汽车覆盖件成形的有限元模拟及模具设计
车顶盖汽车覆盖件模具设计

多目标优化的汽车覆盖件的设计——汽车顶盖模具设计本文以建模软件Pro/E和冲压仿真分析软件Dynaform为工具,以典型汽车覆盖件(车顶盖)为例,应用计算机对产品进行三维建模及仿真计算冲压模具工作过程,通过分析结果,验证模具设计是否合理,防止起皱、拉裂等不良现象。
实践证明,采用冲压仿真分析软件DYNAFORM对汽车覆盖件成形过程进行模拟,并根据仿真结果进行冲压工艺规划和模具的设计,可以降低成本,缩短生产周期,提高模具的设计质量。
主要讲述仿真分析技术在汽车覆盖件模具制造中的实际应用。
探讨了虚拟制造技术在汽车模具制造中的重要性和优势,提出了虚拟制造技术在汽车模具开发领域的应用。
在简单介绍了虚拟制造的原理及其组成部分后,对其在汽车覆盖件模具制造中的应用给出了详细说明,重点介绍了在汽车覆盖件模具制造中如何使用虚拟制造技术,给出了应用的一般流程,并对其中的关键技术和难点技术给予了详细说明。
1绪论1.1汽车覆盖件的概念与特点1.1.1汽车覆盖件的概念汽车覆盖件(以下简称覆盖件)是指构成汽车车身或驾驶室、覆盖发动机和底盘的薄金属板料制成的异形体表面和内部零件。
轿车的车前板和车身、载重车的车前板和驾驶室等都是由覆盖件和一般冲压件构成的。
覆盖件组装后构成了车身或驾驶室的全部外部和内部形状,它既是外观装饰性的零件,又是封闭薄壳状的受力零件。
覆盖件的制造是汽车车身制造的关键环节。
覆盖件的分类:(1)按功能和部位分类:可分为外部覆盖件、内部覆盖件和骨架类覆盖件三类。
外部覆盖件和骨架类覆盖件的外观质量有特殊要求,内部覆盖件的形状往往更复杂。
(2)按工艺特征分类:(a)对称于一个平面的覆盖件。
诸如发动机罩、前围板、后围板、散热器罩和水箱罩等。
这类覆盖件又可分为深度浅呈凹形弯曲形状的、深度均匀形状比较复杂的、深度相差大形状复杂的和深度深的几种。
(b)不对称的覆盖件。
诸如车门的内、外板,翼子板,侧围板等。
这类覆盖件又可分为深度浅度比较平坦的、深度均匀形状较复杂的和深度深的几种。
汽车覆盖件冲压成形的数值模拟

汽车覆盖件冲压成形的数值模拟作者:王家昆李琦胡东勇罗英李再参一、引言对于制造业来说,21 世纪竞争的核心将是新产品的竞争。
围绕新产品的竞争,一场以信息技术为特征的新的制造业革命正在全球波澜壮阔地展开。
如何实现高质量、低成本、短周期的新产品开发,是赢得这场竞争的关键。
汽车覆盖件与一般薄板拉伸件相比,具有材料相对厚度小、结构尺寸大、形状复杂、尺寸精度和表面质量要求较高的特点。
其零件大多是由复杂的空间自由曲面组成,成形时,坯料上各部分的变形复杂、差别较大,各处应力也很不均匀,使零件的冲压工艺性较差,拉伸过程中容易产生起皱或破裂现象。
车身覆盖件的成形过程涉及几何非线性、材料非线性和复杂的接触与摩擦等问题,在传统的冲压生产过程中,无论是覆盖件模具的设计、制造,还是坯料形状和尺寸的确定,冲压工序、工艺参数的规划,都要设计制造原型,经过多次试生产和多次调试修正才能确定,这是一个试错逼近的过程,造成人力、物力和财力的大量消耗,生产成本高,周期长,质量不易控制。
随着计算机技术的不断发展,计算机辅助工程(CAE) 已广泛应用于板料成形过程分析,不仅可用于后期的工艺分析及模具设计,也可用于产品设计阶段,以确保零件具有较好的冲压成形工艺性。
预先在计算机上进行实际生产过程模拟,可在计算机屏幕上观察毛坯的成形过程,预示汽车覆盖件零件冲压成形的可行性,然后通过少量试模验证,就可得出较可靠的可行性结论。
现使用法国ESI 公司开发的PAM-STAMP 2G商业化专业板料冲压成形软件对汽车后盖内覆盖件进行冲压模拟分析。
二、数值模拟1、PAM-STAMP 2G软件简介PAM-STAMP 2G软件的新的系统框架可以在各模块之间进行无缝数据交换,还提供了可以客户化的应用程式编程界面。
PAM-DIEMAKER 通过参数迭代的方法获得实际的仿真模型,能在几分钟内生成模面和工艺补充面,并快速分析判断零件有无过切(负角) ,并计算出最佳的冲压方案,然后可非常简单地对模面和工艺补充面的几何形状进行修改,并参数化地完成所有前期模具设计的控制。
汽车覆盖件成形数值模拟与模具型面设计
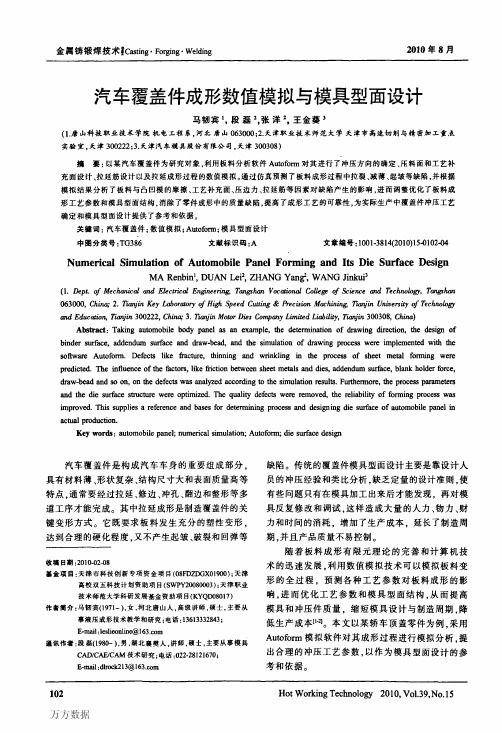
上半月出版Casting·Forging·Welding《'金属铸锻焊技术如图1l所示。
由图lO可以看出,制件拉延效果比较理想,表面未见拉裂现象,板料成形充分,流人均匀,四角处的起皱现象明显改善.产品上的褶皱已经消除。
另外,对于顶盖这类汽车外覆盖件,为了保证产品具有足够的刚性。
除了不能有成形缺陷外。
产品表面的主、副应变也必须达到要求,图11主应变均大于0.02,副应变均大于0,满足要求。
由此可以得出。
最终修改方案所设计的压料面、工艺补充和压边力大小是合理的,能够作为模具型面设计的参考和依据,在UG中设计的模具型面如图12所示。
图ll主应变和副应变Fig.11Majorstrainandminorstrain图12模具型面Fig.12Diesurface利用模拟分析的结果设计制造了顶盖冲压成形模具,并已投入生产使用。
板料成形过程与CAE模拟成形基本一致,证明模拟分析结果对板料成形具有指导意义。
得到的顶盖冲压件实物如图13所示。
4结论图13冲压件实物图Fig.13Actualpressingpanel(1)汽车覆盖件冲压成形是一个复杂的塑性变形过程,而模具型面设计是拉延模设计的关键。
在模具设计初期,利用数值模拟软件对覆盖件零件模型的压料面和工艺补充面进行参数化设计,并模拟拉延成形的全过程,及时预测零件拉裂、起皱等缺陷的部位,分析缺陷产生的原因。
为调整优化工艺参数,完善模具型面设计方案提供依据。
(2)通过获得合格零件。
验证了工艺方案和模具设计的合理性、仿真计算的准确性.提高了冲压工艺和模具设计质量。
在模具设计中应用数值模拟技术,实际上是对模具设计方案的评估优化过程,不仅可以减少实际试模修模次数.还可以缩短模具开发周期,降低模具生产成本。
提高产品品质和市场竞争力。
参考文献:【l】林忠钦.车身覆盖件冲压成形仿真嗍.北京:机械工业出版社.2005.【2】雷正保.汽车覆盖件冲压成形CAE技术嗍.长沙:国防科技大学出版社。
汽车覆盖件冲压成形非线性有限元仿真分析及质量管理

车辆工程技术29车辆技术1 绪论1.1 引言 随着计算机技术及有限元技术的发展,应用数值仿真方法对板料成形过程进行计算机模拟,以替代实际试模,为覆盖件工艺设计、模具设计提供可靠的判据和合理的工艺参数, 已成为当前覆盖件工艺设计、模具设计中一种重要手段。
通过在Auto-Form软件中对某汽车覆盖件进行冲压仿真, 阐述了实现板料成形有限元仿真的基本步骤和仿真分析过程中的一些关键技术问题, 为实际的汽车覆盖件模具冲压成形的优化提供了参考。
1.2 汽车覆盖件冲压技术及其进展 汽车覆盖件主要是指覆盖汽车发动机、底部、驾驶室和车身的用金属薄板冲压形成的表面零件和内部零件。
与一般冲压件相比,汽车覆盖件具有材料薄、形状复杂、自由曲面多、结构尺寸大以及表面质量要求高等特点。
1.3 覆盖件制造工艺流程管理分析 拉延模具开发的关键是模具型面的设计,模具冲压工艺的设计很大程度上依赖于经验,为了避免修模时补焊,生产中一般都采取比较保守的设计原则,造成了后序较大的修模余量,这不仅增加了修模的难度和强度,而且每修模一次,卸、安装模具也要耗费大量时间,使得模具的开发周期和成本难以降低。
1.4 课题的主要研究内容和目的 (1)利用工业工程的相关管理模块对覆盖件模具制造工艺流程进行了初步的设计管理,探讨了在工艺设计流程中,有限元仿真技术在现代设计中的作用。
(2)利用所建立的CAD模型,参照实际生产中的工艺参数,完成前壁板拉延成形过程中成形缺陷的重现,分析缺陷的形成原因和主要影响因素。
(3)针对缺陷的形成原因,以消除破裂和起皱为主要优化目标。
2 车身覆盖件冲压成形非线性有限元仿真理论2.1 概述 冲压成形是一个多重非线性问题,不仅是几何非线性,而且是材料(物理)非线性,需要同时对几何非线性,材料非线性和接触非线性进行分析。
2.2 覆盖件冲压成形理论2.2.1 拉伸失稳理论 拉裂是薄板冲压成形工艺过程中常见的失效形式,从宏观上来说,它是材料拉伸失稳的表现。
汽车覆盖件模具设计

覆盖件冲压工艺方案制定又称工法设计,简称DL设计。工法图也称DL图。
覆盖件的主要冲压工序有: 落料、拉延、整形、修边、切断、翻边、冲孔等,其中最关键的工序是拉延
工序。绝大多数覆盖件通过拉延工序得到全部或部分形状。确定拉延工艺方案是 覆盖件冲压分析的第一步。
汽车覆盖件模具设计 ppt 课件
工艺分析的概念
绝大多数覆盖件由3到5套模具冲压得到,即3到5道冲压工序 ,以下是常见 的几种工序排布方案:
1、拉延(DR)→修边冲孔(TR+PI)→整形(RST) 2、拉延(DR) →修边冲孔(TR+PI) →整形(翻边)(RST)→整形 (侧整、侧修、侧修)(RST+CTR+CPI) 3、落料(BL)→拉延(DR) →修边冲孔(TR+PI) →整形)(RST) → 整形)(RST)
顶盖前横梁没有翻边,形状不复杂,不需要整形。其有两处翻孔,翻孔的工 艺应考虑为先冲孔再翻孔。综上所述,顶盖前横梁应有三道工序:拉延→修边冲 孔→翻孔。考虑到冲孔较多,如果在第二序修边时冲完所有的孔,模具设计有困 难,上模没有足够的空间来布置弹簧、导板、限位螺栓等,模具强度弱,所以应 移一部分孔到3/3工序。
中文 废料 基准侧 公差 CAD数据 刃口间隙 让空 冲压 粗加工 下模重量 上模重量 总重量 冲压方向 送料行程 双凸轮 水平凸轮
英文 UPPER DIE BASE MATCH FACE TRIM STEEL FL UP FL DOWN MATERIAL FINISH CONCAVE CONVEX DIE HEIGHT FEED LEVEL PUNCH RETAINER START POINT PART DRAWING CHECKING FIXTURE
汽车覆盖件数值模拟与拉延模设计

汽车覆盖件数值模拟与拉延模设计汽车覆盖件(简称覆盖件)是指覆盖汽车发动机、底盘、构成驾驶室和车身的薄钢板异形体的表面零件(外覆盖件)和(内部零件),与一般冲压件相比较,具有材料薄、形状复杂、结构尺寸大、表面质量要求高及生产成本高等特点。
在覆盖件的冲压工艺设计、模具设模具制造工艺上,也具有独自的特点【1】,一般需要经过多道工序(如拉延、冲孔修边、翻边、整形等)才能完成。
在其整个生产中,拉延成形则是一道关键的工序,而决定拉延成败和工件质量的,则是拉延成形的模具。
以前采取单件压制,生产效率、材料利用率和设备利用率均比较低。
将拉延工艺作了改进,采用中心对称一模两件的方法重新设计和制模,大大提高了设备利用率和生产效率[2]。
1冲压工艺分析(1)rember冲压工艺rember零件的材料为cr340,板料厚度为1mm, 抗拉强度750 mpa,延伸率16% 。
零件的结构外形如图1所示。
该零件的结构复杂,需要经过多道工序才能完成,根据该工件的工艺分析,工艺路线为:落料→拉延→冲孔、修边→cam修边→翻制→冲孔、分离。
具体工序图如图2所示。
该零件局部成形较多,是冲孔、拉延和翻边、修边复合的结果。
在拉延过程中,采用一模两件对称方式进行拉延,为保证能将拉延件的全部空间形状一次拉延出来,不应有凸模接触不到的“死区”,即既要保证凸模能全部进入,尽量使拉延深度差最小,以减小材料流动性和变形分布的不均匀性。
工艺补充是拉延工艺不可缺少的部分,但工艺补充部分应尽量减少,以提高材料的利用率。
工艺补充部分除考虑拉延工艺和压料面的需要外,还要考虑修边和翻边工序的要求。
该工件的工艺补充面和垂直修边线如图3所示:(2)拉延仿真结果与成形性分析。
拉延仿真选用的材料与上面相同,板坯尺寸为920mm×200mm,摩擦系数为0.1,压边力初定为95kn,冲头速度5000mm/s,在定义好模具各部分运动和边界条件后,提交工作到ls-dyna进行计算。
试析基于有限元分析的汽车覆盖件模具设计方法

试析基于有限元分析的汽车覆盖件模具设计方法摘要:计算机硬件性能和软件设计能力的提高,信息技术的发展特别是弹塑性有限元模拟技术的进步,让CAE技术(计算机辅助工程技术)在汽车工业中获得了广泛地应用,该技术主要以数值模拟技术为核心,它在促进产品设计的不断改进中发挥中了非常重要的作用。
基于有限元分析的汽车覆盖件模具设计不仅具有非常好的设计可靠性,还具有很好的模具设计效率。
关键词:有限元汽车覆盖件模具设计1 有限元有限元有效融合了计算方法、力学理论以及计算机技术等三门学科的理论知识,但是它不是三者的简单相加,而是具有自己理论基础与解题方法的新学科。
有限元特别适合用于解决工程技术问题,因为相对于其他方法具有高效、快速、灵活等优点,因而获得了非常快的发展。
最开始,有限元主要的目的是分析飞机结构中的应力问题,但是随着它逐渐被其他领域所认可,其应用范围已经囊括了生物力学、流体场、固体力学、电磁场、声场以及温度场等诸多领域的数理方程;同时,它的计算机程序基本上可以对数理方程中的所有问题进行求解。
目前,有限元已经成为一种非常通用的解数理方程的数值计算方法。
在进行实际工程技术问题求解的过程中,构建基本方程和确定边界条件不是很苦难,但是因为材料特点、外部荷载以及不规则的几何形状,求解的过程则比较麻烦。
所以,选择求近似解则是比较恰当合理的。
其中有限元方法便是一种应用非常广泛的近似算法。
有限元法将求解区域视为由众多在节点部位连接的较小单元(子域),数学模型会提供基本方程的单元(子域)近似解。
同时,每一个单元(子域)均能够被划分为形状各异、大小不同的区域,因而有限元法对复杂材料特性、边界条件以及几何形状等均有着非常好的适应能力。
更为重要的是,有限元方法背后有着成熟稳定的大型的软件系统作为平台,使其具有高效、快速、灵活等优点,因而获得了非常快的发展。
2 汽车覆盖件成形的模拟及其模具设计汽车覆盖件成形的模拟及其模具设计的大体流程如下:①利用CAD软件对覆盖件进行造型设计→②将vda、iges、stl、fs等格式的文件传入到软件中,利用CAE技术(计算机辅助工程技术)进行如下操作,第一,对修改圆角补充孔、网格、缝隙等进行划分;第二,确定汽车覆盖件的冲压方向,并对模具、设计工艺补充面以及设计压料面等进行确定;第三,布置拉伸筋、明确工艺切口;第四,对拉伸工步以及有关工艺参数进行分析确定;第五,进行有限元模拟,如果成形有缺陷,则再返回第一步重新进行操作,如果成形没有缺陷则进行第③步→③将模具的几何信息以数据文件的形式传入CAM软件当中,同时编制出NC代码用来制造模具。
有限元数值模拟在汽车覆盖件及其模具中的应用

有限元数值模拟在汽车覆盖件及其模具中的应用汽车覆盖件与模具有效利用有限元数值模拟1、有限元模拟理论有限元法是一种基于有限元技术的有效工程模拟方法,它可以把工程中的任何确定系统表达为一个有限元网,对整体系统力学进行模拟分析。
当计算的网的大小是很大的时候,有限元技术可以把采用的解运算时间和所需要的内存资源减少了非常多,可以大大提高解算机的性能和可靠性。
2、汽车覆盖件与模具有限元应用汽车覆盖件是承载力和装入效率的重要要素,而模具是汽车覆盖件工业化制造的重要部件。
汽车覆盖件与模具的有限元模拟,可以模拟出它们的力学性能、热传导性能及流体传质等特性,及时发现新的问题、优化设计、提高安全性和可靠性,减少实验成本。
3、汽车覆盖件有限元应用的优势(1)首先,有限元模拟技术可以明确汽车覆盖件形状及特征尺寸,有助于提高鲁棒性。
(2)其次,有限元模拟可以进行项目仿真分析,改善项目的复杂性、提高安全性和可靠性,明确加工参数,提高加工质量。
(3)再次,有限元模拟可以优化模具设计,改善汽车覆盖件加工工序,降低生产成本。
4、汽车覆盖件有限元技术的不足(1)由于不同系统模型复杂,模型建立会比较困难,且受到有限元理论技术发展水平、模拟计算机软硬件能力及工程师经验等方面的影响,计算结果不一定比传统数学方法更佳。
(2)此外,尽管可以对多体系统进行模拟,但较易模拟大型动力系统的受力平衡问题,而较难模拟小型动力系统的位移运动问题。
总之,汽车覆盖件与模具有限元数字模拟工艺在模具设计和制造中得到了广泛的应用,形成了一个高效的汽车覆盖件制造和加工流程。
未来,这种模拟技术将进一步拓展,并将继续改善汽车覆盖件与模具制造、优化设计及提高加工质量,为国内外汽车覆盖件行业发展做出重要贡献。
汽车覆盖件成开工艺及模具设计方案

3
6.1.2覆盖件的成形特点
1.成形工序多:拉深为关键工序; 2.拉深是复合成形 :常采用一次拉深; 3.拉深时变形不均匀:工艺补充、拉深筋; 4.大而稳定的压边力:双动压床; 5.高强度、高质量、抗腐蚀的钢板; 6. 覆盖件图样和主模型为依据。
4
6.1.3覆盖件的成形分类
汽车覆盖件的冲压成形分类以零件上易破裂或起皱 部位材料的主要变形方式为依据,并根据成形零件的外形 特征、变形量大小、变形特点以及对材料性能的不同要求
13
图6.1.5 拉深深度与拉深方向
14
a)
b)
c)
d)
图 6.1.6 凸模开始拉深时与拉深毛坯的接触状态示意图
15
2.修边方向的确定及修边形式 (1)修边方向的确定 所谓修边就是将拉深件修边线以外的部分切掉。 理想的修边方向: 是修边刃口的运动方向和修边表面垂直。 (2)修边形式
修边形式可分为垂直修边、水平修边和倾斜修边三种,
③当拉深件的法兰面为复杂曲面形状时,还可以在法 兰面上标注上凸、凹模和压料圈型面按工艺模型仿制、配 研的技术要求。
29
6.2.3 拉深、修边和翻边工序间的关系
覆盖件成形各工序间不是相互独立而是相互关联的, 在确定覆盖件冲压方向和加工艺补充部分时,还要考虑修 边、翻边时工序件的定位和各工序件的其它相互关系等问 题。
致局部大的胀形变形而开裂。 位置: 开裂主要发生在圆角部位,开裂部位的厚度变薄很大如
凸模与坯料的接触面积过小、拉深阻力过大等都有可能导致 材料局部胀形变形过大而开裂 。
防裂措施: 为了防止开裂,应从覆盖件的结构、成形工艺以及模具设 计多方面采取相应的措施。
8
(1) 覆盖件的结构上,可采取的措施有: 各圆角半径最好大一些、曲面形状在拉深方向的实际深度 应浅一些、各处深度均匀一些、形状尽量简单且变化尽量平缓 一些等。 (2)拉深工艺方面,可采取的主要措施有: 拉深方向尽量使凸模与坯料的接触面积大、合理的压料面 形状和压边力使压料面各部位阻力均匀适度、降低拉延深度、 开工艺孔和工艺切口等 (如图6.1.3)。 (3)模具设计上 可采取设计合理的拉深筋、采用较大的模具圆角、使凸模 与凹模间隙合理等措施。
%90元分析的汽车覆盖件模具设计及优化

""锻压技术"&##0年"第!期基于有限元分析的汽车覆盖件模具设计及优化徐金波$"董湘怀!华中科技大学塑性成形模拟与模具技术国家重点实验室0$##)0"""摘要!介绍了静力隐式弹塑性有限元板料成形软件>M ,N Q N C F 的基本理论和关键技术#利用>M <,N Q N C F 软件实现了汽车覆盖件模具设计$包括模具压料面%工艺补充面以及拉延筋设计$完成了覆盖件成形过程模拟及优化$改变了传统的在有限元模拟后依靠1>=软件频繁进行模具修改的方法#在有限元软件内部实现了模具的参数化设计$既缩短了模具设计时间$又提高了模具设计可靠性#关键词!覆盖件"模具设计"优化设计"静力隐式"有限元!62-J 1,140/5-+-c ,5-010;5:6/30A 622,144-62;035:6,@50+07-.67048/,16.7,26401;-1-566.6+615,1,.82-2K @&-170"!01J K -,1J:@,-!X M E e L N .B Y .A Z /C +A ,H N *+K A /.K /E .O3/K L .N G N B H"""#7253,A 5&5.,L A +S E S /C $,L //G E +,A K <S G E +,A K *A .A ,//G /F /.,F /,L N O E .O b /H ,/K L .A K E G [E +/O N .+,E ,A K A F S G A K A ,+K L /F /*N C ,L /+A F M G E ,A N .N *,L /*N C F A .BS C N K /++N *+L //,F /,E G E C /A .,C N O M K /O @3L /O /+A B .N *,L /O A /+*N C ,L /E M ,N <F N [A G /[N O H S E ./G $A .K G M <O A .B ,L /O /+A B .N *,L /[A .O /C +M C *E K /$E O O /.O M F+M C *E K /E .O O C E ][/E O $E .O ,L /+A F M G E ,A N .+N *,L /*N C F A .B S C N K /++N *,L /E M ,N <F N [A G /[N O H S E ./G E C /A F S G /F /.,/O]A ,L ,L /S C N B C E F>M ,N Q N C F $]L A K L K L E .B +,L /,C E O A ,A N .E G F /,L N O ,L E ,.//O +*C /U M /.,F N O <A *A K E ,A N .N *,L /O A /+]A ,L E1>=+N *,]E C /E *,/C *A .A ,//G /F /.,+A F M G E ,A N .@V E C E F /,/C A e /O O /+A B .N *,L /O A /A +C /E G A e /O A .,L /*A .A ,//G /F /.,+N *,]E C /$]L A K L +L N C ,/.+,L /O A /O /+A B .A .B ,A F /E .O A .K C /E +/+,L /C /G A E [A G A ,H N *,L /O /+A B.@M 68I 0342&?/,E G +L //,*N C F A .B "=A /O /+A B ."P S ,A F M FO /+A B ."6,E ,A K <A F S G A K A ,"Q A .A ,//G /F /.,F /,L N O 男$&"岁$硕士研究生收稿日期&&##$<#!<!)一!引"言近年来$板料成形的数值模拟已经成为汽车工业的一个强有力的工具#目前大型汽车企业及其供应商广泛地将这一技术应用到产品设计周期中$用以加速和改进产品设计#在汽车设计过程中$成形模拟用于检查零件的几何模型$预测开裂%起皱%回弹等缺陷$优化工艺参数$提高零件的成形工艺性#但是目前大多数的1>=’1>7’1>?系统的集成度不是很高#在1>7和1>=之间$设计人员要不断地进行分析和修改$直到产品的工艺性合格为止$这使得整个开发周期仍旧较长$远远没有发挥出它的优势#并行工程概念的提出就是为了解决这一问题$它主要针对产品的设计过程#目前有些学者提出了面向制造的设计!=Q ?"$强调设计人员在产品设计阶段考虑制造因素$利用计算机辅助技术等工具$进行协同设计$以达到提高产品设计质量$缩短产品开发周期的目的#但是这些先进概念的实现应该有具体的技术支持$通用的1>=软件主要用于产品的建模$大多数1>7软件主要集中在有限元模拟分析中$放弃了设计环节$只是提供一些与其他1>=软件进行数据文件交换的接口#这样在有限元分析后$对模具提出的许多修改都需回到1>=软件中进行#尽管1>=软件的造型功能很强大$有限元分析的技术也很先进$但还是没有完全实现并行设计或=Q ?#为了加快覆盖件模具设计$需要将1>=和1>7集成起来$发挥各自的优势#目前在很多企业使用的板料成形分析软件主要有美国的=H .E Q N C F %瑞士的>M ,N Q N C F %法国的V >?63>?V ’P V <$%3956等!他们的一个共同点是将必要的1>=设计和1>7分析进行了集成!先在通用1>=软件上设计产品模型"随后将模型导入1>7系统"对曲面模型进行网格剖分"设计冲压工序件模型"然后制定冲压工序"定义工具"进行有限元分析!分析后再利用优化程序优化模具"最后得到合理的模具结构以及工艺参数!本文针对静力隐式算法"论述了>M,N Q N C F采用的基本理论和几个关键技术"并利用典型的例子"说明了应用板料成形模拟进行汽车覆盖件模具设计及优化的过程!二!基本理论和关键技术N O虚位移原理在拉延和胀形成形中"主要有两种弯曲作用#一是在材料的流动区域内的弯曲!这里材料的流动在新的时间增量步中"节点由不平衡位置到平衡位置的过程!与纯弯曲变形相比"流动区域内的变形主要沿流动方向进行"形状的细小变化对流动本身基本没有影响"所以三维的板成形过程的弯曲作用是次要的!二是当材料流过一定的圆角部分时"流入圆角时的弯曲和流出时的反弯曲!弯曲作用使得拉伸抗力增大"这种影响在拉延成形中尤其重要!如果忽略弯曲效应"材料流动地迭代的虚位移原理可以用下式表示#.W?C K(’!.(?#+O!(.W?C’!"?#+O!$!%式中".WC&&&中面单元节点的切向虚位移K&&&对应节点力!&&&单元面积?&&&材料厚度(&&&应变张量5&&&应力张量"&&&单元的位移W应变关系矩阵!如果考虑弯曲效应"就不能忽略壳单元的弯曲变形能!由I A C K L L N**假说"壳体中质点的虚位移与其距中面的距离J成正比"即#.W$J%($X4J6%?.W C$&% ""于是虚位移原理可以写成#.W?C K(.W?C’!’J$X4J6%?"$J%?#$J%O J O!$$%式中"X&&&单元张量’7&&&节点的曲率张量$由每一次迭代时的当前几何形状重新确定%!P O非线性方程的解耦求解算法>M,N Q N C F采用了隐式的积分方法"同显式积分算法相比"没有人为引入的惯性效应"计算精度可靠"允许采用较大的时间步长!但是在每一时间增量步中"需要形成大型稀疏刚度矩阵"进行反复的平衡迭代"存在迭代收敛问题"特别是像板料成形这样高度非线性的壳问题"收敛问题尤为突出!考虑到板料法向的弯曲刚度和切向的膜刚度相差几个数量级"为了加快计算实现收敛">M,N Q N C F采用了对非线性方程组解耦的求解算法!首先"在每一个新的时间步长"根据由模具当前的位置决定的边界条件确定板料的形状!板料与模具接触部位的形状由模具确定"其他区域可以近似的采用一些简单的算法确定!随后"材料在这种确定的形状下流动!这样就很好的解决了迭代的收敛问题!这种把板料的形状的确定和材料的流动解耦处理的算法有以下一些优点#$!%计算非线性材料流动迭代时"每一个节点处只有沿板料切向的两个平移自由度!而通常的壳单元"每个节点有%个自由度!由于线性方程直接求解法的计算量是和自由度的$次方成比例的"解耦算法和非解耦算法的计算量比率是"i&!%!$&%解耦之后"在板料的平面位置只考虑了高刚度的膜自由度"忽略了低刚度的弯曲自由度"所得到的方程组是线性的!计算高效"占用较小的内存空间"因而迭代解很好的表示了材料的流动!解耦算法的基本公式如下#对每一次的平衡迭代"新的切向坐标系由当前的几何形状确定"如图!所示!线性化的方程组及其求解只是在局部坐标系内进行"不需要进行局部坐标系到全局坐标系之间的变换#V E2C$W#%4V U22$W#%"V E2+$W#%4V U2+$W#%V E+2$W#%4V U+2$W#%"V E++$W#%4V U2+$W#,-./%0W20W9()A*++(-92$W#%K+-9+$W#9()A*+%$0%式中"W#&&&当前的位移.W&&&位移增量9&&&节点残余力K+&&&切向摩擦力V E&&&刚度切向的膜分量V U&&&由初应力引起的刚度分量平衡迭代的目的就是要使节点残余力趋于#!由于刚度矩阵I是一个自由量"它的改变并不影响节点残余力趋于#"也就是说迭代总是收敛的"节点残余力总能够正确地计算出来!如果图!中定义0 %图&"汽车零件拉延结束时的网格通过这种方法!能够在较小的计算时间和内存空间消耗的情况下对复杂的问题进行足够精确的描述%图&所示的例子中!在拉延结束时!网格数量达到最大值!约为&&!###个%如果采用规则的网格!将会接近!##!###个%三!覆盖件成形模拟和模具设计及优化N O覆盖件成形模拟和模具设计流程冲压成形模拟软件>M,N Q N C F包括零件设计#V E C,=/+A B./C$模块&模具设计#=A/=/+A B./C$模块&增量法#5.K C/F/.,E G$模块&逆算法#P./6,< /S$模块&修边#3C A F$模块以及优化模块等%软件提供了诸如指定最小圆角半径!曲面的删除和填充等常用的曲面修改手段’对板坯自动进行网格细分和粗化’对工具的定义&工序的增删十分灵活’可利用它的修边模块和优化模块对模具型面及工艺参数进行优化’在计算进行中!可实时地利用图形显示观察已得到的中间结果!对于各种物理量分布的检查十分简便%图$所示是覆盖件成形模拟和模具设计流程%首先在通用1>=软件上设计产品模型!然后将设计结果通过5476&\=>Q6&2>639>2等格式的文件导入1>7软件!在导入>M,N Q N C F的过程中自动完成曲面网格剖分%如果对最初设计不满意!可以调整零件的边界!填充孔洞&裂缝&修改模具的圆角等%然后选择冲压方向!既可以根据用户的经验和设备情况进行确定!也可以根据最小拉伸深度&%(图0"坯料尺寸的预测!-预测的坯料尺寸"&-拉延筋位置"$-成形后轮廓线0-凹模入口线"(-对称线图("逆算法分析零件的成形工艺性!E"优化前"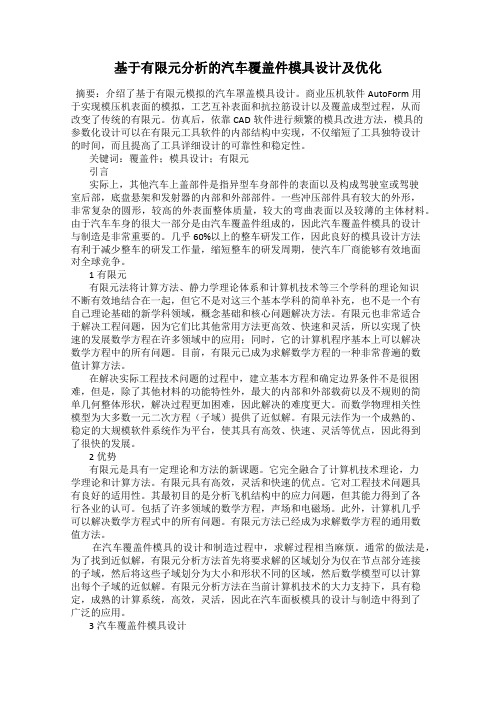
基于有限元分析的汽车覆盖件模具设计及优化摘要:介绍了基于有限元模拟的汽车罩盖模具设计。
商业压机软件AutoForm用于实现模压机表面的模拟,工艺互补表面和抗拉筋设计以及覆盖成型过程,从而改变了传统的有限元。
仿真后,依靠CAD软件进行频繁的模具改进方法,模具的参数化设计可以在有限元工具软件的内部结构中实现,不仅缩短了工具独特设计的时间,而且提高了工具详细设计的可靠性和稳定性。
关键词:覆盖件;模具设计;有限元引言实际上,其他汽车上盖部件是指异型车身部件的表面以及构成驾驶室或驾驶室后部,底盘悬架和发射器的内部和外部部件。
一些冲压部件具有较大的外形,非常复杂的圆形,较高的外表面整体质量,较大的弯曲表面以及较薄的主体材料。
由于汽车车身的很大一部分是由汽车覆盖件组成的,因此汽车覆盖件模具的设计与制造是非常重要的。
几乎60%以上的整车研发工作,因此良好的模具设计方法有利于减少整车的研发工作量,缩短整车的研发周期,使汽车厂商能够有效地面对全球竞争。
1有限元有限元法将计算方法、静力学理论体系和计算机技术等三个学科的理论知识不断有效地结合在一起,但它不是对这三个基本学科的简单补充,也不是一个有自己理论基础的新学科领域,概念基础和核心问题解决方法。
有限元也非常适合于解决工程问题,因为它们比其他常用方法更高效、快速和灵活,所以实现了快速的发展数学方程在许多领域中的应用;同时,它的计算机程序基本上可以解决数学方程中的所有问题。
目前,有限元已成为求解数学方程的一种非常普遍的数值计算方法。
在解决实际工程技术问题的过程中,建立基本方程和确定边界条件不是很困难,但是,除了其他材料的功能特性外,最大的内部和外部载荷以及不规则的简单几何整体形状,解决过程更加困难,因此解决的难度更大。
而数学物理相关性模型为大多数一元二次方程(子域)提供了近似解。
有限元法作为一个成熟的、稳定的大规模软件系统作为平台,使其具有高效、快速、灵活等优点,因此得到了很快的发展。
汽车覆盖件冲压成形仿真有限元方程及其解法
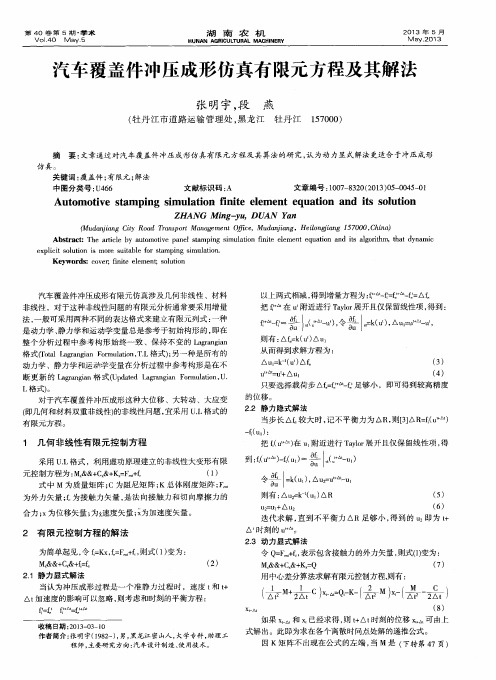
I L J l ( I 】 r L u 『 ) , 令 ( U t ) , △ u I = L u t ,
则有 : A k ( u ) △U
整个分析 过程 中参 考构形始终 一致 、保持 不变 的 L a g r a n g i a n
格式( T o t a l L a g r a n g i a n F o r m u l a t i o n , T . L格 式 ) ; 另 一 种 是 所 有 的
L格 式 ) 。
u t + A t = u + △u l 的位 移 。 2 . 2 静 力 隐式 解 法
( 4 )
只要选择载荷步 Af = f o ' +  ̄ ' - L t 足够小 ,即可得到较高精度
对于汽车覆盖件 冲压成形这种 大位移 、大转 动 、大应 变 f 即几何和材料 双重 非线 性) 的非线性 问题 , 宜采用 U . L格式 的
Au t o mo t i v e s t a mp i n g s i mu l a t i o n i f n i t e e l e me n t e q u a t i o n a nd i t s s o l u t i o n
ZHANG Mi n g- yu ,D UAN Y a n
( Mu d a n j i o  ̄ g C i t y R o M T r a n s p o r t Ma n a g e m e n t O f ic f e , Mu d a n j i a n g ,H e i l o n  ̄i a n g 1 5 7 0 0 0 , C h i n a )
摘
仿 真。
要: 文章通过对 汽车覆盖件 冲压成形仿 真有限元方程及其 算法的研 究, 认 为动 力显式 解法更适合 于冲压成形
汽车覆盖件冲压模具有限元分析

汽车覆盖件冲压模具有限元分析背景在汽车生产过程中,覆盖件的制作是不可避免的步骤,而覆盖件的制作需要用到冲压模具。
冲压模具是以模板、模座、顶针、模芯等为基础设计完成的一种金属制品加工工具,其设计的好坏直接关系到产品成型质量、工艺效率和生产成本。
因此,对于汽车覆盖件冲压模具的有限元分析是必不可少的,可以找出模具在使用中出现的问题并进行改进,提高生产效率和成品率。
有限元分析的具体步骤有限元分析是一种数值分析方法,可以对复杂结构的物体进行分析。
对于冲压模具的有限元分析,具体步骤如下:1.建立有限元模型针对具体的冲压模具进行建模,建立其具体的尺寸和结构。
2.设定模型的边界条件确定模具在使用中需要承受的边界条件,包括外力、初始位移等。
3.进行材料属性分析需要对模具所用的材料进行分析,获取材料的物理特性参数,以便后续分析中使用。
4.进行有限元分析根据建立的有限元模型和设定的边界条件,进行有限元分析,并计算模具在使用中的应力、应变等参数。
5.分析结果根据有限元分析的结果,分析模具出现的问题和需要改进的地方,并作出相应的改进措施。
有限元分析对冲压模具的影响进行有限元分析可以大大提高冲压模具的生产质量和生产效率,具体影响如下:1.提高设计水平有限元分析可以帮助设计者在设计阶段尽早发现模具出现的问题,并加以解决,提高模具的设计水平。
2.减少试错次数进行有限元分析可以有效减少试验的次数,减少了试错的成本和时间,提高了经济效益。
3.提高生产效率通过优化模具设计和改进生产工艺,有限元分析可以提高生产效率,减少了生产成本和生产周期。
冲压模具的常见问题及解决方案在使用中,冲压模具会出现一些常见问题,需要加以解决,具体如下:1.模具容易疲劳在使用一段时间后,模具容易出现疲劳裂纹等问题。
解决方案是在设计中加强模板结构,增加强度和耐磨性。
2.模具易变形在模具加工和使用中易出现变形问题。
解决方案是在设计时采用合适的材料并增加支撑结构。
汽车覆盖件模具设计

汽车覆盖件模具设计汽车覆盖件是轿车外观的重要组成部分。
它们不仅能够使汽车具有特定的风格和外观,而且能够保护汽车的机械和电子部件免受破坏和氧化。
汽车覆盖件的制造需要一系列的模具。
这些模具包括冲压模具、塑料模具和复合材料模具等。
这篇文章将讨论汽车覆盖件模具设计的重要性以及设计模具过程的要点。
汽车覆盖件模具设计的重要性汽车覆盖件模具设计是制造覆盖件的关键环节。
设计合理的模具能够提高生产效率,减少制造成本,提高产品质量。
同时,模具设计也会对生产环境和员工保护产生影响。
设计好的模具可以减小噪音、减少废材、降低工人劳动强度等因素。
设计模具过程的要点1. 前期准备工作在设计模具之前,需要获得有关汽车覆盖件的具体需要和规格要求。
这可能包括颜色、图案、尺寸等。
此外,需要对生产线的计划、技术和生产过程进行评估和优化。
2. 制定详细的模具设计计划首先需要将整个模具设计计划分为三个主要阶段:设计阶段、制造阶段和装配阶段。
接下来,需要确定每个阶段需要的人力物力财力资源以及时间表。
3. 选择合适的材料和制造工艺在选择材料和制造工艺时,需要考虑一些重要因素。
首先,需要选择材料和工艺以确保模具具有足够的耐久性,从而确保模具能够承受大量生产和加工。
此外,需要考虑成本因素,并尝试降低生产过程中废品的量。
4. 进行模具的机械结构设计在进行机械结构设计时,需要考虑到模具的各个部分,例如把手、锁定装置和各种连接件的尺寸和形状等方面。
机械结构的设计必须满足具体的制造和加工要求。
5. 进行模具的电气控制系统设计在进行电气控制系统设计时,需要考虑到模具的各个机动部分,例如电机、液压系统和气动系统的尺寸、形状和控制要求。
此外,必须确保电气系统满足安全要求。
6. 进行模具的装配和调试工作在进行模具装配和调试工作时,需要使用压力和温度测试等方法来测试模具的性能。
必须确保模具的品质和功能已经达到所设计的要求。
7. 进行模具的保养和维护工作在模具设计生产周期结束后,需要进行模具的保养和维护工作以确保其长期使用安全和可靠。
汽车覆盖件模具设计 第1章 汽车覆盖件与覆盖件模具

所在位置:工艺设计 > 模具结构
发动机盖内板拉延模实体图
拉延模结构
发动机罩机盖内板拉延模装配图
发动机盖内板拉延模上模(凹模)
本节目录 退出本节
所在位置:工艺设计 > 模具结构
发动机盖内板拉延模实体图
拉延模结构
发动机机盖内板拉延模下模 1-导板 2-压边圈 3-托料架 4-平衡块 5-定位器 6-下模座 7-安全防护板 8-铸入式起重棒
缩颈
Necking
NEK
英
23
弯曲
Bend
BE
文
24
侧冲孔
CAM Piercing
CAMPI或CAMPRC
对
25
包边
Hemming
HEM
照
26
弯曲整形
Flange AND Restricting FL RST
表
27
落料、冲孔
Blank AND Piercing
BL+PRC
28
剪边、冲孔
Trimming AND Piercing TR+PRC
中
8
修边
Shaving
英
9
引伸
Draw
文
10 再引伸
Redraw
对
11 成形
Form
照
12 辗制成形
Roll-form
表
13 伸展抽制成形 Stretch-draw forming
14 整形
Restricting
本节目录 退出本节
略写
SH BL CUT NOT PI 或 PRC TR SEP SHV DR RDR FO RO-FO S.D.F RST
车身覆盖件冲压仿真的有限元建模技术

________________________来稿日期上海交通大学国家模具CAD工程研究中心200030上海大众汽车有限公司201805博士研究生提 要本文介绍了车身覆盖件冲压仿真的有限元建模技术给出了某型轿车内门板的应用实例关 键 词车身覆盖件冲压仿真0 引 言目前即与此同时性能实用环保等方面为了迎接这一挑战即降低产品开发费用和减轻汽车的重量一个很重要的环节就是降低车身覆盖件模具的制造费用和生产周期[1]形状复杂其成形过程涉及几何非线性随着非线性理论车身覆盖件冲压仿真技术逐渐从实验室阶段走向工业实用阶段降低生产成本的有利工具国外有许多比较成熟的软件可用于板料成形的冲压仿真CFORMPamStamp本文运用UG在eta/Dynaform环境下建立了内门板的有限元模型提出了单元的划分原则32 计算机辅助工程 2001────────────────────────────────────────────1 覆盖件冲压仿真的几何建模一般覆盖件都要经过拉深整形冲孔等几道工序从零件最终成形后的产品造型出发通过非接触式或接触式扫描测量机来获得被测实物表面的离散点的空间位置信息包括凹模压边圈等并确定好模具几何模型中各部分之间及其与坯料之间符合实际的空间位置由于一般的CAE软件的造型功能并不十分强大UGPRO/E等2 车身覆盖件冲压仿真的有限元建模覆盖件的CAD模型建好以后将其转换为通用的数据格式文件就可以转入有限元分析软件的前处理器中得到模具的有限元网格国际产品模型数据交换标准STEPNBS法国航空航天业开发的SET标准现在许多商品化的CAD/CAM软件中并取得了很大成功模型的有些信息不能转换模型的有些数据虽然能转换数据转换时人为修改也很困难薄膜单元薄膜单元由于计算时间短其理论基础是基于平面应力假设的薄膜理论考虑的内力仅为沿薄壳厚度均匀分布的平行于中面的应力因而薄膜单元只适用于分析胀形等弯曲效应不明显的成形过程采用薄膜单元就明显不足了因而可以用来分析弯曲深拉深过程采用体单元来处理复杂的车身覆盖件冲压成形问题时需要很长的计算时间和很大的内存基于壳单元理论的壳单元既能处理弯曲效应因此壳单元被广泛用于板料成形过程的有限元分析中通常都用壳单元对模具和毛坯的几何模型进行有限元网格划分Belytschko-Tsay(BT)壳单元和Hughes-Liu(HL)壳单元其主要缺点是由于采用了局部坐标系和纤维坐标系两种坐标变换BT壳单元是对HL壳单元计算效率的一种修正而提出的[7]计算成本低但基本吻合在板料冲压仿真时选择BTNo.1 车身覆盖件冲压仿真的有限元建模技术 33────────────────────────────────────────────壳单元比较合理在很大程度上取决于初始网格的质量是有限元建模的主要任务之一比较好的方法是利用UG自动生成NASTRAN格式的壳单元网格信息文件利用Dynaform前处理的有限元模型检查功能翘曲等不合理单元加以修改在用三角形或四边形单元对模具和坯料进行离散化建立有限元模型时因而在划分网格时应注意以下原则1在曲面剧烈变化处或圆角过渡及拐角处单元应划分得更密一些3最好把具有共同边界的单面缝合成一张整面同一部件单元法向的一致性5覆盖件冲压成形过程中坯料变形复杂为了更好地反映板料的变形情况这样在计算过程中实现重划分单元的功能Adaptive mesh提高了冲压仿真的准确度因而降低了计算效率边界条件密度杨氏模量屈服强度塑性硬化指数边界条件的定义包括摩擦和润滑等目前应用较成熟的摩擦模型有经典的和修正的Coulomb摩擦运动的定义包括模具凸压边圈等部分的运动如单面接触等2.4 自动对模在成形过程的有限元仿真开始前对模有手工对模和自动对模自动对模相对方便先选定拉深的类型在保证模具各部分单元法向指向坯料且坯料单元法向一致的时候就可以选择Auto position进行自动对模该零件是典型的具有自由曲面和雕塑曲面的汽车覆盖件其实物模型图34 计算机辅助工程 2001────────────────────────────────────────────图3 车门内板模具和坯料有限元网格3 存在问题及今后的研究方向(1) 网格生成是几何定义与有限元的桥梁(2) 三维动态接触算法及摩擦模型的建立有待进一步研究(4) 实现建模的双向可逆性No.1 车身覆盖件冲压仿真的有限元建模技术 35────────────────────────────────────────────参 考 文 献1234567徐伟力等机械工程学报36(7):1-4(38)LS-DYNA User Manual. Livermore Software Technology Corp.,1997印雄飞等机械科学与技术19(3):452-253唐荣锡北京1994胡轶敏等汽车技术。
汽车覆盖件成形的有限元模拟及模具设计

板料成形的有限元模拟主要有三种算法, 即 动 力 显 式( Dy- namic Explicit) 、静 态 隐 式( Static Implicit) 以 及 静 态 显 式( Static Explicit) 算法, 目前应用较多的是前两种算法。有限元分析采用 改进的静态隐式算法, 解决了收敛性差的问题, 使计算时间大大 缩短。
图1 汽车 B 柱
量控制非常困难。因此 B 柱的设计和生产成为汽车车身设计和
制造的一大难点。
综后分析后, 确定 B 柱成形的工艺方案分三道工序, 其中第
一道工序为拉延, 在此工序中通过增加变形区域而获得制件形
状; 第二道工序为修边, 此工序保持和拉延冲压方向一致; 第三道
工序为激光切割, 在制件侧壁及底部有较多的用于安装固定的小
- 194 -
机械设计与制造 Machinery Design & Manufacture
第4期 2008 年 4 月
文章编号: 1001- 3997( 2008) 04- 0194- 02
汽车覆盖件成形的有限元模拟及模具设计
邢忠文 1 方华松 1 徐伟力 2 ( 1 哈尔滨工业大学 机电工程学院, 哈尔滨 150001) ( 2 宝山钢铁股份有限公司, 上海 201900)
深筋的布置, 获得了覆盖件拉深凹模, 如图 3 所示。
图 3 凹模 凹模设计完毕后, 通过偏移就可以分别获得凸模及压边圈, 最终得到整个模具。至此就可以设定工艺参数, 主要包括冲压方 式( 单动还是 双 动) 、模 具 在 各 个 工 步 的 运 动 关 系 、压 边 力 、摩 擦 系数、板料形状等, 进行成形过程的数值模拟。
3.4.1 创建一条拉深筋线
首先根据凹模入口形状, 取其边界轮廓并生成一条轮廓线, 然后把生成的曲线朝外偏置 25mm, 得到一条偏置线。
第章汽车覆盖件成形工艺及模具设计方案

第六章汽车覆盖件成形工艺及模具设计6.1 覆盖件的结构特征与成形特点6.2 覆盖件冲压成形工艺设计6.3 覆盖件成形模具的典型结构和主要零件的设计覆盖件主要指覆盖汽车发动机和底盘、构成驾驶室和车身的一些零件,如轿车的挡泥板、顶盖、车门外板、发动机盖、水箱盖、行李箱盖等<图6.0.1)。
由于覆盖件的结构尺寸较大,所以也称为大型覆盖件。
除汽车外,拖拉机、摩托车、部分燃气灶面等也有覆盖件。
和一般冲压件相比,覆盖件具有材料薄、形状复杂、多为空间曲面且曲面间有较高的连接要求、结构尺寸较大、表面质量要求高、刚性好等特点。
所以覆盖件在冲压工艺制定、冲模设计和模具制造上难度都较大,并具有其独自的特点。
a>b>图6.0.1轿车覆盖件图a> 轿车覆盖件组合图 b>轿车部分覆盖件分解图汽车覆盖件冲压成形工艺相对一般零件的冲压工艺更复杂,所需要考虑的问题也更多,一般需要多道冲压工序才能完成。
常用的主要冲压工序有:落料、拉深、校形、修边、切断、翻边、冲孔等。
其中最关键的工序是拉深工序。
在拉深工序中,毛坯变形复杂,其成形性质已不是简单的拉深成形,而是拉深与胀形同时存在的复合成形。
然而,拉深成形受到多方面因素的影响,仅按覆盖件零件本身的形状尺寸设计工艺不能实现拉深成形,必须在此基础上进行工艺补充形成合理的压料面形状、选择合理的拉深方向、合理的毛坯形状和尺寸、冲压工艺参数等。
因为工艺补充量、压料面形状的确定、冲压方向的选择直接关系到拉深件的质量,甚至关系到冲压拉深成形的成败.可以称为是汽车覆盖件冲压成形的核心技术,标志着冲压成形工艺设计的水平。
如果拉深件设计不好或冲压工艺设计不合理,就会在拉深过程中出现冲压件的破裂、起皱、折叠、面畸变等质量问题。
在制定冲压工艺流程时,要根据具体冲压零件的各项质量要求来考虑工序的安排,以最合理的工序分工保证零件质量,如把最优先保证的质量项的相关工序安排到最后一道工序。
汽车覆盖件成形模拟及模具设计数字化系统的开发的开题报告

汽车覆盖件成形模拟及模具设计数字化系统的开发的开题报告项目背景随着汽车工业的快速发展和市场竞争的日益激烈,汽车制造企业需要不断提高产品质量和生产效率,降低生产成本。
在汽车制造的过程中,汽车覆盖件的成形过程是一个非常重要的环节,对产品的质量和外观都有着决定性的影响。
目前,汽车制造企业在汽车覆盖件的成形过程中普遍采用传统经验法进行设计和生产,这种方式存在着很多缺点,如精度不高、成本高、周期长等,无法满足现代汽车工业的要求。
为了提高汽车生产的高质量、高效率和低成本,本项目旨在开发一种汽车覆盖件成形模拟及模具设计数字化系统,通过数值模拟技术和计算机辅助设计技术,为汽车制造企业提供更加精确、高效和可靠的成形模拟和模具设计服务,推动汽车工业的数字化转型与升级。
研究内容1. 汽车覆盖件成形模拟技术研究:通过建立三维有限元模型,采用成形模拟软件对汽车覆盖件的成形过程进行仿真分析,探究各种因素对汽车覆盖件成形质量的影响规律,并优化成形工艺参数,提高生产效率和降低成本。
2. 汽车覆盖件模具设计技术研究:通过建立三维CAD模型和CAM程序,采用模具设计软件对汽车覆盖件模具进行设计和优化,提高模具的制造精度和使用寿命,降低模具的制造成本和使用成本。
3. 数字化系统开发:基于上述成形模拟和模具设计技术研究,开发一种汽车覆盖件成形模拟及模具设计数字化系统,能够快速实现汽车覆盖件成形模拟和模具设计,提高成形模拟和模具设计精度和效率,为汽车制造企业提供数值化服务和数据支撑,推动汽车工业数字化转型。
项目意义本项目的成果将具有重要的理论和实际意义。
从理论上,本项目将推动汽车成形模拟和模具设计技术的发展,探索汽车工业数字化制造理论体系和实践方法。
从实践上,本项目将为汽车制造企业提供更加精细化、精确化和高效化的成形模拟和模具设计服务,降低生产成本和提高生产效率,促进汽车工业的数字化转型和升级,推动中国制造向中国智造的转型。
- 1、下载文档前请自行甄别文档内容的完整性,平台不提供额外的编辑、内容补充、找答案等附加服务。
- 2、"仅部分预览"的文档,不可在线预览部分如存在完整性等问题,可反馈申请退款(可完整预览的文档不适用该条件!)。
- 3、如文档侵犯您的权益,请联系客服反馈,我们会尽快为您处理(人工客服工作时间:9:00-18:30)。
1 引言
汽车覆盖件成形过程是一个涉及几何非线性、接触非线性 和材料非线性的大挠度、大变形的塑性成形过程, 影响因素很多 并且很难准确判定[1]。因此, 长期以来板料冲压工艺及其模具的 最终设计结果, 很大程度上都依赖于对模具的反复修改和调试, 浪费了大量的时间、人力和物力, 并且这种基于人工的操作难以 满足加工精度日趋提高的要求, 使产品在成本和质量上没有优 势, 而且又不能及时响应市场的变化, 必将被新的方法取代[2]。
凸模 压bin边de圈r
拉伸方向
压边圈 压边圈
1525.7
凹die模
坏料
凹die模
792.9
( a) 毛坯形状及尺寸
( b) 有限元模型
图 4 毛坯及有限元模型
Lin.limit:
最大应变量
- 0.2 0.0 0.2 0.4 0.6 0.8 1.0 1.2 1.4
Excess. Risk thinning of cracks
Fa ilure a na lys is on cold- e xtrus ion die of re cta ngle s pline s ha ft
FENG Wen- jie1, CHEN Ying- ying1, CHEN Bi- nan2 ( 1Automobile College, Chongqing Institute of Technology, Chongqing 400050, China)
Key wor ds: Die design; Finite element; Pr ocessing par ameter; Automotive B- pillar
%%%%%%%%%%%%%%%%%%%%%%%%%%%%%%%%%%%%%%%%%%%%%%%%%%%%%%%$
中图分类号: TH12, U46 文献标识码: A
4 数值模拟及工艺调整
板料成形的有限元模拟主要有三种算法, 即 动 力 显 式( Dy- namic Explicit) 、静 态 隐 式( Static Implicit) 以 及 静 态 显 式( Static Explicit) 算法, 目前应用较多的是前两种算法。有限元分析采用 改进的静态隐式算法, 解决了收敛性差的问题, 使计算时间大大 缩短。
XING Zhong- wen1, FANG Hua- song1, XU Wei- li2 ( 1School of Mechanical and Electrical Engineering, Harbin Institute of Technology, Harbin 150001, China)
3.4.1 创建一条拉深筋线
首先根据凹模入口形状, 取其边界轮廓并生成一条轮廓线, 然后把生成的曲线朝外偏置 25mm, 得到一条偏置线。
3.4.2 定义拉深筋
选择刚刚生成的偏置线, 沿着这条线创建一系列节点, 生成 高度为 5mm, 宽度为 15mm 的一圈实体拉深筋。
通过对冲压方向的确定、压料面和工艺补充的设计以及拉
3.1 冲压方向的确定
汽车覆盖件的产品图是按照其在车身上的安装位置绘制 的, 大多数情况下与冲压时放置的方向不一致, 必须将产品模型 所示的方向进行变换。B 柱两端均有较大尺寸的局部形状, 且互 成一定的角度, 选择合适的冲压方向, 使拉深深度最小, 且零件 各部分都能很好的成形。
3.2 压料面
压料面是指位于压边圈和凹模上表面之间的拉深件上的起 压料作用的那部分材料。覆盖件拉深成形的压料面形状是保证 拉深过程中材料不被破坏和顺利成形的首要条件。结合汽车 B 柱本身的特点: 零件纵向尺寸过大, 且外形成曲面, 选择曲面压 料面, 同时为了平衡各部分的受力情况, 设计压料面的外形尺寸 为。其形状, 如图 2 所示。
B 柱零件的结构特点是: 成形深度较大、零件截面变化比较
复杂; 成形件底部的高
度存在很大的起伏; 零
件 的 圆 角 半 径 较 小 。因
此给工艺及模具设计
带来了很多麻烦; 同
时, 为了满足 B 柱强度
和刚度的要求, 必须使
用屈服强度很高的材
料, 这也增加了工艺和
模具设计的难度, B 柱
的性能要求及结构特 点使零件在成形时质
孔, 比较模具冲孔的效益与效率, 决定采用激光切割方法获得。
3 模具设计
将 使 用 通 用 CAD 软 件 CATIA 中 造 出 的 零 件 模 型 以 igs 格
* 来稿日期: 2007- 07- 18
第4期
邢忠文等: 汽车覆盖件成形的有限元模拟及模具设计
- 195 -
式导入 AutoForm 软件中。通常这种几何模型往往不能完全满足 有限元分析的要求, 存在一些缺陷, 例如曲面有重叠、缝隙, 包含 过于细长的曲面片等等。因此, 需要进行检查和修改, 消除这些缺 陷。另外, 为了模拟程兴过程, 须将工件中的孔全部填满。这样就 可以开始在 AutoForm 软件的 DieDesigner 模块中进行模具设计。
深筋的布置, 获得了覆盖件拉深凹模, 如图 3 所示。
图 3 凹模 凹模设计完毕后, 通过偏移就可以分别获得凸模及压边圈, 最终得到整个模具。至此就可以设定工艺参数, 主要包括冲压方 式( 单动还是 双 动) 、模 具 在 各 个 工 步 的 运 动 关 系 、压 边 力 、摩 擦 系数、板料形状等, 进行成形过程的数值模拟。
为了加快覆盖件的模具设计, 要求 CAD 设计和 CAE 分析 能集成起来, 发挥各自的优势。板料成形专用软件 AutoForm 包 含模具设计模块、分析模块等, 实现了 CAD 和 CAE 的结合[5]。以 汽车车身 B 柱零件为例, 首先在通用 CAD 软件中设计产品模型, 然后倒入 AutoForm 软件中, 完成模具设计和成形的数值模拟。
图 2 压料面
3.3 工艺补充
工艺补充部分的设计是冲压工艺设计的关键一环, 工艺补充 设计的合理与否, 直接影响成形的成败, 影响到拉深成形时毛坯 的 变 形 条 件 、变 形 量 大 小 、变 形 分 布 、表 面 质 量 、破 裂 、起 皱 等 质 量 问题的产生。B 柱各部分变形程度相差太大, 变形分布不均匀。设 计工艺补充面调整零件各段的变形量, 有利于零件质量提高。
"""""""""""""""""""""#34;""""""""""""""""""""$
- 194 -
机械设计与制造 Machinery Design & Manufacture
第4期 2008 年 4 月
文章编号: 1001- 3997( 2008) 04- 0194- 02
汽车覆盖件成形的有限元模拟及模具设计
- 196 -
机械设计与制造 Machinery Design & Manufacture
第4期 2008 年 4 月
文章编号: 1001- 3997( 2008) 04- 0196- 02
矩形花键轴冷挤压模具的失效形式分析*
冯文杰 1 陈莹莹 1 陈碧楠 2 ( 1 重庆工学院 汽车学院, 重庆 400050) ( 2 中冶赛迪工程技术股份有限公司, 重庆 400013)
Safe
lnsuff. stretching
- 0.8 - 0.6 - 0.4 - 0.2 - 0.0 0.2 0.4
最小应变量
成形极限图
图 5 初始模拟结果 零件虽然两头局部形状尺寸较大, 发生了较大的塑性变形, 但在边缘以及拐角区域由于没有得到足够的拉深, 变形程度很 小, 而出现了明显的起皱。零件上出现过多的起皱现象, 说明压
( 2Baoshan Iron & Steel Co., Ltd, Shanghai 201900, China)
"""""""""""""""""""""""""""""""""""""""""""""""""""""""#
【 摘要】介绍了在有限元模拟基础上进行的汽车覆盖件模具设计, 利用专用软件 AutoForm 对某 车型的 B 柱进行了冲压方向的确定、拉深筋的布置、压料面和工艺补充面的设计以及拉深成形过程 的数值模拟。根据模拟结果调整优化了工艺参数和毛坯形状等, 消除了零件成形中的质量缺陷, 提高 了成形工艺稳定性, 对实际生产中 B 柱成形的工艺确定和模具设计提供了依据。
3.4 拉深筋的布置
拉深成形生产中, 尤其是象车身覆盖件等这样的大型工件 的拉深工序中, 往往会因为零件几何型面的不对称, 使得板坯在 成形时各处材料沿凹模口的流动速度不均衡, 造成拉深后的工 件, 局部减薄量大 出 现 颈 缩 或 者 破 裂 , 而 有 些 部 位 出 现 起 皱 、波 纹等质量缺陷。为了改善这种状况, 需要在压料面上控制对工件 不同部位提供的进料阻力 ( 毛坯在进入凹模前遇到的阻力) , 即 在需要材料多的部位相应的进料阻力小, 而在需要材料少的部 位相应的进料阻力大, 从而平衡坯料在凹模口部的流动速度差 异提高零件成形质量。其设置的步骤大致如下。
关键词: 模具设计; 有限元; 工艺参数; 汽车 B 柱 【 Abstr act】The design of the die for the automobile covers based on finite element simulation was introduced.The determination of the drawing direction, the layout of the drawing rib,the design of pressing surface and technological supplementing surface, and the simulation of drawing process were realized with the special software Autoform.The processing parameters are adjusted and optimized according to the simulation results.The quality defects are removed, the stability of forming process is improved, and then the bases of process determining and die design of B- pillar forming are supplied for actual production.