铰孔工艺与编程
铰孔工艺

6.6 铰孔工艺、编程材料: 45#钢,正火处理图6-6-1圆周均布孔加工零件6.6.1 铰孔加工工艺1.铰孔加工概述钻孔是在实体材料中钻出一个孔,而铰孔是扩大一个已经存在的孔。
铰孔和钻孔、扩孔一样都是由刀具本身的尺寸来保证被加工孔的尺寸的,但铰孔的质量要高得多。
铰孔时,铰刀从工件孔壁上切除微量金属层,以提高其尺寸精度和减小其表面粗糙度值,铰孔是孔的精加工方法之一,常用作直径不很大、硬度不太高的工件孔的精加工,也可用于磨孔或研孔前的预加工。
机铰生产率高,劳动强度小,适宜于大批大量生产。
铰孔加工精度可达IT9~IT7级,表面粗糙度一般达Ra1.6~0.8μm。
这是由于铰孔所用的铰刀结构特殊,加工余量小,并用很低的切削速度工作的缘故。
直径在100 mm以内的孔可以采用铰孔,孔径大于100 mm时,多用精镗代替铰孔。
在镗床上铰孔时,孔的加工顺序一般为:钻(或扩)孔一镗孔一铰孔。
对于直径小于12 mm的孔,由于孔小镗孔非常困难,一般先用中心钻定位,然后钻孔、扩孔,最后铰孔,这样才能保证孔的直线度和同轴度。
如图6-6-1所示的工件,加工6×φ20H7均布孔,孔面有Ra1.6的表面质量要求,适合用铰孔方法进行孔的精加工。
一般来说,对于IT8级精度的孔,只要铰削一次就能达到要求;IT7级精度的孔应铰两次,先用小于孔径0.05~0.2 mm的铰刀粗铰一次,再用符合孔径公差的铰刀精铰一次;IT6级精度的孔则应铰削三次。
铰孔对于纠正孔的位置误差的能力很差,因此,孔的有关位置精度应由铰孔前的预加工工序予以保证,在铰削前孔的预加工,应先进行减少和消除位置误差。
如,对于同轴度和位置公差有较高要求的孔,首先使用中心钻或点钻加工,然后钻孔,接着是粗镗,最后才由铰刀完成加工。
另外铰孔前,孔的表面粗糙度应小于Ra3.2μm 。
铰孔操作需要使用冷却液,以得到较好的表面质量并在加工中帮助排屑。
切削中并不会产生大量的热,所以选用标准的冷却液即可。
铰孔加工中的工艺参数
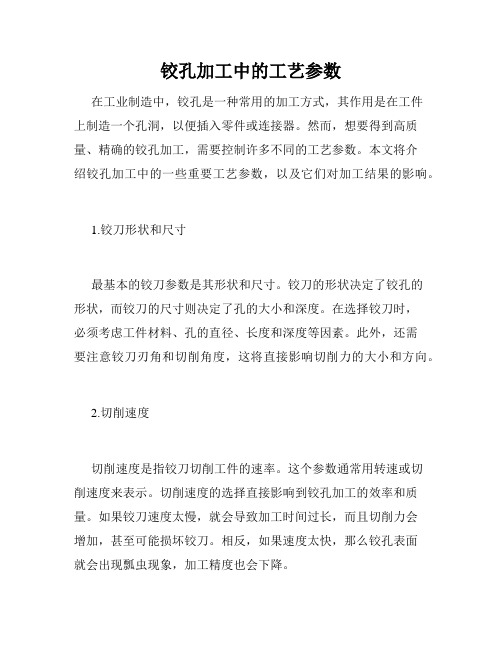
铰孔加工中的工艺参数在工业制造中,铰孔是一种常用的加工方式,其作用是在工件上制造一个孔洞,以便插入零件或连接器。
然而,想要得到高质量、精确的铰孔加工,需要控制许多不同的工艺参数。
本文将介绍铰孔加工中的一些重要工艺参数,以及它们对加工结果的影响。
1.铰刀形状和尺寸最基本的铰刀参数是其形状和尺寸。
铰刀的形状决定了铰孔的形状,而铰刀的尺寸则决定了孔的大小和深度。
在选择铰刀时,必须考虑工件材料、孔的直径、长度和深度等因素。
此外,还需要注意铰刀刃角和切削角度,这将直接影响切削力的大小和方向。
2.切削速度切削速度是指铰刀切削工件的速率。
这个参数通常用转速或切削速度来表示。
切削速度的选择直接影响到铰孔加工的效率和质量。
如果铰刀速度太慢,就会导致加工时间过长,而且切削力会增加,甚至可能损坏铰刀。
相反,如果速度太快,那么铰孔表面就会出现瓢虫现象,加工精度也会下降。
3.进给速度进给速度决定了铰刀在加工过程中每分钟进给的距离。
进给速度与切削速度一样重要,它对加工质量和效率都有影响。
如果进给速度太低,就会导致加工过程中铰孔表面不平滑,甚至出现切削刃痕。
另一方面,如果进给速度过高,则会导致铰刀磨损加速,加工过程中会产生过多的热量,甚至会损坏工件。
4.铰孔深度铰孔深度是铰孔加工的另一个重要参数。
在选择铰刀时,需要根据加工要求确定所需的孔深度,并确保铰孔的深度符合工程要求。
如果铰孔深度过浅,就会导致安装的零件不牢固,而深度过深则会加大工件成本和加工难度。
5.预冲长度预冲长度是指在实际切削铰孔之前,铰刀先在工件上移动的长度。
预冲长度的主要作用是使铰孔与工件表面完全接触,这有利于减少切削刃痕和杂散毛刺等不良现象。
预冲长度的选择应当依据工件材料、孔的直径和深度来确定,并参考铰刀的切削特性和工艺细节。
6.冷却液在铰孔加工过程中,冷却液的选择和使用也是至关重要的工艺参数。
冷却液通过冷却切削区域,降低加工温度,减少摩擦和磨损,并清洗切屑和切屑。
数控铣床铰孔
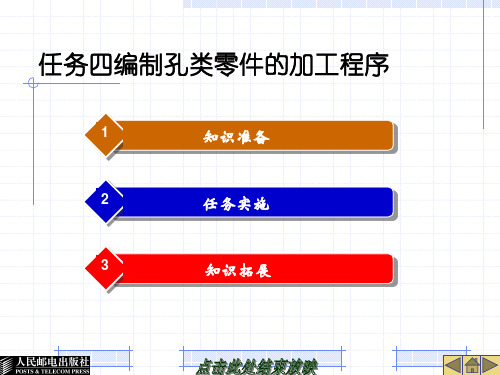
② 固定循环功能表
G指令 G73 G74 G76 G80 G81
G82 G83 G84 G85 G86 G87 G88 G89
加工动作Z向 间歇进给 切削进给 切削进给
切削进给
切削进给 间削进给 切削进给 切削进给 切削进给 切削进给 切削进给 切削进给
在孔底部的动作
主轴正转 主轴定向停止
间。
⑥ G80:取消固定循环;该指令能取消固定循环,同时R 点和Z点也被取消。
2.数控铣床钻孔循环指令编程与加工技能
(1)一般钻孔(中心孔)循环 指令编程与加工技能(G81)。 格式: G98(G99)G81 X_ Y_ Z_ R_ F_
(2)带停顿的钻孔循环编程与加工技能(G82)。 格式: G98(G99)G82 X_ Y_ Z_ R_ P_ F_ (3)高速深孔加工循环指令编程与加工技能(G73)。 格式: G98(G99)G73 X_ Y_ Z_ R_ Q_ K_ F_ L_(华中数控系 统) G98(G99)G73 X_ Y_ Z_ R_ Q_ F_ (FANUC数控系统) (4)深孔加工循环指令编程与加工技能(G83)。
任务四编制孔类零件的加工程序
1
知识准备
2
任务实施
3
知识拓展
一、准备知识
1.数控铣床固定循环指令编程的概述 (1)固定循环指令的含义。
数控加工中,某些加工动作循环已经典型化。例 如,钻孔、镗孔的动作是孔位平面定位、快速引进、工 作进给、快速退回等,这样一系列典型的加工动作已经 预先编好程序,存储在内存中,可用包含G代码的一个程 序段调用,从而简化编程工作。这种包含了典型动作循 环的G代码称为循环指令。
暂停
主轴反转
主轴停止 主轴停止 暂停、主轴停止
铰孔的工艺

铰孔的工艺铰孔是一种常用的加工工艺,用于制造零件的孔加工。
它是通过铰刀在工件上进行旋转运动,以削除工件上的金属材料,最终形成所需的孔形状和尺寸。
铰孔工艺主要包括以下几个方面:工具选择、加工参数、加工步骤和注意事项。
首先,工具选择是铰孔工艺中非常重要的一步。
常见的铰刀有手动铰刀、机械铰刀和数控铰刀。
手动铰刀适用于简单的孔加工,操作简单方便;机械铰刀适用于批量生产,能够提高工作效率;数控铰刀适用于复杂的孔加工,可以实现高精度的加工。
其次,加工参数也是铰孔工艺中需要注意的一个方面。
首先是转速,一般根据工件材料和孔径大小选择合适的转速,以保证加工效果和工具寿命。
其次是进给速度,进给速度过快容易造成毛刺和刀具损坏,进给速度过慢则会影响加工效率。
最后是切削深度,切削深度应根据工件的强度和刚度选取适当的值,以避免过大的切削力和振动。
加工步骤是铰孔工艺中需要严格按照规定执行的步骤。
首先是确定铰刀的位置和夹持工件。
工件应安装牢固,以免产生振动和偏差。
然后是设置加工参数,包括转速、进给速度和切削深度。
接下来是进行试切,通过试切来调整和校准加工参数,确定最佳的加工条件。
最后是正式加工,进行铰孔操作,及时清理切屑和冷却润滑。
最后,铰孔工艺中还需要注意一些事项。
首先是要选择合适的冷却润滑剂,以降低切削温度和减少刀具磨损。
其次是要保持切削刃的锋利度,定期检查和更换刀具,以保证加工质量。
另外,需要注意加工过程中的安全问题,采取必要的防护措施,避免事故发生。
总之,铰孔是一种常用的加工工艺,通过选择合适的工具、设置有效的加工参数、执行正确的加工步骤和注意事项,可以保证加工质量和效率。
同时,铰孔工艺也需要根据具体的情况进行调整和优化,以满足不同零件的加工需求。
数控机床操作与编程:十一 钻、铰孔(面)编程与加工
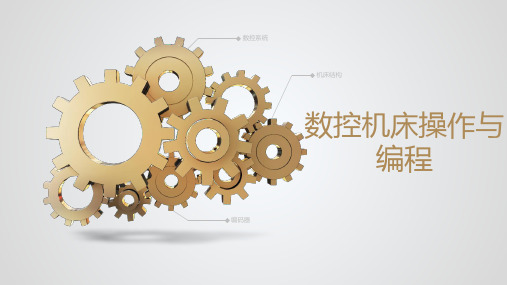
➢➢➢ ➢ ➢ ➢
掌数加掌对掌 理 掌 刀 掌 柱掌0(螺指功i握控工握刀握的握具握面M握G纹令能0利 程 ) 利 操a零能图及图数数切(进1te)用序及用作件力纸确纸控控削G行-T0、FF输实的图。要定要车D加循数0AA系单)NN入操能纸求工求削工环控UU统行、与加力并选件和加工指加CC提程S修工。00对择装道工艺令工功ii供螺MM改的尺数夹具工方(程能的aa纹、能寸控方情艺案序Gtt、ee直9切程力公加案况方--运编F2TT线功削)DD序。差工的合案用制数数插能指、检进车能理的与F控控A补、令快验行床力制能N修机机指MU(速(数、。订力改C床床功令G点模学车外。的S3记进能e定拟2处削圆r能)性行i和e位s、T
任务11.1 带孔座板零件工装选择、刀具选择 和加工工艺卡的制作
11.1.3零件加工工装、刀具和加工工艺卡
1.工装 采用机用虎钳装夹工件。先将机用虎钳安装在铣床工作台面中心上,然后找正、固定。根据工
件的高度情况,在钳口内放入形状合适和表面质量较好的垫铁后,再放入工件。工件的基准面朝下, 与垫铁面紧靠,然后拧紧钳口。机用虎钳外观及各主要组成部分如图10-11 所示。
11.3.2程序录入、程序轨迹检查及首件试切
新建带孔座板加工程序O0003的步骤如下: 编辑 → PROG →输入行输入: O0003 → INSERT →打开O0003程序编程界面。
打开程序O0003的步骤如下: 编辑 → PROG →输入行输入: O0003 → ↓ 或 [O检索] →打开O0003程序(屏幕右上角显示 O0003)。
11.1.2零件编程指令
1.孔加工固定循环指令编程格式 孔加工固定循环功能指令见表11-2。
任务11.1 带孔座板零件工装选择、刀具选择 和加工工艺卡的制作
加工中心铰孔的方法技巧

加工中心铰孔的方法技巧
加工中心铰孔是一种常用的加工方法,下面是一些常用的方法和技巧:
1. 选择合适的刀具:根据工件材料的硬度和形状,选择合适的铰刀。
通常使用硬质合金铰刀,能够提供更好的切削质量和寿命。
2. 铰孔前的工件准备:将工件固定在加工中心上,并确保工件表面光洁,并且没有任何杂质。
合适的刀具和夹具夹紧力度也要得当,以确保铰孔的精度和质量。
3. 铰刀进给量控制:通过合适的进给量控制,可以保证铰孔的质量和精度。
进给量太大可能导致刀具损坏或工件表面质量不佳,进给量太小则可能导致切削效率低下。
4. 切削速度控制:根据工件材料的硬度和形状,选择合适的切削速度。
切削速度过高可能导致刀具磨损过快,切削速度过低则可能导致铰孔质量不佳。
5. 切削润滑:使用适当的切削润滑剂可以降低刀具和工件的摩擦,提高切削质量和工具寿命。
选择合适的切削润滑剂并按照规定的用量进行涂抹。
6. 切削过程监控:在加工过程中,及时监控刀具和工件的状态,如果发现异常情况,及时进行调整或更换刀具。
7. 铰孔之后的后续工艺:铰孔完成后,可能需要进行清洁、测量和其他后续处理工艺。
根据具体情况进行相应的处理。
钻孔、铰孔、攻螺纹(钻孔循环指令)
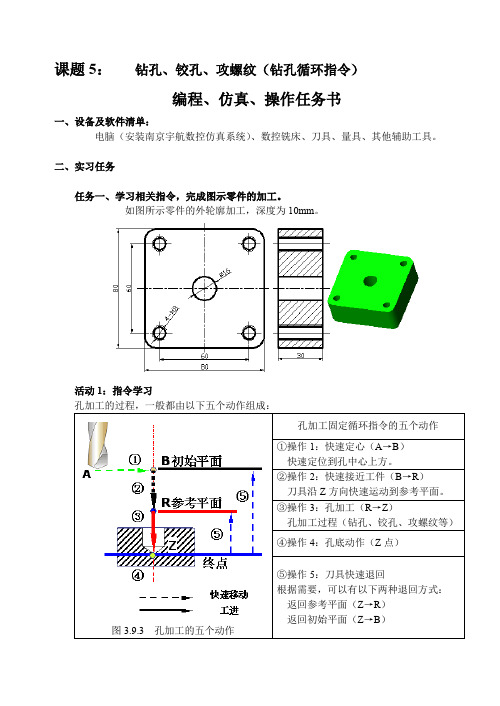
课题5:钻孔、铰孔、攻螺纹(钻孔循环指令)
编程、仿真、操作任务书
一、设备及软件清单:
电脑(安装南京宇航数控仿真系统)、数控铣床、刀具、量具、其他辅助工具。
二、实习任务
任务一、学习相关指令,完成图示零件的加工。
如图所示零件的外轮廓加工,深度为10mm。
活动1:指令学习
孔加工的过程,一般都由以下五个动作组成:
钻孔循环指令G81指令格式:
K_ R_ F_ Z_Y _ X_ G 81 99
98
G G 80G
活动2:程序编制 程序:
活动3:仿真、加工
任务二、完成图示零件的编程加工。
(供有学有余力和有兴趣的同学在任务一完成的基础上选做)
三、课堂评价表
姓名:班级:组别:组员:
四、课外练习
程序:。
数控铣床及加工中心编程与应用项目5铰孔加工

项目5铰孔加工5.1知识准备5.1.1铰孔加工铰孔是利用铰刀从工件孔壁上切除微量金属层,以提高其尺寸精度和表面粗糙度值的加工方法。
铰孔往往作为中小孔钻、扩后的精加工,也可以用于磨孔或研孔前的预加工。
铰孔精度可达到IT9~IT7级,表面粗糙度值R a为1.6~0.8μm,适用于孔的半精加工及精加工。
直径在80mmm以内的孔可以采用铰孔;直径较大的孔多采用精镗加工。
对于小于12mmm 的孔,由于镗孔非常困难,一般先用中心钻定位,然后钻孔(扩孔)、最后铰孔,以保证孔的加工精度。
铰孔不能修正孔的直线度和孔的位置度误差,因此铰孔前孔的直线度和孔的位置精度应符合要求。
一般来说,对于IT8级精度的孔,只要铰削一次就能达到要求;IT7级精度的孔应铰两次,先用小于孔径0.05~0.02mm的铰刀粗铰一次,再用符合孔径公差的铰刀精铰一次。
铰一般孔时,采用直齿铰刀即可;铰不连续孔时,则应采用螺旋齿铰刀;铰通孔时应选用左旋铰刀,切屑向前排出;铰不通孔时,选用右旋铰刀,以使切屑向后排出,但应注意防止“自动进刀”现象引起的振动。
1.铰刀的结构铰刀是对中小直径孔进行半精加工和精加工的刀具,刀具齿数多,槽底直径大、导向性及刚性好。
铰削时,铰刀从工件的孔壁上切除微量的金属层,使被加工孔的精度和表面质量得到提高。
根据铰刀的结构不同,可分为圆柱孔铰刀和锥孔铰刀;根据铰刀制造材料不同可分为高速钢铰刀和硬质合金铰刀。
铰刀的结构如图5-1所示,它是由工作部分、颈部和柄部三部分组成,工作部分包括导锥、切削部分和校准部分。
图5-1 铰刀2.铰刀的装夹铰削的功能是提高孔的尺寸精度和表面质量,而不能提高孔的直线度和孔的位置精度。
铰孔时要求铰刀与机床主轴要有很好的同轴度要求。
采用刚性装夹并不理想,若同轴度误差大,则会出现孔不圆、喇叭口、扩张量大等现象。
因此最好采用浮动装夹装置。
机床或夹具只传递运动和动力,而依靠铰刀的校准部分自我导向。
3.铰削的工艺特点(1)因为采用浮动装夹,铰孔的精度和表面粗糙度主要不是取决于机床的精度,而取决于铰刀的精度、铰刀的安装方式、加工余量、切削用量和切削液等条件。
掌握铰孔的加工工艺与编程

THANKS FOR WATCHING
感谢您的观看
问题原因
刀具材料选择不当、刀具结构不合理、切削参数设置不当、加工环 境恶劣等。
解决方案
选择高性能刀具材料、优化刀具结构、合理设置切削参数、改善加 工环境等。
预防措施
加强刀具使用前的检查,避免使用有裂纹或损伤的刀具。同时,合理 安排加工顺序,避免刀具在加工过程中受到过大的冲击和振动。
07 实际操作注意事项与安全 规范
选用具有良好冷却、润滑和防锈性能 的冷却液,以减少刀具磨损、降低加 工温度和防止孔壁表面锈蚀。
供给方式优化
根据加工条件和要求,选择合适的冷 却液供给方式,如喷淋、浸泡等,以 确保冷却液充分覆盖刀具和工件表面 。
工艺参数调整策略
初始参数设定
根据经验或参考类似加工案例, 设定初始的切削速度、进给量和
背吃刀量等参数。
预防措施
定期检查铰刀磨损情况,及时更换磨损严重的铰 刀。
表面粗糙度不达标改善措施
问题原因
铰刀刃口不锋利、铰削速 度过低、进给量不稳定、 铰孔余量过大等。
解决方案
修磨或更换铰刀、提高铰 削速度、稳定进给量、控 制铰孔余量等。
预防措施
加强铰刀的日常维护和保 养,保持刃口锋利。
刀具断裂或磨损过快预防策略
操作前准备工作检查清单
01
检查机床各部位是否完好无 损,如有异常应及时报告维 修人员进行维修或更换。
02
确认刀具、夹具、量具等是 否齐全、完好,并按照工艺 要求正确安装和调整。
03
检查加工工件是否符合图 纸要求,如有缺陷或变形 应及时处理或更换。
04
清洁工作区域,保持整 洁,避免杂物或油污对 加工过程造成干扰。
(完整版)铰孔方法
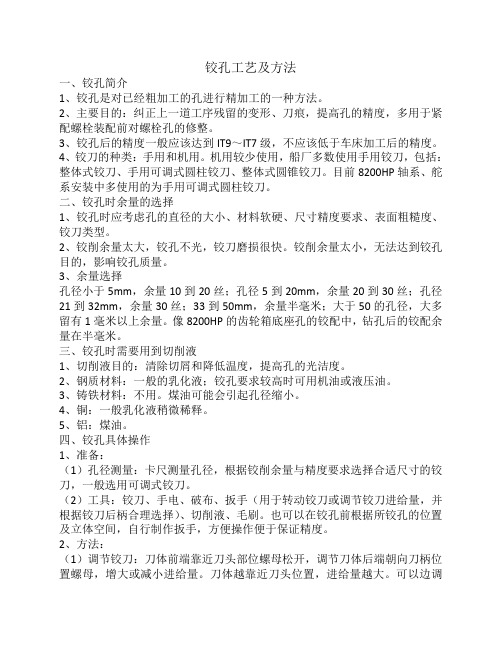
铰孔工艺及方法一、铰孔简介1、铰孔是对已经粗加工的孔进行精加工的一种方法。
2、主要目的:纠正上一道工序残留的变形、刀痕,提高孔的精度,多用于紧配螺栓装配前对螺栓孔的修整。
3、铰孔后的精度一般应该达到IT9~IT7级,不应该低于车床加工后的精度。
4、铰刀的种类:手用和机用。
机用较少使用,船厂多数使用手用铰刀,包括:整体式铰刀、手用可调式圆柱铰刀、整体式圆锥铰刀。
目前8200HP轴系、舵系安装中多使用的为手用可调式圆柱铰刀。
二、铰孔时余量的选择1、铰孔时应考虑孔的直径的大小、材料软硬、尺寸精度要求、表面粗糙度、铰刀类型。
2、铰削余量太大,铰孔不光,铰刀磨损很快。
铰削余量太小,无法达到铰孔目的,影响铰孔质量。
3、余量选择孔径小于5mm,余量10到20丝;孔径5到20mm,余量20到30丝;孔径21到32mm,余量30丝;33到50mm,余量半毫米;大于50的孔径,大多留有1毫米以上余量。
像8200HP的齿轮箱底座孔的铰配中,钻孔后的铰配余量在半毫米。
三、铰孔时需要用到切削液1、切削液目的:清除切屑和降低温度,提高孔的光洁度。
2、钢质材料:一般的乳化液;铰孔要求较高时可用机油或液压油。
3、铸铁材料:不用。
煤油可能会引起孔径缩小。
4、铜:一般乳化液稍微稀释。
5、铝:煤油。
四、铰孔具体操作1、准备:(1)孔径测量:卡尺测量孔径,根据铰削余量与精度要求选择合适尺寸的铰刀,一般选用可调式铰刀。
(2)工具:铰刀、手电、破布、扳手(用于转动铰刀或调节铰刀进给量,并根据铰刀后柄合理选择)、切削液、毛刷。
也可以在铰孔前根据所铰孔的位置及立体空间,自行制作扳手,方便操作便于保证精度。
2、方法:(1)调节铰刀:刀体前端靠近刀头部位螺母松开,调节刀体后端朝向刀柄位置螺母,增大或减小进给量。
刀体越靠近刀头位置,进给量越大。
可以边调节边插进孔内进行试验,以铰刀刀体插入孔内大约一半位置为最理想。
进给量调节好后锁紧上下螺母。
一般情况下,每次的进给量逐步减小,最后一刀完成后可达到铰孔的光洁度和精度要求。
打孔加工中的铰孔技术

打孔加工中的铰孔技术在机械制造领域,孔的加工是一项很重要的工作。
钻孔、铰孔、镗孔等加工方法都是常见的,其中铰孔技术在一些特定的制造场合中,显得非常重要。
本文将重点介绍打孔加工中的铰孔技术,包括铰孔的定义、工作原理、加工方法、技巧以及应用领域等方面,希望能对相关领域的工作者有所帮助。
一、铰孔的定义和工作原理铰孔,是指在制造工艺中,在一定直径范围内先进行一定直径的钻孔或者镗孔,再用一把铰刀进行铰孔,并得到具有一定直径精度和柔性的倒锥孔。
铰孔的作用是让螺纹和轴类零件的安装更加方便和准确。
为了保证铰孔的质量,关键需要掌握铰孔的工作原理。
铰孔技术分为交替铰削和连续铰削两种。
交替铰削就是指在铰刀做上下或前后往复运动时,在铰孔内交替切削,以获得形状精度高、表面质量好的铰孔。
连续铰削是指用铰刀持续运动,直到达到所需要的深度为止。
铰孔的工作原理主要就是进行侧向切削和径向扩孔。
二、铰孔的加工方法铰孔是采用铰孔刀进行加工的。
铰孔刀通常由刀柄、承钳、刀片等三部分构成。
刀旋转时,铰刀的刀片沿孔深向下移动,同时在侧向移动。
通过分离刃和导向刃的不同运动状态来吸取切屑。
铰孔的加工方法分为手动、机械以及数控加工三种。
1. 手动铰孔:手动铰孔是铰孔技术最简单、常见的一种加工方式。
手动铰孔即是用手动工具进行加工。
手动铰孔工具主要包括手动操作铰孔刀和滑板两种。
手动加工通常适用于小型、少量零件生产。
2. 机械铰孔:机械铰孔是指在铰孔刀上通过节流蝶阀或者变压调整深度的加工方法,多用于深孔加工和大批量生产。
3. 数控铰孔:数控铰孔是采用计算机进行控制的铰孔加工方式。
数控铰孔可以实现高度自动化程度和质量,以及提高生产效率等优点。
三、铰孔的技巧铰孔虽然是一项在制造工艺中非常基础的技术,但要想掌握好铰孔技术,还需要注意以下几个方面的技巧:1. 铰孔切屑处理:由于铰孔刀的侧向切削和径向扩孔方式,会形成大量切屑,如果切屑积聚在铰孔中,会影响铰孔的成形精度。
铰孔加工技术
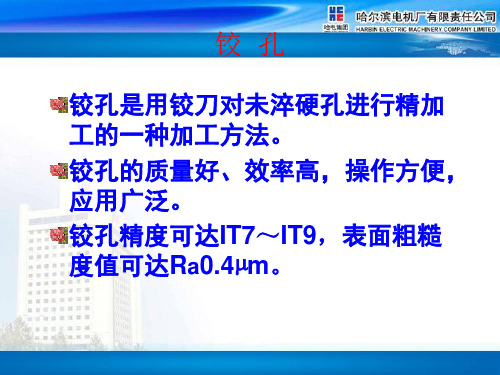
二、铰孔方法
(2)铰孔方法 1)铰通孔(见图) ①摇动尾座手轮,使铰刀引导部分进入孔口约1~2mm。 ②启动车床,加切削液,摇动尾座手轮,均匀进给至铰 刀切削部分的3/4超出孔末端时,反向摇动手轮,退出铰 刀。(退刀时工件继续转动) ③将内孔擦净后,检查孔径尺寸。 2)铰不通孔(见图) ①注意铰削深度,及时退刀。 ②中途退刀几次清除切屑。 注:铰钢件,新刀加乳化液,旧刀加切削油;铰铸件,新 刀加煤油,旧刀不加。
铰 孔
铰孔是用铰刀对未淬硬孔进行精加 工的一种加工方法。 铰孔的质量好、效率高,操作方便, 应用广泛。 铰孔精度可达IT7~IT9,表面粗糙 度值可达Ra0.4µm。
铰 孔
一、铰刀
二、铰孔方法
三、铰孔废品分析
一、铰刀
1、铰刀的几何形状 铰刀由工作部分、颈部和柄部组成。
一、铰刀
1、铰刀的几何形状 (1)柄部 用来夹持和传递转矩。(见图) (2)工作部分 由引导部分l1、切削部分l2、修光部分l3、和倒 锥l4组成。(见图) 1)引导部分 铰刀开始进入孔内时的导向部分。 2)切削部分 担负主要切削工作,铰削时定心好,切屑薄。 3)修光部分 有棱边,起定向、碾光孔壁、控制铰刀直径和 便于测量等作用。 4)倒锥部分 减小铰刀与孔壁之间的摩擦,还可防止产生喇 叭孔和孔径扩大。
使铰刀温度升高
5.余量太多 1.铰刀刀刃不锋利及刀刃上有崩 口、毛刺 表面粗糙 2.余量过大或过小 度差 3.切削速度太高,产生积屑瘤 4.切削液选择不当
2.留适当的铰削余量
3.降低切削速度,用油石把积屑瘤从刀刃上磨去 4.合理选择切削液
机用直柄铰刀
机用锥柄硬质合金铰刀
一、铰刀 3、铰刀尺寸的选择 铰刀的基本尺寸与孔的基本尺寸相同。 上偏差 = 2/3被加工孔公差 下偏差 = 1/3被加工孔公差 4、铰刀的装夹 为保证工件的同轴度,常采用浮动套筒 装夹铰刀。
铰孔编程指令
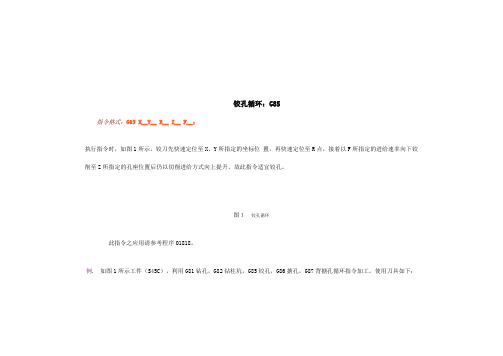
铰孔循环:G85指令格式:G85 X__Y__ R__ Z__ F__;执行指令时,如图1所示。
铰刀先快速定位至X、Y所指定的坐标位置,再快速定位至R点,接着以F所指定的进给速率向下铰削至Z所指定的孔座位置后仍以切削进给方式向上提升。
故此指令适宜铰孔。
图1铰孔循环此指令之应用请参考程序O1818。
例.如图1所示工件(S45C),利用G81钻孔,G82钻柱坑,G85铰孔,G86搪孔,G87背搪孔循环指令加工。
使用刀具如下:T01: 3 mm中心钻头,1500 rpm,125 mm / min。
T02: 6 mm钻头,1200 rpm,120 mm / min。
T03:7.8 mm钻头,1200 rpm,120 mm / min。
T04:8H7螺旋刃铰刀,300 rpm,300 mm / min。
T05:M6沉头铣刀,400 rpm,80 mm / min。
T06:30 mm钻头,200 rpm,50mm / min。
T07:可调式搪孔刀,800 rpm,30mm / min。
T08:可调式背搪孔刀,500 rpm,30mm / min。
图1程序O181801818;=>本程序适用于有臂式的ATC。
G28 G91 Z0;G28 X0 Y0;G54 T01;=>1号刀就换刀位置。
M06 T02;=>将1号刀装上主轴孔内,2号刀就换刀位置。
M03 S1500;G90 G0 X0 Y0;G43 Z5. H01;=>起始点Z5.。
G99 G81 X15. Y55. R3 Z -6. F125;=>钻中心孔。
X30. Y35.;X50. Y15.;X85. Y35.;G80 G28 G91 Z0;M06 T03;=>将2号刀装上主轴孔内,3号刀就换刀位置。
M03 S1200;G43 G90 G0 Z5. H02;G81 Z -24. F120;=>钻Ø6 mm孔。
X50. Y15.;X15. Y55.;G80 G28 G91 Z0;M06 T04;=>将3号刀装上主轴孔内,4号刀就换刀位置。
3.5铰孔

按材料分为 硬质合金铰刀
三、铰削余量
高速钢铰刀: 高速钢铰刀: 0.08mm~0.12mm 硬质合金铰刀: 硬质合金铰刀: 0.15mm~0.20mm
余量太小,不能将前道工序留下的痕迹去掉; 余量太小,不能将前道工序留下的痕迹去掉; 余量太大,影响表面粗糙度,后因负荷过大而崩刃。 余量太大,影响表面粗糙度,后因负荷过大而崩刃。
合理使用切削液: 合理使用切削液: 用新铰刀铰钢件, 用新铰刀铰钢件,用10%~15%的乳化液 的乳化液 用旧铰刀铰削,可用油类作为切削液,使孔稍微扩大 用旧铰刀铰削,可用油类作为切削液, 调整主轴与尾座套筒轴线的同轴度: 调整主轴与尾座套筒轴线的同轴度: 铰孔前必须调整主轴与尾座套筒轴线的同轴度在0.02以内 以内 铰孔前必须调整主轴与尾座套筒轴线的同轴度在 为消除同轴度误差对刀具的破坏力,建议使用浮动套筒。 为消除同轴度误差对刀具的破坏力,建议使用浮动套筒。
五、铰削时切削用量三要素的选择
切削速度: 切削速度: 进给量: 进给量: 小于5m/min 小于 应取大些 钢件,进给量取 钢件,进给量取0.2~1mm/r 铸件, 铸件,进给量还可稍大
背吃刀量: 背吃刀量:
是铰削余量的一半
六、铰削前对孔的要求
高速钢铰刀留余0.08~0.12 高速钢铰刀留余
铰孔前孔径留余为铰削余量
作业
练习二
• 1、铰削加工后能达到的尺寸精度是( 、铰削加工后能达到的尺寸精度是( ),表 ),表 面粗糙度是( ),铰削加工适合加工 铰削加工适合加工( 面粗糙度是( ),铰削加工适合加工( ) 孔。 • 2、铰刀按其用途可分为( 铰刀和( 、铰刀按其用途可分为( )铰刀和( )铰 按其材料可分为( 铰刀和( 铰刀。 刀;按其材料可分为( )铰刀和( )铰刀。 • 3、铰孔的余量根据刀具材料来确定,一般高速钢铰 、铰孔的余量根据刀具材料来确定, 刀余量为( 刀余量为( )mm;硬质合金铰刀余量为 ; ( )mm。 。 • 4、铰孔前对孔的三个要求是什么? 、铰孔前对孔的三个要求是什么? • 5、已知孔的尺寸为 、已知孔的尺寸为Φ20,上偏差为 ,上偏差为+0.021,下偏差 , 为0,计算铰刀的尺寸公差? ,计算铰刀的尺寸公差?
铰孔的方法之欧阳计创编

铰孔的方法、技巧及应用铰孔在模具装配加工中是必不可少的一个环节。
通过铰孔的加工作业,使孔的精度与光洁度、垂直度达到装配要求。
铰孔比钻孔精度要高很多,比扩孔的精度也高。
是普遍的一线工人非常头疼的一个问题,经常不是大就是小,客户每次验收都会把它列为重点检查对象,每次多多少少都有问题。
为避免问题的重复发生,在这里查阅借鉴了一些铰孔的方法,供大家讨论参考:1 铰孔工具:铰刀与绞杠●铰刀铰刀的种类很多。
铰刀按刀体结构可分为整体式铰刀、焊接式铰刀、镶齿式铰刀和装配可调式铰刀;按外形可分为圆柱铰刀和圆锥铰刀;按加工手段可分为机用铰刀和手用铰刀。
我们一般都是使用整体式圆柱机用铰刀。
●铰杠手铰时,铰杠用来夹持铰刀柄部的方榫,带动铰刀旋转的工具为铰杠。
常用的铰杠有普通铰杠和丁字铰杠。
固定式铰杠的方孔尺寸与柄长有一定规格。
可调式铰杠的方孔尺寸可以调节,适用范围广泛。
可调式铰杠的规格用长度表示,使用时应根据铰刀尺寸大小合理选用。
2 铰刀的研磨新铰刀直径上一般留有 O.O05--O.02mm 的研磨量,为保证铰孔精度,铰孔前,应按工件的精度要求研磨铰刀直径。
新铰刀的研磨可用研具在钻床上进行。
另外,铰刀在使用过程中易产生磨损,通常也由钳工进行手工修磨。
●选择油石修磨高速钢和合金工具钢铰刀,可选用W 14、中硬(ZY )或硬(Y )氧化铝油石;修磨硬质合金铰刀,可用碳化硅油石。
研磨方法油石在使用前应在机油中浸泡一段时间。
将铰刀固定,研磨后刀面时,油石与铰刀后刀面贴紧,沿切削刃垂直方向轻轻推动油石,注意不能将油石沿切削刃方向推动,以免由于油石磨出沟痕将刃口磨钝。
当铰刀前刀面需要研磨时,应将油石贴紧在前刀面上,沿齿槽方向轻轻推动,注意不要损坏刃口。
3 铰削余量铰削余量是指上道工序(钻孔或扩孔)完成后,孔径方向留下的加工余量。
一般根据孔径尺寸、孔的精度、表面粗糙度及材料的软硬和铰刀类型等选取,我们常用的可参考表表 14 机铰的铰削速度和进给量铰削钢材时,切削速度 V (8m/m in,进给量 f=O.4m m/r;铰削铸铁时,切削速度V<IOm/m in,进给量f=O.8m m/r。
- 1、下载文档前请自行甄别文档内容的完整性,平台不提供额外的编辑、内容补充、找答案等附加服务。
- 2、"仅部分预览"的文档,不可在线预览部分如存在完整性等问题,可反馈申请退款(可完整预览的文档不适用该条件!)。
- 3、如文档侵犯您的权益,请联系客服反馈,我们会尽快为您处理(人工客服工作时间:9:00-18:30)。
6.6 铰孔工艺、编程材料: 45#钢,正火处理图6-6-1圆周均布孔加工零件6.6.1 铰孔加工工艺1.铰孔加工概述钻孔是在实体材料中钻出一个孔,而铰孔是扩大一个已经存在的孔。
铰孔和钻孔、扩孔一样都是由刀具本身的尺寸来保证被加工孔的尺寸的,但铰孔的质量要高得多。
铰孔时,铰刀从工件孔壁上切除微量金属层,以提高其尺寸精度和减小其表面粗糙度值,铰孔是孔的精加工方法之一,常用作直径不很大、硬度不太高的工件孔的精加工,也可用于磨孔或研孔前的预加工。
机铰生产率高,劳动强度小,适宜于大批大量生产。
铰孔加工精度可达IT9~IT7级,表面粗糙度一般达Ra1.6~0.8μm。
这是由于铰孔所用的铰刀结构特殊,加工余量小,并用很低的切削速度工作的缘故。
直径在100 mm以内的孔可以采用铰孔,孔径大于100 mm时,多用精镗代替铰孔。
在镗床上铰孔时,孔的加工顺序一般为:钻(或扩)孔一镗孔一铰孔。
对于直径小于12 mm的孔,由于孔小镗孔非常困难,一般先用中心钻定位,然后钻孔、扩孔,最后铰孔,这样才能保证孔的直线度和同轴度。
如图6-6-1所示的工件,加工6×φ20H7均布孔,孔面有Ra1.6的表面质量要求,适合用铰孔方法进行孔的精加工。
一般来说,对于IT8级精度的孔,只要铰削一次就能达到要求;IT7级精度的孔应铰两次,先用小于孔径0.05~0.2 mm的铰刀粗铰一次,再用符合孔径公差的铰刀精铰一次;IT6级精度的孔则应铰削三次。
铰孔对于纠正孔的位置误差的能力很差,因此,孔的有关位置精度应由铰孔前的预加工工序予以保证,在铰削前孔的预加工,应先进行减少和消除位置误差。
如,对于同轴度和位置公差有较高要求的孔,首先使用中心钻或点钻加工,然后钻孔,接着是粗镗,最后才由铰刀完成加工。
另外铰孔前,孔的表面粗糙度应小于Ra3.2μm 。
铰孔操作需要使用冷却液,以得到较好的表面质量并在加工中帮助排屑。
切削中并不会产生大量的热,所以选用标准的冷却液即可。
2.铰刀及选用⑴ 铰刀结构在加工中心上铰孔时,多采用通用的标准机用铰刀。
通用标准铰刀,有直柄、锥柄和套式三种。
直柄铰刀直径为φ6mm ~φ20mm ,小孔直柄铰刀直径为φ1 mm ~φ6mm ,锥柄铰刀直径为φ10mm ~φ32mm ,套式铰刀直径为φ25mm ~φ80mm 。
分H7、H8、H9三种精度等级如图6-6-2(a ),整体式铰刀工作部分包括切削部分与校准部分。
铰刀刀头开始部分,称为刀头倒角或“引导锥”,方便刀具进入一个没有倒角的孔。
一些铰刀在刀头设计一段锥形切削刃,为刀具切削部分,承担主要的切削工作,其切削半锥角较小,一般为10~150,因此,铰削时定心好,切屑薄。
校准部分的作用是校正孔径、修光孔壁和导向。
校准部分包括圆柱部分和倒锥部分。
圆柱部分保证铰刀直径和便于测量。
刀体后半部分呈倒锥形可以减小铰刀与孔壁的摩擦。
⑵ 铰刀直径尺寸的确定铰孔的精度主要决定于铰刀的尺寸精度。
由于新的标准圆柱铰刀,直径上留在研磨余量,且其表面粗糙度也较差,所以在铰削IT8级精度以上孔时,应先将铰刀的直径研磨到所需的尺寸精度。
由于铰孔后,孔径会扩张或缩小,目前对孔的扩张或缩小量尚无统一规定,一般铰刀的直径多采用经验数值:铰刀直径的基本尺寸=孔的基本尺寸; 上偏差=2/3被加工孔的直径公差; 下偏差=1/3被加工孔的直径公差;例如:铰削φ20H7(021.00 )的孔,则选用的铰刀直径:铰刀基本尺寸=φ20 mm上偏差=2/3×0.021 mm=0.014 1 mm 下偏差=1/3×0.021 mm=0.007 mm所以选用的铰刀直径尺寸为φ20014.0007.0++mm 。
⑶ 铰刀齿数确定铰刀是多刃刀具,铰刀齿数取决于孔径及加工精度,标准铰刀有4~12齿。
齿数过多,刀具的制造刃磨较困难,在刀具直径一定时,刀齿的强度会降低,容屑空间小,由此造成切屑堵塞和划伤孔壁甚至蹦刃。
齿数过少,则铰削时的稳定性差,刀齿的切削负荷增大,且容易产生几何形状误差。
铰刀齿数可参照表6-6-1选择。
表6-6-1铰刀齿数选择铰刀直径/mm1.5~3 3~14 14~40 >40 齿 数一般加工精度4 4 6 8 高加工精度6810~12铰刀的刀齿又分为直齿和螺旋齿两种。
螺旋齿铰刀带有左旋的螺旋槽,这种设计适合于加工通孔,在切削过程中左旋螺旋槽“迫使”切屑往孔底移动并进入空区。
不过它不适合盲孔加工。
⑷ 铰刀材料确定铰刀材料通常是高速钢、钴合金或带焊接硬质合金刀尖的硬质合金刀具。
硬质合金铰刀耐磨性较好;高速钢铰刀较经济实用,耐磨性较差。
3.铰削用量的选用⑴ 铰削余量铰削余量是留作铰削加工的切深的大小。
通常要进行铰孔余量比扩孔或镗孔的余量要小,铰削余量太大会增大切削压力而损坏铰刀,导致加工表面粗糙度很差。
余量过大时可采取粗铰和精铰分开,以保证技术要求。
另一方面,如果毛坯余量太小会使铰刀过早磨损,不能正常切削,也会使表面粗糙度差。
一般铰削余量为0.1~0.25mm ,对于较大直径的孔,余量不能大于0.3mm 。
有一种经验建议留出铰刀直径1~3%大小的厚度作为铰削余量(直径值),如,Φ20的铰刀加Φ19.6左右的孔直径比较合适:20-(20×2/100)=19.6对于硬材料和一些航空材料,铰孔余量通常取得更小。
⑵铰孔的进给率铰孔的进给率比钻孔要大,通常为它的2~3倍。
取较高进给率的目的是使铰刀切削材料而不是摩擦材料。
但铰孔的粗糙度Ra值随进给量的增加而增大。
进给量过小时,会导致刀具径向摩擦力的增大,铰刀会迅速磨损引起铰刀颤动,使孔的表面变粗糙。
标准高速钢铰刀加工钢件,要得到表面粗糙度Ra0.63,则进给量不能超过0.5mm/r,对于铸铁件,可增加至0.85mm/r。
⑶铰孔操作的主轴转速铰削用量各要素对铰孔的表面粗糙度均有影响,其中以铰削速度影响最大,如用高速钢铰刀铰孔,要获得较好的粗糙度Ra0.63;m,对中碳钢工件来说,铰削速度不应超过5m/min,因为此时不易产生积屑瘤,且速度也不高;而铰削铸铁时,因切屑断为粒状,不会形成积屑瘤,故速度可以提高到8~10m/min。
通常铰孔的主轴转速可选为同材料上钻孔主轴转速的2/3。
例如,如果钻孔主轴转速为500r/min,那么铰孔主轴转速定为它的2/3比较合理:500×0.660=330r/min4.适合于铰孔切削循环通常铰孔的步骤和其他操作一样。
加工盲孔时,先采用钻削然后铰孔,但是在钻孔过程中必然会在孔内留下一些碎屑影响铰孔的正常操作。
因此在铰孔之前,应用M00停止程序,允许操作者除去所有的碎屑。
图6-6-3 G85固定循环路线铰孔编程也需要用到固定循环。
实际上并没有直接定义的铰孔循环。
Fanuc控制系统中比较合适的循环为G85,该循环可实现进给运动“进”和进给运动“出”,且两种运动的进给率相同。
G85固定循环路线如图6-6-3所示。
6.6.2 铰孔工艺编程实例1.工件孔加工任务如图6-6-1零件,毛坯尺寸:90×90×42,材料为45钢,正火处理,已在普通铣床上完成90×90侧面轮廓和基本定位面底平面加工,上表面留下了2㎜的余量,现需要加工:1)铣削上表面,保证尺寸30,上表面达到Ra3.2的表面质量要求;2)6×φ20H7圆周均布通孔加工,孔面达到Ra1.6的表面质量要求。
2.工件坐标系设定:如图6-6-4,工件长、宽向设计基准分别在左右、前后的对称面,设定X、Y向工件零点在工件对称中心,Z向零点设在距底面30㎜上表面。
3.上表面加工工艺分析:上表面加工参考平面铣削工艺。
4.圆周均布通孔加工方法选择选用钻→扩→铰的加工方法加工φ20H7,加工步骤及刀具选择如下:①引正孔:φ4中心钻钻引正孔;②钻孔:φ18麻花钻头钻通孔;③扩孔:φ19.8扩孔钻扩孔,半精加工;④孔口倒角:φ30点钻(钻尖90°)⑤铰孔:φ20H7机用铰刀铰孔精加工。
5.孔加工循环的选择:底孔加工前的中心钻加工中心孔用G82孔加工循环,麻花钻头钻6×φ18mm孔和扩孔钻直径19.8mm用G81孔加工循环,最后机用铰刀铰直径20mm孔应用G84孔加工循环。
6.各孔X、Y位置坐标值:如表6-6-2所示,各孔X、Y位置坐标值有直角坐标、极坐标两种表示法:表6-6-21 2 3 4 5 6直角坐标X=30cos30°Y=30sin30°X=30cos90°Y=30sin90°X=30cos150°Y=30sin150°X=30cos210°Y=30sin210°X=30cos270°Y=30sin270°X=30cos330°Y=30sin330°极坐标X=30Y=30 X=30Y=90X=30Y=150X=30Y=210X=30Y=270X=30Y=330显然当多孔在XY平面内圆周分布时,用极坐标的方法表示点位较直角坐标表示法方便。
7.孔加工循环的高度平面选择Z向R面高度:上表面上方50㎜。
图6-6-4工件工件坐标系初始平面高度:上表面上方5㎜。
孔底高度:引正孔钻至Z-5;φ18麻花钻钻孔深至Z-45;扩φ19.8孔深至Z-40;倒角至Z-11;铰孔深至Z-40。
8.切削用量的计算零件材料为45钢,机用铰刀材料为高速钢,直径20mm,进给量0.8mm/r,转速100 r/min,切削液为30%菜油加70%肥皂水。
其它刀具切削用量参考表6-6-3工序卡9.工序卡表6-6-3工序卡10.孔加工编程加工程序编制如下:主程序:O6600;主程序号G54 G21 G90 G94 G17 T01 初始化设置,同时T01刀准备T01 M98 P8888;调用换刀子程序,T01刀装上主轴M98 P6601;调用T01刀加工程序O6601T02 M98 P8888;调用换刀子程序,T02刀装上主轴M98 P6602;调用T02刀加工程序O6602T03 M98 P8888;调用换刀子程序,T03装上主轴子程序:O6601(T01铣平面)G00 X120 .0Y-5.0 S318 M03;G43 G0 Z50.0 H01;G0 Z-5.0 M08;G1 X-120 F550;G00 Z50.0;M99O6602(T02中心钻钻引正孔)S1200 M03G43 Z50.0 H02 M08G17G16G99 G82 X30 Y30 R5.0 Z-5.0 P100 F100. M98P6607G15M99O6603(T03麻花钻头钻通孔)S550 M03G43 Z50.0 H03 M08G17G16G99 G81 X30 Y30 R5.0 Z-45. F80. M98P6607G15M99O6604(T04φ19.8扩孔钻扩孔,半精加工)S300 M03G43 Z50.0 H04 M08G17G16G99 G81X30Y30 R5.0 Z-40.0 F150.M98 P6607G15M99O6605(T05孔口倒角)S300 M03G43 Z50.0 H05 M08G17G16G99 G82X30Y30 R5.0 Z-11.0 P100 F50. M98P6607G15M99O6606 (T06铰孔)M98 P6603;调用T03刀加工程序O6603T04 M98 P8888;调用换刀子程序,T04刀装上主轴M98 P06604;调用T04刀加工程序O6604T05 M98 P8888;调用换刀子程序,T05装上主轴M98 P6605;调用T05刀加工程序O6605T06 M98 P8888;调用换刀子程序,T06装上主轴M98 P6606;调用T06刀加工程序O6606G91 G28 Z0 回到机床Z向零点M05;主轴停转M30;。