连铸连轧工艺结课论文(DOC)
连铸连扎一-绪论

连铸连轧-绪论 连铸连轧 绪论
第一章
Logo
Contents
1 2 3 4
连铸连轧简介
连铸连轧的优点
连铸技术存在的问题
连铸连轧存在与发展的意义
Company Logo
Logo
1.1 定义及分类
连铸连轧
定义:由连铸机生产出来 定义:
的高温无缺陷坯, 的高温无缺陷坯,无需清理 和再加热(但需经过短时均 和再加热( 热和保温处理) 热和保温处理)而直接轧制 成材,这样把“ 成材,这样把“铸”和“轧 ”直接连成一条生产线的工 艺流程。 艺流程。
连铸: 连铸:95 t 钢坯 模铸: 模铸:86 t 钢坯
Company Logo
Logo
3 连铸技术存在的问题
缺陷
要保证连铸坯直接轧制和热装, 要保证连铸坯直接轧制和热装,无缺 陷铸坯比率越高越好。 陷铸坯比率越高越好。 为保证铸坯有足够的轧制温度, 为保证铸坯有足够的轧制温度,一般 要保证温度在1000~1100℃以上, 要保证温度在 ~ ℃以上, 且断面温度要均匀。 且断面温度要均匀。
美国 中国 日本
英国
世界钢产量与连铸比的关系
我国钢产量与连铸比的关系
Company Logo
Logo
2 连铸连轧的优点
1、简化生产工艺流程。仅连铸工 、简化生产工艺流程。 序就取代了模铸工艺中的整模、 序就取代了模铸工艺中的整模、 铸锭、脱模、均热、开坯等工序。 铸锭、脱模、均热、开坯等工序。
英国
1979 新日铁大分厂建成世界第一个 最新型的钢铁联合企业, 最新型的钢铁联合企业,采用 大型转炉配连铸机, 大型转炉配连铸机,实现全连 铸。
1964 谢尔顿钢铁厂实现全连铸生产。 谢尔顿钢铁厂实现全连铸生产。
连铸连轧工艺
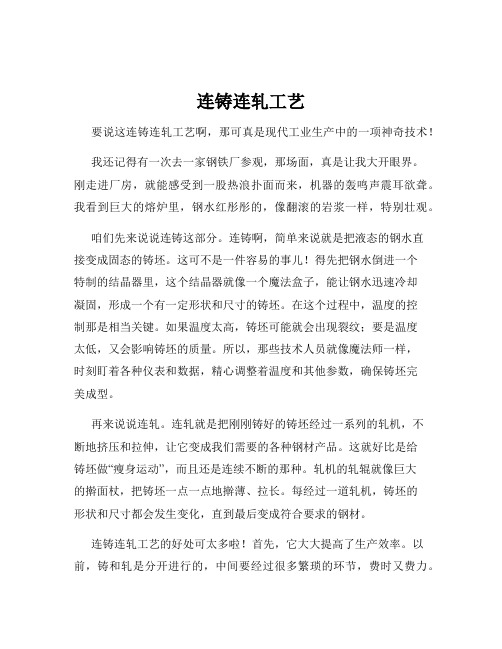
连铸连轧工艺要说这连铸连轧工艺啊,那可真是现代工业生产中的一项神奇技术!我还记得有一次去一家钢铁厂参观,那场面,真是让我大开眼界。
刚走进厂房,就能感受到一股热浪扑面而来,机器的轰鸣声震耳欲聋。
我看到巨大的熔炉里,钢水红彤彤的,像翻滚的岩浆一样,特别壮观。
咱们先来说说连铸这部分。
连铸啊,简单来说就是把液态的钢水直接变成固态的铸坯。
这可不是一件容易的事儿!得先把钢水倒进一个特制的结晶器里,这个结晶器就像一个魔法盒子,能让钢水迅速冷却凝固,形成一个有一定形状和尺寸的铸坯。
在这个过程中,温度的控制那是相当关键。
如果温度太高,铸坯可能就会出现裂纹;要是温度太低,又会影响铸坯的质量。
所以,那些技术人员就像魔法师一样,时刻盯着各种仪表和数据,精心调整着温度和其他参数,确保铸坯完美成型。
再来说说连轧。
连轧就是把刚刚铸好的铸坯经过一系列的轧机,不断地挤压和拉伸,让它变成我们需要的各种钢材产品。
这就好比是给铸坯做“瘦身运动”,而且还是连续不断的那种。
轧机的轧辊就像巨大的擀面杖,把铸坯一点一点地擀薄、拉长。
每经过一道轧机,铸坯的形状和尺寸都会发生变化,直到最后变成符合要求的钢材。
连铸连轧工艺的好处可太多啦!首先,它大大提高了生产效率。
以前,铸和轧是分开进行的,中间要经过很多繁琐的环节,费时又费力。
现在呢,一气呵成,从钢水到钢材,速度快得惊人。
其次,它还能节省能源和原材料。
因为整个过程是连续的,减少了中间的停顿和运输,也就降低了能源的消耗和材料的损失。
而且啊,这种工艺生产出来的钢材质量也更稳定,性能更优越。
在实际应用中,连铸连轧工艺已经广泛用于生产各种类型的钢材,比如建筑用的螺纹钢、汽车制造用的板材等等。
可以说,我们生活中的很多东西都离不开它。
不过,这连铸连轧工艺也不是没有挑战的。
比如说,设备的维护就是个大问题。
那些轧机和结晶器整天高强度工作,很容易出现故障。
一旦出了问题,就得赶紧抢修,否则会影响整个生产进度。
还有就是对操作人员的技术要求很高,他们得时刻保持警惕,应对各种突发情况。
连铸连轧课程论文2

连铸连轧课程论文综述题目:薄板坯连铸连轧技术研发高强度钢的概述姓名专业学号指导教师日期摘要:随着世界大环境对节能降耗的要求越来越高,薄板坯连铸连轧技术以其显著的优势也被各大钢铁企业所采用,利用该技术研发高强度钢也成为了当今热点的研究项目之一。
近年来,该研究已取得了一些成果,不少钢厂有利用薄板坯连铸连轧技术生产的高强度钢投入市场。
但是,薄板坯连铸连轧技术的特点并非完全有利于高强度钢的研发,如何利用该技术在研发方面的优点、克服其缺点,也是亟待解决的问题。
关键词:薄板坯;连铸连轧;高强度钢;产品研发;1 前言薄板坯连铸连轧生产工艺是20世纪90年代世界钢铁工业发展的一项重大新技术,以其投资省、成本低、节能降耗、生产周期短和高钢材收得率等优势,在世界范围内得到迅速地发展[1],[2]。
近年来,随着薄板坯连铸连轧技术研究的深入和其工艺、设备和自动控制等方面技术不断发展,钢铁企业在薄板坯连铸连轧技术不断扩展产品品种,其中,研发生产高强度钢就是其中一项。
一般,我们将拉伸强度在350MPa以上的钢板为高强度钢板,高强度钢板不仅具有较高的拉伸强度和屈服强度,而且还具有高的减重潜力、高的碰撞吸收能、高的成型性和低的平面各向异性等优点。
近20年来,钢材的高强度化成为钢铁工业最具活力和创造性进展的领域,一系列热轧高强度钢(板)被越来越广泛用于建筑业、制造业和加工业,特别是载重汽车、轿车、桥梁、起重机、舰船、铁路、集装箱、容熙、工程机械、甚至航空航天等领域。
可以预见,高强度钢的用途将越来越广泛,也越来越重要,如火车提速、汽车减重等[3]。
2 薄板坯连铸连轧技术研发高强度钢的概况2.1 高强度钢的国内外发展近年来,高强度钢的研发一直受到国内外的高度重视,不少国家,如日本,甚至将其列为国家重点研究项目,在欧洲最高级的研究项目库——尤里卡计划的新材料研究项目自足下,奥迪汽车等联合研制的轻型高强度薄板可以使汽车用钢减少25%。
1994年,世界18家汽车生产厂联手成立了超轻汽车钢财团,支持高强度汽车用钢的研究。
连铸工工作技术总结范文

摘要:本文以连铸工工作为背景,总结了我在连铸岗位上一年来的工作经历和技术提升,旨在回顾过去,展望未来,不断提高自身技能,为公司的发展贡献力量。
正文:一、前言作为一名连铸工,我深知连铸工艺在生产过程中的重要地位。
在过去的一年里,我始终秉持着敬业、勤奋、严谨的工作态度,不断学习新知识、新技术,努力提高自身技能。
现将一年来的工作情况进行总结,以便为今后的工作提供借鉴。
二、工作总结1. 工作态度(1)热爱本职工作,始终以高度的责任心和使命感投入到连铸生产中。
(2)严格遵守操作规程,确保生产安全。
(3)团结协作,与同事保持良好沟通,共同提高生产效率。
2. 技术提升(1)熟练掌握连铸工艺流程,能够独立完成各项操作。
(2)掌握常见故障的排查与处理方法,提高生产稳定性。
(3)学习并应用新技术,如自动控制、节能降耗等,降低生产成本。
(4)积极参加公司组织的培训,提升自身综合素质。
3. 生产成果(1)一年内,连续无事故,生产任务圆满完成。
(2)通过优化工艺参数,提高铸坯质量,降低废品率。
(3)积极参与生产改进,提出合理化建议,为生产效率提升做出贡献。
三、不足与改进1. 不足(1)对连铸工艺的理论知识掌握不够深入,需要进一步加强学习。
(2)在实际操作中,对某些设备的维护保养还不够熟练。
2. 改进措施(1)制定学习计划,深入学习连铸工艺理论知识,提高自身素质。
(2)加强与设备维护人员的沟通,提高设备维护保养技能。
(3)总结经验,不断优化操作方法,提高生产效率。
四、展望未来在新的一年里,我将继续保持敬业精神,努力提高自身技能,为公司的发展贡献自己的力量。
具体目标如下:1. 深入学习连铸工艺理论知识,提高自身综合素质。
2. 熟练掌握设备操作与维护保养技能,确保生产安全。
3. 积极参与生产改进,提出合理化建议,提高生产效率。
4. 加强与同事的沟通与协作,共同推进连铸工艺的发展。
总结,过去的一年,我在连铸岗位上取得了一定的成绩,但仍有不足之处。
冶金-连铸-炼钢-炼铁-毕业论文

冶金-连铸-炼钢-炼铁-毕业论文毕业设计(论文)学校:重庆科技学院专业:冶金工程概论班级:2015级能化一班学生:龚禄星学号:**********指导教师:***摘要溅渣护炉技术作为一项工艺简单、综合经济效益高的新技术,正别外国许多厂家推广、使用,分析了该技术的优势及存在的问题和解决办法,以及该技术的应用现状和应用前景。
转炉溅渣护炉是在出钢后,将转炉内留渣的粘度和氧化镁含量调整到合适的范围,在车间原有的氧枪或另设专用喷枪,向氧化镁含量、高粘度的炉渣喷一定压力和流量的氮气,将粘渣吹溅到炉衬上全面涂挂、冷却、凝固成一层炉渣质的保护层,避免了在冶炼时炉衬和炉渣的直接接触,从而起到减缓耐火材料的蚀损,延长转炉炉龄的作用。
溅渣护炉作为一项实用技术,经过国内外许多钢厂实践后,对提高转炉炉龄和降低耐火材料消耗的效果非常显著。
关键词:溅渣护炉;转炉;应用目录1存在问题及解决办法 (1)2溅渣护炉工艺的冶金因素及其优势 (2)3国外溅渣炉技术的发展 (3)4国内转炉炉龄现状及溅渣护炉技术的发展 (5)5应用现状及应用前景 (6)致谢信 (7)参考文献 (8)1存在问题及解决办法任何一项技术的应用不可能没有缺陷,在一些早期设备上,氧枪结瘤就是一个问题。
溅渣技术使用后,往往使枪结瘤出现次数增加。
实践证明,在溅渣过程中,若炉内残留少量钢水,氧枪结瘤将更加严重。
解决这个问题,有几种方法证明是有效的。
第一,有充足冷却水的炉子不出现结瘤问题;第二,将用于吹炼的热氧枪移走,换上冷枪完成溅渣,氧枪结瘤几乎完全消除。
这表明氧枪结瘤与温度和热量的传递有关。
渣子和冷枪的表面结合并不紧密,如果在溅渣时冷凝钢不出现在氧枪上,那就不会再氧枪上形成粗糙的外壳以使炉渣粘附其上。
溅渣后将氧枪停放在支架上,形成的渣壳将冷却,并与氧枪分离,脱落。
使用底吹搅拌技术的BOF转炉对溅渣技术的应用提出了新的要求。
在溅渣时炼钢工必须小心,不能使炉底的渣太多;氮气的流速必须足够高,以便将炉渣吹离炉底;另外要调整经过透气砖喷吹气体的压力、流量。
连铸工艺与设备之连铸连轧的匹配
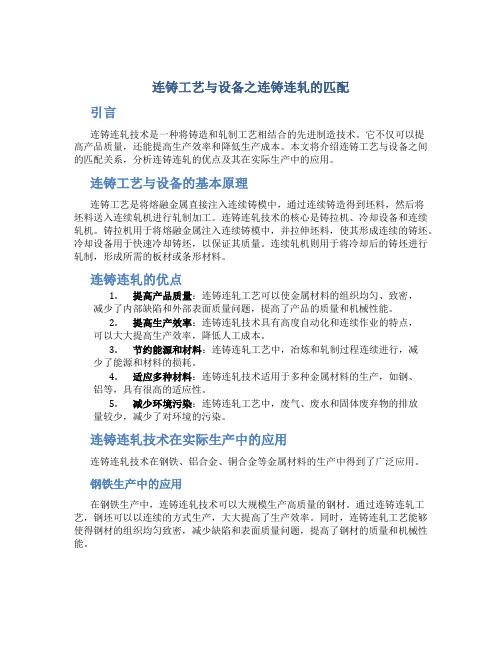
连铸工艺与设备之连铸连轧的匹配引言连铸连轧技术是一种将铸造和轧制工艺相结合的先进制造技术。
它不仅可以提高产品质量,还能提高生产效率和降低生产成本。
本文将介绍连铸工艺与设备之间的匹配关系,分析连铸连轧的优点及其在实际生产中的应用。
连铸工艺与设备的基本原理连铸工艺是将熔融金属直接注入连续铸模中,通过连续铸造得到坯料,然后将坯料送入连续轧机进行轧制加工。
连铸连轧技术的核心是铸拉机、冷却设备和连续轧机。
铸拉机用于将熔融金属注入连续铸模中,并拉伸坯料,使其形成连续的铸坯。
冷却设备用于快速冷却铸坯,以保证其质量。
连续轧机则用于将冷却后的铸坯进行轧制,形成所需的板材或条形材料。
连铸连轧的优点1.提高产品质量:连铸连轧工艺可以使金属材料的组织均匀、致密,减少了内部缺陷和外部表面质量问题,提高了产品的质量和机械性能。
2.提高生产效率:连铸连轧技术具有高度自动化和连续作业的特点,可以大大提高生产效率,降低人工成本。
3.节约能源和材料:连铸连轧工艺中,冶炼和轧制过程连续进行,减少了能源和材料的损耗。
4.适应多种材料:连铸连轧技术适用于多种金属材料的生产,如钢、铝等,具有很高的适应性。
5.减少环境污染:连铸连轧工艺中,废气、废水和固体废弃物的排放量较少,减少了对环境的污染。
连铸连轧技术在实际生产中的应用连铸连轧技术在钢铁、铝合金、铜合金等金属材料的生产中得到了广泛应用。
钢铁生产中的应用在钢铁生产中,连铸连轧技术可以大规模生产高质量的钢材。
通过连铸连轧工艺,钢坯可以以连续的方式生产,大大提高了生产效率。
同时,连铸连轧工艺能够使得钢材的组织均匀致密,减少缺陷和表面质量问题,提高了钢材的质量和机械性能。
铝合金生产中的应用在铝合金生产中,连铸连轧技术可以生产高精度、高品质的铝板和铝带。
通过连续轧制,铝坯可以得到所需的尺寸和厚度,并且具有优良的表面质量。
连铸连轧技术在高速列车、汽车和航空航天等领域的铝合金材料生产中得到了广泛应用。
连铸连轧生产工艺
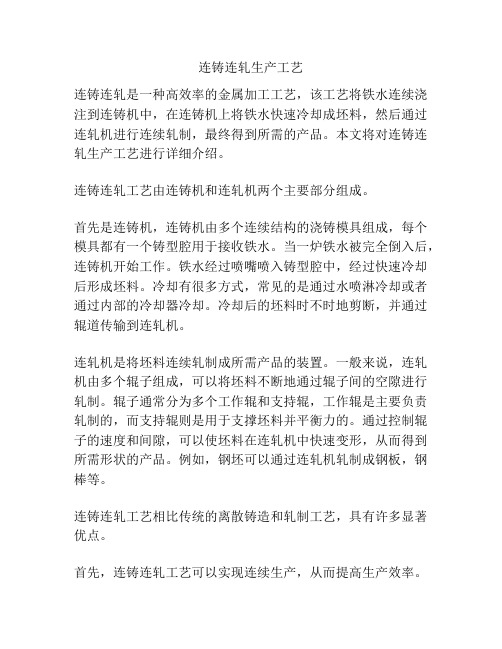
连铸连轧生产工艺连铸连轧是一种高效率的金属加工工艺,该工艺将铁水连续浇注到连铸机中,在连铸机上将铁水快速冷却成坯料,然后通过连轧机进行连续轧制,最终得到所需的产品。
本文将对连铸连轧生产工艺进行详细介绍。
连铸连轧工艺由连铸机和连轧机两个主要部分组成。
首先是连铸机,连铸机由多个连续结构的浇铸模具组成,每个模具都有一个铸型腔用于接收铁水。
当一炉铁水被完全倒入后,连铸机开始工作。
铁水经过喷嘴喷入铸型腔中,经过快速冷却后形成坯料。
冷却有很多方式,常见的是通过水喷淋冷却或者通过内部的冷却器冷却。
冷却后的坯料时不时地剪断,并通过辊道传输到连轧机。
连轧机是将坯料连续轧制成所需产品的装置。
一般来说,连轧机由多个辊子组成,可以将坯料不断地通过辊子间的空隙进行轧制。
辊子通常分为多个工作辊和支持辊,工作辊是主要负责轧制的,而支持辊则是用于支撑坯料并平衡力的。
通过控制辊子的速度和间隙,可以使坯料在连轧机中快速变形,从而得到所需形状的产品。
例如,钢坯可以通过连轧机轧制成钢板,钢棒等。
连铸连轧工艺相比传统的离散铸造和轧制工艺,具有许多显著优点。
首先,连铸连轧工艺可以实现连续生产,从而提高生产效率。
相比离散铸造和轧制工艺,连铸连轧工艺减少了产品在生产过程中的停留时间,有效减少生产周期,提高了生产效率。
其次,连铸连轧工艺可以减少产品的变形和出现缺陷的可能性。
在连铸连轧过程中,坯料的变形是在连续产生的,产品形状相对稳定,因此可以减少变形和出现缺陷的可能性。
同时,由于坯料在连轧过程中受到很大压力的作用,使其内部结构更加紧密,提高了产品的强度和硬度。
最后,连铸连轧工艺还可以减少能耗并降低生产成本。
连续生产可以减少能耗浪费,同时由于工艺参数的控制更加精准,可以减少废品率,降低了生产成本。
总之,连铸连轧是一种高效率的金属加工工艺,通过连续的铸造和轧制过程,可以快速地生产出所需的产品。
其优点包括高生产效率,减少变形和缺陷的可能性,降低能耗和生产成本等。
从连铸工的角度总结连铸工艺技术

从连铸工的角度总结连铸工艺技术连铸是指将钢水连续铸造成长条或板坯等工件的一种铸造方法。
它是大规模生产优质钢材的重要工艺之一,对于现代工业起到了举足轻重的作用。
在整个连铸生产线上,连铸工是很重要的一个环节,他们直接参与生产过程,操作连铸机械设备,关键时刻掌控生产现场,保障了连铸质量和生产效率。
因此,从连铸工的角度来看,总结连铸工艺技术的重要性就不言自明。
本文将从以下几个方面进行总结:引入连铸工艺技术、连铸工艺技术的优势和缺点、连铸工艺技术的发展历程、连铸工艺技术的未来趋势和连铸工如何提高连铸质量。
一、引入连铸工艺技术连铸技术诞生于20世纪50年代末期,起初是为解决板坯、带钢等细长型钢材生产效率低下的问题而发展起来的。
在传统钢铁生产过程中,铸造后的工件需要进行剪切和表面处理,而连铸技术则是直接将钢液连续浇注成材,一次成形。
可以说,连铸工艺技术是钢铁行业的一次革命性创新,它不仅提高了生产效率,更重要的是从根本上改变了钢铁生产的模式和思路,打破了生产方式的束缚,开创了新的局面。
随着生产技术的不断进步,连铸工艺技术也得到了进一步的完善和改进,目前已成为基本的钢铁冶炼技术之一。
二、连铸工艺技术的优势和缺点连铸工艺技术的优点主要集中在以下几个方面:1、高生产效率:连铸技术采用自动化连续生产方式,在单个连铸机上可实现多流速和多种规格的材料铸造生产,生产效率较高。
2、优质铸造:连铸技术确保了钢水的流动性,在铸造过程中能够避免气体夹杂和夹杂物的产生,大大提高了铸造质量。
3、节约能源:连铸工艺技术能够减少施铁熔炼过程中的能源消耗,并能够将低温废气和高温烟气进行回收,实现了节能环保的目标。
4、减少设备投资:采用连铸技术可以省去转炉转渣、轧制等工序,节约了一部分设备投资。
然而,连铸工艺技术也存在一些不足:1、设备需求较大:连铸生产线的投资一般比传统的生产线更大,需要大量投资购买生产设备。
2、管理复杂:连铸生产线涉及到多个工序和设备,对管理水平的要求比较高。
连铸 连轧

内蒙古科技大学连铸连轧工艺结课作业学院:材料与冶金学院专业:材料成型及控制工程班级:成型2013-2班姓名:吴蕊学号:1361105225薄板坯连铸连轧工艺技术发展的概况摘要:薄板坯连铸连轧工艺问世10年来发展迅速,CSP、ISP、FTSR为代表的各种工艺技术的发展各具特色。
总的发展趋势是,提高铸机生产能力充分发挥后部连轧机的生产能力;改进品种质量,提高产品的市场覆盖率;采用无头轧制工艺、生产超薄规格产品,以取代部分冷轧产品的市场;应用范围扩大,越来越多的在以高炉铁水为原料的大型联合企业中得到应用,为该工艺的发展开拓了更广阔的前景。
关键词:薄板坯连铸连轧发展趋势Survey of Technological Development of Thin SlabContinuous Casting and RollingZhang Shaoxian(Wuhan Iron & Steel Design Research Institute)Abstract:Technology of thin slab continuous casting and rolling has been rapidly developped these ten years since its invention.some typical process technologics,such as CSP,ISP and FISR,etc.have been developped with their own characteristics.The overall development tendency is:1)to increase concaster capability to make full use of caster;2)to improve product quality to increase product marketability;3)to produce super thin products with endless rolling process technology to take place of some cold-rolled products in market; 4)to enlarge applications in order to make it widely used in large joint ventures with hot metal as raw material.As a result ,this process will have great expectations in future developmentKeywords:thin slab continuous casting and rolling development tendency▲1 前言自1989年美国纽科格拉福特斯维尔厂第一条CSP薄板坯连铸连轧生产线投产至今的10年中,又相继有CSP、FTSR、CONROOL、TSP等类型的生产线相继投入生产。
连续铸轧技术总结
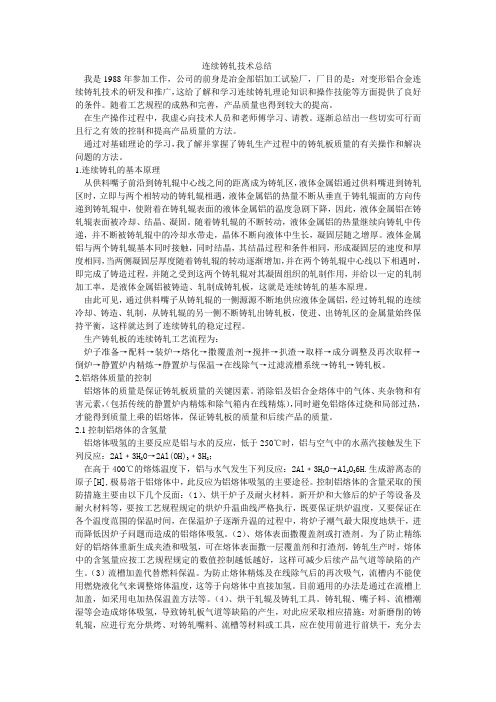
连续铸轧技术总结我是1988年参加工作,公司的前身是冶金部铝加工试验厂,厂目的是:对变形铝合金连续铸轧技术的研发和推广,这给了解和学习连续铸轧理论知识和操作技能等方面提供了良好的条件。
随着工艺规程的成熟和完善,产品质量也得到较大的提高。
在生产操作过程中,我虚心向技术人员和老师傅学习、请教。
逐渐总结出一些切实可行而且行之有效的控制和提高产品质量的方法。
通过对基础理论的学习,我了解并掌握了铸轧生产过程中的铸轧板质量的有关操作和解决问题的方法。
1.连续铸轧的基本原理从供料嘴子前沿到铸轧辊中心线之间的距离成为铸轧区,液体金属铝通过供料嘴进到铸轧区时,立即与两个相转动的铸轧辊相遇,液体金属铝的热量不断从垂直于铸轧辊面的方向传递到铸轧辊中,使附着在铸轧辊表面的液体金属铝的温度急剧下降,因此,液体金属铝在铸轧辊表面被冷却、结晶、凝固。
随着铸轧辊的不断转动,液体金属铝的热量继续向铸轧中传递,并不断被铸轧辊中的冷却水带走,晶体不断向液体中生长,凝固层随之增厚。
液体金属铝与两个铸轧辊基本同时接触,同时结晶,其结晶过程和条件相同,形成凝固层的速度和厚度相同,当两侧凝固层厚度随着铸轧辊的转动逐渐增加,并在两个铸轧辊中心线以下相遇时,即完成了铸造过程,并随之受到这两个铸轧辊对其凝固组织的轧制作用,并给以一定的轧制加工率,是液体金属铝被铸造、轧制成铸轧板,这就是连续铸轧的基本原理。
由此可见,通过供料嘴子从铸轧辊的一侧源源不断地供应液体金属铝,经过铸轧辊的连续冷却、铸造、轧制,从铸轧辊的另一侧不断铸轧出铸轧板,使进、出铸轧区的金属量始终保持平衡,这样就达到了连续铸轧的稳定过程。
生产铸轧板的连续铸轧工艺流程为:炉子准备→配料→装炉→熔化→撒覆盖剂→搅拌→扒渣→取样→成分调整及再次取样→倒炉→静置炉内精炼→静置炉与保温→在线除气→过滤流槽系统→铸轧→铸轧板。
2.铝熔体质量的控制铝熔体的质量是保证铸轧板质量的关键因素。
消除铝及铝合金熔体中的气体、夹杂物和有害元素,(包括传统的静置炉内精炼和除气箱内在线精炼),同时避免铝熔体过烧和局部过热,才能得到质量上乘的铝熔体,保证铸轧板的质量和后续产品的质量。
连铸连轧

连铸连轧工业与技术结业论文姓名:李春杰班级:冶金12-4学号:120123202084薄板坯连铸连轧技术研发高强度钢的概述李春杰(辽宁科技大学材料与冶金学院)摘要:随着世界大环境对节能降耗的要求越来越高,薄板坯连铸连轧技术以其显著的优势也被各大钢铁企业所采用,利用该技术研发高强度钢也成为了当今热点的研究项目之一。
近年来,该研究已取得了一些成果,不少钢厂有利用薄板坯连铸连轧技术生产的高强度钢投入市场。
但是,薄板坯连铸连轧技术的特点并非完全有利于高强度钢的研发,如何利用该技术在研发方面的优点、克服其缺点,也是亟待解决的问题。
关键词:薄板坯;连铸连轧;高强度钢;产品研发Overview of thin slab continuous casting and rolling technology research and development of high strength steelLI Chun-Jie(Liaoning university of science and technology school of material and metallurgy)Abstract: as the world's environment is more and more high to the requirement of saving energy and reducing consumption, thin slab continuous casting and rolling technology, with its significant advantages have also been adopted by each big iron and steel enterprises, the use of the technology research and development of high strength steel has become one of the hotspot of the research project. In recent years, the research has made some achievements, many steel mills have advantage of thin slab continuous casting and rolling technology, production of high strength steel were put on sale. However, the characteristics of thin slab continuous casting and rolling technology is not completely is conducive to the development of the high strength steel how to utilize the advantages of this technology in the research and development, to overcome its shortcomings, is also a problem to be solved.Key words: thin slab; Continuous casting and rolling; High strength steel; Product research and development1薄板坯连铸连轧技术的优势薄板坯连铸连轧的工艺过程与常规厚板坯连铸连轧工艺的最大不同在于热历史不同。
17届国际铜业大会论文_铸机链_
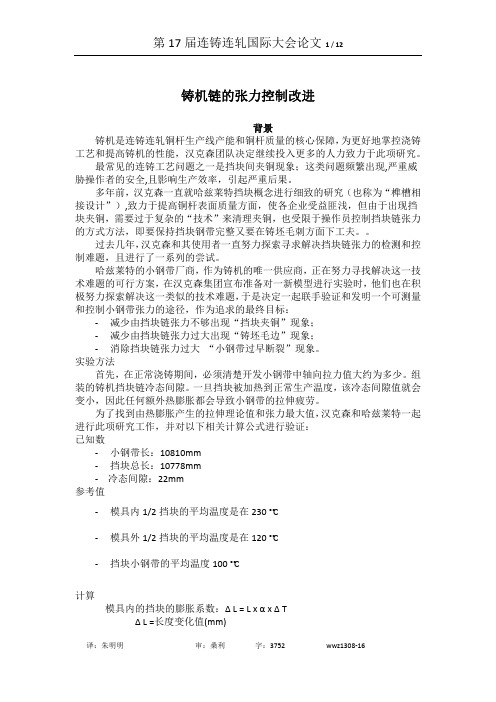
‐ 合力“R”通过挡块2.3.4.移动 ‐ 作用在挡块5右下角的力 Fx 和 Fy ‐ 挡块5上、下的力大小相等、方向相反, ‐ 传感器上的力 FR2 = 2 x Fy
Fy = R sin θ
R = Fy / sin θ
R = Fcomp / cos θ 因此压力 Fcomp = R cos θ = Fy cos θ / sin θ = Fy / tan θ 支撑轮偏移
第 17 届连铸连轧国际大会论文 1 / 12
铸机链的张力控制改进
背景 铸机是连铸连轧铜杆生产线产能和铜杆质量的核心保障,为更好地掌控浇铸 工艺和提高铸机的性能,汉克森团队决定继续投入更多的人力致力于此项研究。 最常见的连铸工艺问题之一是挡块间夹铜现象;这类问题频繁出现,严重威 胁操作者的安全,且影响生产效率,引起严重后果。 多年前,汉克森一直就哈兹莱特挡块概念进行细致的研究(也称为“榫槽相 接设计”),致力于提高铜杆表面质量方面,使各企业受益匪浅,但由于出现挡 块夹铜,需要过于复杂的“技术”来清理夹铜,也受限于操作员控制挡块链张力 的方式方法,即要保持挡块钢带完整又要在铸坯毛刺方面下工夫。。 过去几年,汉克森和其使用者一直努力探索寻求解决挡块链张力的检测和控 制难题,且进行了一系列的尝试。 哈兹莱特的小钢带厂商,作为铸机的唯一供应商,正在努力寻找解决这一技 术难题的可行方案,在汉克森集团宣布准备对一新模型进行实验时,他们也在积 极努力探索解决这一类似的技术难题,于是决定一起联手验证和发明一个可测量 和控制小钢带张力的途径,作为追求的最终目标: ‐ 减少由挡块链张力不够出现“挡块夹铜”现象; ‐ 减少由挡块链张力过大出现“铸坯毛边”现象; ‐ 消除挡块链张力过大 “小钢带过早断裂”现象。 实验方法 首先,在正常浇铸期间,必须清楚开发小钢带中轴向拉力值大约为多少。组 装的铸机挡块链冷态间隙。一旦挡块被加热到正常生产温度,该冷态间隙值就会 变小,因此任何额外热膨胀都会导致小钢带的拉伸疲劳。 为了找到由热膨胀产生的拉伸理论值和张力最大值,汉克森和哈兹莱特一起 进行此项研究工作,并对以下相关计算公式进行验证: 已知数 ‐ 小钢带长:10810mm ‐ 挡块总长:10778mm ‐ 冷态间隙:22mm 参考值
连铸连轧工艺结课论文(DOC)

内蒙古科技大学《连铸连轧工艺结课论文》—保护渣的研究及应用学生姓名:学号:专业:班级:指导教师:目录1.摘要 (2)2.关键词 (2)3.引言 (2)4.概念 (2)5.炼钢连铸工艺流程 (3)6.连铸结晶器保护渣作用 (3)7. 薄板坯连铸技术的特点及对结晶器保护渣的要求 (3)8.结晶器保护渣的成分 (4)9.薄板坯连铸结晶器保护渣的物理性能及冶金特性 (6)10结晶器保护渣的应用 (10)11结论 (11)12.参考文献 (11)连铸连轧工艺结课论文—保护渣的研究及应用[摘要]:连铸结晶器保护渣对铸坯表面质量具有显著影响。
通过对保护渣理化性能、熔化特性的基础研究, 确定了连铸用保护渣的组成及成分范围。
确定的保护渣熔化温度, 粘度被实践证明是合理的, 这为保护渣的研究提供了理论依据。
通过工业性试验的应用证明所研制的保护渣系能满足薄板坯连铸的需要, 使用效果良好, 为我国连铸用保护渣的配制提供了方向。
[关键词]:连铸;保护渣;结晶器Class paper of Continuous Steel Casting and rolling process—Protection slag research and application [Abstract]:Continuous casting crystallizer protection slag on casting surface quality has significant effect. Based on the physical and chemical properties, protective slag melting characteristics of the basic research, determine the continuous casting with protection slag composition and composition range. Certain protection slag melting temperature, viscosity was proved to be reasonable, this for the protection of slag research provides a theoretical basis. Through the application of industrial test that the developed protection slag system can meet the need of slab continuous casting, the use effect is good, for our country with the preparation of the continuous casting slag protection provided direction.[Key words]: Continuous Steel Casting;Protection slag;Slag crystallizer一、引言作为一项划时代的技术进步【1】,薄板坯连铸技术以其简化生产工序、节能降耗、投资省、成本低、提高铸坯质量和经济效益好等优点而得到迅速发展。
连铸论文2
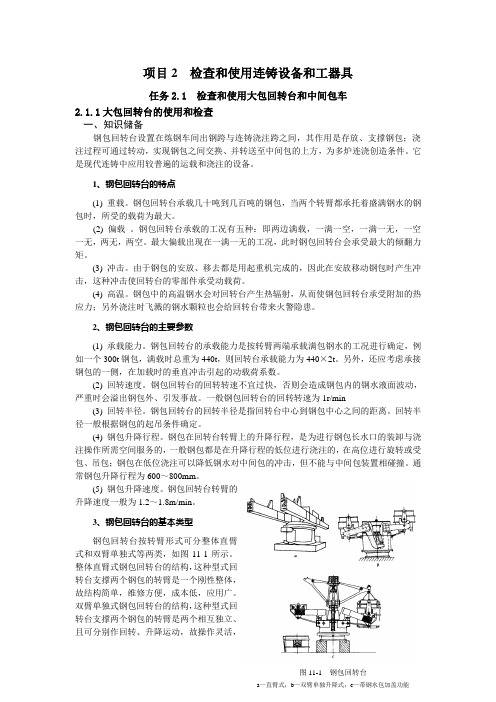
项目2 检查和使用连铸设备和工器具任务2.1 检查和使用大包回转台和中间包车2.1.1大包回转台的使用和检查一、知识储备钢包回转台设置在炼钢车间出钢跨与连铸浇注跨之间,其作用是存放、支撑钢包;浇注过程可通过转动,实现钢包之间交换、并转送至中间包的上方,为多炉连浇创造条件。
它是现代连铸中应用较普遍的运载和浇注的设备。
1、钢包回转台的特点(1) 重载。
钢包回转台承载几十吨到几百吨的钢包,当两个转臂都承托着盛满钢水的钢包时,所受的载荷为最大。
(2) 偏载。
钢包回转台承载的工况有五种:即两边满载,一满一空,一满一无,一空一无,两无,两空。
最大偏载出现在一满一无的工况,此时钢包回转台会承受最大的倾翻力矩。
(3) 冲击。
由于钢包的安放、移去都是用起重机完成的,因此在安放移动钢包时产生冲击,这种冲击使回转台的零部件承受动载荷。
(4) 高温。
钢包中的高温钢水会对回转台产生热辐射,从而使钢包回转台承受附加的热应力;另外浇注时飞溅的钢水颗粒也会给回转台带来火警隐患。
2、钢包回转台的主要参数(1) 承载能力。
钢包回转台的承载能力是按转臂两端承载满包钢水的工况进行确定,例如一个300t钢包,满载时总重为440t,则回转台承载能力为440×2t。
另外,还应考虑承接钢包的一侧,在加载时的垂直冲击引起的动载荷系数。
(2) 回转速度。
钢包回转台的回转转速不宜过快,否则会造成钢包内的钢水液面波动,严重时会溢出钢包外、引发事故。
一般钢包回转台的回转转速为1r/min(3) 回转半径。
钢包回转台的回转半径是指回转台中心到钢包中心之间的距离。
回转半径一般根据钢包的起吊条件确定。
(4) 钢包升降行程。
钢包在回转台转臂上的升降行程,是为进行钢包长水口的装卸与浇注操作所需空间服务的,一般钢包都是在升降行程的低位进行浇注的,在高位进行旋转或受包、吊包;钢包在低位浇注可以降低钢水对中间包的冲击,但不能与中间包装置相碰撞。
通常钢包升降行程为600~800mm。
连铸论文1

电子教案时彦林项目1 认识连续铸钢生产教学目标知识目标:1、了解连铸基本概念、工艺流程。
2、了解主要设备、设备运转模式、连铸各岗位及职责。
3、掌握连铸发展及技术指标能力目标:掌握连铸生产过程及岗位职责情感目标:1、通过创设情境、问题,激发学生的好奇心和求知欲。
2、通过项目学教学,培养学生团队合作精神,养成良好的职业素养。
3、通过连铸入门学习,掌握连铸的重要性和必要性。
教学重点与难点重点:连铸生产过程及岗位职责难点:连铸经济技术指标的理解教学方法项目教学法:将需要解决的问题或要完成的任务交给学生,在教师的指导下,师生一起按照实际工作的完整性对项目进行分析、决策、实施、评估总结。
在项目学习中,根据项目任务,遵循教师为主导,学生为主体,训练为主线的原则,以教师提出的问题为主线,引导学生在操作的同时,掌握相应的理论知识,讨论分析,充分调动学生自主的主动的学习学法:问题引导法、学练结合法等。
教时、教具和课前准备:学时:8学时教学过程一、项目提出以石钢连铸机为载体,引入连铸生产工作过程,对连续铸钢有一定的认识。
二、工作任务掌握连铸基本概念、连铸发展及技术指标、工艺流程、主要设备、设备运转模式、连铸各岗位及职责。
三、项目实施学生分组思考、讨论,提出意见,观看录像、图片了解连铸生产过程,实训室观看模型,仿真软件。
五、教师总结归纳连续铸钢工艺过程及设备组成连铸机分类及连铸优越性连铸机运转模式连铸技术经济指标连铸生产各岗位及职责六、思考题1、连铸机的主体设备由哪些?2、连铸机如何分类?3、连铸的优越性由哪些?任务1 认识连续铸钢工艺过程及设备组成一、目的与目标认识连续铸钢工艺过程及设备组成。
二、教学设计1、情景设计:(1)专业教室观看连续铸钢录像;(2)学习模拟软件;(3)参观实训室连铸模型。
2、学时:2学时3、方法:学生分组思考、讨论,提出意见。
4、教师总结。
三、知识储备见辅导材料。
四、技能实施1、连铸工艺:钢包――大包回转台――中间罐――结晶器――-二次冷却――切割定尺――铸坯输送--冷床――码跺。
连铸论文4
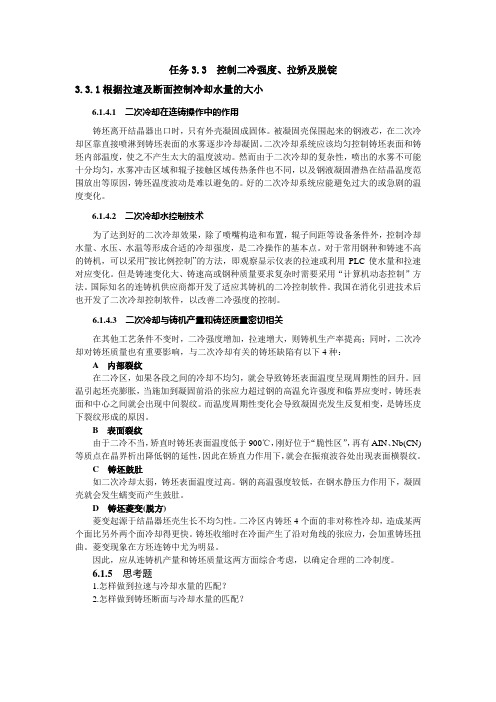
任务3.3 控制二冷强度、拉矫及脱锭3.3.1根据拉速及断面控制冷却水量的大小6.1.4.1 二次冷却在连铸操作中的作用铸坯离开结晶器出口时,只有外壳凝固成固体。
被凝固壳保围起来的钢液芯,在二次冷却区靠直接喷淋到铸坯表面的水雾逐步冷却凝固。
二次冷却系统应该均匀控制铸坯表面和铸坯内部温度,使之不产生太大的温度波动。
然而由于二次冷却的复杂性,喷出的水雾不可能十分均匀,水雾冲击区域和辊子接触区域传热条件也不同,以及钢液凝固潜热在结晶温度范围放出等原因,铸坯温度波动是难以避免的。
好的二次冷却系统应能避免过大的或急剧的温度变化。
6.1.4.2 二次冷却水控制技术为了达到好的二次冷却效果,除了喷嘴构造和布置,辊子间距等设备条件外,控制冷却水量、水压、水温等形成合适的冷却强度,是二冷操作的基本点。
对于常用钢种和铸速不高的铸机,可以采用“按比例控制”的方法,即观察显示仪表的拉速或利用PLC使水量和拉速对应变化。
但是铸速变化大、铸速高或钢种质量要求复杂时需要采用“计算机动态控制”方法。
国际知名的连铸机供应商都开发了适应其铸机的二冷控制软件。
我国在消化引进技术后也开发了二次冷却控制软件,以改善二冷强度的控制。
6.1.4.3 二次冷却与铸机产量和铸坯质量密切相关在其他工艺条件不变时,二冷强度增加,拉速增大,则铸机生产率提高;同时,二次冷却对铸坯质量也有重要影响,与二次冷却有关的铸坯缺陷有以下4种:A 内部裂纹在二冷区,如果各段之间的冷却不均匀,就会导致铸坯表面温度呈现周期性的回升。
回温引起坯壳膨胀,当施加到凝固前沿的张应力超过钢的高温允许强度和临界应变时,铸坯表面和中心之间就会出现中间裂纹。
而温度周期性变化会导致凝固壳发生反复相变,是铸坯皮下裂纹形成的原因。
B 表面裂纹由于二冷不当,矫直时铸坯表面温度低于900℃,刚好位于“脆性区”,再有AIN、Nb(CN)等质点在晶界析出降低钢的延性,因此在矫直力作用下,就会在振痕波谷处出现表面横裂纹。
连铸连轧课程论文5

题目薄板坯连铸连轧技术在高强钢中的应用学院专业年级学生姓名指导教师学号年月日目录1、微合金化高强度钢的生产 (1)1.1 薄板坯连铸连轧工艺特点与微合金化的关系 (1)1.2微合金化的优势 (2)2微合金元素的选择 (2)2.1 钒 (3)2.2 铌 (6)2.3 钒和铌的比较 (7)3 优化工艺参数开发微合金高强度钢 (9)3.1 CSP流程V-N微合金钢冶金学特征研究[4] (11)3.2 CSP工艺热轧400MPa汽车板组织与力学性能的研究[5] (12)摘要微合金化技术是提高钢材综合性能的有效技术措施,随着薄板坯连铸连轧(CSP)技术的推广应用,人们开始研究基于薄板坯连铸连轧流程的微合金化技术的相关问题。
其中主要是以钒、铌为代表,目前已经了产品的系列化。
本文分别介绍了钒、铌合金高强度钢在CSP过程中的的固溶与析出机理,对其进行了相关比较,并介绍了相关冶金学机理。
主要结论为:在CSP流程上采用微合金技术可获得铁素体晶粒尺寸3~4μm的超细晶组织,微合金钢的沉淀强化对进一步提高钢带的强度也有十分重要的贡献。
通过采用微合金化技术,在CSP流程上可开发屈服强度高达550MPa级的高强热轧钢带。
关键词CSP 微合金化钒、铌高强度钢1、微合金化高强度钢的生产1.1 薄板坯连铸连轧工艺特点与微合金化的关系薄板坯连铸连轧工艺中薄板坯厚度在50~100mm,铸坯冷却速度快;铸坯直接热送至加热炉,未经奥氏体向铁素体的相变过程;加热炉的再加热温度一般在1100~1150℃;50mm的板坯不粗轧即进入5~6架的精轧机架,70~100mm的板坯进入5道次精轧前一般也只经1~2粗轧机架。
为了补偿进入精轧机之前的板坯温度,一般在粗轧机后安装卷取箱或保温炉,可为粗轧和终轧间提供进精轧F1机架的速度调整。
最后出F6机架到地下卷取,与目前现有的带钢生产线类似,具备了强有力的层流冷却系统,保证能生产薄规格的产品。
当采用电炉为炼钢炉时,必须考虑残余合金元素和氮含量水平,通常需加入高质量的废钢,适当配加DRI(直接还原铁)和HBI(热压块铁)。
连铸连轧课程论文3

题目薄板坯连铸连轧开发高强度钢综述学院:专业:学号:学生姓名:任课老师日期:摘要本文通过介绍薄板坯连铸连轧技术的起源,概括薄板坯连铸连轧的发展过程,总结其工艺特点及工艺类型,从而了解了薄板坯连铸连轧与传统轧制在工艺流程上的巨大区别。
同时,也让我们看到了薄板坯连铸连轧在钢铁生产上的巨大优势,尽管目前薄板坯连铸连轧在钢铁市场中占有的份额相当大,但在高强度钢生产上却相当有限。
这将极大刺激我们对高强度钢产品的开发。
随后,本文通过总结目前用薄板坯连铸连轧技术来生产高强度钢的研究理论和产品开发、生产经验,说明薄板坯连铸连轧技术在高强度钢产品开发上的可行性和巨大的应用前景。
关键字:薄板坯;连铸连轧;高强度钢;产品开发薄板坯连铸连轧技术是20世纪80年代末世界钢铁工业发展的一项重大技术,由于薄板坯连铸连轧工艺具有流程短、成本低、成材率高、产品质量好、品种覆盖面广等突出优点,而且投资省,见效快,因而成为国际上竞相开发的重大工艺技术[1]。
世界上第一台连铸机于1986年在德国马克公司铸钢车间试验成功,世界上第一条薄板坯连铸连轧生产线于1989年6月在美国的纽柯公司的克劳福兹维尔厂(Crawfords-ville)投产,该生产线采用了西马克(SMS)的连铸连轧技术(CSP),设计年产量为80万t。
我国第一条薄板坯连铸连轧生产线于1999年8月在广州珠江钢厂建成投产。
随后,我国的薄板坯连铸连轧技术发展越来越快,到2007年,我国已有珠钢、邯钢、包钢、鞍钢、唐钢、马钢、涟钢、本钢、通钢、济钢、酒钢、唐钢等12条生产线,年产约3500万t[2]。
经过20多年的不断发展完善,薄板坯连铸连轧生产线的产品质量和产量逐渐提高,已经可以和传统的热轧流程相媲美[3],并有超越之势,而其优点也越来越明显。
薄板坯连铸连轧工艺是连铸技术发展的必然结果,它打破了传统的生产模式,将连铸与热带钢连轧有机地结合在一起。
今日,薄板坯连铸连轧技术已经步入了成熟期。
- 1、下载文档前请自行甄别文档内容的完整性,平台不提供额外的编辑、内容补充、找答案等附加服务。
- 2、"仅部分预览"的文档,不可在线预览部分如存在完整性等问题,可反馈申请退款(可完整预览的文档不适用该条件!)。
- 3、如文档侵犯您的权益,请联系客服反馈,我们会尽快为您处理(人工客服工作时间:9:00-18:30)。
内蒙古科技大学《连铸连轧工艺结课论文》—保护渣的研究及应用学生姓名:学号:专业:班级:指导教师:目录1.摘要 (2)2.关键词 (2)3.引言 (2)4.概念 (2)5.炼钢连铸工艺流程 (3)6.连铸结晶器保护渣作用 (3)7. 薄板坯连铸技术的特点及对结晶器保护渣的要求 (3)8.结晶器保护渣的成分 (4)9.薄板坯连铸结晶器保护渣的物理性能及冶金特性 (6)10结晶器保护渣的应用 (10)11结论 (11)12.参考文献 (11)连铸连轧工艺结课论文—保护渣的研究及应用[摘要]:连铸结晶器保护渣对铸坯表面质量具有显著影响。
通过对保护渣理化性能、熔化特性的基础研究, 确定了连铸用保护渣的组成及成分范围。
确定的保护渣熔化温度, 粘度被实践证明是合理的, 这为保护渣的研究提供了理论依据。
通过工业性试验的应用证明所研制的保护渣系能满足薄板坯连铸的需要, 使用效果良好, 为我国连铸用保护渣的配制提供了方向。
[关键词]:连铸;保护渣;结晶器Class paper of Continuous Steel Casting and rolling process—Protection slag research and application [Abstract]:Continuous casting crystallizer protection slag on casting surface quality has significant effect. Based on the physical and chemical properties, protective slag melting characteristics of the basic research, determine the continuous casting with protection slag composition and composition range. Certain protection slag melting temperature, viscosity was proved to be reasonable, this for the protection of slag research provides a theoretical basis. Through the application of industrial test that the developed protection slag system can meet the need of slab continuous casting, the use effect is good, for our country with the preparation of the continuous casting slag protection provided direction.[Key words]: Continuous Steel Casting;Protection slag;Slag crystallizer一、引言作为一项划时代的技术进步【1】,薄板坯连铸技术以其简化生产工序、节能降耗、投资省、成本低、提高铸坯质量和经济效益好等优点而得到迅速发展。
目前,世界上各类薄板坯连铸机的生产能力已达3800万t/a。
据日本钢铁界人土预测【2】,到2020年连铸薄板坯产量将占连铸坯总产量的45%~60%,连铸带钢产量将占总产量的10%~15%,而传统连铸机所浇铸的连铸坯产量将仅占连铸坯总产量30%~45%。
薄板坯连铸与常规板坯连铸在设计和工艺上最大的区别是结晶器形状及振动方式,浸入式水口的设计和薄板坯连铸结晶器保护渣的物理性能及化学成分的优化二项关键技术。
分析薄板坯连铸技术的发展,结晶器保护渣对稳定薄板坯连铸工艺、扩大薄板坯连铸品种、提高铸坯表而质量和产量以及减轻操作难度有着十分重要的作用。
可以说,薄板坯连铸能达到目前的水平是与结晶。
器保护渣技术密不可分的。
因此,结晶器保护渣技术作为薄板坯连铸技术的重要组成部分,必须下大力量进行开发研究,使之符合薄板坯连铸工艺的要求。
二、概念(1)连铸:连续铸钢(英文,Continuous Steel Casting)的简称,把钢水直接浇注成形的先进技术。
(2)保护渣:由基料、熔剂和熔速控制剂混合而成的具有绝热保温、隔绝空气防止钢水二次氧化、净化钢渣界面吸附钢液中夹杂物和润滑凝固坯壳并改善凝固传热作用的粉状或颗粒状物料。
(2)结晶器:用于结晶操作的设备。
一种槽形容器,器壁设有夹套或器内装有蛇管,用以加热或冷却槽内溶液。
三、炼钢连铸工艺流程目前炼钢方式主要有两种【3】: 电炉炼钢和转炉炼钢。
下面以转炉炼钢为例,介绍其炼钢工艺及起重设备。
转炉炼钢及板坯连铸工艺流程分为铁水冶炼钢水初炼、钢水精炼及板坯连铸三大阶段,包括原料( 铁水、废钢)供应、铁水预处理、转炉内吹炼、炉外精炼、钢水运送、钢渣运送处理、钢水连续浇铸( 连铸) 、铸坯输送搬运等过程。
1) 铁水冶炼钢水初炼阶段: 转炉炼钢用铁水通过铁水罐车运输到加料跨,经过铁水预处理后,由铸造起重机将铁水兑入转炉,并由加料跨加料起重机将部分废钢倒入转炉后进行冶炼。
2) 钢水精炼阶段: 冶炼好后将初炼好的钢水倒入钢水罐,再经过钢水炉外精炼后经铸造起重机将钢水吊至炉外精炼设施处进行二次精炼,然后钢水接受跨铸造起重机将钢水罐吊运到大包回转台。
3) 板坯连铸阶段: 连铸过程是指大包回转台回转180°将钢水罐中的钢水流放到中间罐,中间罐将钢水分流到连铸机,连铸机铸出的钢水经过结晶器二冷区铸成铸坯,钢坯在铸坯辊道上经过切割,形成定尺铸坯,然后由板坯夹钳起重机( 或电磁挂梁、料耙起重机) 将铸坯运送到铸坯跨进行存放贮存。
四、连铸结晶器保护渣的作用连铸结晶器保护渣在钢水而上形成二层结构【4】,即粉渣层一烧结层—液渣层,这三层结构对连铸坯的表而及内部质量有决定性的影响,是影响连铸机生产效率的一个重要因素.结晶器保护渣在连铸生产中具有如下作用:防比结晶器内钢液的二次氧化;在结晶器内钢液表面形成一绝热层,防比结晶器内钢液表而的凝固;吸收结晶器内钢液中上浮的夹杂物,提高结晶器内钢液的纯净度;在结晶器壁和铸坯凝固壳的间隙形成均匀的润滑层,防比产生粘结性漏钢事故;改善铸坯凝固壳与结晶器壁的传热,减少铸坯的表而缺陷.选择和应用合理的结晶器保护渣,使它们的物理、化学性质和热力学、动力学性能达到最佳,既可减少连铸坯表而的缺陷,又可防比连铸生产过程中的粘结漏钢事故。
五、薄板坯连铸技术的特点及对结晶器保护渣的要求①拉坏速度快(3m/min-6m/min)单位时间内注入结界l器内钢液量大【5】,结晶器内钢液搅拌比较强烈,液而稳定性差,容易引起铸坯表面和皮下夹渣及裂纹的产生,同时,结界,器内钢液而上熔渣厚度难以保持均匀;在拉速很高时,山结晶器坏壳厚度薄,如拉坏阻力过大,铸坏易山现横裂。
②铸坏厚度薄(40-60mm或70-90mm )在同等拉速条件卜,结晶器热流大,产生纵裂的倾向增大,而且浸入式水口形状受到限制,易造成钢水液而‘搭桥”以及结晶i器壁各处温度分布小均匀和流股强烈冲刷,使凝固坏壳小均匀,易产生裂纹;结晶器内钢水表面积小,熔渣吸附夫杂物机会小。
③结晶I器冷却强度高(10℃/s~1000℃/s)钢液凝固速度快,结晶器液面温度低,保护渣更容易形成渣圈并聚集或从钢水吸热而造成液面结壳,铸坏产生衣而和皮卜夫济以及皱皮等缺陷;而且冷却速度快,结晶器热流密度大,但导热小均匀,铸坏会产生裂纹。
④衣面积/体积大(50mmx (800-2000)mm薄板坏为1.03一1.06)浇铸的铸坏中的夫杂物更接近于表面;由于连铸薄板坏衣而积大,弯月而区域相对增加,阻碍了夫杂物的上浮;需润滑铸坏衣而积也增加,因此,保护渣消耗量要相应多些;与结晶i器壁接触而积大,钢液散热快,温度下降快,容易造成钢液而结壳。
⑤拉速变化范围宽,幅度大(见图1)拉速波动,容易使铸坏产生夫济和漏钢;要求保证单位时间内的保护渣供应,否则会使润滑或传热不均匀,造成铸坯表面缺陷。
图1拉坯速度变化过程从上可以看出,薄板坯连铸所呈现的每一个技术特点及造成的影响,均与结晶器保护渣有直接的关系。
为了实现最佳操作性能和获得满意的产品质量,薄板坯连铸结晶器保护渣必须满足如下要求:(1)成渣速度快,能够及时补充液渣的快速消耗,在高速铸造或拉速变化较大的情况,仍能维持足够的保护渣消耗量。
(2)结晶器壁与坯壳间的渣膜厚度适宜且分布均匀,防}卜坯壳与结晶器壁直接接触,以降低摩擦力并使结晶器散热均匀化,防止裂纹的产生及粘结漏钢,避免铸坯产生表面缺陷。
(3)足够的熔渣层厚度,防比高速连铸或拉速的较大波动时,熔渣供应不足以及固体渣颗粒流入。
(4)稳定的操作性能,具有良好的溶解吸收夹杂物,改善钢液纯净度的能力,同时不会由于液渣在结晶器内成分或温度变化呈现大的物理性能波动。
(5)控制传热,对于易裂钢种,具有一定的析晶能力,增大热阻,防比热流过大引起的坯壳不均造成应力集中。
(6)良好的绝热保温作用,防比结壳,减少弯月而渣圈的形成。
六、结晶器保护渣的成分结晶器保护渣的主要化学成分是CaO, SiO2, Al2O3, Na2O, CaF2 和炭颗粒.保护渣中的炭颗粒有分离液滴、降低保护渣的熔化速度、提高保护渣的绝热能力的作用。
加入Na2O 和CaF2 可调节保护渣的熔化速度和粘度。
保护渣的熔化速度决定保护渣的性能发挥, 控制着液渣层的厚度, 所以提高保护渣的熔化速度可以采取如下措施:(1)减少保护渣中C 的含量;(2)改变保护渣中C 的类型;(3)降低保护渣的熔化温度;(4)提高浇铸速度。
6.1 保护渣的碱度[ m( CaO) / m( SiO2) ]碱度是保护渣的一个重要理化指标, 它会改变保护渣的粘度和熔化温度, 根据CaO- SiO2 - Al2O3 相图可知, 位于碱度为1.0~ 1.2 范围,熔点变化较平坦. 当碱度小于1 时, 随着碱度的增加, 保护渣的熔化温度增加较快( 如图2) 。
图2碱度对熔化温度的影响保护渣的碱度在1.0~ 1.2 范围内较合适。
另外, 碱度过高, 在浇铸过程中, 对石英质水口侵蚀比较严重, 易使铸坯造成硅质夹杂。
6.2 保护渣中的Al2O3由于Al2O3 能够提高保护渣的粘度( 如图3) , 而我厂生产的Q235钢中,Al2O3 含量波动范围较大, 所以在浇铸过程中保护渣的粘度变化较大. 从我厂使用的各种保护渣来看, 保护渣中Al2O3 含量较高, 在浇铸后期随着保护渣吸收Al2O3 量的增加使保护渣吸附夹杂的能力减弱, 铸坯表面出现夹杂物较多, 严重影响了板坯的质量合格率. 从现场生产来看, 保护渣中Al2O3 小于3%较合适. 为了能使保护渣对Al2O3 等脱氧产物有较好的吸收, 在浇铸过程中, 随着渣中Al2O3 的富集, 可以采用结晶器换渣操作。