自动插件PWB设计参考及检查标准-11
AI PCB设计参考标准

自动插件PCB 设计参考及检查标准一. PCB 尺寸要求:PCB 的外形最小尺寸 50mm*50mm,最大尺寸450mm*450mm二.PCB 定位孔要求:根据PCB 长度L 的范围,插件机对于鹅蛋形定位孔距PCB 边缘的距离 S2 的要求也不同。
注意:圆形定位孔为固定的标准位置,鹅蛋形定位孔应根据PWB 长度L 的不同而其 S2 也有所改变,有关数据请参照下表:另外,当PCB 定位孔过多,生产时容易造成PCB 取放板方向混淆。
故设计PCB 时,只须在该PCB 长边上设计一组定位孔(左边圆形定位孔+右边 鹅蛋形定位孔)。
三. 自动插件机元件引脚直径范围为: 0.38mm -0.71mm因此,自动插件机可插以下元件:1. 1/16W 、1/8W 、1/4W 电阻2. 色环电容3. 0.6mm 跳线4. 二极管5. 色环电感四. 元件跨度C 的范围: 5.0mm -17.0mm设计元件跨度必须同时考虑到元件体长度L ,如果L 过长,插件机容易打伤 元件体或打断元件引脚,损坏插件机刀具,同时对排料机要求非常严格。
如果跨度C 过大,插件机速度会降低,插件时易掉件(插件机刀具夹不牢)、元件易浮脚。
目前AI 部插件最多的是5.0mm 跨度,5.0mm 跨度的元件在插件时比较容易出现拱起、损伤元件等坏机;故建议将AI插件元件的最小跨度定为6.0mm ,以求大幅度降低坏件率。
最小跨度的推算: 一般元件=MAX L +1.3mm二极管、色环电感=MAX L +2.8mm、五. 元件孔径要求:现时PCB 供应商工艺质量控制不是很好,如果再加上元件孔径过小,就不 符合插件机的插件要求,那将会极大的增加AI 插件的坏件率,需要增加大量人手去弥补(检查员检查和补件)。
但是,如果元件孔径过大,又将会导致元件过松容易脱落(过波峰焊前),且会产生锡 点不良等质量问题。
自插机要求:MIN D = MAX d + 0.45考虑以上情况,我们确定如下数据:注意:以上孔径对于手插元件可能过大,故请参考第三、第四、第六、第九、第十点, 分清哪些元件是手插件,以便单独对手插件的孔径采用不同的标准。
常见IPC PCB标准一览表
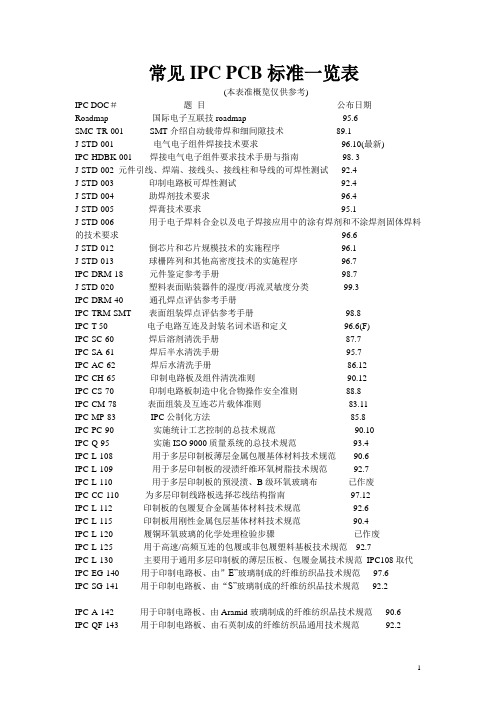
常见IPC PCB标准一览表(本表准概览仅供参考)IPC DOC#题目公布日期Roadmap 国际电子互联技roadmap 95.6SMC-TR-001 SMT介绍自动载带焊和细间隙技术89.1J-STD-001 电气电子组件焊接技术要求96.10(最新)IPC-HDBK-001 焊接电气电子组件要求技术手册与指南98. 3J-STD-002 元件引线、焊端、接线头、接线柱和导线的可焊性测试92.4J-STD-003 印制电路板可焊性测试92.4J-STD-004 助焊剂技术要求96.4J-STD-005 焊膏技术要求95.1J-STD-006 用于电子焊料合金以及电子焊接应用中的涂有焊剂和不涂焊剂固体焊料的技术要求96.6J-STD-012 倒芯片和芯片规模技术的实施程序96.1J-STD-013 球栅阵列和其他高密度技术的实施程序96.7IPC-DRM-18 元件鉴定参考手册98.7J-STD-020 塑料表面贴装器件的湿度/再流灵敏度分类99.3IPC-DRM-40 通孔焊点评估参考手册IPC-TRM-SMT 表面组装焊点评估参考手册98.8IPC-T-50 电子电路互连及封装名词术语和定义96.6(F)IPC-SC-60 焊后溶剂清洗手册87.7IPC-SA-61 焊后半水清洗手册95.7IPC-AC-62 焊后水清洗手册86.12IPC-CH-65 印制电路板及组件清洗准则90.12IPC-CS-70 印制电路板制造中化合物操作安全准则88.8IPC-CM-78 表面组装及互连芯片载体准则83.11IPC-MP-83 IPC公制化方法85.8IPC-PC-90 实施统计工艺控制的总技术规范90.10IPC-Q-95 实施ISO 9000质量系统的总技术规范93.4IPC-L-108 用于多层印制板薄层金属包履基体材料技术规范90.6IPC-L-109 用于多层印制板的浸渍纤维环氧树脂技术规范92.7IPC-L-110 用于多层印制板的预浸渍、B级环氧玻璃布已作废IPC-CC-110 为多层印制线路板选择芯线结构指南97.12IPC-L-112 印制板的包履复合金属基体材料技术规范92.6IPC-L-115 印制板用刚性金属包层基体材料技术规范90.4IPC-L-120 履铜环氧玻璃的化学处理检验步骤已作废IPC-L-125 用于高速/高频互连的包履或非包履塑料基板技术规范92.7IPC-L-130 主要用于通用多层印制板的薄层压板、包履金属技术规范IPC108取代IPC-EG-140 用于印制电路板、由”E”玻璃制成的纤维纺织品技术规范97.6IPC-SG-141 用于印制电路板、由“S”玻璃制成的纤维纺织品技术规范92.2IPC-A-142 用于印制电路板、由Aramid玻璃制成的纤维纺织品技术规范90.6 IPC-QF-143 用于印制电路板、由石英制成的纤维纺织品通用技术规范92.2IPC-CF-148 用于印制板的涂敷环氧树脂的金属98.9 IPC-MF-150 用于印制线路的金属箔92.8 IPC-CF-152 用于印制线路板的复合金属材料技术规范98.3 IPC-FC-203 扁平电缆、圆导体、接地面技术规范85.7 IPC-FC-210 扁平连接器地下电缆性能技术规范85.9 IPC-FC-213 扁平地下电话电缆技术规范84.9 IPC-FC-217IPC-FC-218B接插件、电气扁平电缆类型通用技术规范91.5 IPC-FC-219 航空用密封环境下扁平电缆接插件84.5 IPC-FC-220 非屏蔽扁平电缆、扁平接插件技术规范85.7 IPC-FC-221 用于扁平电缆的扁平铜导体技术规范84.5 IPC-FC-222 非屏蔽扁平电缆圆导体技术规范91.5 IPC-FC-225 扁平电缆设计指南85.10 IPC-FC-231 用于柔性印制线路的柔性基体绝缘材料95.10 IPC-FC-232 用于柔性印制线路和柔性连接膜覆盖板涂镀粘接剂95.10 IPC-FC-233 参考232IPC-FC-241 用于制造柔性印制线路的柔性包履金属绝缘材料95.10 IPC-RF-245 刚柔印制电路板性能技术规范87.4 IPC-D-249 单、双面柔性印制电路板设计标准87.1 IPC-FC-250A 单、双面柔性印制线路技术规范86.9 IPC-FA-251 单面和双面柔性电路指南92.2 IPC-D-275 刚性印制电路板和刚性印制电路板组件设计标准96.4 IPC-RB-276 刚性印制电路板规格和性能技术规范92.3 IPC-D-279 可靠的表面组装技术印制电路板组件设计指南96.7 IPC-D-300 印制电路板尺寸和公差84.1 IPC-D-310 照相工具生成和测量技术指南91.6 IPC-A-311 照相工具生成及使用工艺控制指南96.3 IPC-D-316 采用软基板的微波电路板设计指南95.5 IPC-D-317 采用高速技术的电子封装设计指南95.1 IPC-HF-318 微波终端产品电路板的检验和测试91.12 IPC-D-319 刚性单面和双面印制电路板设计标准87.1 IPC-D-320A 印制电路板、刚性、单面和双面、终端产品标准81.3 IPC-SD-320B 刚性单面和双面印制电路板性能技术规范86.11 IPC-D-322 参照标准板尺寸选择印制线路板尺寸指南91.9 IPC-MC-324 金属芯电路板性能技术规范88.10 IPC-D-325 印制电路板、组件和支持图文件技术要求95.5 IPC-D-326 制造印制电路板组件资料技术要求91.4 IPC-D-330 设计指南手册IPC-PD-335 电子封装手册89.12 IPC-NC-349 布线器计算机数字控制格式化85.8 IPC-D-350 用数字形式描述印制电路板92.7 IPC-D-351 用数字形式描述印制电路板图85.8 IPC-D-352 用数字对式印制电路板的电子设计数据描述85.8IPC-D-354 数字形式印制电路板图库格式描述87.2IPC-D-355 用数字形式描述印制电路板组装95.1IPC-D-356 用数字形式测试的裸板电气性能资料98.1IPC-AM-361 用于加工艺印制电路板的刚性基板技术规范82.1(作废)IPC-MB-380 模制互连器件指南90.10IPC-D-390 自动设计指南88.2IPC-C-406 表面组装接插件设计和应用指南90.1IPC-CI-408 非焊接表面贴装接插件设计和应用指南94.1IPC-BP-421 压装的刚性印制电路板底板通用技术规范90.4IPC-D-422 压装刚性印制电路板底板设计指南82.9IPC-DW-424 密封分立线互连电路板通用技术规范95.1IPC-DW-425 分立线路板设计与终端产品技术要求90.5IPC-DW-426 分立线路组装技术规范87.12IPC-TR-460 印制线路板波峰焊接故障检测表84.2IPC-TR-461 厚薄涂层的可焊性评价79.3IPC-TR-462 为长期保存而涂履保护涂层的印制线路板的可焊性评价87.10IPC-TR-464 用于可焊性评价的加速老化87.12IPC-TR-465-1 关于蒸气老化温度控制稳定性的循环测试93IPC-TR-465-2 蒸气老化时间和温度对可焊性测试结果的影响93IPC-TR-465-3 关于替代涂饰蒸汽老化评价96.7IPC-TR-466 润湿平衡标准重量比较测试95.4IPC-TR-467 ANSI/J-STD-001附件D的支持数据和数字举例96.10IPC-TR-468 影响印制电路板绝缘电阻性能的因素79.3IPC-TR-470 多层互连线路板的热特性74.1IPC-TR-474 分立线路技术综观79.3IPC-TR-476 如何避免电子硬件中金属膨胀问题74.1IPC-TR-480 多层IV 循环测试程序阶段I的结果75.9IPC-TR-481 多层V 循环测试程序的结果81.4IPC-TR-483 薄层压板的尺寸稳定性测试椀?/FONT>1 阶段报告国际循环测试程序86.4 IPC-TR-484 IPC铜箔延展性循环研究的结果86.4IPC-TR-485 IPC铜箔脆性强度测试循环研究结果85.3IPC-TR-549 印制线路板上的斑点73.11IPC-TR-551 印制板电子元件组装和互连的质量评价93.7IPC-DR-570 直径为1/8英寸的硬质合金钻头印制板总技术规范84.4IPC-DR-572 印制电路板钻孔指南88.4IPC-TR-576 加工艺评价77.9IPC-TR-578 引线边缘制造技术报告84.9IPC-TR-579 印制线路板小直径镀履通孔的循环可靠性评估88.9IPC-TR-580 清洗和清洁度测试程序第1阶段测试结果89.10IPC-TR-581 IPC第3 阶段控制气氛焊接研究94.8IPC-TR-582 IPC第3 阶段免洗助焊剂研究94.11IPC-A-600 印制电路板的可接受性(检验标准) 95.8IPC-QE-605A 印制电路板质量评价手册99.2IPC-SS-605 印制电路板质量评价IPC-A-610 电子组件的检验标准95.8IPC-QE-615 组装质量评估手册93.3IPC-SS-615 组装质量评估93.3IPC-AI-640 未贴装元件的厚膜混装基板的自动检测用户指南87.1IPC-AI-641 焊点自动检测用户指南87.1IPC-AI-642 原理图、内层、未贴装元件的PWB自动检测用户指南88.10IPC-OI-645 光学检测仪器标准93.10IPC-TM-650 测试方法手册IPC-ET-652 未贴装元件的印制电路板的电气测试规则和技术要求90.10IPC-QL-653 检验/测试印制电路板、元件、材料的设备鉴定97.11IPC-MI-660 原材料来料检测手册84.2IPC-R-700C 印制电路板和组件的改型、返工、返修指南88.1IPC-TA-720 层压板技术评估手册IPC-TA-721 多层电路板技术评估手册IPC-TA-722 焊接技术评估IPC-TA-723 表面组装技术评估手册IPC-TA-724 净化间技术评估IPC-PE-740 印制电路板制造和组装故障检测指南97.12IPC-CM-770 印制电路板元件贴装96.1IPC-SM-780 表面组装元件的封装和互连88.3IPC-SM-782 表面组装设计和焊盘图形标准96.10 IPC-EM-782 表面组装设计和焊盘分布图形95.12 IPC-SM-784 COB技术应用指南90.11IPC-SM-785 表面贴装焊点连接的快速可靠性测试指南92.11 IPC-SM-786 潮湿气氛/再流感应ICs的特性化和处理步骤95.1IPC-MC-790 多芯片模块技术应用指南92.8IPC-S-804 印制线路板的可焊性测试方法87.1IPC-S-805 元件引线和端点的可焊性测试85.1IPC-MS-810 高容量显微薄片指南93.10 IPC-S-815 焊接电子互连件的通用技术要求87.12 IPC-S-816 SMT工艺指南和清单93.7IPC-SM-817 绝缘表面贴装胶的通用技术要求89.11 IPC-SF-818 用于电子组件焊接的助焊剂通用技术要求91.12IPC-SP-819 用于电子工业的焊膏通用技术要求和测试方法88.10IPC-AJ-820 组装和连接手册96.8IPC-CA-821 导热粘接剂通用技术要求95.1IPC-CC-830 用于印制电路板组件的电子绝缘化合物的鉴定和性能98.10IPC-SM-839 施用焊料掩膜前后的清洗指南90.4IPC-SM-840 用于印制电路板的永久性聚合物涂层的鉴定与性能96.1IPC-H-855 混合微电路设计指南82.10 IPC-D-859 厚膜多层混合电路设计标准89.12 IPC-HM-860 多层混合电路技术规范87.1IPC-TF-870 聚合物厚膜印制电路板的鉴定和性能89.11 IPC-ML-910 被275替代IPC-D-949 刚性多层印制电路板设计标准87.1IPC-ML:-950 刚性多层印制电路板性能技术规范86.11IPC-ML-960 用于多层印制电路板的批量层压面板的鉴定与性能技术规范94.7IPC-ML-975 用于多层印制线路板的终端产品技术规范69.9IPC-ML-990 柔性多层线路性能技术规范72.9IPC-1402 混合微电路设计指南82.10IPC-1710 印制电路板制造者的鉴定曲线(MQP)的OEM标准97.12IPC-1720 组装鉴定曲线(AQP) 96.7IPC-1730 胶合机鉴定曲线(LQP) 98.1IPC-2141 可控阻抗电路板与高速逻辑设计90.4IPC-2221 印制电路板通用标准98.2IPC-2222 刚性有机印制电路板部分设计标准98.2IPC-2223 柔性印制电路板分段设计标准98.11IPC-3406 表面组装用导电胶规则96.7IPC-3408 各向异性导电粘接剂膜通用技术要求96.11IPC-4101 刚性及多层印制板的基体材料技术规范97.12IPC-4110 用于印制电路板非纺织物纤维素纸技术规范与特征化方法98.8IPC-4130 非纺织物”E”玻璃纤维板技术规范与特征化方法98.9IPC-6011 印制电路板通用性能技术规范96.7IPC-6012 刚性印制电路板的鉴定与性能技术规范96.7IPC-6013 柔性印制电路板的鉴定与性能技术规范98.11IPC-6015 有机多芯片模块(MCM-L)组装及互连结构的鉴定与性能技术规范98.2IPC-6018 微波终端产品电路板检验与测试98.1IPC/JPCA-6202 单双面柔性印制线路板性能指导手册99.2IPC-7711 电子组件返修98.4IPC-7721 印制电路板和电子组件的返修与改型98.4IPC-9201 表面绝缘电阻手册96.7IPC-9501 评价电子元件的PWB仿真组装工艺95.7 公布IPC-9504 评价非IC元件的仿真组装工艺98.6 度量图98.4片式元件图98.8鸥翼形元件图98.8J形引线元件图98.8。
PCB、PWB设计及生产流程

根据软硬进行分类
分为普通电路板和柔性电路板、软硬CB 基本设计流程如下: 前期准备PCB 结构设计PCB 布局布线布线优化丝印网络DRC 检查-->结构检查制版。 第一:前期准备。这包括准备元件库和原理图。工欲善其事,必先利 其器, 要做出一块 好的板子, 除了要设计好原理之外, 还要画得好。 在进行 PCB 设计之前, 首先要准备好原理图 SCH 的元件库和 PCB 的元 件库。元件库可以用 peotel 自带的库,但一般情况下很难找到合适 的,最好是自己根据所选器件的标准尺寸资料自己做元件库。原则上 先做 PCB 的元件库,再做 SCH 的元件库。PCB 的元件库要求较高,它 直接影响板子的安装;SCH 的元件库要求相对比较松,只要注意定义 好管脚属性和与 PCB 元件的对应关系就行。PS:注意标准库中的隐藏 管脚。之后就是原理图的设计,做好后就准备开始做 PCB 设计了。 第二:PCB 结构设计。这一步根据已经确定的电路板尺寸和各项机械 定位,在 PCB 设计环境下绘制 PCB 板面,并按定位要求放置所需的接 插件、按键/开关、螺丝孔、装配孔等等。并充分考虑和确定布线区 域和非布线区域(如螺丝孔周围多大范围属于非布线区域)。 第三:PCB 布局。布局说白了就是在板子上放器件。这时如果前面讲 到的准备工作都做好的话,就可以在原理图上生成网络表(Design Create Net list) , 之后在 PCB 图上导入网络表 (Design Load Nets) 。 就看见器件哗啦啦的全堆上去了,各管脚之间还有飞线提示连接。然 后就可以对器件布局了。一般布局按如下原则进行: ①.按电气性能 合理分区,一般分为:数字电路区(即怕干扰、又产生干扰)、模拟电 路区(怕干扰)、功率驱动区(干扰源); ②.完成同一功能的电路, 应尽量靠近放置,并调整各元器件以保证连线最为简洁;同时,调整
插件机设计规范要求样本
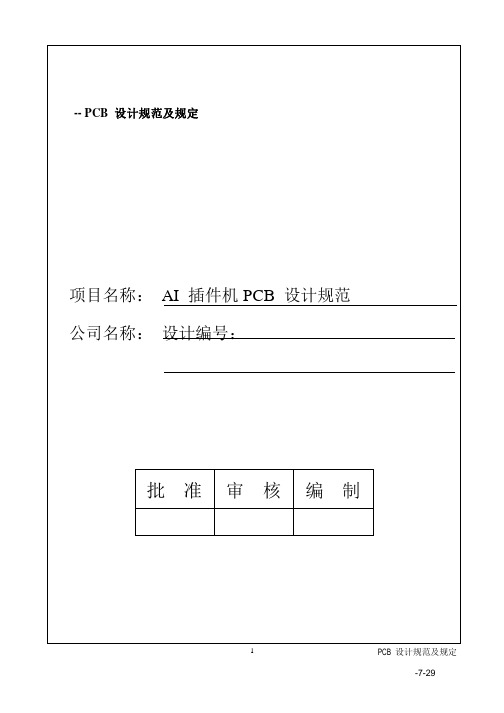
5PCB设计规范及规定
-7-29
印刷线路板公差:
6PCB设计规范及规定
-7-29
最大lb插入跨距p27插入跨距为mm时最大lb34mmpcb设计规范及要求729计算相邻元件之间需留的间隙
--PCB设计规范及规定设计编号:
批准
审核
编制
1PCB设计规范及规定
-7-29
1:印刷线路板设计原则:
2.1印刷线路板规格。
机器正面
2PCB设计规范及规定
-7-29
2.2插入限制:
3PCB设计规范及规定
-7-29
元件长度:
编带精度(I):最大Lb=插入跨距(P)-1.6编带精度(Ⅱ):最大Lb=插入跨距(P)-2.O编带精度(Ⅲ):最大Lb=插入跨距(P)-2.7
★插入跨距为5mm时,最大Lb为3.4mm(5-1.6=3.4)
4PCB设计规范及规定
-7-29
AI立式元件设计参考
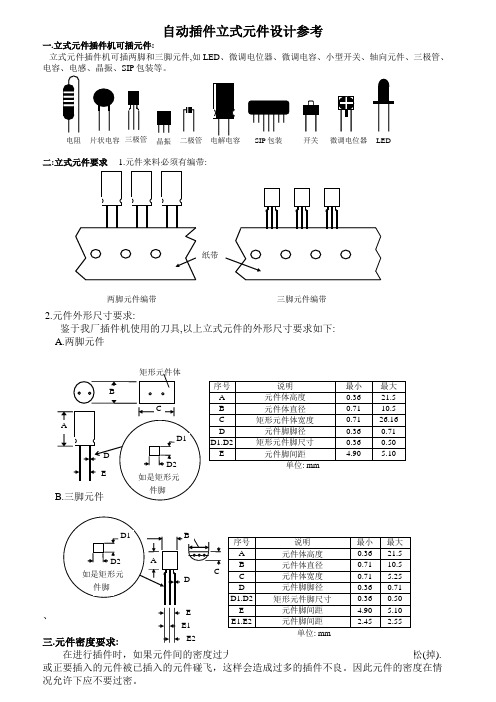
自动插件立式元件设计参考一.立式元件插件机可插元件:立式元件插件机可插两脚和三脚元件,如LED、微调电位器、微调电容、小型开关、轴向元件、三极管、电容、电感、晶振、SIP包装等。
二:立式元件要求 1.元件来料必须有编带:2.元件外形尺寸要求:鉴于我厂插件机使用的刀具,以上立式元件的外形尺寸要求如下:A.两脚元件、三.元件密度要求:在进行插件时,如果元件间的密度过大,会令已插入的元件被正要插入的元件碰松(掉).或正要插入的元件被已插入的元件碰飞,这样会造成过多的插件不良。
因此元件的密度在情况允许下应不要过密。
注:MIN(r1,r2)表示取r1和r2中最小的值,例r1=3.0,r2=5.0,则MIN(r1,r2)=3.0四.立式元件孔位要求平行或垂直(偏差不超过0.05mm,同卧式元件要求一样)五.元件极向要求对于有极性的立式元件,如三极管、二极管、电解电容、LED 等,要求极性方向一致,(通常规定X 方向元件负极向左,Y 方向元件负极向上)。
否则自动插件机生产效率降低,编制插件机程序困难,浪费插件机站位(如果方向不一致,同一种元件要占用2个站位,若方向一致,只需一个站位),而且人手补件时较难辨认极性,容易插反. * 此点对于人手插件PCB 设计同样适用六. PCB 元件孔跨度C(C1)的要求.注意:同一PC 板上立式元件两脚元件间距C 统一为5mm/或2.5mmX 方向元件负极全部向左 Y 方向元件负极全部向上 GOOD 极性不统一:负极向左向右向上向下均有 NO GOOD七. PCB 元件孔径的要求.D1:元件脚直径 D2:元件孔直径请注意:此孔径比较大,如果用人手插件,会产生浮脚、锡点不良等质量问题。
因此在设计时应明确该元件是手插还是机插。
八. 增加白油保护层如果PCB 铜皮面线路较密,自动插件时容易造成元件与相邻铜皮短路,因此在设计PWB 时应在元件焊盘加白油保护.请注意立式元件的弯脚与卧式元件的弯脚不一样,其元件的弯脚是向两边呈45°弯曲成形的。
WXB-11线路保护全部检验作业指导书

编号:Q/×××变电站线WXB-11保护全部检验作业指导书(试行)作业负责人:作业日期年月日至年月日华北电网有限公司前言为进一步加强华北电网继电保护校验工作的规范性、标准化,强化继电保护现场安全管理,决定编制本作业指导书。
通过作业指导书,把继电保护现场工作做实、做细并进行优化,使现场工作可控、在控,以减少现场工作失误,从而有力地保证电网的可靠运行。
本作业指导书以《电力企业标准编制规则》(DL/T800-2001)为基础,参照国家电网公司标准化作业指导书(范本)编写。
本作业指导书的附录A、附录B及附录C、分别为保护装臵的主要技术参数、试验报告及现场工作安全技术措施,是本作业指导书不可分割的部分,具有与本指导书相同的效力。
本作业指导书由华北电网有限公司提出,京津唐电网继电保护作业指导书编写工作组负责编写,由华北电力调度局负责解释。
本作业指导书起草人:李群矩、李钢、刘平本作业指导书审核人:许国峰本作业指导书自发布之日起执行。
1范围1.1本作业指导书适用于WXB11微机保护线路成套继电保护装臵的检验作业。
1.2作业目的是对线路成套继电保护装臵运行过程中的周期性全部检验。
2引用文件下列标准及技术资料所包含的条文,通过在本作业指导书中的引用,而构成为本作业指导书的条文。
本作业指导书出版时,所有版本均为有效。
所有标准及技术资料都会被修订,使用本作业指导书的各方应探讨使用下列标准及技术资料最新版本的可能性。
2.1 《国家电网公司电力安全工作规程》2.2 GB 7261-2001《继电器及继电保护装臵基本试验方法》2.3 GB 14285-93《继电保护和安全自动装臵技术规程》2.4 GB/T 15145-2001《微机线路保护装臵通用技术条件》2.5 DL 478-2001《静态继电保护及安全自动装臵通用技术条件》2.6 DL/T 559-94 220--500kV《电网继电保护装臵运行整定规程》2.7 DL/T 624-1997《继电保护微机型试验装臵技术条件》3检验前准备3.1准备工作安排3.3备品备件3.4工器具3.5材料3.6危险点分析3.7安全措施3.8人员分工4WXB-11线路保护全部检验流程图工作负责人5、作业程序和作业标准(试验记录见附录B) 5.1开工.2 检修电源的使用55.4竣工6、验收记录7、作业指导书执行情况评估附录A(资料性附录)设备主要技术参数B.2.1定值单执行情况记录高频保护:执行字号,年月日距离保护:执行字号,年月日零序保护:执行字号,年月日重合闸:执行字号,年月日人机对话控制字:在保护上电前,进行下列检查,将检查结果填入表1。
SMT_PWB检验标准

板子上金手指部位有锡膏
焊点上的焊料量低于最少需求量,会造成焊点虚焊 零件与焊盘没有焊接 在样品上有零件的位置,实际上没有零件,(过BTU前pad上 无组件,此pad点刨满、光亮) 在样品上有零件的位置,实际上没有零件,(过BTU后在流转 中组件脱落,此pad点灰暗,无光泽.) 有极性的电子零件,正负极性贴装错乱,颠倒 外来多余的锡附在表面形成珠状焊点
焊锡回流不完全
连焊
浮高
晶片状元件不允许存在浮高
L型脚可接受标准: 1.最大浮起高度小于引脚厚度的 2倍 2.引脚基本平贴 3.本题焊接面积大于1/3的PAD 4.不影响结构和功能
J型脚可接受标准: 最大浮起高度小于引脚厚度的2倍
锡珠/锡渣
不可接受标准:
1.锡珠/锡渣分布在焊盘或印制线条周围0.10mm范围内。 2.锡珠直径大于0.13mm。 3.每片PWB上超出2个以上的锡珠,且锡珠都是大于0.13mm。 4.任何会造成短路的锡珠。 5.三倍以内放大镜或目视,可直接看到的锡渣。
3
4 5 6 7 8 9 10 11 12 13 14
多件
多锡 浮高 外来异物 反白 金手指沾锡 少锡 空焊 漏件 撞件 极性贴反 锡珠
FM (Foreign Material)
FP (Flip Part)
零件底部或PCB上有不明物
零件与实际贴片翻转180度背面朝上
GF (Gold Finger)
IS (Insufficient Solder) OP (Open) PM (Pass Missing) IP (Impact Part) RP (Reversed Part) SB(Solder Ball)
TP (Tombstone Part)
SU (Stand-Up) US (Unsolder) WP (Wrong Part) PE (PCB Error) PB (PCB Break) PO (PCB Overheated) PCS (PCB Circuit Short)
PCB检验规范

5.3各层间隔5.3.1 层与层之绝缘至少0.0035"。
5.3.2 每一绝缘层至少须由1片环氧树脂构成。
5.3.3 各层间之绝缘层厚度应对称排列。
5.3.4 各层之排列顺序依原稿底片上之指定5.4、导线5.4.1 导线蚀刻5.4.1.1 Undercut :每一边不可超过铜层的总厚度。
5.4.1.2 Overhang :每一边不可超过铜层的总厚度。
5.4.2 线宽5.4.2.1线路宽度变化不得大于该线路宽之20%或±0.125mm.两者取其轻者,且不得影响最细线宽之要求(0.25mm).5.4.2.2线路缺损所有线路的缺点(缺口、凹陷_、刮伤等):A.其缺损宽度(W)为导体宽度之20%以内或1mm,两者取其轻者。
B.其缺损长度(L)为导体宽度之20%以内或2mm,两者取其轻者。
C.一条导线内至多容许有一个缺点。
D.在100X100mm单位面积下,只容许三处出现缺损。
如下图所示。
5.4.3 间距5.4.3.1两导线间距变化不得大于该间距之1/5或±0.125mm.(取其轻者),且不得违背原最小间距要求(0.5mm).5.4.3.2 线路凸出,不得影响成品最小间距之20%,长度不得大于0.5"。
5.4.3.3 最小间距不得小于0.004"。
5.4.4余铜屑5.4.4.1若残余铜箔造成安全要求不符时, 则不允许。
5.4.4.2不影响安全规范时,两导线之余铜横跨处不可大于两导线间距之50%,且最长边不可大于0.032"。
在100X100mm单位面积中,只允许一处出现。
5.4.4.3 非导线处余铜可以刀片刮掉,但不可露出底材。
5.4.5 线路不可有任何修补的情况。
5.4.6线路与PC板边缘距离至少需0.5mm,其它要求则另行注明。
5.5、焊垫、环垫5.5.1缺损5.5.1.1缺口或凹洞不得超过PAD总面积之10%, 缺损位置不可出现在PAD与线路相接之处(AREA A)。
焊点检验规范

1、特征:焊接成不平滑外表,严重时于线脚四周,产生皱折或裂缝。
2、影响性:焊点寿命较短,容易于使用一段时间后,开始产生焊接不良之现象,导致功能失效。
3、造成原因:焊点凝固时,受到不当震动(如输送皮带震动),焊接物(线脚、焊垫)氧化,润焊时间不足。
4、补救处置:排除焊接时之震动来源;检查线脚及焊垫之氧化状况,如氧化过于严重,可事先Dip 去除氧化、调整焊接速度,加长润焊时间。
针孔:1、特征:于焊点外表上产生如针孔般大小之孔洞2、影响性:外观不良且焊点强度较差3、造成原因:PWB含水气;零件线脚受污染(如硅油);倒通孔之空气受零件阻塞,不易逸出。
4、补救处置:PWB过炉前以80~100℃烘烤2~3小时;严格要求PWB在任何时间任何人都不得以手触碰PWB表面,以避免污染;变更零件脚成型方式,避免Coating落于孔内,或察看孔径与线径之搭配是否有风孔之现象。
1、特征:在不同线路上两个或两个以上之相邻焊点间,其焊垫上之焊锡产生相连现象。
2、影响性:严重影响电气特性,并造成零件严重损害3、造成原因:板面预热温度不足;输送带速度过快,润焊时间不足;助焊剂活化不足;板面吃锡高度过高;锡波表面氧化物过多;零件间距过近;板面过炉方向和锡波方向不配合。
4、补救处置:调高预热温度;调慢输送带速度,并以Profile确认板面温度;更新助焊剂;确认锡波高度为1/2板厚高清除锡槽表面氧化物;变更设计加大零件间距;确认过炉方向,以避免并列线脚同时过炉,或变更设计并列线脚同一方向过炉。
空焊:1、特征:零件线脚四周未与焊锡熔接及包覆2影响性:电路无法导通,电气功能无法显现,偶尔出现焊接不良,电气测试无法检测。
3、造成原因:助焊剂发泡不均匀,泡沫颗粒太大;助焊剂未能完全活化;零件设计过于密集,导致锡波阴影效应;PWB变形锡波过低或有搅流现象;零件脚受污染;PWB氧化、受污染或防焊漆沾附;过炉速度太快,焊锡时间太短。
4、补救处置:调整助焊剂发泡槽气压及定时清洗;调整预热温度与过炉速度之搭配;PWB Layout设计加开气孔;调整框架位置;锡波加高或清除锡渣及定期清理锡炉;更换零件或增加浸锡时间;去厨防焊油墨或更换PWB;调整过炉速度。
PCB检验规范

A.其缺损宽度(W)为导体宽度之20%以内或1mm,两者取其轻者。
B.其缺损长度(L)为导体宽度之20%以内或2mm,两者取其轻者。
C.一条导线内至多容许有一个缺点。
D.在100X100mm单位面积下,只容许三处出现缺损。如下图所示。
5.4.3间距
5.4.3.1两导线间距变化不得大于该间距之1/5或±0.125mm.(取其轻者),且不得违背原最小间距要求(0.5mm).
TGL.
±0.1mm
5.6.2孔位容许误差以TOOLING HOLE为基准原点,其孔位及SMD PATTERN坐标误差不得大于0.1mm,而其圆弧误差以0.25mm为上限。
5.6.3不允许有破孔出现,但确认为安规要求因素造成者除外。
5.6.4不允许有漏钻孔出现。
5.6.5非规格内之多余孔位,须经本公司技术部确认后方可成立。
±0.3 mm.
5.5.2.4锡垫计算:
PAD=D+(0.67XDX2)适用于孔径小于1.8mm的。
PAD=D+(0.50XDX2)适用于孔径大于2.0mm的。
(UNIT: mm)
独立孔
非独立孔
孔径
PAD
孔径
PAD
孔径
PAD
孔径
PAD
孔径
PAD
0.8
1.8
1.6
3.8
2.2
4.4
1.6
3.2
2.2
3.8
5.9.8金手指斜角部份允许露铜。
5.9.9附着力试验方法同5.8.1。
5.10、止焊膜
5.10.1颜色为绿色或红色双面印刷,如有特殊要求则另行注明。
5.10.2导线上止焊膜必须覆盖完全,不可露锡或露铜,但允许止焊膜修补,修补规范如下:
插件物料要求
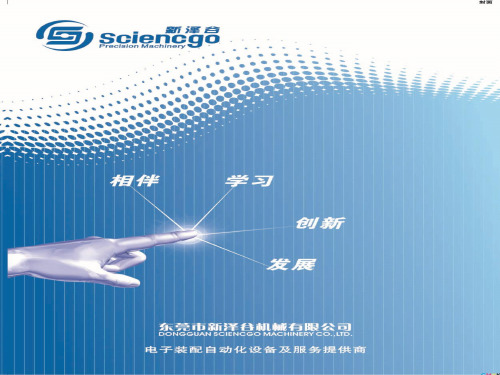
0.05 A CS
A
0.05 A
Hale Waihona Puke 图7图8物料要求
3. 元件插孔直径Ø,按元件引线直径+0.5mm来计算,如 卧插元件: Ø=1.3±0.1mm(塑封整流二极管等0.8mm引线的元件) Ø=1.1±0.1mm(1/2W、1/4W电阻、电感、跳线等0.6mm引线的 元件) Ø=1.0±0.1mm(1/6W、1/8W电阻、玻璃二极管等0.5mm引线的 元件) 立插元件: Ø=1.1±0.1mm
物料要求
C)
立式元件与SMT元件间的密度: 正反面 SMT元件与立式元件的密度 由于立式插件机的元件剪断弯脚部件在进行立式插件时会与PCB的正反有较近的距离,为此对 正反面的SMT元件与立式元件孔的距离有要求。
物料要求
1、(W)4mm×(L)9mm的范围内不可有SMT元件。 2、(W)10mm×(L)16mm的范围内不可有高度大于1mm的SMT元件。 3、(W)13mm×(L)22mm的范围内不可有高度大于5mm的SMT元件。 上下平面的元件高度不可大于6mm。
物料要求
1.3 卧式元件与贴片的密度要求 3mm 3mm
PCB板 卧式零件 1.元件本体、元件引角与SMT贴片元件最小距离为圆周3mm 2.零件脚弯曲度数:15-45度(可调)
物料要求
1.4 元件铜皮设计: 自插机插件时,一直存在如下问题: (1).元件角度过大,容易掉件和产生浮脚 (2).元件角度过小,容易和相邻铜皮短路
物料要求
五、元件形体的限制 1.卧插元件:如图9所示,对元件形体作如下限制 长度 L = 3.0mm ~ 10mm 本体直径 D = 0.6mm ~ 4.0mm 引线直径 d = 0.4mm ~ 0.8mm 跳线 L=5.5mm ~ 30mm
PWB制作说明

编号:PWB制作说明机种:T006PL-C01E/XX 料号:T0067800A-PL 发行时间:090902 技术要求:1.板材FR42.板厚 1.6mm4.板层 25.公差要求PCB板要求厚度为1.6mm (公差-0.15mm);NPTH孔公差±0.05mm6.孔径要求所有孔径都为成品孔径7.空旷区是否要求加铜点无8.拼板方式2拼右边加10MM工艺边,工艺边上下各开直径4毫米的孔,并距板边各5mm9.特殊孔说明(如槽孔) 注意,中间有4个方槽,电源插座SP1有3个方槽. ANT1上有一个方槽10.需要下方绿油严格履盖的元件标号模块U3下方绿油和白油严格覆盖1.11.制作工艺要求采用无铅OSP工艺2.分孔图圆环或方框按线中心为准的尺寸做NTPH孔或NTPT槽3.与线路层焊盘等大的孔做NPTH孔,若需做成PTH孔,将给予特殊说明4.焊盘及开窗上白油允许移出或削去,字符可以移动,但是不能削去;5.所有直径在0.35mm以下的过孔都必须做塞孔处理6.IC盘间距小于0.2mm需要保留阻焊桥,允许削小单边的焊盘。
如果削后焊盘过小,同意不做阻焊桥,此项需要工程确认)7.允许削线路焊盘或移线等保证线路距板边0.4mm以保证不露铜8.稀疏区线距小于0.15mm的允许移线至间距0.2mm10. 不用理会字符层或者钻孔参考层中的标注尺寸,不允许把标注的符号印刷到PCB板上。
11.稀疏光标点允许加分流框12.板面的绿油覆盖厚度要求达到5微米以上13.焊盘及开窗上白油允许移出或削去;字符可以移动,但是不能削去确认人:孙斌拼板示意图(仅做示意,可能与原板不同)红色部分为10MM工艺边在工艺边上下两角开圆形孔,直径4mm,距离板边周围5mm叠层要求审核二审核一拟稿。
水密接插件检验标准国标

水密接插件检验标准国标
水密接插件是一种用于在潮湿或水下环境中连接电气设备的连接器,其检验标准需要符合国家标准。
以下是一些可能涉及的国家标准:1. GB/T 11918-2014《工业用插头插座和耦合器第1 部分:通用要求》:该标准规定了工业用插头插座和耦合器的通用要求,包括尺寸、电气性能、机械性能、防护等级等方面的要求。
2. GB/T 11919-2014《工业用插头插座和耦合器第2 部分:带插销和插套的电器附件的尺寸兼容性要求》:该标准规定了带插销和插套的电器附件的尺寸兼容性要求,以确保不同制造商生产的水密接插件能够相互配合使用。
3. GB/T 24976.1-2010《电器附件环境设计导则第1 部分:总则》:该标准规定了电器附件环境设计的一般原则和要求,包括环境因素的识别、环境适应性设计、环境试验等方面的要求。
4. GB/T 24976.2-2010《电器附件环境设计导则第2 部分:连接器和插头插座》:该标准规定了连接器和插头插座的环境设计要求,包括材料选择、结构设计、防护等级等方面的要求。
这些标准可以帮助确保水密接插件的质量和可靠性,以满足在潮湿或水下环境中使用的要求。
具体的检验标准可能会因产品类型、应用环境和客户要求而有所不同,建议在选择和使用水密接插件时参考相关的国家标准和行业标准,并按照标准要求进行检验和测试。
DIP(插件)-外观检验标准
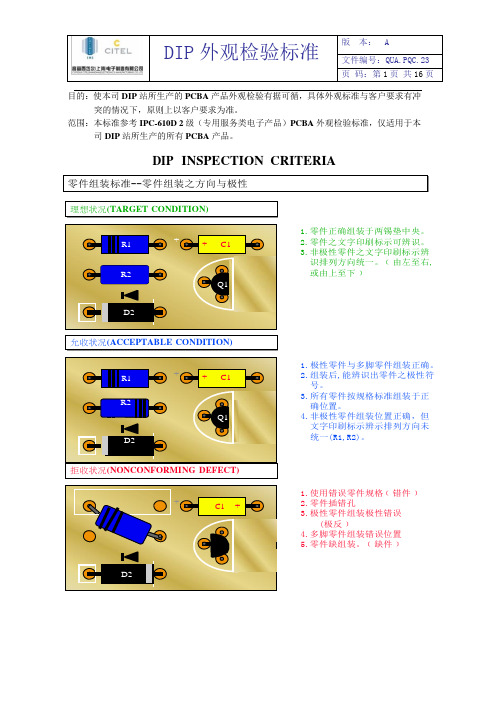
目的:使本司 DIP 站所生产的 PCBA 产品外观检验有据可循,具体外观标准与客户要求有冲突的情况下,原则上以客户要求为准。
范围:本标准参考 IPC-610D 2 级(专用服务类电子产品)PCBA 外观检验标准,仅适用于本司 DIP 站所生产的所有 PCBA 产品。
DIP INSPECTION CRITERIAQ11.零件正确组装于两锡垫中央。
2.零件之文字印刷标示可辨识。
3.非极性零件之文字印刷标示辨 识排列方向统一。
﹝由左至右, 或由上至下﹞Q11.极性零件与多脚零件组装正确。
2.组装后,能辨识出零件之极性符 号。
3.所有零件按规格标准组装于正 确位置。
4.非极性零件组装位置正确,但 文字印刷标示辨示排列方向未 统一(R1,R2)。
1.使用错误零件规格﹝错件﹞2.零件插错孔3.极性零件组装极性错误(极反﹞4.多脚零件组装错误位置5.零件缺组装。
﹝缺件﹞DIP INSPECTION CRITERIA1. 无极性零件之文字标示辨识由上至下。
2. 极性文字标示清晰。
1. 極性零件組裝於正確位置。
2. 可辨識出文字標示與極性。
1.极性零件组装极性错误。
(极反)2.无法辨识零件文字标示。
CONDITION)DIP INSPECTION CRITERIA1. 插件之零件若于焊锡后有浮高或倾斜,须符合零件脚长度标 准。
2. 零件脚长度 L 计算方式 :需从PCB 沾锡面为衡量基准,可目 视零件脚出锡面为基准。
CONDITION)1. 不须剪脚之零件脚长度,目视零件脚露出锡面。
2. Lmin 长度下限标准,为可目视零件脚出锡面为基准, Lmax 零件脚最长长度低于 2.0mm 判定允收。
L零件腳出錫面L零件腳未出錫面1. 无法目视零件脚露出锡面。
2. Lmin 长度下限标准,为可目视零件脚未出锡面,Lmax 零 件脚最长之长度>2.0mm-判 定拒收。
3. 零件脚折脚、未入孔、未出孔、缺件等缺点,判定拒收。
AI插件外观检验标准

本页修改序号:00AI组件外观检验规范页 码: 11 主题内容及适用范围1.1 主题内容本检验规定了PCBA自动插件品质检检细则1.2 适用范围本检验适用于PCBA类产品的AI部分2 相关标准IPC-A-610C-2000《电子组件的接受条件》(Acceptability of Electronic Assemblies) SJ/T 10666 - 1995《表面组装组件的焊点质量评定》SJ/T 10670 - 1995《表面组装工艺通用技术要求》相关产品的工艺文件3 品质判定3.1 轻微缺陷“轻微缺陷”是指与组件装联的理想状况有差异,但不影响该组件在外观、装联配合、机械电气性能方 面使用的一种情形。
3.2 轻缺陷(MI)“轻缺陷(MI)”是指与组件装联标准有差异,可能会对该组件的外观、装联配合、机械电气性能等方 面有所影响的一种情形。
3.3 重缺陷(MA)“重缺陷(MA)”是指不符合组件装联标准,对该组件的外观、装联配合、机械电气性能存在重大品质 隐患的一种情形。
4 处理方式4.1 让步接受在保证品质及可靠性前提下,对组件有条件的限制使用,并由QC负责品质追踪。
在必要情况下以《品质异常联络单》方式,会签相关责任人判定。
4.2 重工依《AI组件外观检验规范》对轻缺陷(MI)品进行重工或更换。
4.3 报废重缺陷不能使用,予以报废处理。
5 AI 组件外观检验规范品质判定:重缺陷(MA)处理方式:重工损伤部分超过跳线1/3直径,全部更换。
品质判定:轻缺陷(MI)处理方式:让步接受轻微损伤或损伤部分小于1/3直径,可不予更换。
品质判定:轻缺陷(MI)处理方式:重工跳线弧度H >1.0mm,须重工。
5.3 元件弧度偏高缺陷类型图示QC检验规范5.1 元件扭曲品质判定: 轻缺陷(MI)处理方式:1、 重工整批性、整板、下板弯脚不符跳线自插规格。
2、 让步接受不定点、个别点位、下板弯脚OK。
卧式元件5.2 元件损伤本页修改序号:00AI 组件外观检验规范页 码:25.1扭曲5.2.1损伤5.2.2 损伤5.3.1 跳线弧度H5.3.1 弧度偏高品质判定:轻缺陷(MI)处理方式:1、 重工整批性脚长>2.0mm±0.5mm,且易造成元件短路。
(新人培训)电子元器件插件工艺检验标准

元件插件工艺及检测标准一、目的:使LED电源PCB板组装(PCBA)工作人员掌握基本的电子元件操作工艺;规范电子元件在PCBA上的插件/焊锡等操作要求, 并为PCBA检验提供检查标准二、范围:适用于本公司PCBA(LED电源PCB的插件/焊锡)的工艺操作和检查。
三、参考文件:工艺要求参照: IPC-A-610B (Class Ⅱ)四、定义:PCBA: Printed Circuit Board Assembly (印刷线路板组装)AX: (轴向)RD: Radial (径向)HT: Horizontal (卧式)VT: Vertical (立式)SMT: Surface Mount Technology (表面安装技术)SMD: Surface Mount Device (表面安装元件)SMC: Surface Mounting Components (表面安装零件)SIP: Simple in-line package 单列直插式封装SOJ: Small Outline J-lead package (具有J型引线的小外形封装) SOP: Small Outline package (小外形封装)SOT: Small Outline Transistor (小外形晶体管)IC: Integrated Circuit (集成电路)PR: Preferred (最佳)AC: Acceptable (可接受的)RE: Reject (拒收)五、元件类别:电阻, 电容, 电感, 二极管, 三极管, IC, IC Socket, 晶体, 整流器, 蜂鸣器, 插头, 插针, PCB, 磁珠等, 在此文件中, 根据本公司情况暂时定义电阻, 电容, 电感, 二极管, 三极管,MOS管工艺标准六、元件插件工艺及检测标准1.卧式(HT) 插元件卧式插元件主要是小功率, 低容量, 低电压的电阻, 电容, 电感, Jumper(跳线), 二极管, IC等, PCBA上的组装工艺要求和接收标准如下:1.1元件在基板上的高度和斜度1.1.1轴向(AX)元件1.1.1.1功率小于1W的电阻, 电容(低电压, 小容量的陶瓷材料), 电感, 二极管, IC等元件PR: 元件体平行于PCB板面且紧贴PCB板面, 如图示:AC: 元件体与PCB表面之间最大倾斜距离(D)不大于3mm, 元件体与PCB表面最低距离(d)不大于0.7mm, 如图示:RE: 元件体与PCB板面距离D>3mm, 或d>0.7mm1.1.1.2耗散功率大于或等于1W的元件PR: 元件体平行于PCB板面且与PCB板面之间的距离D≥1.5mm, 如图示:AC: 元件体与PCB板面之间的距离D≥1.5mm, 元件体与PCB板面的平行不作要求RE: 元件体与PCB板面之间的距离D≤1.5mm1.1.1.3 ICPR: 元件体平行于PCB, IC引脚全部插入焊盘中, 引脚突出PCB面1.mm, 倾斜度=0, 如图示:AC: IC引脚全部插入焊盘中, 引脚突出PCB面大于0.5mm, 如图:RE: IC引脚突出PCB面小于0.5mm, 或看不见元件引脚, 如图:1.1.2径向(RD)元件(电容, 晶振)PR: 元件体平贴于PCB板面, 如图示:AC: 元件脚最少有一边贴紧PCB板面, 如图示:RE: 元件体未接触PCB板面, 如图示:1.2元件的方向性与基板对应符号的关系:1.2.1 轴向(AX) 无极性元件(电阻, 电感, 小陶瓷电容等)PR: 元件插在基板中心标记且元件标记清晰可见, 元件标记方向一致(从左到右, 从上到下), 如图:AC: 元件标记要求清晰, 但方向可不一致, 如图:RE: 元件标记不清楚或插错孔位, 如图:1.2.2 轴向(AX) 有极性元件, 如二几管, 电解电容等PR: 元件的引脚插在对应的极性脚位, 元件标记清晰可看见, 如图:AC: 元件的引脚必须插在相应的极性脚位上, 元件标记可看见, 如图:RE: 元件的引脚未按照极性方向插在相应的脚位上, 如图:1.3元件引脚成形与曲脚1.3.1引脚成形PR: 元件体或引脚保护层到弯曲处之间的距离L>0.8mm, 或元件脚直径弯曲处无损伤, 如图:AC: 元件脚弯曲半径( R )符合以下要求:元件脚直径或厚度( D/T ) 半径( R )≤0.8mm 1 X D0.8~1.2mm 1.5 X D≥1.2mm 2 X DRE: ( 1 ) 元件体与引脚保护弯曲处之间L<0.8mm, 且弯曲处有损伤, 如图: ( 2 ) 或元件脚弯曲内径R小于元件直径, 如图:1.3.2屈脚PR: 元件屈脚平行于相连接的导体, 如图:AC: 屈脚与相间的裸露导体之间距离(H) 大于两条非共通导体间的最小电气间距, 如图:RE: 屈脚与相间的裸露导体之间距离(H) 大于两条非共通导体间的最小电气间距, 如图:1.4元件损伤程度1.4.1元件引脚的损伤PR: 元件引脚无任何损伤, 弯脚处光滑完好, 元件表面标记清晰可见, 如图:AC: 元件引脚不规则弯曲或引脚露铜,但元件或部品引脚损伤程度小于该引脚直径的10%,如图:RE: ( 1 )元件引脚受损大于元件引脚直径的10%,如图:( 2 )严重凹痕锯齿痕,导致元件脚缩小超过元件的10%,如图:1.4.2 IC元件的损伤PR: IC 元件无任何损伤, 如图:AC: 元件表面受损, 但未露密封的玻璃, 如图:RE: 元件表面受损并露出密封的玻璃, 如图:1.4.3轴向(AX)元件损伤PR: 元件表面无任何损伤,如图:AC: 元件表面无明显损伤,元件金属成份无暴露,如图:RE:( 1 )元件面有明显损伤且绝缘封装破裂露出金属成份或元件严重变形,如图:( 2 ) 对于玻璃封装元件,不允许出现小块玻璃脱落或损伤.1.5元件体斜度PR: 元件体与其在基板上两插孔位组成的连线或元件体在基板上的边框线完全平行,无斜度,如图:AC: 元件体与其在基板上两插孔位组成的连线或元件体在基板上的边框线斜度≤1.0mm,如图:RE: 元件体与其在基板上两插孔位组成的连线或元件体在基上的边框线斜度>1.0mm,如图:2. 立式(VT) 插元件2.1.1 轴向(AX) 元件PR: 元件体与PCB板面之间的高度H在0.4mm-1.5mm之间, 且元件体垂直于PCB板面, 如图:AC: H在0.4-3mm之间, 倾斜Q<15°,如图:RE: 元件体与PCB板面倾斜, 且间距H<0.4mm或H>3mm或Q>15°.2.1.2径向(RD)元件2.1.2.1引脚无封装元件PR: 元件体引脚面平行于PCB板面, 元件引脚垂直于PCB板面, 且元件体与PCB板面间距离为0.25-2.0mm, 如图:AC: 元件体与PCB板面斜倾度Q小于15°, 元件体与PCB板面之间的间隙H在0.20-2.0mm之间, 三极管离板面高度最高大于4.0mm, 如图:RE: 元件与PCB板面斜倾角Q>15°或元件体与PCB板面的间隙H>2.0mm或三极管>4.0mm.2.1.2.2:引脚有封装元件PR: 元件垂直PCB板面, 能明显看到封装与元件面焊点间有距离, 如图:AC: 元件质量小于10g且引脚封装刚好触及焊孔且在焊孔中不受力, 而焊点面的引脚焊锡良好(单面板), 且该元件在电路中的受电压<240VAC或DC, 如图:RE: 引脚封装完全插入焊孔中, 且焊点面焊锡不好, 可看见引脚封装料, 如图:2.2元件的方向性与基板符号的对应关系2.2.1轴向(AX)元件PR: 元件引脚插入基板时,引脚极性与基板符号极性完全吻合一致,且正极一般在元件插入基板时的上部,负极在下部,如图:AC: 元件引脚插入基板时,引脚极性与基板符号极性吻合一致,但元件在插入基板时,正极在上和负极在下不作要求,如图:RE: 元件引脚插入基板时,引脚极性与基板符号极性刚好相反,如图:2.2.2径向(RD)元件AC: 元件引脚极性与基板符号极性一致,如图:RE: 元件体引脚极性与基板符号极性相反,如图:2.3元件引脚的紧张度PR: 元件引脚与元件体主轴之间夹角为0°(即引脚与元件主轴平行, 垂直于PCB板面), 如图:AC: 元件引脚与元件体主轴袒闪角Q<15°,如图:RE: 元件引脚与元件体主轴之间夹角Q>15°.2.4元件引脚的电气保护在PCBA板上有些元件要有特殊的电气保护,则通常使用胶套,管或热缩管来保护电路PR: 元件引脚弯曲部分有保护套,垂直或水平部分如跨过导体需有保护套且保护套距离插孔之间距离A为1.0mm-2.0mm,如图:AC: 保护套可起到防止短路作用, 引脚上无保护套时, 引脚所跨过的导体之间的距离B≥0.5mm, 如图:RE: 保护套损坏或A>2.0mm时, 不能起到防止短路作用或引脚上无保护套时, 或引脚所跨过的导体之间距离B<0.5mm,如图:2.5元件间的距离PR: 在PCBA板上,两个或以上踝露金属元件间的距离要D≥2.0mm,如图:AC: 在PCBA板上, 两个或以上踝露金属元件的距离最小D≥1.6mm, 如图:RE: 在PCBA板上, 两个或以上踝露金属元件间的距离D<1.6mm, 如图:2.6元件的损伤PR: 元件表面无任何损伤,且标记清晰可见,如图:AC: 元件表面有轻微的抓、擦、刮伤等,但未露出元件基本面或有效面,如图:RE: 元件面受损并露出元件基本面或有效面积,如图:3. 插式元件焊锡点工艺及检查标准3.1单面板焊锡点单面板焊锡点对于插式元件有两种情形:a. 元件插入基板后需曲脚的焊锡点b. 元件插入基板后无需曲脚(直脚) 的焊锡点3.1.1标准焊锡点之外观特点A. 焊锡与铜片, 焊接面, 元件引脚完全融洽在一起, 且可明显看见元件脚B. 锡点表面光滑, 细腻, 发亮C. 焊锡将整个铜片焊接面完全覆盖, 焊锡与基板面角度Q<90°, 标准焊锡点如图示:3.1.2可接受标准A.多锡焊接时由于焊锡量使用太多,使零件脚及铜片焊接面均被焊锡覆盖着,使整个锡点象球型,元件脚不能看到.AC: 焊锡点虽然肥大Q>90°,但焊锡与元件脚,铜片焊接面焊接良好,焊锡与元件脚,铜片焊接面完全融洽在一起,如图:RE: 焊锡与元件引脚, 铜片焊接状况差, 焊锡与元件脚/铜片焊接面不能完全融洽在一起, 且中间有极小的间隙, 元件引脚不能看到, 且Q>90°, 如图:B.上锡不足(少锡)焊锡、元件引脚、铜片焊接面在上锡过程中,由于焊锡量太少,或焊锡温度及其它方面原因等造成的少锡.AC: 整个焊锡点, 焊锡覆盖铜片焊接面≥75%, 元件脚四周完全上锡, 且上锡良好, 如图:RE: 整个焊锡点, 焊锡不能完全覆盖铜片焊接面<75%, 元件四周亦不能完全上锡, 锡与元件脚接面有极小的间隙, 如图:C.锡尖AC: 焊锡点锡尖, 只要该锡尖的高度或长度h<1.0mm, 而焊锡本身与元件脚、铜片焊接面焊接良好, 如图:RE: 焊锡点锡尖高度或长度h≥1.0mm, 且焊锡与元件脚、铜片焊接面焊接不好, 如图:D. 气孔AC: 焊锡与元件脚、铜片焊接面焊接良好, 锡点面仅有一个气孔且气孔要小于该元件脚的一半, 或孔深<0.2mm, 且不是通孔, 只是焊锡点面上有气孔, 该气孔没有通到焊接面上, 如图:RE: 焊锡点有两个或以上气孔, 或气孔是通孔, 或气孔大于该元件脚半径, 如图:D.起铜皮AC: 焊锡与元件脚、铜片焊接面焊接良好, 但铜皮有翻起h<0.1mm,且铜皮翻起小于整个Pad位的30%, 如图:RE: 焊锡与元件脚、铜片焊接面焊接一般, 但铜皮翻起h>0.1mm, 且翻起面占整个Pad位的的30%以上, 如图:E.焊锡点高度对焊锡点元件脚在基板上的高度要求以保证焊接点有足够的机械强度AC: 元件脚在基板上高度0.5<h≤2.0mm, 焊锡与元件脚, 铜片焊接面焊接良好, 元件脚在焊点中可明显看见, 如图:RE: 元件脚在基板上的高度h<0.5mm或h>2.0mm, 造成整个锡点为少锡, 不露元件脚, 多锡或大锡点等不良现象, 如图:注:对用于固定零件之插脚如变压器或接线端子之插脚高度可接受2.5mm为限.3.1.3不可接受的缺陷焊锡点在基板焊锡点中有些不良锡点绝对不可接收, 现列举部分如下RE: ( 1 ) 冷焊(假焊/虚焊)如图:( 2 ) 焊桥(短路),锡桥,连焊,如图:( 3 ) 溅锡, 如图:( 4 ) 锡球, 锡渣, 脚碎, 如图: ( 5 ) 豆腐渣, 焊锡点粗糙, 如图: ( 6 ) 多层锡, 如图:( 7 )开孔(针孔),如图:3.2双面板焊锡点双面板焊锡点同单面板焊锡点相比有许多的不同点:a. 双面板之PAD位面积较小(即外露铜片焊接面积)b. 双面板每一个焊点PAD位都是镀铜通孔鉴于此两点, 双面板焊锡点在插元件焊接过程及维修过程就会有更高要求, 其焊锡点工艺检查标准就更高, 下面将分别详细讨论双面板之焊锡点收货标准3.2.1标准焊锡点之外观特点A. 焊锡与元件脚, 通孔铜片焊接面完全融洽在一起, 且焊点面元件脚明显可见.B. 元件面和焊点面的焊锡点表面光滑, 细腻, 发亮.C. 焊锡将两面的Pad位及通孔内面100%覆盖, 且锡点与板面角度Q<90°, 如图:3.2.2可接收标准A.多锡焊接时由于焊锡量过多, 使元件脚, 通孔, 铜片焊接面完全覆盖,不是使焊接时的两面元件脚焊点肥大, 焊锡过高AC: 焊锡点元件面引脚焊锡虽然过多, 但焊锡与元件脚, 通孔铜片焊接面两面均焊接良好, 且Q<90°, 如图:RE: 焊锡点元件面引脚肥大, 锡点面引脚锡点肥大, 不能看见元件脚且焊锡与元件脚, 铜片焊接面焊接不良, 如图:B. 上锡不良AC: 焊锡与元件脚, 通孔铜片焊接面焊接良好, 且焊接锡在通孔铜片内的上锡量高度h>75%·T (T: 基板厚度), 从焊点面看上锡程度大于覆盖元件脚四周(360°)铜片的270°, 或从元件面能清楚的看到通孔铜片中的焊锡, 如图:RE: 从焊点面看, 不能清晰的看到元件引脚和通孔铜片焊接面中的焊锡或在通孔铜片焊接面完全无焊锡或元件引脚到Pad位无焊锡或h<75%·T或上锡角度Q<270°(针对Solder Pad 360°而言), 如左图:C. 锡尖在焊接过程中由于焊锡温度过低或焊接时间过长等原因造成的锡尖AC: 焊锡点的锡尖高度或长度h<1.0mm, 而焊锡本身与元件引脚及通孔铜片焊接面焊接良好, Q<90°, 如图:RE: 焊锡点锡尖高度或长度h≥1.0mm, 且焊锡与元件引脚, 通孔铜片焊接面焊接不良, 如图:D. 气孔AC: 焊锡与元件脚, 铜片焊接面焊接良好, 锡点面仅有一个气孔且气孔要小于该元件脚的1/2, 且不是通孔(只是焊锡点表面有气孔, 未通到焊接面上), 如图:RE: 焊锡点上有两个或以上气孔, 或气孔是通孔, 或气孔大于该元件脚直径的1/2, 焊点面亦粗糙, 如图:E. 起铜皮AC: 焊锡点与元件脚, 通孔铜片焊接面焊接良好, 但铜皮翘起高度h<0.1mm, 翘起面积S<30%·F (F为整个焊盘的面积)RE: 焊锡与元件脚, 通孔铜片焊接面焊接质量一般, 但铜皮翘起h>0.1mm, 且翘起面积S>30%·F (F为整个焊盘的面积), 如图:F. 焊接点高度PR: 元件脚在焊锡点中明显可见, 引脚露出高度h=0.1mm, 且焊锡与元件脚, 通孔铜片焊接面焊接良好, 如图:AC: 元件脚露出基板的高度0.5mm<h≤2.0mm, 元件脚在焊锡点中可明显看见, 且焊锡与元件脚, 通孔铜片焊接面焊接良好. (但对于通孔铜片焊接面的双面PCB板, 基板厚度T>2.3mm, 则元件脚露出基板高度可接收0<h≤0.5mm), 如图:RE: 元件脚露出基板高度h<0.5mm或h>2.0mm (仅对于厚度T≤2.3mm 的双面板), 造成整个锡点为少锡, 不露元件脚, 多锡或大锡点等不良现象, 且焊接不良, 如图:3.2.3 不可接收的缺陷焊锡点:在双面板(镀铜通孔铜片焊接面)焊锡点中, 有些不良焊点绝对不可接收, 其不可接收程度完全同于单面板, 详细请参考3.1.3。
自动插件机用机插工艺规范

自动插件机用机插工艺规范为进一步提高机插率,达到提效的目的,重新修订了自动插件机用机插工艺规范,自动插件机用机插工艺规范是根据公司已有机插设备的技术规格书拟制的基本技术要求,是专业排版、工艺、质量、认定等部门必须的技术规范,随着技术的更新换代,本规范会出现遗漏和不足之处,希望大家提出宝贵意见并改进之(注:原普通插件机用机插工艺规范、异型插件机用机插工艺规范同时作废,并停止使用)。
1、PCB外形及尺寸要求:[1] 为适应设备线体传动的要求,印制板四角必须倒圆角,R≥2mm;[2] 印制板尺寸必须满足以下条件:设备允许范围长(L)*宽(W)最小尺寸:102mm*80mm;最大尺寸483mm*406mm:为了适应我公司生产线体的要求以及提高机插效率的要求,对于主板和副板拼板的尺寸要求:长(L)*宽(W)最小尺寸:200mm*150mm;最大尺寸400mm*300mm:最佳尺寸330mm*247mm;2、定位孔[1] 用于机插定位的定位孔主要有5个孔,其中三个虚线孔可去掉,如PCB右下角元器件较为密集,则右下角的虚线椭圆孔必须添加,30mm<L1<50mm;[2] 定位孔的尺寸如上图所示,其中A=5mm±0.1mm;[3] 定位孔8mm的范围内应没有焊盘、元器件及走线;丝印标识除外;定位孔周边直径2.5mm范围图一:印制版(机插)定位孔及外型尺寸示意图3、工艺边及工艺夹持边的设计[1] 工艺边夹持边指在生产过程中设备及工装需要夹持的PCB 的边缘部分。
[2] 元器件与板边的最小间距为A=5mm ,焊盘与板边的最小间距为4mm ;边缘铜箔不得小于1mm ,如此条件无法保证时,则要增加工艺边来保证PCB 有足够的可夹持边缘。
[4] 另外增加工艺夹持边将降低PCB 的挠度,且提高成本,设计布板应尽量不采用。
[5] 需要机插的PCB ,机插定位孔可以加在增加的工艺夹持边上,工艺夹持边的宽度不仅要满足夹持需要,还要满足机插定位孔的排布需要。
pw操作说明书
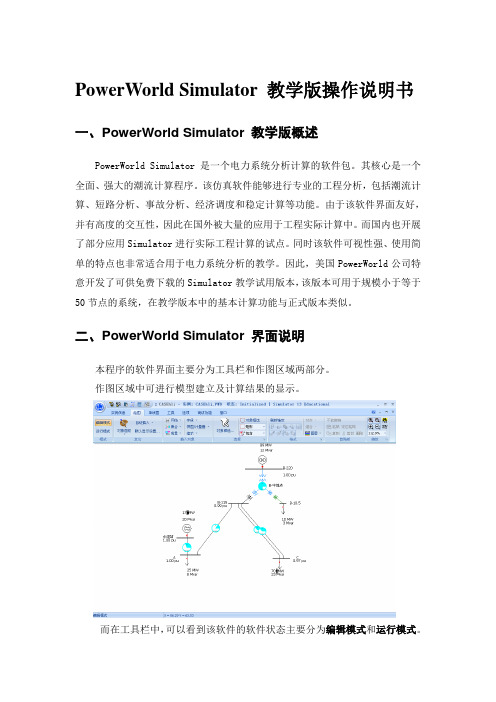
PowerWorld Simulator 教学版操作说明书一、PowerWorld Simulator 教学版概述PowerWorld Simulator是一个电力系统分析计算的软件包。
其核心是一个全面、强大的潮流计算程序。
该仿真软件能够进行专业的工程分析,包括潮流计算、短路分析、事故分析、经济调度和稳定计算等功能。
由于该软件界面友好,并有高度的交互性,因此在国外被大量的应用于工程实际计算中。
而国内也开展了部分应用Simulator进行实际工程计算的试点。
同时该软件可视性强、使用简单的特点也非常适合用于电力系统分析的教学。
因此,美国PowerWorld公司特意开发了可供免费下载的Simulator教学试用版本,该版本可用于规模小于等于50节点的系统,在教学版本中的基本计算功能与正式版本类似。
二、PowerWorld Simulator 界面说明本程序的软件界面主要分为工具栏和作图区域两部分。
作图区域中可进行模型建立及计算结果的显示。
而在工具栏中,可以看到该软件的软件状态主要分为编辑模式和运行模式。
编辑模式用于建模和修改模型,运行模式则供已建的模型上开展不同的电力系统分析。
在使用该软件的任何时候都可以点击工具栏上的编辑模式按钮和运行模式按钮进行两种模式之间的切换。
从横向上看,工具栏主要分为实例信息、绘图、单线图、工具、选项、高级功能和窗口等7个标签页。
●实例信息:主要用于引导和查看用户模型的所有信息。
该标签页中的功能在编辑模式和运行模式中均会用到。
●绘图:主要用于绘制单线图或编辑已有的单线图,通过添加、移动、格式化、或调整已有单线图对象。
该标签页中的功能仅用于编辑模式。
●单线图:主要在用户创建单线图后使用。
该功能区提供定制用户单线图外观风格。
●选项:该功能区的所有按钮从其它功能区都可访问到,这个功能区把所有的选项都放在一个地方。
●工具:这个功能区可访问到PowerWorld Simulator基础包所有分析工具。
插件标准规范

三、插件要点:
1.根据电路板元件丝印图,按照插件次序将元件插入电路板中;
2.电路板若是双面板的,插件时要注意分清元件是从丝印面或是从非丝印面插入;
3.电路若是有两种或以上工作方式,插件时要注意分清各种电路的元件参数及其分布图;
4.小元件可以贴近电路板安装,功率大的电阻应距离电路板7~10 mm,发热量较大的元器件如三端稳压块等按需要安装散热器,电阻的高度应一致及色环方向应一致;
5.注意有极性的元器件(如:二极管、电解电容等)和有方向的元器件(如IC、排阻、插座等),插件时不得搞错其极性和方向;电解电容的长脚一般为正极,外壳都标有“-”为负极;IC脚一般按逆时针数起(第一脚通常是方形焊盘);
6.数码管和发光块两者的元件面必须在同一高度;
二极管符号如下:电解电容符号如下:
+ -
集成电路(即IC)符号如下:三端稳压块符号如下:
四、插件检验要求:
1.对电路板组件所用的元器件进行检查:
A.检查电阻的位置是否正确;
B.检查电解电容的极性及位置是否正确;
C.检查二极管的极性及其位置是否正确;
D.检查桥堆的方向是否正确;
E.检查IC的方向是否正确;
F.检查数码管方向是否正确。
2.检查元件有无明显的挤压应力;
版本
更改内容
生效日期
A/0
2010-7-15
编制/日期:
审核/日期:
批准/日期:
会签记录:
部门会签状态ຫໍສະໝຸດ 部门会签状态分发单位:
■检测中心
文件控制印章
一、适用范围:
适用于一般的手工插件作业,工艺资料如果有特别要求的按工艺资料的要求。
二、插件次序:
- 1、下载文档前请自行甄别文档内容的完整性,平台不提供额外的编辑、内容补充、找答案等附加服务。
- 2、"仅部分预览"的文档,不可在线预览部分如存在完整性等问题,可反馈申请退款(可完整预览的文档不适用该条件!)。
- 3、如文档侵犯您的权益,请联系客服反馈,我们会尽快为您处理(人工客服工作时间:9:00-18:30)。
自動插件PCB設計參考及檢查標準
一〃AI用PCB要求:
現AI部擁有UNIVERSAL插件機,為了使現時自動插件機發揮最大效率,提高產品品質,我們整理和制訂了這份資料,供AI用PWB設計參考。
(一). PCB尺寸要求:
最大尺寸: 508mm(長) × 470mm(寬)。
(457.2mm(長) × 300mm(寬)已考慮錫爐爐膽最大寬度)
(二).PWB定位孔要求:根據PWB長度L的範圍,插件機對於鵝蛋形定位孔距
PWB邊緣的距離
注意:圓形定位孔為固定的標準位置,鵝蛋形定位孔應根據PWB長度L的不同而其S2 也有所改變,
有關資料請參照下表:
另外,當PWB定位孔過多,生產時容易造成PWB取放板方向混淆。
故設計PWB時,只須在該PWB長邊上設計一組定位孔(左邊圓形定位孔+右邊鵝蛋形定位孔)。
(三). 自動插件機元件引腳直徑範圍為: 0.38mm-0.81mm
因此,自動插件機可插以下元件:
1. 1/16W、1/8W、1/4W 電阻
2. 色環電容
3. 0.6mm跳線
4. 二極體
5. 色環電感
(四). Universal 臥式插件機元件跨度C的範圍: 5.0mm-20.0mm
UNIVERSAL JUMPER WIRE 機跨度C的範圍:5.0mm
—33.0mm
UNIVERSAL插件機的跨度是連續可變的;因此不再要求元件跨度C設計成5. 0mm、7.5mm等統一尺寸。
設計元件跨度必須同時考慮到元件體長度L,如果L過長,插件機容易打傷元件體或打斷元件引腳,損壞插件機刀具,同時對排料機要求非常嚴格。
如果跨度C過大,插件機速度會降低,插件時易掉件(插件機刀具夾不牢)、元件易浮腳。
目前AI部插件最多的是5.0mm跨度,5.0mm跨度的元件在插件時比較容易出現拱起、損傷元件
等壞機;故建議將AI插件元件的最小跨度定為6.0mm,以求大幅度降低壞件率。
根據不同元件,我們定出以下標準:
最小跨度的推算:一般元件=MAX L+1.3mm
二極體、色環電感=MAX L+2.8mm
(五). 元件孔徑要求:
現時PWB 供應商工藝品質控制不是很好,如果再加上元件孔徑過小,就不符合插件機的插件要求,那將會極大的增加AI 插件的壞件率,需要增加大量人手去彌補(檢查員檢查和補件)。
但是,如果元件孔徑過大,又將會導致元件過松容易脫落(過波峰焊前),且會產生錫點不良等品質問題。
自插機要求:MIN D = MAX d + 0.45mm
考慮以上情況,我們確定如下資料:
注意:以上孔徑對於手插元件可能過大,故請參考第三、第四、第六、第九、第十點, 分清哪些元件是手插件,以便單獨對手插件的孔徑採用不同的標準。
(六). 元件密度要求:
PWB 上元件密度越大,自插機走位越小,因此效率越高。
但是,元件密度過大插件時會打傷打斷鄰近元件,損壞刀具。
下圖是插件機能夠接受的最大密度:
(七)
. 元件銅皮設計:
自插機插件時,一直存在如下問題:
1.元件角度過大,容易掉件和產生浮腳
2.元件角度過小,容易和相鄰銅皮短路 `
a
a過大,易掉件和浮腳 a過小,易和
相鄰的銅皮短路
為徹底解決以上問題,建議EG 設計PWB 時,採用以下方法:
(八). PWB 變形允許範圍:
(十). 同一型號PWB ,元件孔座標(相對于定位孔中心)誤差不大於0.05mm 。
要求:x 、y 的誤差不大於0.05mm 。
(十一).PWB之間板與板連接位的要求:
板與板之間的連接位元如為針孔連接方式,則需保證連接強度可靠。
如為“V”
形槽連接,“V”形槽的尺寸請參照下圖:
D
D1=D2=1/4 D
(十二).同一廠家生產的同一PWB,要求材料相同,而且材料方向一致。
不同的PWB材料,以及同一材料的不同方向,溫度變化時,膨脹率和收縮率有很大差異,將導致定位孔和元件孔的尺寸、座標差別太大,自插機無法接受。
二〃SMT用PWB和物料要求:
現AI部為了使現有設備發揮最大效率,提高產品品質,我們整理和制訂了這份資料,供PWB設計參考。
理想的SMT PWB外形圖示
(一). PWB外形尺寸(L,W,H):
(二).Mark Point要求(a,b,c,d):
(1)PWB的Mark Point應有對角的2個或兩個以上;
(2)若為拼板(Block),則每個拼板(Block)上應有兩個或兩個以上對角的
Mark Point;
(3)Mark Point應在距PWB中心位置的直線最遠;
(4)Mark Point位置要求:離PWB板邊垂直距離應大於3mm;
(5)Mark Point外形應規則圓形或方形;要求為相同規則的圖形;
(6)對角位置Mark Point之X方向應不相同,即Xa≠Xd,Xb≠Xc;而對其Y方
向則沒有相類似要求;
(三).對板邊或離板邊最近的元件要求(W1,W2):
PWB板邊或離板邊最近的元件(W1,W2)離PWB板邊的垂直距離應大於5mm;
(四).PWB外形要求:
(1)PWB之W方向兩邊不應都為曲面或存在較大缺口;若有,則應設計邊接板邊;
(2)PWB之L方向兩邊應為直線,否則應通過設計連接板邊來達成;
(五). SMT物料要求:
(1)最大尺寸和最小尺寸應視貴司的貼片機的參數而定。
(2)最大高度應視貴司的貼片機的參數而定。