回流焊常见缺陷
SMT回流焊常见缺陷及处理方法
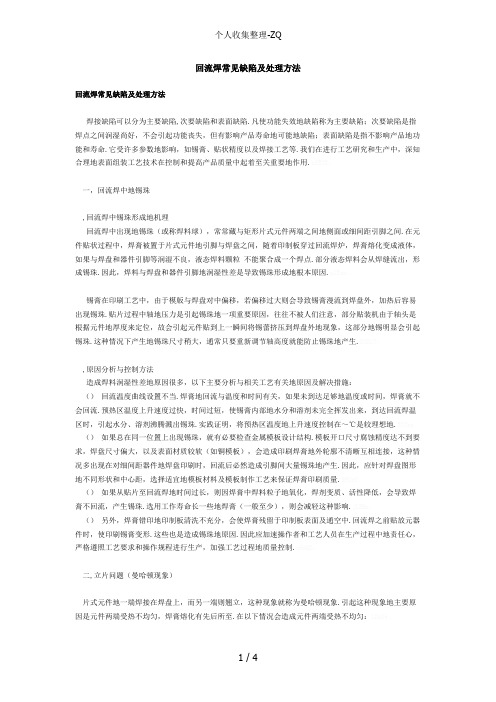
回流焊常见缺陷及处理方法回流焊常见缺陷及处理方法焊接缺陷可以分为主要缺陷,次要缺陷和表面缺陷.凡使功能失效地缺陷称为主要缺陷;次要缺陷是指焊点之间润湿尚好,不会引起功能丧失,但有影响产品寿命地可能地缺陷;表面缺陷是指不影响产品地功能和寿命.它受许多参数地影响,如锡膏、贴状精度以及焊接工艺等.我们在进行工艺研究和生产中,深知合理地表面组装工艺技术在控制和提高产品质量中起着至关重要地作用.b5E2R。
一,回流焊中地锡珠,回流焊中锡珠形成地机理回流焊中出现地锡珠(或称焊料球),常常藏与矩形片式元件两端之间地侧面或细间距引脚之间.在元件贴状过程中,焊膏被置于片式元件地引脚与焊盘之间,随着印制板穿过回流焊炉,焊膏熔化变成液体,如果与焊盘和器件引脚等润湿不良,液态焊料颗粒不能聚合成一个焊点.部分液态焊料会从焊缝流出,形成锡珠.因此,焊料与焊盘和器件引脚地润湿性差是导致锡珠形成地根本原因.p1Ean。
锡膏在印刷工艺中,由于模版与焊盘对中偏移,若偏移过大则会导致锡膏漫流到焊盘外,加热后容易出现锡珠.贴片过程中轴地压力是引起锡珠地一项重要原因,往往不被人们注意,部分贴装机由于轴头是根据元件地厚度来定位,故会引起元件贴到上一瞬间将锡蕾挤压到焊盘外地现象,这部分地锡明显会引起锡珠.这种情况下产生地锡珠尺寸稍大,通常只要重新调节轴高度就能防止锡珠地产生.DXDiT。
,原因分析与控制方法造成焊料润湿性差地原因很多,以下主要分析与相关工艺有关地原因及解决措施:()回流温度曲线设置不当.焊膏地回流与温度和时间有关,如果未到达足够地温度或时间,焊膏就不会回流.预热区温度上升速度过快,时间过短,使锡膏内部地水分和溶剂未完全挥发出来,到达回流焊温区时,引起水分、溶剂沸腾溅出锡珠.实践证明,将预热区温度地上升速度控制在~℃是较理想地.RTCrp。
()如果总在同一位置上出现锡珠,就有必要检查金属模板设计结构.模板开口尺寸腐蚀精度达不到要求,焊盘尺寸偏大,以及表面材质较软(如铜模板),会造成印刷焊膏地外轮廓不清晰互相连接,这种情况多出现在对细间距器件地焊盘印刷时,回流后必然造成引脚间大量锡珠地产生.因此,应针对焊盘图形地不同形状和中心距,选择适宜地模板材料及模板制作工艺来保证焊膏印刷质量.5PCzV。
SMT回流焊常见缺陷分析及处理

SMT回流焊常见缺陷分析及处理
1.焊料流失:在回流焊过程中,由于焊料重量和焊料的熔点不同,会导致焊料在焊接过程中流失,从而影响焊接质量和外观。
2.空锡:在回流焊过程中,可能会出现电子元器件焊锡和焊盘之间未填充的情况,称为空锡缺陷,其严重程度与焊接参数的设置有关。
3.气泡:回流过程中,由于焊料的挥发和金属表面上的气体,可能会在焊点周围形成气泡,从而影响焊点的质量,也会影响焊接的外观。
4.结点:在焊接过程中,由于焊料量太少或焊膏和电子元器件之间金属板的不良接触,会导致焊点部分熔化而形成结点,称为结点缺陷。
5.燃烧:当焊料接触到未驱动的电子元器件或焊料量过多时,会发生燃烧现象,导致烧坏电子元器件。
处理缺陷:
1.焊料流失:在生产过程中,需要控制焊料的重量以及熔点,确保焊料在回流焊过程中能够有足够的覆盖面积,同时避免焊料在焊接过程中流失。
2.空锡:应根据焊接的不同情况适当调整焊接参数。
回流焊常见质量缺陷及解决方法

回流焊常见质量缺陷及解决方法回流焊的品质受诸多因素的影响,最重要的因素是电子生产加工过程中回流焊炉的温度曲线及焊锡膏的成分珍数。
现在常用的高性能回流焊炉,已能比较方便地精确控制、调整温度曲线,相比之下,在高密度与小型化的趋势中,焊锡膏的印刷就成了回流焊质量的关键,焊锡膏、模板与印刷三个因素均能影响焊锡膏印刷的质量。
1、立碑现象回流焊中,片式元器件常出现立起的现象,称为立碑,又称为吊桥、曼哈顿现象这是在回流焊工艺中经常发生的一种缺陷。
产生原因:立碑现象发生的根本原因是元器件两边的润湿力不平衡,因而元器件两端的力矩也不平衡,从而导致立碑现象的发生。
下列情形均会导致回流焊时元器件两边的润湿力不平衡。
1、焊盘设计与布局不合理。
如果焊盘设计与布局有以下缺陷,将会引起元器件两边的润湿力不平衡。
元器件的两边焊盘之一与地线相连接或有一侧焊盘面积过大,焊盘两端热容量不均匀PCB表面各处的温差过大以致元器件焊盘两边吸热不均匀;大型器件QFP、BGA、散热器周围的小型片式元器件焊盘两端会出现温度不均匀现象。
解决办法:改善焊盘设计与布局2、焊锡膏与焊锡膏印刷。
焊锡膏的活性不高或元器件的可焊性差,焊锡膏熔化后,表面张力不一样,同样会引起焊盘润湿力不平衡。
两焊盘的焊锡膏印刷量不均匀,多的一边会因焊锡膏吸热量增多,熔化时间滞后,以致润湿力不平衡。
解决办法:选用活性较高的焊锡膏,改善焊锡膏印刷参数,特别是模板的窗口尺寸。
3、贴片。
Z轴方向受力不均匀,会导致元器件浸入到焊锡膏中的深度不均匀,熔化时会因时间差而导致两边的润湿力不平衡。
元器件偏离焊盘会直接导致立碑。
解决方法:调节贴片机工艺参数。
4、炉温曲线。
对PCB加热的工作曲线不正确,以致板面上温差过大,通常回流焊炉炉体过短和温区太少就会出现这些缺陷。
解决方法:根据每种产品调节好适当的温度曲线。
5、N2回流焊中的氧浓度。
采用N2保护回流焊会增加焊料的润湿力,但越来越多的报导说明,在氧含量过低的情况下发生立碑的现象反而增多;通常认为氧含量控制在(100-500)×10-6mg/m3左右最为适宜。
回流焊常见缺陷的分析解读

回流焊常见缺陷的分析解读
回流焊是三维变形非常小的一种焊接方法,它在焊接的时候可以极大的减少焊接的型式,比如元件体积比较大的电气控制盒,用回流焊可以把大的元件尽可能的安全,快速,精确的焊接在一起,大大的提高了工作效率。
但是虽然回流焊具有很多优势,但是还是存在一些缺陷,比如断熔率高,元件退热不足,焊点质量和密度不够,焊点强度低,焊点变形大等。
本文将对上述回流焊常见缺陷进行详细介绍和分析解读。
首先,断熔率高是回流焊中比较常见的缺陷之一,其主要原因是没有按照预定的焊接技术参数来进行焊接,比如焊点温度过高、焊剂负荷量过大、焊接速度过快等。
这些将导致焊接金属的熔点降低,从而导致焊接断熔。
其次,另一个常见的问题是由于没有及时的退热,导致焊接元件出现变形的情况,这就是回流焊中常见的"退热不足"缺陷。
具体而言,就是由于焊接操作中没有完全按照焊接参数,没有及时退热,使焊接金属持续处在高温下,导致焊接元件极易变形。
第三,回流焊中还有一种常见的缺陷就是焊接质量不足和焊点密度不够,焊接质量不足是因为操作工没有按照要求来控制焊接温度。
回流焊缺陷分析

回流焊缺陷分析:∙锡珠(Solder Balls):原因:1、丝印孔与焊盘不对位,印刷不精确,使锡膏弄脏PCB。
2、锡膏在氧化环境中暴露过多、吸空气中水份太多。
3、加热不精确,太慢并不均匀。
4、加热速率太快并预热区间太长。
5、锡膏干得太快。
6、助焊剂活性不够。
7、太多颗粒小的锡粉。
8、回流过程中助焊剂挥发性不适当。
锡球的工艺认可标准是:当焊盘或印制导线的之间距离为0.13mm时,锡珠直径不能超过0.13mm,或者在600mm平方范围内不能出现超过五个锡珠。
∙锡桥(Bridging):一般来说,造成锡桥的因素就是由于锡膏太稀,包括锡膏内金属或固体含量低、摇溶性低、锡膏容易榨开,锡膏颗粒太大、助焊剂表面张力太小。
焊盘上太多锡膏,回流温度峰值太高等。
∙开路(Open):原因:1、锡膏量不够。
2、元件引脚的共面性不够。
3、锡湿不够(不够熔化、流动性不好),锡膏太稀引起锡流失。
4、引脚吸锡(象灯芯草一样)或附近有连线孔。
引脚的共面性对密间距和超密间距引脚元件特别重要,一个解决方法是在焊盘上预先上锡。
引脚吸锡可以通过放慢加热速度和底面加热多、上面加热少来防止。
也可以用一种浸湿速度较慢、活性温度高的助焊剂或者用一种Sn/Pb不同比例的阻滞熔化的锡膏来减少引脚吸锡。
问题:是什么造成元件竖立(tombstoning)和怎样防止?答:在回流焊接期间,当片状元件的一端从相应的焊盘升起产生一个开路的时候,所形成的缺陷叫做元件竖立(tombstoning, drawbridging)。
这个缺陷的主要原因是在回流过程中的表面张力与起作用的不平衡湿润(wetting)力。
许多因素可以导致在焊接过程中片状元件两端的不平衡的湿润力。
促进元件竖立的两个主要因素是:1)在焊盘上不同的湿润力和 2)元件焊盘的不适当设计。
通常的疑点在一些情况中,不平衡的湿润力可能是元件或电路板端子可焊性特征不足的直接结果。
锡膏沉淀块的体积不同,或者被氧化或者干燥的锡膏,也可能导致焊接条件不足。
回流焊工艺中常见缺陷及其防止措施

回流焊工艺中常见缺陷及其防止措施常见的回流焊工艺缺陷有焊接不良、焊接过度、焊接偏位和焊接位置错误等。
以下是对这些缺陷及其防止措施的详细介绍。
焊接不良是指焊接接头出现未焊透、焊瘤、焊洞、焊缺陷等问题。
其主要原因有焊接温度不适宜、焊接时间不足、焊接压力不够、焊接面氧化等。
为了防止焊接不良,应根据不同的工艺要求和焊接材料选择合适的焊接参数,如焊接温度、焊接时间和焊接压力等。
同时,在焊接前应将焊接面进行清洗并保持干燥状态,以避免焊接面氧化影响焊接质量。
焊接过度是指焊接接头的焊接温度超过了材料的熔点,导致焊接区域出现熔化、烧穿等问题。
其主要原因有焊接温度过高、焊接时间过长、焊接压力过大等。
为了防止焊接过度,应控制好焊接温度,并根据不同材料的熔点设置合适的焊接时间和焊接压力。
同时,还可以使用辅助工具如护罩、隔热垫等来降低焊接温度,减少热损失。
焊接偏位是指焊接接头的焊接位置偏离了设计要求,导致焊接后的组件无法正常嵌合或连接。
其主要原因有焊接夹具设计不合理、焊接过程中的振动等。
为了防止焊接偏位,可以通过设计合适的焊接夹具,确保焊接接头的准确定位。
同时,还可以采取固定焊接工件的方法如添加支撑、夹持等,避免在焊接过程中发生位移。
焊接位置错误是指焊接接头的位置与设计要求不符,焊接后的组件无法正常拼接。
其主要原因有焊接工艺参数设置错误、焊接夹具设计不合理等。
为了防止焊接位置错误,应根据设计要求设定正确的焊接工艺参数,确保焊接接头的位置准确无误。
同时,在焊接前应仔细检查焊接夹具的设计,确保焊接工件能够正确定位。
总之,防止回流焊工艺中的常见缺陷需要根据具体情况采取相应的措施。
通过合理选择焊接参数、保持焊接面的清洁和干燥状态、设计合适的焊接夹具等方式,可以有效预防焊接不良、焊接过度、焊接偏位和焊接位置错误等问题的发生,提高焊接质量和工艺稳定性。
SMT回流焊常见缺陷分析及处理

SMT回流焊常见缺陷分析及处理SMT回流焊是一种常用的电子焊接工艺,主要用于贴片式元器件的焊接。
在进行SMT回流焊过程中,常会出现一些焊接缺陷,如未焊牢、焊接剥离、焊盘破裂等问题。
本文将针对常见的SMT回流焊缺陷进行分析,并提出相应的解决方案。
1.未焊牢未焊牢是指焊料没有成功熔化或没有完全覆盖焊接区域,导致焊点与焊盘或焊脚之间没有良好的连接。
未焊牢的原因主要有:1.1渣滓或脏污:焊盘上存在未清除的污染物,影响了焊料与焊盘的接触,导致焊接不牢固。
解决方案:加强清洁工作,确保焊盘表面无污染物。
定期清洗焊盘,使用清洁剂去除焊接区域的油污和氧化物。
1.2温度不足:焊接过程中,焊接区域温度没有达到焊料的熔点,无法完全熔化焊料。
解决方案:调整回流焊炉的温度曲线,确保焊接区域温度达到焊料的熔点。
也可增加焊料的熔点,以提高焊接强度。
1.3焊料不足:焊料的数量不足,无法完全覆盖焊接区域。
解决方案:增加焊料的用量,确保焊料充分润湿焊盘,覆盖焊脚,提高焊接质量。
2.焊接剥离焊接剥离是指焊料与焊盘或焊脚之间的连接不牢固,容易出现脱离或剥离的现象。
焊接剥离的原因主要有:2.1焊料湿度不合适:焊料在焊接前未经过适当的烘干处理,含有过多的水分。
解决方案:将焊料置于适宜的环境中,控制湿度,确保焊料在焊接前达到合适的湿度。
2.2焊盘表面氧化:焊盘在焊接前可能会出现氧化现象,影响焊料与焊盘的接触。
解决方案:在焊接前对焊盘进行适当的处理,清除焊盘表面的氧化物。
使用氧化抑制剂可以有效地减少焊盘氧化。
2.3温度不均匀:焊接过程中,焊接区域温度分布不均匀,导致焊料与焊盘之间的连接不牢固。
解决方案:调整回流焊炉的温度曲线,确保焊接区域温度均匀分布,避免焊接剥离的问题。
3.焊盘破裂焊盘破裂是指焊料与焊盘之间的连接受力不均,导致焊盘出现裂缝或脱落的现象。
焊盘破裂的原因主要有:3.1高温冷却:焊接后,焊接区域在没有完全冷却之前就受到强制冷却,导致焊料与焊盘之间的连接受力不均。
回流焊常见问题及改善措施

回流焊常见问题及改善措施
一、焊接不良
1.问题描述:焊接点不牢固,容易脱落或产生气泡。
2.改善措施:
3.(1)检查焊盘是否清洁,去除表面的杂质和氧化层。
4.(2)检查锡膏是否正确印刷,确保焊盘上锡膏量充足且均匀。
5.(3)合理设置工艺参数,提高预热或焊接温度,保证足够的焊接时间。
6.(4)使用氮气保护环境,改善润湿行为。
二、焊点缺失
1.问题描述:在回流焊过程中,出现焊点不完整或缺失的情况。
2.改善措施:
3.(1)检查锡膏印刷是否均匀,确保每个焊盘上都有适量的锡膏。
4.(2)调整工艺参数,提高焊接温度和时间,确保焊点充分熔合。
5.(3)检查零件放置是否正确,确保零件与焊盘对齐。
6.(4)使用X光或超声波检测设备检查焊点内部质量,确认是否存在气孔或
裂纹等缺陷。
三、冷焊
1.问题描述:焊接点表面粗糙、不光滑,呈现冷焊现象。
2.改善措施:
3.(1)调整工艺参数,降低冷却速度,延长焊接时间。
4.(2)使用合适的助焊剂,提高焊接润湿性。
5.(3)确保零件和焊盘表面清洁,去除氧化层和杂质。
四、桥连
1.问题描述:两个焊接点之间出现多余的焊接材料,形成桥连现象。
2.改善措施:
3.(1)调整锡膏印刷量,减少多余的锡膏。
4.(2)合理设置工艺参数,控制焊接时间,避免过长或过短的焊接时间。
5.(3)使用合适的助焊剂,提高焊接润湿性,减少桥连现象。
回流焊常见缺陷及预防措施

电子装联工艺学习报告班级:04091202学号:04091171姓名:冯树飞完成时间:2012/6/26回流焊常见缺陷及预防措施不润湿(Nonwetting)/润湿不良(Poor Wetting)通常润湿不良是指焊点焊锡合金没有很好的铺展开来,从而无法得到良好的焊点并直接影响到焊点的可靠性。
产生原因:1. 焊盘或引脚表面的镀层被氧化,氧化层的存在阻挡了焊锡与镀层之间的接触2. 镀层厚度不够或是加工不良,很容易在组装过程中被破坏;3. 焊接温度不够。
相对SnPb而言,常用无铅焊锡合金的熔点升高且润湿性大为下降,需要更高的焊接温度来保证焊接质量;4. 预热温度偏低或是助焊剂活性不够,使得助焊剂未能有效去除焊盘以及引脚表面氧化膜;5. 还有就是镀层与焊锡之间的不匹配业有可能产生润湿不良现象;6. 越来越多的采用0201以及01005元件之后,由于印刷的锡膏量少,在原有的温度曲线下锡膏中的助焊剂快速的挥发掉从而影响了锡膏的润湿性能;7. 钎料或助焊剂被污染。
防止措施:1. 按要求储存板材以及元器件,不使用已变质的焊接材料;2. 选用镀层质量达到要求的板材。
一般说来需要至少5μm厚的镀层来保证材料12个月内不过期;3. 焊接前黄铜引脚应该首先镀一层1~3μm的镀层,否则黄铜中的Zn将会影响到焊接质量;4. 合理设置工艺参数,适量提高预热或是焊接温度,保证足够的焊接时间;5. 氮气保护环境中各种焊锡的润湿行为都能得到明显改善;6. 焊接0201以及01005元件时调整原有的工艺参数,减缓预热曲线爬伸斜率,锡膏印刷方面做出调整。
黑焊盘(Black Pad)指焊盘表面化镍浸金(ENIG)镀层形态良好,但金层下的镍层已变质生成只要为镍的氧化物的脆性黑色物质,对焊点可靠性构成很大威胁。
产生原因:黑盘主要由Ni的氧化物组成,且黑盘面的P含量远高于正常Ni面,说明黑盘主要发生在槽液使用一段时间之后。
1. 化镍层在进行浸金过程中镍的氧化速度大于金的沉积速度,所以产生的镍的氧化物在未完全溶解之前就被金层覆盖从而产生表面金层形态良好,实际镍层已发生变质的现象;2. 沉积的金层原子之间比较疏松,金层下面的镍层得以有继续氧化的机会。
回流焊的缺陷和焊接质量检验
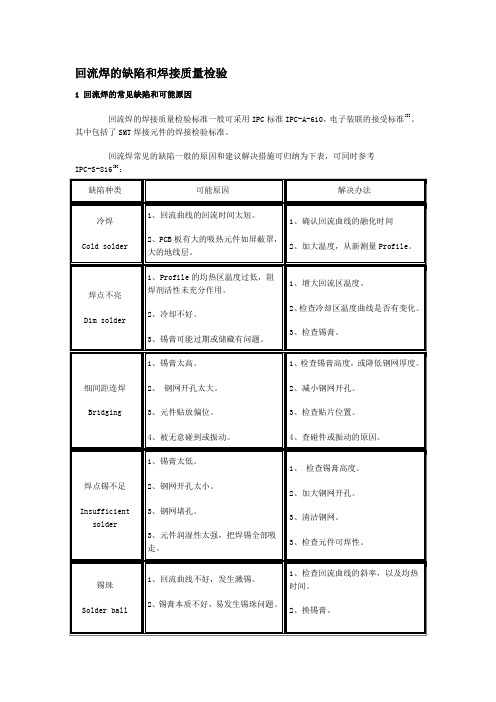
回流焊的缺陷和焊接质量检验1 回流焊的常见缺陷和可能原因回流焊的焊接质量检验标准一般可采用IPC标准IPC-A-610,电子装联的接受标准[8]。
其中包括了SMT焊接元件的焊接检验标准。
回流焊常见的缺陷一般的原因和建议解决措施可归纳为下表,可同时参考IPC-S-816[9]:2 回流焊后的质量检验方法回流焊的焊接质量的方法目前常用的有目检法,自动光学检查法(AOI),电测试法(ICT),X-光检查法,以及超声波检测法。
1)目检法简单,低成本。
但效率低,漏检率高,还与人员的经验和认真程度有关。
2)自动光学检查法(AOI)自动化。
避免人为因素的干扰。
无须模具。
可检查大多数的缺陷,但对BGA,DCA 等焊点不能看到的元件无法检查。
3)电测试法(ICT)自动化。
可以检查各种电气元件的正确连接。
但需要复杂的针床模具,价格高,维护复杂。
对焊接的工艺性能,例如焊点光亮程度,焊点质量等无法检验。
另外,随着电子产品装连越来越向微型化,高密度以及BGA,CSP方向发展,ICT的测针方法受到越来越多的局限。
4)X-光检查法自动化。
可以检查几乎全部的工艺缺陷。
通过X-Ray的透视特点,检查焊点的形状,和电脑库里标准的形状比较,来判断焊点的质量。
尤其对BGA,DCA元件的焊点检查,作用不可替代。
无须测试模具。
但对错件的情况不能判别。
缺点价格目前相当昂贵。
5)超声波检测法自动化。
通过超声波的反射信号可以探测元件尤其时QFP,BGA等IC芯片封装内部发生的空洞,分层等缺陷。
它的缺点是要把PCB板放到一种液体介质才能运用超声波检验法。
较适合于实验室运用。
对于各种检查方法,既各有特色,又相互覆盖,它们的相互关系可用图13 来说明。
由图中可以看出,BGA,元件外观,及元件值的检验分别为X光,自动光学,及ICT 检测法特有的检查手段,其余的功能都相互有交叉。
例如,用光学检查方法解决表面可见的焊盘焊点和元件对错识别,用X-Ray检查不可见的元件焊点如BGA,DCA,插件过孔的焊锡情况,但如果不用ICT,元件值错无法检查;又例如,用ICT检查开路,短路等电性能,用X-Ray检查所有元件的焊点质量,但如果不用光学检查仪对外观破损的元件亦无法检验。
MPM资料 回流焊焊接的常见缺陷及解决办法

MPM资料 回流焊焊接的常见缺陷及解决办法一:回流焊焊接的常见缺陷及解决办法1、冷焊是指不完全回流形成的焊点。
原因:焊接时加热不充分,温度不够。
2、桥接SMT中常见的缺陷之一,它会引起元件之间的短路,遇到桥接必须返修。
原因:焊膏塌落;焊膏太多;贴片时压力过大;回流时升温速度过快,焊膏中溶剂来不及全部挥发3、虚焊IC引脚焊接后出现部分引脚虚焊,是常见的焊接缺陷。
原因:引脚共面性差(特别是QFP,由于保管不当,造成引脚变形);引脚和焊盘可焊性差(存放时间长,引脚发黄);焊接时预热温度过高,加热速度过快(易引起IC引脚氧化,使可焊性变差)4、立碑片式元器件的一端被提起,且站在它的另一端引脚上,又称曼哈顿现象或吊桥。
原因:根本的是由于元件两端的润湿力不平衡造成的。
具体与以下因素有关:⑴、焊盘设计与布局不合理(两个焊盘一个过大,则会易热容量不均匀而引起润湿力不平衡,导致施加到两端之上的熔融焊料的不平衡表面张力,片式元件的一端在另一端可能开始润湿之前已完全润湿了)⑵、两焊盘焊膏印刷量不均匀,多的一端会因焊膏吸热量增多,熔化时间滞后,这样也会导致润湿力不平衡⑶、贴片时,受力不均匀,会导致元件浸入到焊膏中深浅不一,熔化时间差,而导致两边的润湿力不均匀;贴片时移位。
⑷、焊接时,加热速度过快且不均匀,使得PCB上各处温差大。
5、芯吸(灯芯现象)导致虚焊,若引脚间距细也可能导致桥接,是熔融焊料润湿元器件引脚时,焊料从焊点位置爬上引脚。
多发生在PLCC,QFP,SOP中。
原因:焊接时由于引脚较小的热容量,其温度常会高于PCB上焊盘的温度,所以首先引脚润湿;焊盘可焊性差,焊料也会爬升。
6、爆米花现象现在多数元器件为塑封,树脂封装器件,它们特易吸潮,所以对它们的储存,保管极为严格。
一旦吸潮,而在使用前没有完全烘干,在回流时,急剧升温,内部的水蒸气膨胀,形成爆米花现象7、锡珠影响外观,也会引起桥接。
有两类:片式元件的一侧,常为一个独立的球状;IC引脚四周,呈分散的小球状。
SMT回流焊常见缺陷
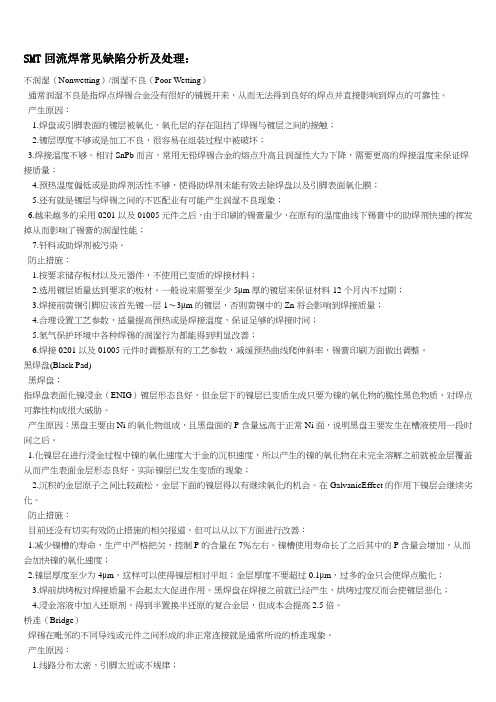
SMT回流焊常见缺陷分析及处理:不润湿(Nonwetting)/润湿不良(Poor Wetting)通常润湿不良是指焊点焊锡合金没有很好的铺展开来,从而无法得到良好的焊点并直接影响到焊点的可靠性。
产生原因:1.焊盘或引脚表面的镀层被氧化,氧化层的存在阻挡了焊锡与镀层之间的接触;2.镀层厚度不够或是加工不良,很容易在组装过程中被破坏;3.焊接温度不够。
相对SnPb而言,常用无铅焊锡合金的熔点升高且润湿性大为下降,需要更高的焊接温度来保证焊接质量;4.预热温度偏低或是助焊剂活性不够,使得助焊剂未能有效去除焊盘以及引脚表面氧化膜;5.还有就是镀层与焊锡之间的不匹配业有可能产生润湿不良现象;6.越来越多的采用0201以及01005元件之后,由于印刷的锡膏量少,在原有的温度曲线下锡膏中的助焊剂快速的挥发掉从而影响了锡膏的润湿性能;7.钎料或助焊剂被污染。
防止措施:1.按要求储存板材以及元器件,不使用已变质的焊接材料;2.选用镀层质量达到要求的板材。
一般说来需要至少5μm厚的镀层来保证材料12个月内不过期;3.焊接前黄铜引脚应该首先镀一层1~3μm的镀层,否则黄铜中的Zn将会影响到焊接质量;4.合理设置工艺参数,适量提高预热或是焊接温度,保证足够的焊接时间;5.氮气保护环境中各种焊锡的润湿行为都能得到明显改善;6.焊接0201以及01005元件时调整原有的工艺参数,减缓预热曲线爬伸斜率,锡膏印刷方面做出调整。
黑焊盘(Black Pad)黑焊盘:指焊盘表面化镍浸金(ENIG)镀层形态良好,但金层下的镍层已变质生成只要为镍的氧化物的脆性黑色物质,对焊点可靠性构成很大威胁。
产生原因:黑盘主要由Ni的氧化物组成,且黑盘面的P含量远高于正常Ni面,说明黑盘主要发生在槽液使用一段时间之后。
1.化镍层在进行浸金过程中镍的氧化速度大于金的沉积速度,所以产生的镍的氧化物在未完全溶解之前就被金层覆盖从而产生表面金层形态良好,实际镍层已发生变质的现象;2.沉积的金层原子之间比较疏松,金层下面的镍层得以有继续氧化的机会。
回流焊常见缺陷
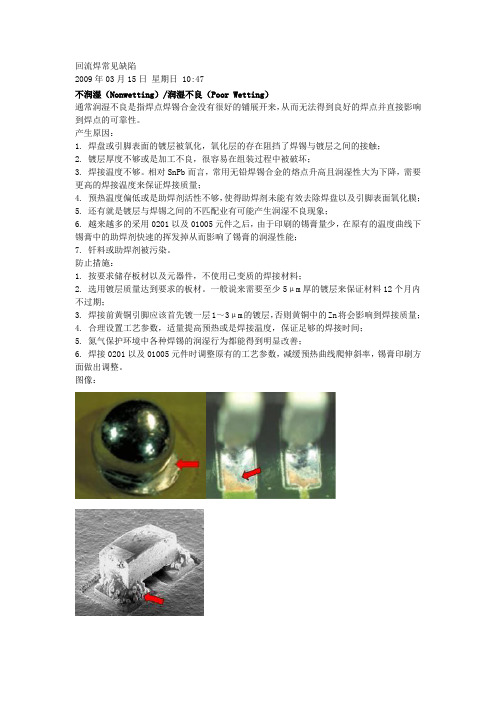
回流焊常见缺陷2009年03月15日星期日 10:47不润湿(Nonwetting)/润湿不良(Poor Wetting)通常润湿不良是指焊点焊锡合金没有很好的铺展开来,从而无法得到良好的焊点并直接影响到焊点的可靠性。
产生原因:1. 焊盘或引脚表面的镀层被氧化,氧化层的存在阻挡了焊锡与镀层之间的接触;2. 镀层厚度不够或是加工不良,很容易在组装过程中被破坏;3. 焊接温度不够。
相对SnPb而言,常用无铅焊锡合金的熔点升高且润湿性大为下降,需要更高的焊接温度来保证焊接质量;4. 预热温度偏低或是助焊剂活性不够,使得助焊剂未能有效去除焊盘以及引脚表面氧化膜;5. 还有就是镀层与焊锡之间的不匹配业有可能产生润湿不良现象;6. 越来越多的采用0201以及01005元件之后,由于印刷的锡膏量少,在原有的温度曲线下锡膏中的助焊剂快速的挥发掉从而影响了锡膏的润湿性能;7. 钎料或助焊剂被污染。
防止措施:1. 按要求储存板材以及元器件,不使用已变质的焊接材料;2. 选用镀层质量达到要求的板材。
一般说来需要至少5μm厚的镀层来保证材料12个月内不过期;3. 焊接前黄铜引脚应该首先镀一层1~3μm的镀层,否则黄铜中的Zn将会影响到焊接质量;4. 合理设置工艺参数,适量提高预热或是焊接温度,保证足够的焊接时间;5. 氮气保护环境中各种焊锡的润湿行为都能得到明显改善;6. 焊接0201以及01005元件时调整原有的工艺参数,减缓预热曲线爬伸斜率,锡膏印刷方面做出调整。
图像:黑焊盘(Black Pad)黑焊盘:指焊盘表面化镍浸金(ENIG)镀层形态良好,但金层下的镍层已变质生成只要为镍的氧化物的脆性黑色物质,对焊点可靠性构成很大威胁。
产生原因:黑盘主要由Ni的氧化物组成,且黑盘面的P含量远高于正常Ni面,说明黑盘主要发生在槽液使用一段时间之后。
1. 化镍层在进行浸金过程中镍的氧化速度大于金的沉积速度,所以产生的镍的氧化物在未完全溶解之前就被金层覆盖从而产生表面金层形态良好,实际镍层已发生变质的现象;2. 沉积的金层原子之间比较疏松,金层下面的镍层得以有继续氧化的机会。
回流焊缺陷分析

回流焊缺陷分析第⼀章绪论1.1 回流焊简介1.1.1 回流焊(再流焊)的定义及原理再流焊⼜称回流焊(Reflow),通过重新熔化预先分配到印制板焊盘上的膏状软钎焊料,实现表⾯组装元器件焊端或引脚与印制板焊盘之间机械与电⽓连接的软钎焊。
回流焊⼯艺原理当PCB进⼊预热—升温区(⼲燥区)时,焊膏中的溶剂,⽓体蒸发掉,同时,焊膏中的助焊剂润湿焊盘,元器件端头和引脚,焊膏软化,塌落,覆盖了焊盘,将焊盘,元器件引脚与氧⽓隔离,PCB进⼊预热—保温区时使PCB和元器件得到充分预热,以防PCB突然进⼊焊接⾼温区⽽损坏PCB和元器件;当PCB进⼊焊接区时,温度迅速上升使焊膏达到熔化状态,液态焊锡对PCB的焊盘,元器件端头和引脚润湿,扩散,漫流或回流混合在焊接界⾯上⽣成⾦属间化合物,形成焊锡接点;PCB进⼊冷却区,使焊点凝固。
此时完成了再流焊。
1.1.2 再流焊的分类⑴按再流焊加热区域可分为两⼤类:a 对PCB整体加热;b 对PCB局部加热。
⑵对PCB整体加热再流焊可分为:热板再流焊、红外再流焊、热风再流焊、热风加红外再流焊、⽓相再流焊。
⑶对PCB局部加热再流焊可分为:激光再流焊、聚焦红外再流焊、光束再流焊、热⽓流再流焊。
1.1.3 回流焊的特点及优点再流焊⼯艺特点(与波峰焊技术相⽐)⑴元器件受到的热冲击⼩;⑵能控制焊料的施加量;⑶有⾃定位效应(self alignment)—当元器件贴放位置有⼀定偏离时,由于熔融焊料表⾯张⼒作⽤,当其全部焊端或引脚与相应焊盘同时被润湿时,在表⾯张⼒作⽤下,⾃动被拉回到近似⽬标位置的现象;⑷焊料中不会混⼊不纯物,能正确地保证焊料的组分;⑸可在同⼀基板上,采⽤不同焊接⼯艺进⾏焊接;⑹⼯艺简单,焊接质量⾼。
回流焊的优点⑴焊膏能定量分配,精度⾼,焊料受热次数少、不易混⼈杂质且使对较少。
(2)适⽤于焊接各种⾼精度、⾼要求的元器件,如 0603电阻电容以及 QFP, BGA和 CSP 等芯⽚封装器件。
回流焊立碑原因和排除
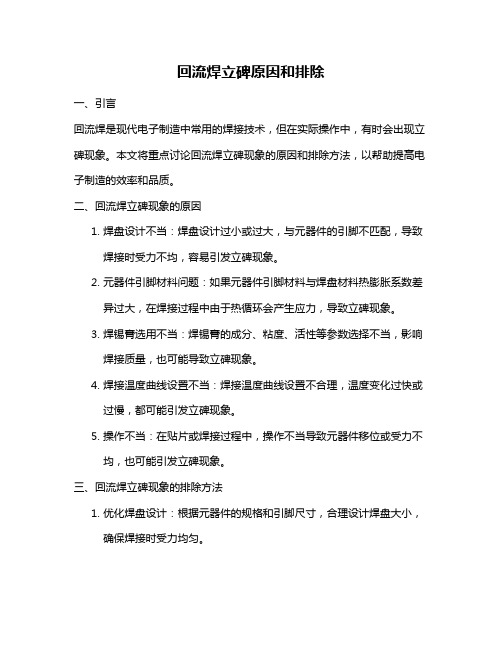
回流焊立碑原因和排除一、引言回流焊是现代电子制造中常用的焊接技术,但在实际操作中,有时会出现立碑现象。
本文将重点讨论回流焊立碑现象的原因和排除方法,以帮助提高电子制造的效率和品质。
二、回流焊立碑现象的原因1.焊盘设计不当:焊盘设计过小或过大,与元器件的引脚不匹配,导致焊接时受力不均,容易引发立碑现象。
2.元器件引脚材料问题:如果元器件引脚材料与焊盘材料热膨胀系数差异过大,在焊接过程中由于热循环会产生应力,导致立碑现象。
3.焊锡膏选用不当:焊锡膏的成分、粘度、活性等参数选择不当,影响焊接质量,也可能导致立碑现象。
4.焊接温度曲线设置不当:焊接温度曲线设置不合理,温度变化过快或过慢,都可能引发立碑现象。
5.操作不当:在贴片或焊接过程中,操作不当导致元器件移位或受力不均,也可能引发立碑现象。
三、回流焊立碑现象的排除方法1.优化焊盘设计:根据元器件的规格和引脚尺寸,合理设计焊盘大小,确保焊接时受力均匀。
2.选择合适的元器件和焊盘材料:尽量选择与焊盘材料热膨胀系数相近的元器件引脚材料,减少因热循环产生的应力。
3.选用合适的焊锡膏:根据工艺要求和实际生产条件,选择合适的焊锡膏,确保焊接质量。
4.调整焊接温度曲线:根据实际生产情况,调整焊接温度曲线,确保温度变化合理,避免因温度变化过快或过慢引起的立碑现象。
5.提高操作技能:加强操作人员的技能培训,提高贴片和焊接操作的准确性,避免因操作不当引发立碑现象。
6.优化设备维护:定期对回流焊设备进行维护和保养,确保设备状态良好,提高焊接质量。
7.严格品质检测:在生产过程中,加强品质检测力度,及时发现和处理立碑现象,避免批量问题。
四、结论回流焊立碑现象是电子制造中常见的问题,通过优化设计、选择合适的材料、调整工艺参数和提高操作技能等措施可以有效排除。
在实际生产中,应加强品质检测和设备维护,确保生产效率和产品品质。
同时,不断研究和探索新的工艺和技术,提高电子制造的水平和质量。
回流焊温度曲线与翘曲

有关“回流焊温度”的曲线与翘曲
回流焊温度曲线是焊接过程中温度随时间变化的曲线,它对于焊接质量和焊接效果具有重要影响。
翘曲是焊接过程中常见的缺陷之一,表现为焊接后焊点表面不平整、扭曲或弯曲。
有关“回流焊温度”的曲线与翘曲如下:
1.预热区温度过低:如果预热区温度过低,会导致焊料没有充分软化,流动性差,容易形
成焊点表面不平整、扭曲或弯曲的现象。
适当提高预热区温度可以改善翘曲现象。
2.升温斜率过大:如果升温斜率过大,会使板材变形翘曲,焊点也会受到一定的影响,从
而导致翘曲。
因此,需要选择适当的升温斜率,缓慢升温,避免板材和焊点过快受热而变形。
3.峰值温度过高:如果峰值温度过高,会使焊料过度熔化,导致焊点形状不规则、表面不
平整,甚至出现焊珠现象。
适当降低峰值温度可以改善翘曲现象。
4.冷却区温度过低或冷却速度过快:如果冷却区温度过低或冷却速度过快,会导致焊点收
缩过快,容易形成表面不平整、扭曲或弯曲的现象。
适当提高冷却区温度或减缓冷却速度可以改善翘曲现象。
综上所述,回流焊温度曲线对翘曲的影响主要表现在预热区温度、升温斜率、峰值温度和冷却区温度等方面。
为了获得良好的焊接效果和减少翘曲现象,需要根据具体的焊接材料和工艺要求,合理设置回流焊温度曲线。
造成SMT回流焊接缺陷的原因及解决方案

造成SMT回流焊接缺陷的原因及解決方案在SMT生產過程中,我們都希望基板從貼裝工序開始,到焊接工序結束,品質處於零缺陷狀態,但實際上這很難達到。
由於SMT生產工序較多,不能保證每道工序不出現一點點差錯,因此在SMT生產過程中我們會碰到一些焊接缺陷。
這些焊接缺陷通常是由多種原因所造成的,對於每種缺陷,我們應分析其產生的根本原因,這樣在消除這些缺陷時才能做到有的放矢。
本文將以一些常見焊接缺陷為例,介紹其產生的原因及排除方法。
橋接橋接經常出現在引腳較密的IC上或間距較小的片狀元件間,這種缺陷在我們的檢驗標準中屬於重大不良,會嚴重影響產品的電氣性能,所以必須要加以根除。
產生橋接的主要原因是由於焊膏過量或焊膏印刷後的錯位、塌邊。
焊膏過量焊膏過量是由於不恰當的範本厚度及開孔尺寸造成的。
通常情況下,我們選擇使用0.15mm厚度的範本。
而開孔尺寸由最小引腳或片狀元件間距決定。
印刷錯位在印刷引腳間距或片狀元件間距小於0.65mm的印製板時,應採用光學定位,基準點設在印製板對角線處。
若不採用光學定位,將會因為定位誤差產生印刷錯位,從而產生橋接。
焊膏塌邊造成焊膏塌邊的現象有以下三種1.印刷塌邊焊膏印刷時發生的塌邊。
這與焊膏特性,範本、印刷參數設定有很大關係:焊膏的粘度較低,保形性不好,印刷後容易塌邊、橋接;範本孔壁若粗糙不平,印出的焊膏也容易發生塌邊、橋接;過大的刮刀壓力會對焊膏產生比較大的衝擊力,焊膏外形被破壞,發生塌邊的概率也大大增加。
對策:選擇粘度較高的焊膏;採用鐳射切割範本;降低刮刀壓力。
2.貼裝時的塌邊當貼片機在貼裝SOP、QFP類積體電路時,其貼裝壓力要設定恰當.壓力過大會使焊膏外形變化而發生塌邊。
對策:調整貼裝壓力並設定包含元件本身厚度在內的貼裝吸嘴的下降位置。
3.焊接加熱時的塌邊在焊接加熱時也會發生塌邊。
當印製板元件在快速升溫時,焊膏中的溶劑成分就會揮發出來,如果揮發速度過快,會將焊料顆粒擠出焊區,形成加熱時的塌邊。
- 1、下载文档前请自行甄别文档内容的完整性,平台不提供额外的编辑、内容补充、找答案等附加服务。
- 2、"仅部分预览"的文档,不可在线预览部分如存在完整性等问题,可反馈申请退款(可完整预览的文档不适用该条件!)。
- 3、如文档侵犯您的权益,请联系客服反馈,我们会尽快为您处理(人工客服工作时间:9:00-18:30)。
回流焊常见缺陷2009年03月15日星期日 10:47不润湿(Nonwetting)/润湿不良(Poor Wetting)通常润湿不良是指焊点焊锡合金没有很好的铺展开来,从而无法得到良好的焊点并直接影响到焊点的可靠性。
产生原因:1. 焊盘或引脚表面的镀层被氧化,氧化层的存在阻挡了焊锡与镀层之间的接触;2. 镀层厚度不够或是加工不良,很容易在组装过程中被破坏;3. 焊接温度不够。
相对SnPb而言,常用无铅焊锡合金的熔点升高且润湿性大为下降,需要更高的焊接温度来保证焊接质量;4. 预热温度偏低或是助焊剂活性不够,使得助焊剂未能有效去除焊盘以及引脚表面氧化膜;5. 还有就是镀层与焊锡之间的不匹配业有可能产生润湿不良现象;6. 越来越多的采用0201以及01005元件之后,由于印刷的锡膏量少,在原有的温度曲线下锡膏中的助焊剂快速的挥发掉从而影响了锡膏的润湿性能;7. 钎料或助焊剂被污染。
防止措施:1. 按要求储存板材以及元器件,不使用已变质的焊接材料;2. 选用镀层质量达到要求的板材。
一般说来需要至少5μm厚的镀层来保证材料12个月内不过期;3. 焊接前黄铜引脚应该首先镀一层1~3μm的镀层,否则黄铜中的Zn将会影响到焊接质量;4. 合理设置工艺参数,适量提高预热或是焊接温度,保证足够的焊接时间;5. 氮气保护环境中各种焊锡的润湿行为都能得到明显改善;6. 焊接0201以及01005元件时调整原有的工艺参数,减缓预热曲线爬伸斜率,锡膏印刷方面做出调整。
图像:黑焊盘(Black Pad)黑焊盘:指焊盘表面化镍浸金(ENIG)镀层形态良好,但金层下的镍层已变质生成只要为镍的氧化物的脆性黑色物质,对焊点可靠性构成很大威胁。
产生原因:黑盘主要由Ni的氧化物组成,且黑盘面的P含量远高于正常Ni面,说明黑盘主要发生在槽液使用一段时间之后。
1. 化镍层在进行浸金过程中镍的氧化速度大于金的沉积速度,所以产生的镍的氧化物在未完全溶解之前就被金层覆盖从而产生表面金层形态良好,实际镍层已发生变质的现象;2. 沉积的金层原子之间比较疏松,金层下面的镍层得以有继续氧化的机会。
在Galvanic Effect的作用下镍层会继续劣化。
防止措施:目前还没有切实有效防止措施的相关报道,但可以从以下方面进行改善:1. 减少镍槽的寿命,生产中严格把关,控制P的含量在7%左右。
镍槽使用寿命长了之后其中的P含量会增加,从而会加快镍的氧化速度;2. 镍层厚度至少为4μm,这样可以使得镍层相对平坦;金层厚度不要超过0.1μm,过多的金只会使焊点脆化;3. 焊前烘烤板对焊接质量不会起太大促进作用。
黑焊盘在焊接之前就已经产生,烘烤过度反而会使镀层恶化;4. 浸金溶液中加入还原剂,得到半置换半还原的复合金层,但成本会提高2.5倍。
图像:桥连(Bridge)焊锡在毗邻的不同导线或元件之间形成的非正常连接就是通常所说的桥连现象。
产生原因:1. 线路分布太密,引脚太近或不规律;2. 板面或引脚上有残留物;3. 预热温度不够或是助焊剂活性不够;4. 锡膏印刷桥连或是偏移等。
注:一定搭配的焊盘与引脚焊点在一定条件下能承载的钎料(锡膏)量是一定的,处理不当多余的部分都可能造成桥连现象。
防止措施:1. 合理设计焊盘,避免过多采用密集布线;2. 适当提高焊接预热温度,同时可以考虑在一定范围内提高焊接温度以提高焊锡合金流动性;3. 氮气环境中桥连现象有所减少。
返修:产生桥连现象的焊点可以用电烙铁进行返修处理。
图像:不共面/脱焊(Noncoplanar)脱焊容易造成桥连、短路、对不准等现象。
产生原因:1. 元件引脚扁平部分的尺寸不符合规定的尺寸;2. 元件引脚共面性差,平面度公差超过±0.002 英寸,扁平封装器件的引线浮动;3.当 SMD 被夹持时与别的器件发生碰撞而使引脚变形翘曲;4. 焊膏印刷量不足,贴片机贴装时压力太小,焊膏厚度与其上的尺寸不匹配。
防止措施:1. 选用合格的元件;2. 避免操作过程中的损伤;3. 焊膏印刷均匀。
图像:墓碑(Tombstone)墓碑现象指元件一端脱离焊锡,直接造成组装板的失效。
产生原因:墓碑的产生与焊接过程中元件两端受力不均匀有关,组装密集化之后该现象更为突出。
1. 锡膏印刷不均匀;2. 元件贴片不精确;3. 温度不均匀;4. 基板材料的导热系数不同以及热容不同;5. 氮气情况下墓碑现象更为明显;6. 元件与导轨平行排列时更容易出现墓碑现象。
防止措施:1. 提高整个过程中的操作精度—印刷精度、贴片精度、温度均匀性;2. 纸基、玻璃环氧树脂基、陶瓷基,出现墓碑的概率依次减少;3. 对板面元件分布进行合理设计。
图像:助焊剂残留(Flux Residues)板面存在较多的助焊剂残留的话,既影响了板面的光洁程度,同时对PCB板本身的电气性也有一定的影响。
产生原因:1. 助焊剂(锡膏)选型错误。
比如要求采用免清洗助焊剂的场合却采用松香树脂型导致残留较多;2. 助焊剂中松香树脂含量过多或是品质不好容易造成残留过多;3. 清洗不够或是清洗方法不当不能有效清除表面残留;4. 工艺参数不相匹配,助焊剂未能有效挥发掉。
防止措施:1. 正确选用助焊剂;2. 对需要清洗的板进行恰当的清洗处理。
图像:锡瘟(Tin Pest)产生原因:13℃或更低的温度条件下Sn会发生同素异形转变,由灰白色的β-Sn(四角形晶体结构)转变为白色脆性的粉末状α-Sn(立方晶体结构),该转变速度在-30℃的时候达到最大值。
航空以及军事电子经常在该转变温度范围内作业,其长期可靠性受到了极大的挑战。
使用无铅钎料合金同样发现锡瘟现象的存在。
防止措施:可以通过Sn的合金化来防止甚至是消除锡瘟,比如Sn与Bi、Sb的合金或是与Sn有良好互溶性的Pb。
Bi、Sb可以在Sn只溶解0.5%或是更少,但是Pb的溶解量至少要达到5%才能起到作用。
传统的SnPb共晶中Pb的含量在37%,所以以前并没有发现锡瘟现象。
图像:元件侧贴(Billboard)/元件反贴(Upside Down)电阻反贴不可接受,电容反贴虽不可接受,但不会造成太大影响。
侧贴元件还会影响到下一步的组装。
产生原因:在元件编带时就反装,电阻反贴意味着元件相对下边缘更少的绝缘长度(仅仅是剥离层和焊膏阻层),贴装前检查喂料器就可以消除。
返修:不足的焊膏使用专业的钎焊烙铁可以移处。
加一些助焊剂到焊点上,再放置一些断续的纤维,把钎焊烙铁尖放到钎焊合金的上表面进行加热,直到焊膏合金溶化后进入纤维后抬起来。
一次不行可以多次。
使用焊膏丝重新钎焊元件端部。
如果必要的化使用异丙醇、棉花球、或软抹布清洗,直到焊剂被去除。
图像:锡球(Solder Ball)板上粘附的直径大于0.13mm或是距离导线0.13mm以内的球状锡颗粒都被统称为锡球。
锡球违反了最小电气间隙原理会影响到组装板的电气可靠性。
注:IPC规定600mm2内多于5个锡球则被视为缺陷。
产生原因:锡球的产生与焊点的排气过程紧密相连。
焊点中的气氛如果未及时逸出的话可能造成填充空洞现象,如果逸出速度太快的话就会带出焊锡合金粘附到阻焊膜上产生锡球,焊点表面已凝固而内部还处于液态阶段逸出的气体可能产生针孔。
1. 板材中含有过多的水分;2. 阻焊膜未经过良好的处理。
阻焊膜的吸附是产生锡球的一个必要条件;3. 助焊剂使用量太大;4. 预热温度不够,助焊剂未能有效挥发;5. 印刷中的粘附板上的锡膏颗粒容易造成锡球现象。
防止措施:1. 合理设计焊盘;2. 通孔铜层至少25μm以避免止板内所含水汽的影响;3. 采用合适的助焊剂涂敷方式,减少助焊剂中混入的气体量;4. 适当提高预热温度;5. 对板进行焊前烘烤处理;6. 采用合适的阻焊膜。
相对来说平整的阻焊膜表面更容易产生锡球现象。
图像:芯吸(Wick)现象:焊料从焊点位置爬上引脚,而没能实现引脚与焊盘之间的良好结合。
产生原因:1. 元器件的引脚的比热容小,在相同的加热条件下,引脚的升温速率大于PCB焊盘的速率;2. 印刷电路板焊盘可焊性差;3. 过孔设计不合理,影响了焊点热容的损失;4. 焊盘镀层可焊性太差或过期;解决方法: ;H #v K1. 使用较慢的加热速率,降低 PCB焊盘和引脚之间的温差;2. 选用合适的焊盘镀层;3. PCB板过孔的设计不能影响到焊点的热容损失。
图像:焊点空洞(Void)焊点内部填充空洞的出现与助焊剂的蒸发不完全有关。
焊接过程中助焊剂使用量控制不当的很容易出现填充空洞现象。
少量的空洞的出现对焊点不会造成太大影响,但大量出现就会影响到焊点可靠性。
产生原因:1.锡膏中助焊剂比例偏大,难以在焊点凝固之前完全逸出;2. 预热温度偏低,助焊剂中的溶剂难以完全挥发,停留在焊点内部就会造成填充空洞现象;3. 焊接时间过短,气体逸出的时间不够的话同样会产生填充空洞;4. 无铅焊锡合金凝固时一般存在有4%的体积收缩,如果最后凝固区域位于焊点内部的话同样会产生空洞;5. 操作过程中沾染的有机物同样会产生空洞现象;预防措施:1. 调整工艺参数,控制好预热温度以及焊接条件;2. 锡膏中助焊剂的比例适当;3. 避免操作过程中的污染情况发生。
图像:BGA空洞(BGA Void)产生原因:1. 锡膏中助焊剂作用的结果;2. 表面张力作用的结果;3. 温度曲线设置不当,BGA焊球由于位于元件下方,因此常常与其他区域存在有一定温差,需要合理设置温度曲线;4. 板材中含有的水分在焊接过程中进入到焊球当中;5. 如果有铅元件搭配无铅锡膏的话,锡铅合金提前熔化并覆盖住无铅合金,使得无铅合金中的助焊剂难以逸出从而产生填充空洞。
防止措施:1. 合理设置温度曲线;2. 避免无铅材料与有铅材料的混用;3. 不使用过期板材。
图像:元件偏移(Component Excursion)一般说来,元件偏移量大于可焊端宽度的50%被认为是不可接受的,通常要求偏移量小于25%。
产生原因:1. 贴片机精度不够;2. 元件的尺寸容差不符合;3. 焊膏粘性不足或元件贴装时压力不足,传输过程中的振动引起SMD 移动;4. 助焊剂含量太高,再流焊时助焊剂沸腾,SMD 在液态钎剂上移动;5. 焊膏塌边引起偏移;6. 锡膏超过使用期限,助焊剂变质所致;7. 如元件旋转,则由程序旋转角度错误;9. 如果同样程度的元件错位在每块板上都发现,那程序需要被修改,如果在每块板上的错位不同,那么很可能是板的加工问题或位置错误;10. 元件移动或是贴片错位对于 MELF 元件很普通,由于他们的造型特殊,末端提起,元件脱离 PCB 表面,脱离黏合剂。
由于不同的厂商,末端的不断变化使之成为一个变化的问题;11. 风量过大。
防止措施:1. 校准定位坐标,注意元件贴装的准确性;2. 使用粘度大的焊膏,增加元件贴装压力,增大粘结力;3. 选用合适的锡膏,防止焊膏塌陷的出现以及具有合适的助焊剂含量;4. 调整马达转速。