齿轮参数计算小软件
KISSSOFT操作与齿轮设计培训教程
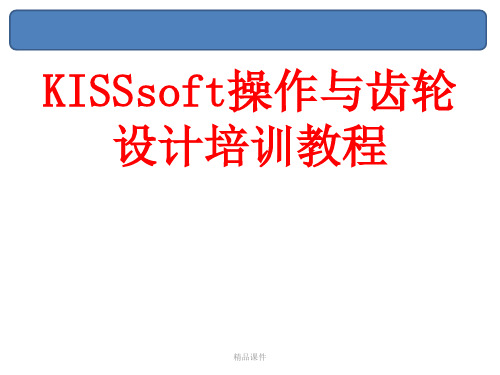
KISSsoft软件齿轮基本模块介绍
二、单对齿轮模块介绍
2.8 齿轮的安全系数(Safety factor)
使用KISSsoft软件提高齿面接触安全系数是非常必要的!0.8795 (0.8618)<1.0很不理想!(增加变位系数、齿向修形均可改善)
在保证齿轮强度的基础上,为了使齿轮产生噪声小、振动水平低, 需设法得到2.0以上的端面重合度。采用尽可能大的齿高系数,这不但可 以增加重叠系数,而且由于齿根减薄,增加了牙齿的柔性,因而更容易 吸收牙齿的震动,减小轮齿间噪声。
精品课件
KISSsoft软件齿轮基本模块介绍
二、单对齿轮模块介绍
2.3齿轮的齿厚偏差参数(Tolerances)
如果齿厚值需要转换,单击齿厚转换按钮,进入齿厚转换对话框。 如果需要 修改则选定的齿厚偏差将变为自定义偏差。
精品课件
KISSsoft软件齿轮基本模块介绍
二、单对齿轮模块介绍
2.3齿轮的齿厚偏差参数(Tolerances)
精品课件
KISSsoft软件齿轮基本模块介绍
二、单对齿轮模块介绍
2.4 齿轮的修形参数(Modifications)
对于使用模具工艺加工齿形,齿顶必须倒圆角,因为尖角在注塑时是不可能很精确的 完成的。最好将齿轮1和齿轮2的这个参数同时在一个界面控制。这样可以确保所有重要的 参数(例如重合度等)计算时可以同时考虑齿顶倒圆角的影响。齿轮的齿顶、齿廓倒角、 倒圆,并无标准计算公式,一般依据各公司的经验。但不宜过大,从而影响齿轮重合度和 强度,一般齿轮倒角如下:
使用DIN3967中指定的方法来定义偏差。在这之前, 必须先知道齿轮和箱体的工作温度和热膨胀系数。这 里必须考虑膨胀产生的影响。尼龙是膨胀最严重的塑 料材料(吸水后会膨胀2%)。无侧隙的齿轮是无法 正常工作的,会出现烧伤、噪音、卡死甚至传动失效 等状况,因此需要适当的侧隙。可以用改变齿轮副中 心距的大小或把齿轮轮齿切薄来获得,一般齿轮副中 心距是不能调整的,因此一般在加工齿轮时按规定的 齿厚极限偏差将轮齿切薄,如图所示。
simpack齿轮啮合力
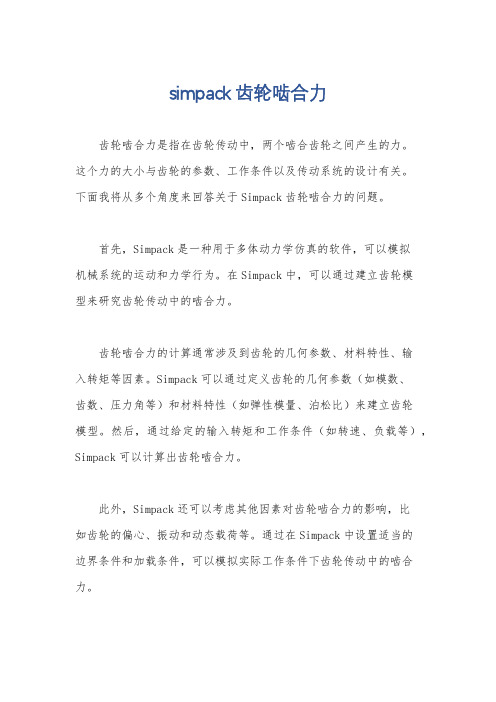
simpack齿轮啮合力
齿轮啮合力是指在齿轮传动中,两个啮合齿轮之间产生的力。
这个力的大小与齿轮的参数、工作条件以及传动系统的设计有关。
下面我将从多个角度来回答关于Simpack齿轮啮合力的问题。
首先,Simpack是一种用于多体动力学仿真的软件,可以模拟
机械系统的运动和力学行为。
在Simpack中,可以通过建立齿轮模
型来研究齿轮传动中的啮合力。
齿轮啮合力的计算通常涉及到齿轮的几何参数、材料特性、输
入转矩等因素。
Simpack可以通过定义齿轮的几何参数(如模数、
齿数、压力角等)和材料特性(如弹性模量、泊松比)来建立齿轮
模型。
然后,通过给定的输入转矩和工作条件(如转速、负载等),Simpack可以计算出齿轮啮合力。
此外,Simpack还可以考虑其他因素对齿轮啮合力的影响,比
如齿轮的偏心、振动和动态载荷等。
通过在Simpack中设置适当的
边界条件和加载条件,可以模拟实际工作条件下齿轮传动中的啮合力。
齿轮啮合力的大小对于齿轮传动的设计和分析非常重要。
通过Simpack的仿真分析,可以评估齿轮传动的工作性能、寿命和可靠性。
同时,还可以优化齿轮的设计参数,以满足特定的工作要求。
总结起来,Simpack可以用于建立齿轮模型并计算齿轮啮合力。
通过考虑齿轮的几何参数、材料特性和工作条件,Simpack可以提
供全面的齿轮啮合力分析和评估。
这对于齿轮传动的设计和优化具
有重要意义。
齿轮Kisssoft全实例教程-2024鲜版

软件内置先进的齿轮分析算法,可对齿轮的强度、刚度、疲劳寿命等 进行精确计算,为设计者提供可靠的参考依据。
丰富的齿轮库
Kisssoft软件自带丰富的齿轮库,包含各种标准和非标准齿轮,方便 用户快速调用和修改。
灵活的参数化设计
软件支持参数化设计,用户可通过修改参数快速调整齿轮结构,提高 设计效率。
Chapter
2024/3/28
19
齿轮参数优化
选择齿轮类型
根据实际需求,选择适合的齿 轮类型,如直齿、斜齿、锥齿
等。
2024/3/28
确定齿轮参数
输入齿轮的模数、齿数、压力 角等基本参数。
优化设计变量
以齿轮的模数、齿数、变位系 数为设计变量,进行优化设计 。
目标函数设定
以齿轮的传动效率、噪声、振 动等性能指标为目标函数,进
实体建模与装配
分别将蜗杆和蜗轮的齿廓曲线 转化为三维实体模型,并进行 装配操作。
设计参数设置
包括模数、蜗杆头数、蜗轮齿 数、导程角等参数设定。
2024/3/28
蜗轮轮廓绘制
根据蜗杆的齿廓曲线和蜗轮齿 数,绘制蜗轮的齿廓曲线。
模型检查与优化
对装配后的模型进行干涉检查 、齿形修正等优化操作。
14
04
齿轮分析实例
查看分析结果
Kisssoft将生成详细的分析报告,包 括齿轮的强度、安全系数等关键指标 。
05
04
运行分析
启动Kisssoft的分析计算功能,对齿轮 进行强度分析。
2024/3/28
16
齿轮疲劳寿命分析
导入齿轮模型
与强度分析相同,首 先需要在Kisssoft中 导入齿轮模型。
选择疲劳寿命分析
齿轮参数计算工具500个全在这了,总有一个是你需要的

齿轮参数计算⼯具500个全在这了,总有⼀个是你需要的齿轮⾃动计算⼯具⼤全下载见⽂章末尾
学机械的朋友都学习过齿轮的相关内容,今天和⼤家在这⼀起回忆下齿轮的知识。
齿轮的参数包括齿数z、模数m、分度圆直径d、齿顶圆直径da和齿根圆直径df、模数z、分度圆
直径d、压⼒⾓α。
其中,模数和齿数是齿轮最主要的参数。
在齿数不变的情况下,模数越⼤则轮齿越⼤,抗折断的能⼒越强,当然齿轮轮坯也越⼤,空间
尺⼨越⼤;模数不变的情况下,齿数越⼤则渐开线越平缓,齿顶圆齿厚、齿根圆齿厚相应地越
厚。
齿廓基本参数与表达:
基本参数图⽰:
今天和⼤家分享的齿轮计算⼯具涵盖了直齿圆柱齿轮设计计算、直齿齿轮副参数以及单齿精度
计算、直(斜)齿锥齿轮计算、汽车差速齿轮计算、外齿轮插齿剃齿验算等等。
在这只列出其中⼏个:
直(斜)齿锥齿轮设计
外啮合直齿齿轮参数计算
内啮合直齿齿轮参数计算
单个直齿齿轮参数计算
还有很多,在这就不⼀⼀列举了。
基于ANSYS的齿轮仿真分析

基于ANSYS的齿轮仿真分析齿轮是一种常见的机械传动元件,广泛应用于工业生产中的各种机械设备中。
齿轮的工作性能直接影响着整个传动系统的性能和可靠性。
为了确保齿轮的正常工作和延长使用寿命,需要对齿轮进行仿真分析。
本文将介绍基于ANSYS软件的齿轮仿真分析方法和流程。
首先,进行齿轮的几何建模。
使用ANSYS软件中的几何建模工具,根据实际齿轮的参数进行几何建模。
包括齿轮的齿数、模数、齿宽等参数。
建立三维模型后,对齿轮进行网格划分,生成有限元模型。
接下来,进行材料属性的定义。
根据实际齿轮的材料,定义材料属性。
包括弹性模量、泊松比、材料密度等参数。
这些参数将被用于后续的载荷和刚度分析。
然后,进行齿轮的载荷分析。
齿轮在工作过程中受到来自外界的载荷作用,主要包括径向力、切向力和轴向力等。
通过ANSYS中的载荷工具,对齿轮进行载荷加载。
可以根据实际工况设置载荷大小和方向。
进行齿轮的接触分析。
齿轮的接触是齿轮传动中的重要性能指标之一、通过ANSYS中的接触分析工具,可以计算齿轮接触面上的应力分布、接触区域和接触压力等参数。
这些参数对于齿轮的寿命和工作性能有重要影响。
进行齿轮的动力学分析。
齿轮在传动过程中会产生振动和噪声。
通过ANSYS中的动力学分析工具,可以计算齿轮的振动模态、固有频率和振动幅度等参数。
这些参数对于齿轮的运行平稳性和噪声控制有重要意义。
最后,进行疲劳分析。
齿轮在长时间使用过程中,容易出现疲劳破坏。
通过ANSYS中的疲劳分析工具,可以预测齿轮的寿命和疲劳破坏位置。
通过疲劳分析结果,可以调整齿轮的设计参数,提高其工作寿命。
综上所述,基于ANSYS的齿轮仿真分析包括几何建模、材料属性定义、载荷分析、接触分析、动力学分析和疲劳分析等步骤。
通过这些分析,可以评估齿轮的工作性能,指导齿轮的设计和改进。
同时,齿轮仿真分析可以帮助优化整个传动系统的工作性能和可靠性,提高机械设备的制造水平和整体效益。
各种齿轮及链轮几何参数计算小软件

渐开线圆柱直齿轮计算 制作:D.R Feng 模数 m21.06任意圆压力角 αk#NUM!齿数 z15齿顶圆齿厚 Sa13.82362731分度圆压力角 α°20任意圆齿厚 Sk#NUM!压力角(弧度值)0.34906585分度圆半径 r157.95分度圆直径 d315.9任意圆半径 r k148变位系数 x0齿顶圆半径 r a179.01齿顶圆直径 d a358.02齿顶圆压力角 αa0.593227771齿根圆直径 d f263.25基圆半径 rb148.4244495基圆直径 d b296.8488989渐开线函数 invαk#NUM!分度圆齿厚 S33.080971标准公法线长度 Wk97.96612687渐开线函数(分度圆)0.014904384测量值 Wk'跨测齿数 k2计算变位系数-6.800422431只需输入绿色部分压力角为 14.5°,20°,22.5°,25°标准模数:1,1.25,1.5,(1.75),2,(2.25),2.5,(2.75),3,(3.5),4,(4.5),5,(5.5),6,(7),8,(9),10,12,(14),16,18,22,28,(30),36标准径节 p=25.4/m: 1,1-1/4,1-1/2,1-3/4,2,2-1/2,2-3/4,3,3-1/2,4,5,6,7,8,9,10,12,14,16,18,20螺旋齿轮几何尺寸计算法面模数 m n配对齿数 Z2齿数 z1螺旋角 β(8-20)分度圆压力角 ∮°螺旋角 β(弧度值)0分度圆直径 d10基圆直径 db0齿顶圆直径 da10压力角(弧度值)0齿根圆直径 df10端面齿距 Pt0法面齿距 Pn0当量齿数0端面模数 m t0中心距0圆锥齿轮几何尺寸计算齿数 Z117锥距 R124.8879498齿数 Z238分度圆齿厚 s9.424777961大端模数 m6齿宽 b<=41.62931659齿根高 hf7.5齿顶高 ha6分度圆直径 d1102当量齿数 z v118.62364163齿顶圆直径 da1112.953819分锥角(弧度值)0.420663349齿根圆直径 df188.3077262分锥角 δ1º24.1022345分度圆直径 d2228齿根圆直径 df2221.8744909齿顶圆直径 da2232.900407当量齿数 z v293.05349053模数系列:1,1.25,1.375,1.5,1.75,2,2.5,2.75,3,3.23,3.5,4,4.5,5,5.5,6,7,8,9,10,11,14,16,18,20,22,28,30,32,36,40涡轮蜗杆几何尺寸计算模数 m 3.75涡轮齿数 z260蜗杆头数 z12蜗杆分度圆直径 d144.3涡轮变位系数 x20顶隙 c0.75涡轮螺旋角 βº9.609072877蜗杆螺旋升角 γº9.609072877齿顶高 h a1 3.75齿根 h f1 4.5直径系数 q11.81333333中心距 a134.65蜗杆轴向齿距 p a111.78097245蜗杆齿根圆直径 d f135.3蜗杆齿顶圆直径 d a151.8蜗杆螺纹部分长度b1>54.75涡轮咽喉母圆半径r g218.4涡轮最大外圆直径d e2<236.25涡轮轮齿包角θ<130º122.5592104涡轮轮缘宽度 b2<38.85涡轮齿顶圆直径 d a2232.5涡轮分度圆直径 d2225涡轮最大外圆直径d e2<238.125涡轮齿根圆直径 d f2216涡轮齿顶高 3.75涡轮齿根高 4.5模数与螺杆直径搭配值模数螺杆头数螺杆分度圆直径标准中心距1,2,4 18,22.4,2840135.5501, 2, 422.4,28,35.563145801,2,428,35.5,451001561251,2,431.5,40,501601711801,2,440,50,632001902501,2,450,63,8028011123151,2,463,80,10035511404001,2,471,90,11245011605001,2,490,112,14012001,2,4112,140,1801200i7~1314~2728~40Z1422,1Z228~5228~5428~80齿数 z36节距 p 15.875齿顶圆直径 da190.0245803齿根部宽度bf 8.836台间最大直径dg164.7770803齿顶部宽度ba 4.7085分度圆直径 d182.1451978内链板宽b19.4倒圆半径〉=15.875节距p内链板宽b1滚子外径dr 排距836 5.649.5255.726.3510.2412.77.758.5113.9212.77.857.9514.3815.8759.410.1618.11Z1,Z2 推荐值166.381012.5链轮尺寸常需变位为配凑中心距,43.152.525。
利用CAD软件进行齿轮传动设计的步骤

利用CAD软件进行齿轮传动设计的步骤齿轮传动是一种常见的机械传动方式,广泛应用于各种机械设备中。
利用计算机辅助设计(CAD)软件进行齿轮传动设计可以提高设计的精度和效率。
下面,我们就来介绍一下利用CAD软件进行齿轮传动设计的步骤。
步骤一:建立齿轮的几何参数通过CAD软件新建一个零件文件,选择适当的坐标系建立齿轮的几何参数。
齿轮的几何参数包括齿数、模数、齿轮宽度、压力角等。
根据设计要求和实际需求,确定齿轮的几何参数,然后用CAD软件绘制齿轮的外形。
步骤二:绘制齿轮的轮廓利用CAD软件提供的绘图功能,用标准齿轮轮廓进行绘制。
选择绘制齿轮的齿廓形状,比如采用直齿、斜齿还是渐开线齿廓等。
按照齿轮几何参数和所选择的齿廓形状,用CAD软件绘制齿轮的轮廓。
步骤三:生成齿轮的三维模型通过CAD软件提供的三维建模功能,利用齿轮的轮廓生成齿轮的三维模型。
将齿轮的轮廓拉伸成一定的高度,形成齿轮的齿面。
可以选择使用CAD软件的旋转、拉伸或公差功能,根据设计要求对齿面进行调整和修正。
步骤四:进行齿轮的装配如果需要设计齿轮的传动系统,可以利用CAD软件的装配功能进行齿轮间的装配。
根据实际情况,选择合适的装配方式,将齿轮按照要求进行装配,形成齿轮传动系统。
可以通过CAD软件的装配分析功能,对装配后的齿轮进行检查和分析,确保装配的正确性和可靠性。
步骤五:进行齿轮的运动分析通过CAD软件提供的运动分析功能,对齿轮传动系统进行动态仿真分析。
可以输入齿轮的运动参数,比如转速、转向等,进行齿轮传动系统的运动分析和性能评估。
根据运动分析的结果,优化齿轮设计,提高传动效率和稳定性。
步骤六:进行齿轮的强度计算利用CAD软件提供的强度计算功能,对齿轮的强度进行计算和评估。
根据齿轮的材料、几何参数和工作条件,进行强度计算和分析,确保齿轮在工作过程中的安全可靠性。
根据强度计算的结果,进行必要的强度优化和改进。
总结:利用CAD软件进行齿轮传动设计的步骤主要包括建立齿轮的几何参数、绘制齿轮的轮廓、生成齿轮的三维模型、进行齿轮的装配、进行齿轮的运动分析和进行齿轮的强度计算。
matlab齿轮强度校核

MATLAB齿轮强度校核1. 引言齿轮是一种常用的传动装置,广泛应用于机械工程领域。
在设计和制造齿轮时,需要对其强度进行校核,以确保其能够承受正常工作条件下的载荷。
MATLAB作为一种功能强大的数值计算软件,可以用于进行齿轮强度校核的计算和分析。
本文将介绍如何使用MATLAB进行齿轮强度校核,并以一个具体的例子进行说明。
2. 齿轮基本参数在进行齿轮强度校核之前,首先需要确定一些基本参数,包括:•齿轮模数(Module):表示每个齿的宽度与圆周长度之比。
•齿数(Number of Teeth):表示一个齿轮上的齿的数量。
•压力角(Pressure Angle):表示传递力矩时,两个相互啮合的齿面所形成的角度。
•链接类型(Gear Type):常见的链接类型有直齿、斜齿、渐开线等。
这些参数将决定了我们在进行强度校核时所需考虑的因素。
3. 材料参数除了齿轮的基本参数外,还需要考虑材料的强度参数,包括:•弹性模量(Elastic Modulus):表示材料的刚度。
•泊松比(Poisson’s Ratio):表示材料在拉伸时横向收缩的程度。
•弯曲强度(Bending Strength):表示材料在受到弯曲载荷时能够承受的最大应力。
这些参数将影响到齿轮强度校核的计算结果。
4. 齿轮强度计算齿轮强度校核主要包括两个方面:齿面接触疲劳强度和齿根抗弯疲劳强度。
下面将分别介绍这两个方面的计算方法。
4.1 齿面接触疲劳强度齿面接触疲劳是指由于齿轮啮合过程中产生的应力集中而导致的表面损伤。
为了评估齿轮在接触疲劳方面的性能,可以使用以下公式进行计算:S = Y * Z * (Kt * Ko * Kv) / (C * I * J)其中,S表示接触疲劳安全系数,Y表示齿轮弯曲强度几何系数,Z表示载荷系数,Kt表示温度调整系数,Ko表示表面质量调整系数,Kv表示动载荷调整系数,C表示材料强度参数,I和J分别为几何修正系数。
4.2 齿根抗弯疲劳强度齿根抗弯疲劳是指由于齿轮在传递力矩时产生的应力而导致的齿根损伤。
齿轮设计计算小软件

齿轮设计计算小软件齿轮是一种常见的传动装置,用于将转速和扭矩从一个轴传递到另一个轴。
齿轮设计计算是齿轮设计过程中的重要环节,它涉及到齿轮的几何参数、传动比、齿面接触载荷等方面的计算。
为了方便工程师进行齿轮设计计算,可以开发一款齿轮设计计算小软件。
这个小软件可以包含以下几个功能:1.齿轮几何参数计算:根据用户输入的齿轮模数、齿数、压力角等参数,计算齿轮的基本几何参数,如齿轮径、齿轮厚度、模数、分度圆直径等。
2.齿轮传动比计算:根据用户输入的齿轮齿数,计算齿轮传动比。
传动比是指输入轴的转速与输出轴的转速之比。
3.齿面接触载荷计算:根据用户输入的齿轮模数、齿数、压力角等参数,计算齿面接触载荷。
齿面接触载荷是齿轮传动中齿面所承受的接触载荷,它对于齿轮的设计和选材是至关重要的。
4.齿轮轴向载荷计算:根据用户输入的齿轮模数、齿数、压力角等参数,计算齿轮轴向载荷。
齿轮轴向载荷是齿轮传动中齿轮所承受的轴向载荷,它对于轴承的选型和齿轮架设的设计有重要影响。
5.齿轮强度计算:根据用户输入的齿轮材料、几何参数、载荷等参数,计算并评估齿轮的强度。
齿轮强度是指齿轮在承受载荷时不发生永久性形变和破坏的能力。
6.齿轮寿命预测:根据用户输入的齿轮材料、几何参数、载荷等参数,根据高尔茨公式等一些寿命预测公式,计算齿轮的预计使用寿命。
7.材料选型:根据用户输入的齿轮载荷、工作条件等参数,提供齿轮材料的选择建议。
不同材料的强度、硬度、耐磨性等性能不同,适用于不同的齿轮工况。
8.结果输出:将计算结果以表格、图表等形式输出,方便用户查看和保存。
通过开发这样一款齿轮设计计算小软件,工程师可以更快速、准确地进行齿轮设计计算,为齿轮的设计和选型提供科学的依据,提高齿轮传动的质量和效率。
KISSsoft软件齿轮基础培训(非常全面)
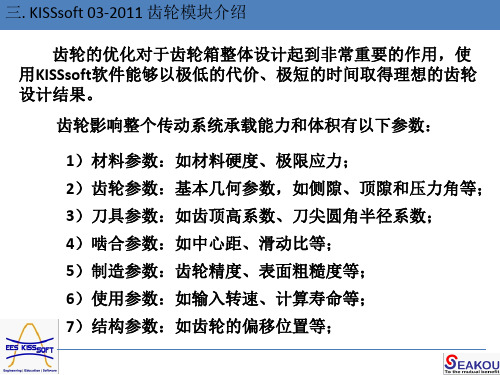
1.1 直齿和斜齿轮的几何定义
1.
有两种方法定义齿轮几何参数:一种在 基本界面中设置;另一种则使用Geometry manager(老版齿轮模块界面的继承)。
2.
五. KISSsoft软件直齿和斜齿轮及行星轮基本模块介绍
齿轮2D几何编辑器
齿轮上这些圆的大小实际取决于两个方面
单齿轮是通过制 造过程控制,结束后 通过标准齿来检验。
三. KISSsoft 03-2011 数据库介绍
如下图,为经典的齿轮材料(金属材料的属性一般差 异性不是很大,而塑料各材料之间则比较大)S—N曲线。
KISSsoft给出的S—N曲线
三. KISSsoft 03-2011 数据库介绍
有了齿轮材料S—N曲线,就可以根据齿轮在载荷谱条 件下的应力—循环次数曲线和S—N曲线计算出齿轮的安全 系数、损伤率和寿命。还可以根据齿轮应力—循环次数曲 线相对的S—N曲线的位置,来直观判断齿轮工作寿命是否 达到设计要求和齿轮材料选取的好坏。 因此,KISSsoft推荐使用各类零件的S—N曲线,并建 议用户建立自己相应的S—N曲线数据库。如果用户暂时没 有自己的,可以根据经验,找材料性能接近的S—N曲线作 为参考,使用KISSsoft软件,对已有准确结果的产品进行 建模,根据实际的结果来修正原材料S—N曲线,经过多次 修正和比较,最后就可以得到一个相对准确的S—N曲线。 对于重要的传动应用和关键零件,KISSsoft推荐必须使用 各类零件自己的S—N曲线。
五. KISSsoft软件直齿和斜齿轮及行星轮基本模块介绍
Roll distance 滚动距离 Each circle segment belongs每段圆弧都属于一个渐 开线段 to an involute segment Length of the circle segments = length of the thread = roll distance 圆弧长度= 线的长度 = 滚动距 离
重庆工学院郭晓冬的锥齿轮设计加工仿真软件GSHgears使用说明书
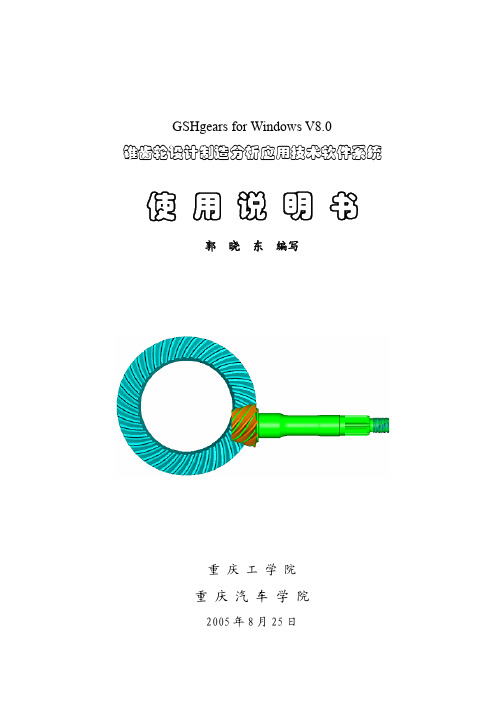
锥齿轮设计制造分析应用技术软件系统
使 用 说 明 书
郭 晓 东 编写
重 庆 工 学 院
重 庆 汽 车 学 院
2005 年 8 月 25 日
GSHgears 最新说明
1. GSHgears 现为 8.0 版本,可根据用户要求运行于 Windows 98、 Windows Me, Windows 2000, Windows XP。为使显示美观,建议将 显示器分辨率设置为 1024×768 或更高。 本版本软件系统新增加支 持在 Gleason No.118、Gleason No.16、Gleason No.112 等机床上 应用 HFT 加工方法加工准双曲面齿轮和弧齿锥齿轮单刀号法, 并且 在调整参数一览表中增加输出了基本调整参数及其加工出完整齿 面的起始和终止摇台角,以便于应用于 Phoenix 等数控型铣齿机 床。此外,还集成了弧齿锥齿轮强度设计和校核计算模块,M&M 精 密仪器系统公司的齿轮测量中心数据接口、 通用坐标测量机用齿面 几何测量数据接口、 根据齿轮测量中心齿面坐标测量结果的切齿调 整参数自动修正、三维有限元接触分析智能建模、基于 AutoCAD 2000i 的切齿仿真等模块。 2. 新 版 软 件 应 用 专 业 安 装 软 件 制 作 自 解 包 安 装 程 序 , 名 为 Setup.exe。运行该程序将安装 GSHgears for Windows 到硬盘 X:\GSHgears,并建立软件所需的文档目录,在开始菜单中建立程 序组和启动快捷键; 同时, 安装程序将根据 Windows 系统的版本自 动安装软件狗的驱动程序,用户不再需要手工安装软件狗驱动程 序。在 Setup.exe 安装程序运行结束后,将自动启动 GSHgears 软 件系统,这时由于软件狗尚未被系统支持,GSHgears 将显示软件 狗读写错误,并运行于演示版本模式。这时,将 GSHgears 软件系 统关闭。
kisssort圆柱齿轮结果分析

过大的安全系数将增大传 动装置的外廓尺寸和重量,提高 制造成本;而过小的安全系数有 可能带来意外的故障和危险性。
11
KISSsoft软件常规齿轮强度计算
SHmin最小齿面接触 疲劳安全系数,主要 考虑的齿面点蚀这种 失效形式,限制齿轮 承载能力和使用寿命 等。对于一般可靠性 要求, SHmin ≥1, 较高可靠性要求, SHmin ≥1.25。
由于轴、轴承、齿轮受载后 弹性变形,必然导致轮齿啮合偏移 及错位,减小单位啮合长度的最大 载荷及传递误差(减小啮合噪声) ,对轮齿进行齿向及齿形修形,就 可以有效减小啮合长度上的载荷, 减小载荷突变,可减小啮合噪声。
18
KISSsoft软件常规齿轮强度计算
传输误差曲线一般以一个周 期的曲线来表示,而左图给出的是 多个周期一起呈现的曲线状况,表 达的意思是一致的。 齿轮的传递误差曲线反映齿 轮系统动态性能的一个重要指标。 研究表明,降低传递误差绝对峰值 的大小,能够使齿轮系统工作时更 加平稳。因此,我们也可以通过传 递误差曲线判断修形的好坏。 好的修形方案使得传递误差的曲线波动峰值小很多, 说明系统平稳的同时还达到了提高齿轮寿命的目的。
3D图
23
KISSsoft软件常规齿轮强度计算
修形前后的对比
24
17பைடு நூலகம்
KISSsoft软件常规齿轮强度计算
该图就是在齿轮副实际啮合过程中产生的传递误差
通过修形之后使得PPTE( Peak to Peak transmission error)值从原先的152.48151.62=0.86减小到目前的148.72148.18=0.54,单位为UM微米。
齿轮噪声主要分成三 种:轮齿啮合撞击、轮齿 啮合噪声、轮齿啮出噪声 。
caxa生成齿轮参数表

caxa生成齿轮参数表
在机械设计中,齿轮是一种常用的传动元件。
为了保证齿轮传动的稳定性和可靠性,需要对齿轮进行准确的设计。
而在齿轮设计过程中,生成齿轮参数表是非常必要的。
CAXA是一种常用的机械设计软件,可以帮助设计师快速生成齿轮参数表。
具体操作步骤如下:
1. 选择齿轮模块
在CAXA软件中选择齿轮模块,打开齿轮设计界面。
2. 输入齿轮基本参数
在齿轮设计界面中输入齿轮的基本参数,如齿轮模数、齿轮齿数、齿轮轴距等。
3. 选择齿轮类型
根据齿轮的实际使用情况,选择合适的齿轮类型,如圆柱齿轮、锥齿轮等。
4. 输入齿轮材料参数
根据齿轮实际使用环境和要求,输入齿轮材料的参数,如弹性模量、泊松比等。
5. 生成齿轮参数表
完成以上步骤后,点击“生成齿轮参数表”按钮,CAXA软件即可自动生成齿轮参数表,包括齿轮尺寸、齿面参数、齿轮材料参数等。
通过CAXA软件生成齿轮参数表,不仅可以提高齿轮设计效率,还可以保证齿轮传动的稳定性和可靠性,为机械设计师的工作提供便
利。
kisssoft齿轮变位系数_解释说明
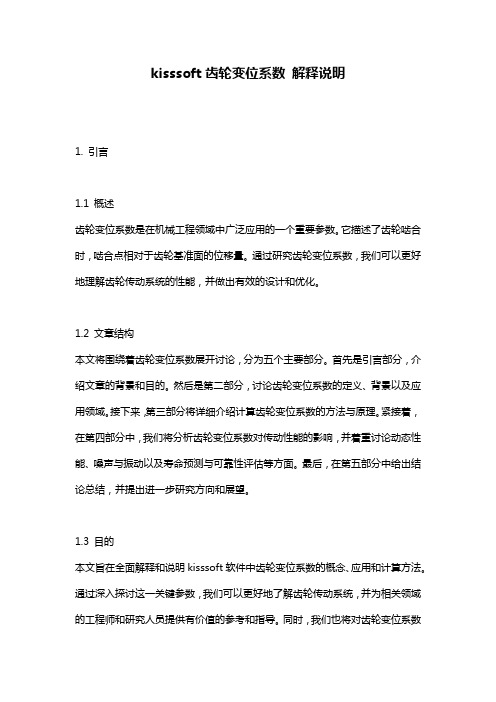
kisssoft齿轮变位系数解释说明1. 引言1.1 概述齿轮变位系数是在机械工程领域中广泛应用的一个重要参数。
它描述了齿轮啮合时,啮合点相对于齿轮基准面的位移量。
通过研究齿轮变位系数,我们可以更好地理解齿轮传动系统的性能,并做出有效的设计和优化。
1.2 文章结构本文将围绕着齿轮变位系数展开讨论,分为五个主要部分。
首先是引言部分,介绍文章的背景和目的。
然后是第二部分,讨论齿轮变位系数的定义、背景以及应用领域。
接下来,第三部分将详细介绍计算齿轮变位系数的方法与原理。
紧接着,在第四部分中,我们将分析齿轮变位系数对传动性能的影响,并着重讨论动态性能、噪声与振动以及寿命预测与可靠性评估等方面。
最后,在第五部分中给出结论总结,并提出进一步研究方向和展望。
1.3 目的本文旨在全面解释和说明kisssoft软件中齿轮变位系数的概念、应用和计算方法。
通过深入探讨这一关键参数,我们可以更好地了解齿轮传动系统,并为相关领域的工程师和研究人员提供有价值的参考和指导。
同时,我们也将对齿轮变位系数对传动性能的影响进行分析,以期对齿轮设计与优化提供实用的建议。
2. 齿轮变位系数的定义与背景:2.1 齿轮变位系数的概念:齿轮变位系数是用来描述齿轮传动中两个啮合齿轮相对于理想位置的偏移程度的参数。
在齿轮传动中,由于制造和安装误差、载荷等因素的影响,实际上啮合的两个齿轮可能存在一定程度的相对位置偏移。
这种位置偏移会导致传动性能下降、噪声和振动增加以及寿命缩短。
2.2 齿轮变位系数的应用领域:齿轮变位系数是齿轮设计和分析中一个重要的参数,广泛应用于机械工程领域。
特别是在高速、精密、大功率传动系统中,更加重视减小齿轮变位系数以提高传动效率和可靠性。
2.3 齿轮变位系数的重要性:齿轮变位系数对于确定有效载荷分布、计算接触应力、考虑弹性变形等都具有重要作用。
通过准确计算和控制齿轮变位系数,可以优化设计方案并提高传动系统的性能。
减小齿轮变位系数可以降低齿轮传动中产生的噪声和振动,提高系统的工作平稳性和舒适性。
直角斜轮齿轮参数设计基于Solidworks软件的Visual Basic程序说明书
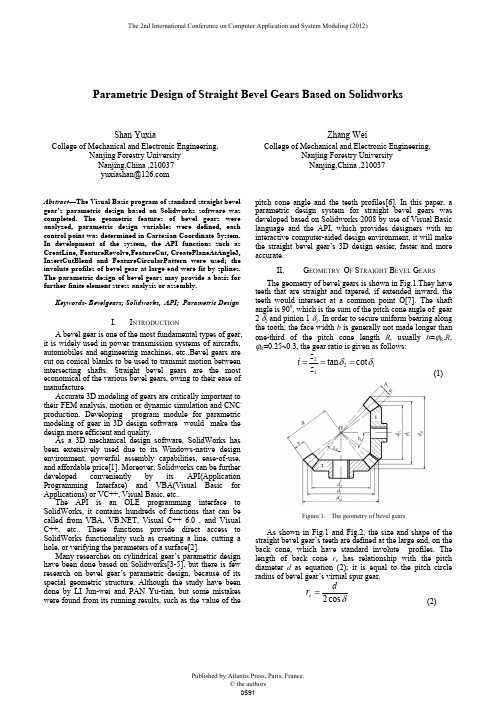
Parametric Design of Straight Bevel Gears Based on SolidworksShan YuxiaCollege of Mechanical and Electronic Engineering, Nanjing Forestry UniversityNanjing,China ,210037Zhang WeiCollege of Mechanical and Electronic Engineering, Nanjing Forestry UniversityNanjing,China ,210037Abstract—The Visual Basic program of standard straight bevel gear’s parametric design based on Solidworks software was completed. The geometric features of bevel gears were analyzed, parametric design variables were defined, each control point was determined in Cartesian Coordinate System.In development of the system, the API functions such as CreatLine, FeatureRevolve,FeatureCut, CreatePlaneAtAngle3, InsertCutBlend and FeatureCircularPattern were used; the involute profiles of bevel gear at large end were fit by splines. The parametric design of bevel gears may provide a basis for further finite element stress analysis or assembly.Keywords- Bevelgears; Solidworks, API; Parametric DesignI.I NTRODUCTIONA bevel gear is one of the most fundamental types of gear,it is widely used in power transmission systems of aircrafts, automobiles and engineering machines, etc..Bevel gears are cut on conical blanks to be used to transmit motion between intersecting shafts. Straight bevel gears are the most economical of the various bevel gears, owing to their ease of manufacture.Accurate 3D modeling of gears are critically important to their FEM analysis, motion or dynamic simulation and CNC production. Developing program module for parametric modeling of gear in 3D design software would make the design more efficient and quality.As a 3D mechanical design software, SolidWorks has been extensively used due to its Windows-native design environment, powerful assembly capabilities, ease-of-use, and affordable price[1]. Moreover, Solidworks can be further developed conveniently by its API(Application Programming Interface) and VBA(Visual Basic for Applications) or VC++, Visual Basic, etc..The API is an OLE programming interface to SolidWorks, it contains hundreds of functions that can be called from VBA, , Visual C++ 6.0 , and VisualC++, etc.. These functions provide direct access to SolidWorks functionality such as creating a line, cutting a hole, or verifying the parameters of a surface[2].Many researches on cylindrical gear’s parametric design have been done based on Solidworks[3-5], but there is few research on bevel gear’s parametric design, because of its special geometric structure. Although the study have been done by LI Jun-wei and PAN Yu-tian, but some mistakes were found from its running results, such as the value of the pitch cone angle and the teeth profiles[6]. In this paper, a parametric design system for straight bevel gears was developed based on Solidworks 2008 by use of Visual Basic language and the API, which provides designers with an interactive computer-aided design environment, it will make the straight bevel gear’s 3D design easier, faster and more accurate.II.G EOMETRY O F S TRAIGHT B EVEL G EARS The geometry of bevel gears is shown in Fig.1.They have teeth that are straight and tapered, if extended inward, the teeth would intersect at a common point O[7]. The shaft angle is 900, which is the sum of the pitch cone angle of gear 2 δ2 and pinion 1 δ1. In order to secure uniform bearing along the tooth, the face width b is generally not made longer than one-third of the pitch cone length R, usually b=ϕR.R, ϕR=0.25~0.3, the gear ratio is given as follows:1212cottanδδ===zzi(1)Figure 1. The geometry of bevel gearsAs shown in Fig.1 and Fig.2, the size and shape of the straight bevel gear’s teeth are defined at the large end, on the back cone, which have standard involute profiles. The length of back cone r e has relationship with the pitch diameter d as equation (2); it is equal to the pitch circle radius of bevel gear’s virtual spur gear.δcos2dre=(2)(a) Back cone (b) Involute profiles of teeth Figure 2.Back cone and shape of teeth on itFigure 3. Generation of an involute curveAn involute curve is the locus of a point on the generating line, as the line rolls without slipping along a base circle[8], see Fig.3. Gear teeth are cut in the shape of an involute curve between the base and the addendum circles, while the part of the tooth between the base and dedendum circles is generally a radial line[9]. In Cartesian Coordinate System, the involute curve is expressed as follows:⎩⎨⎧−=+=)cos (sin )sin (cos θθθθθθb b r y r x (3)Where r b is radius of the base circle, θ is the spread angle, θ=tg αk . Referring to Fig.3, for gear tooth profile the definition interval of θ is 1)/(02−≤≤b a d d θ.Note especially that when determine the involute tooth profile of bevel gear at large end, the geometric parameters of its virtual spur gear at large end should be substituted.III. A CHI E VEMENT O F S TRAIGHT B EVEL G EAR ’SP ARAMETRIC D ESIGN A. Determination of design variablesAccording to geometric features of straight bevel gears stated above, and design equations for bevel gears which are detailed in Mechanical Design Manual[10], the module m at large end, tooth number z 1 of pinion, face width factor ϕR and gear ratio i are determined as parametric design variables. The pressure angle α, addendum height factor h a * and tip clearance factor c * is set as the standard value of 200, 1 and0.2, respectively.The interactive interface was designed as Fig.4, where the standard values of module m in accord with GB12368-90 can be selected directly by the popup-list tile.Figure 4. Parameters entering interfaceB. Coordinates determination of control pointsBefore implementing parametric design by Visual Basic codes and API functions, some coordinates of control points must be determined, according to the design variables stated above and the topological properties of bevel gears. Thus, a Cartesian Coordinate System was set up, as shown in Fig.5, whose origin is at the apex of the back cone. In this coordinate system all the control points were determined, referring to Fig.5 and Tab.1.Figure 5. Coordinate frame for cross section of a bevel gear TABLE I. C OORDINATES DETERMINATION OF CONTROL POINTSC. Procedures of bevel gear’s parametric designAccording to the study results above, parametric design system for straight bevel gears were achieved by use of API functions based on Solidworks 2008.The flow chart of this work is shown as Fig.6.Figure 6. Flow chart of parametric designFirstly, a two-dimensional cross section graph of cone blank(see Fig.5) was sketched, CreatLine function was applied according to coordinates of control points in tab.1; Secondly, the sketch was revolved by FeatureRevolve function to generate a cone blank; and a datum plane was created by CreatePlaneAtAngle3 function,which is tangential to the back cone, as shown in Fig.8(a).Thirdly, two involute curves for toothspace profile were fitted by splines on the datum plane, enclosed by arcs, seeFig.7.Figure 7. Involute toothspace profileFurther, a point was created at apex O of the pitch coneby CreatPoint function, together with the toothspace curves, a toothspace was generated by function of InsertCutBlend, see Fig.8(a).Lastly, the toothspace was arrayed by FeatureCircularPattern2 function, so far the modeling isalmost finished; basing on it, some holes and key slot can beeasily cut by FeatureCut function, see Fig.8(b).(a) Cutting toothspace (b) Completed bevel gear modelFigure 8. Modeling of straight bevel gearD. Usage and resultsRun the macros programmed by Visual Basic codes and API functions in Solidworks part environment, a standard straight bevel gear model would be automatically and quickly generated after interactive operation. A pair of bevel gears created by running the macros was assembled, it showed that they fit well, see Fig.9.Figure 9. Assembled bevel gearsIV. S UMMARIESIn this study, structural features of straight bevel gear were analyzed; design variables were specified, and then the interactive interface was designed; Further, a Cartesian Coordinate System was set up and coordinates of control points were determined according to its geometric relationship. Through Visual Basic language and Solidworks API functions, parametric design of straight bevel gear has been implemented, running results showed that the parametric modeling of bevel gear was speedy and accurate, which will facilitate the 3D modeling of straight bevel gears in Solidworks.However, the methodology proposed in this paper is mainly addressed for straight bevel gears which intersect at right angle, but it provides references for straight bevel gears at other angles and spiral bevel gears. Based on it, the next work is to study the parametric design of them in Solidworks.R EFERENCES[1] L. Kong; J.Y.H. Fuh; K.S. Lee, etc.. A Windows-native 3D Plastic Injection Mold Design System. Journal of Materials Processing Technology[J], 2003.139, PP81-89.[2] Solidworks Corporation. Solidworks Advanced Training:Further Development & API[M]. Beijing:China Machine Press,2009,PP1-121. [3] ZHANG Yan-fu; XIA Chun. A Method of Involute Gear 3d Mode1 With SolidWorks. Machinery Design & Manufacture[J], 2005.11, PP61-62.[4]XUE Chen.Study of gear 3D Design Method Based on Solidworks.Development and Innovation of Machinery & Electrical Products[J], 2010.5, PP88-90.[5]XU Jie.Research on Gear’s 3D Parametrical Design Based on Solidworks.Machinery & Electricity Messages[J] ,2010.30, PP130-131.[6]LI Jun-wei, PAN Yu-tian. Parametric Design and Finite Element Analysis of Straight Bevel Gear Based on SolidWorks[J].Modern Production Engineering,2009.12,PP52-55.[7] M.F.Spotts; T.E.Shoup. Design of Machine Elements[M]. Beijing:China Machine Press,2003,PP596-600.[8]Mathematic Manual Compiling Group. Mathematic Manual[M]. Beijing:Higher Education Press,1979,PP380-381.[9]Ansel C.Ugural.Mechanical Design(An Integrated Approach)[M].Chongqing:Chongqing University Press,2005.1,PP110-111. [10]WU Zong-ze.Mechanical Elements Design Manual[M].Beijing:China Machine Press,2004,PP703-707.。
齿轮设计软件

齿轮设计软件导言齿轮被广泛应用于机械设备中,具有传动效率高、传动精度高等特点,是现代工业中不可或缺的重要组件。
然而,齿轮的设计过程中常常需要经过复杂的计算和繁琐的手工绘图工作。
为了简化齿轮设计的流程,提高设计效率和精度,齿轮设计软件应运而生。
本文将介绍齿轮设计软件的背景、功能以及市场现状。
一、背景在过去的几十年中,齿轮设计一直是机械工程师最重要的任务之一。
传统的齿轮设计方法主要依赖于手工计算和绘图,这种方式存在以下问题:1. 时间消耗:手工计算和绘图需要大量的时间和人力,特别是在复杂齿轮的设计过程中更是如此。
2. 精度限制:手工计算和绘图容易引入误差,限制了齿轮设计的精度。
3. 变更难度:一旦需要对设计进行修改或变更,手工计算和绘图的过程将会非常复杂和耗时。
为了解决这些问题,研发人员开始投入精力研发基于计算机的齿轮设计软件。
二、功能齿轮设计软件在设计过程中提供了许多帮助和辅助功能,大大简化了设计师的工作。
以下是齿轮设计软件通常提供的功能:1. 参数输入:设计师可以输入齿轮的有关参数,如模数、齿数、压力角等。
设计软件会根据这些参数进行计算,并生成相应的齿轮特征。
2. 齿轮建模:设计软件可以根据输入的参数和要求,自动生成齿轮的三维模型。
这样设计师无需手动绘制齿轮的图形,节省了大量时间。
3. 齿轮校验:设计软件可以对生成的齿轮模型进行校验,确保其满足设计要求。
通过计算齿轮的接触应力、接触长度等参数,软件可以判断齿轮是否符合可靠性和传动要求。
4. 优化设计:设计软件可以针对给定的设计要求,自动优化齿轮的参数。
通过迭代计算和自动调整参数,软件可以得到最佳的齿轮设计方案。
5. 结果分析:设计软件可以生成齿轮设计的结果报告,包括齿轮参数、计算结果和分析图表等。
这些结果可以被用于进一步的设计决策和评估。
6. 输出文件:设计软件可以输出齿轮的CAD模型文件或者图纸文件,方便与其他设计软件进行集成和使用。
三、市场现状目前市场上存在各种不同类型的齿轮设计软件,从简单的免费软件到功能强大的商业软件不一而足。
creo修改齿轮参数
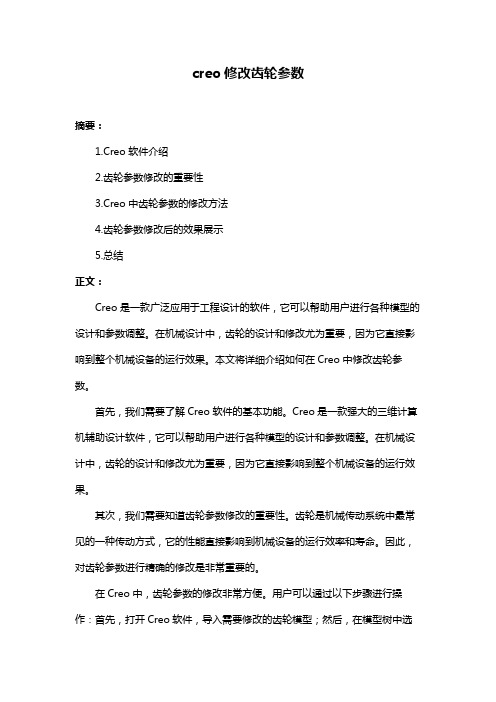
creo修改齿轮参数
摘要:
1.Creo软件介绍
2.齿轮参数修改的重要性
3.Creo中齿轮参数的修改方法
4.齿轮参数修改后的效果展示
5.总结
正文:
Creo是一款广泛应用于工程设计的软件,它可以帮助用户进行各种模型的设计和参数调整。
在机械设计中,齿轮的设计和修改尤为重要,因为它直接影响到整个机械设备的运行效果。
本文将详细介绍如何在Creo中修改齿轮参数。
首先,我们需要了解Creo软件的基本功能。
Creo是一款强大的三维计算机辅助设计软件,它可以帮助用户进行各种模型的设计和参数调整。
在机械设计中,齿轮的设计和修改尤为重要,因为它直接影响到整个机械设备的运行效果。
其次,我们需要知道齿轮参数修改的重要性。
齿轮是机械传动系统中最常见的一种传动方式,它的性能直接影响到机械设备的运行效率和寿命。
因此,对齿轮参数进行精确的修改是非常重要的。
在Creo中,齿轮参数的修改非常方便。
用户可以通过以下步骤进行操作:首先,打开Creo软件,导入需要修改的齿轮模型;然后,在模型树中选
择齿轮,进入参数编辑模式;接下来,用户可以修改齿轮的齿数、齿厚、齿距等参数;最后,点击“确定”按钮,完成参数修改。
在修改齿轮参数后,用户可以通过Creo软件的渲染功能,预览齿轮修改后的效果。
这样,用户可以直观地看到齿轮参数修改后对整个机械设备运行的影响。
总之,Creo软件为齿轮参数的修改提供了方便快捷的方式。
- 1、下载文档前请自行甄别文档内容的完整性,平台不提供额外的编辑、内容补充、找答案等附加服务。
- 2、"仅部分预览"的文档,不可在线预览部分如存在完整性等问题,可反馈申请退款(可完整预览的文档不适用该条件!)。
- 3、如文档侵犯您的权益,请联系客服反馈,我们会尽快为您处理(人工客服工作时间:9:00-18:30)。
mL及公差δL(微米)
齿 轮 直 径 (毫米)
>80~120 >120~200 115 115 120 120 40 130 130 130 130 50 140 140 140 140 70 170
>200~320 160 160 160 160 50 170 190 190 190 70 200 200 210
齿数 模数 变位系数
Z m X
17 6 0
外啮合高变位斜齿轮公法线长度计算 k≈(α n/180)*Z'+0.5+(2xnctgα n)/π Wk=mncosα n π (k-0.5)+Z'invα n+2xntgα n Z'=invα t/invα n α n 压力角 α n(弧度) 压力角(弧度) invα n 压力角渐开线函数 tgα n 压力角正切值 β (弧度) 螺旋角弧度 cosβ 螺旋角余弦值 α t(弧度) tgα n/cosβ 反余切值 invα t 端面压力角渐开线函数 tgα n/cosβ α t 分度圆端面压力角 Z' 假想齿 π (k-0.5) Z'invα n 2xntgα n mncosα n
6
Dc δ L
△mL
7
Dc δ L
△mL
8
Dc
△mL
8
Dc δ L
△mL >10~16 >1~16 >2.5~6 >6~10 >10~16 >2.5~16 — 48 115 — — 65 — 70 140 150 — 95
9
Dc δ L
△mL
外啮合变位斜齿轮跨棒(球)距计算 内啮合变位斜齿轮跨棒(球)距计算 dp=(1.6-1.9)Mn,常用dp=1.68Mn dp=(1.6-1.9)Mn,常用dp=1.68Mn invα M=invα t+dp/(d*cosα t)+2*xn*tgα invα M=invα t+dp/(d*cosα t)+2*xn*tgα n/z-π /(2*z) n/z-π /(2*z) 棒(球)直径 dp 8.25 棒(球)直径 dp 5 invα M 0.008577802 invα M 0.055138591 0.291976191 0.528002256 0.300566231 0.58323658 0.090340059 0.340164908 0.291840732 0.527720825 圆棒(球) 圆棒(球)中 α M α M 30.23617606 16.72124224 中心圆压力 心圆压力角 角 =d*cosα /cosα M+dp M(偶) M(偶)=mt*z*cosα t/cosα Mt-dp 跨棒(球)距(偶数齿) M(偶) 108.3304604 跨棒(球)距(偶数齿) M(偶) 105.9414523 M(奇)=d*cosα /cosα M*cos(90/Z)+dp M(奇)=mt*z*cosα t/cosα Mt*cos90/z-dp 跨棒(球)距(奇数齿) M(奇) 107.9035348 跨棒(球)距(奇数齿) M(奇) 105.4681956 Y3180E/YM3180E滚齿机差动挂轮调整公式 a*c/b*d=±9*[sinβ /(Mn*k)] Mn 6 模数 K 1 滚刀头数 螺旋角 β 0 螺旋角弧度 β (弧) 0 sinβ 0 a*c/b*d 0 差动
20 0.34906585 0.014904384 0.363970234 0 1 0.34906585 0.014904384 0.363970234 20 17 4.71238898 0.253374526 0 5.638155725
公法线长度最小偏差△mL及公差δL(微米)
精 度 等 级 结 合 形 式 代 法面模数 齿 轮 直 径
(毫
m法
号 (毫米) >1~2.5 >2.5~6 >6~10 >10~16 >1~16 >1~2.5 >2.5~6 >6~10 >10~16 >1~16 >1~2.5 >2.5~6 >6~10 ≤50 80 80 — — 34 85 85 — — 38 95 100 — >50~80 95 95 95 — 40 105 105 110 — 50 115 115 120
>320~500 210 210 210 210 50 220 220 240 240 70 240 240 240
150 70 160 160 180 95
180 80 190 200 210 115
210 90 240 240 240 140
240 90 280 280 280 140
反渐开线函数 渐开线函数 0.012221819 20 0.327573647 0.34906585 0.339816093 0.014904384 0.115474977 0.327395022 18.75835299
[
]
跨齿数 k 2 压力角 α 20 螺旋角 β 0 (α n/180)*Z' 1.888888889 2xnctgα n/π 0 K 跨齿数 2.388888889 公法线长度 Wk 27.99774794 端面模数 mt 6 分度圆直径 d 102 齿顶高 ha 6 齿顶圆直径 da 114 齿根高 hf 7.5 齿根圆直径 df 87 全齿高 h 13.5 总变位系数 X∑ 0 检验是否有足够齿宽测量公法线 齿宽b≥Lsinβ 35 Lsinβ 0