烧结烟气氨法脱硫塔气液两相流数值模拟研究-温荣耀
Fluent 资料集合(续)
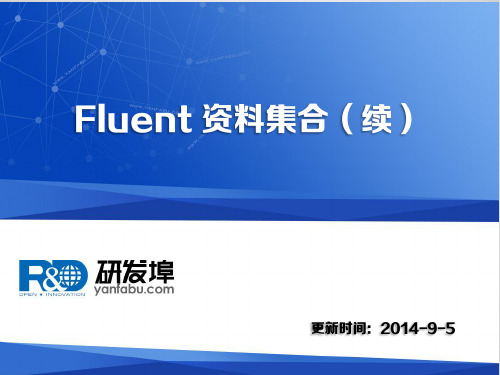
流体动力学的并行计算(EN)
流体动力学的有限元法(EN) 流体动力学的有限元法(卷3)(EN) 流体动力学和流体机械手册卷1(EN)
10.Fluent动网格教程分享
fluent动荡讲座
fluent动态网讲座 fluent动态网教程1—8
11.Fluent软件知多少
相当水力直径进行计算?
A:1.如果不画边界层的计算结果与实验值的误差在工程精度范围内,是 可以接受的;但是,正如贴主所说,有边界层算的更准,那保证网格质 量就没有多大意义了。 2.如果不画边界层网格,建议采用k-epsilon Realizable湍流模型。
3.计算水力直径,应当是计算域流体入口的水力直径:H=4A/C(A为入口
7.2014 ANSYS技术大会讲义集--系统
ANSYS SBU视觉从三维到嵌入式软件 UGM V2
Ansys_基于模型的系统和软件工程_傅金泉_v2.0
UGM V1的SCADE创新 先进的UGM V7系统设计 张国明-云时代的中国仿真 - 2014 ANSYS中国UGM演讲V2
8.FLUENT超级学习手册
Fluent 14.5 Eulerian Wall Film Defogging官方教程
Fluent 14.5自定义输入参数官方教程
Fluent_14.5meshing官方教程 Fluent 14.5 FSI官方教程 Fluent 14.5 built-in tutorials Fluent 14.5传热 官方教程
3.之前利用fluent计算敞水时舵的水动力,采用SST湍流模型,分别用有
边界层和无边界层进行计算,无边界层计算的升力、阻力比有边界层的 大10%左右,有边界层更接近实验值。不过失速角和变化趋势还是一致的
烧结烟气脱硫脱硝技术的研究与应用
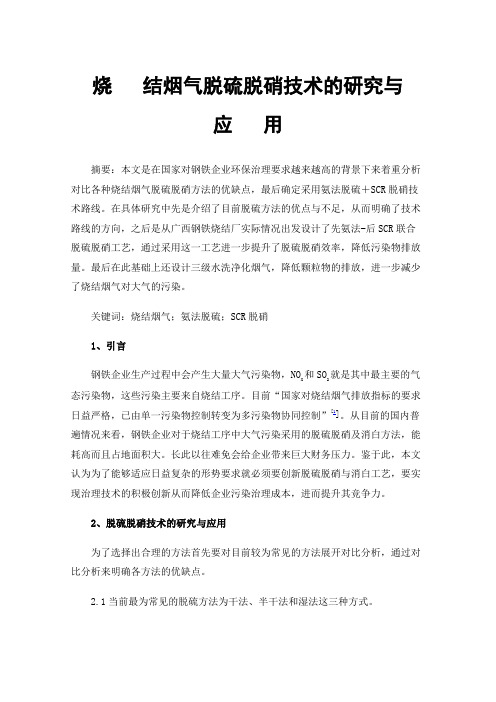
烧结烟气脱硫脱硝技术的研究与应用摘要:本文是在国家对钢铁企业环保治理要求越来越高的背景下来着重分析对比各种烧结烟气脱硫脱硝方法的优缺点,最后确定采用氨法脱硫+SCR脱硝技术路线。
在具体研究中先是介绍了目前脱硫方法的优点与不足,从而明确了技术路线的方向,之后是从广西钢铁烧结厂实际情况出发设计了先氨法-后SCR联合脱硫脱硝工艺,通过采用这一工艺进一步提升了脱硫脱硝效率,降低污染物排放量。
最后在此基础上还设计三级水洗净化烟气,降低颗粒物的排放,进一步减少了烧结烟气对大气的污染。
关键词:烧结烟气;氨法脱硫;SCR脱硝1、引言钢铁企业生产过程中会产生大量大气污染物,NOX 和SO2就是其中最主要的气态污染物,这些污染主要来自烧结工序。
目前“国家对烧结烟气排放指标的要求日益严格,已由单一污染物控制转变为多污染物协同控制”[1]。
从目前的国内普遍情况来看,钢铁企业对于烧结工序中大气污染采用的脱硫脱硝及消白方法,能耗高而且占地面积大。
长此以往难免会给企业带来巨大财务压力。
鉴于此,本文认为为了能够适应日益复杂的形势要求就必须要创新脱硫脱硝与消白工艺,要实现治理技术的积极创新从而降低企业污染治理成本,进而提升其竞争力。
2、脱硫脱硝技术的研究与应用为了选择出合理的方法首先要对目前较为常见的方法展开对比分析,通过对比分析来明确各方法的优缺点。
2.1当前最为常见的脱硫方法为干法、半干法和湿法这三种方式。
干法烟气脱硫的优点点表现在使用设备简单、占地面积小而且操作起来非常方便,其缺点表现为反应速度慢且脱硫率较低。
半干法脱硫是处于干法与湿法之间的另一种脱硫方法,不管是脱硫的效率还是脱硫剂吸收率都在两者之间,这种方法的优势是不仅投资少而且运行费用比较低,它的缺点是脱硫效率比湿法脱硫要低一点。
湿法烟气脱硫“是通过液相氧化-还原吸收来达到脱硫的目的”[2],湿法脱硫技术成熟且脱硫率高,它在脱硫技术中占据了主导地位。
氨法脱硫属于一种湿法脱硫,其优势表现为适用范围广,脱硫效率较高,生产运行安全。
氨法烟气脱硫塔模拟研究
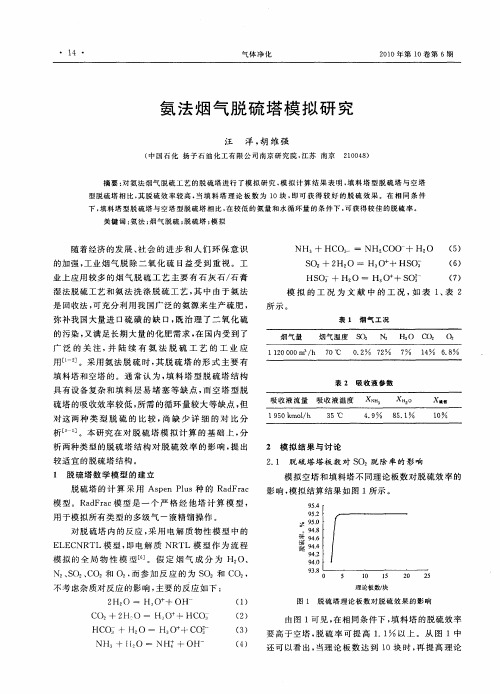
.
脱硫塔 的 计 算 采 用 As e ls 的 R d rc pnPu 种 a F a
模 型 。R d rc 型 是一 个 严 格 经 他 塔 计 算 模 型 , aFa 模
用 于模拟所有 类型 的多级气 一液 精馏操作 。 对脱硫 塔 内的反应 , 用 电解 质 物性 模 型 中的 采 E E NR L C TL模 型 , 电解质 NR 即 TL模 型作 为 流 程 模拟 的全 局 物 性 模 型[ 。假 定 烟 气 成 分 为 H。 6 ] O、 NzS 2 C 和 O , 、 O 、 0z 。 而参 加 反应 的为 S 。和 C , O O。 不考 虑杂质对 反应 的影响 , 主要 的反应如 下 :
下 , 料塔 型脱 硫 塔 与 空 塔 型 脱 硫 塔相 比 , 较 低 的 氨量 和 水 循 环 量 的 条件 下 . 获得 较 佳 的 脱 硫 率 。 填 在 可 关 键 词 : 法 ; 气 脱 硫 ; 硫 塔 ; 拟 氨 烟 脱 模
ห้องสมุดไป่ตู้
随着经济 的发 展 、 会 的 进 步和 人们 环 保 意识 社
・
1 ・ 4
气 体 净 化
21 0 0年 第 1 O卷 第 6期
氨 法 烟 气 脱 硫 塔 模 拟 研 究
汪 洋 , 维 强 胡
( 国石 化 扬 子 石 油 化 工 有 限 公 司南 京 研 究 院 , 苏 南 京 中 江 204) 10 8
摘要 : 对氨 法 烟 气 脱 硫 工 艺 的 脱硫 塔 进 行 了模 拟 研 究 , 拟 计 算 结 果 表 明 , 料 塔 型 脱 硫 塔 与 空 塔 模 填 型脱 硫 塔 相 比 , 脱 硫 效 率 较 高 , 填 料 塔 理 论 板 数 为 1 其 当 O块 , 可 获 得 较 好 的脱 硫 效 果 。在 相 同 条 件 即
烧结烟气氨法脱硫技术介绍与分析

( H )S ,通 过 鼓 风 强 制 氧 化 , 化 为 N :0 转
( H )S N O 。一 定 浓 度 硫 酸 铵 溶 液 进 入 副 产
烟 气脱 硫 , 究 总 结 发 现 烧 结 烟气 有 如 下 一 研
=
在烧结 工艺 中 , 大部 分 的硫 被 燃 烧 生 绝
成 二 氧化硫 , 结 烟 气 的 大 气 排放 已对 环 境 烧
2 H H O , 补 氨 过 程 中 N S 与 氨 N S 在 HH O
反 应 后 生 成 (N )S H O ,反 应 生 成 的
造 成严 重污 染 , 结 机 在 烧 结 过程 中产 生 的 烧
21 0 1年第 3期
冶 金 环 境 保 护
3 7
烧 结烟 气 氨 法脱 硫 技术 介 绍 与分 析
罗海兵 李 啸
武汉 4 07 ) 30 1 ( 汉 都 市 环 保 工 程 技 术 股 份 有 限 公 司 湖北 武
摘 要 本 文 以某 钢 厂 烧 结 机 头烟 气脱 硫 工 程 为例 , 要 的介 绍 了一 种 适 于 钢 厂 烧 结 机 烟 气 处 理 简
烟 气 中的 S , 低 浓 度 的循 环 溶 液 在脱 硫 塔 O ,
冶 金 环 境保 护
2 1 年 第 3期 01
圈
副
聒 榛 翟
H
匦
睾 区
21 0 1年第 3期
冶 金 环 境 保 护
3 9
同时完 成 吸收 和氧化 过程 。在 脱硫塔 内通过
整优 化 。在脱硫 塔 中 , 了保 证 脱 除 S 的 为 O
0. ~3 m 。 1 5
氨法脱硫技术在烧结烟气治理领域的应用
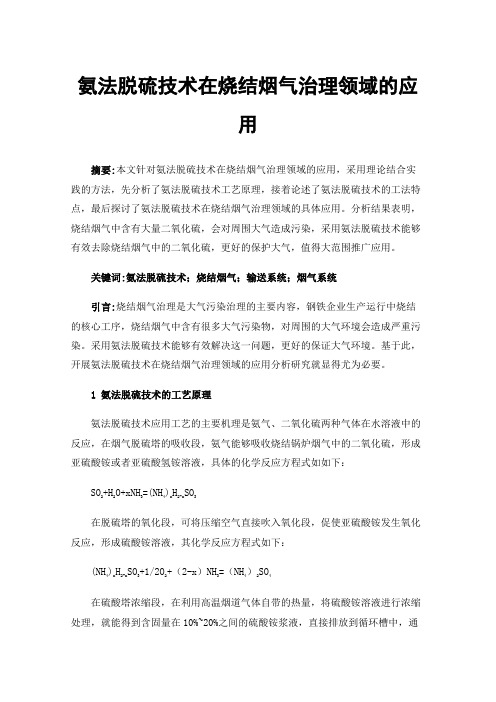
氨法脱硫技术在烧结烟气治理领域的应用摘要:本文针对氨法脱硫技术在烧结烟气治理领域的应用,采用理论结合实践的方法,先分析了氨法脱硫技术工艺原理,接着论述了氨法脱硫技术的工法特点,最后探讨了氨法脱硫技术在烧结烟气治理领域的具体应用。
分析结果表明,烧结烟气中含有大量二氧化硫,会对周围大气造成污染,采用氨法脱硫技术能够有效去除烧结烟气中的二氧化硫,更好的保护大气,值得大范围推广应用。
关键词:氨法脱硫技术;烧结烟气;输送系统;烟气系统引言:烧结烟气治理是大气污染治理的主要内容,钢铁企业生产运行中烧结的核心工序,烧结烟气中含有很多大气污染物,对周围的大气环境会造成严重污染。
采用氨法脱硫技术能够有效解决这一问题,更好的保证大气环境。
基于此,开展氨法脱硫技术在烧结烟气治理领域的应用分析研究就显得尤为必要。
1氨法脱硫技术的工艺原理氨法脱硫技术应用工艺的主要机理是氨气、二氧化硫两种气体在水溶液中的反应,在烟气脱硫塔的吸收段,氨气能够吸收烧结锅炉烟气中的二氧化硫,形成亚硫酸铵或者亚硫酸氢铵溶液,具体的化学反应方程式如如下:SO2+H2O+xNH3=(NH4)xH2-xSO3在脱硫塔的氧化段,可将压缩空气直接吹入氧化段,促使亚硫酸铵发生氧化反应,形成硫酸铵溶液,其化学反应方程式如下:(NH4)xH2-xSO3+1/2O2+(2-x)NH3=(NH4)2SO4在硫酸塔浓缩段,在利用高温烟道气体自带的热量,将硫酸铵溶液进行浓缩处理,就能得到含固量在10%~20%之间的硫酸铵浆液,直接排放到循环槽中,通过旋流器进行分离后,再用离心机进行脱水处理,再经过干燥处理之后,就能得到硫铵产物。
2氨法脱硫技术的工法特点2.1完全资源化在烧结烟气治理中应用氨法脱硫技术能够将回收到的二氧化硫和氨全部转化为化肥,不会产生废水、废气、废渣等,也就没有不存在二次污染,实现了完全资源化,符合绿色、环保、循环经济的发展要求【1】。
2.2副产物价值高应用氨法脱硫技术每吸收1t液氨,可脱除2t二氧化硫,形成4t硫酸钠,按照市场价格算,液氨每吨2000元,硫酸铵每吨700元,烧结烟气中每吨二氧化硫能够体现400元的价值,应用成本比较小。
循环流化床烟气脱硫塔内气液两相流场数值模拟
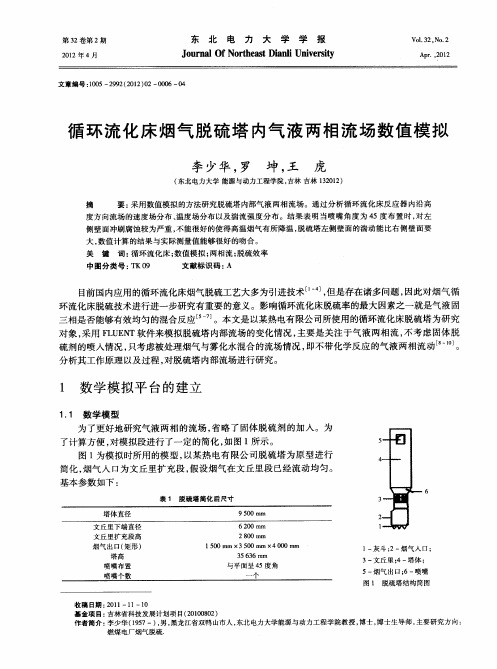
Absr t:I h sp p r, a —i u d t — h s o fed o ic l t u d z d b d f a s lu z to o t ac n t i a e g slq i wo p a ef w l fcr u a i f i ie e ueg sde u f r ai n tw— l i ngl l i
环流化床脱硫技术进行进一步研究有重要的意义。影响循环流化床脱硫率 的最大因素之一就是气液固 三相是否能够有效均匀的混合反应 [ 。本文是以某热 电有限公司所使用的循环流化床脱硫塔为研究 5 ] 对象 , 采用 F U N L E T软件来模拟脱硫塔内部流场的变化情况 , 主要是关注于气液两相流 , 不考虑固体脱 硫 剂 的喷人 情 况 , 只考 虑被 处理 烟气 与雾化 水混合 的流 场情 况 , 即不 带 化学 反应 的气 液 两相 流 动 …。
7 一7 O 6.
[ ] S unc e , i hoJ nu u n t . xe m na s d nFu a eup ui t nb i uan udzdbd[ . rce ig 7 h agh nMa Y a ,ajnH age a E pr e t t yo legs slh rai ycr lt gf ii e C] Poedns Z i 1 i lu d z o c i l e
简化 , 烟气 入 口为文 丘里 扩 充段 , 设 烟气在 文 丘里 段 已经 流动 均 匀 。 假 基 本 参数如 下 :
6
表 1 脱硫 塔 简 化 后 尺 寸
塔体直径 文丘里下端直径 文丘里扩充段高 烟 气 出 口( 形 ) 矩 塔 高
喷 嘴 布 置
62 o mm 0
e s su id b u r a i lt n T e v l ct i r u i n a d tmp r t r e d d s b t n a d t r u rwa t d e y n me c ls i mu ai . h eo i d s b t n e e a u e f l it u i n u b 一 o y t i o i i r o 1n n e s y d sr u in w sa ay e l n h e g to i u ai g f i ie e . h e u t s o e h e ti s n i it b t a n z d ao g t e h ih f r lt u d z d b d T e r s l h w wh n t e t i o l c c n l s n zl sd c r td a n l 4 f s i go el f w l wa ea iey s r u . h ih t mp r tr u a i o ze i e o ae t ge 5, u h n f h t al sr l t l e i s T eh g a l t e v o e e au ef e g sd d l
烧结烟气氨水法脱硫技术研究
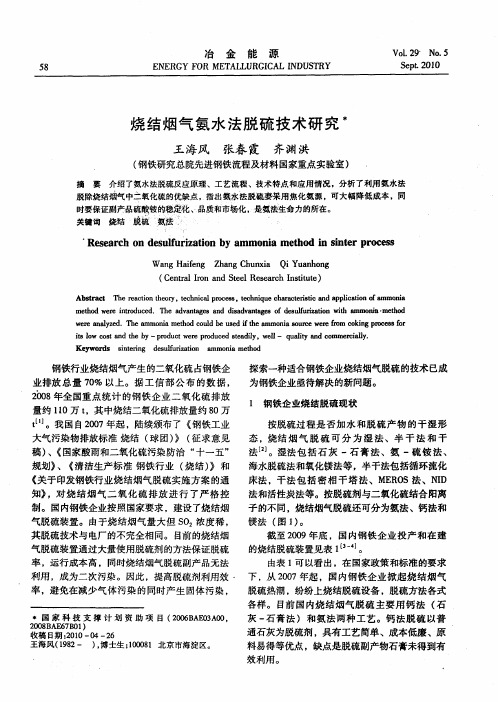
钢铁行业 烧结 烟气产生 的二氧化硫 占钢铁企
探索一种适合钢铁企业烧结烟气脱硫 的技术已成
为钢铁企业 亟待解决 的新 问题 。
1 钢铁企业 烧结脱硫 现状
业排放 总量 7 % 以上。据工信部 公布 的数据 , 0 20 0 8年全 国重 点统 计 的钢 铁 企业 二 氧 化 硫 排放 量约 10万 t 中烧结二 氧化硫排放 量约 8 1 ,其 0万 t … 我 国 自 20 0 7年起 ,陆续颁 布 了 《 钢铁 工业 大气污染 物排放 标准 烧结 ( 团) ( 球 》 征求 意见 稿 ) 国家 酸雨 和二氧化硫 污染 防治 “ 、《 十一 五 ”
Ab t a t T e r a t n te r ,tc nc l r c s , e h iu h r ce s ca d a pi a o fa sr c h e c i o y e h ia o e s tc n q ec a a t r t n p l t n o o h p ii ci mmo a i n me o r n r d c d h t d wee i t u e .T e a v tg s a d ds d a tg s o e uf r ai n w t mm n a・ t o o h d a a e n ia v a e f d s l l t i a o i me h d n n uz o h w r ay e .T e a l na meh d c ud b s ea ee a l z n d h l mo t o o l eu e i t mmo i 0 re’ ef m o ig p o e sfr l i d fh n a8 uc r o c k n r c s r o
i o o ta d t e b t lw c s n h y—p o u tw r rd c d se d l ,w l — q ai d c mme cal . s r d c e e p o u e ta i y el u lya o tn r il y
湿法烟气脱硫塔的优化数值模拟分析

湿法烟气脱硫塔的优化数值模拟分析本文采用FLUENT软件,对于某300MW机组的湿法烟气脱硫塔的流动特性开展了计算机数值模拟。
模拟过程中采用标准k-ε湍流模型来模拟系统内烟气的湍流运动,喷淋液滴采用拉格朗日随机颗粒轨道模型,开展气液两相流动的模拟。
通过模拟和分析入口烟道流场分布、脱硫塔内气-液两相流场分布及脱硫塔内液相分布情况,最终优化烟道导流板、塔内传质构件参数、喷淋层及除雾器布置,保障气液分布均匀,减少烟气逃逸,降低系统压力损失,对其类似项目的设计和实施提供了一定的指导价值。
石灰石-石膏湿法烟气脱硫工艺是国内外主流的燃煤电厂烟气脱硫技术,该技术属于气-液-固三相反应过程,包括了SO2和石灰石在液体中的溶解传质过程以及溶解物在液相中的反映过程。
脱硫塔中,浆液由塔顶喷淋层通过液相喷嘴自上而下喷入脱硫塔,烟气由吸收塔底部区域自下而上通过吸收区域,脱硫浆液在吸收塔内不断循环,完成烟气中SO2的吸收过程。
影响脱硫效率的关键因素是塔内的流动情况,例如脱硫浆液的空间分布、烟气在脱硫塔内的流场及烟气与脱硫浆液的接触情况等。
对于湿法脱硫吸收塔这类大型的气液两相反应器,如通过物理实验很难对塔内的流动情况开展测试,实验工作量十分巨大,实验周期较长;另外,受到实验测量手段及实验方法的限制,很难对现场的工程设计提供指导。
随着计算机计算能力的不断提高,采用计算流体力学(ComputationalFluidDynamics,CFD)软件来开展三维流动的研究已经成为一种重要手段。
合理利用计算机开展仿真数值模拟,不仅能缩短研制周期,降低设计成本,而且能明显提高设计质量,相对于传统的物理实验方法具有优越性。
通过数值模拟可以深入认识吸收塔内烟气和浆液流动规律,这对指导吸收塔的设计起着重要的作用。
而且,随着国家日益严格的燃煤电厂超低排放标准,要求对脱硫塔的设计及运行开展精细化研究。
本文采用FLUENT软件,对于某300MW机组的烟气脱硫塔的流动特性开展了计算机数值模拟,通过模拟和分析入口烟道流场分布、脱硫塔内气-液两相流场分布及脱硫塔内液相分布情况,最终优化烟道导流板、塔内传质构件参数、喷淋层及除雾器布置,保障气液分布均匀,减少烟气逃逸,降低系统压力损失,对其类似项目的设计和实施提供了一定的指导价值。
用数值模拟方法进行脱硫塔的优化设计

嘴采用高低位布置 ,在喷 雾区加装环形导流分布 器,可使 脱硫塔 流场右侧湍流强度明显增加 ,左侧 烟气贴壁 流动有所改善 ,脱硫塔 内流场分布更加 合理,塔 出口温度 低于优化 前温度 ,增加 气液传质 、传热 ,提 高脱硫
效率。
关 键 词 : 硫 塔 ;数 值模 拟 ;优 化 设 计 ;导 流 分布 器 脱
第3 7卷第 2期
2l 00年 3月
华 北 电 力 大 学 学 报
J un o o ra fNo t l rhChn iaElcrcP we e ti o rUnv ri ies y t
Vo. 7 No. 13 , 2
Ma . r ,2 1 00
用 数值 模 拟 方 法进 行 脱 硫 塔 的优 化 设计
Ab ta t ae n n mei l i lt no mut h s lw,Opi zt n d s n o h eup u zt ns rytwe src :B sdo u r a muai f l i aef c s o p o t ai mi o ei fted slh f ai p g i o a o r
d o lt s d srb du ig tep ril ahmo e.Th i rpesWa ec e s i n h a t ep t d 1 c esm ̄ainr ut ftef w a dtmp rt ef lsidct t e l o s so h l o n e eau i d n i — r e a e h n l ft u a nr c s o o 1 h oze r i iha d lw o ie ,isaldt e d tea geo h f egse ta eWa d wn t 5 ,ten zl weeld i hg o c mbn s ntl h e l n s a n n e l a iti tr na c f tmi i o s ryJ esweeo t zt n .Th t d h u b e c nr h ie f eg sdsr uo i fao  ̄o zt nd w pa y r u b ao n a r p i ai mi o a ma etetr u n ei i t d l g s o h o rWa ne sf :tefu a tc o r lh da i rv e tnlf ieo h o r ftetwe Sitn ie i d h l egssu ktwe wa a n mp o e n i et d ftetwe.Th itiu l m s edsr — b t no o f l s r ain 1 i ff w i dWa mo ert a.Th a e eau eo h x o slwe h n b fr. Th o tc aeo o l e o eg tmp r tr fte ep r wa s t o rta eo e eo na t t f r ds lh rzt na e twihs sicesd a dt eef in yo eup ui t n Wa n a cd eup uiai g n t ozwa rae h fie c fd slh r ai s e h n e o n n c z o Ke r s eufr ain twe ;n me c l i lain;o t z t n l eg i rb tr ywo d :d l u i t o r u r a mu t s z o i s o pi a i ;f a dsi uo mi o u s t
烧结烟气有机胺法脱硫工艺_李玲密
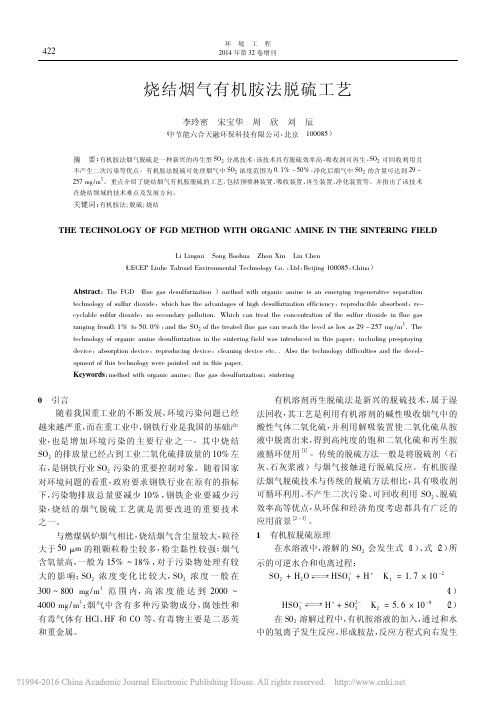
环境工程
2014 年第 32 卷增刊
423
反应,增大了 S02 的溶解量如反应式(3) 。 R3 N + SO2 + H2 O 幈幇 R3 NH + + HSO3- (3)
该 反 应 是 质 子 传 递 过 程,反 应 速 率 常 数[4] K
> 109m3 / kmol·s,反应瞬间完成,主要受气膜控制。随
有机溶剂再生脱硫法是新兴的脱硫技术,属于湿 法回收,其工艺是利用有机溶剂的碱性吸收烟气中的 酸性气体二氧化硫,并利用解吸装置使二氧化硫从胺 液中脱离出来,得到高纯度的饱和二氧化硫和再生胺 液循环使用[1]。传统的脱硫方法一般是将脱硫剂( 石 灰、石灰浆液) 与烟气接触进行脱硫反应。有机胺湿 法烟气脱硫技术与传统的脱硫方法相比,具有吸收剂 可循环利用、不产生二次污染、可回收利用 SO2 、脱硫 效率高等优点,从环保和经济角度考虑都具有广泛的 应用前景[2 - 3]。 1 有机胺脱硫原理
(5)
2 有机胺法脱硫技术发展概况
早在 20 世纪 80 年代,甲基二乙醇胺( MDEA) 就 广泛用于气体净化[5],其特点是能选择性地脱除硫而 将碳保留在净化气中,得到很高纯度的含硫气体可供 回收利用。而乙醇胺( MEA) 和 2 - 甲基 - 2 - 氨基 - 1 - 丙醇( AMP) 也被广泛应用在天然 气 选 择 性 脱 除 H2 S 气体[6 - 7]。BASF 公司开发出了 aMDEA1 - 6 系列 溶剂[8],通过 加 入 不 同 的 活 化 剂 和 添 加 剂 改 善 了 原 MDEA 吸 收 剂 的 性 能。 Winsto Ho[9] 等 人 研 究 了 在 MDEA 中添加位阻胺盐或位阻氨基酸的溶液吸收酸性 气体,对 H2 S 具有相当高的选择性。
大型脱硫塔喷淋段气液两相流动与传热的数值仿真及验证

大型脱硫塔喷淋段气液两相流动与传热的数值仿真及验证摘要:对大型湿法脱硫塔喷淋段内部的气液两相流动和传热过程进行模拟,并将模拟结果同现场运行数据进行对比.结果表明:良好的喷淋层和喷嘴布置可对塔内烟气流动起到很好的整流作用;在烟气入口对面的浆液池上方存在一气相的最高压区;原烟气的高速冲入对浆液滴的运动轨迹产生明显的影响,使得烟气入口处形成了一个斜向下呈带状的液滴浓度高值区;喷淋塔内温度梯度变化较大的区域在靠近吸收塔入口的位置,且此区域随烟气量的增大而扩大——简单忽略塔内气相温度场的不均匀性势必将给计算带来误差;喷淋塔内的气相温度场和水蒸气浓度场分布有明显的一致性规律,证明了塔内的降温过程主要为蒸发冷却.关键词:大型喷淋塔;气液两相流;传热;温度场;水蒸气;数值仿真随着环保标准的日益严格,对烟气脱硫装置的设计和运行也提出了更高要求.当前,很多烧结脱硫装备投资巨大,但无法正常运行,或脱硫效果欠佳,主要原因就在于对脱硫塔内气液两相流动规律的认识不够,以及对烟气降温的控制效果不佳.因此,有必要对脱硫装备内部的流动、传热和传质过程做更深入的分析,从而为设计和运行的优化提供依据.计算流体力学CFD(computationalfluiddynam-ics)仿真是研究湿法脱硫过程的重要手段.针对脱硫塔内气相流场的模拟研究较多[1-3],但未考虑离散相作用的模拟结果在实际应用上的价值有限.吸收塔内多相流模拟则为认识气液两相的相互作用和分布规律提供了重要帮助,但相关文献大多未涉及温度场的模拟[4-9].此外,还有一些针对脱硫塔内化学反应的模拟研究,但基本上也都忽略了烟气降温过程和塔内的温度场变化,即不考虑温度场对反应的影响[10-12];或将塔内温度变化简单假设为沿高度方向的一维函数,忽略其在径向的变化[13-14].可见,对大型脱硫塔内温度变化规律的掌握还有待进一步深入研究.有学者在焚烧烟气急冷段内同时考虑了温度场、气液双膜理论和气固缩核反应模型[15],但仅模拟了几个喷嘴.已有的文献大多受限于计算机的运算速度,故常常对模拟的脱硫塔几何尺寸进行缩减,或仅计算少量喷嘴以减少颗粒轨迹计算和两相耦合迭代的计算开销[15],由此限制了研究结果在大型脱硫塔上的应用和推广.本文借助上海市超级计算机中心的硬件平台,采用计算流体力学仿真的方法,对某大型喷淋塔的全尺寸喷淋段进行研究,详细模拟了塔内的气液两相流场和上百个喷嘴的喷淋,充分考虑了气液两相间的耦合作用(传动量、传热和传质过程),并将气相湍流脉动对颗粒运动的影响也考虑在内,从而获得较精确的塔内温度分布和烟气组分(主要是水蒸气)分布.以此揭示脱硫塔内气相和液滴颗粒相的分布特点,并讨论塔内传热、传质的规律及对脱硫过程的影响.模拟结果和现场实测数据进行对比,以进一步验证模拟的正确性.1数学模型及控制方程本文的气液两相流模拟采用欧拉-拉格朗日方下处理离散相(液滴).对于气相,为了封闭Reynolds时均方程组中的二阶关联项,本文采用标准k-ε模型.离散相颗粒的轨道通过积分拉氏坐标系下的颗粒作用力微分方程来求解.文中还考虑了气相湍流扩散对颗粒相的分布和轨迹的影响,通过颗粒随机轨道模型来计算,即采用随机行走模型(discreteran-domwalkmodel)来考虑湍流脉动对颗粒相的作用.为了更全面地模拟气液两相间的传递过程,本文考虑了能量方程.由于气液间的传热伴随着蒸发乃至沸腾,因此还要加入液滴气相的组分输运方程.因此,当计算离散相的液滴颗粒轨道时,将同时跟踪计算颗粒沿轨道的热量、质量、动量的损益,这些物理量将用于随后的连续相(气相)的计算中去.交替求解离散相与连续相的控制方程,直到二者均收敛为止,此即双向耦合计算.通过积分流场中颗粒的运动、能量以及组分方程,得到颗粒的速度、轨迹、温度和组分分布.以下略去气相控制方程,仅列出离散相方程和气液两相耦合的有关方程.1.1离散相方程颗粒作用力平衡方程在笛卡尔坐标系下的形式为式中:FD为颗粒驰豫时间;Re为颗粒的相对Reynolds数;ui为流体相速度;upi为液滴颗粒相速度;μ为流体相动力黏度;ρp为液滴颗粒密度;dp为颗粒直径;gi为外力对液滴颗粒的加速度.式(1)右边依次为流体对液滴颗粒的曳力项、重力项(包括浮力作用)和其他作用力项.气相湍流对颗粒相的分布和轨迹的影响通过颗粒随机轨道模型来计算.设流体湍流各向同性,认为流体速度脉动值iu′符合高斯分布.当颗粒穿过湍流主气流中的蒸汽浓度由水蒸气的组分输运方程求解得到,即2模拟对象及模型简化本文以某实际运行的大型喷淋塔为模拟研究对象,采用ANSYSFluent12.0计算平台进行模拟.喷淋塔设计烟气量120万m3/h,原烟气入口温度130,℃,原烟气湿度7%(体积分数).共4层喷淋,最上层与最下层喷淋层及喷嘴的布置方式相同.各喷淋层的位置高度为8,m、10,m、11.75,m和13.5,m,底层喷淋距吸收塔入口顶部1.5,m.每层有41个实心锥喷嘴,单喷嘴流量56.6,t/h,喷射角度90°.喷射液滴颗粒的平均直径为1.7,mm,液滴颗粒服从Rosin-Rammler分布.喷淋层结构和喷嘴布置见图1.吸收塔的模拟范围从浆液池的顶部开始,直至除雾器的入口为止,目的是充分模拟吸收塔内喷淋段的气液两相流动和传热过程.吸收塔入口尺寸为8,m×4.5,m,吸收塔直径11,m,模拟段高度15.5,m,如图2所示;烟气入口在第1层下的入口处,烟气出口在上方,各喷淋层的位置也标示其中.边界条件:入口条件为速度入口,出口条件为压力出口.采用Launder和Spaleding提出的标准壁面函数法来进行壁面处理.模拟过程中不考虑浆液管路和喷嘴本体对流动的影响.模型总共划分网格数170万,采用六面体网格.由于采用随机颗粒轨道模型,在整个计算过程中,离散相迭代更新一次总共需跟踪656,000条颗粒轨迹线.因迭代计算量大,所以本文的模拟借助于上海市超级计算机中心的公共平台.根据工程实际情况,本文的计算模型对脱硫塔内的烟气-浆液两相流动做如下的简化和假设.(1)将烟气视作不可压缩牛顿流体.(2)忽略气液两相与塔壁面间的传热;忽略塔内化学反应热和烟气组分在水中的溶解热.(3)将烟气视为理想气体,将液滴视为刚性球体考虑.(4)计算中不考虑液滴颗粒之间的碰撞、破碎及聚并效应.不考虑因为液滴蒸发、变形和传质过程导致的烟气流速和曳力系数的变化.(5)液滴碰壁后便中止液相对气相源项的计算.3数值模拟结果与分析3.1气液两相流动的模拟结果图3为纯气相模拟(不考虑液相)情况下的纵向中心截面的速度矢量场图.可见在没有浆液喷淋的情况下,由于原烟气的刚性和惯性,高速冲入吸收塔后,势必向入口对面的塔壁冲去并折流向上.由于高处仍有较大的气流速度差异.并且由于烟气刚性造成的偏流,使得在吸收塔的左上部和右下侧形成了两个明显的大旋涡.图4 为底层喷淋和顶层喷淋的模拟结果,其中忽略了烟气流动的影响.很明显,图4(b)所示顶层喷淋下来浆液的停留时间更长,因此气液接触时间也更长.从图4(a)可以看出,喷嘴排布设计达到了很好的截面覆盖率.并且各层喷嘴交错布置(如图1所示),这样可以照顾到最大的截面覆盖率,强化气液接触效果,为烟气的快速降温和高效洗涤创造了很好的条件.图5为气液两相流情况下的纵向中心截面的气相相场流线图(坐标用气流速度m/s表征).与图3纯气相时塔内明显偏流相比,在上百个实心锥喷嘴的大喷淋下,烟气偏流的情况得到了很好的克服,而且各层喷嘴互相交错、弥补了前一层可能的气流“短路”,因此气液接触效果很充分.可以看出,高温烟气起初以高速的刚性气流冲入吸收塔,但水平速度分量在大喷淋的作用下急剧衰减,还不到塔中心水平动量就消减得很小了,烟气转而垂直向上,和喷淋液呈逆向流动.与图3相比,图5中底层喷淋上部的烟气速度已趋向一致,烟气偏流导致的高速区也消失,气相在塔中的“充满度”明显提高,消除了大部分旋涡;并且吸收塔出口处的气流速度也非常均匀.烟气在截面上分布均匀,在塔内的停留时间也越长,使气液接触效果趋好.图6 为气液两相流情况下纵向中心截面的压力分布图.可见,由于整流效果良好,因此烟气入口轴线以上的区域基本可视作平推流,即截面上的速度差异已经很小,可以认为基本只有垂直向上的速度分量.此时,压力分布云图上的等压线和烟气流动方向基本垂直.随着烟气向上流动,静压逐渐降低.图6中在吸收塔的右下侧有个压力最高区,对比图5可知,这是由于一部分烟气进入吸收塔后转而向下,朝浆液池冲去,受阻后又向上运动,致使在烟气入口对面的浆液池上部产生一个高压区.图7 为纵向中心截面的离散相浆液滴浓度分布(4 层喷淋).图中红色区域为纵向中心截面正好经过的喷嘴的出口浓度,由于恰为喷嘴的中心,因此离散相浓度最高.而对各喷嘴来说,沿喷射方向离散相浓度逐渐降低(这在图7最上两层喷嘴表现得尤为明显),这显然是喷嘴雾化和液滴扩散的体现.由图7可见,底层喷淋以下的浆液高质量浓度区域范围最大,因为各层喷淋的浆液最终都叠加到喷淋塔下部;沿轴向向上则逐层降低,顶层喷淋的浆液滴质量浓度最低,这和实际情况是吻合的.由图7还可发现,在烟气入口处形成了一个斜向下呈“带状”的液滴质量浓度高值区.这主要是由于原烟气的高速冲入,使得浆液滴改变原先垂直下降的轨迹,而产生一个水平侧向的动量;同时,也因为高温烟气将一部分浆液蒸发,使得对应高温区域的离散相质量浓度降低.3.2气液两相传热的模拟结果图8为纵向中心截面和塔体入口水平中心截面的气相温度分布图.由图8可见,高温烟气冲入吸收塔后,在浆液大喷淋的作用下,被快速冷却到接近饱和温度(52,℃).吸收塔中大部分区域都处于冷却后的温度(冷却终温),只有靠近吸收塔入口处的区域有明显的温度梯度.基本在第1层喷淋以下就完成了烟气冷却过程.在计算过程中,对温度梯度变化明显的地方采取了网格加密.图9为纵向中心截面的水蒸气质量分数分布图.将其与图8对比可发现,温度场分布和水蒸气浓度场分布非常相似.即喷淋液蒸发冷却的过程就是烟气的降温增湿过程,水滴的蒸发相变最终使烟气中的水蒸气浓度达到接近饱和,净烟气温度和大喷淋浆液的温度基本一致.可以近似认为,喷淋浆液的蒸发量和烟气的增湿量是相等的(不考虑烟气出口少量的细液滴夹带).m3/h时(烟气初始温度、湿度同前)、经过4层喷淋后的纵向中心截面的气相温度分布.可见随着烟气量增大,温度梯度变化的区域不断扩大.6×105m3/h烟气量时,温度梯度变化区域在塔体径向仅为吸收塔的1.4倍直径;而在1.4×106,m3/h烟气量时,温度梯度变化区域在塔体左下部已经扩大到吸收塔的中轴线.因此,烟气量越大,同一塔体内的高温区范围也越大.一般来说,塔内烟气温度越高越不利于脱硫效率的提高,由此也说明了为什么大烟气量下要保持、提高脱硫效率就更困难的事实.已有文献[10-12]往往以脱硫塔内温度均一为前提进行模拟计算,本文的模拟则证明塔内的温度不均匀性恰恰是无法忽略的.因为气液间传质的关键参数,如扩散系数、平衡浓度、亨利系数等都和温度密切相关,故忽略温度场的不均匀性就势必会导致传质计算的偏差和不精确性.图10(b)与10(a)的工况相对应,为纵向中心截面的气相水蒸气质量分数分布图.与图10(a)的温度梯度变化相仿,随着烟气量的增大,塔内的湿度梯度变化区域范围也不断增大.可见随着烟气量的增大,气液两相最终完成降温增湿过程的空间区域是不断扩大的.吸收塔内烟气降温的过程实则就是烟气-浆液之间的热湿交换过程,烟气温度降得越低,浆液蒸发总量就越大,烟气的增湿程度也就越大.这种传热与传质的耦合关联,使得可以用脱硫后净烟气的湿度大小来印证烟气降温的效果.图12即为数天内现场吸收塔的排烟湿度(净烟气中水蒸气的体积分数)的截屏曲线和模拟数值的对比.实测数据对应的现场工况虽略有波动,但原烟气参数基本上为:烟气量1.2×106m3/h,原烟气温度130,℃,原烟气中水蒸气的体积分数7%;数值模拟也按照这个工况进行仿真.由图12可见,脱硫后净烟气中水蒸气的体积分数从7%增至12%~13%,已基本达到饱和.图中的模拟数值略低于实际运行曲线,原因可能是模型中在0~100℃之间取了10个温度点来给定水的饱和蒸汽压,模拟过程中其余温度点的蒸汽压通过插值的方法自动计算得到,由此可能会引起一些偏差.但总体来说,数值模拟结果和现场实测的运行曲线相吻合,模拟结果的正确性得到了现场实测数据的检验.4结论本文采用计算流体力学方法对大型脱硫塔的喷淋段进行仿真,模拟过程中充分考虑了气液两相间的耦合作用(传质、传动量和传热过程),得出了详细的气液两相流场和温度场、水蒸气组分场的分布规律,并和现场实际运行数据进行对比.(1)良好的喷淋层设计和喷嘴布置能极大地消除刚性烟气高速冲入吸收塔后形成的旋涡区,从而对烟气流动起到很好的整流作用;防止烟气短路的同时,强化了气液接触的效果.(2)吸收塔内采用实心锥喷嘴喷淋时,烟气入口轴线以上(或底层喷淋层以上)的区域基本可视作平推流,气相压力等势线和纵轴线基本垂直.(3)原烟气的高速冲入对浆液滴的运动轨迹产生了明显的影响,由此在烟气入口处形成了一个斜向下呈“带状”的液滴浓度高值区.(4)高温烟气冲入喷淋塔后,由于多层浆液大喷淋的洗涤,使烟气冷却过程在较短的时间内得以完成.喷淋塔内温度梯度变化较大的区域靠近吸收塔的入口,随着烟气量逐渐增大,温度梯度变化区域不断扩大.由此证明,以往文献中将塔内视为等温条件来进行计算或模拟将会带来误差,结果不精确.(5)喷淋塔内的气相温度场梯度变化和水蒸气浓度场梯度变化有明显的一致性规律,证明了塔内的主要降温过程为蒸发冷却.。
氨法脱硫专业技术在烧结烟气治理领域应用研究
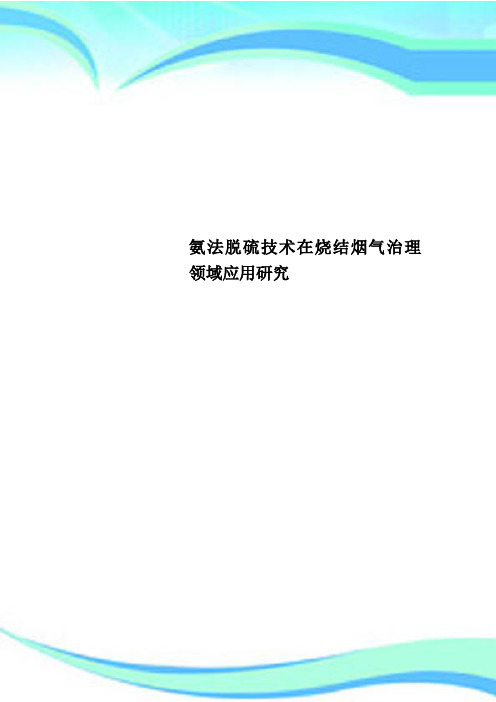
氨法脱硫技术在烧结烟气治理领域应用研究————————————————————————————————作者:————————————————————————————————日期:氨法脱硫技术在烧结烟气治理领域应用研究来源:环境工程更新时间:11-19 10:29 作者: 冷廷双时朝昆廖洪强卢慎敏摘要:LS 氨法烟气脱硫技术是一种在传统基础上进行改进的湿法烟气脱硫技术。
以66 m2 烧结机烟气治理方案为例, 分析LS 氨法烟气脱硫技术各项技术指标,同时对该方法脱硫技术特点、经济运行进行全面分析。
通过论述得出结论, LS 氨法烟气脱硫技术是一种适合于冶金行业烧结机烟气治理的一项湿法技术。
关键词:LS 氨法,烧结烟气,脱硫1 概述我国钢铁行业烧结烟气的治理主要集中在除尘方面,随着环保要求的日益提高,尤其对二氧化硫的排放浓度与排放总量进行了严格控制以后,烧结烟气脱硫逐渐引起了企业的重视。
我国烟气脱硫的研究与工程应用在20 世纪70 年代开始,但真正近20 年才进入了高速发展期,这期间主要集中在电厂的锅炉烟气脱硫。
钢铁行业进行烧结机的烟气脱硫从2003 年后才逐渐走上日程,经过5 年的发展,目前国内上马烧结机烟气脱硫工程的钢铁企业已经有10 余家,涉及烧结机有20 余台。
从电厂锅炉应用的经验来看,成熟的烟气脱硫技术主要有干法和湿法两种。
干法的主要代表工艺有循环流化床工艺、密相干塔工艺、NID 工艺;湿法的主要代表工艺有石灰石- 石膏法、氨法脱硫工艺、镁法脱硫工艺。
与此相对应的烧结烟气脱硫技术也主要以这两种脱硫工艺为主,以上提到的两种工艺均有在国内钢铁企业烧结机应用的实例。
湿法脱硫、半干法脱硫工艺技术参数见表1。
干法与湿法两种脱硫工艺均有比较明显的优缺点:干法脱硫工艺投资小、占地面积小、运行费用低但同时也有运行不稳定,脱硫效率不高的特点。
湿法脱硫工艺占地面积大、投资大、容易腐蚀但运行稳定、脱硫效率高。
本文主要针对湿法烟气脱硫技术中LS 氨法技术进行介绍。
焦炉煤气脱硫吸收塔两相流场计算流体力学数值模拟
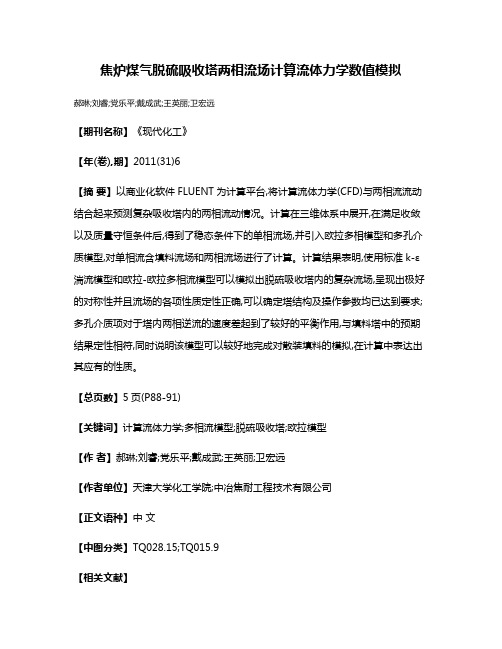
焦炉煤气脱硫吸收塔两相流场计算流体力学数值模拟
郝琳;刘睿;党乐平;戴成武;王英丽;卫宏远
【期刊名称】《现代化工》
【年(卷),期】2011(31)6
【摘要】以商业化软件FLUENT为计算平台,将计算流体力学(CFD)与两相流流动结合起来预测复杂吸收塔内的两相流动情况。
计算在三维体系中展开,在满足收敛以及质量守恒条件后,得到了稳态条件下的单相流场,并引入欧拉多相模型和多孔介质模型,对单相流含填料流场和两相流场进行了计算。
计算结果表明,使用标准k-ε湍流模型和欧拉-欧拉多相流模型可以模拟出脱硫吸收塔内的复杂流场,呈现出极好的对称性并且流场的各项性质定性正确,可以确定塔结构及操作参数均已达到要求;多孔介质项对于塔内两相逆流的速度差起到了较好的平衡作用,与填料塔中的预期结果定性相符,同时说明该模型可以较好地完成对散装填料的模拟,在计算中表达出其应有的性质。
【总页数】5页(P88-91)
【关键词】计算流体力学;多相流模型;脱硫吸收塔;欧拉模型
【作者】郝琳;刘睿;党乐平;戴成武;王英丽;卫宏远
【作者单位】天津大学化工学院;中冶焦耐工程技术有限公司
【正文语种】中文
【中图分类】TQ028.15;TQ015.9
【相关文献】
1.脱硫系统吸收塔内部流场数值模拟 [J], 顾永正;李旭;马士庆
2.脱硫吸收塔空塔流场的简单数值模拟 [J], 齐骥
3.氨法烟气脱硫吸收塔流场数值模拟 [J], 翁建鑫; 华玉龙; 周灵霞; 华宽
4.湿式烟气脱硫系统吸收塔扰流泵技术三维流场的数值模拟 [J], 杨龙
5.脱硫吸收塔深度除尘气液两相流数值模拟研究 [J], 蒋楠;厉雄峰;葛春亮;刘文榉;李晨朗;王先董
因版权原因,仅展示原文概要,查看原文内容请购买。
- 1、下载文档前请自行甄别文档内容的完整性,平台不提供额外的编辑、内容补充、找答案等附加服务。
- 2、"仅部分预览"的文档,不可在线预览部分如存在完整性等问题,可反馈申请退款(可完整预览的文档不适用该条件!)。
- 3、如文档侵犯您的权益,请联系客服反馈,我们会尽快为您处理(人工客服工作时间:9:00-18:30)。
烧结烟气氨法脱硫塔气液两相流数值模拟研究温荣耀1,刘克俭1,魏进超1(1.中冶长天国际工程有限责任公司,410007)[ 摘要] 氨法脱硫是目前广泛应用的烧结烟气脱硫技术。
脱硫塔是氨法脱硫系统的核心设备,塔内的气液分布情况对脱硫效率至关重要。
本文选用FLUENT作为计算工具,以烧结烟气氨法脱硫塔作为研究对象,对塔内气相湍流采用Euler方法描述,对喷淋液滴采用Lagrange颗粒轨道模型描述,研究烟气入口倾角、烟气入口距离浆液池液面高度对脱硫塔内气液两相流场的影响,并对脱硫塔的关键参数取值给出合理建议。
[ 关键词] 氨法脱硫塔;气液两相流;数值模拟;参数优化Numerical Simulation of Two-phase flow in Desulfurization Tower of Sintering Flue Gas AmmoniaProcessWen Rongyao1, Liu kejian1,Wei jinchao1( 1.Zhongye Changtian International Engineering Co.,Ltd,410007)[ Abstract ] Ammonia process is now widely used in desulfurization of the sintering flue gas. The desulfurization tower is the key equipment of a FGD system, and its internal flow is important for increasing the desulfurization efficiency. The commercial computational fluid dynamic software FLUENT is used to analyze the two-phase flow in a sintering flue gas desulfurization spray tower. The Euler-Lagrange method is used to describe the gas flow and the motion of the liquid droplets is described with the particle trajectory model. The influence of different inlet angles and different inlet heights of the sintering flue gas on the flow field in the desulfurization spray tower are studied and the optimal range of the inlet angle and the inlet height are obtained accordingly.[ Keyword ] desulfurization tower; two-phase flow; numerical simulation; parameter optimization1 前言一般情况下,钢铁企业SO2排放总量的40%~60%来自烧结过程,因此做好烧结过程中SO2的排放控制是钢铁企业污染治理的重点。
烟气脱硫国产化是降低工程造价、治理SO2、发展环保产业的需要。
氨法脱硫工艺是国内外烟气脱硫常用的成熟工艺。
氨法烟气脱硫工艺中脱硫塔主要选用喷淋塔,这是因为相对于其它吸收装置,喷淋塔除脱硫效率高外,还具有压降小、内构件相对较少和不易结垢等优点。
实际运行表明,喷淋塔的内部流场会直接影响着脱硫塔内的压降、脱硫效率及除雾效率等关键指标。
因此,对塔内流场的模拟研究成为设计中的重要手段。
利用计算流体力学软件FLUENT,本文建立了脱硫塔计算模型,将烟气作为连续介质,采用Euler方法描述,将喷淋浆滴作为离散颗粒,采用Lagrange颗粒轨道模型描述,研究烟气入口倾角、烟气入口距离浆液池液面高度两个参数对脱硫塔内气液两相流场的影响。
2 脱硫塔模型的建立2.1 物理模型烧结烟气氨法脱硫工艺如图1所示。
烟气进入脱硫塔前,先经过喷淋降温,此后由底部进口进入塔体,在上升过程中依次经过4个喷淋层。
脱硫浆液由布置于喷淋层的雾化喷嘴引入,与烟气形成逆流接触。
经过洗涤之后的烟气进入除雾段,除去烟气夹带的微小液滴,最后烟气进入烟囱排放,而吸收SO2之后的喷淋液下落至浆液池,循环利用。
图1 烧结烟气氨法脱硫工艺 2.2 模型简化对该脱硫塔内烟气与浆液滴两相流动情况作如下假设和简化:(1) 不考虑塔内喷嘴、喷淋层的几何尺寸等组件对塔内气液流场的影响;(2) 喷淋塔模拟区域为浆液池液面以上至除雾器下端,认为浆液为反射面、除雾器出口为等压面;(3) 烧结烟气为不含尘的洁净烟气;(4) 烟气视为不可压缩牛顿流体;(4) 流动为三维、定常,湍流为各向同性;(5) 忽略塔内存在的化学反应;(6) 假设喷淋液滴为球形;2.3 数学模型对脱硫塔进行物理上的简化之后,需要从数学的角度建立控制方程组,并将其离散化、线性化以进行迭代求解。
(1) 连续性方程(2)动量方程(3) 能量方程2(()()2t D v e d q r T f V P V D τρρρ+=+∇⋅∇+⋅+∇⋅⋅(4) 标准ε−k 模型(5)颗粒的作用力平衡方程 不考虑液滴颗粒附加质量力、布朗力、升力,考虑流体对颗粒曳力,由于塔内温度梯度的存在,也考虑热泳力。
3 边界条件(1) 烟气边界条件烟气进口流速12 m/s ,密度1.03 kg/m3,入口温度60°C ,出口压力200Pa 。
(2) 喷淋液滴边界条件喷淋塔内布置了4层喷嘴,每层53个,喷嘴形式为中空锥形,喷射角度为90°。
喷嘴采用cone 射流雾化模型,喷嘴出口液滴速度为5.98m/s ,液滴尺寸采用Rosin-Rammler 分布描述,中位径2650µm ,分布指数2.99。
(3) 壁面边界条件壁面采用绝热边界,液滴与壁面的接触为escape 逃逸。
4 模拟结果与分析仿真表明,烟气入口倾角和烟气入口距离浆液池液面高度对塔内气液流动情况有显著的影响。
4.1 不同烟气入口倾角的仿真结果选取烟气入口角度分别为3°、6°、9°、12°、15°条件下,得到的塔内纵截面流场如图2~图6所示。
图2 进口倾角3°纵截面 图3 进口倾角6°纵截面 图4 进口倾角9°纵截面图5 进口倾角12°纵截面 图6 进口倾角15°纵截面对入口角度分别为3°、6°、9°、12°、15°的塔内流场分析发现:随着烟气入口角度的增加,塔内左右侧壁面附近的垂直方向的气流速度不断增加,15°时最为明显,可以看出15°时已经出现了明显的气流短路现象,这对SO2的吸收极为不利,应尽量避免。
塔内中间区域流场变化不明显,烟气在进入吸收塔后在浆液上方产生一个巨大的回流低压区,气流产生巨大的离心力,对于除尘来说是非常有利的,烟气在塔前喷淋液作用下,烟气中的粉尘被打湿,比重增加,部分发生了凝聚,进入塔内之后在这个巨大的离心力作用下甩向入口对面塔壁面以及下部浆液池液面上。
但是对于气流分布来说是一个不利影响,巨大的回流区的存在使得靠近入口对塔内左右侧壁面的气流速度增加,容易造成气流短路,同时回流区的存在还会伴随着能量的消耗,增加了喷淋塔的阻力。
入口角度分别为 3°、6°、9°、12°、15°时进出口压力损失如图7所示,3°时的压力损失明显大于6°、9°、12°、15°的压力损失,原因是入口角度较小,气流几乎是对着入口对面的塔壁面冲过去,在这个过程中损失掉很大一部分能量。
图7 不同入口角度的进出口压力损失综合考虑塔内流场均匀性和压力损失,最佳的入口烟气角度应该在9°附近。
4.2 烟气入口距浆池液面不同高度的仿真结果选取烟气入口距浆池液面高度分别为0.7m 、1.7m 、2.7m 、3.7m ,得到塔内纵界面流场情况如图8~图11所示。
图8 进口高0.7m 纵截面 图9进口高1.7m 纵截面 图10 进口高2.7m 纵截面 图11进口高3.7m 纵截面对烟道底面距液面高度分别为0.7m、1.7m、2.7m、3.7m的塔内流场分析发现:烟道底面距液面高度为0.7m时,塔内左右侧壁面附近垂直方向的气流速度最小,整个塔的断面速度分布非常均匀,有利于对SO2的吸收,而烟道底面距液面高度1.7m时,塔内左右侧壁面附近垂直方向的气流速度最大,可以看出烟道底面距液面高度1.7m时已经出现了明显的气流短路现象,这对SO2的吸收极为不利,应尽量避免,随着高度的增加这种趋势慢慢的变小,到3.7m时已经没有明显的大面积气流短路。
塔内液面上方区域流场变化明显,除烟道底面距液面高度为0.7m外,烟气在进入吸收塔后在浆液上方产生一个巨大的回流低压区,随着烟道底面距液面高度增加回流区面积越来越大,在回流区气流产生巨大的离心力,对于除尘来说是非常有利的,烟气在塔前喷淋液作用下,烟气中的粉尘被打湿,比重增加,部分发生了凝聚,进入塔内之后在这个巨大的离心力作用下甩向入口对面塔壁面以及下部浆液池液面上,粉尘随之而除去。
但是对于气流分布来说是一个不利影响,巨大的回流区的存在使得靠近塔内左右侧壁面的气流速度增加,容易造成气流短路,同时回流区面积的增加还会伴随着能量的消耗,增加了吸收塔的阻力。
烟道底面距液面高度分别为0.7m、1.7m、2.7m、3.7m时进出口压力损失如图12所示,可见0.7m(830.85Pa)和3.7m(843.21Pa)时的压力损失明显大于1.7m、2.7m的压力损失,造成这两个差别的原因是不同的,烟道底面距液面高度0.7m时,液面上方的空间不利于形成回流区,气流几乎是对着入口对面的塔壁面冲过去,在这个过程中大部分的动能损失掉。
而3.7m时这个高度很大,形成的回流漩涡区面积最大,相应损失的能量也大。
图12 不同入口烟道距离浆液高度的进出口压力损失综合考虑塔内流场均匀性和压力损失,最佳的入口烟道距离浆液的高度应该在2.7m附近。
结论(1) 为了得到最佳的塔内气液流场,最佳的烟气入口倾角在9°附近。
(2) 为了得到最佳的塔内气液流场,最佳的烟气入口距离浆池液面高度在2.7m附近。