PCB吸潮爆板问题研究
PCB回流后出现爆板分层失效分析

PCB回流后出现爆板分层失效分析1.设计问题:PCB设计时,如果在板子上的高温区域没有经过适当的隔离或散热设计,就可能在回流过程中产生过多的热量导致分层失效。
此外,如果板子上的器件密度太高,导致局部区域导热不良,也会导致分层失效。
2.PCB材料问题:PCB材料中的玻璃纤维布和树脂会随着高温的作用而膨胀,如果PCB的设计和制造过程中没有考虑到热胀冷缩的因素,就可能导致分层失效。
此外,如果PCB中使用的材料质量不佳或者存放时间过长,也会导致分层失效。
3.制造工艺问题:PCB的回流过程中需要经历高温高压的环境,如果工艺控制不好,如回流时间过长、温控不准确等,就可能导致分层失效。
此外,如果回流过程中的机械振动过大,也会导致PCB的分层失效。
4.焊接材料问题:回流焊接中使用的焊锡材料可能会对PCB的分层造成影响。
例如,焊锡材料的成分与PCB材料相兼容性差,就容易导致分层失效。
此外,焊接过程中使用的流动剂,如果使用过量或者不合适,也会对PCB的分层造成影响。
对于出现爆板分层失效的PCB,以下是一些可能的处理方法和预防措施:1.设计时应考虑合理的散热设计,确保高温区域有良好的散热和隔离措施。
2.在PCB的设计和制造过程中,应考虑玻璃纤维布和树脂的热胀冷缩因素,合理选择和使用材料。
3.在PCB的制造过程中,严格控制回流焊接的工艺参数,确保回流时间和温度的准确控制。
4.对于焊锡材料的选择,应考虑其与PCB材料的兼容性,避免因为焊锡材料导致的分层失效。
5.合理使用流动剂,避免过量使用,以免对PCB的分层造成影响。
总之,PCB回流后出现爆板分层失效的原因可能多种多样,需要从设计、材料、制造工艺等多个方面综合考虑。
只有在每个环节都做好细致的控制和预防措施,才能有效避免爆板分层失效的问题。
PCB爆板不良成因简报

爆板不良成因描述_板內異物導致爆板 爆板不良成因描述 板內異物導致爆板
爆板不良成因描述_板內吸濕導致爆板 爆板不良成因描述 板內吸濕導致爆板
不良原因: 經調查,發現疑似爆板的不良原因為內層吸濕導致爆板,因包裝破 損,使得板子在貨運中吸入過多水氣,導致不良發生。 改善對策: 1.對於氣泡布包裝改為鋁箔包 2.對於現場包裝人員再次宣導,包裝完後需檢查包裝是否破損
爆板不良成因描述_隔紙殘水導致爆板 爆板不良成因描述 隔紙殘水導致爆板
不良原因: 經調查,發現在棕化之後,為了保護板子的表面,會附加一個隔 板將板子與板子間隔開,而疑似隔板清洗過後,未完全乾燥,導 致有水漬反沾,造成棕化面與膠片接著不良,發生爆板。 (次頁附圖) 改善對策: 針對清洗回廠內之隔板,需由迴流線人員負責挑選未乾之隔板, 避免投入使用,針對未乾之隔板,列製表單確認人員確實執行並 簽名。
不良原因: 棕化收板機之作業吸盤固定架螺絲華司墊片,於保養作業拆卸後遺 留於設備機台上,棕化作業生產時台面移動,致使沾有油污之華司 墊片掉落於棕化後板面上,使板面留有華司墊片形狀的油污狀,於 壓合中造成離形效應,而使板面PP與棕化層分層爆板。 改善對策: 1.於現場張貼重點作業指示以提示作業人員注意。 2.於棕化一級保養表增加保養後吸盤台面清理確認。
爆板不良成因報告
爆板不良成因分類
針對爆板不良成因分類如下: 針對爆板不良成因分類如下: 1.油污附著導致爆板 2.隔紙殘水導致爆板 3.板內異物導致爆板 4.板內吸濕導致爆板 5.壓合排氣不良導致氣泡
ቤተ መጻሕፍቲ ባይዱ
以上為CPC廠內曾發生過的不良爆板成因,詳細不良描 述如後。
爆板不良成因描述_油污附著導致爆板 爆板不良成因描述 油污附著導致爆板
PCB爆板的原因 玻璃转换温度的概念

PCB 爆板的原因玻璃转换温度的概念
电子设计是一个系统性的工作,总会遇到一些超过自己认知范围的问题,这就需要不停的学习。
这篇文章就给大家分享一些关于PCB 爆板的原因,以及其中涉及到的玻璃转换温度的概念。
前段时间有一个朋友遇到了一个问题,说是公司做了一批产品出现了爆板的现象。
由于产品的有一些保密性,没有发图片给我看,所以我就给他出了一个主意:找PCB 供应商帮忙找找问题点,毕竟PCB 板厂有一堆的专家在
研究这些问题。
我认为对于爆板的问题无非就是板材的问题或者加工的问题。
后来有点时间就想进一步的了解下爆板的原因,归纳起来有以下一些情况:
1、吸水导致的爆板;如果是吸水导致的爆板,可用烘烤方式去除水份,
防止爆板。
这也是为什幺在SMT 之前,都会先烘烤板子然后再到下一道工序中。
据了解在一般条件下,48 小时就可吸收约70%水分。
2、板材裂化导致的爆板;发生于单一层树脂内,宜提高板材Tg 及Td。
典型PCB爆板的桉例分析
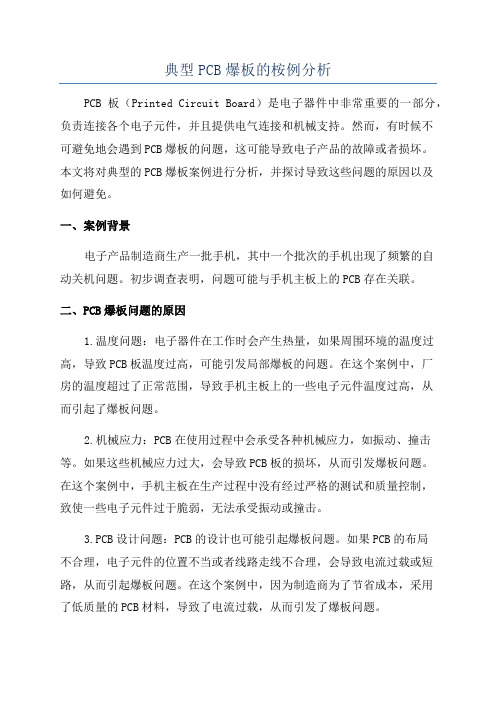
典型PCB爆板的桉例分析PCB板(Printed Circuit Board)是电子器件中非常重要的一部分,负责连接各个电子元件,并且提供电气连接和机械支持。
然而,有时候不可避免地会遇到PCB爆板的问题,这可能导致电子产品的故障或者损坏。
本文将对典型的PCB爆板案例进行分析,并探讨导致这些问题的原因以及如何避免。
一、案例背景电子产品制造商生产一批手机,其中一个批次的手机出现了频繁的自动关机问题。
初步调查表明,问题可能与手机主板上的PCB存在关联。
二、PCB爆板问题的原因1.温度问题:电子器件在工作时会产生热量,如果周围环境的温度过高,导致PCB板温度过高,可能引发局部爆板的问题。
在这个案例中,厂房的温度超过了正常范围,导致手机主板上的一些电子元件温度过高,从而引起了爆板问题。
2.机械应力:PCB在使用过程中会承受各种机械应力,如振动、撞击等。
如果这些机械应力过大,会导致PCB板的损坏,从而引发爆板问题。
在这个案例中,手机主板在生产过程中没有经过严格的测试和质量控制,致使一些电子元件过于脆弱,无法承受振动或撞击。
3.PCB设计问题:PCB的设计也可能引起爆板问题。
如果PCB的布局不合理,电子元件的位置不当或者线路走线不合理,会导致电流过载或短路,从而引起爆板问题。
在这个案例中,因为制造商为了节省成本,采用了低质量的PCB材料,导致了电流过载,从而引发了爆板问题。
三、如何避免PCB爆板问题1.控制温度:在生产过程中,必须确保环境温度处于正常范围内。
此外,可以通过选择合适的散热措施,如散热片、散热风扇等,来降低PCB 板的温度。
2.优化结构:在设计和生产PCB板时,要注意优化结构,确保PCB板能够承受机械应力。
可以采用加固板或者添加缓冲材料等方式来增强PCB 板的机械强度。
3.合理设计:在PCB的设计阶段,应该合理布局电子元件,确保电子元件之间的距离合适,并避免线路走线过于密集。
此外,选择高质量的PCB材料和电子元件也是非常重要的。
爆板原因分析

摘要随着欧盟RoHs法令从2006年7月开始实施,印制电路板装配不得不随之无铅化,传统已使用超过50年的63Sn/37Pb焊接材料被SnAgCu(Sn96.5%/Ag3.0%/Cu0.5%)代替,熔点由原来的187℃提升到21 7℃,相应的焊接温度由220℃~230℃提升到240℃-260℃,印制电路板必须经历熔点以上的焊接时间多出了50多秒,印制电路板吸收热大增,印制电路板必须提高耐热性能与之配合。
在过去的一年中,印制电路板分层问题一直困扰着电路板制造商。
印制板分层的机理是电路板吸热后,不同材料之间产生不同的膨胀系数而形成内应力,如果树脂与树脂,树脂与铜箔的粘接力不足以抵抗这种内应力将产生分层,所以解决分层的思路是:1.生产流程控制尽可能保证板子有最佳的抵抗内应力的能力:2.使用性能优越的材料减少内应力。
文章希望通过研究,在成本和品质双重约束下,找到最佳的解决方案,用最低的成本来解决分层问题。
思路是从研究分层的原因着手,通过实验设计的方法,对分层的因素从材料选择、印制电路板制造过程控制到电路板装配的整个过程,进行系统分析。
本研究项目耗费25万元的试验材料成本,历时三个多月,最终从成本和品质控制,提升公司竞争力的角度,提出解决分层的三套方案。
在将实验结果运用到A公司的实践中后,产生了良好的经济效益,每月减少客诉成本约30万元,减少成本浪费约80万元,取得超过预期效益。
关键词分层;无铅焊接;实验设计:印制电路板1引言1.1研究的背景和意义1.1.1 PCB行业回顾与展望1936年一1940年,英国Paul博士从印刷技术得到启发,首先提出了“印刷电路”的概念,开创了制造印刷电路板的先河。
1967年美国人Beadles.R.L,提出了多层板生产制造工艺(MLB),将印刷电路板推上了更高一层楼。
1984年日本PCB专家项土冢田裕尝试在多层板上采用盲孔结构,HDI技术兴起(High Den sityInterconnection)印制电路板从诞生之日起就依托其互联和承载的功能成为电子产品的航空母舰,任何功能强大的芯片只有集成到印制电路板上,才能展现其威力。
PCB爆板分析教材(pdf 22页)

B界面
內層Cu(無機物)
C界面
D界面
CORE (有機物)
C界面
內層Cu(無機物)
B界面
介電層(有機物)
A界面
F界面
外層Cu(無機物)
界面狀況分析
界面狀況分析: ¾ A界面:外層銅牙與樹脂結合,屬于物理性質+化学結合﹔ ¾ B界面:內層銅黑/棕化面與樹脂結合,屬于物理性質結合(粗糙
度小于銅牙)﹔ ¾ C界面:內層銅牙與CORE的樹脂結合,屬于物理性質+化学結合
棕黑化面本身处理不良,造成结合力不足,如下图所示:
‧ 对于该异常需要加强对板料的清洗,必要时需要以纯水清洗,以保证板面的清洁. ‧ 同时还需要对操作员工进行规范操作培训,以防止对清洗后的板面于操作过程中造成污
染.
爆板原因分析(8)
PP含浸不良或壓合不良,造成玻纖布與樹脂或與玻布經緯紗間分層:
爆板原因分析(13)
PCB严重吸湿后,如果受到强热,材料中的水汽会产生强大的蒸汽压,如果该蒸汽压 所造成的膨胀力大于材料内各个界面的结合力时,则会产生分层,如下说明:
对于防止PCB的吸湿建议如下: PCB的生产过程中应尽量避免存放过久,同时还需要于制做中做必要的烘烤,如钻孔
后烘烤(150度/2小时). 2. 对于PCB成品的包装需要选择透汽率较低的包装材料,建议采用铝箔膜包装.
爆板原因分析(1)
PCB压合后butter core厚度不足,示意图如下:
NG
NG
OK
原理分析: 介电层与内层铜结合主要依靠树脂与棕黑化面的粘结力,玻纤布本身与棕黑
化面没有粘结力.所以,需要足够的树脂层厚度测没法保证良好粘结力. 设计时需要保证butter core(奶油层)厚度以大于0.3MIL(单边)为宜. 压合后玻布厚度参考:
常见PCB爆板的成因与解决方案

常见PCB爆板的成因与解决方案PCB板(Printed Circuit Board)是电子产品的重要组成部分,它承载着各种电子器件和连接电路,起到支持和传输电流、信号的作用。
然而,由于工艺、设计或制造过程中的各种问题,PCB板可能会发生爆板现象,给产品的正常工作和使用带来严重影响。
下面我们将分析常见的PCB爆板成因,并提出相应的解决方案。
首先,PCB爆板的一个常见成因是由于过度应力造成的。
过度应力可能是由于设计不合理、材料选择不当、加工制造过程等原因引起的。
当PCB板上的器件或连接电路在运行中产生热量或受到外力作用时,就会引起板材的膨胀和收缩,从而产生应力。
当应力超过材料的耐力极限时,就会导致板材破裂,出现爆板现象。
解决这个问题的方法可以是改进设计,合理分布布局,减小热量集中度;选择具有较好热传导性质的材料;合理选择和控制加工工艺,避免过度应力。
其次,PCB爆板的另一个常见成因是由于材料问题引起的。
PCB板的材料通常包括基板、导电层、绝缘层等。
如果材料质量不过关,比如基板脆性较大,导电层与绝缘层结合不牢固等,就会导致PCB板容易发生爆板。
解决这个问题的方法可以是选择质量可靠的材料供应商;进行材料检验和质量控制,确保材料符合规范要求;对于出现材料问题的PCB板,及时更换材料。
此外,PCB爆板还可能与设计问题有关。
设计问题包括电路设计、布局设计和堆叠设计等方面。
如果电路设计不合理,信号传输路径设计不合理,或者布局设计中信号线和电源线之间的距离不足等,都容易引发爆板问题。
解决这个问题的方法可以是进行电路仿真和分析,找出设计中的问题;合理布局电路、信号线和电源线,保证安全距离;进行合理的堆叠设计,避免过度叠层导致板材应力过大。
此外,制造过程中的问题也可能导致PCB爆板。
比如,制造过程中的温度控制不准确,过热或过冷都可能引起板材问题;过度机械弯曲、过度挤压等操作也可能导致板材应力过大。
解决这个问题的方法可以是加强制造工艺控制,确保温度在合理范围内;避免过度机械操作,保持适度。
吸潮爆板分析案例pdf

p“无铅化”技术交流
PCB存放3个月以上的性能特征
PCB存放个月后, 经常表现出以下某几种性能特征: • • • 板材的Tg值有所下降, △Tg有所变大 板材的含水率明显增高, 2-3倍于烘板后的结果 板材的热应力大幅度下降, 经常耐不了288℃/10秒一次的热冲出, 烘 板后一般能耐288℃/10秒3次或以上的热冲击。 吸潮导致PCB板耐热性的下降是最明显的特征
360 320 280 240 200 160 120 80 40 0 烘前 烘后 烘前 烘后 烘前 烘后
温度(℃)
1年
2年
2.5年
®
PDF 文件使用 "pdfFactory Pro" 试用版本创建
p“无铅化”技术交流
覆铜板长时间存放性能变化特征
覆铜板长时间存放后的性能特征: • • • 板材的Tg值有所下降, 烘后有明显改善,△Tg能满足≤3℃ 板材的含水率略有提高, 烘前烘后数据相当接近 板材的Td值、耐浸焊极限、T260等指标是稳定的 覆铜板的耐热性并不会随着存放时间的延长而下降
受潮的PCB板能完全修复吗
如果短期内,板材受潮,此时水气还未对分子结构产生直接的破 坏,通过烘板的方法可以将水气去除,板子的耐热性能可以恢复 正常,我们称之为是可逆的受潮。 如果板子受到潮气攻击时间过长,潮气对有机分子结构产生破坏, 此时,烘烤对板子耐热性能的改善空间不大,我们称之为不可逆 的受潮。
®
PDF 文件使用 "pdfFactory Pro" 试用版本创建
p“无铅化”技术交流
不同存放时间覆铜板含水率测试结果分析
含水率测试(TGA)
0.24 百分比(%)
0.16 烘前 烘后 0.08
对PCB进行烘烤的原因

对PCB进行烘烤的原因PCB烘烤的主要目的是去除PCB中含有的或从外界吸收的水分和湿气,因为有些PCB材料容易形成水分子。
另外,PCB生产出来放置一段时间后,也有机会吸收环境中的水分,水是导致PCB爆米花分层的主要杀手之一。
因为当PCB放置在温度超过100℃的环境中,如回流焊炉、波峰焊炉、热风整平或手工焊接时,水会变成水蒸气,然后体积会迅速膨胀。
PCB受热越快,水蒸气膨胀越快。
温度越高,水蒸气的体积越大。
当水蒸气无法立即从PCB中逸出时,很有可能会使PCB膨胀。
尤其是PCB的Z方向最脆弱。
有时,PCB层间的过孔可能会断开,有时,可能会导致PCB层间分离。
更严重的是,连PCB的外观都可以看到有气泡、膨胀、爆板等现象。
有时候,即使在PCB的外观上看不到上述现象,实际上也有内伤,久而久之会导致电器产品功能不稳定或CAF等问题,最终导致产品失效。
PCB板爆炸的真正原因分析及预防措施其实PCB的烘焙过程还是挺麻烦的。
烘烤时,必须将原封装拆下后才能放入烤箱,然后在100℃以上的温度下烘烤,但温度不能太高,以免烘烤时水蒸气过度膨胀,造成PCB爆炸。
一般工业上PCB的烘烤温度大多设定在120±5℃,以保证水汽能真正从PCB 板体中排除,然后在SMT线上打孔,在回流焊炉中焊接。
烘烤时间因PCB板的厚度和尺寸而异,对于较薄或较大的PCB板,烘烤后需要用较重的重物压板。
这是为了减少或避免烘烤后冷却过程中应力释放导致PCB 弯曲变形的悲剧。
因为PCB一旦变形弯曲,在SMT上印刷焊膏时就会出现偏差或厚薄不均的问题,导致后续回流焊出现大量短路或虚焊等缺陷。
PCB烘烤条件的设置目前业界对PCB烘烤的条件和时间一般设定如下:1.PCB应在制造日期的2个月内密封好。
开箱后,应放置在温度和湿度受控的环境中(≦30℃/60%RH,根据IPC-1601)5天以上,并在上线前在120±5℃下烘烤1小时。
2.PCB板应存放超过生产日期2 ~ 6个月,上线前应在120±5℃烘烤2小时。
爆板原因分析及对策

爆板原因分析及对策关于爆板的原因分析及改善对策刘军喜2007/04/28一、定义:通常所说的爆板是指内层芯板经过层压后在热应力作用下出现的PP与芯板分层、起泡等现象。
本文主要讲述压合工序的控制点。
二、原因分析及改善对策:多层板爆板分层发生在棕化层与介质层,Copper FoilDielectric LayerCoreDielectric LayerCopper Foil造成此类分层可从内层芯板、胶片两个原材料方面及制程方面去考虑。
1.叠合持取不当及环境异常造成后续板的分层可能原因:⑴. 胶片或内层板被作业员裸手污染⑵. 内层板或胶片中残留水气或有机物挥发成份(VOC)太多⑶. 叠合作业区温湿度高或不整洁,造成吸水或沉淀吸尘改善对策:⑴. 严格要求作业员带洁净手套或手指套作业,且只允许接触板边⑵.已做过的棕化板,压板前仔细检验,有问题另加处理⑶.内层板棕化前做烘烤处理⑷.半固化片的存放须严格管控(温度;20±2℃湿度:45±5%),对过期半固化片及时进行隔离,以免混用或误用⑸.叠合工作区环境保持干燥,勿使内层板与胶片吸水⑹.建立良好的无尘室(保证万级以下)2.制程问题造成后续板的分层,气泡可能原因:⑴.压合中不当藏入水分、空气、或污染物⑵.压合中热量不足,历程太短,胶片品质不良,压机性能不好导致硬化程度有问题。
⑶.内层板棕化不良,微蚀深度达不到要求,棕化膜太薄或硬度不够⑷.内层板或胶片受污染⑸.胶流量不足⑹.流胶过度,胶片所含胶几乎全部被挤出⑺.压合时压力不足,过度减压造成流胶量不足或接着力不强改善对策:⑴.对内层板棕化前做烘烤处理,做完棕化后保证压合前不超过24小时⑵.对内层有残膜板须退内层做退膜处理,保证芯板的清洁干净、无氧化、无残留膜⑶.层压时相应延长抽真空时间,充分排除半固化片之间及与芯板间的空气和挥发物⑷.严格控制棕化药水浓度、温度、速度、压力、水流量、微蚀量保证有机膜的厚度和硬度,增强内层铜箔与树脂的结合力⑸.排板时须严格执行混压原则,保证混压的有效性,以免造成压力过大或过小,导致胶流量不足或流胶过度⑹.对无尘室内及开料间残胶、有挥发性化学物品进行清除及隔离,保证芯板及半固化片的洁净度⑺.严格按要求补充牛皮纸数量,延长流胶时间,增加流胶量⑻.压合过程中定时检测压机升温曲线、压力是否正常⑼.压合后补烤150℃ 2-4小时,延续硬化。
PCB爆板的真因剖析与防止对策

PCB爆板的真因剖析与防止对策PCB爆板的真因剖析与防止对策PCB电路板会发生爆板(popcorn)或分层(Delamination)的主要原因不外乎一板材吸水二α2/z-CTE太大这两大类,而「板材吸水」所造成的爆板更占了70%的不良,其他原因如PCB结构之涨缩不均,冷热不均、制程受伤与黑化不良…等虽然也不能排除其可能性,但其比率都不太高就是了。
为什么「水」是造成PCB爆板的主要原因?「水」在100°C以下的时候对爆板的影响不大。
当温度超过100°C后,「水」就会成为树脂的可塑剂。
树脂吸水较多时Tg会下降(△Tg应该小于5°C)且橡胶态会提早到来,将引发板材Z方向瞬间肿胀(Swelling)而快速开裂(100°C~Tg之间最容易发生),参考文章最前面的图表,水蒸气超过100°C后的气压(psi)将成等比级数增加。
通常板材的X与Y之CTE(膨胀系数)较稳定,约在15~16ppm/°C之间。
另外,板材内的隐性水份也会变成树脂的可塑剂,与外部的水份一起助纣为虐。
当树脂温度超过Tg点之后,就会转变为橡胶态,这时候「水」份对爆板已经转变成为配角,而且这时候的水份也大多已经该变成水蒸气蒸发掉了,再说橡胶态是软的,也不容易有爆板才对。
PCB的「水」从哪里来?既然「水」对爆板这么重要,那我们得好好研究一下水从哪里来,就我们普遍的了解与认知,大部分的「水」可能都来自于外界,可能是在PCB制程时吸入附著,或是PCB存放时从环境中逐渐扩散(Diffusion)进入;但板材内部结构容易藏水也是可能的原因之一;另外一个你可能想不到的,PCB树脂的分子式里也藏著水分子,加热之后会自行产生水分。
所以总结板材吸「水」及藏水处有:树脂分子本身具有的结构水(树脂分子结构远本具极性(polarity)处已经隐含水分子,只要化学式中含有OH就有机会形成水)。
树脂与玻璃纤维介面处容易藏水(板材使用一条树脂与一条玻璃纤维用经纬编织而成,如果编织不够密实,就会有缝隙,一般建议选用低透气率的扁纤布比较不易藏水)。
爆板原因分析

摘要随着欧盟RoHs法令从2006年7月开始实施,印制电路板装配不得不随之无铅化,传统已使用超过50年的63Sn/37Pb焊接材料被SnAgCu(Sn96.5%/Ag3.0%/Cu0.5%)代替,熔点由原来的187℃提升到21 7℃,相应的焊接温度由220℃~230℃提升到240℃-260℃,印制电路板必须经历熔点以上的焊接时间多出了50多秒,印制电路板吸收热大增,印制电路板必须提高耐热性能与之配合。
在过去的一年中,印制电路板分层问题一直困扰着电路板制造商。
印制板分层的机理是电路板吸热后,不同材料之间产生不同的膨胀系数而形成内应力,如果树脂与树脂,树脂与铜箔的粘接力不足以抵抗这种内应力将产生分层,所以解决分层的思路是:1.生产流程控制尽可能保证板子有最佳的抵抗内应力的能力:2.使用性能优越的材料减少内应力。
文章希望通过研究,在成本和品质双重约束下,找到最佳的解决方案,用最低的成本来解决分层问题。
思路是从研究分层的原因着手,通过实验设计的方法,对分层的因素从材料选择、印制电路板制造过程控制到电路板装配的整个过程,进行系统分析。
本研究项目耗费25万元的试验材料成本,历时三个多月,最终从成本和品质控制,提升公司竞争力的角度,提出解决分层的三套方案。
在将实验结果运用到A公司的实践中后,产生了良好的经济效益,每月减少客诉成本约30万元,减少成本浪费约80万元,取得超过预期效益。
关键词分层;无铅焊接;实验设计:印制电路板1引言1.1研究的背景和意义1.1.1 PCB行业回顾与展望1936年一1940年,英国Paul博士从印刷技术得到启发,首先提出了“印刷电路”的概念,开创了制造印刷电路板的先河。
1967年美国人Beadles.R.L,提出了多层板生产制造工艺(MLB),将印刷电路板推上了更高一层楼。
1984年日本PCB专家项土冢田裕尝试在多层板上采用盲孔结构,HDI技术兴起(High Den sityInterconnection)印制电路板从诞生之日起就依托其互联和承载的功能成为电子产品的航空母舰,任何功能强大的芯片只有集成到印制电路板上,才能展现其威力。
常见PCB爆板的成因与解决方案

常见PCB爆板的成因与解决方案摘要: 爆板是PCB 一种最常见的品质可靠性缺陷,其成因复杂多样,在电子产品的无铅化焊接工艺中,随着焊接温度的提高和焊接时间的延长,在热量增加的情况下,PCB 爆板发生率剧增。
本文通过理论和务实做法试从PCB 设计、材料选择、加工过程等方面进行归纳总结,并提出简单可行的解决方案。
关键词: 爆板无铅焊接一、前言随着欧盟RoHs 法令的实施,组成电子产品的印制电路板、电子器件、组装焊料等全面进入无铅化时代,电子组装工艺发生巨大变化。
应用多年的63/37 锡铅焊料已被Sn-Ag-Cu、Sn-Cu-Ni 等无铅焊料替代,其熔点由183℃剧升到217℃以上,回流焊接温度由220℃升高到250℃,且焊接时间延长20 秒以上,焊接热量的剧增给电路板、电子元器件等的耐热性能提出了更高的要求,在焊接的过程中,爆板(Delamination )是电路板最常见的可靠性缺陷之一。
本文通过理论分析和务实做法试从PCB 设计、材料选择、加工过程等方面对爆板进行归纳总结,以期找到简单可行的解决方案与同行共勉。
二、爆板的成因及解决方案造成PCB 焊接过程爆板的成因众多复杂,我们从PCB 设计、材料选择、焊接曲线、加工过程(包括棕/黑化、压板、钻铣成型及过程吸湿管理等)等四方面对其爆板现象、形成原因和解决方案进行归纳总结。
(一)材料耐热性能不足型爆板1.典型爆板切片图2.成因分析(1) 上述两个爆板案例主要发生在高层板结构中,爆板的位置相对比较固定。
爆板的主要位置发生在BGAPitch 间距较小及BGA 密集区域位置。
(2) 无铅焊接的Profile 峰值温度较传统锡铅焊接平均高出34℃(锡铅焊料熔点为183℃,而无铅焊料熔点最低为217℃),对材料的耐热性提出更高要求。
锡铅焊料在Reflow 时的峰温平均为225℃,波焊峰温平均为250℃,而无铅焊料的Reflow 峰温需提高到245℃,喷锡及波焊温度需提高到270℃,且Reflow 的平均操作时间延长20s 以上,焊接热量的剧增,对PCB 板的损伤加剧。
典型PCB爆板的案例分析

PCB爆板的案例分析摘要:本文通过对一个典型的PCB 爆板失效案例的分析,总结了类似爆板失效的分析思路与方法。
同时发现,水份含量过高仍然是导致PCB 爆板的最主要的诱因,而PCB 内的PP 料与铜箔之间的粘结材料固化不完全或其粘接力不足也可增加爆板的机会。
关键词:印制电路板爆板失效水份含量前言随着电子产品的高密度化,以及电子制造的无铅化,线路板(PCB)产品的技术要求和现有的性能指标水平也面临越来越严峻的挑战。
线路板的电路层数也越来越多,导线之间的间距也越来越小;另外无铅工艺也需要PCB 能够耐更高温度的焊接工艺过程。
因此,在PCB 的设计与生产加工的时候需要更严格的工艺与原材料的控制。
目前由于尚处于技术和工艺的转型期,各方的认识和新技术实施尚未完全到位,于是类似PCB 爆板之类的失效常常发生,并且引起供应商与用户直接的质量责任纷争,为此导致的损失严重。
本文选择一典型的PCB 爆板进行原因分析,供业界控制类似问题的发生提供参考。
1 样品描述客户提供了三片已经经过焊接工艺组装的电路板组件(PCBA),其中已有多个部位发生了爆板或分层的失效现象。
为了便于对失效原因的分析,本文还收集了另外两个料号的同一批次的空白PCB样品,其中一个为PCB 的成品空白板,另外一个为半成品,均非真空包装。
资料显示PCB 为芯板外加PP 和铜箔压合而成。
2 分析过程2.1 外观检查对3PCS 上件板失效品作外观检查,发现板面多处爆板,外观集中表现为外部铜层突起及无铜处基材面泛白,代表照详见图1;将外部铜层突起的部位剥离,发现基材面凹凸不平,铜箔底面颜色与基材面相近,说明外层铜箔下仍覆有很薄一层树脂,剥离后的正反面的爆板部位与正常部位的外观照片见图2。
2.2 金相切片分析对爆板失效的样品作切片分析,发现爆板分层主要发生表面铜箔下的树脂层,内部芯板有爆板,但程度较轻;外部铜箔突起处的切片图显示外层铜下表面几乎无树脂附着,粘接材料的底面树脂断面较平整,代表照详见图3。
电路板组装焊接的爆板问题及解决方法

电路板组装焊接的爆板问题及解决方法爆板就是印刷电路板的分层或起泡的俗称,分层是出现在基材内的层与层之间、基材与导电铜箔之间,或印制板任何其他层内的分离现象。
起泡是表现为层压基材的任意层之间或者基材与导电铜箔或保护性涂覆层之间的局部膨胀和分离的分层。
起泡也是分层的一种表现形式。
电路板组装焊接爆板就是在再流焊接过程中,出现HDI积层高于PCB第二次压合的PP层和次层之间的分离现象,这种情况就被称为是爆板,爆板一般发生在L1-L2层埋孔密集区域,有时候可能会被拉裂。
电路板组装焊接爆板的原因是什么?可能的原因分别是有挥发物,PP与铜箔的附着力比较差导致爆板,再流温度选择不合适,可挥发物逃逸不畅。
挥发物形成是电路板组装焊接产生爆板的必要条件,因为电路板组装焊接爆板都是产生在二次压合之间,所以PP与铜箔的附着力非常重要,再流温度不合适也会导致电路板焊接爆板。
据领智电路工程师分析,爆板的位置都是发生在埋孔的上方,大面积覆盖铜箔的位置。
这种设计确实有问题,主要体现在两个方面,一方面是电路板焊接受热之后,会对积聚在埋孔、层间的可挥发物排放不利。
另一方面,会加剧再流焊接时候的分布不均匀。
如何改善电路板组装焊接爆板的情况?要从根本处解决爆板产生的必要条件。
比如PP存储时候吸潮是导致爆板的原因之一,所以,存储PP的时候,一定要注意防潮。
要严格控制PCB成品仓库的存放条件,抑制爆板产生的充分条件,优化棕化工艺质量,增加其内部附着力。
改善大铜箔面上的透气性,避免内部水汽无法释放。
优化再流焊接的温度,确保良好湿度下的温度值。
电路板组装焊接中的爆板问题和解决方法大概就如此了,如果出现爆板问题的话,不妨可以参考以上的方法进行合理的解决。
- 1、下载文档前请自行甄别文档内容的完整性,平台不提供额外的编辑、内容补充、找答案等附加服务。
- 2、"仅部分预览"的文档,不可在线预览部分如存在完整性等问题,可反馈申请退款(可完整预览的文档不适用该条件!)。
- 3、如文档侵犯您的权益,请联系客服反馈,我们会尽快为您处理(人工客服工作时间:9:00-18:30)。
4 . 2 实验设计
按 照上文2 . 3 节 ,P C B 表 面 粗 糙 度 参 数 选 择 所
了 良好 的 表 面 形 貌数 据 。与 传 统 的 光 学 显 微镜 相 比
较 ,具 备 分辨 率较 高 、清 晰 度 较 好 ,可 实 现 大 面积 全 貌 分 析 ,图 像连 贯 性好 ,可 观 察 三 维 形 貌 、 能够
加 以改善 ,才 能从根 本上 解 除爆 板 之忧 。
以 上 是 本人 在 爆 板 问题 上 的一 些 研 究 结 果 和看
解 决措 施 : ( 1 )水洗 后增 加 烤 板 过程 ,将 水 汽烘 出 ,但 无
法完 全将 水汽 除 去 。 ( 2 )增加 阻焊 堵 孔 , 防止 形 成 半 堵 孔状 态 ,但 同时 也会 带来 成本 的增 加 。
王春 艳 ,工 艺 工程 师 ,主 要 负 责多 层 板 压 合 工
艺。
邸桂 娟 ,现 任 实验 室 主管 ,主 要 负 责实 验 室 工
参考 文献
[ 1 ]G B T 3 5 0 5 . 2 0 0 9 产 品几 何 技 术规 范( G P S ) . 表 面结 构 轮廓 法 术 语, 定义 及表 面结 构参 数. [ 2 】G B T 1 0 3 1 . 2 0 0 9 产 品 几何 技 术规 范( G P S ) . 表 面结 构 轮 廓法 , 表 面粗 糙度 参数 及其 数值 . [ 3 ] 李楠 . 激 光扫 描 共 聚焦 显 微镜 微 术 . 北京 : 人 民军
( 上接第3 7 页)
经 过A线 的半堵 孔产 品 会存在 吸潮 爆板 隐患 。 ( 2 )堵孔 和 过 孔 开 窗 产 品 的不 会 增 加湿 气 ,而 堵孔 产 品在两 条 线都 有或 多或 少 的湿 气 增加 。
问题 也 并 非 每 次 都 单 独 存在 ,这 些 潮 气 也 仿 佛 专 盯 “ 有 缝 的蛋 ” 。所 以 只有找 出 吸潮 问题 背 后 的 真 因
印 制 电路信 息 2 0 1 3 N o . 1 1
检测 、质量控 制与可 靠性 I n s p e c t i o n Qu a l i t y c o n t r o l a n d R e l i a b i l i y t
行 表 面 粗 糙 度 测量 ,量 化 不 同前 处理 方 式对 铜 面 处
理 效 果 ,保 证 干膜 或 油 墨 与铜 面 的结 合 力 ,反 馈 指 导精 益 生产 。
5 结 论 与展望
本 文借 助L E X T O L S 4 0 0 0 激 光 显微 镜对P C B f  ̄ J I 作 流 程 中 不 同 工 序 处理 后 的芯 板 进 行 测 量 研 究 , 得 到
述 , 本 实 验 选 用 轮 廓 的 算 术 平 均 偏 差Ra 表 示 粗 糙
度 。 由此 设 计 DOE 实 验 ,对 印制 电路 板 来 料 芯 板 按 以下 工序 处理 ,然 后 测 量 记 录R a 值 ,共 分 五 组 实 验 : 芯 板 直 接 测 量 、 不织 布 前处 理 后 测 量 、无 机 酸
艺 出版 社.
4 . 4 实验 总结
依据 业 界认可 的不 同处 理后板 面 附着力 从弱 至强
排序 :芯板 不 处 理 <不 织布 <火 山 灰 无 机 酸 <有 机
酸超 粗 化 处 理 。 由表2 ,可 以看 出 ,实验 数 据走 势 与
【 4 】 宋 建远 等. 高频埋 容P C B  ̄ J 作关 键技 术研 究『 J ] . 印 制 电路 信 息。 2 0 1 1 , 4 .
法 ,希 望 能 对 各 位 行 业 同仁 提 供 一 些 帮 助 和 启 发 ,
不 足之 处还 请批 评指 正 !
参 考文 献
[ 1 ] 白蓉 生 . C T 一 0 1 电路 板 失 效 分 析 与 深 入 判 读 [ J ] .
2 01 2 , 0 3 .
( 3 )改造 水 洗 线 ,提 升水 洗 烘 干 能 力 ,避 免 水
快 速 获 取 样 品 表面 的 三 维形 貌 信 息 等 诸 多 优 点 。 随
着 产 品 质 量 的 要 求和 精密 加 工 技 术 的提 高 ,表 面 粗
糙 度 已进入 纳 米 时 代 , 因 而 ,3 D 激 光 显 微 镜在 P C B
前 处 理 后 测 量 、 火 山 灰 前 处理 后 测 量 、有 机 酸 超 粗
第一 作者 简 介
宋 建 远 ,技 术 中 心 工 程 师 , 主 要 从 事P C B 新 产 品、新技 术 的研 发及 公司知 识产 权和标 准化 管理 。
业 界共识 相 一致 。有 此可 以 ,利 用激 光 显微镜 可 以对 P C B 表 面粗 糙度 实施量 化判 定 ,并辅 以三维 直观 图 。
汽残 留 。
作 者简 介
吕永 ,技 术部 机加 工主 管 ,对P C B 钻 孔 、成 型 、 压 合工 艺颇 有 研 究 ,主 要 负责机 加 工 工艺 和A P Q P 方
面 的管 理提 升工 作 。
4 总结
本文 介缁 1 r 热冲 击测 试、T G测 试 和 湿 气 含 量 测 试 种 验 证 吸 潮 导 致 爆 板 的方 法 ,并 对 工 作 中 见 到 的 几种 典 型 爆 板 从 “ 外 部 ”直 观 的 角 度 进 行 了解
化后 测量 。
表面 粗糙 度测 量 领域 的应用 必将 成为 主流 方 向。
致 谢 :本 研 究 得 到广 东省 教 育 部 产 学 研 结 合项
目 ( 2 0 1 1 B 0 9 0 4 0 0 6 3 0 )专 项资 金资助
4 , 3 实验 数据
针 对 上 述 实 验 设 计 ,对 不 同 工序 后 芯板 采 取 多 次 多 点测 量 求 平 均 值 的 方 法缩 小 误 差 。所 测 数 据R a 值及 测量 界面 ,见表2 。