实际市场需求,按需制造商品,避免不必要的产出,从而降低了生产成本,并提高了资源利用率。
最后,改进是一个不断重复的过程,对于任何一个企业,都需要不断调整和改进自己的生产模式。
在这样的一个过程中,需要运用各种考核和分析方法,并培养员工的积极性,同时还要加强员工沟通和合作,以实现提高生产效率和产品质量等目标。
二、Lean制造在生产管理中的实践Lean制造在生产管理中的实践,涉及到企业生产过程中的多方面问题,其中包括:1、精细化生产对于每一项生产任务,需要进行详细的规划,以免出现不必要的生产阻碍或工艺错误。
如此一来,企业才能够在生产过程中积极调整,以实现最佳化的生产效果,同时保持稳定的员工士气。
2、敏捷化生产敏捷化代表了能够快速响应客户的需求,并做出相应的生产调整的能力。
- 1、下载文档前请自行甄别文档内容的完整性,平台不提供额外的编辑、内容补充、找答案等附加服务。
- 2、"仅部分预览"的文档,不可在线预览部分如存在完整性等问题,可反馈申请退款(可完整预览的文档不适用该条件!)。
- 3、如文档侵犯您的权益,请联系客服反馈,我们会尽快为您处理(人工客服工作时间:9:00-18:30)。
DTD (Single Operation) = Total Units of Control Part End of line Rate DTD (Multiple Operation)= DTD(OP 1)+DTD(OP 2)+… End of line Rate
Total Dock To Dock Calculation (DTD)
Process with a sequenced 'batch of many' schedule
定义: 定义 BTS是指在指点的生产日按照正确的生产顺序完成生产计划的比例情况.BTS 反映了工厂能够按照客户的要求完成生产的能力,客户需何种产品,何时需要和客 户使用产品的顺序. BTS% = Volume% X Mix% X Sequence% Volume Performance: 产量性能用于监控生产计划完成情况. Mix Performance: BTS的混线性能用于测量在厂内制造的产品系/型号/类型等在适当的生产日的完 成比率. Sequence Performance: BTS的顺序性能用于测量在适当的生产日按照正确的生产顺序完成生产任务的比 率.
First Time Through Calculation (FTT)
单工序: 单工序: 进入数量 报废 返工 测试 下线修理 FTT% FTT% 多工序: 多工序: FTT (工序1) FTT (工序2) FTT (工序3) 最终检验(工序4) 总FTT% Total FTT% = = = = = 92.87% 87.65% 82.34% 82.34% 92.87% X 87.65% X 82.34% X 82.34% = 1000 = 10 = 15 = 5 = 0 = 1000 -(10+ 15+ 5+ 0) 1000 = 97.0%
Process with a sequenced 'batch of many' schedule
Build to Schedule (BTS)
Build to Schedule (BTS-1) FOCUS/COUGAR/JAGUAR CONDENSER
生产计划
批序号
实际生产
型号 数量 Cougar Focus Cougar Focus Cougar 批序号
1 2 3 4 5
200 100 200 150 160 810
1 2 N/A 4 3
型号 数量 Cougar Focus Jaguar Focus Cougar
190 40 60 300 100 690
Process with a sequenced 'batch of many' schedule
= %
Build to Schedule (BTS)
Definition: Build to schedule is the percentage of products shceduled for a given day that are produced on that day, in the correct sequence. BTS reflects the plant's ability to produce what it's customers want, when it's customers want it, and in the order the customers use the product. BTS% = Volume% X Mix% X Sequence% Volume Performance: Volume Performance, is the traditional measure that manufacturing has used to monitor their performance to schedule. Mix Performance: The Mix component of BTS measures the percentage of product derivatives/models/types that a plant builds on the right day. Sequence Performance: The sequence component of BTS measures the percentage of those products built on the right day that were also built in the right sequence.
=4.93小时 =2.98小时 =0.05小时 =0.05小时 =3.29小时 =11.3小时
Total DTD= 4.93+ 2.98+ 0.05+ 0.05+ 3.29
Overall Equipment Effectiveness (OEE)
Definition: OEE is a combination of three different calculations. It is a measure of the availability, performance efficiency, and quality rate of a given piece of equipment. OEE data will help identify several wastes caused by machine/process inefficiencies. Stretch objective: 85% 定义:OEE是三个不同计算值的乘积,用于测量指定设备的利用率,性能效率 和质量率.OEE 数据可以帮助识别由设备/过程不足引起的不同的浪费. 接受标准: 85% OEE Availability Performance Efficiency Quality = = = = Availability X Performance Efficiency X Quality Operation Time Net Available Time Ideal cycle time X Total parts run Operating Time Total parts run – Total defects Total parts run
= 44.22%
Total Dock To Dock Calculation (DTD)
Definition: Dock to Dock is the elapsed time between the unloading of raw materials and the release of finished goods for shipment. DTD measures how fast raw materials are converted to finished goods and shipped. It is a measure of the speed of material through the plant, not the speed of the processes. 定义: DTD指从原材料到发运产品之间的总运转时间间隔.DTD用于测量原材料转化 成成品发运的速度.也就是指材料通过工厂的速度,而不是加工工艺的速度.
Yes Yes N/A Yes No 3批
Process with a sequenced 'batch of many' schedule
Build to Schedule (BTS-1)
Volume Performance Mix Performance Sequence Performance Build to Schedule = 690 x 100 810 = 540 X 100 690 = 3 X 100 4 = 85.2% = = 78.3% 75.0%
Overall Equipment Effectiveness (OEE)
质量率: 质量率 总零件数 返工数 报废数 质量率 总设备利用率: 总设备利用率: 利用率 性能效率 质量率 总设备利用率 OEE = = = = 86.3% 83.4% 93.8% 86.3% X 83.4% X 93.8% = 1440 = 50 = 40 = 1440 – (50+ 40) = 93.8%
The End of Line Rate is calculated off the last operation in the manufacturing line for a product: 总产量 = 730 (最终工位) 生产时间 = 12小时 (正常生产时间10小时+加班时间2小时) End of Line Rate 各区域数量 原材料 工序1 工序2 工序3 最终产品 DTD(原材料) DTD (工序1) DTD (工序2) DTD (工序3) DTD (最终产品) = = = = = = = = = = = = 730/12 原材料+半成品+最终产品 300 181 3 3 200 300/60.83 181/60.83 3/60.83 3/60.83 200/60.83 =60.83
=85.2%X 78.3%X 75.0% = 50%
Process with a sequenced 'batch of many' schedule
Build to Schedule (BTS-2)
冲压 线 10 20 30 计划生产的零 计划产量 件和生产序号 A B C D E F 1000 2000 4000 1000 1000 1000 10000 实际生产 的零件序 号 A B C E D F 生产数量 混线生产 按序生产 数量 数量 1000 500 7000 1000 2000 0 11500 1000 500 4000 1000 1000 0 7500 1000 500 4000 1000 0 0 6500