LTC1592BIG中文资料
LTC1274CSW#PBF;LTC1274CSW;LTC1274CSW#TR;LTC1274CSW#TRPBF;LTC1277CSW;中文规格书,Datasheet资料
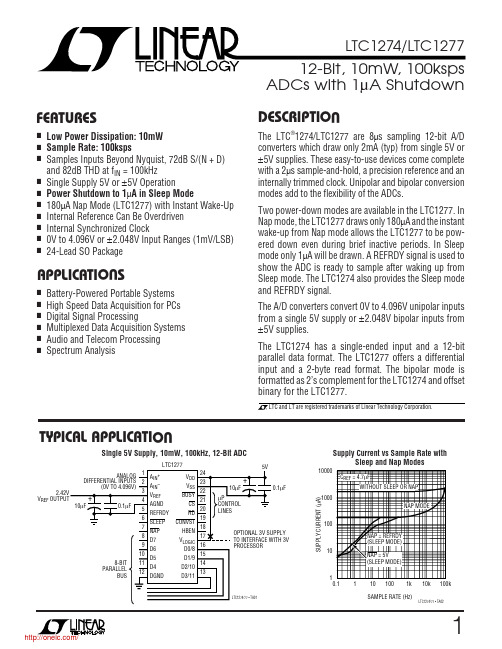
Digital Output Voltage
Unipolar Operation ................... – 0.3V to VDD + 0.3V Bipolar Operation...................... – 0.3V to VDD + 0.3V Power Dissipation ............................................. 500mW
SW PACKAGE
24-LEAD PLASTIC SO WIDE
TJMAX = 110°C, θJA = 130°C/W
ORDER PART NUMBER
LTC1277CSW LTC1277ISW
CO VERTER CHARACTERISTICS With Internal Reference (Notes 5, 6)
PACKAGE/ORDER I FOR ATIO
TOP VIEW
AIN 1 VREF 2 AGND 3 D11 (MSB) 4 D10 5
D9 6 D8 7 D7 8 D6 9 D5 10 D4 11 DGND 12
24 VDD 23 VSS 22 BUSY 21 CS 20 RD 19 CONVST 18 SLEEP 17 REFRDY 16 D0 15 D1 14 D2 13 D3
21 CS
20 RD
19 CONVST
18 HBEN
17 VLOGIC 16
D0/8 15
D1/9 14
D2/10 13
D3/11
+
10µF
µP CONTROL LINES
5V 0.1µF
OPTIONAL 3V SUPPLY TO INTERFACE WITH 3V PROCESSOR
SC1592IMTRT资料

ICNTL_DIS REG(LINE) REG(CNTL) REG(LOAD)
VCNTL = VIN = 16V V EN = 0 2.5V ≤ VIN ≤ 16V 3.3V ≤ VCNTL ≤ 16V, VOUT = VREF 10mA ≤ IOUT ≤ 2A, TJ = 25°C 10mA ≤ IOUT ≤ 3A, -40 < TJ < 125°C
Pin Descriptions
Pin # DDPAK 1 2 3 Pin # SOIC 1 2, 3 4 Pin Name ILIM IN CNTL Pin Function Externally programmable current limit should be set at < 5A. This is the collector input to the power device. The ouput load current is supplied through this pin. This pin is the bias supply for the control circuitry. The current flow into this pin will be approximately 1% of the output current. For the device to regulate, the voltage on this pin must be at least 1.5V greater than the output voltage, but no less than VCNTL_MIN. Ground. This is the power output of the device. This is a feedback input. Enable input. When high, should be less or equal to VCNTL.
LTC4095中文规格书
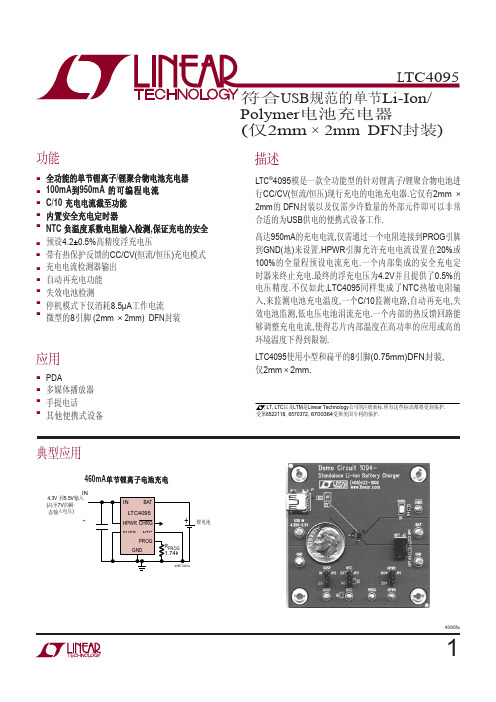
参数
条件
再充电比较器反应时间
BAT 下降中
充电定时器截止周期 失效电池截止时间 充电结束时指示器电流水平Current Level
BAT = VFLOAT BAT < VTRKL (Note 5)
充电结束时比较起反应时间
电池充电器 Power FET 导通电阻 (在IN与BAT之间)
IBAT 下降中 IBAT = 200mA
Differential Undervoltage Lockout Threshold
Differential Undervoltage Lockout Hysteresis PROG 引脚的比较反馈电压
hPROG ITRKL VTRKL ΔVTRKL ΔVRECHRG
Ratio of IBAT to PROG Pin Current 涓流充电电流 涓流充电截止电压 涓流充电迟滞电压 电池再充电门限电压
恒定温度下的最高结温
最小值
3.5 0.4375 0.09
典型值 1.7 4 0.5 0.1 2.2 500
最大值
4.5 0.5625 0.11
单位 ms Hour Hour mA/mA ms mΩ
115
°C
NTC VCOLD VHOT VDIS
ห้องสมุดไป่ตู้
过冷温度错误截止电压 过热温度错误截止电压 NTC失效截止电压
Note 2: The LTC4095 is guaranteed to meet performance specifications from 0°C to 85°C. Specifications over the –40°C to 85°C operating temperature range are assured by design, characterization and correlation with statistical process controls.
LTC4096X资料
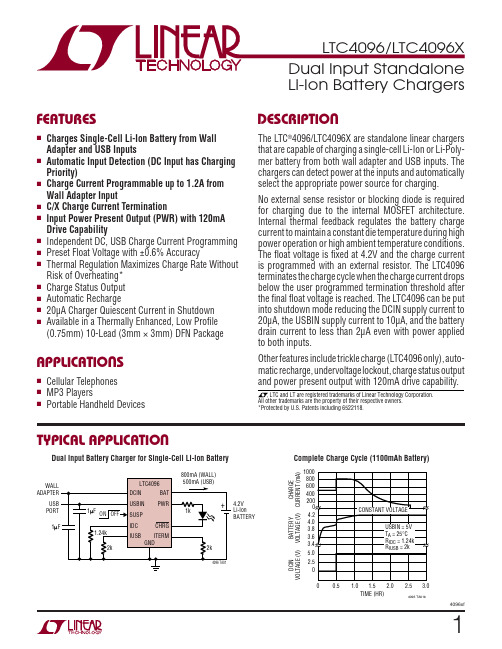
24096xfELECTRICAL CHARACTERISTICS PACKAGE/ORDER INFORMATIONABSOLUTE MAXIMUM RATINGSV DCIN , V USBINt < 1ms and Duty Cycle < 1% ..................–0.3V to 7V Steady State .............................................–0.3V to 6V BAT, C H R G , SUSP ........................................–0.3V to 6V IDC, IUSB, ITERM ...........................–0.3V to VCC + 0.3V BAT Short-Circuit Duration ............................Continuous PWR Short-Circuit Duration ..........................Continuous BAT, DCIN Pin Current (Note 6) ..............................1.25A USBIN Pin Current (Note 6) .....................................1.1A IDC, IUSB, ITERM Pin Current ............................1.25mA Junction Temperature ...........................................125°C Operating Temperature Range (Note 2) ...–40°C to 85°C Storage Temperature Range ...................–65°C to 125°C(Note 1,7)SYMBOL PARAMETER CONDITIONSMIN TYPMAX UNITSV DCIN Adapter Supply Voltage ● 4.25 5.5V V USBIN USB Supply Voltage ● 4.255.5V I DCINDCIN Supply CurrentCharge Mode (Note 4), R IDC = 10kStandby Mode; Charge Terminated Shutdown Mode (SUSP = 5V)●●250502080010040µA µA µA I USBINUSBIN Supply CurrentCharge Mode (Note 5), R IUSB = 10k, V DCIN = 0V Standby Mode; Charge Terminated, V DCIN = 0V Shutdown (V DCIN = 0V, SUSP = 5V)V DCIN > V USBIN●●2505020108001004020µA µA µA µA V FLOAT Regulated Output (Float) Voltage I BAT = 1mAI BAT = 1mA, 0°C ≤ T A ≤ 85°C 4.1794.158 4.24.2 4.2214.242V V I BATBAT Pin CurrentR IDC = 1.25k, Constant-Current Mode R IUSB = 2.1k, Constant-Current Mode R IDC = 10k or R IUSB = 10kStandby Mode, Charge Terminated Shutdown Mode (Charger Disabled)Sleep Mode (V DCIN = 0V, V USBIN = 0V)75045088800476100–5–2–5850500112–8–4–8mA mA mA µA µA µA V IDC IDC Pin Regulated Voltage Constant-Current Mode, R IDC = 1.25k 1V V IUSBIUSB Pin Regulated VoltageConstant-Current Mode, R IUSB = 2k 1VTOP VIEWDD PACKAGE10-LEAD (3mm × 3mm) PLASTIC DFN 1096781145321BAT IDC GND IUSB ITERMDCIN USBIN PWR CHRG SUSPT JMAX = 125°C, θJA = 40°C/W (Note 3)EXPOSED PAD (PIN 11) IS GND, MUST BE SOLDERED TO PCBORDER PART NUMBERDD PART MARKINGLTC4096EDD LTC4096XEDDLCSJ LCLMOrder Options Tape and Reel: Add #TRLead Free: Add #PBF Lead Free Tape and Reel: Add #TRPBF Lead Free Part Marking: /leadfree/Consult LTC Marketing for parts specifi ed with wider operating temperature ranges.The ● denotes the specifi cations which apply over the full operatingtemperature range, otherwise specifi cations are at T A = 25°C. V DCIN = 5V, V USBIN = 5V, R IDC = 1k Ω, R IUSB = 2k Ω, R ITERM = 2k Ω unless otherwise noted.34096xfNote 1: Stresses beyond those listed under Absolute Maximum Ratings may cause permanent damage to the device. Exposure to any Absolute Maximum Rating condition for extended periods may affect device reliability and lifetime.Note 2: The LTC4096 is guaranteed to meet the performance specifi cations from 0°C to 85°C. Specifi cations over the –40°C to 85°C operatingtemperature range are assured by design, characterization and correlation with statistical process controls.Note 3: Failure to correctly solder the Exposed Pad of the package to the PC board will result in a thermal resistance much higher than 40°C/W. See Thermal Considerations.SYMBOL PARAMETERCONDITIONS MIN TYP MAX UNITS I TERMINATECharge Current TerminationThresholdR ITERM = 1k R ITERM = 2k R ITERM = 10k88426100509.51125813mA mA mA I TRIKL Trickle Charge Current (LTC4096 Only)V BAT < V TRIKL ; R IDC = 1k V BAT < V TRIKL ; R IUSB = 2k85421005011558mA mA V TRIKL Trickle Charge Threshold Voltage (LTC4096 Only)V BAT Rising Hysteresis ●2.8 2.91353V mV V UVDC DCIN Undervoltage Lockout VoltageFrom Low to High Hysteresis 4 4.22200 4.4V mV V UVUSB USBIN Undervoltage Lockout VoltageFrom Low to High Hysteresis3.842004.2V mV V ASD-DC V DCIN – V BAT Lockout Threshold VoltageV DCIN from High to Low, V BAT = 4.3V V DCIN from Low to High, V BAT = 4.3V53010055mV mV V ASD-USB V USBIN – V BAT Lockout Threshold Voltage V USBIN from High to Low, V BAT = 4.3V V USBIN from Low to High, V BAT = 4.3V 53015055mV mV V SUSP V IL , Logic Low Voltage 0.5V V IH , Logic High Voltage 1.2V R SUSP SUSP Pulldown Resistance ●1.3 3.47M ΩV C H R G C H R G Output Low Voltage I C H R G = 5mA ●62150mV ΔV RECHRG Recharge Battery Threshold VoltageV FLOAT – V RECHRG305080mV t RECHRG Recharge Comparator Filter Time V BAT from High to Low1.6ms t TERMINATE Termination Comparator Filter TimeI BAT Drops Below Termination Threshold3ms R ON-DC Power FET “ON” Resistance (Between DCIN and BAT)420m ΩR ON-USB Power FET “ON” Resistance (Between USBIN and BAT)470m ΩR DC-PWR Power FET “ON” Resistance (Between DCIN and PWR)V DCIN = 5V, V USBIN = 0V 15ΩR USB-PWR Power FET “ON” Resistance (Between USBIN and PWR)V DCIN = 0V, V USBIN = 5V 6.6ΩT LIMJunction Temperature in Constant-Temperature Mode115°CELECTRICAL CHARACTERISTICS The ● denotes the specifi cations which apply over the full operatingtemperature range, otherwise specifi cations are at T A = 25°C. V DCIN = 5V, V USBIN = 5V, R IDC = 1k Ω, R IUSB = 2k Ω, R ITERM = 2k Ω unless otherwise noted.Note 4: Supply current includes IDC and ITERM pin current (approximately 100µA each) but does not include any current delivered to the battery through the BAT pin.Note 5: Supply current includes IUSB and ITERM pin current(approximately 100µA each) but does not include any current delivered to the battery through the BAT pin.Note 6: Guaranteed by long term current density limitations.Note 7: V CC is greater of DCIN or USBINOPERATIONThe LTC4096 is designed to effi ciently manage charging a single-cell lithium-ion battery from two separate voltage sources: a wall adapter and USB power bus. Using the constant-current/constant-voltage algorithm, the charger can deliver up to 1.2A of charge current from the wall adapter supply or up to 1A of charge current from the USB supply with a fi nal fl oat voltage accuracy of ±0.6%. The LTC4096 has two internal P-channel power MOSFETs, thermal regulation and shut down circuitry. No blocking diodes or external sense resistors are required.Power Source SelectionThe LTC4096 can charge a battery from either the wall adapter input or the USB port input. The LTC4096 automati-cally senses the presence of voltage at each input. If both voltage sources are present, the LTC4096 defaults to the wall adapter source provided suffi cient voltage is present at the DCIN input. “Suffi cient voltage” is defi ned as: • Supply voltage is greater than the UVLO threshold. • Supply voltage is greater than the battery voltage by 30mV (100mV or 150mV rising, 30mV falling).The power present output pin (PWR) indicates that suf-ficient input voltage is available. Table 1 describes the behavior of this status output.Table 1. Power Source SelectionV USBIN > 4V andV USBIN > BAT + 30mV V USBIN < 4V orV USBIN < BAT + 30mVV DCIN > 4.2V andV DCIN > BAT + 30mV Charger powered from wall adapter source;V PWR = V DCIN – R DC-PWR • I PWRUSBIN current < 25µACharger powered from wall adapter sourceV PWR = V DCIN – R DC-PWR • I PWRV DCIN < 4.2V orV DCIN < BAT + 30mV Charger powered from USB source;V PWR = V USBIN – R USB-PWR • I PWRNo chargingPWR: Hi-ZProgramming and Monitoring Charge CurrentThe charge current delivered to the battery from the walladapter supply is programmed using a single resistor fromthe IDC pin to ground.RVIIVRIDCCHRG DCCHRG DCIDC==10001000()(),Similarly, the charge current from the USB supply isprogrammed using a single resistor from the IUSB pinto ground.RVIIVRIUSBCHRG USBCHRG USBIUS==10001000()(),BCharge current out of the BAT pin can be determined atany time by monitoring the IDC or IUSB pin voltage andapplying the following equations:IVRch ing from wall adapterBATIDCIDC=•,(arg1000)•,(arg supIVRch ing from USB pBATIUSBIUSB=1000l y)94096xf104096xfProgramming Charge TerminationThe charge cycle terminates when the charge current falls below the programmed termination threshold during constant-voltage mode. This threshold is set by connect-ing an external resistor, R ITERM , from the ITERM pin to ground.The charge termination current threshold (I TERMINATE ) is set by the following equation:R V I I V R ITERM TERMINATETERMINATE ITERM==100100,The termination condition is detected by using an internal fi ltered comparator to monitor the ITERM pin. When the ITERM pin voltage drops below 100mV* for longer than t TERMINATE (typically 3ms), the charge cycle terminates, charge current latches off and the LTC4096 enters standby mode. When charging, transient loads on the BAT pin can cause the ITERM pin to fall below 100mV for short periods of time before the DC charge current has dropped below the programmed termination current. The 3ms fi lter time (t TERMINATE ) on the termination comparator ensures that transient loads of this nature do not result in premature charge cycle termination. Once the average charge current drops below the programmed termination threshold, the LTC4096 terminates the charge cycle and stops providing any current out of the BAT pin. In this state, any load on the BAT pin must be supplied by the battery.Low-Battery Charge Conditioning (Trickle Charge)This feature ensures that deeply discharged batteries are gradually charged before applying full charge current. If the BAT pin voltage is below 2.9V, the LTC4096 supplies 1/10th of the full charge current to the battery until the BAT pin rises above 2.9V. For example, if the charger is programmed to charge at 800mA from the wall adapter input and 500mA from the USB input, the charge currentOPERATION*Any external sources that hold the ITERM pin above 100mV will prevent the LTC4096 from terminating a charge cycle.during trickle charge mode would be 80mA and 50mA, respectively.The LTC4096X has no trickle charge mode.Automatic RechargeIn standby mode, the charger sits idle and monitors the battery voltage using a comparator with a 1.6ms fi lter time (t RECHRG ). A charge cycle automatically restarts when the battery voltage falls below 4.15V (which corresponds to approximately 80%-90% battery capacity). This ensures that the battery is kept at, or near, a fully charged condi-tion and eliminates the need for periodic charge cycle initiations. If the battery is removed from the charger, a sawtooth waveform appears at the battery output. This is caused by the repeated cycling between termination and recharge events. This cycling results in pulsing at the C H R G output; an LED connected to this pin will exhibit a blinking pattern, indicating to the user that a battery is not present. The frequency of the sawtooth is dependent on the amount of output capacitance.Status IndicatorsThe charge status output (CH R G ) has two states: pull-down and high impedance. The pull-down state indicates that the LTC4096 is in a charge cycle. Once the charge cycle has terminated or the LTC4096 is disabled, the pin state becomes high impedance. The pull-down state is capable of sinking up to 10mA.The power present output (PWR) has two states: DCIN/USBIN voltages and high impedance. These states are described in Table 1 and the circuit is shown in Figure 2. The high impedance state indicates that voltage is not present at either DCIN or USBIN, so LTC4096 lacks suffi cient power to charge the battery. The PWR present output is capable of sourcing up to 120mA steady state and includes short circuit protection.Information furnished by Linear Technology Corporation is believed to be accurate and reliable. However, no responsibility is assumed for its use. Linear Technology Corporation makes no representa-tion that the interconnection of its circuits as described herein will not infringe on existing patent rights.164096xfLinear Technology Corporation1630 McCarthy Blvd., Milpitas, CA 95035-7417(408) 432-1900 ● FAX: (408) 434-0507 ● © LINEAR TECHNOLOGY CORPORA TION 2006LT 1006 • PRINTED IN USARELATED PARTSPART NUMBER DESCRIPTIONCOMMENTSLTC3455Dual DC/DC Converter with USB Power Management and Li-Ion Battery Charger Effi ciency >96%, Accurate USB Current Limiting (500mA/100mA),4mm × 4mm QFN-24 PackageLTC4053USB Compatible Monolithic Li-Ion Battery ChargerStandalone Charger with Programmable Timer, Up to 1.25A Charge Current LTC4054/LTC4054X Standalone Linear Li-Ion Battery Chargerwith Integrated Pass Transistor in ThinSOT TM Thermal Regulation Prevents Overheating, C/10 Termination,C/10 Indicator, Up to 800mA Charge CurrentLTC4055USB Power Controller and Battery ChargerCharges Single-Cell Li-Ion Batteries Directly from USB Port,Thermal Regulation, 4mm × 4mm QFN-16 PackageLTC4058/LTC4058X Standalone 950mA Lithium-Ion Charger in DFN C/10 Charge Termination, Battery Kelvin Sensing, ±7% Charge AccuracyLTC4061Standalone Li-Ion Charger with Thermistor Interface 4.2V, ±0.35% Float Voltage, Up to 1A Charge Current,3mm × 3mm DFN-10 Package LTC4061-4.4Standalone Li-Ion Charger with Thermistor Interface 4.4V, ±0.4% Float Voltage, Up to 1A Charge Current,3mm × 3mm DFN-10 Package LTC4062Standalone Li-Ion Charger with Micropower Comparator4.2V, ±0.35% Float Voltage, Up to 1A Charge Current,3mm × 3mm DFN-10 PackageLTC4065/LTC4065A Standalone 750mA Li-Ion Chargerin 2mm × 2mm DFN 4.2V, ±0.6% Float Voltage, Up to 750mA Charge Current,2mm × 2mm DFN-6 PackageLTC4066USB Power Controller and Li-Ion Linear Battery Charger with Low-Loss Ideal DiodeSeamless Transition Between Input Power Sources: Li-Ion Battery, USB and Wall Adapter, Low-Loss (50m Ω) Ideal Diode, 4mm × 4mm QFN-24 Package LTC4068/LTC4068X Standalone Linear Li-Ion Battery Charger withProgrammable Termination Charge Current up to 950mA, Thermal Regulation,3mm × 3mm DFN-8 PackageLTC4069Standalone Li-Ion Battery Charger with NTC Thermistor Input in 2mm × 2mm DFN 4.2V, ±0.6% Float Voltage, Up to 750mA Charge Current, Timer Termination + C/10 Detection OutputLTC4075Dual Input Standalone Li-Ion Battery ChargerCharges Single-Cell Li-Ion Batteries from Wall Adapter and USB Inputs with Automatic Input Power Detection and Selection, 950mA Charger Current, Thermal Regulation, C/X Charge Termination, 3mm × 3mm DFN Package LTC4076Dual Input Standalone Li-Ion Battery ChargerCharges Single-Cell Li-Ion Batteries from Wall Adapter and USB Inputs with Automatic Input Power Detection and Selection, 950mA Charger Current,Thermal Regulation, C/X Charge Termination, 3mm × 3mm DFN Package LTC4077Dual Input Standalone Li-Ion Battery ChargerCharges Single-Cell Li-Ion Batteries from Wall Adapter and USB Inputs with Automatic Input Power Detection and Selection, 950mA Charger Current, Thermal Regulation, C/10 Charge Termination, 3mm × 3mm DFN Package LTC4085USB Power Manager with Ideal Diode Controller and Li-Ion ChargerCharges Single-Cell Li-Ion Batteries Directly from a USB Port, Thermal Regulation, 200m Ω Ideal Diode with <50m Ω option, 4mm × 3mm DFN-14 PackageLTC4089/LTC4089-5USB Power Manager with Ideal Diode Controller and High Effi ciency Li-Ion Battery Charger High Effi ciency 1.2A Charger from 6V to 36V (40V Max) Input, Charges Single Cell Li-Ion Batteries Directly from a USB Port, Thermal Regulation; 200m ΩIdeal Diode with <50m Ω Option, 4mm × 3mm DFN-14 Package, Bat-Track Adaptive Output Control (LTC4089); Fixed 5V Output (LTC4089-5)LTC4410USB Power Manager and Battery Charger Manages Total Power Between a USB Peripheral and Battery Charger, Ultralow Battery Drain: 1µA, ThinSOT PackageLTC4411/LTC4412Low Loss PowerPath TM Controller in ThinSOTAutomatic Switching Between DC Sources, Load Sharing, Replaces ORing DiodesThinSOT and PowerPath are trademarks of Linear Technology Corporation。
BT152中文资料

BT152中⽂资料GENERAL DESCRIPTIONQUICK REFERENCE DATAGlass passivated thyristors in a plastic SYMBOL PARAMETERMAX.MAX.MAX.UNIT envelope,intended for use in applications requiring high BT152-400R 600R 800R bidirectional blocking voltage V DRM ,Repetitive peak off-state 450650800V capability and high thermal cycling V RRM voltages performance.Typical applications I T(AV)Average on-state current 131313A include motor control,industrial and IT(RMS)RMS on-state current202020A domestic lighting,heating and static I TSMNon-repetitive peak on-state 200200200Aswitching.currentPINNING - TO220ABPIN CONFIGURATIONSYMBOLLIMITING VALUESLimiting values in accordance with the Absolute Maximum System (IEC 134).SYMBOL PARAMETERCONDITIONSMIN.MAX.UNIT -400R -600R -800R V DRM Repetitive peak off-state -45016501800V voltagesI T(AV)Average on-state current half sine wave; T mb ≤ 103 ?C -13A I T(RMS)RMS on-state current all conduction angles-20A I TSMNon-repetitive peak half sine wave; T j = 25 ?C prior to on-state currentsurge t = 10 ms -200A t = 8.3 ms -220A I 2t I 2t for fusingt = 10 ms-200A 2s dI T /dt Repetitive rate of rise of I TM = 50 A; I G = 0.2 A;-200A/µs on-state current after dI G /dt = 0.2 A/µs triggering I GM Peak gate current -5A V GM Peak gate voltage-5V V RGM Peak reverse gate voltage -5V P GM Peak gate power -20W P G(AV)Average gate power over any 20 ms period -0.5W T stg Storage temperature -40150?C T jOperating junction -125Ctemperature1 Although not recommended, off-state voltages up to 800V may be applied without damage, but the thyristor may switch to the on-state. The rate of rise of current should not exceed 15 A/µs.THERMAL RESISTANCESSYMBOL PARAMETERCONDITIONSMIN.TYP.MAX.UNIT R th j-mb Thermal resistance-- 1.1K/W junction to mounting base R th j-aThermal resistance in free air -60-K/Wjunction to ambientSTATIC CHARACTERISTICST j = 25 ?C unless otherwise stated SYMBOL PARAMETER CONDITIONSMIN.TYP.MAX.UNIT I GT Gate trigger current V D = 12 V; I T = 0.1 A -332mA I L Latching current V D = 12 V; I GT = 0.1 A -2580mA I H Holding current V D = 12 V; I GT = 0.1 A -1560mA V T On-state voltage I T = 40 A- 1.4 1.75V V GT Gate trigger voltage V D = 12 V; I T = 0.1 A-0.6 1.5V V D = V DRM(max); I T = 0.1 A; T j = 125 ?C 0.250.4-V I D , I ROff-state leakage currentV D = V DRM(max); V R = V RRM(max); T j = 125 ?C-0.21.0mADYNAMIC CHARACTERISTICST j = 25 ?C unless otherwise stated SYMBOL PARAMETER CONDITIONSMIN.TYP.MAX.UNIT dV D /dt Critical rate of rise of V DM = 67% V DRM(max); T j = 125 ?C;200300-V/µs off-state voltageexponential waveform gate open circuit t gt Gate controlled turn-on V D = V DRM(max); I G = 0.1 A; dI G /dt = 5 A/µs;-2-µs timeI TM = 40 At qCircuit commutated V D = 67% V DRM(max); T j = 125 ?C;-70-µsturn-off timeI TM = 50 A; V R = 25 V; dI TM /dt = 30 A/µs;dV D /dt = 50 V/µs; R GK = 100 ?MECHANICAL DATANotes1. Refer to mounting instructions for TO220 envelopes.2. Epoxy meets UL94 V0 at 1/8".DEFINITIONSData sheet statusObjective specification This data sheet contains target or goal specifications for product development. Preliminary specification This data sheet contains preliminary data; supplementary data may be published later. Product specification This data sheet contains final product specifications.Limiting valuesLimiting values are given in accordance with the Absolute Maximum Rating System (IEC 134). Stress above one or more of the limiting values may cause permanent damage to the device. These are stress ratings only and operation of the device at these or at any other conditions above those given in the Characteristics sections of this specification is not implied. Exposure to limiting values for extended periods may affect device reliability. Application informationWhere application information is given, it is advisory and does not form part of the specification.Philips Electronics N.V. 1997All rights are reserved. Reproduction in whole or in part is prohibited without the prior written consent of the copyright owner.The information presented in this document does not form part of any quotation or contract, it is believed to be accurate and reliable and may be changed without notice. No liability will be accepted by the publisher for any consequence of its use. Publication thereof does not convey nor imply any license under patent or other industrial or intellectual property rights.LIFE SUPPORT APPLICATIONSThese products are not designed for use in life support appliances, devices or systems where malfunction of these products can be reasonably expected to result in personal injury. Philips customers using or selling these products for use in such applications do so at their own risk and agree to fully indemnify Philips for any damages resulting from such improper use or sale.。
《LTCC元器件基础》课件

它是一种高性能、高可靠性的电 子元器件,广泛应用于航空航天 、军事、通信、汽车电子等领域 。
LTCC特点
01
02
03
04
高频性能优异
LTCC材料具有较低的介电常 数和介质损耗,适用于高频电
路。
集成度高
可以实现多层电路集成,减小 了元器件体积,提高了电路密
度。
可靠性高
LTCC材料具有较高的热导率 和机械强度,能够承受恶劣环
振荡器
总结词
高频率稳定性、低相位噪声、小型化
详细描述
LTCC振荡器利用低温共烧陶瓷的优良电气性能和多层布线技术,具有高频率稳定性和低相位噪声。此 外,LTCC振荡器可以实现小型化,广泛应用于各种通信系统和频率计量等领域。
04
LTCC元器件应用案例
手机中的LTCC元器件应用
总结词:小型电常数、低损耗、高稳定性
详细描述
LTCC电容器利用低温共烧陶瓷的优良介电性能,具有高介电常数和低损耗的特点 。这使得LTCC电容器具有高稳定性,能够满足各种高频、高稳定性的应用需求。
滤波器
总结词
高频率选择性、低插入损耗、小型化
详细描述
LTCC滤波器采用多层布线技术和低温 共烧陶瓷的高Q值特性,具有高频率 选择性和低插入损耗。此外,LTCC滤 波器可以实现小型化,方便集成到无 线通信等系统中。
航天器中的LTCC元器件应用
总结词:高精度、高稳定性、轻量化
航天器中使用的LTCC元器件需要具备高精度和高稳定性的特性,以确保航天器的安全和可靠性。LTCC技术在航天器中应用广 泛,如微波组件、天线、滤波器等。
05
LTCC元器件发展趋势与挑战
LTCC元器件发展趋势
01
“开尔文勋爵”威廉汤姆生

“开尔文勋爵”威廉汤姆生在英国的物理学家中,有三位物理学家大家比较熟悉,他们生前都被封以爵位,死后又都被安葬于英国伦敦著名的威斯敏斯特教堂。
第一位是牛顿(1642-1727年),1705年英国女王加封他为艾萨克爵士,1727年以85岁高龄死后被葬于威斯敏斯特教堂;还有两位都是汤姆生。
一位是我已经撰文介绍过的约瑟夫.约翰.汤姆生即J.J.汤姆生(1856-1940年),1908年受封为爵士,1906年因为发现电子而荣获诺贝尔物理学奖,1940年死后被安葬于威斯敏斯特教堂牛顿的旁边。
还有一位是威廉.汤姆生即W.汤姆生(1824-1907年),1892年英国女王维多利亚封他为勋爵,领衔“开尔文勋爵”,1907年死后同样被安葬于威斯敏斯特教堂。
今天,我撰文介绍英国大物理学家威廉.汤姆生即“开尔文勋爵”。
威廉.汤姆生(1824-1907年)于1824年7月26日出生于英格兰贝尔法斯特的英国知识分子家庭,其父亲是英国皇家学会的著名数学教授。
汤姆生童年丧母,又当爹来又当娘的父亲,尽管对他和哥哥杰姆十分疼爱,当为了孩子们的前途,在他很小的时候,老汤姆生就对他和哥哥进行了严格而系统的教育。
从6岁开始,他就在父亲的指导下学习数学。
他父亲还经常在凌晨带他去郊外散步,一路上向他提出各种各样有趣的问题,培养他思考问题的习惯。
这对汤姆生后来善于独立思考起了很大的作用。
汤姆生从启蒙到中学教育,都是由父亲自编教材,在家里完成的。
1832年,汤姆生的父亲应聘出任格拉斯哥大学数学教授,全家一起迁到了格拉斯哥城。
后来,汤姆生一生主要的科学活动都是在格拉斯哥进行的。
也是从这一年开始,刚刚8岁的汤姆生,这个从未进过学校的小孩,直接到格拉斯哥大学开始旁听数学、电学等课程,当了两年的旁听生。
在这两年里,汤姆生和哥哥很争气,也很淘气。
不仅学到了科学知识,而且还自制了莱顿瓶、伏打电堆等实验用品。
不过,淘气的兄弟俩还曾经玩了一次恶作剧,欺骗好奇的妹妹维丽用手摸充了电的莱顿瓶,妹妹被电得大哭。
LTC4155EUFD#TRPBF;LTC4155IUFD#PBF;LTC4155IUFD#TRPBF;LTC4155EUFD#PBF;中文规格书,Datasheet资料
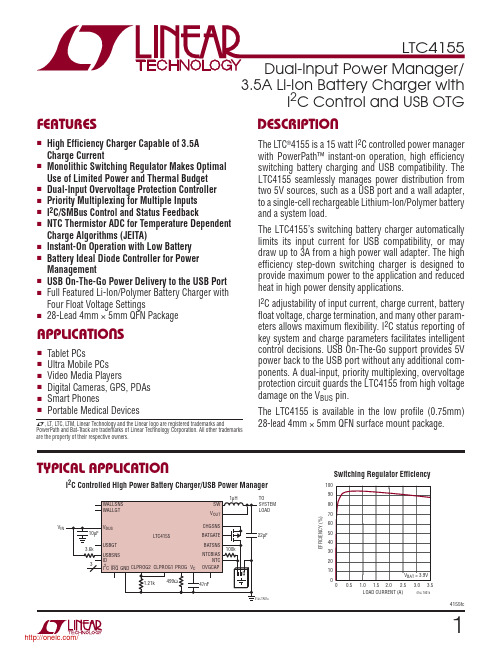
14155fcT YPICAL APPLICATIONF EATURES D ESCRIPTION3.5A Li-Ion Battery Charger withI 2C Control and USB OTGThe L TC ®4155 is a 15 watt I 2C controlled power managerwith PowerPath™ instant-on operation, high efficiency switching battery charging and USB compatibility. The LTC4155 seamlessly manages power distribution from two 5V sources, such as a USB port and a wall adapter, to a single-cell rechargeable Lithium-Ion/Polymer battery and a system load.The LTC4155’s switching battery charger automatically limits its input current for USB compatibility, or may draw up to 3A from a high power wall adapter. The high efficiency step-down switching charger is designed to provide maximum power to the application and reduced heat in high power density applications.I 2C adjustability of input current, charge current, battery float voltage, charge termination, and many other param-eters allows maximum flexibility. I 2C status reporting of key system and charge parameters facilitates intelligent control decisions. USB On-The-Go support provides 5V power back to the USB port without any additional com-ponents. A dual-input, priority multiplexing, overvoltage protection circuit guards the LTC4155 from high voltage damage on the V BUS pin.The LTC4155 is available in the low profile (0.75mm) 28-lead 4mm × 5mm QFN surface mount package.I 2C Controlled High Power Battery Charger/USB Power ManagerA PPLICATIONS nHigh Efficiency Charger Capable of 3.5A Charge Currentn Monolithic Switching Regulator Makes Optimal Use of Limited Power and Thermal Budget n Dual-Input Overvoltage Protection Controller n Priority Multiplexing for Multiple Inputs n I 2C/SMBus Control and Status Feedbackn NTC Thermistor ADC for Temperature Dependent Charge Algorithms (JEITA)n Instant-On Operation with Low Battery n Battery Ideal Diode Controller for Power Managementn USB On-The-Go Power Delivery to the USB Port n Full Featured Li-Ion/Polymer Battery Charger with Four Float Voltage Settings n 28-Lead 4mm × 5mm QFN PackagenTablet PCsn Ultra Mobile PCs n Video Media Playersn Digital Cameras, GPS, PDAs n Smart Phonesn Portable Medical DevicesL , L T, L TC, L TM, Linear Technology and the Linear logo are registered trademarks andPowerPath and Bat-T rack are trademarks of Linear Technology Corporation. All other trademarks are the property of their respective owners.V INLOAD CURRENT (A)0E F F I C I E N C Y (%)1030405010070 1.0 2.0 2.54155 TA01b208090600.51.5 3.03.5Switching Regulator Efficiency/T ABLE OF CONTENTSFeatures (1)Applications (1)Typical Application (1)Description (1)Absolute Maximum Ratings (3)Order Information (3)Pin Configuration (3)Electrical Characteristics (4)Typical Performance Characteristics (9)Pin Functions (12)Block Diagram (15)Timing Diagrams (16)Operation (17)I2C (17)Applications Information (40)Typical Applications (47)Package Description (51)Typical Application (52)Related Parts (52)24155fc/34155fcP IN CONFIGURATIONA BSOLUTE MAXIMUM RATINGS V BUS (Transient) t < 1ms, Duty Cycle < 1% ...–0.3V to 7VV BUS (Steady State), BATSNS, IRQ , NTC......–0.3V to 6V DVCC, SDA, SCL (Note 3) ........................–0.3V to V MAX I WALLSNS , I USBSNS ...............................................±20mA I NTCBIAS , I IRQ ..........................................................10mAI SW , I VOUT , I CHGSNS (Both Pins in Each Case)..............4A Operating Junction Temperature Range ...–40°C to 125°C Storage Temperature Range ..................–65°C to 150°C(Notes 1, 2)910TOP VIEW29GNDUFD PACKAGE28-LEAD (4mm w 5mm) PLASTIC QFN11121328272625241423654321SDA DVCC IRQ ID CLPROG1CLPROG2WALLSNS USBSNS V OUT V OUT CHGSNSCHGSNS PROG BATGATE BATSNS NTCS C LS WS WV B U SV B U S V B U SU S B G TO V G C A PW A L L G TV CV O U T S N SN T C B I A S717181920212216815T JMAX = 125°C, θJA = 43°C/WEXPOSED PAD (PIN 29) IS GND, MUST BE SOLDERED TO PCBO RDER INFORMATION LEAD FREE FINISH TAPE AND REEL PART MARKING*PACKAGE DESCRIPTIONTEMPERATURE RANGE LTC4155EUFD#PBF LTC4155EUFD#TRPBF 415528-Lead (4mm × 5mm × 0.75mm) Plastic QFN –40°C to 125°C LTC4155IUFD#PBFLTC4155IUFD#TRPBF415528-Lead (4mm × 5mm × 0.75mm) Plastic QFN–40°C to 125°CConsult L TC Marketing for parts specified with wider operating temperature ranges. *The temperature grade is identified by a label on the shipping container.Consult L TC Marketing for information on non-standard lead based finish parts.For more information on lead free part marking, go to: /leadfree/For more information on tape and reel specifications, go to: /tapeandreel//Thel denotes the specifications which apply over the specified operating junction temperature range, otherwise specifications are at T A≈ T J = 25°C (Note 2). V BUS = 5V, BATSNS = 3.7V, DVCC = 3.3V,R CLPROG1 = R CLPROG2 = 1.21k, R PROG = 499Ω, unless otherwise noted.E LECTRICAL CHARACTERISTICSSYMBOL PARAMETER CONDITIONS MIN TYP MAX UNITS Switching Battery ChargerV BUS Input Supply Voltage l 4.35 5.5V V BUSREG Undervoltage Current Reduction Input Undervoltage Current Limit Enabled 4.30VI VBUSQ Input Quiescent Current USB Suspend Mode100mA I VBUS Mode, I VOUT = 0μA, Charger Off500mA – 3A I VBUS Modes, I VOUT = 0μA, Charger Off 0.0600.56017mAmAmAI BATQ Battery Drain Current V BUS > V UVLO, Battery Charger Off, I VOUT = 0μAV BUS = 0V, I VOUT = 0μAStorage and Shipment Mode, DVCC = 0V 7.02.00.63.01.25μAμAμAI VBUSLIM Total Input Current When LoadExceeds Power Limit 100mA I VBUS Mode (USB Lo Power) (Default)500mA I VBUS Mode (USB Hi Power)600mA I VBUS Mode700mA I VBUS Mode800mA I VBUS Mode900mA I VBUS Mode (USB 3.0)1.00A I VBUS Mode1.25A I VBUS Mode1.50A I VBUS Mode1.75A I VBUS Mode2.00A I VBUS Mode2.25A I VBUS Mode2.50A I VBUS Mode2.75A I VBUS Mode3.00A I VBUS Mode (Default)2.5mA I VBUS Mode (USB Suspend)lll6546055065074580095011501425165019002050235025502800804805706707708501000123015001750200021752475272529501.81005006007008009001025130015751875212523002600290031002.5mAmAmAmAmAmAmAmAmAmAmAmAmAmAmAmAV FLOAT BATSNS Regulated Output VoltageSelected by I2C Control.Switching Modes 4.05V Setting (Default)4.10V Setting4.15V Setting4.20V Settingllll4.024.074.124.174.054.104.154.204.084.134.184.23VVVVI CHARGE Regulated Battery Charge CurrentSelected by I2C Control 12.50% Charge Current Mode18.75% Charge Current Mode25.00% Charge Current Mode31.25% Charge Current Mode37.50% Charge Current Mode43.75% Charge Current Mode50.00% Charge Current Mode56.25% Charge Current Mode62.50% Charge Current Mode68.75% Charge Current Mode75.00% Charge Current Mode81.25% Charge Current Mode87.50% Charge Current Mode93.75% Charge Current Mode100.0% Charge Current Mode (Default)290430590730880102511801330148516351780191520652210235031546562077092510751230138515351685183519802130228024303405006508109701125128014401585173518902045219523502500mAmAmAmAmAmAmAmAmAmAmAmAmAmAmAI CHARGE(MAX)Regulated Battery Charge Current100.0% Charge Current Mode, R PROG = 340Ω 3.44 3.57 3.70AV OUT PowerPath Regulated OutputVoltage (V BUS Power Available)Suspend Mode, I VOUT = 1mABattery Charger Enabled, Charging, BATSNS ≥ 3.5VBattery Charger Terminated or Battery ChargerDisabled4.35BATSNS4.354.54.5VVVV OUT(MIN)Low Battery Instant-On OutputVoltage (V BUS Power Available)Battery Charger Enabled, Charging, BATSNS ≤ 3.3V 3.40 3.50V /44155fcELECTRICAL CHARACTERISTICSThel denotes the specifications which apply over the specified operating junction temperature range, otherwise specifications are at T A≈ T J = 25°C (Note 2). V BUS = 5V, BATSNS = 3.7V, DVCC = 3.3V, R CLPROG1 = R CLPROG2 = 1.21k, R PROG = 499Ω, unless otherwise noted.SYMBOL PARAMETER CONDITIONS MIN TYP MAX UNITSI VOUT V OUT Current Available BeforeLoading Battery 2.5mA I VBUS Mode (USB Suspend)100mA I VBUS Mode, BAT = 3.3V500mA I VBUS Mode, BAT = 3.3V600mA I VBUS Mode, BAT = 3.3V700mA I VBUS Mode, BAT = 3.3V800mA I VBUS Mode, BAT = 3.3V900mA I VBUS Mode, BAT = 3.3V1.00A I VBUS Mode, BAT = 3.3V1.25A I VBUS Mode, BAT = 3.3V1.50A I VBUS Mode, BAT = 3.3V1.75A I VBUS Mode, BAT = 3.3V2.00A I VBUS Mode, BAT =3.3V2.25A I VBUS Mode, BAT =3.3V2.50A I VBUS Mode, BAT =3.3V2.75A I VBUS Mode, BAT =3.3V3.00A I VBUS Mode, BAT = 3.3V1 1.37667381094410931200139717282072241127002846315434083657mAmAmAmAmAmAmAmAmAmAmAmAmAmAmAmAV PROG PROG Pin Servo Voltage12.50% Charge Current Mode18.75% Charge Current Mode25.00% Charge Current Mode31.25% Charge Current Mode37.50% Charge Current Mode43.75% Charge Current Mode50.00% Charge Current Mode56.25% Charge Current Mode62.50% Charge Current Mode68.75% Charge Current Mode75.00% Charge Current Mode81.25% Charge Current Mode87.50% Charge Current Mode93.75% Charge Current Mode100.0% Charge Current Mode (Default)150225300375450525600675750825900975105011251200mVmVmVmVmVmVmVmVmVmVmVmVmVmVmVV RECHRG Recharge Battery ThresholdVoltageThreshold Voltage Relative to V FLOAT96.697.698.4%t TERMINATE Safety Timer Termination PeriodSelected by I2C Control. TimerStarts When BATSNS ≥ V FLOAT 1-Hour Mode2-Hour Mode4-Hour Mode (Default)8-Hour Mode0.951.903.817.631.062.124.248.481.172.334.669.32HoursHoursHoursHoursV LOWBAT Threshold Voltage Rising ThresholdHysteresis 2.65 2.81302.95VmVt BADBAT Bad Battery Termination Time BATSNS < (V LOWBAT – ΔV LOWBAT)0.470.530.59HoursV C/x Full Capacity Charge IndicationPROG Voltage Selected by I2CControl C/10 Mode (I CHARGE = 10%FS) (Default)C/5 Mode (I CHARGE = 20%FS)C/20 Mode (I CHARGE = 5%FS)C/50 Mode (I CHARGE = 2%FS)110230155012024024601302503370mVmVmVmVh PROG Ratio of I CHGSNS to PROG PinCurrent1000mA/mAh CLPROG1 (Note 4)Ratio of Measured V BUS Current toCLPROG1 Sense CurrentCLPROG1 I VBUS Mode990mA/mA/54155fcELECTRICAL CHARACTERISTICSThel denotes the specifications which apply over the specified operating junction temperature range, otherwise specifications are at T A≈ T J = 25°C (Note 2). V BUS = 5V, BATSNS = 3.7V, DVCC = 3.3V, R CLPROG1 = R CLPROG2 = 1.21k, R PROG = 499Ω, unless otherwise noted.SYMBOL PARAMETER CONDITIONS MIN TYP MAX UNITSh CLPROG2 (Note 4)Ratio of Measured V BUS Current toCLPROG2 Sense Current2.5mA I VBUS Mode (USB Suspend)100mA I VBUS Mode500mA I VBUS Mode600mA I VBUS Mode700mA I VBUS Mode800mA I VBUS Mode900mA I VBUS Mode1.00A I VBUS Mode1.25A I VBUS Mode1.50A I VBUS Mode1.75A I VBUS Mode2.00A I VBUS Mode2.25A I VBUS Mode2.50A I VBUS Mode2.75A I VBUS Mode3.00A I VBUS Mode197946655765775883999012221494174619992175247727302956mA/mAmA/mAmA/mAmA/mAmA/mAmA/mAmA/mAmA/mAmA/mAmA/mAmA/mAmA/mAmA/mAmA/mAmA/mAmA/mAV CLPROG1CLPROG1 Servo Voltage inCurrent LimitCLPROG1 I VBUS Mode 1.2VV CLPROG2CLPROG2 Servo Voltage inCurrent Limit 2.5mA I VBUS Mode (USB Suspend)100mA – 3A I VBUS Modes1031.2mVVf OSC Switching Frequency 2.05 2.25 2.50MHz R PMOS High Side Switch On Resistance0.090ΩR NMOS Low Side Switch On Resistance0.080ΩR CHG Battery Charger Current SenseResistance0.040ΩI PEAK Peak Inductor Current Clamp500mA – 3A I VBUS Modes 6.7A Step-Up Mode PowerPath Switching Regulator (USB On-The-Go)V BUS Output Voltage0mA ≤ I VBUS ≤ 500mA 4.75 5.25V V OUT Input Voltage 2.9V I VBUSOTG Output Current Limit 1.4A I VOUTOTGQ V OUT Quiescent Current I VBUS = 0mA 1.96mA V CLPROG2Output Current Limit Servo Voltage 1.2VV BATSNSUVLO V BATSNS Undervoltage Lockout V BATSNS FallingHysteresis 2.65 2.81302.95VmVt SCFAUL T Short-Circuit Fault Delay V BUS < 4V7.2ms Overvoltage Protection, Priority Multiplexer and Undervoltage Lockout; USB Input Connected to USBSNS Through 3.6k Resistor; WALL Input Connected to WALLSNS Through 3.6k ResistorV UVLO USB Input, Wall InputUndervoltage Lockout Rising ThresholdFalling ThresholdHysteresis4.053.901004.454.25VVmVV DUVLO USB Input, Wall Input to BATSNSDifferential Undervoltage Lockout Rising ThresholdFalling ThresholdHysteresis1005070425375mVmVmVV OVLO USB Input, Wall Input OvervoltageProtection ThresholdRising Threshold 5.75 6.0 6.3V V USBGTACTV USBGT Output Voltage Active USBSNS < V USBOVLO 2 • V USBSNS V V WALLGTACTV WALLGT Output Voltage Active WALLSNS < V WALLOVLO 2 • V WALLSNS V V USBGTPROT USBGT Output Voltage Protected USBSNS > V USBOVLO0Vh t t p://o n e i c.c o m/64155fcELECTRICAL CHARACTERISTICSThel denotes the specifications which apply over the specified operating junction temperature range, otherwise specifications are at T A≈ T J = 25°C (Note 2). V BUS = 5V, BATSNS = 3.7V, DVCC = 3.3V,R CLPROG1 = R CLPROG2 = 1.21k, R PROG = 499Ω, unless otherwise noted.SYMBOL PARAMETER CONDITIONS MIN TYP MAX UNITS V WALLGTPROT WALLGT Output Voltage Protected WALLSNS > V WALLOVLO0VV USBGTLOAD, V WALLGTLOAD USBGT, WALLGT Voltage UnderLoad5V Through 3.6k into WALLSNS, USBSNS,I USBGT, I WALLGT = 1μA8.48.9VI USBSNSQ USBSNS Quiescent Current V USBSNS = 5V, V USBSNS > V WALLSNSV USBSNS = 5V, V WALLSNS > V USBSNS 2754μAμAI WALLSNSQ WALLSNS Quiescent Current V WALLSNS = 5V, V WALLSNS > V USBSNSV WALLSNS = 5V, V USBSNS > V WALLSNS 2754μAμAt RISE OVGCAP Time to Reach Regulation C OVGCAP = 1nF 1.2ms IRQ Pin CharacteristicsI IRQ IRQ Pin Leakage Current V IRQ = 5V1μA V IRQ IRQ Pin Output Low Voltage I IRQ = 5mA75100mV ID Pin CharacteristicsI ID ID Pin Pull-Up Current V ID = 0V355585μAV ID_OTG ID Pin Threshold Voltage ID Pin FallingHysteresis 0.50.860.20.95VVOvertemperature Battery ConditionerI BATOVERTEMP Overtemp Battery DischargeCurrentOnly When Enabled via I2C Control125mA V BATOVERTEMP Overtemp Battery Voltage Target Only When Enabled via I2C Control 3.85V Thermistor Measurement SystemκOFFSET V NTC/V NTCBIAS A/D Lower RangeEnd V NTC/V NTCBIAS Ratio Below Which Only 0x00Is Returned0.113V/VκHIGH V NTC/V NTCBIAS A/D Upper RangeEnd V NTC/V NTCBIAS Ratio Above Which Only 0x7FIs Returned0.895V/VκSPAN A/D Span Coefficient(Decimal Format)6.091 6.162 6.191mV/V/LSBd TOO_COLD NTCVAL at NTC_TOO_COLD(Decimal Format)Warning ThresholdReset Threshold102981029810298CountCountd TOO_WARM NTCVAL at NTC_TOO_WARM(Decimal Format)Warning ThresholdReset Threshold414541454145CountCountd HOT_FAUL T NTCVALatHOT_FAUL T(Decimal Format)Fault ThresholdReset Threshold192319231923CountCountI NTC NTC Leakage Current–100100nAIdeal DiodeV FWD Forward Voltage Detection Input Power Available, Battery Charger Off15mV I2C PortDVCC I2C Logic Reference Level(Note 3) 1.7V MAX VI DVCCQ DVCC Current SCL/SDA = 0kHz0.25μAV DVCC_UVLO DVCC UVLO 1.0V ADDRESS I2C Address0001_001[R/W]bV IH,SDA,SCL Input High Threshold70% DVCC V IL,SDA,SCL Input Low Threshold30% DVCCI IH,SDA,SCL Input Leakage High SDA, SCL = DVCC–11μA /74155fcELECTRICAL CHARACTERISTICSThel denotes the specifications which apply over the specified operating junction temperature range, otherwise specifications are at T A≈ T J = 25°C (Note 2). V BUS = 5V, BATSNS = 3.7V, DVCC = 3.3V,R CLPROG1 = R CLPROG2 = 1.21k, R PROG = 499Ω, unless otherwise noted.SYMBOL PARAMETER CONDITIONS MIN TYP MAX UNITS I IL,SDA,SCL Input Leakage Low SDA, SCL = 0V–11μA V OL Digital Output Low (SDA)I SDA = 3mA0.4V f SCL Clock Operating Frequency400kHz t BUF Bus Free Time Between STOP andSTART Condition1.3μst HD_SDA Hold Time After (Repeated) STARTCondition0.6μst SU_SDA Repeated START Condition Set-UpTime0.6μs t SU_STO STOP Condition Time0.6μs t HD_DAT(OUT)Data Hold Time0900ns t HD_DAT(IN)Input Data Hold Time0ns t SU_DAT Data Set-Up Time100ns t LOW Clock LOW Period 1.3μs t HIGH Clock HIGH Period0.6μs t f Clock Data Fall Time20300ns t r Clock Data Rise Time20300ns t SP Spike Suppression Time50nsNote 1: Stresses beyond those listed under Absolute Maximum Ratings may cause permanent damage to the device. Exposure to any Absolute Maximum Rating condition for extended periods may affect device reliability and lifetime.Note 2: The LTC4155E is tested under pulsed load conditions such that T J≈ T A. The LTC4155E is guaranteed to meet performance specifications from 0°C to 85°C junction temperature. Specifications over the–40°C to 125°C operating junction temperature range are assured by design, characterization and correlation with statistical process controls. The LTC4155I is guaranteed over the full –40°C to 125°C operating junction temperature range. The junction temperature (T J, in °C) is calculated from the ambient temperature (T A, in °C) and power dissipation (P D, in watts) according to the formula:T J = T A + (P D • θJA), where the package thermal impedanceθJA = 43°C/W)Note that the maximum ambient temperature consistent with these specifications is determined by specific operating conditions in conjunction with board layout, the rated package thermal resistance and other environmental factors.Note 3. V MAX is the maximum of V BUS or BATSNSNote 4. Total input current is I VBUSQ + V CLPROG/R CLPROG • (h CLPROG + 1)./84155fc94155fcT YPICAL PERFORMANCE CHARACTERISTICS Switching Regulator EfficiencyBattery Charger Total Effi ciency vs Battery VoltageBattery and V BUS Currents vs V OUT CurrentBattery and V BUS Currentsvs V OUT CurrentBattery Drain Current vs TemperatureV OUT CURRENT (A)C U R R E N T (A )0.20.40.60.84155 G01–0.2–0.40.20.40.6 1.0V OUT CURRENT (A)0–2C U R R E N T (A )–10123412344155 G025CURRENT (A)E F F I C I E N C Y (%)POWER LOST (W)92.5 1.54155 G0485.080.00.51.02.0INCLUDES LOSSES FROM 2w Si7938DP OVP FETSXFL4020-102ME INDUCTOR AND Si5481DU CHARGER FET77.575.095.090.087.582.5 3.52.01.00.54.03.02.51.52.53.0 3.5BATTERY VOLTAGE (V)2.40.50L O A D C U R R E N T (A )0.751.001.251.501.752.73.0 3.3 3.64155 G063.94.2USB Compliant Load Current Available Before Discharging Battery500mA USB Limited BatteryCharge Current vs Battery Voltage100mA USB Limited BatteryCharge Current vs Battery VoltageV OUT Voltage vs Battery VoltageBATTERY VOLTAGE (V)2.40.70.60.50.40.30.20.10 3.3 3.94155 G072.73.03.64.2C H A R G E C U R R E N T (A )TEMPERATURE (°C)–25C U R R E N T (μA )6810954155 G03425793153565–10–40110205080125BATTERY VOLTAGE (V)2.455E F F I C I E N C Y (%)60707580 3.61004155 G0565 3.02.73.93.34.2859095INCLUDES LOSSES FROM 2w Si7938DP OVP FETSXFL4020-102ME INDUCTOR AND Si5481DU CHARGER FETBATTERY VOLTAGE (V)2.40C H A R G E C U R R E N T (m A )204060801002.73.0 3.3 3.64155 G083.94.2BATTERY VOLTAGE (V)2.43.4V O U T V O L T A G E (V )3.63.53.83.74.03.94.24.14.44.3 2.73.0 3.3 3.64155 G093.94.2T A = 25°C (Note 2). V BUS = 5V, BATSNS = 3.7V, DVCC = 3.3V, R CLPROG1 = R CLPROG2 = 1.21k, R PROG = 499Ω, unless otherwise noted./104155fcTYPICAL PERFORMANCE CHARACTERISTICSOscillator Frequency vs TemperatureAutomatic Charge Current Reduction vs Battery VoltageV BUS Current vs V BUS Voltage in USB Suspend ModeV OUT Voltage vs V OUT Current in USB Suspend ModeV BUS Current vs V OUT Current in USB Suspend ModeBattery Charger Resistancevs TemperatureNormalized Float Voltage vs TemperatureT A = 25°C (Note 2). V BUS = 5V, BATSNS = 3.7V,DVCC = 3.3V, R CLPROG1 = R CLPROG2 = 1.21k, R PROG = 499Ω, unless otherwise noted.TEMPERATURE (°C)–40C H A R G E R T O T A L R E S I S T A N C E (m Ω)505560604613 G10454035–15103585BATTERY VOLTAGE (V)2.4N O R M A L I Z E D C H A R G E C U R R E N T (%)20406080100120 2.7 3.0 3.3 3.64155 G13V BUS VOLTAGE (V)2.5V B U S C U R R E N T (m A )0.51.01.52.03.0 3.03.54.0 4.54155 G145.05.52.5V OUT CURRENT (mA)0V O U T V O L T A G E (V )3.94.04.1 1.52.54155 G153.83.73.60.51.02.04.24.34.4V OUT CURRENT (mA)V B U S C U R R E N T (m A )1.52.02.04155 G161.00.50.51.01.52.52.5Static DVCC Current vs DVCC VoltageRising Overvoltage Lockout Threshold vs TemperatureTEMPERATURE (°C)–400.995N O R M A L I Z E D F L O A T V O L T A G E (V )0.9960.9980.9991.000–1020351254155 G110.997–25550659511080TEMPERATURE (°C)2.17O S C I L L A T O R F R E Q U E N C Y (M H z )2.212.252.292.192.232.27–102050804155 G12125110–25–405356595DVCC VOLTAGE (V)D V C C C U R RE N T (μA )0.30.40.5354155 G170.20.11240.60.70.8TEMPERATURE (°C)6.07V B U S V O L T A G E (V )6.096.116.086.106.12–102050804155 G18125110–25–405356595h t t p ://o n e i c .c o m /分销商库存信息:LINEAR-TECHNOLOGYLTC4155EUFD#TRPBF LTC4155IUFD#PBF LTC4155IUFD#TRPBF LTC4155EUFD#PBF。
ASTM C1592-04 无损检测的测量指南
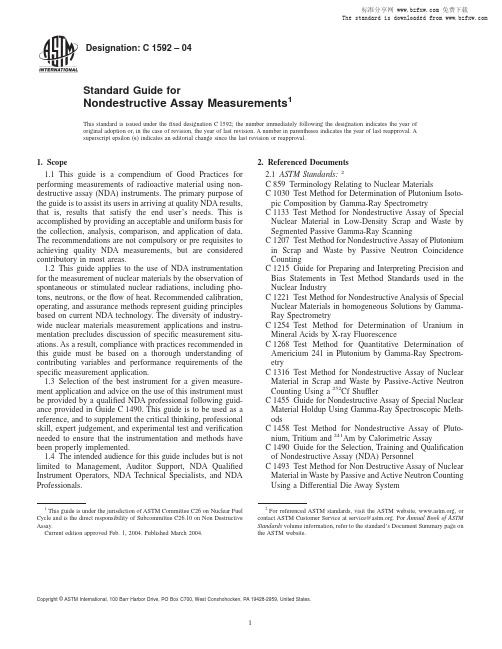
Designation:C1592–04Standard Guide forNondestructive Assay Measurements1This standard is issued under thefixed designation C1592;the number immediately following the designation indicates the year of original adoption or,in the case of revision,the year of last revision.A number in parentheses indicates the year of last reapproval.A superscript epsilon(e)indicates an editorial change since the last revision or reapproval.1.Scope1.1This guide is a compendium of Good Practices for performing measurements of radioactive material using non-destructive assay(NDA)instruments.The primary purpose of the guide is to assist its users in arriving at quality NDA results, that is,results that satisfy the end user’s needs.This is accomplished by providing an acceptable and uniform basis for the collection,analysis,comparison,and application of data. The recommendations are not compulsory or pre requisites to achieving quality NDA measurements,but are considered contributory in most areas.1.2This guide applies to the use of NDA instrumentation for the measurement of nuclear materials by the observation of spontaneous or stimulated nuclear radiations,including pho-tons,neutrons,or theflow of heat.Recommended calibration, operating,and assurance methods represent guiding principles based on current NDA technology.The diversity of industry-wide nuclear materials measurement applications and instru-mentation precludes discussion of specific measurement situ-ations.As a result,compliance with practices recommended in this guide must be based on a thorough understanding of contributing variables and performance requirements of the specific measurement application.1.3Selection of the best instrument for a given measure-ment application and advice on the use of this instrument must be provided by a qualified NDA professional following guid-ance provided in Guide C1490.This guide is to be used as a reference,and to supplement the critical thinking,professional skill,expert judgement,and experimental test and verification needed to ensure that the instrumentation and methods have been properly implemented.1.4The intended audience for this guide includes but is not limited to Management,Auditor Support,NDA Qualified Instrument Operators,NDA Technical Specialists,and NDA Professionals.2.Referenced Documents2.1ASTM Standards:2C859Terminology Relating to Nuclear MaterialsC1030Test Method for Determination of Plutonium Isoto-pic Composition by Gamma-Ray SpectrometryC1133Test Method for Nondestructive Assay of Special Nuclear Material in Low-Density Scrap and Waste by Segmented Passive Gamma-Ray ScanningC1207Test Method for Nondestructive Assay of Plutonium in Scrap and Waste by Passive Neutron Coincidence CountingC1215Guide for Preparing and Interpreting Precision and Bias Statements in Test Method Standards used in the Nuclear IndustryC1221Test Method for Nondestructive Analysis of Special Nuclear Materials in homogeneous Solutions by Gamma-Ray SpectrometryC1254Test Method for Determination of Uranium in Mineral Acids by X-ray FluorescenceC1268Test Method for Quantitative Determination of Americium241in Plutonium by Gamma-Ray Spectrom-etryC1316Test Method for Nondestructive Assay of Nuclear Material in Scrap and Waste by Passive-Active Neutron Counting Using a252Cf ShufflerC1455Guide for Nondestructive Assay of Special Nuclear Material Holdup Using Gamma-Ray Spectroscopic Meth-odsC1458Test Method for Nondestructive Assay of Pluto-nium,Tritium and241Am by Calorimetric AssayC1490Guide for the Selection,Training and Qualification of Nondestructive Assay(NDA)PersonnelC1493Test Method for Non Destructive Assay of Nuclear Material in Waste by Passive and Active Neutron Counting Using a Differential Die Away System1This guide is under the jurisdiction of ASTM Committee C26on Nuclear Fuel Cycle and is the direct responsibility of Subcommittee C26.10on Non Destructive Assay.Current edition approved Feb.1,2004.Published March2004.2For referenced ASTM standards,visit the ASTM website,,or contact ASTM Customer Service at service@.For Annual Book of ASTM Standards volume information,refer to the standard’s Document Summary page on the ASTM website.1Copyright©ASTM International,100Barr Harbor Drive,PO Box C700,West Conshohocken,PA19428-2959,United States.标准分享网 免费下载The standard is downloaded from C1514Test Method for Measurement of235U Fraction Using the Enrichment Meter Principle3.Terminology3.1Definitions presented here are confined to those terms not defined in common nuclear materials glossaries/references or whose use is specific to this application.The use of statistical terms is consistent with the definitions in American National Standard Statistical Terminology and Notation for Nuclear Materials Management,N15.5-1972.Some of those definitions are repeated here for convenience to the reader. 3.2Definitions:3.2.1(a n)reactions—(a,n)reactions occur when energetic alpha particles collide with low atomic number nuclei,such as O,F,or Mg,producing single neutrons.3.2.2240Pu effective mass—m eff is the mass of240Pu that would produce the same coincident,or total,neutron response in the instrument as the assay item,all other factors remaining unchanged.It is correlated to the quantity of even mass isotopes of plutonium in the assay item.3.2.3absorber foils—thin metal foils that are used to reduce the contribution of low-energy gamma rays to the overall count rate.3.2.4accidentals—the accidental or random summing of neutrons generate a signature like that from true or Real coincidences.For shift register pulse train deconvolution the number of neutrons detected in the(A)gate period following the initial detection of each neutron during the selected count time t.This is a measured quantity.3.2.5accuracy—(1)bias;(2)the closeness of a measured value to the true value;and(3)the closeness of a measured value to an accepted reference or standard value.3.2.6assay—to determine quantitatively the amount of one or more nuclides of interest contained in an item,or the result of such a determination.3.2.7background—extraneous signal superimposed on the signal of interest.3.2.8benign matrix—bulk material that has no effect on the result of the measured parameter.3.2.9bias—a constant positive or negative deviation of the method average from the correct value or accepted reference value.3.2.10calibration—the determination of the values of the significant parameters by comparison with values indicated by a reference instrument,by a set of reference standards or modeled parameters.C859 3.2.11certification—a written declaration from a certifying body or its legitimate designee that a particular measurement process complies with stated criteria,or a measured item has the stated characteristics.3.2.12coincident neutrons—two or more neutrons emitted simultaneously from single event,such as from a nucleus duringfission.3.2.13collimator—usually constructed of lead or tungsten,a collimator serves to define a gamma-ray detector’s horizontal and vertical viewing angles and to shield the detector from ambient radiation.3.2.14confidence interval—the range of values,calculated from an estimate of the mean and standard deviation,which is expected to include the population mean with a stated level of confidence.3.2.15control chart—a graphical plot of test results with respect to time or sequence of measurement together with limits in which they are expected to lie when the system is ina state of statistical control.3.2.16control limits—the limits shown on a control chart beyond which it is highly improbable that a point could lie while the system remains in a state of statistical control.3.2.17corrections—techniques that are part of the data analysis or method,which compensate for the effects of variables that interfere with the measurement and degrade accuracy.These corrections account for such things as matrix material,lumps,heterogeneity,dead time,and background.3.2.18dead time—the period following the detection of an event during which the system cannot register a subsequent event.Dead time is usually expressed as a percentage of elapsed time.3.2.19differential die away technique(DDT)—an NDA technique for characterizing the prompt neutrons fromfission-able isotopes in scrap and waste using a neutron generator interrogation source.3.2.20good measurement practice—an acceptable way to perform some operation associated with a specific measure-ment technique that is known or believed to influence the quality of a measurement(a way to perform some operation associated with a specific NDA technique in a manner that meets the quality requirements of a measurement).3.2.21holdup—the amount of nuclear material remaining in process equipment and facilities after the in process material, stored materials and product are removed.3.2.22homogeneous matrix—the degree to which the ma-trix materials are spread uniformly throughout the item con-tainer.Non homogeneous matrices are referred to as heteroge-neous.3.2.23in process material—the nuclear material in a pro-cess stream,excluding holdup.3.2.24item—nuclear material in a container or other suit-able configuration for assay.3.2.25lower limit of detectability—a stated limiting value which designates the lowest concentration,mass,or activity that can be detected with confidence and which is specific to a particular measurement.C859,C1215 3.2.26low level waste—waste that is not defined as transu-ranic or high level waste.DOE order435.1 3.2.27matrix—the material,which comprises the bulk of the item,except for the special nuclear material and the container.This is the material in which the special nuclear material is embedded.3.2.28matrix-specific calibration—uses a calibration ma-trix similar to the matrix to be measured.No matrix correction factors are used.This calibration is generally not appropriate for other matrices.3.2.29modeling—the use of mathematical techniques to simulate a measurement process or alternatively the process of creating a physical mock up of ameasurement.3.2.30neutron absorbers—materials,which have relatively large thermal-neutron absorption cross sections.Absorbers with the largest cross sections are commonly known as neutron poisons.Some examples are lithium,boron,cadmium,and gadolinium.3.2.31neutron moderators—materials which slow down neutrons through elastic scattering or inelastic interactions. Materials containing large amounts of low atomic weight materials,for example,hydrogen are highly moderating.3.2.32neutron multiplication—multiplication takes place when a neutron interaction yields more than one neutron as a product.Inducedfission is the primary mechanism for neutron multiplication,however(n,2n)interactions are also multipli-cation events.3.2.33nondestructive assay(NDA)—the observation of spontaneous or stimulated nuclear radiations,interpreted to estimate the content of one or more nuclides of interest in the item assayed,without affecting the physical or chemical form of the material.3.2.33.1active assay—assay based on the observation of radiation(s)induced by irradiation from an external source.3.2.33.2passive assay—assay based on the observation of naturally occurring or spontaneous nuclear radiation(s).3.2.34nuclide—an atomic species characterized by the composition of its nucleus,that is,by the number of protons and neutrons it contains.3.2.35passive neutron coincidence counting—a technique used to measure the rate of coincident neutron emission in the assay item.The terminology used in this test method refers specifically to shift-register electronics.3.2.36Poisson assumption—for counting measurements,it is assumed that the net counts in afixed period of time follow a Poisson distribution.This assumption can be verified by comparing the observed standard deviation of a series of measurements on an item with the square root of the average number of counts.If the Poisson assumption is correct,these numbers should be equal within random error.3.2.37precision—a generic concept used to describe the dispersion of a set of measured values.Measures frequently used to describe precision are standard deviation,relative standard deviation,variance,repeatability,reproducibility,con-fidence interval,and range.(See Guide C1215for a more complete discussion of precision.)3.2.38procedure—a set of systematic instruction for usinga method of measurement or of the steps associated with the method.3.2.39qualitative analysis—an analysis in which some or all of the components of an item are determined.A measure-ment in which the amount of one or more components of an item are determined.3.2.40radioactive emissions—alpha,beta,gamma-ray, x-ray,heat,and neutron emissions from spontaneousfission, inducedfission,or delayed neutron emission following beta decay.3.2.41radioactive scrap—materials that contain sufficient quantities of source or special nuclear material to be worthy of recovery.C8593.2.42radioactive waste—items containing radioactive ma-terials not currently considered useful or economically recov-erable.C859 3.2.43random error—the chance variation encountered in all measurement work,characterized by the random occurrence of deviations from the mean value.C1215 3.2.44rate loss correction—a correction for count rate related losses that are used for some gamma-ray NDA tech-niques.The correction may use radioactive sources with gamma-ray energies lower than the gamma-ray from the nuclide of interest or a pulser.3.2.45reals—this quantity is the difference between the (R+A)and(A)quantities.3.2.46reals plus accidentals—the number of events de-tected in the(R+A)gate period following the initial detection of each neutron associated with neutron counting.This is a measured quantity during the count time.3.2.47repeatability—the within group dispersion of several groups of measurements.C1215 3.2.48replicate—a counterpart of another measurement.It is the general case for which duplicate,consisting of two measurements,is the special case.3.2.49reproducibility—the between group dispersion of several groups of measurements.C1215 3.2.50sample—a portion of a population or lot.In the context of NDA measurements,it may consist of measure-ments of items that are part of a larger group that could have been considered.3.2.51secular equilibrium—the state of equilibrium that exists when series of radioisotopes have equal and constant activity levels.Secular equilibrium is established when the half life of the parent is much greater than that of the decay products.3.2.52segmented gamma scanner—a nondestructive assay technique used to measure the gamma-ray emissions from low-density scrap and waste packaged in cylindrical contain-ers.The technique involves independent measurements of the vertical segments of the container and may incorporate correc-tions for count rate losses and matrix attenuation.3.2.53self-attenuation—the attenuation of emitted radiation by the emitting material itself.3.2.54sensitivity—the capability of methodology or instru-mentation to discriminate between items having differing concentrations or containing differing amounts of a radioactive material.3.2.55shift-register-based coincidence circuit—an elec-tronic circuit for determining totals T,Reals plus Accidentals (R+A),and accidentals(A)in a selected count time(t)during neutron counting.3.2.56shuffler—an NDA technique for characterizing the delayed neutrons fromfissionable isotopes in scrap and waste using a252Cf interrogation source.3.2.57special nuclear material(SNM)—Plutonium,233U, uranium enriched in233U or235U to greater than its natural abundance,and any other materials defined as SNM under the Atomic Energy Act of1954,as amended.This term does not include source materials.C859 3.2.58standard:3.2.58.1calibration standard—an item sometimes physi-cally and chemically similar to the items to be assayed,for which the mass of the nuclide(s)of interest and all properties to which the measurement technique is sensitive are known.3.2.58.2working standard—an item used to check the performance of an NDA instrument,nominally representative of the items to be assayed,and fabricated and handled to ensure its internal integrity so that deviations in its measured response can be attributed to the instrument.)3.2.59total measurement uncertainty(TMU)—an estimated parameter,either mass,activity,concentration,or fractional, used to quantify the overall confidence in the assay result at a prescribed level including all sources of precision and bias. The TMU is qualified by the assumptions of the error propa-gation model.3.2.60totals—the total number of neutrons detected during the count time.This is a measured quantity.3.2.61traceability—the property determined by a measure-ment which can be related to appropriate standards,generally national or international standards,through an unbroken chain of comparisons.3.2.62transmission source—a radioactive source external to the item being measured that is used to determine the attenuation of gamma rays of interest by the matrix material in the item.3.2.63transuranic waste(TRU waste)—as defined in DOE Order5820.2and DOE Order435.1,transuranic waste is radioactive waste containing alpha-emitting isotopes with atomic number greater than92and half-life greater than20 years,and with activity concentrations greater than100nCi per gram of waste at the time of the measurement.3.2.64uncertainty—a generic term describing the inability of a measurement process to determine the correct value. (Alternate definition:Parameters associated with the result of a measurement that characterizes the dispersion of values that could reasonable be attributed to the measurement.)3.2.65validation—an evaluation that shows the quality assurance and quality control mechanisms are in place and functioning properly to ensure that the waste characterization information is collected and analyzed in a manner described by procedures and meets assigned data quality objectives.3.2.66verification—an evaluation of the critical item char-acteristics to ensure the collected characterization data repre-sents the true characteristics of the sample population to an acceptable degree of accuracy and precision.3.2.67waste acceptance criteria(WAC)—the set of require-ments pertaining to a waste item that must be satisfied before it can be shipped to a designated facility or disposal.4.Significance and Use4.1Good NDA measurement practices are described in this guide.The application of the material provided in this guide should be determined on a case by case basis.Not all elements are required for all applications.4.2Nondestructive assay measurements are typically per-formed when the items measured or goals of the measurement program favor NDA over destructive analysis.NDA is typi-cally favored when collecting a representative sample of the item is difficult or impractical(for example,scrap and waste items),personnel exposure would be significant,spread of contamination from sampling would occur,generation of secondary waste must be minimized,the weight and/or tare weight of the item cannot easily be determined(for example,in place process equipment),rapid turn around of the measure-ment results is needed,or the NDA measurement is signifi-cantly less expensive than the equivalent destructive analysis.4.3The principles provided in this guide should be used to determine which type of measurement is best suited to the measurement application.This determination involves consid-eration of the characteristics of the items to be measured,as well as the goals of the measurement program.4.4This guide applies to the suite of NDA instruments and measurement methods,many of which are described in detail in Refs(1)and(2).3A partial listing of measurement methods and applicable use references is provided in5.2.It is incumbent upon the user to seek additional guidance within ASTM method-specific standards,as this guide does not take prece-dence.Additional information on specific methods is best found in technical meeting transactions,journals,commercial application notes,and NRC/DOE publications.4.5This guide may be applied to many situations spanning the range of nuclear materials from product through waste. Typical applications include:the measurement and character-ization of transuranic wastes,low-level wastes,and mixed wastes;the determination of radioactivity below some regula-tory threshold;estimated for non detected radionuclides,the measurement of safeguarded nuclear materials;shipper re-ceiver confirmation;confirmation of nuclear material inven-tory;support of nuclear criticality safety evaluations;measure-ment of holdup of special nuclear material in process systems; support of decontamination and decommissioning activities; and in-situ analyses of facilities,glove-boxes,hot cells,and the environment prior to and following demolition.4.6When applied to measurement of waste,this guide should be used in conjunction with a waste management plan that segregates the contents of assay items into material categories according to some or all of the following criteria: bulk density of the waste,chemical forms of the radioactive constituents and matrix,(a,n)neutron intensity,hydrogen (moderator)and absorber content,thickness offissile mass(es), and the assay item container size and composition.Each matrix may require a different set of calibration standards and may have different mass calibration limits.The effect on the quality of the assay(that is,minimizing precision and bias)can significantly depend on the degree of adherence to this waste management plan.4.7This guide addresses elements of good practice such as; nuclear measurement instrumentation and its care;common hazards;facility readiness and requirements to support the NDA equipment;project scoping,requirements and objectives; assembly and deployment of the instrument;calibration and test;computational modeling to augment physical testing; measurement validation;preventive maintenance;and the mea-surement control program.3The boldface numbers in parentheses refer to the list of references at the end of thisstandard.5.Good Practice5.1Introduction—NDA measurements of nuclear material are performed to determine the relative or absolute abundance of one or more nuclides.Typically,such a determination is made by comparing the observed response of an unknown amount of material to the response of one or more known standards by means of a functional relationship established by calibration.NDA refers to the qualification and quantification of radionuclides using instrumentation capable of detecting a feature of the radioactive-decay process.These features in-clude such radioactive emissions as alpha,beta,gamma-ray, x-ray,heat,and neutron emissions from spontaneousfission, inducedfission,or delayed neutron emission following beta decay.5.2The primary goal of NDA measurements is to arrive ata quality result,that is,one that satisfies the user’s measure-ment needs.Adequately analyzing problems and applying appropriate measurement techniques support this goal.5.3Each NDA technique has advantages and limitations that must be judged against the specific requirements of the intended applications.No single technique can satisfy all requirements.It is the responsibility of the user to consider the potential problems,and select the proper balance of measure-ment capability and desired precision and accuracy for the specific application.5.4The observed response of an NDA system shows sensi-tivity to a wide variety of factors that can bias the assay result. By careful selection of the measurement technique,attention to potential sources of error,implementation of operational pro-cedures to control item categorization and packaging,operator training and instrument maintenance,supplemental measure-ments and calculations,and proper organization and evaluation of test data,the quality of assay results can be optimized. 5.5Because performance requirements for NDA systems are application dependent,only general guidance for the selection of a system can be provided.If more than one technique can satisfy the specific measurement requirements, other considerations such as economics,ease of operation,and availability of instrumentation will ordinarily determine the choice of a system.The following parameters are among those that should be considered when selecting NDA measurement systems:(a)The radionuclides to be measured,including the ex-pected range of assays and interferences that may arise between radionuclides,(b)The physical form(particle size,particle density, radioactive material distribution,etc.),(c)The matrix(for example,pure product,oily waste,dry waste,degree of heterogeneity,average density,etc.),(d)The container and packing material(for example,size, wall thickness,mass,wall material),(e)Environmental conditions,(f)Measurement quality objectives,(g)The degree to which parameters affecting measurement results are known,(h)Location(s)at which measurements are needed,(i)Costs(instrument,set up,and operating costs),(j)Availability of instrumentation,(k)System maintenance requirements(reliability,stability, ruggedness,etc.),(l)Training requirements,(m)Ease of operation,(n)Program schedule,and(o)Item throughput.5.6NDA methods are often nuclide sensitive rather than element sensitive.Frequently the reaction of interest is possible in more than one species of nucleus present.Determination of the elemental content of an item from a measurement of radiations emitted by isotope(s)of the elemental species and,in some cases,by their decay products requires knowledge of the relative radionuclide composition of the itemassayed. FIG.1NDATechniques5.6.1Many of the approaches to specific NDA measurement techniques are described by ASTM Standards as shown in Fig.1.A listing of applicable ASTM and ANSI standards is provided in Section7,Test Methods.Other standards may also be considered.5.6.2Neutron Measurement Techniques—Neutron tech-niques are based on the detection of neutrons,which are emitted with various energies.Neutron energies are generally not measured.A passive neutron measurement is made when the neutrons measured are a result of spontaneousfission,self inducedfission,or(a,n)reaction.Passive neutron assay systems are usually more effective for plutonium than for uranium,although applications for both exist.An active measurement is performed when the measured neutrons are the result of inducedfission.The quantity of a particular isotope may be obtained by measuring unusually low or high emission rates,distinctive time distributions,or markedly different energy spectra.To establish the quantity of radionuclide of interest from the directly observable neutron assay result(s) relative isotopic information is necessary.Correction or allow-ances may be needed for:(a)(a,n)contaminants,(b)Hydrogen content,(c)Neutron moderation and absorption(poisons),(d)Container wall effects,(e)Item size,(f)Influence of uranium on plutonium assay,(g)Source self-shielding,(h)Non-uniformity in source/matrix distribution as it relates to neutron moderation and absorption,(i)Unexpected neutron generating radionuclides,(j)Chemical composition,(k)System dead time,(l)Item size(physical dimensions and amount offission-able material),(m)Measurement geometry,(n)Background radiation,(o)Density,and(p)Neutron multiplication.5.6.2.1Passive Neutron Counting:(1)Total neutron counting serves as a suitable technique if the material to be assayed is homogeneous with respect to all attributes affecting the measurement,if it contains little or well characterized(a,n)target material,and if the nuclidic ratios are well known.The primary strengths of total neutron counting are that it usually does not depend on the use of external sources of radiation and that passive neutrons are of sufficient energy to escape from most items without significant attenuation.The costs for total neutron emission measurement programs are often considerably less than for active measure-ment techniques.In addition,because external neutron sources are not required,risk of personnel exposure to radiation is generally lower for total neutron assay.The primary disadvan-tages of total neutron assay relative to active neutron assay are that counting rates are often lower and contaminants contribute to the totals count rate resulting in a bias.The presence of(a, n)target material can result in a bias unless the relative amount of this material and its yield are well known and appropriate compensation is included in quantity estimates.(2)Passive Coincidence-neutron counting is a viable tech-nique for the measurement of240Pu effective mass or238U in low enriched uranium.Isotopic ratios are necessary to compute the grams of element.Coincidence neutron counting is less sensitive to many of the biases typical of total neutron counting because their contribution(for example,the presence of[a,n] target material)is eliminated.In addition,spontaneousfission of244Cm interferes with the measurement of240Pu effective mass.(3)Multiplicity counting is a viable assay technique for plutonium in cases where sufficient counting precision may be obtained for higher order coincidences.In principle,the technique does not require representative standards,but they are often used to provide corrections to assays.It provides improved accuracy over conventional coincidence counting in cases where the measured items are impure or heterogeneous and the multiplication and/or(a,n)yield are not known prior to the measurement.The precision is usually poorer because of lower count rates for the higher moments.It can be used to reduce cosmic ray background even when the count rates for the higher moments are low.5.6.2.2Active assay by neutron interrogation is applicable when235U is present or when passive signals are weak. Selection of an appropriate interrogating-neutron spectrum is important.Active techniques are sometimes used when the uncertainty in the passive result is unacceptable.Costs may be significantly higher than for passive assay systems.In addition, the matrix in which the measured nuclides are contained is often an important consideration.5.6.2.3Thermal neutrons can be used for active neutron assay systems if they can adequately penetrate the item.The presence of thermal-neutron absorbers such as gadolinium (Gd)in light-water-reactor(LWR)fuel may preclude the use of a thermal spectrum.Thermal-neutron interrogation may be possible for small items with high moderation,for example, hydrogen(H)content(for example,solutions).Interrogation with thermal neutrons offers the advantage of higher detection sensitivity because of increasedfission cross sections at low neutron energies infissile material.5.6.2.4For the assay of uranium-bearing items of high density,interrogation by neutrons having energies greater than thermal is recommended.Interrogating-neutron spectra can originate from various sources such as spontaneousfission isotopes,neutron generators or accelerators.5.6.2.5A major problem in active neutron assay is differ-entiation between the interrogating radiation and the stimulated response radiation.Ideally,the detector should be insensitive to the interrogating radiation.Although total insensitivity is seldom achieved,the amount of interrogating radiation de-tected can be reduced by several techniques.These techniques include using an energy-biased detector,coincidence counting, timing,and shielding.5.6.3Calorimetric Assay—Applications of calorimetry to NDA refer to the measurement of heatflow from radioactive decay.Calorimetric assay typically provides assays with very good precision and low bias.Typical assay times range from4。
LTC1923EGN中文资料
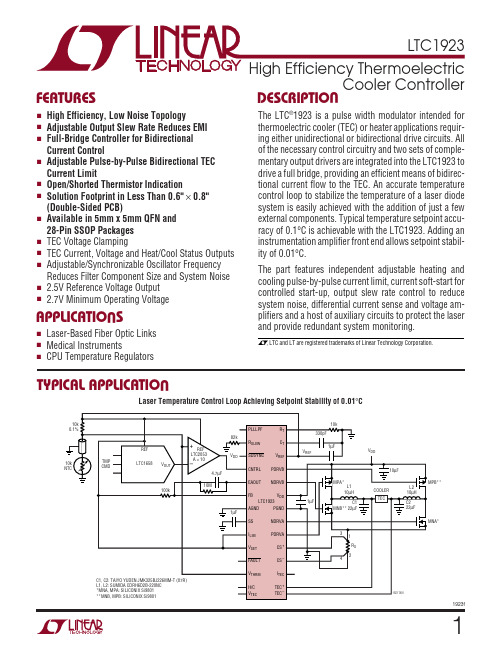
Laser-Based Fiber Optic Links Medical Instruments CPU Temperature Regulators
TYPICAL APPLICATIO
10k 0.1%
Laser Temperature Control Loop Achieving Setpoint Stability of 0.01°C
U U W PACKAGE/ORDER I FOR ATIO
SDSYNC PLLLPF RSLEW VREF
NC
NC
RT
CT
32 31 30 29 28 27 26 25 CNTRL 1 EAOUT 2 FB 3 AGND 4 NC 5 SS 6 ILIM 7 VSET 8 9 10 11 12 13 14 15 16 FAULT VTEC VTHRM TEC – TEC + ITEC H/C CS – PIN 1 TOP VIEW 24 PDRVB 23 NDRVB 22 VDD 21 VDD 20 PGND 19 NDRVA 18 PDRVA 17 CS
MJL21193 D和MJL21194 Silicon Power Transistors的数据手册

MJL21193 (PNP),MJL21194 (NPN)Silicon Power TransistorsThe MJL21193 and MJL21194 utilize Perforated Emitter technology and are specifically designed for high power audio output,disk head positioners and linear applications.Features•Total Harmonic Distortion Characterized •High DC Current Gain •Excellent Gain Linearity •High SOA•These Devices are Pb −Free and are RoHS Compliant*MAXIMUM RATINGSRatingSymbol Value Unit Collector −Emitter Voltage V CEO 250Vdc Collector −Base Voltage V CBO 400Vdc Emitter −Base VoltageV EBO5Vdc Collector −Emitter Voltage − 1.5 V V CEX 400Vdc Collector Current −Continuous I C 16Adc Collector Current −Peak (Note 1)I CM 30Adc Base Current − ContinuousI B 5Adc Total Power Dissipation @ T C = 25_C Derate above 25_CP D 2001.43W W/_C Operating and Storage Junction Temperature RangeT J , T stg−65 to +150_CStresses exceeding Maximum Ratings may damage the device. Maximum Ratings are stress ratings only. Functional operation above the Recommended Operating Conditions is not implied. Extended exposure to stresses above the Recommended Operating Conditions may affect device reliability.1.Pulse Test: Pulse Width = 300 m s, Duty Cycle ≤2%THERMAL CHARACTERISTICSCharacteristicSymbol Max Unit Thermal Resistance, Junction −to −CaseR q JC0.7_C/W*For additional information on our Pb −Free strategy and soldering details, please download the ON Semiconductor Soldering and Mounting Techniques Reference Manual, SOLDERRM/D.x =3 or 4A = Assembly Location YY =YearWW =Work WeekG= Pb −Free PackageDevice Package Shipping †ORDERING INFORMATIONMJL21193G TO −264(Pb −Free)25 Units / Rail MJL21194GTO −264(Pb −Free)25 Units / Rail†For information on tape and reel specifications,including part orientation and tape sizes, please refer to our T ape and Reel Packaging Specifications Brochure, BRD8011/D.16 AMPERE COMPLEMENTARYSILICON POWER TRANSISTORS 250 VOLTS, 200 WATTSMJL2119x AYYWWGTO −264CASE 340G STYLE 2MARKING DIAGRAM1BASE2 COLLECTOR 3EMITTER 311PNPNPNELECTRICAL CHARACTERISTICS (T C = 25°C unless otherwise noted)CharacteristicSymbolMinTypMaxUnitOFF CHARACTERISTICSCollector −Emitter Sustaining Voltage (I C = 100 mAdc, I B = 0)V CEO(sus)250−−Vdc Collector Cutoff Current (V CE = 200 Vdc, I B = 0)I CEO −−100m Adc Emitter Cutoff Current (V CE = 5 Vdc, I C = 0)I EBO −−100m Adc Collector Cutoff Current(V CE = 250 Vdc, V BE(off) = 1.5 Vdc)I CEX−−100m AdcSECOND BREAKDOWNSecond Breakdown Collector Current with Base Forward Biased (V CE = 50 Vdc, t = 1 s (non −repetitive)(V CE = 80 Vdc, t = 1 s (non −repetitive)I S/b4.02.25−−−−AdcON CHARACTERISTICS DC Current Gain(I C = 8 Adc, V CE = 5 Vdc)(I C = 16 Adc, I B = 5 Adc)h FE258−−75−Base −Emitter On Voltage (I C = 8 Adc, V CE = 5 Vdc)V BE(on)−−2.2Vdc Collector −Emitter Saturation Voltage (I C = 8 Adc, I B = 0.8 Adc)(I C = 16 Adc, I B = 3.2 Adc)V CE(sat)−−−−1.44VdcDYNAMIC CHARACTERISTICSTotal Harmonic Distortion at the OutputV RMS = 28.3 V, f = 1 kHz, P LOAD = 100 W RMS h FEunmatched (Matched pair h FE = 50 @ 5 A/5 V)h FE matchedT HD−−0.80.08−−%Current Gain Bandwidth Product(I C = 1 Adc, V CE = 10 Vdc, f test = 1 MHz)f T 4−−MHz Output Capacitance(V CB = 10 Vdc, I E = 0, f test = 1 MHz)C ob−−500pF I C COLLECTOR CURRENT (AMPS)Figure 1. Typical Current Gain Bandwidth Product Figure 2. Typical Current Gain Bandwidth Productf , C U R R E N T G A I N B A N D W I D T H P R O D U C T (M H z )TPNP MJL21193f , C U R R E N T G A I N B A N D W I D T H P R O D U C T (M H z )T NPN MJL21194I C COLLECTOR CURRENT (AMPS)6.56.05.55.04.54.03.53.08.07.0V CE , COLLECTOR-EMITTER VOLTAGE (VOLTS)I C , C O L L E C T O R C U R R E N T (A )NPN MJL211945.0Figure 3. DC Current Gain, V CE = 20 VFigure 4. DC Current Gain, V CE = 20 VFigure 5. DC Current Gain, V CE = 5 V Figure 6. DC Current Gain, V CE = 5 Vh F E , D C C U R R E N T G A I NI C COLLECTOR CURRENT (AMPS)I C COLLECTOR CURRENT (AMPS)h F E , D C C U R R E N T G A I Nh F E , D C C U R R E N T G A I NI C COLLECTOR CURRENT (AMPS)I C COLLECTOR CURRENT (AMPS)V CE , COLLECTOR-EMITTER VOLTAGE (VOLTS)Figure 7. Typical Output CharacteristicsI C , C O L L E C T O R C U R R E N T (A )Figure 8. Typical Output Characteristicsh F E , D C C U R R E N T G A I NPNP MJL21193PNP MJL21193NPN MJL21194100010010100010010100010010V B E (o n ), B A S E -E M I T T E R V O L T A G E (V O L T S )Figure 9. Typical Saturation Voltages I C , COLLECTOR CURRENT (AMPS)S A T U R A T I O N V O L T A G E (V O L T S )Figure 10. Typical Saturation VoltagesI C , COLLECTOR CURRENT (AMPS)S A T U R A T I O N V O L T A G E (V O L T S )Figure 11. Typical Base −Emitter Voltage I C , COLLECTOR CURRENT (AMPS)Figure 12. Typical Base −Emitter VoltageI C , COLLECTOR CURRENT (AMPS)V B E (o n ), B A S E -E M I T T E R V O L T A G E (V O L T S )There are two limitations on the power handling ability of a transistor; average junction temperature and secondary breakdown. Safe operating area curves indicate I C − V CE lim-its of the transistor that must be observed for reliable opera-tion; i.e., the transistor must not be subjected to greater dissip-ation than the curves indicate.The data of Figure 13 is based on T J(pk) = 150°C; T C is vari-able depending on conditions. At high case temperatures,thermal limitations will reduce the power than can be handled to values less than the limitations imposed by second break-down.PNP MJL21193NPN MJL21194Figure 13. Active Region Safe Operating AreaV CE , COLLECTOR-EMITTER VOLTAGE (VOLTS)I C , C O L L E C T O R C U R R E N T (A M P S )3.02.52.01.51.00.501.41.21.00.80.60.40.20101.00.1100101.00.1Figure 14. MJL21193 Typical Capacitance V R , REVERSE VOLTAGE (VOLTS)C , C A P A C I T A N C E (p F )Figure 15. MJL21194 Typical CapacitanceV R , REVERSE VOLTAGE (VOLTS)C , C A P A C I T A N C E (p F )8.0 WFigure 16. Typical Total Harmonic DistortionFigure 17. Total Harmonic Distortion Test CircuitFREQUENCY (Hz)T H D , T O T A L H A R M O N I C D I S T O R T I O N (%)1.21.11.00.90.80.70.610000010000100010010STYLE 1:PIN 1.GATE2.DRAIN3.SOURCE STYLE 2:PIN 1.BASE2.COLLECTOR3.EMITTER STYLE 3:PIN 1.GATE2.SOURCE3.DRAINSTYLE 4:PIN 1.DRAIN2.SOURCE3.GATEDIM A MIN MAX MIN MAX INCHES28.029.0 1.102 1.142MILLIMETERS B 19.320.30.7600.800C 4.7 5.30.1850.209D 0.93 1.480.0370.058E 1.9 2.10.0750.083F 2.2 2.40.0870.102G 5.45 BSC 0.215 BSC H 2.6 3.00.1020.118J 0.430.780.0170.031K 17.618.80.6930.740L 11.2 REF 0.411 REF N 4.35 REF 0.172 REF P 2.2 2.60.0870.102Q 3.1 3.50.1220.137R 2.25 REF0.089 REF U 6.3 REF 0.248 REF W2.83.20.1100.125NOTES:1.DIMENSIONING AND TOLERANCING PER ANSI Y14.5M, 1982.2.CONTROLLING DIMENSION: MILLIMETER.STYLE 5:PIN 1.GATE2.COLLECTOR3.EMITTER0.25 (0.010) M T BSSCALE 1:2TO −3BPL (TO −264)CASE 340G−02ISSUE JDATE 17 DEC 2004GENERICMARKING DIAGRAM**This information is generic. Please refer to device data sheet for actual part marking.Pb −Free indicator, “G” or microdot “ G ”,may or may not be present.XXXXXX AYYWWXXXXXX = Specific Device Code A = Location Code YY = YearWW = Work WeekMECHANICAL CASE OUTLINEPACKAGE DIMENSIONSON Semiconductor and are trademarks of Semiconductor Components Industries, LLC dba ON Semiconductor or its subsidiaries in the United States and/or other countries.ON Semiconductor reserves the right to make changes without further notice to any products herein. ON Semiconductor makes no warranty, representation or guarantee regarding the suitability of its products for any particular purpose, nor does ON Semiconductor assume any liability arising out of the application or use of any product or circuit, and specifically disclaims any and all liability, including without limitation special, consequential or incidental damages. ON Semiconductor does not convey any license under its patent rights nor theADDITIONAL INFORMATIONTECHNICAL PUBLICATIONS:Technical Library:/design/resources/technical−documentation onsemi Website: ONLINE SUPPORT: /supportFor additional information, please contact your local Sales Representative at /support/sales。
THAT2155资料

Min
+5 -5
2151 Typ Max
+12 -12 2.4 175 +15 -15 4 750
Min
+5 -5 — —
2150A Typ Max
+12 -12 2.4 175 +15 -15 4 750
Min
+5 -5 — —
2155 Typ Max
+12 -12 2.4 125 +15 -15 4 550
-15V
-15V
Figure 3. Typical Application Circuit
Figure 4. Frequency Response Vs. Gain (2150A)
Figure 5. Noise (20kHz NBW) Vs. Gain (2150A)
THAT Corporation; 734 Forest Street; Marlborough, Massachusetts 01752; USA Tel: (508) 229-2500; Fax: (508) 229-2590; Web:
Units
V V mA µArms
VCC-VEE= 24 V ISET= 2.4 mA
— —
Electrical Characteristics 2
Parameter
Supply Current Equiv. Input Bias Current Input Offset Voltage Output Offset Voltage
Symbol
ICC IB VOFF(IN) VOFF(OUT)
Conditions
No Signal No Signal No Signal Rout=20 kΩ 0 dB gain +15 dB gain +40 dB gain
1911172资料
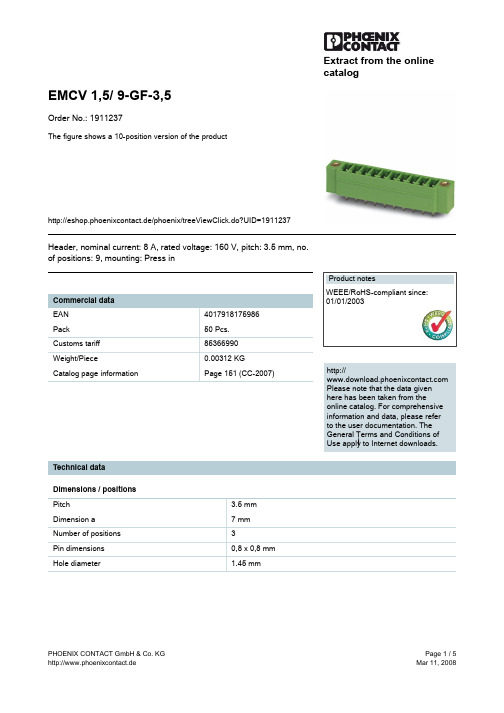
Extract from the onlinecatalogEMCV 1,5/ 9-GF-3,5Order No.: 1911237The figure shows a 10-position version of the producthttp://eshop.phoenixcontact.de/phoenix/treeViewClick.do?UID=1911237Header, nominal current: 8 A, rated voltage: 160 V, pitch: 3.5 mm, no. of positions: 9, mounting: Press inhttp://Please note that the data givenhere has been taken from theonline catalog. For comprehensiveinformation and data, please referto the user documentation. TheGeneral Terms and Conditions ofUse apply to Internet downloads. Technical dataDimensions / positionsPitch 3.5 mmDimension a7 mmNumber of positions3Pin dimensions0,8 x 0,8 mmHole diameter 1.45 mmTechnical dataInsulating material group IIIaRated surge voltage (III/3) 2.5 kVRated surge voltage (III/2) 2.5 kVRated surge voltage (II/2) 2.5 kVRated voltage (III/2)160 VRated voltage (II/2)250 VConnection in acc. with standard EN-VDENominal current I N8 ANominal voltage U N160 VMaximum load current8 AInsulating material PBTInflammability class acc. to UL 94V0Certificates / ApprovalsApproval logoCULNominal voltage U N300 VNominal current I N8 AULNominal voltage U N300 VNominal current I N8 ACertification CUL, GOST, ULAccessoriesItem Designation DescriptionAssembly1877258EMC 1,5-SH Stamp holder, for upper and lower stamp1877274EMCV 1,5-SS 1Stamp set, consisting of upper and lower stamp for 3.81 mm pitch,2 to 16-pos.Marking0804073SK 3,5/2,8:FORTL.ZAHLEN Marker card, printed horizontally, self-adhesive, 10-section markerstrip, 14 identical decades marked 1-10, 11-20 etc. up to 91-100,sufficient for 140 terminal blocksPlug/Adapter1734634CP-MSTB Coding profile, is inserted into the slot on the plug or invertedheader, red insulating materialAdditional productsItem Designation DescriptionGeneral1847068MC 1,5/ 3-STF-3,5Plug component, nominal current: 8 A, rated voltage: 160 V, pitch:3.5 mm, no. of positions: 3, type of connection: Screw connection 1863314MCVR 1,5/ 3-STF-3,5Plug component, nominal current: 8 A, rated voltage: 160 V, pitch:3.5 mm, no. of positions: 3, type of connection: Screw connection 1863013MCVW 1,5/ 3-STF-3,5Plug component, nominal current: 8 A, rated voltage: 160 V, pitch:3.5 mm, no. of positions: 3, type of connection: Screw connection DrawingsDrilling diagramDimensioned drawingAddressPHOENIX CONTACT GmbH & Co. KGFlachsmarktstr. 832825 Blomberg,GermanyPhone +49 5235 3 00Fax +49 5235 3 41200http://www.phoenixcontact.de© 2008 Phoenix ContactTechnical modifications reserved;。
LTC1592资料
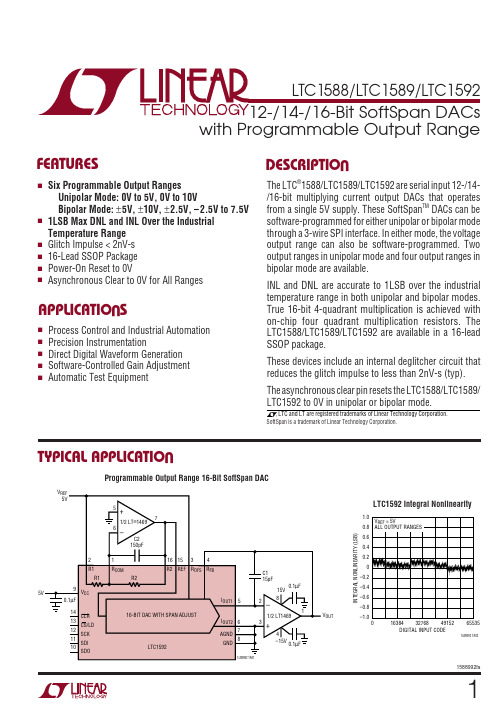
1.0 0.8 0.6 0.4 0.20–0.2–0.4–0.6–0.8–1.0V REF = 5VALL OUTPUT RANGES1LTC1588/LTC1589/LTC159223LTC1588/LTC1589/LTC159245LTC1588/LTC1589/LTC15921588992faTYPICAL PERFOR A CE CHARACTERISTICSU W(LTC1588)Integral NonlinearityDifferential NonlinearityDIGITAL INPUT CODEI N T E G R A L N O N L I N E A R I T Y (L S B )0.20.61.01588992 G11–0.2–0.600.40.8–0.4–0.8–1.08001600240032004095DIGITAL INPUT CODED I F FE R E N T I A L N O N L I N E A R I T Y (L S B )0.20.61.01588992 G12–0.2–0.600.40.8–0.4–0.8–1.08001600240032004095(LTC1589)Integral NonlinearityDifferential NonlinearityDIGITAL INPUT CODEI N T E G R A L N O N L I N E A R I T Y (L S B )0.20.61.01588992 G13–0.2–0.600.40.8–0.4–0.8–1.0411282241233616383DIGITAL INPUT CODED I F FE R E N T I A L N O N L I N E A R I T Y (L S B )0.20.61.01588992 G14–0.2–0.600.40.8–0.4–0.8–1.0411282241233616383Integral Nonlinearity vs Reference Voltage in Unipolar ModeREFERENCE VOLTAGE (V)–10I N T E G R A L N O N L I N E A R I T Y (L S B )0.20.61.061588992 G05–0.2–0.600.40.8–0.4–0.8–1.0–6–22–88–40410Integral Nonlinearity (INL)DIGITAL INPUT CODE–1.0I N T E G R A L N O N L I N E A R I T Y (L S B )–0.8–0.4–0.201.00.416384327681588992 G01–0.60.60.80.24915265535DIGITAL INPUT CODE–1.0D I F FE R E N T I A L N O N L I N E A R I T Y (L S B )–0.8–0.4–0.201.00.416384327681588992 G02–0.60.60.80.24915265535Differential Nonlinearity (DNL)(LTC1592)6LTC1588/LTC1589/LTC15921588992faREFERENCE VOLTAGE (V)–10I N T E G R A L N O N L I N E A R I T Y (L S B )0.20.61.061588992 G06–0.2–0.600.40.8–0.4–0.8–1.0–6–22–88–40410Integral Nonlinearityvs Reference Voltage in Bipolar ModeDifferential Nonlinearity vs Reference Voltage in Unipolar ModeREFERENCE VOLTAGE (V)–10D I F F E R E N T I A L N O N L I N E A R I T Y (L S B )0.20.61.061588992 G07–0.2–0.600.40.8–0.4–0.8–1.0–6–22–88–40410TYPICAL PERFOR A CE CHARACTERISTICS U WDifferential Nonlinearity vs Reference Voltage in Bipolar ModeREFERENCE VOLTAGE (V)–10D I F F E R E N T I A L N O N L I N E A R I T Y (L S B )0.20.61.061588992 G08–0.2–0.600.40.8–0.4–0.8–1.0–6–22–88–40410(LTC1592)U U UPI FU CTIO SR COM (Pin 1): Center Tap Point of the Two Bipolar Resis-tors R1 and R2. Normally tied to the inverting input of an external amplifier. When these resistors are not used,connect this pin to ground. The absolute maximum volt-age range on this pin is –0.3V to 12V.R1 (Pin 2): Bipolar Resistor R1. The main reference input V REF , typically 5V. Accepts up to ±15V. Normally tied to R OFS (Pin 3) and the reference input voltage V REF (5V).When not used connect this pin to ground.R OFS (Pin 3): Bipolar Offset Network. This pin provides the offset of the output voltage range for bipolar modes.Accepts up to ±15V. Normally tied to R1 and the reference input voltage V REF (5V). Alternatively, this pin may be driven from a different voltage than V REF .R FB (Pin 4): Feedback Network. Normally tied to the output of the current to voltage converter op amp. Range limited to ±15V.Full-Scale Settling WaveformGATED SETTLING WAVEFORM 500µV/DIVLD PULSE 5V/DIV 500ns/DIV1592 G04USING LT1468 OP AMP C FEEDBACK = 20pF 0V TO 10V STEP7LTC1588/LTC1589/LTC159289LTC1588/LTC1589/LTC15921588992faOPERATIOUSerial InterfaceWhen the CS/LD is brought to a logic low, the data on the SDI input is loaded into the shift register on the rising edge of the clock. A 4-bit command word (C3 C2 C1 C0),followed by four “don’t care” bits and 16 data bits (MSB-first) is the minimum loading sequence required for the LTC1588/LTC1589/LTC1592. When the CS/LD is brought to a logic high, the clock is disabled internally and the command word is executed.If no daisy-chaining is required, the input stream can be 24-bit wide as shown in Figure 1a. The first four bits are the command word, followed by four “don’t care” bits, then a 16-bit data word. The last four bits (LSBs) of this 16-bit data word are don’t cares for the LTC1588. For the LTC1589, the last 2 bits of the 16-bit data word are don’t cares.If daisy-chaining is required or the input needs to be written in two 16-bit wide segments, then the input stream must be 32-bit wide and the first 8 bits loaded are “don’t care” bits. The remaining bits work the same as a 24-bit stream which is described in the previous paragraph. The output of the internal 32-bit shift register is available on the SDO pin 32 clock cycles later.Multiple LTC1588/LTC1589/LTC1592s may be daisy-chained together by connecting the SDO pin to the SDI pin of the next IC. The clock and CS/LD signals should remain common to all ICs in the daisy-chain. The serial data isclocked to all ICs, then the CS/LD signal is pulled high to update all of them simultaneously.Power-On Reset and ClearWhen the power supply is first turned on, the LTC1588/LTC1589/LTC1592 will power up in 5V unipolar mode (C3C2 C1 C0 = 1000). All the internal registers are set to zeros and the DAC is set to zero code.The LTC1588/LTC1589/LTC1592 must first be pro-grammed in either unipolar or bipolar mode. There are six operating modes available and can be software-pro-grammed by the command word. When a CLR signal is brought to low, it clears all internal registers to zero. The DAC output voltage goes to zero volts. If an update DAC command (C3 C2 C1 C0 = 0001) is issued immediately after the CLR signal, the DAC output remains at zero volts.If a CLR signal is given within a 100ns interval immediately after CS/LD goes high, the user should reload the output range.Output Range ProgrammingThere are two output ranges available in unipolar mode and four output ranges available in bipolar mode. See Function Table for details. All output ranges are with re-spect to a 5V reference input. When changing the LTC1588/LTC1589/LTC1592 to a new mode, the command word and data are given at the same time (24 or 32 bit). WhenC3COMMAND DON’T CARE DATA (16 BITS)C2C1C0XXXXD13D14D15D12D11D10D9D8D7D6D5D4D3D2D1D01588992 TD2MSBLSBC3COMMAND DON’T CARE DATA (14 BITS + 2 DON’T-CARE BITS)C2C1C0XXXXD13D12D11D10D9D8D7D6D5D4D3D2D1D0X X1588992 TD3MSBLSBC3COMMAND DON’T CARE DATA (12 BITS + 4 DON’T-CARE BITS)C2C1C0XXXXD11D10D9D8D7D6D5D4D3D2D1D0XXXX1588992 TD4MSBLSBINPUT WORD (LTC1592)INPUT WORD (LTC1589)INPUT WORD (LTC1588)LTC1588/LTC1589/LTC1592101112LTC1588/LTC1589/LTC15921588992faWhile not directly addressed by the simple equations in Tables 2 and 3, temperature effects can be handled just as easily for unipolar and bipolar applications. First, consult an op amp’s data sheet to find the worst-case V OS and I B over temperature. Then, plug these numbers in the V OS and I B equations from Table 3 and calculate the tempera-ture induced effects.For applications where fast settling time is important, Appli-cation Note 74, entitled “Component and MeasurementAdvances Ensure 16-Bit DAC Settling Time ,” offers a thor-ough discussion of 16-bit DAC settling time and op amp selection.Precision Voltage Reference Considerations Much in the same way selecting an operational amplifier for use with the LTC1592 is critical to the performance of the system, selecting a precision voltage reference also requires due diligence. The output voltage of the LTC1592is directly affected by the voltage reference; thus, any voltage reference error will appear as a DAC output voltage error.There are three primary error sources to consider when selecting a precision voltage reference for 16-bit applica-tions: output voltage initial tolerance, output voltage tem-perature coefficient and output voltage noise.Initial reference output voltage tolerance, if uncorrected,generates a full-scale error term. Choosing a referenceAPPLICATIO S I FOR ATIOW UUU Table 4. Partial List of LTC Precision Amplifiers Recommended for Use with the LTC1588/LTC1589/LTC1592,with Relevant SpecificationsAMPLIFIER SPECIFICATIONSVOLTAGE CURRENT SLEW GAIN BANDWIDTHt SETTLING POWER V OS I B A OL NOISE NOISE RATE PRODUCT with LTC1592DISSIPATIONAMPLIFIER µV nA V/mV nV/√Hz pA/√Hz V/µs MHzµsmWLT1001252800100.120.250.812046LT1097500.351000140.0080.20.712011LT1112 (Dual)600.251500140.0080.160.7511510.5/Op Amp LT1124 (Dual)70204000 2.70.3 4.512.51969/Op Amp LT14687510500050.62290 2.5117LT1469 (Dual)12510200050.622902.5123/Op Amp()5VVREF ()5VVREF ()16.5kAVOL1OP AMPV OS1 (mV)I B1 (nA)A VOL1 (V/V)V OS2 (mV)I B2 (mV)A VOL2 (V/V)V OS1 • 2.4 • I B1 • 0.0003 • A1 • 0 0 0INL (LSB)()5VVREF ()5VVREF ()1.5k AVOL1()66k A VOL2()131k A VOL1()131kA VOL1()131kA VOL2()131k A VOL2V OS1 • 0.6 • I B1 • 0.00008 • A2 • 0 0 0DNL (LSB)()5VVREF ()5VVREF V OS1 • 13.2 • I B1 • 0.13 •0 0 0UNIPOLAR OFFSET (LSB)()5VVREF()5V V REF ()5V V REF V OS1 • 13.2 • I B1 • 0.0018 • A5 •V OS2 • 26.2 •I B2 • 0.1 •BIPOLAR GAIN ERROR (LSB)()5V V REF ()5VV REF()()()5V V REF ()5V V REF A3 • V OS1 • 19.8 • I B1 • 0.01 • 0 A4 • V OS2 • 13.1 •A4 • I B2 • 0.05 • A4 • BIPOLAR ZERO ERROR (LSB)UNIPOLAR GAIN ERROR (LSB)()5V V REF ()5V V REF ()5V V REF ()5VV REF()5VV REFV OS1 • 13.2 • I B1 • 0.0018 • A5 •V OS2 • 26.2 •I B2 • 0.1 • Table 3. Easy-to-Use Equations Determine Op Amp Effects on DAC Accuracy in All Output RangesTable 2. Variables for Each Output Range That Adjust the Equations in Table 3OUTPUT RANGEA1A2A3A4A55V 1.12110V 2.23 1.5±5V 22 1.21 1.5±10V 44 1.21 2.5±2.5V 11 1.611–2.5V to 7.5V1.9310.51.513LTC1588/LTC1589/LTC15921588992faAPPLICATIO S I FOR ATIOW UUU with low output voltage initial tolerance, like the LT1236(±0.05%), minimizes the gain error caused by the refer-ence; however, a calibration sequence that corrects for system zero- and full-scale error is always recommended.A reference’s output voltage temperature coefficient af-fects not only the full-scale error, but can also affect the circuit’s INL and DNL performance. If a reference is chosen with a loose output voltage temperature coeffi-cient, then the DAC output voltage along its transfer characteristic will be very dependent on ambient condi-tions. Minimizing the error due to reference temperature coefficient can be achieved by choosing a precision reference with a low output voltage temperature coeffi-cient and/or tightly controlling the ambient temperature of the circuit to minimize temperature gradients.As precision DAC applications move to 16-bit and higher performance, reference output voltage noise may contrib-ute a dominant share of the system’s noise floor. This in turn can degrade system dynamic range and signal-to-noise ratio. Care should be exercised in selecting a voltage reference with as low an output noise voltage as practical for the system resolution desired. Precision voltage refer-ences, like the LT1236, produce low output noise in the 0.1Hz to 10Hz region, well below the 16-bit LSB level in 5V or 10V full-scale systems. However, as the circuit band-widths increase, filtering the output of the reference may be required to minimize output noise.Table 5. Partial List of LTC Precision References Recommended for Use with the LTC1588/LTC1589/LTC1592 with Relevant SpecificationsINITIAL TEMPERATURE0.1Hz to 10Hz REFERENCE TOLERANCE DRIFT NOISE LT1019A-5,±0.05%5ppm/°C 12µV P-P LT1019A-10LT1236A-5,±0.05%5ppm/°C 3µV P-P LT1236A-10LT1460A-5,±0.075%10ppm/°C 20µV P-P LT1460A-10LT1790A-2.5±0.05%10ppm/°C12µV P-PGroundingAs with any high resolution converter, clean grounding is important. A low impedance analog ground plane and star grounding techniques should be used. I OUT2 must be tied to the star ground with as low a resistance as possible.When it is not possible to locate star ground close to I OUT2,a low resistance trace should be used to route this pin to star ground. This minimizes the voltage drop from this pin to ground caused by the code dependent current flowing to ground. When the resistance of this circuit board trace becomes greater than 1Ω, a force/sense amplified con-figuration should be used to drive this pin (see Figure 2).This preserves the excellent accuracy (1LSB INL and DNL)of the LTC1588/LTC1589/LTC1592.An Isolated 16-Bit Subsystem Using the LTC1592The circuit in Figure 4 is a complete example of an optically isolated analog output subsystem that supports most of the legacy ranges that are still common in industrial environments. This circuit uses only two optoisolators,the load pulse (CS/LD) being derived from a series of transitions on the data line (SDI) after the clock (SCK) is halted high. If a single chip microcontroller with an auto-mated SPI interface is to be used, the SPI port can transfer the 24 bits as three bytes. Subsequently, the data output port pin can be reassigned to general purpose port opera-tion and exercised to produce a number of transitions to generate the load pulse. Alternatively, the entire sequence can be programmed bit by bit with a general purpose port.Figure 5 shows the timing.The DC/DC converter, Figure 3 based on the LT ®3439ultralow noise transformer driver provides a compact means of powering this circuit, and allows the output to deliver output current that is only limited by the LT1468capabilities. The output capability of the DC/DC converter itself is 80mA at ±12V and is available as demo board DC511A. This circuit as shown requires approximately 130mA of the 5V supply (no load). The total surface area required is less than 2 square inches.LTC1588/LTC1589/LTC159214Information furnished by Linear Technology Corporation is believed to be accurate and reliable. However, no responsibility is assumed for its use. Linear Technology Corporation makes no represen-tation that the interconnection of its circuits as described herein will not infringe on existing patent rights.1516LTC1588/LTC1589/LTC1592LT/TP 0503 1K REV A • PRINTED IN USA© LINEAR TECHNOLOGY CORPORATION 20011630 McCarthy Blvd., Milpitas, CA 95035-7417(408) 432-1900 q FAX: (408) 434-0507 q 。
LTC1859CG中文资料
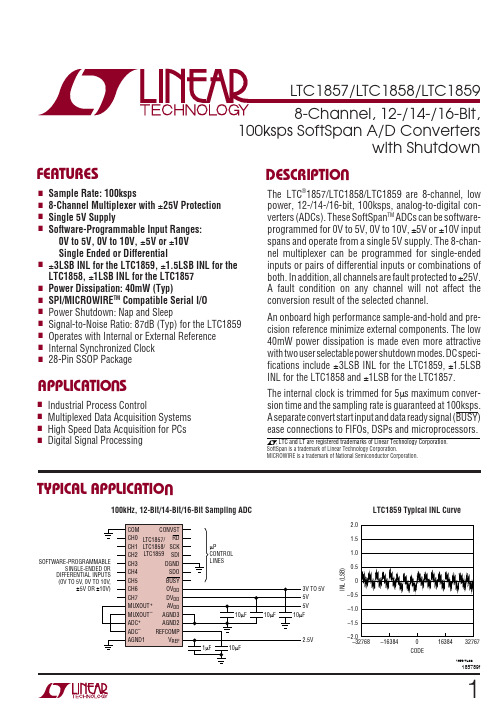
WU
U
CO VERTER A D ULTIPLEXER CHARACTERISTICS
The ● denotes the specifications which apply over the full operating temperature range, otherwise specifications are at TA = 25°C. MUXOUT connected to ADC inputs. (Notes 5, 6)
LINES
10µF
10µF
1µF
10µF
3V TO 5V 5V 5V 10µF
2.5V
INL (LSB)
LTC1859 Typical INL Curve
2.0
1.5
1.0
0.5
0
– 0.5
–1.0
–1.5
–2.0 –32768 –16384
0 CODE
16384 32767
1859 TA02h performance sample-and-hold and precision reference minimize external components. The low 40mW power dissipation is made even more attractive with two user selectable power shutdown modes. DC specifications include ±3LSB INL for the LTC1859, ±1.5LSB INL for the LTC1858 and ±1LSB for the LTC1857.
ORDER PART NUMBER
ltc1966真有效值--DC转换器中文资料
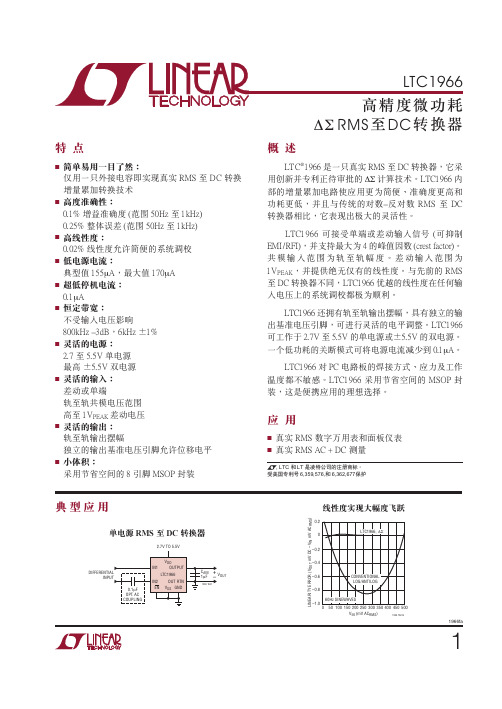
}z05~ CH0 : 1/^PpCH1 : /P CH0 : 1//^PpCH1 : /P CH0 : 1/^PpCH1 : /P
? ? ?
i/-0
G; P P P P
PBSM
?H;<F? =zy.
} Z,*|_>La-Z9qbz-tZJ`c<z]r } [,u2 .JN5pJN6/ 7S,< URR Z UEE -Qb0P4ND]r Pwbu29mwVt-pGtb/Kz<54bBi8r } \,LSD5=:: um .UOTS/ ef>.pFfti9mkCz-p wWjRtbytr } ],LSD5=::D 3 LSD5=::J D3M y 84*c <9*SPqcO3w Bmr } ^,LSD5=::D D3M 4*c ;4*qcODHLaiZpTfK O t q L aZ p1 - A M y 84 * c <9 * q c O - L ai Zpl1MbSPqcOtdZo2rLSD5=::J GD3M y 84*c <9*qcO-ALaiZr } _,fTbltdFZ9 DBUF @ 54GG ;erLSD5=:: M DBUF @ 66cG C 544- XqtdrjStdh8t?ntdD3k YOXtj3wBmp9xiZz-ZzUD3r } `,fTbltdFZM :4In u28;erLSD5=:: M ED Z 54`In u2A^8Xq 544- tdrM 94bU c 794bU ED u 2 3 < 8 - t < K 6 N t 5 y /n L tH FQQ qU OOR q UJOR TVi::rjStdh8t?ntdD3kYOX tj3wBmp9xiZz-ZzUD3r
i/-1 i/-3 i/-5 i/-7 i0-/ 5/Bf MCH?Q;P?M / 4/ 0// 04/ 1// 14/ 2// 24/ 3// 34/ 4// PCH }^P ;=LGM~ 0855 N;/0V =IHP?HNCIH;F FIA.;HNCFIA
单片机产品

6.飞思卡尔单片机
飞思卡尔半导体(Freescale Semiconductor)是全球领先的半导体公司,飞思卡尔的产品 主要面向汽车、网络、工业和消费电子市场,它的主要应用包括汽车安全、混合动力和全电动汽 车、下一代无线基础设施、智能能源管理、便携式医疗器件、消费电子、工业、医疗保健等。
其产品范围包括8位微控制器、16位微控制器、32位ARM Cortex-M架构微控制器Kinetis系 列、ARM Cortex-A架构i.MX系列处理器、Power Architecture™/PowerQUICC™、高性能网络 处理器、高性能多媒体处理器、高性能工业控制处理器、CodeWarrior™开发工具、数字信号处 理器与控制器、电源管理、RF射频功率放大器、高性能线性功率放大器GPA、音视频家电射频多 媒体处理器、传感器等。
7.瑞萨单片机
RENESAS是2003年4月1日由日立制 作所半导体部门和三菱电机半导体部门合 并成立的。它是制造嵌入式半导体的全球 领先供应商,也是世界第六大半导体制造 商。RENESAS结合了日立与三菱在半导体 方面的先进技术和丰富经验,其产品遍布 无线网络、汽车、消费与工业市场设计等 领域。
9
8
飞思卡尔公司协办了全国大学生 “飞思卡尔”杯智能汽车竞赛。该竞 赛得到了教育部相关领导、飞思卡尔 公司领导及各高校师生的高度认可。 目前,它已发展成全国30个省市自治 区、近300所高校广泛参与的全国大 学生智能汽车竞赛。2008年,该竞赛 被教育部列为国家教学质量与教学改 革工程资助项目中的科技人文竞赛之 一。
9.ST公司单片机
ST公司旗下的微控制器从8位到32位 都有。8位的STM8系列单片机和32位的 STM32 ARM CortexM微控制器均具有强 大的功能,它们通常用于LCD控制器、马 达控制定时器、防篡改保护、嵌入式 EEPROM、DMA矩阵和针对电池供电的 低功耗模式等场合。
- 1、下载文档前请自行甄别文档内容的完整性,平台不提供额外的编辑、内容补充、找答案等附加服务。
- 2、"仅部分预览"的文档,不可在线预览部分如存在完整性等问题,可反馈申请退款(可完整预览的文档不适用该条件!)。
- 3、如文档侵犯您的权益,请联系客服反馈,我们会尽快为您处理(人工客服工作时间:9:00-18:30)。
1.0 0.8 0.6 0.4 0.20–0.2–0.4–0.6–0.8–1.0V REF = 5VALL OUTPUT RANGES1LTC1588/LTC1589/LTC159223LTC1588/LTC1589/LTC159245LTC1588/LTC1589/LTC15921588992faTYPICAL PERFOR A CE CHARACTERISTICSU W(LTC1588)Integral NonlinearityDifferential NonlinearityDIGITAL INPUT CODEI N T E G R A L N O N L I N E A R I T Y (L S B )0.20.61.01588992 G11–0.2–0.600.40.8–0.4–0.8–1.08001600240032004095DIGITAL INPUT CODED I F FE R E N T I A L N O N L I N E A R I T Y (L S B )0.20.61.01588992 G12–0.2–0.600.40.8–0.4–0.8–1.08001600240032004095(LTC1589)Integral NonlinearityDifferential NonlinearityDIGITAL INPUT CODEI N T E G R A L N O N L I N E A R I T Y (L S B )0.20.61.01588992 G13–0.2–0.600.40.8–0.4–0.8–1.0411282241233616383DIGITAL INPUT CODED I F FE R E N T I A L N O N L I N E A R I T Y (L S B )0.20.61.01588992 G14–0.2–0.600.40.8–0.4–0.8–1.0411282241233616383Integral Nonlinearity vs Reference Voltage in Unipolar ModeREFERENCE VOLTAGE (V)–10I N T E G R A L N O N L I N E A R I T Y (L S B )0.20.61.061588992 G05–0.2–0.600.40.8–0.4–0.8–1.0–6–22–88–40410Integral Nonlinearity (INL)DIGITAL INPUT CODE–1.0I N T E G R A L N O N L I N E A R I T Y (L S B )–0.8–0.4–0.201.00.416384327681588992 G01–0.60.60.80.24915265535DIGITAL INPUT CODE–1.0D I F FE R E N T I A L N O N L I N E A R I T Y (L S B )–0.8–0.4–0.201.00.416384327681588992 G02–0.60.60.80.24915265535Differential Nonlinearity (DNL)(LTC1592)6LTC1588/LTC1589/LTC15921588992faREFERENCE VOLTAGE (V)–10I N T E G R A L N O N L I N E A R I T Y (L S B )0.20.61.061588992 G06–0.2–0.600.40.8–0.4–0.8–1.0–6–22–88–40410Integral Nonlinearityvs Reference Voltage in Bipolar ModeDifferential Nonlinearity vs Reference Voltage in Unipolar ModeREFERENCE VOLTAGE (V)–10D I F F E R E N T I A L N O N L I N E A R I T Y (L S B )0.20.61.061588992 G07–0.2–0.600.40.8–0.4–0.8–1.0–6–22–88–40410TYPICAL PERFOR A CE CHARACTERISTICS U WDifferential Nonlinearity vs Reference Voltage in Bipolar ModeREFERENCE VOLTAGE (V)–10D I F F E R E N T I A L N O N L I N E A R I T Y (L S B )0.20.61.061588992 G08–0.2–0.600.40.8–0.4–0.8–1.0–6–22–88–40410(LTC1592)U U UPI FU CTIO SR COM (Pin 1): Center Tap Point of the Two Bipolar Resis-tors R1 and R2. Normally tied to the inverting input of an external amplifier. When these resistors are not used,connect this pin to ground. The absolute maximum volt-age range on this pin is –0.3V to 12V.R1 (Pin 2): Bipolar Resistor R1. The main reference input V REF , typically 5V. Accepts up to ±15V. Normally tied to R OFS (Pin 3) and the reference input voltage V REF (5V).When not used connect this pin to ground.R OFS (Pin 3): Bipolar Offset Network. This pin provides the offset of the output voltage range for bipolar modes.Accepts up to ±15V. Normally tied to R1 and the reference input voltage V REF (5V). Alternatively, this pin may be driven from a different voltage than V REF .R FB (Pin 4): Feedback Network. Normally tied to the output of the current to voltage converter op amp. Range limited to ±15V.Full-Scale Settling WaveformGATED SETTLING WAVEFORM 500µV/DIVLD PULSE 5V/DIV 500ns/DIV1592 G04USING LT1468 OP AMP C FEEDBACK = 20pF 0V TO 10V STEP7LTC1588/LTC1589/LTC159289LTC1588/LTC1589/LTC15921588992faOPERATIOUSerial InterfaceWhen the CS/LD is brought to a logic low, the data on the SDI input is loaded into the shift register on the rising edge of the clock. A 4-bit command word (C3 C2 C1 C0),followed by four “don’t care” bits and 16 data bits (MSB-first) is the minimum loading sequence required for the LTC1588/LTC1589/LTC1592. When the CS/LD is brought to a logic high, the clock is disabled internally and the command word is executed.If no daisy-chaining is required, the input stream can be 24-bit wide as shown in Figure 1a. The first four bits are the command word, followed by four “don’t care” bits, then a 16-bit data word. The last four bits (LSBs) of this 16-bit data word are don’t cares for the LTC1588. For the LTC1589, the last 2 bits of the 16-bit data word are don’t cares.If daisy-chaining is required or the input needs to be written in two 16-bit wide segments, then the input stream must be 32-bit wide and the first 8 bits loaded are “don’t care” bits. The remaining bits work the same as a 24-bit stream which is described in the previous paragraph. The output of the internal 32-bit shift register is available on the SDO pin 32 clock cycles later.Multiple LTC1588/LTC1589/LTC1592s may be daisy-chained together by connecting the SDO pin to the SDI pin of the next IC. The clock and CS/LD signals should remain common to all ICs in the daisy-chain. The serial data isclocked to all ICs, then the CS/LD signal is pulled high to update all of them simultaneously.Power-On Reset and ClearWhen the power supply is first turned on, the LTC1588/LTC1589/LTC1592 will power up in 5V unipolar mode (C3C2 C1 C0 = 1000). All the internal registers are set to zeros and the DAC is set to zero code.The LTC1588/LTC1589/LTC1592 must first be pro-grammed in either unipolar or bipolar mode. There are six operating modes available and can be software-pro-grammed by the command word. When a CLR signal is brought to low, it clears all internal registers to zero. The DAC output voltage goes to zero volts. If an update DAC command (C3 C2 C1 C0 = 0001) is issued immediately after the CLR signal, the DAC output remains at zero volts.If a CLR signal is given within a 100ns interval immediately after CS/LD goes high, the user should reload the output range.Output Range ProgrammingThere are two output ranges available in unipolar mode and four output ranges available in bipolar mode. See Function Table for details. All output ranges are with re-spect to a 5V reference input. When changing the LTC1588/LTC1589/LTC1592 to a new mode, the command word and data are given at the same time (24 or 32 bit). WhenC3COMMAND DON’T CARE DATA (16 BITS)C2C1C0XXXXD13D14D15D12D11D10D9D8D7D6D5D4D3D2D1D01588992 TD2MSBLSBC3COMMAND DON’T CARE DATA (14 BITS + 2 DON’T-CARE BITS)C2C1C0XXXXD13D12D11D10D9D8D7D6D5D4D3D2D1D0X X1588992 TD3MSBLSBC3COMMAND DON’T CARE DATA (12 BITS + 4 DON’T-CARE BITS)C2C1C0XXXXD11D10D9D8D7D6D5D4D3D2D1D0XXXX1588992 TD4MSBLSBINPUT WORD (LTC1592)INPUT WORD (LTC1589)INPUT WORD (LTC1588)LTC1588/LTC1589/LTC1592101112LTC1588/LTC1589/LTC15921588992faWhile not directly addressed by the simple equations in Tables 2 and 3, temperature effects can be handled just as easily for unipolar and bipolar applications. First, consult an op amp’s data sheet to find the worst-case V OS and I B over temperature. Then, plug these numbers in the V OS and I B equations from Table 3 and calculate the tempera-ture induced effects.For applications where fast settling time is important, Appli-cation Note 74, entitled “Component and MeasurementAdvances Ensure 16-Bit DAC Settling Time ,” offers a thor-ough discussion of 16-bit DAC settling time and op amp selection.Precision Voltage Reference Considerations Much in the same way selecting an operational amplifier for use with the LTC1592 is critical to the performance of the system, selecting a precision voltage reference also requires due diligence. The output voltage of the LTC1592is directly affected by the voltage reference; thus, any voltage reference error will appear as a DAC output voltage error.There are three primary error sources to consider when selecting a precision voltage reference for 16-bit applica-tions: output voltage initial tolerance, output voltage tem-perature coefficient and output voltage noise.Initial reference output voltage tolerance, if uncorrected,generates a full-scale error term. Choosing a referenceAPPLICATIO S I FOR ATIOW UUU Table 4. Partial List of LTC Precision Amplifiers Recommended for Use with the LTC1588/LTC1589/LTC1592,with Relevant SpecificationsAMPLIFIER SPECIFICATIONSVOLTAGE CURRENT SLEW GAIN BANDWIDTHt SETTLING POWER V OS I B A OL NOISE NOISE RATE PRODUCT with LTC1592DISSIPATIONAMPLIFIER µV nA V/mV nV/√Hz pA/√Hz V/µs MHzµsmWLT1001252800100.120.250.812046LT1097500.351000140.0080.20.712011LT1112 (Dual)600.251500140.0080.160.7511510.5/Op Amp LT1124 (Dual)70204000 2.70.3 4.512.51969/Op Amp LT14687510500050.62290 2.5117LT1469 (Dual)12510200050.622902.5123/Op Amp()5VVREF ()5VVREF ()16.5kAVOL1OP AMPV OS1 (mV)I B1 (nA)A VOL1 (V/V)V OS2 (mV)I B2 (mV)A VOL2 (V/V)V OS1 • 2.4 • I B1 • 0.0003 • A1 • 0 0 0INL (LSB)()5VVREF ()5VVREF ()1.5k AVOL1()66k A VOL2()131k A VOL1()131kA VOL1()131kA VOL2()131k A VOL2V OS1 • 0.6 • I B1 • 0.00008 • A2 • 0 0 0DNL (LSB)()5VVREF ()5VVREF V OS1 • 13.2 • I B1 • 0.13 •0 0 0UNIPOLAR OFFSET (LSB)()5VVREF()5V V REF ()5V V REF V OS1 • 13.2 • I B1 • 0.0018 • A5 •V OS2 • 26.2 •I B2 • 0.1 •BIPOLAR GAIN ERROR (LSB)()5V V REF ()5VV REF()()()5V V REF ()5V V REF A3 • V OS1 • 19.8 • I B1 • 0.01 • 0 A4 • V OS2 • 13.1 •A4 • I B2 • 0.05 • A4 • BIPOLAR ZERO ERROR (LSB)UNIPOLAR GAIN ERROR (LSB)()5V V REF ()5V V REF ()5V V REF ()5VV REF()5VV REFV OS1 • 13.2 • I B1 • 0.0018 • A5 •V OS2 • 26.2 •I B2 • 0.1 • Table 3. Easy-to-Use Equations Determine Op Amp Effects on DAC Accuracy in All Output RangesTable 2. Variables for Each Output Range That Adjust the Equations in Table 3OUTPUT RANGEA1A2A3A4A55V 1.12110V 2.23 1.5±5V 22 1.21 1.5±10V 44 1.21 2.5±2.5V 11 1.611–2.5V to 7.5V1.9310.51.513LTC1588/LTC1589/LTC15921588992faAPPLICATIO S I FOR ATIOW UUU with low output voltage initial tolerance, like the LT1236(±0.05%), minimizes the gain error caused by the refer-ence; however, a calibration sequence that corrects for system zero- and full-scale error is always recommended.A reference’s output voltage temperature coefficient af-fects not only the full-scale error, but can also affect the circuit’s INL and DNL performance. If a reference is chosen with a loose output voltage temperature coeffi-cient, then the DAC output voltage along its transfer characteristic will be very dependent on ambient condi-tions. Minimizing the error due to reference temperature coefficient can be achieved by choosing a precision reference with a low output voltage temperature coeffi-cient and/or tightly controlling the ambient temperature of the circuit to minimize temperature gradients.As precision DAC applications move to 16-bit and higher performance, reference output voltage noise may contrib-ute a dominant share of the system’s noise floor. This in turn can degrade system dynamic range and signal-to-noise ratio. Care should be exercised in selecting a voltage reference with as low an output noise voltage as practical for the system resolution desired. Precision voltage refer-ences, like the LT1236, produce low output noise in the 0.1Hz to 10Hz region, well below the 16-bit LSB level in 5V or 10V full-scale systems. However, as the circuit band-widths increase, filtering the output of the reference may be required to minimize output noise.Table 5. Partial List of LTC Precision References Recommended for Use with the LTC1588/LTC1589/LTC1592 with Relevant SpecificationsINITIAL TEMPERATURE0.1Hz to 10Hz REFERENCE TOLERANCE DRIFT NOISE LT1019A-5,±0.05%5ppm/°C 12µV P-P LT1019A-10LT1236A-5,±0.05%5ppm/°C 3µV P-P LT1236A-10LT1460A-5,±0.075%10ppm/°C 20µV P-P LT1460A-10LT1790A-2.5±0.05%10ppm/°C12µV P-PGroundingAs with any high resolution converter, clean grounding is important. A low impedance analog ground plane and star grounding techniques should be used. I OUT2 must be tied to the star ground with as low a resistance as possible.When it is not possible to locate star ground close to I OUT2,a low resistance trace should be used to route this pin to star ground. This minimizes the voltage drop from this pin to ground caused by the code dependent current flowing to ground. When the resistance of this circuit board trace becomes greater than 1Ω, a force/sense amplified con-figuration should be used to drive this pin (see Figure 2).This preserves the excellent accuracy (1LSB INL and DNL)of the LTC1588/LTC1589/LTC1592.An Isolated 16-Bit Subsystem Using the LTC1592The circuit in Figure 4 is a complete example of an optically isolated analog output subsystem that supports most of the legacy ranges that are still common in industrial environments. This circuit uses only two optoisolators,the load pulse (CS/LD) being derived from a series of transitions on the data line (SDI) after the clock (SCK) is halted high. If a single chip microcontroller with an auto-mated SPI interface is to be used, the SPI port can transfer the 24 bits as three bytes. Subsequently, the data output port pin can be reassigned to general purpose port opera-tion and exercised to produce a number of transitions to generate the load pulse. Alternatively, the entire sequence can be programmed bit by bit with a general purpose port.Figure 5 shows the timing.The DC/DC converter, Figure 3 based on the LT ®3439ultralow noise transformer driver provides a compact means of powering this circuit, and allows the output to deliver output current that is only limited by the LT1468capabilities. The output capability of the DC/DC converter itself is 80mA at ±12V and is available as demo board DC511A. This circuit as shown requires approximately 130mA of the 5V supply (no load). The total surface area required is less than 2 square inches.LTC1588/LTC1589/LTC159214Information furnished by Linear Technology Corporation is believed to be accurate and reliable. However, no responsibility is assumed for its use. Linear Technology Corporation makes no represen-tation that the interconnection of its circuits as described herein will not infringe on existing patent rights.1516LTC1588/LTC1589/LTC1592LT/TP 0503 1K REV A • PRINTED IN USA© LINEAR TECHNOLOGY CORPORATION 20011630 McCarthy Blvd., Milpitas, CA 95035-7417(408) 432-1900 q FAX: (408) 434-0507 q 。