PCBA制程检验标准
PCBA检验标准(最完整版)

PCBA检验标准(最完整版)PCBA检验标准本检验规范的制定旨在为生产和检验过程提供可依据的标准。
定义:CR——严重缺陷:指单位产品的极严重质量特性不符合规定,或者单位产品的质量特性极严重不符合规定。
其中包括可靠性能达不到要求,可能对人身及财产带来危害或不符合法规规定,外观极严重不合格(降低产品等级,影响产品价格),与客户要求完全不一致等。
MA——主要缺陷:指单位产品的严重质量特性不符合规定,或者单位产品的质量特性严重不符合规定。
其中包括产品性能降低,产品外观严重不合格,功能达不到规定要求,客户难于接受的其他缺陷等。
MI——次要缺陷:指单位产品的一般质量特性不符合规定,或者单位产品的质量特性轻微不符合规定。
其中包括轻微的外观不合格,不影响客户接受的其他缺陷等。
短路和断路:短路是指两个独立的相邻的焊点之间,在焊锡之后形成接合,造成不应导通而导通的结果;断路是指线路该导通而未导通。
沾锡情况:良好沾锡是指接触角度小于等于60°,焊锡均匀扩散,焊点形成良好的轮廓且光亮。
要形成良好的焊锡,应有清洁的焊接表面,正确的锡丝和适当的加热。
按焊锡在金属面上的扩散情况,可分为全扩散(0°<接触角≤30°)和半扩散(30°<接触角≤60°)。
不良沾锡是指接触角度大于60°,焊锡熔化后形成不均匀的锡膜覆盖在金属表面上,而未紧贴其上。
形成不良沾锡的可能原因有不良的操作方法、加热或加锡不均匀、表面有油污、助焊剂未达到引导扩散的效果等。
按焊锡在金属面上的扩散情况,可分为劣扩散(60°<接触角≤90°)和无扩散(90°<接触角<180°)。
不沾锡是指焊锡熔化后瞬间沾附于金属表面,随后溜走。
不沾锡的可能原因有焊接表面被严重玷污、加热不足、焊锡由烙铁头流下、烙铁太热破坏了焊锡结构或使焊锡表面氧化等。
按部品的外观形状,将SMT实装部品分为有引脚产品和无引脚产品。
PCBA检验判定标准

1.目的:定义SMT作业(Workmanship)及品质检验标准。
2.范围:凡本公司或委外生产之SMA产品皆适用。
3.参考资料:无4.定义:4.1理想状况(TARGETCONDITION):此组装状况为接近理想与完美之组装状况。
能有良好组装可靠度,判定为理想状况。
4.2允收状况(ACCEPTABLECONDITION):此组装状况为未符合接近理想状况,但能维持组装可靠度故视为合格状况,判定为允收状况。
4.3拒收状况(REJECTCONDITION):此组装状况为未能符合标准之不合格缺点状况,判定为拒收状况。
4.4主要缺点(Majordefect):系指缺点对制品之实质功能上已失去实用性或造成可靠度降低,产品损坏、功能不良称为主要缺点,以MA表示之。
4.2次要缺点(Minordefect):系指单位缺点之使用性能,实质上并无降低其实用性,且仍能达到所期望目的,一般为外观或机构组装之差异,以MI表示之。
5.判定标准:SMT 零件置件标准—电阻,电容,电感(有极性Chip)零件置件准确度(Y 方向)1.零件纵向偏移,锡垫未保 有其零件宽度的20%(MI)。
(Y1<1/5W)2.金属封头纵向偏移出锡垫, 盖住焊垫不足1/5W (MI)。
(Y2<1/5W)<1/5W<1/5W1.零件座落在锡垫的中央且 未发生偏移,所有各金属封 头都能完全与锡垫接触。
1.零件Y 向偏移,但锡垫尚保 有其零件宽度的20%以上。
(Y1≧1/5W)2.金属封头纵向偏移出锡垫, 但仍盖住锡垫1/5W 以上。
(Y2≧1/5W)≧1/5W≧1/5W理想状况(TargetCondition)允收状况(AcceptCondition)拒收状况(RejectCondition)SMT零件置件标准—电阻,电容,电感(有极性Chip)零件之置件准确度(置件X方向)1.零件座落在锡垫的中央且未发生偏移,所有各金属封头都能完全与锡垫接触。
1.零件横向超出锡垫以外,但尚未大于其零件宽度的50%。
PCBA检验标准(最完整版)

W
S
X≦1/2W
S≧5mil
理想状况
1﹑各接脚都能座落在各焊垫的中央,没有发 生偏滑。(W 为接脚宽度,S 为接脚边缘与 焊垫外缘的垂直距离)
允收条件 1﹑零件各接脚发生偏滑,但偏出焊垫以外的
接脚小于接脚本身宽度的 1/2。 2﹑偏移接脚的边缘与焊垫外缘的垂直距离不
小于 0.13mm(5mil)。
标准工作程序 第 11 頁,共 68 頁
标准工作程序 第 3 頁,共 68 頁
PCBA 检验标准
3.2 SMT 部分﹕
项次
内容
1
极性反
2
缺件
3
错件
4
多件
5
撞件
6
损件
7
锡尖
8
短路
9
冷焊
10
空焊
11
锡渣
12 锡珠(锡球)
13
多锡
14
锡不足
15
残留物
16
偏移
不良现象描述
缺点分类 主要 次要
有极性的零件方向插错(二极管 焊垫左(右)侧宽度≦25%零件直径
◎
标准工作程序 第 4 頁,共 68 頁
PCBA 检验标准
项次
内容
不良现象描述
缺点分类 主要 次要
17
零件翻面 有区别的相对称的两面零件互换位置
◎
宽和高有差别的片状零件侧放﹐零件规格在 0805(含 0805)以下
18
侧放
宽和高有差别的片状零件侧放﹐零件规格在 0805 以上
◎
颜色不符或严重刮伤
◎
27
LED
本体破损
◎
28
排线
大小板之连接排线过孔吃锡不饱满﹐排线上作记号或排线有烫伤 (for TEAC)
最新PCBA质量检查标准(最)

最新PCBA质量检查标准(最)最新PCBA质量检查标准(最完整版)目的:本文档旨在提供一份最新、最完整的PCBA(Printed Circuit Board Assembly,印刷电路板装配)质量检查标准,以确保PCBA产品具备优质和可靠性。
本文档适用于所有与PCBA相关的质量检查工作,包括原材料检查、工艺检查和最终产品检查。
本文档旨在提供一份最新、最完整的PCBA(Printed Circuit Board Assembly,印刷电路板装配)质量检查标准,以确保PCBA产品具备优质和可靠性。
本文档适用于所有与PCBA相关的质量检查工作,包括原材料检查、工艺检查和最终产品检查。
1. 原材料检查1.1 元器件质量检查- 检查元器件是否符合规定的规格和参数要求。
- 检查元器件的包装是否完好无损,无明显的变形或损坏。
- 确认元器件的批次和生产日期,并核实其与采购记录是否一致。
1.2 PCB板材质量检查- 检查PCB板材的厚度是否符合要求。
- 检查PCB板材的颜色、纹理和表面光洁度是否合格。
- 核实PCB板材的型号和批次,并与采购记录进行比对。
1.3 焊料和助焊剂质量检查- 检查焊料和助焊剂的型号和批次,并与采购记录进行比对。
- 检查焊料和助焊剂的保存条件是否符合要求,确保其未过期或受到污染。
2. 工艺检查2.1 手工焊接检查- 检查焊接是否均匀、牢固,焊接点是否完整且无冷焊现象。
- 检查焊接的位置、角度和间距是否符合要求。
2.2 焊接过程控制检查- 确保焊接过程中的温度、时间和压力控制合理,避免过热或冷焊等问题。
- 检查焊接过程中是否有明显的焊接留痕或未焊接到位的情况。
2.3 绝缘和包装检查- 检查绝缘层是否完整且与焊点隔离良好。
- 检查产品的包装是否完好无损,且与运输过程中的标准保持一致。
3. 最终产品检查3.1 外观检查- 检查产品外壳的加工和涂装是否符合要求。
- 检查产品的尺寸、标识和标志是否清晰可辨。
PCBA检验标准(最完整版)

PCBA检验标准(最完整版)第一章:前言PCBA的质量是影响整个电子产品质量的重要因素之一。
为保证PCBA质量,我们需要对其进行严格的检验。
本文将介绍完整的PCBA检验标准,帮助您进行准确、高效、有效的PCBA检验。
第二章:PCBA检验目的2.1 保证产品质量PCBA作为电子产品的核心部件,其质量直接影响整个产品性能的稳定性、可靠性、耐久性和安全性。
2.2 提高产品市场竞争力对PCBA进行全面、准确、有效的检验可以有效降低产品故障率,提高用户体验,提高产品的市场竞争力。
2.3 降低生产成本通过全面检验,可以及时发现问题,减少返修率,最终降低生产成本。
第三章:PCBA检验内容3.1 外观检验外观检验用于判断PCBA外观是否符合要求,主要包括:•确认PCBA板面无明显瑕疵、变形和氧化;•确认PCBA连接部件是否有氧化、变形、松动、断裂等缺陷;•确认焊点是否完整、齐全、无虚焊、错位、多焊等问题。
3.2 尺寸检验尺寸检验用于判断PCBA的尺寸是否符合要求,主要包括:•确认PCBA的长度、宽度及厚度是否符合标准尺寸;•确认组件间距和组件贴附位置是否准确。
3.3 组件安装检验组件安装检验用于确认PCBA组件的安装是否正确,主要包括:•确认组件的安装方向是否正确;•确认组件与PCBA板面焊点是否正确对接;•确认组件是否缺失、脱落或存在异物。
3.4 电气性能检验电气性能检验用于测试PCBA的电气性能,主要包括:•确认PCBA的输入输出是否稳定;•确认电容、电阻及其他元器件的数值是否正常;•确认板间连接电阻是否正常。
3.5 环境适应性检验环境适应性检验用于测试PCBA在不同环境条件下的稳定性和可靠性,主要包括:•确认PCBA在不同温度、湿度、震动和冲击条件下的工作状况;•确认PCBA在不同环境条件下的EMC性能是否正常。
第四章:PCBA检验工具为了保证PCBA检验的准确性,我们需要配备相应的检验工具,主要包括:•显微镜:用于检查焊点情况和检验组件是否正确安装;•万用表:用于测试电气性能和元器件数值;•热风枪:用于检验焊点锡膏情况和测试环境适应性;•多功能测试仪:用于测试电气性能和工作稳定性。
PCBA检验标准
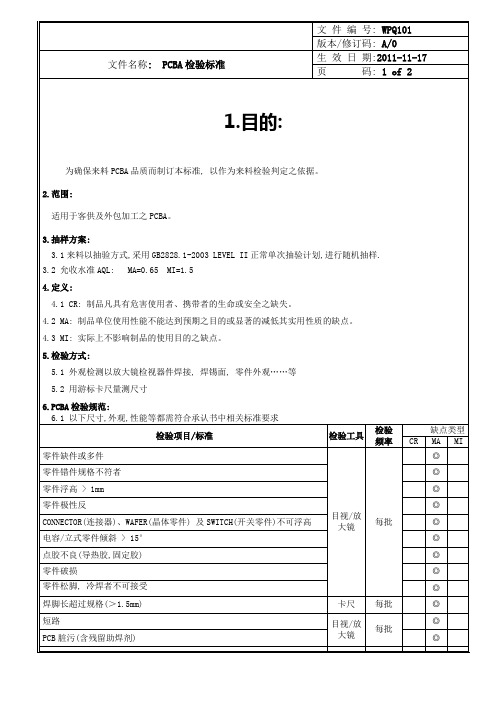
检验工具
检验
频率
缺点类型
CR
MA
MI
零件缺件或多件
目视/放大镜
每批
◎
零件错件规格不符者
◎
零件浮高> 1mm
◎
零件极性反
◎
CONNECTOR(连接器)、WAFER(晶体零件)及SWITCH(开关零件)不可浮高
◎
电容/立式零件倾斜> 15°
◎
点胶不良(导热胶,固定胶)
◎
零件破损
◎
零件松脚, 冷焊者不可接受
◎
焊脚长超过规格(>1.5mm)
卡尺
每批
◎
短路
目视/放大镜
每批
◎
PCB脏污(含残留助焊剂)
PCB白化
锡球、锡珠(实际大小会造成零件之间及两PIN短路)
◎
未贴VERSION 卷标
○
检验项目/标准
检验工具
检验 频率
缺点类型
CR
MA
MI
空焊
目视/放大镜
每批
◎
锡洞> 50%
焊锡面插件及PTH焊点锡尖高度不可超过100 mils
1.目的:
为确保来料PCBA品质而制订本标准, 以作为来料检验判定之依据。
2.范围:
适用于客供及外包加工之PCBA。
3.抽样方案:
3.1来料以抽验方式,采用GB2828.1-2003 LEVEL II正常单次抽验计划,进行随机抽样.
3.2 允收水准AQL: MA=0.65 MI=1.5
4.定义:
4.1 CR: 制品凡具有危害使用者、携带者的生命或安全之缺失。
4.2 MA: 制品单位使用性能不能达到预期之目的或显著的减低其实用性质的缺点。
pcba验收标准(一)
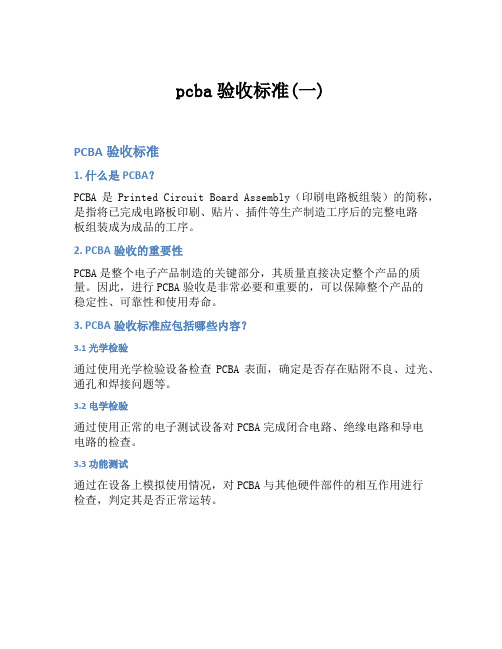
pcba验收标准(一)PCBA验收标准1. 什么是PCBA?PCBA是Printed Circuit Board Assembly(印刷电路板组装)的简称,是指将已完成电路板印刷、贴片、插件等生产制造工序后的完整电路板组装成为成品的工序。
2. PCBA验收的重要性PCBA是整个电子产品制造的关键部分,其质量直接决定整个产品的质量。
因此,进行PCBA验收是非常必要和重要的,可以保障整个产品的稳定性、可靠性和使用寿命。
3. PCBA验收标准应包括哪些内容?3.1 光学检验通过使用光学检验设备检查PCBA表面,确定是否存在贴附不良、过光、通孔和焊接问题等。
3.2 电学检验通过使用正常的电子测试设备对PCBA完成闭合电路、绝缘电路和导电电路的检查。
3.3 功能测试通过在设备上模拟使用情况,对PCBA与其他硬件部件的相互作用进行检查,判定其是否正常运转。
4. 如何实施PCBA验收?4.1 开发验收表开发验收表是指一个主要检查项的清单,它记录有关设备的各种详细信息,包括整个过程中需要使用的测试设备和工具。
这样能够有助于测试工程师更好地组织和整合测试工作。
4.2 准备测试环境测试环境的准备是PCBA的重要步骤。
在准备测试环境时,需要确认设备所需的原基础设施、测试设备和所需的人员资源是否充足。
4.3 实施验证在实施PCBA的实际验证过程中,要尽可能地模拟现实的使用情况,以便更准确地测试电路板组装完整性和电路连接问题。
5. 总结PCBA验收是电子产品制造过程中不可或缺的一步。
通过执行严谨的PCBA验收标准,可以降低产品的错误率,并确保产品的持续质量和性能。
6. 注意事项6.1 保持严谨性在进行PCBA验收时,一定要严格执行规定的检测标准和程序,不得随意更改。
否则会影响结果的可靠性和准确性。
6.2 专业化测试设备对于高品质,精密PCBA组装产品,必须配置高精度的测试设备来进行检测,这些设备通常需要配合专业化的测试软件来实现验证。
pcba测试检验标准
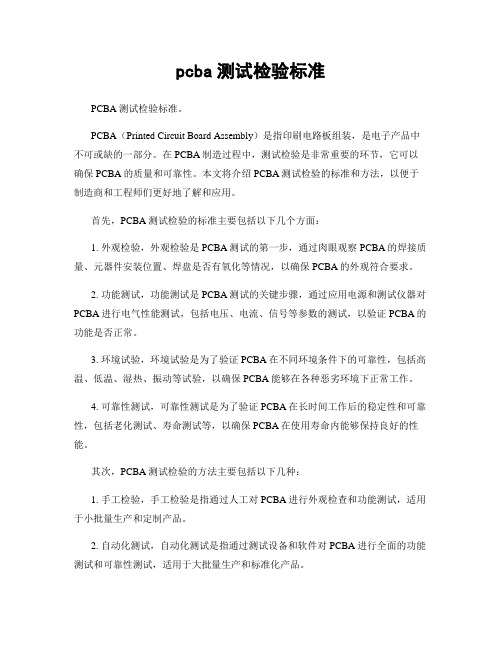
pcba测试检验标准PCBA测试检验标准。
PCBA(Printed Circuit Board Assembly)是指印刷电路板组装,是电子产品中不可或缺的一部分。
在PCBA制造过程中,测试检验是非常重要的环节,它可以确保PCBA的质量和可靠性。
本文将介绍PCBA测试检验的标准和方法,以便于制造商和工程师们更好地了解和应用。
首先,PCBA测试检验的标准主要包括以下几个方面:1. 外观检验,外观检验是PCBA测试的第一步,通过肉眼观察PCBA的焊接质量、元器件安装位置、焊盘是否有氧化等情况,以确保PCBA的外观符合要求。
2. 功能测试,功能测试是PCBA测试的关键步骤,通过应用电源和测试仪器对PCBA进行电气性能测试,包括电压、电流、信号等参数的测试,以验证PCBA的功能是否正常。
3. 环境试验,环境试验是为了验证PCBA在不同环境条件下的可靠性,包括高温、低温、湿热、振动等试验,以确保PCBA能够在各种恶劣环境下正常工作。
4. 可靠性测试,可靠性测试是为了验证PCBA在长时间工作后的稳定性和可靠性,包括老化测试、寿命测试等,以确保PCBA在使用寿命内能够保持良好的性能。
其次,PCBA测试检验的方法主要包括以下几种:1. 手工检验,手工检验是指通过人工对PCBA进行外观检查和功能测试,适用于小批量生产和定制产品。
2. 自动化测试,自动化测试是指通过测试设备和软件对PCBA进行全面的功能测试和可靠性测试,适用于大批量生产和标准化产品。
3. 抽样检验,抽样检验是指通过对PCBA进行抽样检测,以代表整个批次的质量水平,适用于中等规模生产和一般产品。
4. 定期检验,定期检验是指对PCBA进行定期的环境试验和可靠性测试,以确保PCBA的长期稳定性和可靠性,适用于长周期生产和高可靠性产品。
总之,PCBA测试检验是确保PCBA质量和可靠性的重要环节,制造商和工程师们应该根据标准和方法对PCBA进行全面的测试检验,以确保产品质量和客户满意度。
PCBA检验标准

PCBA检验标准PCBA 检验标准1.0⽬的⽤以规范和统⼀本公司所有内部⽣产和外协⼚加⼯的PCBA 检验。
2.0 适⽤范围2.1 适⽤于本公司内部⽣产和外协⼚加⼯的所有PCBA产品的检验。
2.2 可供本公司各相关单位参照使⽤3.0名词定义3.1 PCBA:Printed Circuit Boards Assembled是指已经经过部分或完整的零件贴装(SMT)或插件安装的PCB板。
3.2 冷焊:在焊点固化阶段,被焊零件发⽣移动,焊接后吃锡表⾯具有⼀层“霜”⼀样的外观层,造成吃锡层脆弱,零件易脱落。
如果出现裂缝或引脚起焊点断裂,那就定义为焊接裂纹。
3.3 连焊:不同线路的两焊盘或焊点被锡连接,会造成短路。
3.4 虚焊:由于电极或引脚氧化造成吃锡不良,被焊物体与锡接触但并没有完全焊接上,会造成焊接不牢,元件易脱落。
4.0作业程序4.1 缺陷分类定义A 类:有明显或潜在的危及使⽤者安全之缺陷(如:漏电,爆炸等);B 类:影响使⽤者正常使⽤之缺陷(如:缺件等)C 类:不影响使⽤者正常使⽤之缺陷(如:焊接外观不良等)4.2 元器件缺失或多出:将所要检验的PCBA 和图纸进⾏⽐较,主板上任何元器件缺失或多出都是不可接收的。
4.3 极性相反:任何有极性的元器件的⽅向必须与图纸⼀致,不⼀致的都是不可接收的。
4.4 元器件缺陷:4.4.1 任何元器件的断裂,破损,翘起或引脚缺失都是不可接收的。
4.4.2 元器件两端⾦属层宽度少于50%或长度少于75%都是不可接收的。
4.4.3 任何元器件受损导致内在材料暴露都是不可接收的。
4.4.4 任何元器件的镀层氧化,腐蚀都是不可接收的。
4.5 元器件上料错误:元器件的标记、颜⾊、代码、机械尺⼨与图纸、资料有不⼀致都是不可接收的。
4.6 元器件偏移:4.6.1 ⽚状元器件(SMD)错位导致焊接在焊盘上的⾦属层少于50%都是不可接收的。
4.6.2 有脚元器件任何⼀只脚焊接在焊盘上的⾦属层少于50%都是不可接收的。
PCBA检测标准
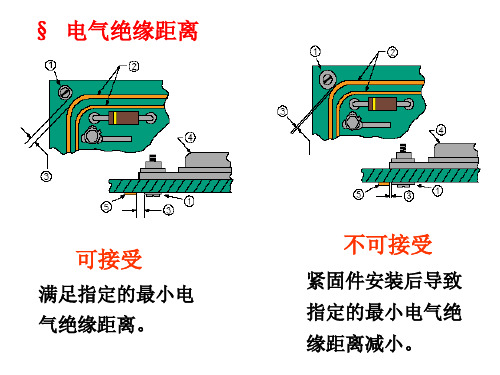
• 极性元件的方向安装错误 • 多引腿元件放置的方向错
误
可接受
• 元器件与PCB板平行,元件本体与PCB板 面完全接触。
• 由于设计需要而高出板面安装的元件,距 离板面最少1.5毫米,如,高散热器件。
不可接受
• 无需固定的元件本体 没有与安装表面接触。
• 在需要固定的情况下没 有使用固定材料。
• 每6002毫米多于5个焊锡球。
§ 锡珠、碎
不可接受
• 焊锡球/泼溅违反最小电气间隙。 • 未固定的焊锡球/泼溅或未粘附于金属表面。
§ 桥接 § 毛刺
①
不可接受
• 焊锡在不同导线或元 件间形成桥接。
不可接受
① 焊锡毛刺违反组 装的最大高度要求
② 焊锡毛刺违反最 小电气间隙
②
§ 不润湿
不可接受
需要焊接的引脚 或焊盘不润湿
§ 助焊剂残留物
可接受
• 对需清洗焊剂而言, 应无可见残留物.
• 对免清洗焊剂而言, 允许有焊剂残留物.
不可接受
有需清洗焊剂的残留 物,或者在电气连接表 面有活性焊剂残留物.
§ 助焊剂残留物
不可接受
• 表面残留了灰尘和颗粒 物质,如:灰尘、纤维丝、 渣滓、金属颗粒等.
§ 电气绝缘距离
可接受
满足指定的最小电 气绝缘距离。
不可接受
紧固件安装后导致 指定的最小电气绝 缘距离减小。
不可接受
不可接受
安装孔上过多的焊锡
对于过大的穿孔和槽
(不平)影响机械组装。 形孔缺少扁平垫片。
§ 插机(定位)
可接受
• 元器件放置于两焊盘 之间位置居中
• 元器件的标识清晰。
不可接受
• 未按规定选用正确的元件 • 元器件没有安装在正确的
PCBA测试标准(最完整版)
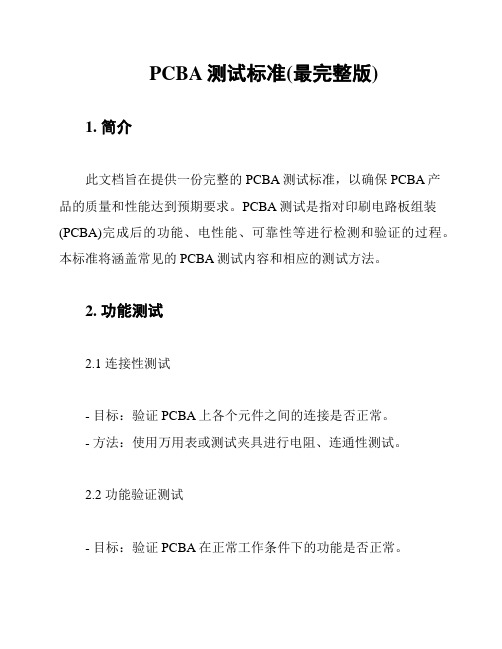
PCBA测试标准(最完整版)1. 简介此文档旨在提供一份完整的PCBA测试标准,以确保PCBA产品的质量和性能达到预期要求。
PCBA测试是指对印刷电路板组装(PCBA)完成后的功能、电性能、可靠性等进行检测和验证的过程。
本标准将涵盖常见的PCBA测试内容和相应的测试方法。
2. 功能测试2.1 连接性测试- 目标:验证PCBA上各个元件之间的连接是否正常。
- 方法:使用万用表或测试夹具进行电阻、连通性测试。
2.2 功能验证测试- 目标:验证PCBA在正常工作条件下的功能是否正常。
- 方法:将PCBA连接到相应的电源和信号源,观察并记录PCBA的反应、输出等情况。
3. 电性能测试3.1 电压测试- 目标:验证PCBA在额定电压下的性能是否正常。
- 方法:使用数字电压表或示波器测试PCBA上各个电压节点的电压值。
3.2 电流测试- 目标:验证PCBA在额定电流下的性能是否正常。
- 方法:使用电流表或电流探头进行电流测试。
4. 可靠性测试4.1 温度循环测试- 目标:验证PCBA在温度变化环境下的性能是否正常。
- 方法:将PCBA暴露在一系列温度变化的环境中,观察并记录PCBA的响应和性能。
4.2 湿度测试- 目标:验证PCBA在湿度变化环境下的性能是否正常。
- 方法:将PCBA暴露在一系列湿度变化的环境中,观察并记录PCBA的响应和性能。
5. 其他测试5.1 阻抗测试- 目标:验证PCBA上各个电路的阻抗是否满足设计要求。
- 方法:使用阻抗测试仪或示波器进行阻抗测试。
5.2 焊接质量测试- 目标:验证PCBA上焊接质量是否良好。
- 方法:使用目视检查或显微镜检查焊点的质量和焊接问题。
6. 测试报告测试完成后,应撰写测试报告,包括测试方法、测试结果、异常情况等详细信息,并结合标准要求对测试结果进行评估和总结。
以上是PCBA测试的最完整版标准,通过进行严格的测试,可以有效确保PCBA产品的质量和稳定性。
请根据具体项目需求,在此基础上进行适当调整和补充。
pcba板检验及接收标准
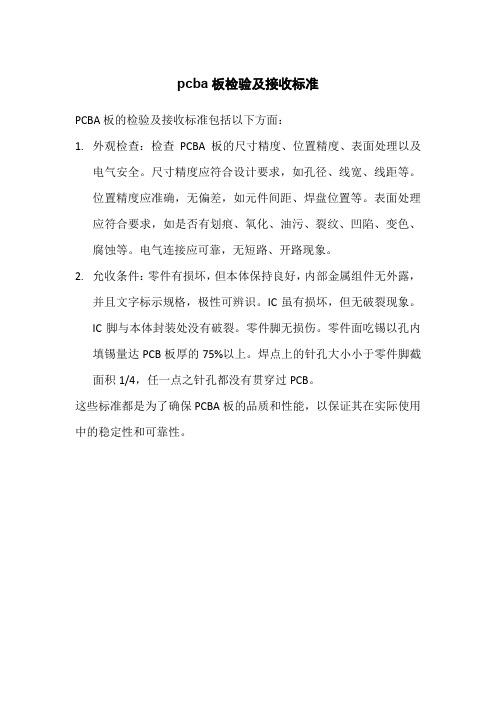
pcba板检验及接收标准
PCBA板的检验及接收标准包括以下方面:
1.外观检查:检查PCBA板的尺寸精度、位置精度、表面处理以及
电气安全。
尺寸精度应符合设计要求,如孔径、线宽、线距等。
位置精度应准确,无偏差,如元件间距、焊盘位置等。
表面处理应符合要求,如是否有划痕、氧化、油污、裂纹、凹陷、变色、腐蚀等。
电气连接应可靠,无短路、开路现象。
2.允收条件:零件有损坏,但本体保持良好,内部金属组件无外露,
并且文字标示规格,极性可辨识。
IC虽有损坏,但无破裂现象。
IC脚与本体封装处没有破裂。
零件脚无损伤。
零件面吃锡以孔内填锡量达PCB板厚的75%以上。
焊点上的针孔大小小于零件脚截面积1/4,任一点之针孔都没有贯穿过PCB。
这些标准都是为了确保PCBA板的品质和性能,以保证其在实际使用中的稳定性和可靠性。
PCBA检查标准
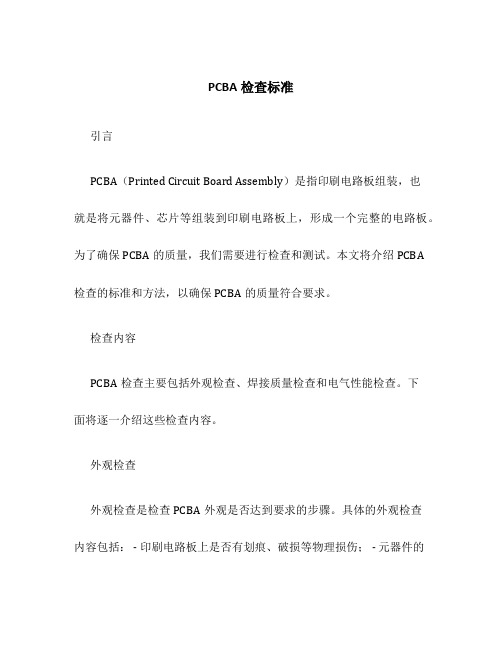
PCBA检查标准引言PCBA(Printed Circuit Board Assembly)是指印刷电路板组装,也就是将元器件、芯片等组装到印刷电路板上,形成一个完整的电路板。
为了确保PCBA的质量,我们需要进行检查和测试。
本文将介绍PCBA检查的标准和方法,以确保PCBA的质量符合要求。
检查内容PCBA检查主要包括外观检查、焊接质量检查和电气性能检查。
下面将逐一介绍这些检查内容。
外观检查外观检查是检查PCBA外观是否达到要求的步骤。
具体的外观检查内容包括: - 印刷电路板上是否有划痕、破损等物理损伤; - 元器件的位置是否正确; - 元器件与电路板之间的焊接是否牢固; - 元器件是否有漏焊、多焊、错位等问题; - PCB上的标识、文字等是否清晰可辨。
焊接质量检查焊接质量检查主要是检查PCBA焊接工艺是否符合要求。
具体的检查内容包括: - 元器件焊接是否均匀、光滑; - 焊盘与元器件引脚之间是否有间隙; - 焊盘上是否有锡丝、锡球等异物; - 是否有焊接过程中产生的焊渣; - 焊盘上的焊盘量是否符合要求。
电气性能检查电气性能检查是检查PCBA的电性能是否符合要求。
具体的电气性能检查内容包括: - 使用万用表或测试仪器对PCBA进行电阻、电流等基本参数的测试; - 使用示波器对PCBA进行波形测试,检查信号质量;- 使用逻辑分析仪对PCBA进行逻辑测试,检查信号时序等。
检查方法PCBA检查可以采用目视检查和仪器检测相结合的方法。
下面将介绍具体的检查方法。
目视检查目视检查是最基本的检查方法,可以通过肉眼观察PCBA的外观、焊接质量等情况。
目视检查时,需要注意以下几点: - 在光线明亮的环境下进行检查,以确保观察结果准确; - 观察时要仔细观察每个元器件的位置、焊接质量等情况,确保没有遗漏; - 可以使用放大镜来进行细致观察,以发现微小的问题。
仪器检测仪器检测是通过使用测试仪器对PCBA的各项电性能进行检测。
pcba检验标准

pcba检验标准PCBA检验标准。
PCBA(Printed Circuit Board Assembly)是指印刷电路板组装,是电子产品制造过程中的一个重要环节。
为了确保PCBA产品的质量和稳定性,需要进行严格的检验。
本文将介绍PCBA检验的标准及相关内容。
首先,PCBA检验标准包括外观检验和功能性检验两部分。
外观检验主要是对PCBA产品的外观进行检查,包括焊接质量、元件安装位置、焊盘状态等。
而功能性检验则是对PCBA产品的功能进行测试,包括电气性能、信号传输、温度稳定性等。
在进行外观检验时,需要注意焊接质量是否良好,焊盘是否出现虚焊、短路等情况,元件安装位置是否准确,元件是否倒装、漏装等。
同时,还需要检查PCBA产品的外观是否完整,有无划痕、变形等情况。
而在进行功能性检验时,需要根据PCBA产品的设计要求,进行相应的测试。
例如,对于电源板,需要测试电压、电流是否稳定;对于通信板,需要测试信号传输是否正常;对于控制板,需要测试程序运行是否正常等。
除了以上提到的检验内容外,还需要根据PCBA产品的具体要求,进行特定的检验。
例如,对于在恶劣环境下使用的PCBA产品,还需要进行耐高温、耐低温、耐湿热等环境测试。
在进行PCBA检验时,需要严格按照相关的标准进行操作,以确保检验结果的准确性和可靠性。
同时,还需要使用专业的检验设备和工具,以提高检验效率和准确性。
总之,PCBA检验是确保产品质量的重要环节,需要严格按照标准进行操作,同时结合实际情况,进行全面的检验。
只有通过严格的检验,才能保证PCBA产品的质量和稳定性,满足客户的需求和期望。
PCBA过程检验标准大全
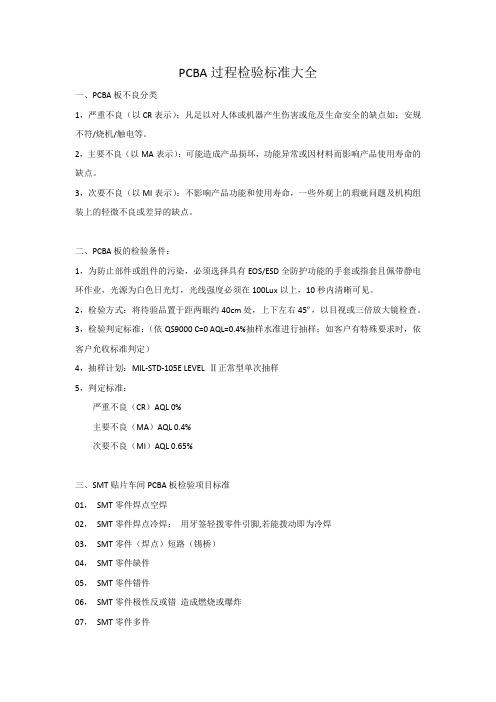
PCBA过程检验标准大全一、PCBA板不良分类1,严重不良(以CR表示):凡足以对人体或机器产生伤害或危及生命安全的缺点如:安规不符/烧机/触电等。
2,主要不良(以MA表示):可能造成产品损坏,功能异常或因材料而影响产品使用寿命的缺点。
3,次要不良(以MI表示):不影响产品功能和使用寿命,一些外观上的瑕疵问题及机构组装上的轻微不良或差异的缺点。
二、PCBA板的检验条件:1,为防止部件或组件的污染,必须选择具有EOS/ESD全防护功能的手套或指套且佩带静电环作业,光源为白色日光灯,光线强度必须在100Lux以上,10秒内清晰可见。
2,检验方式:将待验品置于距两眼约40cm处,上下左右45º,以目视或三倍放大镜检查。
3,检验判定标准:(依QS9000 C=0 AQL=0.4%抽样水准进行抽样;如客户有特殊要求时,依客户允收标准判定)4,抽样计划:MIL-STD-105E LEVEL Ⅱ正常型单次抽样5,判定标准:严重不良(CR)AQL 0%主要不良(MA)AQL 0.4%次要不良(MI)AQL 0.65%三、SMT贴片车间PCBA板检验项目标准01,SMT零件焊点空焊02,SMT零件焊点冷焊:用牙签轻拨零件引脚,若能拨动即为冷焊03,SMT零件(焊点)短路(锡桥)04,SMT零件缺件05,SMT零件错件06,SMT零件极性反或错造成燃烧或爆炸07,SMT零件多件08,SMT零件翻件:文字面朝下09,SMT零件侧立:片式元件长≤3mm,宽≤1.5mm不超过五个(MI)10,SMT零件墓碑:片式元件末端翘起11,SMT零件零件脚偏移:侧面偏移小于或等于可焊端宽度的1/212,SMT零件浮高:元件底部与基板距离<1mm13,SMT零件脚高翘:翘起之高度大于零件脚的厚度14,SMT零件脚跟未平贴脚跟未吃锡15,SMT零件无法辨识(印字模糊)16,SMT零件脚或本体氧化17,SMT零件本体破损:电容破损(MA);电阻破损小于元件宽度或厚度的1/4(MI);IC破损之任一方向长度<1.5mm(MI),露出内部材质(MA)18,SMT零件使用非指定供应商:依BOM,ECN19,SMT零件焊点锡尖:锡尖高度大于零件本体高度20,SMT零件吃锡过少:最小焊点高度小于焊锡厚度加可焊端高度的25%或焊锡厚度加0.5mm,其中较小者为(MA)21,SMT零件吃锡过多:最大焊点高度超出焊盘或爬伸至金属镀层端帽可焊端的顶部为允收,焊锡接触元件本体(MA)22,锡球/锡渣:每600mm2多于5个锡球或焊锡泼溅(0.13mm或更小)为(MA)23,焊点有针孔/吹孔:一个焊点有一个(含)以上为(MI)24,结晶现象:在PCB板表面,焊接端子或端子周围有白色残留物,金属表面有白色结晶25,板面不洁:手臂长距离30秒内无法发现的不洁为允收26,点胶不良:粘胶位于待焊区域,减少待焊端的宽度超过50%27,PCB铜箔翘皮28,PCB露铜:线路(金手指)露铜宽度大于0.5mm为(MA)29,PCB刮伤:刮伤未见底材30,PCB焦黄:PCB经过回焊炉或维修后有烤焦发黄与PCB颜色不同时31,PCB弯曲:任一方向之弯曲在每300mm间的变形超过1mm (300:1)为(MA)32,PCB内层分离(汽泡):发生起泡和分层的区域不超出镀覆孔间或内部导线间距离的25%(MI);在镀覆孔间或内部导线间起泡(MA)33,PCB沾异物:导电者(MA);非导电者(MI)34,PCB版本错误:依BOM,ECN35,金手指沾锡:沾锡位置落在板边算起80%内(MA)四、DIP后焊车间PCBA板检验项目标准01,DIP零件焊点空焊02,DIP零件焊点冷焊:用牙签轻拨零件引脚,若能拨动即为冷焊03,DIP零件(焊点)短路(锡桥)04,DIP零件缺件:05,DIP零件线脚长:Φ≤0.8mm→线脚长度小于等于1.5mmΦ>0.8mm→线脚长度小于等于2.0mm特殊剪脚要求除外06,DIP零件错件:07,DIP零件极性反或错造成燃烧或爆炸08,DIP零件脚变形:引脚弯曲超过引脚厚度的50%09,DIP零件浮高或高翘:参考IPC-A-610E,根据组装依特殊情况而定10,DIP零件焊点锡尖:锡尖高度大于1.5mm11,DIP零件无法辨识:(印字模糊)12,DIP零件脚或本体氧化13,DIP零件本体破损:元件表面有损伤,但未露出元件内部的金属材质14,DIP零件使用非指定供应商:依BOM,ECN15,PTH孔垂直填充和周边润湿:最少75%垂直填充,引脚和孔壁至少270º润湿16,锡球/锡渣:每600mm2多于5个锡球或焊锡泼溅(0.13mm或更小)为(MA)17,焊点有针孔/吹孔:一个焊点有三个(含)以上为(MI)18,结晶现象:在PCB板表面,焊接端子或端子周围有白色残留物,金属表面有白色结晶19,板面不洁:手臂长距离30秒内无法发现的不洁为允收20,点胶不良:粘胶位于待焊区域,减少待焊端的宽度超过50%21,PCB铜箔翘皮:22,PCB露铜:线路(金手指)露铜宽度大于0.5mm为(MA)23,PCB刮伤:刮伤未见底材24,PCB焦黄:PCB经过回焊炉或维修后有烤焦发黄与PCB颜色不同时25,PCB弯曲:任一方向之弯曲在每300mm间的变形超过1mm (300:1)为(MA)26,PCB内层分离(汽泡):发生起泡和分层的区域不超出镀覆孔间或内部导线间距离的25%(MI);在镀覆孔间或内部导线间起泡(MA)27,PCB沾异物:导电者(MA);非导电者(MI)28,PCB版本错误:依BOM,ECN29,金手指沾锡:沾锡位置落在板边算起80%内(MA)。
pcba检验标准

pcba检验标准一、目的和范围本标准旨在为PCB(Printed Circuit Board,印刷电路板)组装过程的品质检查提供一个通用准则。
其范围涵盖了从原材料到成品组装过程中所有阶段的品质检查。
二、引用标准本标准参考了IPC-A-610C《电子设备验收条件》和IPC-7711/7721《线路板可接受条件/元件可接受条件》等标准,以及其他相关的国家和行业标准。
三、术语和定义1.PCBA:印刷电路组装件,指在印刷电路板上组装了电子元件的组件。
2.缺陷:不符合规格要求的项目或条件。
3.致命缺陷:可能导致产品失效、人员伤亡或重大财产损失的缺陷。
4.严重缺陷:可能影响产品性能或对产品可靠性产生负面影响的缺陷。
5.轻微缺陷:对产品性能和可靠性影响较小的缺陷。
四、检验要求1.检验分类检验分为来料检验、过程检验和成品检验三个阶段。
2.检验环境检验应在符合产品特性的环境下进行,如温度、湿度、洁净度等。
3.检验设备应使用符合标准的检验设备和工具,确保其准确性和可靠性。
4.检验人员检验人员应具备相应的专业知识和技能,能够正确理解和执行检验标准。
5.抽样方案根据实际情况制定合理的抽样方案,采用随机抽样或系统抽样方式。
6.缺陷分类与判定缺陷分类与判定应符合IPC-A-610C和IPC-7711/7721等标准的要求。
7.不合格品处理不合格品应按照相关规定进行处理,如返工、返修、报废等。
8.记录与报告应做好检验记录,定期生成品质报告,以便对品质状况进行分析和改进。
9.持续改进根据品质报告和客户反馈,持续优化检验标准和改进生产过程,提高产品质量和可靠性。
10.定期评审与更新定期对检验标准进行评审和更新,以确保其适应性和有效性。
五、检验方法1.目视检验目视检验是指通过观察PCB板的外观和元器件排列、焊接状况等来判断其是否符合要求的检验方法。
目视检验应关注表面是否有污渍、刮伤、变色等不良现象,焊点是否饱满、无气泡,元器件是否错装、漏装等。
pcba检验标准
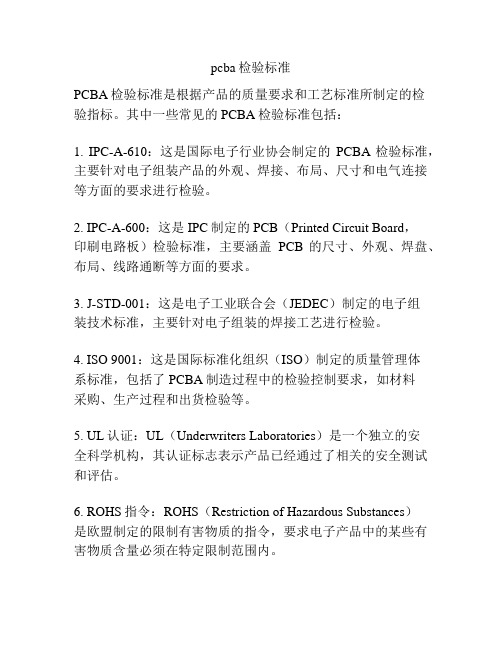
pcba检验标准
PCBA检验标准是根据产品的质量要求和工艺标准所制定的检
验指标。
其中一些常见的PCBA检验标准包括:
1. IPC-A-610:这是国际电子行业协会制定的PCBA检验标准,主要针对电子组装产品的外观、焊接、布局、尺寸和电气连接等方面的要求进行检验。
2. IPC-A-600:这是IPC制定的PCB(Printed Circuit Board,
印刷电路板)检验标准,主要涵盖PCB的尺寸、外观、焊盘、布局、线路通断等方面的要求。
3. J-STD-001:这是电子工业联合会(JEDEC)制定的电子组
装技术标准,主要针对电子组装的焊接工艺进行检验。
4. ISO 9001:这是国际标准化组织(ISO)制定的质量管理体
系标准,包括了PCBA制造过程中的检验控制要求,如材料
采购、生产过程和出货检验等。
5. UL认证:UL(Underwriters Laboratories)是一个独立的安
全科学机构,其认证标志表示产品已经通过了相关的安全测试和评估。
6. ROHS指令:ROHS(Restriction of Hazardous Substances)
是欧盟制定的限制有害物质的指令,要求电子产品中的某些有害物质含量必须在特定限制范围内。
以上是一些常见的PCBA检验标准,具体的检验标准可能根据产品的要求和行业的不同而有所差异。
pcba检验标准
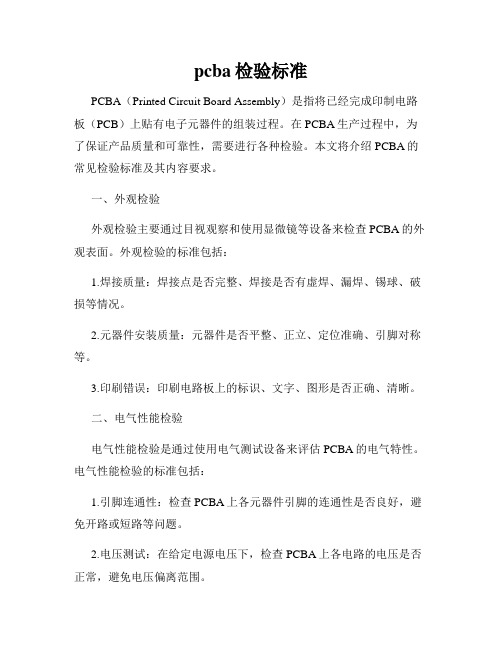
pcba检验标准PCBA(Printed Circuit Board Assembly)是指将已经完成印制电路板(PCB)上贴有电子元器件的组装过程。
在PCBA生产过程中,为了保证产品质量和可靠性,需要进行各种检验。
本文将介绍PCBA的常见检验标准及其内容要求。
一、外观检验外观检验主要通过目视观察和使用显微镜等设备来检查PCBA的外观表面。
外观检验的标准包括:1.焊接质量:焊接点是否完整、焊接是否有虚焊、漏焊、锡球、破损等情况。
2.元器件安装质量:元器件是否平整、正立、定位准确、引脚对称等。
3.印刷错误:印刷电路板上的标识、文字、图形是否正确、清晰。
二、电气性能检验电气性能检验是通过使用电气测试设备来评估PCBA的电气特性。
电气性能检验的标准包括:1.引脚连通性:检查PCBA上各元器件引脚的连通性是否良好,避免开路或短路等问题。
2.电压测试:在给定电源电压下,检查PCBA上各电路的电压是否正常,避免电压偏离范围。
3.信号测试:检查PCBA上各信号线路的传输是否正常,避免信号干扰或失真。
三、功能性检验功能性检验是通过应用场景或特定工作负载来评估PCBA的功能和性能。
功能性检验的标准包括:1.开机测试:检查PCBA在通电的情况下是否能够正常启动和运行。
2.通信测试:测试PCBA上的通信接口是否能够正常连接和传输数据。
3.特定工作负载测试:对特定功能模块或处理器进行负载测试,如处理器性能、温度等。
四、环境可靠性检验环境可靠性检验是通过将PCBA置于不同的环境条件下进行测试,以评估其在不同环境下的可靠性和稳定性。
环境可靠性检验的标准包括:1.温度循环测试:将PCBA放置在不同温度下进行循环测试,以模拟实际工作环境中的温度变化。
2.湿度测试:将PCBA放置在高湿度环境下进行测试,以评估其抗潮湿性能。
3.振动和冲击测试:对PCBA进行振动和冲击测试,以评估其抗震性能。
五、安全性检验安全性检验是评估PCBA在使用过程中的电气、机械和环境安全性能。
pcba验收标准

pcba验收标准**PCBA验收标准详细文档**---**一、引言**PCBA(Printed Circuit Board Assembly)即印刷电路板组装件,是电子制造过程中的关键环节。
其质量直接影响到最终产品的功能性能及稳定性。
本篇文档旨在明确和规范PCBA验收的标准与流程,以确保产品质量符合设计要求和行业规范。
**二、PCBA外观检验**1. **焊点质量**:所有焊点应饱满、光亮且无虚焊、假焊、桥连等现象。
焊料应完全覆盖焊盘和引脚,形状规则,无冷焊、拉尖或过多焊锡。
2. **元器件安装**:元器件方向正确,无倒置、歪斜、浮高现象,且紧固可靠。
贴片元件居中度良好,插件元件引脚弯折适度,不触及邻近线路或元件。
3. **PCB板品质**:PCB表面平整无明显变形,无划痕、破裂、烧焦等异常痕迹,字符标识清晰可见。
4. **清洁度**:PCBA表面需干净无残留物,如flux残留、尘埃、异物等。
**三、电气性能测试**1. **电路通断测试**:对PCBA上的每个网络进行连续性和绝缘性测试,确保线路连接正确,无短路或开路现象。
2. **元器件功能验证**:通过专用设备或程序对所有芯片、电阻、电容、电感等元件进行电气参数测量,确保其实际值在规格范围内。
3. **功能测试**:模拟实际工作环境,对PCBA进行全面的功能测试,包括但不限于电源上电测试、信号传输测试、系统运行测试等。
**四、可靠性测试**1. **耐温测试**:进行高低温循环测试、恒温老化试验,评估PCBA在极端温度条件下的工作稳定性和寿命。
2. **机械强度测试**:如振动测试、冲击测试,检查PCBA结构的稳固性和元器件的固定可靠性。
3. **环境适应性测试**:如湿度测试、盐雾测试等,检验PCBA在各种恶劣环境下的防护能力。
**五、文档资料验收**PCBA验收还需包含相关的生产过程记录、质量控制报告、元器件清单及来源证明、测试数据记录等文件资料,确保产品生产和验收过程的可追溯性。
PCBA制程工艺检验规范

序号
项 目
3、剪脚高度为1.5mm±0.5mm 页次:第 10 页 共 10 页
MA
MI
5、插针不允许有氧化锈斑、间隙≤0.5mm 3、立插斜高:
a 、一端高H ≤0.5mm (垂直
扭曲、高低不平、弯曲、镀MI
5.5.3.3清洁
搭在脚上
斑、标签纸等)
2、板上不允许有白斑油污、导电物质(如:棉絮、松香
及多余的助焊剂(特殊要求的除外)
5.5.3.2剪脚
2、不允许有未剪断的脚头连1、板面、板底不允许有多余1、尺寸应与插座配套
的导体(如:金属线)或非规定点胶的地方必须点胶,不允许不点胶
4、卧插斜高H ≤0.3mm 不允许出现跪脚、断脚等现象
MA
2、插针不允许透出绝缘体
3、连接导线不允许有破伤现象
1、剪脚处不允许有毛刺、尖角
MA
MI
层脱落等
熔胶固定
方向翘高)
插头
b 、一边高H ≤0.3mm (水平方向偏离高度)
标 准 要 求
判定图 解
5.5.2 接插件
1、外壳不允许有破损
2、两端平行,与板面之间的插座
5.5.2.1
MA
5.5.3.1
5.5.3 其它5.5.2.2
白斑
助焊
PCB
点胶处
插针透出
线破伤
插头
破损
翘
PCB
斜高
≤0.5mm
多余导体
多余的非导电体
跪脚。
- 1、下载文档前请自行甄别文档内容的完整性,平台不提供额外的编辑、内容补充、找答案等附加服务。
- 2、"仅部分预览"的文档,不可在线预览部分如存在完整性等问题,可反馈申请退款(可完整预览的文档不适用该条件!)。
- 3、如文档侵犯您的权益,请联系客服反馈,我们会尽快为您处理(人工客服工作时间:9:00-18:30)。
1 目的Purpose
为更好地控制电子产品质量,对PCBA在生产过程中的检验标准进行规定。
2 范围适用Scope
本规定由电子开发部编制,对电子产品PCBA进行过程管理和控制。
3 介绍
3.1三个优先原则
a) 与客户的协议。
b) 标准中,文字优先于图例。
c) 特殊的依双方协商。
3.2验收级别
a) 目标级(Target)。
b) 可接收级(Acceptable)。
c) 缺陷级(Defect)。
d) 过程警示(Process Indicator)
4 电子组件操作
4.1 电子组件操作准则
a) 保持工作台干净整洁,在工作区域不可有任何食品、饮料或烟草制品。
b) 尽可能的减少去电子组件的操作,防止损坏。
c) 使用手套时,需要及时更换,防止因手套肮脏引起的污染。
d) 不可用裸露的手或手指接触可焊表面,人体油脂和盐分会降低可焊性,加重腐蚀。
e) 不可使用未经认可的手霜,它们会引起可焊性和涂覆粘附性问题。
f) 绝不可堆叠电子组件,否则会导致机械性损伤,需要在组装区使用特定的搁架用于临时存放。
g) 对于没有ESDS标志的也应作为ESDS操作。
h) 人员必须经过培训并遵循ESD规章制度执行。
i) 除非有合适的防护包装,否则决不能运送ESDS设备。
4.2 检查放大倍率
焊盘宽度或焊盘直径用于检测放大倍数用于仲裁放大倍数
>1.0mm 1.75~3X 4X
>0.5~1.0mm 3~7.5X 10X
0.25~0.5mm 10X 20X
<0.25mm 20X 40X
5 电子元件的安装位置与方向
5.1 轴向/径向元件 水平/垂直 安装标准
a) 水平方位
可接受缺陷
b) 垂直方位
可接受缺陷
) 水平安装-轴向引脚-支撑孔
目标
制程警示目标必—必要方式
元件离板高度要求
目标 缺陷 目标 可接受 缺陷
目标 可接受 H min. 最小高度 0.4 mm [0.016 in]
目标缺陷
) 垂直安装-径向引脚
目标制程警示
目标制程警示缺陷(非支撑孔
缺陷(非支撑孔)
目标制程警示
k) 安装-线/脚末端-印制板-伸出-直插引脚和部分弯折引脚
L min.
引脚可辨认
最小长度
目标可接受
非等电位导体
缺陷
3) 安装-引脚横跨导体 最小内弯半径
可接受
可接受 缺陷 可接受 缺陷 可接受 可接受 缺陷 最小内弯半径 (R)
矩形截面的引脚以脚厚作为直径
5.3 元件引脚成型和应力释放要求
1) 引脚成型-应力释放-支撑孔/非支撑孔
可接受
2) 引脚成型—应力释放—支撑孔
可接受缺陷
胶水
2) 损伤-DIP和SOIC
3) 损伤-轴向引脚和玻璃体封装的元件
制程警示
无件表面有损伤,但是未暴露出元件内部的金属材质,元件管脚的密封完好 缺陷
元件表面的绝缘涂层受到损伤,造成元件内部的金属材质暴露在外,或元件严重变形
缺陷
1.玻璃封装上的破裂超出元件的规范。
玻璃封装上的残缺引起的裂痕延伸到管脚的密封处
元件体没有刮痕、残缺、可接受
元件体有轻微的刮痕、残缺,但元件缺陷
制程警示缺陷
制程警示
6.3 针孔/吹孔 6.4 焊锡毛刺 制程警示
距离连接盘或导线在0.13毫米[0.00512英寸以内的粘附的焊锡球,或直径大于0.13毫米缺陷
焊锡球/泼溅违反最小电气间隙。
未固定的焊锡球/泼溅(例如,免清除的残渣焊锡毛刺违反组装的最大高度要求或引脚凸出要求(表6-1)中的最小者 缺陷
焊锡毛刺不满足最小电气间隙
7 清洁度的可接受条件 7.1 颗粒状物体
目标清洁。
缺陷
表面残留了灰尘和颗粒物质,如:灰尘、纤维丝、渣滓、金属颗粒等。
目标
清洁。
在印刷板表面有白色残留物。
在焊接端子上或端子周围有白色残留物存在。
可接受
助焊剂残留在连接盘、元器件引线或导线上,或围绕在其周围,或在其上造成了在很大程度上造成了桥连。
助焊剂残留物未影响目视检查。
缺陷
免清洗残留物上有指纹。
潮湿、有粘性、或过多的焊剂残留物,可能扩展到其他表面。
在电气配件的表面,有影响电气联接的免清洗
可接受
清洁的金属表面轻微发暗。
缺陷
金属表面或装配件上存在有色残留物或锈斑。
标记可接受条件
蚀刻标记(包括手印标记) 缺陷
明显的腐蚀。
8.3 印章标记
8.6 标签-标记粘贴和损坏
10 线路板的可接受条件
10.1 白斑/微裂纹
可接受
分散孤立的白色斑点或“十字纹”。
10.2 层压板损伤-起泡和分层
起泡分层
缺陷
1.在镀覆孔间或内部导线间起泡
10.4 晕圈和边缘分层 10.5 粉红圈
可接受
可接受缺陷
可接受
可接受
中国·国威科技有限公司
10.8 弓曲和扭曲
10.9 导体/焊盘损伤 —焊盘翘起
可接受 目标 缺陷
缺陷
烧焦造成表面或组件的物理损伤。
11.2 片式元件-底部可焊端 焊点宽度
可接受
缺陷
可焊端偏移超出焊盘
目标 1.无粘胶在待焊表面。
2.粘胶位于各焊盘中间。
缺陷
粘胶从元件下蔓延出并在待焊区域可。
缺陷
焊盘和待焊端被粘胶污染,未可接受 侧面偏移(A )大于元件可焊端宽度(25%或焊盘宽度(P )的25%,其中较小末端焊点宽度(C )等于元件可焊端宽度(P ),其中较小者。
目标
侧面焊点长度(D)等于元件可焊端长度(
可接受
最小焊点高度
末端重叠
11.3 圆柱体端帽形可焊端
可接受
缺陷侧面偏移(A)小于元件直径宽(
或焊盘宽度(P)的25%,其中较小者
b) 最小末端焊点宽度
可接受
最大侧面偏移(A)不大于引脚宽度(W)的25%或0.5毫米[0.02英寸],其中较小者。
缺陷
侧面偏移(A)大于引脚宽度(W)的25%或0.5毫米[0.02英寸],其中较小者。
目标
末端焊点宽度等于或大于可接受
最小末端焊点宽度(C)为引脚宽度(W)的
d) 最大跟部焊点高度
11.6 SMT异常情况
立碑
c) 锡膏的回流
缺陷
缺陷缺陷
缺陷
缺陷
缺陷
缺陷
缺陷l) 元件损伤 — 裂缝和缺损
缺陷可接受
缺陷。