高碳钢大方坯连铸水冷工艺参数优化试验研究
连铸坯热装热送中的冷却水循环系统优化策略

连铸坯热装热送中的冷却水循环系统优化策略连铸坯热装热送中的冷却水循环系统是钢铁生产过程中一个至关重要的环节。
它对连铸坯的质量和生产效率具有直接的影响。
为了提高连铸坯的质量和生产效率,我们需要优化冷却水循环系统的操作策略。
本文将探讨连铸坯热装热送中的冷却水循环系统优化的一些策略。
一、优化冷却水流量控制策略冷却水流量控制是冷却水循环系统中最基本的操作之一。
合理的冷却水流量控制可以保证连铸坯在冷却过程中获得足够的冷却效果,同时避免流量过大导致资源的浪费。
在优化冷却水流量控制策略时,我们可以考虑以下几个方面。
首先,根据连铸坯的尺寸和材料特性,确定合理的冷却水流量范围。
其次,通过监控连铸坯的温度变化和冷却水流量的实时数据,调整冷却水流量,保证连铸坯的冷却效果。
最后,结合连铸坯的生产进度和产能要求,灵活调整冷却水流量,合理分配资源,提高生产效率。
二、优化冷却水温度控制策略除了合理控制冷却水流量外,冷却水的温度也是影响连铸坯冷却效果的重要因素。
优化冷却水温度控制策略可以提高连铸坯的冷却质量,降低能耗。
在优化冷却水温度控制策略时,我们可以考虑以下几个方面。
首先,根据连铸坯的尺寸和材料特性,确定合理的冷却水温度范围。
其次,通过监控连铸坯的温度变化和冷却水温度的实时数据,调整冷却水温度,保证连铸坯的冷却效果。
最后,结合连铸坯的生产进度和产能要求,灵活调整冷却水温度,降低能耗,提高生产效率。
三、优化冷却水循环系统的管道布局冷却水循环系统的管道布局是影响冷却水流动和循环效果的关键因素之一。
合理的管道布局可以减小冷却水流阻力,提高冷却水的流动速度和循环效果。
在优化冷却水循环系统的管道布局时,我们可以考虑以下几个方面。
首先,合理规划冷却水循环系统的管道走向,避免死角和复杂的弯曲装置。
其次,选择合适的管道材料和直径,降低冷却水的流动阻力。
最后,定期清洗管道,确保冷却水的流通畅通,提高循环效果。
四、优化冷却水循环系统的水质管理冷却水循环系统的水质管理是确保冷却水质量稳定的重要措施。
高碳钢连铸方坯质量控制

高碳钢连铸方坯质量控制蔡开科1.前言高碳钢制品入钢轨,硬线,钢丝等广泛应用于国民经济各个部门。
对高碳钢制品要求是:抗拉强度高,可承载较重的震动载荷承载能力大,使用安全可靠在高速条件下工作,运转平稳有良好的抗压性,耐磨性,耐腐蚀性等目前高碳钢生产有两件工艺:BOF(EAF)-LF(VD)-bloom大方坯BOF(EAF)-LF-Billet小方坯不管那种工艺,为获得高质量的产品,必须得到高质量的连铸坯。
(1)高的洁净度,非金属夹杂物类型,数量,尺寸分布如表1表1 洁净度要求硬线钢由于夹杂易造成的冷拔断裂如图1图1 夹杂物所致冷拔断裂重轨钢,滚珠钢由于脆性夹杂产生疲劳裂纹而断裂(2)铸坯良好的低倍结构要紧是指中心缺陷(锻孔,疏松,中心偏析)。
硬线钢的杯锥状断裂(图2)是由中心偏析所致图2 杯锥状断口硬线钢劈裂状断口(图3)要紧是由中心疏松缩孔引起的。
图3 劈裂状断口重轨钢由于中心偏析(C.S)而产生轨腰的断裂(图4)图4 钢轨形貌2.铸坯中夹杂物操纵当钢水凝固成固体后,铸坯中夹杂物数量就无法改变了。
因此铸坯中夹杂物决定于炼钢-精炼-连铸的全过程。
炼钢是一个氧化过程,钢中夹杂物可用总氧T[O]来评判:T[O] = [O]D + [O]I出钢时:钢水中[O]I→O T[O] = [O]D=a[O]脱氧合金化后:[O]D(a[O])→O T[O] = [O]I由此,可用总氧T[O]来表示钢的洁净度,也确实是夹杂物水平。
为使钢中夹杂物少,必须操纵钢T[O],为此(1)降低[O]D,转炉终点a[O](2)降低[O]I,脱氧(夹杂物工程),精炼(3)防止钢水再污染:连铸过程2.1转炉终点氧操纵转炉终点a[O]是产生夹杂物的源头。
重点a[O]决定于:[C]终渣中(FeO)钢水温度图5 转炉终点钢中[C]与a[O]关系关于中高碳钢转炉终点操纵方法:低拉碳增碳法高拉碳补吹法两种方法结果比较于表2表2 低拉碳与高拉碳结果比较由表可知高拉碳法特点:增C量小,成品C波动小终点a[O]低对铁水S,P要求研低拉碳法特点:对铁水S,P要求可放宽些有利于脱S,P终点a[O]高增C量大,碳粉收得率不稳,成品C波动在±0.05%以上两种方法各有优缺点,各厂依照具体条件决定采纳哪种方法。
武钢SWRH82B高碳钢连铸坯中心偏析的研究

根据实际测试数据得到的平均碳偏析指数分别为1.18和1.41,即偏析钢的碳含量分别为0.96%和1.16%。在实验室按前两种碳含量冶炼出相应的钢试样并分别编号为1号和2号,试样在Gleeble2000热模拟实验机上加热至900℃奥氏体化5min,然后以不同的冷却速度进行冷却得到不同冷却速度下的组织。
降低连铸坯中心偏析的措施
降低钢水的过热度;
末端电磁搅拌
轻压下
重压下(未采用)
通过采用降低钢水过热度和轻夺下的措施,SWRH82B铸坯中心的碳偏析得到明显改善,平均偏析系数达到1.06,偏析系数小于1.10的比率稳定在70%以上。
根据试验结果绘制钢的CCT曲线,并对正常和偏析的SWRH82B的CCT曲线进行比较。结果显示,正常SWRH82B钢的冷速在2-5℃/S,此时钢的强度满足要求,索氏体化也最高;2号偏析钢不出现马氏体的冷速为≤2℃/S,因为盘条中心在控制冷却中的冷速比边缘要小,因此,适当调整控冷工艺就可在铸坯中心碳偏析指数不大于1.12级综合偏析指数不大于1.20的情况下,在控冷时,盘条中心比正常SWRH82B钢稍后一点形成正常组织,不会形成马氏体。若铸坯中心偏析指数大于1.12及综合偏析指数大于1.20,在盘条控冷时,中心部分要形成正常组织,就要使盘条中心的冷却速度比盘条其它部位的冷速慢得多(≤0.5℃/S),而这实际上办不到,因此在此处情况下会形成中心马氏体,因为盘条的直径只有5.5-20mm,为了保证得到正常组织,该钢必须轧后快冷,这就使盘条中心不会比其它部位的冷速慢很多,只可能稍慢一点。因此,可初步判定该钢的最高铸坯中心偏析指数不应大于1.12及综合偏析指数不应大于1.20。
0.65-0.85
≤0.025
≤0.020
≤0.20
连铸坯热装热送中的冷却水循环系统优化方案

连铸坯热装热送中的冷却水循环系统优化方案在连铸工艺中,冷却水循环系统扮演着关键的角色。
它通过对连铸坯进行冷却,有效控制坯料温度,确保铸造质量和生产效率。
本文将针对连铸坯热装热送中的冷却水循环系统提出优化方案。
一、现状问题分析在连铸坯热装热送过程中,冷却水循环系统存在一些问题。
首先,水循环系统的流量调节不够灵活,无法根据连铸坯的不同要求进行精确调整。
其次,由于冷却水中存在悬浮物和杂质,会导致管道堵塞、水泵损坏等问题。
此外,冷却水的温度也需要在一定的范围内进行控制,以保证连铸坯的质量。
二、优化方案为解决上述问题,可以采取以下优化方案:1. 系统流量调节优化引入智能流量控制器,通过传感器感知连铸坯的温度和速度等参数,精确调节冷却水的流量。
根据不同的铸造要求,自动调整水的流速,以实现坯体的均匀冷却。
同时,结合先进的调节算法,动态跟踪坯体温度变化,及时调整水温和流量,以确保铸造质量。
2. 悬浮物过滤处理在系统的进水口设置合适的过滤装置,及时去除冷却水中的悬浮物和杂质。
可以采用微孔滤网等过滤器,有效阻止固体颗粒进入系统,减少管道堵塞和水泵损坏的风险。
此外,定期对过滤器进行清洗和更换,保证其正常工作。
3. 温度控制手段改进运用先进的温度控制技术,通过空气冷却和冷却剂循环等方式,确保冷却水的温度在一定的范围内稳定控制。
可以采用温度传感器实时监测水温,通过PID控制算法进行精确调节。
同时,根据连铸坯的特点和要求,合理设定温度范围,以保证坯体的冷却效果。
4. 系统检修与维护加强冷却水循环系统的检修与维护,定期对设备进行巡检和保养,及时发现和处理问题。
定期清洗水泵、管道和冷却器,确保系统的正常运行。
此外,需要制定完善的操作规程,培训操作人员,提高其对系统的了解和应急处理能力。
三、效果与可行性分析通过以上优化方案的实施,可以取得以下效果:1. 提高冷却水循环系统的灵活性,根据连铸坯的不同要求进行精确调节,提高生产效率和产品质量。
连铸二次冷却工艺的优化

R9m方坯连铸二次冷却工艺的优化发布时间:2006年12月7日1 前言山东石横特钢集团有限公司(简称石横特钢)现有R9m四机四流连铸机1台,浇注钢种有:碳素结构钢、合金结构钢、高碳钢、焊条钢等,生产150mm×150mm方坯供高速线材车间,其质量要求严格。
而方坯连铸二次冷却与铸坯质量有密切关系,在生产优钢过程中,由于二次冷却制度不当,出现一些铸坯缺陷:(1)内部裂纹,在二冷区,如果各段冷却不均匀,部分回温太大,或冷却强度大,都会导致内部裂纹。
(2)铸坯菱变(脱方),二冷区铸坯四个面的非对称性冷却,造成某两个面比另外两个面冷却得更快,在冷面产生沿对角线的应力,加重铸坯扭转,产生菱变。
(3)铸坯鼓肚,如二次冷却太弱,铸坯表面温度过高,钢的高温强度较低,在钢水静压力作用下,凝固壳就会发生蠕变而产生鼓肚。
(4)表面裂纹,由于二冷不当,矫直时铸坯表面温度低于900℃,刚好位于“脆性区”,再有AlN、Nb(CN)等质点存在,容易在振痕波谷处产生表面裂纹。
2 二次冷却工艺优化2.1 连铸坯配水基本原则铸坯出结晶器后,随二冷水喷向铸坯,凝固壳厚度加厚,其依据规律为:δ = K(τ)1/2 (1)式中δ——铸坯厚度;K——凝固系数;τ——凝固时间。
由式(1)可知:铸坯厚度δ是随凝固时间τ的平方根而增加,凝固壳厚度达到一定时,坯壳传热成为坯壳增长的限制环节,坯壳厚度越大,传热阻力增加,温差也越大。
因而冷却水量应随铸坯厚度δ的增加而降低,即二冷水量Q与铸坯厚度δ成反比。
所以不同位置的水量Q与(τ)-1/2成正比。
而τ ∝s/v(s为结晶器液面到二冷区某一点的长度,v为拉速),所以:Q ∝(s/v)-1/2 (2)当拉速v一定时,二冷水量Q与结晶器液面到二冷区某一点的长度s的平方根成反比,由此得到结论:二冷配水冷却水量沿铸坯方向从上到下应是逐渐减少的。
2.2 不同钢种二冷水的设定对于不同钢种,因其冷却特性不同,其二冷配水制度应该不同。
连铸坯热装热送中的冷却水循环系统优化

连铸坯热装热送中的冷却水循环系统优化连铸是钢铁生产过程中重要的工艺环节,而冷却水循环系统在连铸坯热装热送中起到了至关重要的作用。
为了优化该系统的性能,提高连铸坯质量和生产效率,以下是对连铸坯热装热送中的冷却水循环系统优化的详细分析。
一、系统概述连铸坯热装热送中的冷却水循环系统由循环水泵、冷却器、冷却水管道、水箱等组成。
其主要功能是将高温的连铸坯冷却成一定温度以便顺利进行后续工序。
二、优化目标1. 提高冷却水的循环效率,减少水的消耗。
2. 控制冷却水的温度稳定性,以确保连铸坯冷却效果。
3. 降低系统运行的能耗,减少生产成本。
三、优化措施1. 水泵系统优化a. 选择高效节能的循环水泵,提高水泵的效率,降低能耗。
b. 采用变频控制技术,根据实际冷却需求调整水泵的运行速度,减少能耗。
2. 冷却器优化a. 选用大面积高效的冷却器,增大冷却面积,提高冷却效果。
b. 定期清洗冷却器,防止堵塞,保证冷却器的正常工作。
3. 冷却水管道优化a. 采用优质材料制作冷却水管道,减少泄漏,提高系统的运行稳定性。
b. 对冷却水管道进行维护和检修,确保水流畅通,减少阻力。
4. 水箱优化a. 设计合理的水箱容积,以满足系统的冷却需求,避免水位过高或过低。
b. 定期清洗水箱,清除杂质,保证水质的清洁和流通性。
5. 温控系统优化a. 安装合适的温度传感器,及时监测冷却水的温度。
b. 配置PID控制系统,根据实时温度数据对冷却水的供水和回水进行调节,保持稳定的温度,提高冷却效果。
四、优化效果通过以上优化措施的实施,连铸坯热装热送中的冷却水循环系统可以达到如下效果:1. 提高冷却水的循环效率,减少水的消耗,降低生产成本。
2. 控制冷却水的温度稳定性,确保连铸坯冷却效果,提高产品质量。
3. 降低系统运行的能耗,减少能源消耗,减轻环境负担。
总结:通过对连铸坯热装热送中的冷却水循环系统进行优化,我们可以有效提高连铸坯的质量和生产效率。
在实施优化措施的同时,需要注意系统的运行状态,并进行定期的维护和检修,以确保系统的正常运行。
大方坯连铸二次冷却工艺研究

大方坯连铸二次冷却工艺研究大方坯连铸二次冷却工艺是现代钢铁生产过程中重要的一部分,它是将原料连续铸造成长条形、宽板条型或其他形状的钢坯,再将其通过二次冷却的工艺精炼成各种形状的型材。
其主要特点有:高质量,高效率,绿色环保,低能耗,可以有效改善规格复杂的型材生产过程中的产品品质,节约能源,提高经济效益,满足多元化的需求。
一、大方坯连铸冷却工艺实现机制大方坯连铸二次冷却工艺分为两个主要阶段,即热处理阶段和冷却阶段。
热处理阶段:在这个阶段,钢坯经过精细煅烧,以提高坯体的力学性能。
其中,温度控制是调节材料性能的关键,温度的高低会影响材料的均匀性、微观结构、硬度等。
冷却阶段:在这个阶段,将已经加热的钢坯安装在专用的铸轧机上,然后通过冷却装置进行二次冷却,使其受热位移、变形膨胀和减薄膨胀回复形变等处理,最终得到熔融分离的长条或宽板条形。
二、连铸二次冷却工艺技术应用1.加工方面:连铸二次冷却工艺在加工方面,可以提供精密、灵活的加工对象,从而满足客户对型材外形质量及内外表面质量要求。
2.产量方面:连铸二次冷却工艺能满足客户的大批量订单要求,大大提高生产效率,提升经济效益。
3.产品质量方面:连铸二次冷却工艺能够有效改善型材内外表面质量,能达到抛光等级,提升产品品质。
4.技术先进性:连铸二次冷却工艺涉及技术比较复杂,在操作方面需要经验丰富的技术人员,生产时需要实时反馈、控制、调节,提高生产过程中的可靠性。
三、连铸二次冷却工艺部分设备1.冷却塔:冷却塔是连铸二次冷却工艺的核心设备,主要用于控制坯体的冷却温度,实现坯体表面温度的快速降温,控制坯体变形和减薄膨胀回复形变。
2.辊道:辊道是常用的连铸二次冷却工艺设备,主要用于拉伸坯体,实现改变坯体外形和精细加工坯体表面等。
3.焊接机:焊接机是连铸二次冷却工艺的支撑设备,主要用于连接各加工过程的设备,保证坯体的原位运动和防止污染。
4.水冷棒:水冷棒是一种现代的铸造工具,它可以根据客户的要求,调整坯体的厚度和形状,以达到精确的加工精度。
关于100t电炉连铸工程循环冷却水工艺的研究

24工业技术 在炼钢的过程中,对于水资源的利用及其处理成为一大难题。
钢铁企业在生产过程中的用水量是非常巨大的,但是我们需要了解的是工业用水和生活用水是有区别的,生活用水是需要层层审查的,特别是关乎人们身体健康的质量标准,而工业用水的审核标准与生活用水的检测标准相比就比较弱一些。
在炼钢过程中常常会涉及到循环冷却水的处理问题,在技术越来越发展的今天,传统的冷却方法出现了一定的弊端,运用新兴的工艺技术对其处理是非常必要的。
它与我国工业的进一步发展紧密相关,特别是钢铁企业,需要在循环冷却水处理的问题上进行技术性的革新,引进一些比较先进的处理设备。
本文结合个人多年实践工作经验,就此问题展开了分析并给出了具体的解决方案。
1 闭路软水循环系统 在软水循环系统中,温度差对于最后的处理结果是会有影响的,同时这里涉及到一个温度差的程度问题,温度差如果缩小到一定范围是没有影响的,当温度差超过这个范围,就会产生不利的影响,在高温差的情况下会发生高负荷热的现象,极易发生腐蚀,腐蚀现象对金属表面的损害是非常严重的,金属在直接接触水和空气的情况下会发生氧化反应,这种情况一旦发生,只能采取除锈的措施,然而除锈的过程也是对金属表层一个损耗的过程,长此以往,对于金属来说是一种极大的损害。
在这种情况下,对于设备来说也会产生一定程度的威胁,此外,还会影响到工作的正常进行,生产安全的性能会减弱。
因此软水的认真选择是非常必要的,一级软水虽然不能完全避免上述情况,但是可以在一定程度上有效地减小上述情况发生的几率。
在此就要用到闭路循环的装置,其安全性能大大加强。
2 大电流、变压器开路软水循环冷却系统 大电流、变压器开路软水循环冷却系统是其中的一个重要组成部分,这种系统的利用率是相当高的,它可以冷却的对象有多种,EAF 炉是其中一种常用的对象,除此之外,还有LF炉变压器以及液压站等等。
这里所涉及到的变压器是一种功率较高的变压器,大功率的设备往往会带来一些安全隐患,因此在使用过程中保障其安全性能是异常重要的,无压回水的形式是比较实用的,提升泵增压以后,冷却水会在一种高效率的情况下进行运行,此外,为进一步保障其安全性能,这里还设置了一种叫做事故供水的管路。
某钢厂连铸机铸坯冷却系统优化改造与应用
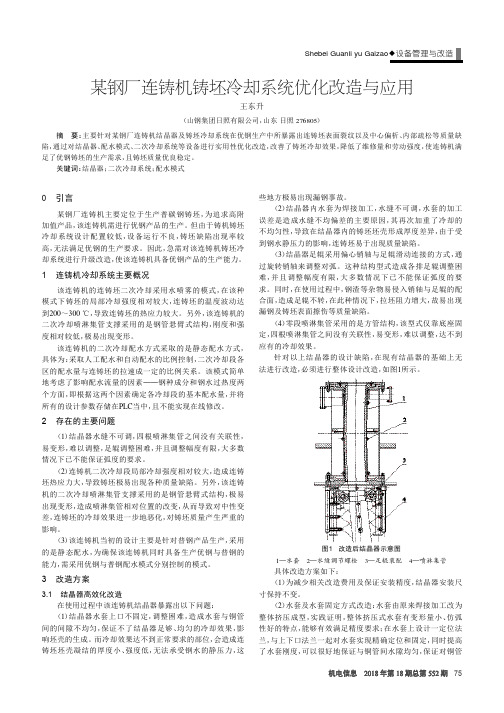
某钢厂连铸机铸坯冷却系统优化改造与应用王东升(山钢集团日照有限公司,山东日照276805)摘要:主要针对某钢厂连铸机结晶器及铸坯冷却系统在优钢生产中所暴露出连铸坯表面裂纹以及中心偏析、内部疏松等质量缺陷,通过对结晶器、配水模式、二次冷却系统等设备进行实用性优化改造,改善了铸坯冷却效果,降低了维修量和劳动强度,使连铸机满足了优钢铸坯的生产需求,且铸坯质量优良稳定。
关键词:结晶器;二次冷却系统;配水模式0引言某钢厂连铸机主要定位于生产普碳钢铸坯,为追求高附加值产品,该连铸机需进行优钢产品的生产。
但由于铸机铸坯冷却系统设计配置较低,设备运行不良,铸坯缺陷出现率较高,无法满足优钢的生产要求。
因此,急需对该连铸机铸坯冷却系统进行升级改造,使该连铸机具备优钢产品的生产能力。
1连铸机冷却系统主要概况该连铸机的连铸坯二次冷却采用水喷雾的模式,在该种模式下铸坯的局部冷却强度相对较大,连铸坯的温度波动达到200~300℃,导致连铸坯的热应力较大。
另外,该连铸机的二次冷却喷淋集管支撑采用的是钢管悬臂式结构,刚度和强度相对较低,极易出现变形。
该连铸机的二次冷却配水方式采取的是静态配水方式,具体为:采取人工配水和自动配水的比例控制,二次冷却段各区的配水量与连铸坯的拉速成一定的比例关系。
该模式简单地考虑了影响配水流量的因素———钢种成分和钢水过热度两个方面,即根据这两个因素确定各冷却段的基本配水量,并将所有的设计参数存储在PLC当中,且不能实现在线修改。
2存在的主要问题(1)结晶器水缝不可调,四根喷淋集管之间没有关联性,易变形,难以调整,足辊调整困难,并且调整幅度有限,大多数情况下已不能保证弧度的要求。
(2)连铸机二次冷却段局部冷却强度相对较大,造成连铸坯热应力大,导致铸坯极易出现各种质量缺陷。
另外,该连铸机的二次冷却喷淋集管支撑采用的是钢管悬臂式结构,极易出现变形,造成喷淋集管相对位置的改变,从而导致对中性变差,连铸坯的冷却效果进一步地恶化,对铸坯质量产生严重的影响。
对高碳钢连铸工艺的优化研究

对高碳钢连铸工艺的优化研究作者:张向东来源:《科技风》2018年第25期摘要:高碳钢又叫工具钢,其碳含量一般在0.6%到1.7%之间,能够淬火和回火。
在工业生产中高碳钢具有不可替代的作用,因此在智能化和机械化的高碳钢连铸工艺中,必须优化铸造工艺,提升高碳钢的质量。
本文通过对高碳钢的成分进行分析,提出了在高碳钢连铸中的工艺控制,希望能给炼钢企业有益的启示。
关键词:高碳钢;连铸工艺;优化高碳钢主要用来铸造各种精密的工具等,因此也被称为工具钢,在工业生产中高碳钢起到了其他钢不可替代的作用,高碳钢的碳含量一般在0.6%到1.7%之间,是一种特种特别坚硬的特种钢材,具有良好的淬火和回火的性能,平时生活中常见的大锤和撬棒就是利用高碳钢来制造的,碳含量约为075%,一些精密钻头和铰刀等切割工具也是由高碳钢制造而成,碳含量约为1%。
由于高碳钢在我国各个生产领域都有广泛的应用,因此很多钢厂都在进行高质量的高碳钢的生产,高碳钢的产量也在逐年增加,工艺水平也越来越高,尤其是现在伴随着连铸工艺的出现,在炼钢工艺中更应该注意在智能化、自动化和机械化的生产过程中实现高碳钢的质量控制。
1 高碳钢中添加成分的论述在工业炼钢生产的过程中,只加入一定量的碳元素不添加其他化合物,经过一定的加热处理,然后进行冷拔形成钢坯,在通过硬化处理手段就形成了高碳钢。
这种钢与其他钢的区别就在与硬度高、强度大。
而且高碳钢具有较好的弹性,磨损和切口的极限也较好,具备削切的功能,因此高碳钢在工业领域得到了广泛的应用。
社会生产对于高质量的高碳钢需求越来越高,对于钢厂来说必须不断提升高碳钢的产品质量,以高碳钢的连铸工艺为出发点,对炼钢过程中的成分添加进行分析。
不同的元素能够起到不同的化学作用,比如添加碳元素、硅元素、锰元素目的是增加钢的强度、硫元素的目的是增加钢的脆性等。
高碳钢的连铸工艺包含了复杂的反应过程,既有物理反应也有化学反应,因此在连铸过程中需要密切关注整个工艺流程,不同成分的配比要适当,由于在连铸工艺中需要与空气接触,因此还需要注意空气中不同元素对高碳钢的性能影响,主要是氧气、氮气等因素。
《特厚矩形坯连铸机二冷配水工艺的研究》范文

《特厚矩形坯连铸机二冷配水工艺的研究》篇一一、引言随着钢铁工业的快速发展,特厚矩形坯连铸机作为钢铁生产中的重要设备,其生产效率和产品质量直接影响到整个钢铁企业的经济效益。
二冷配水工艺作为连铸机的重要环节,对铸坯的质量和性能具有重要影响。
因此,对特厚矩形坯连铸机二冷配水工艺进行研究,具有重要的理论意义和实际应用价值。
二、特厚矩形坯连铸机概述特厚矩形坯连铸机是钢铁生产中的重要设备,主要用于生产特厚矩形坯。
其工作原理是通过熔融金属的连续浇注和凝固,形成一定规格的铸坯。
特厚矩形坯连铸机的运行效率和产品质量,直接影响到钢铁企业的经济效益。
三、二冷配水工艺的重要性二冷配水工艺是连铸机生产过程中的重要环节,对铸坯的质量和性能具有重要影响。
在二冷区,通过喷水冷却的方式对铸坯进行冷却,以达到控制铸坯质量和提高生产效率的目的。
二冷配水工艺的合理与否,直接影响到铸坯的质量和生产成本。
四、特厚矩形坯连铸机二冷配水工艺研究(一)研究方法本研究采用理论分析、数值模拟和实际生产相结合的方法,对特厚矩形坯连铸机二冷配水工艺进行研究。
首先,通过理论分析,研究二冷配水工艺的基本原理和影响因素;其次,利用数值模拟软件,对二冷配水工艺进行模拟分析;最后,结合实际生产数据,对模拟结果进行验证和优化。
(二)研究内容1. 二冷配水工艺的基本原理和影响因素研究。
通过理论分析,研究二冷配水工艺的基本原理和影响因素,包括喷水压力、喷水量、喷水角度等。
2. 数值模拟分析。
利用数值模拟软件,对特厚矩形坯连铸机二冷配水工艺进行模拟分析。
通过建立数学模型,模拟二冷区的喷水过程和铸坯的冷却过程,分析喷水参数对铸坯质量和生产效率的影响。
3. 实际生产数据验证与优化。
结合实际生产数据,对数值模拟结果进行验证和优化。
通过对比实际生产和模拟结果的差异,调整喷水参数和工艺流程,以达到优化生产的目的。
(三)研究结果通过本研究,得出以下结论:1. 二冷配水工艺的喷水压力、喷水量和喷水角度等参数对铸坯的质量和生产成本具有重要影响。
连铸方坯二冷冷却的优化及改进

连铸方坯二冷冷却的优化及改进发表时间:2020-11-27T07:52:34.796Z 来源:《防护工程》2020年23期作者:万占成[导读] 尤其是对内部质量提出了更高的标准,二次冷却问题受到越来越多的重视。
新疆伊犁钢铁有限责任公司炼钢厂新疆伊宁 835800摘要:本文介绍了新疆伊犁钢铁有限责任公司炼钢厂小方坯连铸优化二次冷却制度过程,并根据实践结果对二冷配水量控制等方面进行了分析,并对二次冷却配水参数进行了优化以及调整,使铸坯质量得到明显提高。
关键词:二次冷却的重要性;存在问题;优化过程1.前言连铸机的二次冷却系统起着对铸坯进行连续冷却,使其逐渐完全凝固的作用。
在连铸生产中,二次冷却系统对铸坯的表面质量、坯壳厚度均匀形成、矫直效果等都有至关重要的影响,因此连铸二冷技术对连铸生产过程顺行、产品质量和生产效率均有重要影响。
随着连铸技术的高速发展,以及市场对铸坯质量要求的不断提高,尤其是对内部质量提出了更高的标准,二次冷却问题受到越来越多的重视。
2存在问题在生产过程中,由于二次冷却制度不当,出现的铸坯缺陷有:1在二冷区各段之间冷却不均匀,铸坯表面温度呈现周期性的回升。
回温引起坯壳膨胀,当施加到凝固前沿的张应力超过钢的高温允许强度和临界应变时,铸坯表面和中心之间就会出现中间裂纹,从而导致铸坯出现内部质量问题。
2二冷区铸坯四个面的非对称性冷却,造成某两个面比另外两个面冷却得更快,铸坯收缩时在冷面产生沿对角线的压力,加重铸坯扭转,产生菱变,从而导致铸坯脱方加剧,制约了连铸的产量及钢坯质量。
3二次冷却太弱,铸坯表面温度过高,钢的高温强度较低,钢水在静压力作用下,凝固壳就会发生蠕变而产生鼓肚。
3原因分析及解决措施3.1二冷配水原则连铸机的生产率与铸坯质量在很大程度上取决于二次冷却。
为保证铸坯质量和产量,基于这两个方面的考虑,二次冷却都应遵循以下几个原则[1]:1上强下弱。
铸坯出结晶器后,在二冷上段坯壳薄、热阻小、坯壳收缩产生的应力亦小,这些条件有利于强冷以增加坯壳厚度,减少漏钢事故。
连铸二冷水系统的工艺优化

连铸二冷水系统的工艺优化【摘要】针对邯宝公司连铸二冷水系统由于喷嘴堵塞影响炼钢生产的原因进行了分析,通过技术改造、系统优化,取得了良好的效果,满足炼钢生产需求。
【关键词】连铸机喷嘴二冷水水质1 前言在连铸二冷水喷林系统中,喷嘴的堵塞是一个常见的现象,喷嘴的堵塞与产品质量的关系是十分密切的,一旦喷嘴严重堵塞,产品质量无法保证,严重时造成非计划停浇,甚至漏钢。
邯宝炼钢自投产以来,连铸二冷水系统经常出现自清洗过滤器及管道滤网的堵塞,系统循环率降低,连铸机喷嘴堵塞,管道腐蚀等现象,严重影响炼钢的正常生产,通过对该系统工艺优化、技术改进使得上述问题得以解决,满足了炼钢正常生产。
2 工艺流程邯宝炼钢有DANIELI连铸机2台,二次喷淋水系统共有喷头2000多个,系统用水由能源中心的钢轧泵站供给。
水系统的处理设备包括给水泵、自清洗过滤器、旋流井、稀土磁盘、平流池、多介质过滤器、冷却塔、冷水井等。
该系的工艺流程如图1。
3 二冷水系统存在问题及原因分析为解决水系统制约炼钢正常生产的问题,我们对该系统进行几个月的跟踪调查及水质分析,通过查问题、找原因,结合其它钢厂的使用情况初步确定二次喷淋冷却水系统影响炼钢生产的几个问题:3.1 二冷水系统水量不平衡主要由于设备间接冷却水不能形成有效循环大量泄露,进入浊环二冷水的循环系统,导致二冷水大量溢流,造成环境污染、水资源浪费、系统循环率降低、水质稳定无法保证。
3.2 设备及管道腐蚀,腐蚀产物堵塞喷嘴3.2.1 自身条件的腐蚀首先在炼钢生产过程中的保护渣中含有大量的氟化钙在高温条件下与水反应生成HF,HF溶于水的同时又极易挥发,挥发性的HF在潮湿的环境中形成酸雾,造成金属外部腐蚀,腐蚀产物多为氧化铁为主的混合锈蚀物;其次连铸机弧形区域处于一种相对密封状态,但区域的所有设备所处状态均不相同,有时对于无水状态,有时处于含水状态,在相对密闭的高温区不断交替,造成干湿交替腐蚀。
3.2.2 系统水质对设备的腐蚀循环水系统中阴离子腐蚀主要表现为Cl-、SO42-、氧气等对设备的影响。
探讨高碳钢连铸冷却工艺技术

探讨高碳钢连铸冷却工艺技术1高碳钢连铸技术目前对于含碳量高的钢连铸坯在生产加工时容易出现问题,例如高碳钢连铸坯的表面凹陷,表面纵裂,更严重甚至会发生漏钢,这一系列高碳钢连铸坯加工缺陷严重影响了产品的后续质量。
高碳钢连铸工艺技术的改进与完善目前已成为高碳钢连铸生产中的研究热点。
理论研究和工程实践表明,高碳钢零塑性区范围在1250℃以上,这就意味着在1250℃以上的温度范围内很小应变就会造成铸坯凝固前沿开裂这一问题;并且在1050℃~1250℃范围内,高碳钢的铸坯塑性也很差,产生的裂纹倾向性较大。
在结晶器对高碳钢的钢水冷却过程中,结晶器周向铸坯会出现热量传递和钢水凝固的不均匀现象,主要表现在靠近铸坯宽度中心的坯壳厚度较薄,并且由于高碳钢的含碳量较高,碳与其他金属反应生成碳化物进一步加剧了凝固坯壳厚度的不均匀性。
所以为了避免在高碳钢连铸过程中出现产品缺陷,需要对高碳钢连铸冷却技术进行研究探讨,从结晶器和二冷区连铸冷却工艺入手,得到表面质量和内部质量都符合要求的高质量连铸坯,提高高碳钢连铸坯质量,增加高碳钢产品质量2结晶器冷却工艺技术在高碳钢连铸冷却工艺中,因为结晶器决定了连铸坯表面质量的好坏,所以被誉为连铸设备的“心脏”。
连铸结晶器传热效率和冷却效果直接关系到结晶器寿命、铸坯表面质量、连铸漏钢和连铸其它缺陷。
2.1结晶器特性结晶器自身良好的导热性和导热均匀性决定了结晶器的功能作用,即主要功能是将结晶器内流动的钢水的热量通过坯壳、渣膜、气隙传递到结晶器上,然后冷却水把这部分热量带走,钢水流出结晶器后形成具有一定厚度的坯壳。
与此同时,良好的导热性和导热均匀性也保证了结晶器出口处的铸坯厚度均匀,不会产生变形,裂纹和漏钢的缺陷。
此外结晶器良好的耐磨性和抗热应力作用性能可以满足由于连铸过程中坯壳与结晶器铜板不可避免地接触、摩擦这一问题带来的挑战;结晶器重量轻和刚性好的优势赋予了结晶器良好的结构钢性,并且方便拆装调整和维修。
气雾全水组合冷却的高碳钢连铸生产方法与设计方案

气雾全水组合冷却的高碳钢连铸生产方法与设计方案一、气雾全水组合冷却的原理1.气雾冷却:在连铸过程中,通过喷射细小的水雾,有效增大了钢坯受冷面积,提高了冷却效率。
气雾冷却有效地促进了钢坯表面温度的迅速下降,避免了钢坯表面在连铸过程中产生脱碳和氧化。
2.全水冷却:通过喷射大量的水流对钢坯进行冷却,可以使钢坯内部温度均匀降低,防止出现温度梯度过大的情况。
全水冷却也能够增加钢坯内部应力的释放,减小钢坯的变形和裂纹的产生。
3.组合冷却:将气雾冷却和全水冷却结合起来,可以在快速冷却的同时保持较低的冷却速度,避免由于过快冷却而导致的应力过大和裂纹的产生。
二、气雾全水组合冷却的设计方案1.喷头设计:在气雾全水组合冷却中,喷头的设计是非常重要的。
喷头应该能够提供细小的气雾和充足的水流,以达到快速冷却的效果。
同时,喷头应具备均匀喷雾和喷水的能力,确保钢坯表面的温度分布均匀。
2.喷雾和喷水参数:喷雾和喷水的参数也直接影响到冷却效果。
对于气雾冷却,喷雾的粒径应该较小,一般为10-50μm。
对于全水冷却,水流的速度应该较大,一般为3-5m/s。
控制好喷雾和喷水的参数能够提高冷却效果。
3.冷却区域布置:在连铸机中,冷却区域的布置直接影响到冷却效果。
应根据钢坯的尺寸和形状合理设计冷却区域,并保证气雾和水流的覆盖面积。
同时,冷却区域应具备适当的冷却时间和空间,确保钢坯能够充分冷却。
4.控制系统:为了保证冷却效果,还需要一个可靠的控制系统。
控制系统应能够实时监测钢坯温度,并自动控制喷雾和喷水的参数。
同时,控制系统还应具备报警和自动停机等功能,以防止因温度异常而引发事故。
总之,气雾全水组合冷却是一种高效的高碳钢连铸生产方法。
通过合理的设计方案和控制系统,可以实现快速冷却和均匀温度分布,保证高碳钢连铸的质量和产量。
- 1、下载文档前请自行甄别文档内容的完整性,平台不提供额外的编辑、内容补充、找答案等附加服务。
- 2、"仅部分预览"的文档,不可在线预览部分如存在完整性等问题,可反馈申请退款(可完整预览的文档不适用该条件!)。
- 3、如文档侵犯您的权益,请联系客服反馈,我们会尽快为您处理(人工客服工作时间:9:00-18:30)。
包 钢 科 技 Science & Technology of Baotou Steel ( Group) Corporation
Vol. 28 ,No. 4 Auguest ,2002
高碳钢大方坯连铸水冷工艺参数优化试验研究Ξ
郭进毅 ,孟志泉 ,吕文 ,苏红亮 ,庞志杰 ,马 涛 ,罗海炯
3
0
0少
No. 1 2 流 1
0
3
2
1
0
0
0 Φ4 2
3
0
1少
1 Φ2 0
3
0
0少
1
0
0
3
0
0少
115 Φ2 0
2
0
0
0
110 0 115 2
0
0
0
115 Φ3 2 215 0
0少
0 Φ7 0 115 0
0
0
2 Φ1 115 2
0
0
0
No. 2 3 流 1 Φ3 2
3
1
0
0
1 Φ8 0
3 115 0
1 前言
连铸工艺以其先进的技术经济性在全国范围内 迅速取代了模铸工艺而成为钢水成型的首选工艺 。 然而 ,并非所有钢种都可以轻而易举的进行连铸 。 大量的试验研究和生产实践证明[1] ,低碳钢和高碳 钢因其凝固特性决定了其内部易产生的一些质量缺 陷 。高碳钢因其凝固间隔较大 ,即固液共存区间较 宽 ,加之固态导热系数较大 ,易于形成柱状晶 ,同时 , 在凝固后期存在快速凝固区间 ;这就使得高碳钢大 方坯的中心部位易出现疏松 、夹杂 ,以及程度不同的 缩孔和微裂纹同时伴随着夹杂 。易出现发达的柱状 晶区域 ,且极易产生裂纹 ,这在连铸坯中常以中间裂 纹出现 。当连铸水冷工艺参数设置不当时会加剧高 碳钢大方坯的内裂缺陷和中心缺陷 。
909
882
1005
970
937
915
885
(a) (280 ×325) No. 5 (204511)
(b) (280 ×325) No. 4 (204505) 图 3 No. 4 和 No. 5 方案的热酸照片
4 结论
经过五个水冷方案的试验得出如下结论 : ①高碳钢大方坯的中间裂纹产生于结晶器 ,发 展于二冷区 ; ②优化一冷和二冷可扩大等轴晶率 ; ③采用 No. 5 可使铸坯在矫直区的温度达到 900 ℃以上 ,从而避开矫直脆性区 ,避免因矫直而产 生中间裂纹 ; ④通过优化一冷和二冷水工艺参数可减少或消 除高碳钢大方坯的中间裂纹 。
出二冷室
第一架 拉矫机前
第二架 拉矫机前
第三架 拉矫机前
第四架 拉矫机前
986
953
924
920
890
1001
980
950
913
1002
975
944
918
889
996
953
924
914
897
1005
977
956
931
893
1004
984
951
915
892
998
966
942
911
888
993
975
938
(包钢 (集团) 公司炼钢厂 ,内蒙古 包头 014010)
摘 要 :通过对大量低倍试样的检验找出了高碳钢大方坯中间裂纹产生的原因 。经一定的计算及经验制定出了五 个方案 ,进行了小型及扩大试验 。从内部晶体结构方面阐述了高碳钢大方坯产生中间裂纹的原因 ,提出了中间裂 纹产生于结晶器 ,发展于二冷区的新分析思路 。 关键词 :高碳钢 ;大方坯 ;连铸水冷工艺参数优化 中图分类号 :TF77712 文献标识码 :B 文章编号 :1009 - 5438 (2002) 04 - 0001 - 04
而τ= S/ Vc 其中 S :铸坯离开结晶器的距离
Vc :拉速 故有 QC ∝ S/ Vc 二冷水比水量及其在二冷各区的分配比对铸坯 的内部晶体结构是关键工艺参数 。在同成份 ,同过 热度的情况下 ,二冷水的比水量及分配比将是铸坯 内部晶体结构的决定因素 。而内裂纹往往产生于粗 大晶体结构之处 ,如柱状晶区或粗大等轴晶区 。
(a) No. 4 (等轴晶率 5113 %) (104526 403)
(b) No. 3 (等轴晶率 4617 %) (104526 303) 图 2 No. 4 与 No. 3 对比 (同位置) 照片
31214 扩大试验结果 以 No. 4 方案 7 月进行了 2715 炉试验 ,结果见
表 6 、表 7 、表 8 及图 3 。
2 水冷工艺参数优化方案的制定
211 结晶器水量 (一冷) 的确定 确保进出口水温度 < 10 ℃,出口水温度 < 50 ℃。
水速 > 6m/ s 即可 ,一般地取周边每毫米 1135~2L/ min 。 212 二冷水比水量的确定
铸坯在凝固时 ,由于热应力和相变应力而产生 的内裂纹是随着比水量 (二冷强度) 的减少而减少
表 6 采用 No. 4 扩大试验结果
中心裂
中间裂
日 炉数 试样总数
2级 3级 2级 3级
22
9
18
5
1
4
61)
23~
815
16
24
4
0
7
2
25
10
31
7
0
6
3
合计 2715
65
16
1
17 8 (11)
比率 %
2416 115 2612 1213 (1619)
注 :1) 代表其中 3 个试样为鼓肚造成 3 级中间裂纹
GUO Jin - yi , M ENG Zhi - quan , LV Wen - jing , SU Hong - liang , PANG Zhi - jie , MA Tao , LUO Hai - jiong
( Steelmaking Plant of B aotou Steel ( Group) Corporation , B aotou 014010 , China)
从大量的热酸试验观测可看出 ,凡是产生中间 裂纹的试样与之相伴的是结晶器内形成的细晶及初 生极细的柱状晶厚度很不均匀 。在薄厚过渡区生长 出的粗大柱状晶内出现裂纹的几率很大 。其原因如 下:
(1) 中间裂纹产生于结晶器 : 由于板式组合式结晶器在宽面与窄面的结合处 为水冷却盲区 , 当有水之处为极强的冷却时 , 与之 相交的盲区就为相对更弱的冷却 , 这就势必加剧了 强冷与弱冷的差距 , 使得结晶器内的坯壳极度不均 匀 , 薄与厚的过渡区受到相变及凝固收缩应力和拉 应力作用 , 出结晶器时在固 - 液界面产生了裂纹 源。 (2) 中间裂纹扩展于二冷区 : 当二冷强度及分配比不当时会加剧产生于结晶 器内的中间裂纹源的扩展 ,只要是不利于坯壳均匀 生长的因素都会促进中间裂纹的长大 ,形成较严重 的中间裂纹 。 当采用弱的二冷冷却强度 ,同时加大出结晶器 后的一区的水量 ,这样可以加快将结晶器内形成的 不均匀坯壳的均匀化 。同时可以形成极细的柱状 晶 ,有利于抑制中间裂纹的扩展 ,从而减轻了中间裂 纹[2] 。 由此 ,可以想到在出结晶器的一区若采用角部 冷却会更有利于坯壳的均匀化 ,但因设备原因 ,该想 法未能得以试验 。 31213 改变结晶器水量的试验 基于上述分析又进行了下调结晶器水量和比水 量的试验 ,结果见表 5 和图 2 。
表 3 No. 1 与 No. 3 铸坯出二冷室后温度对比
位置
出二冷室 WS 前
WSM1 前 WSM2 前 WSM3 前
2 流 (No. 1)
97717 (970~998) 96013 (939~985) 93717 (926~953) 89116 (880~908) 86515 (849~876)
表 1 (280 ×380) 小试验结果(按国标检验 YBT153 - 1999)
试验方
中心 中心 中心 中间 皮下 角部 夹杂
流号
缩孔
案号
疏松 (mm) 裂纹 裂纹 裂纹 裂纹 物
No. 1 1 流 1
0
1 115 0
0
0
115 Φ3 1
3
0
0
0
1
0
1 115 0
0少
115 0
1
3
0
0
0
115 Φ8 0
3 试验结果与分析
311 试验方法与过程 31111 试验方法
取样在每炉每流的相同铸坯顺序号上取成对对
Ξ 收稿日期 :2001208224 作者简介 :郭进毅 (19662) 男 ,内蒙古土右旗人 ,1991 年毕业于北京科技大学冶金专业 ,获硕士学位 ,现从事炼钢及连铸工 艺技术工作 ,高级工程师 。
0
1 Φ5 115 1
1
0少
20 115 30 Nhomakorabea0少
115 0
0
0 115 0 少
110 0 110 115 0
0
0
115 Φ3 0 215 115 0
0
115 0
1 115 1
115 Φ6 0
2
0
No. 3 4 流 1 Φ2 115 1
1
0少
0
0
1
0
1
0
0 115 0
0
0
1
0 115 1
0
1 Φ3 0 115 1
4
包钢科技 第 28 卷
表 7 (280 ×325) 采用 No. 5 热酸检验结果
炉数
样数
中心裂 2级 3级
中间裂 2级 3级